service INFINITI QX56 2009 Factory Service Manual
[x] Cancel search | Manufacturer: INFINITI, Model Year: 2009, Model line: QX56, Model: INFINITI QX56 2009Pages: 4171, PDF Size: 84.65 MB
Page 3192 of 4171
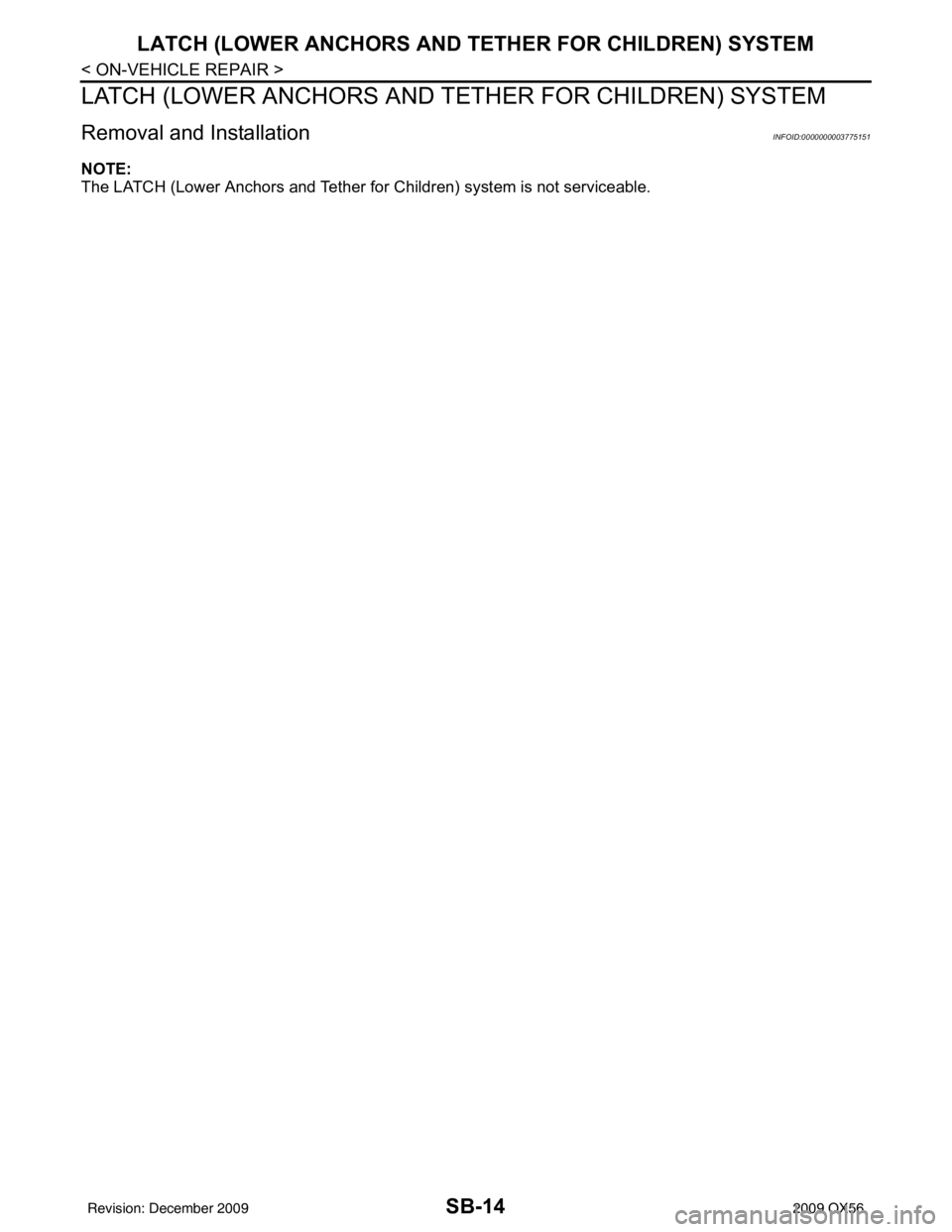
SB-14
< ON-VEHICLE REPAIR >
LATCH (LOWER ANCHORS AND TETHER FOR CHILDREN) SYSTEM
LATCH (LOWER ANCHORS AND TETHER FOR CHILDREN) SYSTEM
Removal and InstallationINFOID:0000000003775151
NOTE:
The LATCH (Lower Anchors and Tether for Children) system is not serviceable.
Revision: December 20092009 QX56
Page 3232 of 4171
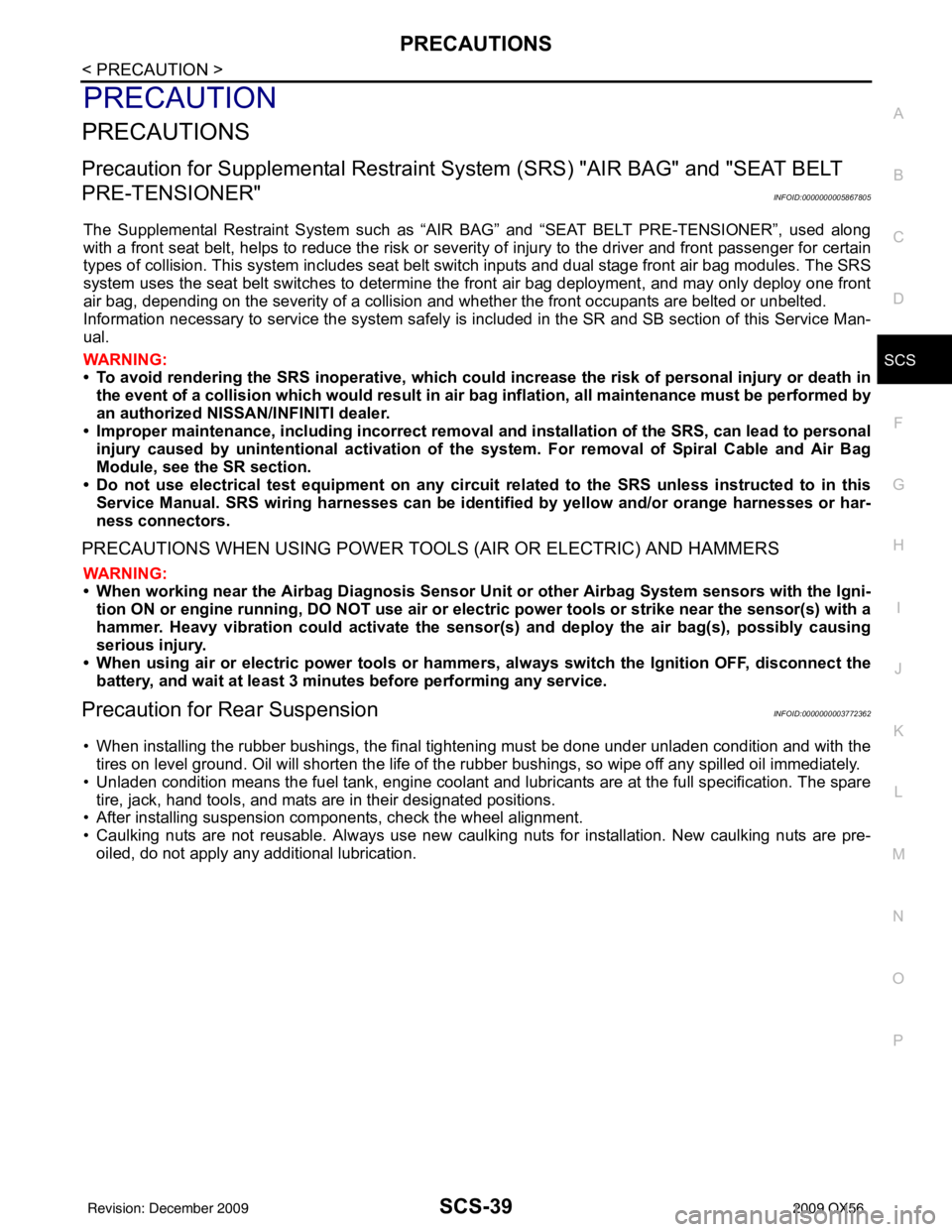
PRECAUTIONSSCS-39
< PRECAUTION >
C
DF
G H
I
J
K L
M A
B
SCS
N
O P
PRECAUTION
PRECAUTIONS
Precaution for Supplemental Restraint System (SRS) "AIR BAG" and "SEAT BELT
PRE-TENSIONER"
INFOID:0000000005867805
The Supplemental Restraint System such as “AIR BAG” and “SEAT BELT PRE-TENSIONER”, used along
with a front seat belt, helps to reduce the risk or severi ty of injury to the driver and front passenger for certain
types of collision. This system includes seat belt switch inputs and dual stage front air bag modules. The SRS
system uses the seat belt switches to determine the front air bag deployment, and may only deploy one front
air bag, depending on the severity of a collision and w hether the front occupants are belted or unbelted.
Information necessary to service the system safely is included in the SR and SB section of this Service Man-
ual.
WARNING:
• To avoid rendering the SRS inoper ative, which could increase the risk of personal injury or death in
the event of a collision which would result in air bag inflation, all maintenance must be performed by
an authorized NISSAN/INFINITI dealer.
• Improper maintenance, including in correct removal and installation of the SRS, can lead to personal
injury caused by unintentional act ivation of the system. For removal of Spiral Cable and Air Bag
Module, see the SR section.
• Do not use electrical test equipm ent on any circuit related to the SRS unless instructed to in this
Service Manual. SRS wiring harnesses can be identi fied by yellow and/or orange harnesses or har-
ness connectors.
PRECAUTIONS WHEN USING POWER TOOLS (AIR OR ELECTRIC) AND HAMMERS
WARNING:
• When working near the Airbag Diagnosis Sensor Un it or other Airbag System sensors with the Igni-
tion ON or engine running, DO NOT use air or el ectric power tools or strike near the sensor(s) with a
hammer. Heavy vibration could activate the sensor( s) and deploy the air bag(s), possibly causing
serious injury.
• When using air or electric power tools or hammers, always switch the Ignition OFF, disconnect the battery, and wait at least 3 minutes before performing any service.
Precaution for Rear SuspensionINFOID:0000000003772362
• When installing the rubber bushings, the final tightening must be done under unladen condition and with thetires on level ground. Oil will shorten the life of the rubber bushings, so wipe off any spilled oil immediately.
• Unladen condition means the fuel tank, engine coolant and lubricants are at the full specification. The spare tire, jack, hand tools, and mats are in their designated positions.
• After installing suspension components, check the wheel alignment.
• Caulking nuts are not reusable. Always use new caulking nuts for installation. New caulking nuts are pre-
oiled, do not apply any additional lubrication.
Revision: December 20092009 QX56
Page 3234 of 4171
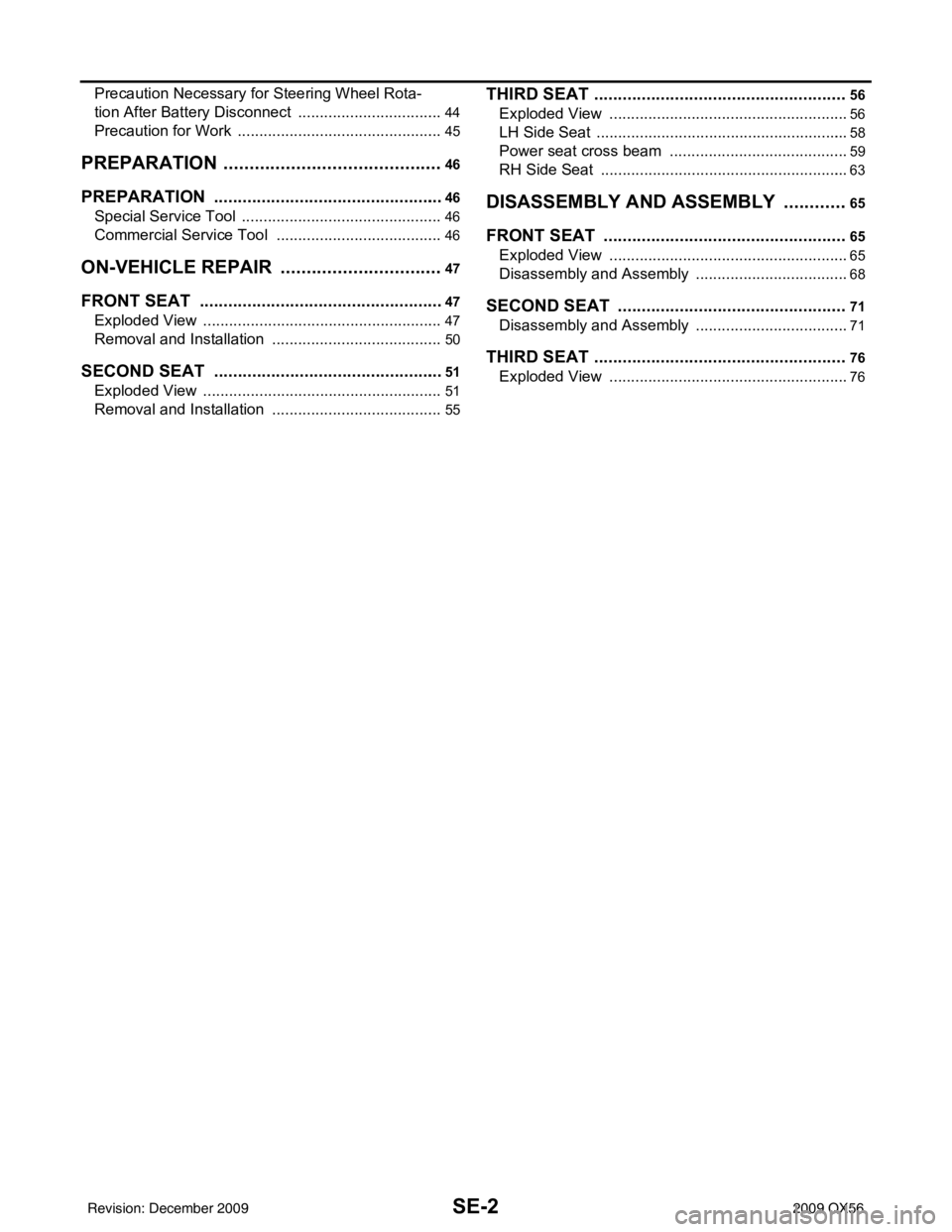
SE-2
Precaution Necessary for Steering Wheel Rota-
tion After Battery Disconnect ..................................
44
Precaution for Work ................................................45
PREPARATION ...........................................46
PREPARATION .............................................. ...46
Special Service Tool ............................................ ...46
Commercial Service Tool .......................................46
ON-VEHICLE REPAIR ................................47
FRONT SEAT ................................................. ...47
Exploded View ..................................................... ...47
Removal and Installation ........................................50
SECOND SEAT .................................................51
Exploded View ..................................................... ...51
Removal and Installation ........................................55
THIRD SEAT ......................................................56
Exploded View ..................................................... ...56
LH Side Seat ...........................................................58
Power seat cross beam ..........................................59
RH Side Seat ..........................................................63
DISASSEMBLY AND ASSEMBLY ............65
FRONT SEAT ................................................. ...65
Exploded View ..................................................... ...65
Disassembly and Assembly ....................................68
SECOND SEAT .................................................71
Disassembly and Assembly ................................. ...71
THIRD SEAT ......................................................76
Exploded View ..................................................... ...76
Revision: December 20092009 QX56
Page 3262 of 4171
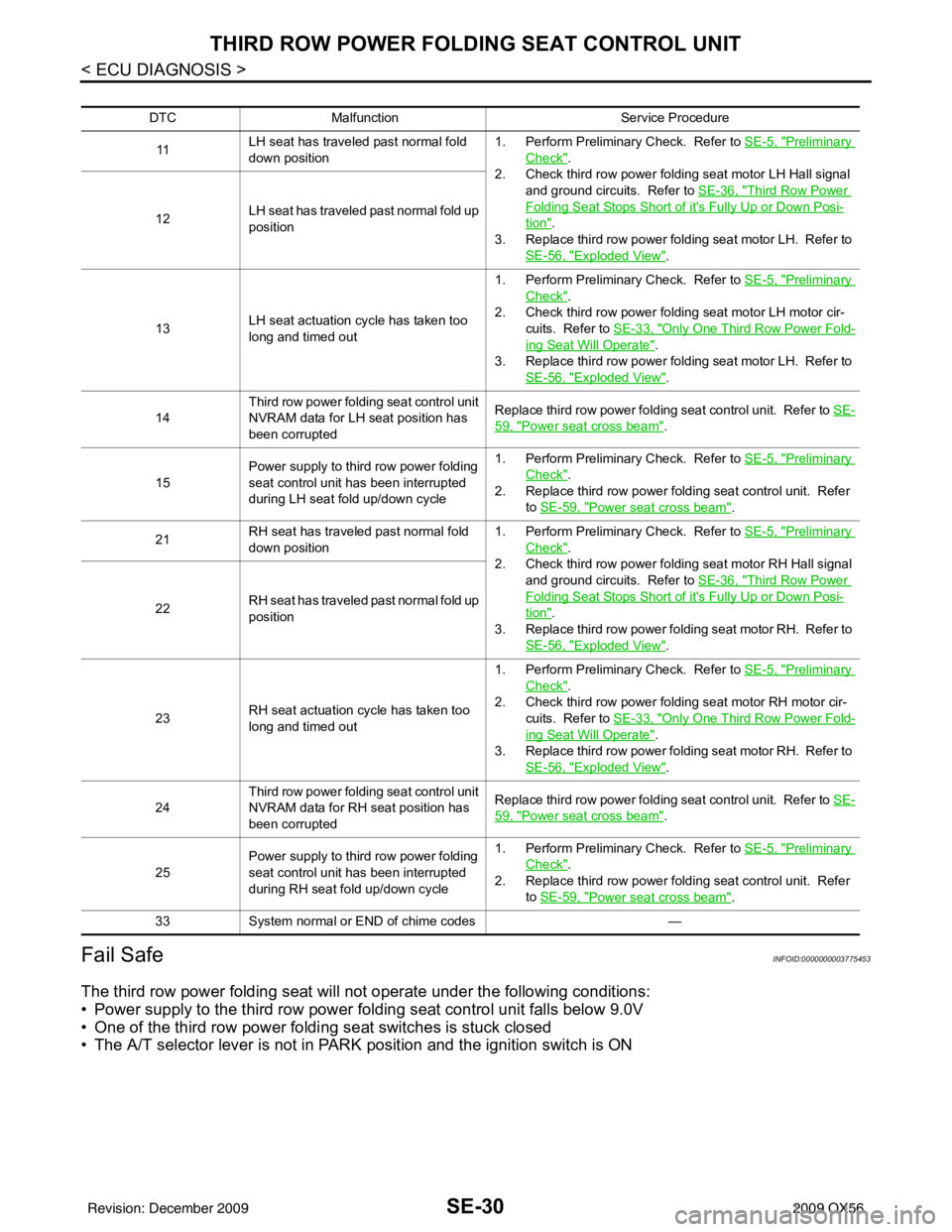
SE-30
< ECU DIAGNOSIS >
THIRD ROW POWER FOLDING SEAT CONTROL UNIT
Fail Safe
INFOID:0000000003775453
The third row power folding seat will not operate under the following conditions:
• Power supply to the third row power folding seat control unit falls below 9.0V
• One of the third row power foldi ng seat switches is stuck closed
• The A/T selector lever is not in PARK position and the ignition switch is ON
DTCMalfunction Service Procedure
11 LH seat has traveled past normal fold
down position 1. Perform Preliminary Check. Refer to
SE-5, "
Preliminary
Check".
2. Check third row power folding seat motor LH Hall signal and ground circuits. Refer to SE-36, "
Third Row Power
Folding Seat Stops Short of it's Fully Up or Down Posi-
tion".
3. Replace third row power folding seat motor LH. Refer to SE-56, "
Exploded View".
12
LH seat has traveled past normal fold up
position
13 LH seat actuation cycle has taken too
long and timed out 1. Perform Preliminary Check. Refer to
SE-5, "
Preliminary
Check".
2. Check third row power folding seat motor LH motor cir- cuits. Refer to SE-33, "
Only One Third Row Power Fold-
ing Seat Will Operate".
3. Replace third row power folding seat motor LH. Refer to SE-56, "
Exploded View".
14 Third row power folding seat control unit
NVRAM data for LH seat position has
been corrupted Replace third row power folding seat control unit. Refer to
SE-
59, "Power seat cross beam".
15 Power supply to thir
d row power folding
seat control unit has been interrupted
during LH seat fold up/down cycle 1. Perform Preliminary Check. Refer to
SE-5, "
Preliminary
Check".
2. Replace third row power folding seat control unit. Refer to SE-59, "
Power seat cross beam".
21 RH seat has traveled past normal fold
down position 1. Perform Preliminary Check. Refer to
SE-5, "
Preliminary
Check".
2. Check third row power folding seat motor RH Hall signal and ground circuits. Refer to SE-36, "
Third Row Power
Folding Seat Stops Short of it's Fully Up or Down Posi-
tion".
3. Replace third row power folding seat motor RH. Refer to SE-56, "
Exploded View".
22
RH seat has traveled past normal fold up
position
23 RH seat actuation cycle has taken too
long and timed out 1. Perform Preliminary Check. Refer to
SE-5, "
Preliminary
Check".
2. Check third row power folding seat motor RH motor cir- cuits. Refer to SE-33, "
Only One Third Row Power Fold-
ing Seat Will Operate".
3. Replace third row power folding seat motor RH. Refer to SE-56, "
Exploded View".
24 Third row power folding seat control unit
NVRAM data for RH seat position has
been corrupted Replace third row power folding seat control unit. Refer to
SE-
59, "Power seat cross beam".
25 Power supply to thir
d row power folding
seat control unit has been interrupted
during RH seat fold up/down cycle 1. Perform Preliminary Check. Refer to
SE-5, "
Preliminary
Check".
2. Replace third row power folding seat control unit. Refer
to SE-59, "
Power seat cross beam".
33 System normal or END of chime codes —
Revision: December 20092009 QX56
Page 3270 of 4171
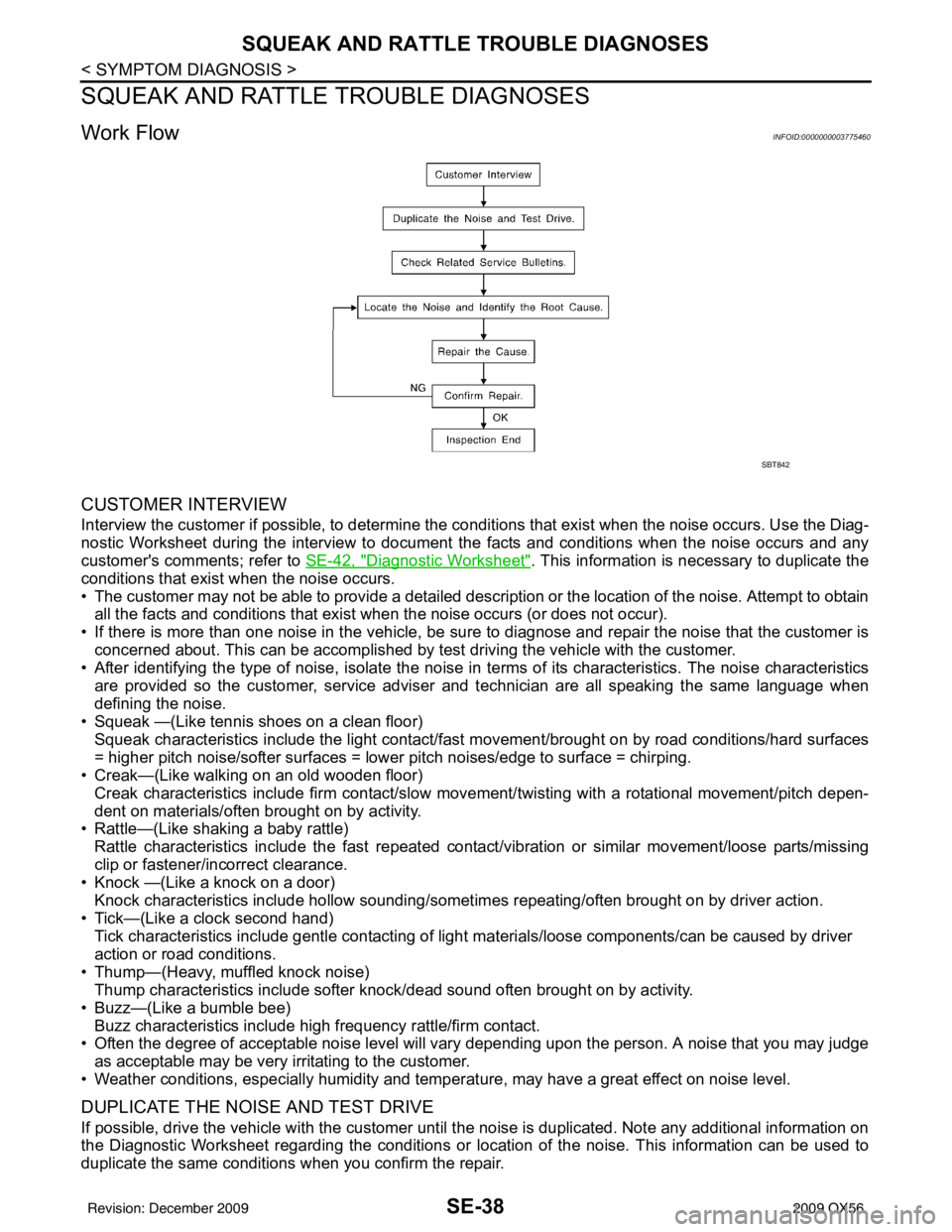
SE-38
< SYMPTOM DIAGNOSIS >
SQUEAK AND RATTLE TROUBLE DIAGNOSES
SQUEAK AND RATTLE TROUBLE DIAGNOSES
Work FlowINFOID:0000000003775460
CUSTOMER INTERVIEW
Interview the customer if possible, to determine the conditions that exist when the noise occurs. Use the Diag-
nostic Worksheet during the interview to document the facts and conditions when the noise occurs and any
customer's comments; refer to SE-42, "
Diagnostic Worksheet". This information is necessary to duplicate the
conditions that exist when the noise occurs.
• The customer may not be able to provide a detailed description or the location of the noise. Attempt to obtain all the facts and conditions that exist w hen the noise occurs (or does not occur).
• If there is more than one noise in the vehicle, be sure to diagnose and repair the noise that the customer is
concerned about. This can be accomplished by test driving the vehicle with the customer.
• After identifying the type of noise, isolate the noise in terms of its characteristics. The noise characteristics
are provided so the customer, service adviser and technician are all speaking the same language when
defining the noise.
• Squeak —(Like tennis shoes on a clean floor)
Squeak characteristics include the light contact/fast movement/brought on by road conditions/hard surfaces
= higher pitch noise/softer surfaces = lower pitch noises/edge to surface = chirping.
• Creak—(Like walking on an old wooden floor)
Creak characteristics include firm contact/slow mo vement/twisting with a rotational movement/pitch depen-
dent on materials/often brought on by activity.
• Rattle—(Like shaking a baby rattle)
Rattle characteristics include the fast repeated contac t/vibration or similar movement/loose parts/missing
clip or fastener/incorrect clearance.
• Knock —(Like a knock on a door)
Knock characteristics include hollow sounding/someti mes repeating/often brought on by driver action.
• Tick—(Like a clock second hand) Tick characteristics include gentle contacting of light materials/loose components/can be caused by driver
action or road conditions.
• Thump—(Heavy, muffled knock noise) Thump characteristics include softer k nock/dead sound often brought on by activity.
• Buzz—(Like a bumble bee)
Buzz characteristics include hi gh frequency rattle/firm contact.
• Often the degree of acceptable noise level will vary depending upon the person. A noise that you may judge as acceptable may be very irritating to the customer.
• Weather conditions, especially humidity and temperat ure, may have a great effect on noise level.
DUPLICATE THE NOISE AND TEST DRIVE
If possible, drive the vehicle with the customer until the noise is duplicated. Note any additional information on
the Diagnostic Worksheet regarding the conditions or lo cation of the noise. This information can be used to
duplicate the same conditions when you confirm the repair.
SBT842
Revision: December 20092009 QX56
Page 3271 of 4171
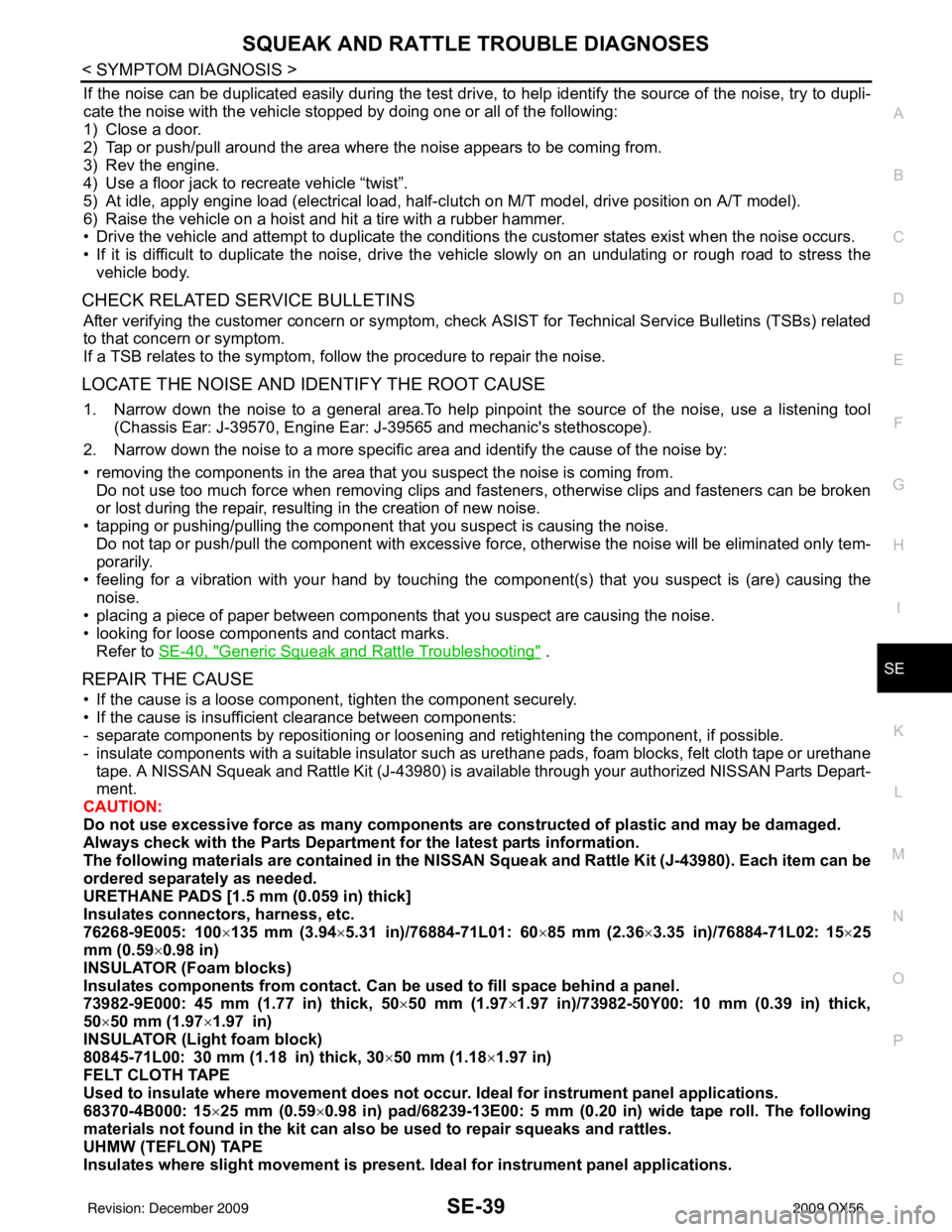
SQUEAK AND RATTLE TROUBLE DIAGNOSESSE-39
< SYMPTOM DIAGNOSIS >
C
DE
F
G H
I
K L
M A
B
SE
N
O P
If the noise can be duplicated easily during the test drive, to help identify the source of the noise, try to dupli-
cate the noise with the vehicle stopped by doing one or all of the following:
1) Close a door.
2) Tap or push/pull around the area where the noise appears to be coming from.
3) Rev the engine.
4) Use a floor jack to recreate vehicle “twist”.
5) At idle, apply engine load (electrical load, half- clutch on M/T model, drive position on A/T model).
6) Raise the vehicle on a hoist and hit a tire with a rubber hammer.
• Drive the vehicle and attempt to duplicate the conditions the customer states exist when the noise occurs.
• If it is difficult to duplicate the noise, drive the vehicle slowly on an undulating or rough road to stress the vehicle body.
CHECK RELATED SERVICE BULLETINS
After verifying the customer concern or symptom, check ASIST for Technical Service Bulletins (TSBs) related
to that concern or symptom.
If a TSB relates to the symptom, follow the procedure to repair the noise.
LOCATE THE NOISE AND IDENTIFY THE ROOT CAUSE
1. Narrow down the noise to a general area.To help pinpoint the source of the noise, use a listening tool (Chassis Ear: J-39570, Engine Ear: J-39565 and mechanic's stethoscope).
2. Narrow down the noise to a more specific area and identify the cause of the noise by:
• removing the components in the area that you suspect the noise is coming from. Do not use too much force when removing clips and fasteners, otherwise clips and fasteners can be broken
or lost during the repair, resulting in the creation of new noise.
• tapping or pushing/pulling the component that you suspect is causing the noise.
Do not tap or push/pull the component with excessive force, otherwise the noise will be eliminated only tem-
porarily.
• feeling for a vibration with your hand by touching the component(s) that you suspect is (are) causing the
noise.
• placing a piece of paper between components that you suspect are causing the noise.
• looking for loose components and contact marks. Refer to SE-40, "
Generic Squeak and Rattle Troubleshooting" .
REPAIR THE CAUSE
• If the cause is a loose component, tighten the component securely.
• If the cause is insufficient clearance between components:
- separate components by repositioning or loos ening and retightening the component, if possible.
- insulate components with a suitable insulator such as urethane pads, foam blocks, felt cloth tape or urethane tape. A NISSAN Squeak and Rattle Kit (J-43980) is available through your authorized NISSAN Parts Depart-
ment.
CAUTION:
Do not use excessive force as many components are constructed of plastic and may be damaged.
Always check with the Parts Department for the latest parts information.
The following materials are contained in the NISSAN Squeak and Rattle Kit (J-43980). Each item can be
ordered separately as needed.
URETHANE PADS [1.5 mm (0.059 in) thick]
Insulates connectors, harness, etc.
76268-9E005: 100 ×135 mm (3.94 ×5.31 in)/76884-71L01: 60 ×85 mm (2.36× 3.35 in)/76884-71L02: 15× 25
mm (0.59 ×0.98 in)
INSULATOR (Foam blocks)
Insulates components from contact. Can be used to fill space behind a panel.
73982-9E000: 45 mm (1.77 in) thick, 50× 50 mm (1.97×1.97 in)/73982-50Y00: 10 mm (0.39 in) thick,
50× 50 mm (1.97 ×1.97 in)
INSULATOR (Light foam block)
80845-71L00: 30 mm (1.18 in) thick, 30 ×50 mm (1.18 ×1.97 in)
FELT CLOTH TAPE
Used to insulate where movement does not occu r. Ideal for instrument panel applications.
68370-4B000: 15 ×25 mm (0.59 ×0.98 in) pad/68239-13E00: 5 mm (0.20 in) wide tape roll. The following
materials not found in the kit can also be used to repair squeaks and rattles.
UHMW (TEFLON) TAPE
Insulates where slight movement is present. Ideal for instrument panel applications.
Revision: December 20092009 QX56
Page 3276 of 4171
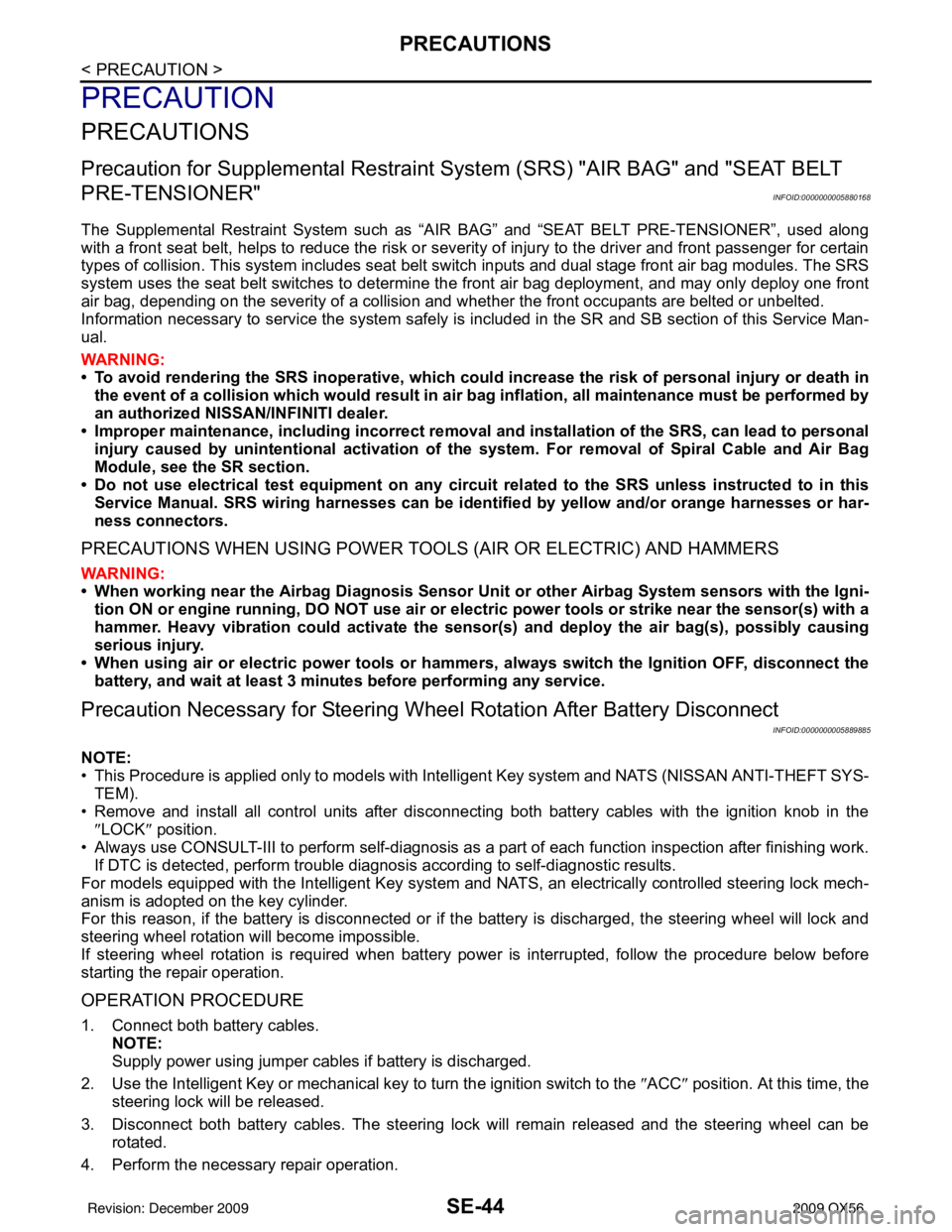
SE-44
< PRECAUTION >
PRECAUTIONS
PRECAUTION
PRECAUTIONS
Precaution for Supplemental Restraint System (SRS) "AIR BAG" and "SEAT BELT
PRE-TENSIONER"
INFOID:0000000005880168
The Supplemental Restraint System such as “A IR BAG” and “SEAT BELT PRE-TENSIONER”, used along
with a front seat belt, helps to reduce the risk or severity of injury to the driver and front passenger for certain
types of collision. This system includes seat belt switch inputs and dual stage front air bag modules. The SRS
system uses the seat belt switches to determine the front air bag deployment, and may only deploy one front
air bag, depending on the severity of a collision and w hether the front occupants are belted or unbelted.
Information necessary to service the system safely is included in the SR and SB section of this Service Man-
ual.
WARNING:
• To avoid rendering the SRS inopera tive, which could increase the risk of personal injury or death in
the event of a collision which would result in air bag inflation, all maintenance must be performed by
an authorized NISSAN/INFINITI dealer.
• Improper maintenance, including in correct removal and installation of the SRS, can lead to personal
injury caused by unintent ional activation of the system. For re moval of Spiral Cable and Air Bag
Module, see the SR section.
• Do not use electrical test equipmen t on any circuit related to the SRS unless instructed to in this
Service Manual. SRS wiring harn esses can be identified by yellow and/or orange harnesses or har-
ness connectors.
PRECAUTIONS WHEN USING POWER TOOLS (AIR OR ELECTRIC) AND HAMMERS
WARNING:
• When working near the Airbag Diagnosis Sensor Unit or other Airbag System sensors with the Igni-
tion ON or engine running, DO NOT use air or electri c power tools or strike near the sensor(s) with a
hammer. Heavy vibration could activate the sensor( s) and deploy the air bag(s), possibly causing
serious injury.
• When using air or electric power tools or hammers , always switch the Ignition OFF, disconnect the
battery, and wait at least 3 minu tes before performing any service.
Precaution Necessary for Steering W heel Rotation After Battery Disconnect
INFOID:0000000005889885
NOTE:
• This Procedure is applied only to models with Intelligent Key system and NATS (NISSAN ANTI-THEFT SYS-
TEM).
• Remove and install all control units after disconnecting both battery cables with the ignition knob in the
″LOCK ″ position.
• Always use CONSULT-III to perform self-diagnosis as a part of each function inspection after finishing work.
If DTC is detected, perform trouble diagnosis according to self-diagnostic results.
For models equipped with the Intelligent Key system and NATS, an electrically controlled steering lock mech-
anism is adopted on the key cylinder.
For this reason, if the battery is disconnected or if the battery is discharged, the steering wheel will lock and
steering wheel rotation will become impossible.
If steering wheel rotation is required when battery pow er is interrupted, follow the procedure below before
starting the repair operation.
OPERATION PROCEDURE
1. Connect both battery cables. NOTE:
Supply power using jumper cables if battery is discharged.
2. Use the Intelligent Key or mechanical key to turn the ignition switch to the ″ACC ″ position. At this time, the
steering lock will be released.
3. Disconnect both battery cables. The steering lock will remain released and the steering wheel can be rotated.
4. Perform the necessary repair operation.
Revision: December 20092009 QX56
Page 3278 of 4171
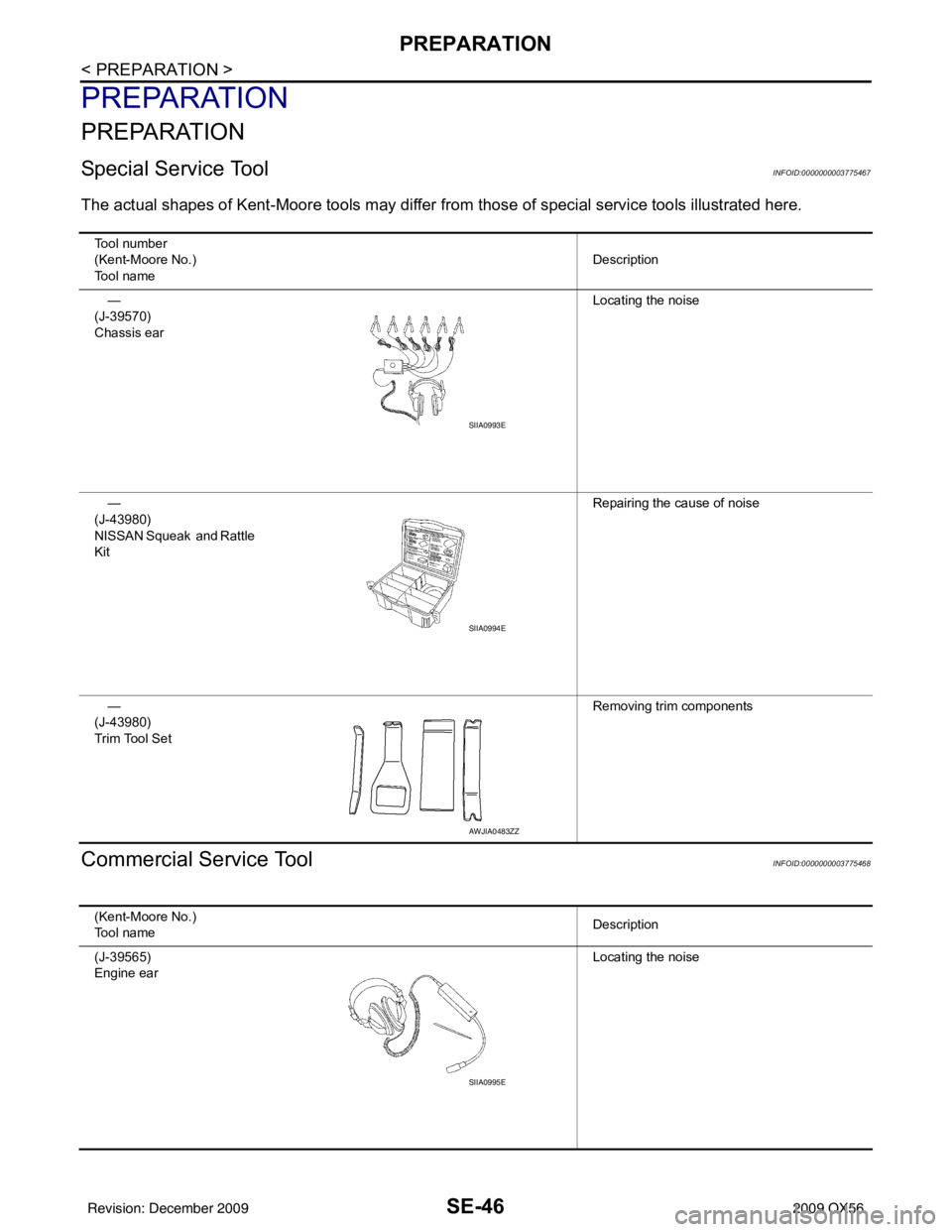
SE-46
< PREPARATION >
PREPARATION
PREPARATION
PREPARATION
Special Service ToolINFOID:0000000003775467
The actual shapes of Kent-Moore tools may differ from those of special service tools illustrated here.
Commercial Service ToolINFOID:0000000003775468
Tool number
(Kent-Moore No.)
Tool name Description
—
(J-39570)
Chassis ear Locating the noise
—
(J-43980)
NISSAN Squeak and Rattle
Kit Repairing the cause of noise
—
(J-43980)
Trim Tool Set Removing trim components
SIIA0993E
SIIA0994E
AWJIA0483ZZ
(Kent-Moore No.)
Tool name
Description
(J-39565)
Engine ear Locating the noise
SIIA0995E
Revision: December 20092009 QX56
Page 3311 of 4171
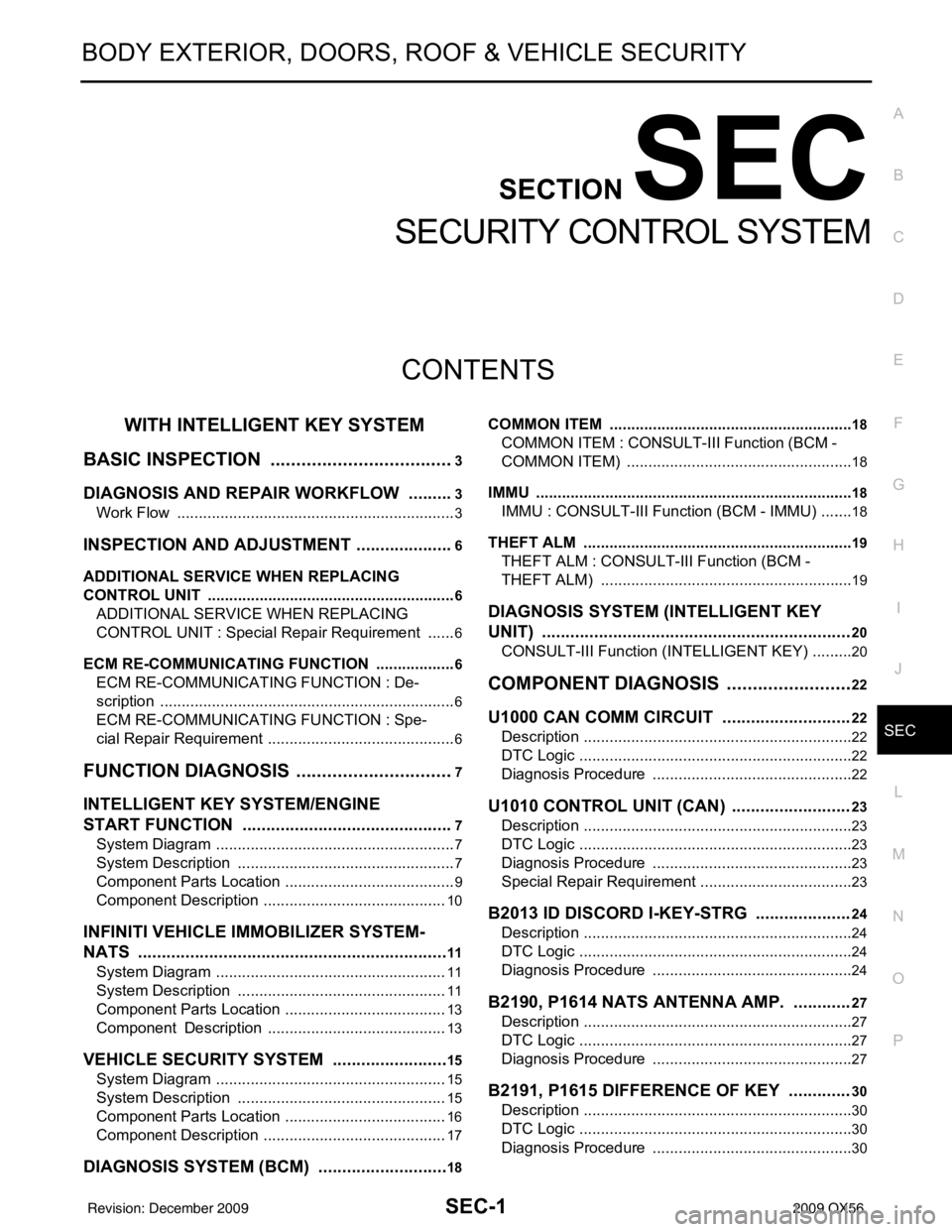
SEC-1
BODY EXTERIOR, DOORS, ROOF & VEHICLE SECURITY
C
DE
F
G H
I
J
L
M
SECTION SEC
A
B
SEC
N
O P
CONTENTS
SECURITY CONTROL SYSTEM
WITH INTELLIGENT KEY SYSTEM
BASIC INSPECTION ....... .............................
3
DIAGNOSIS AND REPAIR WORKFLOW ..... .....3
Work Flow ........................................................... ......3
INSPECTION AND ADJUSTMENT .....................6
ADDITIONAL SERVICE WHEN REPLACING
CONTROL UNIT .................................................... ......
6
ADDITIONAL SERVICE WHEN REPLACING
CONTROL UNIT : Special Repair Requirement .......
6
ECM RE-COMMUNICATING FUNCTION ............. ......6
ECM RE-COMMUNICATING FUNCTION : De-
scription .....................................................................
6
ECM RE-COMMUNICATING FUNCTION : Spe-
cial Repair Requirement ............................................
6
FUNCTION DIAGNOSIS ...............................7
INTELLIGENT KEY SYSTEM/ENGINE
START FUNCTIO N ........................................ .....
7
System Diagram .................................................. ......7
System Description ...................................................7
Component Parts Location ........................................9
Component Description ...........................................10
INFINITI VEHICLE IMMOBILIZER SYSTEM-
NATS ..................................................................
11
System Diagram .................................................. ....11
System Description .................................................11
Component Parts Location ......................................13
Component Description ..........................................13
VEHICLE SECURITY SYSTEM .........................15
System Diagram .................................................. ....15
System Description .................................................15
Component Parts Location ......................................16
Component Description ...........................................17
DIAGNOSIS SYSTEM (BCM) ............................18
COMMON ITEM ..................................................... ....18
COMMON ITEM : CONSULT-III Function (BCM -
COMMON ITEM) .....................................................
18
IMMU ...................................................................... ....18
IMMU : CONSULT-III Function (BCM - IMMU) ........18
THEFT ALM ........................................................... ....19
THEFT ALM : CONSULT-III Function (BCM -
THEFT ALM) ....................................................... ....
19
DIAGNOSIS SYSTEM (INTELLIGENT KEY
UNIT) .................................................................
20
CONSULT-III Function (INTELLIGENT KEY) ..........20
COMPONENT DIAGNOSIS .........................22
U1000 CAN COMM CIRCUIT ...........................22
Description ........................................................... ....22
DTC Logic ................................................................22
Diagnosis Procedure ...............................................22
U1010 CONTROL UNIT (CAN) .........................23
Description ...............................................................23
DTC Logic ................................................................23
Diagnosis Procedure ...............................................23
Special Repair Requirement ....................................23
B2013 ID DISCORD I-KEY-STRG ....................24
Description ...............................................................24
DTC Logic ................................................................24
Diagnosis Procedure ...............................................24
B2190, P1614 NATS ANTENNA AMP. ............27
Description ...............................................................27
DTC Logic ................................................................27
Diagnosis Procedure ...............................................27
B2191, P1615 DIFFERENCE OF KEY .............30
Description ...............................................................30
DTC Logic ................................................................30
Diagnosis Procedure ...............................................30
Revision: December 20092009 QX56
Page 3314 of 4171
![INFINITI QX56 2009 Factory Service Manual SEC-4
< BASIC INSPECTION >[WITH INTELLIGENT KEY SYSTEM]
DIAGNOSIS AND REPAIR WORKFLOW
1.GET INFORMATION FOR SYMPTOM
Get the detailed information from the customer about the symptom (the condition and INFINITI QX56 2009 Factory Service Manual SEC-4
< BASIC INSPECTION >[WITH INTELLIGENT KEY SYSTEM]
DIAGNOSIS AND REPAIR WORKFLOW
1.GET INFORMATION FOR SYMPTOM
Get the detailed information from the customer about the symptom (the condition and](/img/42/57031/w960_57031-3313.png)
SEC-4
< BASIC INSPECTION >[WITH INTELLIGENT KEY SYSTEM]
DIAGNOSIS AND REPAIR WORKFLOW
1.GET INFORMATION FOR SYMPTOM
Get the detailed information from the customer about the symptom (the condition and the environment when
the incident/malfunction occurred).
>> GO TO 2
2.CHECK DTC
1. Check DTC for Intelligent Key unit and BCM.
2. Perform the following procedure if DTC is displayed.
- Erase DTC.
- Study the relationship between the cause detected by DTC and the symptom described by the customer.
3. Check related service bulletins for information.
Is any symptom described and any DTC detected?
Symptom is described, DTC is displayed>>GO TO 3
Symptom is described, DTC is not displayed>>GO TO 4
Symptom is not described, DTC is displayed>>GO TO 5
3.CONFIRM THE SYMPTOM
Confirm the symptom described by the customer.
Connect CONSULT-III to the vehicle in “DATA MO NITOR” mode and check real-time diagnosis results.
Verify relation between the symptom and the condition when the symptom is detected.
>> GO TO 5
4.CONFIRM THE SYMPTOM
Confirm the symptom described by the customer.
Connect CONSULT-III to the vehicle in “DATA MO NITOR ” mode and check real-time diagnosis results.
Verify relation between the symptom and the condition when the symptom is detected.
>> GO TO 6
5.PERFORM DTC CONFIRMATION PROCEDURE
Perform DTC Confirmation Procedure for the display ed DTC, and then check that DTC is detected again.
If two or more DTCs are detected, refer to SEC-95, "
DTCInspectionPriorityChart" (Intelligent Key unit),
SEC-77, "
DTCInspectionPriorityChart" (BCM) and determine trouble diagnosis order.
Is DTC detected?
YES >> GO TO 8
NO >> Refer to GI-38, "
Intermittent Incident".
6.PERFORM BASIC INSPECTION
Perform Basic Inspection. Refer to SEC-107, "
Basic Inspection".
>> GO TO 7
7.DETECT MALFUNCTIONING SYSTEM BY SYMPTOM TABLE
Detect malfunctioning system according to Symptom Table based on the confirmed symptom in step 4.
>> GO TO 8
8.DETECT MALFUNCTIONING PART BY DIAGNOSTIC PROCEDURE
Inspect according to Diagnostic Procedure of the system.
NOTE:
The Diagnostic Procedure is described based on open circuit inspection. A short circuit inspection is also
required for the circuit check in the Diagnostic Procedure.
>> GO TO 9
Revision: December 20092009 QX56