relay INFINITI QX4 2005 Factory Manual Online
[x] Cancel search | Manufacturer: INFINITI, Model Year: 2005, Model line: QX4, Model: INFINITI QX4 2005Pages: 3419, PDF Size: 80.18 MB
Page 1592 of 3419
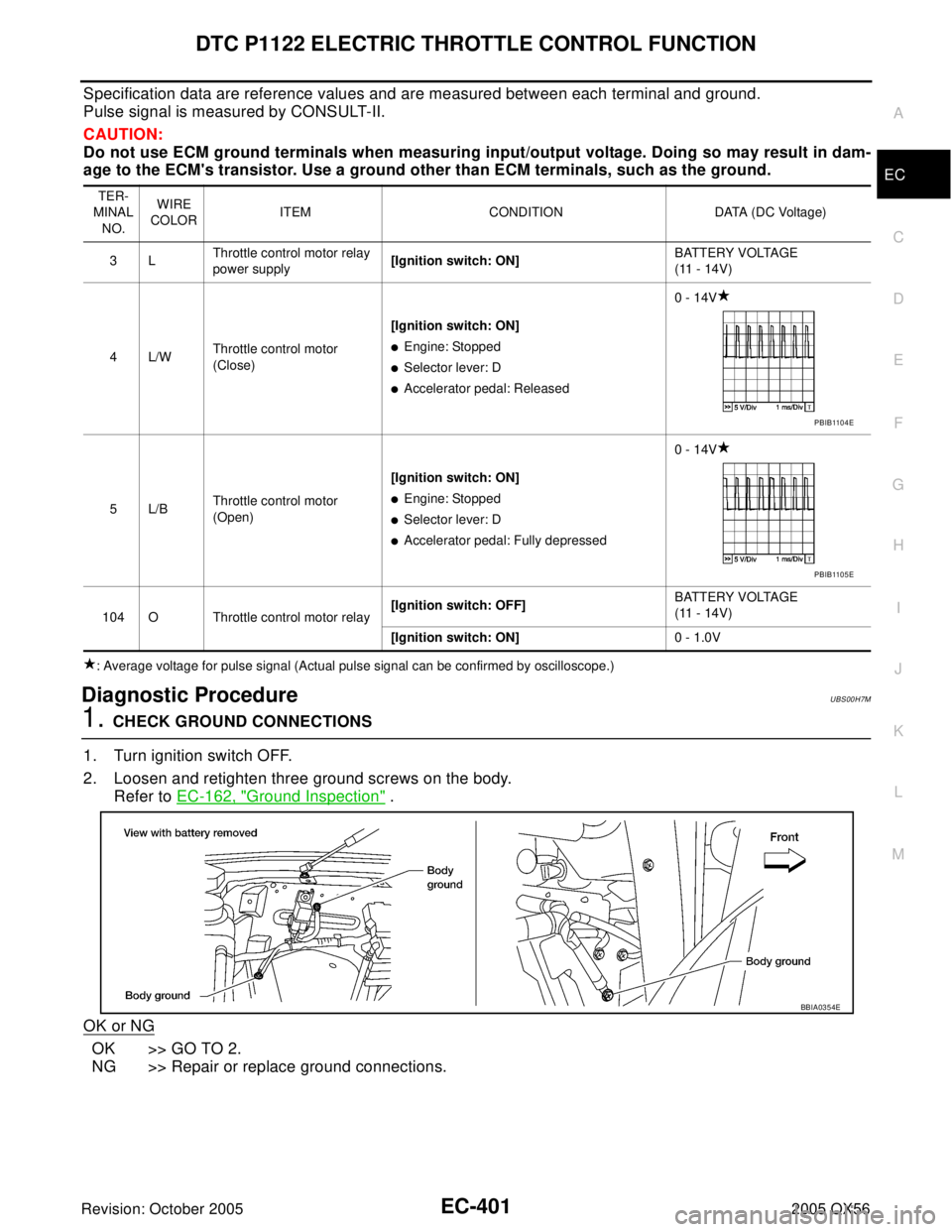
DTC P1122 ELECTRIC THROTTLE CONTROL FUNCTION
EC-401
C
D
E
F
G
H
I
J
K
L
MA
EC
Revision: October 20052005 QX56
Specification data are reference values and are measured between each terminal and ground.
Pulse signal is measured by CONSULT-II.
CAUTION:
Do not use ECM ground terminals when measuring input/output voltage. Doing so may result in dam-
age to the ECM's transistor. Use a ground other than ECM terminals, such as the ground.
: Average voltage for pulse signal (Actual pulse signal can be confirmed by oscilloscope.)
Diagnostic ProcedureUBS00H7M
1. CHECK GROUND CONNECTIONS
1. Turn ignition switch OFF.
2. Loosen and retighten three ground screws on the body.
Refer to EC-162, "
Ground Inspection" .
OK or NG
OK >> GO TO 2.
NG >> Repair or replace ground connections.
TER-
MINAL
NO.WIRE
COLORITEM CONDITION DATA (DC Voltage)
3LThrottle control motor relay
power supply[Ignition switch: ON]BATTERY VOLTAGE
(11 - 14V)
4L/WThrottle control motor
(Close)[Ignition switch: ON]
Engine: Stopped
Selector lever: D
Accelerator pedal: Released0 - 14V
5L/BThrottle control motor
(Open)[Ignition switch: ON]
Engine: Stopped
Selector lever: D
Accelerator pedal: Fully depressed0 - 14V
104 O Throttle control motor relay[Ignition switch: OFF]BATTERY VOLTAGE
(11 - 14V)
[Ignition switch: ON]0 - 1.0V
PBIB1104E
PBIB1105E
BBIA0354E
Page 1593 of 3419
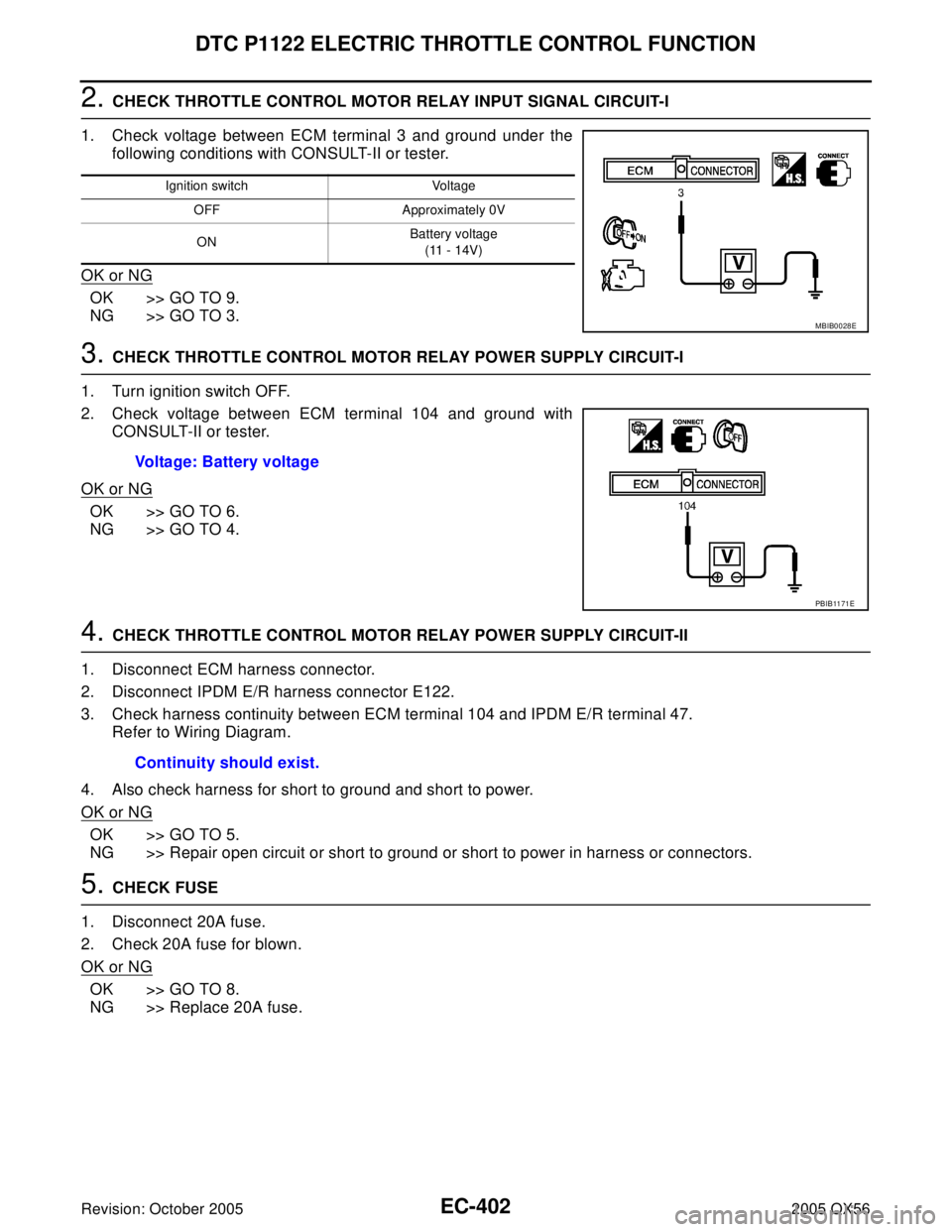
EC-402Revision: October 2005
DTC P1122 ELECTRIC THROTTLE CONTROL FUNCTION
2005 QX56
2. CHECK THROTTLE CONTROL MOTOR RELAY INPUT SIGNAL CIRCUIT-I
1. Check voltage between ECM terminal 3 and ground under the
following conditions with CONSULT-II or tester.
OK or NG
OK >> GO TO 9.
NG >> GO TO 3.
3. CHECK THROTTLE CONTROL MOTOR RELAY POWER SUPPLY CIRCUIT-I
1. Turn ignition switch OFF.
2. Check voltage between ECM terminal 104 and ground with
CONSULT-II or tester.
OK or NG
OK >> GO TO 6.
NG >> GO TO 4.
4. CHECK THROTTLE CONTROL MOTOR RELAY POWER SUPPLY CIRCUIT-II
1. Disconnect ECM harness connector.
2. Disconnect IPDM E/R harness connector E122.
3. Check harness continuity between ECM terminal 104 and IPDM E/R terminal 47.
Refer to Wiring Diagram.
4. Also check harness for short to ground and short to power.
OK or NG
OK >> GO TO 5.
NG >> Repair open circuit or short to ground or short to power in harness or connectors.
5. CHECK FUSE
1. Disconnect 20A fuse.
2. Check 20A fuse for blown.
OK or NG
OK >> GO TO 8.
NG >> Replace 20A fuse.
Ignition switch Voltage
OFF Approximately 0V
ONBattery voltage
(11 - 14V)
MBIB0028E
Voltage: Battery voltage
PBIB11 71 E
Continuity should exist.
Page 1594 of 3419
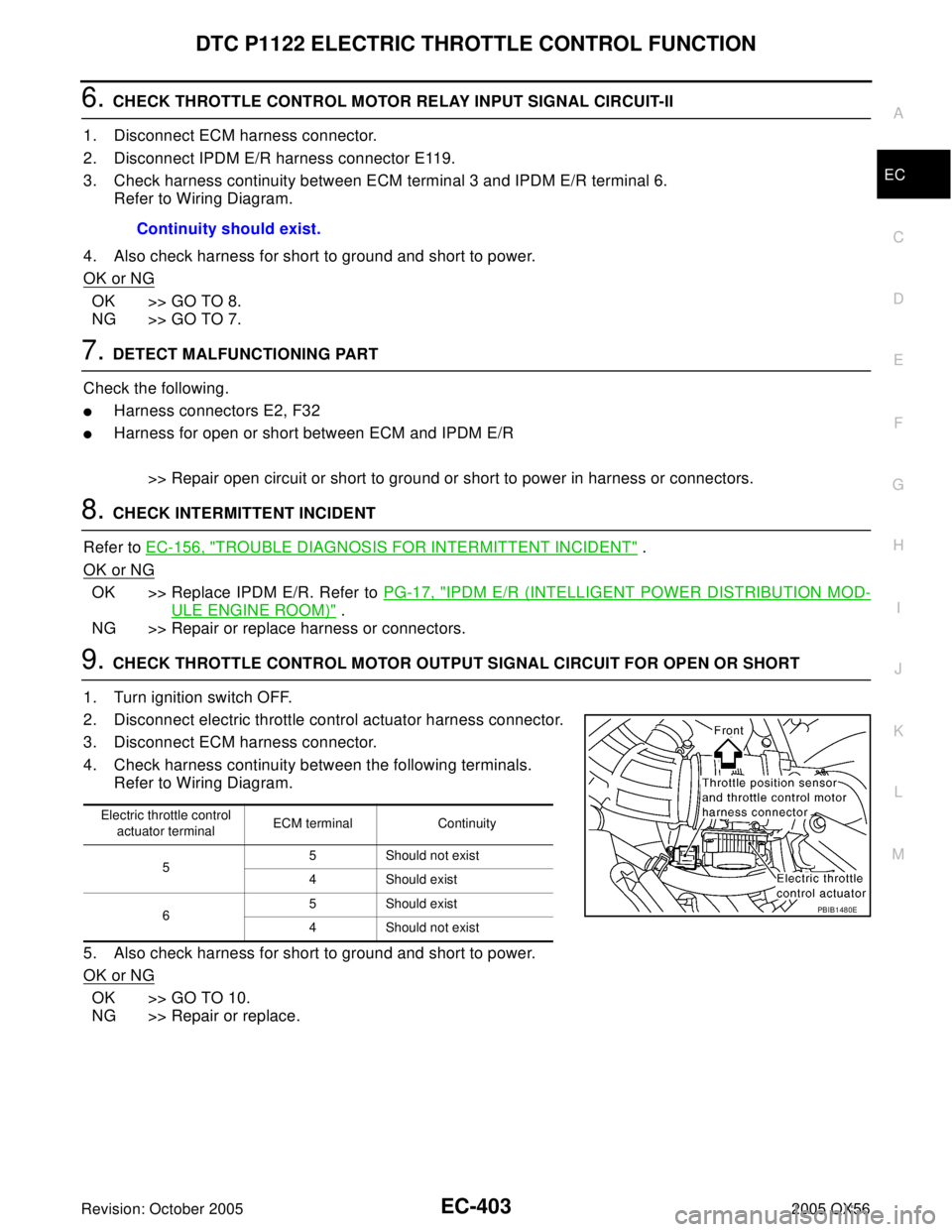
DTC P1122 ELECTRIC THROTTLE CONTROL FUNCTION
EC-403
C
D
E
F
G
H
I
J
K
L
MA
EC
Revision: October 20052005 QX56
6. CHECK THROTTLE CONTROL MOTOR RELAY INPUT SIGNAL CIRCUIT-II
1. Disconnect ECM harness connector.
2. Disconnect IPDM E/R harness connector E119.
3. Check harness continuity between ECM terminal 3 and IPDM E/R terminal 6.
Refer to Wiring Diagram.
4. Also check harness for short to ground and short to power.
OK or NG
OK >> GO TO 8.
NG >> GO TO 7.
7. DETECT MALFUNCTIONING PART
Check the following.
Harness connectors E2, F32
Harness for open or short between ECM and IPDM E/R
>> Repair open circuit or short to ground or short to power in harness or connectors.
8. CHECK INTERMITTENT INCIDENT
Refer to EC-156, "
TROUBLE DIAGNOSIS FOR INTERMITTENT INCIDENT" .
OK or NG
OK >> Replace IPDM E/R. Refer to PG-17, "IPDM E/R (INTELLIGENT POWER DISTRIBUTION MOD-
ULE ENGINE ROOM)" .
NG >> Repair or replace harness or connectors.
9. CHECK THROTTLE CONTROL MOTOR OUTPUT SIGNAL CIRCUIT FOR OPEN OR SHORT
1. Turn ignition switch OFF.
2. Disconnect electric throttle control actuator harness connector.
3. Disconnect ECM harness connector.
4. Check harness continuity between the following terminals.
Refer to Wiring Diagram.
5. Also check harness for short to ground and short to power.
OK or NG
OK >> GO TO 10.
NG >> Repair or replace.Continuity should exist.
Electric throttle control
actuator terminalECM terminal Continuity
55 Should not exist
4 Should exist
65 Should exist
4 Should not exist
PBIB1480E
Page 1596 of 3419
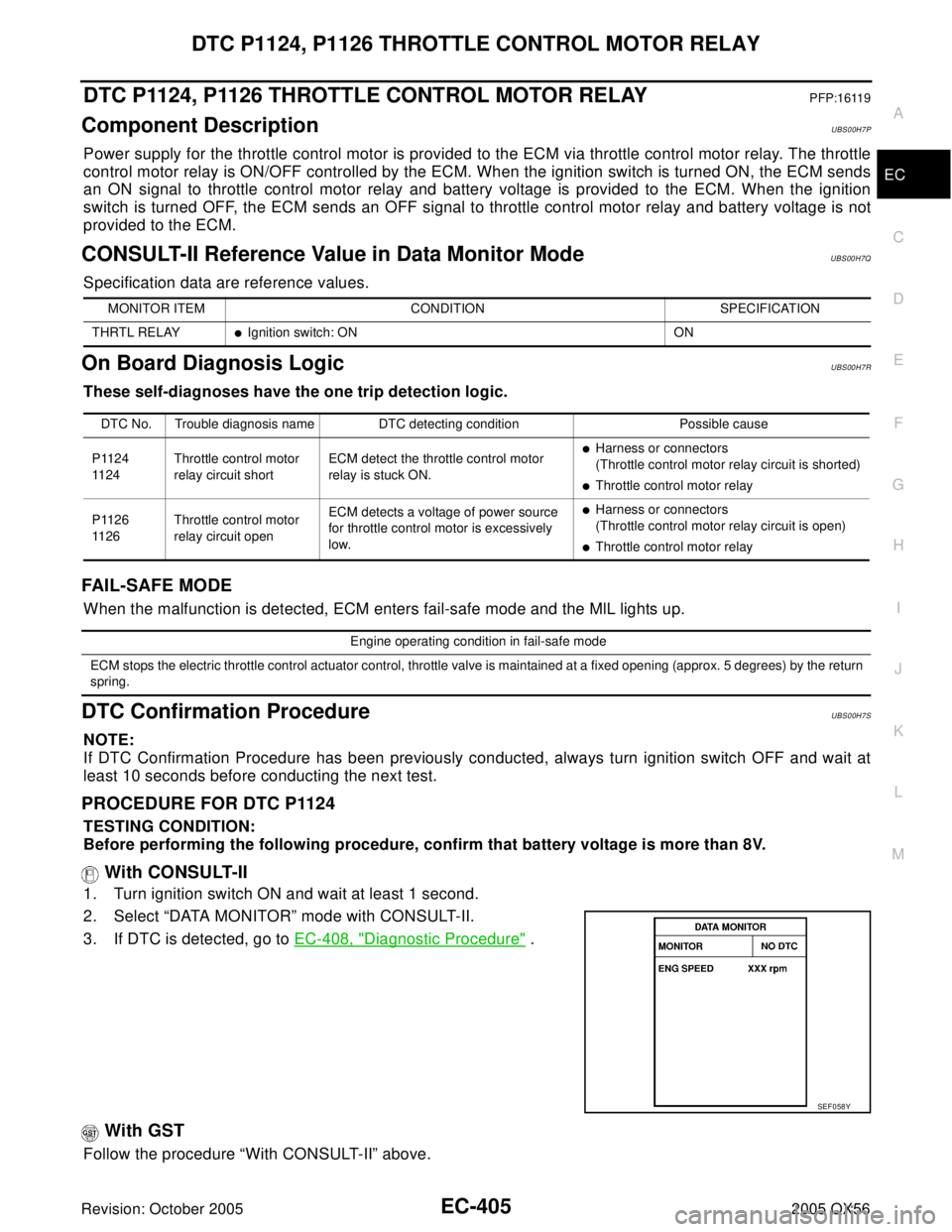
DTC P1124, P1126 THROTTLE CONTROL MOTOR RELAY
EC-405
C
D
E
F
G
H
I
J
K
L
MA
EC
Revision: October 20052005 QX56
DTC P1124, P1126 THROTTLE CONTROL MOTOR RELAYPFP:16119
Component DescriptionUBS00H7P
Power supply for the throttle control motor is provided to the ECM via throttle control motor relay. The throttle
control motor relay is ON/OFF controlled by the ECM. When the ignition switch is turned ON, the ECM sends
an ON signal to throttle control motor relay and battery voltage is provided to the ECM. When the ignition
switch is turned OFF, the ECM sends an OFF signal to throttle control motor relay and battery voltage is not
provided to the ECM.
CONSULT-II Reference Value in Data Monitor ModeUBS00H7Q
Specification data are reference values.
On Board Diagnosis LogicUBS00H7R
These self-diagnoses have the one trip detection logic.
FAIL-SAFE MODE
When the malfunction is detected, ECM enters fail-safe mode and the MlL lights up.
DTC Confirmation ProcedureUBS00H7S
NOTE:
If DTC Confirmation Procedure has been previously conducted, always turn ignition switch OFF and wait at
least 10 seconds before conducting the next test.
PROCEDURE FOR DTC P1124
TESTING CONDITION:
Before performing the following procedure, confirm that battery voltage is more than 8V.
With CONSULT-II
1. Turn ignition switch ON and wait at least 1 second.
2. Select “DATA MONITOR” mode with CONSULT-II.
3. If DTC is detected, go to EC-408, "
Diagnostic Procedure" .
With GST
Follow the procedure “With CONSULT-II” above.
MONITOR ITEM CONDITION SPECIFICATION
THRTL RELAY
Ignition switch: ON ON
DTC No. Trouble diagnosis name DTC detecting condition Possible cause
P1124
11 2 4Throttle control motor
relay circuit shortECM detect the throttle control motor
relay is stuck ON.
Harness or connectors
(Throttle control motor relay circuit is shorted)
Throttle control motor relay
P1126
11 2 6Throttle control motor
relay circuit openECM detects a voltage of power source
for throttle control motor is excessively
low.
Harness or connectors
(Throttle control motor relay circuit is open)
Throttle control motor relay
Engine operating condition in fail-safe mode
ECM stops the electric throttle control actuator control, throttle valve is maintained at a fixed opening (approx. 5 degrees) by the return
spring.
SEF 0 58 Y
Page 1597 of 3419
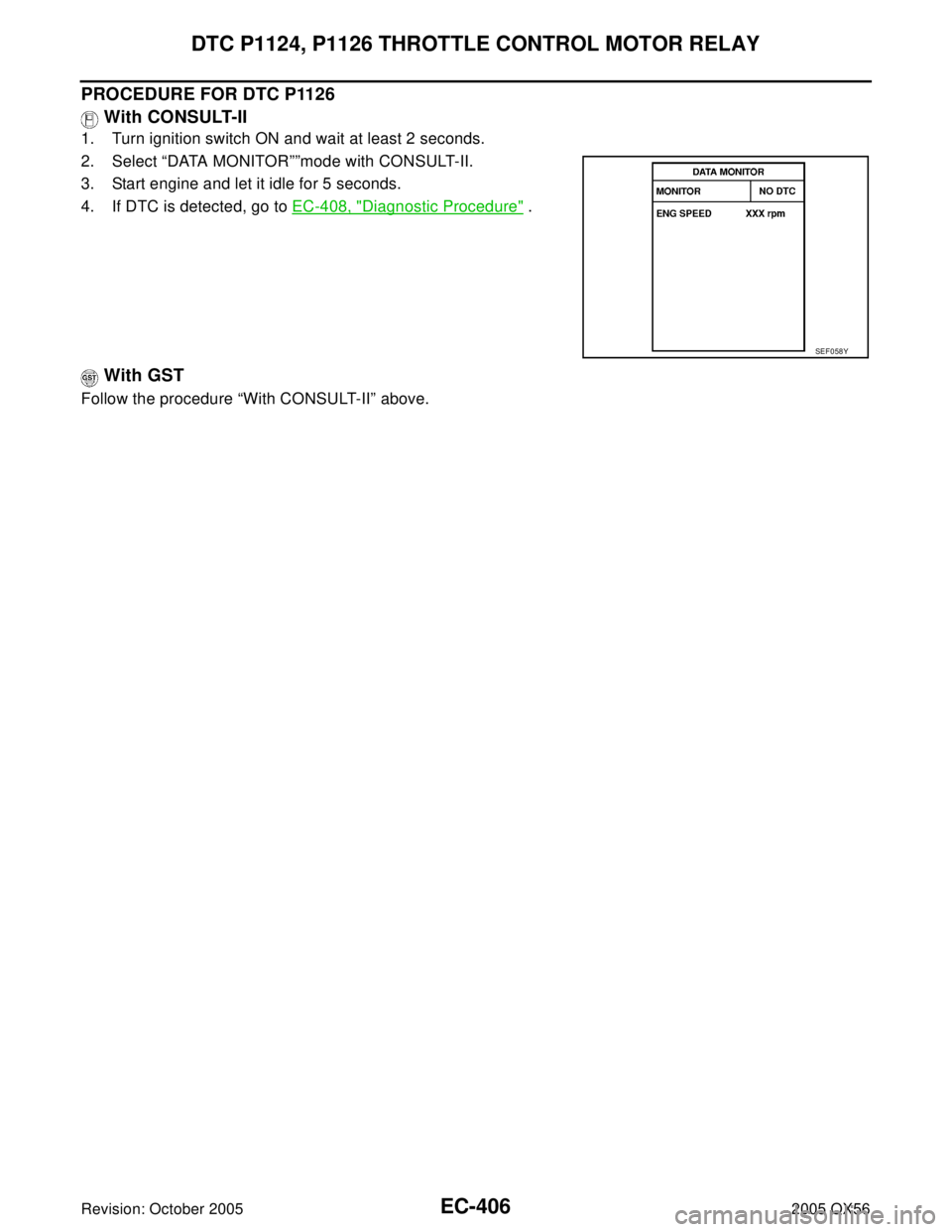
EC-406Revision: October 2005
DTC P1124, P1126 THROTTLE CONTROL MOTOR RELAY
2005 QX56
PROCEDURE FOR DTC P1126
With CONSULT-II
1. Turn ignition switch ON and wait at least 2 seconds.
2. Select “DATA MONITOR””mode with CONSULT-II.
3. Start engine and let it idle for 5 seconds.
4. If DTC is detected, go to EC-408, "
Diagnostic Procedure" .
With GST
Follow the procedure “With CONSULT-II” above.
SEF 0 58 Y
Page 1598 of 3419
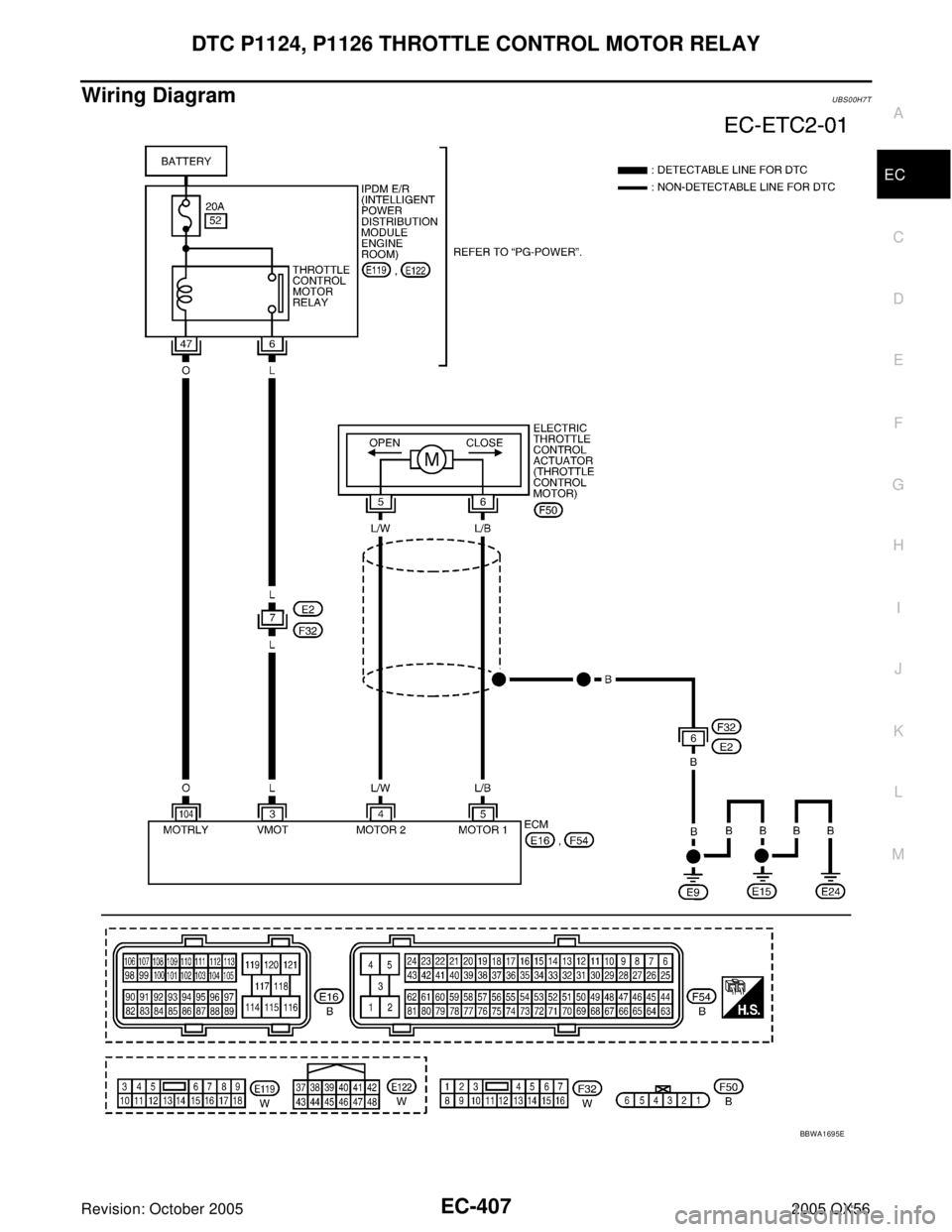
DTC P1124, P1126 THROTTLE CONTROL MOTOR RELAY
EC-407
C
D
E
F
G
H
I
J
K
L
MA
EC
Revision: October 20052005 QX56
Wiring DiagramUBS00H7T
BBWA1695E
Page 1599 of 3419
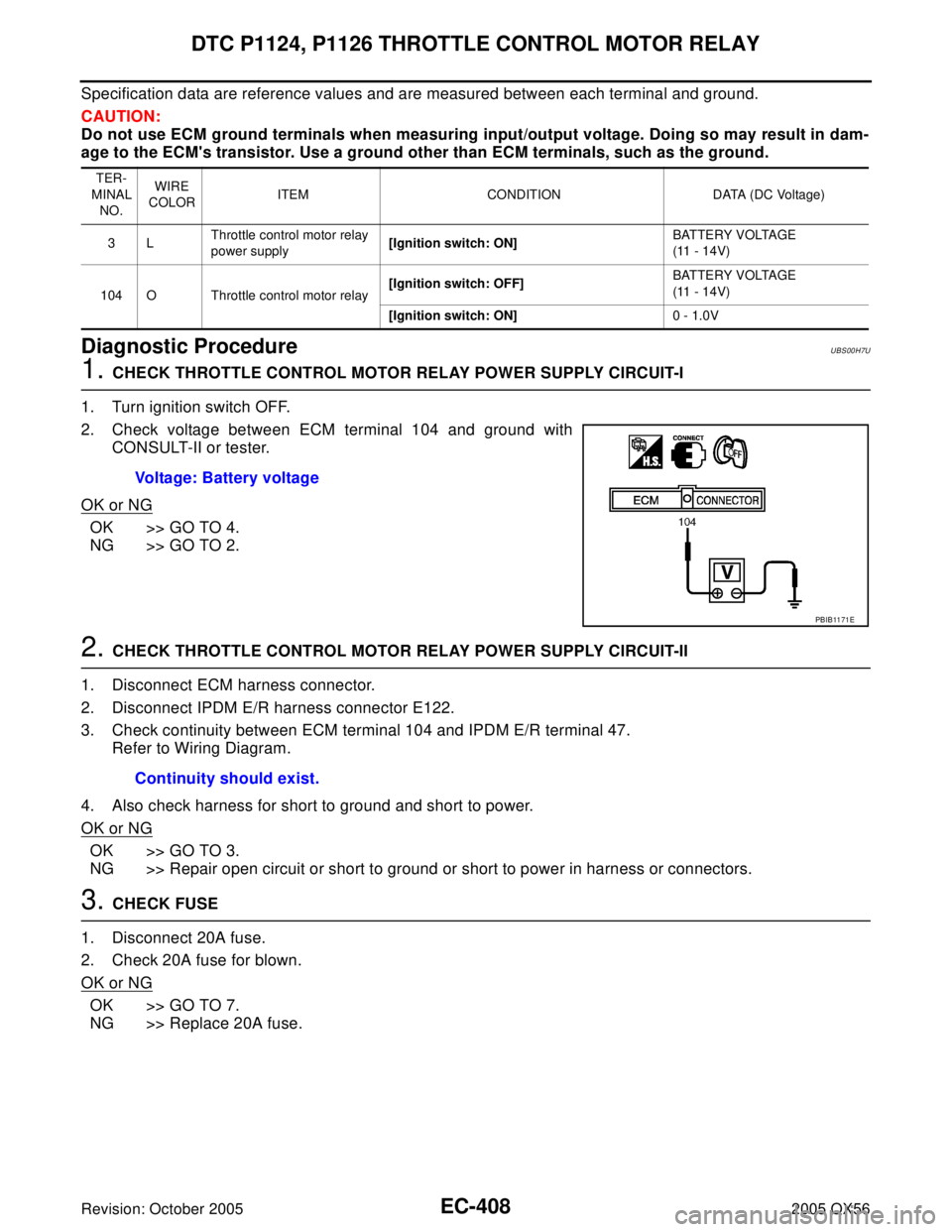
EC-408Revision: October 2005
DTC P1124, P1126 THROTTLE CONTROL MOTOR RELAY
2005 QX56
Specification data are reference values and are measured between each terminal and ground.
CAUTION:
Do not use ECM ground terminals when measuring input/output voltage. Doing so may result in dam-
age to the ECM's transistor. Use a ground other than ECM terminals, such as the ground.
Diagnostic ProcedureUBS00H7U
1. CHECK THROTTLE CONTROL MOTOR RELAY POWER SUPPLY CIRCUIT-I
1. Turn ignition switch OFF.
2. Check voltage between ECM terminal 104 and ground with
CONSULT-II or tester.
OK or NG
OK >> GO TO 4.
NG >> GO TO 2.
2. CHECK THROTTLE CONTROL MOTOR RELAY POWER SUPPLY CIRCUIT-II
1. Disconnect ECM harness connector.
2. Disconnect IPDM E/R harness connector E122.
3. Check continuity between ECM terminal 104 and IPDM E/R terminal 47.
Refer to Wiring Diagram.
4. Also check harness for short to ground and short to power.
OK or NG
OK >> GO TO 3.
NG >> Repair open circuit or short to ground or short to power in harness or connectors.
3. CHECK FUSE
1. Disconnect 20A fuse.
2. Check 20A fuse for blown.
OK or NG
OK >> GO TO 7.
NG >> Replace 20A fuse.
TER-
MINAL
NO.WIRE
COLORITEM CONDITION DATA (DC Voltage)
3LThrottle control motor relay
power supply[Ignition switch: ON]BATTERY VOLTAGE
(11 - 14V)
104 O Throttle control motor relay[Ignition switch: OFF]BATTERY VOLTAGE
(11 - 14V)
[Ignition switch: ON]0 - 1.0V
Voltage: Battery voltage
PBIB11 71 E
Continuity should exist.
Page 1600 of 3419
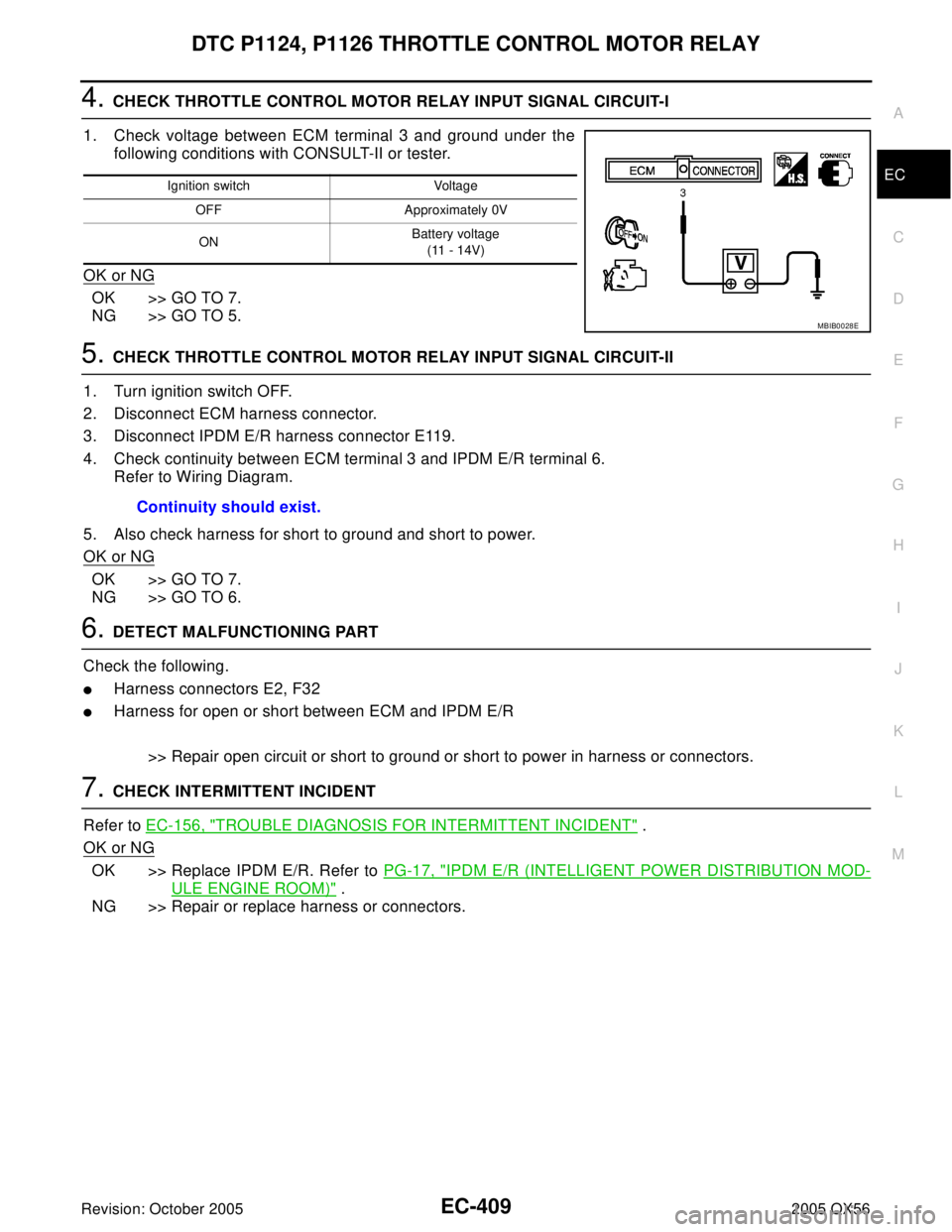
DTC P1124, P1126 THROTTLE CONTROL MOTOR RELAY
EC-409
C
D
E
F
G
H
I
J
K
L
MA
EC
Revision: October 20052005 QX56
4. CHECK THROTTLE CONTROL MOTOR RELAY INPUT SIGNAL CIRCUIT-I
1. Check voltage between ECM terminal 3 and ground under the
following conditions with CONSULT-II or tester.
OK or NG
OK >> GO TO 7.
NG >> GO TO 5.
5. CHECK THROTTLE CONTROL MOTOR RELAY INPUT SIGNAL CIRCUIT-II
1. Turn ignition switch OFF.
2. Disconnect ECM harness connector.
3. Disconnect IPDM E/R harness connector E119.
4. Check continuity between ECM terminal 3 and IPDM E/R terminal 6.
Refer to Wiring Diagram.
5. Also check harness for short to ground and short to power.
OK or NG
OK >> GO TO 7.
NG >> GO TO 6.
6. DETECT MALFUNCTIONING PART
Check the following.
Harness connectors E2, F32
Harness for open or short between ECM and IPDM E/R
>> Repair open circuit or short to ground or short to power in harness or connectors.
7. CHECK INTERMITTENT INCIDENT
Refer to EC-156, "
TROUBLE DIAGNOSIS FOR INTERMITTENT INCIDENT" .
OK or NG
OK >> Replace IPDM E/R. Refer to PG-17, "IPDM E/R (INTELLIGENT POWER DISTRIBUTION MOD-
ULE ENGINE ROOM)" .
NG >> Repair or replace harness or connectors.
Ignition switch Voltage
OFF Approximately 0V
ONBattery voltage
(11 - 14V)
MBIB0028E
Continuity should exist.
Page 1631 of 3419
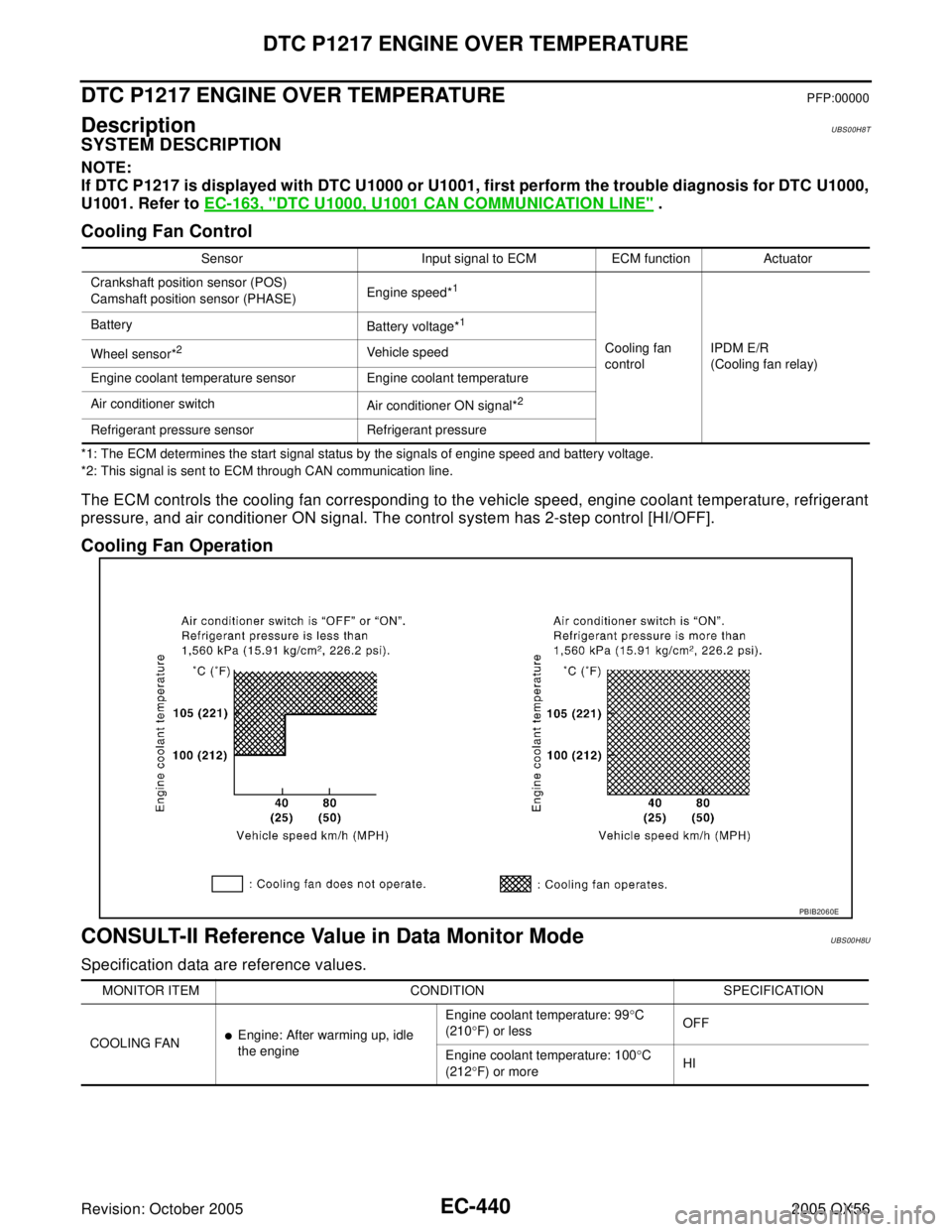
EC-440Revision: October 2005
DTC P1217 ENGINE OVER TEMPERATURE
2005 QX56
DTC P1217 ENGINE OVER TEMPERATUREPFP:00000
DescriptionUBS00H8T
SYSTEM DESCRIPTION
NOTE:
If DTC P1217 is displayed with DTC U1000 or U1001, first perform the trouble diagnosis for DTC U1000,
U1001. Refer to EC-163, "
DTC U1000, U1001 CAN COMMUNICATION LINE" .
Cooling Fan Control
*1: The ECM determines the start signal status by the signals of engine speed and battery voltage.
*2: This signal is sent to ECM through CAN communication line.
The ECM controls the cooling fan corresponding to the vehicle speed, engine coolant temperature, refrigerant
pressure, and air conditioner ON signal. The control system has 2-step control [HI/OFF].
Cooling Fan Operation
CONSULT-II Reference Value in Data Monitor ModeUBS00H8U
Specification data are reference values.
Sensor Input signal to ECM ECM function Actuator
Crankshaft position sensor (POS)
Camshaft position sensor (PHASE)Engine speed*
1
Cooling fan
controlIPDM E/R
(Cooling fan relay) Battery
Battery voltage*
1
Wheel sensor*2Vehicle speed
Engine coolant temperature sensor Engine coolant temperature
Air conditioner switch
Air conditioner ON signal*
2
Refrigerant pressure sensor Refrigerant pressure
PBIB2060E
MONITOR ITEM CONDITION SPECIFICATION
COOLING FAN
Engine: After warming up, idle
the engineEngine coolant temperature: 99°C
(210°F) or lessOFF
Engine coolant temperature: 100°C
(212°F) or moreHI
Page 1632 of 3419
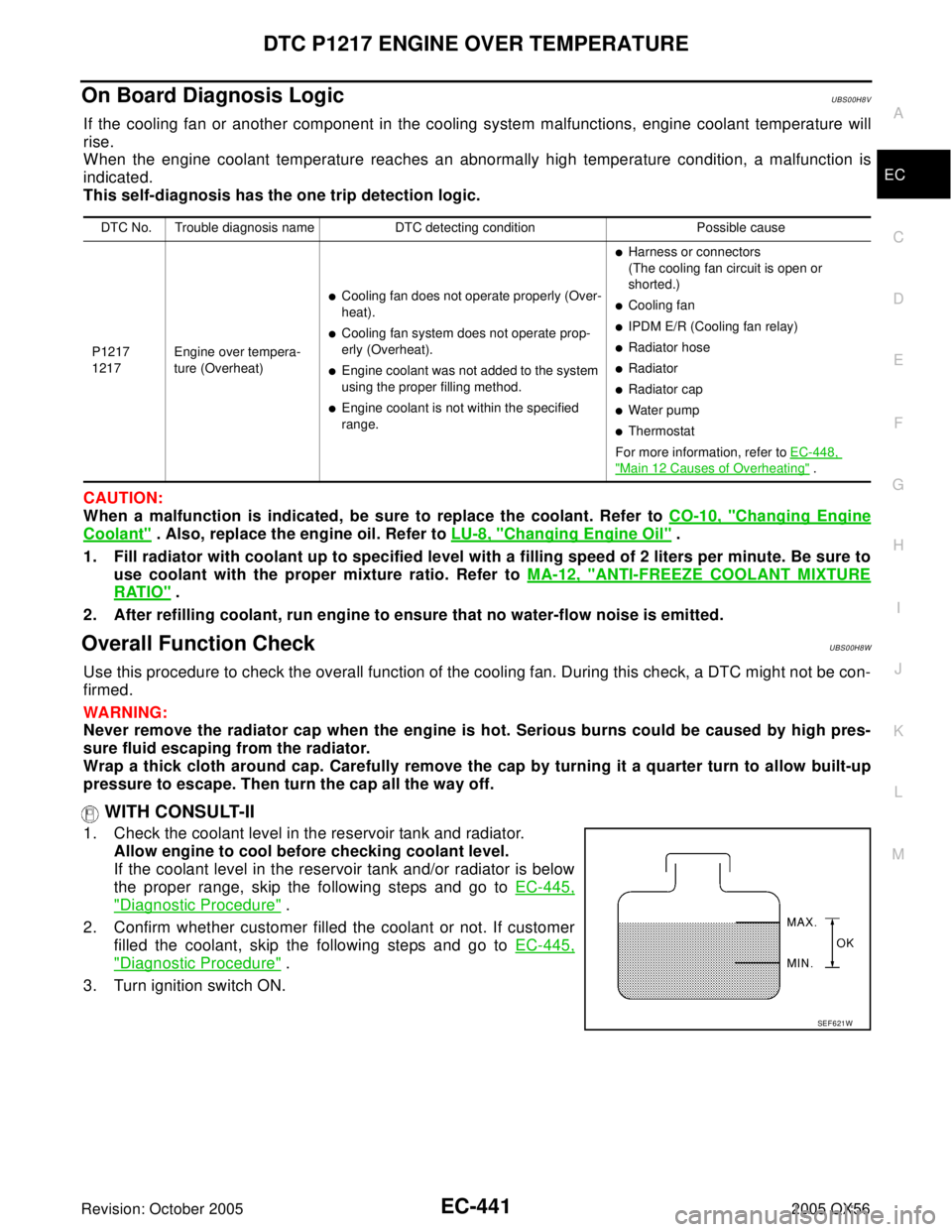
DTC P1217 ENGINE OVER TEMPERATURE
EC-441
C
D
E
F
G
H
I
J
K
L
MA
EC
Revision: October 20052005 QX56
On Board Diagnosis LogicUBS00H8V
If the cooling fan or another component in the cooling system malfunctions, engine coolant temperature will
rise.
When the engine coolant temperature reaches an abnormally high temperature condition, a malfunction is
indicated.
This self-diagnosis has the one trip detection logic.
CAUTION:
When a malfunction is indicated, be sure to replace the coolant. Refer to CO-10, "
Changing Engine
Coolant" . Also, replace the engine oil. Refer to LU-8, "Changing Engine Oil" .
1. Fill radiator with coolant up to specified level with a filling speed of 2 liters per minute. Be sure to
use coolant with the proper mixture ratio. Refer to MA-12, "
ANTI-FREEZE COOLANT MIXTURE
RATIO" .
2. After refilling coolant, run engine to ensure that no water-flow noise is emitted.
Overall Function CheckUBS00H8W
Use this procedure to check the overall function of the cooling fan. During this check, a DTC might not be con-
firmed.
WA RN ING:
Never remove the radiator cap when the engine is hot. Serious burns could be caused by high pres-
sure fluid escaping from the radiator.
Wrap a thick cloth around cap. Carefully remove the cap by turning it a quarter turn to allow built-up
pressure to escape. Then turn the cap all the way off.
WITH CONSULT-II
1. Check the coolant level in the reservoir tank and radiator.
Allow engine to cool before checking coolant level.
If the coolant level in the reservoir tank and/or radiator is below
the proper range, skip the following steps and go to EC-445,
"Diagnostic Procedure" .
2. Confirm whether customer filled the coolant or not. If customer
filled the coolant, skip the following steps and go to EC-445,
"Diagnostic Procedure" .
3. Turn ignition switch ON.
DTC No. Trouble diagnosis name DTC detecting condition Possible cause
P1217
1217Engine over tempera-
ture (Overheat)
Cooling fan does not operate properly (Over-
heat).
Cooling fan system does not operate prop-
erly (Overheat).
Engine coolant was not added to the system
using the proper filling method.
Engine coolant is not within the specified
range.
Harness or connectors
(The cooling fan circuit is open or
shorted.)
Cooling fan
IPDM E/R (Cooling fan relay)
Radiator hose
Radiator
Radiator cap
Water pump
Thermostat
For more information, refer to EC-448,
"Main 12 Causes of Overheating" .
SEF 6 21 W