torque INFINITI QX56 2010 Factory User Guide
[x] Cancel search | Manufacturer: INFINITI, Model Year: 2010, Model line: QX56, Model: INFINITI QX56 2010Pages: 4210, PDF Size: 81.91 MB
Page 484 of 4210
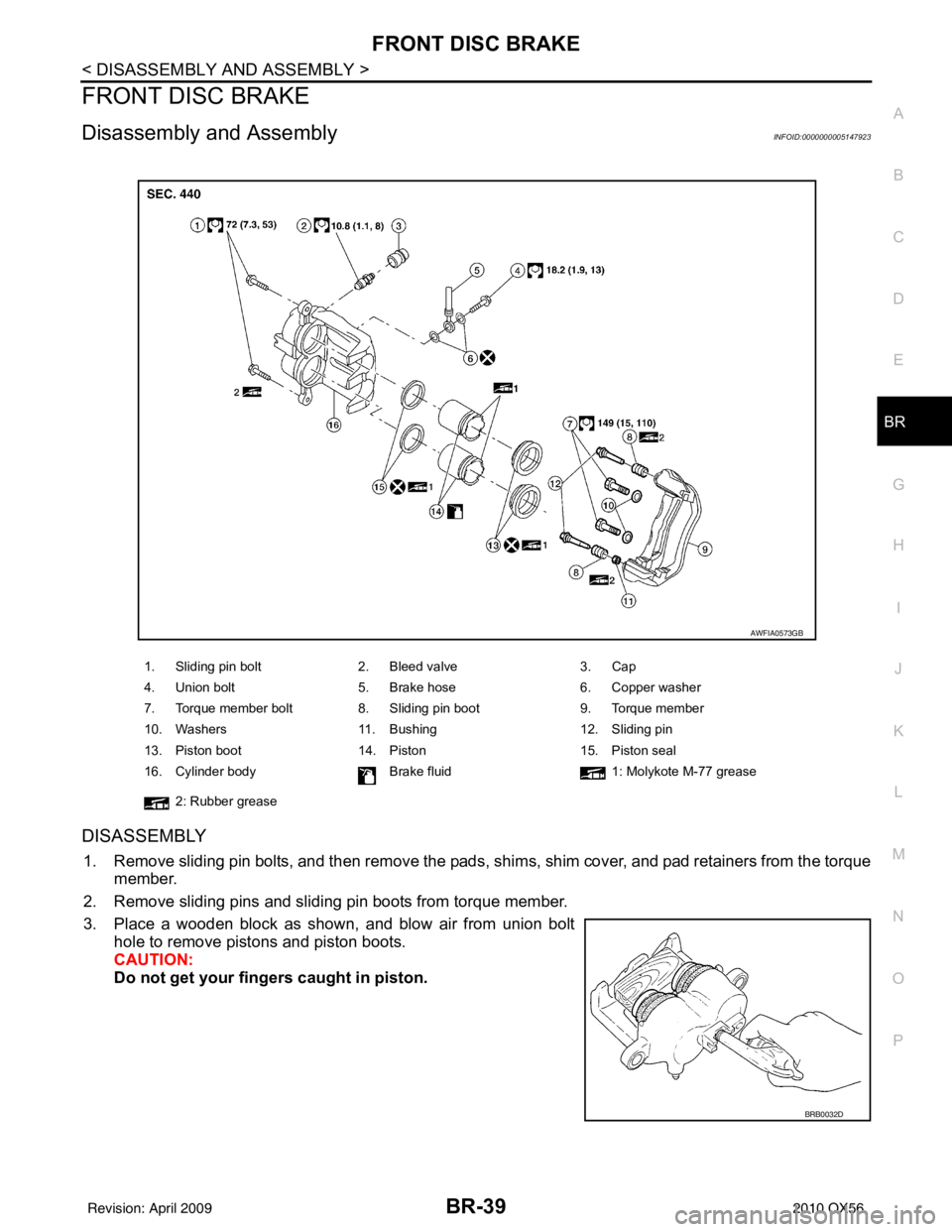
FRONT DISC BRAKEBR-39
< DISASSEMBLY AND ASSEMBLY >
C
DE
G H
I
J
K L
M A
B
BR
N
O P
FRONT DISC BRAKE
Disassembly and AssemblyINFOID:0000000005147923
DISASSEMBLY
1. Remove sliding pin bolts, and then remove the pads, sh ims, shim cover, and pad retainers from the torque
member.
2. Remove sliding pins and sliding pin boots from torque member.
3. Place a wooden block as shown, and blow air from union bolt hole to remove pistons and piston boots.
CAUTION:
Do not get your fingers caught in piston.
1. Sliding pin bolt 2. Bleed valve 3. Cap
4. Union bolt 5. Brake hose 6. Copper washer
7. Torque member bolt 8. Sliding pin boot 9. Torque member
10. Washers 11. Bushing 12. Sliding pin
13. Piston boot 14. Piston 15. Piston seal
16. Cylinder body Brake fluid1: Molykote M-77 grease
2: Rubber grease
AWFIA0573GB
BRB0032D
Revision: April 20092010 QX56
Page 485 of 4210
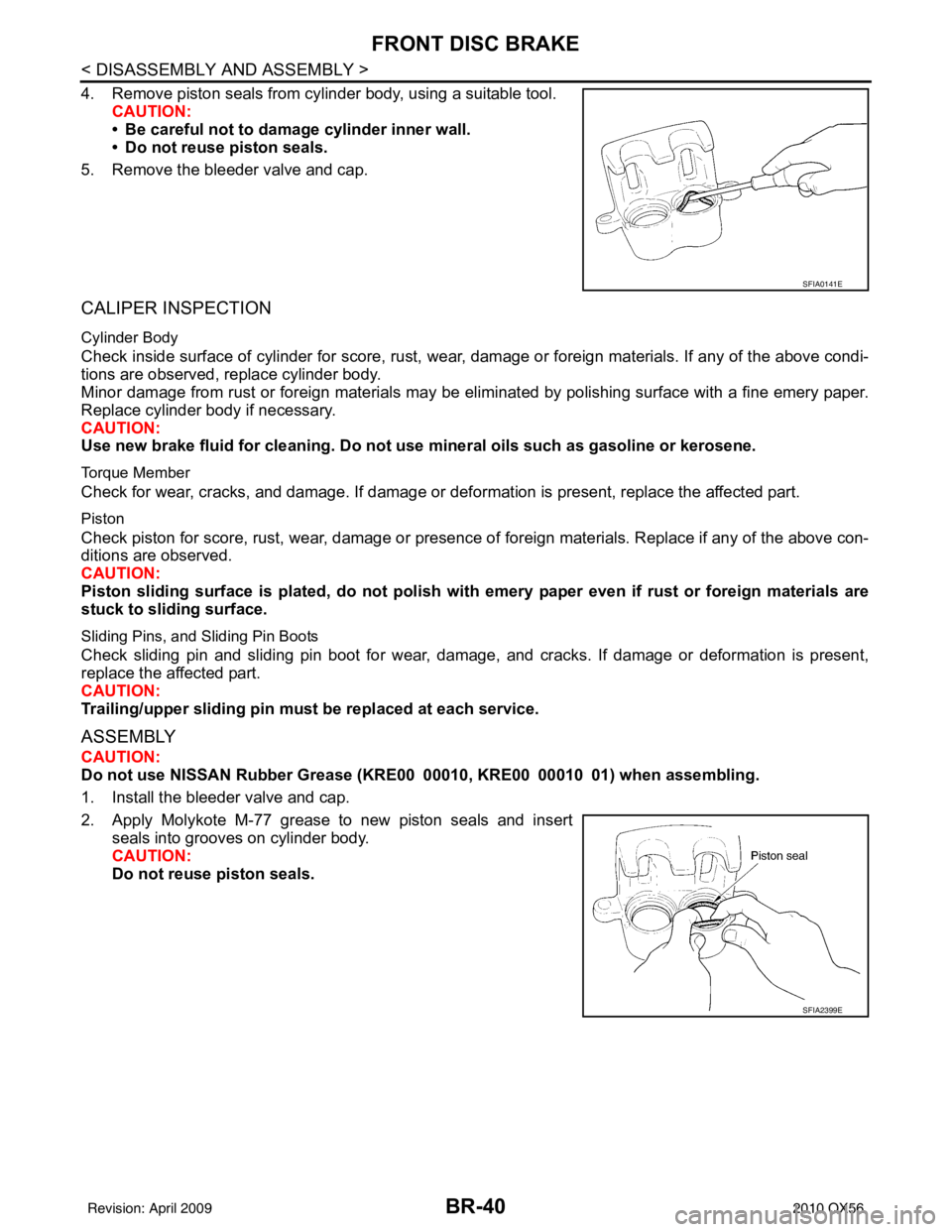
BR-40
< DISASSEMBLY AND ASSEMBLY >
FRONT DISC BRAKE
4. Remove piston seals from cylinder body, using a suitable tool.CAUTION:
• Be careful not to damage cylinder inner wall.
• Do not reuse piston seals.
5. Remove the bleeder valve and cap.
CALIPER INSPECTION
Cylinder Body
Check inside surface of cylinder for score, rust, wear, damage or foreign materials. If any of the above condi-
tions are observed, replace cylinder body.
Minor damage from rust or foreign materials may be el iminated by polishing surface with a fine emery paper.
Replace cylinder body if necessary.
CAUTION:
Use new brake fluid for cleaning. Do not use mineral oils such as gasoline or kerosene.
Torque Member
Check for wear, cracks, and damage. If damage or def ormation is present, replace the affected part.
Piston
Check piston for score, rust, wear, damage or presence of foreign materials. Replace if any of the above con-
ditions are observed.
CAUTION:
Piston sliding surface is plated, do not polish with emery paper even if rust or foreign materials are
stuck to sliding surface.
Sliding Pins, and Sliding Pin Boots
Check sliding pin and sliding pin boot for wear, damage, and cracks. If damage or deformation is present,
replace the affected part.
CAUTION:
Trailing/upper slidi ng pin must be replaced at each service.
ASSEMBLY
CAUTION:
Do not use NISSAN Rubber Grease ( KRE00 00010, KRE00 00010 01) when assembling.
1. Install the bleeder valve and cap.
2. Apply Molykote M-77 grease to new piston seals and insert seals into grooves on cylinder body.
CAUTION:
Do not reuse piston seals.
SFIA0141E
SFIA2399E
Revision: April 20092010 QX56
Page 486 of 4210
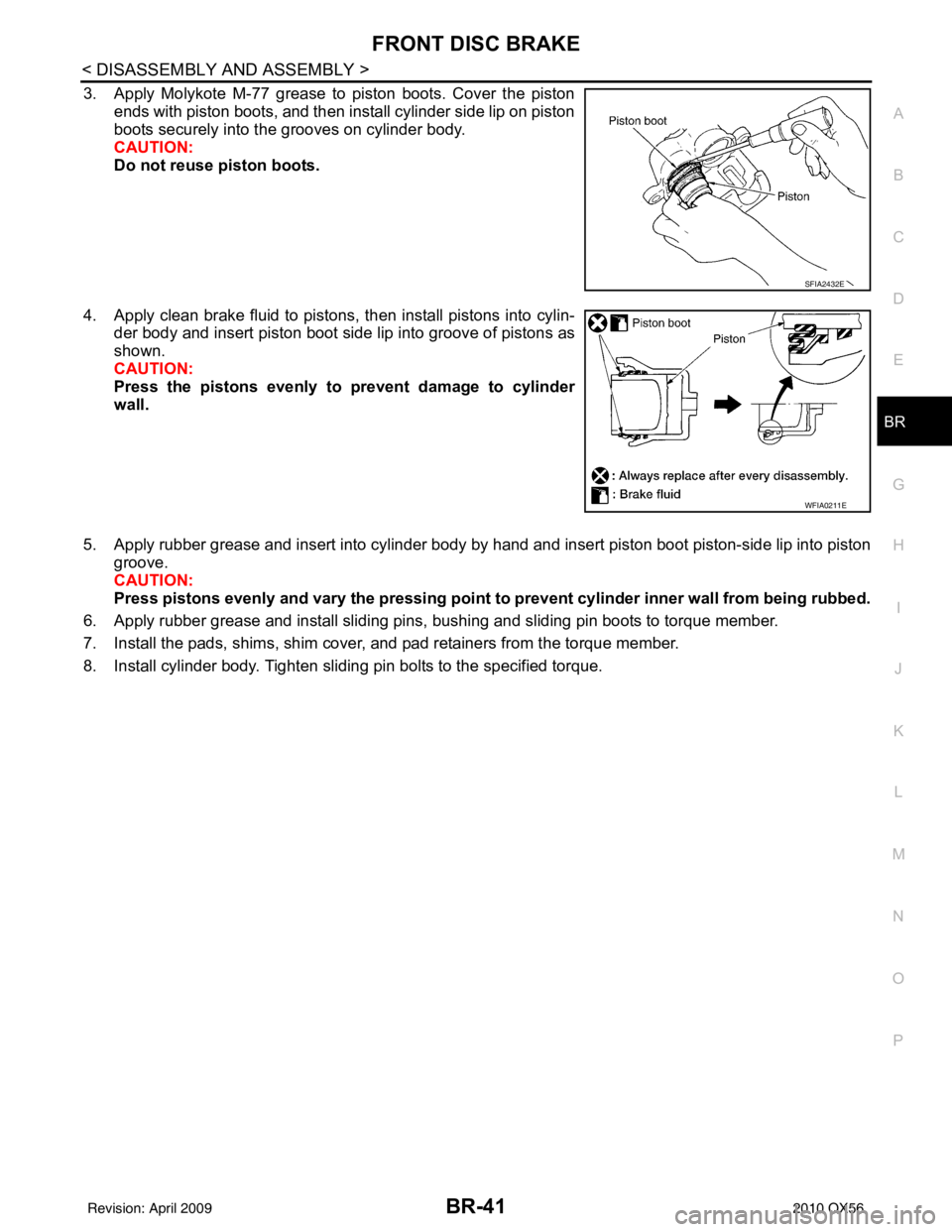
FRONT DISC BRAKEBR-41
< DISASSEMBLY AND ASSEMBLY >
C
DE
G H
I
J
K L
M A
B
BR
N
O P
3. Apply Molykote M-77 grease to piston boots. Cover the piston ends with piston boots, and then install cylinder side lip on piston
boots securely into the grooves on cylinder body.
CAUTION:
Do not reuse piston boots.
4. Apply clean brake fluid to pistons, then install pistons into cylin- der body and insert piston boot side lip into groove of pistons as
shown.
CAUTION:
Press the pistons evenly to prevent damage to cylinder
wall.
5. Apply rubber grease and insert into cylinder body by hand and insert piston bo\
ot piston-side lip into piston groove.
CAUTION:
Press pistons evenly and vary the pr essing point to prevent cylinder inner wall from being rubbed.
6. Apply rubber grease and install sliding pins, bushing and sliding pin boots to torque member.
7. Install the pads, shims, shim cover, and pad retainers from the torque member.
8. Install cylinder body. Tighten sliding pin bolts to the specified torque.
SFIA2432E
WFIA0211E
Revision: April 20092010 QX56
Page 488 of 4210
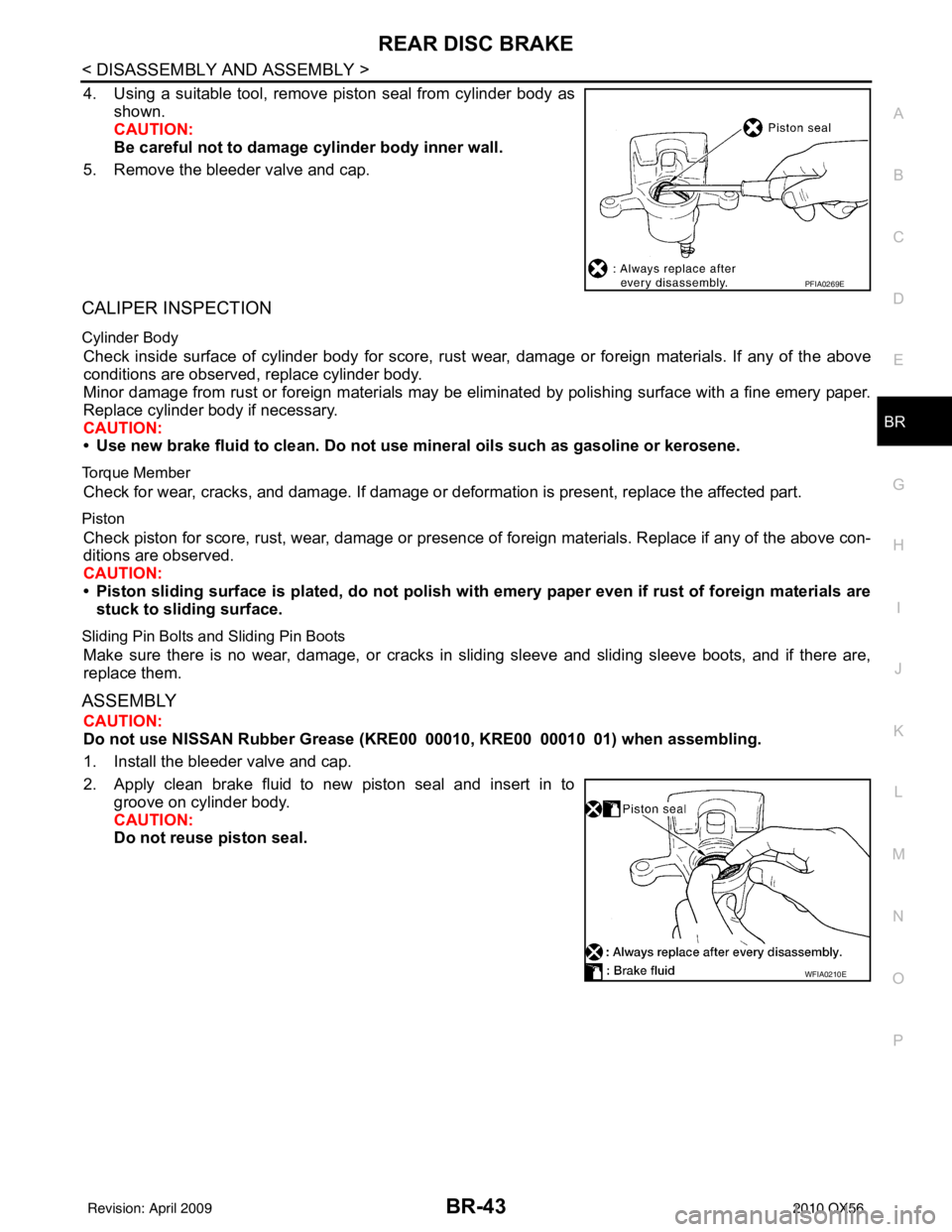
REAR DISC BRAKEBR-43
< DISASSEMBLY AND ASSEMBLY >
C
DE
G H
I
J
K L
M A
B
BR
N
O P
4. Using a suitable tool, remove piston seal from cylinder body as shown.
CAUTION:
Be careful not to damage cylinder body inner wall.
5. Remove the bleeder valve and cap.
CALIPER INSPECTION
Cylinder Body
Check inside surface of cylinder body for score, rust wear, damage or foreign materials. If any of the above
conditions are observed, replace cylinder body.
Minor damage from rust or foreign materials may be eliminated by polishing surface with a fine emery paper.
Replace cylinder body if necessary.
CAUTION:
• Use new brake fluid to clean. Do not use mi neral oils such as gasoline or kerosene.
Torque Member
Check for wear, cracks, and damage. If damage or deformation is present, replace the affected part.
Piston
Check piston for score, rust, wear, damage or presence of foreign materials. Replace if any of the above con-
ditions are observed.
CAUTION:
• Piston sliding surface is plated, do not polish with emery paper even if rust of foreign materials are
stuck to sliding surface.
Sliding Pin Bolts and Sliding Pin Boots
Make sure there is no wear, damage, or cracks in sliding sleeve and sliding sleeve boots, and if there are,
replace them.
ASSEMBLY
CAUTION:
Do not use NISSAN Rubber Grease ( KRE00 00010, KRE00 00010 01) when assembling.
1. Install the bleeder valve and cap.
2. Apply clean brake fluid to new piston seal and insert in to groove on cylinder body.
CAUTION:
Do not reuse piston seal.
PFIA0269E
WFIA0210E
Revision: April 20092010 QX56
Page 506 of 4210
![INFINITI QX56 2010 Factory User Guide BRC-14
< FUNCTION DIAGNOSIS >[VDC/TCS/ABS]
TCS
TCS
System DiagramINFOID:0000000005147950
System DescriptionINFOID:0000000005147951
• Traction Control System is a function that electronically control INFINITI QX56 2010 Factory User Guide BRC-14
< FUNCTION DIAGNOSIS >[VDC/TCS/ABS]
TCS
TCS
System DiagramINFOID:0000000005147950
System DescriptionINFOID:0000000005147951
• Traction Control System is a function that electronically control](/img/42/57032/w960_57032-505.png)
BRC-14
< FUNCTION DIAGNOSIS >[VDC/TCS/ABS]
TCS
TCS
System DiagramINFOID:0000000005147950
System DescriptionINFOID:0000000005147951
• Traction Control System is a function that electronically controls engine torque, brake fluid pressure and A/T
gear position to ensure the optimum slippage ratio at drive wheels by computing wheel speed signals from 4
wheel sensors. When ABS actuator and electric unit (control unit) detects a spin at drive wheels (rear
wheels), it compares wheel speed signals from all 4 wheels. At this time, LH and RH rear brake fluid pres-
sure are controlled, while fuel being cut to engine and throttle valve being closed to reduce engine torque by
the control unit. Further more, throttle position is continuously controlled to ensure the optimum engine
torque at all times.
• During TCS operation, it informs driver of syst em operation by flashing SLIP indicator lamp.
• Electrical system diagnosis by CONSULT-III is available.
AWFIA0065GB
Revision: April 20092010 QX56
Page 603 of 4210
![INFINITI QX56 2010 Factory User Guide PRECAUTIONSBRC-111
< PRECAUTION > [VDC/TCS/ABS]
C
D
E
G H
I
J
K L
M A
B
BRC
N
O P
5. When the repair work is completed, return the ignition switch to the ″LOCK ″ position before connecting
the ba INFINITI QX56 2010 Factory User Guide PRECAUTIONSBRC-111
< PRECAUTION > [VDC/TCS/ABS]
C
D
E
G H
I
J
K L
M A
B
BRC
N
O P
5. When the repair work is completed, return the ignition switch to the ″LOCK ″ position before connecting
the ba](/img/42/57032/w960_57032-602.png)
PRECAUTIONSBRC-111
< PRECAUTION > [VDC/TCS/ABS]
C
D
E
G H
I
J
K L
M A
B
BRC
N
O P
5. When the repair work is completed, return the ignition switch to the ″LOCK ″ position before connecting
the battery cables. (At this time, the steering lock mechanism will engage.)
6. Perform a self-diagnosis check of al l control units using CONSULT-III.
Precaution for Brake SystemINFOID:0000000005148094
CAUTION:
• Always use recommended brake fluid. Refer to MA-13, "
Fluids and Lubricants".
• Never reuse drained brake fluid.
• Be careful not to splash brake fluid on painted areas; it may cause paint damage. If brake fluid is
splashed on painted areas, wash it away with water immediately.
• To clean or wash all parts of master cylin der and disc brake caliper, use clean brake fluid.
• Never use mineral oils such as gasoline or kerosen e. They will ruin rubber parts of the hydraulic sys-
tem.
• Use flare nut wrench when removing and installing brake
tube.
• If a brake fluid leak is found, the part must be disassembled
without fail. Then it has to be replaced with a new one if a
defect exists.
• Turn the ignition switch OFF and remove the connector of the ABS actuator and electric unit (con trol unit) or the battery ter-
minal before performing the work.
• Always torque brake lines when installing.
• Burnish the brake contact surf aces after refinishing or replac-
ing rotors, after replacing pads, or if a soft pedal occurs at
very low mileage.
Refer to BR-30, "
Brake Burnishing Procedure" (front disc brake) or BR-35, "Brake Burnishing Proce-
dure" (rear disc brake).
WARNING:
• Clean brake pads and shoes with a waste cl oth, then wipe with a dust collector.
Precaution for Brake ControlINFOID:0000000005148095
• During ABS operation, the brake pedal may vibrate lightly and a mechanical noise may be heard. This is
normal.
• Just after starting vehicle, the brake pedal may vibrate or a motor operating noise may be heard from engine
compartment. This is a normal status of operation check.
• Stopping distance may be longer than that of vehicles without ABS when vehicle drives on rough, gravel, or snow-covered (fresh, deep snow) roads.
• When an error is indicated by ABS or another warning lamp, collect all necessary information from customer (what symptoms are present under what conditions) and check for simple causes before starting diagnosis.
Besides electrical system inspection, check boos ter operation, brake fluid level, and fluid leaks.
• If incorrect tire sizes or types are installed on the vehicle or brake pads are not Genuine NISSAN parts, stop-
ping distance or steering stability may deteriorate.
• If there is a radio, antenna or related wiring near control module, ABS function may have a malfunction or
error.
• If aftermarket parts (car stereo, CD player, etc.) have been installed, check for incidents such as harness pinches, open circuits or improper wiring.
• If the following components are replaced with non-genuine components or modified, the VDC OFF indicator lamp and SLIP indicator lamp may turn on or the VDC system may not operate properly. Components
related to suspension (shock absorbers, struts, springs , bushings, etc.), tires, wheels (exclude specified
size), components related to brake system (pads, roto rs, calipers, etc.), components related to engine (muf-
fler, ECM, etc.), components related to body reinforcement (roll bar, tower bar, etc.).
• Driving with broken or excessively worn suspensi on components, tires or brake system components may
cause the VDC OFF indicator lamp and the SLIP indicator lamp to turn on, and the VDC system may not
operate properly.
• When the TCS or VDC is activated by sudden acceleration or sudden turn, some noise may occur. The noise is a result of the normal operation of the TCS and VDC.
• When driving on roads which have extreme slopes (such as mountainous roads) or high banks (such as sharp curves on a freeway), the VDC may not operate no rmally, or the VDC warning lamp and the SLIP indi-
cator lamp may turn on. This is not a problem if normal operation can be resumed after restarting the engine.
SBR686C
Revision: April 20092010 QX56
Page 605 of 4210
![INFINITI QX56 2010 Factory User Guide PREPARATIONBRC-113
< PREPARATION > [VDC/TCS/ABS]
C
D
E
G H
I
J
K L
M A
B
BRC
N
O P
PREPARATION
PREPARATION
Special Service ToolINFOID:0000000005148097
The actual shapes of Kent-Moore tools may differ INFINITI QX56 2010 Factory User Guide PREPARATIONBRC-113
< PREPARATION > [VDC/TCS/ABS]
C
D
E
G H
I
J
K L
M A
B
BRC
N
O P
PREPARATION
PREPARATION
Special Service ToolINFOID:0000000005148097
The actual shapes of Kent-Moore tools may differ](/img/42/57032/w960_57032-604.png)
PREPARATIONBRC-113
< PREPARATION > [VDC/TCS/ABS]
C
D
E
G H
I
J
K L
M A
B
BRC
N
O P
PREPARATION
PREPARATION
Special Service ToolINFOID:0000000005148097
The actual shapes of Kent-Moore tools may differ from those of special service tools illustrated here.
Commercial Service ToolINFOID:0000000005148098
Tool number
(Kent-Moore No.)
Tool name Description
KV991J0080
(J-45741)
ABS active wheel sensor tester Checking operation of ABS active wheel sen-
sors
WFIA0101E
Tool name
Description
1. Flare nut crowfoot
2. Torque wrench Removing and installing brake piping
a: 10 mm (0.39 in)/12 mm (0.47 in)
S-NT360
Revision: April 20092010 QX56
Page 608 of 4210
![INFINITI QX56 2010 Factory User Guide BRC-116
< REMOVAL AND INSTALLATION >[VDC/TCS/ABS]
ACTUATOR AND ELECTRIC UNIT (ASSEMBLY)
ACTUATOR AND ELECTRIC UNIT (ASSEMBLY)
Removal and InstallationINFOID:0000000005148101
REMOVAL
1. Disconnect the INFINITI QX56 2010 Factory User Guide BRC-116
< REMOVAL AND INSTALLATION >[VDC/TCS/ABS]
ACTUATOR AND ELECTRIC UNIT (ASSEMBLY)
ACTUATOR AND ELECTRIC UNIT (ASSEMBLY)
Removal and InstallationINFOID:0000000005148101
REMOVAL
1. Disconnect the](/img/42/57032/w960_57032-607.png)
BRC-116
< REMOVAL AND INSTALLATION >[VDC/TCS/ABS]
ACTUATOR AND ELECTRIC UNIT (ASSEMBLY)
ACTUATOR AND ELECTRIC UNIT (ASSEMBLY)
Removal and InstallationINFOID:0000000005148101
REMOVAL
1. Disconnect the battery negative terminal. Refer to
PG-74, "Removal and Installation".
2. Remove the air cleaner and air duct assembly. Refer to EM-25, "
Removal and Installation".
3. Drain the brake fluid. Refer to BR-17, "
Drain and Refill".
4. Disconnect the actuator harness connector from t he ABS actuator and electric unit (control unit).
CAUTION:
• To remove the brake tubes, use a flare nut wrench to prevent the flare nuts and brake tubes from
being damaged.
• Be careful not to splash brake fluid on painted areas; it may cause paint damage. If brake fluid is splashed on painted areas, wash it away with water immediately.
5. Disconnect the brake tubes.
6. Remove the three bolts and remove the ABS actuator and electric unit (control unit).
INSTALLATION
Installation is in the reverse order of removal.
CAUTION:
• To install, use a flare nut crowfoot and torque wrench (commercial service tools).
1. To rear left caliper
16.2 N·m (1.7 kg-m, 12 ft-lb) 2. To rear right caliper
16.2 N·m (1.7 kg-m, 12 ft-lb) 3. To front left caliper
16.2 N·m (1.7 kg-m, 12 ft-lb)
4. To front right caliper 16.2 N·m (1.7 kg-m, 12 ft-lb) 5. From the master cylinder secondary side
18.2 N·m (1.9 kg-m, 13 ft-lb) 6. From the master cylinder primary side
18.2 N·m (1.9 kg-m, 13 ft-lb)
7. ABS actuator and electric unit (control unit) 8. Actuator harness connector
WFIA0375E
Revision: April 20092010 QX56
Page 650 of 4210
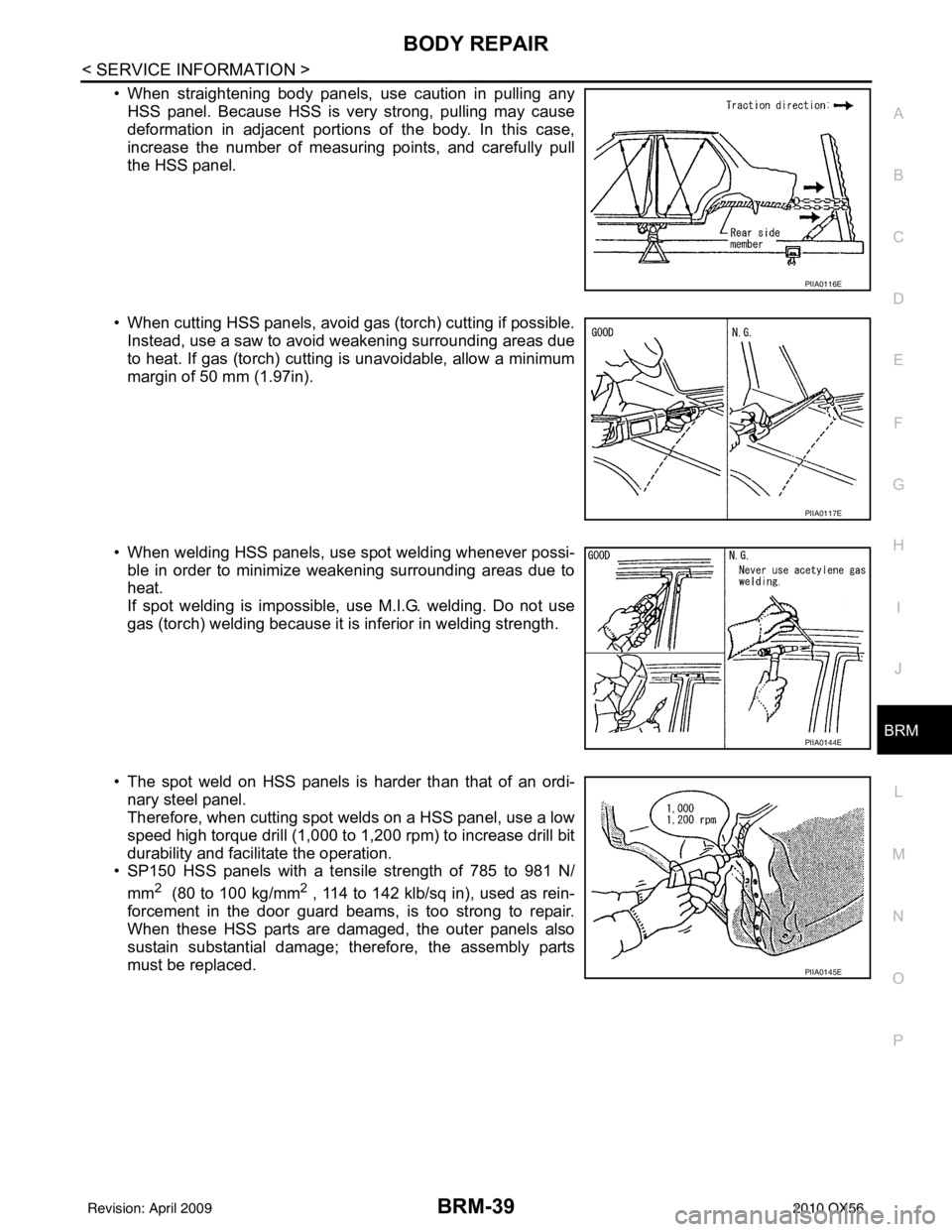
BODY REPAIRBRM-39
< SERVICE INFORMATION >
C
DE
F
G H
I
J
L
M A
B
BRM
N
O P
• When straightening body panels, use caution in pulling any HSS panel. Because HSS is very strong, pulling may cause
deformation in adjacent portions of the body. In this case,
increase the number of measuring points, and carefully pull
the HSS panel.
• When cutting HSS panels, avoid gas (torch) cutting if possible. Instead, use a saw to avoid weakening surrounding areas due
to heat. If gas (torch) cutting is unavoidable, allow a minimum
margin of 50 mm (1.97in).
• When welding HSS panels, use spot welding whenever possi- ble in order to minimize weakening surrounding areas due to
heat.
If spot welding is impossible, use M.I.G. welding. Do not use
gas (torch) welding because it is inferior in welding strength.
• The spot weld on HSS panels is harder than that of an ordi- nary steel panel.
Therefore, when cutting spot welds on a HSS panel, use a low
speed high torque drill (1,000 to 1,200 rpm) to increase drill bit
durability and facilitate the operation.
• SP150 HSS panels with a tensile strength of 785 to 981 N/
mm
2 (80 to 100 kg/mm2 , 114 to 142 klb/sq in), used as rein-
forcement in the door guard beams, is too strong to repair.
When these HSS parts are damaged, the outer panels also
sustain substantial damage; therefore, the assembly parts
must be replaced.
PIIA0116E
PIIA0117E
PIIA0144E
PIIA0145E
Revision: April 20092010 QX56
Page 1068 of 4210
![INFINITI QX56 2010 Factory User Guide DLK-234
< ON-VEHICLE REPAIR >[WITH INTELLIGENT KEY SYSTEM]
HOOD
CLEARANCE AND SURFACE HEIGHT ADJUSTMENT
1. Remove the front grille. Refer to
EXT-17, "Removal and Installation".
2. Remove the hood loc INFINITI QX56 2010 Factory User Guide DLK-234
< ON-VEHICLE REPAIR >[WITH INTELLIGENT KEY SYSTEM]
HOOD
CLEARANCE AND SURFACE HEIGHT ADJUSTMENT
1. Remove the front grille. Refer to
EXT-17, "Removal and Installation".
2. Remove the hood loc](/img/42/57032/w960_57032-1067.png)
DLK-234
< ON-VEHICLE REPAIR >[WITH INTELLIGENT KEY SYSTEM]
HOOD
CLEARANCE AND SURFACE HEIGHT ADJUSTMENT
1. Remove the front grille. Refer to
EXT-17, "Removal and Installation".
2. Remove the hood lock assembly and adjust the height by rotating the bumper rubber until the hood clear- ance of hood and fender becomes 1 mm (0.04 in) lower than fitting standard dimension.
3. Temporarily tighten the hood lock, and position it by engaging it with the hood striker. Check the lock and striker for looseness, and tighten the lock mounting bolt to the specified torque.
4. Adjust the clearance and surface height of hood and fender according to \
the fitting standard dimension by rotating right and left bumper rubbers.
CAUTION:
Adjust right/left gap between hood and each part to the following specification.
5. Install the front grille. Refer to EXT-17, "
Removal and Installation".
HOOD LOCK ADJUSTMENT
1. Remove the front grille. Refer to EXT-17, "Removal and Installation".
2. Move the hood lock to the left or right so that striker center is vertically aligned with hood lock center (when viewed from vehicle front).
3. Make sure the secondary latch is properly engaged with the sec- ondary striker with hood's own weight by dropping it from
approx. 200 mm (7.87 in) height or by pressing it lightly approx.
3 kg (29 N, 7lb).
CAUTION:
Do not drop the hood from 300 mm (11.81 in) height or
higher.
4. After adjusting hood lock, tighten the lock bolts.
5. Install the front grille. Refer to EXT-17, "
Removal and Installa-
tion".
Removal and Installation of Hood AssemblyINFOID:0000000005147051
1. Support the hood striker with proper material to prevent it from falling.
WARNING:
Body injury may occur if no supporting rod is holding the
hood open when removing the damper stay.
2. Remove the hinge nuts from the hood to remove the hood assembly.
CAUTION:
Operate with two workers, because of its heavy weight.
Installation is in the reverse order of removal. Hood and headlamp (B–B) : 2.0 mm or less
PIIA3806E
LIIA1443E
Revision: April 20092010 QX56