engine ISUZU TF SERIES 2004 Workshop Manual
[x] Cancel search | Manufacturer: ISUZU, Model Year: 2004, Model line: TF SERIES, Model: ISUZU TF SERIES 2004Pages: 4264, PDF Size: 72.63 MB
Page 1197 of 4264
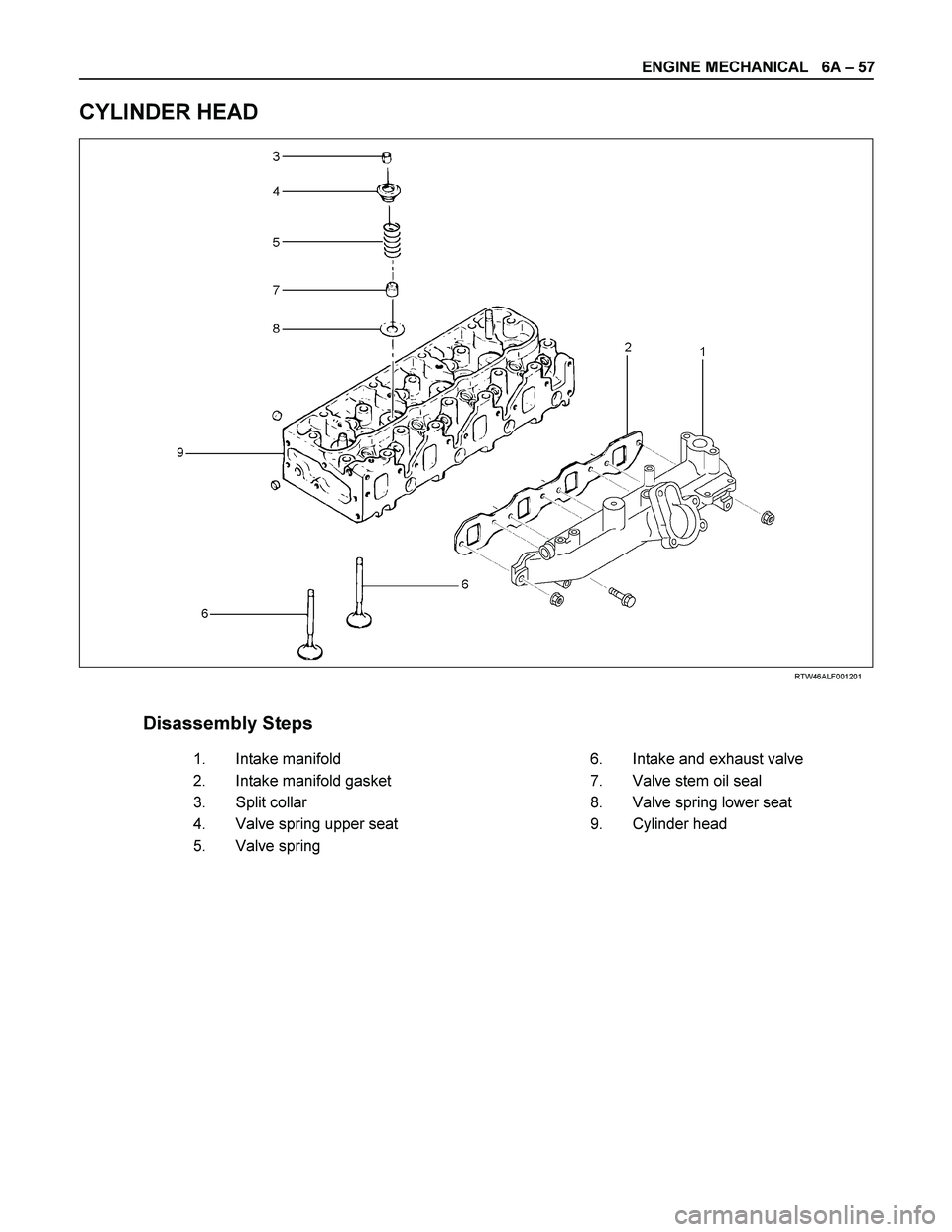
ENGINE MECHANICAL 6A – 57
CYLINDER HEAD
RTW46ALF001201
Disassembly Steps
1.
Intake manifold 6.
Intake and exhaust valve
2.
Intake manifold gasket 7.
Valve stem oil seal
3.
Split collar 8.
Valve spring lower seat
4.
Valve spring upper seat 9.
Cylinder head
5.
Valve spring
Page 1198 of 4264
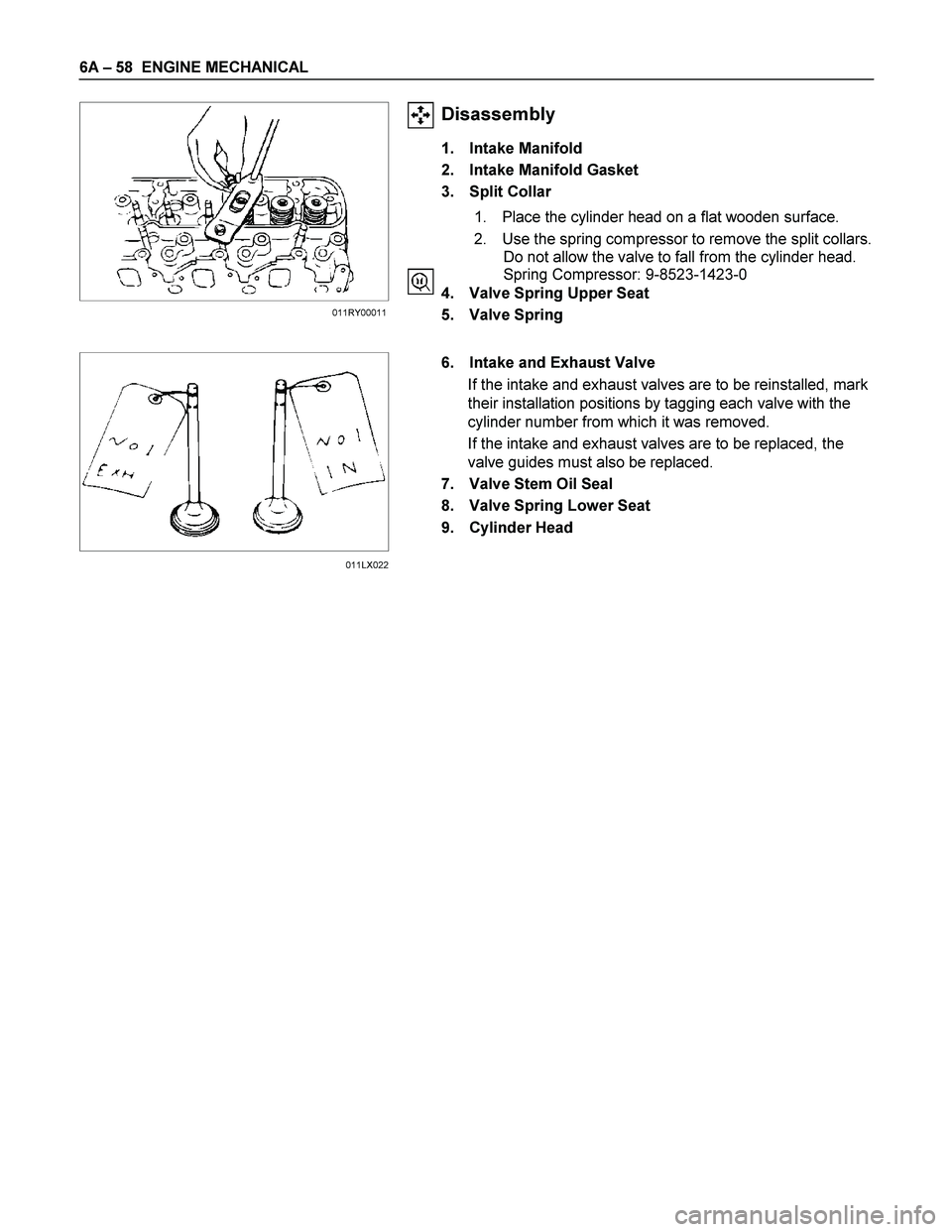
6A – 58 ENGINE MECHANICAL
Disassembly
1. Intake Manifold
2. Intake Manifold Gasket
3. Split Collar
1. Place the cylinder head on a flat wooden surface.
2. Use the spring compressor to remove the split collars.
Do not allow the valve to fall from the cylinder head.
Spring Compressor: 9-8523-1423-0
4. Valve Spring Upper Seat
5. Valve Spring
6. Intake and Exhaust Valve
If the intake and exhaust valves are to be reinstalled, mark
their installation positions by tagging each valve with the
cylinder number from which it was removed.
If the intake and exhaust valves are to be replaced, the
valve guides must also be replaced.
7. Valve Stem Oil Seal
8. Valve Spring Lower Seat
9. Cylinder Head
011RY00011
011LX022
Page 1199 of 4264
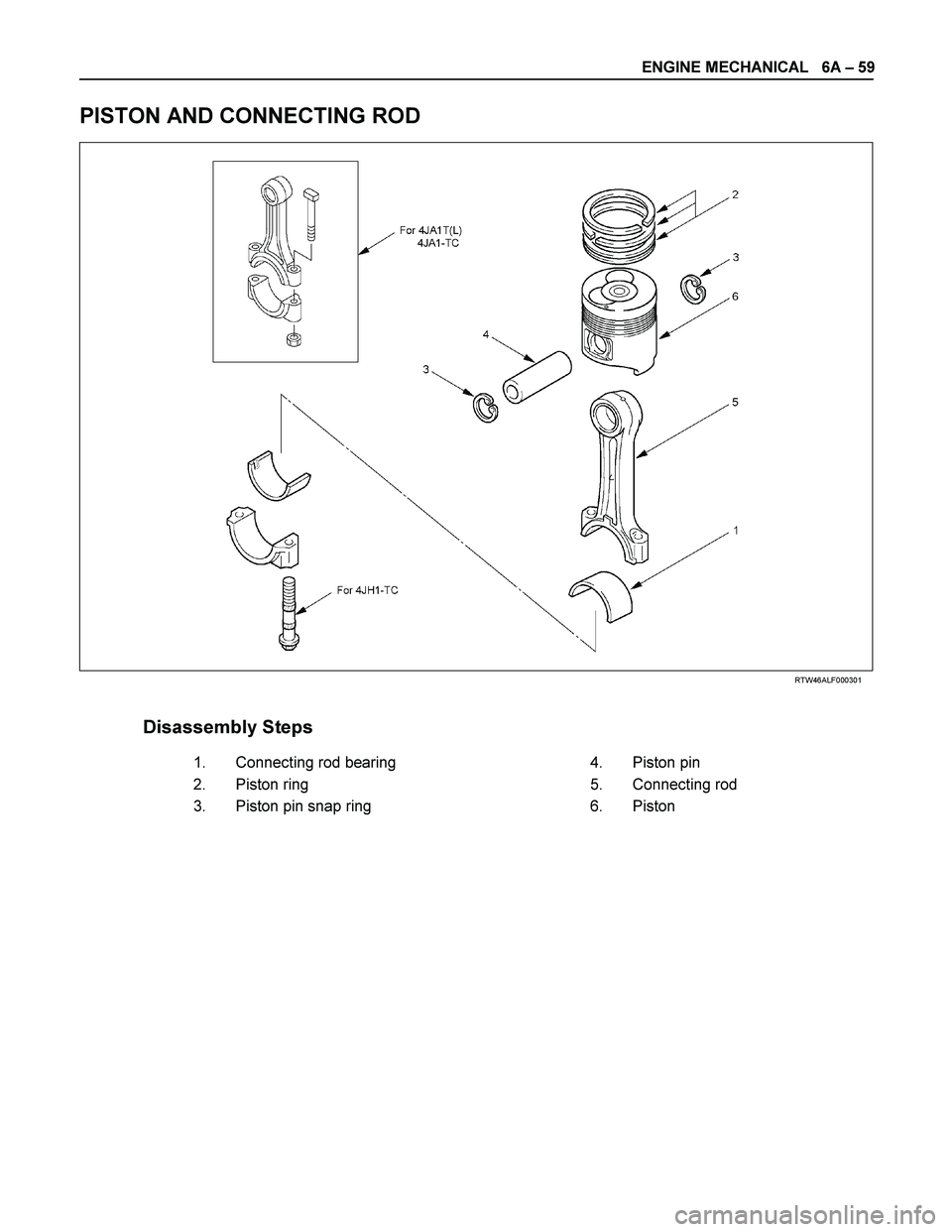
ENGINE MECHANICAL 6A – 59
PISTON AND CONNECTING ROD
RTW46ALF000301
Disassembly Steps
1.
Connecting rod bearing 4.
Piston pin
2.
Piston ring 5.
Connecting rod
3.
Piston pin snap ring 6.
Piston
Page 1200 of 4264
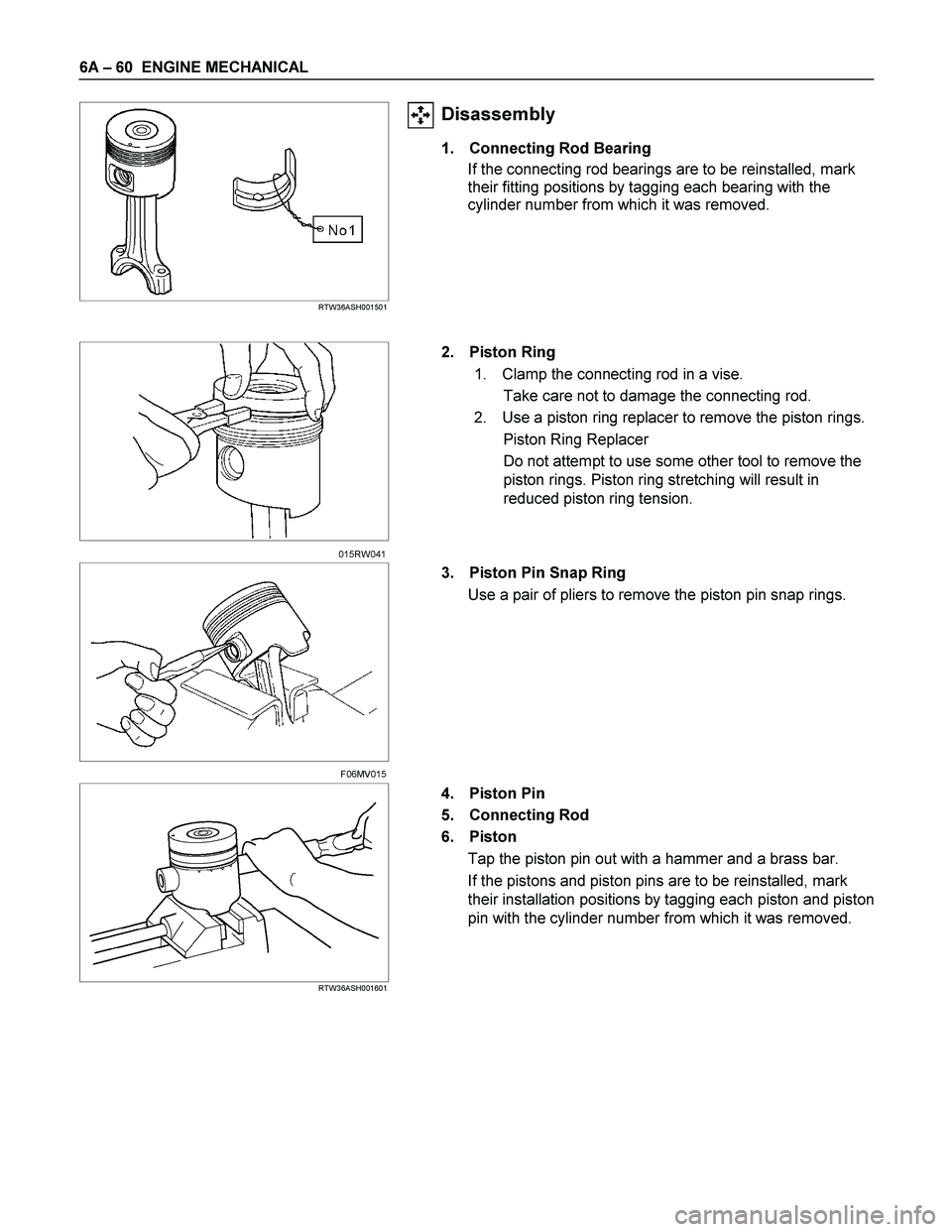
6A – 60 ENGINE MECHANICAL
RTW36ASH001501
Disassembly
1. Connecting Rod Bearing
If the connecting rod bearings are to be reinstalled, mark
their fitting positions by tagging each bearing with the
cylinder number from which it was removed.
2. Piston Ring
1. Clamp the connecting rod in a vise.
Take care not to damage the connecting rod.
2. Use a piston ring replacer to remove the piston rings.
Piston Ring Replacer
Do not attempt to use some other tool to remove the
piston rings. Piston ring stretching will result in
reduced piston ring tension.
3. Piston Pin Snap Ring
Use a pair of pliers to remove the piston pin snap rings.
RTW36ASH001601
4. Piston Pin
5. Connecting Rod
6. Piston
Tap the piston pin out with a hammer and a brass bar.
If the pistons and piston pins are to be reinstalled, mark
their installation positions by tagging each piston and piston
pin with the cylinder number from which it was removed.
015RW041
F06MV015
Page 1201 of 4264
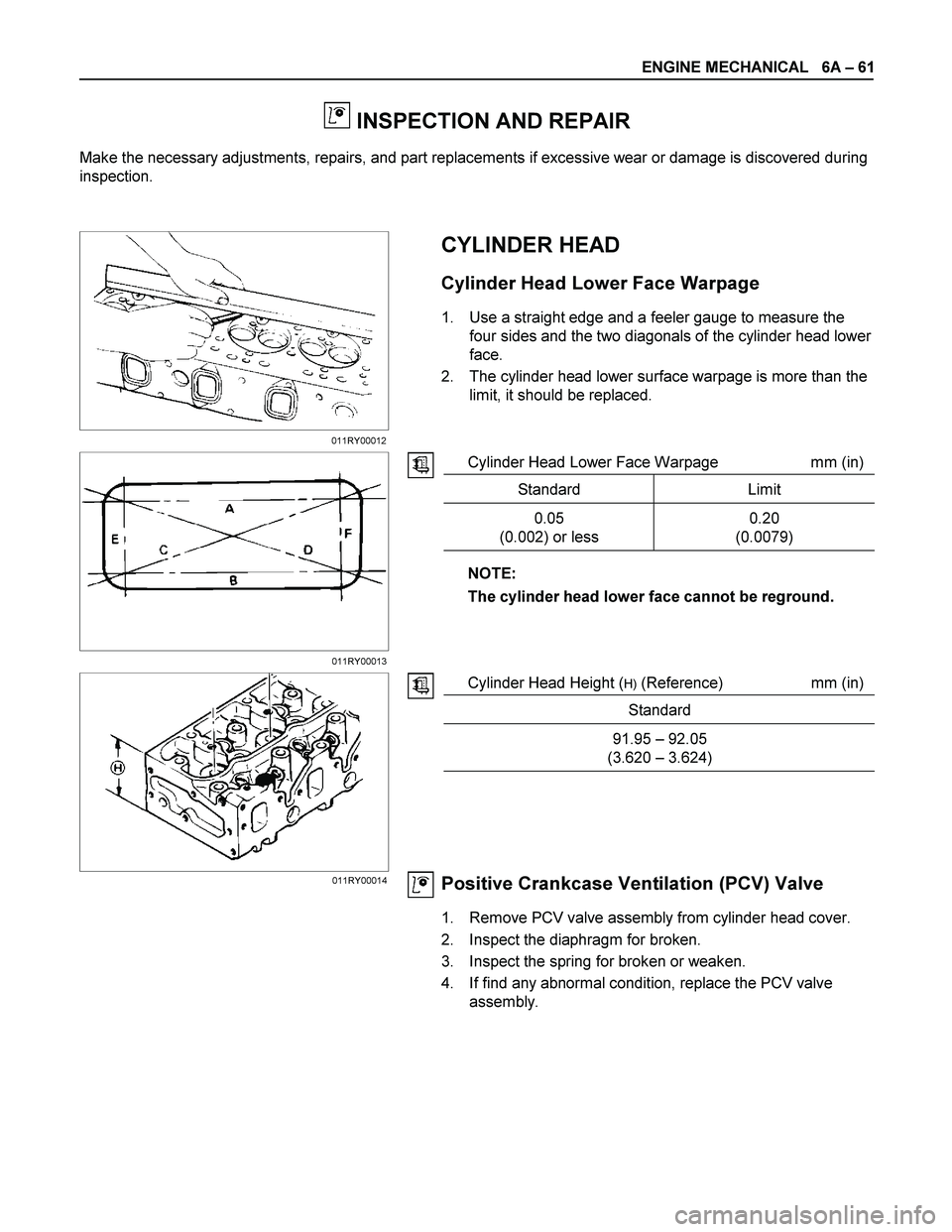
ENGINE MECHANICAL 6A – 61
INSPECTION AND REPAIR
Make the necessary adjustments, repairs, and part replacements if excessive wear or damage is discovered during
inspection.
CYLINDER HEAD
Cylinder Head Lower Face Warpage
1. Use a straight edge and a feeler gauge to measure the
four sides and the two diagonals of the cylinder head lower
face.
2. The cylinder head lower surface warpage is more than the
limit, it should be replaced.
Cylinder Head Lower Face Warpage mm (in)
Standard Limit
0.05
(0.002) or less 0.20
(0.0079)
NOTE:
The cylinder head lower face cannot be reground.
Cylinder Head Height (
H) (Reference) mm (in)
Standard
91.95 – 92.05
(3.620 – 3.624)
Positive Crankcase Ventilation (PCV) Valve
1. Remove PCV valve assembly from cylinder head cover.
2. Inspect the diaphragm for broken.
3. Inspect the spring for broken or weaken.
4. If find any abnormal condition, replace the PCV valve
assembly.
011RY00012
011RY00013
011RY00014
Page 1202 of 4264
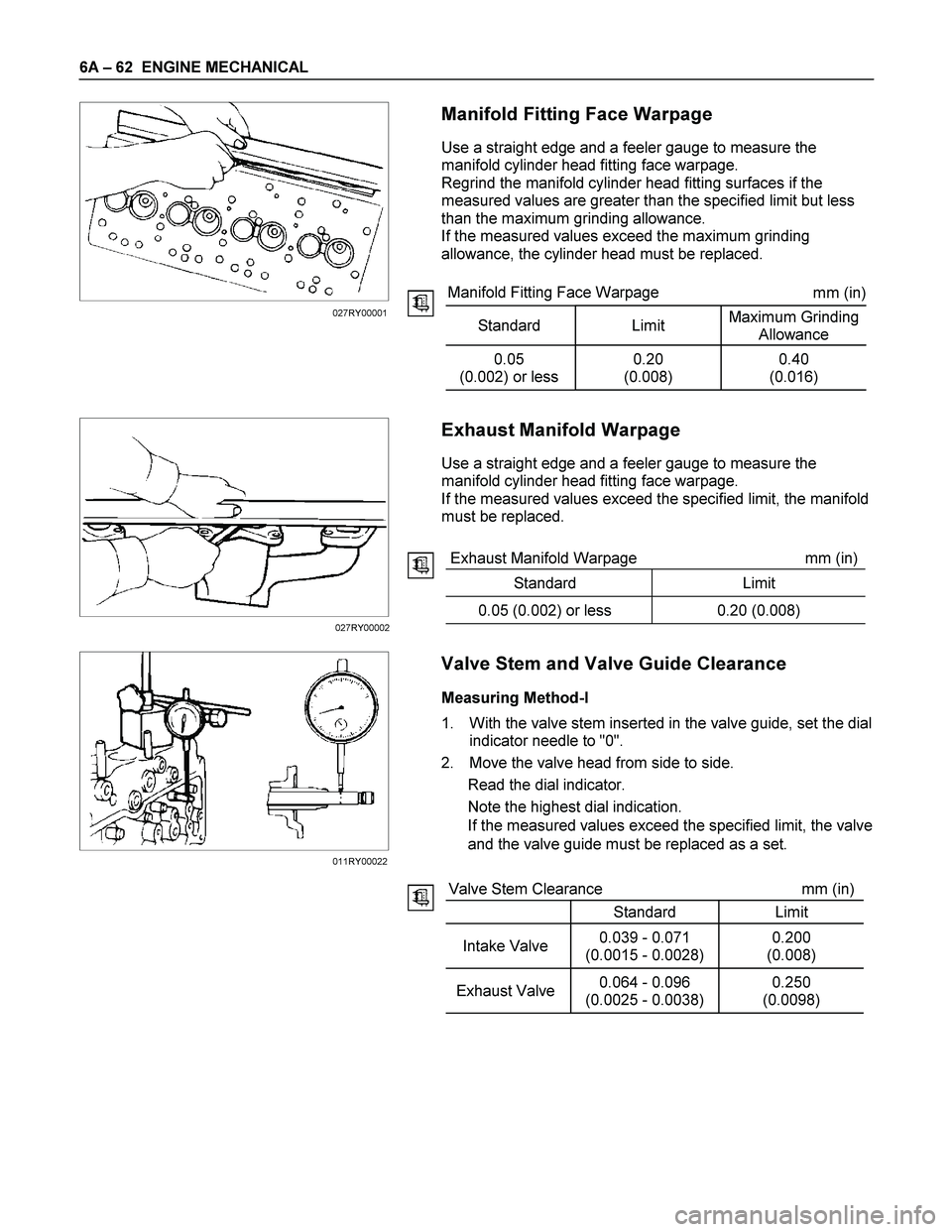
6A – 62 ENGINE MECHANICAL
Manifold Fitting Face Warpage
Use a straight edge and a feeler gauge to measure the
manifold cylinder head fitting face warpage.
Regrind the manifold cylinder head fitting surfaces if the
measured values are greater than the specified limit but less
than the maximum grinding allowance.
If the measured values exceed the maximum grinding
allowance, the cylinder head must be replaced.
Manifold Fitting Face Warpage
mm (in)
Standard Limit Maximum Grinding
Allowance
0.05
(0.002) or less 0.20
(0.008) 0.40
(0.016)
Exhaust Manifold Warpage
Use a straight edge and a feeler gauge to measure the
manifold cylinder head fitting face warpage.
If the measured values exceed the specified limit, the manifold
must be replaced.
Exhaust Manifold Warpage mm (in)
Standard Limit
0.05 (0.002) or less 0.20 (0.008)
Valve Stem and Valve Guide Clearance
Measuring Method-I
1. With the valve stem inserted in the valve guide, set the dial
indicator needle to "0".
2. Move the valve head from side to side.
Read the dial indicator.
Note the highest dial indication.
If the measured values exceed the specified limit, the valve
and the valve guide must be replaced as a set.
Valve Stem Clearance mm (in)
Standard Limit
Intake Valve 0.039 - 0.071
(0.0015 - 0.0028) 0.200
(0.008)
Exhaust Valve 0.064 - 0.096
(0.0025 - 0.0038) 0.250
(0.0098)
027RY00001
027RY00002
011RY00022
Page 1203 of 4264
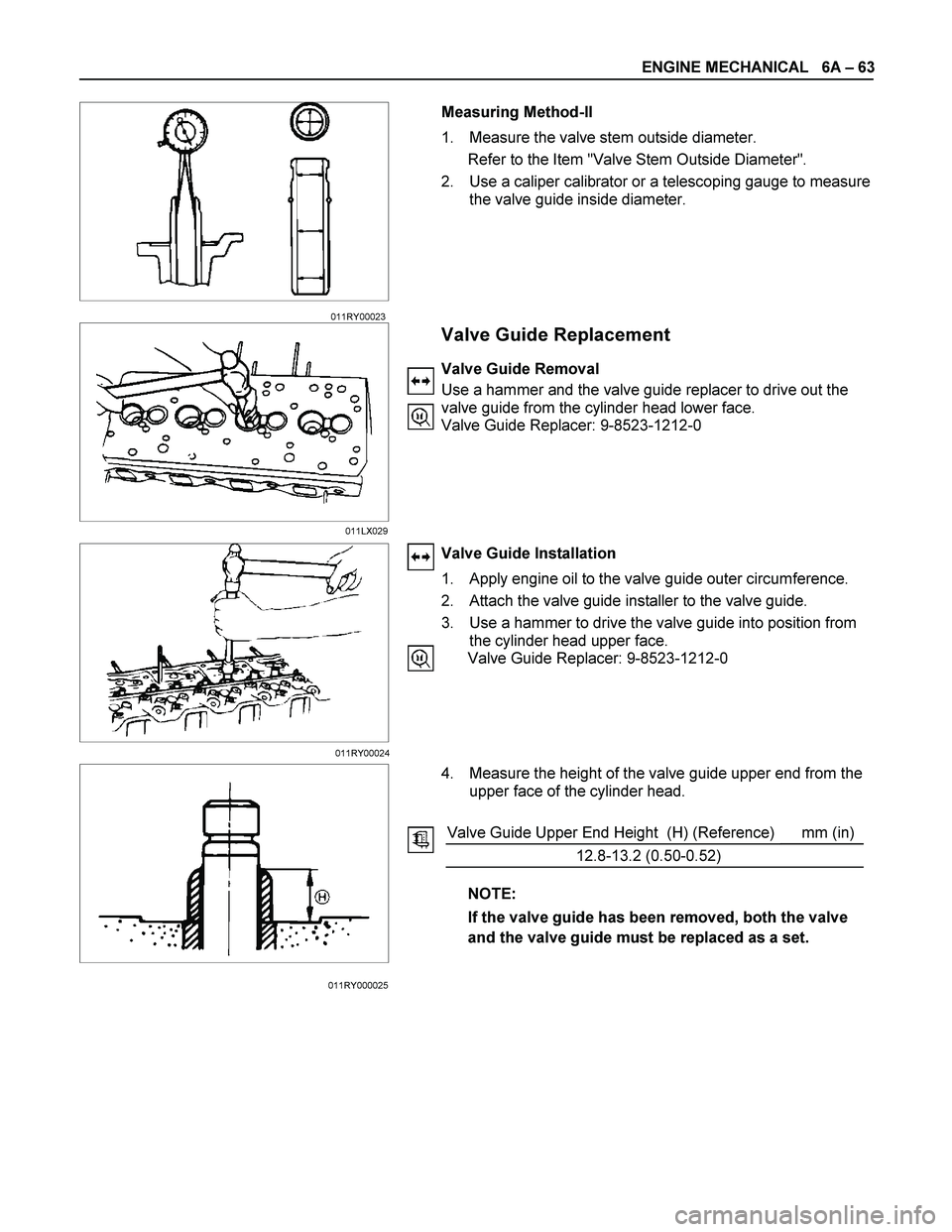
ENGINE MECHANICAL 6A – 63
Measuring Method-II
1. Measure the valve stem outside diameter.
Refer to the Item "Valve Stem Outside Diameter".
2. Use a caliper calibrator or a telescoping gauge to measure
the valve guide inside diameter.
Valve Guide Replacement
Valve Guide Removal
Use a hammer and the valve guide replacer to drive out the
valve guide from the cylinder head lower face.
Valve Guide Replacer: 9-8523-1212-0
Valve Guide Installation
1. Apply engine oil to the valve guide outer circumference.
2. Attach the valve guide installer to the valve guide.
3. Use a hammer to drive the valve guide into position from
the cylinder head upper face.
Valve Guide Replacer: 9-8523-1212-0
4. Measure the height of the valve guide upper end from the
upper face of the cylinder head.
Valve Guide Upper End Height (H) (Reference) mm (in)
12.8-13.2 (0.50-0.52)
NOTE:
If the valve guide has been removed, both the valve
and the valve guide must be replaced as a set.
011LX029
011RY00024
011RY000025011RY00023
Page 1204 of 4264
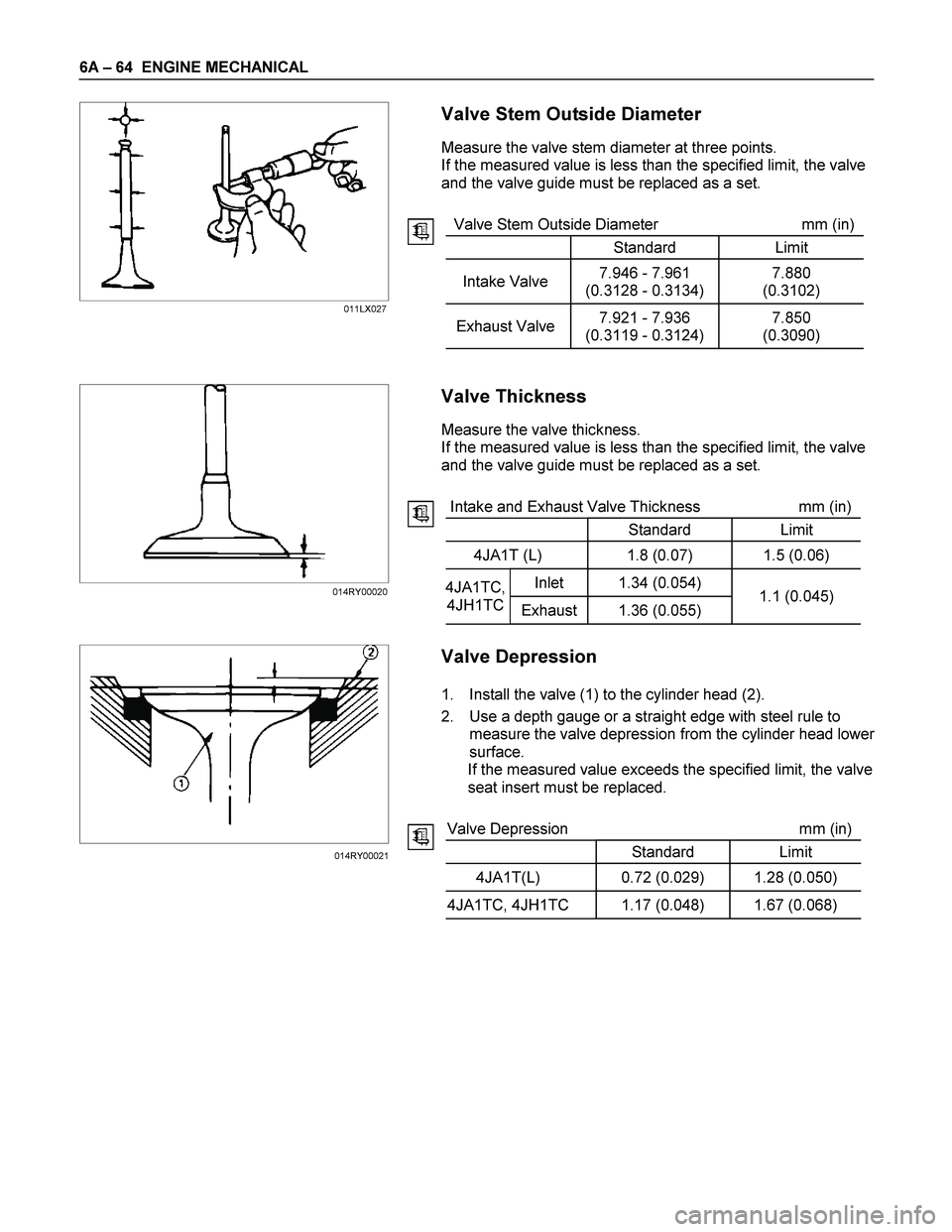
6A – 64 ENGINE MECHANICAL
Valve Stem Outside Diameter
Measure the valve stem diameter at three points.
If the measured value is less than the specified limit, the valve
and the valve guide must be replaced as a set.
Valve Stem Outside Diameter mm (in)
Standard Limit
Intake Valve 7.946 - 7.961
(0.3128 - 0.3134) 7.880
(0.3102)
Exhaust Valve 7.921 - 7.936
(0.3119 - 0.3124) 7.850
(0.3090)
Valve Thickness
Measure the valve thickness.
If the measured value is less than the specified limit, the valve
and the valve guide must be replaced as a set.
Intake and Exhaust Valve Thickness mm (in)
Standard Limit
4JA1T (L) 1.8 (0.07) 1.5 (0.06)
Inlet 1.34 (0.054) 4JA1TC,
4JH1TC
Exhaust 1.36 (0.055) 1.1 (0.045)
Valve Depression
1. Install the valve (1) to the cylinder head (2).
2. Use a depth gauge or a straight edge with steel rule to
measure the valve depression from the cylinder head lowe
r
surface.
If the measured value exceeds the specified limit, the valve
seat insert must be replaced.
Valve Depression mm (in)
Standard Limit
4JA1T(L) 0.72 (0.029) 1.28 (0.050)
4JA1TC, 4JH1TC 1.17 (0.048) 1.67 (0.068)
011LX027
014RY00020
014RY00021
Page 1205 of 4264
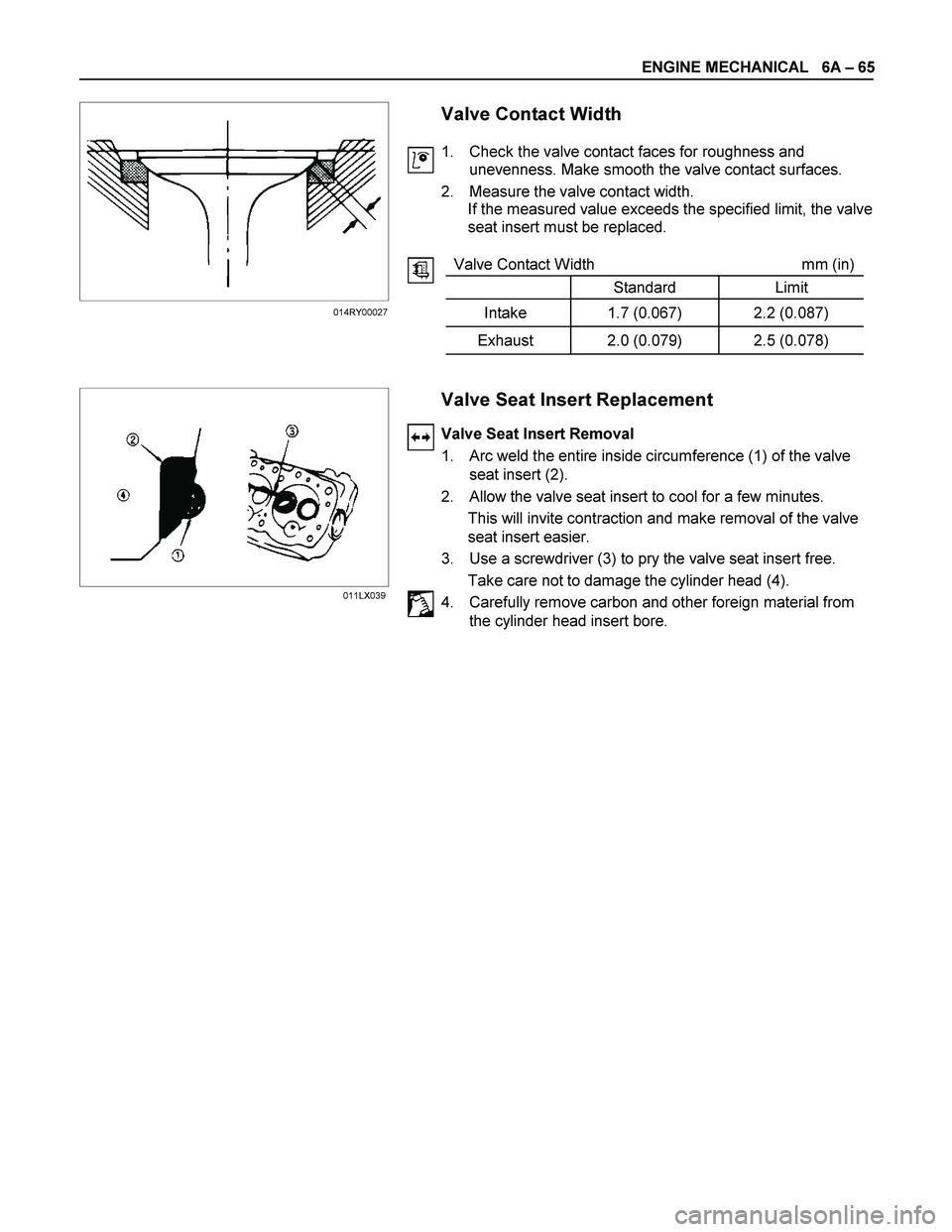
ENGINE MECHANICAL 6A – 65
Valve Contact Width
1. Check the valve contact faces for roughness and
unevenness. Make smooth the valve contact surfaces.
2. Measure the valve contact width.
If the measured value exceeds the specified limit, the valve
seat insert must be replaced.
Valve Contact Width mm (in)
Standard Limit
Intake 1.7 (0.067) 2.2 (0.087)
Exhaust 2.0 (0.079) 2.5 (0.078)
Valve Seat Insert Replacement
Valve Seat Insert Removal
1. Arc weld the entire inside circumference (1) of the valve
seat insert (2).
2. Allow the valve seat insert to cool for a few minutes.
This will invite contraction and make removal of the valve
seat insert easier.
3. Use a screwdriver (3) to pry the valve seat insert free.
Take care not to damage the cylinder head (4).
4. Carefully remove carbon and other foreign material from
the cylinder head insert bore.
014RY00027
011LX039
Page 1206 of 4264
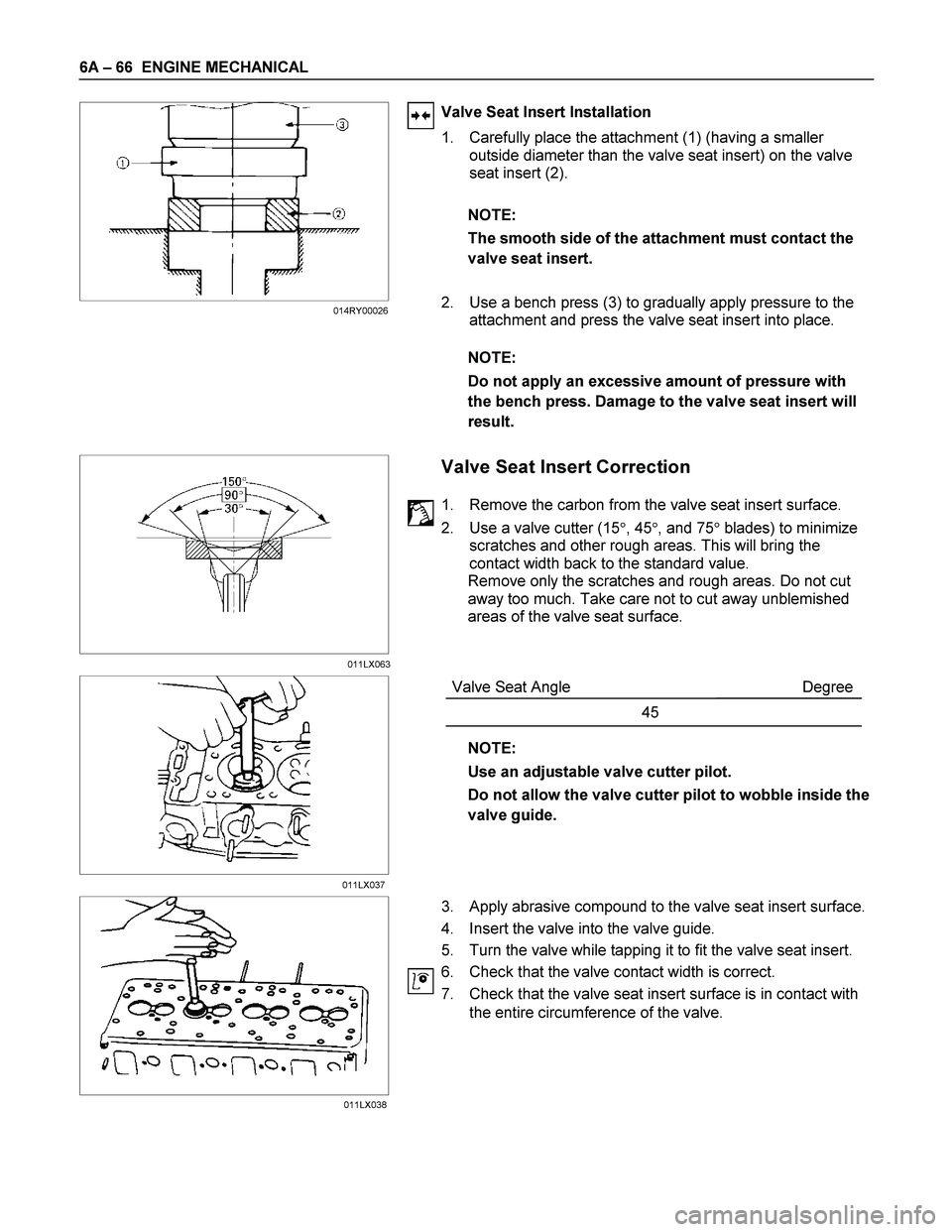
6A – 66 ENGINE MECHANICAL
Valve Seat Insert Installation
1. Carefully place the attachment (1) (having a smaller
outside diameter than the valve seat insert) on the valve
seat insert (2).
NOTE:
The smooth side of the attachment must contact the
valve seat insert.
2. Use a bench press (3) to gradually apply pressure to the
attachment and press the valve seat insert into place.
NOTE:
Do not apply an excessive amount of pressure with
the bench press. Damage to the valve seat insert will
result.
Valve Seat Insert Correction
1. Remove the carbon from the valve seat insert surface.
2. Use a valve cutter (15, 45, and 75 blades) to minimize
scratches and other rough areas. This will bring the
contact width back to the standard value.
Remove only the scratches and rough areas. Do not cut
away too much. Take care not to cut away unblemished
areas of the valve seat surface.
Valve Seat Angle Degree
45
NOTE:
Use an adjustable valve cutter pilot.
Do not allow the valve cutter pilot to wobble inside the
valve guide.
3. Apply abrasive compound to the valve seat insert surface.
4. Insert the valve into the valve guide.
5. Turn the valve while tapping it to fit the valve seat insert.
6. Check that the valve contact width is correct.
7. Check that the valve seat insert surface is in contact with
the entire circumference of the valve.
011LX063 014RY00026
011LX037
011LX038