check oil INFINITI QX56 2008 Factory User Guide
[x] Cancel search | Manufacturer: INFINITI, Model Year: 2008, Model line: QX56, Model: INFINITI QX56 2008Pages: 4083, PDF Size: 81.73 MB
Page 645 of 4083
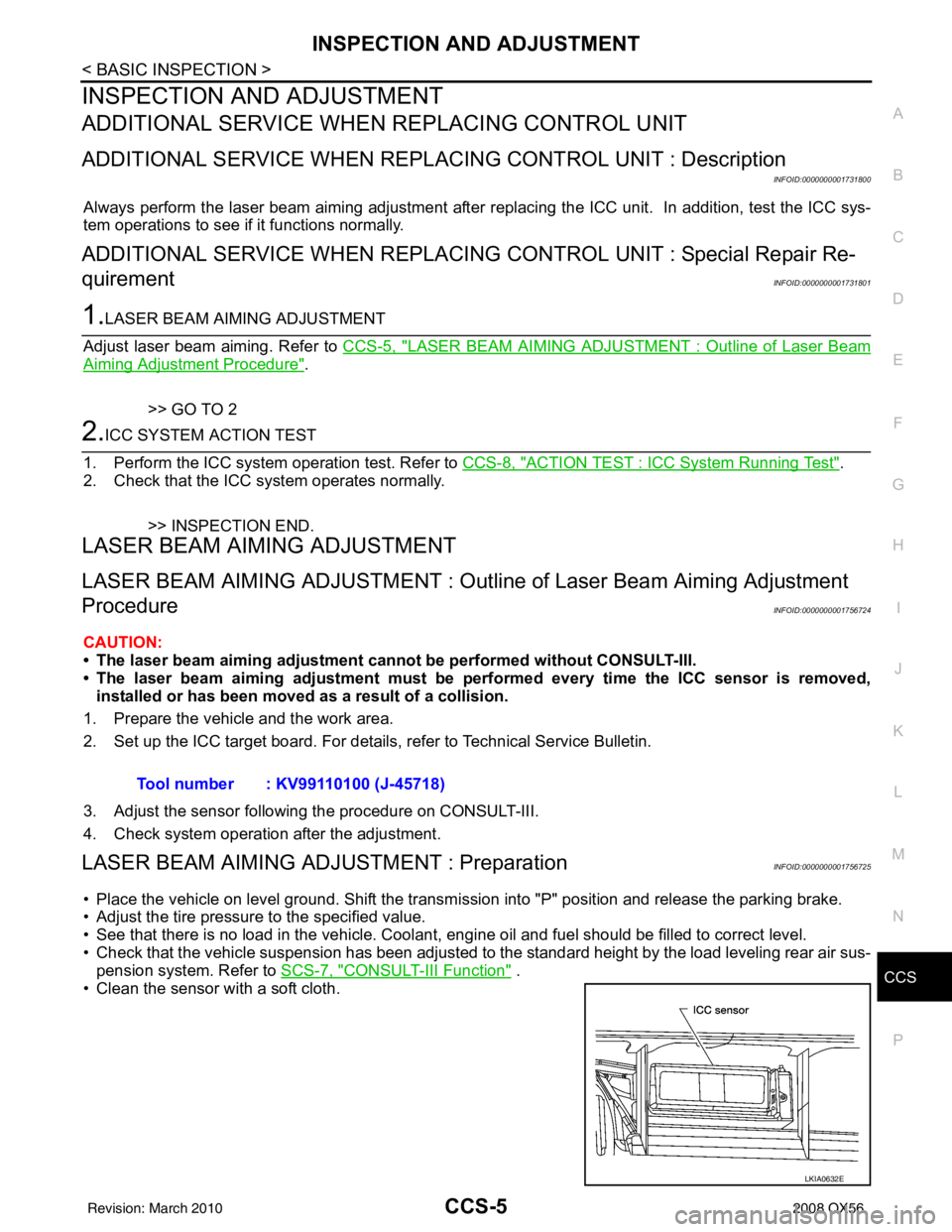
CCS
INSPECTION AND ADJUSTMENTCCS-5
< BASIC INSPECTION >
C
DE
F
G H
I
J
K L
M B
N P A
INSPECTION AND ADJUSTMENT
ADDITIONAL SERVICE WHEN REPLACING CONTROL UNIT
ADDITIONAL SERVICE WHEN REPL ACING CONTROL UNIT : Description
INFOID:0000000001731800
Always perform the laser beam aiming adjustment after repl acing the ICC unit. In addition, test the ICC sys-
tem operations to see if it functions normally.
ADDITIONAL SERVICE WHEN REPLACING CONTROL UNIT : Special Repair Re-
quirement
INFOID:0000000001731801
1.LASER BEAM AIMING ADJUSTMENT
Adjust laser beam aiming. Refer to CCS-5, "
LASER BEAM AIMING ADJUSTMENT : Outline of Laser Beam
Aiming Adjustment Procedure".
>> GO TO 2
2.ICC SYSTEM ACTION TEST
1. Perform the ICC system operation test. Refer to CCS-8, "
ACTION TEST : ICC System Running Test".
2. Check that the ICC system operates normally.
>> INSPECTION END.
LASER BEAM AIMI NG ADJUSTMENT
LASER BEAM AIMING ADJUSTMENT : Outlin e of Laser Beam Aiming Adjustment
Procedure
INFOID:0000000001756724
CAUTION:
• The laser beam aiming adjustment can not be performed without CONSULT-III.
• The laser beam aiming adjustment must be performed every time the ICC sensor is removed,
installed or has been moved as a result of a collision.
1. Prepare the vehicle and the work area.
2. Set up the ICC target board. For details, refer to Technical Service Bulletin.
3. Adjust the sensor following the procedure on CONSULT-III.
4. Check system operation after the adjustment.
LASER BEAM AIMING ADJU STMENT : PreparationINFOID:0000000001756725
• Place the vehicle on level ground. Shift the transmi ssion into "P" position and release the parking brake.
• Adjust the tire pressure to the specified value.
• See that there is no load in the vehicle. Coolant , engine oil and fuel should be filled to correct level.
• Check that the vehicle suspension has been adjusted to the standard height by the load leveling rear air sus-
pension system. Refer to SCS-7, "
CONSULT-III Function" .
• Clean the sensor with a soft cloth. Tool number : KV99110100 (J-45718)
LKIA0632E
Revision: March 2010
2008 QX56
Page 674 of 4083
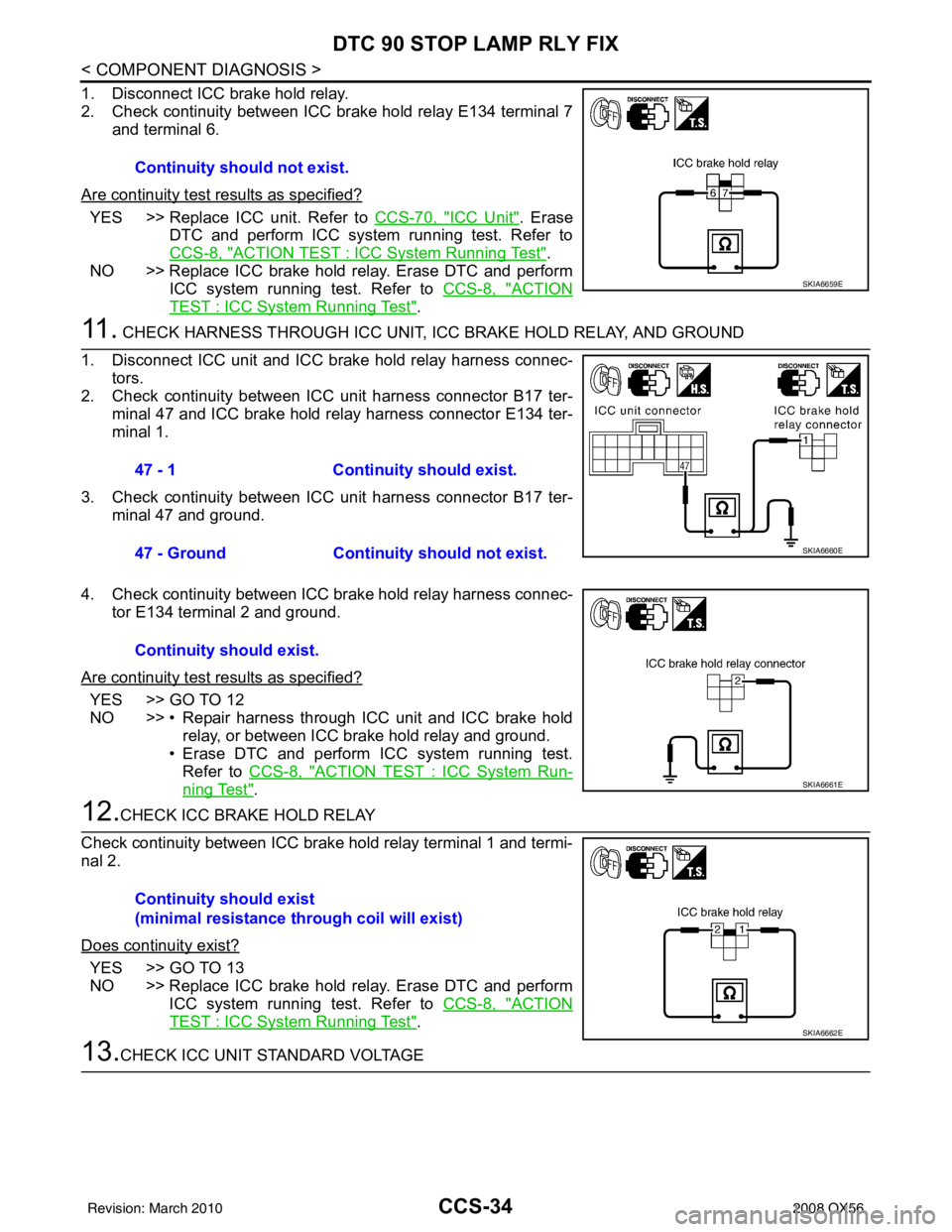
CCS-34
< COMPONENT DIAGNOSIS >
DTC 90 STOP LAMP RLY FIX
1. Disconnect ICC brake hold relay.
2. Check continuity between ICC brake hold relay E134 terminal 7and terminal 6.
Are continuity test results as specified?
YES >> Replace ICC unit. Refer to CCS-70, "ICC Unit". Erase
DTC and perform ICC system running test. Refer to
CCS-8, "
ACTION TEST : ICC System Running Test".
NO >> Replace ICC brake hold relay. Erase DTC and perform ICC system running test. Refer to CCS-8, "
ACTION
TEST : ICC System Running Test".
11 . CHECK HARNESS THROUGH ICC UNIT, ICC BRAKE HOLD RELAY, AND GROUND
1. Disconnect ICC unit and ICC brake hold relay harness connec- tors.
2. Check continuity between I CC unit harness connector B17 ter-
minal 47 and ICC brake hold relay harness connector E134 ter-
minal 1.
3. Check continuity between I CC unit harness connector B17 ter-
minal 47 and ground.
4. Check continuity between ICC brake hold relay harness connec- tor E134 terminal 2 and ground.
Are continuity test results as specified?
YES >> GO TO 12
NO >> • Repair harness through ICC unit and ICC brake hold relay, or between ICC brake hold relay and ground.
• Erase DTC and perform ICC system running test.
Refer to CCS-8, "
ACTION TEST : ICC System Run-
ning Test".
12.CHECK ICC BRAKE HOLD RELAY
Check continuity between ICC brake hold relay terminal 1 and termi-
nal 2.
Does continuity exist?
YES >> GO TO 13
NO >> Replace ICC brake hold relay. Erase DTC and perform ICC system running test. Refer to CCS-8, "
ACTION
TEST : ICC System Running Test".
13.CHECK ICC UNIT STANDARD VOLTAGE Continuity should not exist.
SKIA6659E
47 - 1
Continuity should exist.
47 - Ground Continuity should not exist.
SKIA6660E
Continuity should exist.
SKIA6661E
Continuity should exist
(minimal resistance through coil will exist)
SKIA6662E
Revision: March 2010 2008 QX56
Page 738 of 4083

PRECAUTIONSCO-3
< PRECAUTION >
C
DE
F
G H
I
J
K L
M A
CO
NP
O
5. When the repair work is completed, return the ignition switch to the
″LOCK ″ position before connecting
the battery cables. (At this time, the steering lock mechanism will engage.)
6. Perform a self-diagnosis check of al l control units using CONSULT-III.
Precaution for Liquid GasketINFOID:0000000001538852
REMOVAL OF LIQUID GASKET SEALING
• After removing the bolts and nuts, separate the mating surface and
remove the old liquid gasket sealing using Tool.
CAUTION:
Do not damage the mating surfaces.
• Tap the seal cutter to insert it (1).
• In areas where the Tool is difficult to use, lightly tap to slide it (2).
LIQUID GASKET APPLICATION PROCEDURE
1. Remove the old liquid gasket adhering to the gasket application surface and the mating surface using suitable tool.
• Remove the liquid gasket completely from the groove of the
liquid gasket application surface, bolts, and bolt holes.
2. Thoroughly clean the mating surfaces and remove adhering moisture, grease and foreign material.
3. Attach the liquid gasket tube to the Tool. Use Genuine RTV Silicone Sealant or equivalent. Refer to
GI-15, "
Recommended Chemical Products and Sealants".
4. Apply the liquid gasket without breaks to the specified location with the specified dimensions.
• If there is a groove for the liquid gasket application, apply theliquid gasket to the groove.
• As for the bolt holes, normally apply the liquid gasket inside
the holes. If specified in the procedure, it should also be
applied outside the holes.
• Within five minutes of liquid gasket application, install the mat-
ing component.
• If the liquid gasket protrudes, wipe it off immediately.
• Do not retighten after the installation.
• Wait 30 minutes or more after installation before refilling the engine with engine oil and engine coolant.
CAUTION:
If there are specific instructions in this manual, observe them.
Tool number : KV10111100 (J-37228)
WBIA0566E
PBIC0003E
Tool number : WS39930000 ( — )
WBIA0567E
SEM159F
Revision: March 2010
2008 QX56
Page 739 of 4083
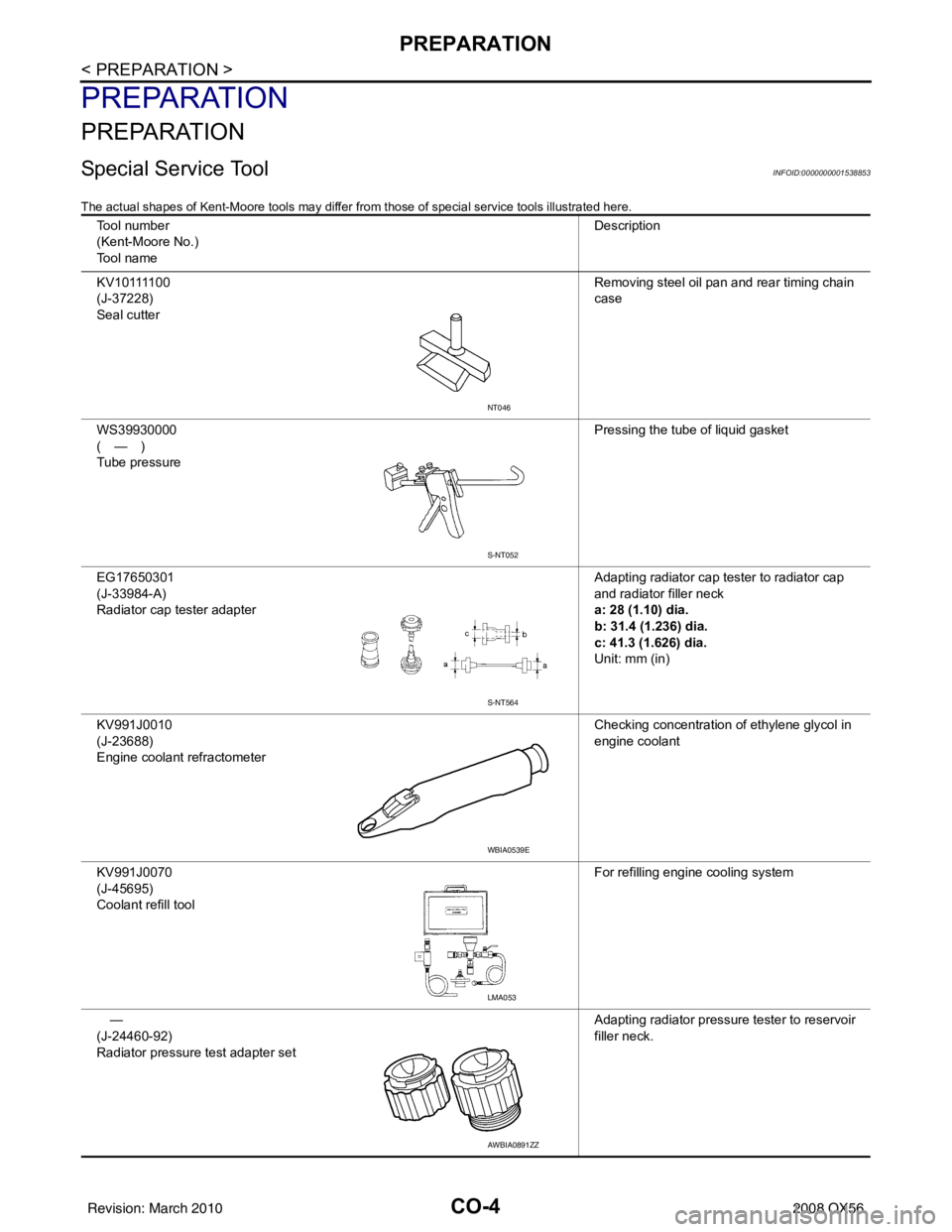
CO-4
< PREPARATION >
PREPARATION
PREPARATION
PREPARATION
Special Service ToolINFOID:0000000001538853
The actual shapes of Kent-Moore tools may differ from those of special service tools illustrated here.
Tool number
(Kent-Moore No.)
Tool name Description
K V 1 0 1111 0 0
(J-37228)
Seal cutter Removing steel oil pan and rear timing chain
case
WS39930000
(—)
Tube pressure Pressing the tube of liquid gasket
EG17650301
(J-33984-A)
Radiator cap tester adapter Adapting radiator cap tester to radiator cap
and radiator filler neck
a: 28 (1.10) dia.
b: 31.4 (1.236) dia.
c: 41.3 (1.626) dia.
Unit: mm (in)
KV991J0010
(J-23688)
Engine coolant refractometer Checking concentration of ethylene glycol in
engine coolant
KV991J0070
(J-45695)
Coolant refill tool For refilling engine cooling system
—
(J-24460-92)
Radiator pressure test adapter set Adapting radiator pressure tester to reservoir
filler neck.
NT046
S-NT052
S-NT564
WBIA0539E
LMA053
AWBIA0891ZZ
Revision: March 2010
2008 QX56
Page 746 of 4083
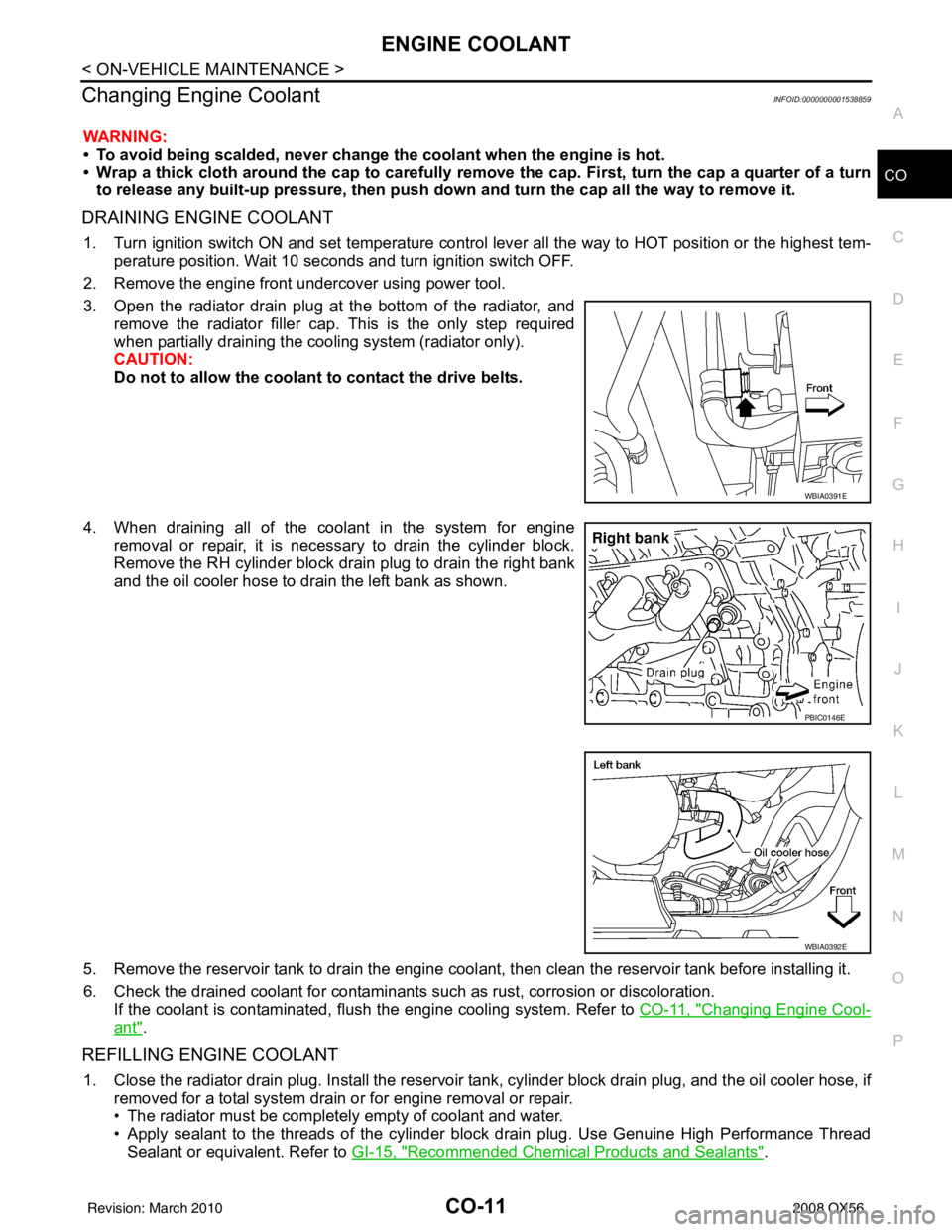
ENGINE COOLANTCO-11
< ON-VEHICLE MAINTENANCE >
C
DE
F
G H
I
J
K L
M A
CO
NP
O
Changing Engine CoolantINFOID:0000000001538859
WARNING:
• To avoid being scalded, never change the coolant when the engine is hot.
• Wrap a thick cloth around the cap to carefully remo
ve the cap. First, turn the cap a quarter of a turn
to release any built-up pressure, then push down and turn the cap all the way to remove it.
DRAINING ENGINE COOLANT
1. Turn ignition switch ON and set temperature control lever all the way to HOT position or the highest tem-
perature position. Wait 10 seconds and turn ignition switch OFF.
2. Remove the engine front undercover using power tool.
3. Open the radiator drain plug at the bottom of the radiator, and remove the radiator filler cap. This is the only step required
when partially draining the cooling system (radiator only).
CAUTION:
Do not to allow the coolant to contact the drive belts.
4. When draining all of the coolant in the system for engine removal or repair, it is necessary to drain the cylinder block.
Remove the RH cylinder block drain plug to drain the right bank
and the oil cooler hose to drain the left bank as shown.
5. Remove the reservoir tank to drain the engine cool ant, then clean the reservoir tank before installing it.
6. Check the drained coolant for contaminants such as rust, corrosion or discoloration. If the coolant is contaminated, flush the engine cooling system. Refer to CO-11, "
Changing Engine Cool-
ant".
REFILLING ENGINE COOLANT
1. Close the radiator drain plug. Install the reservoir tank, cylinder block drain plug, and the oil cooler hose, if
removed for a total system drain or for engine removal or repair.
• The radiator must be complete ly empty of coolant and water.
• Apply sealant to the threads of the cylinder block drain plug. Use Genuine High Performance Thread Sealant or equivalent. Refer to GI-15, "
Recommended Chemical Products and Sealants".
WBIA0391E
PBIC0146E
WBIA0392E
Revision: March 2010 2008 QX56
Page 753 of 4083
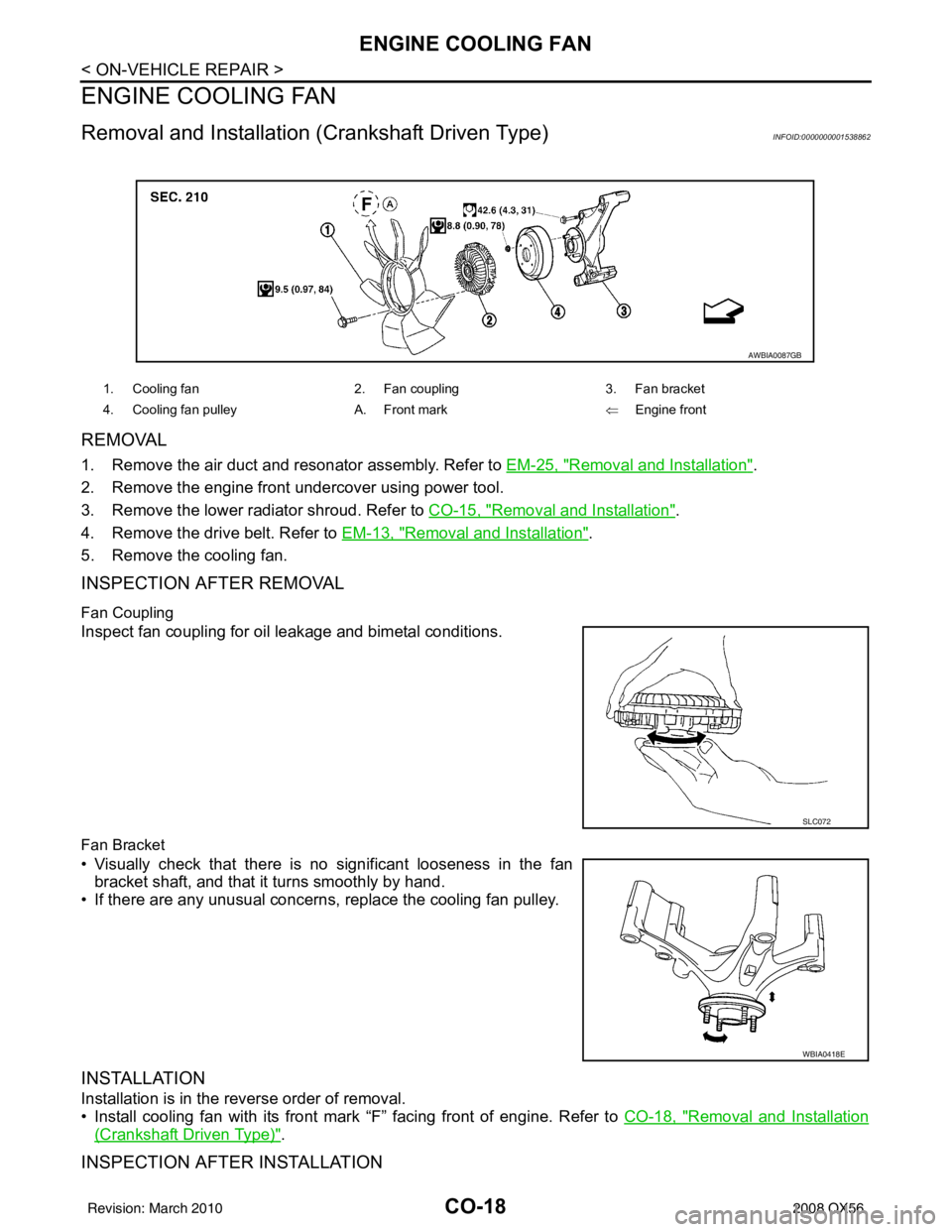
CO-18
< ON-VEHICLE REPAIR >
ENGINE COOLING FAN
ENGINE COOLING FAN
Removal and Installation (Crankshaft Driven Type)INFOID:0000000001538862
REMOVAL
1. Remove the air duct and resonator assembly. Refer to EM-25, "Removal and Installation".
2. Remove the engine front undercover using power tool.
3. Remove the lower radiator shroud. Refer to CO-15, "
Removal and Installation".
4. Remove the drive belt. Refer to EM-13, "
Removal and Installation".
5. Remove the cooling fan.
INSPECTION AFTER REMOVAL
Fan Coupling
Inspect fan coupling for oil leakage and bimetal conditions.
Fan Bracket
• Visually check that there is no significant looseness in the fan bracket shaft, and that it turns smoothly by hand.
• If there are any unusual concerns, replace the cooling fan pulley.
INSTALLATION
Installation is in the reverse order of removal.
• Install cooling fan with its front mark “F” facing front of engine. Refer to CO-18, "
Removal and Installation
(Crankshaft Driven Type)".
INSPECTION AFTER INSTALLATION
1. Cooling fan 2. Fan coupling3. Fan bracket
4. Cooling fan pulley A. Front mark ⇐Engine front
AWBIA0087GB
SLC072
WBIA0418E
Revision: March 2010 2008 QX56
Page 792 of 4083
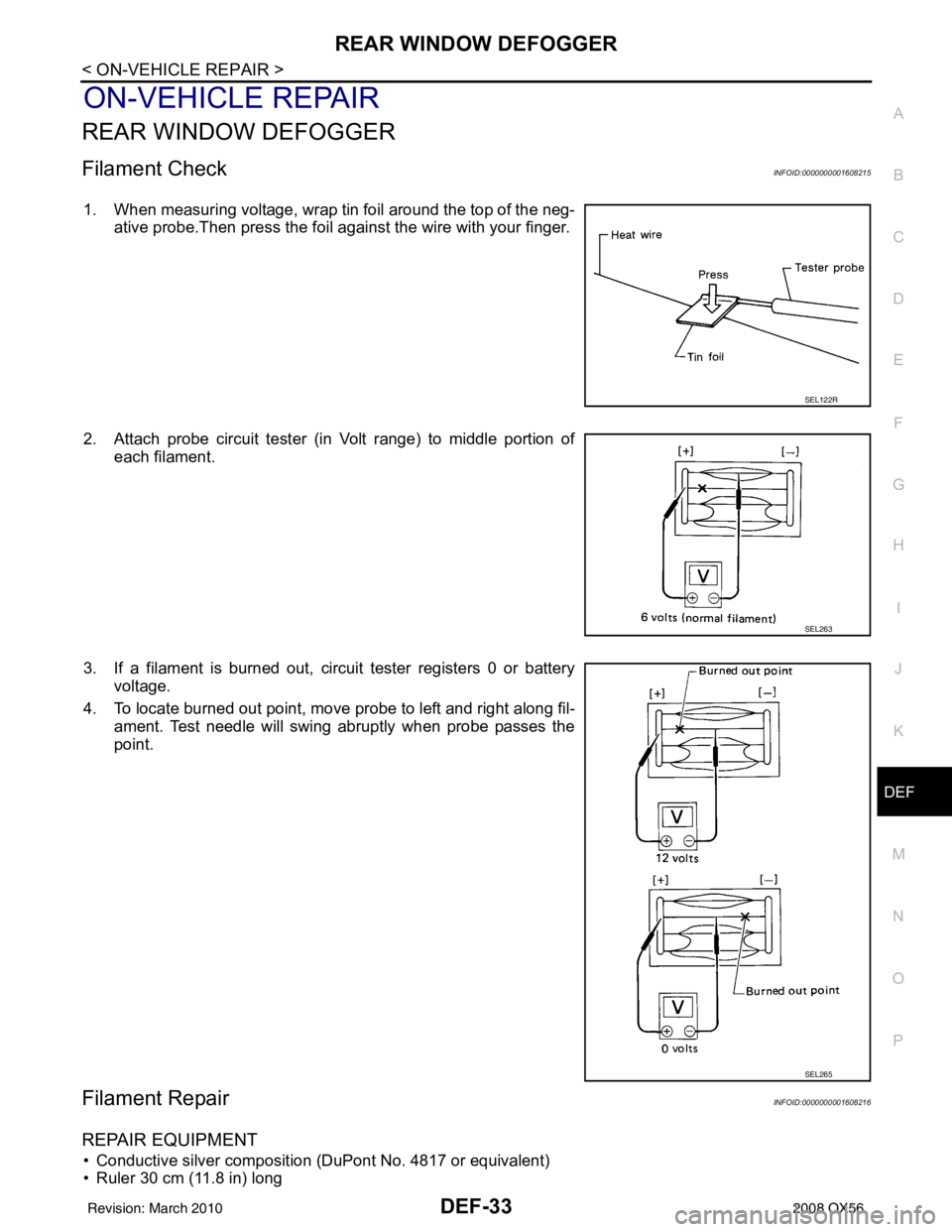
REAR WINDOW DEFOGGERDEF-33
< ON-VEHICLE REPAIR >
C
DE
F
G H
I
J
K
M A
B
DEF
N
O P
ON-VEHICLE REPAIR
REAR WINDOW DEFOGGER
Filament CheckINFOID:0000000001608215
1. When measuring voltage, wrap tin foil around the top of the neg- ative probe.Then press the foil against the wire with your finger.
2. Attach probe circuit tester (in Volt range) to middle portion of each filament.
3. If a filament is burned out, circuit tester registers 0 or battery voltage.
4. To locate burned out point, move probe to left and right along fil- ament. Test needle will swing abruptly when probe passes the
point.
Filament RepairINFOID:0000000001608216
REPAIR EQUIPMENT
• Conductive silver composition (DuPont No. 4817 or equivalent)
• Ruler 30 cm (11.8 in) long
SEL122R
SEL263
SEL265
Revision: March 2010 2008 QX56
Page 1034 of 4083
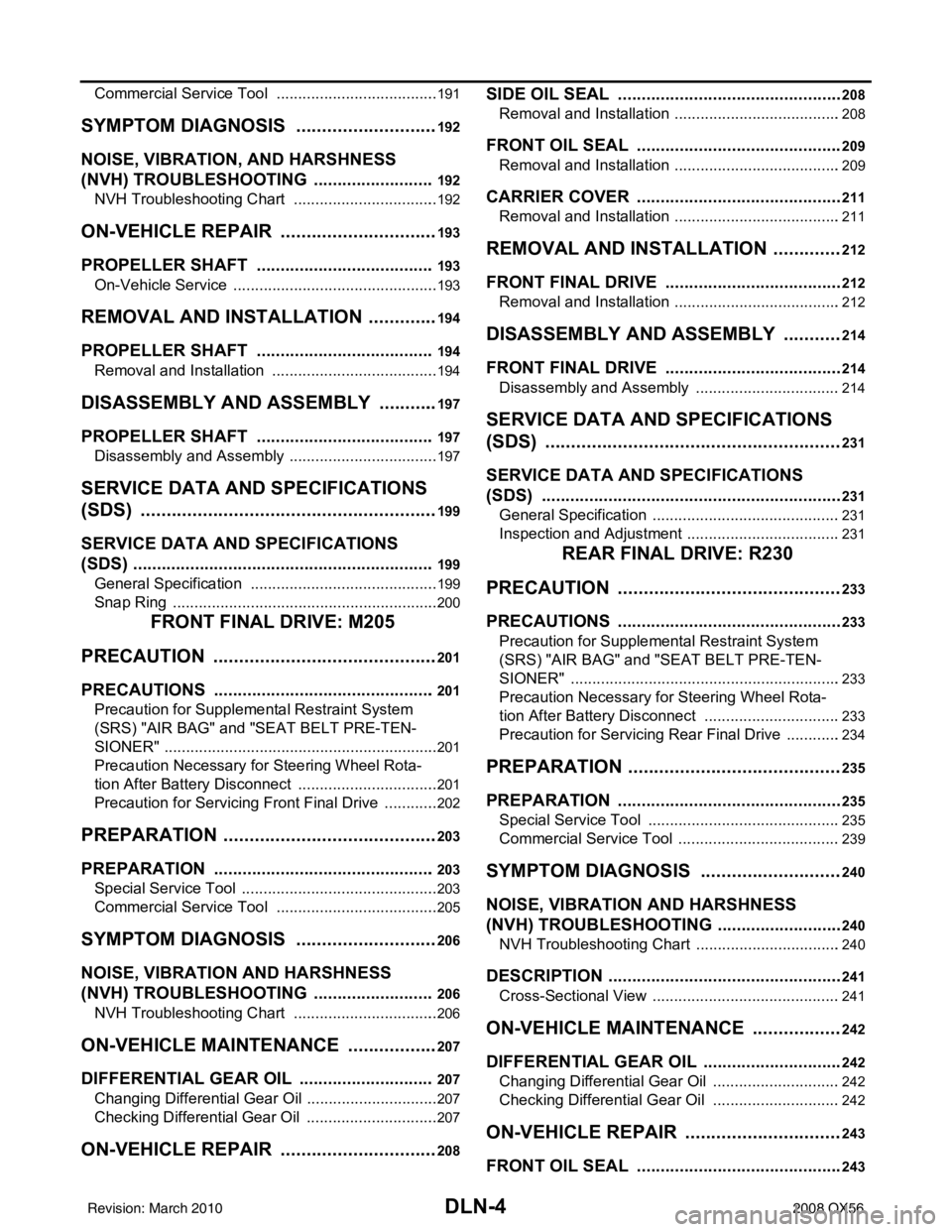
DLN-4
Commercial Service Tool ......................................191
SYMPTOM DIAGNOSIS ............................192
NOISE, VIBRATION, AND HARSHNESS
(NVH) TROUBLESHOOTING ......................... .
192
NVH Troubleshooting Chart ................................ ..192
ON-VEHICLE REPAIR ...............................193
PROPELLER SHAFT ..................................... .193
On-Vehicle Service .............................................. ..193
REMOVAL AND INSTALLATION ..............194
PROPELLER SHAFT ..................................... .194
Removal and Installation ..................................... ..194
DISASSEMBLY AND ASSEMBLY ............197
PROPELLER SHAFT ..................................... .197
Disassembly and Assembly ................................. ..197
SERVICE DATA AND SPECIFICATIONS
(SDS) ........................................................ ..
199
SERVICE DATA AND SPECIFICATIONS
(SDS) ............................................................... .
199
General Specification .......................................... ..199
Snap Ring ..............................................................200
FRONT FINAL DRIVE: M205
PRECAUTION .............. ..............................
201
PRECAUTIONS .............................................. .201
Precaution for Supplemental Restraint System
(SRS) "AIR BAG" and "SEAT BELT PRE-TEN-
SIONER" .............................................................. ..
201
Precaution Necessary for Steering Wheel Rota-
tion After Battery Disconnect .................................
201
Precaution for Servicing Front Final Drive .............202
PREPARATION ..........................................203
PREPARATION .............................................. .203
Special Service Tool ............................................ ..203
Commercial Service Tool ......................................205
SYMPTOM DIAGNOSIS ............................206
NOISE, VIBRATION AND HARSHNESS
(NVH) TROUBLESHOOTING ......................... .
206
NVH Troubleshooting Chart ................................ ..206
ON-VEHICLE MAINTENANCE ..................207
DIFFERENTIAL GEAR OIL ............................ .207
Changing Differential Gear Oil ...............................207
Checking Differential Gear Oil ............................. ..207
ON-VEHICLE REPAIR ...............................208
SIDE OIL SEAL .............................................. ..208
Removal and Installation .......................................208
FRONT OIL SEAL ............................................209
Removal and Installation .......................................209
CARRIER COVER .......................................... ..211
Removal and Installation .......................................211
REMOVAL AND INSTALLA TION .............212
FRONT FINAL DRIVE .................................... ..212
Removal and Installation .......................................212
DISASSEMBLY AND ASSEMBLY ...........214
FRONT FINAL DRIVE .................................... ..214
Disassembly and Assembly ................................. .214
SERVICE DATA AND SPECIFICATIONS
(SDS) ........ .................................................
231
SERVICE DATA AND SPECIFICATIONS
(SDS) .............................................................. ..
231
General Specification ........................................... .231
Inspection and Adjustment ....................................231
REAR FINAL DRIVE: R230
PRECAUTION ............... ............................
233
PRECAUTIONS .............................................. ..233
Precaution for Supplemental Restraint System
(SRS) "AIR BAG" and "SEAT BELT PRE-TEN-
SIONER" .............................................................. .
233
Precaution Necessary for Steering Wheel Rota-
tion After Battery Disconnect ................................
233
Precaution for Servicing Rear Final Drive .............234
PREPARATION .........................................235
PREPARATION .............................................. ..235
Special Service Tool ............................................ .235
Commercial Service Tool ......................................239
SYMPTOM DIAGNOSIS ...........................240
NOISE, VIBRATION AND HARSHNESS
(NVH) TROUBLESHOOTING ......................... ..
240
NVH Troubleshooting Chart ..................................240
DESCRIPTION ................................................ ..241
Cross-Sectional View ........................................... .241
ON-VEHICLE MAINTENANCE .................242
DIFFERENTIAL GEAR OIL ..............................242
Changing Differential Gear Oil ............................. .242
Checking Differential Gear Oil ..............................242
ON-VEHICLE REPAIR ..............................243
FRONT OIL SEAL ............................................243
Revision: March 2010 2008 QX56
Page 1044 of 4083
![INFINITI QX56 2008 Factory User Guide DLN-14
< FUNCTION DIAGNOSIS >[ATX14B]
4WD SYSTEM
• Displays 4LO condition while engine is running. 4LO indicator lamp flashes if transfer gear does not shift
completely under 2WD, AUTO, 4H ⇔4LO. ( INFINITI QX56 2008 Factory User Guide DLN-14
< FUNCTION DIAGNOSIS >[ATX14B]
4WD SYSTEM
• Displays 4LO condition while engine is running. 4LO indicator lamp flashes if transfer gear does not shift
completely under 2WD, AUTO, 4H ⇔4LO. (](/img/42/57030/w960_57030-1043.png)
DLN-14
< FUNCTION DIAGNOSIS >[ATX14B]
4WD SYSTEM
• Displays 4LO condition while engine is running. 4LO indicator lamp flashes if transfer gear does not shift
completely under 2WD, AUTO, 4H ⇔4LO. (When 4WD warning lamp is turned on, 4LO indicator lamp is
turned off.)
• Turns ON for approximately 1 second when ignition switch is turned ON, for purpose of lamp check.
4WD WARNING LAMP
Turns on or flashes when there is a malfunction in 4WD system.
Also turns on when ignition switch is turned ON, for purpose of lamp che\
ck. Turns OFF approximately 1 sec-
ond after the engine starts if system is normal.
4WD Warning Lamp Indication
ATP WARNING LAMP
When the A/T selector lever is in P position, the vehicle may move if the transfer case is in neutral. ATP warn-
ing lamp is turned on to indicate this condition to the driver.
LINE PRESSURE SWITCH
• With the transfer system design, control of the oil pressure provides the transmission of drive torque to the
front wheels. The main pressure to control the oil pressure is referred to as the line pressure.
• The line pressure switch determines whether or not adequate line pressure has built up under different oper- ating conditions.
• The line pressure switch closes when line pressure is produced.
• The line pressure switch senses line pressure abnormalities and turns the 4WD warning lamp ON.
CLUTCH PRESSURE SWITCH
• The clutch pressure switch determines whether or not adequate clutch pressure has built up under different
operating conditions.
• The clutch pressure switch closes when clutch pressure is produced.
• The clutch pressure switch senses clutch pressure abnormalities and turns the 4WD warning lamp ON.
WAIT DETECTION SWITCH
• The wait detection switch operates when there is circulating torque produced in the propeller shaft (L→H) or
when there is a phase difference between 2-4 sleeve and clutch drum (H →L). After the release of the circu-
lating torque, the wait detection switch helps provi de the 4WD lock gear (clutch drum) shifts. A difference
may occur between the operation of the 4WD shift swit ch and actual drive mode. At this point, the wait
detection switch senses an actual drive mode.
• The wait detection switch operates as follows.
- 4WD lock gear (clutch drum) locked: ON
- 4WD lock gear (clutch drum) released: OFF
• The wait detection switch senses an actual drive mode and the 4WD shift indicator lamp indicates the vehi-
cle drive mode.
ATP SWITCH
ATP switch detects if transfer case is in neutral by the position of the L-H shift fork.
NOTE:
Transfer case may be in neutral when shifting between 4H-4LO.
NEUTRAL-4LO SWITCH
The neutral-4LO switch detects that transfer gear is in neutral or 4LO (or shifting from neutral to 4LO) condi-
tion by L-H shift fork position.
Condition 4WD warning lamp
System normal OFF
Lamp check Turns ON when ignition switch is turned ON.
Turns OFF after engine start.
4WD system malfunction ON
During self-diagnosis Flashes malfunction mode.
Large difference in diameter of front/
rear tires Flashes slow (1 flash / 2 seconds)
(Continues to flash until the ignition switch is turned OFF)
High fluid temperature in transfer case Flashes rapidly (2 flashes / 1 second)
(Continues to flash until fluid temperature returns to normal)
Revision: March 2010 2008 QX56
Page 1097 of 4083
![INFINITI QX56 2008 Factory User Guide P1826 TRANSFER FLUID TEMPERATUREDLN-67
< COMPONENT DIAGNOSIS > [ATX14B]
C
EF
G H
I
J
K L
M A
B
DLN
N
O P
P1826 TRANSFER FLUID TEMPERATURE
DescriptionINFOID:0000000001737155
Signal voltage from the tra INFINITI QX56 2008 Factory User Guide P1826 TRANSFER FLUID TEMPERATUREDLN-67
< COMPONENT DIAGNOSIS > [ATX14B]
C
EF
G H
I
J
K L
M A
B
DLN
N
O P
P1826 TRANSFER FLUID TEMPERATURE
DescriptionINFOID:0000000001737155
Signal voltage from the tra](/img/42/57030/w960_57030-1096.png)
P1826 TRANSFER FLUID TEMPERATUREDLN-67
< COMPONENT DIAGNOSIS > [ATX14B]
C
EF
G H
I
J
K L
M A
B
DLN
N
O P
P1826 TRANSFER FLUID TEMPERATURE
DescriptionINFOID:0000000001737155
Signal voltage from the transfer fluid temperature sens or is abnormally high (Transfer fluid temperature is
abnormally low) while driving.
DTC LogicINFOID:0000000001737156
DTC DETECTION LOGIC
DTC CONFIRMATION PROCEDURE
1.DTC CONFIRMATION PROCEDURE
1. Turn ignition switch ON.
2. Perform self-diagnosis.
Is DTC P1826 displayed?
YES >> Perform diagnosis procedure. Refer to DLN-67, "Diagnosis Procedure".
NO >> Inspection End.
Diagnosis ProcedureINFOID:0000000001737157
1.CHECK TRANSFER FLUID TE MPERATURE SENSOR SIGNAL
With CONSULT-III
1. Start engine.
2. Select DATA MONITOR mode for ALL MODE AWD/4WD with CONSULT-III.
3. Read out the value of FLUID TEMP SE.
Without CONSULT-III
1. Start engine.
2. Check voltage between transfer control unit harness connector
terminals and ground.
Are inspection results normal?
YES >> GO TO 4.
NO >> GO TO 2.
2.CHECK HARNESS BETWEEN TRANSF ER CONTROL UNIT AND TRANSFER TERMINAL CORD AS-
DTCCONSULT-III Diagnostic item is detected when... Reference
[P1826] OIL TEMP SEN Signal voltage from transfer fluid temper-
ature sensor is abnormally high (Trans-
fer fluid temperature is abnormally low)
while driving.Refer to DLN-67
.
Condition
Display value
(Approx.)
Transfer fluid temperature approx. 20 - 80 °C (68 - 176° F) 1.1 - 0.3V
Connector Terminal ConditionData
(Approx.)
E143 28 -
Ground Always
0V
31 -
Ground Ignition switch:
ON Transfer fluid temperature
approx. 20
°C (68 °F) 1.1V
Transfer fluid temperature
approx. 80 °C (176 °F) 0.3V
SDIA2742E
Revision: March 2010
2008 QX56