engine oil INFINITI QX56 2007 Factory Service Manual
[x] Cancel search | Manufacturer: INFINITI, Model Year: 2007, Model line: QX56, Model: INFINITI QX56 2007Pages: 3061, PDF Size: 64.56 MB
Page 1775 of 3061
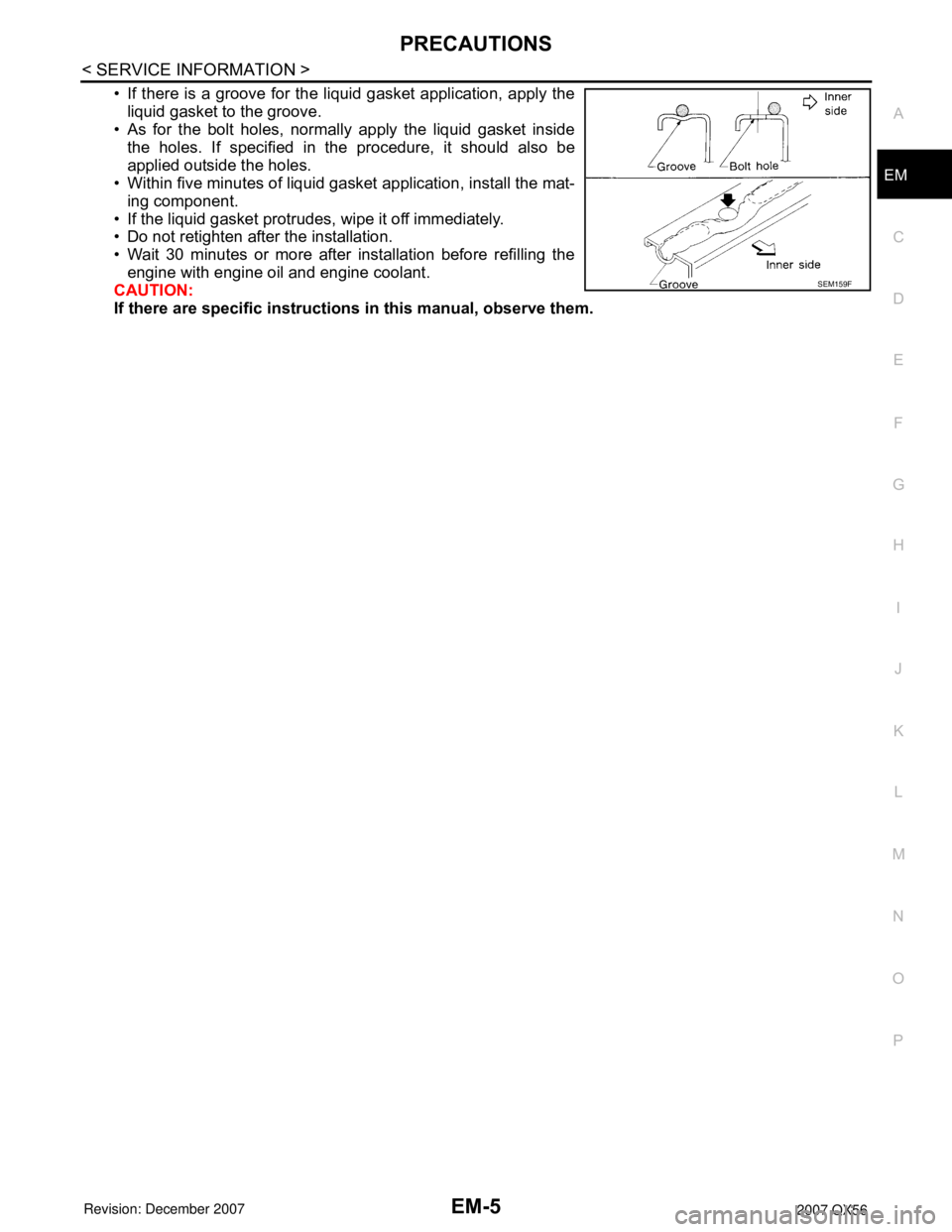
PRECAUTIONSEM-5
< SERVICE INFORMATION >
C
DE
F
G H
I
J
K L
M A
EM
NP
O
• If there is a groove for the liquid gasket application, apply the
liquid gasket to the groove.
• As for the bolt holes, normally apply the liquid gasket inside
the holes. If specified in t he procedure, it should also be
applied outside the holes.
• Within five minutes of liquid gasket application, install the mat-
ing component.
• If the liquid gasket protrudes, wipe it off immediately.
• Do not retighten after the installation.
• Wait 30 minutes or more after installation before refilling the
engine with engine oil and engine coolant.
CAUTION:
If there are specific instructions in this manual, observe them.
SEM159F
Page 1781 of 3061
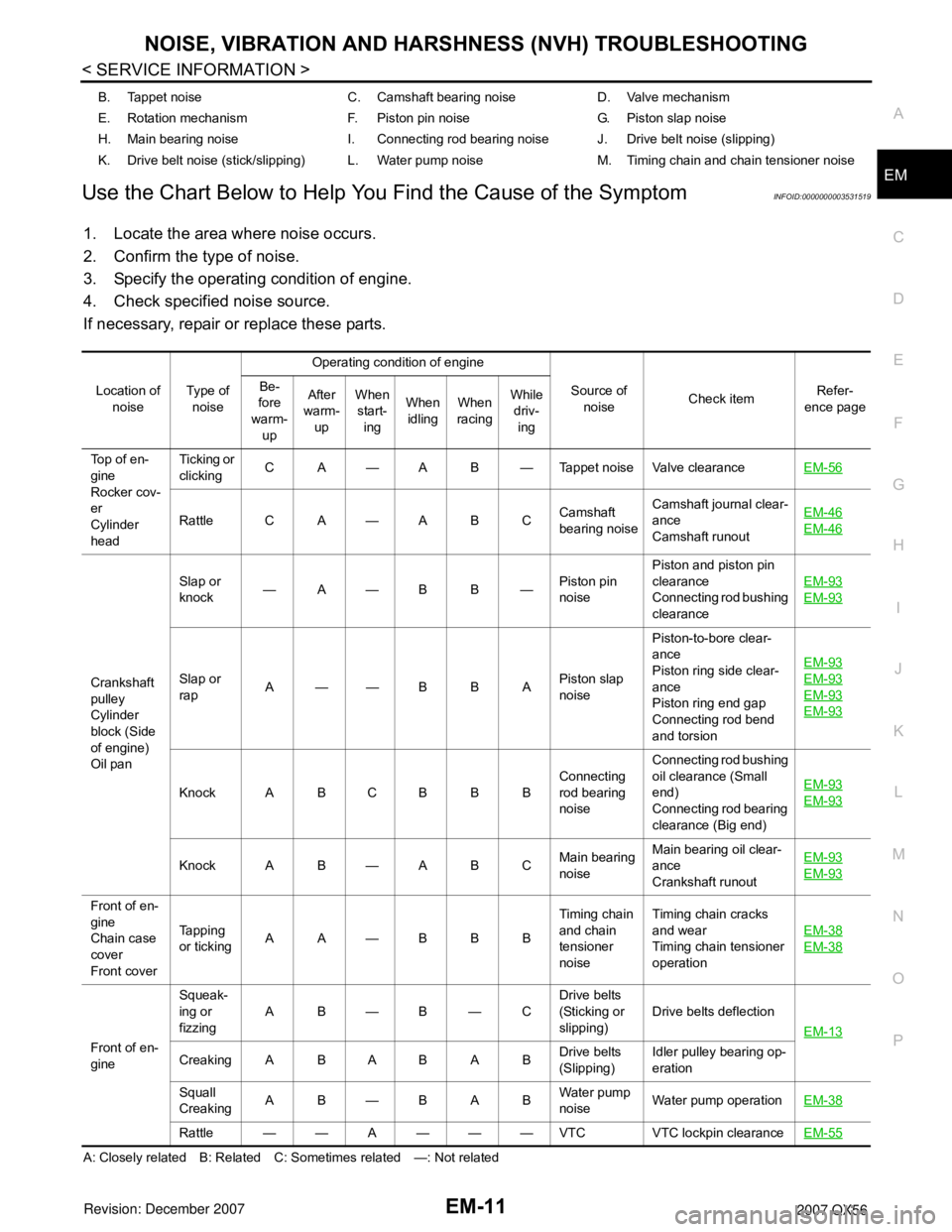
NOISE, VIBRATION AND HARSHNESS (NVH) TROUBLESHOOTINGEM-11
< SERVICE INFORMATION >
C
DE
F
G H
I
J
K L
M A
EM
NP
O
Use the Chart Below to Help You
Find the Cause of the SymptomINFOID:0000000003531519
1. Locate the area where noise occurs.
2. Confirm the type of noise.
3. Specify the operating condition of engine.
4. Check specified noise source.
If necessary, repair or replace these parts.
A: Closely related B: Related C: Sometimes related —: Not relatedB. Tappet noise C. Camshaft bearing noise D. Valve mechanism
E. Rotation mechanism F. Piston pin noise G. Piston slap noise
H. Main bearing noise I. Connecting rod bearing noise J. Drive belt noise (slipping)
K. Drive belt noise (stick/slipping) L. Water pump noise M. Timing chain and chain tensioner noise
Location of noise Ty p e o f
noise Operating condition of engine
Source of noise Check item
Refer-
ence page
Be-
fore
warm- up After
warm-
up When
start-
ing When
idling When
racing While
driv-
ing
Top of en-
gine
Rocker cov-
er
Cylinder
head Ticking or
clicking
C A — A B — Tappet noise Valve clearance
EM-56
Rattle C A — A B CCamshaft
bearing noiseCamshaft journal clear-
ance
Camshaft runout EM-46EM-46
Crankshaft
pulley
Cylinder
block (Side
of engine)
Oil panSlap or
knock
—A—B B— Piston pin
noisePiston and piston pin
clearance
Connecting rod bushing
clearance EM-93
EM-93
Slap or
rap
A——B B A Piston slap
noisePiston-to-bore clear-
ance
Piston ring side clear-
ance
Piston ring end gap
Connecting rod bend
and torsion EM-93EM-93
EM-93
EM-93
Knock A B C B B B
Connecting
rod bearing
noiseConnecting rod bushing
oil clearance (Small
end)
Connecting rod bearing
clearance (Big end)
EM-93EM-93
Knock A B — A B C
Main bearing
noiseMain bearing oil clear-
ance
Crankshaft runout EM-93EM-93
Front of en-
gine
Chain case
cover
Front coverTapping
or ticking
AA—BBB Timing chain
and chain
tensioner
noiseTiming chain cracks
and wear
Timing chain tensioner
operation
EM-38
EM-38
Front of en-
gineSqueak-
ing or
fizzing
AB—B—C
Drive belts
(Sticking or
slipping)Drive belts deflection
EM-13Creaking A B A B A B Drive belts
(Slipping)Idler pulley bearing op-
eration
Squall
Creaking AB—BAB Water pump
noiseWater pump operation
EM-38
Rattle — — A — — — VTC VTC lockpin clearance EM-55
Page 1789 of 3061
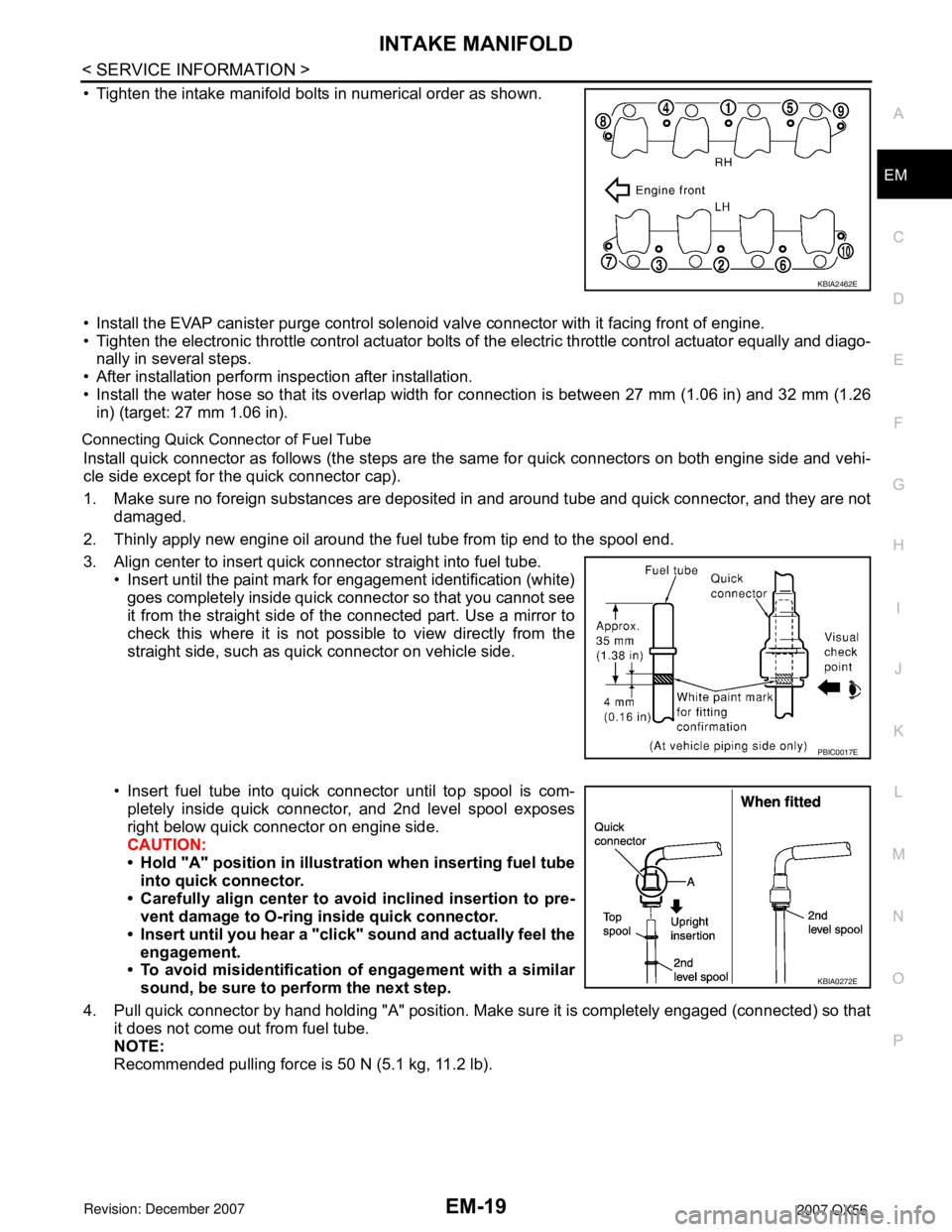
INTAKE MANIFOLDEM-19
< SERVICE INFORMATION >
C
DE
F
G H
I
J
K L
M A
EM
NP
O
• Tighten the intake manifold bolts in numerical order as shown.
• Install the EVAP canister purge control solenoi
d valve connector with it facing front of engine.
• Tighten the electronic throttle control actuator bolts of the electric throttle control actuator equally and diago-
nally in several steps.
• After installation perform inspection after installation.
• Install the water hose so that its overlap width for connection is between 27 mm (1.06 in) and 32 mm (1.26
in) (target: 27 mm 1.06 in).
Connecting Quick Connector of Fuel Tube
Install quick connector as follows (the steps are the same for quick connectors on both engine side and vehi-
cle side except for the quick connector cap).
1. Make sure no foreign substances are deposited in and around tube and quick connector, and they are not
damaged.
2. Thinly apply new engine oil around the fuel tube from tip end to the spool end.
3. Align center to insert quick connector straight into fuel tube. • Insert until the paint mark for engagement identification (white)
goes completely inside quick connector so that you cannot see
it from the straight side of the connected part. Use a mirror to
check this where it is not possible to view directly from the
straight side, such as quick connector on vehicle side.
• Insert fuel tube into quick connector until top spool is com- pletely inside quick connector, and 2nd level spool exposes
right below quick connector on engine side.
CAUTION:
• Hold "A" position in illustration when inserting fuel tubeinto quick connector.
• Carefully align center to avoid inclined insertion to pre-
vent damage to O-ring inside quick connector.
• Insert until you hear a "click" sound and actually feel the engagement.
• To avoid misidentification of engagement with a similar
sound, be sure to perform the next step.
4. Pull quick connector by hand holding "A" position. Make sure it is completely engaged (connected) so that it does not come out from fuel tube.
NOTE:
Recommended pulling force is 50 N (5.1 kg, 11.2 lb).
KBIA2462E
PBIC0017E
KBIA0272E
Page 1792 of 3061
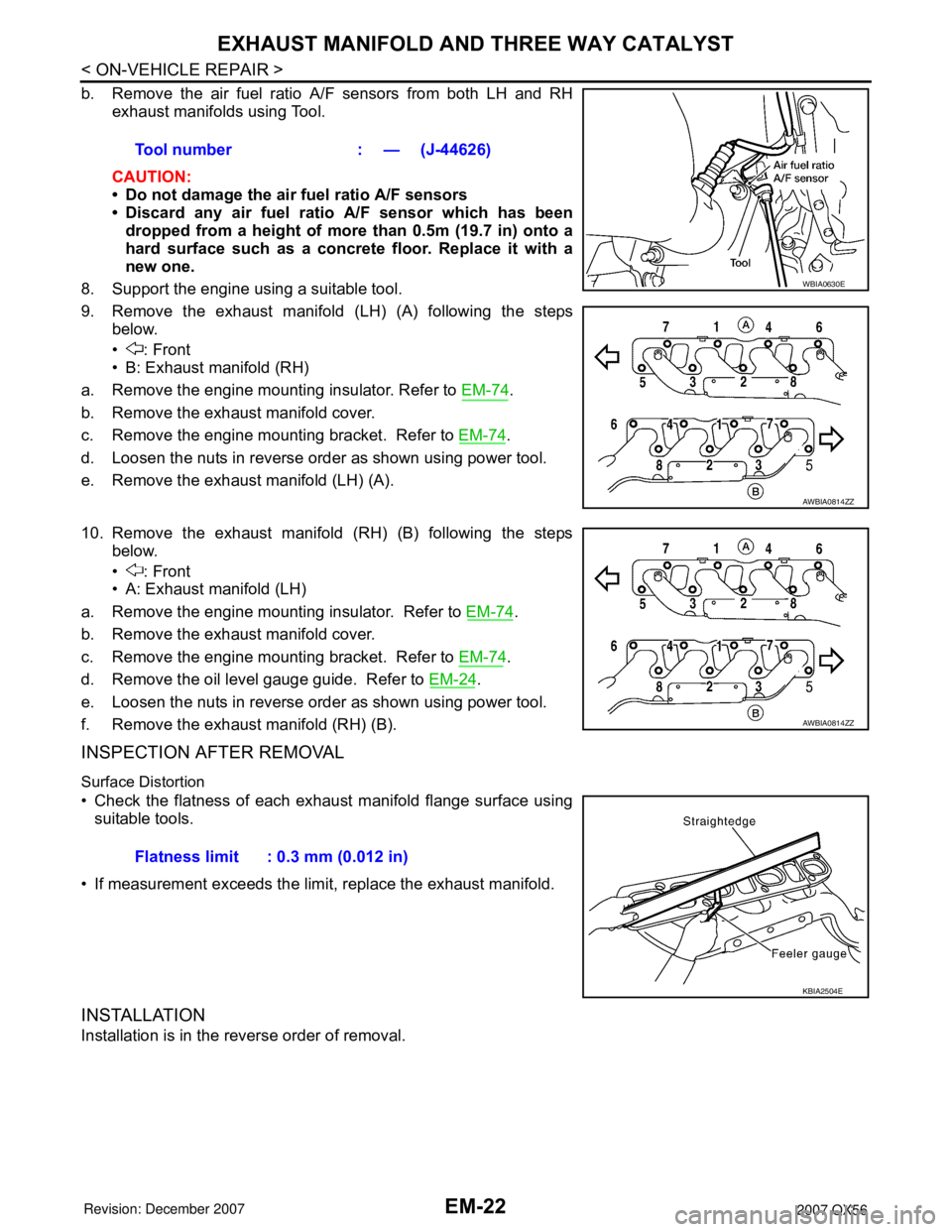
EM-22
< ON-VEHICLE REPA IR >
EXHAUST MANIFOLD AND THREE WAY CATALYST
b. Remove the air fuel ratio A /F sensors from both LH and RH
exhaust
manifolds using T ool.
CAUTIO
N:
•Do not damage the air fuel ratio A/F sensors
•D iscard any air fuel ratio A /F sensor which h as been
dr
opped from a heig ht of more than 0.5m ( 19.7 in) onto a
h ard surface such as a c on crete floor. Re place it with a
new one.
8. Support the engine using a suitable t ool.
9. Remove the exhaust manifold (LH) (A) following the steps
belo
w.
•: Front
•B: Exhaust manifold (RH)
a. Remove the engine mounting insulator. Refer to EM-74.
b. Remove the exhaust manif old cover.
c. Remove the engine mounting bracket. Refer to EM-74.
d. Loosen the nuts in reverse order as shown using power tool.
e. Remove the exhaust manifold (LH) (A).
10
. Remove the exhaust manifold (RH) (B) following the steps
belo
w.
•: Front
•A: Exhaust manifold (LH)
a. Remove the engine mounting insulator. Refer to EM-74.
b. Remove the exhaust manif old c over.
c. Remove the engine mounting bracket. Refer to EM-74.
d. Remove the oil level gauge guide. Refer to EM-24.
e. Loosen the nuts in reverse order as shown using power tool.
f. Remove the ex hau st manif old (RH) (B).
INSP ECTION AFTER REMOVAL
Surface Distortion
•C heck the flatness of each exhaust manifold flange surface using
sui
t able tools.
•If measurement exc eeds the limi t, replace the exhaust manifold.
INST ALLA TION
Installation is in the reverse order of removal.
To ol number: — (J-4 4626)
WBIA 0630E
AW BIA0814ZZ
AW BIA0814ZZ
Fl atness limit: 0.3 mm (0. 012 in)
KBIA 2504E
Page 1794 of 3061
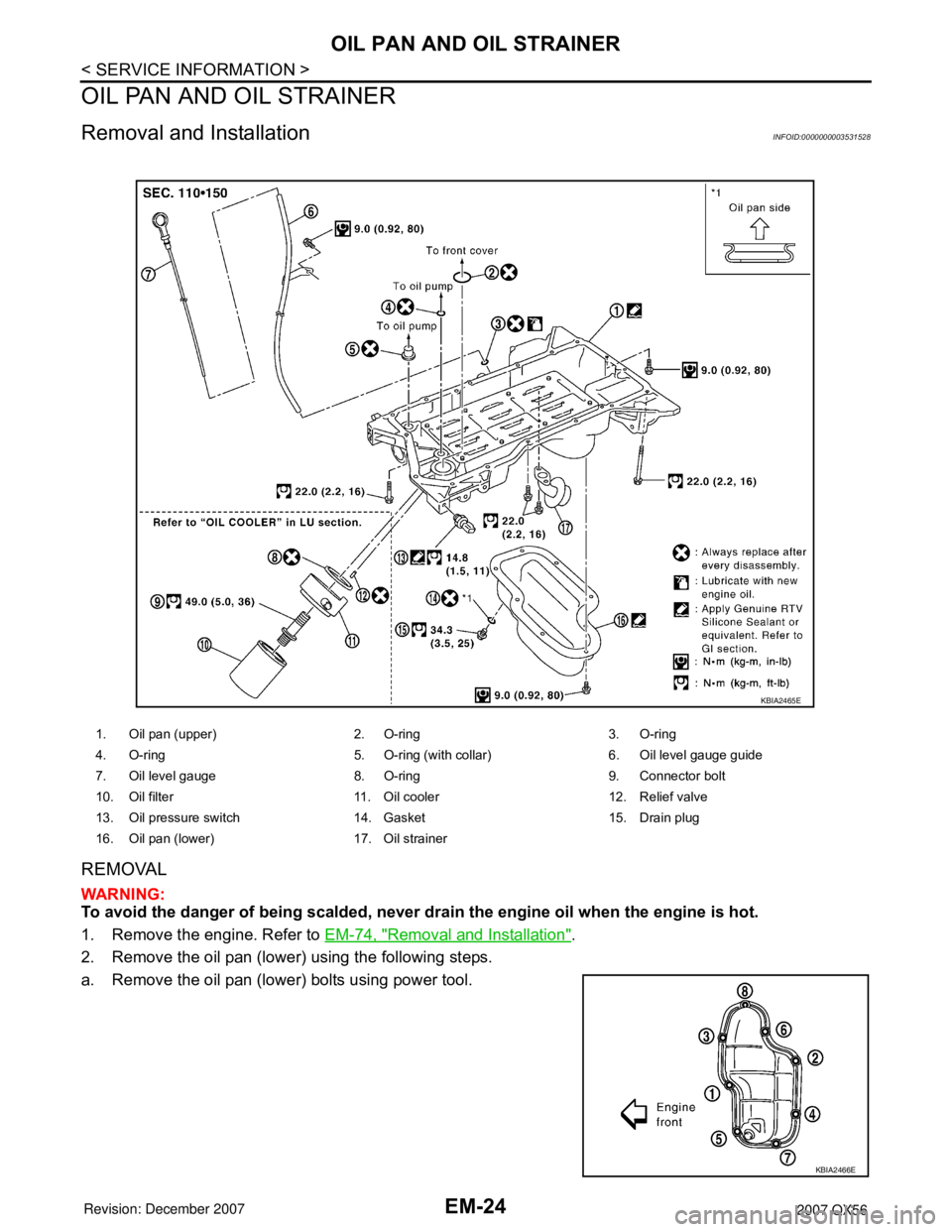
EM-24
< SERVICE INFORMATION >
OIL PAN AND OIL STRAINER
OIL PAN AND OIL STRAINER
Removal and InstallationINFOID:0000000003531528
REMOVAL
WARNING:
To avoid the danger of being scalded, never drain the engine oil when the engine is hot.
1. Remove the engine. Refer to EM-74, "
Removal and Installation".
2. Remove the oil pan (lower) using the following steps.
a. Remove the oil pan (lower) bolts using power tool.
1. Oil pan (upper) 2. O-ring 3. O-ring
4. O-ring 5. O-ring (with collar) 6. Oil level gauge guide
7. Oil level gauge 8. O-ring 9. Connector bolt
10. Oil filter 11. Oil cooler 12. Relief valve
13. Oil pressure switch 14. Gasket 15. Drain plug
16. Oil pan (lower) 17. Oil strainer
KBIA2465E
KBIA2466E
Page 1797 of 3061
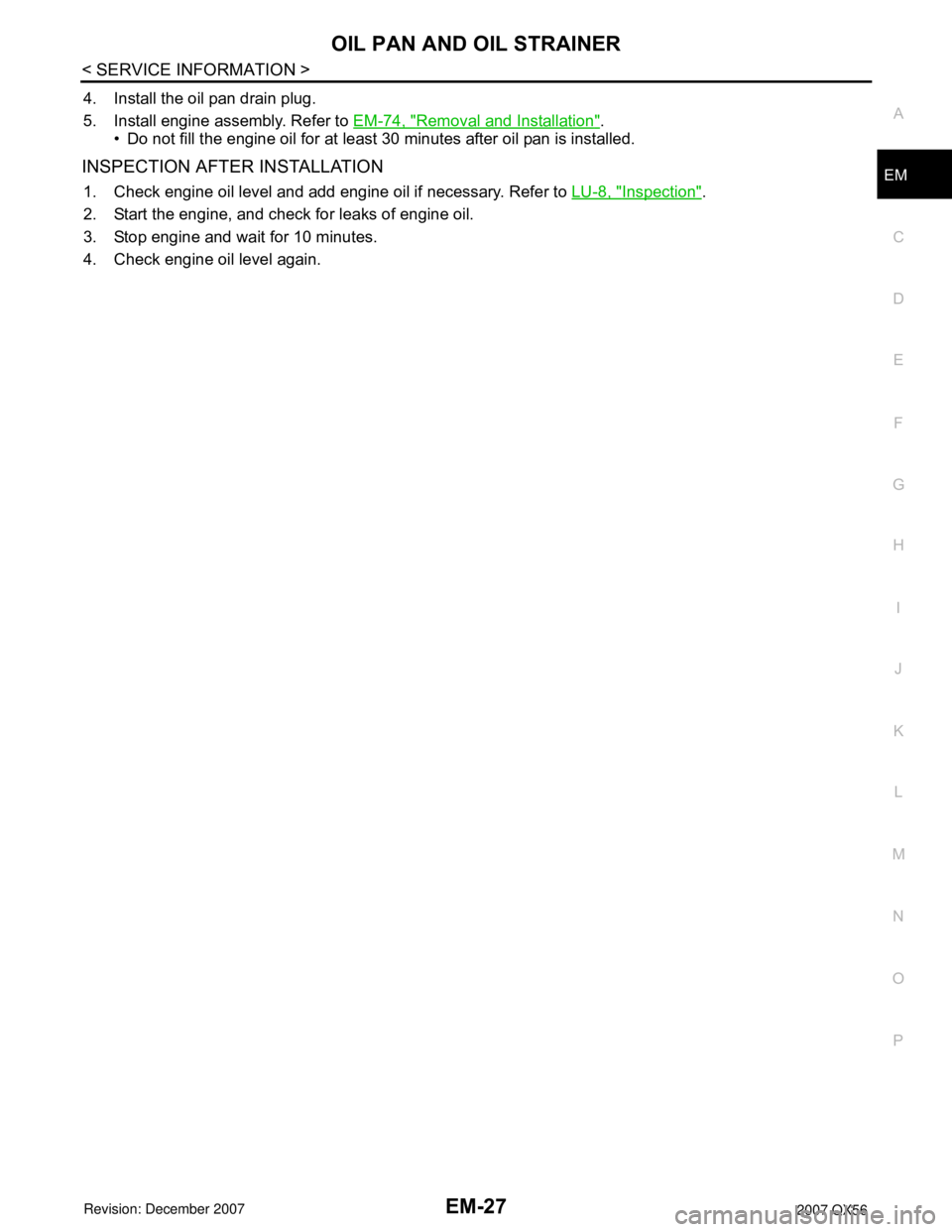
OIL PAN AND OIL STRAINEREM-27
< SERVICE INFORMATION >
C
DE
F
G H
I
J
K L
M A
EM
NP
O
4. Install the oil pan drain plug.
5. Install engine assembly. Refer to
EM-74, "
Removal and Installation".
• Do not fill the engine oil for at least 30 minutes after oil pan is installed.
INSPECTION AFTER INSTALLATION
1. Check engine oil level and add engine oil if necessary. Refer to LU-8, "Inspection".
2. Start the engine, and check for leaks of engine oil.
3. Stop engine and wait for 10 minutes.
4. Check engine oil level again.
Page 1798 of 3061
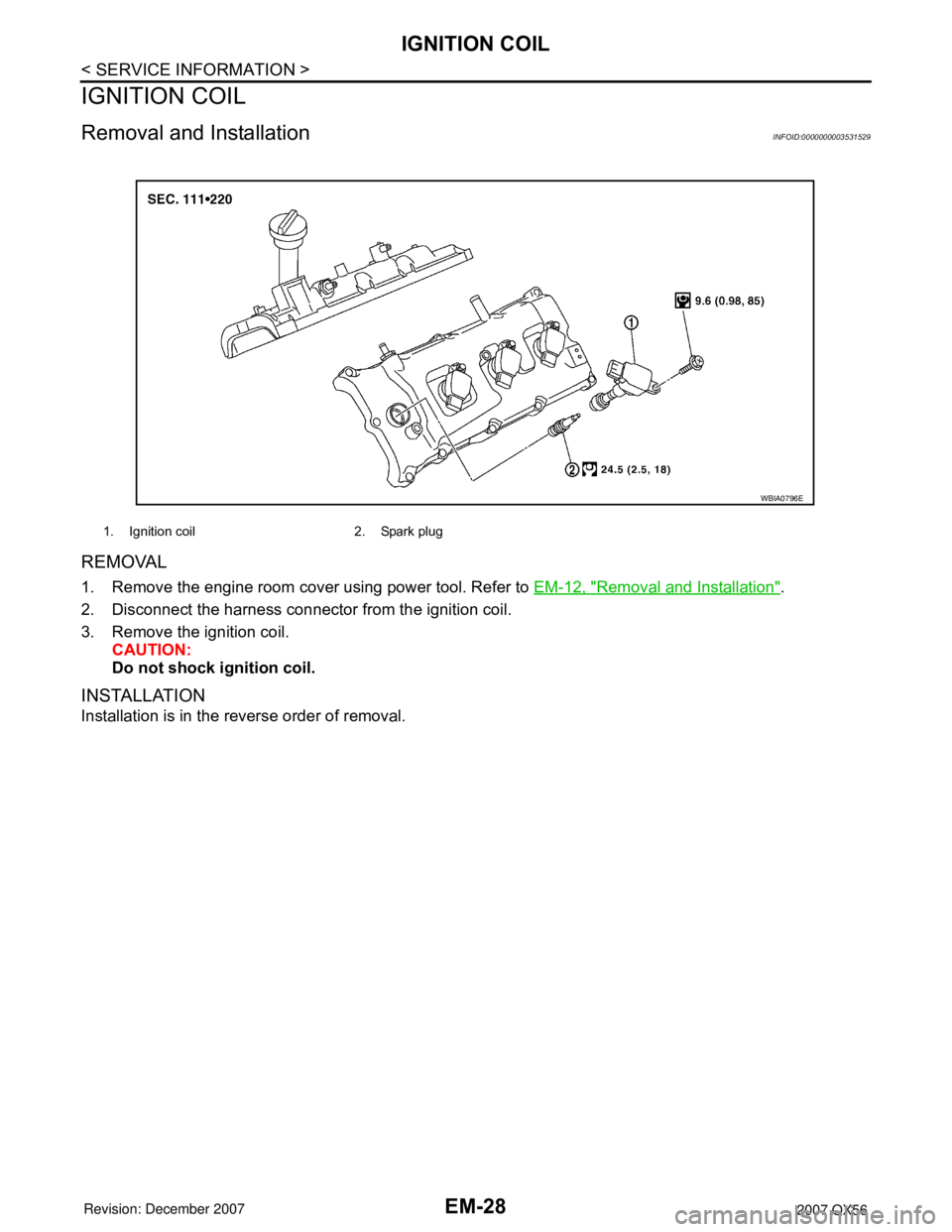
EM-28
< SERVICE INFORMATION >
IGNITION COIL
IGNITION COIL
Removal and InstallationINFOID:0000000003531529
REMOVAL
1. Remove the engine room cover using power tool. Refer to EM-12, "Removal and Installation".
2. Disconnect the harness connector from the ignition coil.
3. Remove the ignition coil. CAUTION:
Do not shock ig nition coil.
INSTALLATION
Installation is in the reverse order of removal.
1. Ignition coil 2. Spark plug
WBIA0796E
Page 1802 of 3061
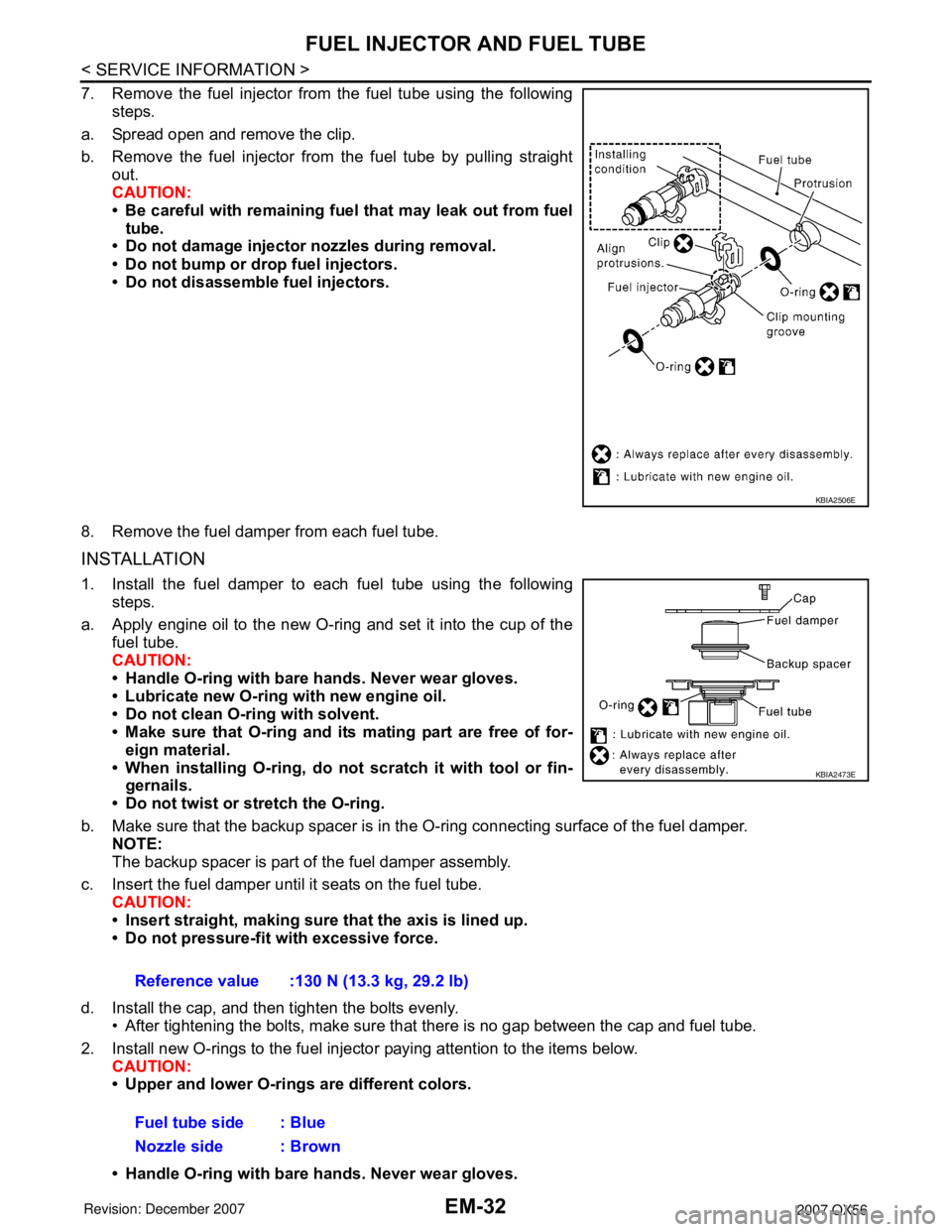
EM-32
< SERVICE INFORMATION >
FUEL INJECTOR AND FUEL TUBE
7. Remove the fuel injector from the fuel tube using the followingsteps.
a. Spread open and remove the clip.
b. Remove the fuel injector from the fuel tube by pulling straight out.
CAUTION:
• Be careful with remaining fuel that may leak out from fueltube.
• Do not damage injector nozzles during removal.
• Do not bump or drop fuel injectors.
• Do not disassemble fuel injectors.
8. Remove the fuel damper from each fuel tube.
INSTALLATION
1. Install the fuel damper to each fuel tube using the following steps.
a. Apply engine oil to the new O-ring and set it into the cup of the fuel tube.
CAUTION:
• Handle O-ring with bare hands. Never wear gloves.
• Lubricate new O-ring with new engine oil.
• Do not clean O-ring with solvent.
• Make sure that O-ring and its mating part are free of for-eign material.
• When installing O-ring, do not scratch it with tool or fin-
gernails.
• Do not twist or stretch the O-ring.
b. Make sure that the backup spacer is in the O-ring connecting surface of the fuel damper.
NOTE:
The backup spacer is part of the fuel damper assembly.
c. Insert the fuel damper until it seats on the fuel tube. CAUTION:
• Insert straight, making sure that the axis is lined up.
• Do not pressure-fit with excessive force.
d. Install the cap, and then tighten the bolts evenly. • After tightening the bolts, make sure that there is no gap between the cap and fuel tube.
2. Install new O-rings to the fuel injector paying attention to the items below. CAUTION:
• Upper and lower O-rings are different colors.
• Handle O-ring with bare hands. Never wear gloves.
KBIA2506E
Reference value :130 N (13.3 kg, 29.2 lb)
Fuel tube side : Blue
Nozzle side : Brown
KBIA2473E
Page 1803 of 3061
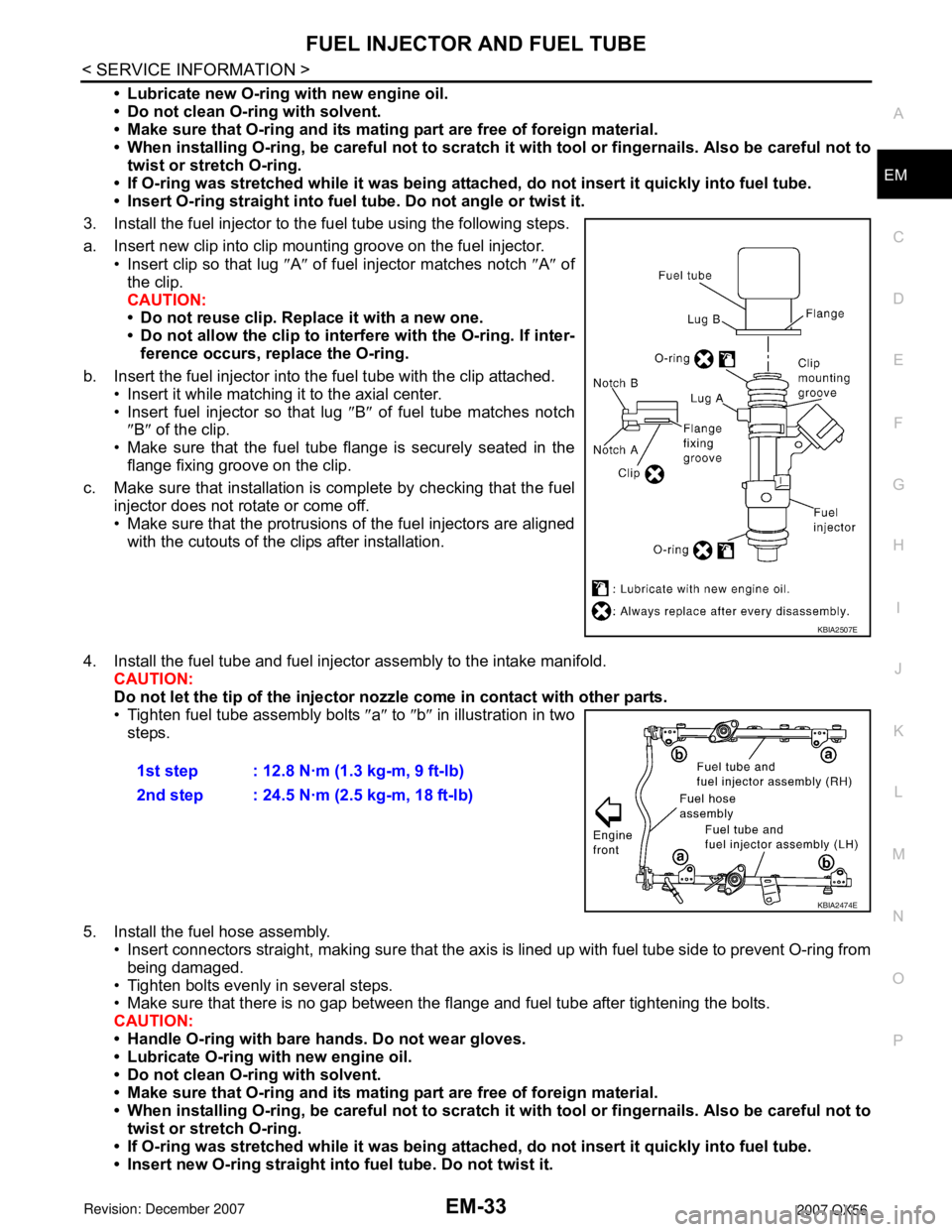
FUEL INJECTOR AND FUEL TUBEEM-33
< SERVICE INFORMATION >
C
DE
F
G H
I
J
K L
M A
EM
NP
O
• Lubricate new O-ring with new engine oil.
• Do not clean O-ring with solvent.
• Make sure that O-ring and its mating
part are free of foreign material.
• When installing O-ring, be careful not to scratch it with tool or fingernails. Also be careful not to
twist or stretch O-ring.
• If O-ring was stretched while it was being att ached, do not insert it quickly into fuel tube.
• Insert O-ring straight into fuel tube. Do not angle or twist it.
3. Install the fuel injector to the fuel tube using the following steps.
a. Insert new clip into clip mounting groove on the fuel injector. • Insert clip so that lug ″A ″ of fuel injector matches notch ″A ″ of
the clip.
CAUTION:
• Do not reuse clip. Replace it with a new one.
• Do not allow the clip to interf ere with the O-ring. If inter-
ference occurs, replace the O-ring.
b. Insert the fuel injector into the fuel tube with the clip attached. • Insert it while matching it to the axial center.
• Insert fuel injector so that lug ″B ″ of fuel tube matches notch
″ B ″ of the clip.
• Make sure that the fuel tube flange is securely seated in the flange fixing groove on the clip.
c. Make sure that installation is complete by checking that the fuel injector does not rotate or come off.
• Make sure that the protrusions of the fuel injectors are alignedwith the cutouts of the clips after installation.
4. Install the fuel tube and fuel injector assembly to the intake manifold. CAUTION:
Do not let the tip of the injector nozz le come in contact with other parts.
• Tighten fuel tube assembly bolts ″a ″ to ″b ″ in illustration in two
steps.
5. Install the fuel hose assembly. • Insert connectors straight, making su re that the axis is lined up with fuel tube side to prevent O-ring from
being damaged.
• Tighten bolts evenly in several steps.
• Make sure that there is no gap between the flange and fuel tube after tightening the bolts.
CAUTION:
• Handle O-ring with bare hands. Do not wear gloves.
• Lubricate O-ring with new engine oil.
• Do not clean O-ring with solvent.
• Make sure that O-ring and its mating part are free of foreign material.
• When installing O-ring, be careful not to scratch it with tool or fingernails. Also be careful not to
twist or stretch O-ring.
• If O-ring was stretched while it was being att ached, do not insert it quickly into fuel tube.
• Insert new O-ring straight into fuel tube. Do not twist it.
KBIA2507E
1st step : 12.8 N·m (1.3 kg-m, 9 ft-lb)
2nd step : 24.5 N·m (2.5 kg-m, 18 ft-lb)
KBIA2474E
Page 1805 of 3061
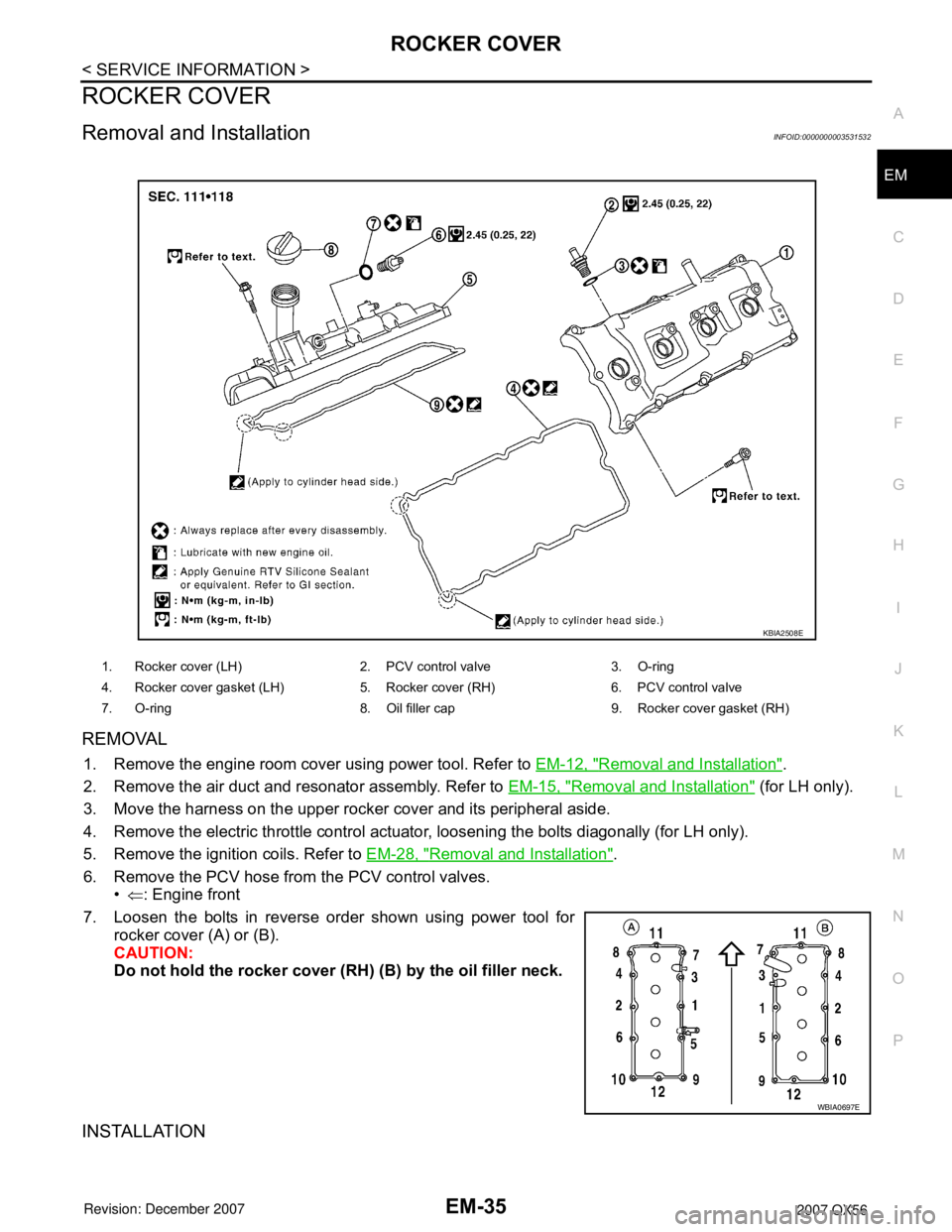
ROCKER COVEREM-35
< SERVICE INFORMATION >
C
DE
F
G H
I
J
K L
M A
EM
NP
O
ROCKER COVER
Removal and InstallationINFOID:0000000003531532
REMOVAL
1. Remove the engine room cover using power tool. Refer to
EM-12, "Removal and Installation".
2. Remove the air duct and resonator assembly. Refer to EM-15, "
Removal and Installation" (for LH only).
3. Move the harness on the upper rocker cover and its peripheral aside.
4. Remove the electric throttle control actuator, loosening the bolts diagonally (for LH only).
5. Remove the ignition coils. Refer to EM-28, "
Removal and Installation".
6. Remove the PCV hose from the PCV control valves. •⇐ : Engine front
7. Loosen the bolts in reverse order shown using power tool for rocker cover (A) or (B).
CAUTION:
Do not hold the rocker cover ( RH) (B) by the oil filler neck.
INSTALLATION
1. Rocker cover (LH) 2. PCV control valve 3. O-ring
4. Rocker cover gasket (LH) 5. Rocker cover (RH) 6. PCV control valve
7. O-ring 8. Oil filler cap 9 . Rocker cover gasket (RH)
KBIA2508E
WBIA0697E