Ins INFINITI QX56 2004 Factory Service Manual
[x] Cancel search | Manufacturer: INFINITI, Model Year: 2004, Model line: QX56, Model: INFINITI QX56 2004Pages: 3371, PDF Size: 78.5 MB
Page 2849 of 3371
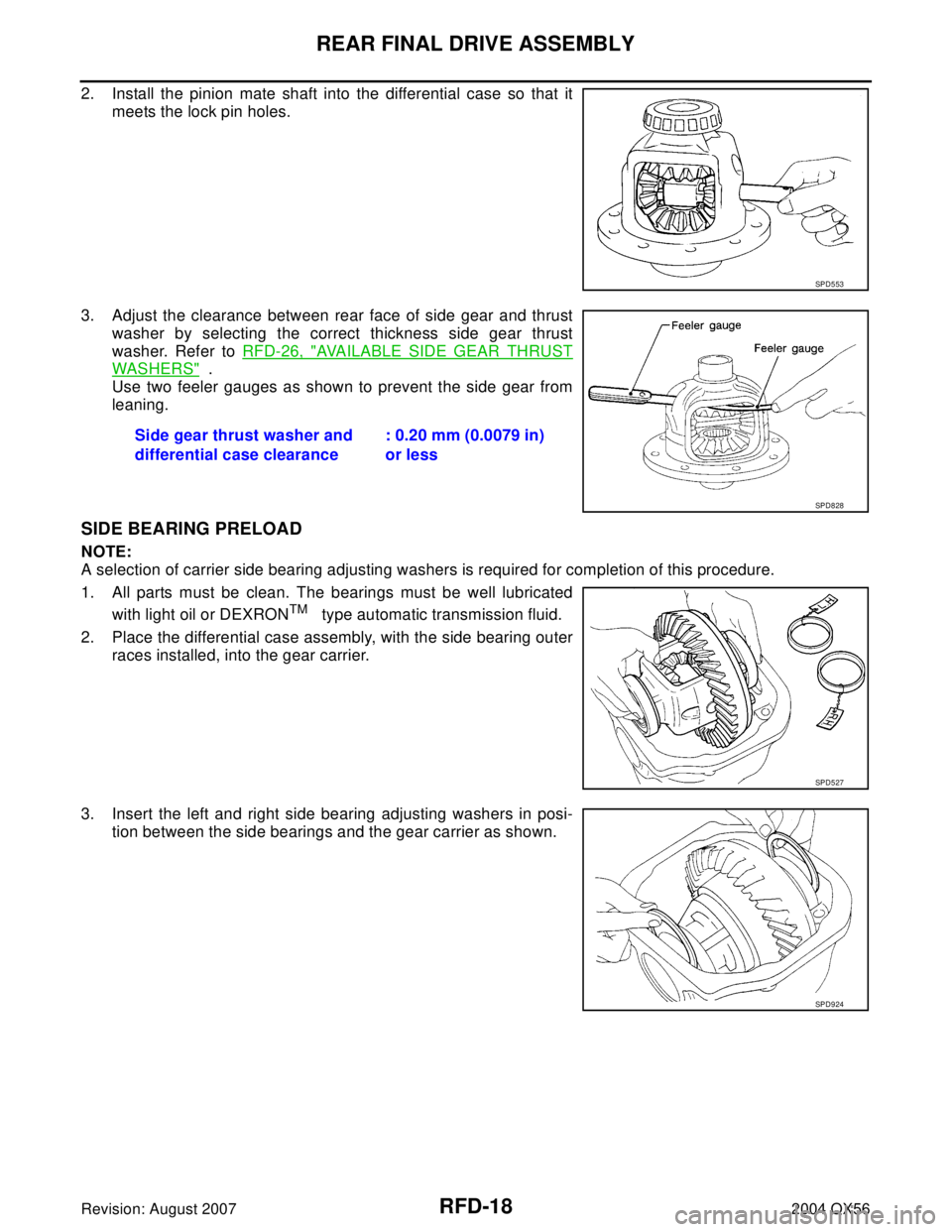
RFD-18
REAR FINAL DRIVE ASSEMBLY
Revision: August 20072004 QX56
2. Install the pinion mate shaft into the differential case so that it
meets the lock pin holes.
3. Adjust the clearance between rear face of side gear and thrust
washer by selecting the correct thickness side gear thrust
washer. Refer to RFD-26, "
AVAILABLE SIDE GEAR THRUST
WAS HER S" .
Use two feeler gauges as shown to prevent the side gear from
leaning.
SIDE BEARING PRELOAD
NOTE:
A selection of carrier side bearing adjusting washers is required for completion of this procedure.
1. All parts must be clean. The bearings must be well lubricated
with light oil or DEXRON
TM type automatic transmission fluid.
2. Place the differential case assembly, with the side bearing outer
races installed, into the gear carrier.
3. Insert the left and right side bearing adjusting washers in posi-
tion between the side bearings and the gear carrier as shown.
SPD5 53
Side gear thrust washer and
differential case clearance: 0.20 mm (0.0079 in)
or less
SPD8 28
SPD5 27
SPD9 24
Page 2850 of 3371
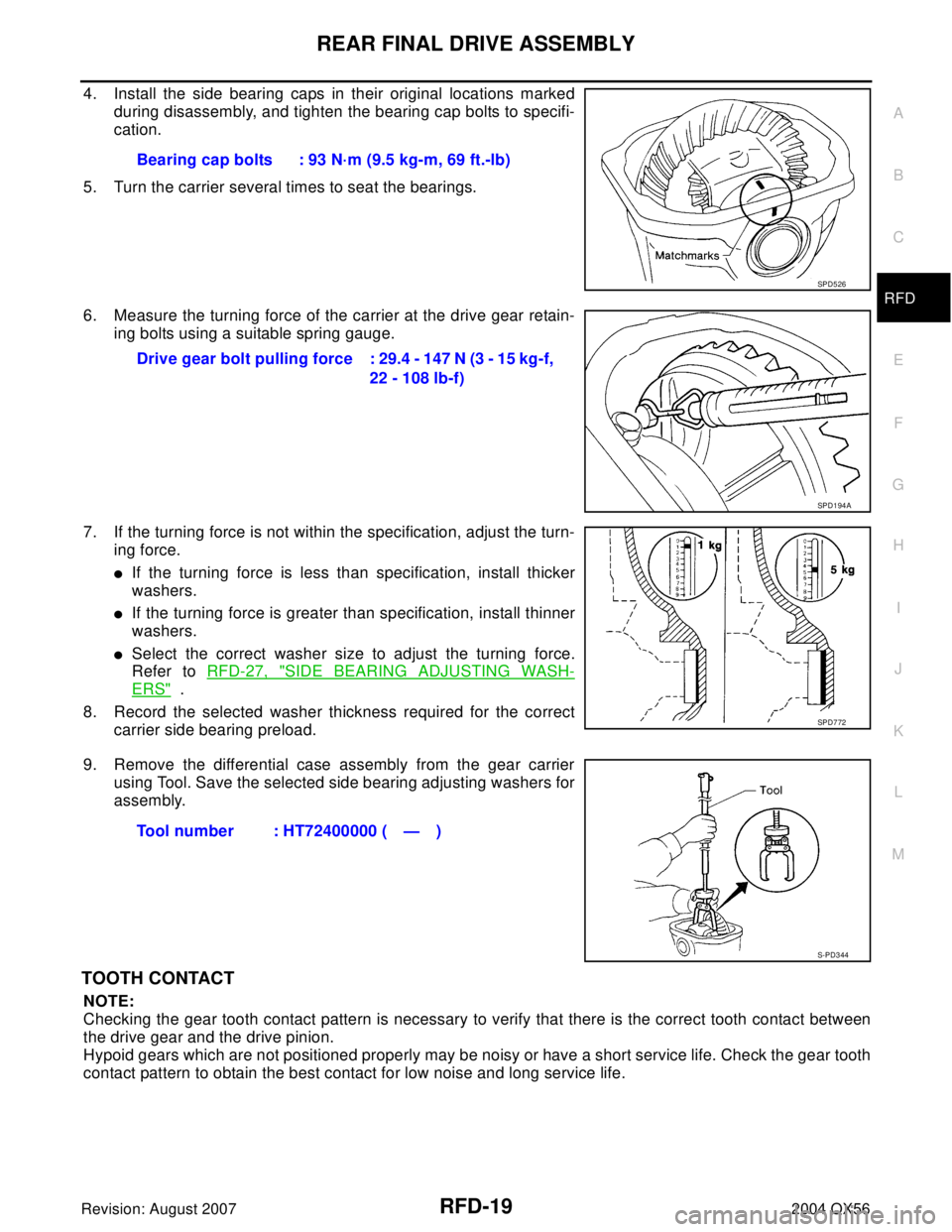
REAR FINAL DRIVE ASSEMBLY
RFD-19
C
E
F
G
H
I
J
K
L
MA
B
RFD
Revision: August 20072004 QX56
4. Install the side bearing caps in their original locations marked
during disassembly, and tighten the bearing cap bolts to specifi-
cation.
5. Turn the carrier several times to seat the bearings.
6. Measure the turning force of the carrier at the drive gear retain-
ing bolts using a suitable spring gauge.
7. If the turning force is not within the specification, adjust the turn-
ing force.
If the turning force is less than specification, install thicker
washers.
If the turning force is greater than specification, install thinner
washers.
Select the correct washer size to adjust the turning force.
Refer to RFD-27, "
SIDE BEARING ADJUSTING WASH-
ERS" .
8. Record the selected washer thickness required for the correct
carrier side bearing preload.
9. Remove the differential case assembly from the gear carrier
using Tool. Save the selected side bearing adjusting washers for
assembly.
TOOTH CONTACT
NOTE:
Checking the gear tooth contact pattern is necessary to verify that there is the correct tooth contact between
the drive gear and the drive pinion.
Hypoid gears which are not positioned properly may be noisy or have a short service life. Check the gear tooth
contact pattern to obtain the best contact for low noise and long service life.Bearing cap bolts : 93 N·m (9.5 kg-m, 69 ft.-lb)
SPD5 26
Drive gear bolt pulling force : 29.4 - 147 N (3 - 15 kg-f,
22 - 108 lb-f)
SPD1 94 A
SPD7 72
Tool number : HT72400000 ( — )
S-PD3 44
Page 2851 of 3371
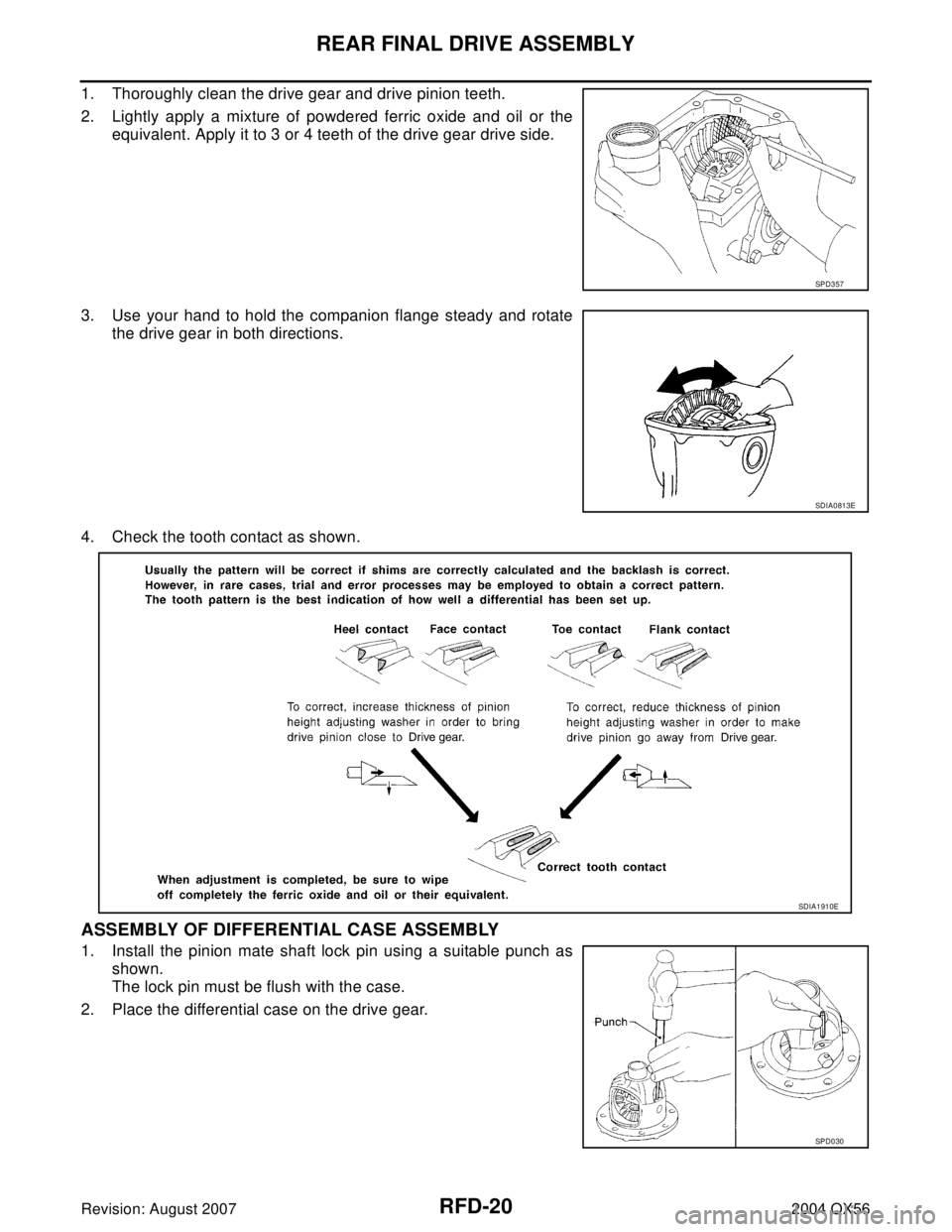
RFD-20
REAR FINAL DRIVE ASSEMBLY
Revision: August 20072004 QX56
1. Thoroughly clean the drive gear and drive pinion teeth.
2. Lightly apply a mixture of powdered ferric oxide and oil or the
equivalent. Apply it to 3 or 4 teeth of the drive gear drive side.
3. Use your hand to hold the companion flange steady and rotate
the drive gear in both directions.
4. Check the tooth contact as shown.
ASSEMBLY OF DIFFERENTIAL CASE ASSEMBLY
1. Install the pinion mate shaft lock pin using a suitable punch as
shown.
The lock pin must be flush with the case.
2. Place the differential case on the drive gear.
SPD3 57
SDIA0813E
SDIA1910E
SPD0 30
Page 2852 of 3371
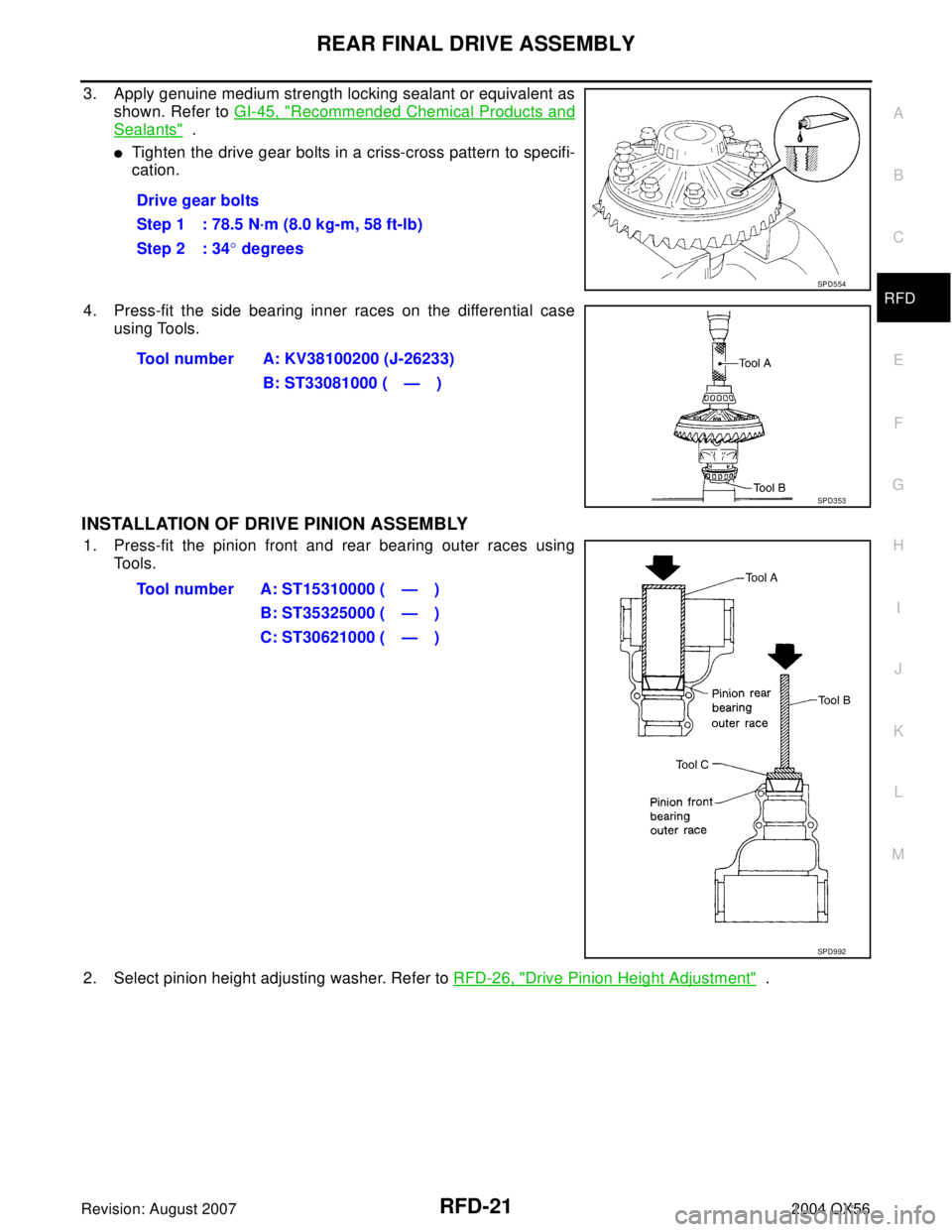
REAR FINAL DRIVE ASSEMBLY
RFD-21
C
E
F
G
H
I
J
K
L
MA
B
RFD
Revision: August 20072004 QX56
3. Apply genuine medium strength locking sealant or equivalent as
shown. Refer to GI-45, "
Recommended Chemical Products and
Sealants" .
Tighten the drive gear bolts in a criss-cross pattern to specifi-
cation.
4. Press-fit the side bearing inner races on the differential case
using Tools.
INSTALLATION OF DRIVE PINION ASSEMBLY
1. Press-fit the pinion front and rear bearing outer races using
Tools.
2. Select pinion height adjusting washer. Refer to RFD-26, "
Drive Pinion Height Adjustment" . Drive gear bolts
Step 1 : 78.5 N·m (8.0 kg-m, 58 ft-lb)
Step 2 : 34° degrees
SPD5 54
Tool number A: KV38100200 (J-26233)
B: ST33081000 ( — )
SPD3 53
Tool number A: ST15310000 ( — )
B: ST35325000 ( — )
C: ST30621000 ( — )
SPD9 92
Page 2853 of 3371
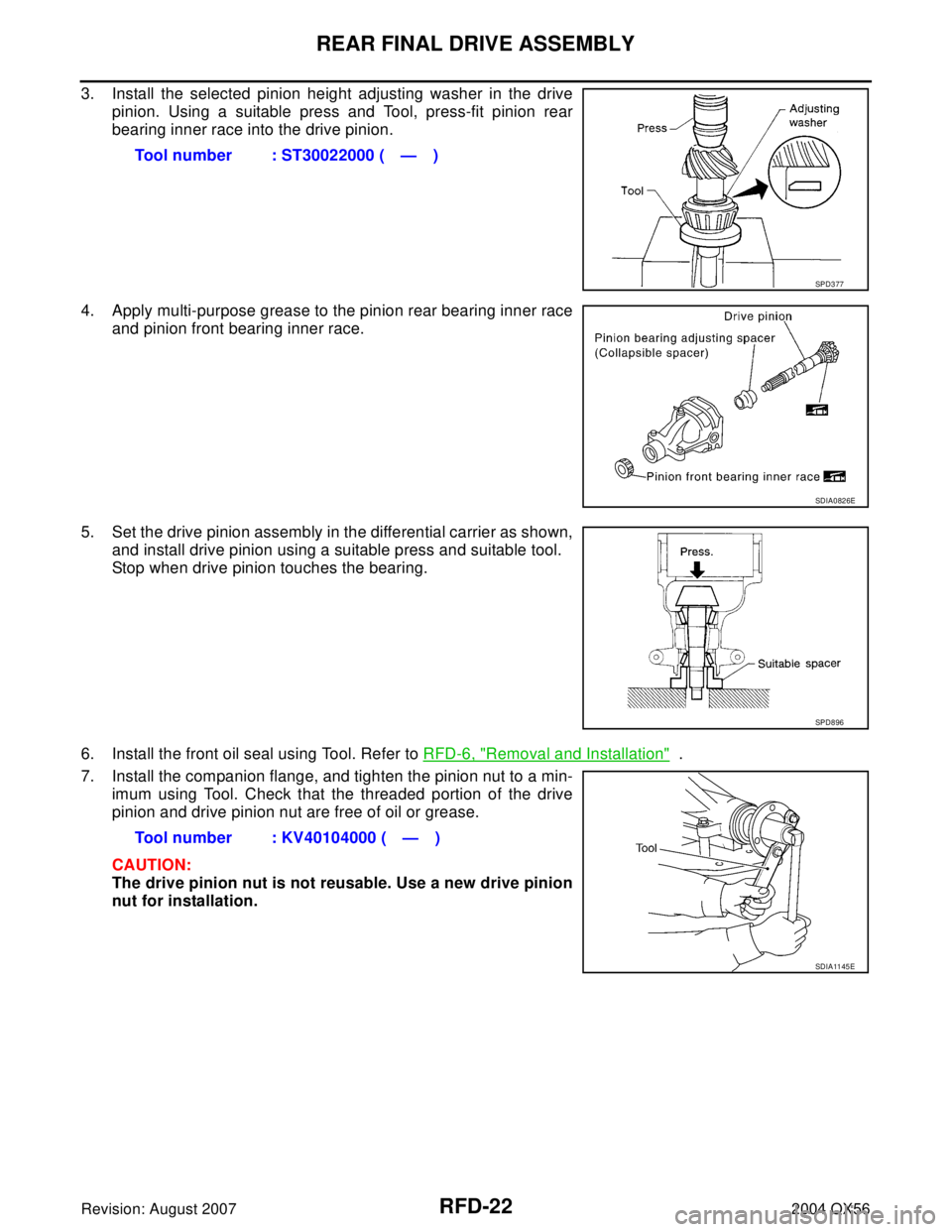
RFD-22
REAR FINAL DRIVE ASSEMBLY
Revision: August 20072004 QX56
3. Install the selected pinion height adjusting washer in the drive
pinion. Using a suitable press and Tool, press-fit pinion rear
bearing inner race into the drive pinion.
4. Apply multi-purpose grease to the pinion rear bearing inner race
and pinion front bearing inner race.
5. Set the drive pinion assembly in the differential carrier as shown,
and install drive pinion using a suitable press and suitable tool.
Stop when drive pinion touches the bearing.
6. Install the front oil seal using Tool. Refer to RFD-6, "
Removal and Installation" .
7. Install the companion flange, and tighten the pinion nut to a min-
imum using Tool. Check that the threaded portion of the drive
pinion and drive pinion nut are free of oil or grease.
CAUTION:
The drive pinion nut is not reusable. Use a new drive pinion
nut for installation. Tool number : ST30022000 ( — )
SPD3 77
SDIA0826E
SPD8 96
Tool number : KV40104000 ( — )
SDIA11 45 E
Page 2854 of 3371
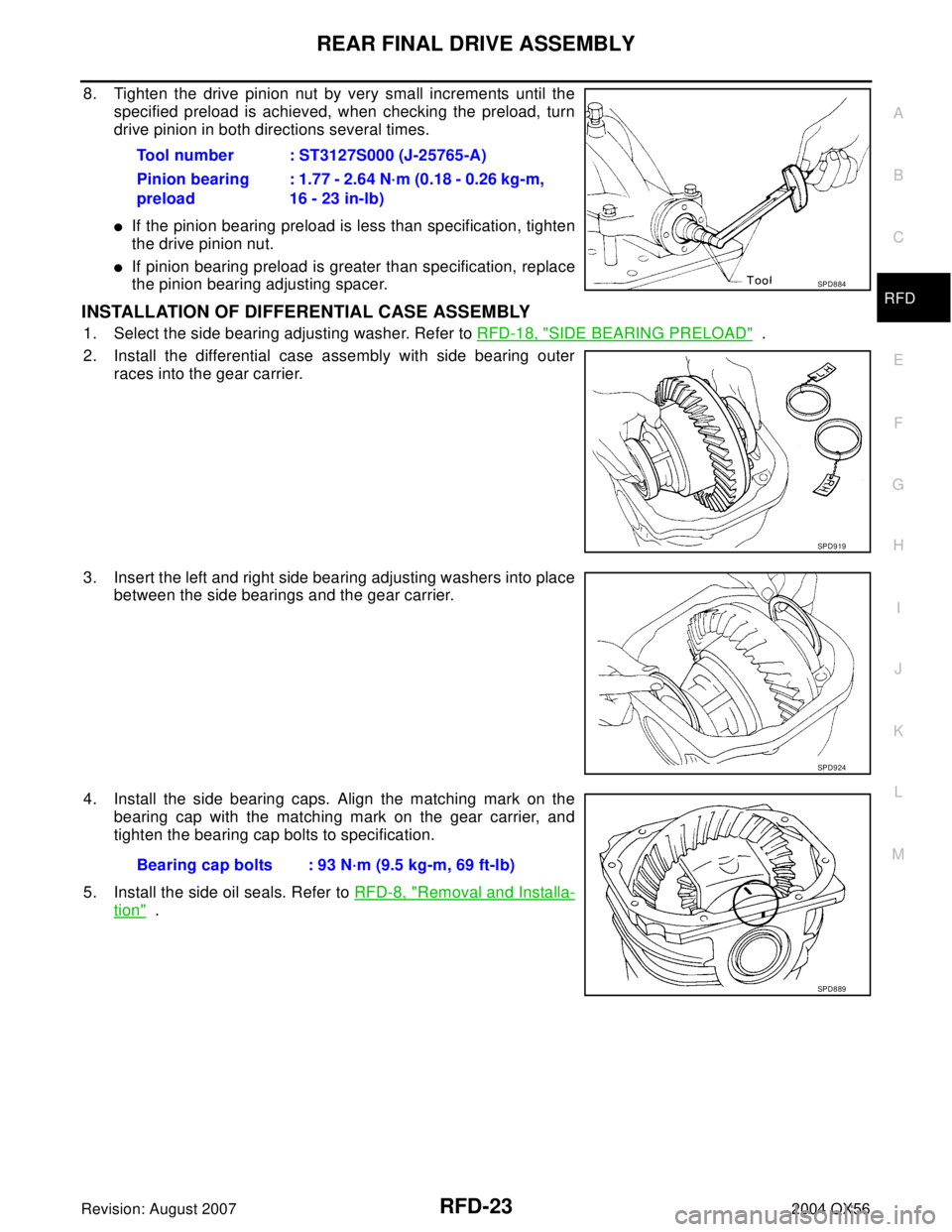
REAR FINAL DRIVE ASSEMBLY
RFD-23
C
E
F
G
H
I
J
K
L
MA
B
RFD
Revision: August 20072004 QX56
8. Tighten the drive pinion nut by very small increments until the
specified preload is achieved, when checking the preload, turn
drive pinion in both directions several times.
If the pinion bearing preload is less than specification, tighten
the drive pinion nut.
If pinion bearing preload is greater than specification, replace
the pinion bearing adjusting spacer.
INSTALLATION OF DIFFERENTIAL CASE ASSEMBLY
1. Select the side bearing adjusting washer. Refer to RFD-18, "SIDE BEARING PRELOAD" .
2. Install the differential case assembly with side bearing outer
races into the gear carrier.
3. Insert the left and right side bearing adjusting washers into place
between the side bearings and the gear carrier.
4. Install the side bearing caps. Align the matching mark on the
bearing cap with the matching mark on the gear carrier, and
tighten the bearing cap bolts to specification.
5. Install the side oil seals. Refer to RFD-8, "
Removal and Installa-
tion" . Tool number : ST3127S000 (J-25765-A)
Pinion bearing
preload: 1.77 - 2.64 N·m (0.18 - 0.26 kg-m,
16 - 23 in-lb)
SPD8 84
SPD9 19
SPD9 24
Bearing cap bolts : 93 N·m (9.5 kg-m, 69 ft-lb)
SPD8 89
Page 2856 of 3371
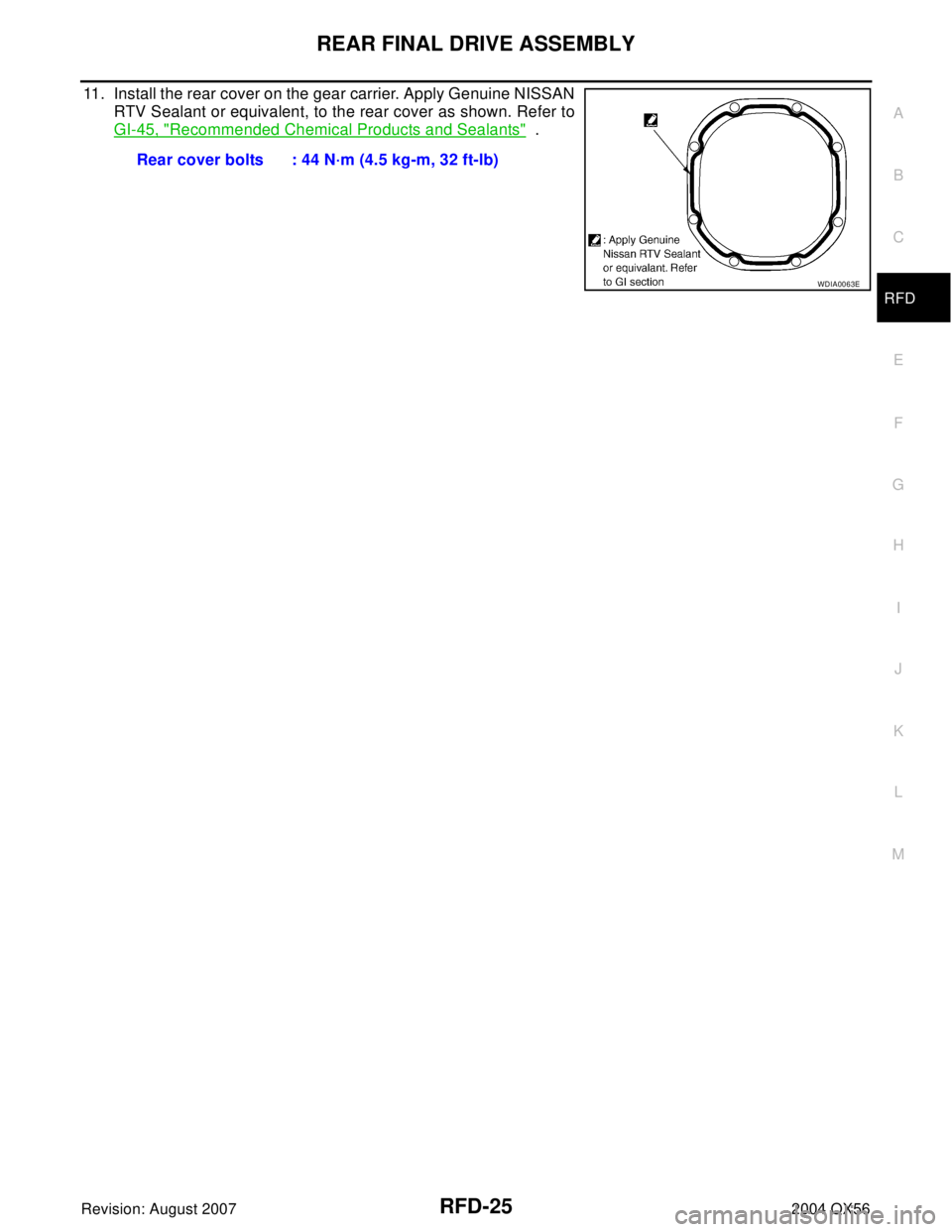
REAR FINAL DRIVE ASSEMBLY
RFD-25
C
E
F
G
H
I
J
K
L
MA
B
RFD
Revision: August 20072004 QX56
11. Install the rear cover on the gear carrier. Apply Genuine NISSAN
RTV Sealant or equivalent, to the rear cover as shown. Refer to
GI-45, "
Recommended Chemical Products and Sealants" .
Rear cover bolts : 44 N·m (4.5 kg-m, 32 ft-lb)
WDIA0063E
Page 2860 of 3371
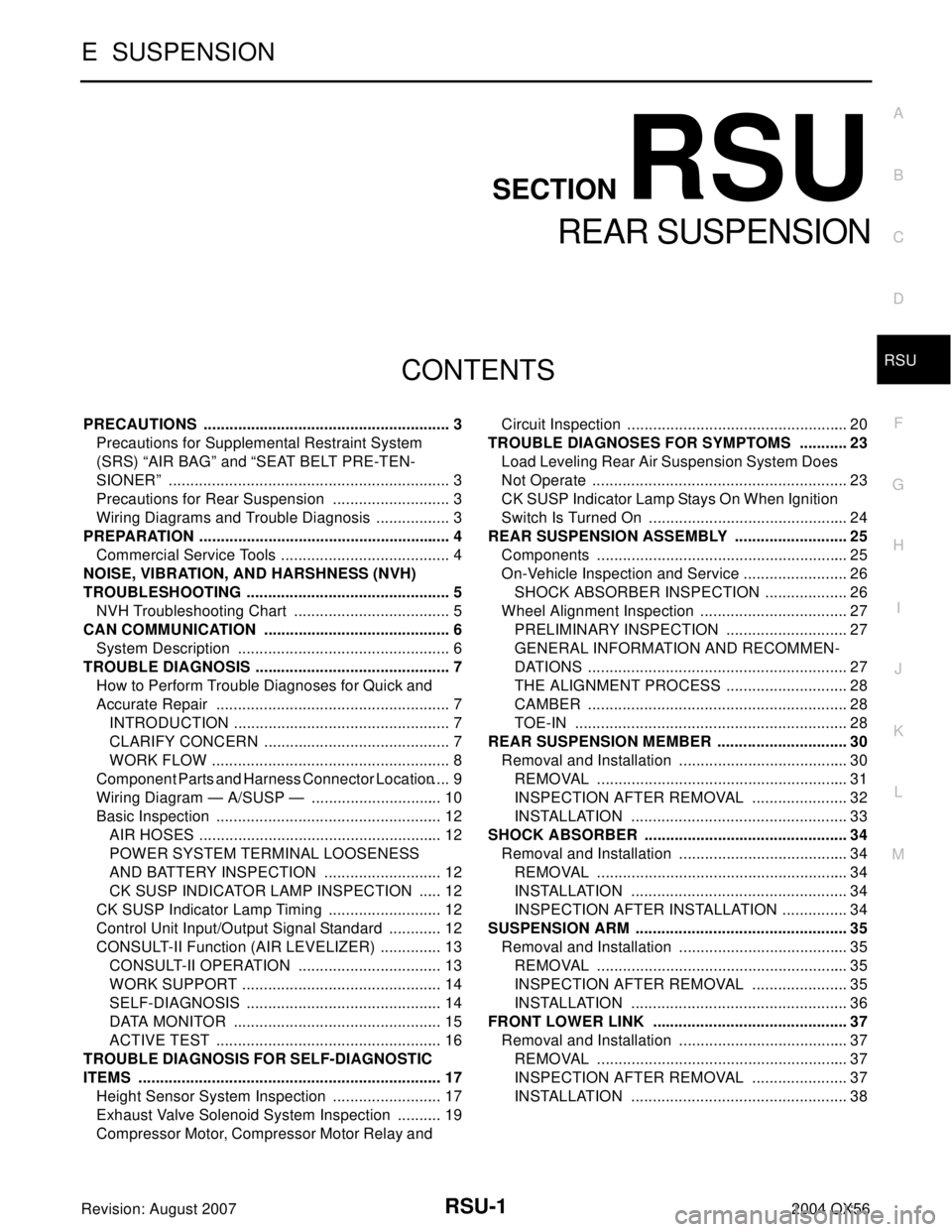
RSU-1
REAR SUSPENSION
E SUSPENSION
CONTENTS
C
D
F
G
H
I
J
K
L
M
SECTION RSU
A
B
RSU
Revision: August 20072004 QX56 PRECAUTIONS .......................................................... 3
Precautions for Supplemental Restraint System
(SRS) “AIR BAG” and “SEAT BELT PRE-TEN-
SIONER” .................................................................. 3
Precautions for Rear Suspension ............................ 3
Wiring Diagrams and Trouble Diagnosis .................. 3
PREPARATION ........................................................... 4
Commercial Service Tools ........................................ 4
NOISE, VIBRATION, AND HARSHNESS (NVH)
TROUBLESHOOTING ................................................ 5
NVH Troubleshooting Chart ..................................... 5
CAN COMMUNICATION ............................................ 6
System Description .................................................. 6
TROUBLE DIAGNOSIS .............................................. 7
How to Perform Trouble Diagnoses for Quick and
Accurate Repair ....................................................... 7
INTRODUCTION ................................................... 7
CLARIFY CONCERN ............................................ 7
WORK FLOW ........................................................ 8
Component Parts and Harness Connector Location ..... 9
Wiring Diagram — A/SUSP — ............................... 10
Basic Inspection ..................................................... 12
AIR HOSES ......................................................... 12
POWER SYSTEM TERMINAL LOOSENESS
AND BATTERY INSPECTION ............................ 12
CK SUSP INDICATOR LAMP INSPECTION ...... 12
CK SUSP Indicator Lamp Timing ........................... 12
Control Unit Input/Output Signal Standard ............. 12
CONSULT-II Function (AIR LEVELIZER) ............... 13
CONSULT-II OPERATION .................................. 13
WORK SUPPORT ............................................... 14
SELF-DIAGNOSIS .............................................. 14
DATA MONITOR ................................................. 15
ACTIVE TEST ..................................................... 16
TROUBLE DIAGNOSIS FOR SELF-DIAGNOSTIC
ITEMS ....................................................................... 17
Height Sensor System Inspection .......................... 17
Exhaust Valve Solenoid System Inspection ........... 19
Compressor Motor, Compressor Motor Relay and Circuit Inspection .................................................... 20
TROUBLE DIAGNOSES FOR SYMPTOMS ............ 23
Load Leveling Rear Air Suspension System Does
Not Operate ............................................................ 23
CK SUSP Indicator Lamp Stays On When Ignition
Switch Is Turned On ............................................... 24
REAR SUSPENSION ASSEMBLY ........................... 25
Components ........................................................... 25
On-Vehicle Inspection and Service ......................... 26
SHOCK ABSORBER INSPECTION .................... 26
Wheel Alignment Inspection ................................... 27
PRELIMINARY INSPECTION ............................. 27
GENERAL INFORMATION AND RECOMMEN-
DATIONS ............................................................. 27
THE ALIGNMENT PROCESS ............................. 28
CAMBER ............................................................. 28
TOE-IN ................................................................ 28
REAR SUSPENSION MEMBER ............................... 30
Removal and Installation ........................................ 30
REMOVAL ........................................................... 31
INSPECTION AFTER REMOVAL ....................... 32
INSTALLATION ................................................... 33
SHOCK ABSORBER ................................................ 34
Removal and Installation ........................................ 34
REMOVAL ........................................................... 34
INSTALLATION ................................................... 34
INSPECTION AFTER INSTALLATION ................ 34
SUSPENSION ARM .................................................. 35
Removal and Installation ........................................ 35
REMOVAL ........................................................... 35
INSPECTION AFTER REMOVAL ....................... 35
INSTALLATION ................................................... 36
FRONT LOWER LINK .............................................. 37
Removal and Installation ........................................ 37
REMOVAL ........................................................... 37
INSPECTION AFTER REMOVAL ....................... 37
INSTALLATION ................................................... 38
Page 2861 of 3371
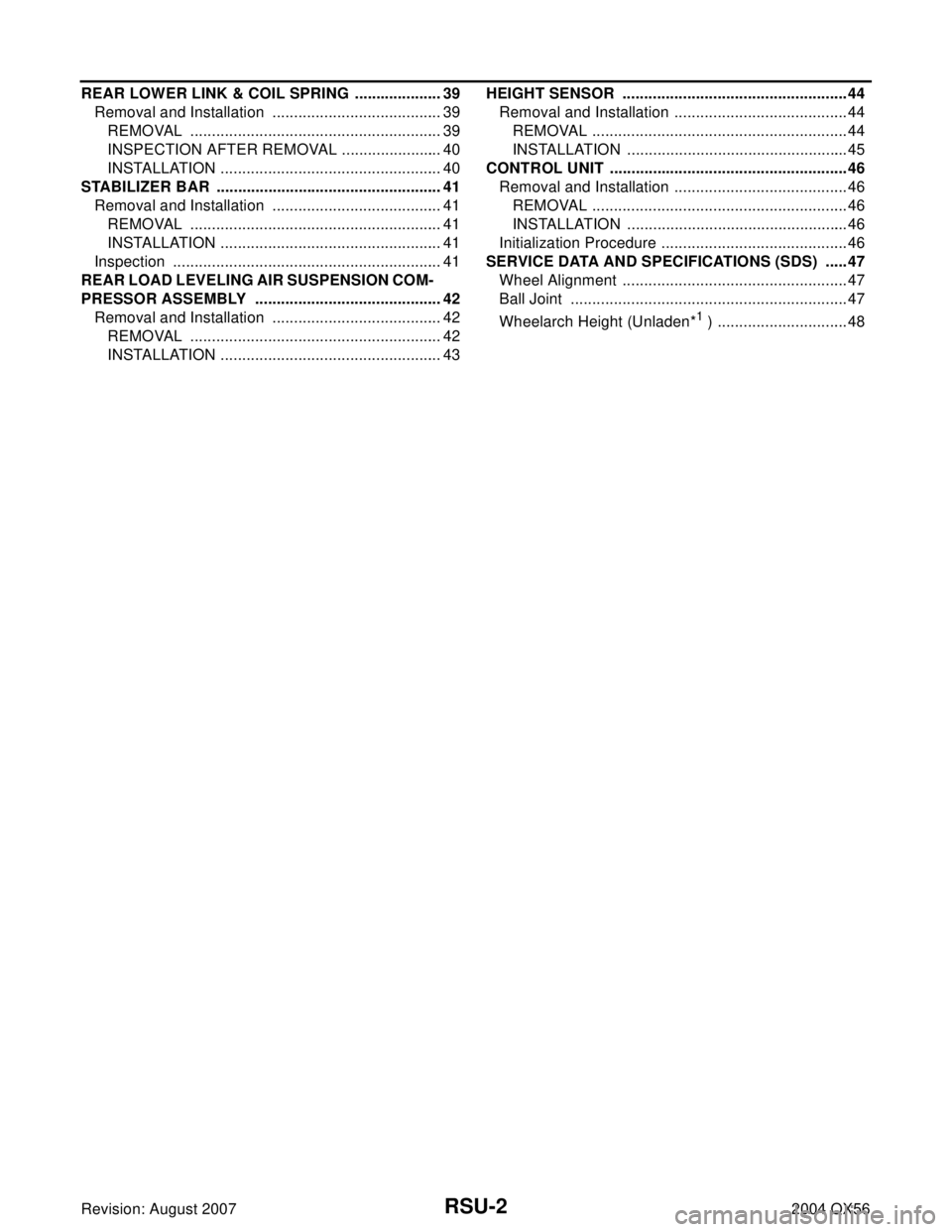
RSU-2Revision: August 20072004 QX56 REAR LOWER LINK & COIL SPRING ..................... 39
Removal and Installation ........................................ 39
REMOVAL ........................................................... 39
INSPECTION AFTER REMOVAL ........................ 40
INSTALLATION .................................................... 40
STABILIZER BAR ..................................................... 41
Removal and Installation ........................................ 41
REMOVAL ........................................................... 41
INSTALLATION .................................................... 41
Inspection ............................................................... 41
REAR LOAD LEVELING AIR SUSPENSION COM-
PRESSOR ASSEMBLY ............................................ 42
Removal and Installation ........................................ 42
REMOVAL ........................................................... 42
INSTALLATION .................................................... 43HEIGHT SENSOR .....................................................44
Removal and Installation .........................................44
REMOVAL ............................................................44
INSTALLATION ....................................................45
CONTROL UNIT ........................................................46
Removal and Installation .........................................46
REMOVAL ............................................................46
INSTALLATION ....................................................46
Initialization Procedure ............................................46
SERVICE DATA AND SPECIFICATIONS (SDS) ......47
Wheel Alignment .....................................................47
Ball Joint .................................................................47
Wheelarch Height (Unladen*
1 ) ...............................48
Page 2862 of 3371
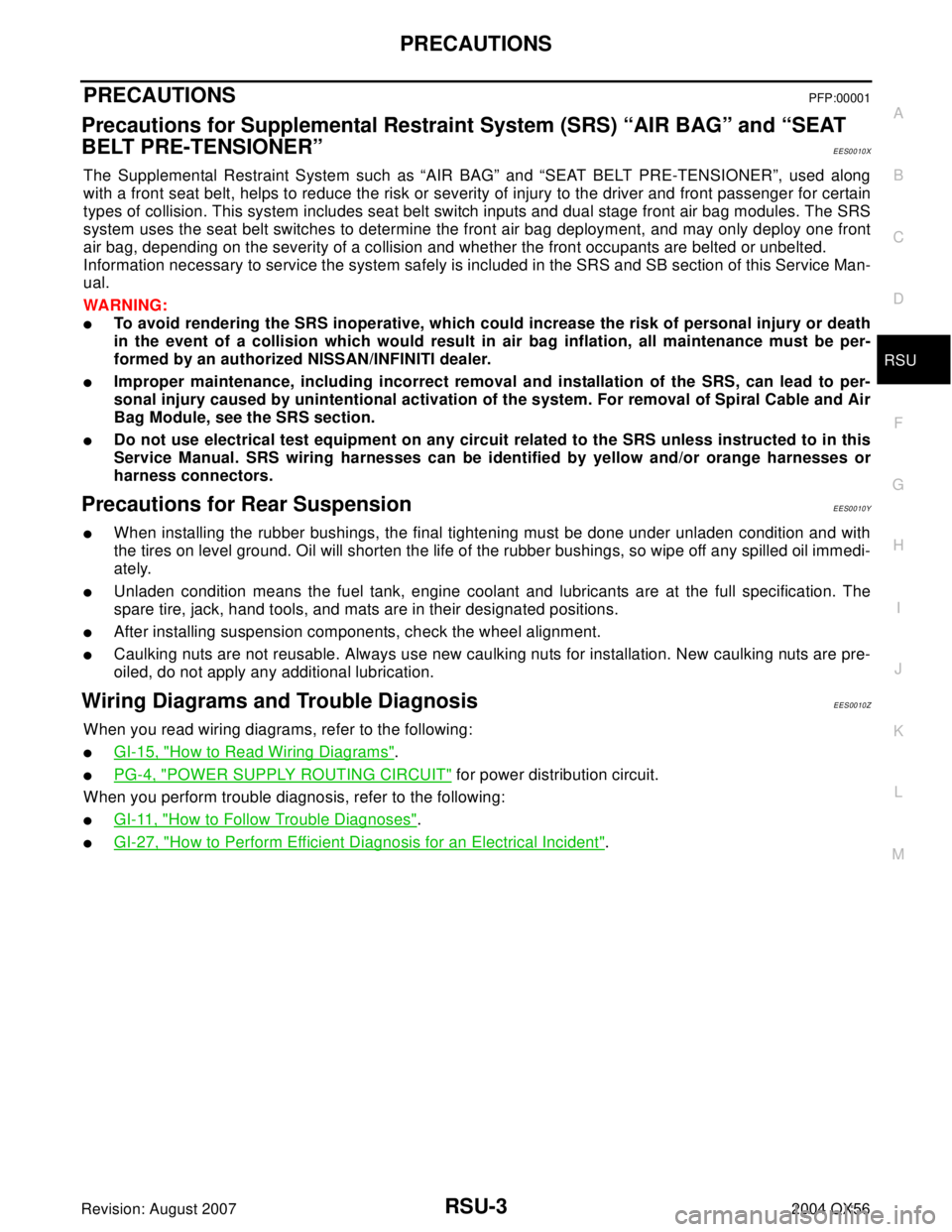
PRECAUTIONS
RSU-3
C
D
F
G
H
I
J
K
L
MA
B
RSU
Revision: August 20072004 QX56
PRECAUTIONSPFP:00001
Precautions for Supplemental Restraint System (SRS) “AIR BAG” and “SEAT
BELT PRE-TENSIONER”
EES0010X
The Supplemental Restraint System such as “AIR BAG” and “SEAT BELT PRE-TENSIONER”, used along
with a front seat belt, helps to reduce the risk or severity of injury to the driver and front passenger for certain
types of collision. This system includes seat belt switch inputs and dual stage front air bag modules. The SRS
system uses the seat belt switches to determine the front air bag deployment, and may only deploy one front
air bag, depending on the severity of a collision and whether the front occupants are belted or unbelted.
Information necessary to service the system safely is included in the SRS and SB section of this Service Man-
ual.
WA RN ING:
To avoid rendering the SRS inoperative, which could increase the risk of personal injury or death
in the event of a collision which would result in air bag inflation, all maintenance must be per-
formed by an authorized NISSAN/INFINITI dealer.
Improper maintenance, including incorrect removal and installation of the SRS, can lead to per-
sonal injury caused by unintentional activation of the system. For removal of Spiral Cable and Air
Bag Module, see the SRS section.
Do not use electrical test equipment on any circuit related to the SRS unless instructed to in this
Service Manual. SRS wiring harnesses can be identified by yellow and/or orange harnesses or
harness connectors.
Precautions for Rear SuspensionEES0010Y
When installing the rubber bushings, the final tightening must be done under unladen condition and with
the tires on level ground. Oil will shorten the life of the rubber bushings, so wipe off any spilled oil immedi-
ately.
Unladen condition means the fuel tank, engine coolant and lubricants are at the full specification. The
spare tire, jack, hand tools, and mats are in their designated positions.
After installing suspension components, check the wheel alignment.
Caulking nuts are not reusable. Always use new caulking nuts for installation. New caulking nuts are pre-
oiled, do not apply any additional lubrication.
Wiring Diagrams and Trouble DiagnosisEES0010Z
When you read wiring diagrams, refer to the following:
GI-15, "How to Read Wiring Diagrams".
PG-4, "POWER SUPPLY ROUTING CIRCUIT" for power distribution circuit.
When you perform trouble diagnosis, refer to the following:
GI-11, "How to Follow Trouble Diagnoses".
GI-27, "How to Perform Efficient Diagnosis for an Electrical Incident".