wheel INFINITI M35 2007 Factory Service Manual
[x] Cancel search | Manufacturer: INFINITI, Model Year: 2007, Model line: M35, Model: INFINITI M35 2007Pages: 4647, PDF Size: 93.69 MB
Page 4037 of 4647
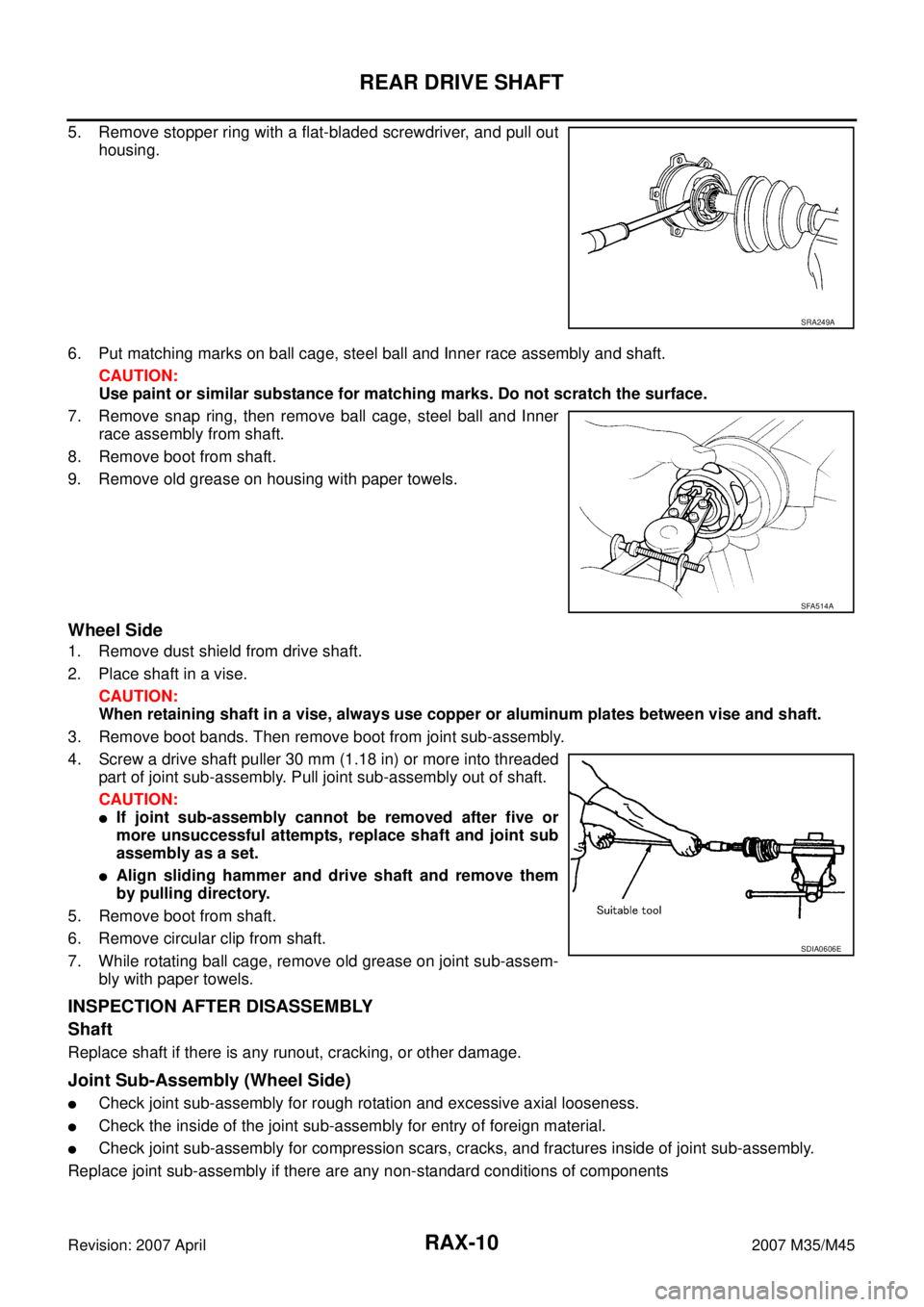
RAX-10
REAR DRIVE SHAFT
Revision: 2007 April2007 M35/M45
5. Remove stopper ring with a flat-bladed screwdriver, and pull out
housing.
6. Put matching marks on ball cage, steel ball and Inner race assembly and shaft.
CAUTION:
Use paint or similar substance for matching marks. Do not scratch the surface.
7. Remove snap ring, then remove ball cage, steel ball and Inner
race assembly from shaft.
8. Remove boot from shaft.
9. Remove old grease on housing with paper towels.
Wheel Side
1. Remove dust shield from drive shaft.
2. Place shaft in a vise.
CAUTION:
When retaining shaft in a vise, always use copper or aluminum plates between vise and shaft.
3. Remove boot bands. Then remove boot from joint sub-assembly.
4. Screw a drive shaft puller 30 mm (1.18 in) or more into threaded
part of joint sub-assembly. Pull joint sub-assembly out of shaft.
CAUTION:
If joint sub-assembly cannot be removed after five or
more unsuccessful attempts, replace shaft and joint sub
assembly as a set.
Align sliding hammer and drive shaft and remove them
by pulling directory.
5. Remove boot from shaft.
6. Remove circular clip from shaft.
7. While rotating ball cage, remove old grease on joint sub-assem-
bly with paper towels.
INSPECTION AFTER DISASSEMBLY
Shaft
Replace shaft if there is any runout, cracking, or other damage.
Joint Sub-Assembly (Wheel Side)
Check joint sub-assembly for rough rotation and excessive axial looseness.
Check the inside of the joint sub-assembly for entry of foreign material.
Check joint sub-assembly for compression scars, cracks, and fractures inside of joint sub-assembly.
Replace joint sub-assembly if there are any non-standard conditions of components
SRA249A
SFA514A
SDIA0606E
Page 4039 of 4647
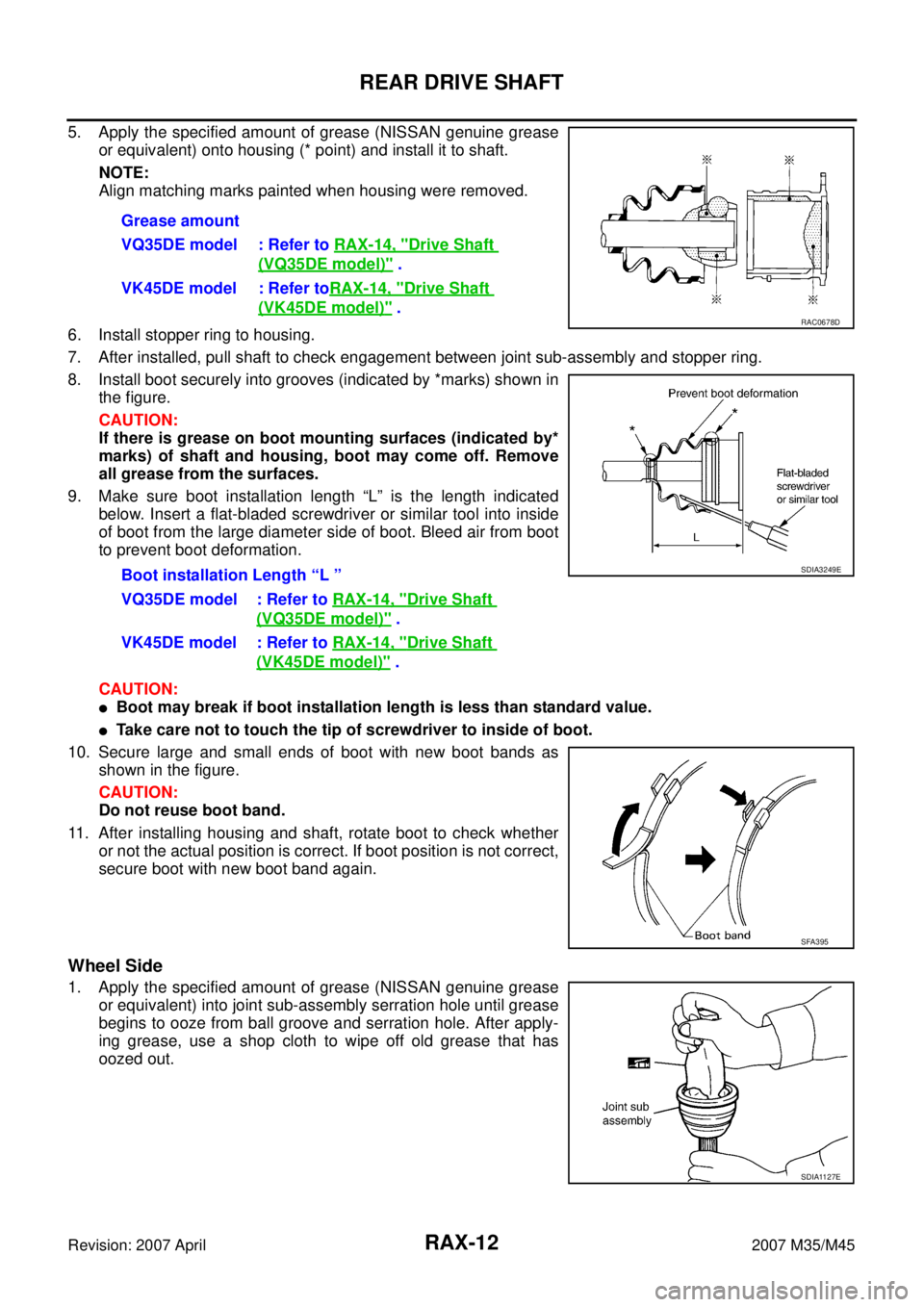
RAX-12
REAR DRIVE SHAFT
Revision: 2007 April2007 M35/M45
5. Apply the specified amount of grease (NISSAN genuine grease
or equivalent) onto housing (* point) and install it to shaft.
NOTE:
Align matching marks painted when housing were removed.
6. Install stopper ring to housing.
7. After installed, pull shaft to check engagement between joint sub-assembly and stopper ring.
8. Install boot securely into grooves (indicated by *marks) shown in
the figure.
CAUTION:
If there is grease on boot mounting surfaces (indicated by*
marks) of shaft and housing, boot may come off. Remove
all grease from the surfaces.
9. Make sure boot installation length “L” is the length indicated
below. Insert a flat-bladed screwdriver or similar tool into inside
of boot from the large diameter side of boot. Bleed air from boot
to prevent boot deformation.
CAUTION:
Boot may break if boot installation length is less than standard value.
Take care not to touch the tip of screwdriver to inside of boot.
10. Secure large and small ends of boot with new boot bands as
shown in the figure.
CAUTION:
Do not reuse boot band.
11. After installing housing and shaft, rotate boot to check whether
or not the actual position is correct. If boot position is not correct,
secure boot with new boot band again.
Wheel Side
1. Apply the specified amount of grease (NISSAN genuine grease
or equivalent) into joint sub-assembly serration hole until grease
begins to ooze from ball groove and serration hole. After apply-
ing grease, use a shop cloth to wipe off old grease that has
oozed out.Grease amount
VQ35DE model : Refer to RAX-14, "
Drive Shaft
(VQ35DE model)" .
VK45DE model : Refer toRAX-14, "
Drive Shaft
(VK45DE model)" .
Boot installation Length “L ”
VQ35DE model : Refer to RAX-14, "
Drive Shaft
(VQ35DE model)" .
VK45DE model : Refer to RAX-14, "
Drive Shaft
(VK45DE model)" .
RAC0678D
SDIA3249E
SFA395
SDIA1127E
Page 4041 of 4647
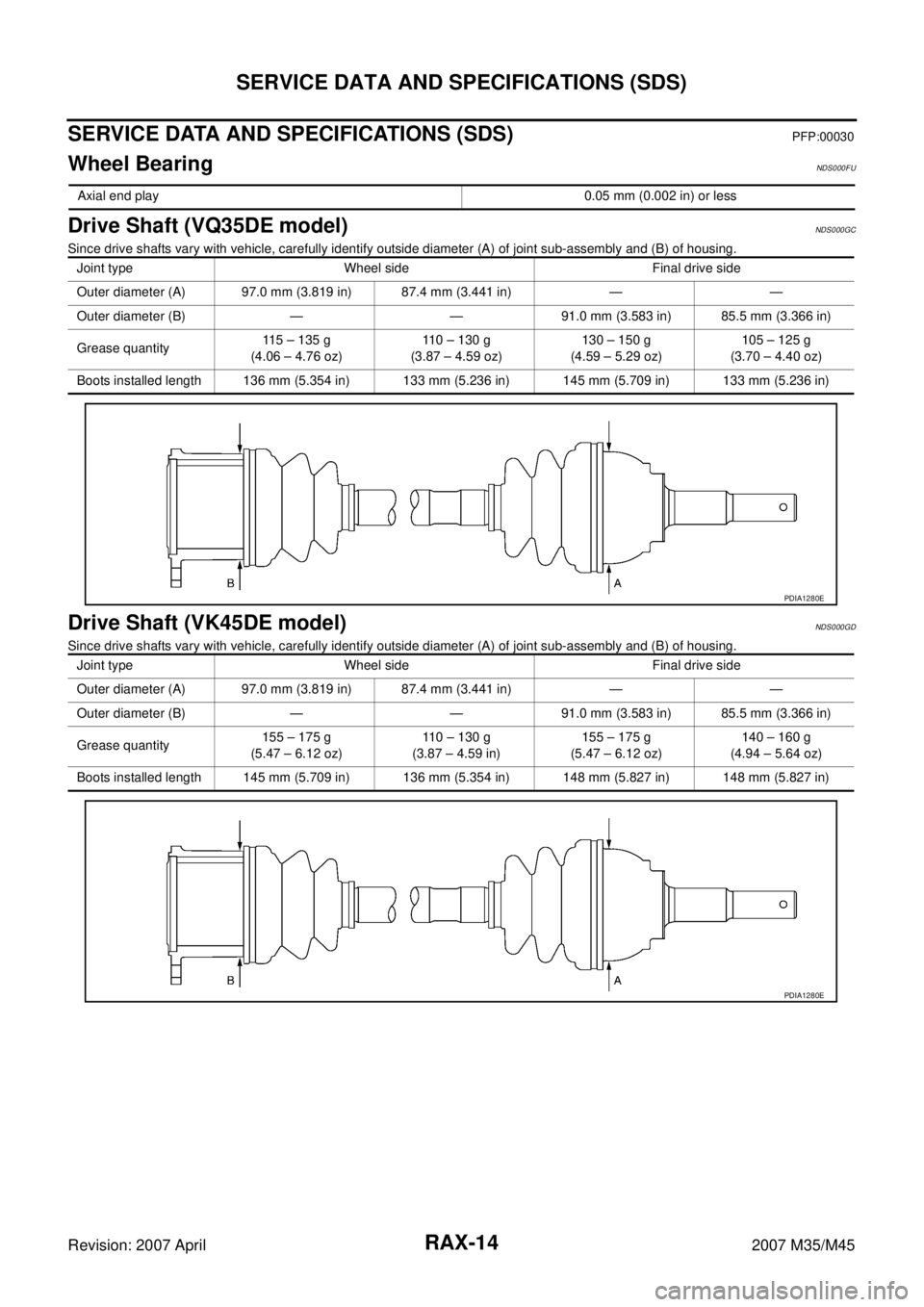
RAX-14
SERVICE DATA AND SPECIFICATIONS (SDS)
Revision: 2007 April2007 M35/M45
SERVICE DATA AND SPECIFICATIONS (SDS)PFP:00030
Wheel BearingNDS000FU
Drive Shaft (VQ35DE model)NDS000GC
Since drive shafts vary with vehicle, carefully identify outside diameter (A) of joint sub-assembly and (B) of housing.
Drive Shaft (VK45DE model)NDS000GD
Since drive shafts vary with vehicle, carefully identify outside diameter (A) of joint sub-assembly and (B) of housing.Axial end play0.05 mm (0.002 in) or less
Joint type Wheel side Final drive side
Outer diameter (A) 97.0 mm (3.819 in) 87.4 mm (3.441 in) — —
Outer diameter (B) — — 91.0 mm (3.583 in) 85.5 mm (3.366 in)
Grease quantity115 – 135 g
(4.06 – 4.76 oz)110 – 130 g
(3.87 – 4.59 oz)130 – 150 g
(4.59 – 5.29 oz)105 – 125 g
(3.70 – 4.40 oz)
Boots installed length 136 mm (5.354 in) 133 mm (5.236 in) 145 mm (5.709 in) 133 mm (5.236 in)
PDIA1280E
Joint type Wheel side Final drive side
Outer diameter (A) 97.0 mm (3.819 in) 87.4 mm (3.441 in) — —
Outer diameter (B) — — 91.0 mm (3.583 in) 85.5 mm (3.366 in)
Grease quantity155 – 175 g
(5.47 – 6.12 oz)110 – 130 g
(3.87 – 4.59 in)155 – 175 g
(5.47 – 6.12 oz)140 – 160 g
(4.94 – 5.64 oz)
Boots installed length 145 mm (5.709 in) 136 mm (5.354 in) 148 mm (5.827 in) 148 mm (5.827 in)
PDIA1280E
Page 4076 of 4647
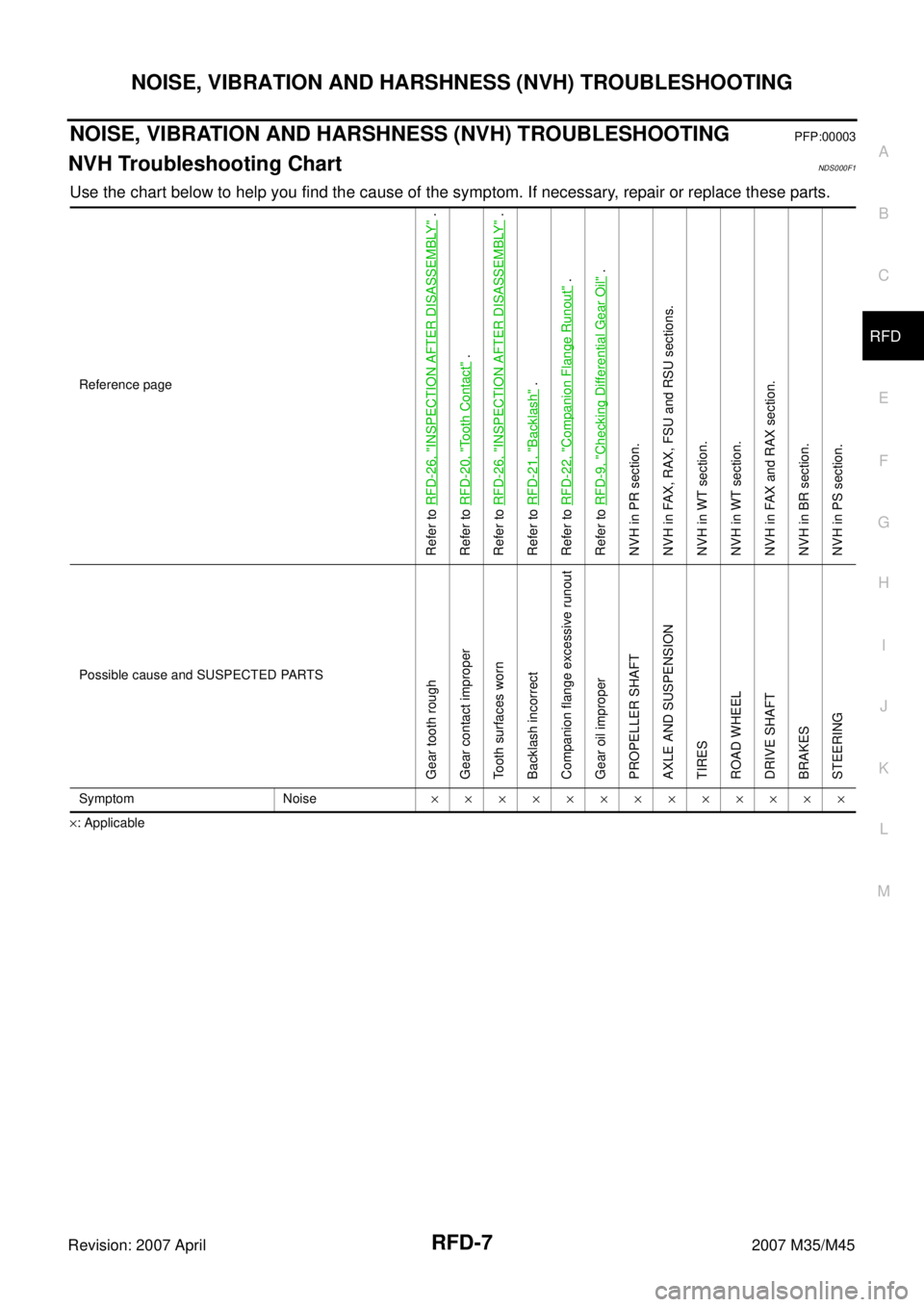
NOISE, VIBRATION AND HARSHNESS (NVH) TROUBLESHOOTING
RFD-7
C
E
F
G
H
I
J
K
L
MA
B
RFD
Revision: 2007 April2007 M35/M45
NOISE, VIBRATION AND HARSHNESS (NVH) TROUBLESHOOTINGPFP:00003
NVH Troubleshooting ChartNDS000F1
Use the chart below to help you find the cause of the symptom. If necessary, repair or replace these parts.
×: ApplicableReference page
Refer to RFD-26, "
INSPECTION AFTER DISASSEMBLY
" .
Refer to RFD-20, "
Tooth Contact
" .
Refer to RFD-26, "
INSPECTION AFTER DISASSEMBLY
" .
Refer to RFD-21, "
Backlash
" .
Refer to RFD-22, "
Companion Flange Runout
" .
Refer to RFD-9, "
Checking Differential Gear Oil
" .
NVH in PR section.
NVH in FAX, RAX, FSU and RSU sections.
NVH in WT section.
NVH in WT section.
NVH in FAX and RAX section.
NVH in BR section.
NVH in PS section.
Possible cause and SUSPECTED PARTS
Gear tooth rough
Gear contact improper
Tooth surfaces worn
Backlash incorrect
Companion flange excessive runout
Gear oil improper
PROPELLER SHAFT
AXLE AND SUSPENSION
TIRES
ROAD WHEEL
DRIVE SHAFT
BRAKES
STEERING
Symptom Noise×××××××××××××
Page 4079 of 4647
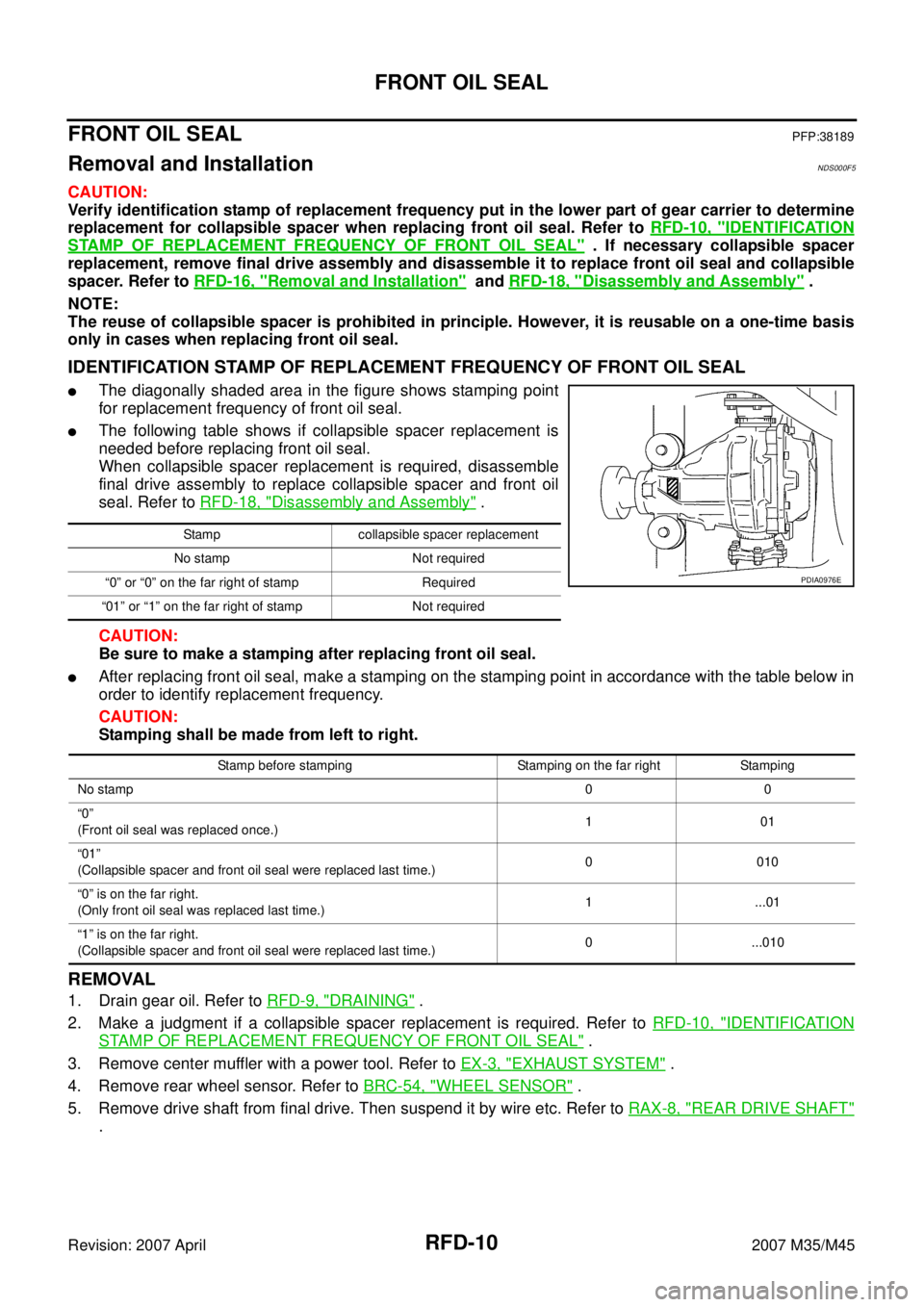
RFD-10
FRONT OIL SEAL
Revision: 2007 April2007 M35/M45
FRONT OIL SEALPFP:38189
Removal and InstallationNDS000F5
CAUTION:
Verify identification stamp of replacement frequency put in the lower part of gear carrier to determine
replacement for collapsible spacer when replacing front oil seal. Refer to RFD-10, "
IDENTIFICATION
STAMP OF REPLACEMENT FREQUENCY OF FRONT OIL SEAL" . If necessary collapsible spacer
replacement, remove final drive assembly and disassemble it to replace front oil seal and collapsible
spacer. Refer to RFD-16, "
Removal and Installation" and RFD-18, "Disassembly and Assembly" .
NOTE:
The reuse of collapsible spacer is prohibited in principle. However, it is reusable on a one-time basis
only in cases when replacing front oil seal.
IDENTIFICATION STAMP OF REPLACEMENT FREQUENCY OF FRONT OIL SEAL
The diagonally shaded area in the figure shows stamping point
for replacement frequency of front oil seal.
The following table shows if collapsible spacer replacement is
needed before replacing front oil seal.
When collapsible spacer replacement is required, disassemble
final drive assembly to replace collapsible spacer and front oil
seal. Refer to RFD-18, "
Disassembly and Assembly" .
CAUTION:
Be sure to make a stamping after replacing front oil seal.
After replacing front oil seal, make a stamping on the stamping point in accordance with the table below in
order to identify replacement frequency.
CAUTION:
Stamping shall be made from left to right.
REMOVAL
1. Drain gear oil. Refer to RFD-9, "DRAINING" .
2. Make a judgment if a collapsible spacer replacement is required. Refer to RFD-10, "
IDENTIFICATION
STAMP OF REPLACEMENT FREQUENCY OF FRONT OIL SEAL" .
3. Remove center muffler with a power tool. Refer to EX-3, "
EXHAUST SYSTEM" .
4. Remove rear wheel sensor. Refer to BRC-54, "
WHEEL SENSOR" .
5. Remove drive shaft from final drive. Then suspend it by wire etc. Refer to RAX-8, "
REAR DRIVE SHAFT"
.
Stamp collapsible spacer replacement
No stamp Not required
“0” or “0” on the far right of stamp Required
“01” or “1” on the far right of stamp Not required
PDIA0976E
Stamp before stamping Stamping on the far right Stamping
No stamp00
“0”
(Front oil seal was replaced once.)101
“01”
(Collapsible spacer and front oil seal were replaced last time.)0 010
“0” is on the far right.
(Only front oil seal was replaced last time.)1...01
“1” is on the far right.
(Collapsible spacer and front oil seal were replaced last time.)0 ...010
Page 4082 of 4647
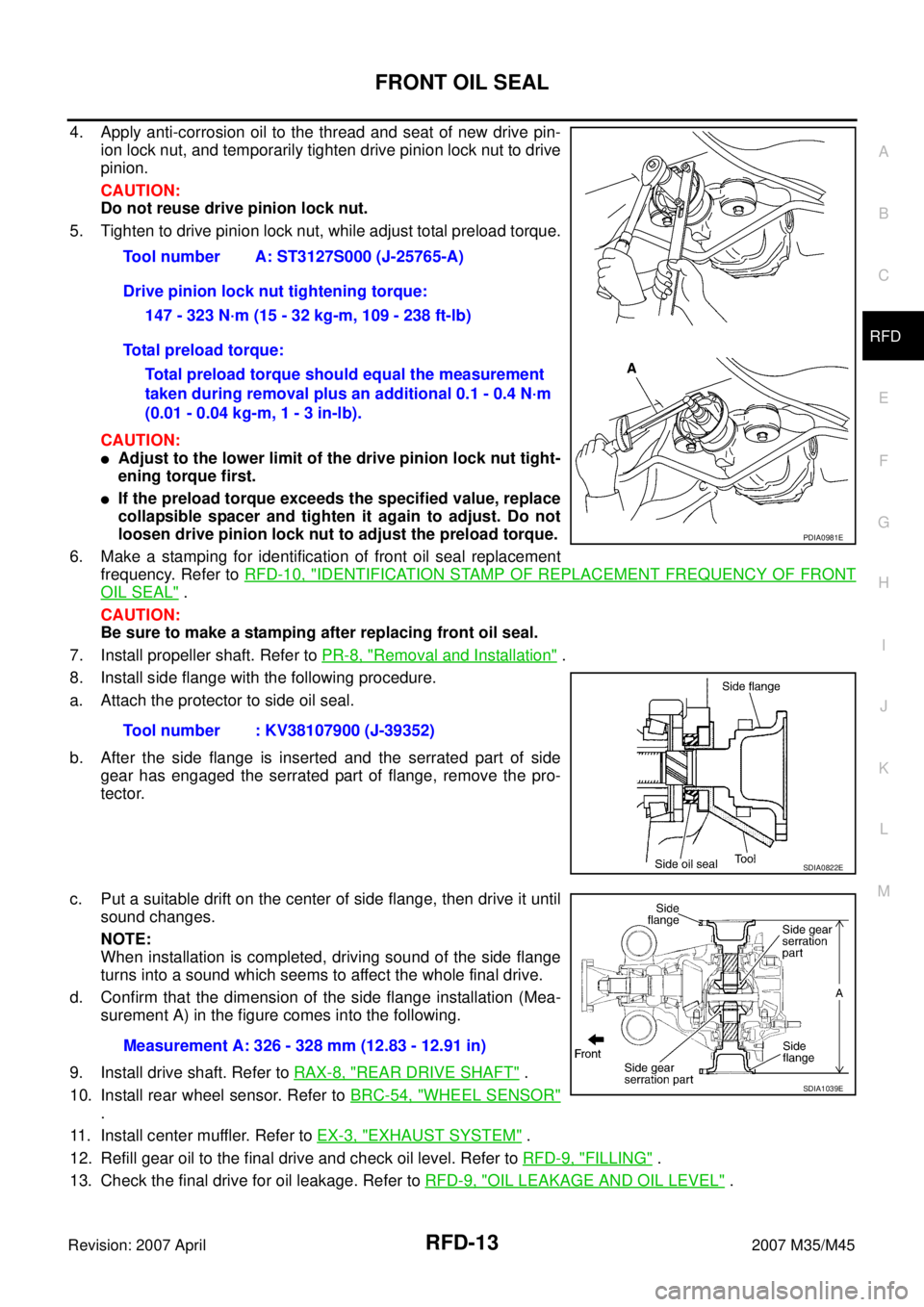
FRONT OIL SEAL
RFD-13
C
E
F
G
H
I
J
K
L
MA
B
RFD
Revision: 2007 April2007 M35/M45
4. Apply anti-corrosion oil to the thread and seat of new drive pin-
ion lock nut, and temporarily tighten drive pinion lock nut to drive
pinion.
CAUTION:
Do not reuse drive pinion lock nut.
5. Tighten to drive pinion lock nut, while adjust total preload torque.
CAUTION:
Adjust to the lower limit of the drive pinion lock nut tight-
ening torque first.
If the preload torque exceeds the specified value, replace
collapsible spacer and tighten it again to adjust. Do not
loosen drive pinion lock nut to adjust the preload torque.
6. Make a stamping for identification of front oil seal replacement
frequency. Refer to RFD-10, "
IDENTIFICATION STAMP OF REPLACEMENT FREQUENCY OF FRONT
OIL SEAL" .
CAUTION:
Be sure to make a stamping after replacing front oil seal.
7. Install propeller shaft. Refer to PR-8, "
Removal and Installation" .
8. Install side flange with the following procedure.
a. Attach the protector to side oil seal.
b. After the side flange is inserted and the serrated part of side
gear has engaged the serrated part of flange, remove the pro-
tector.
c. Put a suitable drift on the center of side flange, then drive it until
sound changes.
NOTE:
When installation is completed, driving sound of the side flange
turns into a sound which seems to affect the whole final drive.
d. Confirm that the dimension of the side flange installation (Mea-
surement A) in the figure comes into the following.
9. Install drive shaft. Refer to RAX-8, "
REAR DRIVE SHAFT" .
10. Install rear wheel sensor. Refer to BRC-54, "
WHEEL SENSOR"
.
11. Install center muffler. Refer to EX-3, "
EXHAUST SYSTEM" .
12. Refill gear oil to the final drive and check oil level. Refer to RFD-9, "
FILLING" .
13. Check the final drive for oil leakage. Refer to RFD-9, "
OIL LEAKAGE AND OIL LEVEL" . Tool number A: ST3127S000 (J-25765-A)
Drive pinion lock nut tightening torque:
147 - 323 N·m (15 - 32 kg-m, 109 - 238 ft-lb)
Total preload torque:
Total preload torque should equal the measurement
taken during removal plus an additional 0.1 - 0.4 N·m
(0.01 - 0.04 kg-m, 1 - 3 in-lb).
Tool number : KV38107900 (J-39352)
PDIA0981E
SDIA0822E
Measurement A: 326 - 328 mm (12.83 - 12.91 in)
SDIA1039E
Page 4083 of 4647
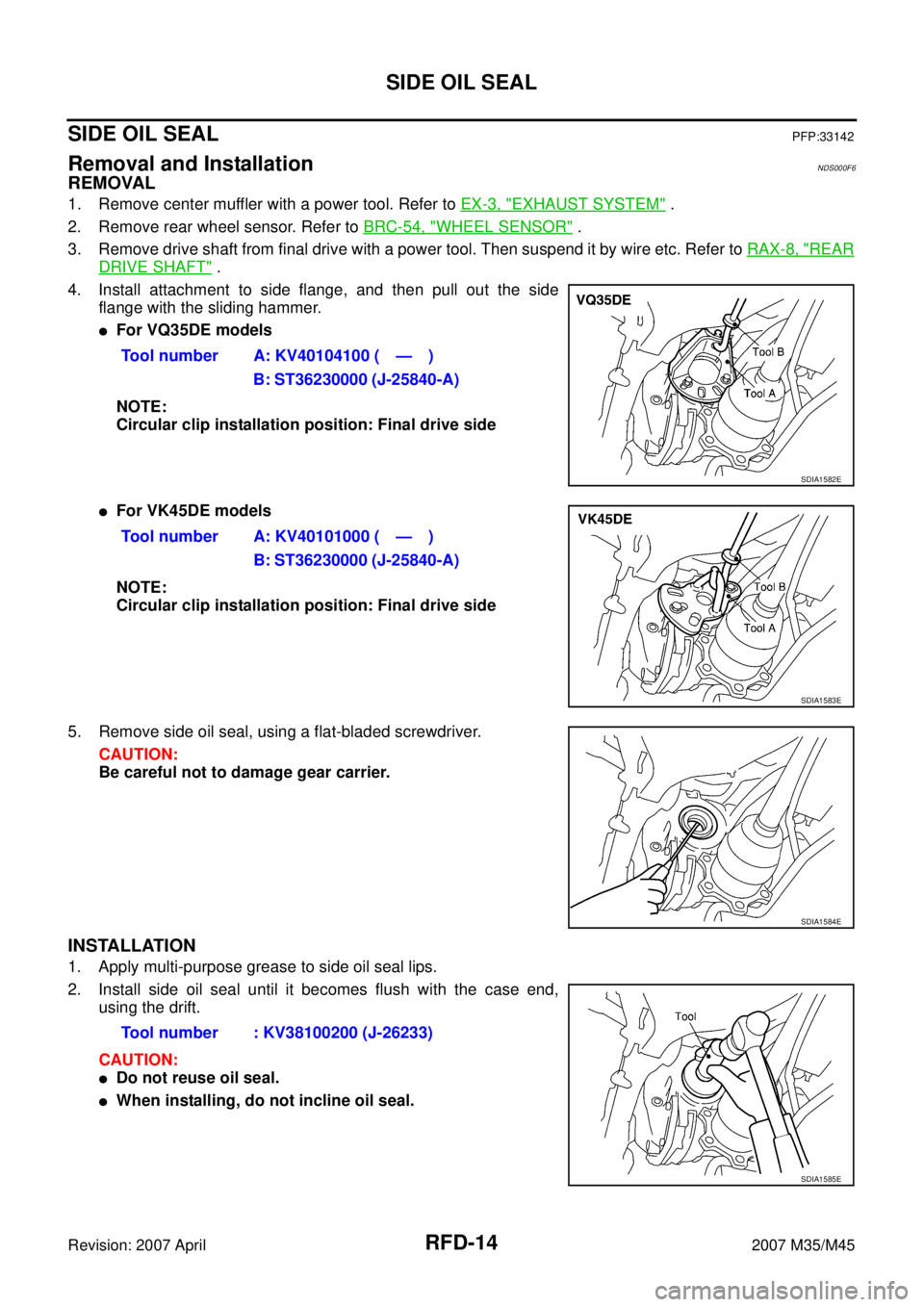
RFD-14
SIDE OIL SEAL
Revision: 2007 April2007 M35/M45
SIDE OIL SEALPFP:33142
Removal and InstallationNDS000F6
REMOVAL
1. Remove center muffler with a power tool. Refer to EX-3, "EXHAUST SYSTEM" .
2. Remove rear wheel sensor. Refer to BRC-54, "
WHEEL SENSOR" .
3. Remove drive shaft from final drive with a power tool. Then suspend it by wire etc. Refer to RAX-8, "
REAR
DRIVE SHAFT" .
4. Install attachment to side flange, and then pull out the side
flange with the sliding hammer.
For VQ35DE models
NOTE:
Circular clip installation position: Final drive side
For VK45DE models
NOTE:
Circular clip installation position: Final drive side
5. Remove side oil seal, using a flat-bladed screwdriver.
CAUTION:
Be careful not to damage gear carrier.
INSTALLATION
1. Apply multi-purpose grease to side oil seal lips.
2. Install side oil seal until it becomes flush with the case end,
using the drift.
CAUTION:
Do not reuse oil seal.
When installing, do not incline oil seal.Tool number A: KV40104100 ( — )
B: ST36230000 (J-25840-A)
SDIA1582E
Tool number A: KV40101000 ( — )
B: ST36230000 (J-25840-A)
SDIA1583E
SDIA1584E
Tool number : KV38100200 (J-26233)
SDIA1585E
Page 4084 of 4647
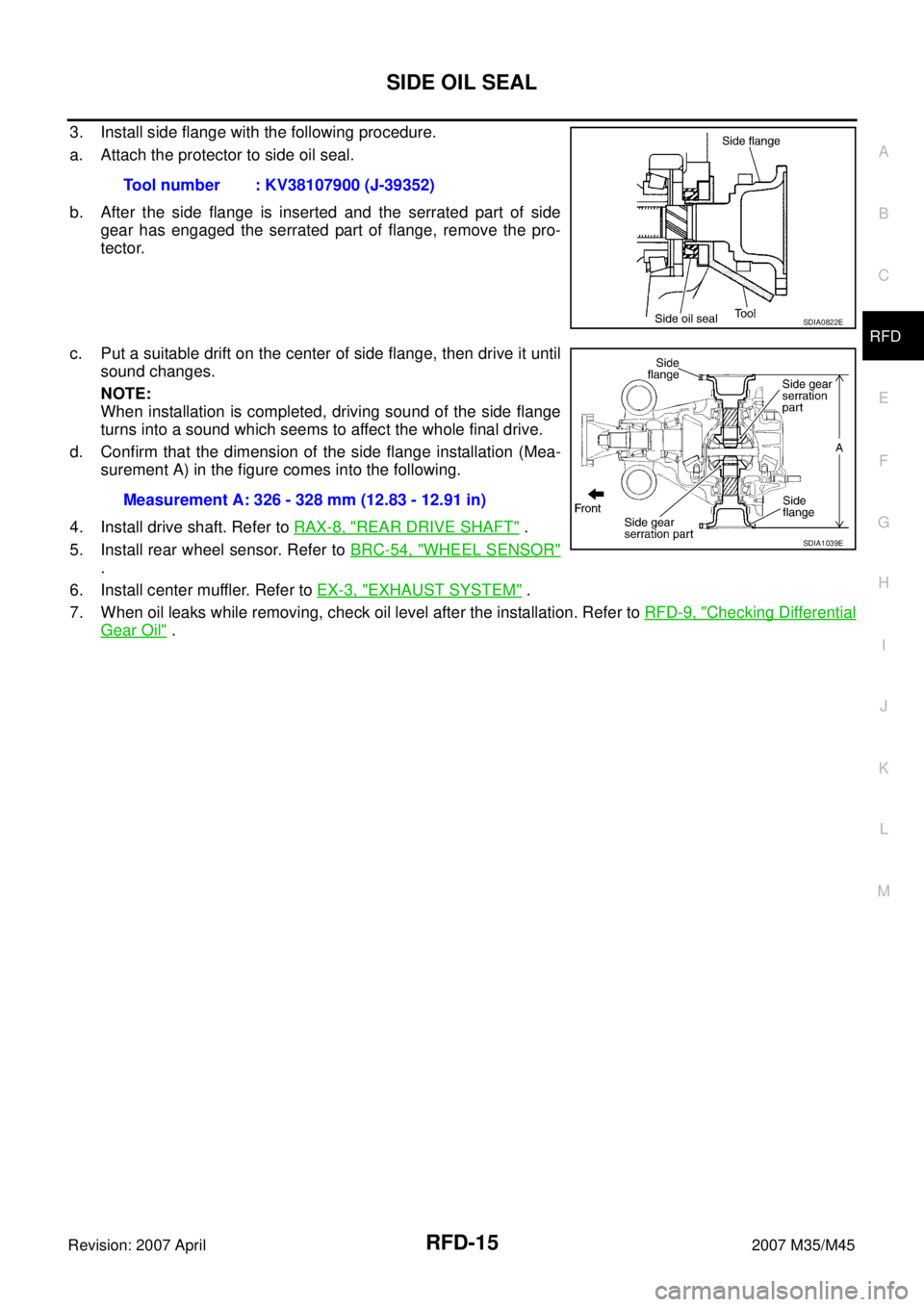
SIDE OIL SEAL
RFD-15
C
E
F
G
H
I
J
K
L
MA
B
RFD
Revision: 2007 April2007 M35/M45
3. Install side flange with the following procedure.
a. Attach the protector to side oil seal.
b. After the side flange is inserted and the serrated part of side
gear has engaged the serrated part of flange, remove the pro-
tector.
c. Put a suitable drift on the center of side flange, then drive it until
sound changes.
NOTE:
When installation is completed, driving sound of the side flange
turns into a sound which seems to affect the whole final drive.
d. Confirm that the dimension of the side flange installation (Mea-
surement A) in the figure comes into the following.
4. Install drive shaft. Refer to RAX-8, "
REAR DRIVE SHAFT" .
5. Install rear wheel sensor. Refer to BRC-54, "
WHEEL SENSOR"
.
6. Install center muffler. Refer to EX-3, "
EXHAUST SYSTEM" .
7. When oil leaks while removing, check oil level after the installation. Refer to RFD-9, "
Checking Differential
Gear Oil" . Tool number : KV38107900 (J-39352)
SDIA0822E
Measurement A: 326 - 328 mm (12.83 - 12.91 in)
SDIA1039E
Page 4085 of 4647
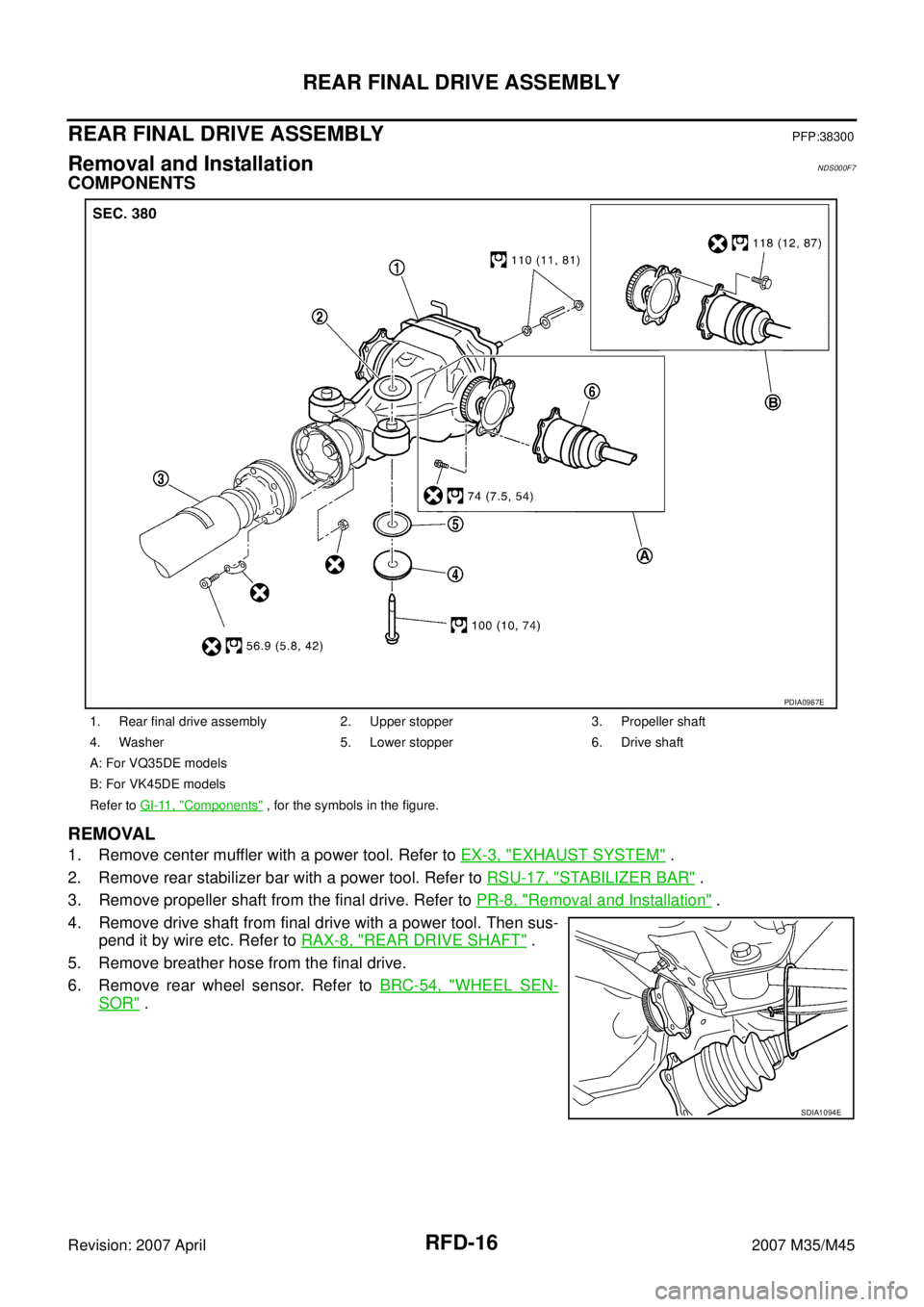
RFD-16
REAR FINAL DRIVE ASSEMBLY
Revision: 2007 April2007 M35/M45
REAR FINAL DRIVE ASSEMBLYPFP:38300
Removal and InstallationNDS000F7
COMPONENTS
REMOVAL
1. Remove center muffler with a power tool. Refer to EX-3, "EXHAUST SYSTEM" .
2. Remove rear stabilizer bar with a power tool. Refer to RSU-17, "
STABILIZER BAR" .
3. Remove propeller shaft from the final drive. Refer to PR-8, "
Removal and Installation" .
4. Remove drive shaft from final drive with a power tool. Then sus-
pend it by wire etc. Refer to RAX-8, "
REAR DRIVE SHAFT" .
5. Remove breather hose from the final drive.
6. Remove rear wheel sensor. Refer to BRC-54, "
WHEEL SEN-
SOR" .
1. Rear final drive assembly 2. Upper stopper 3. Propeller shaft
4. Washer 5. Lower stopper 6. Drive shaft
A: For VQ35DE models
B: For VK45DE models
Refer to GI-11, "
Components" , for the symbols in the figure.
PDIA0967E
SDIA1094E
Page 4108 of 4647
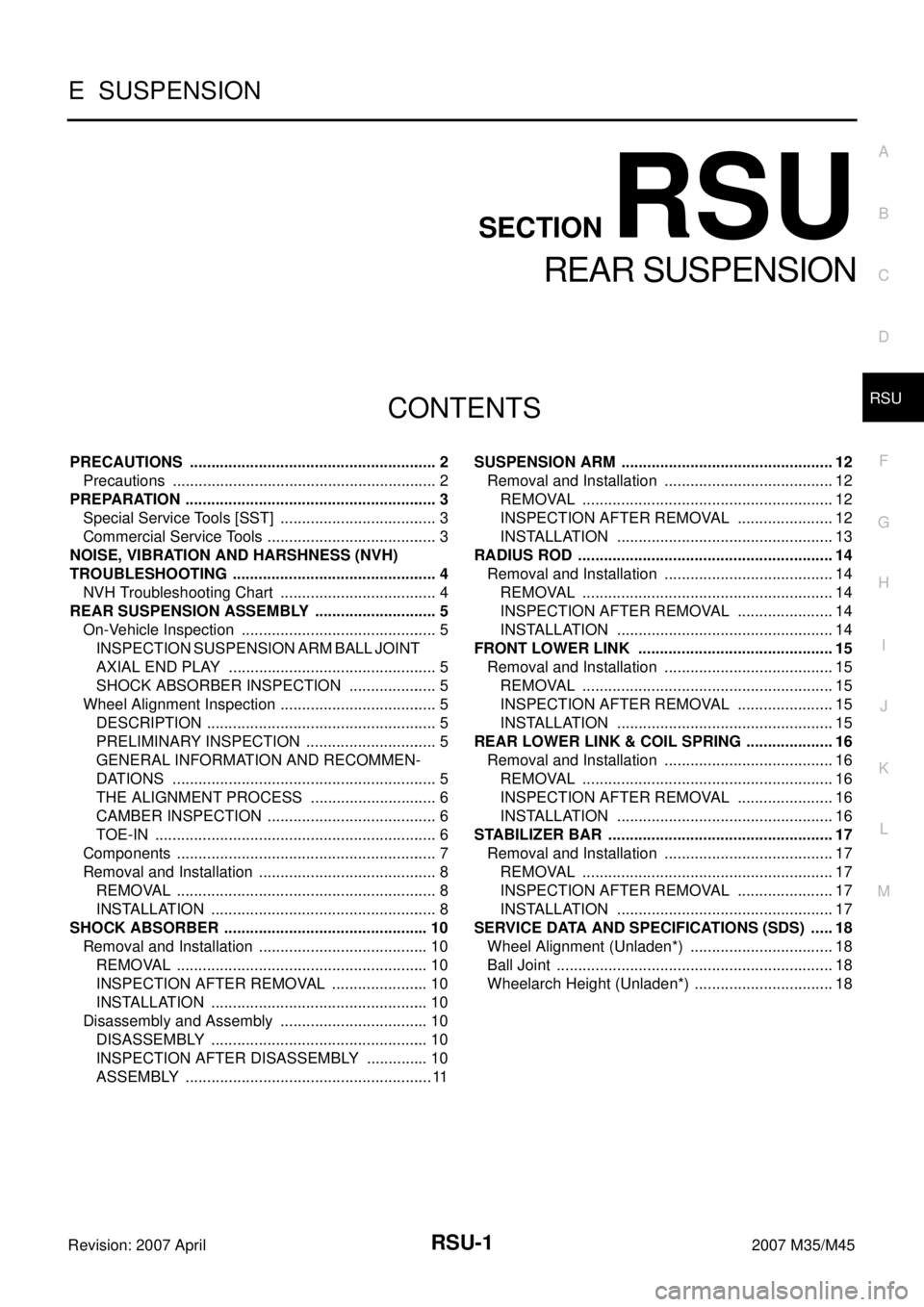
RSU-1
REAR SUSPENSION
E SUSPENSION
CONTENTS
C
D
F
G
H
I
J
K
L
M
SECTION RSU
A
B
RSU
Revision: 2007 April2007 M35/M45
REAR SUSPENSION
PRECAUTIONS .......................................................... 2
Precautions .............................................................. 2
PREPARATION ........................................................... 3
Special Service Tools [SST] ..................................... 3
Commercial Service Tools ........................................ 3
NOISE, VIBRATION AND HARSHNESS (NVH)
TROUBLESHOOTING ................................................ 4
NVH Troubleshooting Chart ..................................... 4
REAR SUSPENSION ASSEMBLY ............................. 5
On-Vehicle Inspection .............................................. 5
INSPECTION SUSPENSION ARM BALL JOINT
AXIAL END PLAY ................................................. 5
SHOCK ABSORBER INSPECTION ..................... 5
Wheel Alignment Inspection ..................................... 5
DESCRIPTION ...................................................... 5
PRELIMINARY INSPECTION ............................... 5
GENERAL INFORMATION AND RECOMMEN-
DATIONS .............................................................. 5
THE ALIGNMENT PROCESS .............................. 6
CAMBER INSPECTION ........................................ 6
TOE-IN .................................................................. 6
Components ............................................................. 7
Removal and Installation .......................................... 8
REMOVAL ............................................................. 8
INSTALLATION ..................................................... 8
SHOCK ABSORBER ................................................ 10
Removal and Installation ........................................ 10
REMOVAL ........................................................... 10
INSPECTION AFTER REMOVAL ....................... 10
INSTALLATION ................................................... 10
Disassembly and Assembly ................................... 10
DISASSEMBLY ................................................... 10
INSPECTION AFTER DISASSEMBLY ............... 10
ASSEMBLY .......................................................... 11SUSPENSION ARM .................................................. 12
Removal and Installation ........................................ 12
REMOVAL ........................................................... 12
INSPECTION AFTER REMOVAL ....................... 12
INSTALLATION ................................................... 13
RADIUS ROD ............................................................ 14
Removal and Installation ........................................ 14
REMOVAL ........................................................... 14
INSPECTION AFTER REMOVAL ....................... 14
INSTALLATION ................................................... 14
FRONT LOWER LINK .............................................. 15
Removal and Installation ........................................ 15
REMOVAL ........................................................... 15
INSPECTION AFTER REMOVAL ....................... 15
INSTALLATION ................................................... 15
REAR LOWER LINK & COIL SPRING ..................... 16
Removal and Installation ........................................ 16
REMOVAL ........................................................... 16
INSPECTION AFTER REMOVAL ....................... 16
INSTALLATION ................................................... 16
STABILIZER BAR ..................................................... 17
Removal and Installation ........................................ 17
REMOVAL ........................................................... 17
INSPECTION AFTER REMOVAL ....................... 17
INSTALLATION ................................................... 17
SERVICE DATA AND SPECIFICATIONS (SDS) ...... 18
Wheel Alignment (Unladen*) .................................. 18
Ball Joint ................................................................. 18
Wheelarch Height (Unladen*) ................................. 18