service INFINITI QX56 2004 Factory Service Manual
[x] Cancel search | Manufacturer: INFINITI, Model Year: 2004, Model line: QX56, Model: INFINITI QX56 2004Pages: 3371, PDF Size: 78.5 MB
Page 1522 of 3371
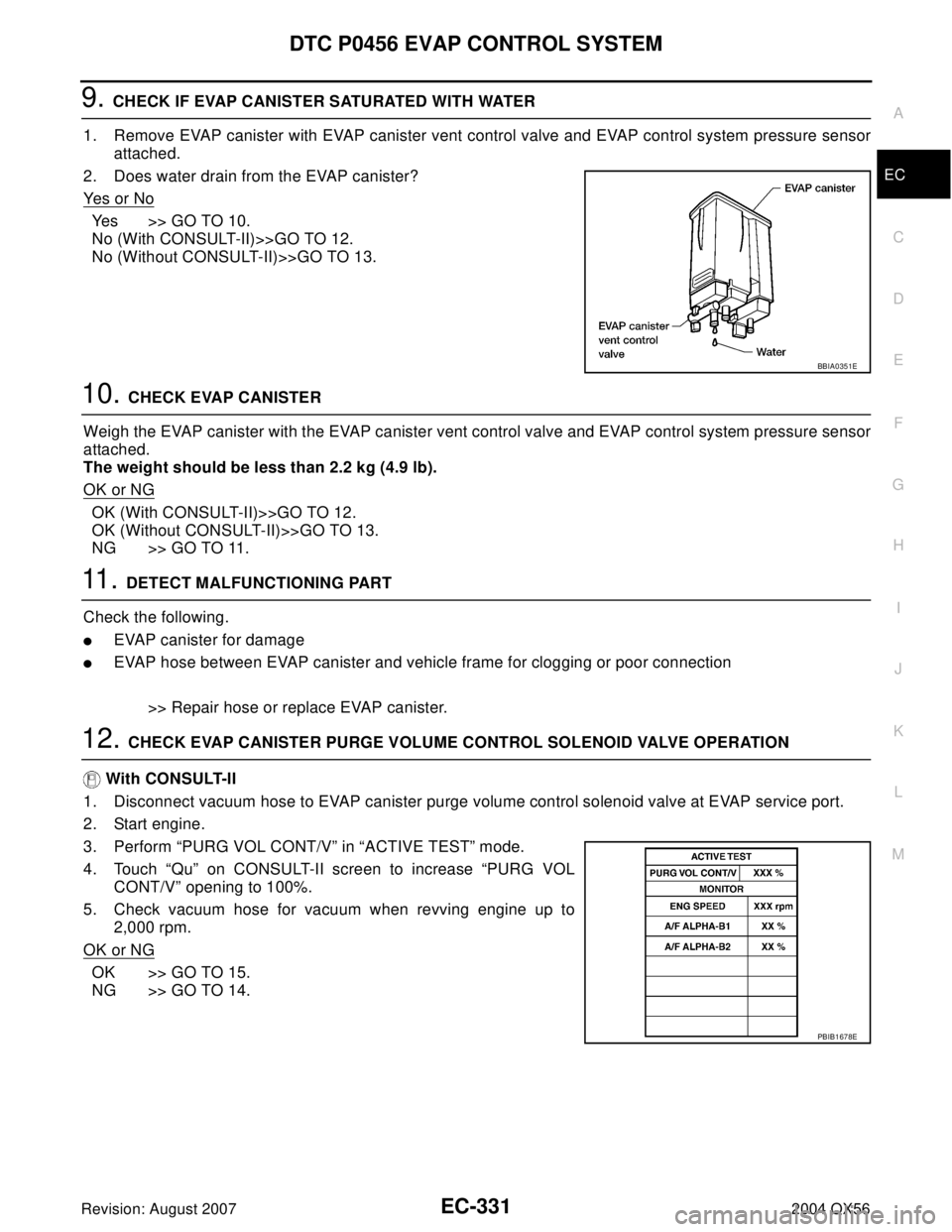
DTC P0456 EVAP CONTROL SYSTEM
EC-331
C
D
E
F
G
H
I
J
K
L
MA
EC
Revision: August 20072004 QX56
9. CHECK IF EVAP CANISTER SATURATED WITH WATER
1. Remove EVAP canister with EVAP canister vent control valve and EVAP control system pressure sensor
attached.
2. Does water drain from the EVAP canister?
Ye s o r N o
Yes >> GO TO 10.
No (With CONSULT-II)>>GO TO 12.
No (Without CONSULT-II)>>GO TO 13.
10. CHECK EVAP CANISTER
Weigh the EVAP canister with the EVAP canister vent control valve and EVAP control system pressure sensor
attached.
The weight should be less than 2.2 kg (4.9 lb).
OK or NG
OK (With CONSULT-II)>>GO TO 12.
OK (Without CONSULT-II)>>GO TO 13.
NG >> GO TO 11.
11 . DETECT MALFUNCTIONING PART
Check the following.
EVAP canister for damage
EVAP hose between EVAP canister and vehicle frame for clogging or poor connection
>> Repair hose or replace EVAP canister.
12. CHECK EVAP CANISTER PURGE VOLUME CONTROL SOLENOID VALVE OPERATION
With CONSULT-II
1. Disconnect vacuum hose to EVAP canister purge volume control solenoid valve at EVAP service port.
2. Start engine.
3. Perform “PURG VOL CONT/V” in “ACTIVE TEST” mode.
4. Touch “Qu” on CONSULT-II screen to increase “PURG VOL
CONT/V” opening to 100%.
5. Check vacuum hose for vacuum when revving engine up to
2,000 rpm.
OK or NG
OK >> GO TO 15.
NG >> GO TO 14.
BBIA0351E
PBIB1678E
Page 1523 of 3371
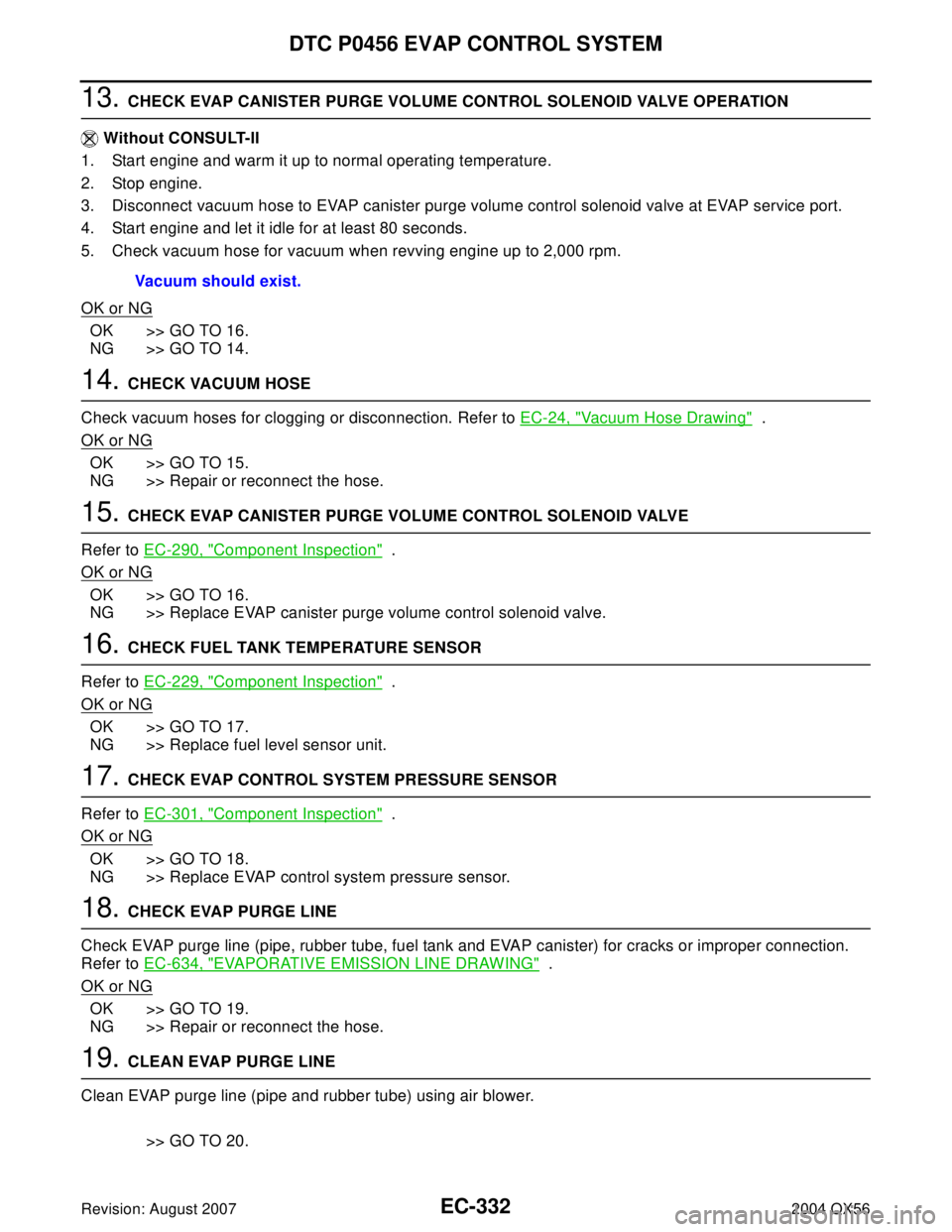
EC-332Revision: August 2007
DTC P0456 EVAP CONTROL SYSTEM
2004 QX56
13. CHECK EVAP CANISTER PURGE VOLUME CONTROL SOLENOID VALVE OPERATION
Without CONSULT-II
1. Start engine and warm it up to normal operating temperature.
2. Stop engine.
3. Disconnect vacuum hose to EVAP canister purge volume control solenoid valve at EVAP service port.
4. Start engine and let it idle for at least 80 seconds.
5. Check vacuum hose for vacuum when revving engine up to 2,000 rpm.
OK or NG
OK >> GO TO 16.
NG >> GO TO 14.
14. CHECK VACUUM HOSE
Check vacuum hoses for clogging or disconnection. Refer to EC-24, "
Vacuum Hose Drawing" .
OK or NG
OK >> GO TO 15.
NG >> Repair or reconnect the hose.
15. CHECK EVAP CANISTER PURGE VOLUME CONTROL SOLENOID VALVE
Refer to EC-290, "
Component Inspection" .
OK or NG
OK >> GO TO 16.
NG >> Replace EVAP canister purge volume control solenoid valve.
16. CHECK FUEL TANK TEMPERATURE SENSOR
Refer to EC-229, "
Component Inspection" .
OK or NG
OK >> GO TO 17.
NG >> Replace fuel level sensor unit.
17. CHECK EVAP CONTROL SYSTEM PRESSURE SENSOR
Refer to EC-301, "
Component Inspection" .
OK or NG
OK >> GO TO 18.
NG >> Replace EVAP control system pressure sensor.
18. CHECK EVAP PURGE LINE
Check EVAP purge line (pipe, rubber tube, fuel tank and EVAP canister) for cracks or improper connection.
Refer to EC-634, "
EVAPORATIVE EMISSION LINE DRAWING" .
OK or NG
OK >> GO TO 19.
NG >> Repair or reconnect the hose.
19. CLEAN EVAP PURGE LINE
Clean EVAP purge line (pipe and rubber tube) using air blower.
>> GO TO 20. Vacuum should exist.
Page 1533 of 3371
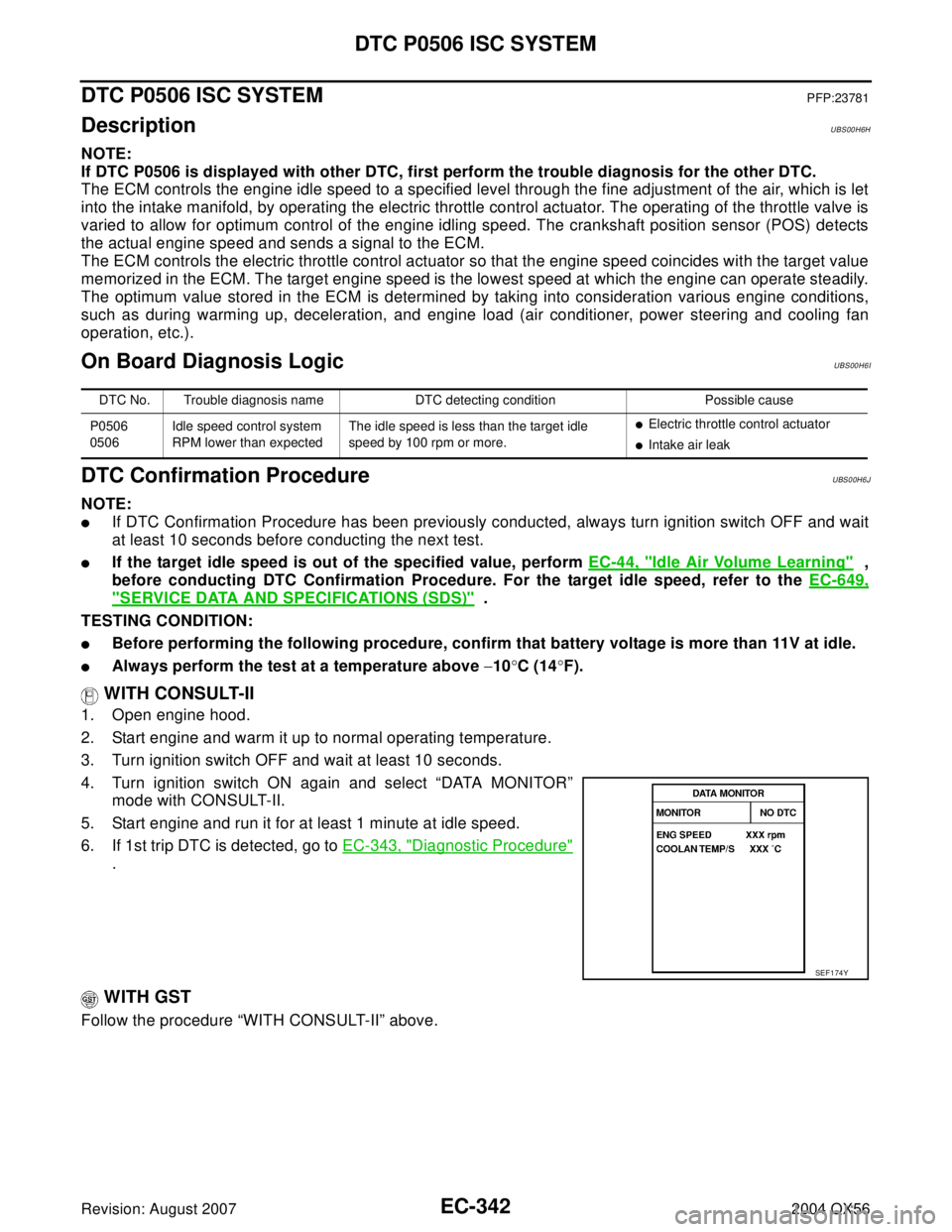
EC-342Revision: August 2007
DTC P0506 ISC SYSTEM
2004 QX56
DTC P0506 ISC SYSTEMPFP:23781
DescriptionUBS00H6H
NOTE:
If DTC P0506 is displayed with other DTC, first perform the trouble diagnosis for the other DTC.
The ECM controls the engine idle speed to a specified level through the fine adjustment of the air, which is let
into the intake manifold, by operating the electric throttle control actuator. The operating of the throttle valve is
varied to allow for optimum control of the engine idling speed. The crankshaft position sensor (POS) detects
the actual engine speed and sends a signal to the ECM.
The ECM controls the electric throttle control actuator so that the engine speed coincides with the target value
memorized in the ECM. The target engine speed is the lowest speed at which the engine can operate steadily.
The optimum value stored in the ECM is determined by taking into consideration various engine conditions,
such as during warming up, deceleration, and engine load (air conditioner, power steering and cooling fan
operation, etc.).
On Board Diagnosis LogicUBS00H6I
DTC Confirmation ProcedureUBS00H6J
NOTE:
If DTC Confirmation Procedure has been previously conducted, always turn ignition switch OFF and wait
at least 10 seconds before conducting the next test.
If the target idle speed is out of the specified value, perform EC-44, "Idle Air Volume Learning" ,
before conducting DTC Confirmation Procedure. For the target idle speed, refer to the EC-649,
"SERVICE DATA AND SPECIFICATIONS (SDS)" .
TESTING CONDITION:
Before performing the following procedure, confirm that battery voltage is more than 11V at idle.
Always perform the test at a temperature above −10°C (14°F).
WITH CONSULT-II
1. Open engine hood.
2. Start engine and warm it up to normal operating temperature.
3. Turn ignition switch OFF and wait at least 10 seconds.
4. Turn ignition switch ON again and select “DATA MONITOR”
mode with CONSULT-II.
5. Start engine and run it for at least 1 minute at idle speed.
6. If 1st trip DTC is detected, go to EC-343, "
Diagnostic Procedure"
.
WITH GST
Follow the procedure “WITH CONSULT-II” above.
DTC No. Trouble diagnosis name DTC detecting condition Possible cause
P0506
0506Idle speed control system
RPM lower than expectedThe idle speed is less than the target idle
speed by 100 rpm or more.
Electric throttle control actuator
Intake air leak
SEF 1 74 Y
Page 1535 of 3371
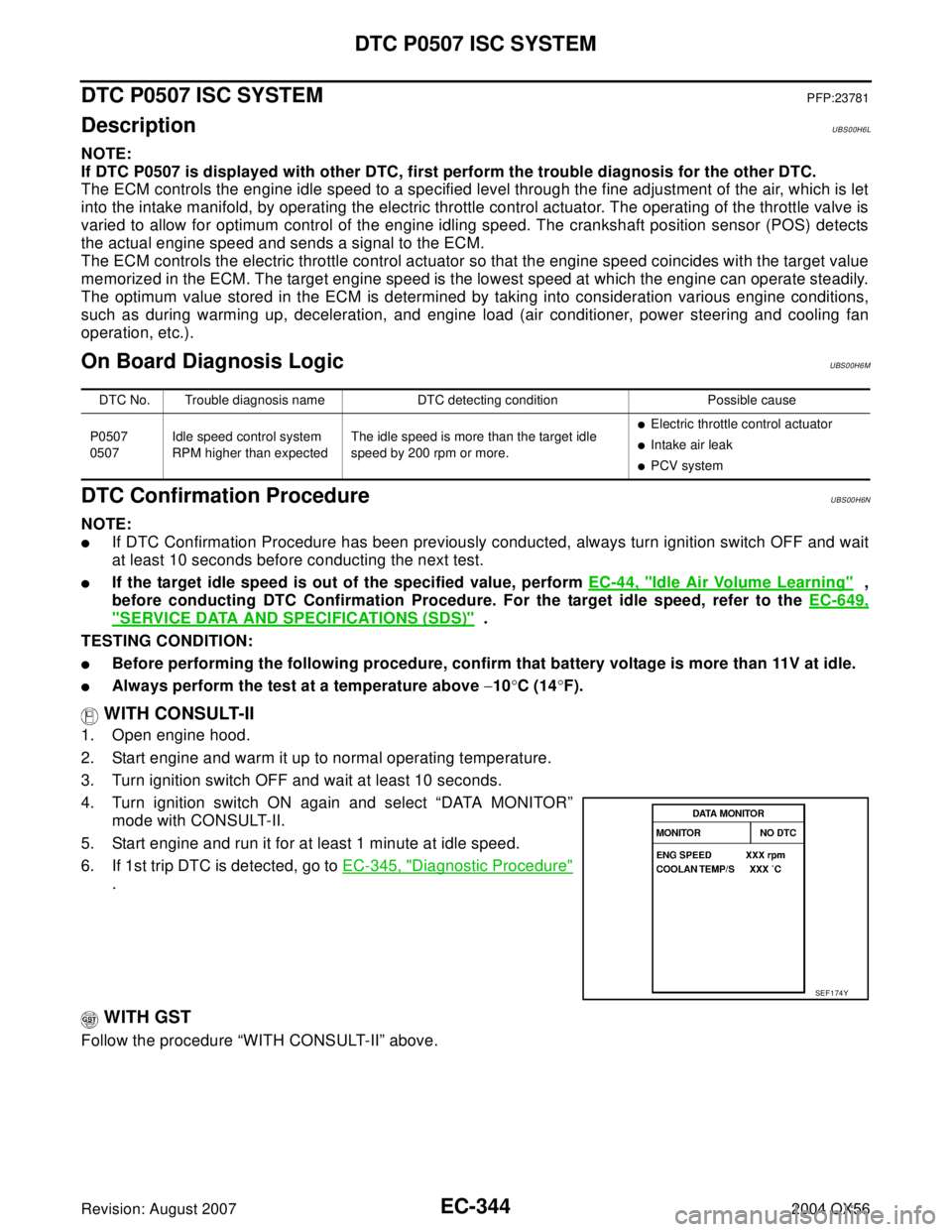
EC-344Revision: August 2007
DTC P0507 ISC SYSTEM
2004 QX56
DTC P0507 ISC SYSTEMPFP:23781
DescriptionUBS00H6L
NOTE:
If DTC P0507 is displayed with other DTC, first perform the trouble diagnosis for the other DTC.
The ECM controls the engine idle speed to a specified level through the fine adjustment of the air, which is let
into the intake manifold, by operating the electric throttle control actuator. The operating of the throttle valve is
varied to allow for optimum control of the engine idling speed. The crankshaft position sensor (POS) detects
the actual engine speed and sends a signal to the ECM.
The ECM controls the electric throttle control actuator so that the engine speed coincides with the target value
memorized in the ECM. The target engine speed is the lowest speed at which the engine can operate steadily.
The optimum value stored in the ECM is determined by taking into consideration various engine conditions,
such as during warming up, deceleration, and engine load (air conditioner, power steering and cooling fan
operation, etc.).
On Board Diagnosis LogicUBS00H6M
DTC Confirmation ProcedureUBS00H6N
NOTE:
If DTC Confirmation Procedure has been previously conducted, always turn ignition switch OFF and wait
at least 10 seconds before conducting the next test.
If the target idle speed is out of the specified value, perform EC-44, "Idle Air Volume Learning" ,
before conducting DTC Confirmation Procedure. For the target idle speed, refer to the EC-649,
"SERVICE DATA AND SPECIFICATIONS (SDS)" .
TESTING CONDITION:
Before performing the following procedure, confirm that battery voltage is more than 11V at idle.
Always perform the test at a temperature above −10°C (14°F).
WITH CONSULT-II
1. Open engine hood.
2. Start engine and warm it up to normal operating temperature.
3. Turn ignition switch OFF and wait at least 10 seconds.
4. Turn ignition switch ON again and select “DATA MONITOR”
mode with CONSULT-II.
5. Start engine and run it for at least 1 minute at idle speed.
6. If 1st trip DTC is detected, go to EC-345, "
Diagnostic Procedure"
.
WITH GST
Follow the procedure “WITH CONSULT-II” above.
DTC No. Trouble diagnosis name DTC detecting condition Possible cause
P0507
0507Idle speed control system
RPM higher than expectedThe idle speed is more than the target idle
speed by 200 rpm or more.
Electric throttle control actuator
Intake air leak
PCV system
SEF 1 74 Y
Page 1828 of 3371
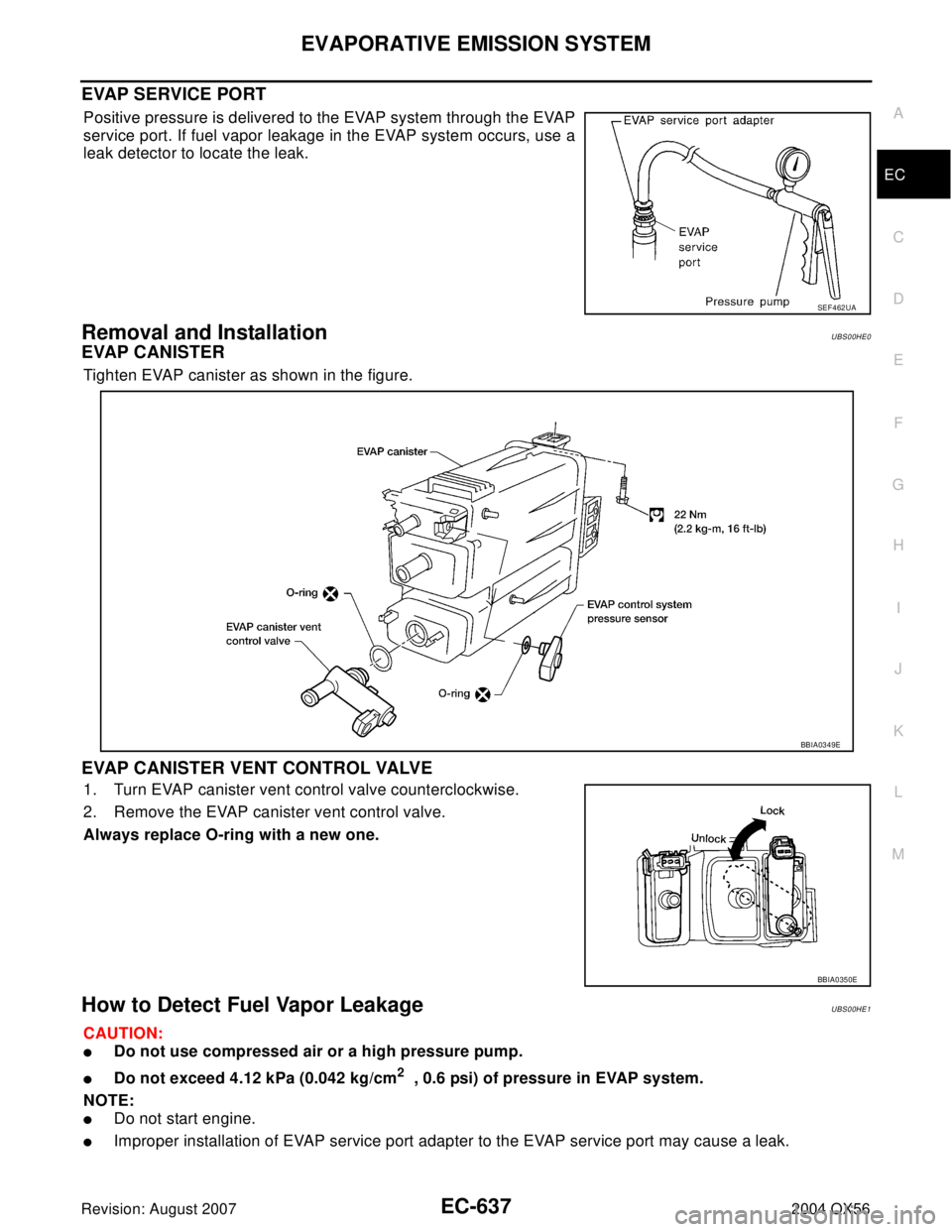
EVAPORATIVE EMISSION SYSTEM
EC-637
C
D
E
F
G
H
I
J
K
L
MA
EC
Revision: August 20072004 QX56
EVAP SERVICE PORT
Positive pressure is delivered to the EVAP system through the EVAP
service port. If fuel vapor leakage in the EVAP system occurs, use a
leak detector to locate the leak.
Removal and InstallationUBS00HE0
EVAP CANISTER
Tighten EVAP canister as shown in the figure.
EVAP CANISTER VENT CONTROL VALVE
1. Turn EVAP canister vent control valve counterclockwise.
2. Remove the EVAP canister vent control valve.
Always replace O-ring with a new one.
How to Detect Fuel Vapor LeakageUBS00HE1
CAUTION:
Do not use compressed air or a high pressure pump.
Do not exceed 4.12 kPa (0.042 kg/cm2 , 0.6 psi) of pressure in EVAP system.
NOTE:
Do not start engine.
Improper installation of EVAP service port adapter to the EVAP service port may cause a leak.
SEF 4 62 UA
BBIA0349E
BBIA0350E
Page 1829 of 3371
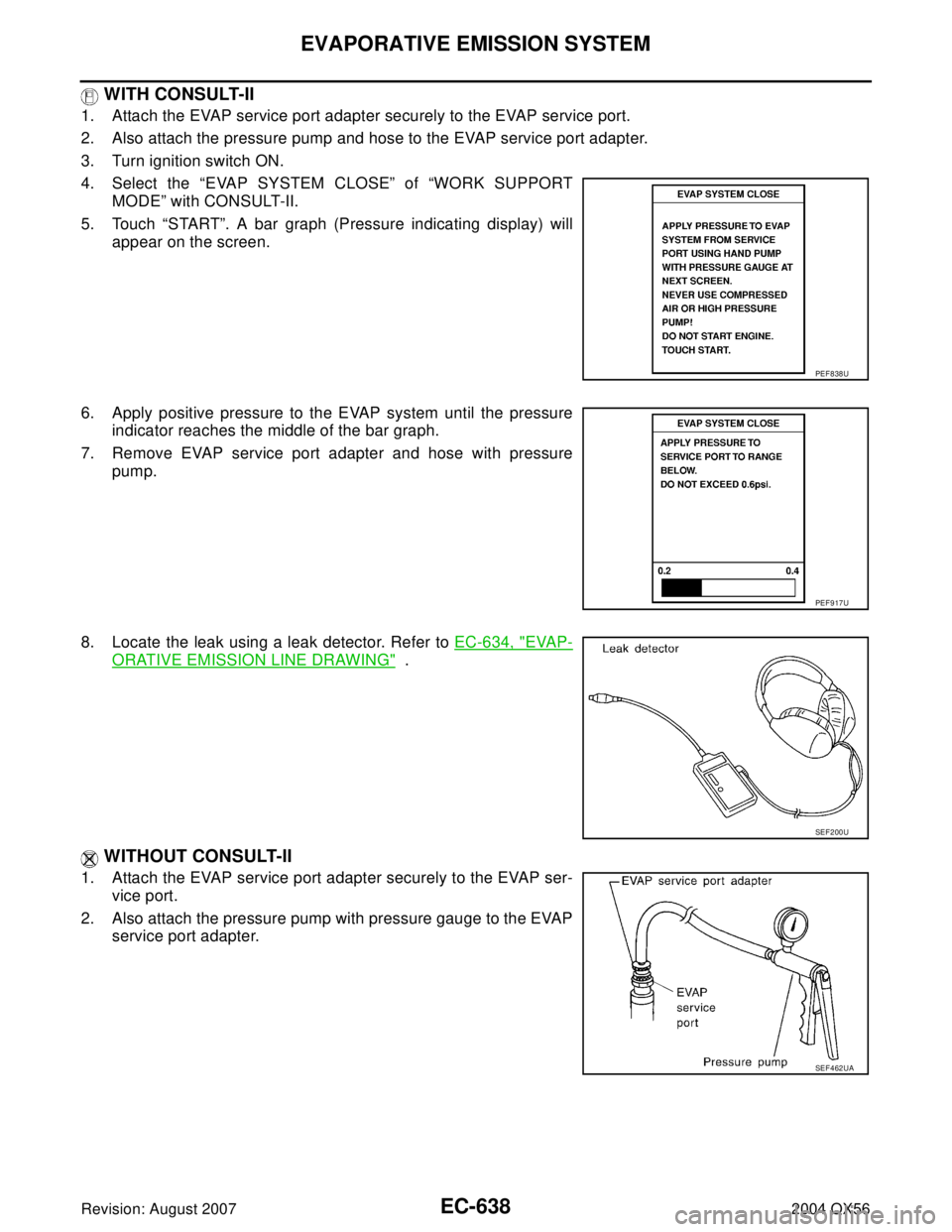
EC-638Revision: August 2007
EVAPORATIVE EMISSION SYSTEM
2004 QX56
WITH CONSULT-II
1. Attach the EVAP service port adapter securely to the EVAP service port.
2. Also attach the pressure pump and hose to the EVAP service port adapter.
3. Turn ignition switch ON.
4. Select the “EVAP SYSTEM CLOSE” of “WORK SUPPORT
MODE” with CONSULT-II.
5. Touch “START”. A bar graph (Pressure indicating display) will
appear on the screen.
6. Apply positive pressure to the EVAP system until the pressure
indicator reaches the middle of the bar graph.
7. Remove EVAP service port adapter and hose with pressure
pump.
8. Locate the leak using a leak detector. Refer to EC-634, "
EVAP-
ORATIVE EMISSION LINE DRAWING" .
WITHOUT CONSULT-II
1. Attach the EVAP service port adapter securely to the EVAP ser-
vice port.
2. Also attach the pressure pump with pressure gauge to the EVAP
service port adapter.
PEF 8 38 U
PEF 9 17 U
SEF 2 00 U
SEF 4 62 UA
Page 1830 of 3371
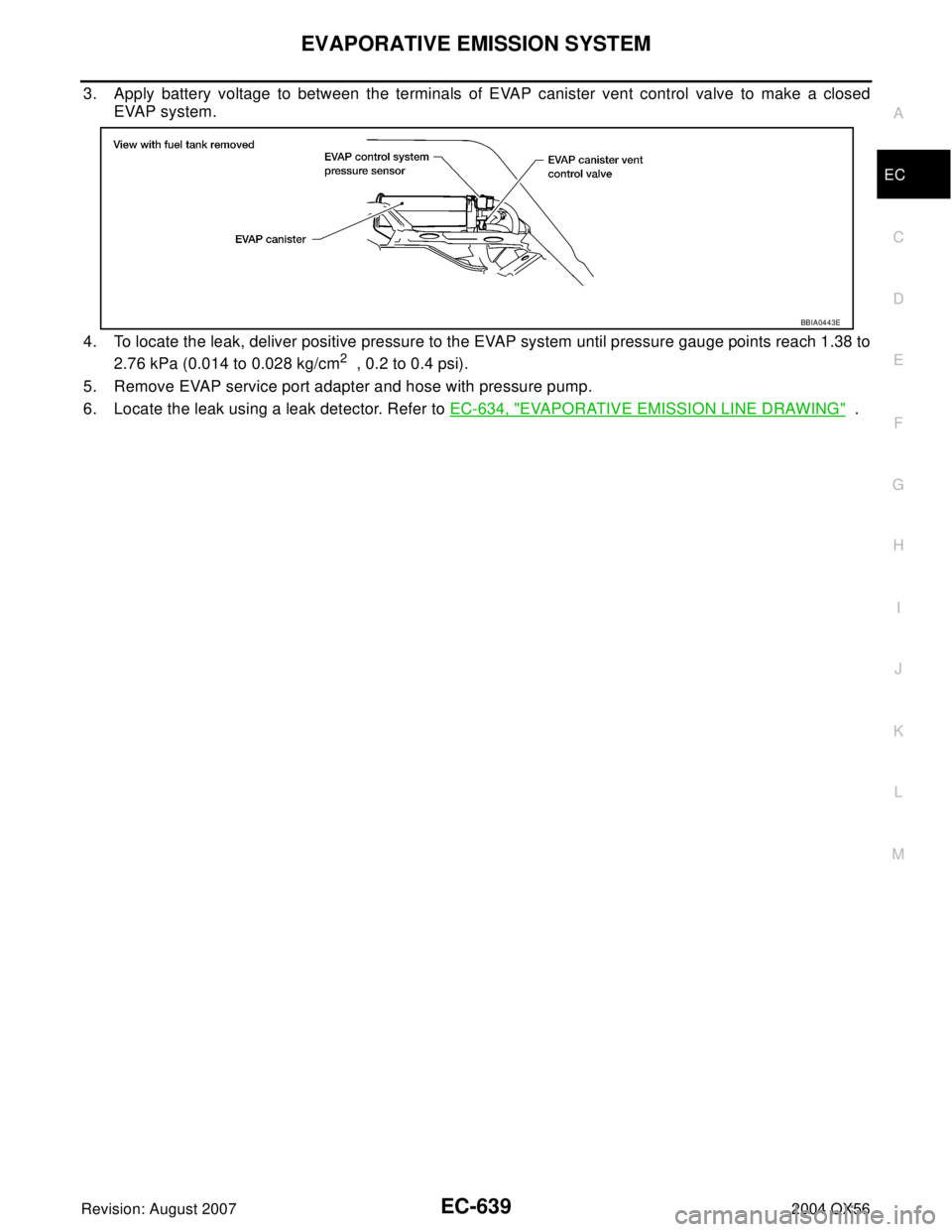
EVAPORATIVE EMISSION SYSTEM
EC-639
C
D
E
F
G
H
I
J
K
L
MA
EC
Revision: August 20072004 QX56
3. Apply battery voltage to between the terminals of EVAP canister vent control valve to make a closed
EVAP system.
4. To locate the leak, deliver positive pressure to the EVAP system until pressure gauge points reach 1.38 to
2.76 kPa (0.014 to 0.028 kg/cm
2 , 0.2 to 0.4 psi).
5. Remove EVAP service port adapter and hose with pressure pump.
6. Locate the leak using a leak detector. Refer to EC-634, "
EVAPORATIVE EMISSION LINE DRAWING" .
BBIA0443E
Page 1840 of 3371
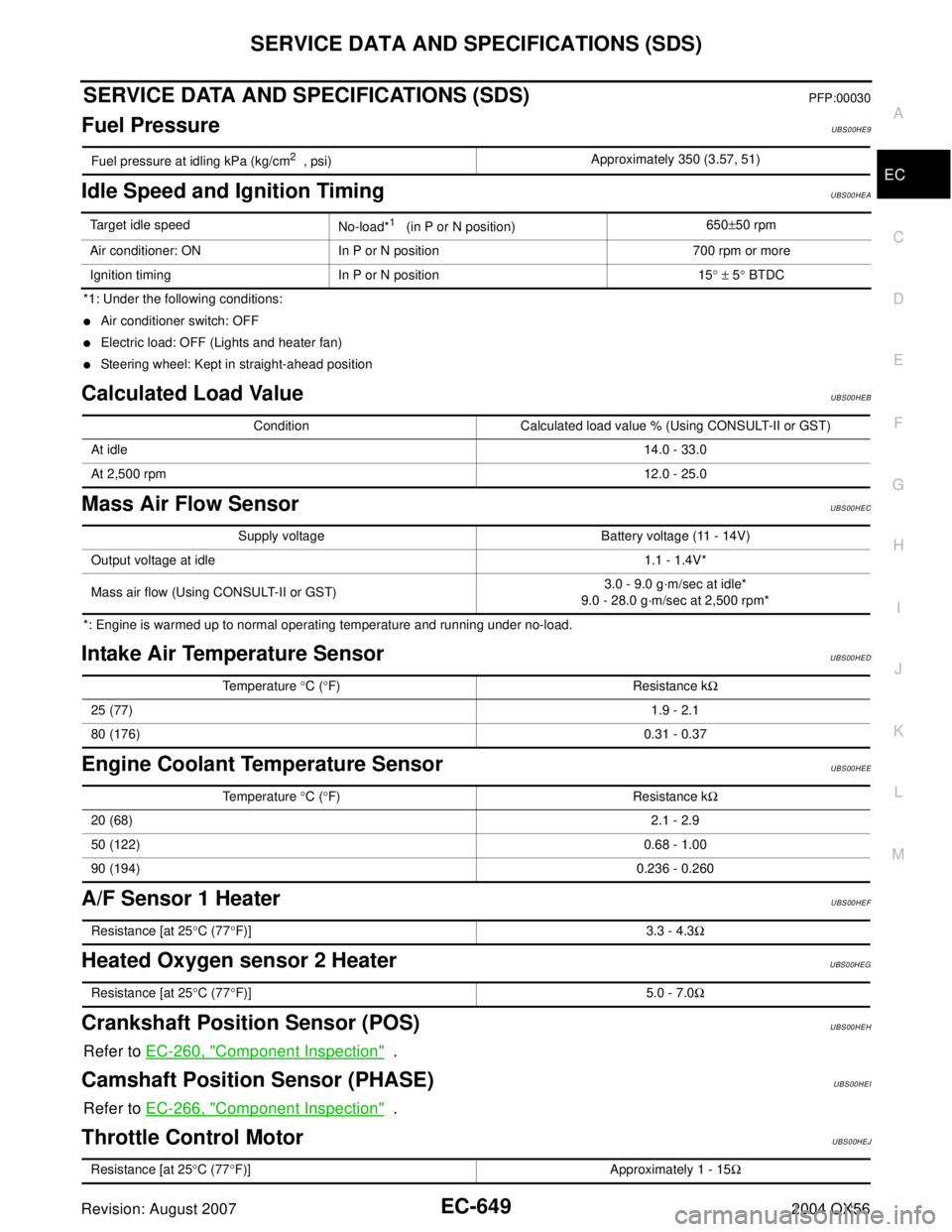
SERVICE DATA AND SPECIFICATIONS (SDS)
EC-649
C
D
E
F
G
H
I
J
K
L
MA
EC
Revision: August 20072004 QX56
SERVICE DATA AND SPECIFICATIONS (SDS)PFP:00030
Fuel PressureUBS00HE9
Idle Speed and Ignition TimingUBS00HEA
*1: Under the following conditions:
Air conditioner switch: OFF
Electric load: OFF (Lights and heater fan)
Steering wheel: Kept in straight-ahead position
Calculated Load ValueUBS00HEB
Mass Air Flow SensorUBS00HEC
*: Engine is warmed up to normal operating temperature and running under no-load.
Intake Air Temperature SensorUBS00HED
Engine Coolant Temperature SensorUBS00HEE
A/F Sensor 1 HeaterUBS00HEF
Heated Oxygen sensor 2 HeaterUBS00HEG
Crankshaft Position Sensor (POS)UBS00HEH
Refer to EC-260, "Component Inspection" .
Camshaft Position Sensor (PHASE)UBS00HEI
Refer to EC-266, "Component Inspection" .
Throttle Control MotorUBS00HEJ
Fuel pressure at idling kPa (kg/cm2 , psi)Approximately 350 (3.57, 51)
Target idle speed
No-load*1 (in P or N position)650±50 rpm
Air conditioner: ON In P or N position 700 rpm or more
Ignition timing In P or N position 15° ± 5° BTDC
Condition Calculated load value % (Using CONSULT-II or GST)
At idle14.0 - 33.0
At 2,500 rpm12.0 - 25.0
Supply voltage Battery voltage (11 - 14V)
Output voltage at idle1.1 - 1.4V*
Mass air flow (Using CONSULT-II or GST)3.0 - 9.0 g·m/sec at idle*
9.0 - 28.0 g·m/sec at 2,500 rpm*
Temperature °C (°F) Resistance kΩ
25 (77)1.9 - 2.1
80 (176)0.31 - 0.37
Temperature °C (°F) Resistance kΩ
20 (68)2.1 - 2.9
50 (122)0.68 - 1.00
90 (194)0.236 - 0.260
Resistance [at 25°C (77°F)] 3.3 - 4.3Ω
Resistance [at 25°C (77°F)] 5.0 - 7.0Ω
Resistance [at 25°C (77°F)] Approximately 1 - 15Ω
Page 1841 of 3371
![INFINITI QX56 2004 Factory Service Manual EC-650Revision: August 2007
SERVICE DATA AND SPECIFICATIONS (SDS)
2004 QX56
InjectorUBS00HEK
Fuel PumpUBS00HEL
Resistance [at 10 - 60°C (50 - 140°F)] 11.1 - 14.5Ω
Resistance [at 25°C (77°F)] 0.2 INFINITI QX56 2004 Factory Service Manual EC-650Revision: August 2007
SERVICE DATA AND SPECIFICATIONS (SDS)
2004 QX56
InjectorUBS00HEK
Fuel PumpUBS00HEL
Resistance [at 10 - 60°C (50 - 140°F)] 11.1 - 14.5Ω
Resistance [at 25°C (77°F)] 0.2](/img/42/57034/w960_57034-1840.png)
EC-650Revision: August 2007
SERVICE DATA AND SPECIFICATIONS (SDS)
2004 QX56
InjectorUBS00HEK
Fuel PumpUBS00HEL
Resistance [at 10 - 60°C (50 - 140°F)] 11.1 - 14.5Ω
Resistance [at 25°C (77°F)] 0.2 - 5.0Ω
Page 1842 of 3371
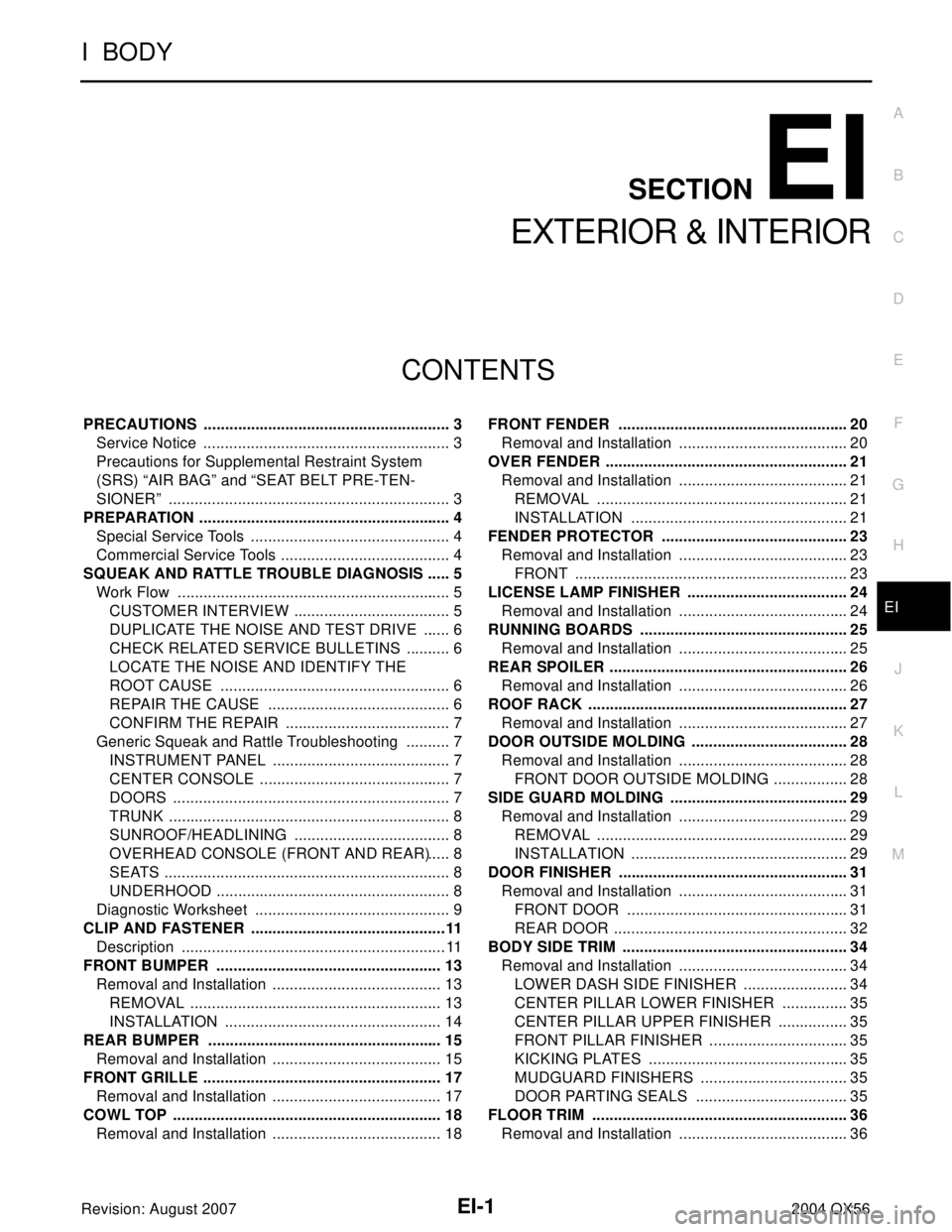
EI-1
EXTERIOR & INTERIOR
I BODY
CONTENTS
C
D
E
F
G
H
J
K
L
M
SECTION EI
A
B
EI
Revision: August 20072004 QX56 PRECAUTIONS .......................................................... 3
Service Notice .......................................................... 3
Precautions for Supplemental Restraint System
(SRS) “AIR BAG” and “SEAT BELT PRE-TEN-
SIONER” .................................................................. 3
PREPARATION ........................................................... 4
Special Service Tools ............................................... 4
Commercial Service Tools ........................................ 4
SQUEAK AND RATTLE TROUBLE DIAGNOSIS ...... 5
Work Flow ................................................................ 5
CUSTOMER INTERVIEW ..................................... 5
DUPLICATE THE NOISE AND TEST DRIVE ....... 6
CHECK RELATED SERVICE BULLETINS ........... 6
LOCATE THE NOISE AND IDENTIFY THE
ROOT CAUSE ...................................................... 6
REPAIR THE CAUSE ........................................... 6
CONFIRM THE REPAIR ....................................... 7
Generic Squeak and Rattle Troubleshooting ........... 7
INSTRUMENT PANEL .......................................... 7
CENTER CONSOLE ............................................. 7
DOORS ................................................................. 7
TRUNK .................................................................. 8
SUNROOF/HEADLINING ..................................... 8
OVERHEAD CONSOLE (FRONT AND REAR) ..... 8
SEATS ................................................................... 8
UNDERHOOD ....................................................... 8
Diagnostic Worksheet .............................................. 9
CLIP AND FASTENER ..............................................11
Description ..............................................................11
FRONT BUMPER ..................................................... 13
Removal and Installation ........................................ 13
REMOVAL ........................................................... 13
INSTALLATION ................................................... 14
REAR BUMPER ....................................................... 15
Removal and Installation ........................................ 15
FRONT GRILLE ........................................................ 17
Removal and Installation ........................................ 17
COWL TOP ............................................................... 18
Removal and Installation ........................................ 18FRONT FENDER ...................................................... 20
Removal and Installation ........................................ 20
OVER FENDER ......................................................... 21
Removal and Installation ........................................ 21
REMOVAL ........................................................... 21
INSTALLATION ................................................... 21
FENDER PROTECTOR ............................................ 23
Removal and Installation ........................................ 23
FRONT ................................................................ 23
LICENSE LAMP FINISHER ...................................... 24
Removal and Installation ........................................ 24
RUNNING BOARDS ................................................. 25
Removal and Installation ........................................ 25
REAR SPOILER ........................................................ 26
Removal and Installation ........................................ 26
ROOF RACK ............................................................. 27
Removal and Installation ........................................ 27
DOOR OUTSIDE MOLDING ..................................... 28
Removal and Installation ........................................ 28
FRONT DOOR OUTSIDE MOLDING .................. 28
SIDE GUARD MOLDING .......................................... 29
Removal and Installation ........................................ 29
REMOVAL ........................................................... 29
INSTALLATION ................................................... 29
DOOR FINISHER ...................................................... 31
Removal and Installation ........................................ 31
FRONT DOOR .................................................... 31
REAR DOOR ....................................................... 32
BODY SIDE TRIM ..................................................... 34
Removal and Installation ........................................ 34
LOWER DASH SIDE FINISHER ......................... 34
CENTER PILLAR LOWER FINISHER ................ 35
CENTER PILLAR UPPER FINISHER ................. 35
FRONT PILLAR FINISHER ................................. 35
KICKING PLATES ............................................... 35
MUDGUARD FINISHERS ................................... 35
DOOR PARTING SEALS .................................... 35
FLOOR TRIM ............................................................ 36
Removal and Installation ........................................ 36