sensor ISUZU AXIOM 2002 Service Repair Manual
[x] Cancel search | Manufacturer: ISUZU, Model Year: 2002, Model line: AXIOM, Model: ISUZU AXIOM 2002Pages: 2100, PDF Size: 19.35 MB
Page 819 of 2100
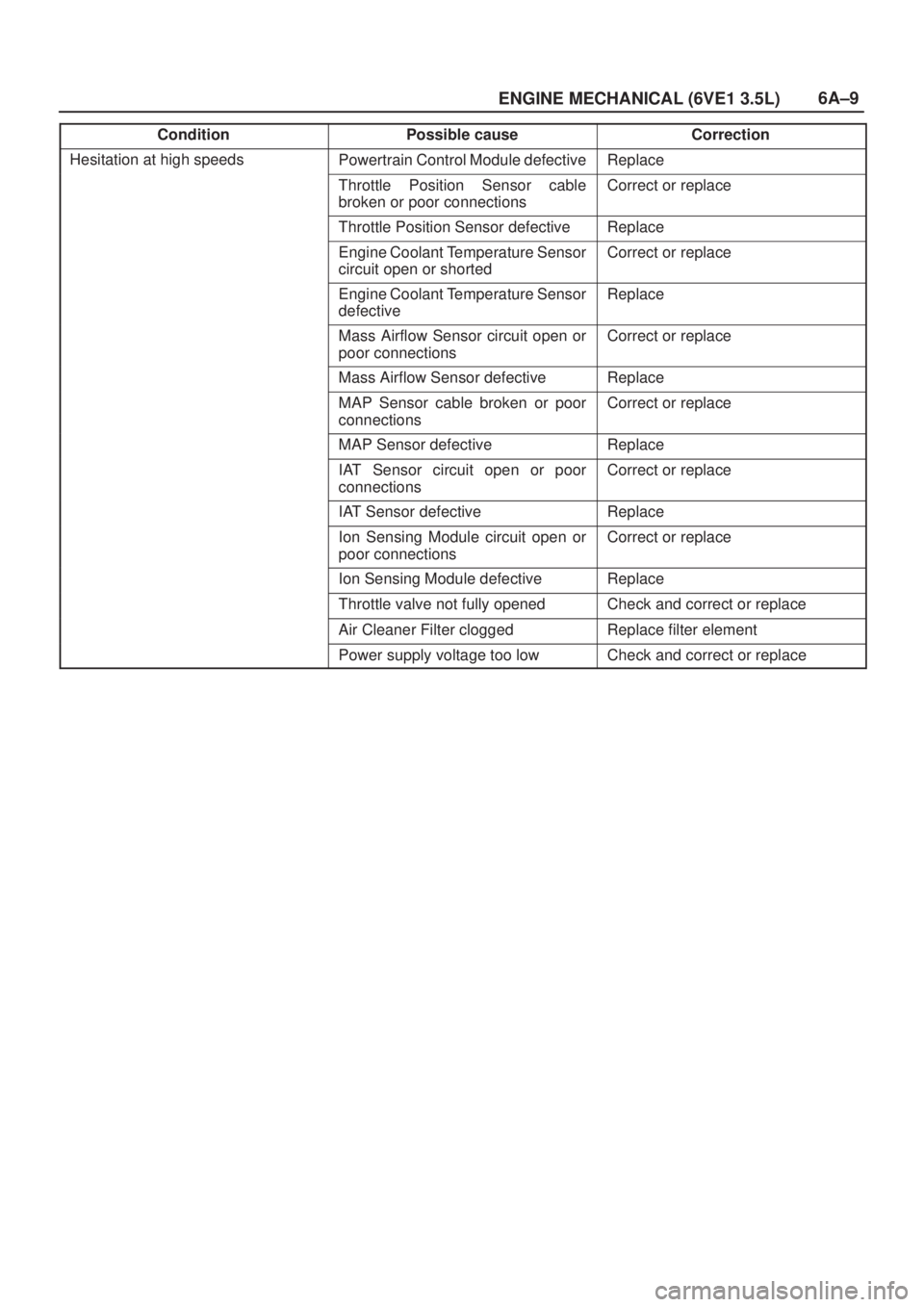
6A±9
ENGINE MECHANICAL (6VE1 3.5L)
Condition CorrectionPossible cause
Hesitation at high speedsPowertrain Control Module defectiveReplace
Throttle Position Sensor cable
broken or poor connectionsCorrect or replace
Throttle Position Sensor defectiveReplace
Engine Coolant Temperature Sensor
circuit open or shortedCorrect or replace
Engine Coolant Temperature Sensor
defectiveReplace
Mass Airflow Sensor circuit open or
poor connectionsCorrect or replace
Mass Airflow Sensor defectiveReplace
MAP Sensor cable broken or poor
connectionsCorrect or replace
MAP Sensor defectiveReplace
IAT Sensor circuit open or poor
connectionsCorrect or replace
IAT Sensor defectiveReplace
Ion Sensing Module circuit open or
poor connectionsCorrect or replace
Ion Sensing Module defectiveReplace
Throttle valve not fully openedCheck and correct or replace
Air Cleaner Filter cloggedReplace filter element
Power supply voltage too lowCheck and correct or replace
Page 820 of 2100
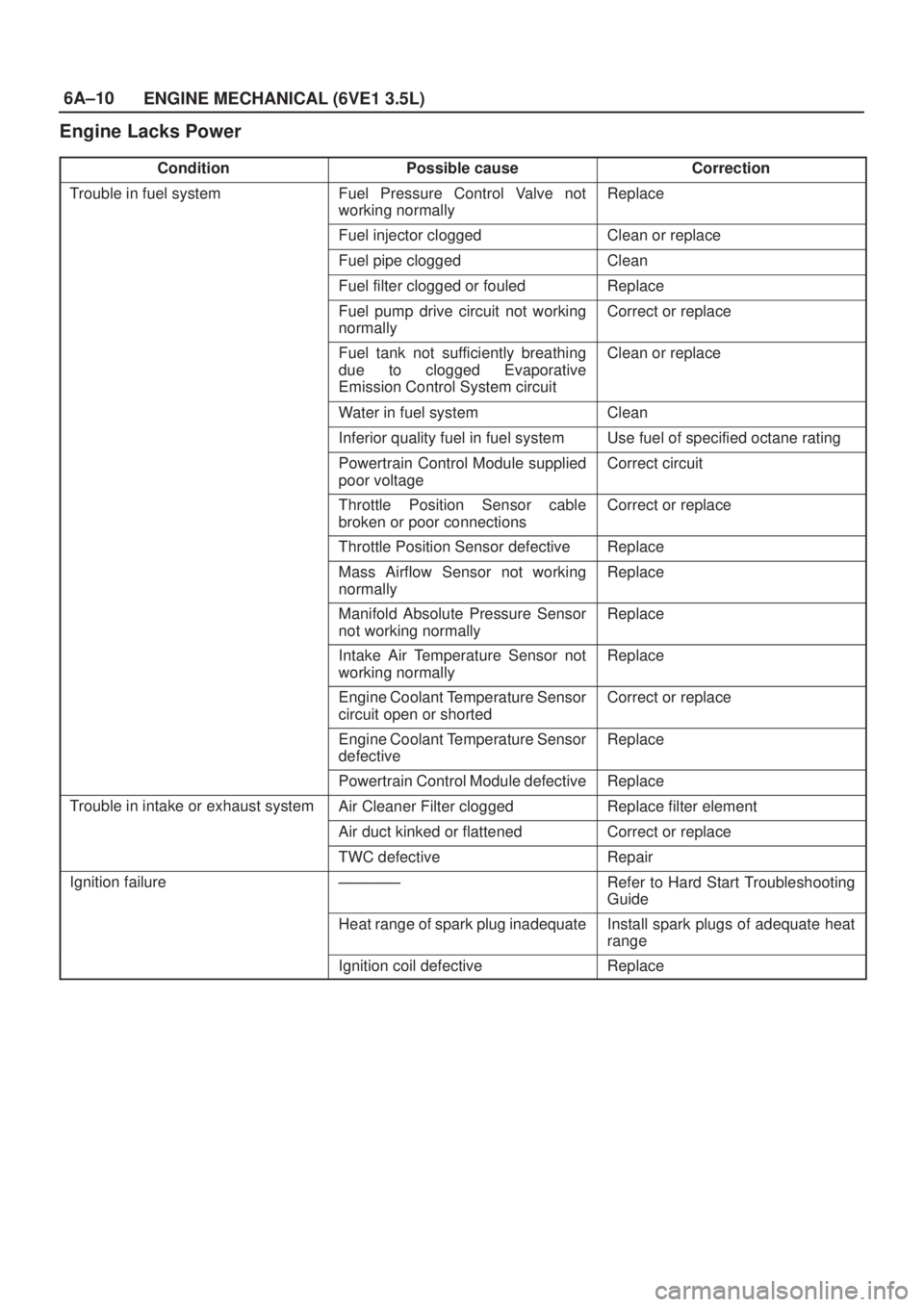
6A±10
ENGINE MECHANICAL (6VE1 3.5L)
Engine Lacks Power
ConditionPossible causeCorrection
Trouble in fuel systemFuel Pressure Control Valve not
working normallyReplace
Fuel injector cloggedClean or replace
Fuel pipe cloggedClean
Fuel filter clogged or fouledReplace
Fuel pump drive circuit not working
normallyCorrect or replace
Fuel tank not sufficiently breathing
due to clogged Evaporative
Emission Control System circuitClean or replace
Water in fuel systemClean
Inferior quality fuel in fuel systemUse fuel of specified octane rating
Powertrain Control Module supplied
poor voltageCorrect circuit
Throttle Position Sensor cable
broken or poor connectionsCorrect or replace
Throttle Position Sensor defectiveReplace
Mass Airflow Sensor not working
normallyReplace
Manifold Absolute Pressure Sensor
not working normallyReplace
Intake Air Temperature Sensor not
working normallyReplace
Engine Coolant Temperature Sensor
circuit open or shortedCorrect or replace
Engine Coolant Temperature Sensor
defectiveReplace
Powertrain Control Module defectiveReplace
Trouble in intake or exhaust systemAir Cleaner Filter cloggedReplace filter element
Air duct kinked or flattenedCorrect or replace
TWC defectiveRepair
Ignition failureÐÐÐÐRefer to Hard Start Troubleshooting
Guide
Heat range of spark plug inadequateInstall spark plugs of adequate heat
range
Ignition coil defectiveReplace
Page 821 of 2100
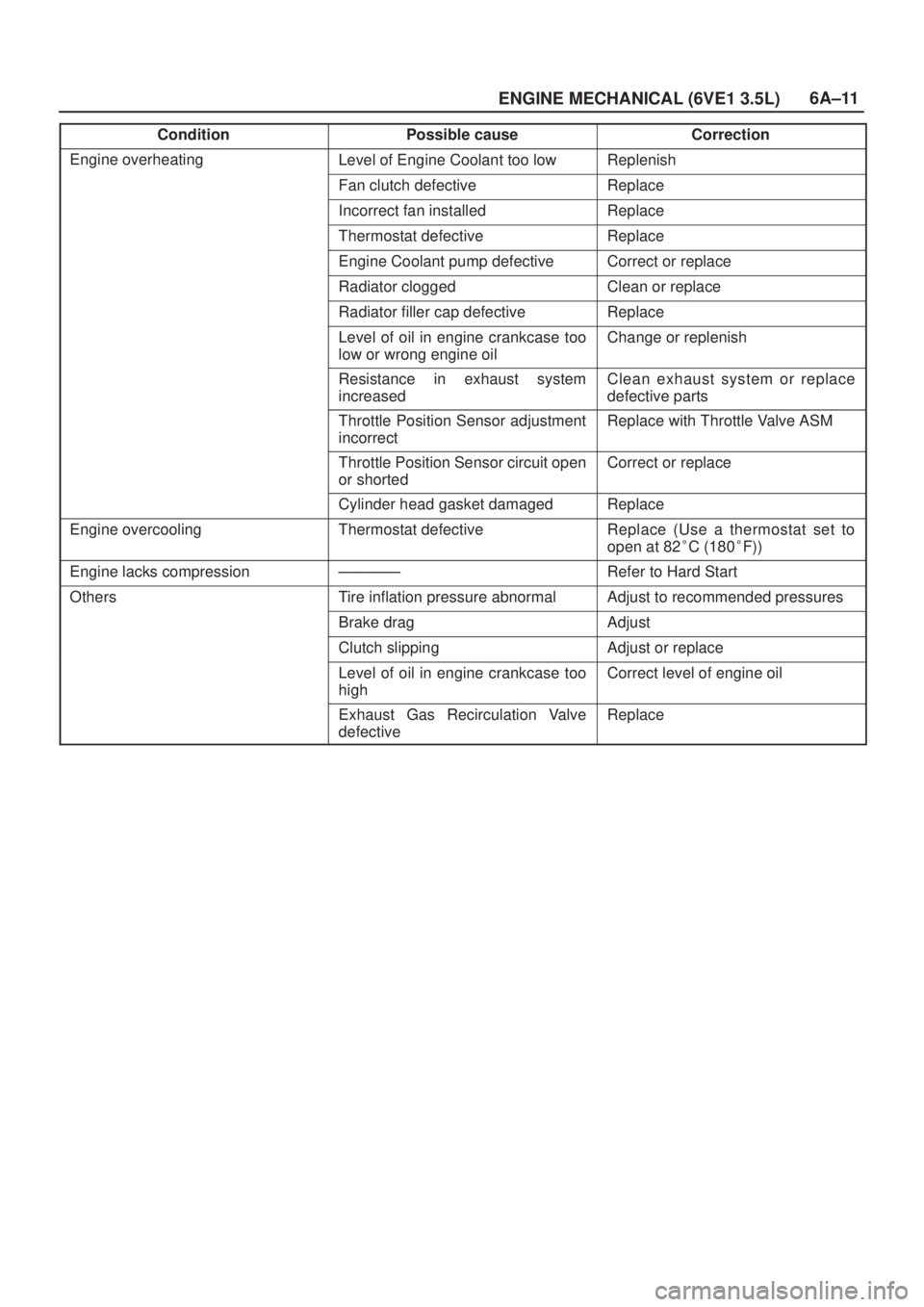
6A±11
ENGINE MECHANICAL (6VE1 3.5L)
Condition CorrectionPossible cause
Engine overheatingLevel of Engine Coolant too lowReplenish
Fan clutch defectiveReplace
Incorrect fan installedReplace
Thermostat defectiveReplace
Engine Coolant pump defectiveCorrect or replace
Radiator cloggedClean or replace
Radiator filler cap defectiveReplace
Level of oil in engine crankcase too
low or wrong engine oilChange or replenish
Resistance in exhaust system
increasedClean exhaust system or replace
defective parts
Throttle Position Sensor adjustment
incorrectReplace with Throttle Valve ASM
Throttle Position Sensor circuit open
or shortedCorrect or replace
Cylinder head gasket damagedReplace
Engine overcoolingThermostat defectiveReplace (Use a thermostat set to
open at 82C (180F))
Engine lacks compressionÐÐÐÐRefer to Hard Start
OthersTire inflation pressure abnormalAdjust to recommended pressures
Brake dragAdjust
Clutch slippingAdjust or replace
Level of oil in engine crankcase too
highCorrect level of engine oil
Exhaust Gas Recirculation Valve
defectiveReplace
Page 824 of 2100
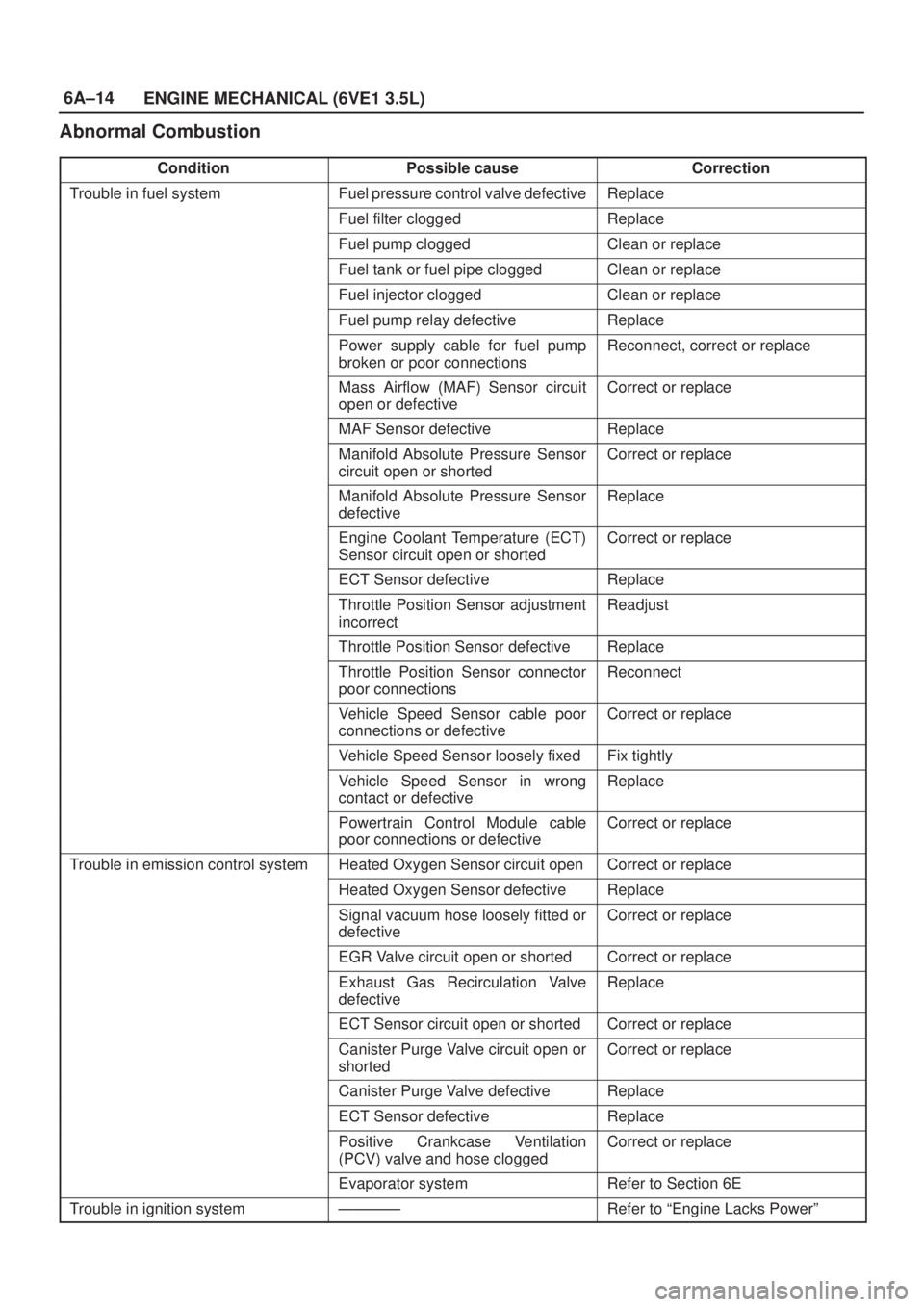
6A±14
ENGINE MECHANICAL (6VE1 3.5L)
Abnormal Combustion
ConditionPossible causeCorrection
Trouble in fuel systemFuel pressure control valve defectiveReplace
Fuel filter cloggedReplace
Fuel pump cloggedClean or replace
Fuel tank or fuel pipe cloggedClean or replace
Fuel injector cloggedClean or replace
Fuel pump relay defectiveReplace
Power supply cable for fuel pump
broken or poor connectionsReconnect, correct or replace
Mass Airflow (MAF) Sensor circuit
open or defectiveCorrect or replace
MAF Sensor defectiveReplace
Manifold Absolute Pressure Sensor
circuit open or shortedCorrect or replace
Manifold Absolute Pressure Sensor
defectiveReplace
Engine Coolant Temperature (ECT)
Sensor circuit open or shortedCorrect or replace
ECT Sensor defectiveReplace
Throttle Position Sensor adjustment
incorrectReadjust
Throttle Position Sensor defectiveReplace
Throttle Position Sensor connector
poor connectionsReconnect
Vehicle Speed Sensor cable poor
connections or defectiveCorrect or replace
Vehicle Speed Sensor loosely fixedFix tightly
Vehicle Speed Sensor in wrong
contact or defectiveReplace
Powertrain Control Module cable
poor connections or defectiveCorrect or replace
Trouble in emission control systemHeated Oxygen Sensor circuit openCorrect or replace
Heated Oxygen Sensor defectiveReplace
Signal vacuum hose loosely fitted or
defectiveCorrect or replace
EGR Valve circuit open or shortedCorrect or replace
Exhaust Gas Recirculation Valve
defectiveReplace
ECT Sensor circuit open or shortedCorrect or replace
Canister Purge Valve circuit open or
shortedCorrect or replace
Canister Purge Valve defectiveReplace
ECT Sensor defectiveReplace
Positive Crankcase Ventilation
(PCV) valve and hose cloggedCorrect or replace
Evaporator systemRefer to Section 6E
Trouble in ignition systemÐÐÐÐRefer to ªEngine Lacks Powerº
Page 828 of 2100
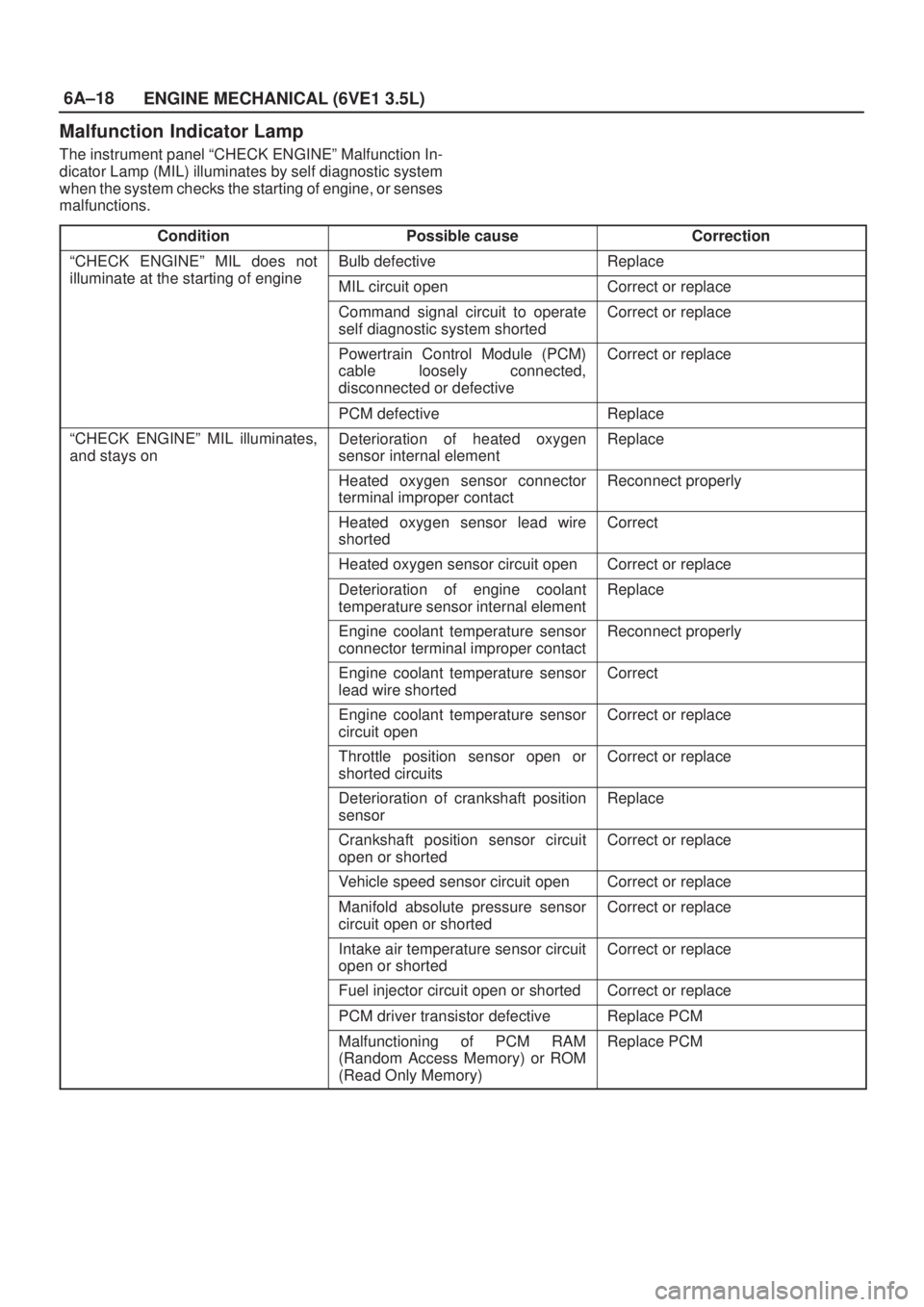
6A±18
ENGINE MECHANICAL (6VE1 3.5L)
Malfunction Indicator Lamp
The instrument panel ªCHECK ENGINEº Malfunction In-
dicator Lamp (MIL) illuminates by self diagnostic system
when the system checks the starting of engine, or senses
malfunctions.
Condition
Possible causeCorrection
ªCHECK ENGINEº MIL does not
illuminate at the starting of engine
Bulb defectiveReplace
illuminate at the starting of engineMIL circuit openCorrect or replace
Command signal circuit to operate
self diagnostic system shortedCorrect or replace
Powertrain Control Module (PCM)
cable loosely connected,
disconnected or defectiveCorrect or replace
PCM defectiveReplace
ªCHECK ENGINEº MIL illuminates,
and stays onDeterioration of heated oxygen
sensor internal elementReplace
Heated oxygen sensor connector
terminal improper contactReconnect properly
Heated oxygen sensor lead wire
shortedCorrect
Heated oxygen sensor circuit openCorrect or replace
Deterioration of engine coolant
temperature sensor internal elementReplace
Engine coolant temperature sensor
connector terminal improper contactReconnect properly
Engine coolant temperature sensor
lead wire shortedCorrect
Engine coolant temperature sensor
circuit openCorrect or replace
Throttle position sensor open or
shorted circuitsCorrect or replace
Deterioration of crankshaft position
sensorReplace
Crankshaft position sensor circuit
open or shortedCorrect or replace
Vehicle speed sensor circuit openCorrect or replace
Manifold absolute pressure sensor
circuit open or shortedCorrect or replace
Intake air temperature sensor circuit
open or shortedCorrect or replace
Fuel injector circuit open or shortedCorrect or replace
PCM driver transistor defectiveReplace PCM
Malfunctioning of PCM RAM
(Random Access Memory) or ROM
(Read Only Memory)Replace PCM
Page 832 of 2100
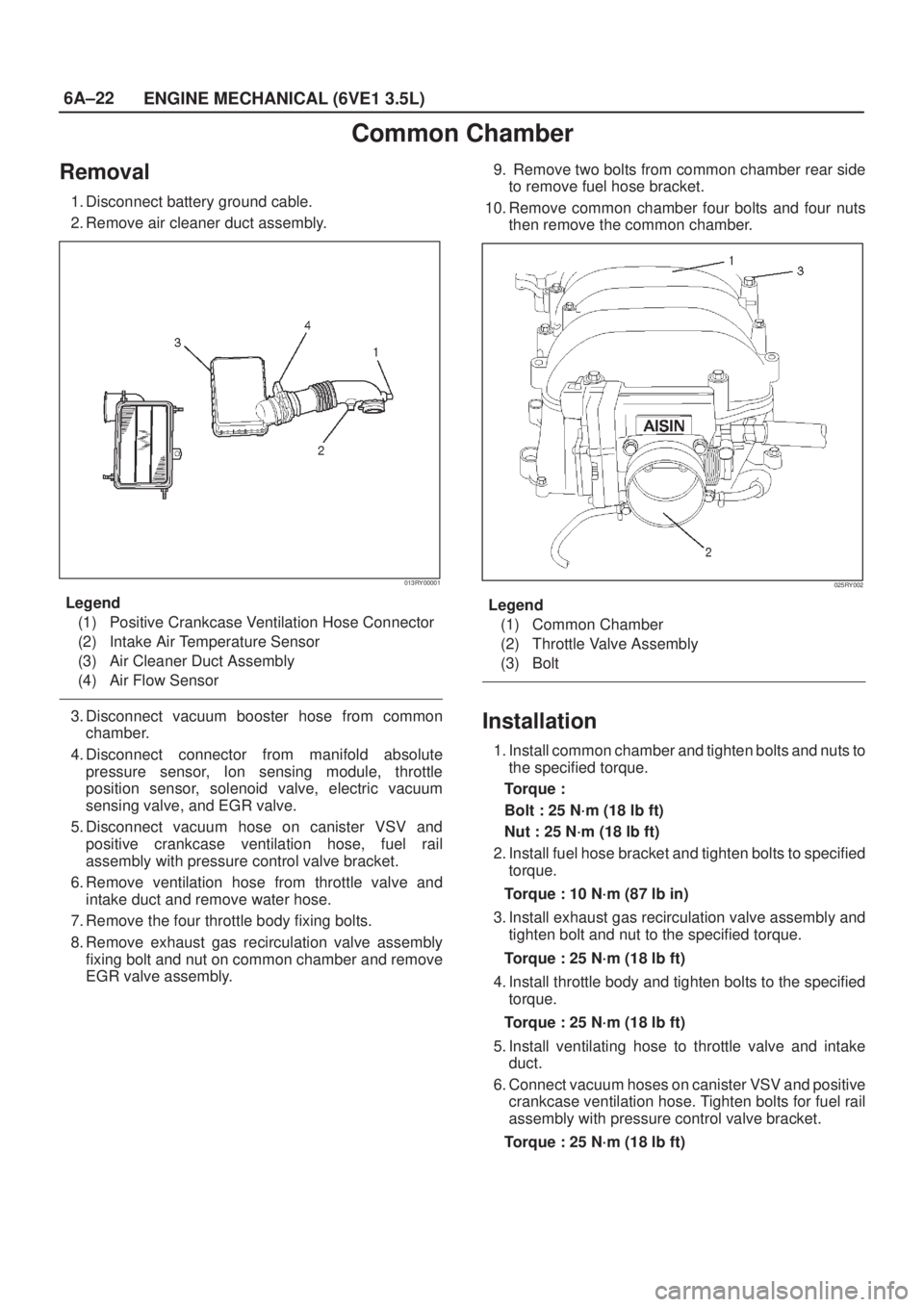
6A±22
ENGINE MECHANICAL (6VE1 3.5L)
Common Chamber
Removal
1. Disconnect battery ground cable.
2. Remove air cleaner duct assembly.
013RY00001
Legend
(1) Positive Crankcase Ventilation Hose Connector
(2) Intake Air Temperature Sensor
(3) Air Cleaner Duct Assembly
(4) Air Flow Sensor
3. Disconnect vacuum booster hose from common
chamber.
4. Disconnect connector from manifold absolute
pressure sensor, Ion sensing module, throttle
position sensor, solenoid valve, electric vacuum
sensing valve, and EGR valve.
5. Disconnect vacuum hose on canister VSV and
positive crankcase ventilation hose, fuel rail
assembly with pressure control valve bracket.
6. Remove ventilation hose from throttle valve and
intake duct and remove water hose.
7. Remove the four throttle body fixing bolts.
8. Remove exhaust gas recirculation valve assembly
fixing bolt and nut on common chamber and remove
EGR valve assembly.9. Remove two bolts from common chamber rear side
to remove fuel hose bracket.
10. Remove common chamber four bolts and four nuts
then remove the common chamber.
025RY002
Legend
(1) Common Chamber
(2) Throttle Valve Assembly
(3) Bolt
Installation
1. Install common chamber and tighten bolts and nuts to
the specified torque.
Torque :
Bolt : 25 N´m (18 lb ft)
Nut : 25 N´m (18 lb ft)
2. Install fuel hose bracket and tighten bolts to specified
torque.
Torque : 10 N´m (87 lb in)
3. Install exhaust gas recirculation valve assembly and
tighten bolt and nut to the specified torque.
Torque : 25 N´m (18 lb ft)
4. Install throttle body and tighten bolts to the specified
torque.
Torque : 25 N´m (18 lb ft)
5. Install ventilating hose to throttle valve and intake
duct.
6. Connect vacuum hoses on canister VSV and positive
crankcase ventilation hose. Tighten bolts for fuel rail
assembly with pressure control valve bracket.
Torque : 25 N´m (18 lb ft)
Page 833 of 2100
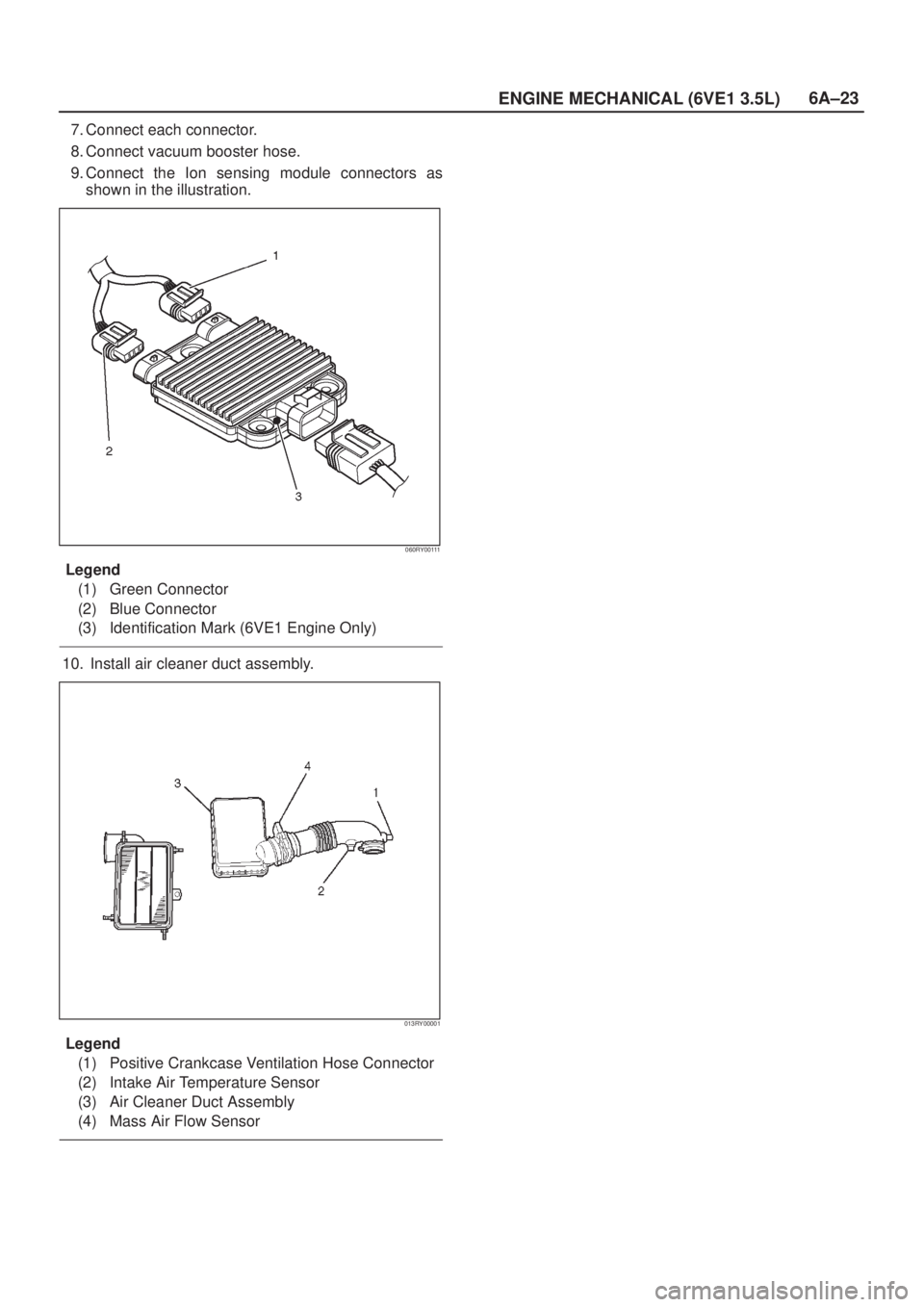
6A±23
ENGINE MECHANICAL (6VE1 3.5L)
7. Connect each connector.
8. Connect vacuum booster hose.
9. Connect the Ion sensing module connectors as
shown in the illustration.
060RY00111
Legend
(1) Green Connector
(2) Blue Connector
(3) Identification Mark (6VE1 Engine Only)
10. Install air cleaner duct assembly.
013RY00001
Legend
(1) Positive Crankcase Ventilation Hose Connector
(2) Intake Air Temperature Sensor
(3) Air Cleaner Duct Assembly
(4) Mass Air Flow Sensor
Page 834 of 2100
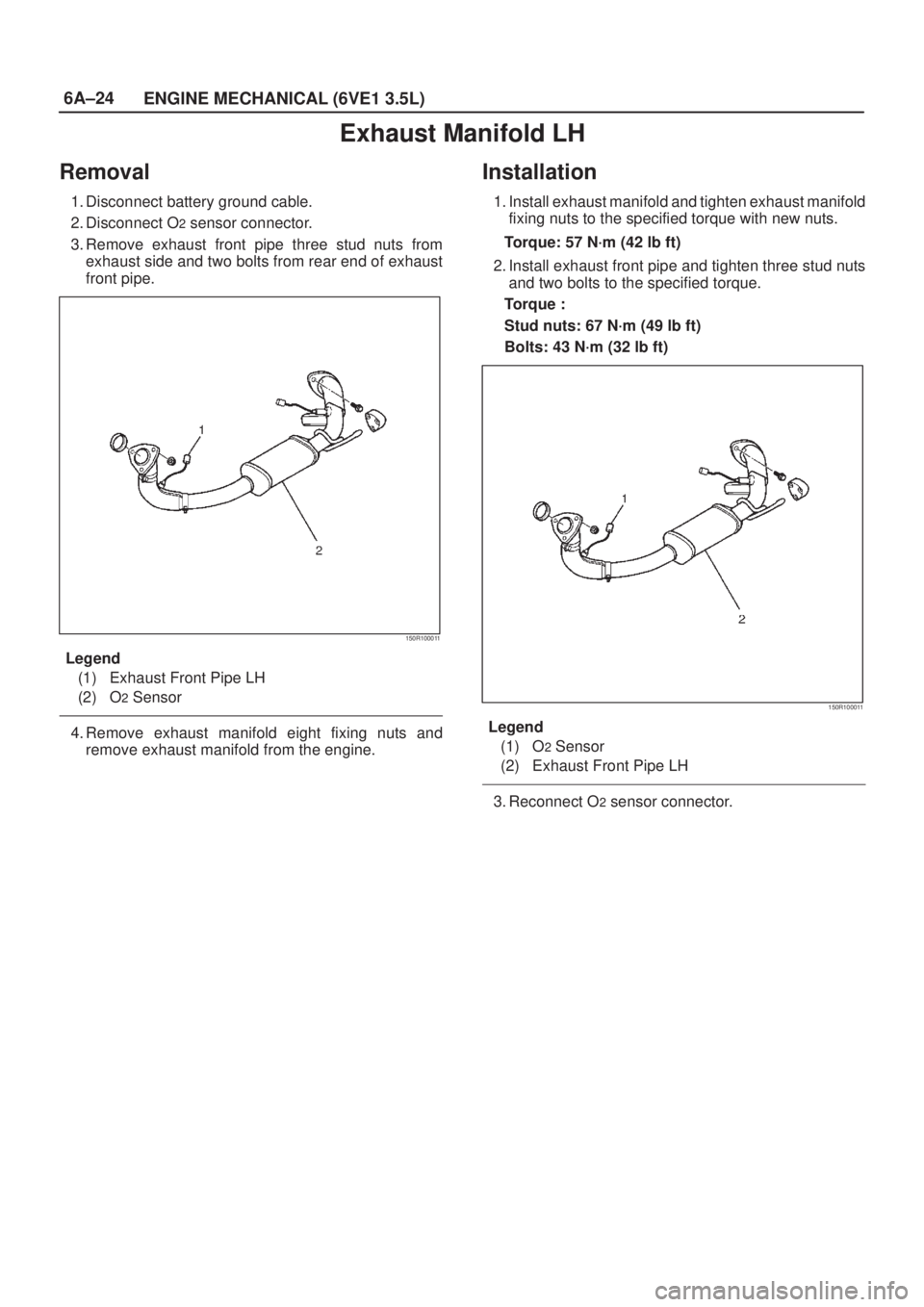
6A±24
ENGINE MECHANICAL (6VE1 3.5L)
Exhaust Manifold LH
Removal
1. Disconnect battery ground cable.
2. Disconnect O
2 sensor connector.
3. Remove exhaust front pipe three stud nuts from
exhaust side and two bolts from rear end of exhaust
front pipe.
150R100011
Legend
(1) Exhaust Front Pipe LH
(2) O
2 Sensor
4. Remove exhaust manifold eight fixing nuts and
remove exhaust manifold from the engine.
Installation
1. Install exhaust manifold and tighten exhaust manifold
fixing nuts to the specified torque with new nuts.
Torque: 57 N´m (42 lb ft)
2. Install exhaust front pipe and tighten three stud nuts
and two bolts to the specified torque.
Torque :
Stud nuts: 67 N´m (49 lb ft)
Bolts: 43 N´m (32 lb ft)
150R100011
Legend
(1) O
2 Sensor
(2) Exhaust Front Pipe LH
3. Reconnect O2 sensor connector.
Page 835 of 2100
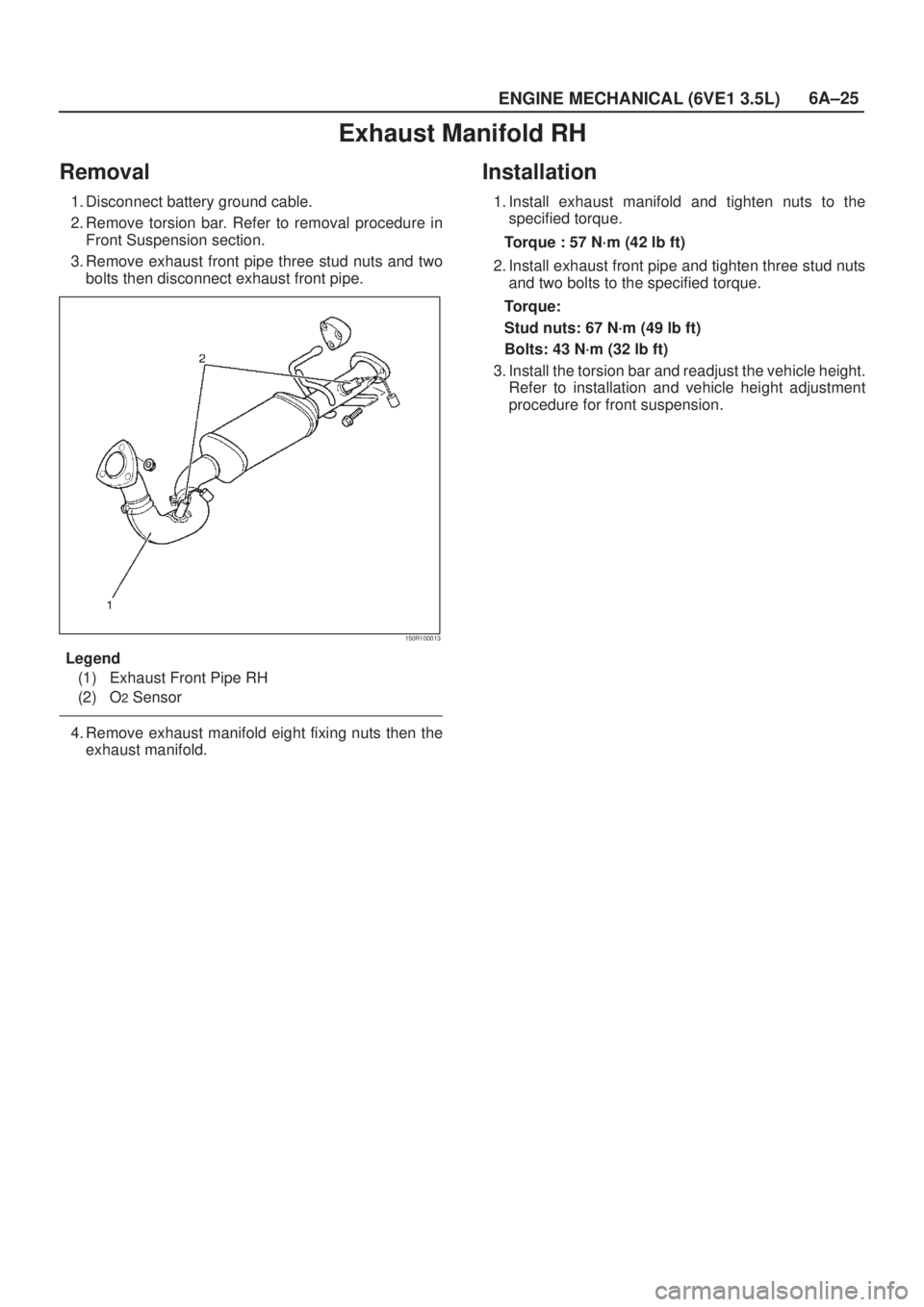
6A±25
ENGINE MECHANICAL (6VE1 3.5L)
Exhaust Manifold RH
Removal
1. Disconnect battery ground cable.
2. Remove torsion bar. Refer to removal procedure in
Front Suspension section.
3. Remove exhaust front pipe three stud nuts and two
bolts then disconnect exhaust front pipe.
150R100013
Legend
(1) Exhaust Front Pipe RH
(2) O
2 Sensor
4. Remove exhaust manifold eight fixing nuts then the
exhaust manifold.
Installation
1. Install exhaust manifold and tighten nuts to the
specified torque.
Torque : 57 N´m (42 lb ft)
2. Install exhaust front pipe and tighten three stud nuts
and two bolts to the specified torque.
Torque:
Stud nuts: 67 N´m (49 lb ft)
Bolts: 43 N´m (32 lb ft)
3. Install the torsion bar and readjust the vehicle height.
Refer to installation and vehicle height adjustment
procedure for front suspension.
Page 836 of 2100
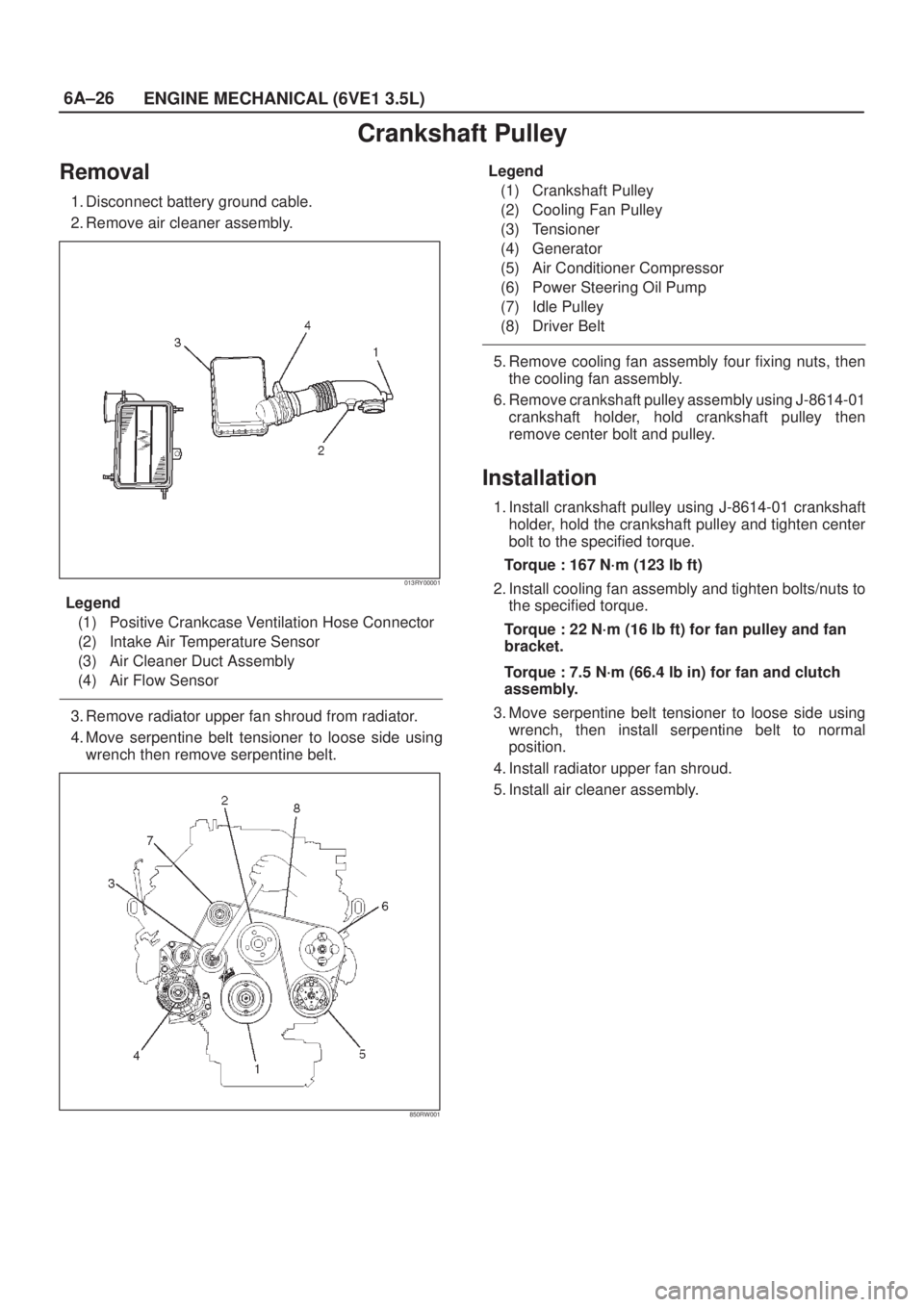
6A±26
ENGINE MECHANICAL (6VE1 3.5L)
Crankshaft Pulley
Removal
1. Disconnect battery ground cable.
2. Remove air cleaner assembly.
013RY00001
Legend
(1) Positive Crankcase Ventilation Hose Connector
(2) Intake Air Temperature Sensor
(3) Air Cleaner Duct Assembly
(4) Air Flow Sensor
3. Remove radiator upper fan shroud from radiator.
4. Move serpentine belt tensioner to loose side using
wrench then remove serpentine belt.
850RW001
Legend
(1) Crankshaft Pulley
(2) Cooling Fan Pulley
(3) Tensioner
(4) Generator
(5) Air Conditioner Compressor
(6) Power Steering Oil Pump
(7) Idle Pulley
(8) Driver Belt
5. Remove cooling fan assembly four fixing nuts, then
the cooling fan assembly.
6. Remove crankshaft pulley assembly using J-8614-01
crankshaft holder, hold crankshaft pulley then
remove center bolt and pulley.
Installation
1. Install crankshaft pulley using J-8614-01 crankshaft
holder, hold the crankshaft pulley and tighten center
bolt to the specified torque.
Torque : 167 N´m (123 lb ft)
2. Install cooling fan assembly and tighten bolts/nuts to
the specified torque.
Torque : 22 N´m (16 lb ft) for fan pulley and fan
bracket.
Torque : 7.5 N´m (66.4 lb in) for fan and clutch
assembly.
3. Move serpentine belt tensioner to loose side using
wrench, then install serpentine belt to normal
position.
4. Install radiator upper fan shroud.
5. Install air cleaner assembly.