service INFINITI QX56 2007 Factory Service Manual
[x] Cancel search | Manufacturer: INFINITI, Model Year: 2007, Model line: QX56, Model: INFINITI QX56 2007Pages: 3061, PDF Size: 64.56 MB
Page 3012 of 3061
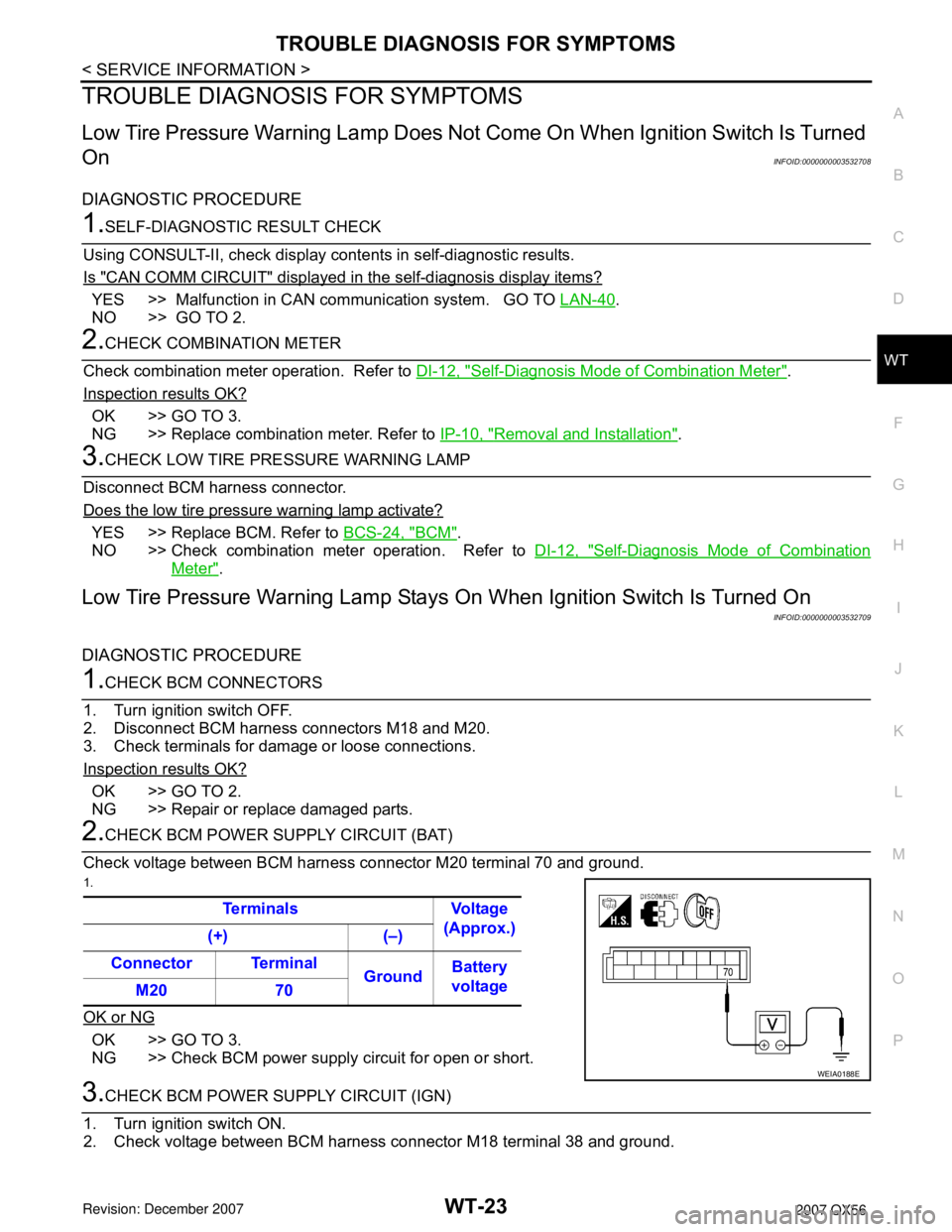
TROUBLE DIAGNOSIS FOR SYMPTOMS
WT-23
< SERVICE INFORMATION >
C
D
F
G
H
I
J
K
L
MA
B
WT
N
O
P
TROUBLE DIAGNOSIS FOR SYMPTOMS
Low Tire Pressure Warning Lamp Does Not Come On When Ignition Switch Is Turned
On
INFOID:0000000003532708
DIAGNOSTIC PROCEDURE
1.SELF-DIAGNOSTIC RESULT CHECK
Using CONSULT-II, check display contents in self-diagnostic results.
Is "CAN COMM CIRCUIT" displayed in the self-diagnosis display items?
YES >> Malfunction in CAN communication system. GO TO LAN-40.
NO >> GO TO 2.
2.CHECK COMBINATION METER
Check combination meter operation. Refer to DI-12, "
Self-Diagnosis Mode of Combination Meter".
Inspection results OK?
OK >> GO TO 3.
NG >> Replace combination meter. Refer to IP-10, "
Removal and Installation".
3.CHECK LOW TIRE PRESSURE WARNING LAMP
Disconnect BCM harness connector.
Does the low tire pressure warning lamp activate?
YES >> Replace BCM. Refer to BCS-24, "BCM".
NO >> Check combination meter operation. Refer to DI-12, "
Self-Diagnosis Mode of Combination
Meter".
Low Tire Pressure Warning Lamp Stays On When Ignition Switch Is Turned On
INFOID:0000000003532709
DIAGNOSTIC PROCEDURE
1.CHECK BCM CONNECTORS
1. Turn ignition switch OFF.
2. Disconnect BCM harness connectors M18 and M20.
3. Check terminals for damage or loose connections.
Inspection results OK?
OK >> GO TO 2.
NG >> Repair or replace damaged parts.
2.CHECK BCM POWER SUPPLY CIRCUIT (BAT)
Check voltage between BCM harness connector M20 terminal 70 and ground.
1.
OK or NG
OK >> GO TO 3.
NG >> Check BCM power supply circuit for open or short.
3.CHECK BCM POWER SUPPLY CIRCUIT (IGN)
1. Turn ignition switch ON.
2. Check voltage between BCM harness connector M18 terminal 38 and ground.Terminals Voltage
(Approx.)
(+) (–)
Connector Terminal
GroundBattery
voltage
M20 70
WEIA0188E
Page 3013 of 3061
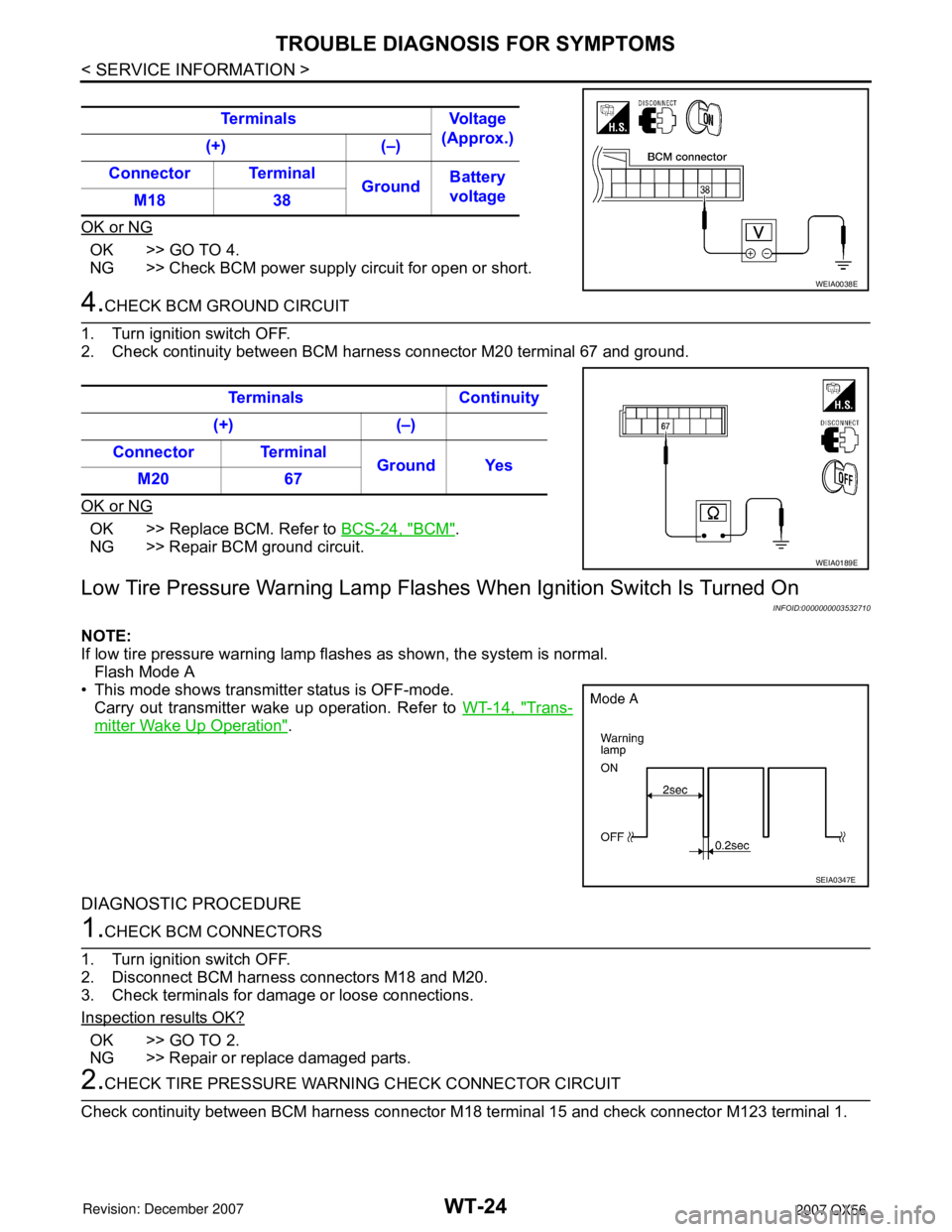
WT-24
< SERVICE INFORMATION >
TROUBLE DIAGNOSIS FOR SYMPTOMS
OK or NG
OK >> GO TO 4.
NG >> Check BCM power supply circuit for open or short.
4.CHECK BCM GROUND CIRCUIT
1. Turn ignition switch OFF.
2. Check continuity between BCM harness connector M20 terminal 67 and ground.
OK or NG
OK >> Replace BCM. Refer to BCS-24, "BCM".
NG >> Repair BCM ground circuit.
Low Tire Pressure Warning Lamp Flashes When Ignition Switch Is Turned On
INFOID:0000000003532710
NOTE:
If low tire pressure warning lamp flashes as shown, the system is normal.
Flash Mode A
• This mode shows transmitter status is OFF-mode.
Carry out transmitter wake up operation. Refer to WT-14, "
Trans-
mitter Wake Up Operation".
DIAGNOSTIC PROCEDURE
1.CHECK BCM CONNECTORS
1. Turn ignition switch OFF.
2. Disconnect BCM harness connectors M18 and M20.
3. Check terminals for damage or loose connections.
Inspection results OK?
OK >> GO TO 2.
NG >> Repair or replace damaged parts.
2.CHECK TIRE PRESSURE WARNING CHECK CONNECTOR CIRCUIT
Check continuity between BCM harness connector M18 terminal 15 and check connector M123 terminal 1. Terminals Voltage
(Approx.)
(+) (–)
Connector Terminal
GroundBattery
voltage
M18 38
WEIA0038E
Terminals Continuity
(+) (–)
Connector Terminal
Ground Yes
M20 67
WEIA0189E
SEIA0347E
Page 3014 of 3061
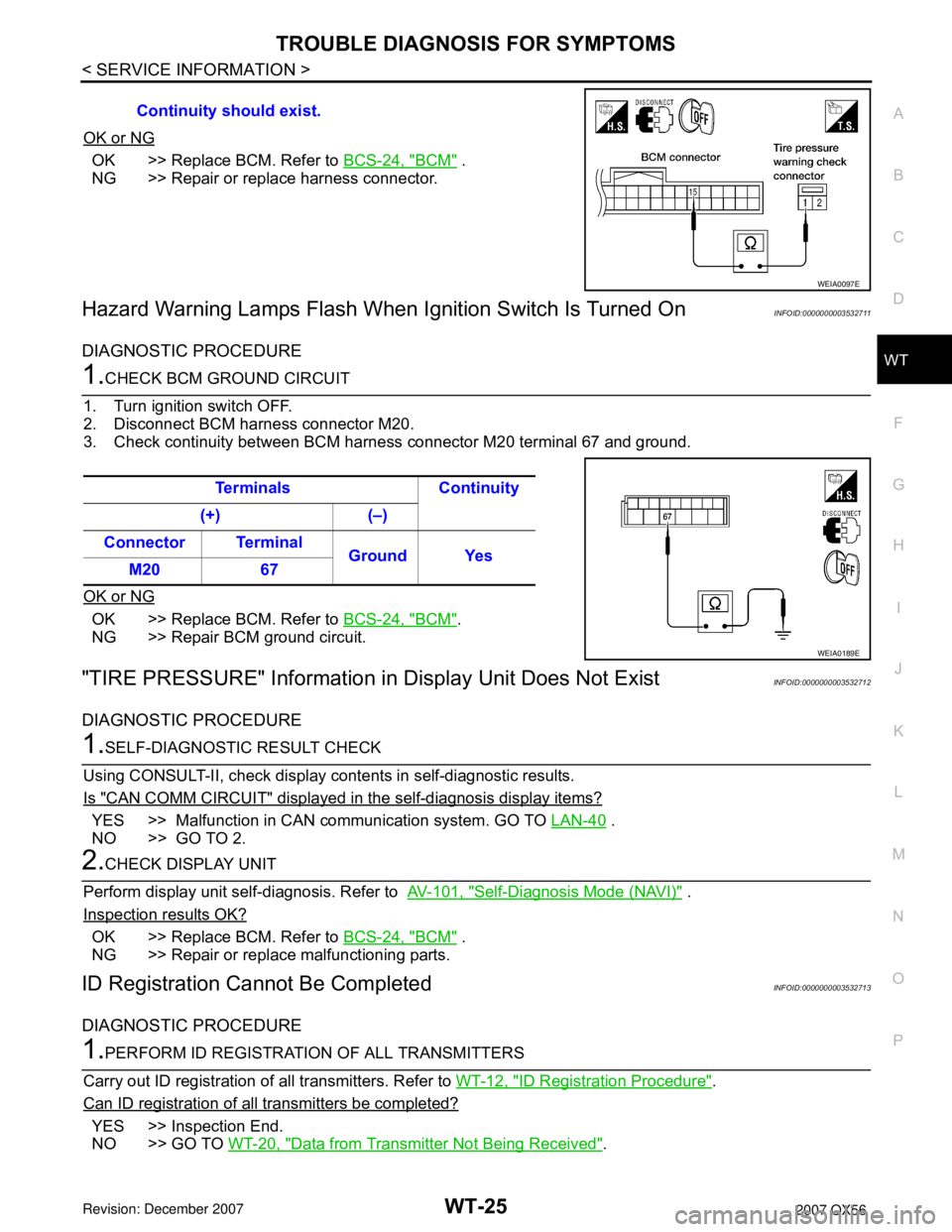
TROUBLE DIAGNOSIS FOR SYMPTOMS
WT-25
< SERVICE INFORMATION >
C
D
F
G
H
I
J
K
L
MA
B
WT
N
O
P
OK or NG
OK >> Replace BCM. Refer to BCS-24, "BCM" .
NG >> Repair or replace harness connector.
Hazard Warning Lamps Flash When Ignition Switch Is Turned OnINFOID:0000000003532711
DIAGNOSTIC PROCEDURE
1.CHECK BCM GROUND CIRCUIT
1. Turn ignition switch OFF.
2. Disconnect BCM harness connector M20.
3. Check continuity between BCM harness connector M20 terminal 67 and ground.
OK or NG
OK >> Replace BCM. Refer to BCS-24, "BCM".
NG >> Repair BCM ground circuit.
"TIRE PRESSURE" Information in Display Unit Does Not ExistINFOID:0000000003532712
DIAGNOSTIC PROCEDURE
1.SELF-DIAGNOSTIC RESULT CHECK
Using CONSULT-II, check display contents in self-diagnostic results.
Is "CAN COMM CIRCUIT" displayed in the self-diagnosis display items?
YES >> Malfunction in CAN communication system. GO TO LAN-40 .
NO >> GO TO 2.
2.CHECK DISPLAY UNIT
Perform display unit self-diagnosis. Refer to AV-101, "
Self-Diagnosis Mode (NAVI)" .
Inspection results OK?
OK >> Replace BCM. Refer to BCS-24, "BCM" .
NG >> Repair or replace malfunctioning parts.
ID Registration Cannot Be CompletedINFOID:0000000003532713
DIAGNOSTIC PROCEDURE
1.PERFORM ID REGISTRATION OF ALL TRANSMITTERS
Carry out ID registration of all transmitters. Refer to WT-12, "
ID Registration Procedure".
Can ID registration of all transmitters be completed?
YES >> Inspection End.
NO >> GO TO WT-20, "
Data from Transmitter Not Being Received". Continuity should exist.
WEIA0097E
Terminals Continuity
(+) (–)
Connector Terminal
Ground Yes
M20 67
WEIA0189E
Page 3015 of 3061
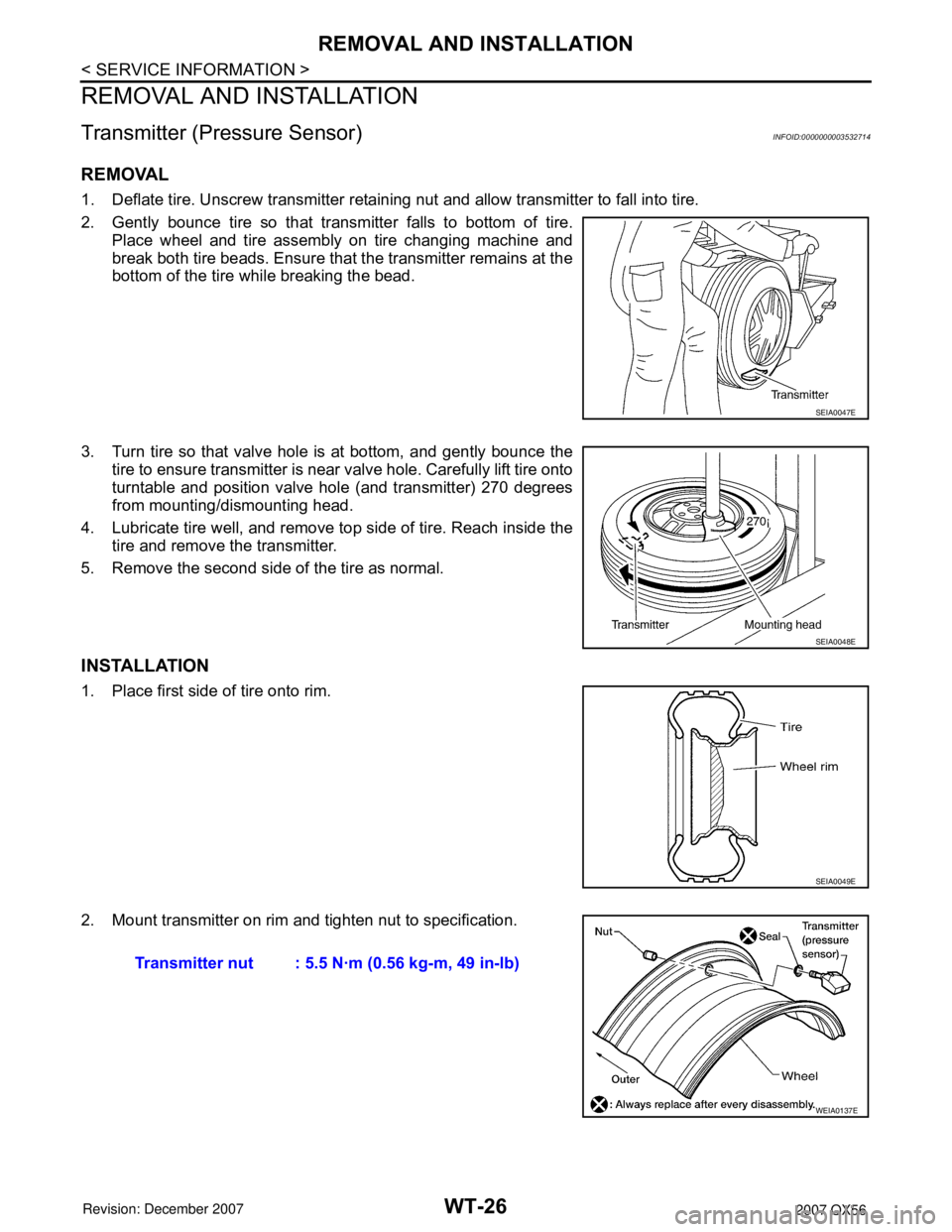
WT-26
< SERVICE INFORMATION >
REMOVAL AND INSTALLATION
REMOVAL AND INSTALLATION
Transmitter (Pressure Sensor)INFOID:0000000003532714
REMOVAL
1. Deflate tire. Unscrew transmitter retaining nut and allow transmitter to fall into tire.
2. Gently bounce tire so that transmitter falls to bottom of tire.
Place wheel and tire assembly on tire changing machine and
break both tire beads. Ensure that the transmitter remains at the
bottom of the tire while breaking the bead.
3. Turn tire so that valve hole is at bottom, and gently bounce the
tire to ensure transmitter is near valve hole. Carefully lift tire onto
turntable and position valve hole (and transmitter) 270 degrees
from mounting/dismounting head.
4. Lubricate tire well, and remove top side of tire. Reach inside the
tire and remove the transmitter.
5. Remove the second side of the tire as normal.
INSTALLATION
1. Place first side of tire onto rim.
2. Mount transmitter on rim and tighten nut to specification.
SEIA0047E
SEIA0048E
SEIA0049E
Transmitter nut : 5.5 N·m (0.56 kg-m, 49 in-lb)
WEIA0137E
Page 3016 of 3061
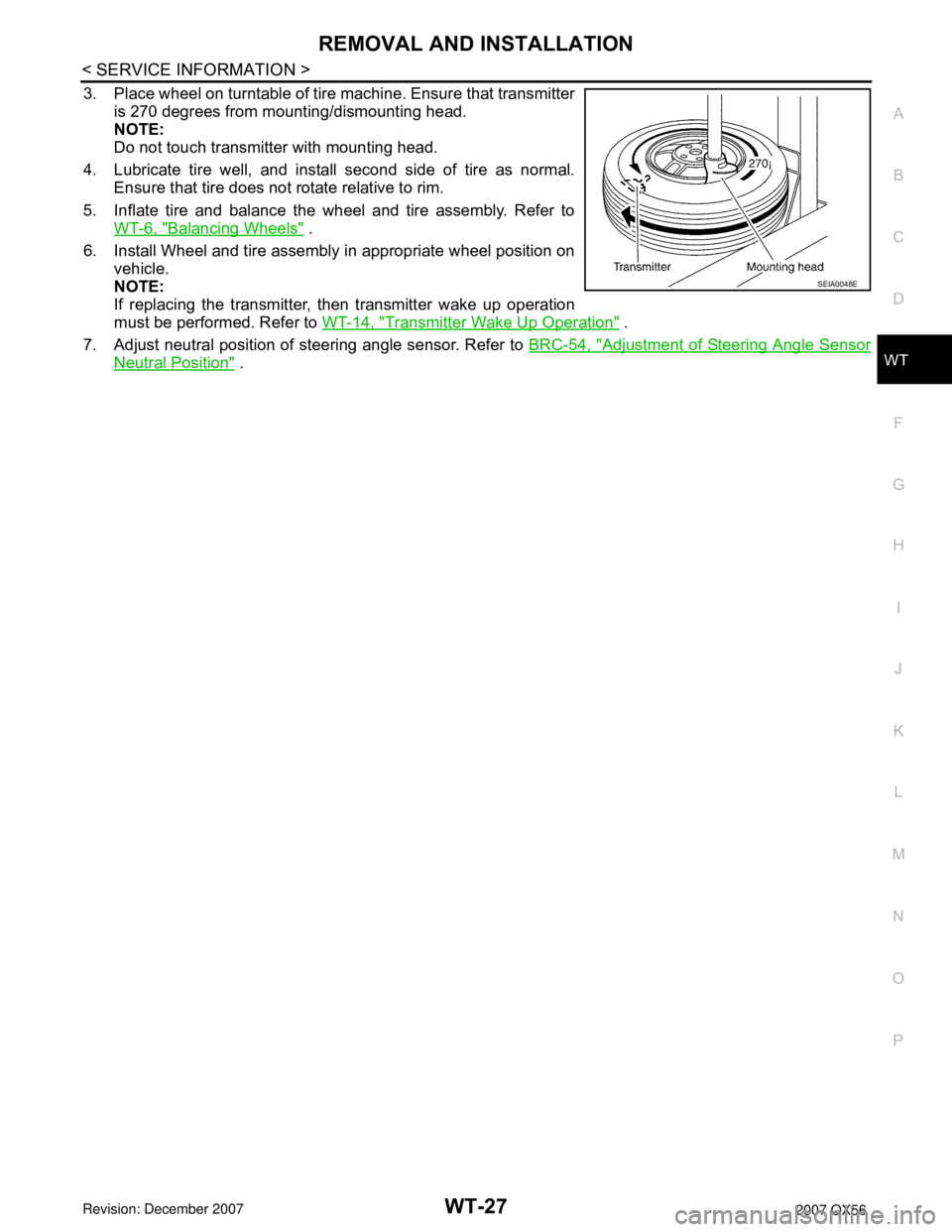
REMOVAL AND INSTALLATION
WT-27
< SERVICE INFORMATION >
C
D
F
G
H
I
J
K
L
MA
B
WT
N
O
P
3. Place wheel on turntable of tire machine. Ensure that transmitter
is 270 degrees from mounting/dismounting head.
NOTE:
Do not touch transmitter with mounting head.
4. Lubricate tire well, and install second side of tire as normal.
Ensure that tire does not rotate relative to rim.
5. Inflate tire and balance the wheel and tire assembly. Refer to
WT-6, "
Balancing Wheels" .
6. Install Wheel and tire assembly in appropriate wheel position on
vehicle.
NOTE:
If replacing the transmitter, then transmitter wake up operation
must be performed. Refer to WT-14, "
Transmitter Wake Up Operation" .
7. Adjust neutral position of steering angle sensor. Refer to BRC-54, "
Adjustment of Steering Angle Sensor
Neutral Position" .
SEIA0048E
Page 3017 of 3061
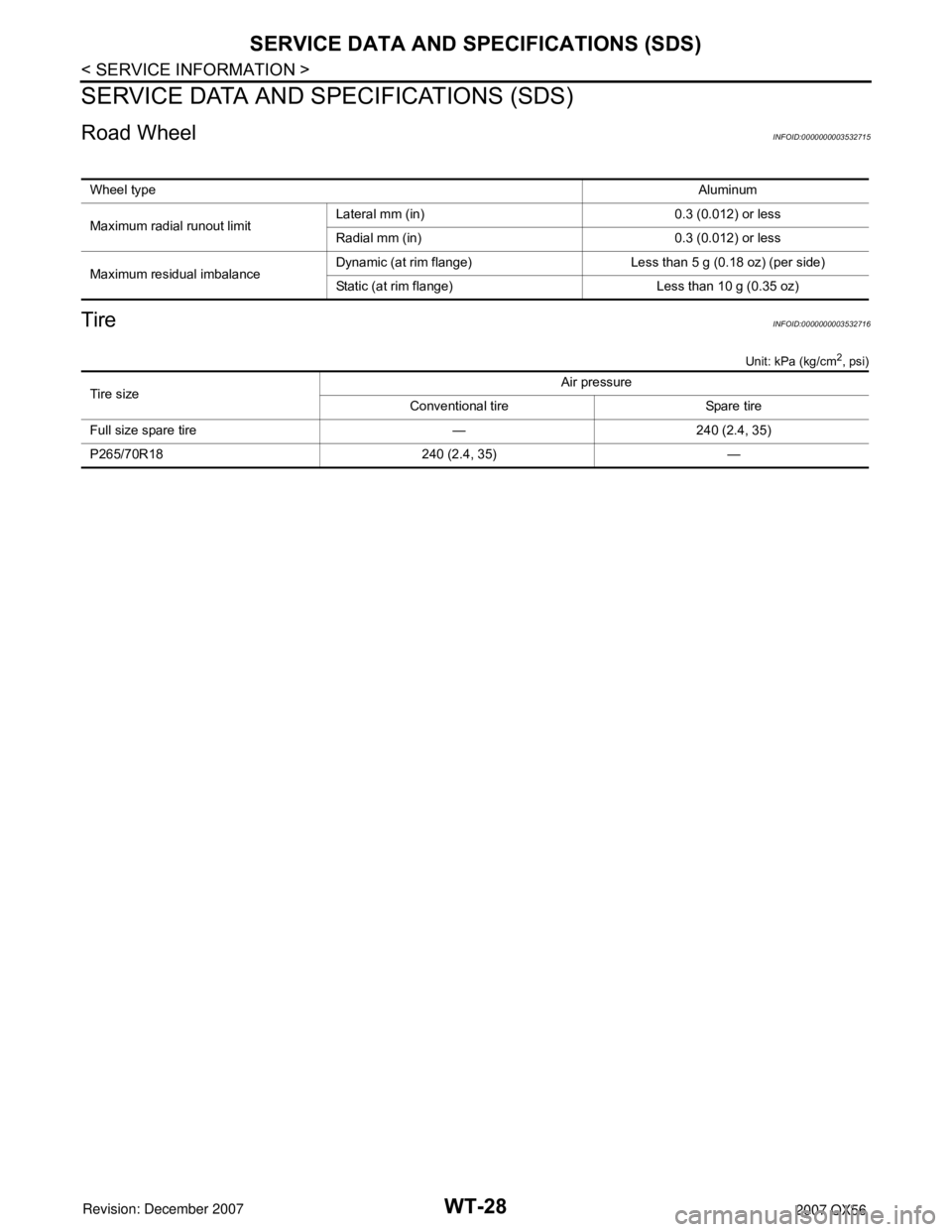
WT-28
< SERVICE INFORMATION >
SERVICE DATA AND SPECIFICATIONS (SDS)
SERVICE DATA AND SPECIFICATIONS (SDS)
Road WheelINFOID:0000000003532715
TireINFOID:0000000003532716
Unit: kPa (kg/cm2, psi)
Wheel typeAluminum
Maximum radial runout limitLateral mm (in) 0.3 (0.012) or less
Radial mm (in) 0.3 (0.012) or less
Maximum residual imbalanceDynamic (at rim flange) Less than 5 g (0.18 oz) (per side)
Static (at rim flange) Less than 10 g (0.35 oz)
Tire sizeAir pressure
Conventional tire Spare tire
Full size spare tire — 240 (2.4, 35)
P265/70R18 240 (2.4, 35) —
Page 3018 of 3061
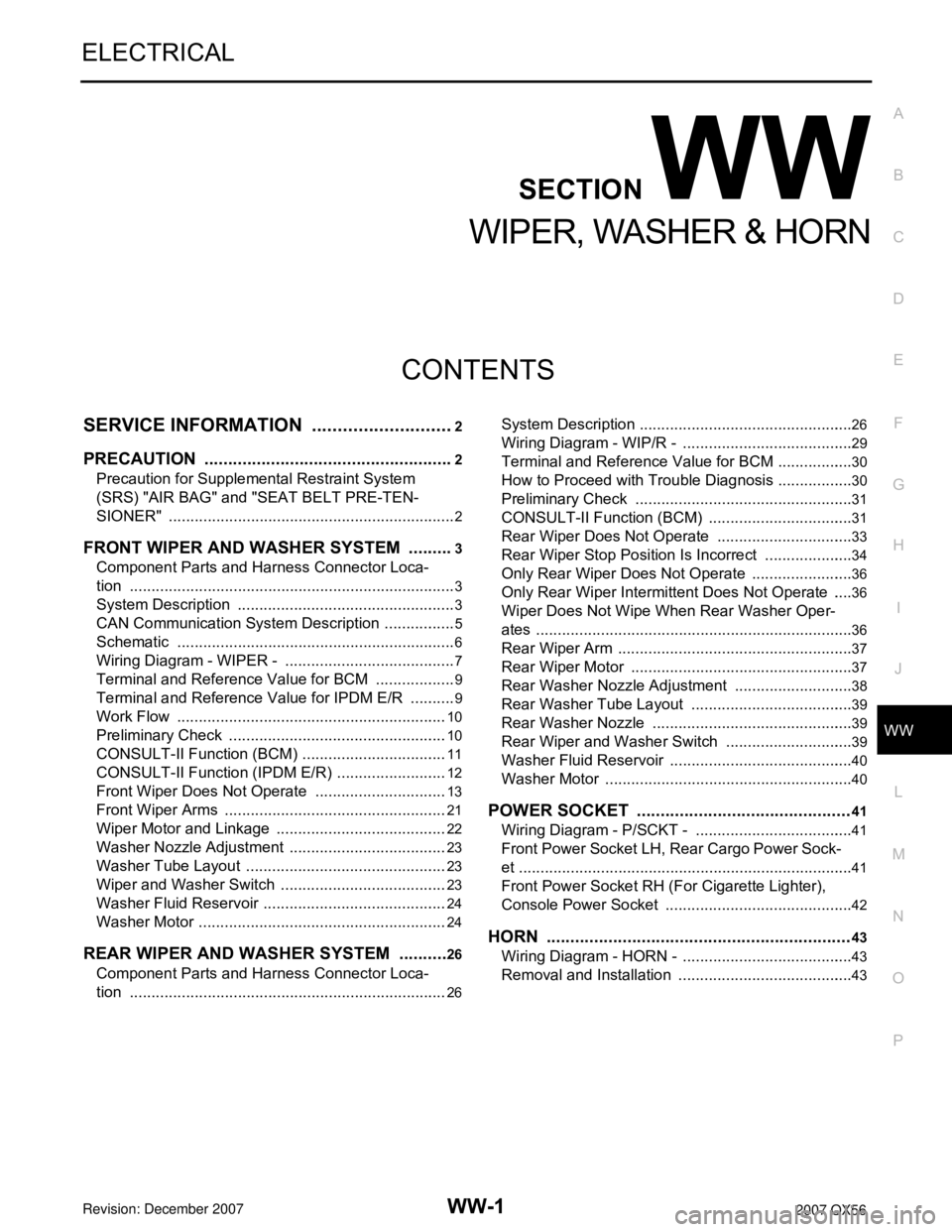
WW-1
ELECTRICAL
C
D
E
F
G
H
I
J
L
M
SECTION WW
A
B
WW
N
O
P
CONTENTS
WIPER, WASHER & HORN
SERVICE INFORMATION ............................2
PRECAUTION .....................................................2
Precaution for Supplemental Restraint System
(SRS) "AIR BAG" and "SEAT BELT PRE-TEN-
SIONER" ...................................................................
2
FRONT WIPER AND WASHER SYSTEM ..........3
Component Parts and Harness Connector Loca-
tion ............................................................................
3
System Description ...................................................3
CAN Communication System Description .................5
Schematic .................................................................6
Wiring Diagram - WIPER - ........................................7
Terminal and Reference Value for BCM ...................9
Terminal and Reference Value for IPDM E/R ...........9
Work Flow ...............................................................10
Preliminary Check ...................................................10
CONSULT-II Function (BCM) ..................................11
CONSULT-II Function (IPDM E/R) ..........................12
Front Wiper Does Not Operate ...............................13
Front Wiper Arms ....................................................21
Wiper Motor and Linkage ........................................22
Washer Nozzle Adjustment .....................................23
Washer Tube Layout ...............................................23
Wiper and Washer Switch .......................................23
Washer Fluid Reservoir ...........................................24
Washer Motor ..........................................................24
REAR WIPER AND WASHER SYSTEM ...........26
Component Parts and Harness Connector Loca-
tion ..........................................................................
26
System Description ..................................................26
Wiring Diagram - WIP/R - ........................................29
Terminal and Reference Value for BCM ..................30
How to Proceed with Trouble Diagnosis ..................30
Preliminary Check ...................................................31
CONSULT-II Function (BCM) ..................................31
Rear Wiper Does Not Operate ................................33
Rear Wiper Stop Position Is Incorrect .....................34
Only Rear Wiper Does Not Operate ........................36
Only Rear Wiper Intermittent Does Not Operate .....36
Wiper Does Not Wipe When Rear Washer Oper-
ates ..........................................................................
36
Rear Wiper Arm .......................................................37
Rear Wiper Motor ....................................................37
Rear Washer Nozzle Adjustment ............................38
Rear Washer Tube Layout ......................................39
Rear Washer Nozzle ...............................................39
Rear Wiper and Washer Switch ..............................39
Washer Fluid Reservoir ...........................................40
Washer Motor ..........................................................40
POWER SOCKET .............................................41
Wiring Diagram - P/SCKT - .....................................41
Front Power Socket LH, Rear Cargo Power Sock-
et ..............................................................................
41
Front Power Socket RH (For Cigarette Lighter),
Console Power Socket ............................................
42
HORN ................................................................43
Wiring Diagram - HORN - ........................................43
Removal and Installation .........................................43
Page 3019 of 3061
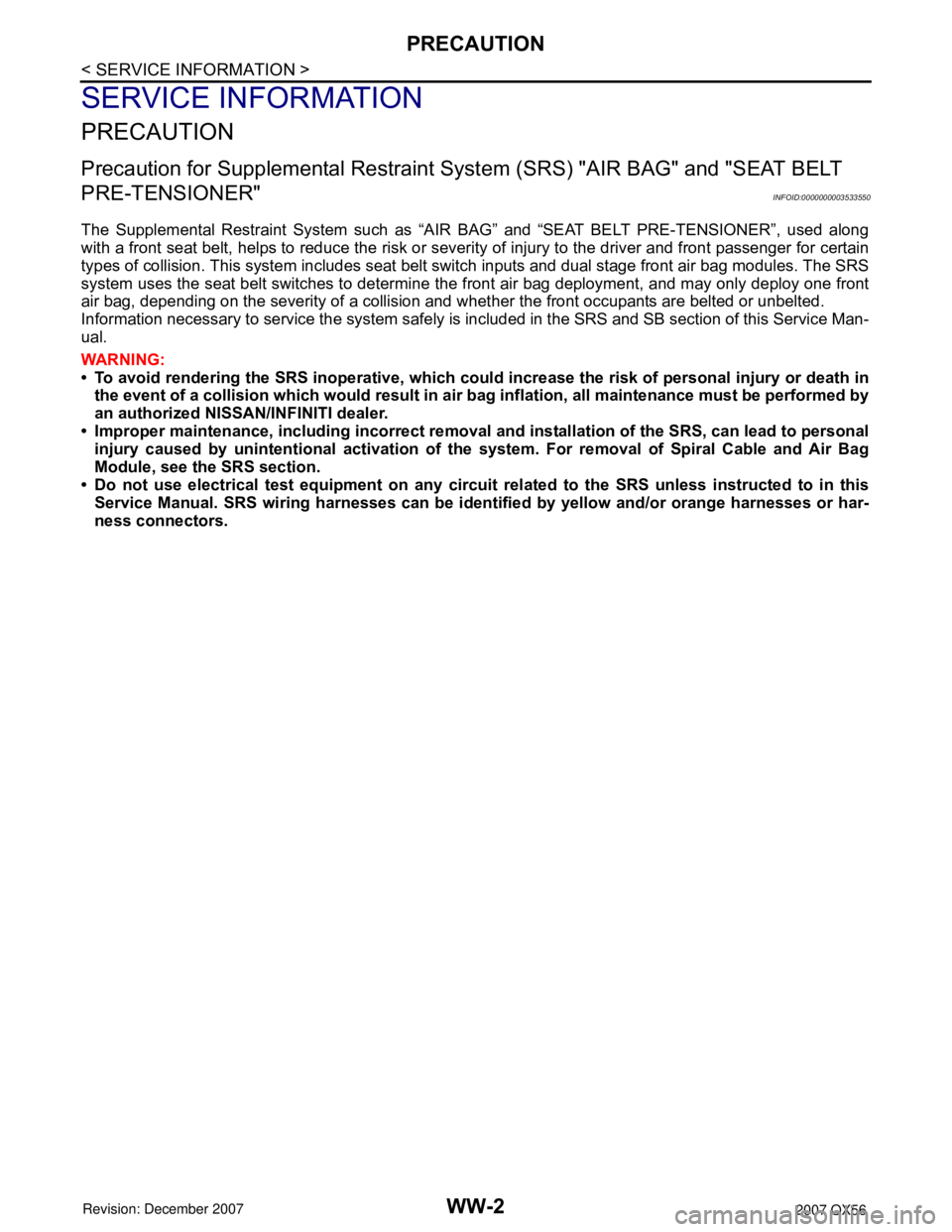
WW-2
< SERVICE INFORMATION >
PRECAUTION
SERVICE INFORMATION
PRECAUTION
Precaution for Supplemental Restraint System (SRS) "AIR BAG" and "SEAT BELT
PRE-TENSIONER"
INFOID:0000000003533550
The Supplemental Restraint System such as “AIR BAG” and “SEAT BELT PRE-TENSIONER”, used along
with a front seat belt, helps to reduce the risk or severity of injury to the driver and front passenger for certain
types of collision. This system includes seat belt switch inputs and dual stage front air bag modules. The SRS
system uses the seat belt switches to determine the front air bag deployment, and may only deploy one front
air bag, depending on the severity of a collision and whether the front occupants are belted or unbelted.
Information necessary to service the system safely is included in the SRS and SB section of this Service Man-
ual.
WARNING:
• To avoid rendering the SRS inoperative, which could increase the risk of personal injury or death in
the event of a collision which would result in air bag inflation, all maintenance must be performed by
an authorized NISSAN/INFINITI dealer.
• Improper maintenance, including incorrect removal and installation of the SRS, can lead to personal
injury caused by unintentional activation of the system. For removal of Spiral Cable and Air Bag
Module, see the SRS section.
• Do not use electrical test equipment on any circuit related to the SRS unless instructed to in this
Service Manual. SRS wiring harnesses can be identified by yellow and/or orange harnesses or har-
ness connectors.
Page 3020 of 3061
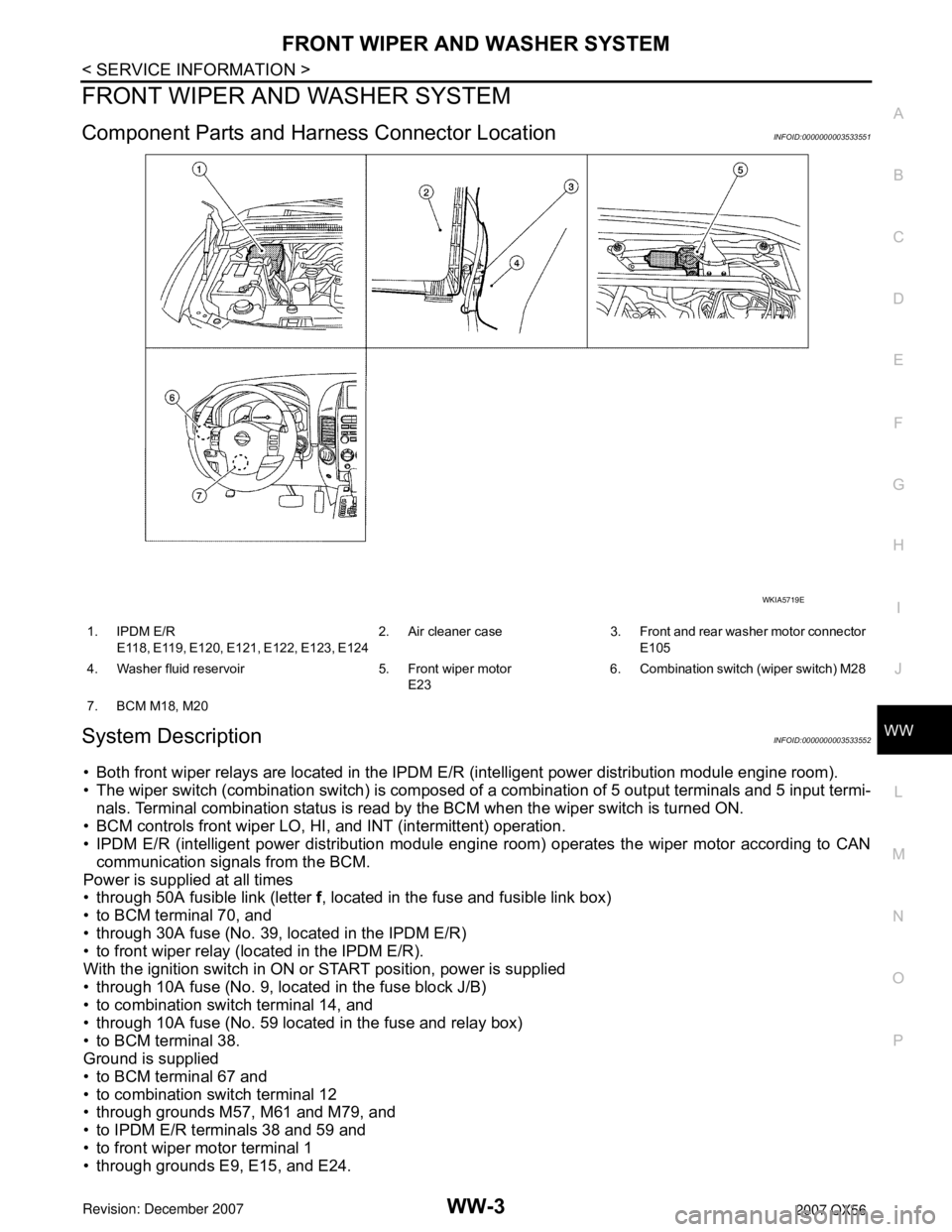
FRONT WIPER AND WASHER SYSTEM
WW-3
< SERVICE INFORMATION >
C
D
E
F
G
H
I
J
L
MA
B
WW
N
O
P
FRONT WIPER AND WASHER SYSTEM
Component Parts and Harness Connector LocationINFOID:0000000003533551
System DescriptionINFOID:0000000003533552
• Both front wiper relays are located in the IPDM E/R (intelligent power distribution module engine room).
• The wiper switch (combination switch) is composed of a combination of 5 output terminals and 5 input termi-
nals. Terminal combination status is read by the BCM when the wiper switch is turned ON.
• BCM controls front wiper LO, HI, and INT (intermittent) operation.
• IPDM E/R (intelligent power distribution module engine room) operates the wiper motor according to CAN
communication signals from the BCM.
Power is supplied at all times
• through 50A fusible link (letter f, located in the fuse and fusible link box)
• to BCM terminal 70, and
• through 30A fuse (No. 39, located in the IPDM E/R)
• to front wiper relay (located in the IPDM E/R).
With the ignition switch in ON or START position, power is supplied
• through 10A fuse (No. 9, located in the fuse block J/B)
• to combination switch terminal 14, and
• through 10A fuse (No. 59 located in the fuse and relay box)
• to BCM terminal 38.
Ground is supplied
• to BCM terminal 67 and
• to combination switch terminal 12
• through grounds M57, M61 and M79, and
• to IPDM E/R terminals 38 and 59 and
• to front wiper motor terminal 1
• through grounds E9, E15, and E24.
WKIA5719E
1. IPDM E/R
E118, E119, E120, E121, E122, E123, E1242. Air cleaner case 3. Front and rear washer motor connector
E105
4. Washer fluid reservoir 5. Front wiper motor
E236. Combination switch (wiper switch) M28
7. BCM M18, M20
Page 3021 of 3061
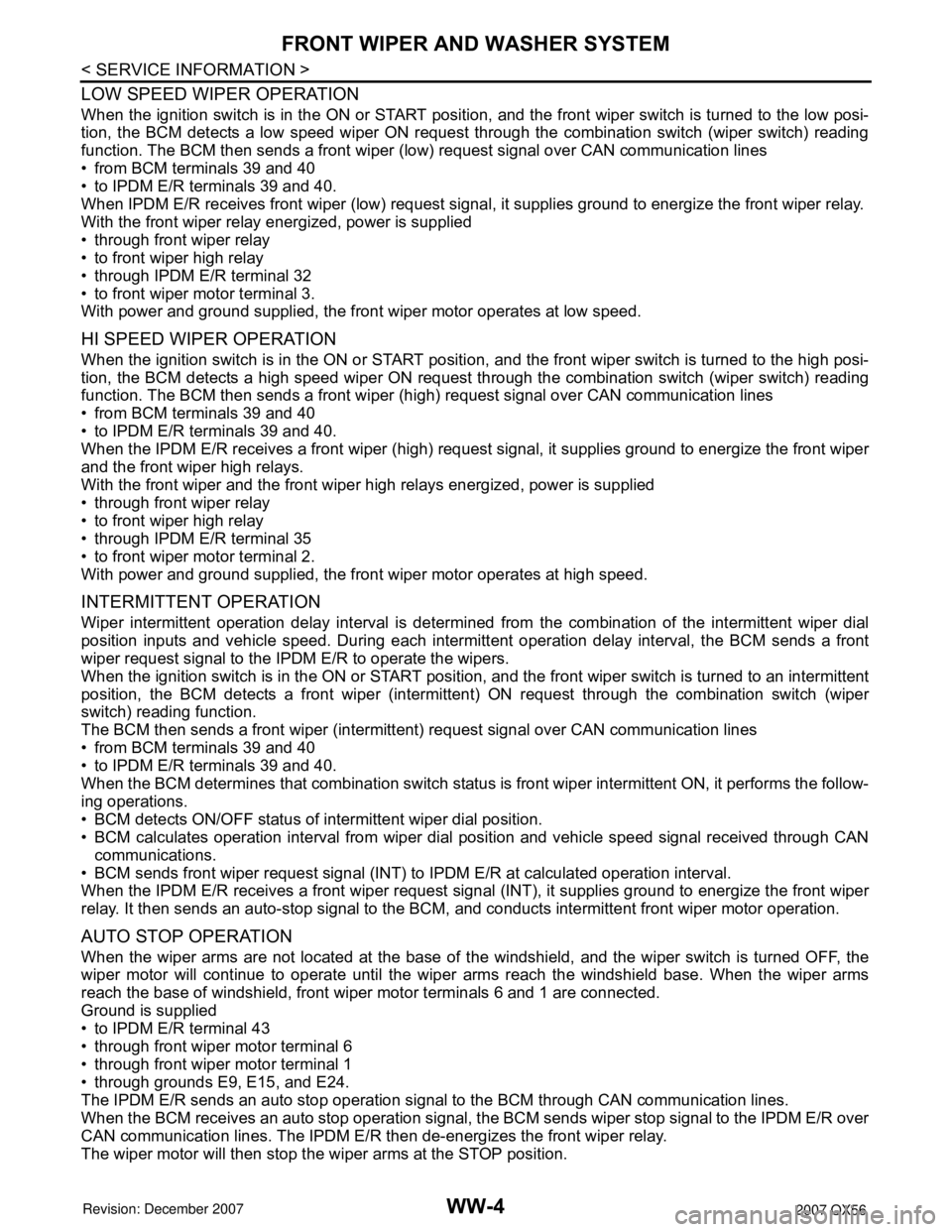
WW-4
< SERVICE INFORMATION >
FRONT WIPER AND WASHER SYSTEM
LOW SPEED WIPER OPERATION
When the ignition switch is in the ON or START position, and the front wiper switch is turned to the low posi-
tion, the BCM detects a low speed wiper ON request through the combination switch (wiper switch) reading
function. The BCM then sends a front wiper (low) request signal over CAN communication lines
• from BCM terminals 39 and 40
• to IPDM E/R terminals 39 and 40.
When IPDM E/R receives front wiper (low) request signal, it supplies ground to energize the front wiper relay.
With the front wiper relay energized, power is supplied
• through front wiper relay
• to front wiper high relay
• through IPDM E/R terminal 32
• to front wiper motor terminal 3.
With power and ground supplied, the front wiper motor operates at low speed.
HI SPEED WIPER OPERATION
When the ignition switch is in the ON or START position, and the front wiper switch is turned to the high posi-
tion, the BCM detects a high speed wiper ON request through the combination switch (wiper switch) reading
function. The BCM then sends a front wiper (high) request signal over CAN communication lines
• from BCM terminals 39 and 40
• to IPDM E/R terminals 39 and 40.
When the IPDM E/R receives a front wiper (high) request signal, it supplies ground to energize the front wiper
and the front wiper high relays.
With the front wiper and the front wiper high relays energized, power is supplied
• through front wiper relay
• to front wiper high relay
• through IPDM E/R terminal 35
• to front wiper motor terminal 2.
With power and ground supplied, the front wiper motor operates at high speed.
INTERMITTENT OPERATION
Wiper intermittent operation delay interval is determined from the combination of the intermittent wiper dial
position inputs and vehicle speed. During each intermittent operation delay interval, the BCM sends a front
wiper request signal to the IPDM E/R to operate the wipers.
When the ignition switch is in the ON or START position, and the front wiper switch is turned to an intermittent
position, the BCM detects a front wiper (intermittent) ON request through the combination switch (wiper
switch) reading function.
The BCM then sends a front wiper (intermittent) request signal over CAN communication lines
• from BCM terminals 39 and 40
• to IPDM E/R terminals 39 and 40.
When the BCM determines that combination switch status is front wiper intermittent ON, it performs the follow-
ing operations.
• BCM detects ON/OFF status of intermittent wiper dial position.
• BCM calculates operation interval from wiper dial position and vehicle speed signal received through CAN
communications.
• BCM sends front wiper request signal (INT) to IPDM E/R at calculated operation interval.
When the IPDM E/R receives a front wiper request signal (INT), it supplies ground to energize the front wiper
relay. It then sends an auto-stop signal to the BCM, and conducts intermittent front wiper motor operation.
AUTO STOP OPERATION
When the wiper arms are not located at the base of the windshield, and the wiper switch is turned OFF, the
wiper motor will continue to operate until the wiper arms reach the windshield base. When the wiper arms
reach the base of windshield, front wiper motor terminals 6 and 1 are connected.
Ground is supplied
• to IPDM E/R terminal 43
• through front wiper motor terminal 6
• through front wiper motor terminal 1
• through grounds E9, E15, and E24.
The IPDM E/R sends an auto stop operation signal to the BCM through CAN communication lines.
When the BCM receives an auto stop operation signal, the BCM sends wiper stop signal to the IPDM E/R over
CAN communication lines. The IPDM E/R then de-energizes the front wiper relay.
The wiper motor will then stop the wiper arms at the STOP position.