stop start INFINITI FX35 2005 Service Manual
[x] Cancel search | Manufacturer: INFINITI, Model Year: 2005, Model line: FX35, Model: INFINITI FX35 2005Pages: 4731, PDF Size: 60.13 MB
Page 4123 of 4731
![INFINITI FX35 2005 Service Manual LU-30
[VK45DE]
OIL COOLER
Revision: 2005 July 2005 FX
6. Remove water pipe, as necessary.
INSPECTION AFTER REMOVAL
Oil Cooler
Check oil cooler for cracks. Check oil cooler for clogging by blowing thr INFINITI FX35 2005 Service Manual LU-30
[VK45DE]
OIL COOLER
Revision: 2005 July 2005 FX
6. Remove water pipe, as necessary.
INSPECTION AFTER REMOVAL
Oil Cooler
Check oil cooler for cracks. Check oil cooler for clogging by blowing thr](/img/42/57020/w960_57020-4122.png)
LU-30
[VK45DE]
OIL COOLER
Revision: 2005 July 2005 FX
6. Remove water pipe, as necessary.
INSPECTION AFTER REMOVAL
Oil Cooler
Check oil cooler for cracks. Check oil cooler for clogging by blowing through engine coolant inlet. If necessary,
replace oil cooler.
Relief Valve
Check relief valve for movement, cracks and breaks by pushing the ball. If replacement is necessary, remove
relief valve by prying it out with suitable tool. Install a new valve in place by tapping it.
INSTALLATION
Note the following, and install in the reverse order of removal.
Make sure that no foreign objects are adhering to the installation planes of oil cooler or oil pan.
Tighten connector bolt after aligning stopper on the oil pan side
with protrusion of oil cooler.
INSPECTION AFTER INSTALLATION
1. Make sure level of engine oil and engine coolant, and adjust engine oil and engine coolant. Refer to LU-
25, "ENGINE OIL" and CO-37, "ENGINE COOLANT" .
2. Start engine, and make sure there is no leak of engine oil or engine coolant.
3. Stop engine and wait for 15 minutes.
4. Check the engine oil level and the engine coolant level again. Refer to LU-25, "
ENGINE OIL" and CO-37,
"ENGINE COOLANT" .
PBIC1527E
Page 4125 of 4731
![INFINITI FX35 2005 Service Manual LU-32
[VK45DE]
OIL PUMP
Revision: 2005 July 2005 FX
3. Install in the reverse order of removal after this step.
INSPECTION AFTER INSTALLATION
1. Check the engine oil level. refer to LU-25, "ENGINE OIL INFINITI FX35 2005 Service Manual LU-32
[VK45DE]
OIL PUMP
Revision: 2005 July 2005 FX
3. Install in the reverse order of removal after this step.
INSPECTION AFTER INSTALLATION
1. Check the engine oil level. refer to LU-25, "ENGINE OIL](/img/42/57020/w960_57020-4124.png)
LU-32
[VK45DE]
OIL PUMP
Revision: 2005 July 2005 FX
3. Install in the reverse order of removal after this step.
INSPECTION AFTER INSTALLATION
1. Check the engine oil level. refer to LU-25, "ENGINE OIL" .
2. Start engine, and check there is no leak of engine oil.
3. Stop engine and wait for 15 minutes.
4. Check the engine oil level and adjust engine oil. Refer to LU-25, "
ENGINE OIL" .
Disassembly and AssemblyABS006J8
DISASSEMBLY
1. Remove oil pump cover.
2. Remove oil pump inner rotor and oil pump outer rotor from oil pump body.
3. After removing regulator valve plug, remove regulator valve spring and regulator valve.
INSPECTION AFTER DISASSEMBLY
Oil Pump Clearance
Measure the clearance with feeler gauge.
–Clearance between oil pump outer rotor and oil pump body
(Position 1)
–Tip clearance between oil pump inner rotor and oil pump outer
rotor (Position 2)
Measure the clearance with feeler gauge and straightedge.
–Side clearance between oil pump inner rotor and oil pump body
(Position 3)
–Side clearance between oil pump outer rotor and oil pump body
(Position 4)
Calculate the clearance between oil pump inner rotor and oil pump body as follows:
OIL PUMP INNER ROTOR OUTER DIAMETER
–Measure the outer diameter of protruded portion of oil pump
inner rotor with micrometer. (Position 5) Standard : 0.114 - 0.200 mm (0.0045 - 0.0079 in)
Standard : Below 0.180 mm (0.0071 in)
PBIC0139E
Standard : 0.030 - 0.070 mm (0.0012 - 0.0028 in)
Standard : 0.030 - 0.090 mm (0.0012 - 0.0035 in)
PBIC0140E
PBIC0141E
Page 4147 of 4731
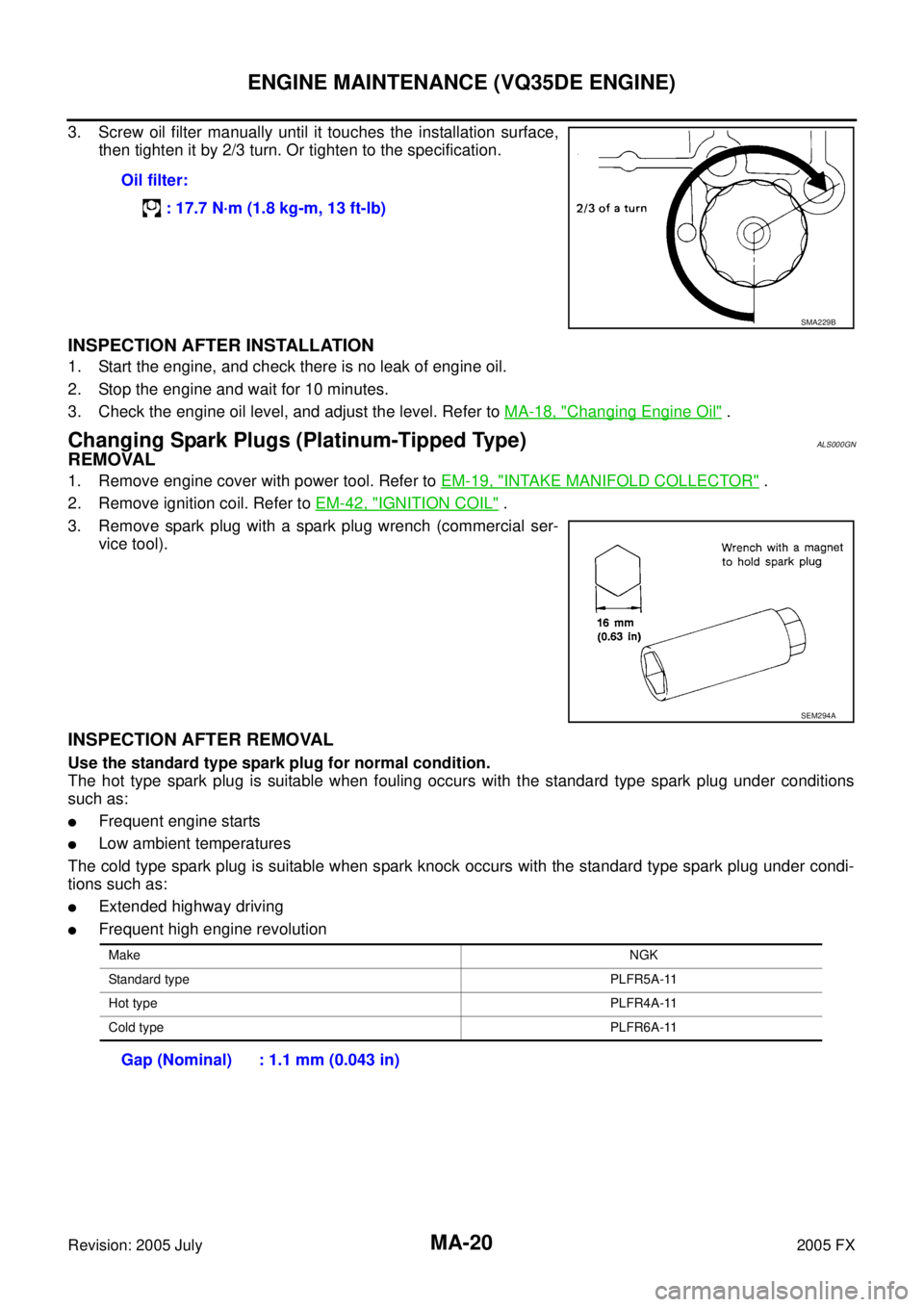
MA-20
ENGINE MAINTENANCE (VQ35DE ENGINE)
Revision: 2005 July 2005 FX
3. Screw oil filter manually until it touches the installation surface,
then tighten it by 2/3 turn. Or tighten to the specification.
INSPECTION AFTER INSTALLATION
1. Start the engine, and check there is no leak of engine oil.
2. Stop the engine and wait for 10 minutes.
3. Check the engine oil level, and adjust the level. Refer to MA-18, "
Changing Engine Oil" .
Changing Spark Plugs (Platinum-Tipped Type)ALS000GN
REMOVAL
1. Remove engine cover with power tool. Refer to EM-19, "INTAKE MANIFOLD COLLECTOR" .
2. Remove ignition coil. Refer to EM-42, "
IGNITION COIL" .
3. Remove spark plug with a spark plug wrench (commercial ser- vice tool).
INSPECTION AFTER REMOVAL
Use the standard type spark plug for normal condition.
The hot type spark plug is suitable when fouling occurs with the standard type spark plug under conditions
such as:
Frequent engine starts
Low ambient temperatures
The cold type spark plug is suitable when spark knock occurs with the standard type spark plug under condi-
tions such as:
Extended highway driving
Frequent high engine revolution Oil filter:
: 17.7 N·m (1.8 kg-m, 13 ft-lb)
SMA229B
SEM294A
Make NGK
Standard type PLFR5A-11
Hot type PLFR4A-11
Cold type PLFR6A-11
Gap (Nominal) : 1.1 mm (0.043 in)
Page 4154 of 4731
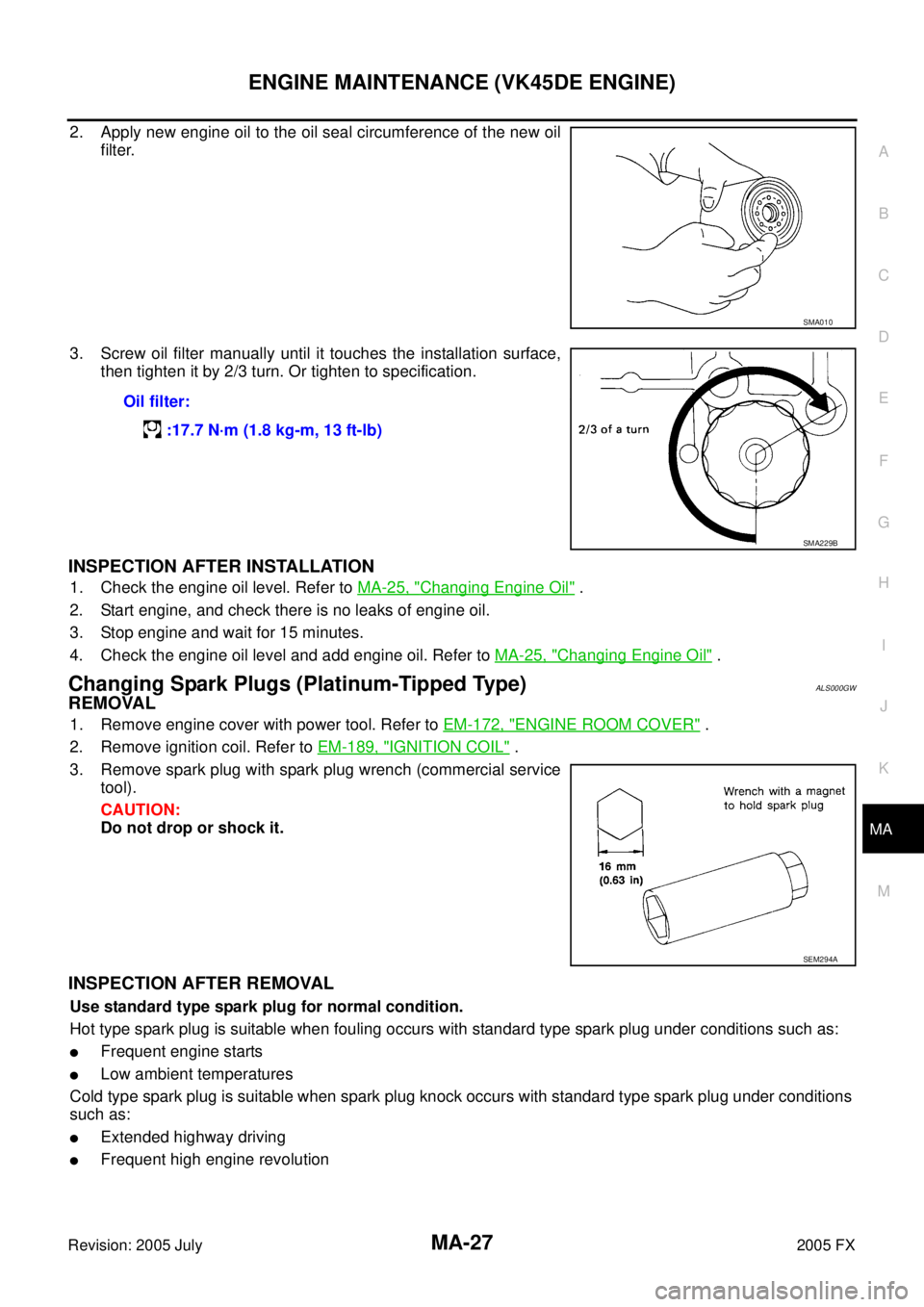
ENGINE MAINTENANCE (VK45DE ENGINE) MA-27
C
D E
F
G H
I
J
K
M A
B
MA
Revision: 2005 July 2005 FX
2. Apply new engine oil to the oil seal circumference of the new oil
filter.
3. Screw oil filter manually until it touches the installation surface, then tighten it by 2/3 turn. Or tighten to specification.
INSPECTION AFTER INSTALLATION
1. Check the engine oil level. Refer to MA-25, "Changing Engine Oil" .
2. Start engine, and check there is no leaks of engine oil.
3. Stop engine and wait for 15 minutes.
4. Check the engine oil level and add engine oil. Refer to MA-25, "
Changing Engine Oil" .
Changing Spark Plugs (Platinum-Tipped Type)ALS000GW
REMOVAL
1. Remove engine cover with power tool. Refer to EM-172, "ENGINE ROOM COVER" .
2. Remove ignition coil. Refer to EM-189, "
IGNITION COIL" .
3. Remove spark plug with spark plug wrench (commercial service tool).
CAUTION:
Do not drop or shock it.
INSPECTION AFTER REMOVAL
Use standard type spark plug for normal condition.
Hot type spark plug is suitable when fouling occurs with standard type spark plug under conditions such as:
Frequent engine starts
Low ambient temperatures
Cold type spark plug is suitable when spark plug knock occurs with standard type spark plug under conditions
such as:
Extended highway driving
Frequent high engine revolution
SMA010
Oil filter:
:17.7 N·m (1.8 kg-m, 13 ft-lb)
SMA229B
SEM294A
Page 4158 of 4731
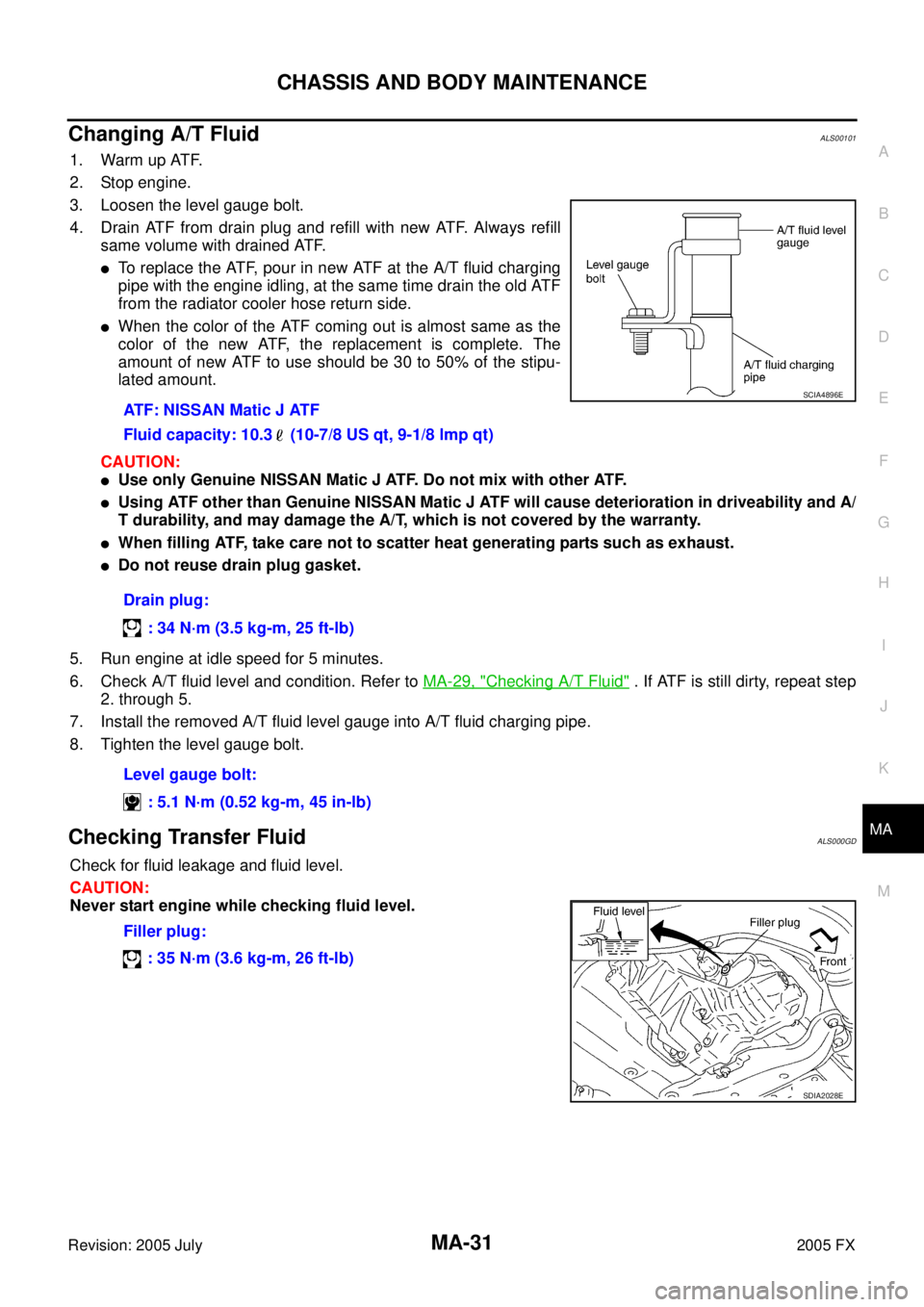
CHASSIS AND BODY MAINTENANCE MA-31
C
D E
F
G H
I
J
K
M A
B
MA
Revision: 2005 July 2005 FX
Changing A/T FluidALS00101
1. Warm up ATF.
2. Stop engine.
3. Loosen the level gauge bolt.
4. Drain ATF from drain plug and refill with new ATF. Always refill same volume with drained ATF.
To replace the ATF, pour in new ATF at the A/T fluid charging
pipe with the engine idling, at the same time drain the old ATF
from the radiator cooler hose return side.
When the color of the ATF coming out is almost same as the
color of the new ATF, the replacement is complete. The
amount of new ATF to use should be 30 to 50% of the stipu-
lated amount.
CAUTION:
Use only Genuine NISSAN Matic J ATF. Do not mix with other ATF.
Using ATF other than Genuine NISSAN Matic J ATF will cause deterioration in driveability and A/
T durability, and may damage the A/T, which is not covered by the warranty.
When filling ATF, take care not to scatter heat generating parts such as exhaust.
Do not reuse drain plug gasket.
5. Run engine at idle speed for 5 minutes.
6. Check A/T fluid level and condition. Refer to MA-29, "
Checking A/T Fluid" . If ATF is still dirty, repeat step
2. through 5.
7. Install the removed A/T fluid level gauge into A/T fluid charging pipe.
8. Tighten the level gauge bolt.
Checking Transfer FluidALS000GD
Check for fluid leakage and fluid level.
CAUTION:
Never start engine while checking fluid level. ATF: NISSAN Matic J ATF
Fluid capacity: 10.3 (10-7/8 US qt, 9-1/8 lmp qt)
Drain plug:
: 34 N·m (3.5 kg-m, 25 ft-lb)
Level gauge bolt: : 5.1 N·m (0.52 kg-m, 45 in-lb)
SCIA4896E
Filler plug: : 35 N·m (3.6 kg-m, 26 ft-lb)
SDIA2028E
Page 4199 of 4731
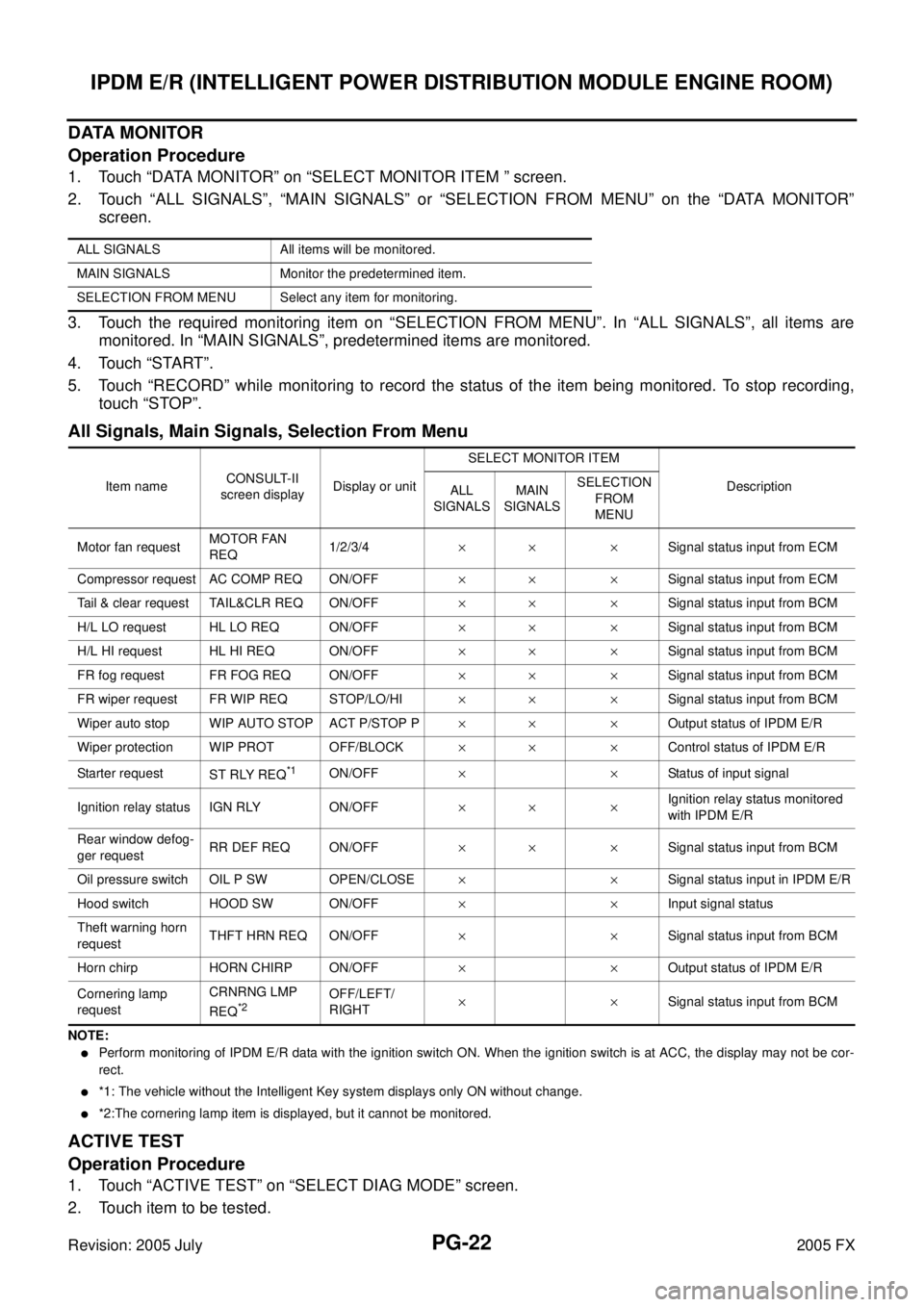
PG-22
IPDM E/R (INTELLIGENT POWER DISTRIBUTION MODULE ENGINE ROOM)
Revision: 2005 July 2005 FX
DATA MONITOR
Operation Procedure
1. Touch “DATA MONITOR” on “SELECT MONITOR ITEM ” screen.
2. Touch “ALL SIGNALS”, “MAIN SIGNALS” or “SELECTION FROM MENU” on the “DATA MONITOR” screen.
3. Touch the required monitoring item on “SELECTION FROM MENU”. In “ALL SIGNALS”, all items are monitored. In “MAIN SIGNALS”, predetermined items are monitored.
4. Touch “START”.
5. Touch “RECORD” while monitoring to record the status of the item being monitored. To stop recording, touch “STOP”.
All Signals, Main Signals, Selection From Menu
NOTE:
Perform monitoring of IPDM E/R data with the ignition switch ON. When the ignition switch is at ACC, the display may not be cor -
rect.
*1: The vehicle without the Intelligent Key system displays only ON without change.
*2:The cornering lamp item is displayed, but it cannot be monitored.
ACTIVE TEST
Operation Procedure
1. Touch “ACTIVE TEST” on “SELECT DIAG MODE” screen.
2. Touch item to be tested.
ALL SIGNALS All items will be monitored.
MAIN SIGNALS Monitor the predetermined item.
SELECTION FROM MENU Select any item for monitoring.
Item name CONSULT-II
screen display Display or unit SELECT MONITOR ITEM
Description
ALL
SIGNALS MAIN
SIGNALS SELECTION
FROM
MENU
Motor fan request MOTOR FAN
REQ 1/2/3/4
×× × Signal status input from ECM
Compressor request AC COMP REQ ON/OFF ×× ×Signal status input from ECM
Tail & clear request TAIL&CLR REQ ON/OFF ×× ×Signal status input from BCM
H/L LO request HL LO REQ ON/OFF ×× ×Signal status input from BCM
H/L HI request HL HI REQ ON/OFF ×× ×Signal status input from BCM
FR fog request FR FOG REQ ON/OFF ×× ×Signal status input from BCM
FR wiper request FR WIP REQ STOP/LO/HI ×× ×Signal status input from BCM
Wiper auto stop WIP AUTO STOP ACT P/STOP P ×× ×Output status of IPDM E/R
Wiper protection WIP PROT OFF/BLOCK ×× ×Control status of IPDM E/R
Starter request ST RLY REQ
*1ON/OFF ×× Status of input signal
Ignition relay status IGN RLY ON/OFF ×× × Ignition relay status monitored
with IPDM E/R
Rear window defog-
ger request RR DEF REQ ON/OFF
×× ×Signal status input from BCM
Oil pressure switch OIL P SW OPEN/CLOSE ××Signal status input in IPDM E/R
Hood switch HOOD SW ON/OFF ××Input signal status
Theft warning horn
request THFT HRN REQ ON/OFF
××Signal status input from BCM
Horn chirp HORN CHIRP ON/OFF ××Output status of IPDM E/R
Cornering lamp
request CRNRNG LMP
REQ
*2OFF/LEFT/
RIGHT ××
Signal status input from BCM
Page 4200 of 4731
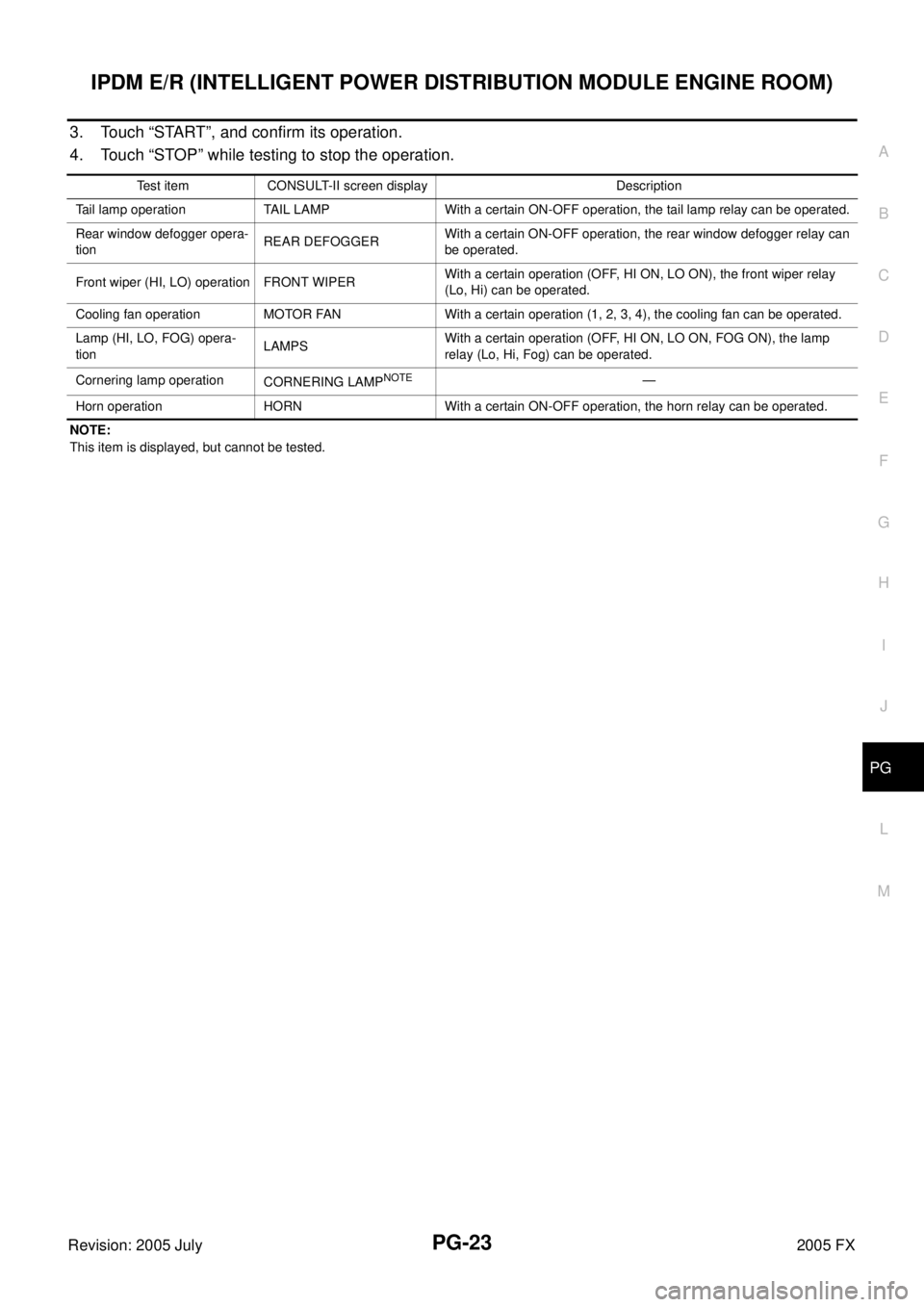
IPDM E/R (INTELLIGENT POWER DISTRIBUTION MODULE ENGINE ROOM) PG-23
C
D E
F
G H
I
J
L
M A
B
PG
Revision: 2005 July 2005 FX
3. Touch “START”, and confirm its operation.
4. Touch “STOP” while testing to stop the operation.
NOTE:
This item is displayed, but cannot be tested. Test item CONSULT-II screen display Description
Tail lamp operation TAIL LAMP With a certain ON-OFF operation, the tail lamp relay can be operated.
Rear window defogger opera-
tion REAR DEFOGGER
With a certain ON-OFF operation, the rear window defogger relay can
be operated.
Front wiper (HI, LO) operation FRONT WIPER With a certain operation (OFF, HI ON, LO ON), the front wiper relay
(Lo, Hi) can be operated.
Cooling fan operation MOTOR FAN With a certain operation (1, 2, 3, 4), the cooling fan can be operated.
Lamp (HI, LO, FOG) opera-
tion LAMPSWith a certain operation (OFF, HI ON, LO ON, FOG ON), the lamp
relay (Lo, Hi, Fog) can be operated.
Cornering lamp operation CORNERING LAMP
NOTE—
Horn operation HORN With a certain ON-OFF operation, the horn relay can be operated.
Page 4246 of 4731
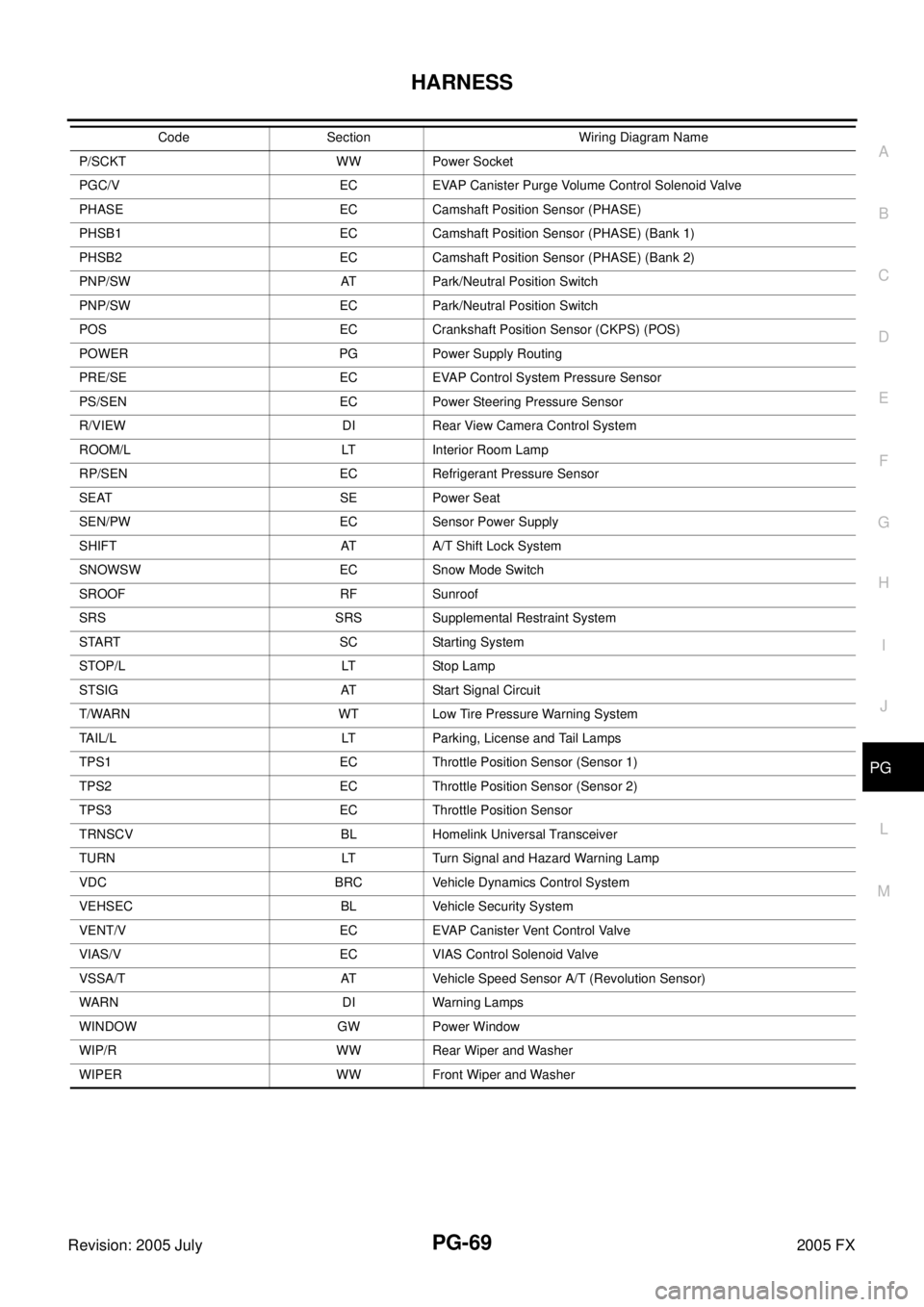
HARNESS PG-69
C
D E
F
G H
I
J
L
M A
B
PG
Revision: 2005 July 2005 FX
P/SCKT WW Power Socket
PGC/V EC EVAP Canister Purge Volume Control Solenoid Valve
PHASE EC Camshaft Position Sensor (PHASE)
PHSB1 EC Camshaft Position Sensor (PHASE) (Bank 1)
PHSB2 EC Camshaft Position Sensor (PHASE) (Bank 2)
PNP/SW AT Park/Neutral Position Switch
PNP/SW EC Park/Neutral Position Switch
POS EC Crankshaft Position Sensor (CKPS) (POS)
POWER PG Power Supply Routing
PRE/SE EC EVAP Control System Pressure Sensor
PS/SEN EC Power Steering Pressure Sensor
R/VIEW DI Rear View Camera Control System
ROOM/L LT Interior Room Lamp
RP/SEN EC Refrigerant Pressure Sensor
SEAT SE Power Seat
SEN/PW EC Sensor Power Supply
SHIFT AT A/T Shift Lock System
SNOWSW EC Snow Mode Switch
SROOF RF Sunroof
SRS SRS Supplemental Restraint System
START SC Starting System
STOP/L LT Stop Lamp
STSIG AT Start Signal Circuit
T/WARN WT Low Tire Pressure Warning System
TAIL/L LT Parking, License and Tail Lamps
TPS1 EC Throttle Position Sensor (Sensor 1)
TPS2 EC Throttle Position Sensor (Sensor 2)
TPS3 EC Throttle Position Sensor
TRNSCV BL Homelink Universal Transceiver
TURN LT Turn Signal and Hazard Warning Lamp
VDC BRC Vehicle Dynamics Control System
VEHSEC BL Vehicle Security System
VENT/V EC EVAP Canister Vent Control Valve
VIAS/V EC VIAS Control Solenoid Valve
VSSA/T AT Vehicle Speed Sensor A/T (Revolution Sensor)
WARN DI Warning Lamps
WINDOW GW Power Window
WIP/R WW Rear Wiper and Washer
WIPER WW Front Wiper and Washer Code Section Wiring Diagram Name
Page 4345 of 4731
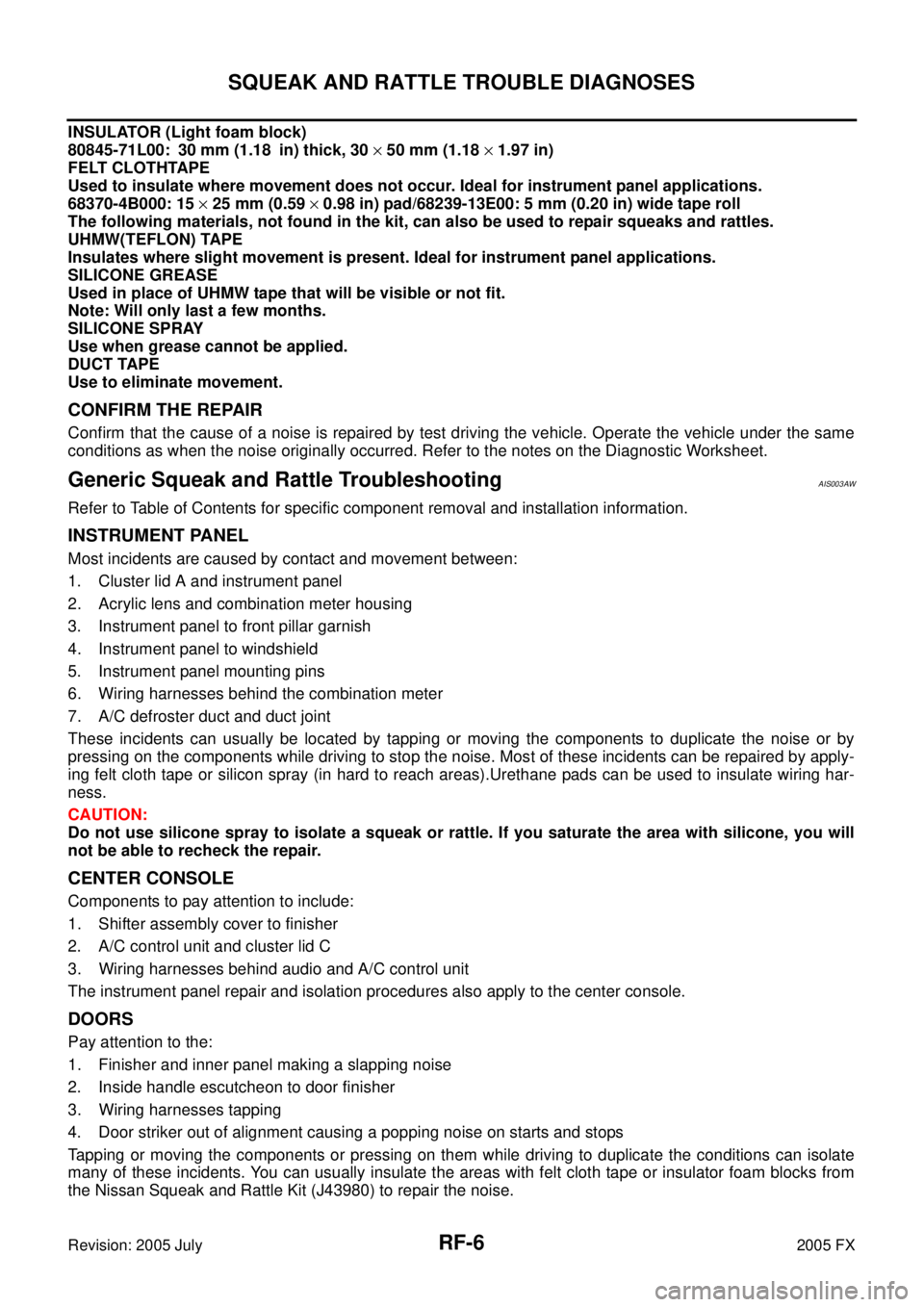
RF-6
SQUEAK AND RATTLE TROUBLE DIAGNOSES
Revision: 2005 July 2005 FX
INSULATOR (Light foam block)
80845-71L00: 30 mm (1.18 in) thick, 30 × 50 mm (1.18 × 1.97 in)
FELT CLOTHTAPE
Used to insulate where movement does not occur. Ideal for instrument panel applications.
68370-4B000: 15 × 25 mm (0.59 × 0.98 in) pad/68239-13E00: 5 mm (0.20 in) wide tape roll
The following materials, not found in the kit, can also be used to repair squeaks and rattles.
UHMW(TEFLON) TAPE
Insulates where slight movement is present. Ideal for instrument panel applications.
SILICONE GREASE
Used in place of UHMW tape that will be visible or not fit.
Note: Will only last a few months.
SILICONE SPRAY
Use when grease cannot be applied.
DUCT TAPE
Use to eliminate movement.
CONFIRM THE REPAIR
Confirm that the cause of a noise is repaired by test driving the vehicle. Operate the vehicle under the same
conditions as when the noise originally occurred. Refer to the notes on the Diagnostic Worksheet.
Generic Squeak and Rattle TroubleshootingAIS003AW
Refer to Table of Contents for specific component removal and installation information.
INSTRUMENT PANEL
Most incidents are caused by contact and movement between:
1. Cluster lid A and instrument panel
2. Acrylic lens and combination meter housing
3. Instrument panel to front pillar garnish
4. Instrument panel to windshield
5. Instrument panel mounting pins
6. Wiring harnesses behind the combination meter
7. A/C defroster duct and duct joint
These incidents can usually be located by tapping or moving the components to duplicate the noise or by
pressing on the components while driving to stop the noise. Most of these incidents can be repaired by apply-
ing felt cloth tape or silicon spray (in hard to reach areas).Urethane pads can be used to insulate wiring har-
ness.
CAUTION:
Do not use silicone spray to isolate a squeak or rattle. If you saturate the area with silicone, you will
not be able to recheck the repair.
CENTER CONSOLE
Components to pay attention to include:
1. Shifter assembly cover to finisher
2. A/C control unit and cluster lid C
3. Wiring harnesses behind audio and A/C control unit
The instrument panel repair and isolation procedures also apply to the center console.
DOORS
Pay attention to the:
1. Finisher and inner panel making a slapping noise
2. Inside handle escutcheon to door finisher
3. Wiring harnesses tapping
4. Door striker out of alignment causing a popping noise on starts and stops
Tapping or moving the components or pressing on them while driving to duplicate the conditions can isolate
many of these incidents. You can usually insulate the areas with felt cloth tape or insulator foam blocks from
the Nissan Squeak and Rattle Kit (J43980) to repair the noise.
Page 4378 of 4731
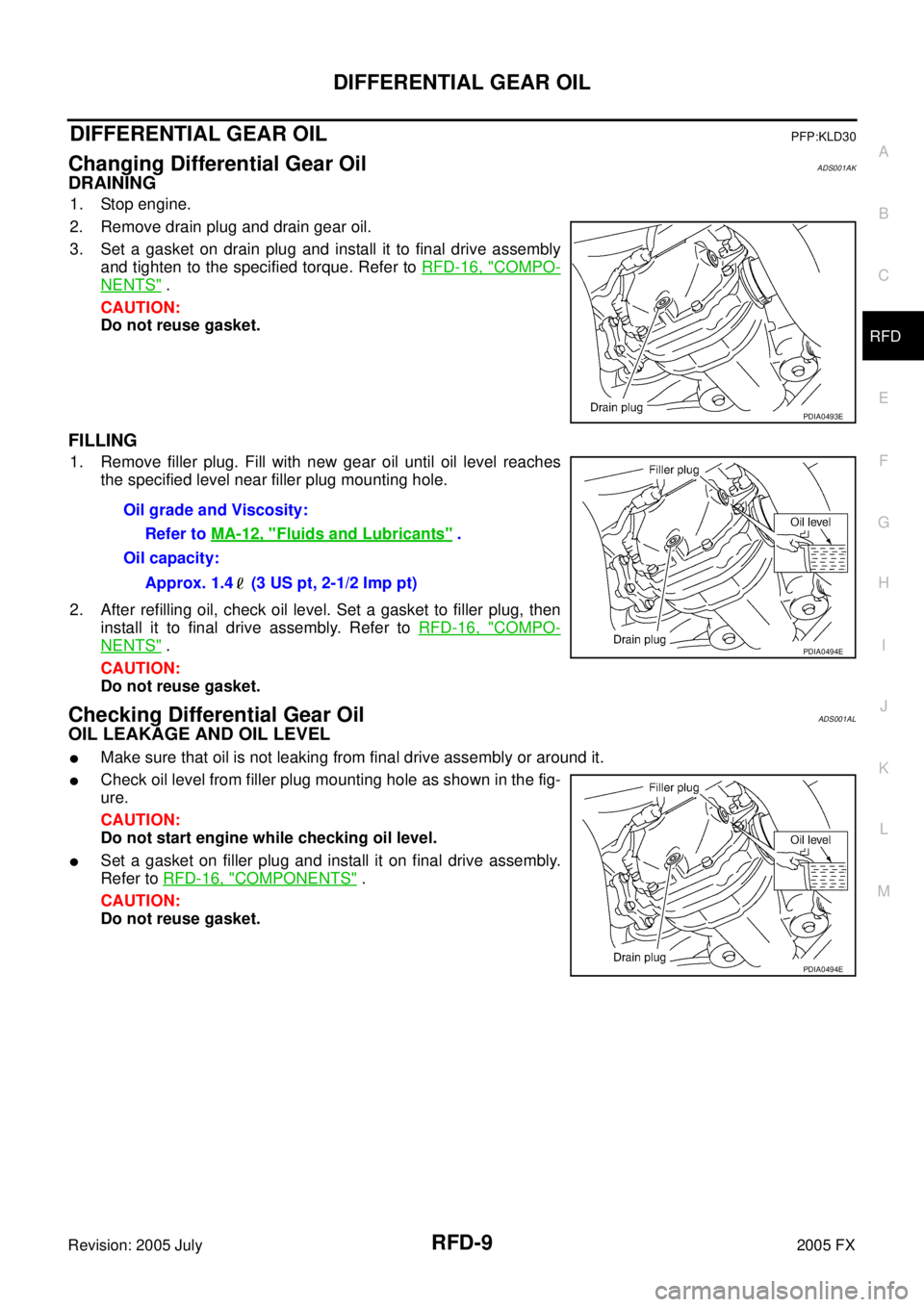
DIFFERENTIAL GEAR OIL RFD-9
C E F
G H
I
J
K L
M A
B
RFD
Revision: 2005 July 2005 FX
DIFFERENTIAL GEAR OILPFP:KLD30
Changing Differential Gear OilADS001AK
DRAINING
1. Stop engine.
2. Remove drain plug and drain gear oil.
3. Set a gasket on drain plug and install it to final drive assembly and tighten to the specified torque. Refer to RFD-16, "
COMPO-
NENTS" .
CAUTION:
Do not reuse gasket.
FILLING
1. Remove filler plug. Fill with new gear oil until oil level reaches
the specified level near filler plug mounting hole.
2. After refilling oil, check oil level. Set a gasket to filler plug, then install it to final drive assembly. Refer to RFD-16, "
COMPO-
NENTS" .
CAUTION:
Do not reuse gasket.
Checking Differential Gear OilADS001AL
OIL LEAKAGE AND OIL LEVEL
Make sure that oil is not leaking from final drive assembly or around it.
Check oil level from filler plug mounting hole as shown in the fig-
ure.
CAUTION:
Do not start engine while checking oil level.
Set a gasket on filler plug and install it on final drive assembly.
Refer to RFD-16, "
COMPONENTS" .
CAUTION:
Do not reuse gasket.
PDIA0493E
Oil grade and Viscosity:
Refer to MA-12, "
Fluids and Lubricants" .
Oil capacity:
Approx. 1.4 (3 US pt, 2-1/2 Imp pt)
PDIA0494E
PDIA0494E