ignition INFINITI QX56 2008 Factory Service Manual
[x] Cancel search | Manufacturer: INFINITI, Model Year: 2008, Model line: QX56, Model: INFINITI QX56 2008Pages: 4083, PDF Size: 81.73 MB
Page 1231 of 4083
![INFINITI QX56 2008 Factory Service Manual PRECAUTIONSDLN-201
< PRECAUTION > [FRONT FINAL DRIVE: M205]
C
EF
G H
I
J
K L
M A
B
DLN
N
O P
PRECAUTION
PRECAUTIONS
Precaution for Supplemental Restraint System (SRS) "AIR BAG" and "SEAT BELT
PRE-TE INFINITI QX56 2008 Factory Service Manual PRECAUTIONSDLN-201
< PRECAUTION > [FRONT FINAL DRIVE: M205]
C
EF
G H
I
J
K L
M A
B
DLN
N
O P
PRECAUTION
PRECAUTIONS
Precaution for Supplemental Restraint System (SRS) "AIR BAG" and "SEAT BELT
PRE-TE](/img/42/57030/w960_57030-1230.png)
PRECAUTIONSDLN-201
< PRECAUTION > [FRONT FINAL DRIVE: M205]
C
EF
G H
I
J
K L
M A
B
DLN
N
O P
PRECAUTION
PRECAUTIONS
Precaution for Supplemental Restraint System (SRS) "AIR BAG" and "SEAT BELT
PRE-TENSIONER"
INFOID:0000000004857592
The Supplemental Restraint System such as “AIR BAG” and “SEAT BELT PRE-TENSIONER”, used along
with a front seat belt, helps to reduce the risk or severi ty of injury to the driver and front passenger for certain
types of collision. This system includes seat belt switch inputs and dual stage front air bag modules. The SRS
system uses the seat belt switches to determine the front air bag deployment, and may only deploy one front
air bag, depending on the severity of a collision and w hether the front occupants are belted or unbelted.
Information necessary to service the system safely is included in the SR and SB section of this Service Man-
ual.
WARNING:
• To avoid rendering the SRS inoper ative, which could increase the risk of personal injury or death in
the event of a collision which would result in air bag inflation, all maintenance must be performed by
an authorized NISSAN/INFINITI dealer.
• Improper maintenance, including in correct removal and installation of the SRS, can lead to personal
injury caused by unintentional act ivation of the system. For removal of Spiral Cable and Air Bag
Module, see the SR section.
• Do not use electrical test equipm ent on any circuit related to the SRS unless instructed to in this
Service Manual. SRS wiring harnesses can be identi fied by yellow and/or orange harnesses or har-
ness connectors.
PRECAUTIONS WHEN USING POWER TOOLS (AIR OR ELECTRIC) AND HAMMERS
WARNING:
• When working near the Airbag Diagnosis Sensor Un it or other Airbag System sensors with the Igni-
tion ON or engine running, DO NOT use air or el ectric power tools or strike near the sensor(s) with a
hammer. Heavy vibration could activate the sensor( s) and deploy the air bag(s), possibly causing
serious injury.
• When using air or electric power tools or hammers, always switch the Ignition OFF, disconnect the battery, and wait at least 3 minutes before performing any service.
Precaution Necessary for Steering Wheel Rotation After Battery Disconnect
INFOID:0000000004857591
NOTE:
• This Procedure is applied only to models with Intelligent Key system and NATS (NISSAN ANTI-THEFT SYS-
TEM).
• Remove and install all control units after disconnecti ng both battery cables with the ignition knob in the
″ LOCK ″ position.
• Always use CONSULT-III to perform self-diagnosis as a part of each function inspection after finishing work.
If DTC is detected, perform trouble diagnosis according to self-diagnostic results.
For models equipped with the Intelligent Key system and NATS , an electrically controlled steering lock mech-
anism is adopted on the key cylinder.
For this reason, if the battery is disconnected or if the battery is discharged, the steering wheel will lock and
steering wheel rotation will become impossible.
If steering wheel rotation is required when battery power is interrupted, follow the procedure below before
starting the repair operation.
OPERATION PROCEDURE
1. Connect both battery cables. NOTE:
Supply power using jumper cables if battery is discharged.
2. Use the Intelligent Key or mechanical key to turn the ignition switch to the ″ACC ″ position. At this time, the
steering lock will be released.
3. Disconnect both battery cables. The steering lock will remain released and the steering wheel can be
rotated.
4. Perform the necessary repair operation.
Revision: March 2010 2008 QX56
Page 1232 of 4083
![INFINITI QX56 2008 Factory Service Manual DLN-202
< PRECAUTION >[FRONT FINAL DRIVE: M205]
PRECAUTIONS
5. When the repair work is completed, return the ignition switch to the
″LOCK ″ position before connecting
the battery cables. (At this INFINITI QX56 2008 Factory Service Manual DLN-202
< PRECAUTION >[FRONT FINAL DRIVE: M205]
PRECAUTIONS
5. When the repair work is completed, return the ignition switch to the
″LOCK ″ position before connecting
the battery cables. (At this](/img/42/57030/w960_57030-1231.png)
DLN-202
< PRECAUTION >[FRONT FINAL DRIVE: M205]
PRECAUTIONS
5. When the repair work is completed, return the ignition switch to the
″LOCK ″ position before connecting
the battery cables. (At this time, the steering lock mechanism will engage.)
6. Perform a self-diagnosis check of a ll control units using CONSULT-III.
Precaution for Servicing Front Final DriveINFOID:0000000001604439
• Before starting diagnosis of the vehicle, understand the symptoms well. Perform correct and systematic
operations.
• Check for the correct installation status prior to re moval or disassembly. When matching marks are required,
be certain they do not interfere with the function of the parts they are applied to.
• Overhaul should be done in a clean work area, a dust proof area is recommended.
• Before disassembly, completely remove sand and mud from the exterior of the unit, preventing them from
entering into the unit during disassembly or assembly.
• Always use shop paper for cleaning the inside of components.
• Avoid using cotton gloves or a shop cloth to prevent the entering of lint.
• Check appearance of the disassembled parts for dam age, deformation, and abnormal wear. Replace them
with new ones if necessary.
• Gaskets, seals and O-rings should be replaced any time the unit is disassembled.
• Clean and flush the parts sufficiently and blow them dry.
• Be careful not to damage sliding surfaces and mating surfaces.
• When applying sealant, remove the old sealant from the mating surface; then remove any moisture, oil, and
foreign materials from the application and mating surfaces.
• In principle, tighten nuts or bolts gradually in severa l steps working diagonally from inside to outside. If a
tightening sequence is specified, observe it.
• During assembly, observe the specified tightening torque.
• Add new differential gear oil, petroleum jelly, or multi-purpose grease, as specified.
Revision: March 2010 2008 QX56
Page 1263 of 4083
![INFINITI QX56 2008 Factory Service Manual PRECAUTIONSDLN-233
< PRECAUTION > [REAR FINAL DRIVE: R230]
C
EF
G H
I
J
K L
M A
B
DLN
N
O P
PRECAUTION
PRECAUTIONS
Precaution for Supplemental Restraint System (SRS) "AIR BAG" and "SEAT BELT
PRE-TEN INFINITI QX56 2008 Factory Service Manual PRECAUTIONSDLN-233
< PRECAUTION > [REAR FINAL DRIVE: R230]
C
EF
G H
I
J
K L
M A
B
DLN
N
O P
PRECAUTION
PRECAUTIONS
Precaution for Supplemental Restraint System (SRS) "AIR BAG" and "SEAT BELT
PRE-TEN](/img/42/57030/w960_57030-1262.png)
PRECAUTIONSDLN-233
< PRECAUTION > [REAR FINAL DRIVE: R230]
C
EF
G H
I
J
K L
M A
B
DLN
N
O P
PRECAUTION
PRECAUTIONS
Precaution for Supplemental Restraint System (SRS) "AIR BAG" and "SEAT BELT
PRE-TENSIONER"
INFOID:0000000004857594
The Supplemental Restraint System such as “AIR BAG” and “SEAT BELT PRE-TENSIONER”, used along
with a front seat belt, helps to reduce the risk or severi ty of injury to the driver and front passenger for certain
types of collision. This system includes seat belt switch inputs and dual stage front air bag modules. The SRS
system uses the seat belt switches to determine the front air bag deployment, and may only deploy one front
air bag, depending on the severity of a collision and w hether the front occupants are belted or unbelted.
Information necessary to service the system safely is included in the SR and SB section of this Service Man-
ual.
WARNING:
• To avoid rendering the SRS inoper ative, which could increase the risk of personal injury or death in
the event of a collision which would result in air bag inflation, all maintenance must be performed by
an authorized NISSAN/INFINITI dealer.
• Improper maintenance, including in correct removal and installation of the SRS, can lead to personal
injury caused by unintentional act ivation of the system. For removal of Spiral Cable and Air Bag
Module, see the SR section.
• Do not use electrical test equipm ent on any circuit related to the SRS unless instructed to in this
Service Manual. SRS wiring harnesses can be identi fied by yellow and/or orange harnesses or har-
ness connectors.
PRECAUTIONS WHEN USING POWER TOOLS (AIR OR ELECTRIC) AND HAMMERS
WARNING:
• When working near the Airbag Diagnosis Sensor Un it or other Airbag System sensors with the Igni-
tion ON or engine running, DO NOT use air or el ectric power tools or strike near the sensor(s) with a
hammer. Heavy vibration could activate the sensor( s) and deploy the air bag(s), possibly causing
serious injury.
• When using air or electric power tools or hammers, always switch the Ignition OFF, disconnect the battery, and wait at least 3 minutes before performing any service.
Precaution Necessary for Steering Wheel Rotation After Battery Disconnect
INFOID:0000000004857593
NOTE:
• This Procedure is applied only to models with Intelligent Key system and NATS (NISSAN ANTI-THEFT SYS-
TEM).
• Remove and install all control units after disconnecti ng both battery cables with the ignition knob in the
″ LOCK ″ position.
• Always use CONSULT-III to perform self-diagnosis as a part of each function inspection after finishing work.
If DTC is detected, perform trouble diagnosis according to self-diagnostic results.
For models equipped with the Intelligent Key system and NATS , an electrically controlled steering lock mech-
anism is adopted on the key cylinder.
For this reason, if the battery is disconnected or if the battery is discharged, the steering wheel will lock and
steering wheel rotation will become impossible.
If steering wheel rotation is required when battery power is interrupted, follow the procedure below before
starting the repair operation.
OPERATION PROCEDURE
1. Connect both battery cables. NOTE:
Supply power using jumper cables if battery is discharged.
2. Use the Intelligent Key or mechanical key to turn the ignition switch to the ″ACC ″ position. At this time, the
steering lock will be released.
3. Disconnect both battery cables. The steering lock will remain released and the steering wheel can be
rotated.
4. Perform the necessary repair operation.
Revision: March 2010 2008 QX56
Page 1264 of 4083
![INFINITI QX56 2008 Factory Service Manual DLN-234
< PRECAUTION >[REAR FINAL DRIVE: R230]
PRECAUTIONS
5. When the repair work is completed, return the ignition switch to the
″LOCK ″ position before connecting
the battery cables. (At this INFINITI QX56 2008 Factory Service Manual DLN-234
< PRECAUTION >[REAR FINAL DRIVE: R230]
PRECAUTIONS
5. When the repair work is completed, return the ignition switch to the
″LOCK ″ position before connecting
the battery cables. (At this](/img/42/57030/w960_57030-1263.png)
DLN-234
< PRECAUTION >[REAR FINAL DRIVE: R230]
PRECAUTIONS
5. When the repair work is completed, return the ignition switch to the
″LOCK ″ position before connecting
the battery cables. (At this time, the steering lock mechanism will engage.)
6. Perform a self-diagnosis check of a ll control units using CONSULT-III.
Precaution for Servicing Rear Final DriveINFOID:0000000001604452
• Before starting diagnosis of the vehicle, understand the symptoms well. Perform correct and systematic
operations.
• Check for the correct installation status prior to re moval or disassembly. When matching marks are required,
be certain they do not interfere with the function of the parts they are applied to.
• Overhaul should be done in a clean work area, a dust proof area is recommended.
• Before disassembly, completely remove sand and mud from the exterior of the unit, preventing them from
entering into the unit during disassembly or assembly.
• Always use shop paper for cleaning the inside of components.
• Avoid using cotton gloves or a shop cloth to prevent the entering of lint.
• Check appearance of the disassembled parts for dam age, deformation, and abnormal wear. Replace them
with new ones if necessary.
• Gaskets, seals and O-rings should be replaced any time the unit is disassembled.
• Clean and flush the parts sufficiently and blow them dry.
• Be careful not to damage sliding surfaces and mating surfaces.
• When applying sealant, remove the old sealant from the mating surface; then remove any moisture, oil, and
foreign materials from the application and mating surfaces.
• In principle, tighten nuts or bolts gradually in severa l steps working diagonally from inside to outside. If a
tightening sequence is specified, observe it.
• During assembly, observe the specified tightening torque.
• Add new differential gear oil, petroleum jelly, or multi-purpose grease, as specified.
Revision: March 2010 2008 QX56
Page 1300 of 4083
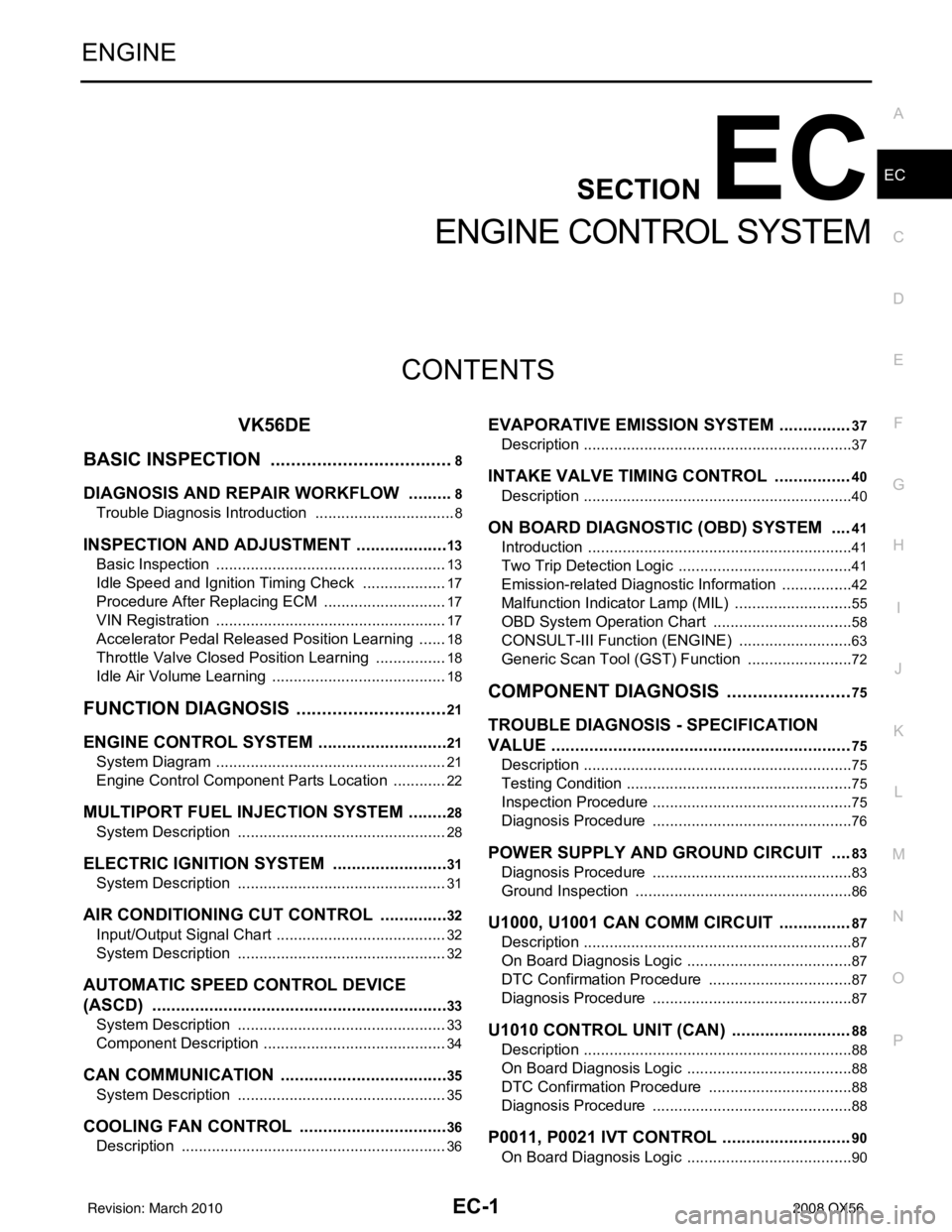
EC-1
ENGINE
C
DE
F
G H
I
J
K L
M
SECTION EC
A
EC
N
O P
CONTENTS
ENGINE CONTROL SYSTEM
VK56DE
BASIC INSPECTION ....... .............................
8
DIAGNOSIS AND REPAIR WORKFLOW ..... .....8
Trouble Diagnosis Introduction ........................... ......8
INSPECTION AND ADJUSTMENT ....................13
Basic Inspection .................................................. ....13
Idle Speed and Ignition Timing Check ....................17
Procedure After Replacing ECM .............................17
VIN Registration ......................................................17
Accelerator Pedal Released Position Learning .......18
Throttle Valve Closed Position Learning .................18
Idle Air Volume Learning .........................................18
FUNCTION DIAGNOSIS ..............................21
ENGINE CONTROL SYSTEM ........................ ....21
System Diagram .................................................. ....21
Engine Control Component Parts Location .............22
MULTIPORT FUEL INJECTION SYSTEM ..... ....28
System Description ............................................. ....28
ELECTRIC IGNITION SYSTEM ..................... ....31
System Description ............................................. ....31
AIR CONDITIONING CUT CONTROL ...............32
Input/Output Signal Chart .................................... ....32
System Description .................................................32
AUTOMATIC SPEED CONTROL DEVICE
(ASCD) ...............................................................
33
System Description ............................................. ....33
Component Description ...........................................34
CAN COMMUNICATION ....................................35
System Description ............................................. ....35
COOLING FAN CONTROL ................................36
Description ..............................................................36
EVAPORATIVE EMISSION SYSTEM ...............37
Description ........................................................... ....37
INTAKE VALVE TIMING CONTROL ................40
Description ...............................................................40
ON BOARD DIAGNOSTIC (OBD) SYSTEM ....41
Introduction ..............................................................41
Two Trip Detection Logic .........................................41
Emission-related Diagnostic Information .................42
Malfunction Indicator Lamp (MIL) ............................55
OBD System Operation Chart .................................58
CONSULT-III Function (ENGINE) ...........................63
Generic Scan Tool (GST) Function .........................72
COMPONENT DIAGNOSIS .........................75
TROUBLE DIAGNOSIS - SPECIFICATION
VALUE ...............................................................
75
Description ........................................................... ....75
Testing Condition .....................................................75
Inspection Procedure ...............................................75
Diagnosis Procedure ...............................................76
POWER SUPPLY AND GROUND CIRCUIT ....83
Diagnosis Procedure ...............................................83
Ground Inspection ...................................................86
U1000, U1001 CAN COMM CIRCUIT ...............87
Description ...............................................................87
On Board Diagnosis Logic .......................................87
DTC Confirmation Procedure ..................................87
Diagnosis Procedure ...............................................87
U1010 CONTROL UNIT (CAN) .........................88
Description ...............................................................88
On Board Diagnosis Logic .......................................88
DTC Confirmation Procedure ..................................88
Diagnosis Procedure ...............................................88
P0011, P0021 IVT CONTROL ...........................90
On Board Diagnosis Logic .......................................90
Revision: March 2010 2008 QX56
Page 1305 of 4083
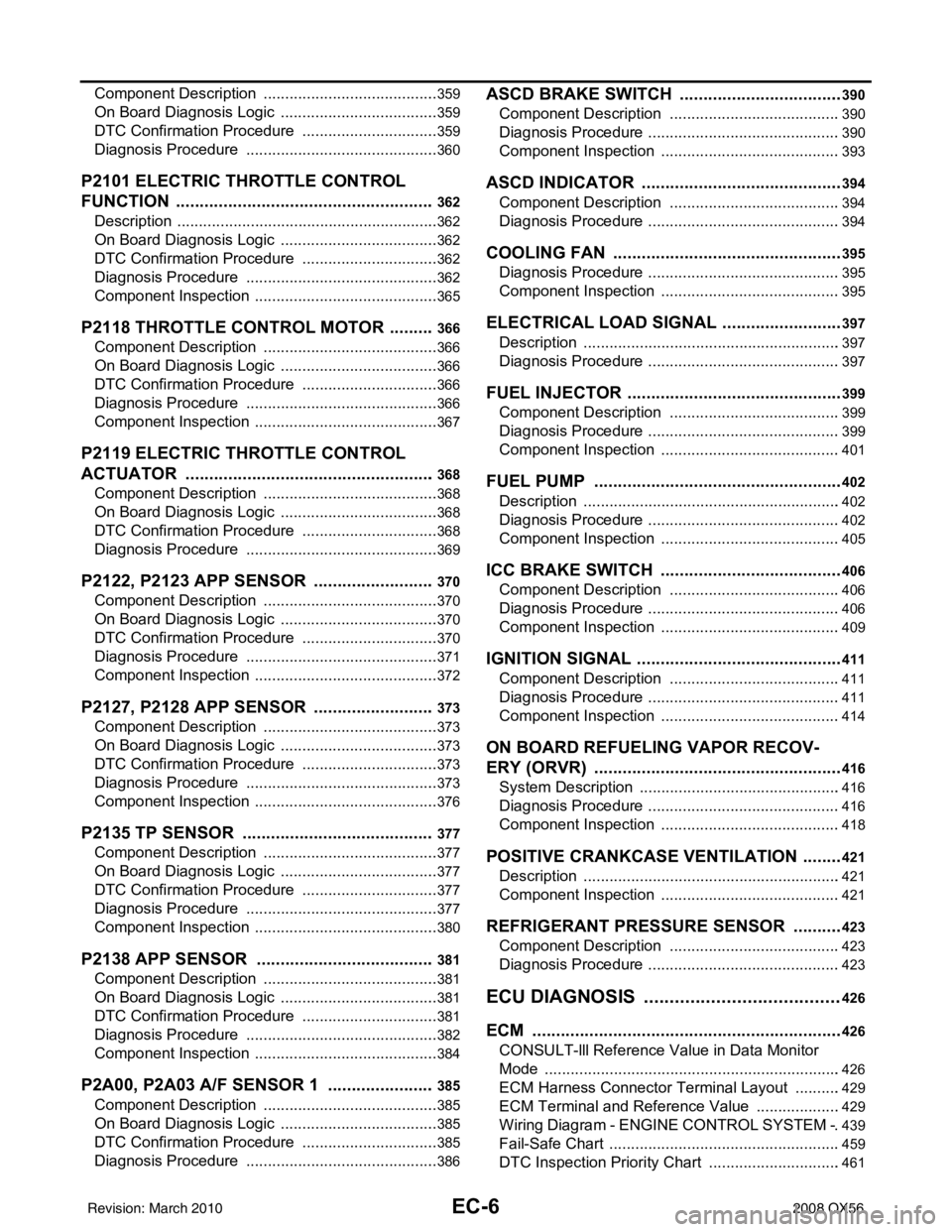
EC-6
Component Description .........................................359
On Board Diagnosis Logic .....................................359
DTC Confirmation Procedure ................................359
Diagnosis Procedure .............................................360
P2101 ELECTRIC THROTTLE CONTROL
FUNCTION .......................................................
362
Description ........................................................... ..362
On Board Diagnosis Logic .....................................362
DTC Confirmation Procedure ................................362
Diagnosis Procedure .............................................362
Component Inspection ...........................................365
P2118 THROTTLE CONTROL MOTOR ..........366
Component Description ....................................... ..366
On Board Diagnosis Logic .....................................366
DTC Confirmation Procedure ................................366
Diagnosis Procedure .............................................366
Component Inspection ...........................................367
P2119 ELECTRIC THROTTLE CONTROL
ACTUATOR .....................................................
368
Component Description ....................................... ..368
On Board Diagnosis Logic .....................................368
DTC Confirmation Procedure ................................368
Diagnosis Procedure .............................................369
P2122, P2123 APP SENSOR ..........................370
Component Description ....................................... ..370
On Board Diagnosis Logic .....................................370
DTC Confirmation Procedure ................................370
Diagnosis Procedure .............................................371
Component Inspection ...........................................372
P2127, P2128 APP SENSOR ..........................373
Component Description ....................................... ..373
On Board Diagnosis Logic .....................................373
DTC Confirmation Procedure ................................373
Diagnosis Procedure .............................................373
Component Inspection ...........................................376
P2135 TP SENSOR .........................................377
Component Description ....................................... ..377
On Board Diagnosis Logic .....................................377
DTC Confirmation Procedure ................................377
Diagnosis Procedure .............................................377
Component Inspection ...........................................380
P2138 APP SENSOR ......................................381
Component Description ....................................... ..381
On Board Diagnosis Logic .....................................381
DTC Confirmation Procedure ................................381
Diagnosis Procedure .............................................382
Component Inspection ...........................................384
P2A00, P2A03 A/F SENSOR 1 .......................385
Component Description ....................................... ..385
On Board Diagnosis Logic .....................................385
DTC Confirmation Procedure ................................385
Diagnosis Procedure .............................................386
ASCD BRAKE SWITCH ...................................390
Component Description ....................................... .390
Diagnosis Procedure .............................................390
Component Inspection ..........................................393
ASCD INDICATOR ...........................................394
Component Description ....................................... .394
Diagnosis Procedure .............................................394
COOLING FAN .................................................395
Diagnosis Procedure ............................................ .395
Component Inspection ..........................................395
ELECTRICAL LOAD SIGNAL ..........................397
Description ........................................................... .397
Diagnosis Procedure .............................................397
FUEL INJECTOR ..............................................399
Component Description ....................................... .399
Diagnosis Procedure .............................................399
Component Inspection ..........................................401
FUEL PUMP .....................................................402
Description ........................................................... .402
Diagnosis Procedure .............................................402
Component Inspection ..........................................405
ICC BRAKE SWITCH ..................................... ..406
Component Description ....................................... .406
Diagnosis Procedure .............................................406
Component Inspection ..........................................409
IGNITION SIGNAL ............................................411
Component Description ....................................... .411
Diagnosis Procedure .............................................411
Component Inspection ..........................................414
ON BOARD REFUELING VAPOR RECOV-
ERY (ORVR) .....................................................
416
System Description .............................................. .416
Diagnosis Procedure .............................................416
Component Inspection ..........................................418
POSITIVE CRANKCASE VENTILATION .........421
Description ........................................................... .421
Component Inspection ..........................................421
REFRIGERANT PRESSURE SENSOR ...........423
Component Description ....................................... .423
Diagnosis Procedure .............................................423
ECU DIAGNOSIS ......................................426
ECM ................................................................ ..426
CONSULT-lll Reference Value in Data Monitor
Mode .................................................................... .
426
ECM Harness Connector Terminal Layout ...........429
ECM Terminal and Reference Value ....................429
Wiring Diagram - ENGINE CONTROL SYSTEM - .439
Fail-Safe Chart ......................................................459
DTC Inspection Priority Chart ...............................461
Revision: March 2010 2008 QX56
Page 1306 of 4083
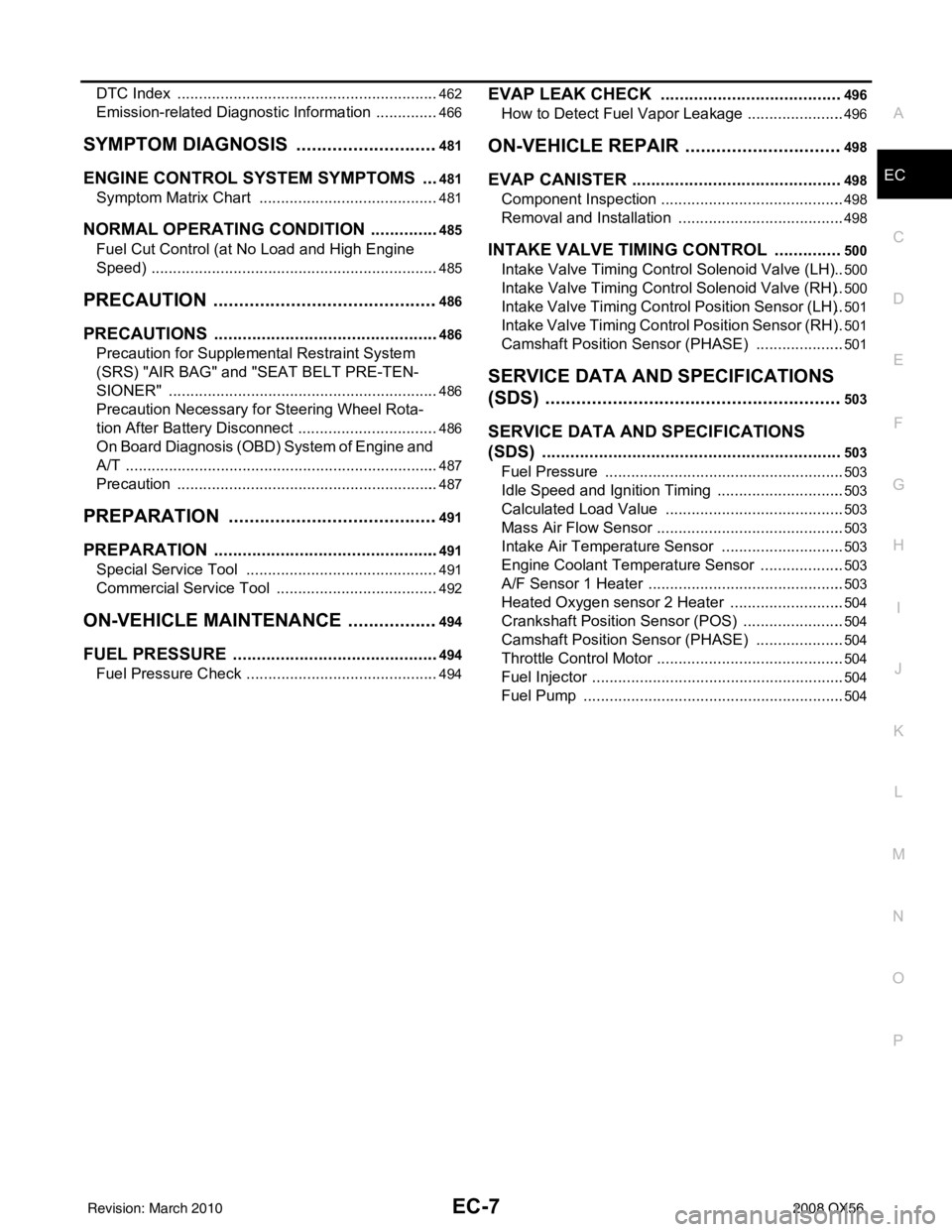
EC-7
C
DE
F
G H
I
J
K L
M
EC A
N
O P
DTC Index ...........................................................
..
462
Emission-related Diagnostic Information ...............466
SYMPTOM DIAGNOSIS ..... .......................481
ENGINE CONTROL SYSTEM SYMPTOMS .. ..481
Symptom Matrix Chart ........................................ ..481
NORMAL OPERATING CONDITION ...............485
Fuel Cut Control (at No Load and High Engine
Speed) ................................................................. ..
485
PRECAUTION ............................................486
PRECAUTIONS .............................................. ..486
Precaution for Supplemental Restraint System
(SRS) "AIR BAG" and "SEAT BELT PRE-TEN-
SIONER" ............................................................. ..
486
Precaution Necessary for Steering Wheel Rota-
tion After Battery Disconnect ............................... ..
486
On Board Diagnosis (OBD) System of Engine and
A/T .........................................................................
487
Precaution .............................................................487
PREPARATION .........................................491
PREPARATION .............................................. ..491
Special Service Tool ........................................... ..491
Commercial Service Tool ......................................492
ON-VEHICLE MAINTENANCE ..................494
FUEL PRESSURE .......................................... ..494
Fuel Pressure Check .............................................494
EVAP LEAK CHECK ......................................496
How to Detect Fuel Vapor Leakage ..................... ..496
ON-VEHICLE REPAIR ...............................498
EVAP CANISTER ............................................498
Component Inspection ......................................... ..498
Removal and Installation .......................................498
INTAKE VALVE TIMING CONTROL ..............500
Intake Valve Timing Control Solenoid Valve (LH) ..500
Intake Valve Timing Cont rol Solenoid Valve (RH) ..500
Intake Valve Timing Control Position Sensor (LH) ..501
Intake Valve Timing Control Position Sensor (RH) ..501
Camshaft Position Sensor (PHASE) .....................501
SERVICE DATA AND SPECIFICATIONS
(SDS) ............... .......................................... .
503
SERVICE DATA AND SPECIFICATIONS
(SDS) ...............................................................
503
Fuel Pressure ...................................................... ..503
Idle Speed and Ignition Timing ..............................503
Calculated Load Value ..........................................503
Mass Air Flow Sensor ............................................503
Intake Air Temperature Sensor .............................503
Engine Coolant Temperature Sensor ....................503
A/F Sensor 1 Heater ..............................................503
Heated Oxygen sensor 2 Heater ...........................504
Crankshaft Position Sensor (POS) ........................504
Camshaft Position Sensor (PHASE) .....................504
Throttle Control Motor ............................................504
Fuel Injector ...........................................................504
Fuel Pump .............................................................504
Revision: March 2010 2008 QX56
Page 1307 of 4083
![INFINITI QX56 2008 Factory Service Manual EC-8
< BASIC INSPECTION >[VK56DE]
DIAGNOSIS AND REPAIR WORKFLOW
BASIC INSPECTION
DIAGNOSIS AND REPAIR WORKFLOW
Trouble Diagnosis IntroductionINFOID:0000000001351337
INTRODUCTION
The engine has an ECM INFINITI QX56 2008 Factory Service Manual EC-8
< BASIC INSPECTION >[VK56DE]
DIAGNOSIS AND REPAIR WORKFLOW
BASIC INSPECTION
DIAGNOSIS AND REPAIR WORKFLOW
Trouble Diagnosis IntroductionINFOID:0000000001351337
INTRODUCTION
The engine has an ECM](/img/42/57030/w960_57030-1306.png)
EC-8
< BASIC INSPECTION >[VK56DE]
DIAGNOSIS AND REPAIR WORKFLOW
BASIC INSPECTION
DIAGNOSIS AND REPAIR WORKFLOW
Trouble Diagnosis IntroductionINFOID:0000000001351337
INTRODUCTION
The engine has an ECM to control major systems such as fuel con-
trol, ignition control, idle air control system, etc. The ECM accepts
input signals from sensors and instantly drives actuators. It is essen-
tial that both input and output signals are proper and stable. At the
same time, it is important that there are no malfunctions such as vac-
uum leaks, fouled spark plugs, or
other malfunctions with the engine.
It is much more difficult to diagnose an incident that occurs intermit-
tently rather than continuously. Most intermittent incidents are
caused by poor electric connections or improper wiring. In this case,
careful checking of suspected circuits may help prevent the replace-
ment of good parts.
A visual check only may not find the cause of the incidents. A road
test with CONSULT-III (or GST) or a circuit tester connected should
be performed. Follow the Work Flow on "WORK FLOW" .
Before undertaking actual checks, take a few minutes to talk with a
customer who approaches with a driveability complaint. The cus-
tomer can supply good information about such incidents, especially
intermittent ones. Find out what symptoms are present and under
what conditions they occur. A Di agnostic Worksheet like the example
on "Worksheet Sample" should be used.
Start your diagnosis by looking fo r conventional malfunctions first.
This will help troubleshoot driveability malfunctions on an electroni-
cally controlled engine vehicle.
WORK FLOW
MEF036D
SEF233G
SEF234G
Revision: March 2010 2008 QX56
Page 1313 of 4083
![INFINITI QX56 2008 Factory Service Manual EC-14
< BASIC INSPECTION >[VK56DE]
INSPECTION AND ADJUSTMENT
2. Rev engine (2,000 to 3,000 rpm) two or three times under no
load, then run engine at idle speed for about 1 minute.
3. Read idle speed i INFINITI QX56 2008 Factory Service Manual EC-14
< BASIC INSPECTION >[VK56DE]
INSPECTION AND ADJUSTMENT
2. Rev engine (2,000 to 3,000 rpm) two or three times under no
load, then run engine at idle speed for about 1 minute.
3. Read idle speed i](/img/42/57030/w960_57030-1312.png)
EC-14
< BASIC INSPECTION >[VK56DE]
INSPECTION AND ADJUSTMENT
2. Rev engine (2,000 to 3,000 rpm) two or three times under no
load, then run engine at idle speed for about 1 minute.
3. Read idle speed in “DATA MONITOR” mode with CONSULT-III. Refer to EC-17, "
Idle Speed and Ignition
Timing Check" .
Without CONSULT-III
1. Run engine at about 2,000 rpm for about 2 minutes under no load.
2. Rev engine (2,000 to 3,000 rpm) two or three times under no load, then run engine at idle speed for about
1 minute.
3. Check idle speed.
Refer to EC-17, "
Idle Speed and Ignition Timing Check" .
OK or NG
OK >> GO TO 10.
NG >> GO TO 4.
4.PERFORM ACCELERATOR PEDAL RE LEASED POSITION LEARNING
1. Stop engine.
2. Perform EC-18, "
Accelerator Pedal Released Position Learning" .
>> GO TO 5.
5.PERFORM THROTTLE VALVE CL OSED POSITION LEARNING
Perform EC-18, "
Throttle Valve Closed Position Learning" .
>> GO TO 6.
6.PERFORM IDLE AIR VOLUME LEARNING
Refer to EC-18, "
Idle Air Volume Learning" .
Is Idle Air Volume Lear ning carried out successfully?
Ye s o r N o
Ye s > > G O T O 7 .
No >> 1. Follow the instruction of Idle Air Volume Learning. 2. GO TO 4.
7.CHECK TARGET IDLE SPEED AGAIN
With CONSULT-III
1. Start engine and warm it up to normal operating temperature.
2. Read idle speed in “DATA MONITOR” mode with CONSULT-III. Refer to EC-17, "
Idle Speed and Ignition Timing Check" .
Without CONSULT-III
PBIA8513J
650 ± 50 rpm (in P or N position)
650 ± 50 rpm (in P or N position)
650 ± 50 rpm (in P or N position)
Revision: March 2010 2008 QX56
Page 1314 of 4083
![INFINITI QX56 2008 Factory Service Manual INSPECTION AND ADJUSTMENTEC-15
< BASIC INSPECTION > [VK56DE]
C
D
E
F
G H
I
J
K L
M A
EC
NP
O
1. Start engine and warm it up to normal operating temperature.
2. Check idle speed.
Refer to EC-17, "
Idl INFINITI QX56 2008 Factory Service Manual INSPECTION AND ADJUSTMENTEC-15
< BASIC INSPECTION > [VK56DE]
C
D
E
F
G H
I
J
K L
M A
EC
NP
O
1. Start engine and warm it up to normal operating temperature.
2. Check idle speed.
Refer to EC-17, "
Idl](/img/42/57030/w960_57030-1313.png)
INSPECTION AND ADJUSTMENTEC-15
< BASIC INSPECTION > [VK56DE]
C
D
E
F
G H
I
J
K L
M A
EC
NP
O
1. Start engine and warm it up to normal operating temperature.
2. Check idle speed.
Refer to EC-17, "
Idle Speed and Ignition Timing Check" .
OK or NG
OK >> GO TO 10.
NG >> GO TO 8.
8.DETECT MALFUNCTIONING PART
Check the following.
• Check camshaft position sensor (PHASE) and circuit. Refer to EC-211
.
• Check crankshaft position sensor (POS) and circuit. Refer to EC-207
.
OK or NG
OK >> GO TO 9.
NG >> 1. Repair or replace. 2. GO TO 4.
9.CHECK ECM FUNCTION
1. Substitute another known-good ECM to check ECM f unction. (ECM may be the cause of an incident, but
this is a rare case.)
2. Perform initialization of IVIS (NAT S) system and registration of all IVIS (NATS) ignition key IDs. Refer to
SEC-13, "
System Diagram".
>> GO TO 4.
10.CHECK IGNITION TIMING
1. Run engine at idle.
2. Check ignition timing with a timing light. Refer to EC-17, "
Idle Speed and Ignition Timing Check" .
OK or NG
OK >> GO TO 19.
NG >> GO TO 11.
11 .PERFORM ACCELERATOR PEDAL RELEASED POSITION LEARNING
1. Stop engine.
2. Perform EC-18, "
Accelerator Pedal Released Position Learning" .
>> GO TO 12.
12.PERFORM THROTTLE VALVE CLOSED POSITION LEARNING
Perform EC-18, "
Throttle Valve Closed Position Learning" .
>> GO TO 13.
13.PERFORM IDLE AIR VOLUME LEARNING
Refer to EC-18, "
Idle Air Volume Learning" .
Is Idle Air Volume Learning carried out successfully?
Ye s o r N o
Yes >> GO TO 14.
No >> 1. Follow the instruction of Idle Air Volume Learning. 650
± 50 rpm (in P or N position)
15 ± 5 ° BTDC (in P or N position)
BBIA0379E
Revision: March 2010 2008 QX56