service INFINITI QX56 2006 Factory Owners Manual
[x] Cancel search | Manufacturer: INFINITI, Model Year: 2006, Model line: QX56, Model: INFINITI QX56 2006Pages: 3383, PDF Size: 51.76 MB
Page 1010 of 3383
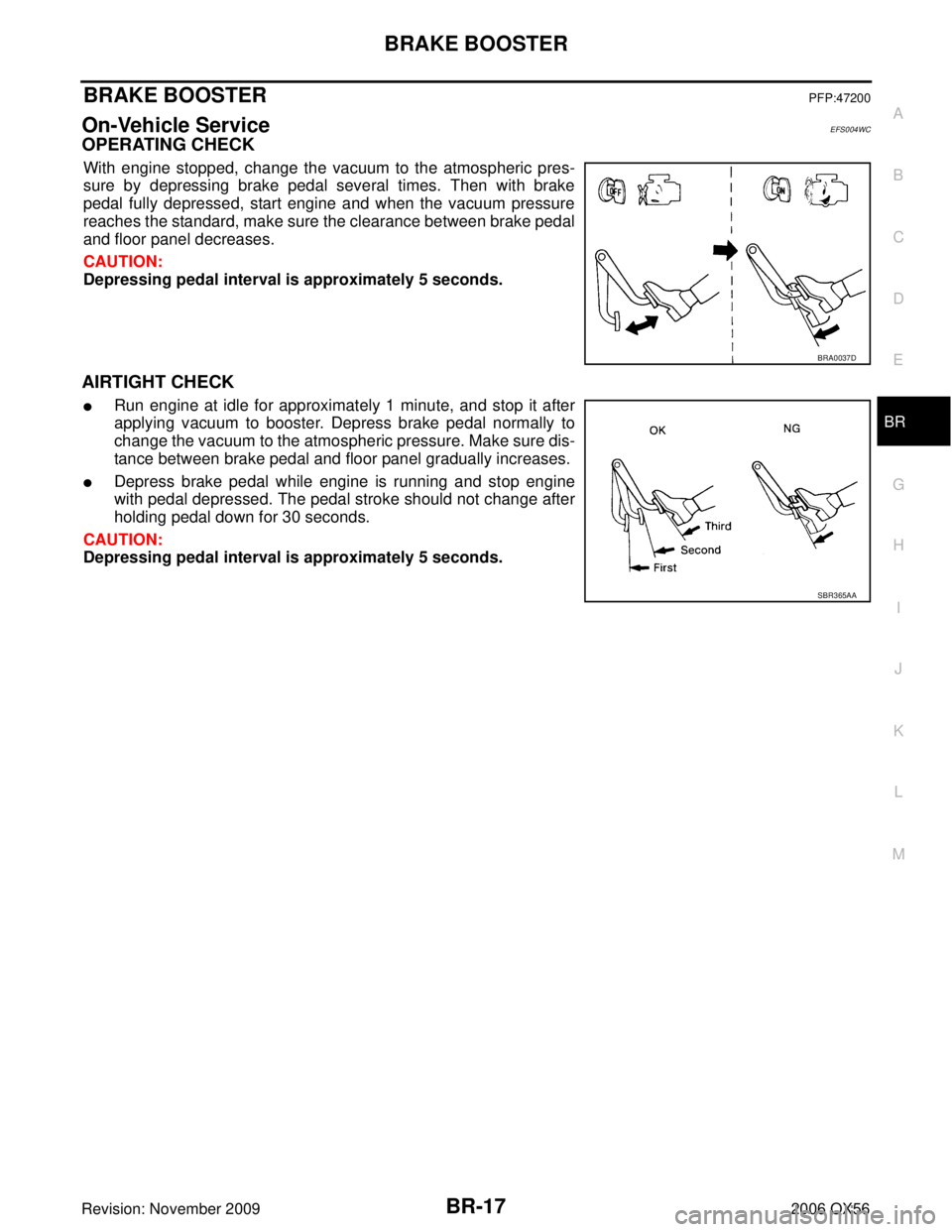
BRAKE BOOSTERBR-17
C
DE
G H
I
J
K L
M A
B
BR
Revision: November 2009 2006 QX56
BRAKE BOOSTERPFP:47200
On-Vehicle ServiceEFS004WC
OPERATING CHECK
With engine stopped, change the vacuum to the atmospheric pres-
sure by depressing brake pedal several times. Then with brake
pedal fully depressed, start engine and when the vacuum pressure
reaches the standard, make sure the clearance between brake pedal
and floor panel decreases.
CAUTION:
Depressing pedal interval is approximately 5 seconds.
AIRTIGHT CHECK
Run engine at idle for approximately 1 minute, and stop it after
applying vacuum to booster. Depress brake pedal normally to
change the vacuum to the atmospheric pressure. Make sure dis-
tance between brake pedal and floor panel gradually increases.
Depress brake pedal while engine is running and stop engine
with pedal depressed. The pedal stroke should not change after
holding pedal down for 30 seconds.
CAUTION:
Depressing pedal interval is approximately 5 seconds.
BRA0037D
SBR365AA
Page 1015 of 3383
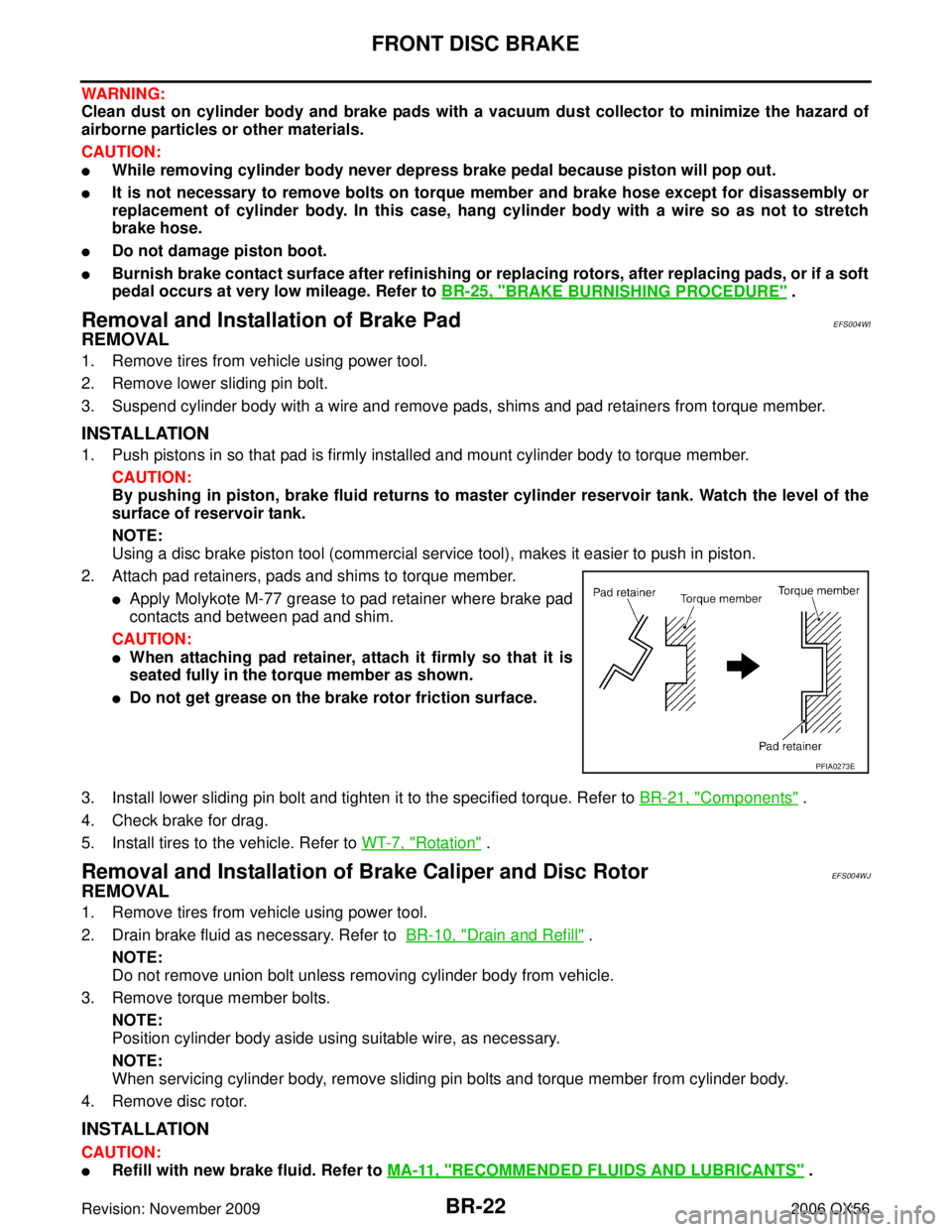
BR-22
FRONT DISC BRAKE
Revision: November 20092006 QX56
WARNING:
Clean dust on cylinder body and brake pads with a vacuum dust collector to minimize the hazard of
airborne particles or other materials.
CAUTION:
While removing cylinder body never depress brake pedal because piston will pop out.
It is not necessary to remove bolts on torque member and brake hose except for disassembly or
replacement of cylinder body. In this case, hang cylinder body with a wire so as not to stretch
brake hose.
Do not damage piston boot.
Burnish brake contact surface after refinishing or replacing rotors, after replacing pads, or if a soft
pedal occurs at very low mileage. Refer to BR-25, "
BRAKE BURNISHING PROCEDURE" .
Removal and Installation of Brake PadEFS004WI
REMOVAL
1. Remove tires from vehicle using power tool.
2. Remove lower sliding pin bolt.
3. Suspend cylinder body with a wire and remove pads, shims and pad retainers from torque member.
INSTALLATION
1. Push pistons in so that pad is firmly installed and mount cylinder body to torque member.
CAUTION:
By pushing in piston, brake fluid returns to master cylinder reservoir tank. Watch the level of the
surface of reservoir tank.
NOTE:
Using a disc brake piston tool (commercial service tool), makes it easier to push in piston.
2. Attach pad retainers, pads and shims to torque member.
Apply Molykote M-77 grease to pad retainer where brake pad
contacts and between pad and shim.
CAUTION:
When attaching pad retainer, attach it firmly so that it is
seated fully in the torque member as shown.
Do not get grease on the brake rotor friction surface.
3. Install lower sliding pin bolt and tighten it to the specified torque. Refer to BR-21, "
Components" .
4. Check brake for drag.
5. Install tires to the vehicle. Refer to WT-7, "
Rotation" .
Removal and Installation of Brake Caliper and Disc RotorEFS004WJ
REMOVAL
1. Remove tires from vehicle using power tool.
2. Drain brake fluid as necessary. Refer to BR-10, "
Drain and Refill" .
NOTE:
Do not remove union bolt unless removing cylinder body from vehicle.
3. Remove torque member bolts.
NOTE:
Position cylinder body aside using suitable wire, as necessary.
NOTE:
When servicing cylinder body, remove sliding pin bolts and torque member from cylinder body.
4. Remove disc rotor.
INSTALLATION
CAUTION:
Refill with new brake fluid. Refer to MA-11, "RECOMMENDED FLUIDS AND LUBRICANTS" .
PFIA0273E
Page 1017 of 3383
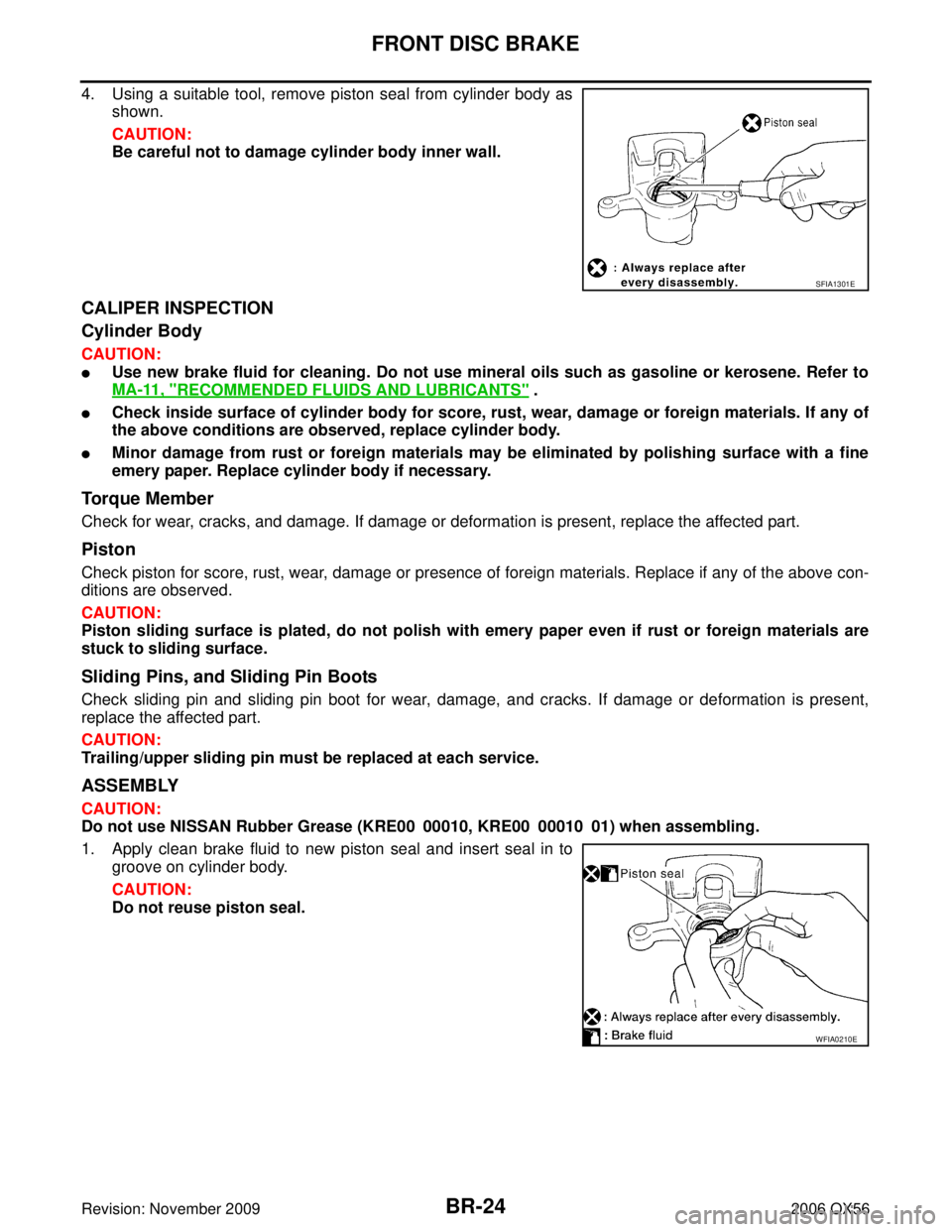
BR-24
FRONT DISC BRAKE
Revision: November 20092006 QX56
4. Using a suitable tool, remove piston seal from cylinder body as
shown.
CAUTION:
Be careful not to damage cylinder body inner wall.
CALIPER INSPECTION
Cylinder Body
CAUTION:
Use new brake fluid for cleaning. Do not use mineral oils such as gasoline or kerosene. Refer to
MA-11, "
RECOMMENDED FLUIDS AND LUBRICANTS" .
Check inside surface of cylinder body for score, rust, wear, damage or foreign materials. If any of
the above conditions are observed, replace cylinder body.
Minor damage from rust or foreign materials may be eliminated by polishing surface with a fine
emery paper. Replace cylinder body if necessary.
To r q u e M e m b e r
Check for wear, cracks, and damage. If damage or deformation is present, replace the affected part.
Piston
Check piston for score, rust, wear, damage or presence of foreign materials. Replace if any of the above con-
ditions are observed.
CAUTION:
Piston sliding surface is plated, do not polish with emery paper even if rust or foreign materials are
stuck to sliding surface.
Sliding Pins, and Sliding Pin Boots
Check sliding pin and sliding pin boot for wear, damage, and cracks. If damage or deformation is present,
replace the affected part.
CAUTION:
Trailing/upper sliding pin must be replaced at each service.
ASSEMBLY
CAUTION:
Do not use NISSAN Rubber Grease (KRE00 00010, KRE00 00010 01) when assembling.
1. Apply clean brake fluid to new piston seal and insert seal in to
groove on cylinder body.
CAUTION:
Do not reuse piston seal.
SFIA1301E
WFIA0210E
Page 1018 of 3383

FRONT DISC BRAKEBR-25
C
DE
G H
I
J
K L
M A
B
BR
Revision: November 2009 2006 QX56
2. Apply brake fluid to piston and piston boot, then install piston
boot in to piston groove.
CAUTION:
Do not reuse piston boot.
3. Insert into cylinder body by hand and insert piston boot piston-side lip into piston groove. CAUTION:
Press piston evenly and vary the pressing point to prevent cylinder body inner wall from being
rubbed.
4. Install sliding pins and sliding pin boots to torque member.
CAUTION:
Trailing/upper sliding pin must be replaced at each service.
5. Install cylinder body. Tighten sliding pin bolt to the specification. Refer to BR-21, "
Components" .
DISC ROTOR INSPECTION
Visual Inspection
Check surface of disc rotor for uneven wear, cracks, and serious damage. If any of them is detected, replace
applicable part.
Runout Inspection
1. Using 2 or more wheel nuts, temporarily install disc rotor to wheel hub.
2. Inspect runout using a dial gauge. (Measured at 10mm (0.39 in)
inside the disc edge.)
NOTE:
Make sure that wheel bearing axial end play is within the specifi-
cations before measuring runout. Refer to FA X - 5 , "
WHEEL
BEARING INSPECTION" .
3. If runout is outside the limit, find the minimum runout point by shifting mounting positions of disc rotor and wheel hub by one
hole.
4. If runout still out of specification, turn rotor with on-car brake lathe.
Thickness Inspection
Using a micrometer, check thickness of disc rotor. If thickness is
either at or below the wear limit, or exceeds maximum uneven wear,
replace disc rotor.
BRAKE BURNISHING PROCEDURE
Burnish brake contact surface according to the following procedure after refinishing or replacing rotors, after
replacing pads, or if a soft pedal occurs at very low mileage.
WFIA0211E
Runout limit (on vehicle) : Refer to BR-32,
"Front Disc Brake" .
BRA0013D
Standard thickness : Refer to BR-32, "Front
Disc Brake" .
Repair limit thickness : Refer to BR-32, "
Front
Disc Brake" .
Maximum uneven wear
(Measured at 8 positions) : Refer to
BR-32, "
Front
Disc Brake" .
SBR020B
Page 1021 of 3383
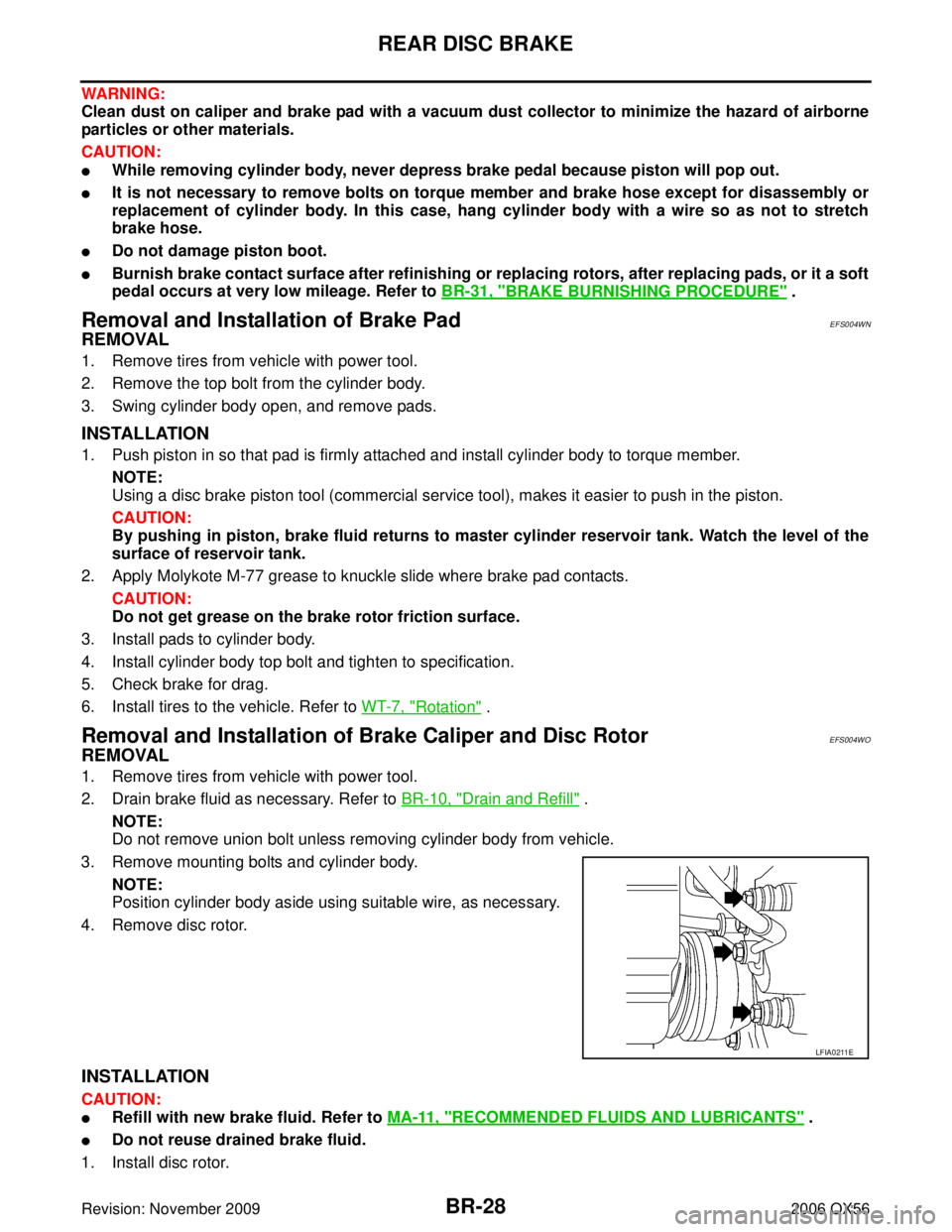
BR-28
REAR DISC BRAKE
Revision: November 20092006 QX56
WARNING:
Clean dust on caliper and brake pad with a vacuum dust collector to minimize the hazard of airborne
particles or other materials.
CAUTION:
While removing cylinder body, never depress brake pedal because piston will pop out.
It is not necessary to remove bolts on torque member and brake hose except for disassembly or
replacement of cylinder body. In this case, hang cylinder body with a wire so as not to stretch
brake hose.
Do not damage piston boot.
Burnish brake contact surface after refinishing or replacing rotors, after replacing pads, or it a soft
pedal occurs at very low mileage. Refer to BR-31, "
BRAKE BURNISHING PROCEDURE" .
Removal and Installation of Brake PadEFS004WN
REMOVAL
1. Remove tires from vehicle with power tool.
2. Remove the top bolt from the cylinder body.
3. Swing cylinder body open, and remove pads.
INSTALLATION
1. Push piston in so that pad is firmly attached and install cylinder body to torque member.
NOTE:
Using a disc brake piston tool (commercial service tool), makes it easier to push in the piston.
CAUTION:
By pushing in piston, brake fluid returns to master cylinder reservoir tank. Watch the level of the
surface of reservoir tank.
2. Apply Molykote M-77 grease to knuckle slide where brake pad contacts.
CAUTION:
Do not get grease on the brake rotor friction surface.
3. Install pads to cylinder body.
4. Install cylinder body top bolt and tighten to specification.
5. Check brake for drag.
6. Install tires to the vehicle. Refer to WT-7, "
Rotation" .
Removal and Installation of Brake Caliper and Disc RotorEFS004WO
REMOVAL
1. Remove tires from vehicle with power tool.
2. Drain brake fluid as necessary. Refer to BR-10, "
Drain and Refill" .
NOTE:
Do not remove union bolt unless removing cylinder body from vehicle.
3. Remove mounting bolts and cylinder body. NOTE:
Position cylinder body aside using suitable wire, as necessary.
4. Remove disc rotor.
INSTALLATION
CAUTION:
Refill with new brake fluid. Refer to MA-11, "RECOMMENDED FLUIDS AND LUBRICANTS" .
Do not reuse drained brake fluid.
1. Install disc rotor.
LFIA0211E
Page 1025 of 3383

BR-32
SERVICE DATA AND SPECIFICATIONS (SDS)
Revision: November 20092006 QX56
SERVICE DATA AND SPECIFICATIONS (SDS)PFP:00030
General SpecificationsEFS004WQ
Unit: mm (in)
Brake PedalEFS004WR
Brake BoosterEFS004WS
Check ValveEFS004WT
Front Disc BrakeEFS004WU
Front brake Brake modelCLZ31VCAD41VA
Rotor outer diameter × thickness 320 × 26 (12.60 × 1.02) 350 x 30 (13.78 x 1.181)
Pad Length × width × thickness 111 . 0
× 73.5 × 11.88 (4.73 ×
2.894 × 0.468) 151.6 x 56.5 x 12 (5.968 x
2.224 x 0.47)
Cylinder bore diameter 51 (2.01)51 (2.01)
Rear brake Brake model AD14VE
Rotor outer diameter × thickness 320 × 14 (12.60 × 0.55)
Pad Length × width × thickness 83.0 × 33.0 × 8.5 (3.268 × 1.299 × 0.335)
Cylinder bore diameter 48 (1.89)
Control valve Valve model Electric brake force distribution
Brake booster Booster model
C215T
Diaphragm diameter 215 (8.46)
Recommended brake fluid Genuine NISSAN Super Heavy Duty Brake Fluid or equivalent
Brake pedal height (from dash lower panel top surface) 182.3 − 192.3 mm (7.18 − 7.57 in)
Depressed pedal height [under a force of 490 N (50 kg-f, 110 lb-f)
with engine running] More than 90.3 mm (3.55 in)
Clearance between stopper rubber and the threaded end of stop
lamp switch 0.74
− 1.96 mm (0.029 − 0.077 in)
Pedal play 3 − 11 mm (0.12 − 0.43 in)
Output rod installation standard dimension 15.6 − 15.9 mm (0.614 − 0.626 in)
Vacuum leakage
[at vacuum of – 66.7 kPa(– 500 mmHg, – 19.69 inHg)] Within 1.3 kPa (10 mmHg, 0.39 inHg) of vacuum for 15 seconds
Brake model
CLZ31VCAD41VA
Brake pad Standard thickness (new)
11.88 mm (0.468 in)12 mm (0.47 in)
Repair limit thickness 1.0 mm (0.039 in)1.0 mm (0.039 in)
Disc rotor Standard thickness (new)
26.0 mm (1.024 in) 30.0 mm (1.181 in)
Repair limit thickness 24.5 mm (0.965 in) 28.5 mm (1.122 in)
Maximum uneven wear (measured at 8 positions) 0.015 mm (0.0006 in)
Runout limit (with it attached to the vehicle) 0.03 mm (0.001 in)
Page 1026 of 3383
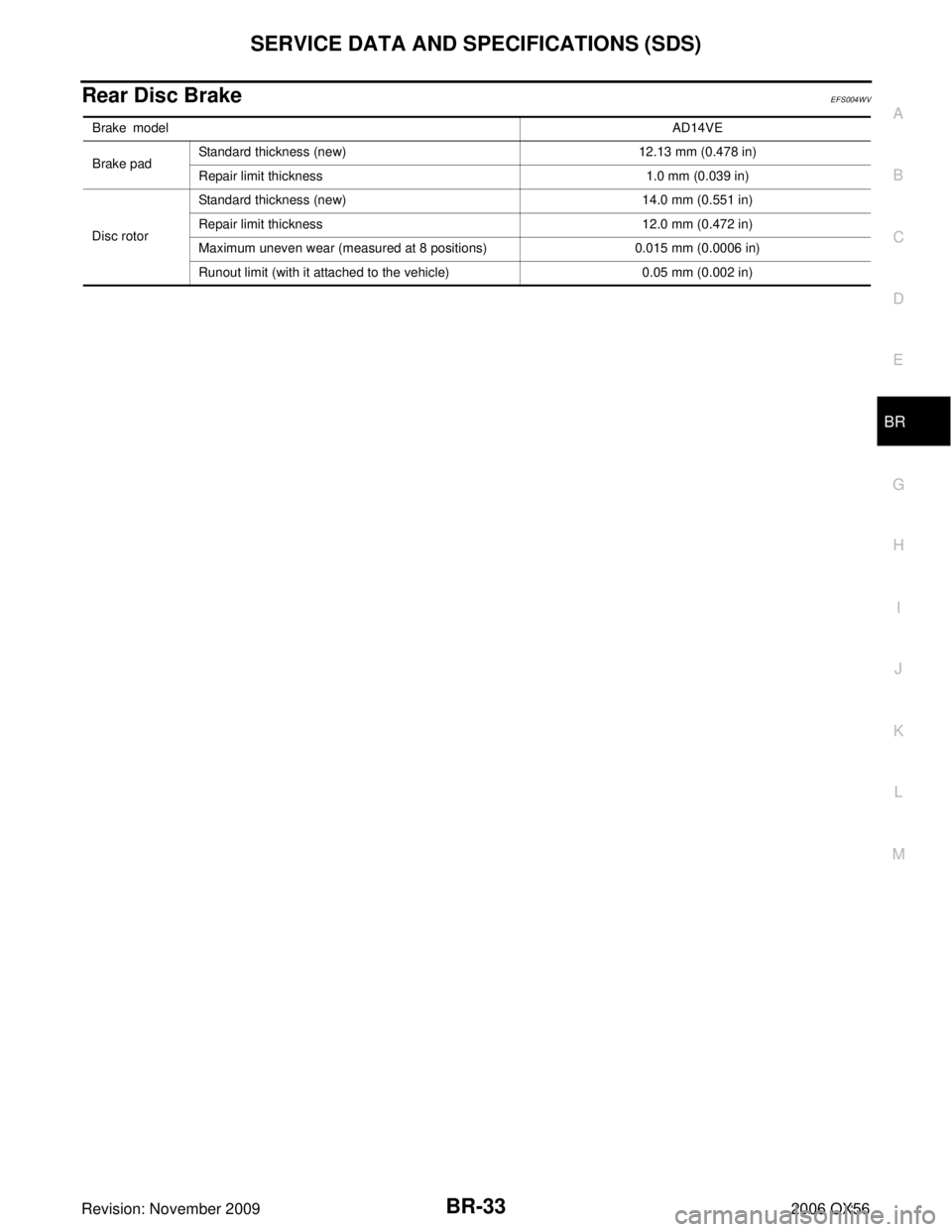
SERVICE DATA AND SPECIFICATIONS (SDS)BR-33
C
DE
G H
I
J
K L
M A
B
BR
Revision: November 2009 2006 QX56
Rear Disc BrakeEFS004WV
Brake modelAD14VE
Brake pad Standard thickness (new)
12.13 mm (0.478 in)
Repair limit thickness 1.0 mm (0.039 in)
Disc rotor Standard thickness (new)
14.0 mm (0.551 in)
Repair limit thickness 12.0 mm (0.472 in)
Maximum uneven wear (measured at 8 positions) 0.015 mm (0.0006 in)
Runout limit (with it attached to the vehicle) 0.05 mm (0.002 in)
Page 1027 of 3383
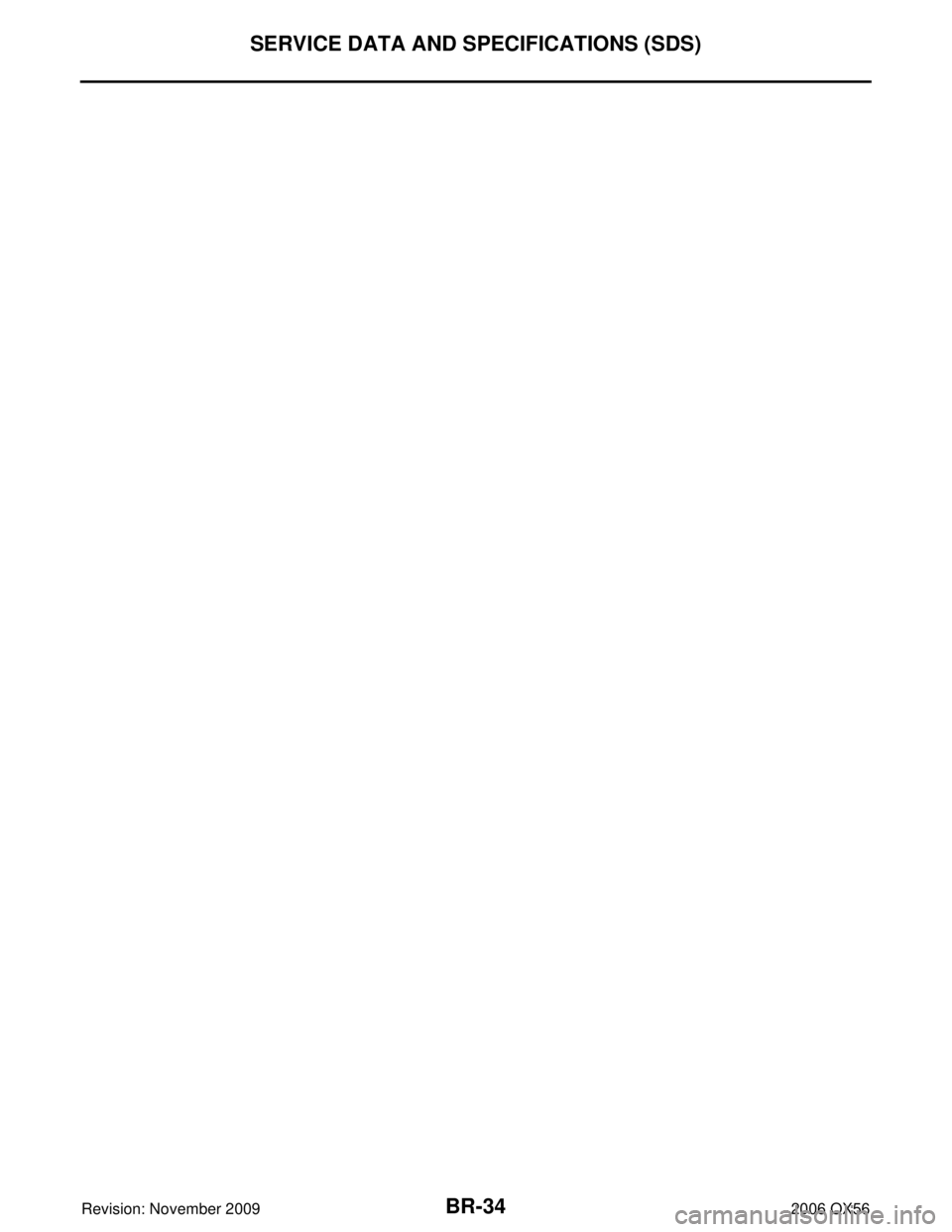
BR-34
SERVICE DATA AND SPECIFICATIONS (SDS)
Revision: November 20092006 QX56
Page 1028 of 3383
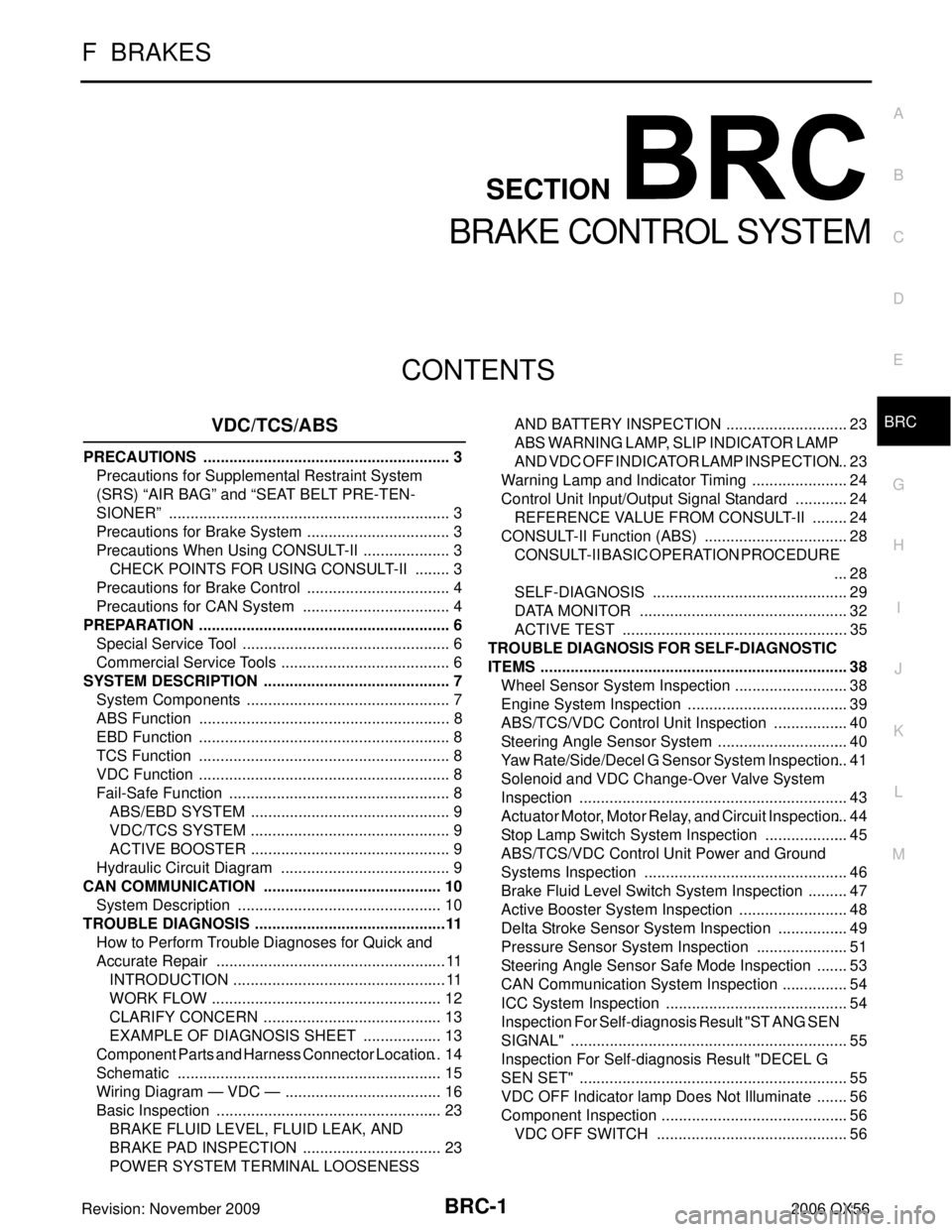
BRC-1
BRAKE CONTROL SYSTEM
F BRAKES
CONTENTS
C
DE
G H
I
J
K L
M
SECTION
A
B
BRC
Revision: November 2009 2006 QX56VDC/TCS/ABS
PRECAUTIONS .......................................................... 3
Precautions for Supplemental Restraint System
(SRS) “AIR BAG” and “SEAT BELT PRE-TEN-
SIONER” ............................................................. ..... 3
Precautions for Brake System ............................. ..... 3
Precautions When Using CONSULT-II ................ ..... 3
CHECK POINTS FOR USING CONSULT-II .... ..... 3
Precautions for Brake Control ............................. ..... 4
Precautions for CAN System .............................. ..... 4
PREPARATION ...................................................... ..... 6
Special Service Tool ............................................ ..... 6
Commercial Service Tools ................................... ..... 6
SYSTEM DESCRIPTION ............................................ 7 System Components ........................................... ..... 7
ABS Function ........................................................... 8
EBD Function ...................................................... ..... 8
TCS Function ...................................................... ..... 8
VDC Function ...................................................... ..... 8
Fail-Safe Function .................................................... 8 ABS/EBD SYSTEM .......................................... ..... 9
VDC/TCS SYSTEM .......................................... ..... 9
ACTIVE BOOSTER .......................................... ..... 9
Hydraulic Circuit Diagram ................................... ..... 9
CAN COMMUNICATION ....................................... ... 10
System Description ............................................. ... 10
TROUBLE DIAGNOSIS ......................................... ....11
How to Perform Trouble Diagnoses for Quick and
Accurate Repair .................................................. .... 11
INTRODUCTION .............................................. .... 11
WORK FLOW ................................................... ... 12
CLARIFY CONCERN ....................................... ... 13
EXAMPLE OF DIAGNOSIS SHEET ................ ... 13
Component Parts and Harness Connector Location ... 14
Schematic ........................................................... ... 15
Wiring Diagram — VDC — .................................. ... 16
Basic Inspection .................................................. ... 23
BRAKE FLUID LEVEL, FLUID LEAK, AND
BRAKE PAD INSPECTION .............................. ... 23
POWER SYSTEM TERMINAL LOOSENESS AND BATTERY INSPECTION ..........................
... 23
ABS WARNING LAMP, SLIP INDICATOR LAMP
AND VDC OFF INDICATOR LAMP INSPECTION ... 23
Warning Lamp and Indicator Timing .................... ... 24
Control Unit Input/Output Signal Standard .......... ... 24
REFERENCE VALUE FROM CONSULT-II ...... ... 24
CONSULT-II Function (ABS) ............................... ... 28
CONSULT-II BASIC OPERATION PROCEDURE ... 28
SELF-DIAGNOSIS ........................................... ... 29
DATA MONITOR .............................................. ... 32
ACTIVE TEST ..................................................... 35
TROUBLE DIAGNOSIS FOR SELF-DIAGNOSTIC
ITEMS ..................................................................... ... 38
Wheel Sensor System Inspection ........................ ... 38
Engine System Inspection ................................... ... 39
ABS/TCS/VDC Control Unit Inspection ............... ... 40
Steering Angle Sensor System ............................ ... 40
Yaw Rate/Side/Decel G Sensor System Inspection ... 41
Solenoid and VDC Change-Over Valve System
Inspection ............................................................ ... 43
Actuator Motor, Motor Relay, and Circuit Inspection ... 44
Stop Lamp Switch System Inspection ................. ... 45
ABS/TCS/VDC Control Unit Power and Ground
Systems Inspection ............................................. ... 46
Brake Fluid Level Switch System Inspection ....... ... 47
Active Booster System Inspection ....................... ... 48
Delta Stroke Sensor System Inspection .............. ... 49
Pressure Sensor System Inspection ................... ... 51
Steering Angle Sensor Safe Mode Inspection ..... ... 53
CAN Communication System Inspection ............. ... 54
ICC System Inspection ........................................ ... 54
Inspection For Self-diagnosis Result "ST ANG SEN
SIGNAL" .............................................................. ... 55
Inspection For Self-diagnosis Result "DECEL G
SEN SET" ............................................................ ... 55
VDC OFF Indicator lamp Does Not Illuminate ..... ... 56
Component Inspection ......................................... ... 56
VDC OFF SWITCH .......................................... ... 56
Page 1029 of 3383
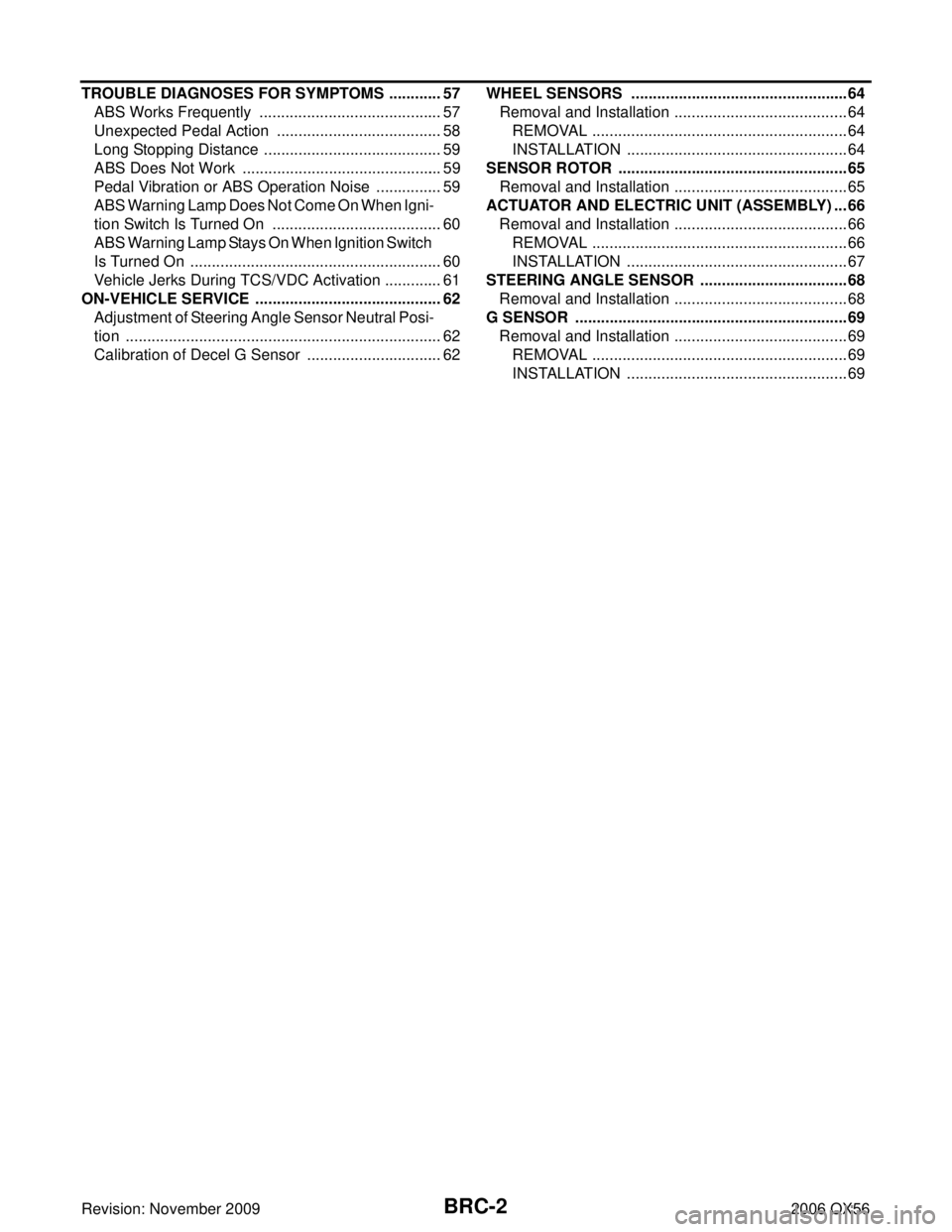
BRC-2Revision: November 20092006 QX56
TROUBLE DIAGNOSES FOR SYMPTOMS ..........
... 57
ABS Works Frequently ........................................ ... 57
Unexpected Pedal Action .................................... ... 58
Long Stopping Distance ....................................... ... 59
ABS Does Not Work ............................................... 59
Pedal Vibration or ABS Operation Noise ............. ... 59
ABS Warning Lamp Does Not Come On When Igni-
tion Switch Is Turned On ..................................... ... 60
ABS Warning Lamp Stays On When Ignition Switch
Is Turned On ........................................................... 60
Vehicle Jerks During TCS/VDC Activation ........... ... 61
ON-VEHICLE SERVICE ......................................... ... 62
Adjustment of Steering Angle Sensor Neutral Posi-
tion ....................................................................... ... 62
Calibration of Decel G Sensor ............................. ... 62WHEEL SENSORS ................................................
... 64
Removal and Installation ...................................... ... 64
REMOVAL ......................................................... ... 64
INSTALLATION ................................................. ... 64
SENSOR ROTOR ................................................... ... 65
Removal and Installation ...................................... ... 65
ACTUATOR AND ELECTRIC UNIT (ASSEMBLY) ... 66 Removal and Installation ...................................... ... 66
REMOVAL ......................................................... ... 66
INSTALLATION ................................................. ... 67
STEERING ANGLE SENSOR ................................ ... 68
Removal and Installation ...................................... ... 68
G SENSOR ............................................................. ... 69
Removal and Installation ...................................... ... 69
REMOVAL ......................................................... ... 69
INSTALLATION ................................................. ... 69