sensor INFINITI QX56 2010 Factory Service Manual
[x] Cancel search | Manufacturer: INFINITI, Model Year: 2010, Model line: QX56, Model: INFINITI QX56 2010Pages: 4210, PDF Size: 81.91 MB
Page 1933 of 4210
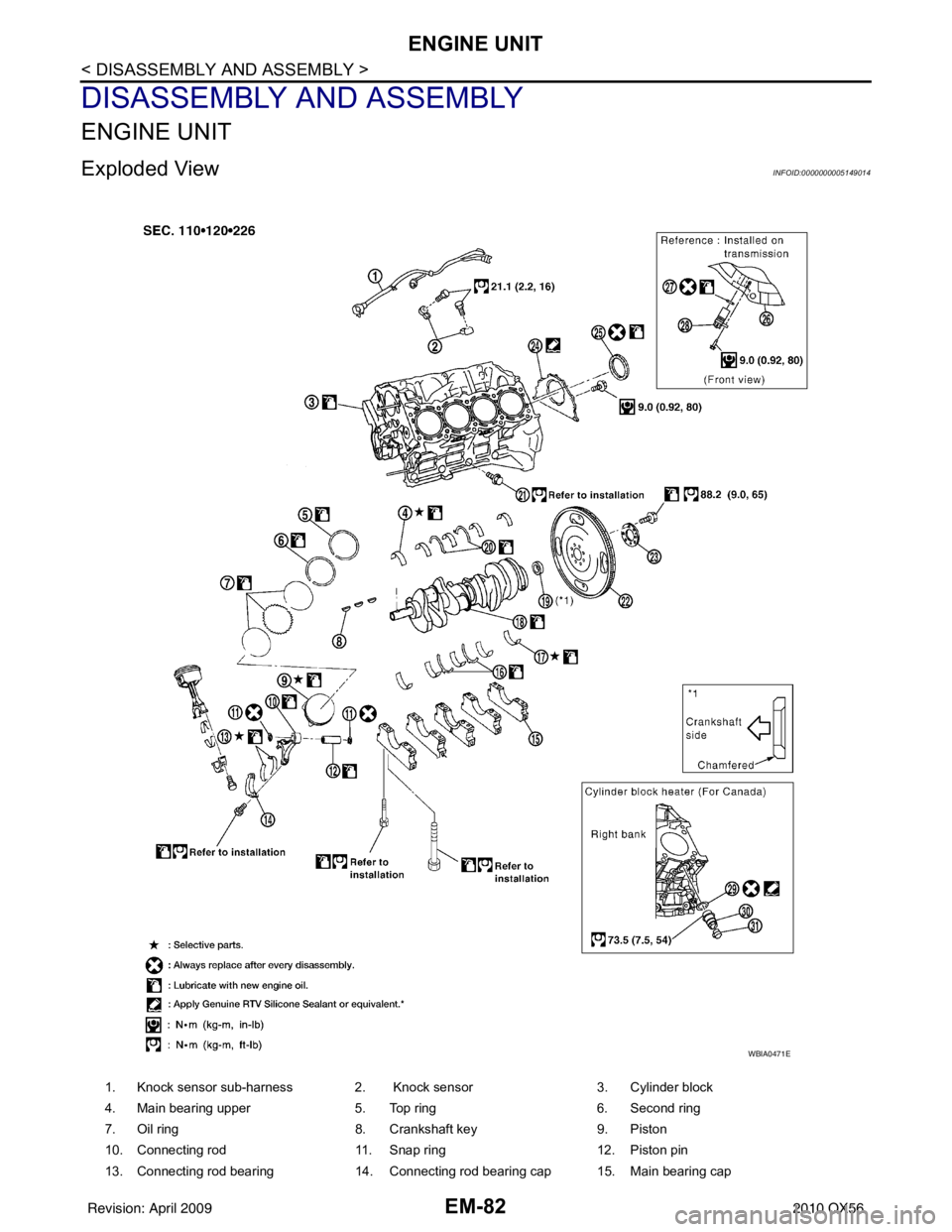
EM-82
< DISASSEMBLY AND ASSEMBLY >
ENGINE UNIT
DISASSEMBLY AND ASSEMBLY
ENGINE UNIT
Exploded ViewINFOID:0000000005149014
1. Knock sensor sub-harness 2. Knock sensor3. Cylinder block
4. Main bearing upper 5. Top ring6. Second ring
7. Oil ring 8. Crankshaft key9. Piston
10. Connecting rod 11. Snap ring12. Piston pin
13. Connecting rod bearing 14. Connecting rod bearing cap 15. Main bearing cap
WBIA0471E
Revision: April 20092010 QX56
Page 1934 of 4210
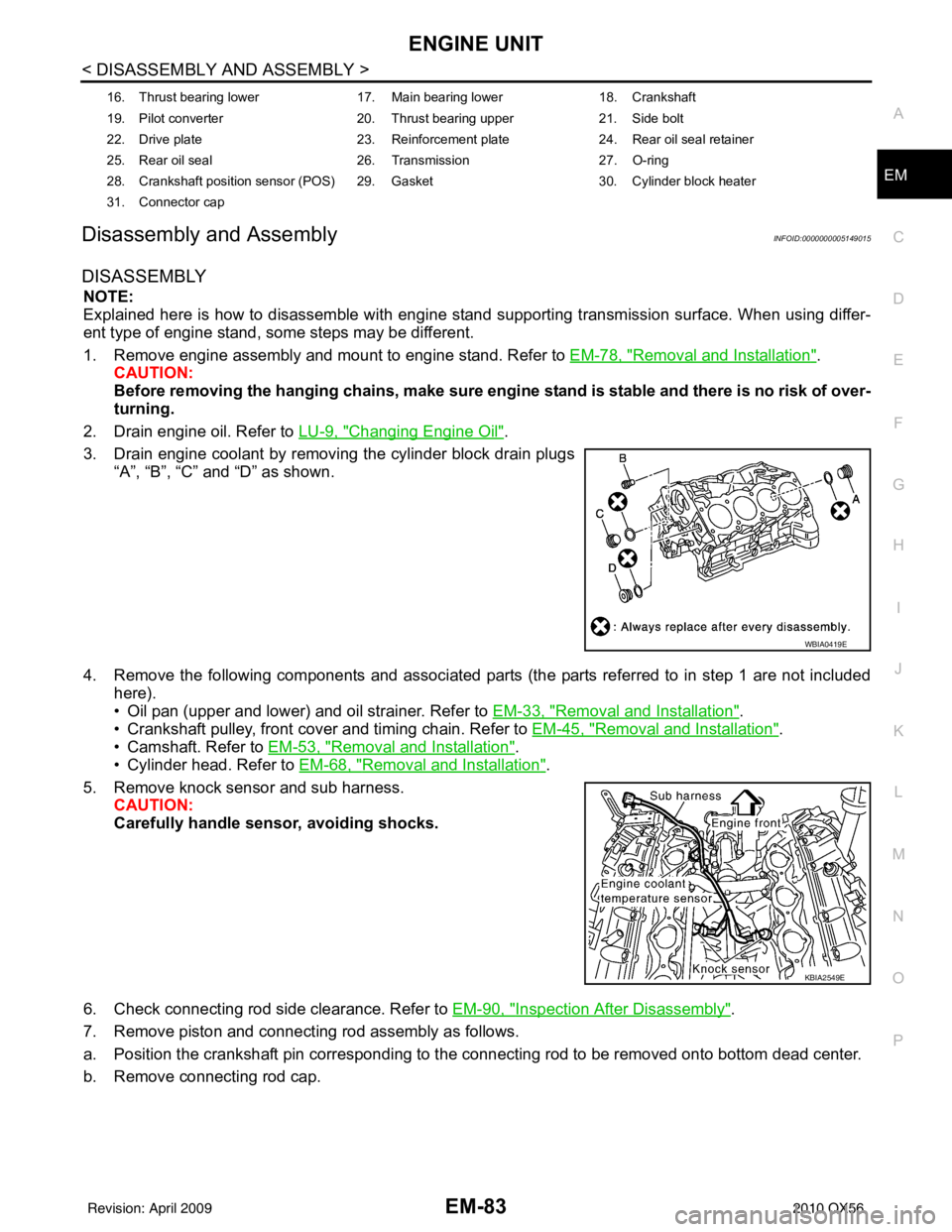
ENGINE UNITEM-83
< DISASSEMBLY AND ASSEMBLY >
C
DE
F
G H
I
J
K L
M A
EM
NP
O
Disassembly and AssemblyINFOID:0000000005149015
DISASSEMBLY
NOTE:
Explained here is how to disassemble with engine stand supporting transmission surface. When using differ-
ent type of engine stand, some steps may be different.
1. Remove engine assembly and mount to engine stand. Refer to
EM-78, "
Removal and Installation".
CAUTION:
Before removing the hanging chains, make sure engi ne stand is stable and there is no risk of over-
turning.
2. Drain engine oil. Refer to LU-9, "
Changing Engine Oil".
3. Drain engine coolant by removing the cylinder block drain plugs “A”, “B”, “C” and “D” as shown.
4. Remove the following components and associated parts (the parts referred to in step 1 are not included here).
• Oil pan (upper and lower) and oil strainer. Refer to EM-33, "
Removal and Installation".
• Crankshaft pulley, front cover and timing chain. Refer to EM-45, "
Removal and Installation".
• Camshaft. Refer to EM-53, "
Removal and Installation".
• Cylinder head. Refer to EM-68, "
Removal and Installation".
5. Remove knock sensor and sub harness. CAUTION:
Carefully handle sensor, avoiding shocks.
6. Check connecting rod side clearance. Refer to EM-90, "
Inspection After Disassembly".
7. Remove piston and connecting rod assembly as follows.
a. Position the crankshaft pin corresponding to the connecting rod to be removed onto bottom dead center.
b. Remove connecting rod cap.
16. Thrust bearing lower 17. Main bearing lower18. Crankshaft
19. Pilot converter 20. Thrust bearing upper21. Side bolt
22. Drive plate 23. Reinforcement plate24. Rear oil seal retainer
25. Rear oil seal 26. Transmission27. O-ring
28. Crankshaft position sensor (POS) 29. Gasket 30. Cylinder block heater
31. Connector cap
WBIA0419E
KBIA2549E
Revision: April 20092010 QX56
Page 1941 of 4210
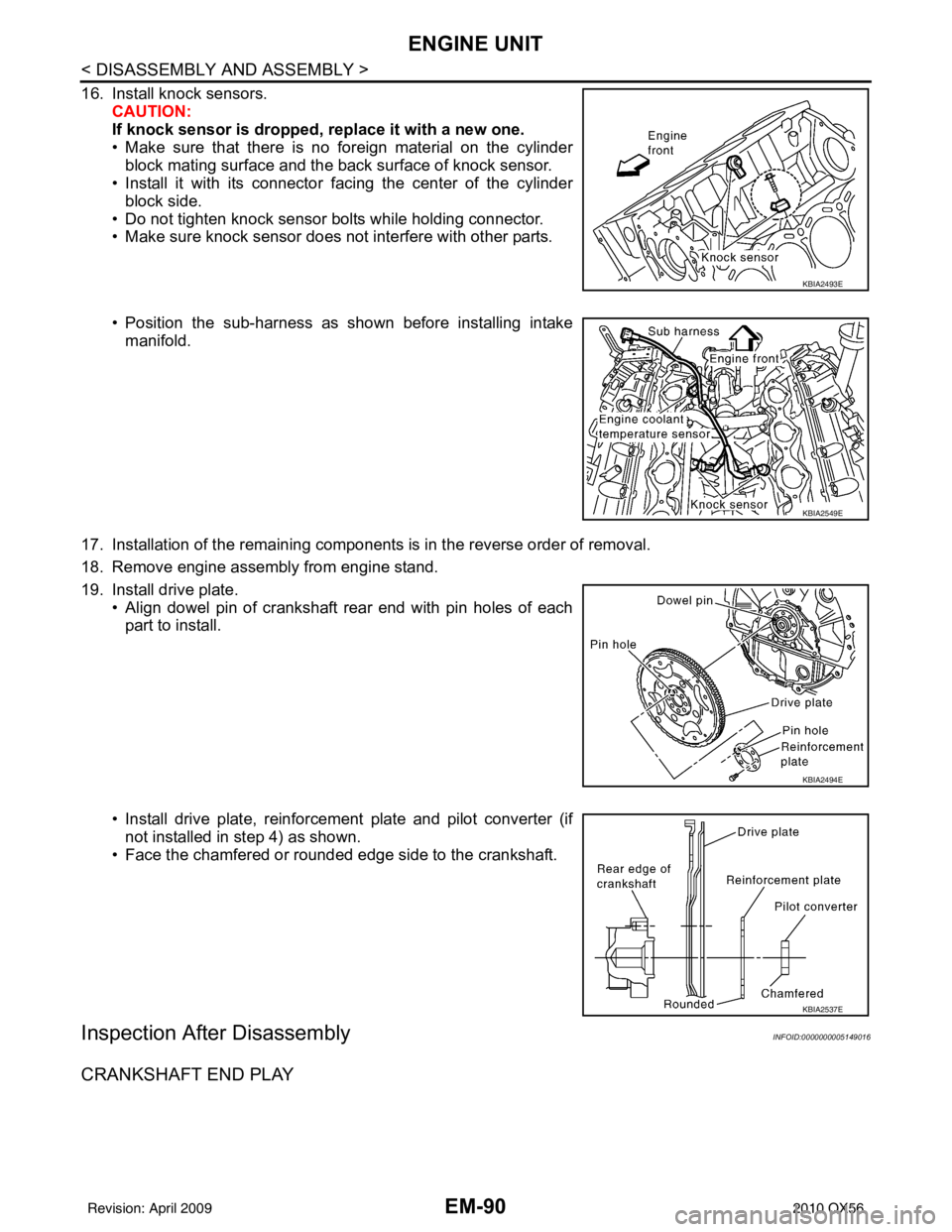
EM-90
< DISASSEMBLY AND ASSEMBLY >
ENGINE UNIT
16. Install knock sensors.CAUTION:
If knock sensor is dropped, replace it with a new one.
• Make sure that there is no foreign material on the cylinderblock mating surface and the back surface of knock sensor.
• Install it with its connector facing the center of the cylinder
block side.
• Do not tighten knock sensor bolts while holding connector.
• Make sure knock sensor does not interfere with other parts.
• Position the sub-harness as shown before installing intake manifold.
17. Installation of the remaining components is in the reverse order of removal.
18. Remove engine assembly from engine stand.
19. Install drive plate. • Align dowel pin of crankshaft rear end with pin holes of eachpart to install.
• Install drive plate, reinforcement plate and pilot converter (if not installed in step 4) as shown.
• Face the chamfered or rounded edge side to the crankshaft.
Inspection After DisassemblyINFOID:0000000005149016
CRANKSHAFT END PLAY
KBIA2493E
KBIA2549E
KBIA2494E
KBIA2537E
Revision: April 20092010 QX56
Page 1971 of 4210
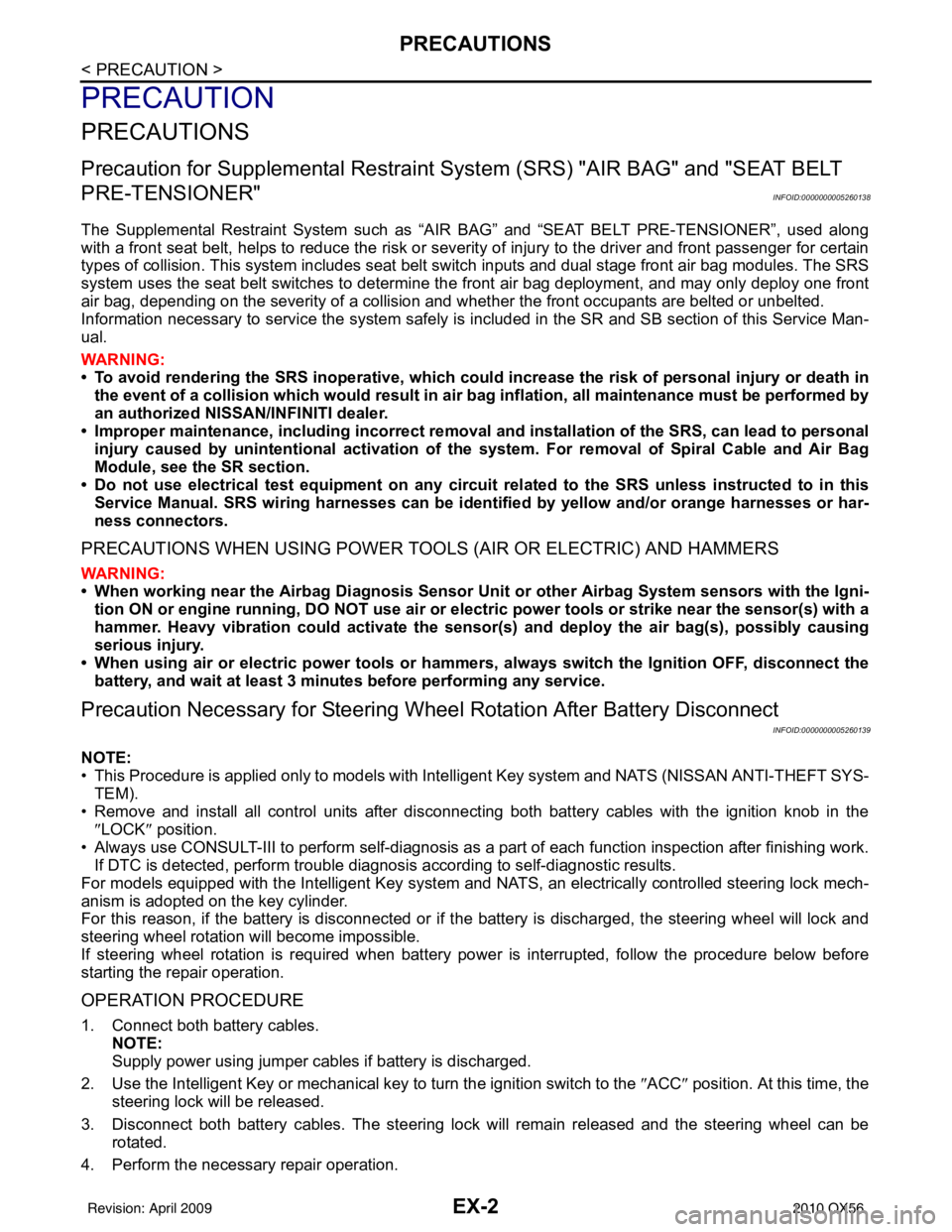
EX-2
< PRECAUTION >
PRECAUTIONS
PRECAUTION
PRECAUTIONS
Precaution for Supplemental Restraint System (SRS) "AIR BAG" and "SEAT BELT
PRE-TENSIONER"
INFOID:0000000005260138
The Supplemental Restraint System such as “A IR BAG” and “SEAT BELT PRE-TENSIONER”, used along
with a front seat belt, helps to reduce the risk or severity of injury to the driver and front passenger for certain
types of collision. This system includes seat belt switch inputs and dual stage front air bag modules. The SRS
system uses the seat belt switches to determine the front air bag deployment, and may only deploy one front
air bag, depending on the severity of a collision and w hether the front occupants are belted or unbelted.
Information necessary to service the system safely is included in the SR and SB section of this Service Man-
ual.
WARNING:
• To avoid rendering the SRS inopera tive, which could increase the risk of personal injury or death in
the event of a collision which would result in air bag inflation, all maintenance must be performed by
an authorized NISSAN/INFINITI dealer.
• Improper maintenance, including in correct removal and installation of the SRS, can lead to personal
injury caused by unintent ional activation of the system. For re moval of Spiral Cable and Air Bag
Module, see the SR section.
• Do not use electrical test equipmen t on any circuit related to the SRS unless instructed to in this
Service Manual. SRS wiring harn esses can be identified by yellow and/or orange harnesses or har-
ness connectors.
PRECAUTIONS WHEN USING POWER TOOLS (AIR OR ELECTRIC) AND HAMMERS
WARNING:
• When working near the Airbag Diagnosis Sensor Unit or other Airbag System sensors with the Igni-
tion ON or engine running, DO NOT use air or electri c power tools or strike near the sensor(s) with a
hammer. Heavy vibration could activate the sensor( s) and deploy the air bag(s), possibly causing
serious injury.
• When using air or electric power tools or hammers , always switch the Ignition OFF, disconnect the
battery, and wait at least 3 minu tes before performing any service.
Precaution Necessary for Steering W heel Rotation After Battery Disconnect
INFOID:0000000005260139
NOTE:
• This Procedure is applied only to models with Intelligent Key system and NATS (NISSAN ANTI-THEFT SYS-
TEM).
• Remove and install all control units after disconnecting both battery cables with the ignition knob in the
″LOCK ″ position.
• Always use CONSULT-III to perform self-diagnosis as a part of each function inspection after finishing work.
If DTC is detected, perform trouble diagnosis according to self-diagnostic results.
For models equipped with the Intelligent Key system and NATS, an electrically controlled steering lock mech-
anism is adopted on the key cylinder.
For this reason, if the battery is disconnected or if the battery is discharged, the steering wheel will lock and
steering wheel rotation will become impossible.
If steering wheel rotation is required when battery pow er is interrupted, follow the procedure below before
starting the repair operation.
OPERATION PROCEDURE
1. Connect both battery cables. NOTE:
Supply power using jumper cables if battery is discharged.
2. Use the Intelligent Key or mechanical key to turn the ignition switch to the ″ACC ″ position. At this time, the
steering lock will be released.
3. Disconnect both battery cables. The steering lock will remain released and the steering wheel can be rotated.
4. Perform the necessary repair operation.
Revision: April 20092010 QX56
Page 1973 of 4210
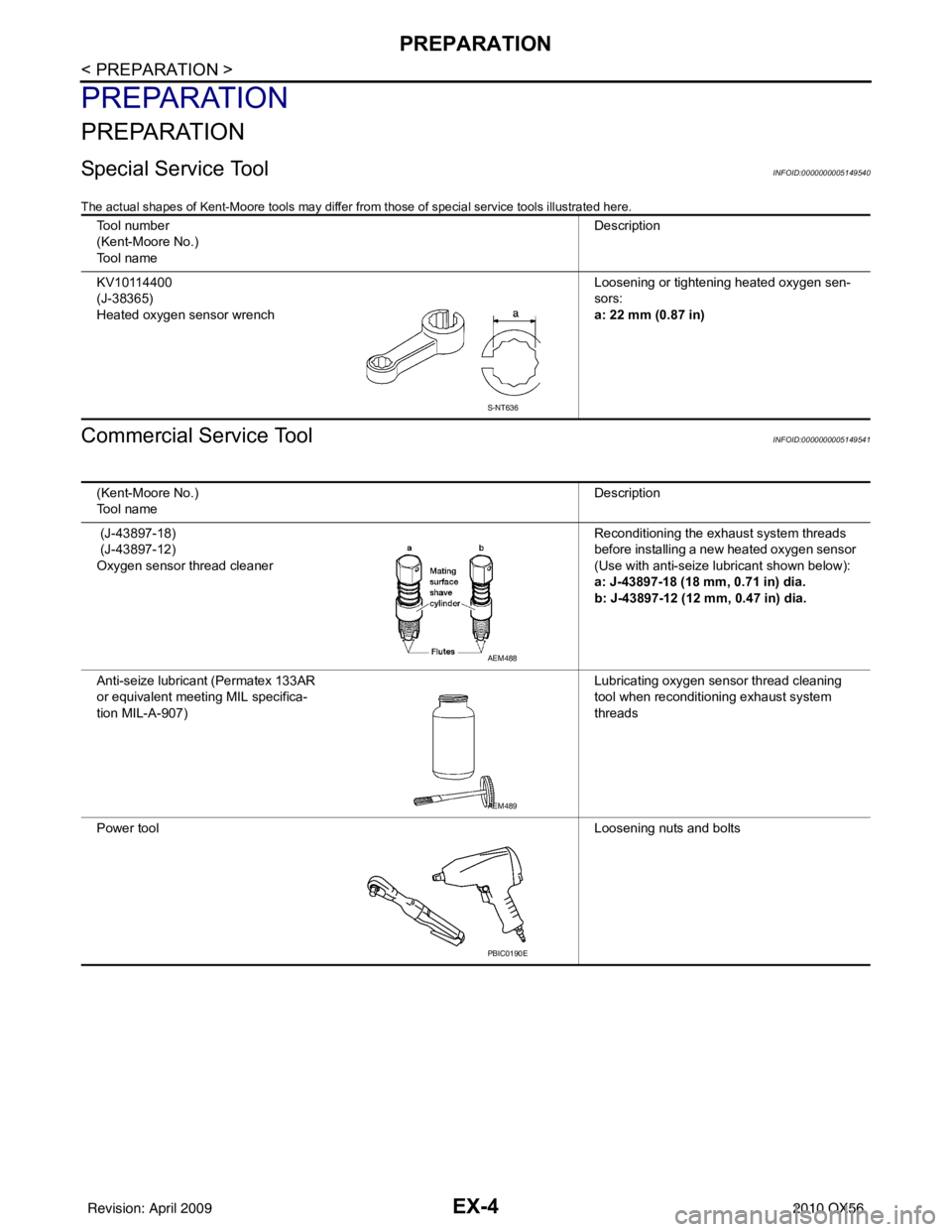
EX-4
< PREPARATION >
PREPARATION
PREPARATION
PREPARATION
Special Service ToolINFOID:0000000005149540
The actual shapes of Kent-Moore tools may differ from those of special service tools illustrated here.
Commercial Service ToolINFOID:0000000005149541
Tool number
(Kent-Moore No.)
Tool name Description
KV10114400
(J-38365)
Heated oxygen sensor wrench Loosening or tightening heated oxygen sen-
sors:
a: 22 mm (0.87 in)
S-NT636
(Kent-Moore No.)
Tool name
Description
(J-43897-18)
(J-43897-12)
Oxygen sensor thread cleaner Reconditioning the exhaust system threads
before installing a new heated oxygen sensor
(Use with anti-seize lubricant shown below):
a: J-43897-18 (18 mm, 0.71 in) dia.
b: J-43897-12 (12 mm, 0.47 in) dia.
Anti-seize lubricant (Permatex 133AR
or equivalent meeting MIL specifica-
tion MIL-A-907) Lubricating oxygen sensor thread cleaning
tool when reconditioning exhaust system
threads
Power tool Loosening nuts and bolts
AEM488
AEM489
PBIC0190E
Revision: April 20092010 QX56
Page 1975 of 4210
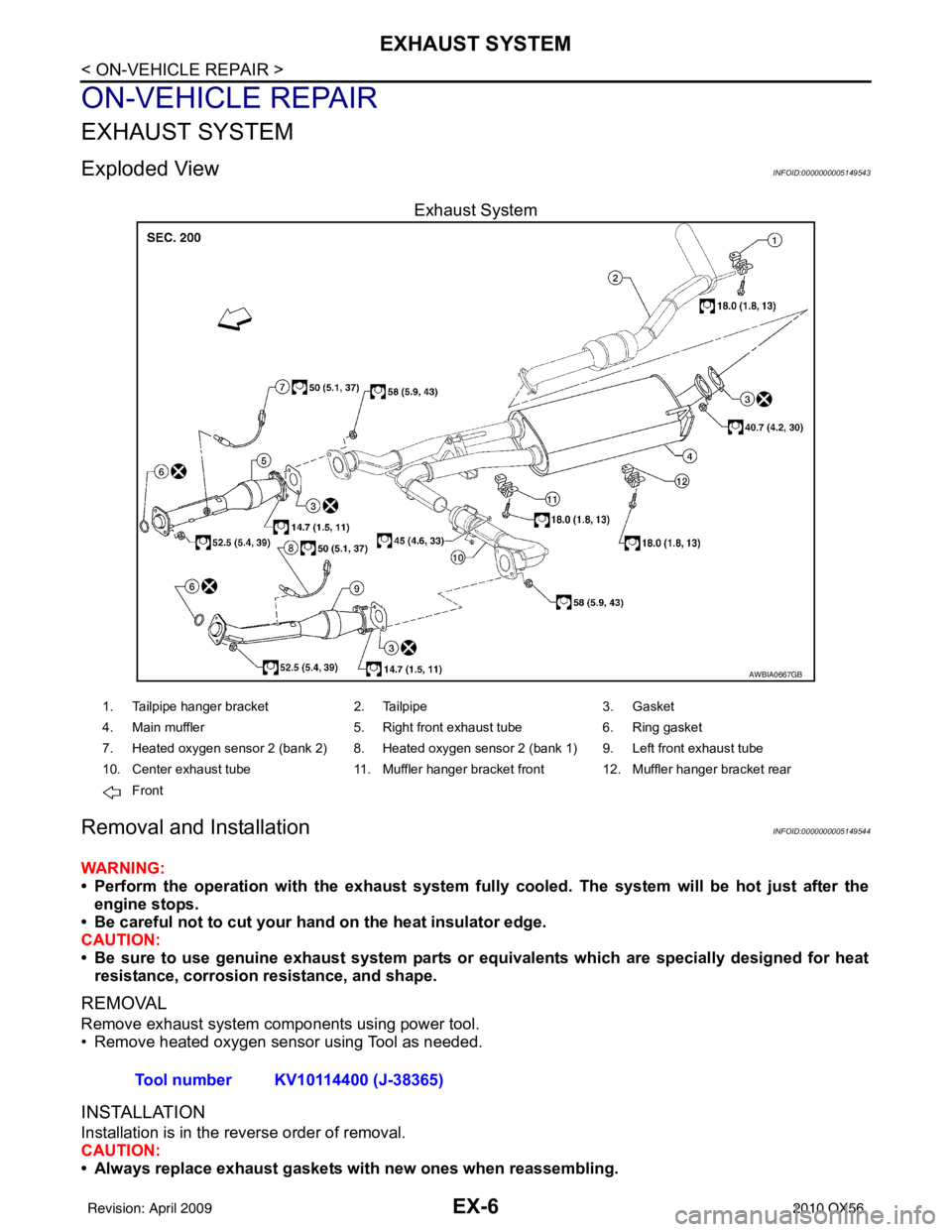
EX-6
< ON-VEHICLE REPAIR >
EXHAUST SYSTEM
ON-VEHICLE REPAIR
EXHAUST SYSTEM
Exploded ViewINFOID:0000000005149543
Exhaust System
Removal and InstallationINFOID:0000000005149544
WARNING:
• Perform the operation with the exhaust system fully cooled. The system will be hot just after the
engine stops.
• Be careful not to cut your hand on the heat insulator edge.
CAUTION:
• Be sure to use genuine exhaust system parts or equivalents which are specially designed for heat
resistance, corrosion resistance, and shape.
REMOVAL
Remove exhaust system components using power tool.
• Remove heated oxygen sensor using Tool as needed.
INSTALLATION
Installation is in the reverse order of removal.
CAUTION:
• Always replace exhaust gaskets with new ones when reassembling.
AWBIA0667GB
1. Tailpipe hanger bracket 2. Tailpipe3. Gasket
4. Main muffler 5. Right front exhaust tube6. Ring gasket
7. Heated oxygen sensor 2 (bank 2) 8. Heated oxygen sensor 2 (bank 1) 9. Left front exhaust tube
10. Center exhaust tube 11. Muffler hanger bracket front 12. Muffler hanger bracket rear
Front
Tool number KV10114400 (J-38365)
Revision: April 20092010 QX56
Page 1976 of 4210
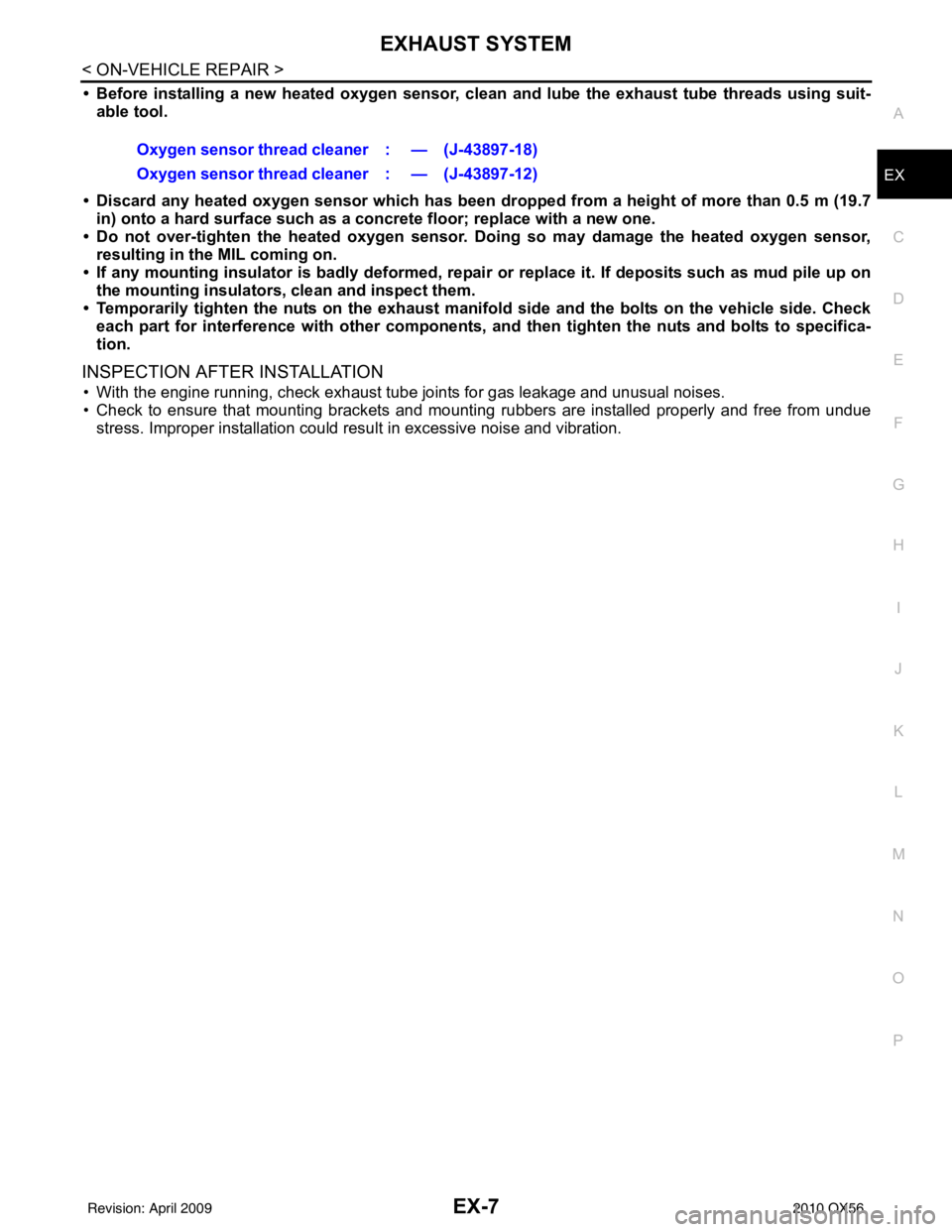
EXHAUST SYSTEMEX-7
< ON-VEHICLE REPAIR >
C
DE
F
G H
I
J
K L
M A
EX
NP
O
• Before installing a new heated o
xygen sensor, clean and lube the exhaust tube threads using suit-
able tool.
• Discard any heated oxygen sensor which has been dr opped from a height of more than 0.5 m (19.7
in) onto a hard surface such as a co ncrete floor; replace with a new one.
• Do not over-tighten the heated oxygen sensor. Doing so may damage the heated oxygen sensor, resulting in the MIL coming on.
• If any mounting insulator is badly deformed, repair or replace it. If deposits such as mud pile up on
the mounting insulators, clean and inspect them.
• Temporarily tighten the nuts on the exhaust manifold side and th e bolts on the vehicle side. Check
each part for interference with other components, an d then tighten the nuts and bolts to specifica-
tion.
INSPECTION AFTER INSTALLATION
• With the engine running, check exhaust tube joints for gas leakage and unusual noises.
• Check to ensure that mounting brackets and mount ing rubbers are installed properly and free from undue
stress. Improper installation could resu lt in excessive noise and vibration.
Oxygen sensor thread cleaner : — (J-43897-18)
Oxygen sensor thread cleaner : — (J-43897-12)
Revision: April 20092010 QX56
Page 1978 of 4210
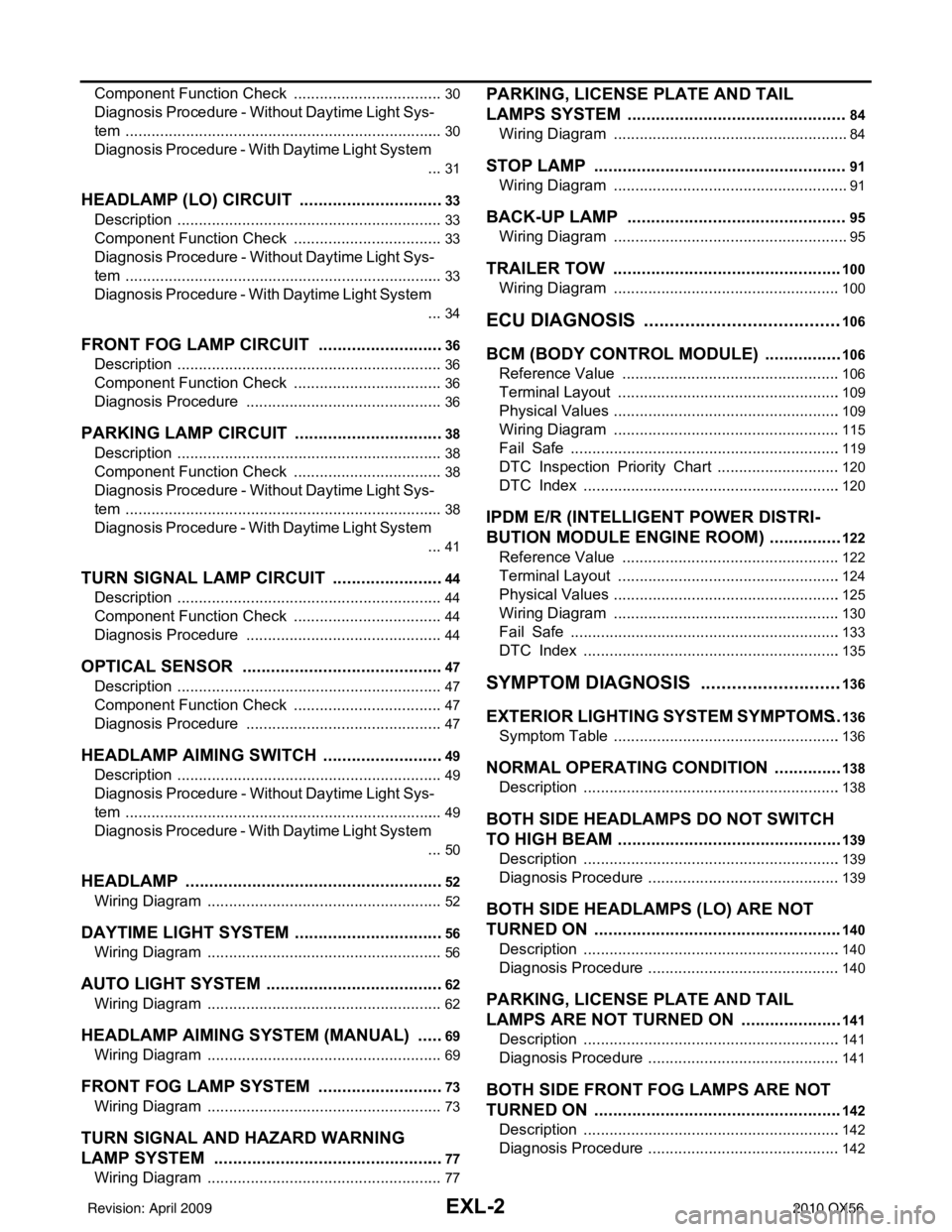
EXL-2
Component Function Check ...................................30
Diagnosis Procedure - Without Daytime Light Sys-
tem ..........................................................................
30
Diagnosis Procedure - With Daytime Light System
...
31
HEADLAMP (LO) CIRCUIT ...............................33
Description ........................................................... ...33
Component Function Check ...................................33
Diagnosis Procedure - Without Daytime Light Sys-
tem ..........................................................................
33
Diagnosis Procedure - With Daytime Light System
...
34
FRONT FOG LAMP CIRCUIT ...........................36
Description ........................................................... ...36
Component Function Check ...................................36
Diagnosis Procedure ..............................................36
PARKING LAMP CIRCUIT ................................38
Description ........................................................... ...38
Component Function Check ...................................38
Diagnosis Procedure - Without Daytime Light Sys-
tem ..........................................................................
38
Diagnosis Procedure - With Daytime Light System
...
41
TURN SIGNAL LAMP CIRCUIT ........................44
Description ........................................................... ...44
Component Function Check ...................................44
Diagnosis Procedure ..............................................44
OPTICAL SENSOR ...........................................47
Description ..............................................................47
Component Function Check ...................................47
Diagnosis Procedure ..............................................47
HEADLAMP AIMING SWITCH ..........................49
Description ........................................................... ...49
Diagnosis Procedure - Without Daytime Light Sys-
tem ..........................................................................
49
Diagnosis Procedure - With Daytime Light System
...
50
HEADLAMP .......................................................52
Wiring Diagram .................................................... ...52
DAYTIME LIGHT SYSTEM ................................56
Wiring Diagram .................................................... ...56
AUTO LIGHT SYSTEM ......................................62
Wiring Diagram .................................................... ...62
HEADLAMP AIMING SYSTEM (MANUAL) ......69
Wiring Diagram .................................................... ...69
FRONT FOG LAMP SYSTEM ...........................73
Wiring Diagram .................................................... ...73
TURN SIGNAL AND HAZARD WARNING
LAMP SYSTEM .............................................. ...
77
Wiring Diagram .................................................... ...77
PARKING, LICENSE PLATE AND TAIL
LAMPS SYSTEM ...............................................
84
Wiring Diagram .................................................... ...84
STOP LAMP ......................................................91
Wiring Diagram .................................................... ...91
BACK-UP LAMP ............................................ ...95
Wiring Diagram .................................................... ...95
TRAILER TOW .................................................100
Wiring Diagram .....................................................100
ECU DIAGNOSIS ......................................106
BCM (BODY CONTROL MODULE) ............... ..106
Reference Value .................................................. .106
Terminal Layout ....................................................109
Physical Values .....................................................109
Wiring Diagram .....................................................115
Fail Safe ...............................................................119
DTC Inspection Priority Chart .............................120
DTC Index ............................................................120
IPDM E/R (INTELLIGENT POWER DISTRI-
BUTION MODULE ENGINE ROOM) ................
122
Reference Value .................................................. .122
Terminal Layout ....................................................124
Physical Values .....................................................125
Wiring Diagram .....................................................130
Fail Safe ...............................................................133
DTC Index ............................................................135
SYMPTOM DIAGNOSIS ...........................136
EXTERIOR LIGHTING SYSTEM SYMPTOMS ..136
Symptom Table .................................................... .136
NORMAL OPERATING CONDITION ...............138
Description ........................................................... .138
BOTH SIDE HEADLAMPS DO NOT SWITCH
TO HIGH BEAM ................................................
139
Description ........................................................... .139
Diagnosis Procedure .............................................139
BOTH SIDE HEADLAMPS (LO) ARE NOT
TURNED ON .....................................................
140
Description ............................................................140
Diagnosis Procedure .............................................140
PARKING, LICENSE PLATE AND TAIL
LAMPS ARE NOT TURNED ON ......................
141
Description ........................................................... .141
Diagnosis Procedure .............................................141
BOTH SIDE FRONT FOG LAMPS ARE NOT
TURNED ON .....................................................
142
Description ............................................................142
Diagnosis Procedure .............................................142
Revision: April 20092010 QX56
Page 1987 of 4210
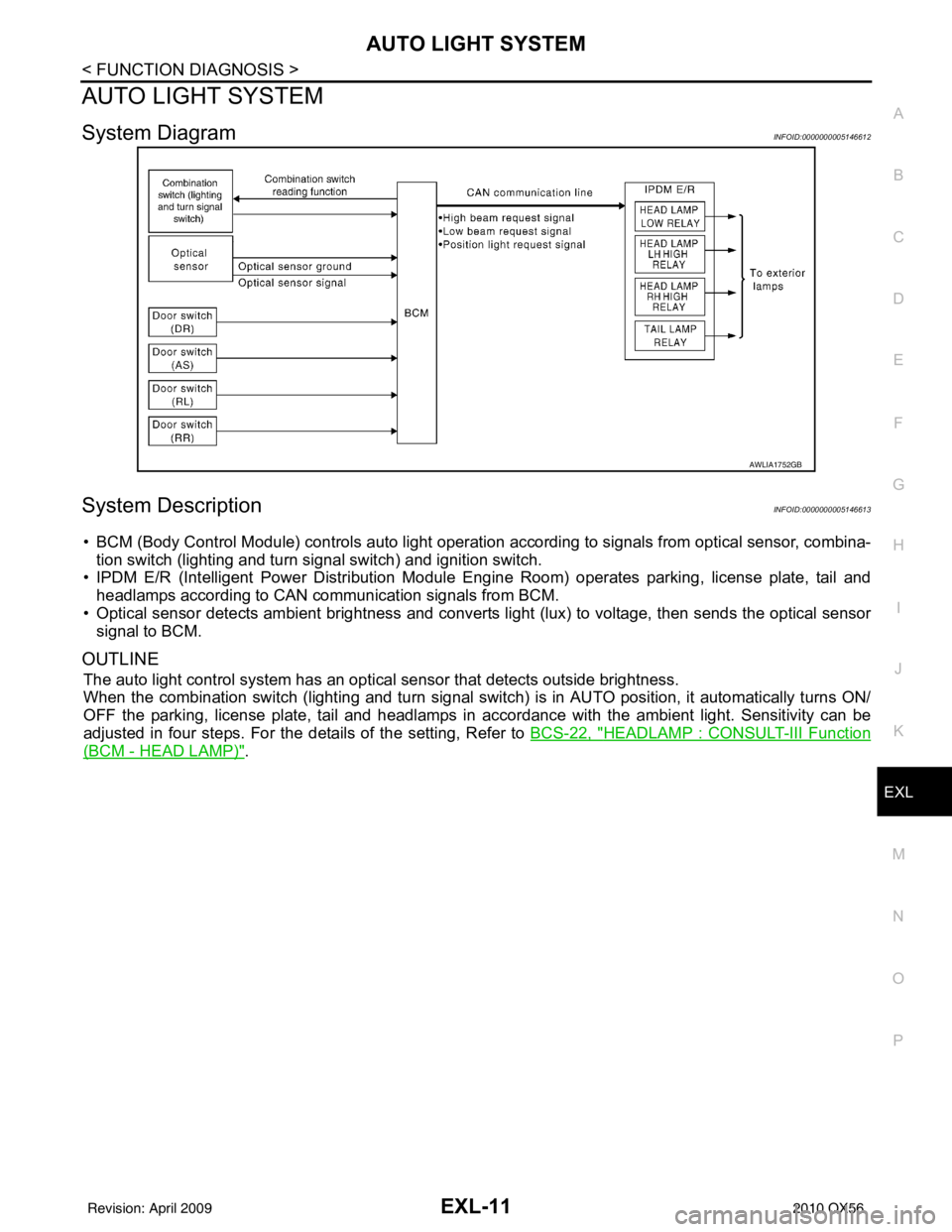
AUTO LIGHT SYSTEMEXL-11
< FUNCTION DIAGNOSIS >
C
DE
F
G H
I
J
K
M A
B
EXL
N
O P
AUTO LIGHT SYSTEM
System DiagramINFOID:0000000005146612
System DescriptionINFOID:0000000005146613
• BCM (Body Control Module) controls auto light operati on according to signals from optical sensor, combina-
tion switch (lighting and turn signal switch) and ignition switch.
• IPDM E/R (Intelligent Power Distribution Module Engine Room) operates parking, license plate, tail and
headlamps according to CAN communication signals from BCM.
• Optical sensor detects ambient br ightness and converts light (lux) to voltage, then sends the optical sensor
signal to BCM.
OUTLINE
The auto light control system has an optical sensor that detects outside brightness.
When the combination switch (lighting and turn signal switch) is in AUTO position, it automatically turns ON/
OFF the parking, license plate, tail and headlamps in accordance with the ambient light. Sensitivity can be
adjusted in four steps. For the details of the setting, Refer to BCS-22, "
HEADLAMP : CONSULT-III Function
(BCM - HEAD LAMP)".
AWLIA1752GB
Revision: April 20092010 QX56
Page 1988 of 4210
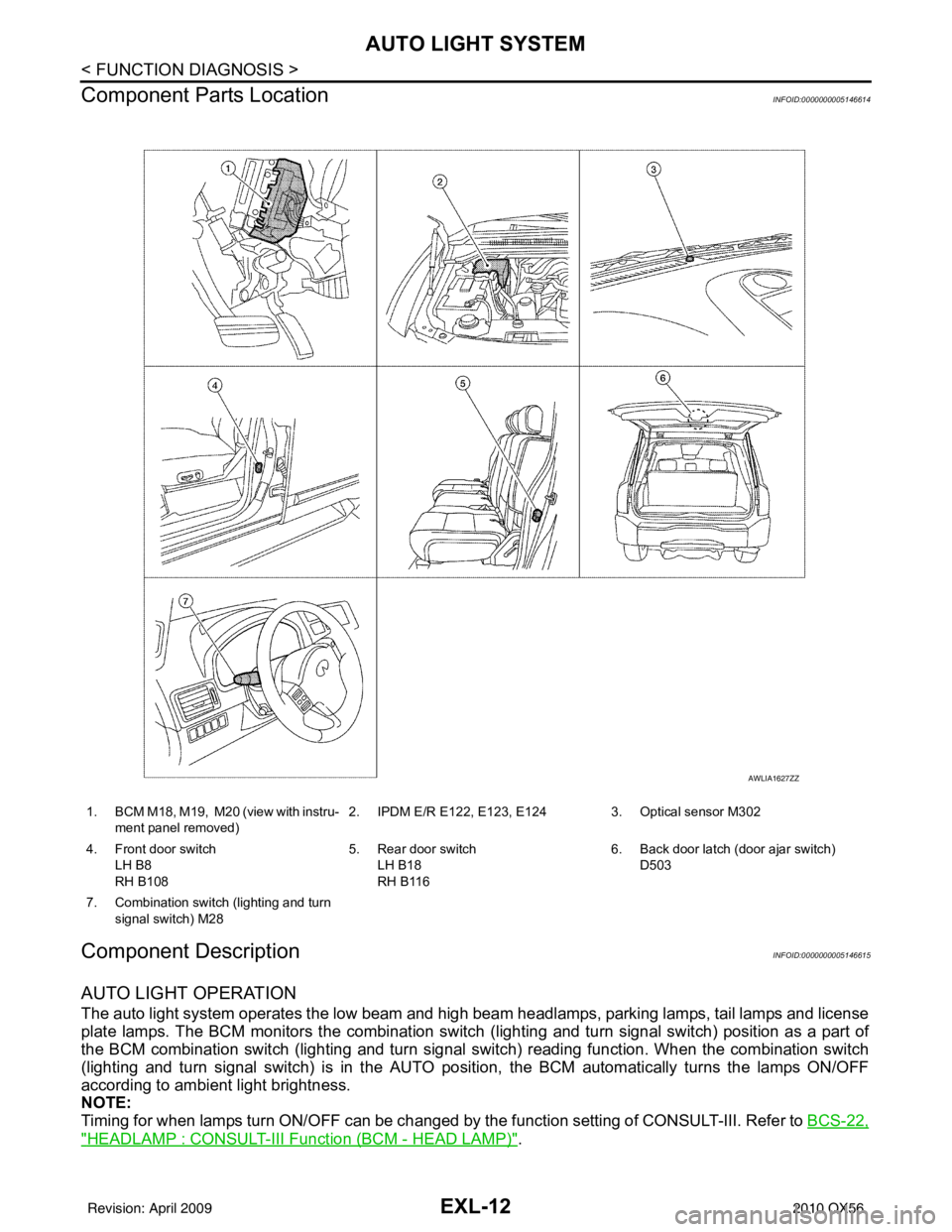
EXL-12
< FUNCTION DIAGNOSIS >
AUTO LIGHT SYSTEM
Component Parts Location
INFOID:0000000005146614
Component DescriptionINFOID:0000000005146615
AUTO LIGHT OPERATION
The auto light system operates t he low beam and high beam headlamps, parking lamps, tail lamps and license
plate lamps. The BCM monitors the combination switch (lighting and turn signal switch) position as a part of
the BCM combination switch (lighting and turn signal switch) reading function. When the combination switch
(lighting and turn signal switch) is in the AUTO position, the BCM automatically turns the lamps ON/OFF
according to ambient light brightness.
NOTE:
Timing for when lamps turn ON/OFF can be changed by the function setting of CONSULT-III. Refer to BCS-22,
"HEADLAMP : CONSULT-III Function (BCM - HEAD LAMP)".
1. BCM M18, M19, M20 (view with instru-
ment panel removed) 2. IPDM E/R E122, E123, E124 3. Optical sensor M302
4. Front door switch LH B8
RH B108 5. Rear door switch
LH B18
RH B116 6. Back door latch (door ajar switch)
D503
7. Combination switch (lighting and turn signal switch) M28
AWLIA1627ZZ
Revision: April 20092010 QX56