power steering INFINITI QX56 2004 Factory Owners Manual
[x] Cancel search | Manufacturer: INFINITI, Model Year: 2004, Model line: QX56, Model: INFINITI QX56 2004Pages: 3371, PDF Size: 78.5 MB
Page 2980 of 3371
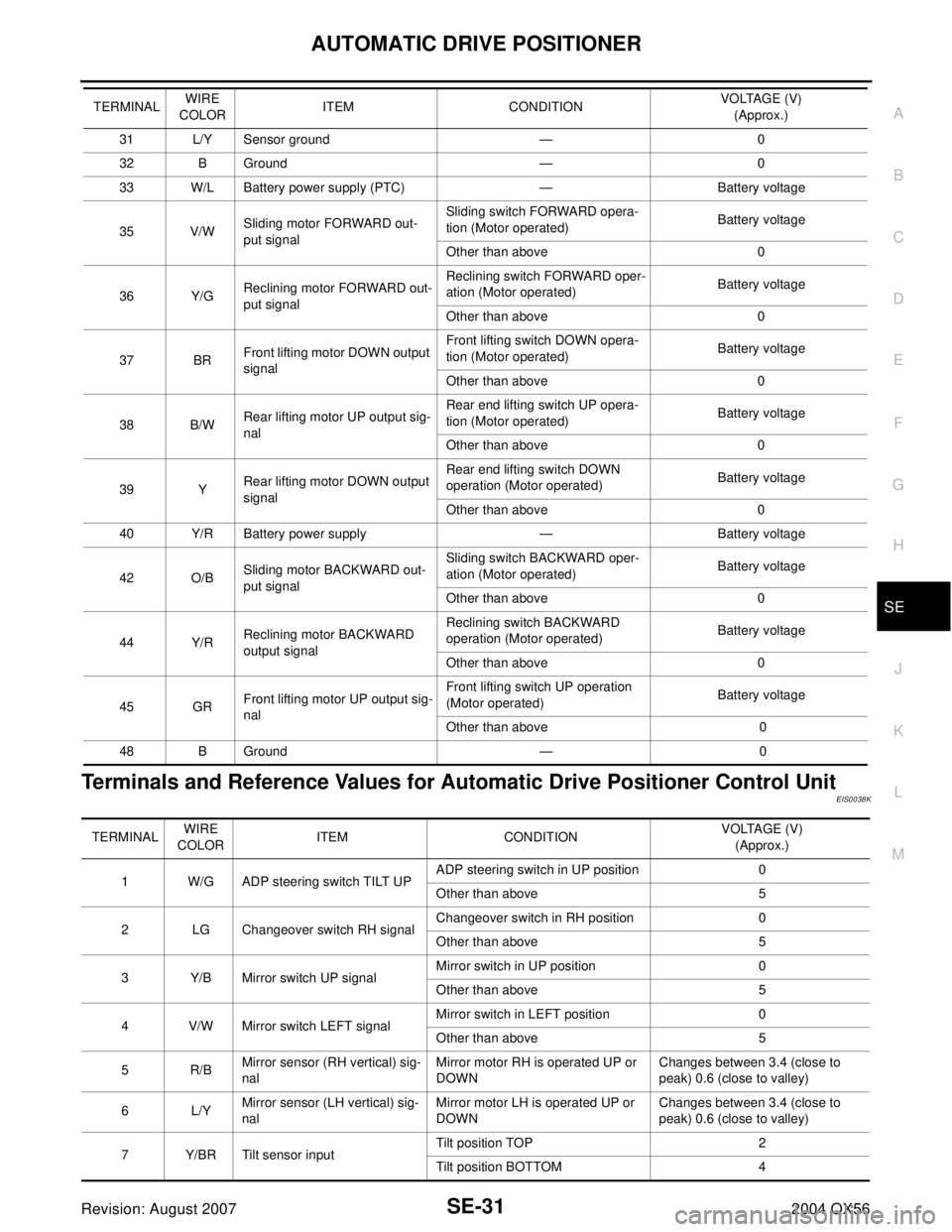
AUTOMATIC DRIVE POSITIONER
SE-31
C
D
E
F
G
H
J
K
L
MA
B
SE
Revision: August 20072004 QX56
Terminals and Reference Values for Automatic Drive Positioner Control UnitEIS0038K
31 L/Y Sensor ground — 0
32 B Ground — 0
33 W/L Battery power supply (PTC) — Battery voltage
35 V/WSliding motor FORWARD out-
put signalSliding switch FORWARD opera-
tion (Motor operated)Battery voltage
Other than above 0
36 Y/GReclining motor FORWARD out-
put signalReclining switch FORWARD oper-
ation (Motor operated)Battery voltage
Other than above 0
37 BRFront lifting motor DOWN output
signalFront lifting switch DOWN opera-
tion (Motor operated)Battery voltage
Other than above 0
38 B/WRear lifting motor UP output sig-
nalRear end lifting switch UP opera-
tion (Motor operated)Battery voltage
Other than above 0
39 YRear lifting motor DOWN output
signalRear end lifting switch DOWN
operation (Motor operated)Battery voltage
Other than above 0
40 Y/R Battery power supply — Battery voltage
42 O/BSliding motor BACKWARD out-
put signalSliding switch BACKWARD oper-
ation (Motor operated)Battery voltage
Other than above 0
44 Y/RReclining motor BACKWARD
output signalReclining switch BACKWARD
operation (Motor operated)Battery voltage
Other than above 0
45 GRFront lifting motor UP output sig-
nalFront lifting switch UP operation
(Motor operated)Battery voltage
Other than above 0
48 B Ground — 0 TERMINALWIRE
COLORITEM CONDITIONVOLTAGE (V)
(Approx.)
TERMINAL WIRE
COLORITEM CONDITIONVOLTAGE (V)
(Approx.)
1 W/G ADP steering switch TILT UPADP steering switch in UP position 0
Other than above 5
2 LG Changeover switch RH signalChangeover switch in RH position 0
Other than above 5
3 Y/B Mirror switch UP signalMirror switch in UP position 0
Other than above 5
4 V/W Mirror switch LEFT signalMirror switch in LEFT position 0
Other than above 5
5R/BMirror sensor (RH vertical) sig-
nalMirror motor RH is operated UP or
DOWNChanges between 3.4 (close to
peak) 0.6 (close to valley)
6L/YMirror sensor (LH vertical) sig-
nalMirror motor LH is operated UP or
DOWNChanges between 3.4 (close to
peak) 0.6 (close to valley)
7 Y/BR Tilt sensor inputTilt position TOP 2
Tilt position BOTTOM 4
Page 2982 of 3371
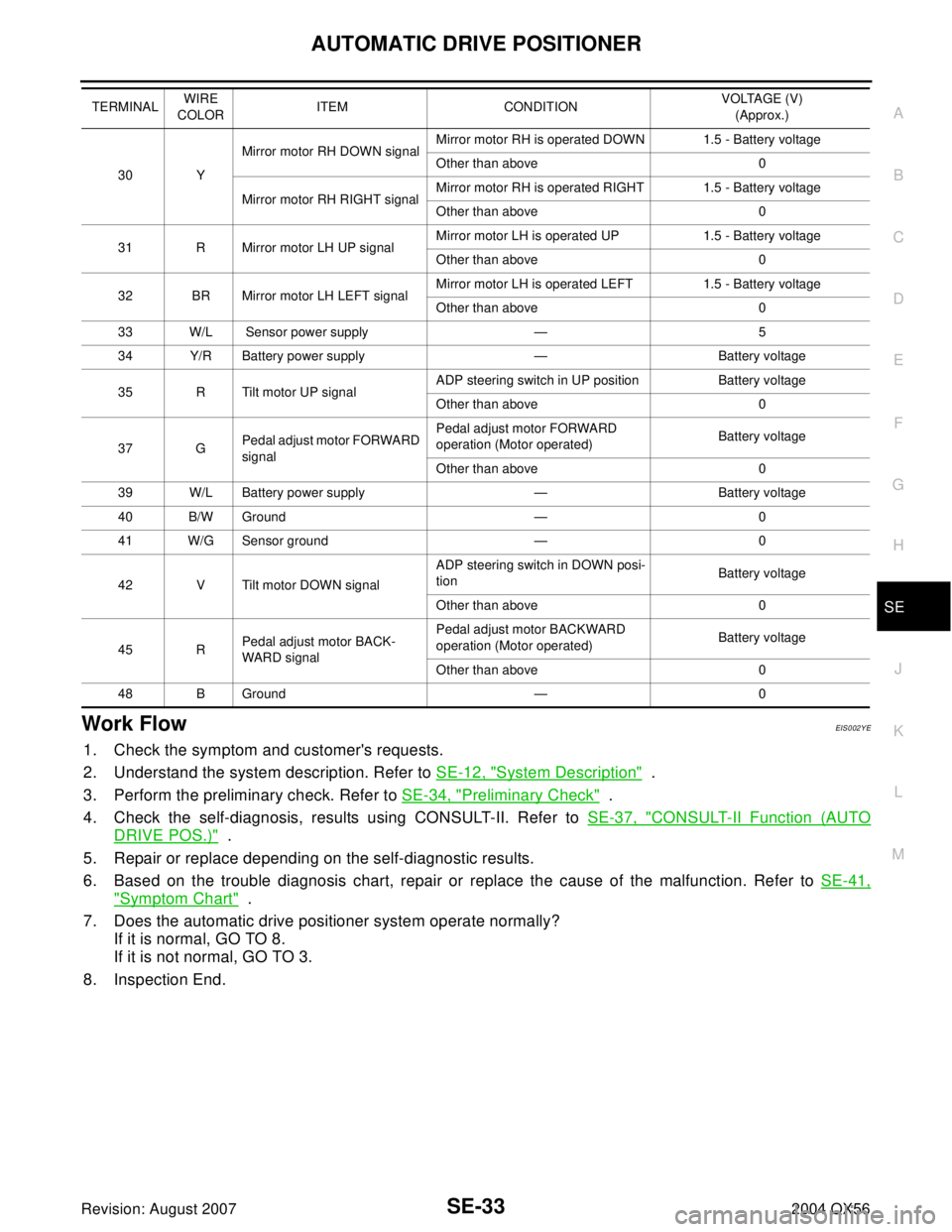
AUTOMATIC DRIVE POSITIONER
SE-33
C
D
E
F
G
H
J
K
L
MA
B
SE
Revision: August 20072004 QX56
Work Flow EIS002YE
1. Check the symptom and customer's requests.
2. Understand the system description. Refer to SE-12, "
System Description" .
3. Perform the preliminary check. Refer to SE-34, "
Preliminary Check" .
4. Check the self-diagnosis, results using CONSULT-II. Refer to SE-37, "
CONSULT-II Function (AUTO
DRIVE POS.)" .
5. Repair or replace depending on the self-diagnostic results.
6. Based on the trouble diagnosis chart, repair or replace the cause of the malfunction. Refer to SE-41,
"Symptom Chart" .
7. Does the automatic drive positioner system operate normally?
If it is normal, GO TO 8.
If it is not normal, GO TO 3.
8. Inspection End.
30 YMirror motor RH DOWN signalMirror motor RH is operated DOWN 1.5 - Battery voltage
Other than above 0
Mirror motor RH RIGHT signalMirror motor RH is operated RIGHT 1.5 - Battery voltage
Other than above 0
31 R Mirror motor LH UP signalMirror motor LH is operated UP 1.5 - Battery voltage
Other than above 0
32 BR Mirror motor LH LEFT signalMirror motor LH is operated LEFT 1.5 - Battery voltage
Other than above 0
33 W/L Sensor power supply — 5
34 Y/R Battery power supply — Battery voltage
35 R Tilt motor UP signalADP steering switch in UP position Battery voltage
Other than above 0
37 GPedal adjust motor FORWARD
signalPedal adjust motor FORWARD
operation (Motor operated)Battery voltage
Other than above 0
39 W/L Battery power supply — Battery voltage
40 B/W Ground — 0
41 W/G Sensor ground — 0
42 V Tilt motor DOWN signalADP steering switch in DOWN posi-
tionBattery voltage
Other than above 0
45 RPedal adjust motor BACK-
WARD signalPedal adjust motor BACKWARD
operation (Motor operated)Battery voltage
Other than above 0
48 B Ground — 0 TERMINAL WIRE
COLORITEM CONDITIONVOLTAGE (V)
(Approx.)
Page 2983 of 3371
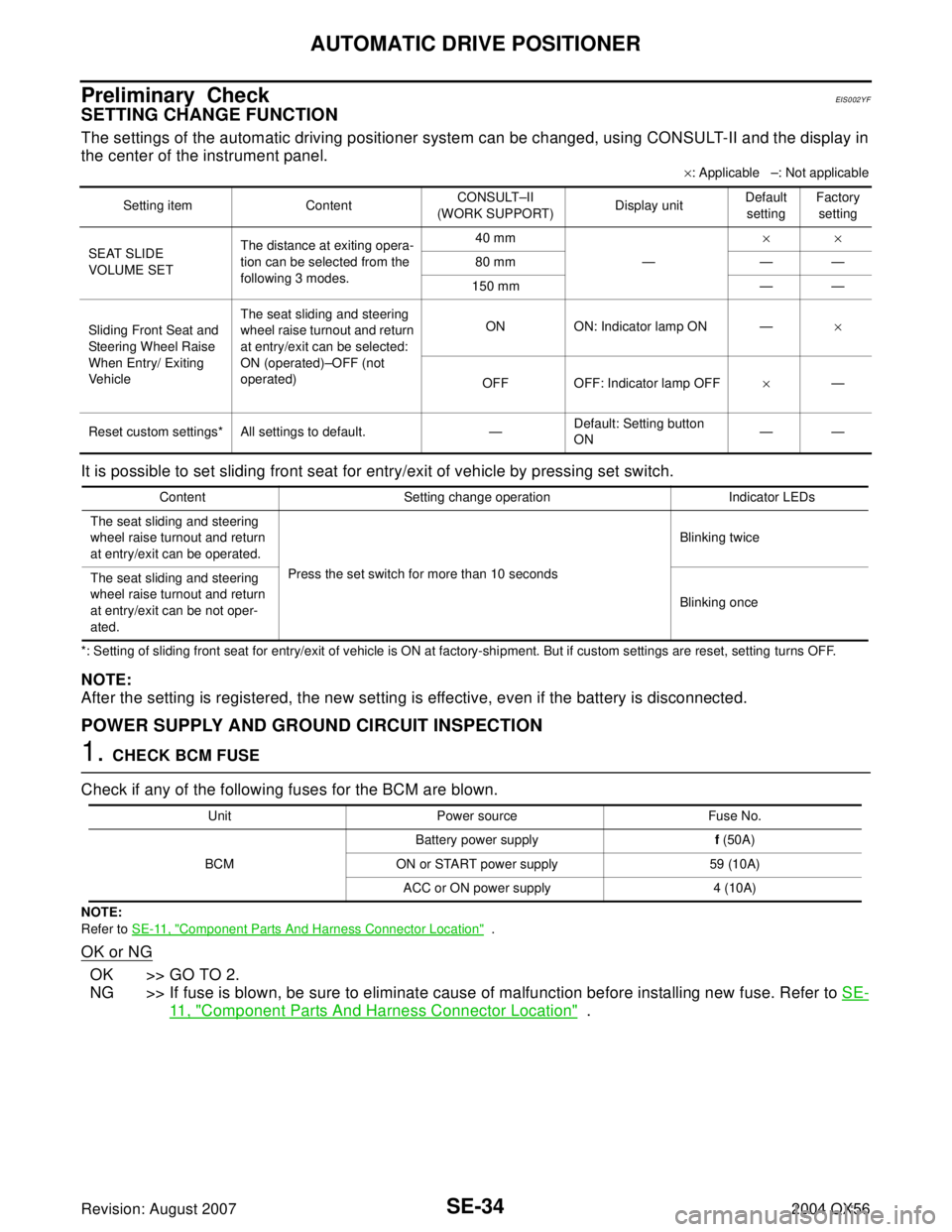
SE-34
AUTOMATIC DRIVE POSITIONER
Revision: August 20072004 QX56
Preliminary CheckEIS002YF
SETTING CHANGE FUNCTION
The settings of the automatic driving positioner system can be changed, using CONSULT-II and the display in
the center of the instrument panel.
×: Applicable –: Not applicable
It is possible to set sliding front seat for entry/exit of vehicle by pressing set switch.
*: Setting of sliding front seat for entry/exit of vehicle is ON at factory-shipment. But if custom settings are reset, setting turns OFF.
NOTE:
After the setting is registered, the new setting is effective, even if the battery is disconnected.
POWER SUPPLY AND GROUND CIRCUIT INSPECTION
1. CHECK BCM FUSE
Check if any of the following fuses for the BCM are blown.
NOTE:
Refer to SE-11, "
Component Parts And Harness Connector Location" .
OK or NG
OK >> GO TO 2.
NG >> If fuse is blown, be sure to eliminate cause of malfunction before installing new fuse. Refer to SE-
11 , "Component Parts And Harness Connector Location" .
Setting item ContentCONSULT–II
(WORK SUPPORT)Display unitDefault
settingFactory
setting
SEAT SLIDE
VOLUME SETThe distance at exiting opera-
tion can be selected from the
following 3 modes.40 mm
—××
80 mm — —
150 mm — —
Sliding Front Seat and
Steering Wheel Raise
When Entry/ Exiting
VehicleThe seat sliding and steering
wheel raise turnout and return
at entry/exit can be selected:
ON (operated)–OFF (not
operated)ON ON: Indicator lamp ON —×
OFF OFF: Indicator lamp OFF×—
Reset custom settings* All settings to default. —Default: Setting button
ON——
Content Setting change operation Indicator LEDs
The seat sliding and steering
wheel raise turnout and return
at entry/exit can be operated.
Press the set switch for more than 10 secondsBlinking twice
The seat sliding and steering
wheel raise turnout and return
at entry/exit can be not oper-
ated.Blinking once
Unit Power source Fuse No.
BCMBattery power supplyf (50A)
ON or START power supply 59 (10A)
ACC or ON power supply 4 (10A)
Page 3064 of 3371
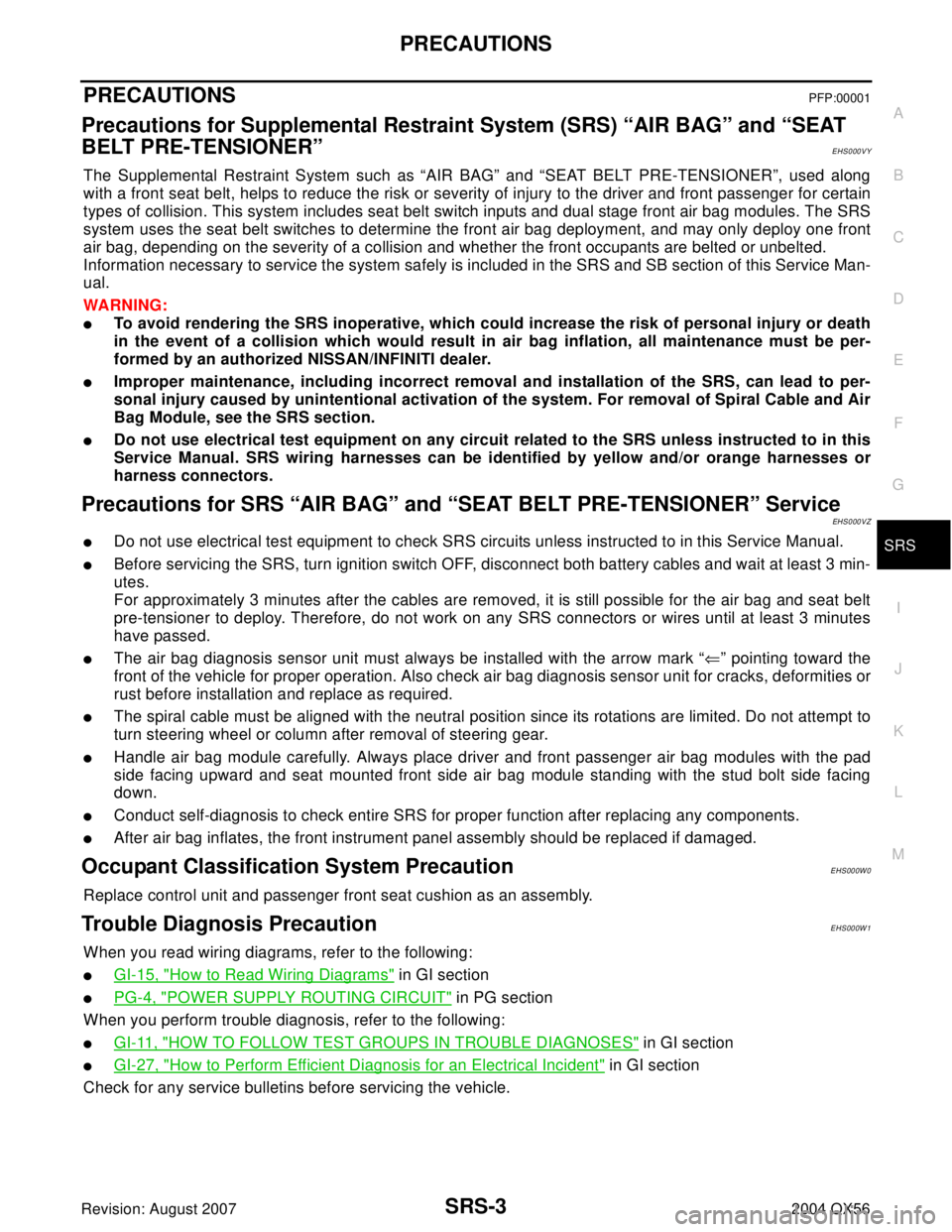
PRECAUTIONS
SRS-3
C
D
E
F
G
I
J
K
L
MA
B
SRS
Revision: August 20072004 QX56
PRECAUTIONSPFP:00001
Precautions for Supplemental Restraint System (SRS) “AIR BAG” and “SEAT
BELT PRE-TENSIONER”
EHS000VY
The Supplemental Restraint System such as “AIR BAG” and “SEAT BELT PRE-TENSIONER”, used along
with a front seat belt, helps to reduce the risk or severity of injury to the driver and front passenger for certain
types of collision. This system includes seat belt switch inputs and dual stage front air bag modules. The SRS
system uses the seat belt switches to determine the front air bag deployment, and may only deploy one front
air bag, depending on the severity of a collision and whether the front occupants are belted or unbelted.
Information necessary to service the system safely is included in the SRS and SB section of this Service Man-
ual.
WA RN ING:
To avoid rendering the SRS inoperative, which could increase the risk of personal injury or death
in the event of a collision which would result in air bag inflation, all maintenance must be per-
formed by an authorized NISSAN/INFINITI dealer.
Improper maintenance, including incorrect removal and installation of the SRS, can lead to per-
sonal injury caused by unintentional activation of the system. For removal of Spiral Cable and Air
Bag Module, see the SRS section.
Do not use electrical test equipment on any circuit related to the SRS unless instructed to in this
Service Manual. SRS wiring harnesses can be identified by yellow and/or orange harnesses or
harness connectors.
Precautions for SRS “AIR BAG” and “SEAT BELT PRE-TENSIONER” ServiceEHS000VZ
Do not use electrical test equipment to check SRS circuits unless instructed to in this Service Manual.
Before servicing the SRS, turn ignition switch OFF, disconnect both battery cables and wait at least 3 min-
utes.
For approximately 3 minutes after the cables are removed, it is still possible for the air bag and seat belt
pre-tensioner to deploy. Therefore, do not work on any SRS connectors or wires until at least 3 minutes
have passed.
The air bag diagnosis sensor unit must always be installed with the arrow mark “⇐” pointing toward the
front of the vehicle for proper operation. Also check air bag diagnosis sensor unit for cracks, deformities or
rust before installation and replace as required.
The spiral cable must be aligned with the neutral position since its rotations are limited. Do not attempt to
turn steering wheel or column after removal of steering gear.
Handle air bag module carefully. Always place driver and front passenger air bag modules with the pad
side facing upward and seat mounted front side air bag module standing with the stud bolt side facing
down.
Conduct self-diagnosis to check entire SRS for proper function after replacing any components.
After air bag inflates, the front instrument panel assembly should be replaced if damaged.
Occupant Classification System PrecautionEHS000W0
Replace control unit and passenger front seat cushion as an assembly.
Trouble Diagnosis PrecautionEHS000W1
When you read wiring diagrams, refer to the following:
GI-15, "How to Read Wiring Diagrams" in GI section
PG-4, "POWER SUPPLY ROUTING CIRCUIT" in PG section
When you perform trouble diagnosis, refer to the following:
GI-11, "HOW TO FOLLOW TEST GROUPS IN TROUBLE DIAGNOSES" in GI section
GI-27, "How to Perform Efficient Diagnosis for an Electrical Incident" in GI section
Check for any service bulletins before servicing the vehicle.
Page 3158 of 3371
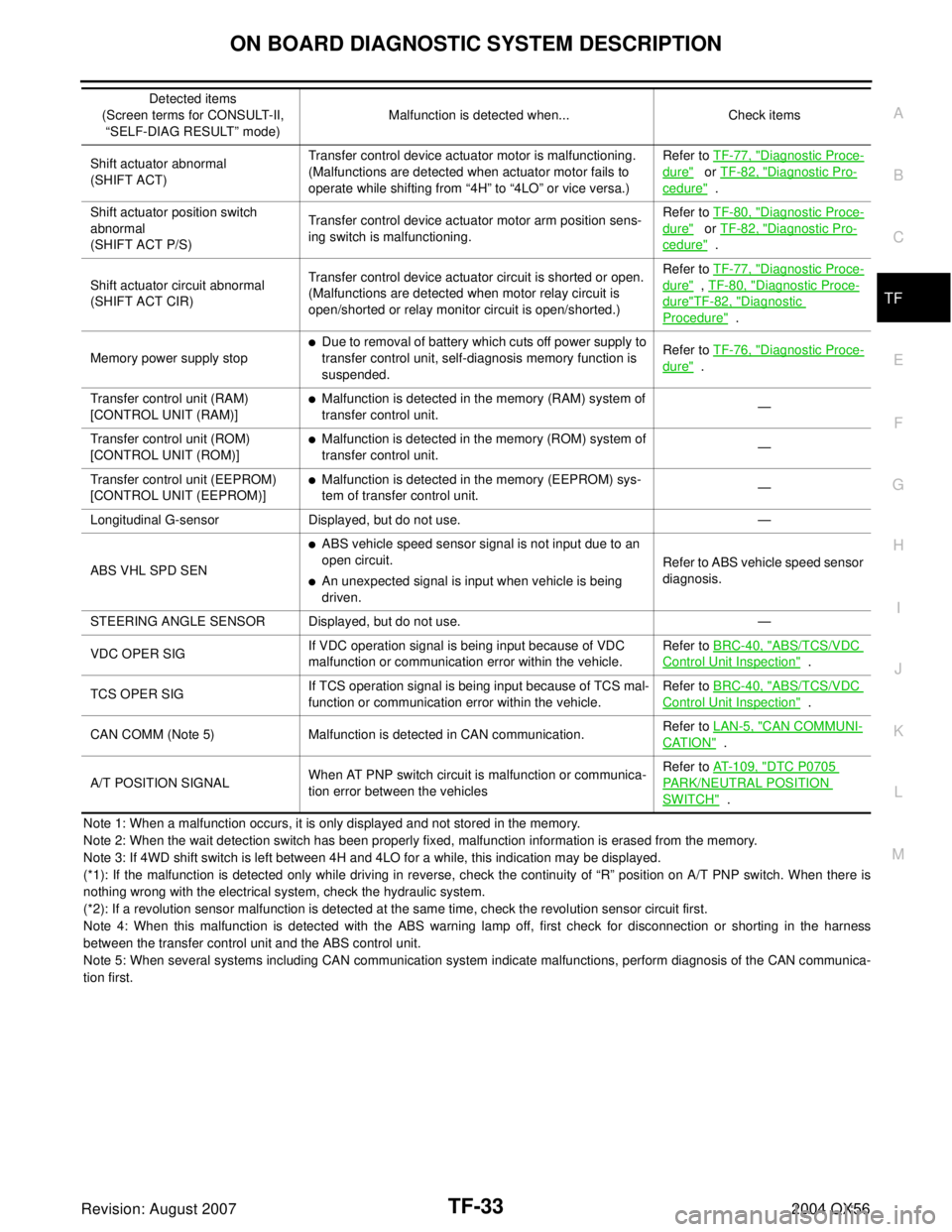
ON BOARD DIAGNOSTIC SYSTEM DESCRIPTION
TF-33
C
E
F
G
H
I
J
K
L
MA
B
TF
Revision: August 20072004 QX56
Note 1: When a malfunction occurs, it is only displayed and not stored in the memory.
Note 2: When the wait detection switch has been properly fixed, malfunction information is erased from the memory.
Note 3: If 4WD shift switch is left between 4H and 4LO for a while, this indication may be displayed.
(*1): If the malfunction is detected only while driving in reverse, check the continuity of “R” position on A/T PNP switch. When there is
nothing wrong with the electrical system, check the hydraulic system.
(*2): If a revolution sensor malfunction is detected at the same time, check the revolution sensor circuit first.
Note 4: When this malfunction is detected with the ABS warning lamp off, first check for disconnection or shorting in the harness
between the transfer control unit and the ABS control unit.
Note 5: When several systems including CAN communication system indicate malfunctions, perform diagnosis of the CAN communica-
tion first.Shift actuator abnormal
(SHIFT ACT)Transfer control device actuator motor is malfunctioning.
(Malfunctions are detected when actuator motor fails to
operate while shifting from “4H” to “4LO” or vice versa.) Refer to TF-77, "
Diagnostic Proce-
dure" or TF-82, "Diagnostic Pro-
cedure" .
Shift actuator position switch
abnormal
(SHIFT ACT P/S)Transfer control device actuator motor arm position sens-
ing switch is malfunctioning.Refer to TF-80, "
Diagnostic Proce-
dure" or TF-82, "Diagnostic Pro-
cedure" .
Shift actuator circuit abnormal
(SHIFT ACT CIR)Transfer control device actuator circuit is shorted or open.
(Malfunctions are detected when motor relay circuit is
open/shorted or relay monitor circuit is open/shorted.)Refer to TF-77, "
Diagnostic Proce-
dure" , TF-80, "Diagnostic Proce-
dure"TF-82, "Diagnostic
Procedure" .
Memory power supply stop
Due to removal of battery which cuts off power supply to
transfer control unit, self-diagnosis memory function is
suspended.Refer to TF-76, "Diagnostic Proce-
dure" .
Transfer control unit (RAM)
[CONTROL UNIT (RAM)]
Malfunction is detected in the memory (RAM) system of
transfer control unit.—
Transfer control unit (ROM)
[CONTROL UNIT (ROM)]
Malfunction is detected in the memory (ROM) system of
transfer control unit.—
Transfer control unit (EEPROM)
[CONTROL UNIT (EEPROM)]
Malfunction is detected in the memory (EEPROM) sys-
tem of transfer control unit.—
Longitudinal G-sensor Displayed, but do not use. —
ABS VHL SPD SEN
ABS vehicle speed sensor signal is not input due to an
open circuit.
An unexpected signal is input when vehicle is being
driven.Refer to ABS vehicle speed sensor
diagnosis.
STEERING ANGLE SENSOR Displayed, but do not use. —
VDC OPER SIGIf VDC operation signal is being input because of VDC
malfunction or communication error within the vehicle.Refer to BRC-40, "
ABS/TCS/VDC
Control Unit Inspection" .
TCS OPER SIGIf TCS operation signal is being input because of TCS mal-
function or communication error within the vehicle.Refer to BRC-40, "
ABS/TCS/VDC
Control Unit Inspection" .
CAN COMM (Note 5) Malfunction is detected in CAN communication.Refer to LAN-5, "
CAN COMMUNI-
CATION" .
A/T POSITION SIGNALWhen AT PNP switch circuit is malfunction or communica-
tion error between the vehiclesRefer to AT-109, "
DTC P0705
PARK/NEUTRAL POSITION
SWITCH" . Detected items
(Screen terms for CONSULT-II,
“SELF-DIAG RESULT” mode)Malfunction is detected when... Check items