Back up INFINITI QX56 2004 Factory Service Manual
[x] Cancel search | Manufacturer: INFINITI, Model Year: 2004, Model line: QX56, Model: INFINITI QX56 2004Pages: 3371, PDF Size: 78.5 MB
Page 2978 of 3371
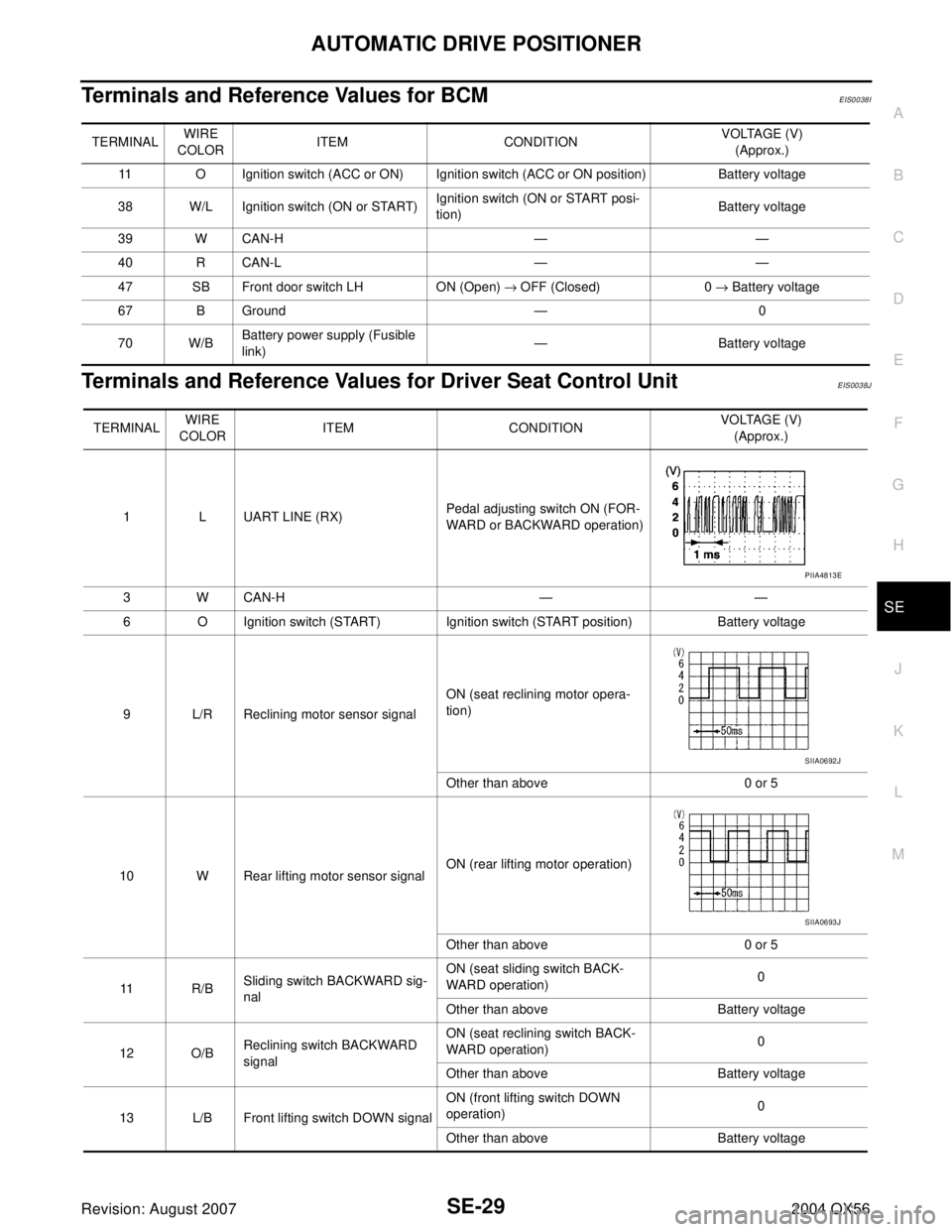
AUTOMATIC DRIVE POSITIONER
SE-29
C
D
E
F
G
H
J
K
L
MA
B
SE
Revision: August 20072004 QX56
Terminals and Reference Values for BCMEIS0038I
Terminals and Reference Values for Driver Seat Control UnitEIS0038J
TERMINAL WIRE
COLORITEM CONDITIONVOLTAGE (V)
(Approx.)
11 O Ignition switch (ACC or ON) Ignition switch (ACC or ON position) Battery voltage
38 W/L Ignition switch (ON or START)Ignition switch (ON or START posi-
tion)Battery voltage
39 W CAN-H — —
40 R CAN-L — —
47 SB Front door switch LH ON (Open) → OFF (Closed) 0 → Battery voltage
67 B Ground — 0
70 W/BBattery power supply (Fusible
link)— Battery voltage
TERMINALWIRE
COLORITEM CONDITIONVOLTAGE (V)
(Approx.)
1 L UART LINE (RX)Pedal adjusting switch ON (FOR-
WARD or BACKWARD operation)
3 W CAN-H — —
6 O Ignition switch (START) Ignition switch (START position) Battery voltage
9 L/R Reclining motor sensor signalON (seat reclining motor opera-
tion)
Other than above 0 or 5
10 W Rear lifting motor sensor signalON (rear lifting motor operation)
Other than above 0 or 5
11 R / BSliding switch BACKWARD sig-
nalON (seat sliding switch BACK-
WARD operation)0
Other than above Battery voltage
12 O/BReclining switch BACKWARD
signalON (seat reclining switch BACK-
WARD operation)0
Other than above Battery voltage
13 L/B Front lifting switch DOWN signalON (front lifting switch DOWN
operation)0
Other than above Battery voltage
PIIA4813E
SIIA0692J
SIIA0693J
Page 2979 of 3371
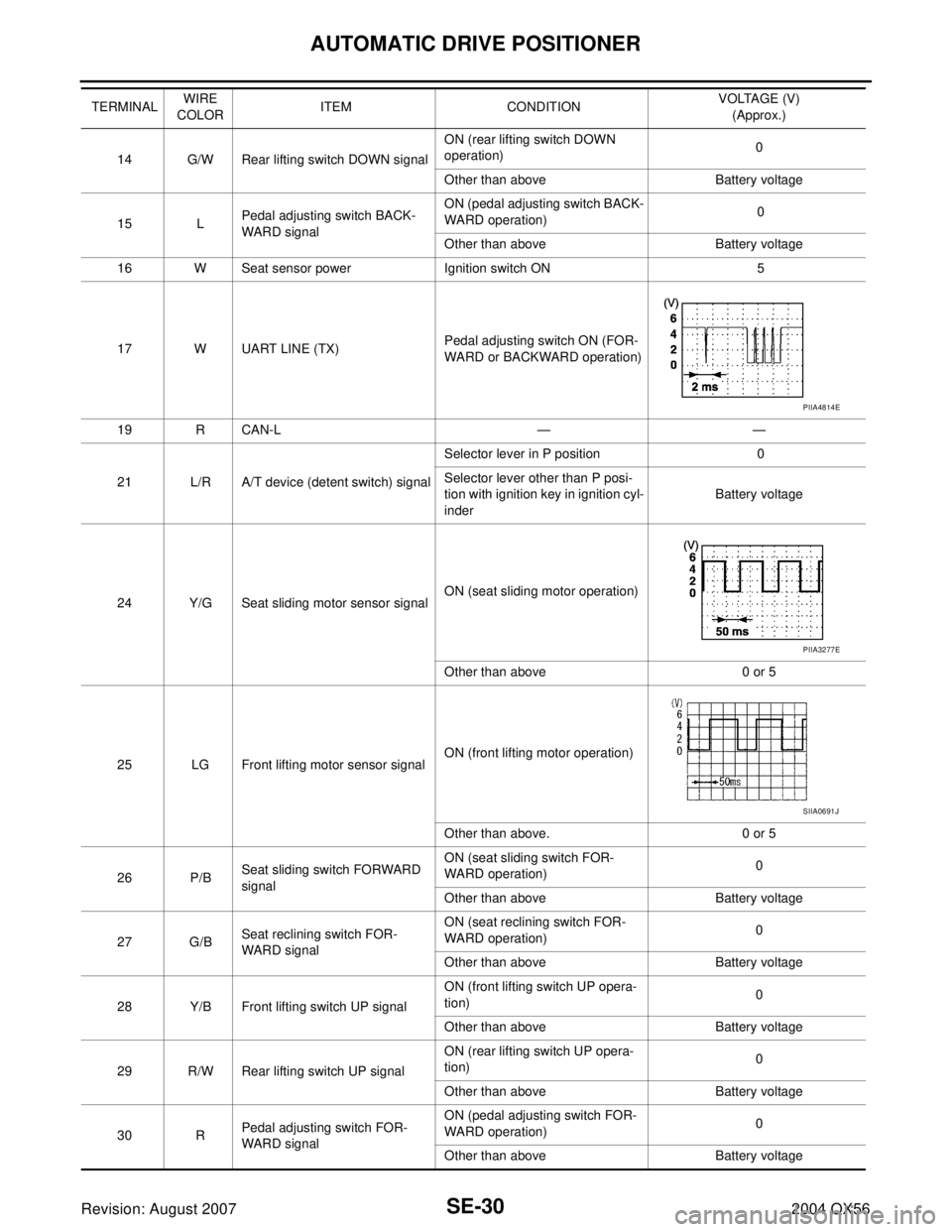
SE-30
AUTOMATIC DRIVE POSITIONER
Revision: August 20072004 QX56
14 G/W Rear lifting switch DOWN signalON (rear lifting switch DOWN
operation)0
Other than above Battery voltage
15 LPedal adjusting switch BACK-
WARD signalON (pedal adjusting switch BACK-
WARD operation) 0
Other than above Battery voltage
16 W Seat sensor power Ignition switch ON 5
17 W UART LINE (TX)Pedal adjusting switch ON (FOR-
WARD or BACKWARD operation)
19 R CAN-L — —
21 L/R A/T device (detent switch) signalSelector lever in P position 0
Selector lever other than P posi-
tion with ignition key in ignition cyl-
inderBattery voltage
24 Y/G Seat sliding motor sensor signalON (seat sliding motor operation)
Other than above 0 or 5
25 LG Front lifting motor sensor signalON (front lifting motor operation)
Other than above. 0 or 5
26 P/BSeat sliding switch FORWARD
signalON (seat sliding switch FOR-
WARD operation)0
Other than above Battery voltage
27 G/BSeat reclining switch FOR-
WARD signalON (seat reclining switch FOR-
WARD operation)0
Other than above Battery voltage
28 Y/B Front lifting switch UP signalON (front lifting switch UP opera-
tion)0
Other than above Battery voltage
29 R/W Rear lifting switch UP signalON (rear lifting switch UP opera-
tion)0
Other than above Battery voltage
30 RPedal adjusting switch FOR-
WARD signalON (pedal adjusting switch FOR-
WARD operation)0
Other than above Battery voltage TERMINALWIRE
COLORITEM CONDITIONVOLTAGE (V)
(Approx.)
PIIA4814E
PIIA3277E
SIIA0691J
Page 2980 of 3371
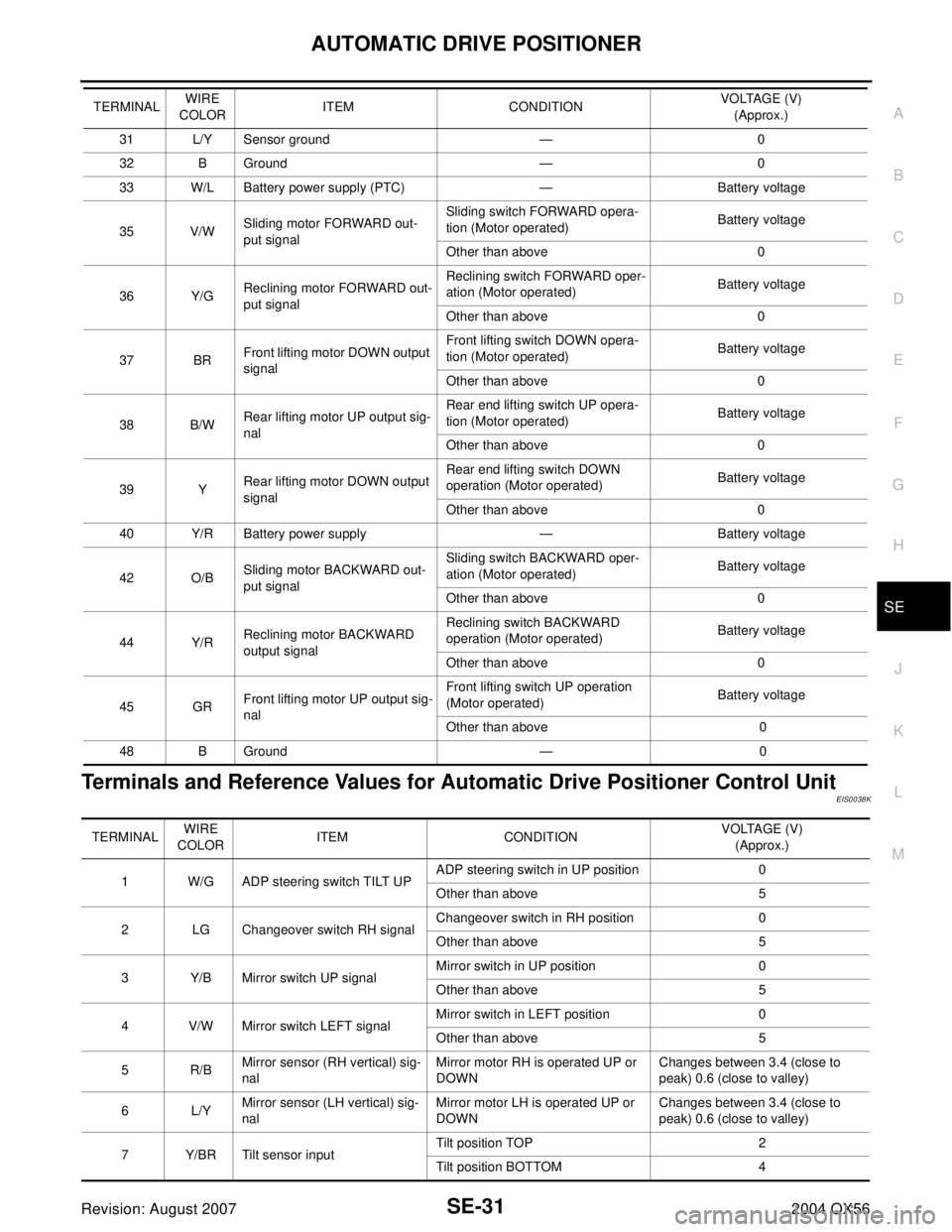
AUTOMATIC DRIVE POSITIONER
SE-31
C
D
E
F
G
H
J
K
L
MA
B
SE
Revision: August 20072004 QX56
Terminals and Reference Values for Automatic Drive Positioner Control UnitEIS0038K
31 L/Y Sensor ground — 0
32 B Ground — 0
33 W/L Battery power supply (PTC) — Battery voltage
35 V/WSliding motor FORWARD out-
put signalSliding switch FORWARD opera-
tion (Motor operated)Battery voltage
Other than above 0
36 Y/GReclining motor FORWARD out-
put signalReclining switch FORWARD oper-
ation (Motor operated)Battery voltage
Other than above 0
37 BRFront lifting motor DOWN output
signalFront lifting switch DOWN opera-
tion (Motor operated)Battery voltage
Other than above 0
38 B/WRear lifting motor UP output sig-
nalRear end lifting switch UP opera-
tion (Motor operated)Battery voltage
Other than above 0
39 YRear lifting motor DOWN output
signalRear end lifting switch DOWN
operation (Motor operated)Battery voltage
Other than above 0
40 Y/R Battery power supply — Battery voltage
42 O/BSliding motor BACKWARD out-
put signalSliding switch BACKWARD oper-
ation (Motor operated)Battery voltage
Other than above 0
44 Y/RReclining motor BACKWARD
output signalReclining switch BACKWARD
operation (Motor operated)Battery voltage
Other than above 0
45 GRFront lifting motor UP output sig-
nalFront lifting switch UP operation
(Motor operated)Battery voltage
Other than above 0
48 B Ground — 0 TERMINALWIRE
COLORITEM CONDITIONVOLTAGE (V)
(Approx.)
TERMINAL WIRE
COLORITEM CONDITIONVOLTAGE (V)
(Approx.)
1 W/G ADP steering switch TILT UPADP steering switch in UP position 0
Other than above 5
2 LG Changeover switch RH signalChangeover switch in RH position 0
Other than above 5
3 Y/B Mirror switch UP signalMirror switch in UP position 0
Other than above 5
4 V/W Mirror switch LEFT signalMirror switch in LEFT position 0
Other than above 5
5R/BMirror sensor (RH vertical) sig-
nalMirror motor RH is operated UP or
DOWNChanges between 3.4 (close to
peak) 0.6 (close to valley)
6L/YMirror sensor (LH vertical) sig-
nalMirror motor LH is operated UP or
DOWNChanges between 3.4 (close to
peak) 0.6 (close to valley)
7 Y/BR Tilt sensor inputTilt position TOP 2
Tilt position BOTTOM 4
Page 2981 of 3371
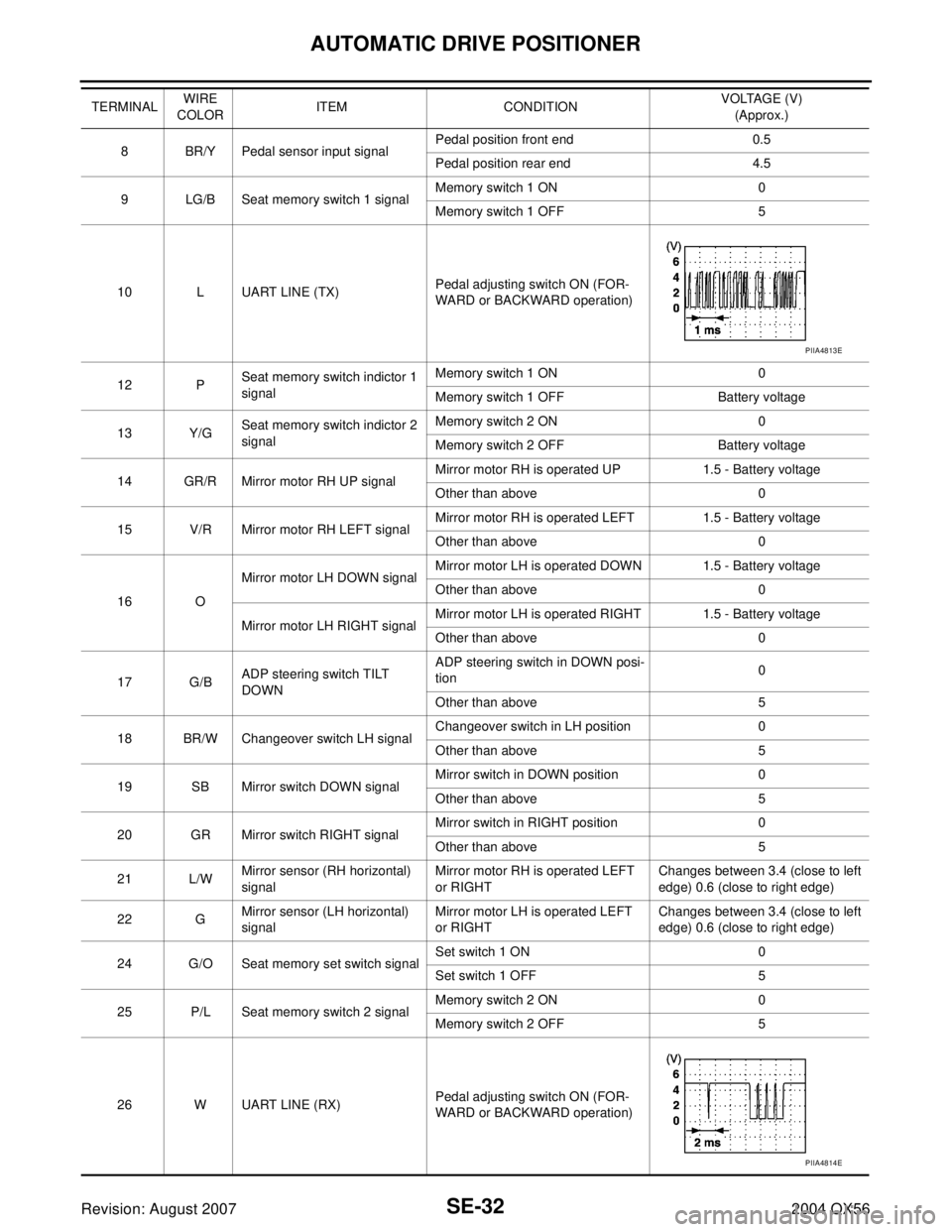
SE-32
AUTOMATIC DRIVE POSITIONER
Revision: August 20072004 QX56
8 BR/Y Pedal sensor input signalPedal position front end 0.5
Pedal position rear end 4.5
9 LG/B Seat memory switch 1 signalMemory switch 1 ON 0
Memory switch 1 OFF 5
10 L UART LINE (TX)Pedal adjusting switch ON (FOR-
WARD or BACKWARD operation)
12 PSeat memory switch indictor 1
signalMemory switch 1 ON 0
Memory switch 1 OFF Battery voltage
13 Y/GSeat memory switch indictor 2
signalMemory switch 2 ON 0
Memory switch 2 OFF Battery voltage
14 GR/R Mirror motor RH UP signalMirror motor RH is operated UP 1.5 - Battery voltage
Other than above 0
15 V/R Mirror motor RH LEFT signalMirror motor RH is operated LEFT 1.5 - Battery voltage
Other than above 0
16 OMirror motor LH DOWN signalMirror motor LH is operated DOWN 1.5 - Battery voltage
Other than above 0
Mirror motor LH RIGHT signalMirror motor LH is operated RIGHT 1.5 - Battery voltage
Other than above 0
17 G/BADP steering switch TILT
DOWNADP steering switch in DOWN posi-
tion0
Other than above 5
18 BR/W Changeover switch LH signalChangeover switch in LH position 0
Other than above 5
19 SB Mirror switch DOWN signalMirror switch in DOWN position 0
Other than above 5
20 GR Mirror switch RIGHT signalMirror switch in RIGHT position 0
Other than above 5
21 L/WMirror sensor (RH horizontal)
signalMirror motor RH is operated LEFT
or RIGHTChanges between 3.4 (close to left
edge) 0.6 (close to right edge)
22 GMirror sensor (LH horizontal)
signalMirror motor LH is operated LEFT
or RIGHTChanges between 3.4 (close to left
edge) 0.6 (close to right edge)
24 G/O Seat memory set switch signalSet switch 1 ON 0
Set switch 1 OFF 5
25 P/L Seat memory switch 2 signalMemory switch 2 ON 0
Memory switch 2 OFF 5
26 W UART LINE (RX)Pedal adjusting switch ON (FOR-
WARD or BACKWARD operation) TERMINAL WIRE
COLORITEM CONDITIONVOLTAGE (V)
(Approx.)
PIIA4813E
PIIA4814E
Page 2982 of 3371
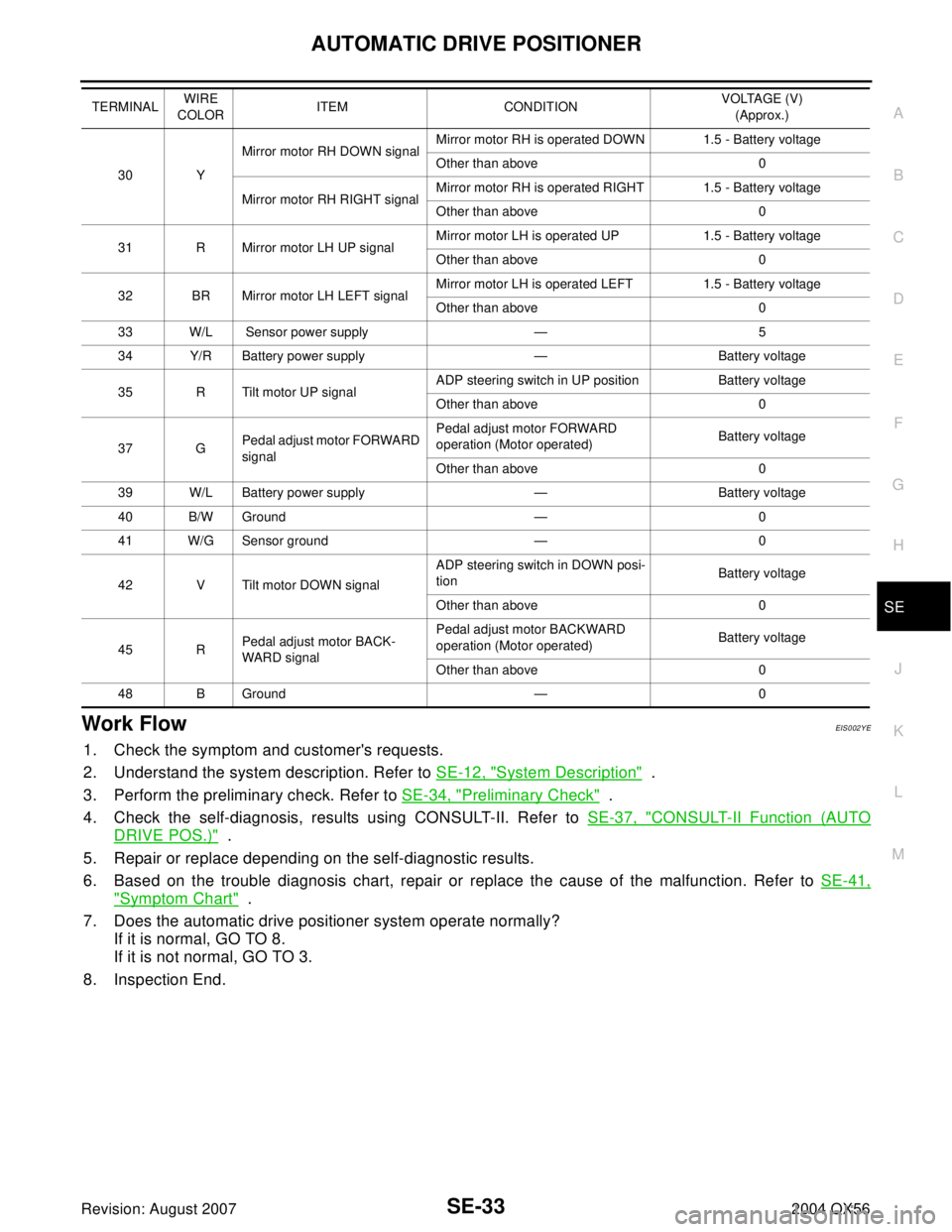
AUTOMATIC DRIVE POSITIONER
SE-33
C
D
E
F
G
H
J
K
L
MA
B
SE
Revision: August 20072004 QX56
Work Flow EIS002YE
1. Check the symptom and customer's requests.
2. Understand the system description. Refer to SE-12, "
System Description" .
3. Perform the preliminary check. Refer to SE-34, "
Preliminary Check" .
4. Check the self-diagnosis, results using CONSULT-II. Refer to SE-37, "
CONSULT-II Function (AUTO
DRIVE POS.)" .
5. Repair or replace depending on the self-diagnostic results.
6. Based on the trouble diagnosis chart, repair or replace the cause of the malfunction. Refer to SE-41,
"Symptom Chart" .
7. Does the automatic drive positioner system operate normally?
If it is normal, GO TO 8.
If it is not normal, GO TO 3.
8. Inspection End.
30 YMirror motor RH DOWN signalMirror motor RH is operated DOWN 1.5 - Battery voltage
Other than above 0
Mirror motor RH RIGHT signalMirror motor RH is operated RIGHT 1.5 - Battery voltage
Other than above 0
31 R Mirror motor LH UP signalMirror motor LH is operated UP 1.5 - Battery voltage
Other than above 0
32 BR Mirror motor LH LEFT signalMirror motor LH is operated LEFT 1.5 - Battery voltage
Other than above 0
33 W/L Sensor power supply — 5
34 Y/R Battery power supply — Battery voltage
35 R Tilt motor UP signalADP steering switch in UP position Battery voltage
Other than above 0
37 GPedal adjust motor FORWARD
signalPedal adjust motor FORWARD
operation (Motor operated)Battery voltage
Other than above 0
39 W/L Battery power supply — Battery voltage
40 B/W Ground — 0
41 W/G Sensor ground — 0
42 V Tilt motor DOWN signalADP steering switch in DOWN posi-
tionBattery voltage
Other than above 0
45 RPedal adjust motor BACK-
WARD signalPedal adjust motor BACKWARD
operation (Motor operated)Battery voltage
Other than above 0
48 B Ground — 0 TERMINAL WIRE
COLORITEM CONDITIONVOLTAGE (V)
(Approx.)
Page 2989 of 3371
![INFINITI QX56 2004 Factory Service Manual SE-40
AUTOMATIC DRIVE POSITIONER
Revision: August 20072004 QX56
DATA MONITOR
CAN DIAGNOSIS SUPPORT MONITOR
SELECTIOM FROM MEMU
Monitor item [UNIT] Contents
CAN COMM [OK/NG] When CAN communication circ INFINITI QX56 2004 Factory Service Manual SE-40
AUTOMATIC DRIVE POSITIONER
Revision: August 20072004 QX56
DATA MONITOR
CAN DIAGNOSIS SUPPORT MONITOR
SELECTIOM FROM MEMU
Monitor item [UNIT] Contents
CAN COMM [OK/NG] When CAN communication circ](/img/42/57034/w960_57034-2988.png)
SE-40
AUTOMATIC DRIVE POSITIONER
Revision: August 20072004 QX56
DATA MONITOR
CAN DIAGNOSIS SUPPORT MONITOR
SELECTIOM FROM MEMU
Monitor item [UNIT] Contents
CAN COMM [OK/NG] When CAN communication circuit is malfunctioning, it displays “NG”.
CAN CIRC 1 [OK/UNKWN]
Displays [OK/UNKWN] condition of the CAN communication judged by each sig-
nal input. CAN CIRC 2 [OK/UNKWN]
CAN CIRC 3 [OK/UNKWN]
CAN CIRC 4 [OK/UNKWN]
Monitor item [OPERATION or UNIT] Contents
SLIDE SW–FR “ON/OFF” ON/OFF status judged from the sliding switch (FR) signal is displayed.
SLIDE SW–RR “ON/OFF” ON/OFF status judged from the sliding switch (RR) signal is displayed.
RECLN SW–FR “ON/OFF” ON/OFF status judged from the reclining switch (FR) signal is displayed.
RECLN SW–RR “ON/OFF” ON/OFF status judged from the reclining switch (RR) signal is displayed.
LIFT FR SW–UP “ON/OFF” ON/OFF status judged from the FR lifter switch (UP) signal is displayed.
LIFT FR SW–DN “ON/OFF” ON/OFF status judged from the FR lifter switch (DOWN) signal is displayed.
LIFT RR SW–UP “ON/OFF” ON/OFF status judged from the RR lifter switch (UP) signal is displayed.
LIFT RR SW–DN “ON/OFF” ON/OFF status judged from the RR lifter switch (DOWN) signal is displayed.
MIR CON SW–UP “ON/OFF” ON/OFF status judged from the door mirror switch (UP) signal is displayed.
MIR CON SW–DN “ON/OFF” ON/OFF status judged from the door mirror switch (DOWN) signal is displayed.
MIR CON SW–RH “ON/OFF” ON/OFF status judged from the door mirror switch (RIGHT) signal is displayed.
MIR CON SW–LH “ON/OFF” ON/OFF status judged from the door mirror switch (LEFT) signal is displayed.
MIR CHNG SW–R “ON/OFF”ON/OFF status judged from the door mirror switch (switching to RIGHT) signal is
displayed.
MIR CHNG SW–L “ON/OFF”ON/OFF status judged from the door mirror switch (switching to LEFT) signal is
displayed.
SET SW “ON/OFF” ON/OFF status judged from the setting switch signal is displayed.
TILT SW-UP “ON/OFF” ON/OFF status judged from the tilt adjusting switch (UP) signal is displayed.
PEDAL SW-FR “ON/OFF” ON/OFF status judged from the pedal adjusting switch (FR) signal is displayed.
PEDAL SW-RR “ON/OFF” ON/OFF status judged from the pedal adjusting switch (RR) signal is displayed.
MEMORY SW1 “ON/OFF” ON/OFF status judged from the seat memory switch 1 signal is displayed.
MEMORY SW2 “ON/OFF” ON/OFF status judged from the seat memory switch 2 signal is displayed.
DETENT SW “ON/OFF”The selector lever position “OFF (P position) / ON (other than P position)” judged
from the park switch signal is displayed.
STARTER SW “ON/OFF”Ignition key switch ON (START, ON) /OFF (ignition switch IGN, ACC, or OFF)
status judged from the ignition switch signal is displayed.
SLIDE PULSE —Value (32768) when battery connects is as standard. If it moves BACKWARD, the
value increases. If it moves FORWARD, the value decreases.
RECLN PULSE —Value (32768) when battery connects is as standard. If it moves BACKWARD, the
value increases. If it moves FORWARD, the value decreases.
LIFT FR PULSE —Value (32768) when battery connects is as standard. If it moves DOWN, the value
increases. If it moves UP, the value decreases.
LIFT RR PULSE —Value (32768) when battery connects is as standard. If it moves DOWN, the value
increases. If it moves UP, the value decreases.
MIR/SEN RH R–L “V” Voltage output from RH door mirror sensor (LH/RH) is displayed.
MIR/SEN RH U–D “V” Voltage output from RH door mirror sensor (UP/DOWN) is displayed.
MIR/SEN LH R–L “V” Voltage output from LH door mirror sensor (LH/RH) is displayed.
Page 2993 of 3371
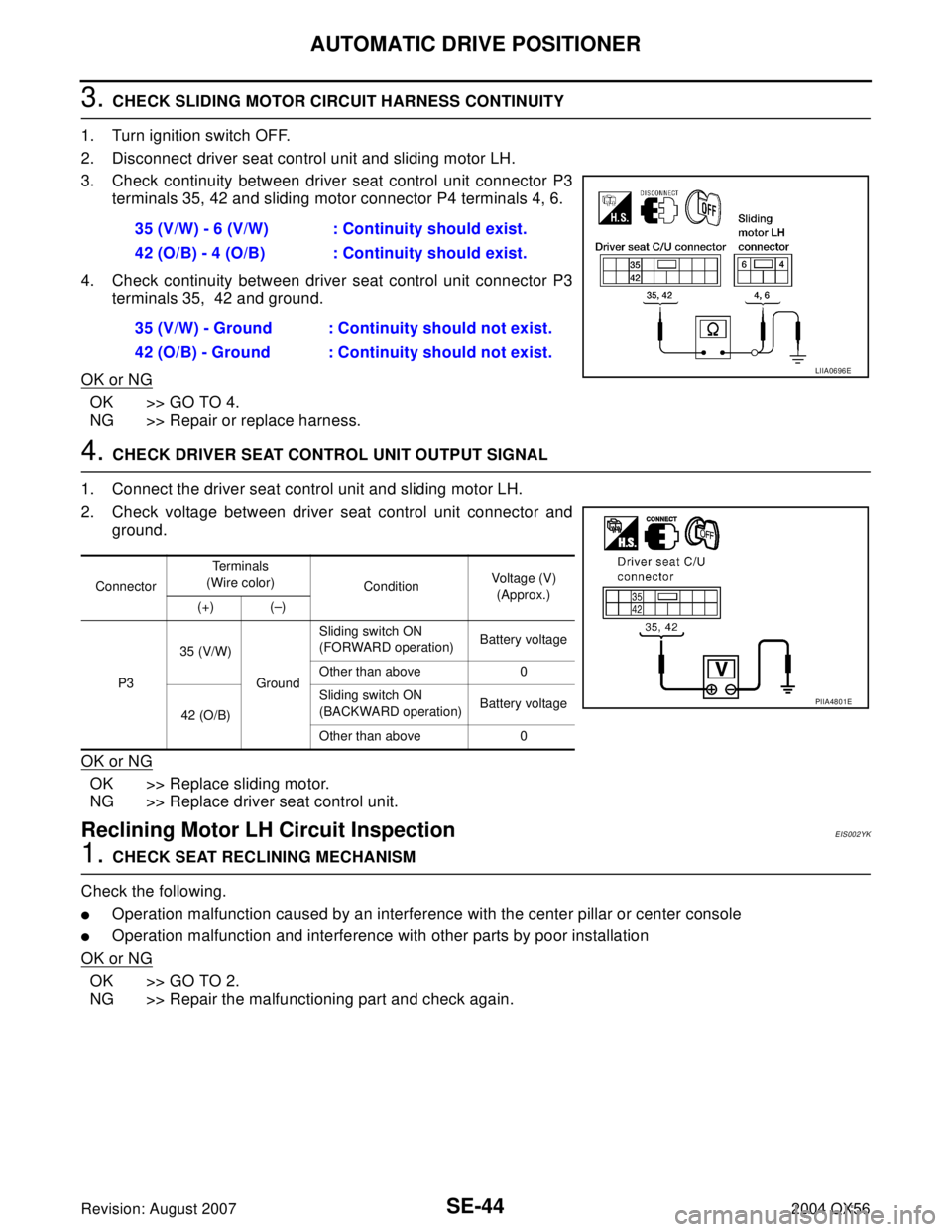
SE-44
AUTOMATIC DRIVE POSITIONER
Revision: August 20072004 QX56
3. CHECK SLIDING MOTOR CIRCUIT HARNESS CONTINUITY
1. Turn ignition switch OFF.
2. Disconnect driver seat control unit and sliding motor LH.
3. Check continuity between driver seat control unit connector P3
terminals 35, 42 and sliding motor connector P4 terminals 4, 6.
4. Check continuity between driver seat control unit connector P3
terminals 35, 42 and ground.
OK or NG
OK >> GO TO 4.
NG >> Repair or replace harness.
4. CHECK DRIVER SEAT CONTROL UNIT OUTPUT SIGNAL
1. Connect the driver seat control unit and sliding motor LH.
2. Check voltage between driver seat control unit connector and
ground.
OK or NG
OK >> Replace sliding motor.
NG >> Replace driver seat control unit.
Reclining Motor LH Circuit InspectionEIS002YK
1. CHECK SEAT RECLINING MECHANISM
Check the following.
Operation malfunction caused by an interference with the center pillar or center console
Operation malfunction and interference with other parts by poor installation
OK or NG
OK >> GO TO 2.
NG >> Repair the malfunctioning part and check again.35 (V/W) - 6 (V/W) : Continuity should exist.
42 (O/B) - 4 (O/B) : Continuity should exist.
35 (V/W) - Ground : Continuity should not exist.
42 (O/B) - Ground : Continuity should not exist.
LIIA0696E
ConnectorTe r m i n a l s
(Wire color)
ConditionVoltage (V)
(Approx.)
(+) (–)
P335 (V/W)
GroundSliding switch ON
(FORWARD operation)Battery voltage
Other than above 0
42 (O/B)Sliding switch ON
(BACKWARD operation)Battery voltage
Other than above 0
PIIA4801E
Page 2995 of 3371
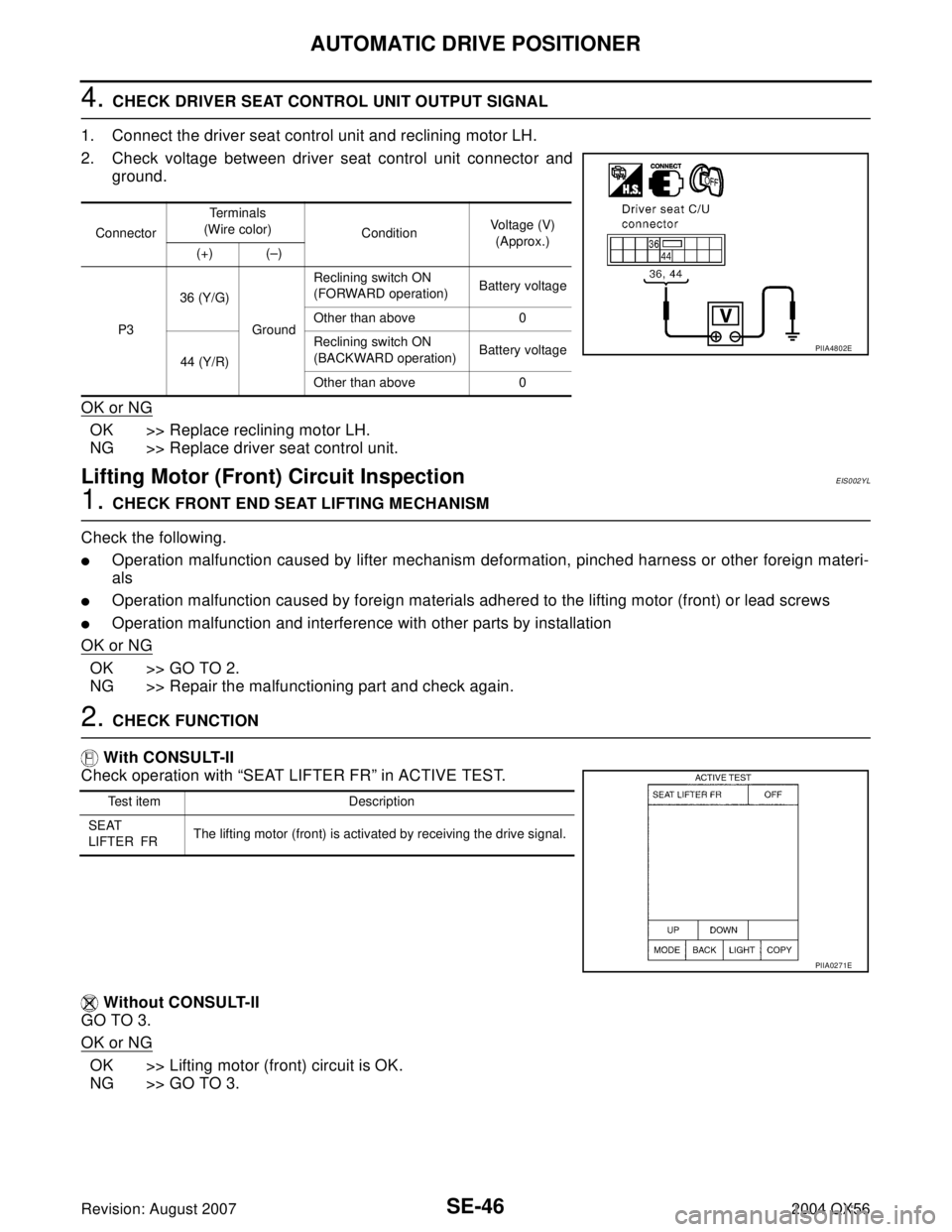
SE-46
AUTOMATIC DRIVE POSITIONER
Revision: August 20072004 QX56
4. CHECK DRIVER SEAT CONTROL UNIT OUTPUT SIGNAL
1. Connect the driver seat control unit and reclining motor LH.
2. Check voltage between driver seat control unit connector and
ground.
OK or NG
OK >> Replace reclining motor LH.
NG >> Replace driver seat control unit.
Lifting Motor (Front) Circuit InspectionEIS002YL
1. CHECK FRONT END SEAT LIFTING MECHANISM
Check the following.
Operation malfunction caused by lifter mechanism deformation, pinched harness or other foreign materi-
als
Operation malfunction caused by foreign materials adhered to the lifting motor (front) or lead screws
Operation malfunction and interference with other parts by installation
OK or NG
OK >> GO TO 2.
NG >> Repair the malfunctioning part and check again.
2. CHECK FUNCTION
With CONSULT-II
Check operation with “SEAT LIFTER FR” in ACTIVE TEST.
Without CONSULT-II
GO TO 3.
OK or NG
OK >> Lifting motor (front) circuit is OK.
NG >> GO TO 3.
ConnectorTerminals
(Wire color)
ConditionVoltage (V)
(Approx.)
(+) (–)
P336 (Y/G)
GroundReclining switch ON
(FORWARD operation)Battery voltage
Other than above 0
44 (Y/R)Reclining switch ON
(BACKWARD operation)Battery voltage
Other than above 0
PIIA4802E
Test item Description
SEAT
LIFTER FRThe lifting motor (front) is activated by receiving the drive signal.
PIIA0271E
Page 2999 of 3371
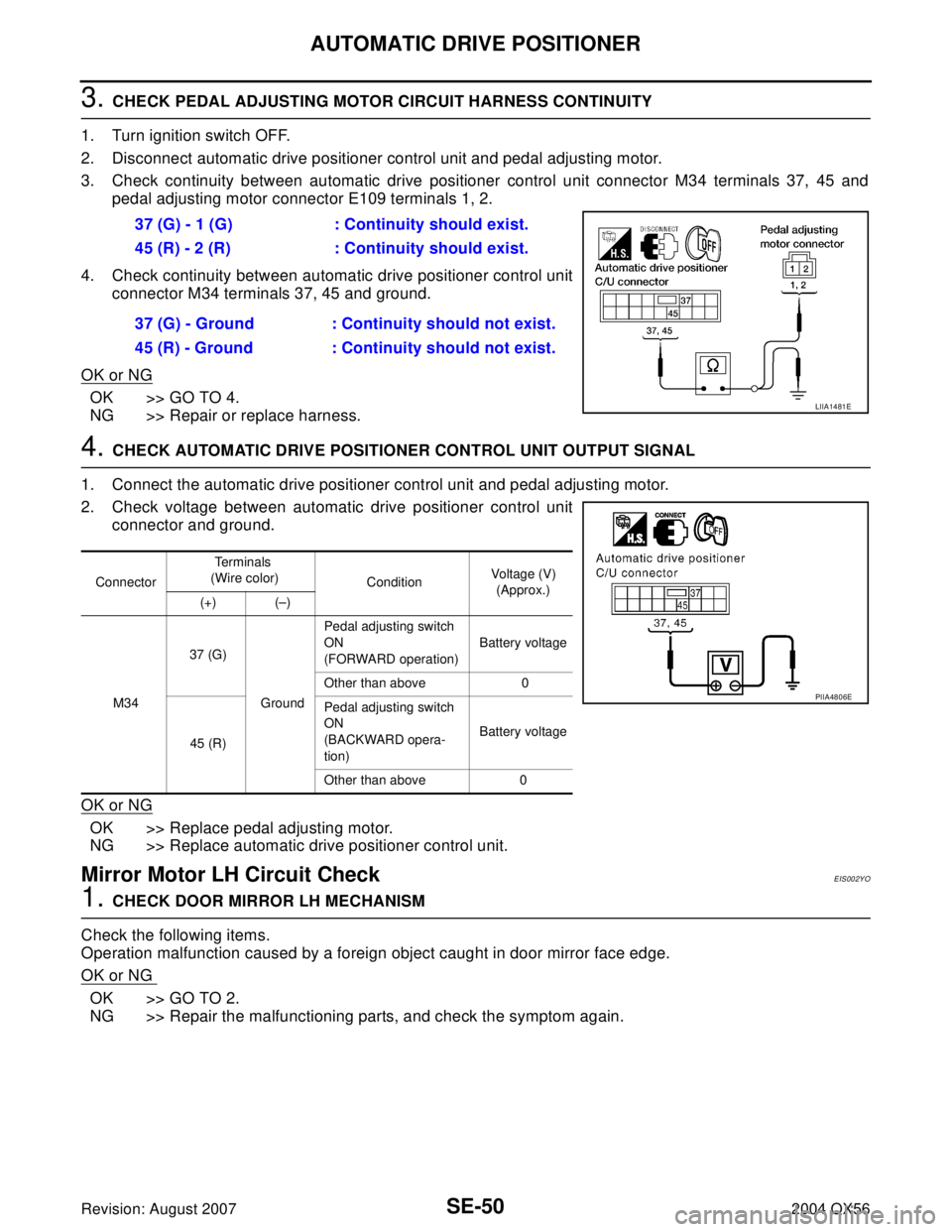
SE-50
AUTOMATIC DRIVE POSITIONER
Revision: August 20072004 QX56
3. CHECK PEDAL ADJUSTING MOTOR CIRCUIT HARNESS CONTINUITY
1. Turn ignition switch OFF.
2. Disconnect automatic drive positioner control unit and pedal adjusting motor.
3. Check continuity between automatic drive positioner control unit connector M34 terminals 37, 45 and
pedal adjusting motor connector E109 terminals 1, 2.
4. Check continuity between automatic drive positioner control unit
connector M34 terminals 37, 45 and ground.
OK or NG
OK >> GO TO 4.
NG >> Repair or replace harness.
4. CHECK AUTOMATIC DRIVE POSITIONER CONTROL UNIT OUTPUT SIGNAL
1. Connect the automatic drive positioner control unit and pedal adjusting motor.
2. Check voltage between automatic drive positioner control unit
connector and ground.
OK or NG
OK >> Replace pedal adjusting motor.
NG >> Replace automatic drive positioner control unit.
Mirror Motor LH Circuit CheckEIS002YO
1. CHECK DOOR MIRROR LH MECHANISM
Check the following items.
Operation malfunction caused by a foreign object caught in door mirror face edge.
OK or NG
OK >> GO TO 2.
NG >> Repair the malfunctioning parts, and check the symptom again.37 (G) - 1 (G) : Continuity should exist.
45 (R) - 2 (R) : Continuity should exist.
37 (G) - Ground : Continuity should not exist.
45 (R) - Ground : Continuity should not exist.
LIIA1481E
ConnectorTerminals
(Wire color)
ConditionVoltage (V)
(Approx.)
(+) (–)
M3437 (G)
GroundPedal adjusting switch
ON
(FORWARD operation)Battery voltage
Other than above 0
45 (R)Pedal adjusting switch
ON
(BACKWARD opera-
tion)Battery voltage
Other than above 0
PIIA4806E
Page 3008 of 3371
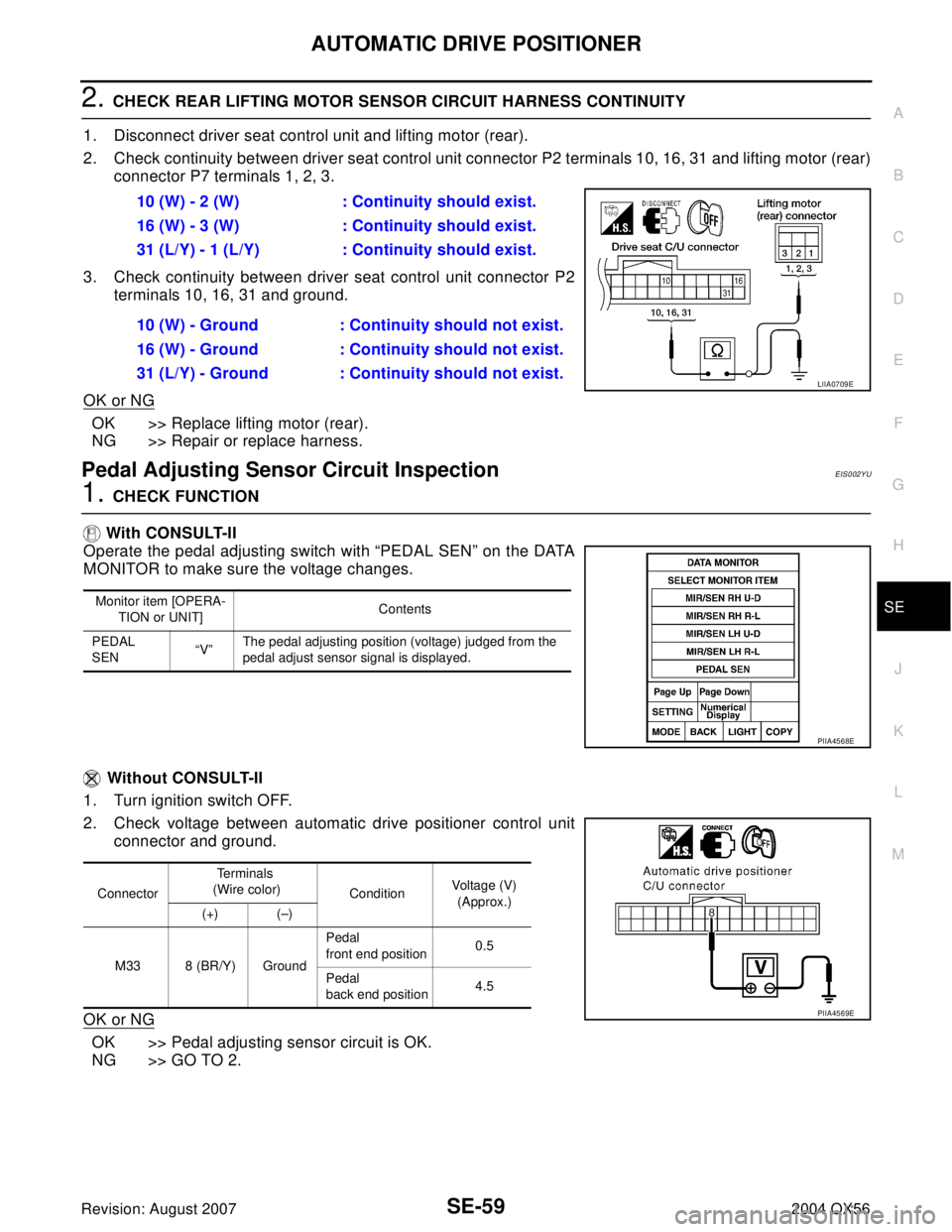
AUTOMATIC DRIVE POSITIONER
SE-59
C
D
E
F
G
H
J
K
L
MA
B
SE
Revision: August 20072004 QX56
2. CHECK REAR LIFTING MOTOR SENSOR CIRCUIT HARNESS CONTINUITY
1. Disconnect driver seat control unit and lifting motor (rear).
2. Check continuity between driver seat control unit connector P2 terminals 10, 16, 31 and lifting motor (rear)
connector P7 terminals 1, 2, 3.
3. Check continuity between driver seat control unit connector P2
terminals 10, 16, 31 and ground.
OK or NG
OK >> Replace lifting motor (rear).
NG >> Repair or replace harness.
Pedal Adjusting Sensor Circuit InspectionEIS002YU
1. CHECK FUNCTION
With CONSULT-II
Operate the pedal adjusting switch with “PEDAL SEN” on the DATA
MONITOR to make sure the voltage changes.
Without CONSULT-II
1. Turn ignition switch OFF.
2. Check voltage between automatic drive positioner control unit
connector and ground.
OK or NG
OK >> Pedal adjusting sensor circuit is OK.
NG >> GO TO 2.10 (W) - 2 (W) : Continuity should exist.
16 (W) - 3 (W) : Continuity should exist.
31 (L/Y) - 1 (L/Y) : Continuity should exist.
10 (W) - Ground : Continuity should not exist.
16 (W) - Ground : Continuity should not exist.
31 (L/Y) - Ground : Continuity should not exist.
LIIA0709E
Monitor item [OPERA-
TION or UNIT]Contents
PEDAL
SEN“V”The pedal adjusting position (voltage) judged from the
pedal adjust sensor signal is displayed.
PIIA4568E
ConnectorTe r m i n a l s
(Wire color)
ConditionVoltage (V)
(Approx.)
(+) (–)
M33 8 (BR/Y) GroundPedal
front end position0.5
Pedal
back end position4.5
PIIA4569E