Engine INFINITI FX35 2004 Service Manual
[x] Cancel search | Manufacturer: INFINITI, Model Year: 2004, Model line: FX35, Model: INFINITI FX35 2004Pages: 4449, PDF Size: 99.66 MB
Page 2675 of 4449
![INFINITI FX35 2004 Service Manual EC-1334
[VK45DE]
AUTOMATIC SPEED CONTROL DEVICE (ASCD)
Revision: 2004 November 2004 FX35/FX45
AUTOMATIC SPEED CONTROL DEVICE (ASCD)PFP:18930
System DescriptionABS00CG0
INPUT/OUTPUT SIGNAL CHART
*: Thi INFINITI FX35 2004 Service Manual EC-1334
[VK45DE]
AUTOMATIC SPEED CONTROL DEVICE (ASCD)
Revision: 2004 November 2004 FX35/FX45
AUTOMATIC SPEED CONTROL DEVICE (ASCD)PFP:18930
System DescriptionABS00CG0
INPUT/OUTPUT SIGNAL CHART
*: Thi](/img/42/57021/w960_57021-2674.png)
EC-1334
[VK45DE]
AUTOMATIC SPEED CONTROL DEVICE (ASCD)
Revision: 2004 November 2004 FX35/FX45
AUTOMATIC SPEED CONTROL DEVICE (ASCD)PFP:18930
System DescriptionABS00CG0
INPUT/OUTPUT SIGNAL CHART
*: This signal is sent to the ECM through CAN communication line.
BASIC ASCD SYSTEM
Refer to Owner's Manual for ASCD operating instructions.
Automatic Speed Control Device (ASCD) allows a driver to keep vehicle at predetermined constant speed
without pressing accelerator pedal. Driver can set vehicle speed in advance between approximately 40 km/h
(25 MPH) and 144 km/h (89 MPH).
ECM controls throttle angle of electric throttle control actuator to regulate engine speed.
Operation status of ASCD is indicated by CRUISE indicator and SET indicator in combination meter. If any
malfunction occurs in ASCD system, it automatically deactivates control.
SET OPERATION
Press ON/OFF (MAIN) switch. (The CRUISE indicator in combination meter illuminates.)
When vehicle speed reaches a desired speed between approximately 40 km/h (25 MPH) and 144 km/h (89
MPH), press COAST/SET switch. (Then SET indicator in combination meter illuminates.)
ACCEL OPERATION
If the ACCEL/RESUME switch is pressed during cruise control driving, increase the vehicle speed until the
switch is released or vehicle speed reaches maximum speed controlled by the system.
And then ASCD will keep the new set speed.
CANCEL OPERATION
When any of following conditions exist, cruise operation will be canceled.
CANCEL switch is pressed
More than 2 switches at ASCD steering switch are pressed at the same time (Set speed will be cleared)
Brake pedal is depressed
Selector lever is changed to N, P, R position
Vehicle speed decreased to 13 km/h (8 MPH) lower than the set speed
VDC/TCS system is operated
When the ECM detects any of the following conditions, the ECM will cancel the cruise operation and inform
the driver by blinking indicator lamp.
Engine coolant temperature is slightly higher than the normal operating temperature, CRUISE lamp may
blink slowly.
When the engine coolant temperature decreases to the normal operating temperature, CRUISE lamp will
stop blinking and the cruise operation will be able to work by pressing COAST/SET switch or ACCEL/
RESUME switch.
Malfunction for some self-diagnoses regarding ASCD control: SET lamp will blink quickly.
If ON/OFF (MAIN) switch is turned to OFF during ASCD is activated, all of ASCD operations will be canceled
and vehicle speed memory will be erased.
COAST OPERATION
When the COAST/SET switch is pressed during cruise control driving, decrease vehicle set speed until the
switch is released. And then ASCD will keep the new set speed.
Sensor Input signal to ECM ECM function Actuator
ASCD brake switch Brake pedal operation
ASCD vehicle speed controlElectric throttle control
actuator Stop lamp switch Brake pedal operation
ASCD steering switch ASCD steering switch operation
Park/Neutral position (PNP)
switchGear position
Unified meter and A/C amp.* Vehicle speed
TCM* Powertrain revolution
Page 2677 of 4449
![INFINITI FX35 2004 Service Manual EC-1336
[VK45DE]
SERVICE DATA AND SPECIFICATIONS (SDS)
Revision: 2004 November 2004 FX35/FX45
SERVICE DATA AND SPECIFICATIONS (SDS)PFP:00030
Fuel PressureABS00CG2
Idle Speed and Ignition TimingABS00CG INFINITI FX35 2004 Service Manual EC-1336
[VK45DE]
SERVICE DATA AND SPECIFICATIONS (SDS)
Revision: 2004 November 2004 FX35/FX45
SERVICE DATA AND SPECIFICATIONS (SDS)PFP:00030
Fuel PressureABS00CG2
Idle Speed and Ignition TimingABS00CG](/img/42/57021/w960_57021-2676.png)
EC-1336
[VK45DE]
SERVICE DATA AND SPECIFICATIONS (SDS)
Revision: 2004 November 2004 FX35/FX45
SERVICE DATA AND SPECIFICATIONS (SDS)PFP:00030
Fuel PressureABS00CG2
Idle Speed and Ignition TimingABS00CG3
*1: Under the following conditions:
Air conditioner switch: OFF
Electric load: OFF (Lights, heater fan & rear window defogger)
Steering wheel: Kept in straight-ahead position
Calculated Load ValueABS00CG4
Mass Air Flow SensorABS00CG5
*: Engine is warmed up to normal operating temperature and running under no-load.
Intake Air Temperature SensorABS00CG6
Engine Coolant Temperature SensorABS00CG7
Heated Oxygen Sensor 1 HeaterABS00CG8
Heated Oxygen Sensor 2 HeaterABS00CG9
Crankshaft Position Sensor (POS)ABS00CGA
Refer to EC-964, "Component Inspection" .
Camshaft Position Sensor (PHASE)ABS00CGB
Refer to EC-970, "Component Inspection" .
Throttle Control MotorABS00CGC
Fuel pressure at idling kPa (kg/cm2 , psi)Approximately 350 (3.57, 51)
Target idle speed
No-load*1 (in P or N position)650±50 rpm
Air conditioner: ON In P or N position 700 rpm or more
Ignition timing In P or N position 12° ± 5° BTDC
Condition Calculated load value% (Using CONSULT-II or GST)
At idle14.0 - 33.0
At 2,500 rpm12.0 - 25.0
Supply voltageBattery voltage (11 - 14V)
Output voltage at idle1.2 - 1.8V*
Mass air flow (Using CONSULT-II or GST)2.0 - 6.0 g·m/sec at idle*
7.0 - 20.0 g·m/sec at 2,500 rpm*
Temperature °C (°F) Resistance kΩ
25 (77)1.9 - 2.1
80 (176)0.31 - 0.37
Temperature °C (°F) Resistance kΩ
20 (68)2.1 - 2.9
50 (122)0.68 - 1.00
90 (194)0.236 - 0.260
Resistance [at 25°C (77°F)] 3.3 - 4.0Ω
Resistance [at 25°C (77°F)] 5.0 - 7.0Ω
Resistance [at 25°C (77°F)] Approximately 1 - 15Ω
Page 2683 of 4449
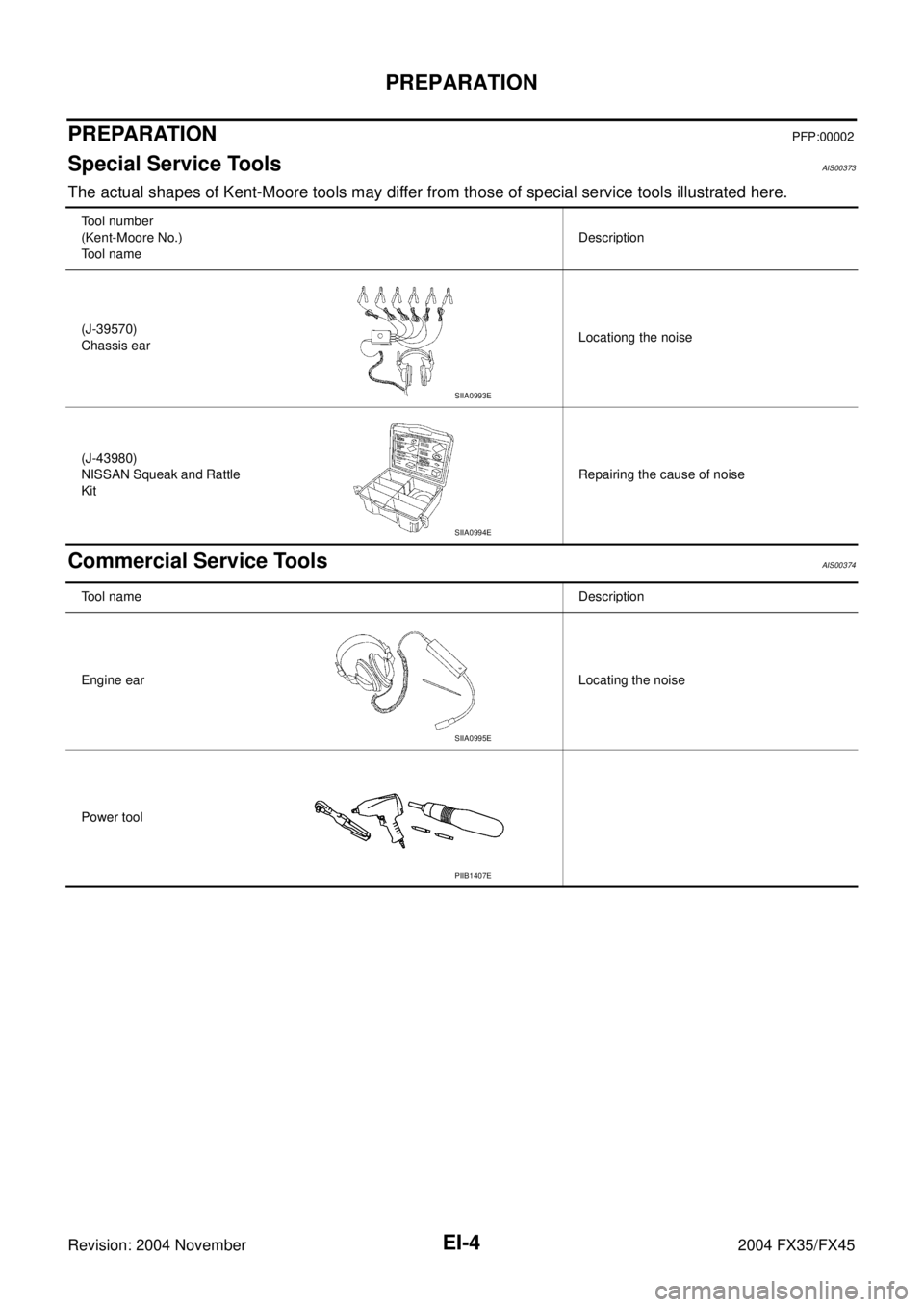
EI-4
PREPARATION
Revision: 2004 November 2004 FX35/FX45
PREPARATIONPFP:00002
Special Service ToolsAIS00373
The actual shapes of Kent-Moore tools may differ from those of special service tools illustrated here.
Commercial Service ToolsAIS00374
Tool number
(Kent-Moore No.)
Tool nameDescription
(J-39570)
Chassis earLocationg the noise
(J-43980)
NISSAN Squeak and Rattle
KitRepairing the cause of noise
SIIA0993E
SIIA0994E
Tool nameDescription
Engine earLocating the noise
Power tool
SIIA0995E
PIIB1407E
Page 2685 of 4449
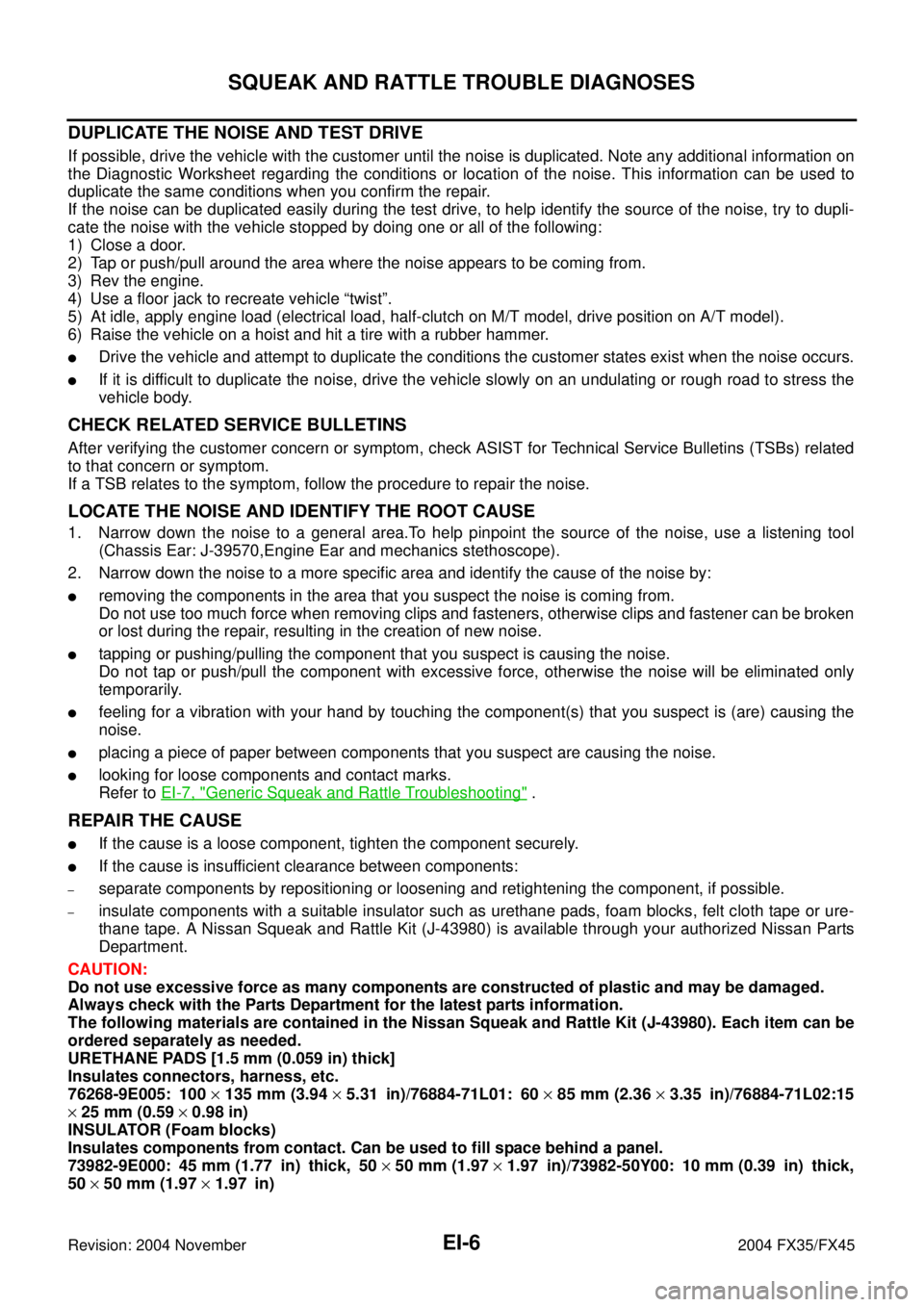
EI-6
SQUEAK AND RATTLE TROUBLE DIAGNOSES
Revision: 2004 November 2004 FX35/FX45
DUPLICATE THE NOISE AND TEST DRIVE
If possible, drive the vehicle with the customer until the noise is duplicated. Note any additional information on
the Diagnostic Worksheet regarding the conditions or location of the noise. This information can be used to
duplicate the same conditions when you confirm the repair.
If the noise can be duplicated easily during the test drive, to help identify the source of the noise, try to dupli-
cate the noise with the vehicle stopped by doing one or all of the following:
1) Close a door.
2) Tap or push/pull around the area where the noise appears to be coming from.
3) Rev the engine.
4) Use a floor jack to recreate vehicle “twist”.
5) At idle, apply engine load (electrical load, half-clutch on M/T model, drive position on A/T model).
6) Raise the vehicle on a hoist and hit a tire with a rubber hammer.
Drive the vehicle and attempt to duplicate the conditions the customer states exist when the noise occurs.
If it is difficult to duplicate the noise, drive the vehicle slowly on an undulating or rough road to stress the
vehicle body.
CHECK RELATED SERVICE BULLETINS
After verifying the customer concern or symptom, check ASIST for Technical Service Bulletins (TSBs) related
to that concern or symptom.
If a TSB relates to the symptom, follow the procedure to repair the noise.
LOCATE THE NOISE AND IDENTIFY THE ROOT CAUSE
1. Narrow down the noise to a general area.To help pinpoint the source of the noise, use a listening tool
(Chassis Ear: J-39570,Engine Ear and mechanics stethoscope).
2. Narrow down the noise to a more specific area and identify the cause of the noise by:
removing the components in the area that you suspect the noise is coming from.
Do not use too much force when removing clips and fasteners, otherwise clips and fastener can be broken
or lost during the repair, resulting in the creation of new noise.
tapping or pushing/pulling the component that you suspect is causing the noise.
Do not tap or push/pull the component with excessive force, otherwise the noise will be eliminated only
temporarily.
feeling for a vibration with your hand by touching the component(s) that you suspect is (are) causing the
noise.
placing a piece of paper between components that you suspect are causing the noise.
looking for loose components and contact marks.
Refer to EI-7, "
Generic Squeak and Rattle Troubleshooting" .
REPAIR THE CAUSE
If the cause is a loose component, tighten the component securely.
If the cause is insufficient clearance between components:
–separate components by repositioning or loosening and retightening the component, if possible.
–insulate components with a suitable insulator such as urethane pads, foam blocks, felt cloth tape or ure-
thane tape. A Nissan Squeak and Rattle Kit (J-43980) is available through your authorized Nissan Parts
Department.
CAUTION:
Do not use excessive force as many components are constructed of plastic and may be damaged.
Always check with the Parts Department for the latest parts information.
The following materials are contained in the Nissan Squeak and Rattle Kit (J-43980). Each item can be
ordered separately as needed.
URETHANE PADS [1.5 mm (0.059 in) thick]
Insulates connectors, harness, etc.
76268-9E005: 100 × 135 mm (3.94 × 5.31 in)/76884-71L01: 60 × 85 mm (2.36 × 3.35 in)/76884-71L02:15
× 25 mm (0.59 × 0.98 in)
INSULATOR (Foam blocks)
Insulates components from contact. Can be used to fill space behind a panel.
73982-9E000: 45 mm (1.77 in) thick, 50 × 50 mm (1.97 × 1.97 in)/73982-50Y00: 10 mm (0.39 in) thick,
50 × 50 mm (1.97 × 1.97 in)
Page 2687 of 4449
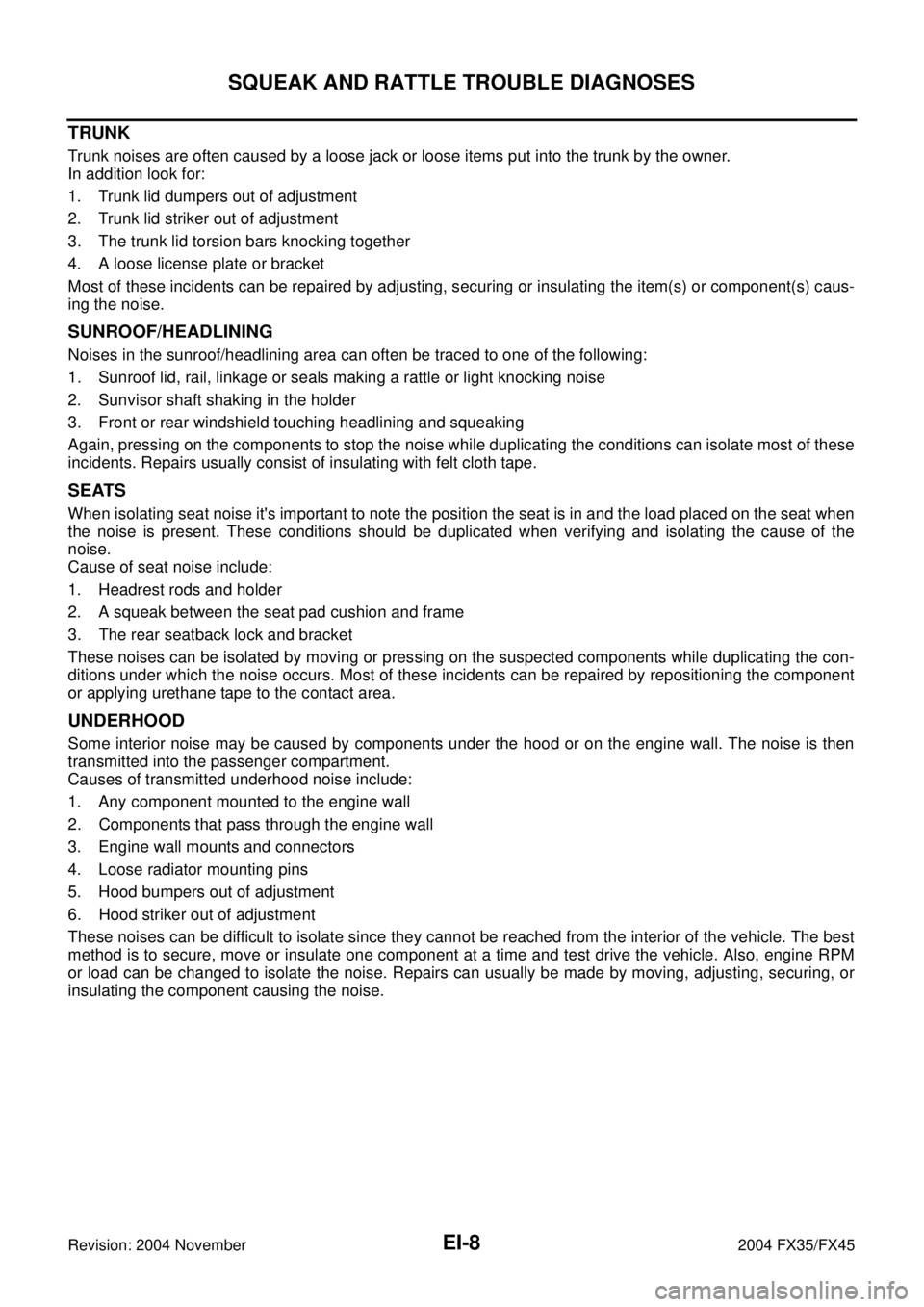
EI-8
SQUEAK AND RATTLE TROUBLE DIAGNOSES
Revision: 2004 November 2004 FX35/FX45
TRUNK
Trunk noises are often caused by a loose jack or loose items put into the trunk by the owner.
In addition look for:
1. Trunk lid dumpers out of adjustment
2. Trunk lid striker out of adjustment
3. The trunk lid torsion bars knocking together
4. A loose license plate or bracket
Most of these incidents can be repaired by adjusting, securing or insulating the item(s) or component(s) caus-
ing the noise.
SUNROOF/HEADLINING
Noises in the sunroof/headlining area can often be traced to one of the following:
1. Sunroof lid, rail, linkage or seals making a rattle or light knocking noise
2. Sunvisor shaft shaking in the holder
3. Front or rear windshield touching headlining and squeaking
Again, pressing on the components to stop the noise while duplicating the conditions can isolate most of these
incidents. Repairs usually consist of insulating with felt cloth tape.
SEATS
When isolating seat noise it's important to note the position the seat is in and the load placed on the seat when
the noise is present. These conditions should be duplicated when verifying and isolating the cause of the
noise.
Cause of seat noise include:
1. Headrest rods and holder
2. A squeak between the seat pad cushion and frame
3. The rear seatback lock and bracket
These noises can be isolated by moving or pressing on the suspected components while duplicating the con-
ditions under which the noise occurs. Most of these incidents can be repaired by repositioning the component
or applying urethane tape to the contact area.
UNDERHOOD
Some interior noise may be caused by components under the hood or on the engine wall. The noise is then
transmitted into the passenger compartment.
Causes of transmitted underhood noise include:
1. Any component mounted to the engine wall
2. Components that pass through the engine wall
3. Engine wall mounts and connectors
4. Loose radiator mounting pins
5. Hood bumpers out of adjustment
6. Hood striker out of adjustment
These noises can be difficult to isolate since they cannot be reached from the interior of the vehicle. The best
method is to secure, move or insulate one component at a time and test drive the vehicle. Also, engine RPM
or load can be changed to isolate the noise. Repairs can usually be made by moving, adjusting, securing, or
insulating the component causing the noise.
Page 2726 of 4449
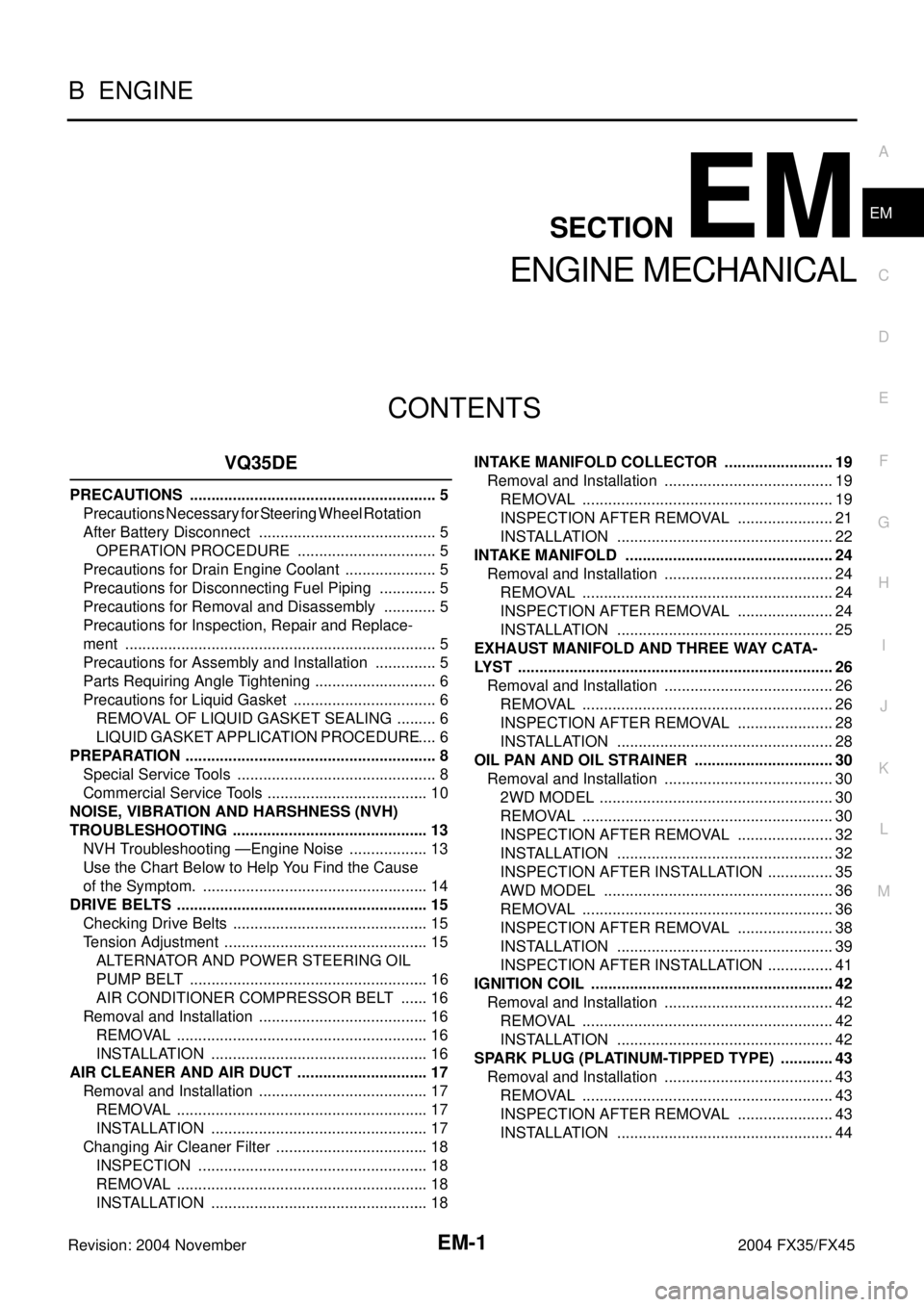
EM-1
ENGINE MECHANICAL
B ENGINE
CONTENTS
C
D
E
F
G
H
I
J
K
L
M
SECTION EM
A
EM
Revision: 2004 November 2004 FX35/FX45
ENGINE MECHANICAL
VQ35DE
PRECAUTIONS .......................................................... 5
Precautions Necessary for Steering Wheel Rotation
After Battery Disconnect .......................................... 5
OPERATION PROCEDURE ................................. 5
Precautions for Drain Engine Coolant ...................... 5
Precautions for Disconnecting Fuel Piping .............. 5
Precautions for Removal and Disassembly ............. 5
Precautions for Inspection, Repair and Replace-
ment ......................................................................... 5
Precautions for Assembly and Installation ............... 5
Parts Requiring Angle Tightening ............................. 6
Precautions for Liquid Gasket .................................. 6
REMOVAL OF LIQUID GASKET SEALING .......... 6
LIQUID GASKET APPLICATION PROCEDURE ..... 6
PREPARATION ........................................................... 8
Special Service Tools ............................................... 8
Commercial Service Tools ...................................... 10
NOISE, VIBRATION AND HARSHNESS (NVH)
TROUBLESHOOTING .............................................. 13
NVH Troubleshooting —Engine Noise ................... 13
Use the Chart Below to Help You Find the Cause
of the Symptom. ..................................................... 14
DRIVE BELTS ........................................................... 15
Checking Drive Belts .............................................. 15
Tension Adjustment ................................................ 15
ALTERNATOR AND POWER STEERING OIL
PUMP BELT ........................................................ 16
AIR CONDITIONER COMPRESSOR BELT ....... 16
Removal and Installation ........................................ 16
REMOVAL ........................................................... 16
INSTALLATION ................................................... 16
AIR CLEANER AND AIR DUCT ............................... 17
Removal and Installation ........................................ 17
REMOVAL ........................................................... 17
INSTALLATION ................................................... 17
Changing Air Cleaner Filter .................................... 18
INSPECTION ...................................................... 18
REMOVAL ........................................................... 18
INSTALLATION ................................................... 18INTAKE MANIFOLD COLLECTOR .......................... 19
Removal and Installation ........................................ 19
REMOVAL ........................................................... 19
INSPECTION AFTER REMOVAL ....................... 21
INSTALLATION ................................................... 22
INTAKE MANIFOLD ................................................. 24
Removal and Installation ........................................ 24
REMOVAL ........................................................... 24
INSPECTION AFTER REMOVAL ....................... 24
INSTALLATION ................................................... 25
EXHAUST MANIFOLD AND THREE WAY CATA-
LYST .......................................................................... 26
Removal and Installation ........................................ 26
REMOVAL ........................................................... 26
INSPECTION AFTER REMOVAL ....................... 28
INSTALLATION ................................................... 28
OIL PAN AND OIL STRAINER ................................. 30
Removal and Installation ........................................ 30
2WD MODEL ....................................................... 30
REMOVAL ........................................................... 30
INSPECTION AFTER REMOVAL ....................... 32
INSTALLATION ................................................... 32
INSPECTION AFTER INSTALLATION ................ 35
AWD MODEL ...................................................... 36
REMOVAL ........................................................... 36
INSPECTION AFTER REMOVAL ....................... 38
INSTALLATION ................................................... 39
INSPECTION AFTER INSTALLATION ................ 41
IGNITION COIL ......................................................... 42
Removal and Installation ........................................ 42
REMOVAL ........................................................... 42
INSTALLATION ................................................... 42
SPARK PLUG (PLATINUM-TIPPED TYPE) ............. 43
Removal and Installation ........................................ 43
REMOVAL ........................................................... 43
INSPECTION AFTER REMOVAL ....................... 43
INSTALLATION ................................................... 44
Page 2727 of 4449
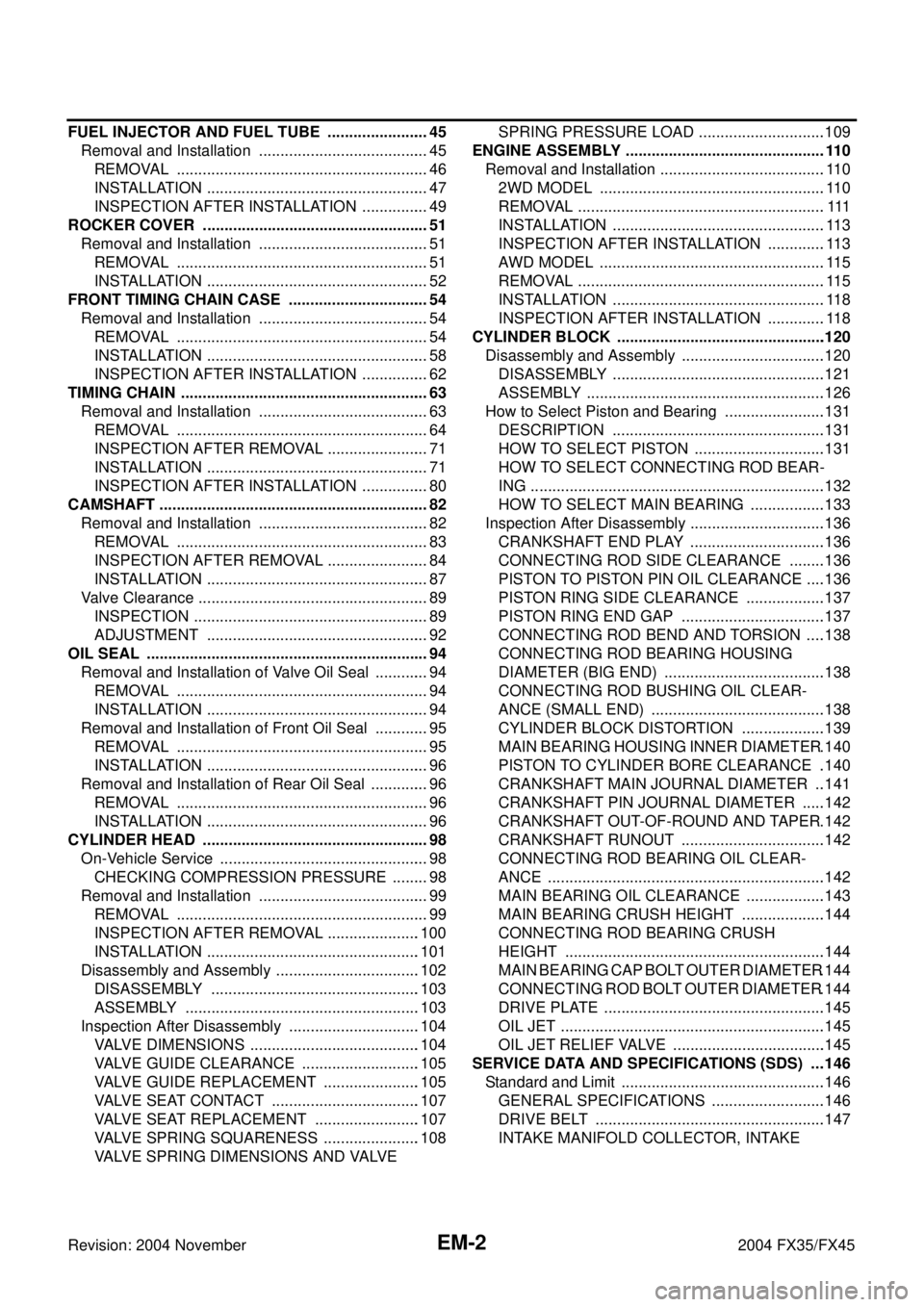
EM-2Revision: 2004 November 2004 FX35/FX45 FUEL INJECTOR AND FUEL TUBE ........................ 45
Removal and Installation ........................................ 45
REMOVAL ........................................................... 46
INSTALLATION .................................................... 47
INSPECTION AFTER INSTALLATION ................ 49
ROCKER COVER ..................................................... 51
Removal and Installation ........................................ 51
REMOVAL ........................................................... 51
INSTALLATION .................................................... 52
FRONT TIMING CHAIN CASE ................................. 54
Removal and Installation ........................................ 54
REMOVAL ........................................................... 54
INSTALLATION .................................................... 58
INSPECTION AFTER INSTALLATION ................ 62
TIMING CHAIN .......................................................... 63
Removal and Installation ........................................ 63
REMOVAL ........................................................... 64
INSPECTION AFTER REMOVAL ........................ 71
INSTALLATION .................................................... 71
INSPECTION AFTER INSTALLATION ................ 80
CAMSHAFT ............................................................... 82
Removal and Installation ........................................ 82
REMOVAL ........................................................... 83
INSPECTION AFTER REMOVAL ........................ 84
INSTALLATION .................................................... 87
Valve Clearance ...................................................... 89
INSPECTION ....................................................... 89
ADJUSTMENT .................................................... 92
OIL SEAL .................................................................. 94
Removal and Installation of Valve Oil Seal ............. 94
REMOVAL ........................................................... 94
INSTALLATION .................................................... 94
Removal and Installation of Front Oil Seal ............. 95
REMOVAL ........................................................... 95
INSTALLATION .................................................... 96
Removal and Installation of Rear Oil Seal .............. 96
REMOVAL ........................................................... 96
INSTALLATION .................................................... 96
CYLINDER HEAD ..................................................... 98
On-Vehicle Service ................................................. 98
CHECKING COMPRESSION PRESSURE ......... 98
Removal and Installation ........................................ 99
REMOVAL ........................................................... 99
INSPECTION AFTER REMOVAL ......................100
INSTALLATION ..................................................101
Disassembly and Assembly ..................................102
DISASSEMBLY .................................................103
ASSEMBLY .......................................................103
Inspection After Disassembly ...............................104
VALVE DIMENSIONS ........................................104
VALVE GUIDE CLEARANCE ............................105
VALVE GUIDE REPLACEMENT .......................105
VALVE SEAT CONTACT ...................................107
VALVE SEAT REPLACEMENT .........................107
VALVE SPRING SQUARENESS .......................108
VALVE SPRING DIMENSIONS AND VALVE SPRING PRESSURE LOAD ..............................109
ENGINE ASSEMBLY ...............................................110
Removal and Installation .......................................110
2WD MODEL .....................................................110
REMOVAL .......................................................... 111
INSTALLATION ..................................................113
INSPECTION AFTER INSTALLATION ..............113
AWD MODEL .....................................................115
REMOVAL ..........................................................115
INSTALLATION ..................................................118
INSPECTION AFTER INSTALLATION ..............118
CYLINDER BLOCK .................................................120
Disassembly and Assembly ..................................120
DISASSEMBLY ..................................................121
ASSEMBLY ........................................................126
How to Select Piston and Bearing ........................131
DESCRIPTION ..................................................131
HOW TO SELECT PISTON ...............................131
HOW TO SELECT CONNECTING ROD BEAR-
ING .....................................................................132
HOW TO SELECT MAIN BEARING ..................133
Inspection After Disassembly ................................136
CRANKSHAFT END PLAY ................................136
CONNECTING ROD SIDE CLEARANCE .........136
PISTON TO PISTON PIN OIL CLEARANCE .....136
PISTON RING SIDE CLEARANCE ...................137
PISTON RING END GAP ..................................137
CONNECTING ROD BEND AND TORSION .....138
CONNECTING ROD BEARING HOUSING
DIAMETER (BIG END) ......................................138
CONNECTING ROD BUSHING OIL CLEAR-
ANCE (SMALL END) .........................................138
CYLINDER BLOCK DISTORTION ....................139
MAIN BEARING HOUSING INNER DIAMETER .140
PISTON TO CYLINDER BORE CLEARANCE ..140
CRANKSHAFT MAIN JOURNAL DIAMETER ...141
CRANKSHAFT PIN JOURNAL DIAMETER ......142
CRANKSHAFT OUT-OF-ROUND AND TAPER .142
CRANKSHAFT RUNOUT ..................................142
CONNECTING ROD BEARING OIL CLEAR-
ANCE .................................................................142
MAIN BEARING OIL CLEARANCE ...................143
MAIN BEARING CRUSH HEIGHT ....................144
CONNECTING ROD BEARING CRUSH
HEIGHT .............................................................144
MAIN BEARING CAP BOLT OUTER DIAMETER .144
CONNECTING ROD BOLT OUTER DIAMETER .144
DRIVE PLATE ....................................................145
OIL JET ..............................................................145
OIL JET RELIEF VALVE ....................................145
SERVICE DATA AND SPECIFICATIONS (SDS) ....146
Standard and Limit ................................................146
GENERAL SPECIFICATIONS ...........................146
DRIVE BELT ......................................................147
INTAKE MANIFOLD COLLECTOR, INTAKE
Page 2728 of 4449
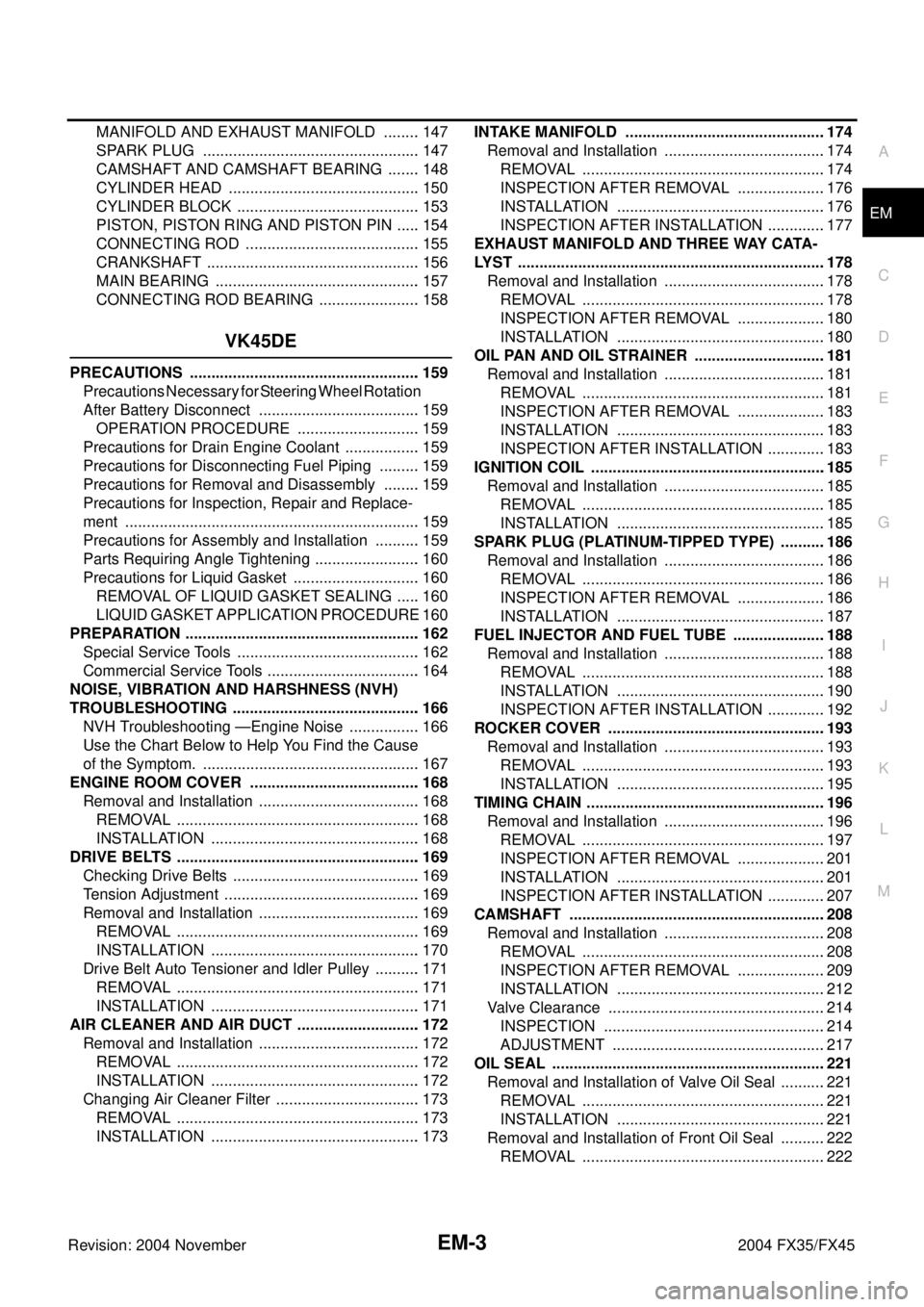
EM-3
C
D
E
F
G
H
I
J
K
L
M
EMA
Revision: 2004 November 2004 FX35/FX45MANIFOLD AND EXHAUST MANIFOLD ......... 147
SPARK PLUG ................................................... 147
CAMSHAFT AND CAMSHAFT BEARING ........ 148
CYLINDER HEAD ............................................. 150
CYLINDER BLOCK ........................................... 153
PISTON, PISTON RING AND PISTON PIN ...... 154
CONNECTING ROD ......................................... 155
CRANKSHAFT .................................................. 156
MAIN BEARING ................................................ 157
CONNECTING ROD BEARING ........................ 158
VK45DE
PRECAUTIONS ...................................................... 159
Precautions Necessary for Steering Wheel Rotation
After Battery Disconnect ...................................... 159
OPERATION PROCEDURE ............................. 159
Precautions for Drain Engine Coolant .................. 159
Precautions for Disconnecting Fuel Piping .......... 159
Precautions for Removal and Disassembly ......... 159
Precautions for Inspection, Repair and Replace-
ment ..................................................................... 159
Precautions for Assembly and Installation ........... 159
Parts Requiring Angle Tightening ......................... 160
Precautions for Liquid Gasket .............................. 160
REMOVAL OF LIQUID GASKET SEALING ...... 160
LIQUID GASKET APPLICATION PROCEDURE . 160
PREPARATION ....................................................... 162
Special Service Tools ........................................... 162
Commercial Service Tools .................................... 164
NOISE, VIBRATION AND HARSHNESS (NVH)
TROUBLESHOOTING ............................................ 166
NVH Troubleshooting —Engine Noise ................. 166
Use the Chart Below to Help You Find the Cause
of the Symptom. ................................................... 167
ENGINE ROOM COVER ........................................ 168
Removal and Installation ...................................... 168
REMOVAL ......................................................... 168
INSTALLATION ................................................. 168
DRIVE BELTS ......................................................... 169
Checking Drive Belts ............................................ 169
Tension Adjustment .............................................. 169
Removal and Installation ...................................... 169
REMOVAL ......................................................... 169
INSTALLATION ................................................. 170
Drive Belt Auto Tensioner and Idler Pulley ........... 171
REMOVAL ......................................................... 171
INSTALLATION ................................................. 171
AIR CLEANER AND AIR DUCT ............................. 172
Removal and Installation ...................................... 172
REMOVAL ......................................................... 172
INSTALLATION ................................................. 172
Changing Air Cleaner Filter .................................. 173
REMOVAL ......................................................... 173
INSTALLATION ................................................. 173INTAKE MANIFOLD ...............................................174
Removal and Installation ......................................174
REMOVAL .........................................................174
INSPECTION AFTER REMOVAL .....................176
INSTALLATION .................................................176
INSPECTION AFTER INSTALLATION ..............177
EXHAUST MANIFOLD AND THREE WAY CATA-
LYST ........................................................................178
Removal and Installation ......................................178
REMOVAL .........................................................178
INSPECTION AFTER REMOVAL .....................180
INSTALLATION .................................................180
OIL PAN AND OIL STRAINER ...............................181
Removal and Installation ......................................181
REMOVAL .........................................................181
INSPECTION AFTER REMOVAL .....................183
INSTALLATION .................................................183
INSPECTION AFTER INSTALLATION ..............183
IGNITION COIL .......................................................185
Removal and Installation ......................................185
REMOVAL .........................................................185
INSTALLATION .................................................185
SPARK PLUG (PLATINUM-TIPPED TYPE) ...........186
Removal and Installation ......................................186
REMOVAL .........................................................186
INSPECTION AFTER REMOVAL .....................186
INSTALLATION .................................................187
FUEL INJECTOR AND FUEL TUBE ......................188
Removal and Installation ......................................188
REMOVAL .........................................................188
INSTALLATION .................................................190
INSPECTION AFTER INSTALLATION ..............192
ROCKER COVER ...................................................193
Removal and Installation ......................................193
REMOVAL .........................................................193
INSTALLATION .................................................195
TIMING CHAIN ........................................................196
Removal and Installation ......................................196
REMOVAL .........................................................197
INSPECTION AFTER REMOVAL .....................201
INSTALLATION .................................................201
INSPECTION AFTER INSTALLATION ..............207
CAMSHAFT ............................................................208
Removal and Installation ......................................208
REMOVAL .........................................................208
INSPECTION AFTER REMOVAL .....................209
INSTALLATION .................................................212
Valve Clearance ...................................................214
INSPECTION ....................................................214
ADJUSTMENT ..................................................217
OIL SEAL ................................................................221
Removal and Installation of Valve Oil Seal ...........221
REMOVAL .........................................................221
INSTALLATION .................................................221
Removal and Installation of Front Oil Seal ...........222
REMOVAL .........................................................222
Page 2729 of 4449
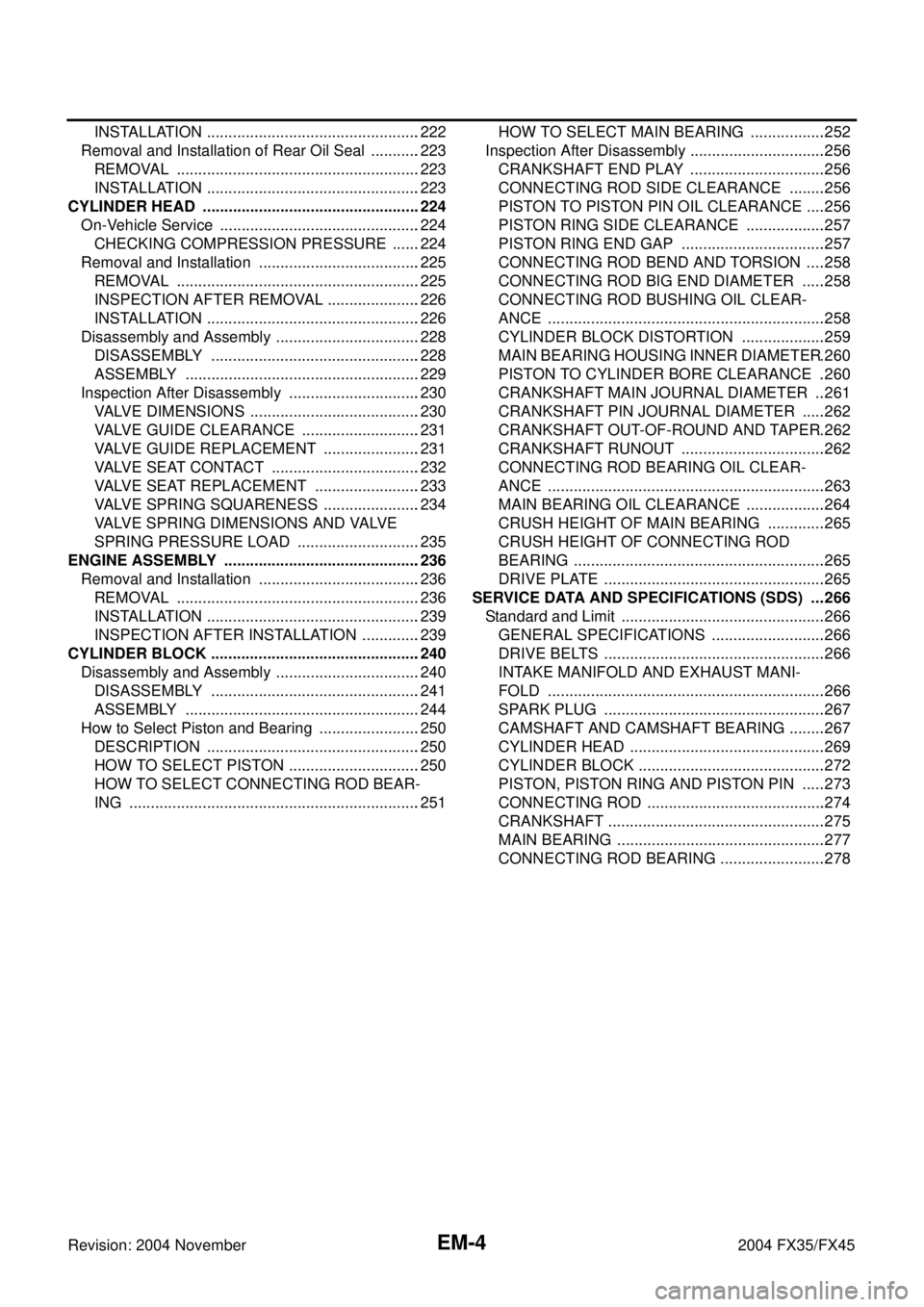
EM-4Revision: 2004 November 2004 FX35/FX45INSTALLATION ..................................................222
Removal and Installation of Rear Oil Seal ............223
REMOVAL .........................................................223
INSTALLATION ..................................................223
CYLINDER HEAD ...................................................224
On-Vehicle Service ...............................................224
CHECKING COMPRESSION PRESSURE .......224
Removal and Installation ......................................225
REMOVAL .........................................................225
INSPECTION AFTER REMOVAL ......................226
INSTALLATION ..................................................226
Disassembly and Assembly ..................................228
DISASSEMBLY .................................................228
ASSEMBLY .......................................................229
Inspection After Disassembly ...............................230
VALVE DIMENSIONS ........................................230
VALVE GUIDE CLEARANCE ............................231
VALVE GUIDE REPLACEMENT .......................231
VALVE SEAT CONTACT ...................................232
VALVE SEAT REPLACEMENT .........................233
VALVE SPRING SQUARENESS .......................234
VALVE SPRING DIMENSIONS AND VALVE
SPRING PRESSURE LOAD .............................235
ENGINE ASSEMBLY ..............................................236
Removal and Installation ......................................236
REMOVAL .........................................................236
INSTALLATION ..................................................239
INSPECTION AFTER INSTALLATION ..............239
CYLINDER BLOCK .................................................240
Disassembly and Assembly ..................................240
DISASSEMBLY .................................................241
ASSEMBLY .......................................................244
How to Select Piston and Bearing ........................250
DESCRIPTION ..................................................250
HOW TO SELECT PISTON ...............................250
HOW TO SELECT CONNECTING ROD BEAR-
ING ....................................................................251HOW TO SELECT MAIN BEARING ..................252
Inspection After Disassembly ................................256
CRANKSHAFT END PLAY ................................256
CONNECTING ROD SIDE CLEARANCE .........256
PISTON TO PISTON PIN OIL CLEARANCE .....256
PISTON RING SIDE CLEARANCE ...................257
PISTON RING END GAP ..................................257
CONNECTING ROD BEND AND TORSION .....258
CONNECTING ROD BIG END DIAMETER ......258
CONNECTING ROD BUSHING OIL CLEAR-
ANCE .................................................................258
CYLINDER BLOCK DISTORTION ....................259
MAIN BEARING HOUSING INNER DIAMETER .260
PISTON TO CYLINDER BORE CLEARANCE ..260
CRANKSHAFT MAIN JOURNAL DIAMETER ...261
CRANKSHAFT PIN JOURNAL DIAMETER ......262
CRANKSHAFT OUT-OF-ROUND AND TAPER .262
CRANKSHAFT RUNOUT ..................................262
CONNECTING ROD BEARING OIL CLEAR-
ANCE .................................................................263
MAIN BEARING OIL CLEARANCE ...................264
CRUSH HEIGHT OF MAIN BEARING ..............265
CRUSH HEIGHT OF CONNECTING ROD
BEARING ...........................................................265
DRIVE PLATE ....................................................265
SERVICE DATA AND SPECIFICATIONS (SDS) ....266
Standard and Limit ................................................266
GENERAL SPECIFICATIONS ...........................266
DRIVE BELTS ....................................................266
INTAKE MANIFOLD AND EXHAUST MANI-
FOLD .................................................................266
SPARK PLUG ....................................................267
CAMSHAFT AND CAMSHAFT BEARING .........267
CYLINDER HEAD ..............................................269
CYLINDER BLOCK ............................................272
PISTON, PISTON RING AND PISTON PIN ......273
CONNECTING ROD ..........................................274
CRANKSHAFT ...................................................275
MAIN BEARING .................................................277
CONNECTING ROD BEARING .........................278
Page 2730 of 4449
![INFINITI FX35 2004 Service Manual PRECAUTIONS
EM-5
[VQ35DE]
C
D
E
F
G
H
I
J
K
L
MA
EM
Revision: 2004 November 2004 FX35/FX45
[VQ35DE]PRECAUTIONSPFP:00001
Precautions Necessary for Steering Wheel Rotation After Battery DisconnectABS00B INFINITI FX35 2004 Service Manual PRECAUTIONS
EM-5
[VQ35DE]
C
D
E
F
G
H
I
J
K
L
MA
EM
Revision: 2004 November 2004 FX35/FX45
[VQ35DE]PRECAUTIONSPFP:00001
Precautions Necessary for Steering Wheel Rotation After Battery DisconnectABS00B](/img/42/57021/w960_57021-2729.png)
PRECAUTIONS
EM-5
[VQ35DE]
C
D
E
F
G
H
I
J
K
L
MA
EM
Revision: 2004 November 2004 FX35/FX45
[VQ35DE]PRECAUTIONSPFP:00001
Precautions Necessary for Steering Wheel Rotation After Battery DisconnectABS00B3I
NOTE:
This Procedure is applied only to models with Intelligent Key system and NVIS/IVIS (NISSAN/INFINITI
VEHICLE IMMOBILIZER SYSTEM - NATS).
Remove and install all control units after disconnecting both battery cables with the ignition knob in the
″LOCK″ position.
Always use CONSULT-II to perform self-diagnosis as a part of each function inspection after finishing
work. If DTC is detected, perform trouble diagnosis according to self-diagnostic results.
For models equipped with the Intelligent Key system and NVIS/IVIS, an electrically controlled steering lock
mechanism is adopted on the key cylinder.
For this reason, if the battery is disconnected or if the battery is discharged, the steering wheel will lock and
steering wheel rotation will become impossible.
If steering wheel rotation is required when battery power is interrupted, follow the procedure below before
starting the repair operation.
OPERATION PROCEDURE
1. Connect both battery cables.
NOTE:
Supply power using jumper cables if battery is discharged.
2. Use the Intelligent Key or mechanical key to turn the ignition switch to the ″ACC″ position. At this time, the
steering lock will be released.
3. Disconnect both battery cables. The steering lock will remain released and the steering wheel can be
rotated.
4. Perform the necessary repair operation.
5. When the repair work is completed, return the ignition switch to the ″LOCK″ position before connecting
the battery cables. (At this time, the steering lock mechanism will engage.)
6. Perform a self-diagnosis check of all control units using CONSULT-II.
Precautions for Drain Engine CoolantABS005ZK
Drain engine coolant when engine is cooled.
Precautions for Disconnecting Fuel PipingABS005ZL
Before starting work, make sure no fire or spark producing items are in the work area.
Release fuel pressure before disconnecting and disassembly.
After disconnecting pipes, plug openings to stop fuel leakage.
Precautions for Removal and DisassemblyABS005ZM
When instructed to use special service tools, use the specified tools. Always be careful to work safely,
avoid forceful or uninstructed operations.
Exercise maximum care to avoid damage to mating or sliding surfaces.
Cover openings of engine system with tape or the equivalent, if necessary, to seal out foreign materials.
Mark and arrange disassembly parts in an organized way for easy troubleshooting and re-assembly.
When loosening nuts and bolts, as a basic rule, start with the one furthest outside, then the one diagonally
opposite, and so on. If the order of loosening is specified, do exactly as specified. Power tools may be
used where noted in the step.
Precautions for Inspection, Repair and ReplacementABS005ZN
Before repairing or replacing, thoroughly inspect parts. Inspect new replacement parts in the same way, and
replace if necessary.
Precautions for Assembly and InstallationABS005ZO
Use torque wrench to tighten bolts or nuts to specification.