alignment INFINITI FX35 2004 Owner's Manual
[x] Cancel search | Manufacturer: INFINITI, Model Year: 2004, Model line: FX35, Model: INFINITI FX35 2004Pages: 4449, PDF Size: 99.66 MB
Page 3088 of 4449
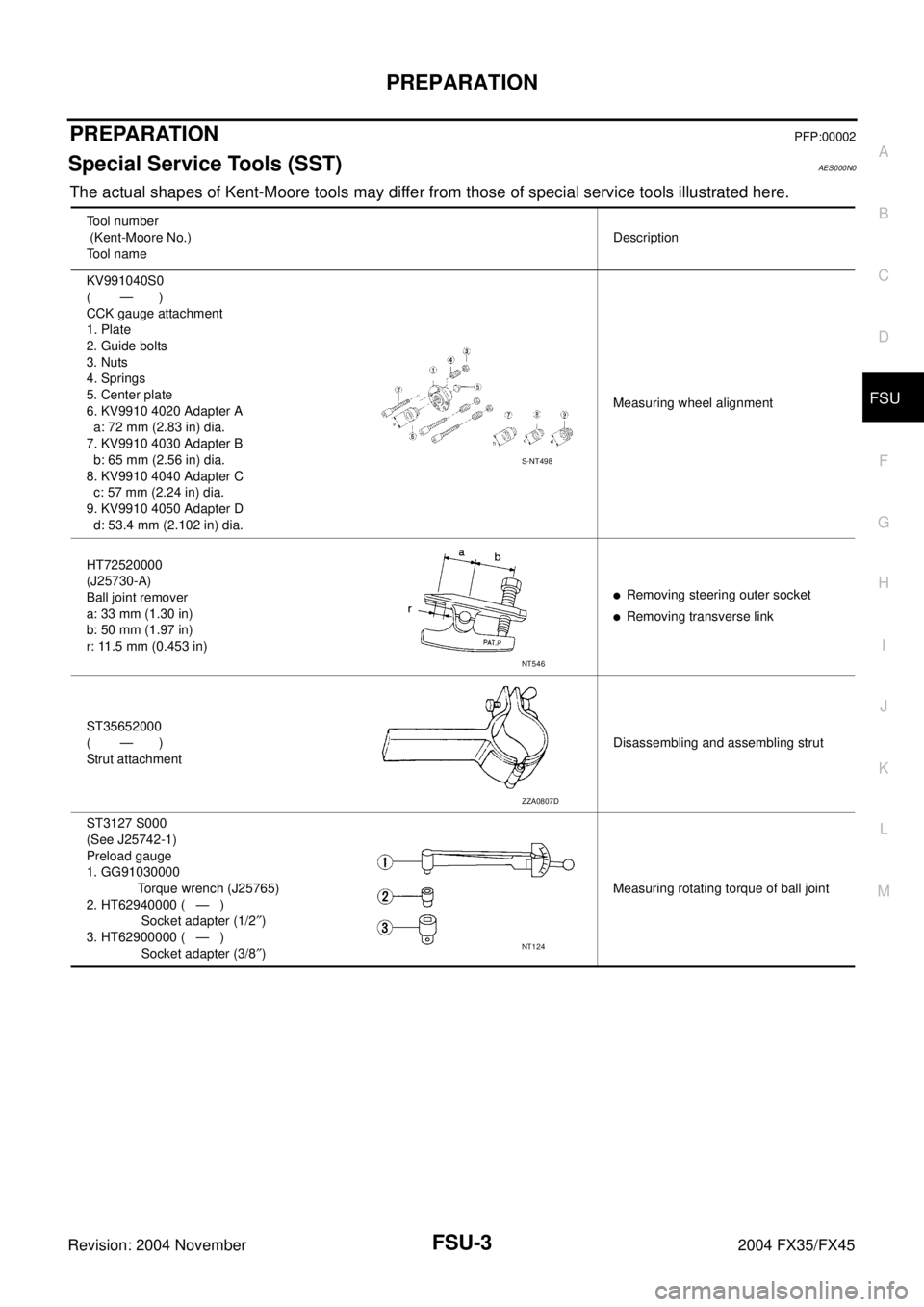
PREPARATION
FSU-3
C
D
F
G
H
I
J
K
L
MA
B
FSU
Revision: 2004 November 2004 FX35/FX45
PREPARATIONPFP:00002
Special Service Tools (SST)AES000N0
The actual shapes of Kent-Moore tools may differ from those of special service tools illustrated here.
Tool number
(Kent-Moore No.)
Tool nameDescription
KV991040S0
( — )
CCK gauge attachment
1. Plate
2. Guide bolts
3. Nuts
4. Springs
5. Center plate
6. KV9910 4020 Adapter A
a: 72 mm (2.83 in) dia.
7. KV9910 4030 Adapter B
b: 65 mm (2.56 in) dia.
8. KV9910 4040 Adapter C
c: 57 mm (2.24 in) dia.
9. KV9910 4050 Adapter D
d: 53.4 mm (2.102 in) dia.Measuring wheel alignment
HT72520000
(J25730-A)
Ball joint remover
a: 33 mm (1.30 in)
b: 50 mm (1.97 in)
r: 11.5 mm (0.453 in)
Removing steering outer socket
Removing transverse link
ST35652000
( — )
Strut attachmentDisassembling and assembling strut
ST3127 S000
(See J25742-1)
Preload gauge
1. GG91030000
Torque wrench (J25765)
2. HT62940000 ( — )
Socket adapter (1/2″)
3. HT62900000 ( — )
Socket adapter (3/8″)Measuring rotating torque of ball joint
S-NT498
NT546
ZZA0807D
NT124
Page 3090 of 4449
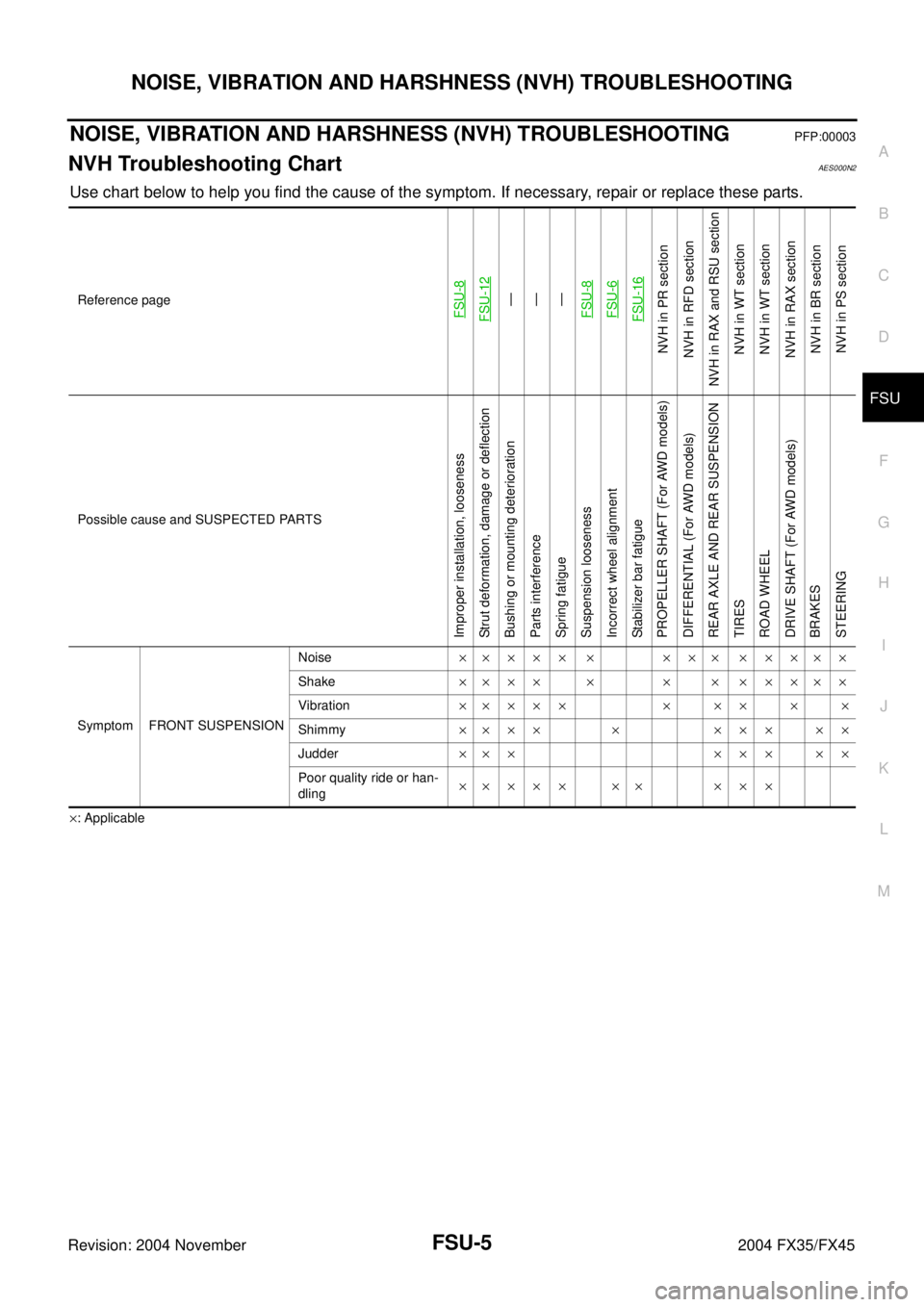
NOISE, VIBRATION AND HARSHNESS (NVH) TROUBLESHOOTING
FSU-5
C
D
F
G
H
I
J
K
L
MA
B
FSU
Revision: 2004 November 2004 FX35/FX45
NOISE, VIBRATION AND HARSHNESS (NVH) TROUBLESHOOTINGPFP:00003
NVH Troubleshooting ChartAES000N2
Use chart below to help you find the cause of the symptom. If necessary, repair or replace these parts.
×: ApplicableReference page
FSU-8FSU-12
—
—
—
FSU-8FSU-6FSU-16
NVH in PR section
NVH in RFD section
NVH in RAX and RSU section
NVH in WT section
NVH in WT section
NVH in RAX section
NVH in BR section
NVH in PS section
Possible cause and SUSPECTED PARTS
Improper installation, looseness
Strut deformation, damage or deflection
Bushing or mounting deterioration
Parts interference
Spring fatigue
Suspension looseness
Incorrect wheel alignment
Stabilizer bar fatigue
PROPELLER SHAFT (For AWD models)
DIFFERENTIAL (For AWD models)
REAR AXLE AND REAR SUSPENSION
TIRES
ROAD WHEEL
DRIVE SHAFT (For AWD models)
BRAKES
STEERING
Symptom FRONT SUSPENSIONNoise××××× × ××× ×××××
Shake×××× × × × ×××××
Vibration××××× × ×× × ×
Shimmy×××× × ××× ××
Judder××× ××× ××
Poor quality ride or han-
dling××××× ×× ×××
Page 3091 of 4449
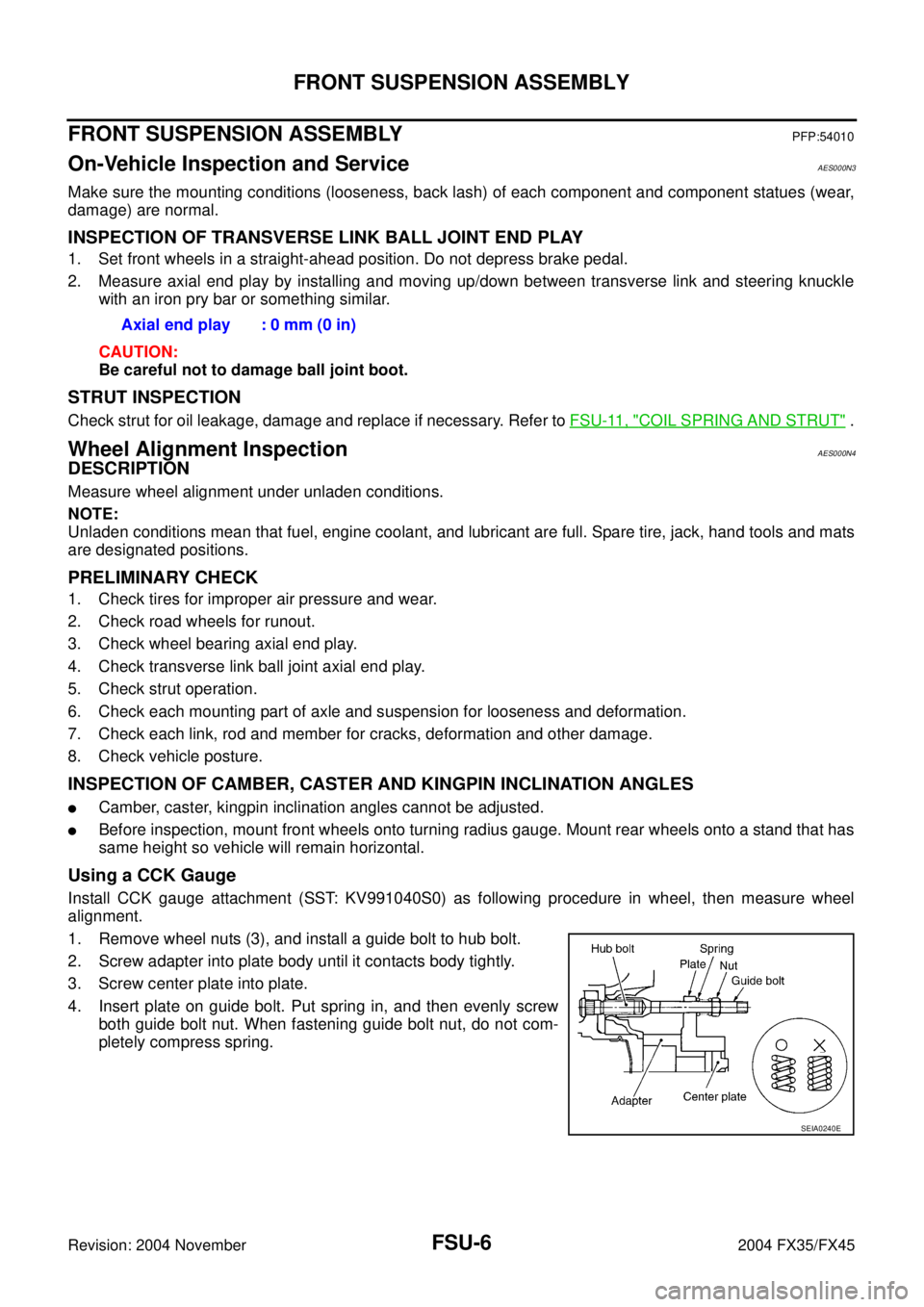
FSU-6
FRONT SUSPENSION ASSEMBLY
Revision: 2004 November 2004 FX35/FX45
FRONT SUSPENSION ASSEMBLYPFP:54010
On-Vehicle Inspection and ServiceAES000N3
Make sure the mounting conditions (looseness, back lash) of each component and component statues (wear,
damage) are normal.
INSPECTION OF TRANSVERSE LINK BALL JOINT END PLAY
1. Set front wheels in a straight-ahead position. Do not depress brake pedal.
2. Measure axial end play by installing and moving up/down between transverse link and steering knuckle
with an iron pry bar or something similar.
CAUTION:
Be careful not to damage ball joint boot.
STRUT INSPECTION
Check strut for oil leakage, damage and replace if necessary. Refer to FSU-11, "COIL SPRING AND STRUT" .
Wheel Alignment InspectionAES000N4
DESCRIPTION
Measure wheel alignment under unladen conditions.
NOTE:
Unladen conditions mean that fuel, engine coolant, and lubricant are full. Spare tire, jack, hand tools and mats
are designated positions.
PRELIMINARY CHECK
1. Check tires for improper air pressure and wear.
2. Check road wheels for runout.
3. Check wheel bearing axial end play.
4. Check transverse link ball joint axial end play.
5. Check strut operation.
6. Check each mounting part of axle and suspension for looseness and deformation.
7. Check each link, rod and member for cracks, deformation and other damage.
8. Check vehicle posture.
INSPECTION OF CAMBER, CASTER AND KINGPIN INCLINATION ANGLES
Camber, caster, kingpin inclination angles cannot be adjusted.
Before inspection, mount front wheels onto turning radius gauge. Mount rear wheels onto a stand that has
same height so vehicle will remain horizontal.
Using a CCK Gauge
Install CCK gauge attachment (SST: KV991040S0) as following procedure in wheel, then measure wheel
alignment.
1. Remove wheel nuts (3), and install a guide bolt to hub bolt.
2. Screw adapter into plate body until it contacts body tightly.
3. Screw center plate into plate.
4. Insert plate on guide bolt. Put spring in, and then evenly screw
both guide bolt nut. When fastening guide bolt nut, do not com-
pletely compress spring.Axial end play : 0 mm (0 in)
SEIA0240E
Page 3092 of 4449
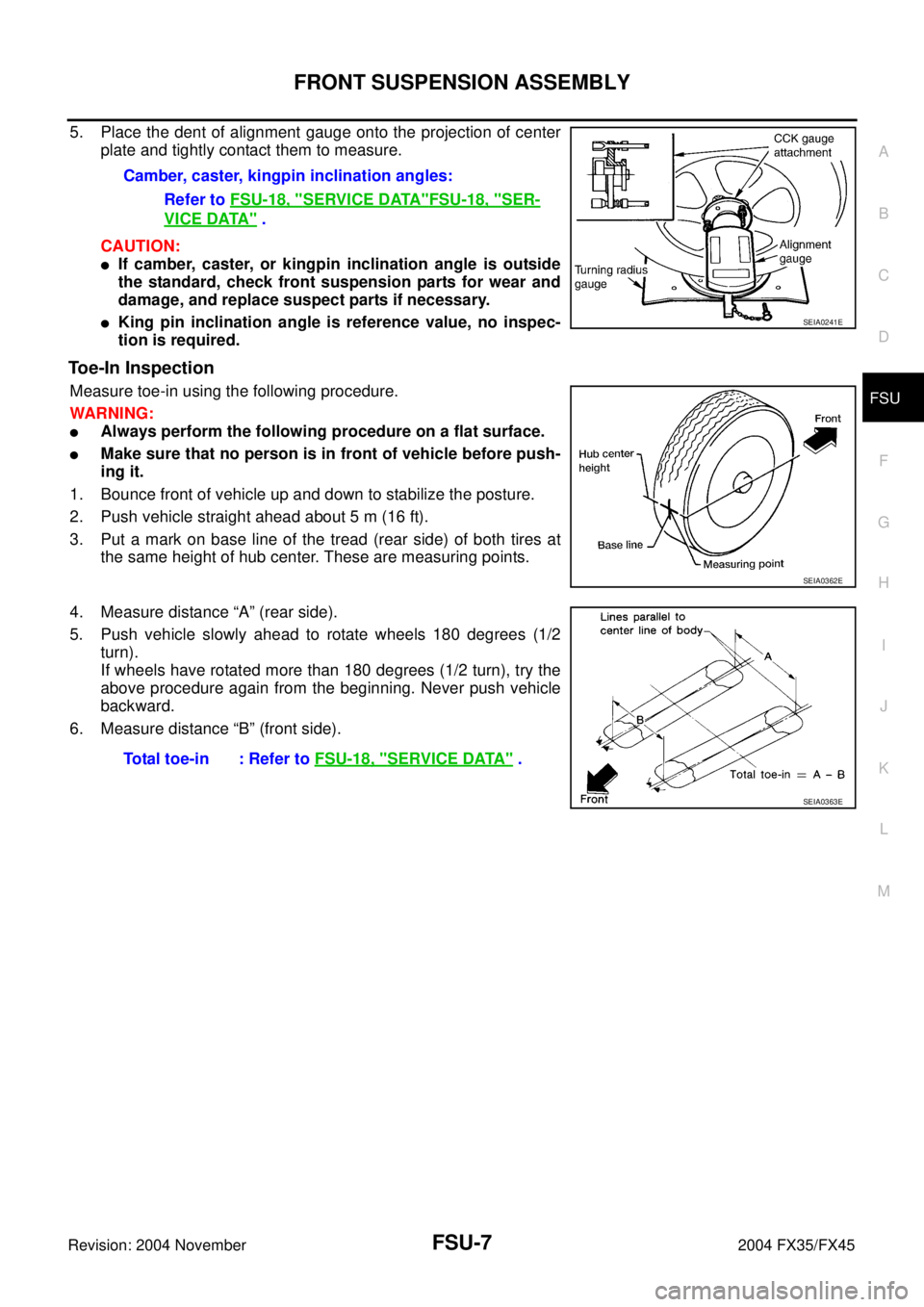
FRONT SUSPENSION ASSEMBLY
FSU-7
C
D
F
G
H
I
J
K
L
MA
B
FSU
Revision: 2004 November 2004 FX35/FX45
5. Place the dent of alignment gauge onto the projection of center
plate and tightly contact them to measure.
CAUTION:
If camber, caster, or kingpin inclination angle is outside
the standard, check front suspension parts for wear and
damage, and replace suspect parts if necessary.
King pin inclination angle is reference value, no inspec-
tion is required.
Toe-In Inspection
Measure toe-in using the following procedure.
WARNING:
Always perform the following procedure on a flat surface.
Make sure that no person is in front of vehicle before push-
ing it.
1. Bounce front of vehicle up and down to stabilize the posture.
2. Push vehicle straight ahead about 5 m (16 ft).
3. Put a mark on base line of the tread (rear side) of both tires at
the same height of hub center. These are measuring points.
4. Measure distance “A” (rear side).
5. Push vehicle slowly ahead to rotate wheels 180 degrees (1/2
turn).
If wheels have rotated more than 180 degrees (1/2 turn), try the
above procedure again from the beginning. Never push vehicle
backward.
6. Measure distance “B” (front side).Camber, caster, kingpin inclination angles:
Refer to FSU-18, "
SERVICE DATA"FSU-18, "SER-
VICE DATA" .
SEIA0241E
SEIA0362E
Total toe-in : Refer to FSU-18, "SERVICE DATA" .
SEIA0363E
Page 3095 of 4449
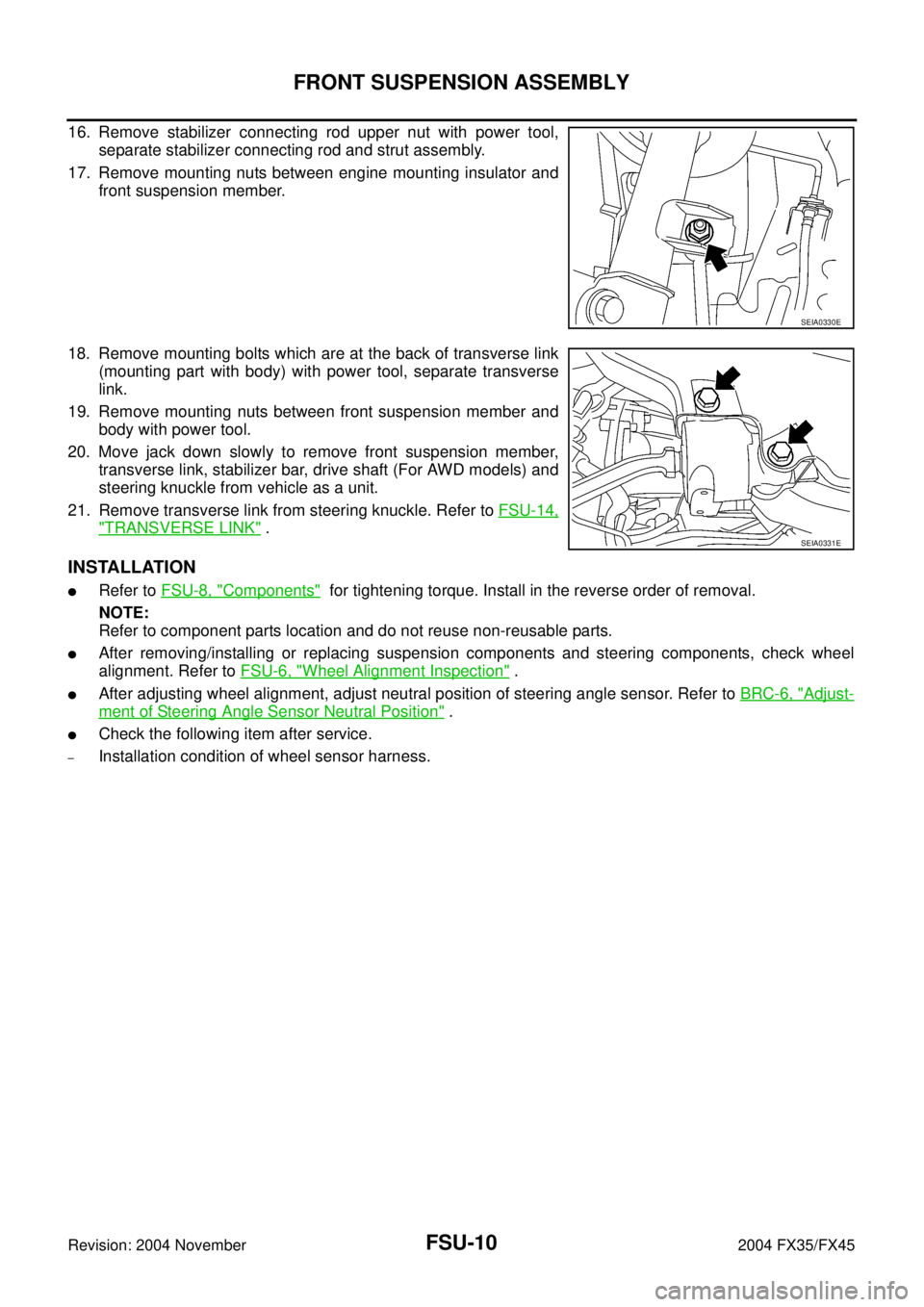
FSU-10
FRONT SUSPENSION ASSEMBLY
Revision: 2004 November 2004 FX35/FX45
16. Remove stabilizer connecting rod upper nut with power tool,
separate stabilizer connecting rod and strut assembly.
17. Remove mounting nuts between engine mounting insulator and
front suspension member.
18. Remove mounting bolts which are at the back of transverse link
(mounting part with body) with power tool, separate transverse
link.
19. Remove mounting nuts between front suspension member and
body with power tool.
20. Move jack down slowly to remove front suspension member,
transverse link, stabilizer bar, drive shaft (For AWD models) and
steering knuckle from vehicle as a unit.
21. Remove transverse link from steering knuckle. Refer to FSU-14,
"TRANSVERSE LINK" .
INSTALLATION
Refer to FSU-8, "Components" for tightening torque. Install in the reverse order of removal.
NOTE:
Refer to component parts location and do not reuse non-reusable parts.
After removing/installing or replacing suspension components and steering components, check wheel
alignment. Refer to FSU-6, "
Wheel Alignment Inspection" .
After adjusting wheel alignment, adjust neutral position of steering angle sensor. Refer to BRC-6, "Adjust-
ment of Steering Angle Sensor Neutral Position" .
Check the following item after service.
–Installation condition of wheel sensor harness.
SEIA0330E
SEIA0331E
Page 3096 of 4449
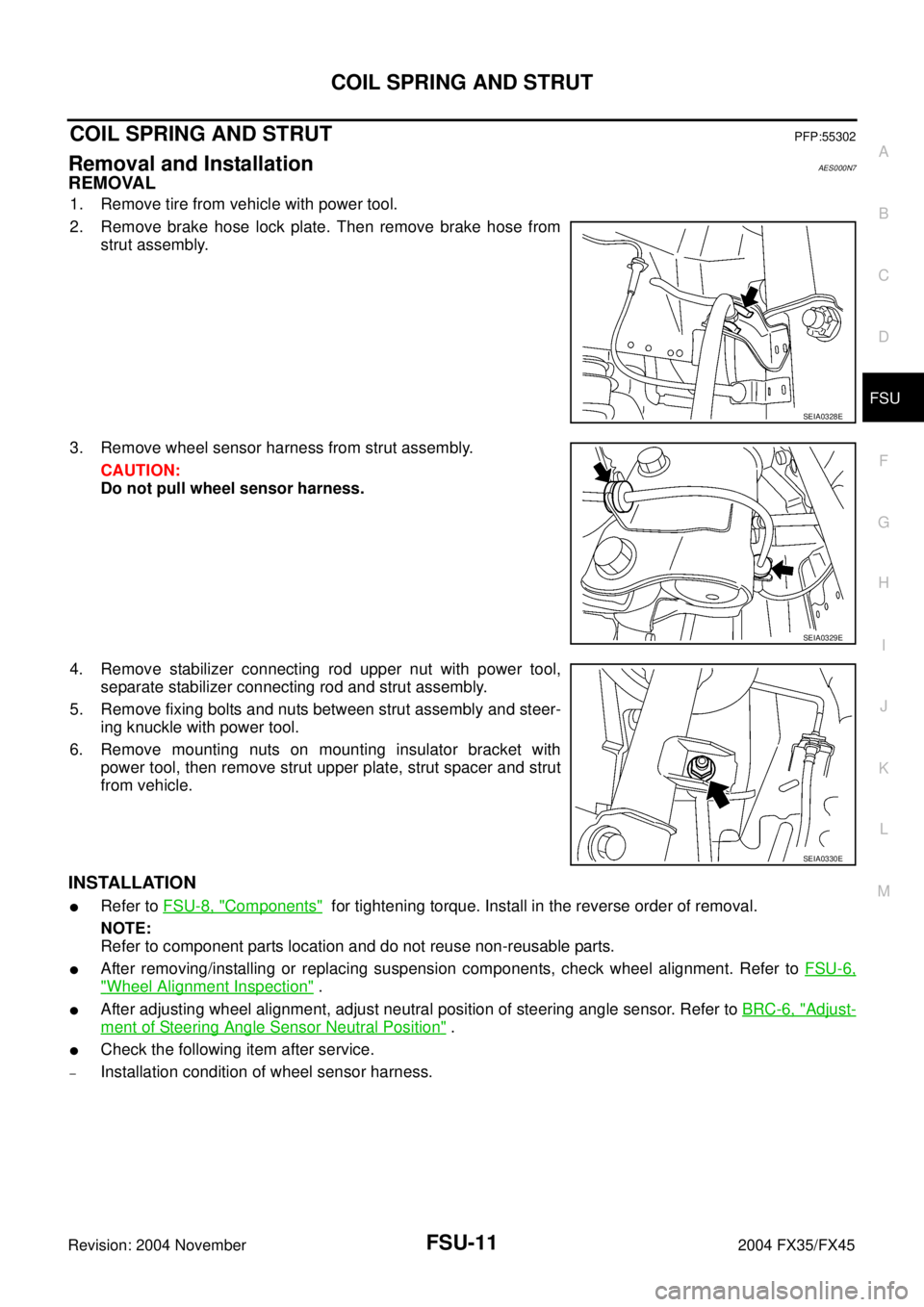
COIL SPRING AND STRUT
FSU-11
C
D
F
G
H
I
J
K
L
MA
B
FSU
Revision: 2004 November 2004 FX35/FX45
COIL SPRING AND STRUTPFP:55302
Removal and InstallationAES000N7
REMOVAL
1. Remove tire from vehicle with power tool.
2. Remove brake hose lock plate. Then remove brake hose from
strut assembly.
3. Remove wheel sensor harness from strut assembly.
CAUTION:
Do not pull wheel sensor harness.
4. Remove stabilizer connecting rod upper nut with power tool,
separate stabilizer connecting rod and strut assembly.
5. Remove fixing bolts and nuts between strut assembly and steer-
ing knuckle with power tool.
6. Remove mounting nuts on mounting insulator bracket with
power tool, then remove strut upper plate, strut spacer and strut
from vehicle.
INSTALLATION
Refer to FSU-8, "Components" for tightening torque. Install in the reverse order of removal.
NOTE:
Refer to component parts location and do not reuse non-reusable parts.
After removing/installing or replacing suspension components, check wheel alignment. Refer to FSU-6,
"Wheel Alignment Inspection" .
After adjusting wheel alignment, adjust neutral position of steering angle sensor. Refer to BRC-6, "Adjust-
ment of Steering Angle Sensor Neutral Position" .
Check the following item after service.
–Installation condition of wheel sensor harness.
SEIA0328E
SEIA0329E
SEIA0330E
Page 3100 of 4449
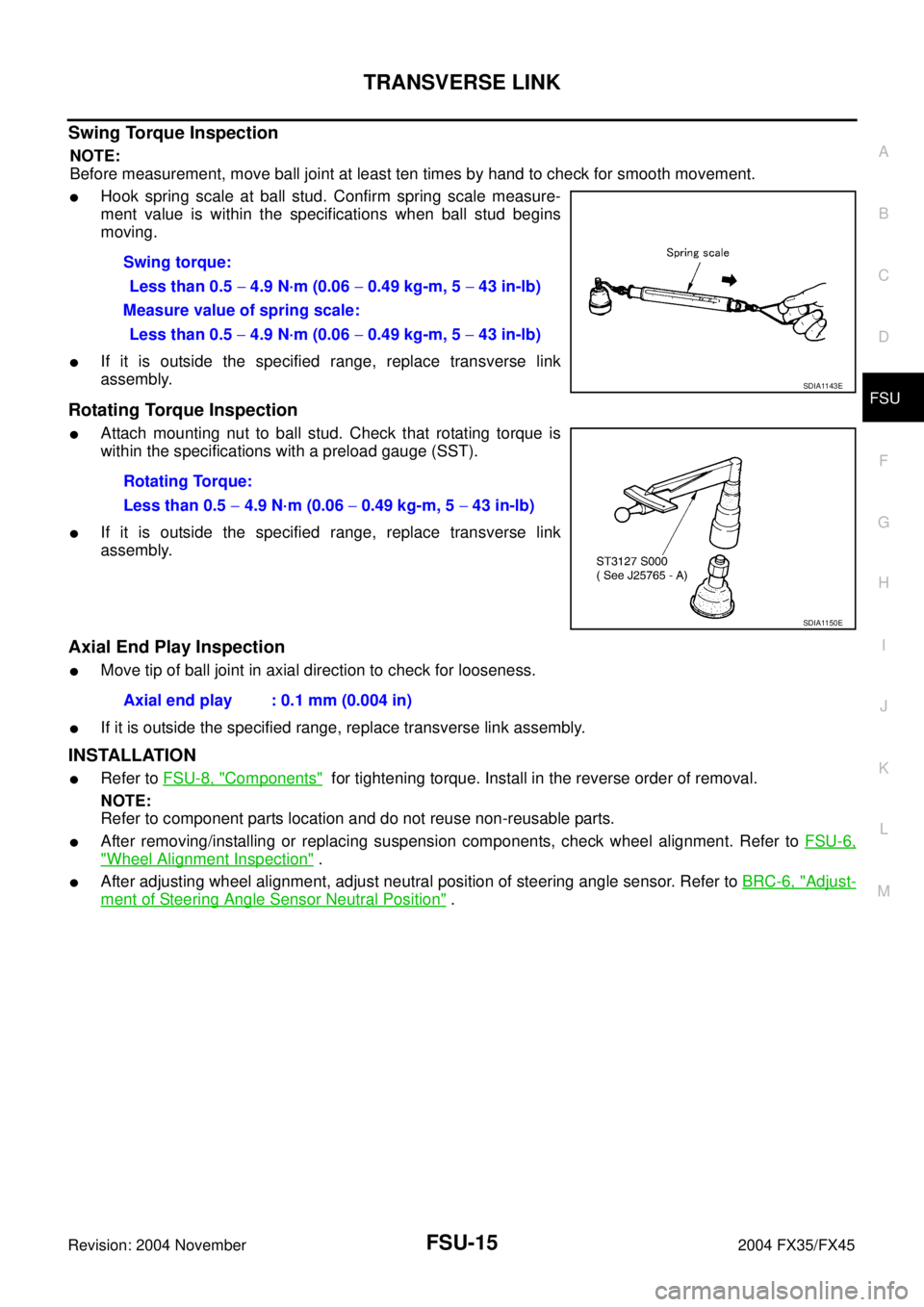
TRANSVERSE LINK
FSU-15
C
D
F
G
H
I
J
K
L
MA
B
FSU
Revision: 2004 November 2004 FX35/FX45
Swing Torque Inspection
NOTE:
Before measurement, move ball joint at least ten times by hand to check for smooth movement.
Hook spring scale at ball stud. Confirm spring scale measure-
ment value is within the specifications when ball stud begins
moving.
If it is outside the specified range, replace transverse link
assembly.
Rotating Torque Inspection
Attach mounting nut to ball stud. Check that rotating torque is
within the specifications with a preload gauge (SST).
If it is outside the specified range, replace transverse link
assembly.
Axial End Play Inspection
Move tip of ball joint in axial direction to check for looseness.
If it is outside the specified range, replace transverse link assembly.
INSTALLATION
Refer to FSU-8, "Components" for tightening torque. Install in the reverse order of removal.
NOTE:
Refer to component parts location and do not reuse non-reusable parts.
After removing/installing or replacing suspension components, check wheel alignment. Refer to FSU-6,
"Wheel Alignment Inspection" .
After adjusting wheel alignment, adjust neutral position of steering angle sensor. Refer to BRC-6, "Adjust-
ment of Steering Angle Sensor Neutral Position" . Swing torque:
Less than 0.5 − 4.9 N·m (0.06 − 0.49 kg-m, 5 − 43 in-lb)
Measure value of spring scale:
Less than 0.5 − 4.9 N·m (0.06 − 0.49 kg-m, 5 − 43 in-lb)
SDIA1143E
Rotating Torque:
Less than 0.5 − 4.9 N·m (0.06 − 0.49 kg-m, 5 − 43 in-lb)
SDIA1150E
Axial end play : 0.1 mm (0.004 in)
Page 3101 of 4449
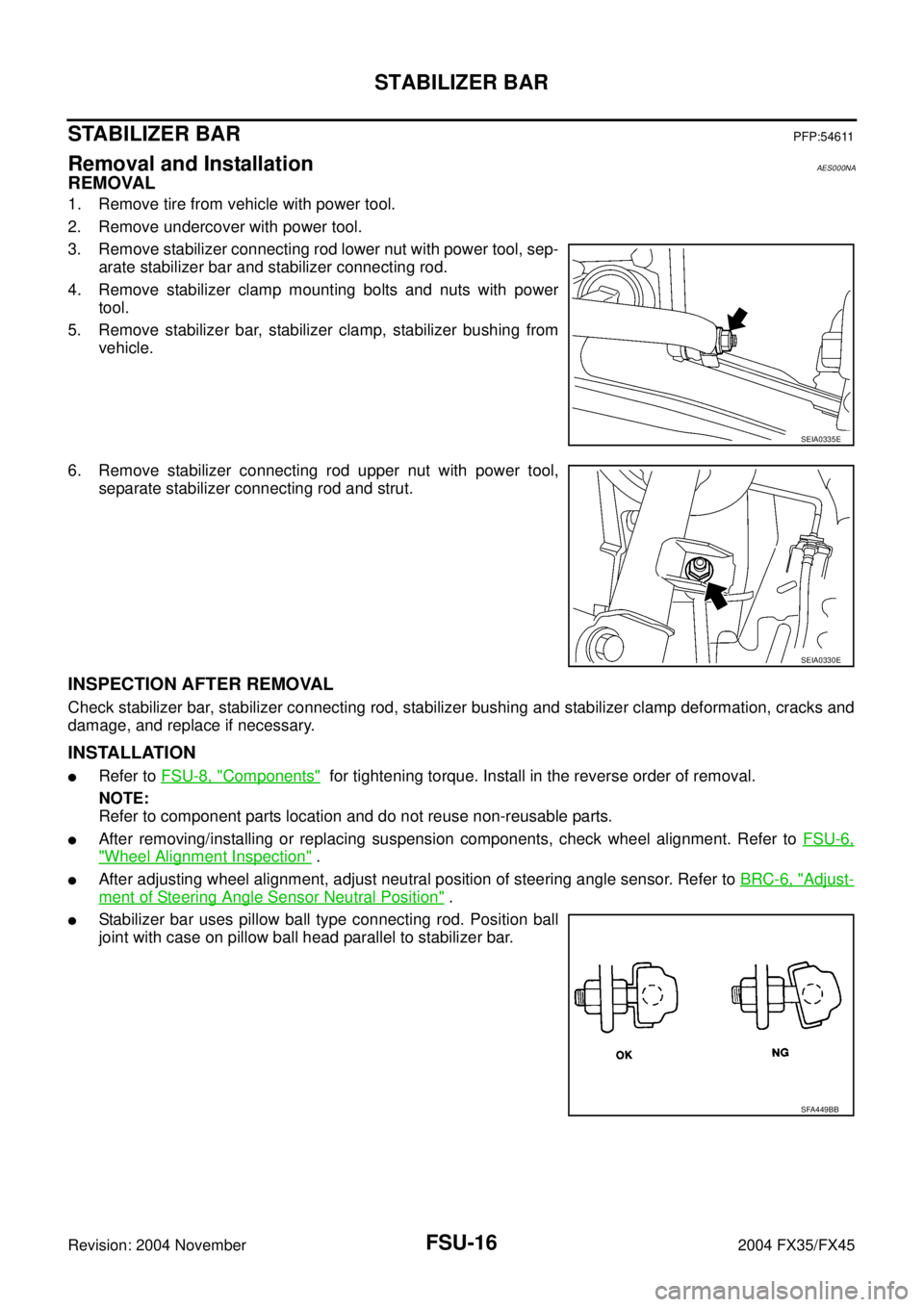
FSU-16
STABILIZER BAR
Revision: 2004 November 2004 FX35/FX45
STABILIZER BARPFP:54611
Removal and InstallationAES000NA
REMOVAL
1. Remove tire from vehicle with power tool.
2. Remove undercover with power tool.
3. Remove stabilizer connecting rod lower nut with power tool, sep-
arate stabilizer bar and stabilizer connecting rod.
4. Remove stabilizer clamp mounting bolts and nuts with power
tool.
5. Remove stabilizer bar, stabilizer clamp, stabilizer bushing from
vehicle.
6. Remove stabilizer connecting rod upper nut with power tool,
separate stabilizer connecting rod and strut.
INSPECTION AFTER REMOVAL
Check stabilizer bar, stabilizer connecting rod, stabilizer bushing and stabilizer clamp deformation, cracks and
damage, and replace if necessary.
INSTALLATION
Refer to FSU-8, "Components" for tightening torque. Install in the reverse order of removal.
NOTE:
Refer to component parts location and do not reuse non-reusable parts.
After removing/installing or replacing suspension components, check wheel alignment. Refer to FSU-6,
"Wheel Alignment Inspection" .
After adjusting wheel alignment, adjust neutral position of steering angle sensor. Refer to BRC-6, "Adjust-
ment of Steering Angle Sensor Neutral Position" .
Stabilizer bar uses pillow ball type connecting rod. Position ball
joint with case on pillow ball head parallel to stabilizer bar.
SEIA0335E
SEIA0330E
SFA449BB
Page 3102 of 4449
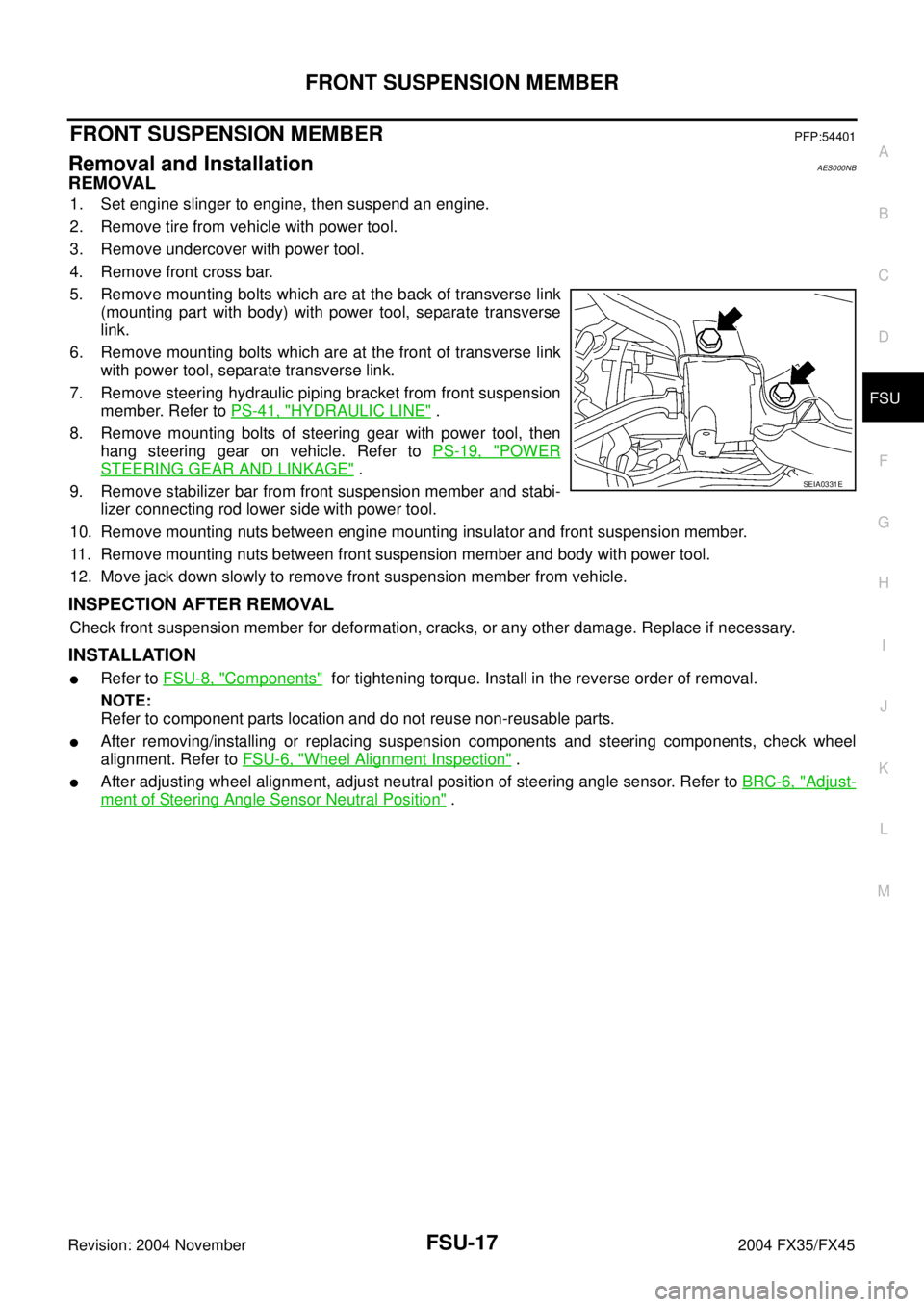
FRONT SUSPENSION MEMBER
FSU-17
C
D
F
G
H
I
J
K
L
MA
B
FSU
Revision: 2004 November 2004 FX35/FX45
FRONT SUSPENSION MEMBERPFP:54401
Removal and InstallationAES000NB
REMOVAL
1. Set engine slinger to engine, then suspend an engine.
2. Remove tire from vehicle with power tool.
3. Remove undercover with power tool.
4. Remove front cross bar.
5. Remove mounting bolts which are at the back of transverse link
(mounting part with body) with power tool, separate transverse
link.
6. Remove mounting bolts which are at the front of transverse link
with power tool, separate transverse link.
7. Remove steering hydraulic piping bracket from front suspension
member. Refer to PS-41, "
HYDRAULIC LINE" .
8. Remove mounting bolts of steering gear with power tool, then
hang steering gear on vehicle. Refer to PS-19, "
POWER
STEERING GEAR AND LINKAGE" .
9. Remove stabilizer bar from front suspension member and stabi-
lizer connecting rod lower side with power tool.
10. Remove mounting nuts between engine mounting insulator and front suspension member.
11. Remove mounting nuts between front suspension member and body with power tool.
12. Move jack down slowly to remove front suspension member from vehicle.
INSPECTION AFTER REMOVAL
Check front suspension member for deformation, cracks, or any other damage. Replace if necessary.
INSTALLATION
Refer to FSU-8, "Components" for tightening torque. Install in the reverse order of removal.
NOTE:
Refer to component parts location and do not reuse non-reusable parts.
After removing/installing or replacing suspension components and steering components, check wheel
alignment. Refer to FSU-6, "
Wheel Alignment Inspection" .
After adjusting wheel alignment, adjust neutral position of steering angle sensor. Refer to BRC-6, "Adjust-
ment of Steering Angle Sensor Neutral Position" .
SEIA0331E
Page 3103 of 4449
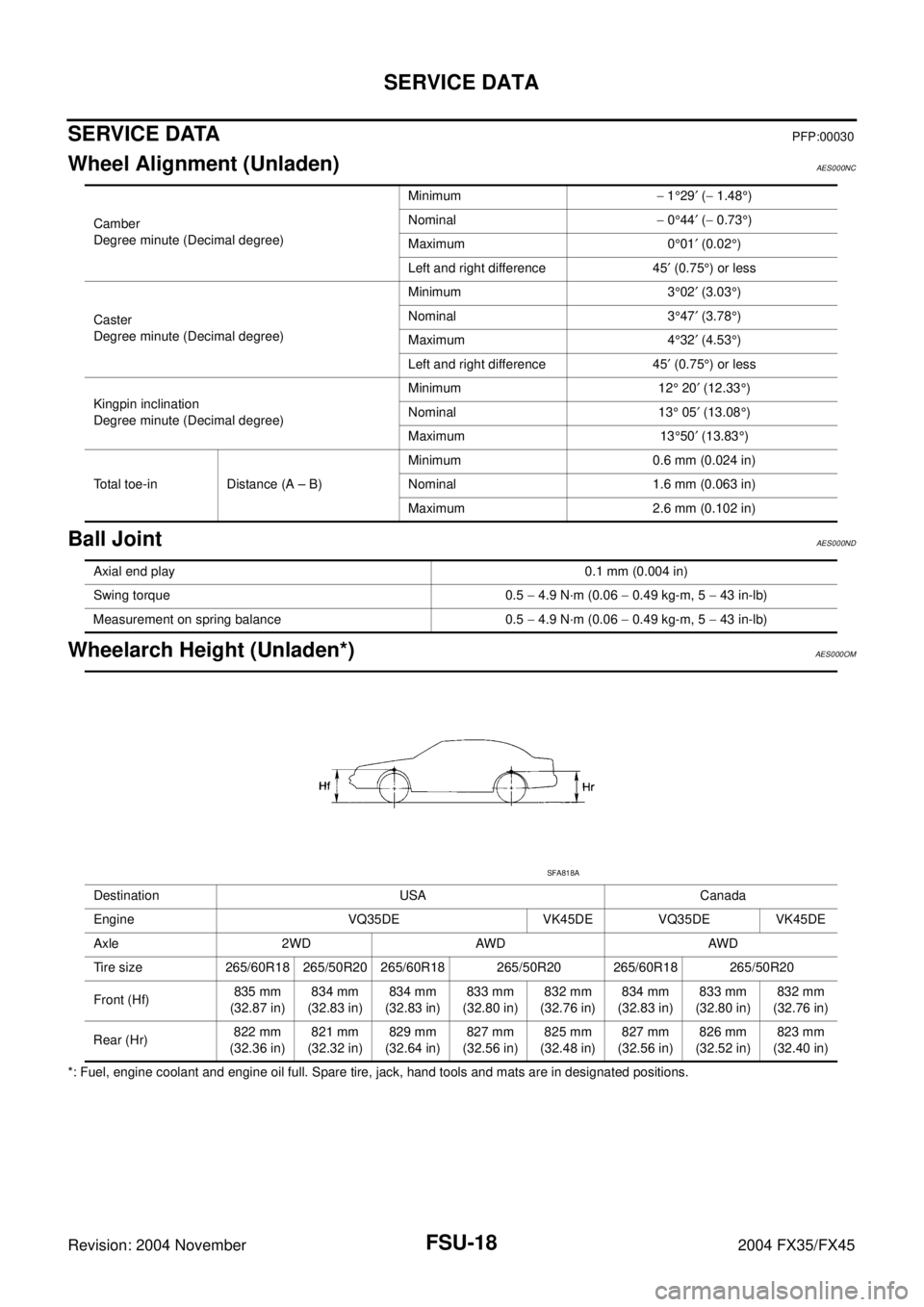
FSU-18
SERVICE DATA
Revision: 2004 November 2004 FX35/FX45
SERVICE DATAPFP:00030
Wheel Alignment (Unladen)AES000NC
Ball JointAES000ND
Wheelarch Height (Unladen*)AES000OM
*: Fuel, engine coolant and engine oil full. Spare tire, jack, hand tools and mats are in designated positions.Camber
Degree minute (Decimal degree)Minimum− 1°29′ (− 1.48°)
Nominal− 0°44′ (− 0.73°)
Maximum 0°01′ (0.02°)
Left and right difference 45′ (0.75°) or less
Caster
Degree minute (Decimal degree)Minimum 3°02′ (3.03°)
Nominal 3°47′ (3.78°)
Maximum 4°32′ (4.53°)
Left and right difference 45′ (0.75°) or less
Kingpin inclination
Degree minute (Decimal degree)Minimum 12° 20′ (12.33°)
Nominal 13° 05′ (13.08°)
Maximum 13°50′ (13.83°)
Total toe-in Distance (A – B)Minimum 0.6 mm (0.024 in)
Nominal 1.6 mm (0.063 in)
Maximum 2.6 mm (0.102 in)
Axial end play 0.1 mm (0.004 in)
Swing torque 0.5 − 4.9 N·m (0.06 − 0.49 kg-m, 5 − 43 in-lb)
Measurement on spring balance 0.5 − 4.9 N·m (0.06 − 0.49 kg-m, 5 − 43 in-lb)
Destination USA Canada
Engine VQ35DE VK45DE VQ35DE VK45DE
Axle 2WD AWD AWD
Tire size 265/60R18 265/50R20 265/60R18 265/50R20 265/60R18 265/50R20
Front (Hf)835 mm
(32.87 in)834 mm
(32.83 in)834 mm
(32.83 in)833 mm
(32.80 in)832 mm
(32.76 in)834 mm
(32.83 in)833 mm
(32.80 in)832 mm
(32.76 in)
Rear (Hr)822 mm
(32.36 in)821 mm
(32.32 in)829 mm
(32.64 in)827 mm
(32.56 in)825 mm
(32.48 in)827 mm
(32.56 in)826 mm
(32.52 in)823 mm
(32.40 in)
SFA818A