set clock INFINITI FX35 2008 User Guide
[x] Cancel search | Manufacturer: INFINITI, Model Year: 2008, Model line: FX35, Model: INFINITI FX35 2008Pages: 3924, PDF Size: 81.37 MB
Page 2550 of 3924
![INFINITI FX35 2008 User Guide
EM-66
< SERVICE INFORMATION >[VQ35DE]
TIMING CHAIN
Loosen mounting bolts in reverse order as shown in the figure.
Use the seal cutter [SST: KV10111100 (J37228)] to cut liquid
gasket for removal.
INFINITI FX35 2008 User Guide
EM-66
< SERVICE INFORMATION >[VQ35DE]
TIMING CHAIN
Loosen mounting bolts in reverse order as shown in the figure.
Use the seal cutter [SST: KV10111100 (J37228)] to cut liquid
gasket for removal.](/img/42/57017/w960_57017-2549.png)
EM-66
< SERVICE INFORMATION >[VQ35DE]
TIMING CHAIN
Loosen mounting bolts in reverse order as shown in the figure.
Use the seal cutter [SST: KV10111100 (J37228)] to cut liquid
gasket for removal.
CAUTION:
Shaft is internally jointed wi th camshaft sprocket (INT) cen-
ter hole. When removing, keep it horizontal until it is com-
pletely disconnected.
19. Remove collared O-ring from front timing chain case (left and right side).
20. Remove rocker covers (right and left). Refer to EM-51, "
Component".
21. Remove oil pans (lower and upper). Refer to EM-30, "
Component (2WD Models)".
22. Obtain No. 1 cylinder at TDC of its compression stroke as follows:
a. Rotate crankshaft pulley clockwise to align timing mark (grooved line without color) with timing indicator.
b. Make sure that intake and exhaust cam noses on No. 1 cylinder (engine front side of right bank) are located as shown in the fig-
ure.
If not, turn crankshaft one revolution (360 degrees) and alignas shown in the figure.
23. Remove crankshaft pulley as follows:
a. Remove rear cover plate (2WD models) or starter motor (AWD models) and set the ring gear stopper (SST). Refer to EM-30, "
Component (2WD Models)" (2WD models) or SC-8, "System Description" (AWD
models).
SEM728G
PBIC2631E
KBIA1717J
SEM418G
3AA93ABC3ACD3AC03ACA3AC03AC63AC53A913A773A893A873A873A8E3A773A983AC73AC93AC03AC3
3A893A873A873A8F3A773A9D3AAF3A8A3A8C3A863A9D3AAF3A8B3A8C
Page 2576 of 3924
![INFINITI FX35 2008 User Guide
EM-92
< SERVICE INFORMATION >[VQ35DE]
CAMSHAFT
In cases of removing/installing or replacing camshaft and valve-
related parts, or of unusual engine conditions due to changes in
valve clearance (found INFINITI FX35 2008 User Guide
EM-92
< SERVICE INFORMATION >[VQ35DE]
CAMSHAFT
In cases of removing/installing or replacing camshaft and valve-
related parts, or of unusual engine conditions due to changes in
valve clearance (found](/img/42/57017/w960_57017-2575.png)
EM-92
< SERVICE INFORMATION >[VQ35DE]
CAMSHAFT
In cases of removing/installing or replacing camshaft and valve-
related parts, or of unusual engine conditions due to changes in
valve clearance (found malfunctions during stating, idling or causing
noise), perform inspection as follows:
1. Remove rocker covers (right and left bank). Refer to
EM-51, "
Component".
2. Measure the valve clearance as follows:
a. Set No. 1 cylinder at TDC of its compression stroke. Rotate crankshaft pulley clockwise to align timing mark(grooved line without color) with timing indicator.
Make sure that intake and exhaust cam nose on No. 1 cylinder (engine front side of right bank) are located as shown in the
figure.
If not, turn crankshaft one revolution (360 degrees) and align as shown in the figure.
b. Use a feeler gauge, measure t he clearance between valve lifter
and camshaft.
Valve clearance:
Unit: mm (in)
*: Approximately 80°C (176 °F)
SEM713A
KBIA1717J
SEM418G
SEM139D
Items Cold Hot * (reference data)
Intake 0.26 - 0.34 (0.010 - 0.013) 0.304 - 0.416 (0.012 - 0.016)
Exhaust 0.29 - 0.37 (0.011 - 0.015) 0.308 - 0.432 (0.012 - 0.017)
3AA93ABC3ACD3AC03ACA3AC03AC63AC53A913A773A893A873A873A8E3A773A983AC73AC93AC03AC3
3A893A873A873A8F3A773A9D3AAF3A8A3A8C3A863A9D3AAF3A8B3A8C
Page 2702 of 3924
![INFINITI FX35 2008 User Guide
EM-218
< SERVICE INFORMATION >[VK45DE]
CAMSHAFT
a. Release fuel pressure. Refer to
EC-665, "Fuel Pressure Check".
b. Disconnect ignition coil and injector harness connectors.
3. Remove intake valve INFINITI FX35 2008 User Guide
EM-218
< SERVICE INFORMATION >[VK45DE]
CAMSHAFT
a. Release fuel pressure. Refer to
EC-665, "Fuel Pressure Check".
b. Disconnect ignition coil and injector harness connectors.
3. Remove intake valve](/img/42/57017/w960_57017-2701.png)
EM-218
< SERVICE INFORMATION >[VK45DE]
CAMSHAFT
a. Release fuel pressure. Refer to
EC-665, "Fuel Pressure Check".
b. Disconnect ignition coil and injector harness connectors.
3. Remove intake valve timing control solenoid valve. Refer to EM-199, "
Component".
4. Crank the engine, and then make sure that engine oil comes out from intake valve timing control cover oil hole. End crank after
checking.
WARNING:
Be careful not to touch rotati ng parts (drive belt, idler pul-
ley, and crankshaft pulley, etc.).
CAUTION:
Engine oil may squirt from intake valve timing control sole-
noid valve installation hole during cranking. Use a shop
cloth to prevent the engine co mponents and the vehicle. Do
not allow engine oil to get on rubber components such as
drive belt or engine mount insulators. Immediately wipe off
any splashed engine oil.
Clean oil groove between oil strainer and intake valve timing control solenoid valve if engine oil does not come out from intake valve timing control cover oil hole. Refer to LU-21, "
Lubrication Circuit".
5. Remove components between intake valve timing c ontrol solenoid valve and camshaft sprocket (INT),
and then check each oil groove for clogging.
Clean oil groove if necessary. Refer to LU-21, "
Lubrication Circuit".
6. After inspection, install removed parts.
Valve ClearanceINFOID:0000000001325792
INSPECTION
In cases of removing/installing or replacing camshaft and valve-related parts, or of unusual engine conditions
due to changes in valve clearance (found malfunctions dur ing starting, idling or causing noise), perform
inspection as follows:
1. Remove rocker covers (right and left bank). Refer to EM-196, "
Component".
2. Measure the valve clearance as follows:
a. Set No. 1 cylinder at TDC of its compression stroke. Rotate crankshaft pulley in clockwise to align TDC identifica-
tion notch (without paint mark) with timing indicator on front
cover.
Make sure that both intake and exhaust cam noses of No. 1 cylinder (engine front side of left bank) are located as shown in
the figure.
If not, turn crankshaft one revolution (360 degrees) and align
as shown in the figure.
PBIC2848E
PBIC2341E
KBIA0400J
3AA93ABC3ACD3AC03ACA3AC03AC63AC53A913A773A893A873A873A8E3A773A983AC73AC93AC03AC3
3A893A873A873A8F3A773A9D3AAF3A8A3A8C3A863A9D3AAF3A8B3A8C
Page 3272 of 3924
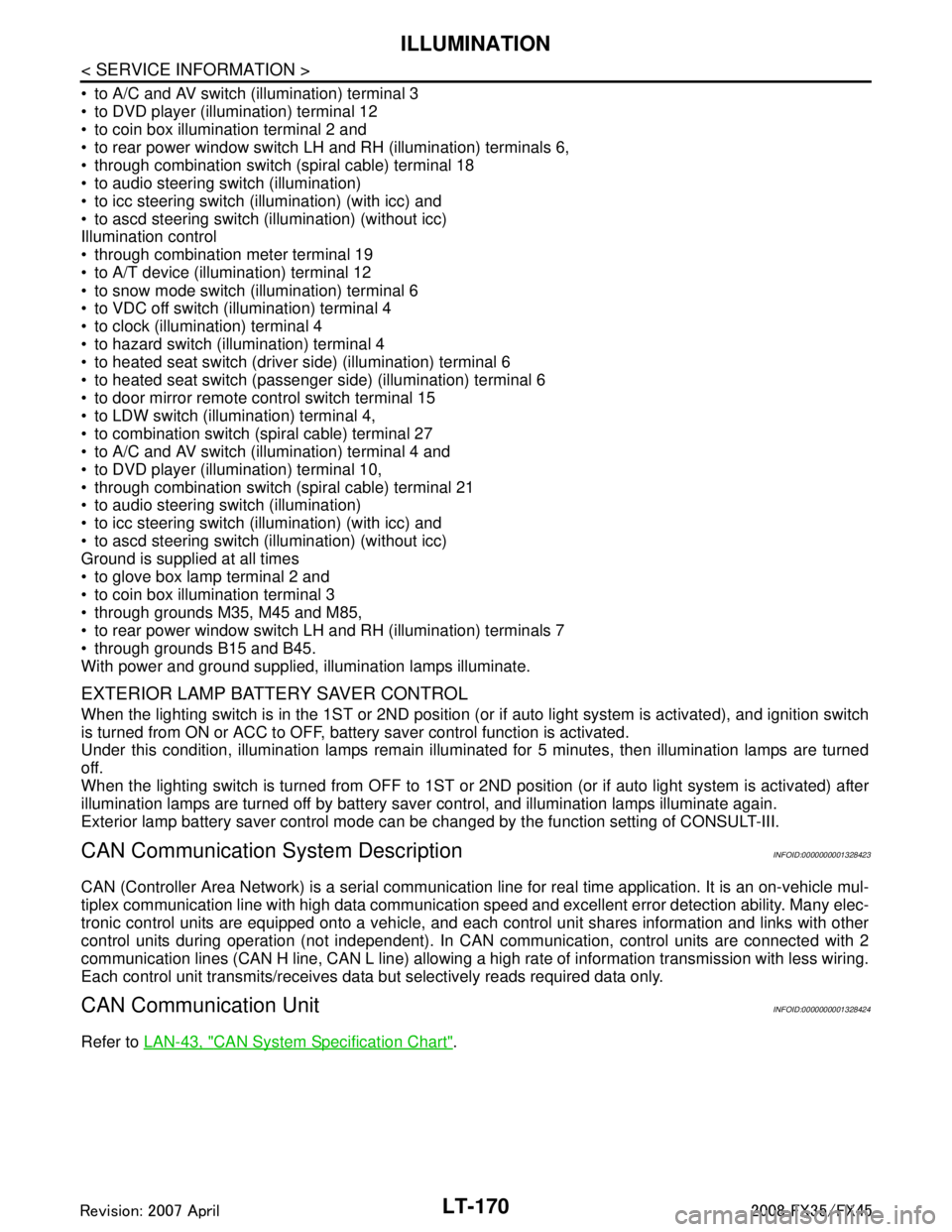
LT-170
< SERVICE INFORMATION >
ILLUMINATION
to A/C and AV switch (illumination) terminal 3
to DVD player (illumination) terminal 12
to coin box illumination terminal 2 and
to rear power window switch LH and RH (illumination) terminals 6,
through combination switch (spiral cable) terminal 18
to audio steering switch (illumination)
to icc steering switch (illumination) (with icc) and
to ascd steering switch (illumination) (without icc)
Illumination control
through combination meter terminal 19
to A/T device (illumination) terminal 12
to snow mode switch (illumination) terminal 6
to VDC off switch (illumination) terminal 4
to clock (illumination) terminal 4
to hazard switch (illumination) terminal 4
to heated seat switch (driver side) (illumination) terminal 6
to heated seat switch (passenger side) (illumination) terminal 6
to door mirror remote control switch terminal 15
to LDW switch (illumination) terminal 4,
to combination switch (spiral cable) terminal 27
to A/C and AV switch (illumination) terminal 4 and
to DVD player (illumination) terminal 10,
through combination switch (spiral cable) terminal 21
to audio steering switch (illumination)
to icc steering switch (illumination) (with icc) and
to ascd steering switch (illumination) (without icc)
Ground is supplied at all times
to glove box lamp terminal 2 and
to coin box illumination terminal 3
through grounds M35, M45 and M85,
to rear power window switch LH and RH (illumination) terminals 7
through grounds B15 and B45.
With power and ground supplied, illumination lamps illuminate.
EXTERIOR LAMP BATTERY SAVER CONTROL
When the lighting switch is in the 1ST or 2ND position (or if auto light system is activated), and ignition switch
is turned from ON or ACC to OFF, batte ry saver control function is activated.
Under this condition, illumination lamps remain illuminated for 5 minutes, then illumination lamps are turned
off.
When the lighting switch is turned from OFF to 1ST or 2 ND position (or if auto light system is activated) after
illumination lamps are turned off by battery save r control, and illumination lamps illuminate again.
Exterior lamp battery saver control mode can be changed by the function setting of CONSULT-III.
CAN Communication System DescriptionINFOID:0000000001328423
CAN (Controller Area Network) is a serial communication line for real time application. It is an on-vehicle mul-
tiplex communication line with high data communication s peed and excellent error detection ability. Many elec-
tronic control units are equipped onto a vehicle, and each control unit shares information and links with other
control units during operation (not independent). In CA N communication, control units are connected with 2
communication lines (CAN H line, CAN L line) allowing a high rate of information transmission with less wiring.
Each control unit transmits/receives data but selectively reads required data only.
CAN Communication UnitINFOID:0000000001328424
Refer to LAN-43, "CAN System Specification Chart".
3AA93ABC3ACD3AC03ACA3AC03AC63AC53A913A773A893A873A873A8E3A773A983AC73AC93AC03AC3
3A893A873A873A8F3A773A9D3AAF3A8A3A8C3A863A9D3AAF3A8B3A8C
Page 3480 of 3924
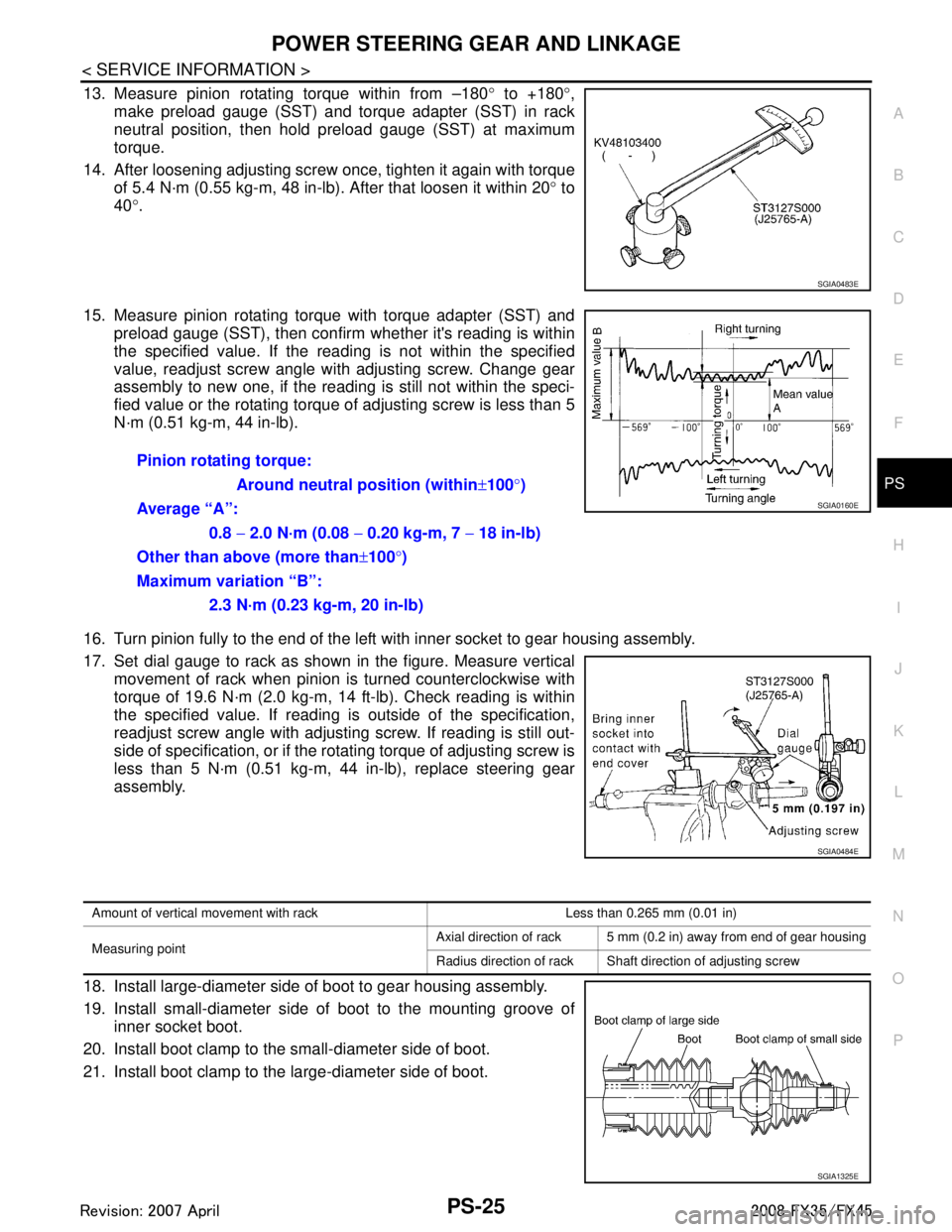
POWER STEERING GEAR AND LINKAGEPS-25
< SERVICE INFORMATION >
C
DE
F
H I
J
K L
M A
B
PS
N
O P
13. Measure pinion rotating torque within from –180 ° to +180 °,
make preload gauge (SST) and torque adapter (SST) in rack
neutral position, then hold preload gauge (SST) at maximum
torque.
14. After loosening adjusting screw once, tighten it again with torque of 5.4 N·m (0.55 kg-m, 48 in-lb). After that loosen it within 20 ° to
40 °.
15. Measure pinion rotating torque with torque adapter (SST) and preload gauge (SST), then confirm w hether it's reading is within
the specified value. If the r eading is not within the specified
value, readjust screw angle with adjusting screw. Change gear
assembly to new one, if the readi ng is still not within the speci-
fied value or the rotating torque of adjusting screw is less than 5
N·m (0.51 kg-m, 44 in-lb).
16. Turn pinion fully to the end of the left with inner socket to gear housing assembly.
17. Set dial gauge to rack as shown in the figure. Measure vertical movement of rack when pinion is turned counterclockwise with
torque of 19.6 N·m (2.0 kg-m, 14 ft-lb). Check reading is within
the specified value. If reading is outside of the specification,
readjust screw angle with adjusting screw. If reading is still out-
side of specification, or if the rotating torque of adjusting screw is
less than 5 N·m (0.51 kg-m, 44 in-lb), replace steering gear
assembly.
18. Install large-diameter side of boot to gear housing assembly.
19. Install small-diameter side of boot to the mounting groove of inner socket boot.
20. Install boot clamp to the small-diameter side of boot.
21. Install boot clamp to the large-diameter side of boot.
SGIA0483E
Pinion rotating torque:
Around neutral position (within ±100 °)
Average “A”:
0.8 − 2.0 N·m (0.08 − 0.20 kg-m, 7 − 18 in-lb)
Other than above (more than ±100 °)
Maximum variation “B”:
2.3 N·m (0.23 kg-m, 20 in-lb)
SGIA0160E
SGIA0484E
Amount of vertical movement with rack Less than 0.265 mm (0.01 in)
Measuring point Axial direction of rack 5 mm (0.2 in) away from end of gear housing
Radius direction of rack Shaft direction of adjusting screw
SGIA1325E
3AA93ABC3ACD3AC03ACA3AC03AC63AC53A913A773A893A873A873A8E3A773A983AC73AC93AC03AC3
3A893A873A873A8F3A773A9D3AAF3A8A3A8C3A863A9D3AAF3A8B3A8C
Page 3774 of 3924
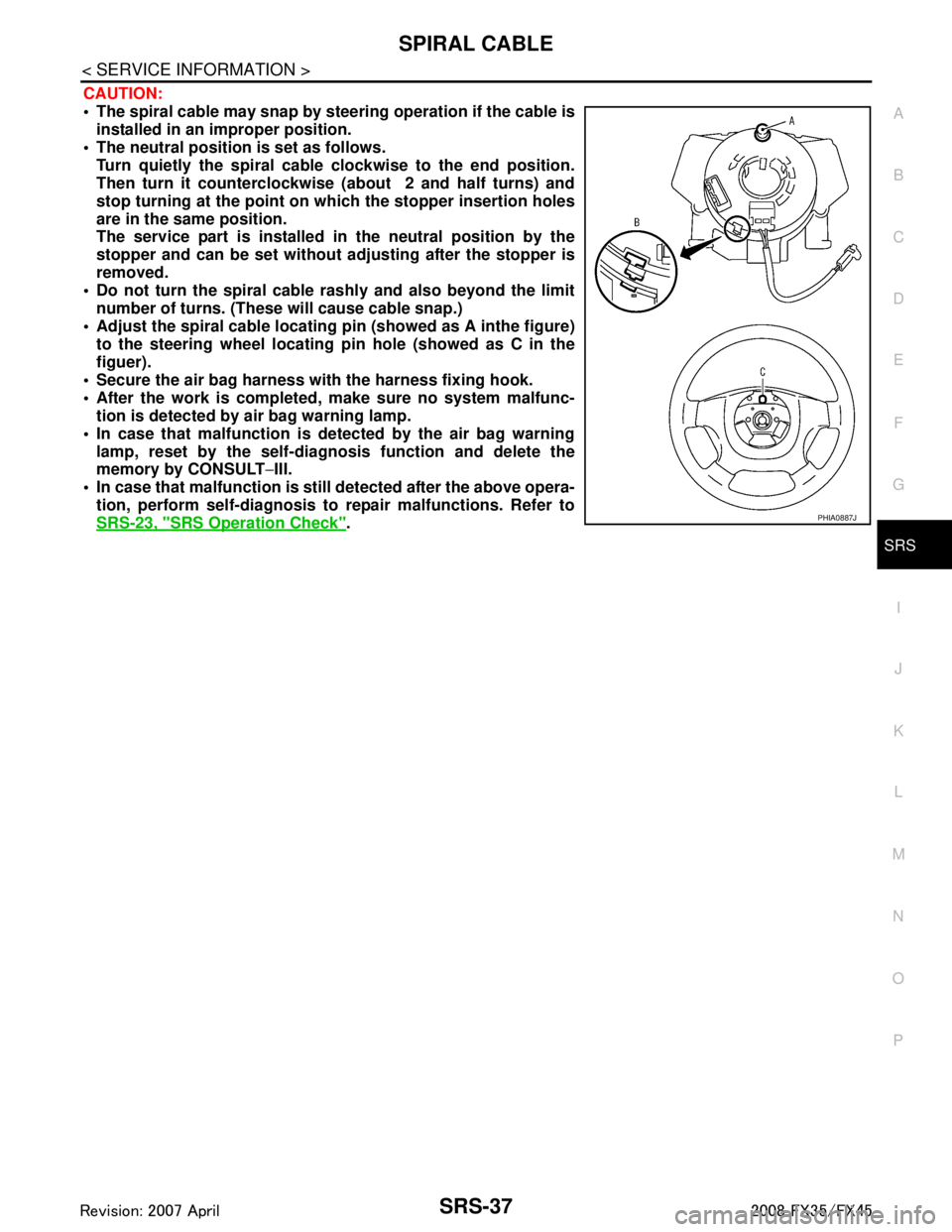
SPIRAL CABLESRS-37
< SERVICE INFORMATION >
C
DE
F
G
I
J
K L
M A
B
SRS
N
O P
CAUTION:
The spiral cable may snap by steering operation if the cable is
installed in an improper position.
The neutral position is set as follows. Turn quietly the spiral cable clockwise to the end position.
Then turn it counterclockwise (about 2 and half turns) and
stop turning at the point on which the stopper insertion holes
are in the same position.
The service part is installed in the neutral position by the
stopper and can be set without adjusting after the stopper is
removed.
Do not turn the spiral cable r ashly and also beyond the limit
number of turns. (These will cause cable snap.)
Adjust the spiral cable locating pin (showed as A inthe figure) to the steering wheel locating pin hole (showed as C in the
figuer).
Secure the air bag harness wi th the harness fixing hook.
After the work is completed, make sure no system malfunc- tion is detected by air bag warning lamp.
In case that malfunction is detected by the air bag warning lamp, reset by the self-diagnosis function and delete the
memory by CONSULT −III.
In case that malfunction is still detected after the above opera-
tion, perform self-diagnosis to repair malfunctions. Refer to
SRS-23, "
SRS Operation Check".PHIA0887J
3AA93ABC3ACD3AC03ACA3AC03AC63AC53A913A773A893A873A873A8E3A773A983AC73AC93AC03AC3
3A893A873A873A8F3A773A9D3AAF3A8A3A8C3A863A9D3AAF3A8B3A8C