engine ISUZU TF SERIES 2004 Workshop Manual
[x] Cancel search | Manufacturer: ISUZU, Model Year: 2004, Model line: TF SERIES, Model: ISUZU TF SERIES 2004Pages: 4264, PDF Size: 72.63 MB
Page 1227 of 4264
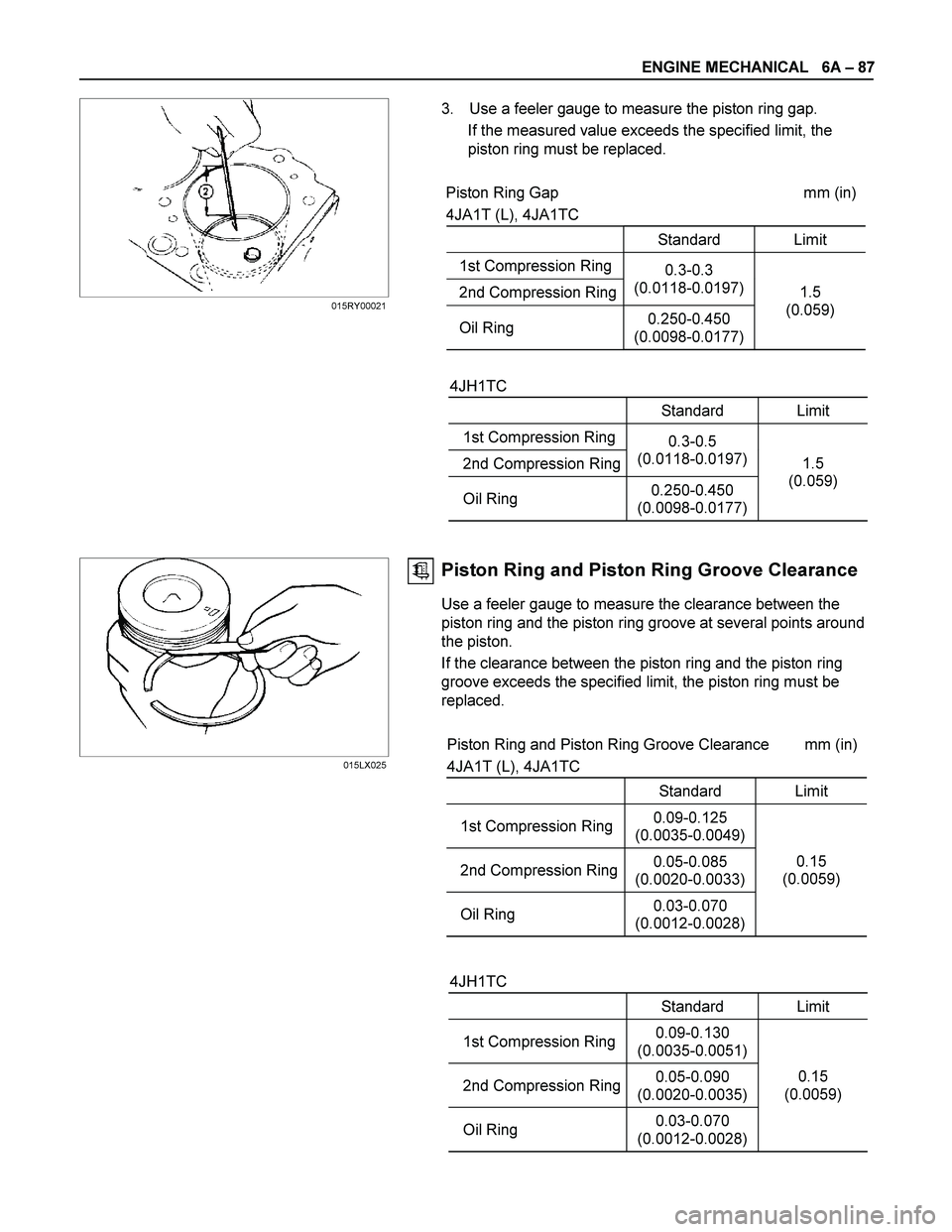
ENGINE MECHANICAL 6A – 87
3. Use a feeler gauge to measure the piston ring gap.
If the measured value exceeds the specified limit, the
piston ring must be replaced.
Piston Ring Gap mm (in)
4JA1T (L), 4JA1TC
Standard Limit
1st Compression Ring
2nd Compression Ring0.3-0.3
(0.0118-0.0197)
Oil Ring 0.250-0.450
(0.0098-0.0177) 1.5
(0.059)
4JH1TC
Standard Limit
1st Compression Ring
2nd Compression Ring0.3-0.5
(0.0118-0.0197)
Oil Ring 0.250-0.450
(0.0098-0.0177) 1.5
(0.059)
Piston Ring and Piston Ring Groove Clearance
Use a feeler gauge to measure the clearance between the
piston ring and the piston ring groove at several points around
the piston.
If the clearance between the piston ring and the piston ring
groove exceeds the specified limit, the piston ring must be
replaced.
Piston Ring and Piston Ring Groove Clearance mm (in)
4JA1T (L), 4JA1TC
Standard Limit
1st Compression Ring0.09-0.125
(0.0035-0.0049)
2nd Compression Ring0.05-0.085
(0.0020-0.0033)
Oil Ring 0.03-0.070
(0.0012-0.0028) 0.15
(0.0059)
4JH1TC
Standard Limit
1st Compression Ring0.09-0.130
(0.0035-0.0051)
2nd Compression Ring0.05-0.090
(0.0020-0.0035)
Oil Ring 0.03-0.070
(0.0012-0.0028) 0.15
(0.0059)
015RY00021
015LX025
Page 1228 of 4264
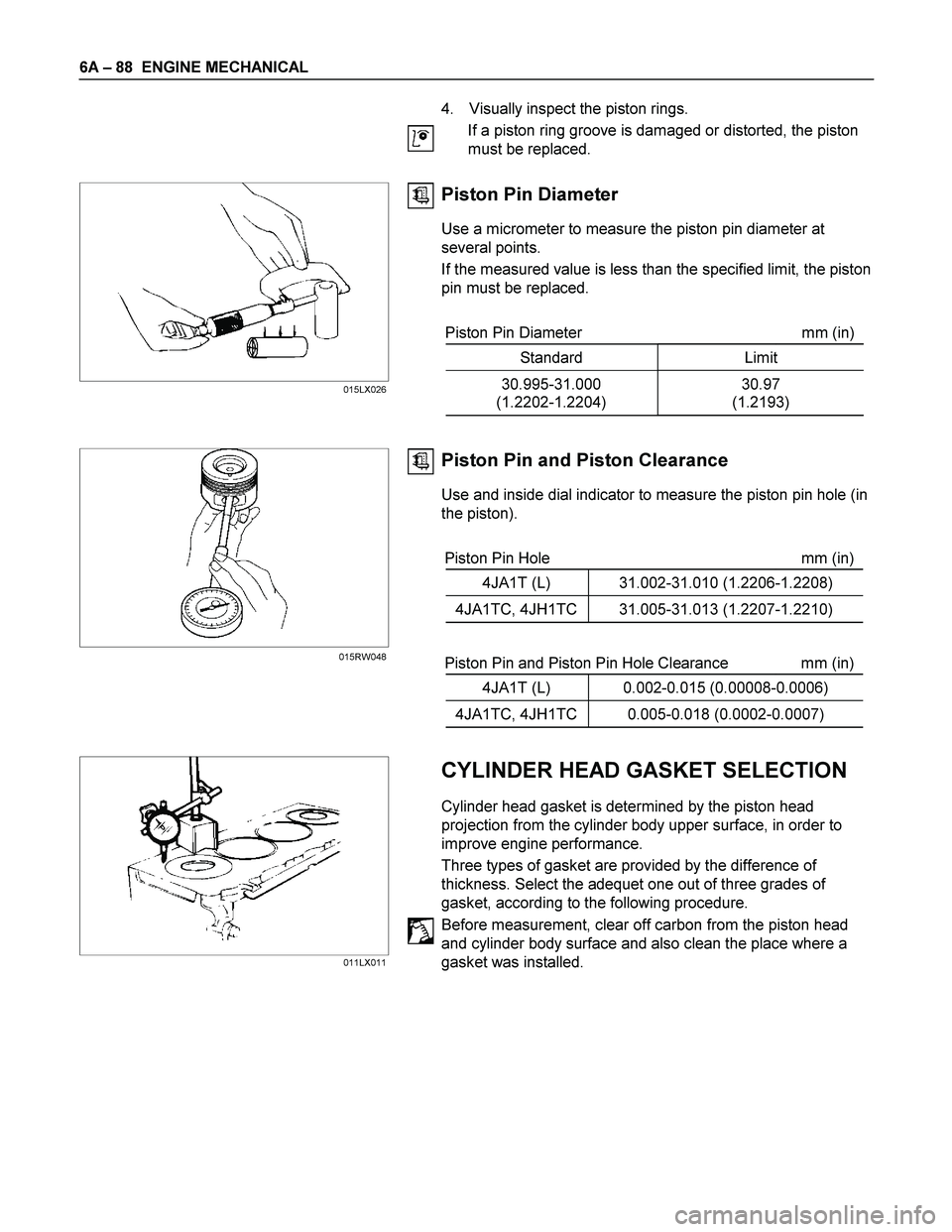
6A – 88 ENGINE MECHANICAL
4. Visually inspect the piston rings.
If a piston ring groove is damaged or distorted, the piston
must be replaced.
Piston Pin Diameter
Use a micrometer to measure the piston pin diameter at
several points.
If the measured value is less than the specified limit, the piston
pin must be replaced.
Piston Pin Diameter mm (in)
Standard Limit
30.995-31.000
(1.2202-1.2204) 30.97
(1.2193)
Piston Pin and Piston Clearance
Use and inside dial indicator to measure the piston pin hole (in
the piston).
Piston Pin Hole mm (in)
4JA1T (L) 31.002-31.010 (1.2206-1.2208)
4JA1TC, 4JH1TC 31.005-31.013 (1.2207-1.2210)
Piston Pin and Piston Pin Hole Clearance mm (in)
4JA1T (L) 0.002-0.015 (0.00008-0.0006)
4JA1TC, 4JH1TC 0.005-0.018 (0.0002-0.0007)
CYLINDER HEAD GASKET SELECTION
Cylinder head gasket is determined by the piston head
projection from the cylinder body upper surface, in order to
improve engine performance.
Three types of gasket are provided by the difference of
thickness. Select the adequet one out of three grades of
gasket, according to the following procedure.
Before measurement, clear off carbon from the piston head
and cylinder body surface and also clean the place where a
gasket was installed.
015LX026
015RW048
011LX011
Page 1229 of 4264
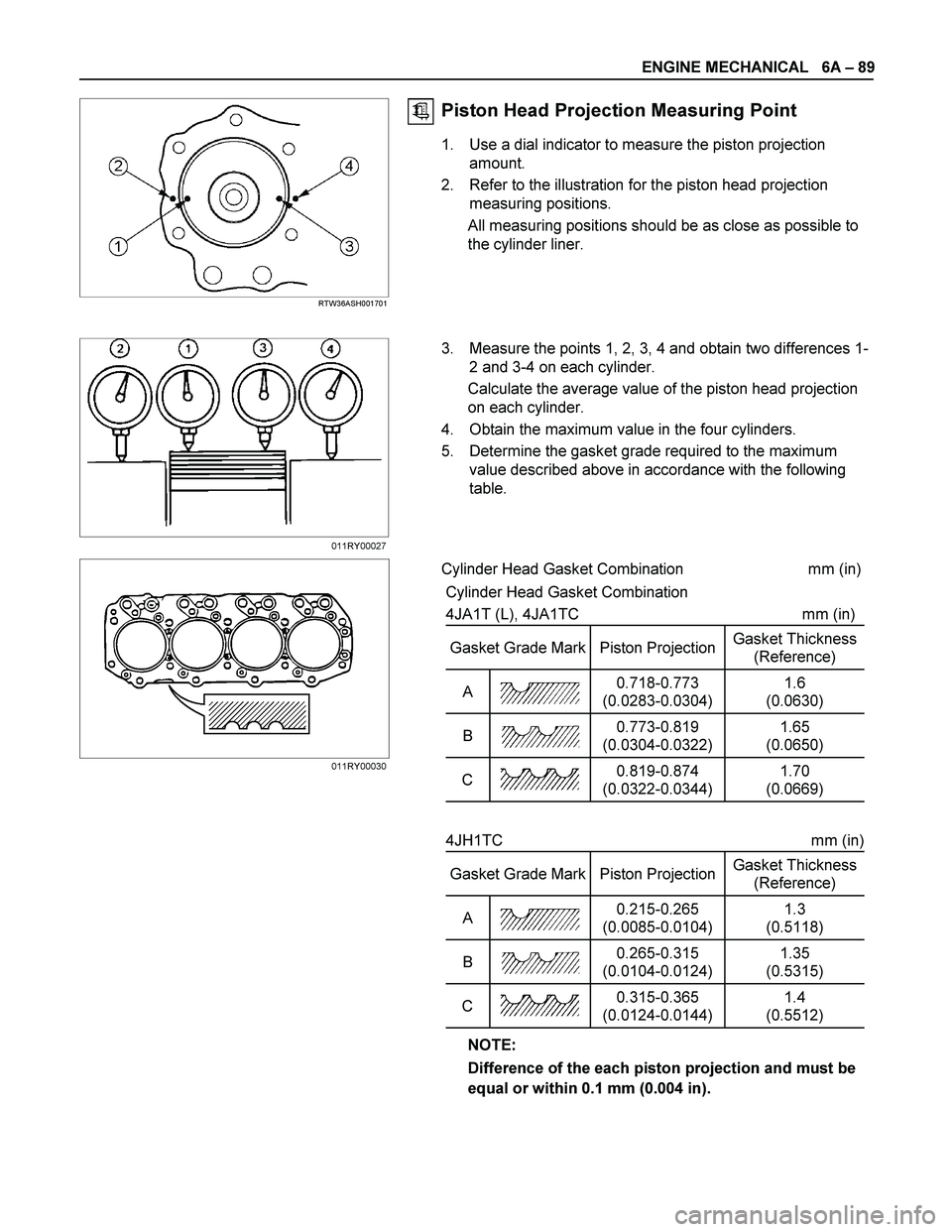
ENGINE MECHANICAL 6A – 89
RTW36ASH001701
Piston Head Projection Measuring Point
1. Use a dial indicator to measure the piston projection
amount.
2. Refer to the illustration for the piston head projection
measuring positions.
All measuring positions should be as close as possible to
the cylinder liner.
3. Measure the points 1, 2, 3, 4 and obtain two differences 1-
2 and 3-4 on each cylinder.
Calculate the average value of the piston head projection
on each cylinder.
4. Obtain the maximum value in the four cylinders.
5. Determine the gasket grade required to the maximum
value described above in accordance with the following
table.
Cylinder Head Gasket Combination mm (in)
Cylinder Head Gasket Combination
4JA1T (L), 4JA1TC mm (in)
Gasket Grade Mark Piston Projection Gasket Thickness
(Reference)
A 0.718-0.773
(0.0283-0.0304) 1.6
(0.0630)
B 0.773-0.819
(0.0304-0.0322) 1.65
(0.0650)
C 0.819-0.874
(0.0322-0.0344) 1.70
(0.0669)
4JH1TC mm (in)
Gasket Grade Mark Piston Projection Gasket Thickness
(Reference)
A 0.215-0.265
(0.0085-0.0104) 1.3
(0.5118)
B 0.265-0.315
(0.0104-0.0124) 1.35
(0.5315)
C 0.315-0.365
(0.0124-0.0144) 1.4
(0.5512)
NOTE:
Difference of the each piston projection and must be
equal or within 0.1 mm (0.004 in).
011RY00027
011RY00030
Page 1230 of 4264
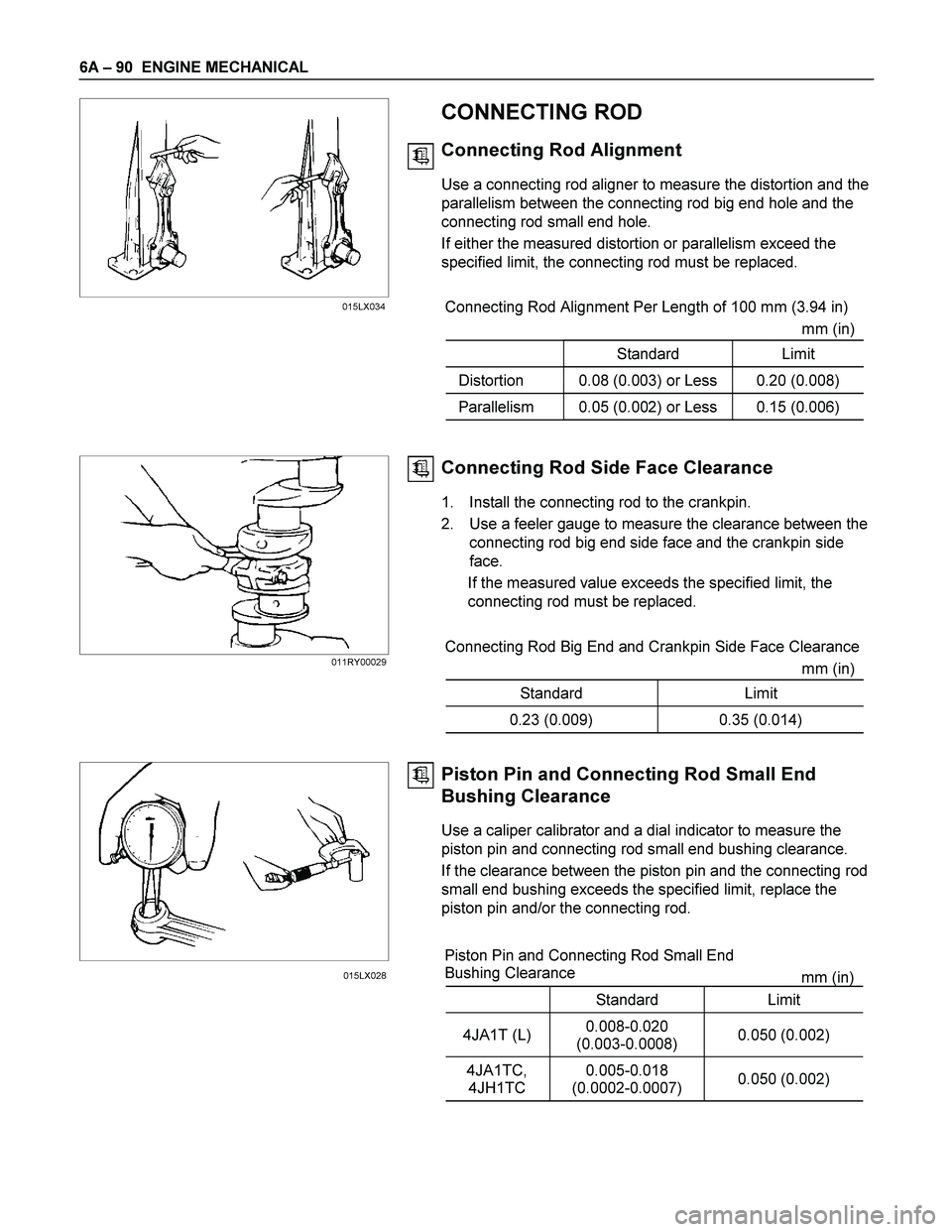
6A – 90 ENGINE MECHANICAL
CONNECTING ROD
Connecting Rod Alignment
Use a connecting rod aligner to measure the distortion and the
parallelism between the connecting rod big end hole and the
connecting rod small end hole.
If either the measured distortion or parallelism exceed the
specified limit, the connecting rod must be replaced.
Connecting Rod Alignment Per Length of 100 mm (3.94 in)
mm (in)
Standard Limit
Distortion 0.08 (0.003) or Less 0.20 (0.008)
Parallelism 0.05 (0.002) or Less 0.15 (0.006)
Connecting Rod Side Face Clearance
1. Install the connecting rod to the crankpin.
2. Use a feeler gauge to measure the clearance between the
connecting rod big end side face and the crankpin side
face.
If the measured value exceeds the specified limit, the
connecting rod must be replaced.
Connecting Rod Big End and Crankpin Side Face Clearance
mm (in)
Standard Limit
0.23 (0.009) 0.35 (0.014)
Piston Pin and Connecting Rod Small End
Bushing Clearance
Use a caliper calibrator and a dial indicator to measure the
piston pin and connecting rod small end bushing clearance.
If the clearance between the piston pin and the connecting rod
small end bushing exceeds the specified limit, replace the
piston pin and/or the connecting rod.
Piston Pin and Connecting Rod Small End
Bushing Clearance
mm (in)
Standard Limit
4JA1T (L) 0.008-0.020
(0.003-0.0008) 0.050 (0.002)
4JA1TC,
4JH1TC 0.005-0.018
(0.0002-0.0007) 0.050 (0.002)
015LX034
011RY00029
015LX028
Page 1231 of 4264
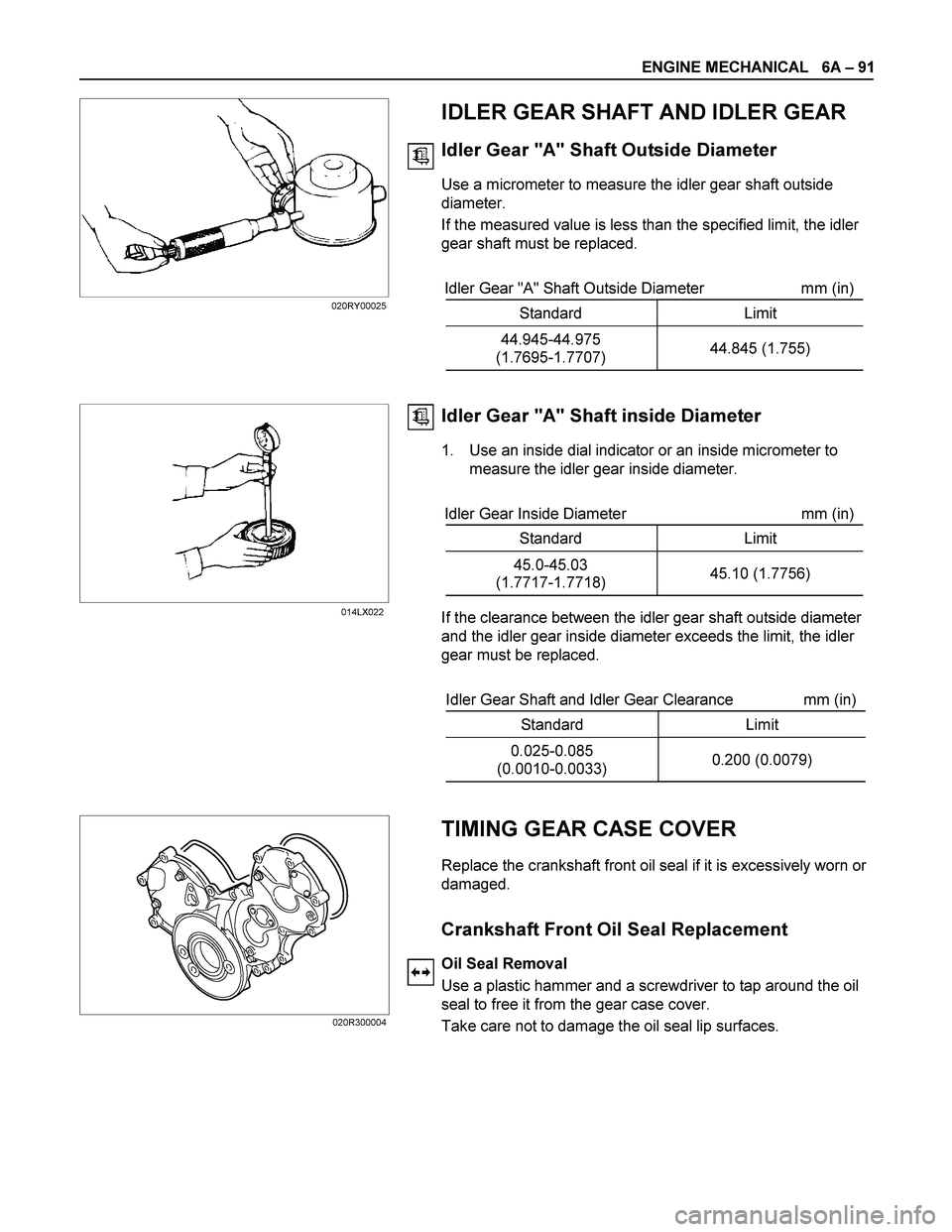
ENGINE MECHANICAL 6A – 91
IDLER GEAR SHAFT AND IDLER GEAR
Idler Gear "A" Shaft Outside Diameter
Use a micrometer to measure the idler gear shaft outside
diameter.
If the measured value is less than the specified limit, the idler
gear shaft must be replaced.
Idler Gear "A" Shaft Outside Diameter mm (in)
Standard Limit
44.945-44.975
(1.7695-1.7707) 44.845 (1.755)
Idler Gear "A" Shaft inside Diameter
1. Use an inside dial indicator or an inside micrometer to
measure the idler gear inside diameter.
Idler Gear Inside Diameter mm (in)
Standard Limit
45.0-45.03
(1.7717-1.7718) 45.10 (1.7756)
If the clearance between the idler gear shaft outside diameter
and the idler gear inside diameter exceeds the limit, the idler
gear must be replaced.
Idler Gear Shaft and Idler Gear Clearance mm (in)
Standard Limit
0.025-0.085
(0.0010-0.0033) 0.200 (0.0079)
TIMING GEAR CASE COVER
Replace the crankshaft front oil seal if it is excessively worn or
damaged.
Crankshaft Front Oil Seal Replacement
Oil Seal Removal
Use a plastic hammer and a screwdriver to tap around the oil
seal to free it from the gear case cover.
Take care not to damage the oil seal lip surfaces.
020RY00025
014LX022
020R300004
Page 1232 of 4264
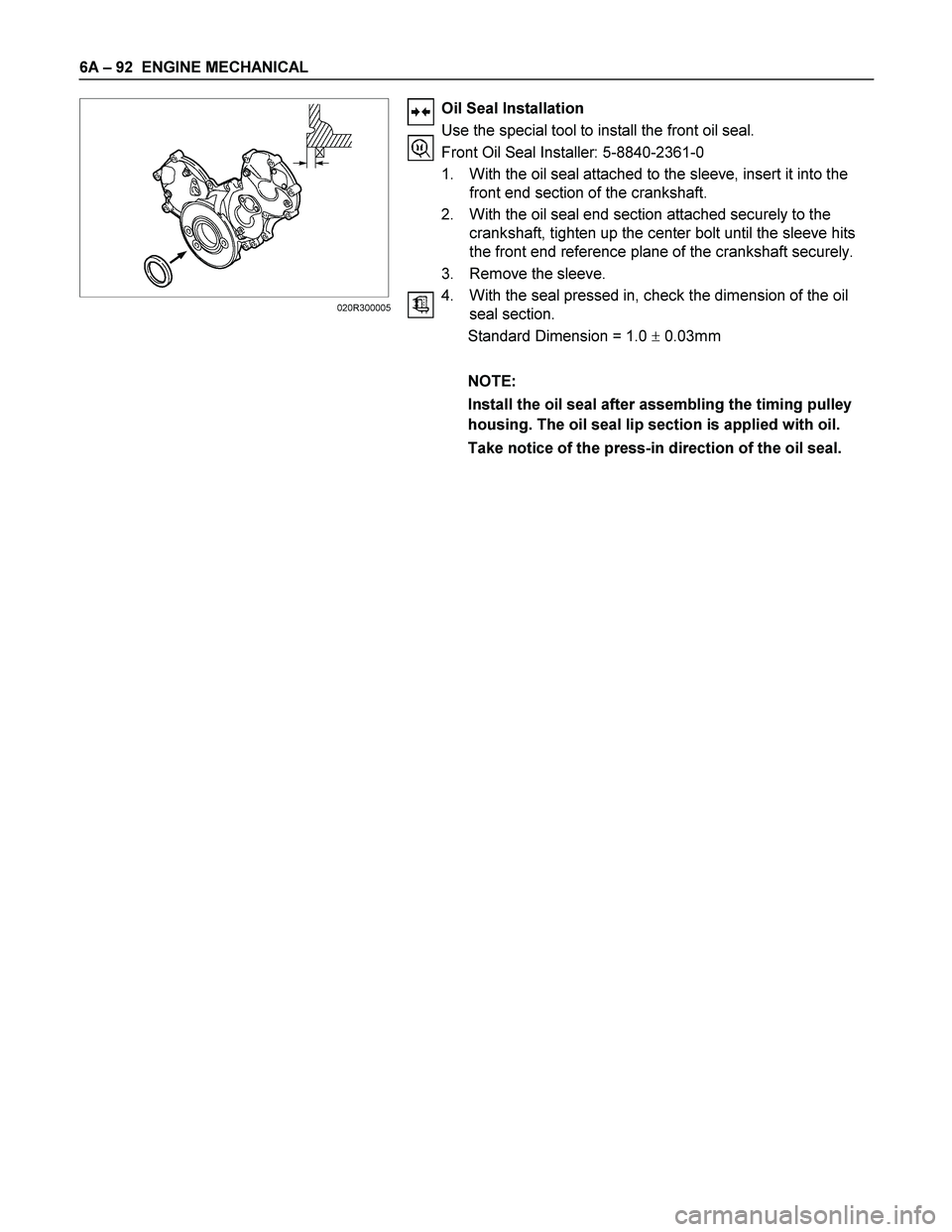
6A – 92 ENGINE MECHANICAL
Oil Seal Installation
Use the special tool to install the front oil seal.
Front Oil Seal Installer: 5-8840-2361-0
1. With the oil seal attached to the sleeve, insert it into the
front end section of the crankshaft.
2. With the oil seal end section attached securely to the
crankshaft, tighten up the center bolt until the sleeve hits
the front end reference plane of the crankshaft securely.
3. Remove the sleeve.
4. With the seal pressed in, check the dimension of the oil
seal section.
Standard Dimension = 1.0 0.03mm
NOTE:
Install the oil seal after assembling the timing pulley
housing. The oil seal lip section is applied with oil.
Take notice of the press-in direction of the oil seal.
020R300005
Page 1233 of 4264

ENGINE MECHANICAL 6A – 93
REASSEMBLY
INTERNAL PARTS
MINOR COMPONENT
ROCKER ARM SHAFT AND ROCKER ARM
020RY00029
Reassembly Steps
1.
Rocker arm shaft 5.
Rocker arm
2.
Rocker arm shaft snap ring 6.
Rocker arm shaft spring
3.
Rocker arm 7.
Rocker arm shaft snap ring
4.
Rocker arm shaft bracket
Reassembly
1. Rocker Arm Shaft
1. Position the rocker arm shaft with the large oil hole (4
) facing the front of the engine.
2. Install the rocker arm shaft together with the rocker
arm, the rocker arm shaft bracket, and the spring.
2. Rocker Arm Shaft Snap Ring
3. Rocker Arm
4. Rocker Arm Shaft Bracket
5. Rocker Arm
6. Rocker Arm Shaft Spring
7. Rocker Arm Shaft Snap Ring
014RY00037
Page 1234 of 4264
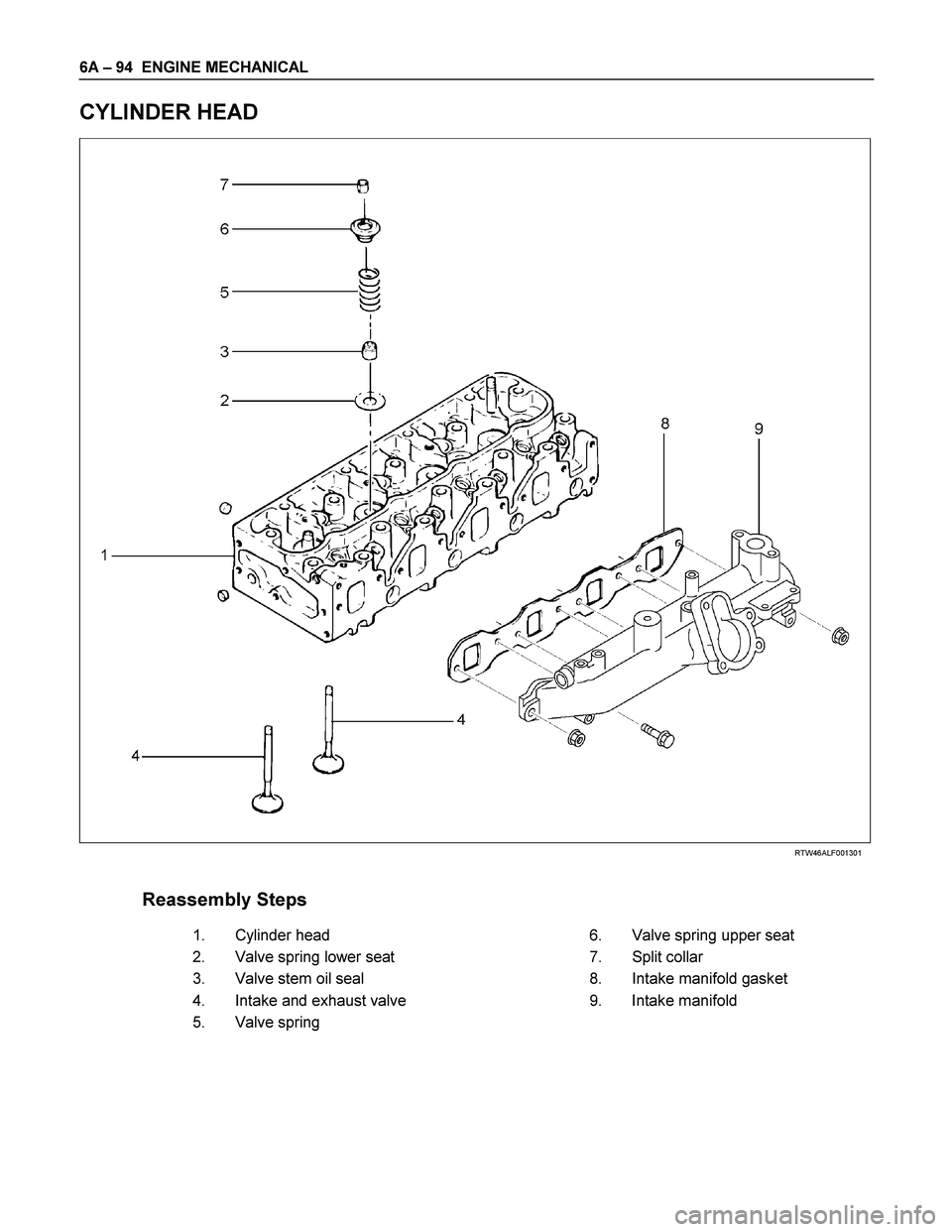
6A – 94 ENGINE MECHANICAL
CYLINDER HEAD
RTW46ALF001301
Reassembly Steps
1.
Cylinder head 6.
Valve spring upper seat
2.
Valve spring lower seat 7.
Split collar
3.
Valve stem oil seal 8.
Intake manifold gasket
4. Intake and exhaust valve 9. Intake manifold
5.
Valve spring
Page 1235 of 4264
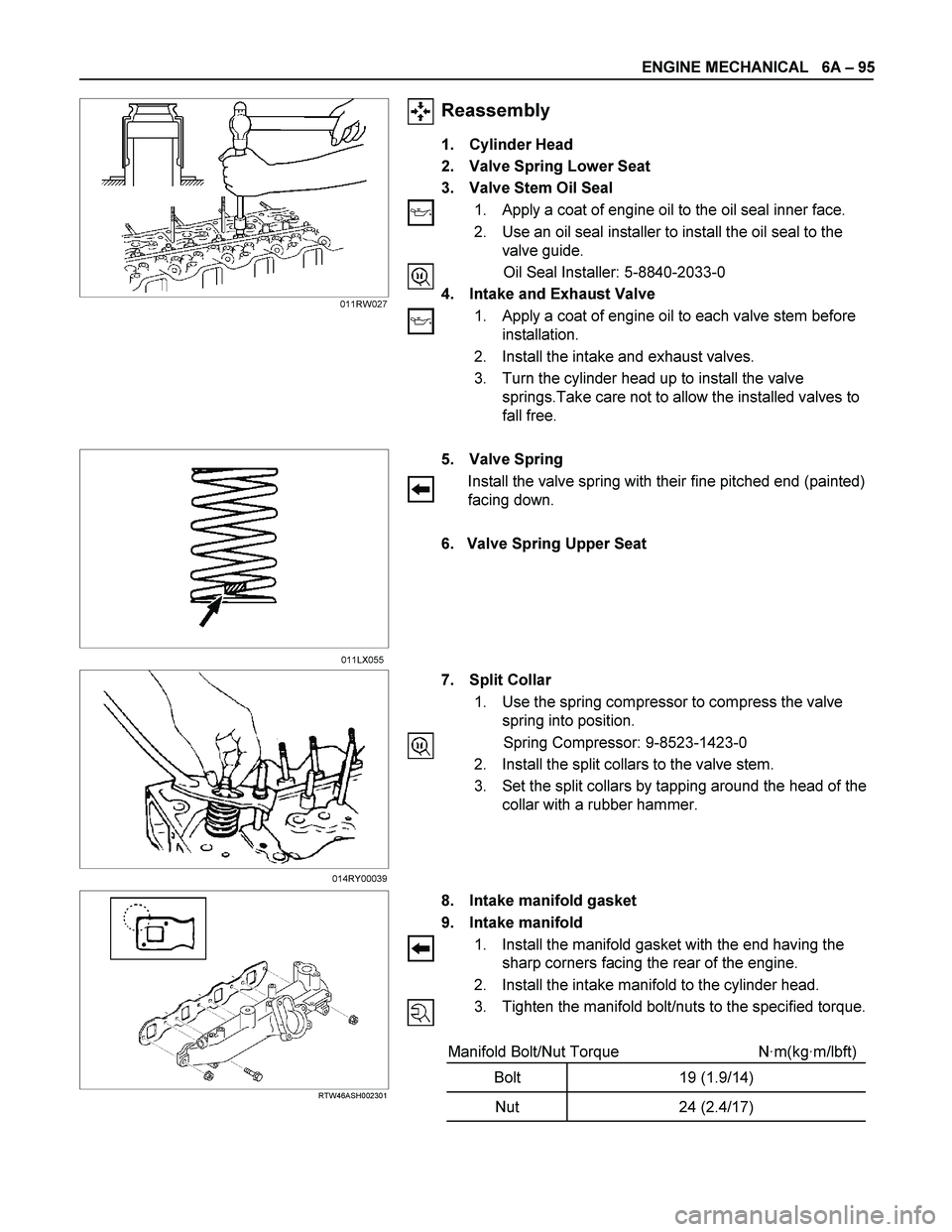
ENGINE MECHANICAL 6A – 95
Reassembly
1. Cylinder Head
2. Valve Spring Lower Seat
3. Valve Stem Oil Seal
1. Apply a coat of engine oil to the oil seal inner face.
2. Use an oil seal installer to install the oil seal to the
valve guide.
Oil Seal Installer: 5-8840-2033-0
4. Intake and Exhaust Valve
1. Apply a coat of engine oil to each valve stem before
installation.
2. Install the intake and exhaust valves.
3. Turn the cylinder head up to install the valve
springs.Take care not to allow the installed valves to
fall free.
5. Valve Spring
Install the valve spring with their fine pitched end (painted)
facing down.
6. Valve Spring Upper Seat
7. Split Collar
1. Use the spring compressor to compress the valve
spring into position.
Spring Compressor: 9-8523-1423-0
2. Install the split collars to the valve stem.
3. Set the split collars by tapping around the head of the
collar with a rubber hammer.
RTW46ASH002301
8. Intake manifold gasket
9. Intake manifold
1. Install the manifold gasket with the end having the
sharp corners facing the rear of the engine.
2. Install the intake manifold to the cylinder head.
3. Tighten the manifold bolt/nuts to the specified torque.
Manifold Bolt/Nut Torque N·m(kg·m/lbft)
Bolt 19 (1.9/14)
Nut 24 (2.4/17)
011RW027
011LX055
014RY00039
Page 1236 of 4264
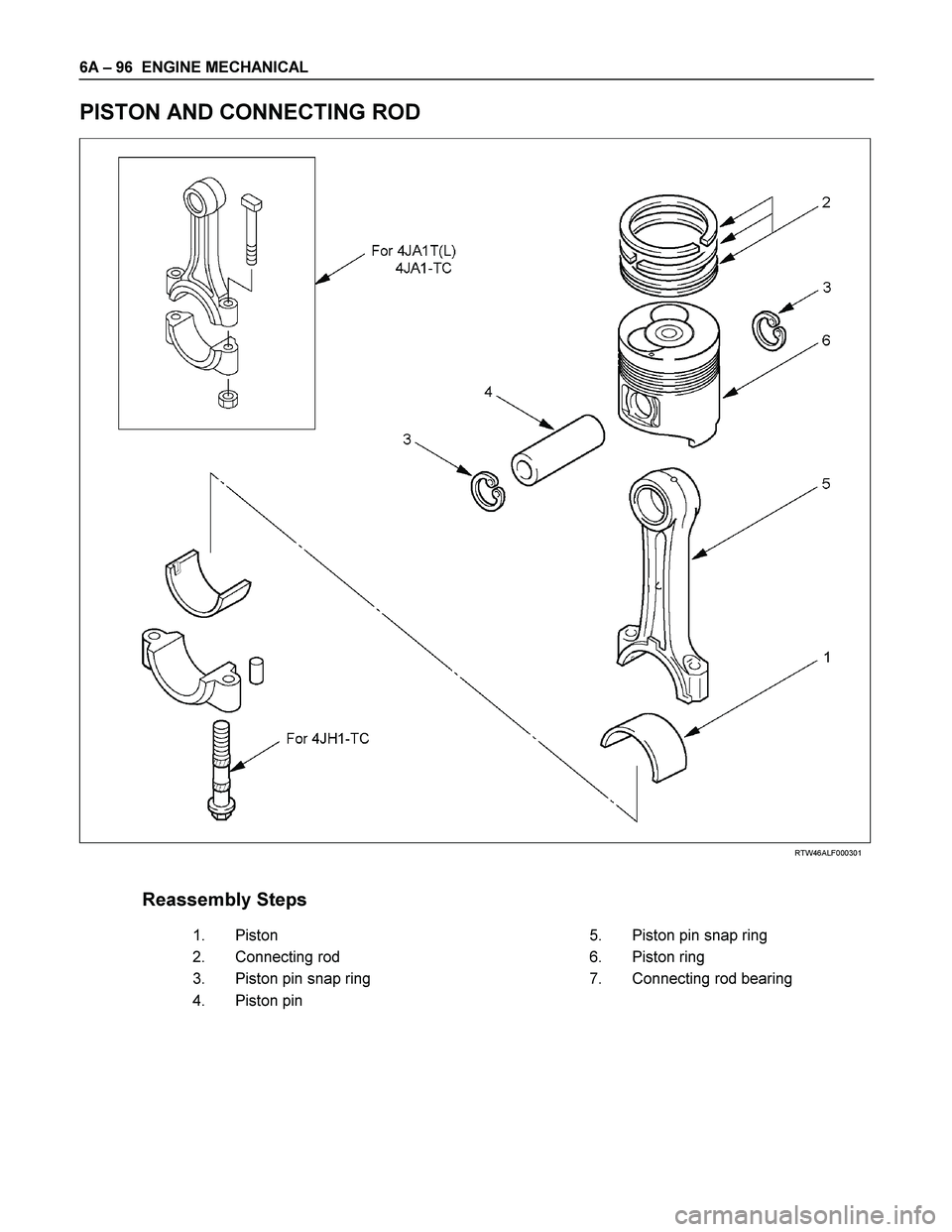
6A – 96 ENGINE MECHANICAL
PISTON AND CONNECTING ROD
RTW46ALF000301
Reassembly Steps
1.
Piston 5.
Piston pin snap ring
2.
Connecting rod 6.
Piston ring
3.
Piston pin snap ring 7.
Connecting rod bearing
4.
Piston pin