set clock INFINITI FX35 2008 Service Manual
[x] Cancel search | Manufacturer: INFINITI, Model Year: 2008, Model line: FX35, Model: INFINITI FX35 2008Pages: 3924, PDF Size: 81.37 MB
Page 315 of 3924
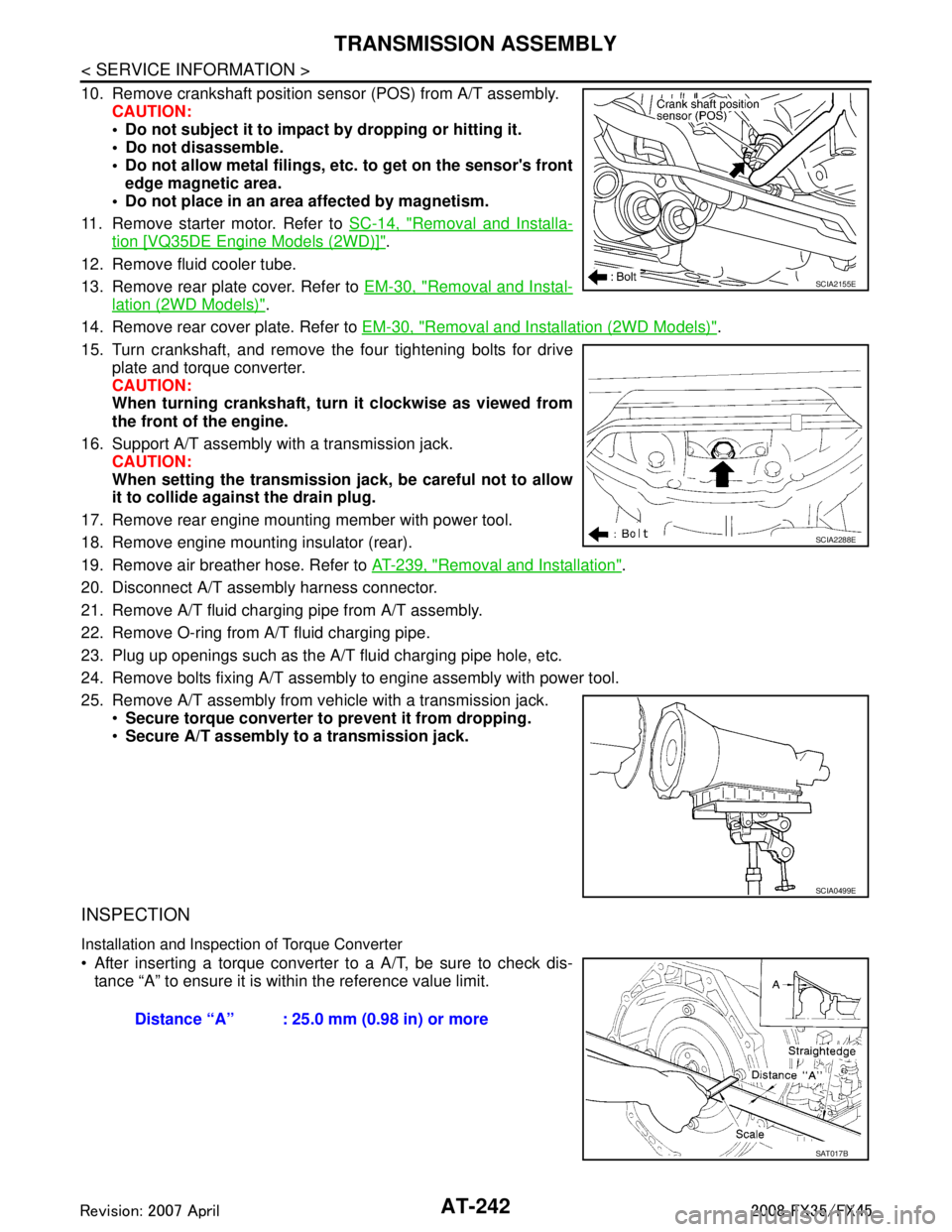
AT-242
< SERVICE INFORMATION >
TRANSMISSION ASSEMBLY
10. Remove crankshaft position sensor (POS) from A/T assembly.CAUTION:
Do not subject it to impact by dropping or hitting it.
Do not disassemble.
Do not allow metal filings, etc. to get on the sensor's front
edge magnetic area.
Do not place in an area affected by magnetism.
11. Remove starter motor. Refer to SC-14, "
Removal and Installa-
tion [VQ35DE Engine Models (2WD)]".
12. Remove fluid cooler tube.
13. Remove rear plate cover. Refer to EM-30, "
Removal and Instal-
lation (2WD Models)".
14. Remove rear cover plate. Refer to EM-30, "
Removal and Installation (2WD Models)".
15. Turn crankshaft, and remove the four tightening bolts for drive plate and torque converter.
CAUTION:
When turning crankshaft, turn it clockwise as viewed from
the front of the engine.
16. Support A/T assembly with a transmission jack. CAUTION:
When setting the transmission j ack, be careful not to allow
it to collide agai nst the drain plug.
17. Remove rear engine mounting member with power tool.
18. Remove engine mounting insulator (rear).
19. Remove air breather hose. Refer to AT-239, "
Removal and Installation".
20. Disconnect A/T assembly harness connector.
21. Remove A/T fluid charging pipe from A/T assembly.
22. Remove O-ring from A/T fluid charging pipe.
23. Plug up openings such as the A/T fluid charging pipe hole, etc.
24. Remove bolts fixing A/T assembly to engine assembly with power tool.
25. Remove A/T assembly from vehicle with a transmission jack. Secure torque converter to prevent it from dropping.
Secure A/T assembly to a transmission jack.
INSPECTION
Installation and Inspection of Torque Converter
After inserting a torque converter to a A/T, be sure to check dis-
tance “A” to ensure it is within the reference value limit.
SCIA2155E
SCIA2288E
SCIA0499E
Distance “A” : 25.0 mm (0.98 in) or more
SAT017B
3AA93ABC3ACD3AC03ACA3AC03AC63AC53A913A773A893A873A873A8E3A773A983AC73AC93AC03AC3
3A893A873A873A8F3A773A9D3AAF3A8A3A8C3A863A9D3AAF3A8B3A8C
Page 319 of 3924
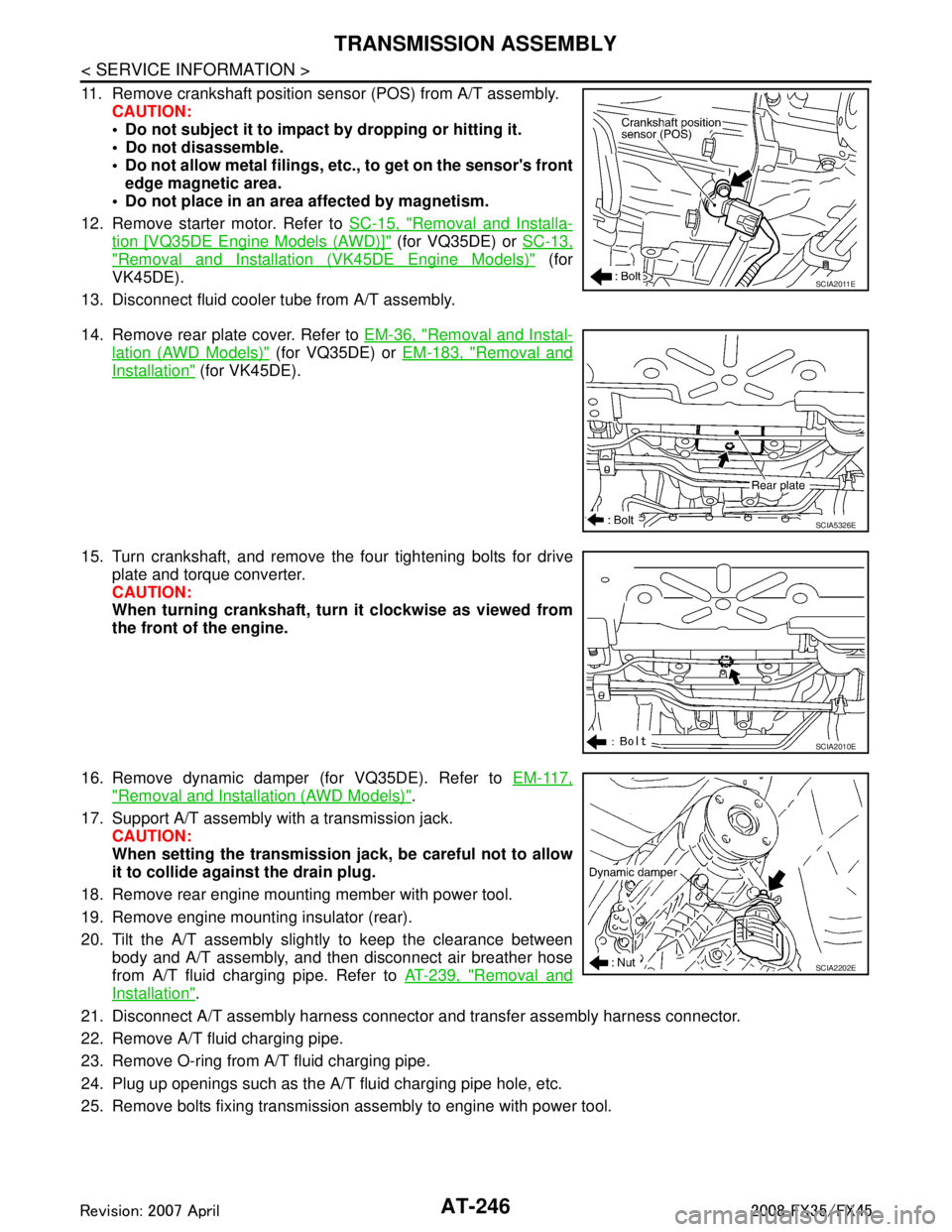
AT-246
< SERVICE INFORMATION >
TRANSMISSION ASSEMBLY
11. Remove crankshaft position sensor (POS) from A/T assembly.CAUTION:
Do not subject it to impact by dropping or hitting it.
Do not disassemble.
Do not allow metal filings, et c., to get on the sensor's front
edge magnetic area.
Do not place in an area affected by magnetism.
12. Remove starter motor. Refer to SC-15, "
Removal and Installa-
tion [VQ35DE Engine Models (AWD)]" (for VQ35DE) or SC-13,
"Removal and Installation (VK45DE Engine Models)" (for
VK45DE).
13. Disconnect fluid cooler tube from A/T assembly.
14. Remove rear plate cover. Refer to EM-36, "
Removal and Instal-
lation (AWD Models)" (for VQ35DE) or EM-183, "Removal and
Installation" (for VK45DE).
15. Turn crankshaft, and remove the four tightening bolts for drive plate and torque converter.
CAUTION:
When turning crankshaft, turn it clockwise as viewed from
the front of the engine.
16. Remove dynamic damper (for VQ35DE). Refer to EM-117,
"Removal and Installation (AWD Models)".
17. Support A/T assembly with a transmission jack. CAUTION:
When setting the transmission j ack, be careful not to allow
it to collide agai nst the drain plug.
18. Remove rear engine mounting member with power tool.
19. Remove engine mounting insulator (rear).
20. Tilt the A/T assembly slightly to keep the clearance between body and A/T assembly, and then disconnect air breather hose
from A/T fluid charging pipe. Refer to AT-239, "
Removal and
Installation".
21. Disconnect A/T assembly harness connector and transfer assembly harness connector.
22. Remove A/T fluid charging pipe.
23. Remove O-ring from A/T fluid charging pipe.
24. Plug up openings such as the A/T fluid charging pipe hole, etc.
25. Remove bolts fixing transmission assembly to engine with power tool.
SCIA2011E
SCIA5326E
SCIA2010E
SCIA2202E
3AA93ABC3ACD3AC03ACA3AC03AC63AC53A913A773A893A873A873A8E3A773A983AC73AC93AC03AC3
3A893A873A873A8F3A773A9D3AAF3A8A3A8C3A863A9D3AAF3A8B3A8C
Page 624 of 3924
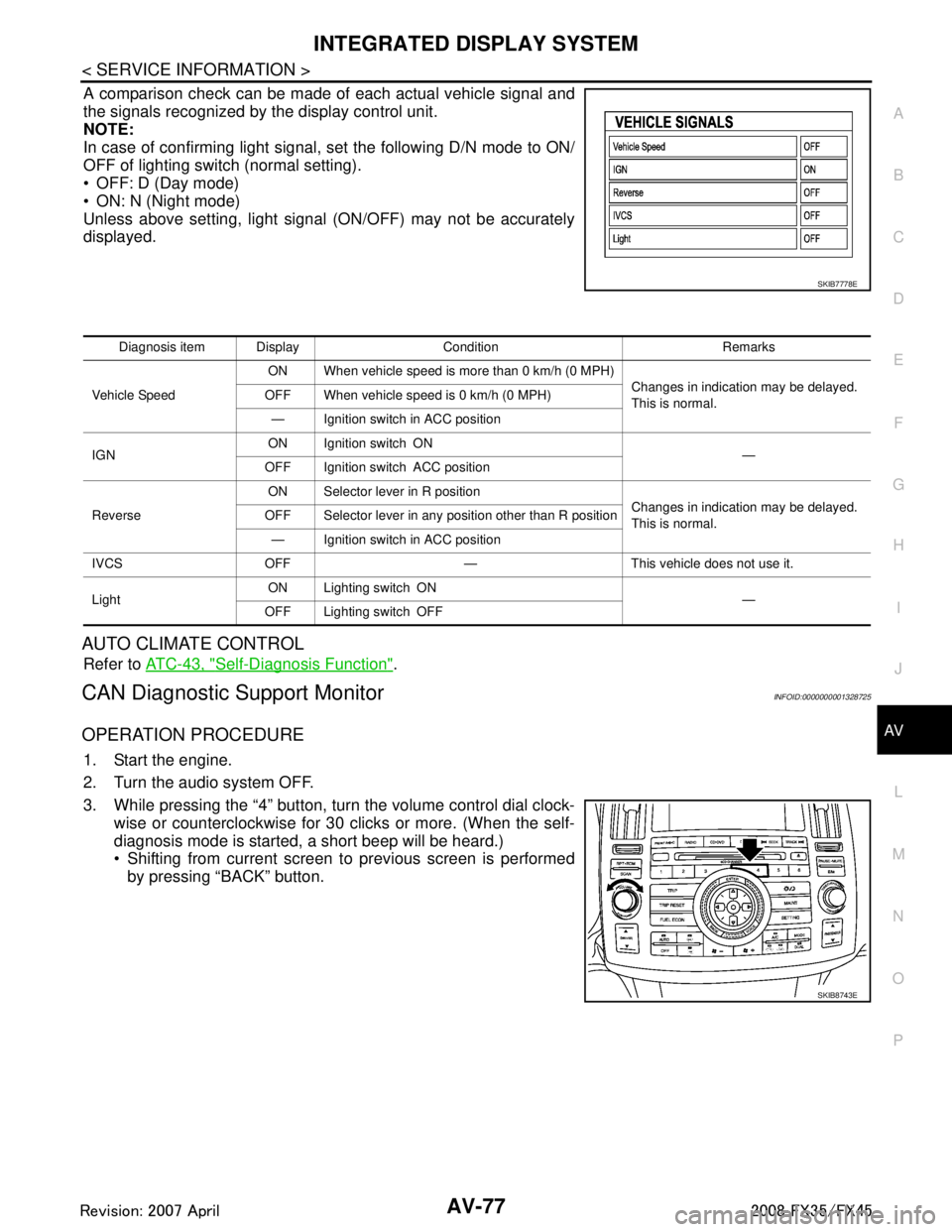
INTEGRATED DISPLAY SYSTEMAV-77
< SERVICE INFORMATION >
C
DE
F
G H
I
J
L
M A
B
AV
N
O P
A comparison check can be made of each actual vehicle signal and
the signals recognized by the display control unit.
NOTE:
In case of confirming light signal, set the following D/N mode to ON/
OFF of lighting switch (normal setting).
OFF: D (Day mode)
ON: N (Night mode)
Unless above setting, light signal (ON/OFF) may not be accurately
displayed.
AUTO CLIMATE CONTROL
Refer to ATC-43, "Self-Diagnosis Function".
CAN Diagnostic Support MonitorINFOID:0000000001328725
OPERATION PROCEDURE
1. Start the engine.
2. Turn the audio system OFF.
3. While pressing the “4” button, turn the volume control dial clock-
wise or counterclockwise for 30 clicks or more. (When the self-
diagnosis mode is started, a short beep will be heard.)
Shifting from current screen to previous screen is performedby pressing “BACK” button.
SKIB7778E
Diagnosis item Display Condition Remarks
Vehicle Speed ON When vehicle speed is more than 0 km/h (0 MPH)
Changes in indication may be delayed.
This is normal.
OFF When vehicle speed is 0 km/h (0 MPH)
— Ignition switch in ACC position
IGN ON Ignition switch ON
—
OFF Ignition switch ACC position
Reverse ON Selector lever in R position
Changes in indication may be delayed.
This is normal.
OFF Selector lever in any position other than R position
— Ignition switch in ACC position
IVCS OFF — This vehicle does not use it.
Light ON Lighting switch ON
—
OFF Lighting switch OFF
SKIB8743E
3AA93ABC3ACD3AC03ACA3AC03AC63AC53A913A773A893A873A873A8E3A773A983AC73AC93AC03AC3
3A893A873A873A8F3A773A9D3AAF3A8A3A8C3A863A9D3AAF3A8B3A8C
Page 989 of 3924
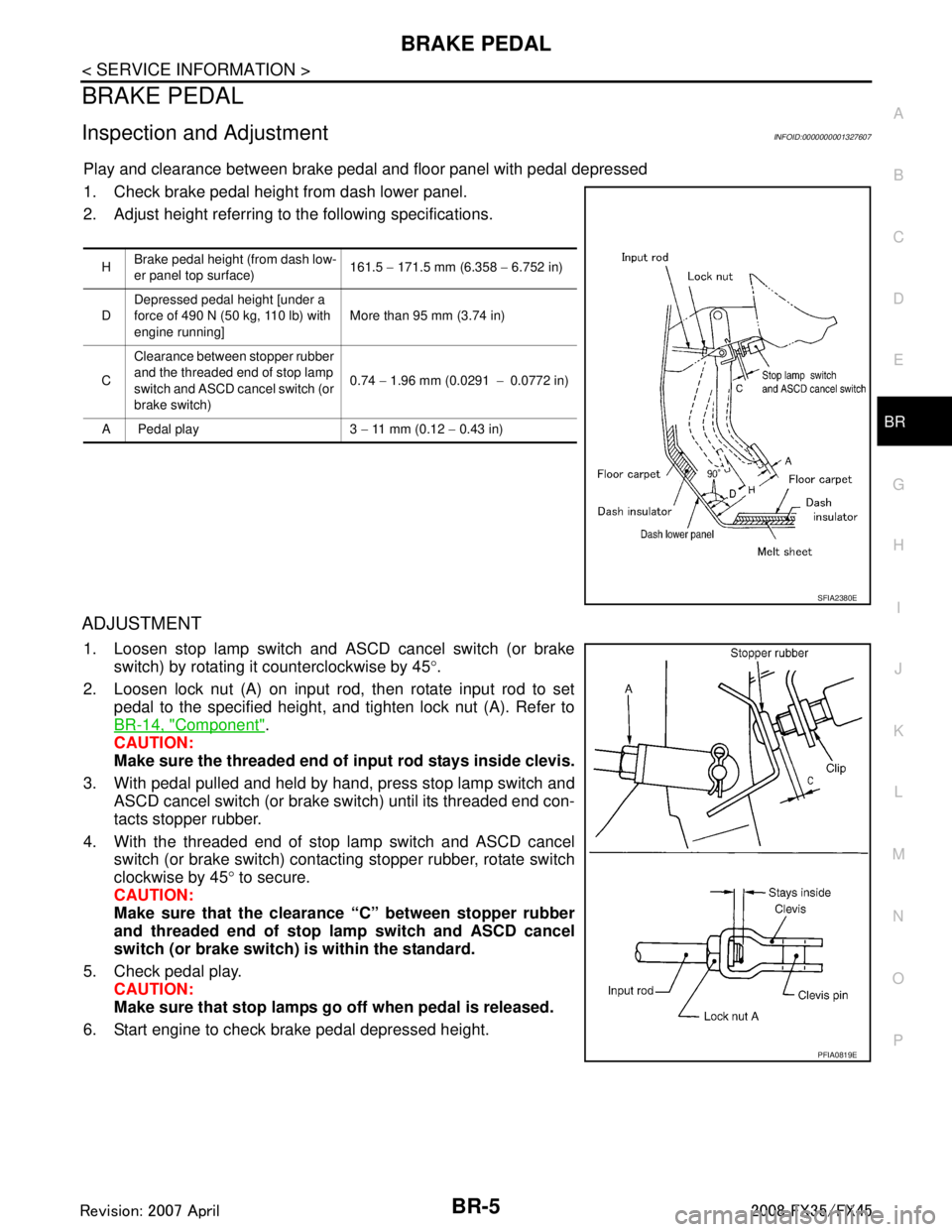
BRAKE PEDALBR-5
< SERVICE INFORMATION >
C
DE
G H
I
J
K L
M A
B
BR
N
O P
BRAKE PEDAL
Inspection and AdjustmentINFOID:0000000001327607
Play and clearance between brake pedal and floor panel with pedal depressed
1. Check brake pedal height from dash lower panel.
2. Adjust height referring to the following specifications.
ADJUSTMENT
1. Loosen stop lamp switch and ASCD cancel switch (or brake switch) by rotating it counterclockwise by 45 °.
2. Loosen lock nut (A) on input rod, then rotate input rod to set pedal to the specified height, and tighten lock nut (A). Refer to
BR-14, "
Component".
CAUTION:
Make sure the threaded end of input rod stays inside clevis.
3. With pedal pulled and held by hand, press stop lamp switch and ASCD cancel switch (or brake switch) until its threaded end con-
tacts stopper rubber.
4. With the threaded end of stop lamp switch and ASCD cancel switch (or brake switch) contacting stopper rubber, rotate switch
clockwise by 45 ° to secure.
CAUTION:
Make sure that the clearance “C” between stopper rubber
and threaded end of stop lamp switch and ASCD cancel
switch (or brake switch) is within the standard.
5. Check pedal play. CAUTION:
Make sure that stop lamps go off when pedal is released.
6. Start engine to check brake pedal depressed height.
H Brake pedal height (from dash low-
er panel top surface) 161.5
− 171.5 mm (6.358 − 6.752 in)
D Depressed pedal height [under a
force of 490 N (50 kg, 110 lb) with
engine running] More than 95 mm (3.74 in)
C Clearance between stopper rubber
and the threaded end of stop lamp
switch and ASCD cancel switch (or
brake switch) 0.74
− 1.96 mm (0.0291 −0.0772 in)
A Pedal play 3 − 11 mm (0.12 − 0.43 in)
SFIA2380E
PFIA0819E
3AA93ABC3ACD3AC03ACA3AC03AC63AC53A913A773A893A873A873A8E3A773A983AC73AC93AC03AC3
3A893A873A873A8F3A773A9D3AAF3A8A3A8C3A863A9D3AAF3A8B3A8C
Page 1128 of 3924

DI-2
CONSULT-III Function (BCM) ................................60
Trouble Diagnosis ...................................................61
Symptom Chart .......................................................61
Power Supply and Ground Circuit Inspection .........61
Combination Meter Buzzer Circuit Inspection .........62
Front Door Switch (Driver Side) Signal Inspection ...63
Key Switch Signal Inspection (Without Intelligent
Key) ..................................................................... ...
64
Key Switch and Ignition Knob Switch Signal In-
spection (With Intelligent Key, When Mechanical
Key Is Used) ........................................................ ...
65
Lighting Switch Signal Inspection ...........................66
Seat Belt Buckle Switch (Driver Side) Signal In-
spection ............................................................... ...
66
Component Inspection ............................................67
LANE DEPARTURE WARNING SYSTEM ........69
Precaution for Lane Departure Warning (LDW)
system ................................................................. ...
69
System Description .................................................69
Action Test ..............................................................71
Camera Aiming Adjustment ....................................71
Component Parts and Harness Connector Loca-
tion ..........................................................................
76
Schematic ...............................................................77
Wiring Diagram - LDW - .........................................78
Terminal and Reference Value for LDW Camera
Unit .........................................................................
81
CONSULT-III Function (LDW) ................................81
Trouble Diagnosis ...................................................83
Preliminary Check ..................................................84
Power Supply and Ground Circuit Inspection .........84
DTC [C1B00] CAMERA UNIT MALF ......................85
DTC [C1B01] CAM AIMING INCMP .......................85
DTC [C1B02] VHCL SPD DATA MALF ..................85
DTC [C1B03] ABNRML TEMP DETECT ................86
DTC [U1000] CAN COMM CIRCUIT ......................86
DTC [U1010] CONTROL UNIT (CAN) ....................86
LDW Chime Circuit Inspection ................................86
LDW Switch Circuit Inspection ...............................88
LDW Indicator Lamp Circuit Inspection ..................90
Turn Signal Input Inspection ................................ ...91
Electrical Component Inspection ............................91
Removal and Installation for LDW Camera Unit .....91
Removal and Installation for LDW Chime ............ ...91
Removal and Installation for LDW Switch ...............92
CAN COMMUNICATION ...................................93
System Description .............................................. ...93
CAN Communication Unit .......................................93
COMPASS .........................................................94
Precaution for Compass ...................................... ...94
System Description .................................................94
Troubleshooting ......................................................94
Zone Variation Setting Procedure ...........................95
Calibration Procedure .............................................95
Wiring Diagram - COMPAS - ..................................97
Removal and Installation of Compass ....................97
CLOCK ..............................................................98
Wiring Diagram - CLOCK - .................................. ...98
Removal and Installation of Clock ...........................98
REAR VIEW MONITOR ....................................100
System Description .............................................. .100
Component Parts and Harness Connector Loca-
tion ........................................................................
101
Schematic .............................................................102
Wiring Diagram - R/VIEW - ...................................103
Terminal and Reference Value for Rear View
Camera Control Unit .............................................
106
CONSULT-III Function (REARVIEW CAMERA) ...106
Side Distance Guideline Correction ......................107
Power Supply and Ground Circuit Inspection .......108
Rear View Is Not Displayed with the A/T Selector
Lever in R-Position ................................................
108
The Rear View Image Is Distorted ........................112
Removal and Installation of Rear View Camera
Control Unit .......................................................... .
113
Removal and Installation of Rear View Camera ...113
3AA93ABC3ACD3AC03ACA3AC03AC63AC53A913A773A893A873A873A8E3A773A983AC73AC93AC03AC3
3A893A873A873A8F3A773A9D3AAF3A8A3A8C3A863A9D3AAF3A8B3A8C
Page 1312 of 3924
![INFINITI FX35 2008 Service Manual
EC-72
< SERVICE INFORMATION >[VQ35DE]
ON BOARD DIAGNOSTIC (OBD) SYSTEM
When there is an open circuit on MIL circuit, the ECM c
annot warn the driver by lighting up MIL when there is
malfunction on en INFINITI FX35 2008 Service Manual
EC-72
< SERVICE INFORMATION >[VQ35DE]
ON BOARD DIAGNOSTIC (OBD) SYSTEM
When there is an open circuit on MIL circuit, the ECM c
annot warn the driver by lighting up MIL when there is
malfunction on en](/img/42/57017/w960_57017-1311.png)
EC-72
< SERVICE INFORMATION >[VQ35DE]
ON BOARD DIAGNOSTIC (OBD) SYSTEM
When there is an open circuit on MIL circuit, the ECM c
annot warn the driver by lighting up MIL when there is
malfunction on engine control system.
Therefore, when electrical controlled throttle and part of ECM related diagnoses are continuously detected as
NG for 5 trips, ECM warns the driver that engine cont rol system malfunctions and MIL circuit is open by means
of operating fail-safe function.
The fail-safe function also operates when above diagnos es except MIL circuit are detected and demands the
driver to repair the malfunction.
MIL Flashing Without DTC
When any SRT codes are not set, MIL may fl ash without DTC. For the details, refer to EC-55, "Emission-
Related Diagnostic Information".
HOW TO SWITCH DIAGNOSTIC TEST MODE
NOTE:
It is better to count the ti me accurately with a clock.
It is impossible to switch the di agnostic mode when an accelerator pedal position sensor circuit has
a malfunction.
Always ECM returns to Diagnostic Test Mode I after ignition switch is turned OFF.
How to Set Diagnostic Test Mode II (Self-Diagnostic Results)
1. Confirm that accelerator pedal is fully released, turn ignition switch ON and wait 3 seconds.
2. Repeat the following procedure quickly 5 times within 5 seconds.
a. Fully depress the accelerator pedal.
b. Fully release the accelerator pedal.
3. Wait 7 seconds, fully depress the accelerator pedal and keep it for approx. 10 seconds until the MIL starts
blinking.
NOTE:
Diagnostic Test
Mode KEY and ENG.
Status Function Explanation of Function
Mode I Ignition switch in ON position
Engine stopped BULB CHECK This function checks the MIL bulb for damage (blown, open
circuit, etc.).
If the MIL does not come on, check MIL circuit.
Engine running MALFUNCTION WARNING This is a usual driving condition. When a malfunction is de-
tected twice in two consecutive driving cycles (two trip de-
tection logic), the MIL will light up to inform the driver that a
malfunction has been detected.
The following malfunctions will light up or blink the MIL in
the 1st trip.
Misfire (Possible three way catalyst damage)
One trip detection diagnoses
Mode II Ignition switch in ON position
Engine stopped SELF-DIAGNOSTIC
RESULTS
This function allows DTCs an
d 1st trip DTCs to be read.
Engine operating condition in fail-safe mode Engine speed will not rise more than 2,500 rpm due to the fuel cut
3AA93ABC3ACD3AC03ACA3AC03AC63AC53A913A773A893A873A873A8E3A773A983AC73AC93AC03AC3
3A893A873A873A8F3A773A9D3AAF3A8A3A8C3A863A9D3AAF3A8B3A8C
Page 1636 of 3924
![INFINITI FX35 2008 Service Manual
EC-396
< SERVICE INFORMATION >[VQ35DE]
DTC P0456 EVAP CONTROL SYSTEM
2. Set the pressure pump and a hose.
3. Also set a vacuum gauge via 3-way connector and a hose.
4. Turn ignition switch ON.
5. Con INFINITI FX35 2008 Service Manual
EC-396
< SERVICE INFORMATION >[VQ35DE]
DTC P0456 EVAP CONTROL SYSTEM
2. Set the pressure pump and a hose.
3. Also set a vacuum gauge via 3-way connector and a hose.
4. Turn ignition switch ON.
5. Con](/img/42/57017/w960_57017-1635.png)
EC-396
< SERVICE INFORMATION >[VQ35DE]
DTC P0456 EVAP CONTROL SYSTEM
2. Set the pressure pump and a hose.
3. Also set a vacuum gauge via 3-way connector and a hose.
4. Turn ignition switch ON.
5. Connect GST and select Service $08.
6. Using Service $08 control the EVAP canister vent control valve
(close).
7. Apply pressure and make sure the following conditions are sat- isfied.
Pressure to be applied: 2.7 kPa (20 mmHg, 0.79 inHg)
Time to be waited after the pressure drawn in to the EVAP
system and the pressure to be dropped: 60 seconds and
the pressure should not be dropped more than 0.4 kPa (3
mmHg, 0.12 inHg).
If NG, go to EC-396, "
Diagnosis Procedure".
If OK, go to next step.
8. Disconnect GST.
9. Start engine and warm it up to normal operating temperature.
10. Turn ignition switch OFF and wait at least 10 seconds.
11. Restart engine and let it idle for 90 seconds.
12. Keep engine speed at 2,000 rpm for 30 seconds.
13. Turn ignition switch OFF. NOTE:
For more information, refer to GST Instruction Manual.
Diagnosis ProcedureINFOID:0000000001326225
1.CHECK FUEL FILLER CAP DESIGN
1. Turn ignition switch OFF.
2. Check for genuine NISSAN fuel filler cap design.
OK or NG
OK >> GO TO 2.
NG >> Replace with genuine NISSAN fuel filler cap.
2.CHECK FUEL FILLER CAP INSTALLATION
Check that the cap is tightened proper ly by rotating the cap clockwise.
OK or NG
OK >> GO TO 3.
NG >> 1. Open fuel filler cap, then clean cap and fuel filler neck threads using air blower.
2. Retighten until ratcheting sound is heard.
3.CHECK FUEL FILLER CAP FUNCTION
Check for air releasing sound while opening the fuel filler cap.
OK or NG
OK >> GO TO 5.
NG >> GO TO 4.
4.CHECK FUEL TANK VACUUM RELIEF VALVE
Refer to EC-42, "
Component Inspection".
OK or NG
OK >> GO TO 5.
NG >> Replace fuel filler cap with a genuine one.
SEF462UI
SEF915U
3AA93ABC3ACD3AC03ACA3AC03AC63AC53A913A773A893A873A873A8E3A773A983AC73AC93AC03AC3
3A893A873A873A8F3A773A9D3AAF3A8A3A8C3A863A9D3AAF3A8B3A8C
Page 1890 of 3924
![INFINITI FX35 2008 Service Manual
EC-650
< SERVICE INFORMATION >[VK45DE]
ON BOARD DIAGNOSTIC (OBD) SYSTEM
When there is an open circuit on MIL circuit, the ECM c
annot warn the driver by lighting up MIL when there is
malfunction on e INFINITI FX35 2008 Service Manual
EC-650
< SERVICE INFORMATION >[VK45DE]
ON BOARD DIAGNOSTIC (OBD) SYSTEM
When there is an open circuit on MIL circuit, the ECM c
annot warn the driver by lighting up MIL when there is
malfunction on e](/img/42/57017/w960_57017-1889.png)
EC-650
< SERVICE INFORMATION >[VK45DE]
ON BOARD DIAGNOSTIC (OBD) SYSTEM
When there is an open circuit on MIL circuit, the ECM c
annot warn the driver by lighting up MIL when there is
malfunction on engine control system.
Therefore, when electrical controlled throttle and part of ECM related diagnoses are continuously detected as
NG for 5 trips, ECM warns the driver that engine cont rol system malfunctions and MIL circuit is open by means
of operating fail-safe function.
The fail-safe function also operates when above diagnos es except MIL circuit are detected and demands the
driver to repair the malfunction.
MIL Flashing Without DTC
When any SRT codes are not set, MIL may fl ash without DTC. For the details, refer to EC-633, "Emission-
related Diagnostic Information".
HOW TO SWITCH DIAGNOSTIC TEST MODE
NOTE:
It is better to count the ti me accurately with a clock.
It is impossible to switch the di agnostic mode when an accelerator pedal position sensor circuit has
a malfunction.
Always ECM returns to Diagnostic Test Mode I after ignition switch is turned OFF.
How to Set Diagnostic Test Mode II (Self-diagnostic Results)
1. Confirm that accelerator pedal is fully released, turn ignition switch ON and wait 3 seconds.
2. Repeat the following procedure quickly five times within 5 seconds.
a. Fully depress the accelerator pedal.
b. Fully release the accelerator pedal.
3. Wait 7 seconds, fully depress the accelerator pedal and keep it for approx. 10 seconds until the MIL starts
blinking.
NOTE:
Diagnostic Test
Mode KEY and ENG.
Status Function Explanation of Function
Mode I Ignition switch in ON position
Engine stopped BULB CHECK This function checks the MIL bulb for damage (blown, open
circuit, etc.).
If the MIL does not come on, check MIL circuit.
Engine running MALFUNCTION WARNING This is a usual driving condition. When a malfunction is de-
tected twice in two consecutive driving cycles (two trip de-
tection logic), the MIL will light up to inform the driver that a
malfunction has been detected.
The following malfunctions will light up or blink the MIL in
the 1st trip.
Misfire (Possible three way catalyst damage)
One trip detection diagnoses
Mode II Ignition switch in ON position
Engine stopped SELF-DIAGNOSTIC
RESULTS
This function allows DTCs an
d 1st trip DTCs to be read.
Engine operating condition in fail-safe mode Engine speed will not rise more than 2,500 rpm due to the fuel cut
3AA93ABC3ACD3AC03ACA3AC03AC63AC53A913A773A893A873A873A8E3A773A983AC73AC93AC03AC3
3A893A873A873A8F3A773A9D3AAF3A8A3A8C3A863A9D3AAF3A8B3A8C
Page 2221 of 3924
![INFINITI FX35 2008 Service Manual
DTC P0456 EVAP CONTROL SYSTEMEC-981
< SERVICE INFORMATION > [VK45DE]
C
D
E
F
G H
I
J
K L
M A
EC
NP
O
2. Set the pressure pump and a hose.
3. Also set a vacuum gauge via 3-way connector and a hose.
4. INFINITI FX35 2008 Service Manual
DTC P0456 EVAP CONTROL SYSTEMEC-981
< SERVICE INFORMATION > [VK45DE]
C
D
E
F
G H
I
J
K L
M A
EC
NP
O
2. Set the pressure pump and a hose.
3. Also set a vacuum gauge via 3-way connector and a hose.
4.](/img/42/57017/w960_57017-2220.png)
DTC P0456 EVAP CONTROL SYSTEMEC-981
< SERVICE INFORMATION > [VK45DE]
C
D
E
F
G H
I
J
K L
M A
EC
NP
O
2. Set the pressure pump and a hose.
3. Also set a vacuum gauge via 3-way connector and a hose.
4. Turn ignition switch ON.
5. Connect GST and select “Service $08”.
6. Using “Service $08” control the EV
AP canister vent control valve
(close).
7. Apply pressure and make sure the following conditions are sat- isfied.
Pressure to be applied: 2.7 kPa (20 mmHg, 0.79 inHg)
Time to be waited after the pressure drawn in to the EVAP
system and the pressure to be dropped: 60 seconds and
the pressure should not be dropped more than 0.4 kPa (3 mmHg, 0.12 inHg).
If NG, go to EC-981, "
Diagnosis Procedure".
If OK, go to next step.
8. Disconnect GST.
9. Start engine and warm it up to normal operating temperature.
10. Turn ignition switch OFF and wait at least 10 seconds.
11. Restart engine and let it idle for 90 seconds.
12. Keep engine speed at 2,000 rpm for 30 seconds.
13. Turn ignition switch OFF. NOTE:
For more information, refer to GST instruction manual.
Diagnosis ProcedureINFOID:0000000001326822
1.CHECK FUEL FILLER CAP DESIGN
1. Turn ignition switch OFF.
2. Check for genuine NISSAN fuel filler cap design.
OK or NG
OK >> GO TO 2.
NG >> Replace with genuine NISSAN fuel filler cap.
2.CHECK FUEL FILLER CAP INSTALLATION
Check that the cap is tightened properly by rotating the cap clockwise.
OK or NG
OK >> GO TO 3.
NG >> 1. Open fuel filler cap, then clean cap and fuel filler neck threads using air blower. 2. Retighten until ratcheting sound is heard.
3.CHECK FUEL FILLER CAP FUNCTION
Check for air releasing sound while opening the fuel filler cap.
OK or NG
OK >> GO TO 5.
NG >> GO TO 4.
4.CHECK FUEL TANK VACUUM RELIEF VALVE
Refer to EC-620, "
Component Inspection".
OK or NG
OK >> GO TO 5.
SEF462UI
SEF915U
3AA93ABC3ACD3AC03ACA3AC03AC63AC53A913A773A893A873A873A8E3A773A983AC73AC93AC03AC3
3A893A873A873A8F3A773A9D3AAF3A8A3A8C3A863A9D3AAF3A8B3A8C
Page 2539 of 3924
![INFINITI FX35 2008 Service Manual
FRONT TIMING CHAIN CASEEM-55
< SERVICE INFORMATION > [VQ35DE]
C
D
E
F
G H
I
J
K L
M A
EM
NP
O
16. Remove collared O-ring from front timing chain case (left and
right side).
17. Remove rocker covers ( INFINITI FX35 2008 Service Manual
FRONT TIMING CHAIN CASEEM-55
< SERVICE INFORMATION > [VQ35DE]
C
D
E
F
G H
I
J
K L
M A
EM
NP
O
16. Remove collared O-ring from front timing chain case (left and
right side).
17. Remove rocker covers (](/img/42/57017/w960_57017-2538.png)
FRONT TIMING CHAIN CASEEM-55
< SERVICE INFORMATION > [VQ35DE]
C
D
E
F
G H
I
J
K L
M A
EM
NP
O
16. Remove collared O-ring from front timing chain case (left and
right side).
17. Remove rocker covers (right and left banks). Refer to EM-51, "
Component".
NOTE:
When only timing chain (primary) is removed, rocker cover does not need to be removed.
18. Obtain No. 1 cylinder at TDC of its compression stroke as follows: NOTE:
When timing chain is not removed/installed, this step is not required.
a. Rotate crankshaft pulley clockwise to align timing mark (grooved line without color) with timing indicator.
b. Make sure that intake and exhaust cam noses on No. 1 cylinder (engine front side of right bank) are located as shown in the fig-
ure.
If not, turn crankshaft one revolution (360 degrees) and alignas shown in the figure.
NOTE:
When only timing chain (primary) is removed, rocker cover does
not need to be removed. To make sure that No. 1 cylinder is at
its compression TDC, remove front timing chain case first. Then
check mating marks on camshaft sprockets. Refer to EM-65,
"Removal and Installation".
19. Remove crankshaft pulley as follows:
a. Remove rear cover plate (2WD models) or star ter motor (AWD models) and set ring gear stopper (SST).
Refer to EM-30, "
Component (2WD Models)" (2WD models) or SC-8, "System Description" (AWD mod-
els).
b. Loosen crankshaft pulley bolt and locate bolt seating surface as 10 mm (0.39 in) from its original position.
CAUTION:
Do not remove crankshaft pulley bolt as it will be used as a
supporting point for suitable puller.
PBIC2631E
KBIA1717J
SEM418G
PBIC1103E
3AA93ABC3ACD3AC03ACA3AC03AC63AC53A913A773A893A873A873A8E3A773A983AC73AC93AC03AC3
3A893A873A873A8F3A773A9D3AAF3A8A3A8C3A863A9D3AAF3A8B3A8C