fuel pressure ISUZU TF SERIES 2004 Workshop Manual
[x] Cancel search | Manufacturer: ISUZU, Model Year: 2004, Model line: TF SERIES, Model: ISUZU TF SERIES 2004Pages: 4264, PDF Size: 72.63 MB
Page 2830 of 4264
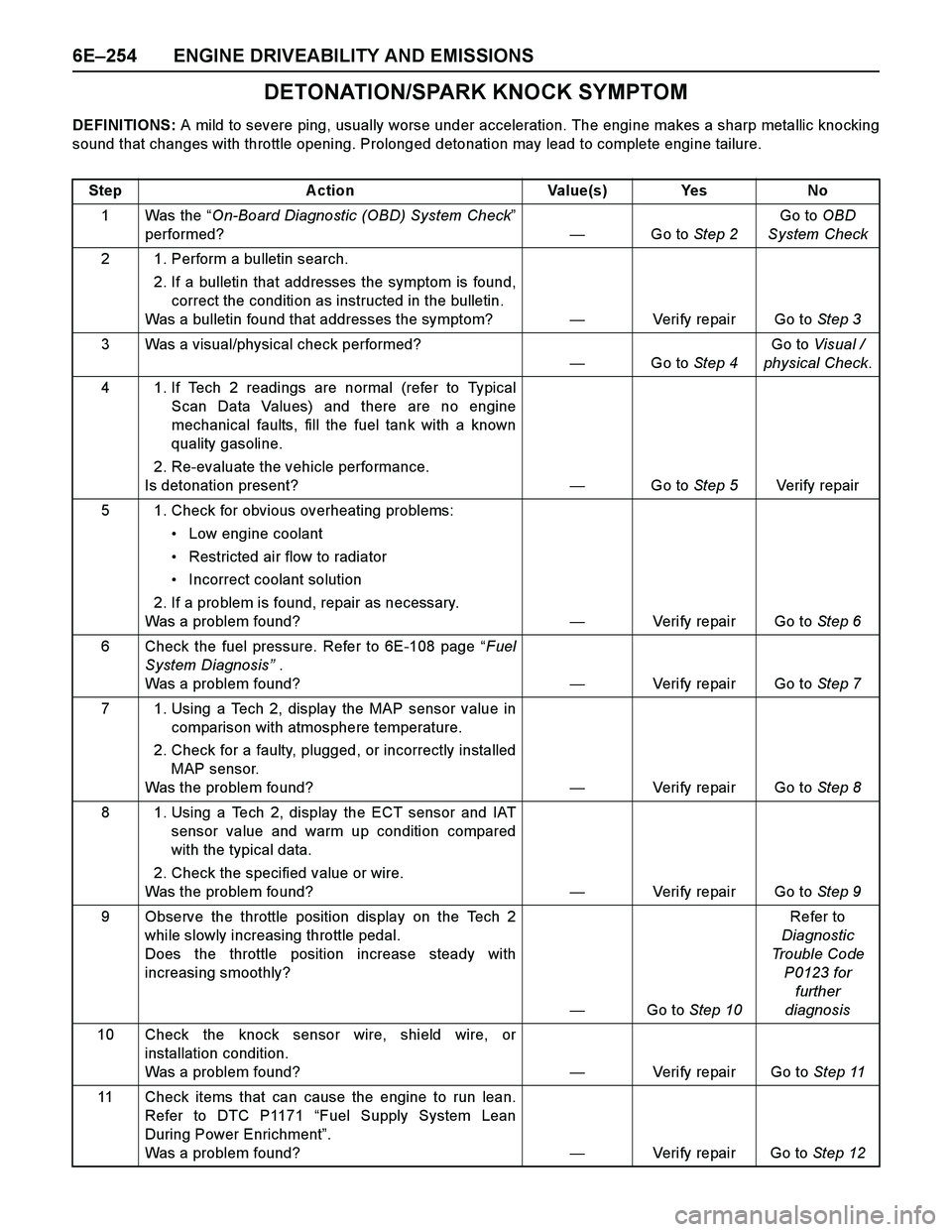
6E–254 ENGINE DRIVEABILITY AND EMISSIONS
DETONATION/SPARK KNOCK SYMPTOM
DEFINITIONS: A mild to severe ping, usually worse under acceleration. The engine makes a sharp metallic knocking
sound that changes with throttle opening. Prolonged detonation may lead to complete engine tailure.
Step Action Value(s) Yes No
1Was the “On-Board Diagnostic (OBD) System Check”
performed?—Go to Step 2Go to OBD
System Check
2 1. Perform a bulletin search.
2. If a bulletin that addresses the symptom is found,
correct the condition as instructed in the bulletin.
Was a bulletin found that addresses the symptom?—Verify repair Go to Step 3
3 Was a visual/physical check performed?
—Go to Step 4Go to Visual /
physical Check.
4 1. If Tech 2 readings are normal (refer to Typical
Scan Data Values) and there are no engine
mechanical faults, fill the fuel tank with a known
quality gasoline.
2. Re-evaluate the vehicle performance.
Is detonation present?—Go to Step 5Verify repair
5 1. Check for obvious overheating problems:
Low engine coolant
Restricted air flow to radiator
Incorrect coolant solution
2. If a problem is found, repair as necessary.
Was a problem found?—Verify repair Go to Step 6
6 Check the fuel pressure. Refer to 6E-108 page “Fuel
System Diagnosis” .
Was a problem found?—Verify repair Go to Step 7
7 1. Using a Tech 2, display the MAP sensor value in
comparison with atmosphere temperature.
2. Check for a faulty, plugged, or incorrectly installed
MAP sensor.
Was the problem found?—Verify repair Go to Step 8
8 1. Using a Tech 2, display the ECT sensor and IAT
sensor value and warm up condition compared
with the typical data.
2. Check the specified value or wire.
Was the problem found?—Verify repair Go to Step 9
9 Observe the throttle position display on the Tech 2
while slowly increasing throttle pedal.
Does the throttle position increase steady with
increasing smoothly?
—Go to Step 10Refer to
Diagnostic
Trouble Code
P0123 for
further
diagnosis
10 Check the knock sensor wire, shield wire, or
installation condition.
Was a problem found?—Verify repair Go to Step 11
11 Check items that can cause the engine to run lean.
Refer to DTC P1171 “Fuel Supply System Lean
During Power Enrichment”.
Was a problem found?—Verify repair Go to Step 12
Page 2832 of 4264
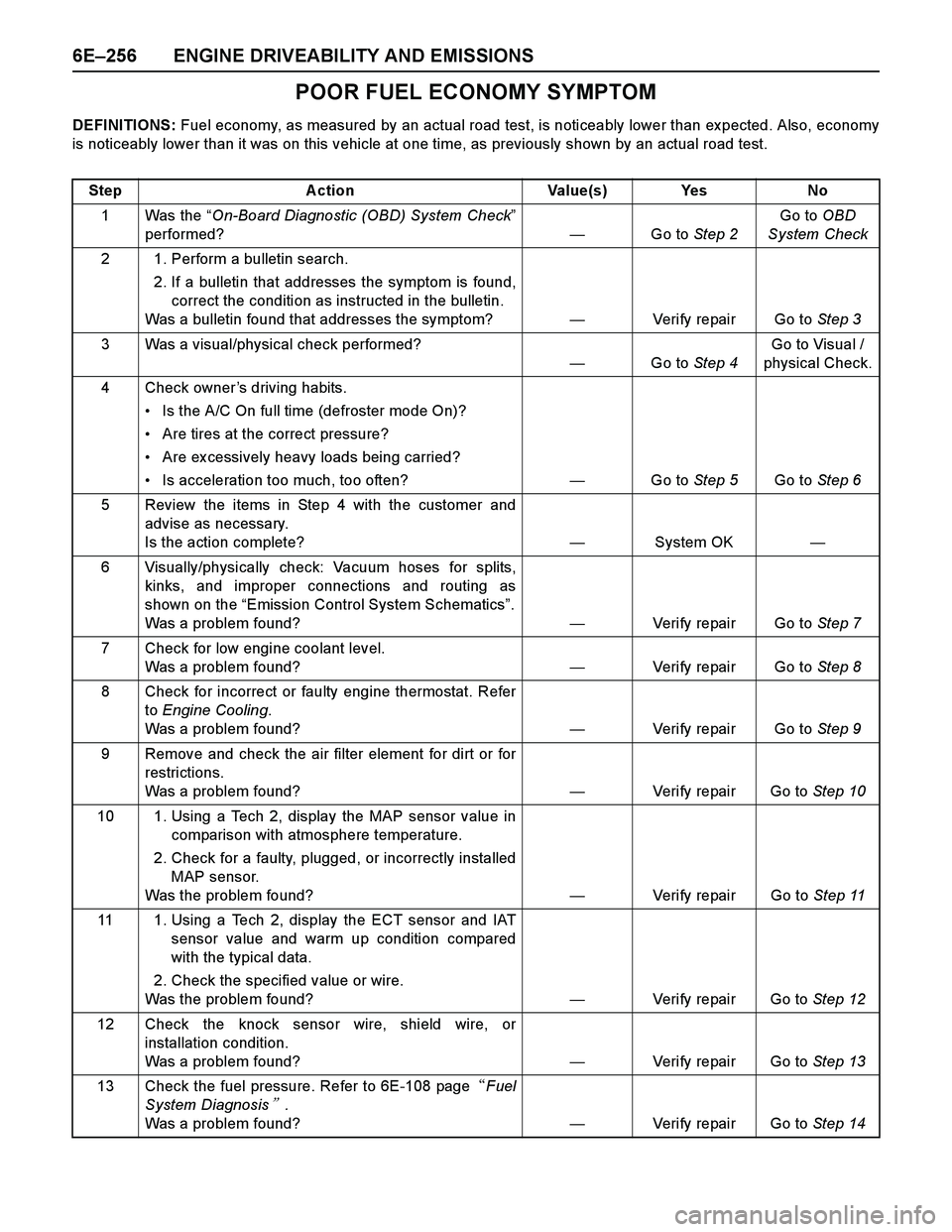
6E–256 ENGINE DRIVEABILITY AND EMISSIONS
POOR FUEL ECONOMY SYMPTOM
DEFINITIONS: Fuel economy, as measured by an actual road test, is noticeably lower than expected. Also, economy
is noticeably lower than it was on this vehicle at one time, as previously shown by an actual road test.
Step Action Value(s) Yes No
1Was the “On-Board Diagnostic (OBD) System Check”
performed?—Go to Step 2Go to OBD
System Check
2 1. Perform a bulletin search.
2. If a bulletin that addresses the symptom is found,
correct the condition as instructed in the bulletin.
Was a bulletin found that addresses the symptom?—Verify repair Go to Step 3
3 Was a visual/physical check performed?
—Go to Step 4Go to Visual /
physical Check.
4 Check owner’s driving habits.
Is the A/C On full time (defroster mode On)?
Are tires at the correct pressure?
Are ex cessively heavy loads being carried?
Is acceleration too much, too often?—Go to Step 5Go to Step 6
5 Review the items in Step 4 with the customer and
advise as necessary.
Is the action complete?—System OK—
6 Visually/physically check: Vacuum hoses for splits,
kinks, and improper connections and routing as
shown on the “Emission Control System Schematics”.
Was a problem found?—Verify repair Go to Step 7
7 Check for low engine coolant level.
Was a problem found? —Verify repair Go to Step 8
8 Check for incorrect or faulty engine thermostat. Refer
to Engine Cooling.
Was a problem found?—Verify repair Go to Step 9
9 Remove and check the air filter element for dirt or for
restrictions.
Was a problem found?—Verify repair Go to Step 10
10 1. Using a Tech 2, display the MAP sensor value in
comparison with atmosphere temperature.
2. Check for a faulty, plugged, or incorrectly installed
MAP sensor.
Was the problem found?—Verify repair Go to Step 11
11 1. Using a Tech 2, display the ECT sensor and IAT
sensor value and warm up condition compared
with the typical data.
2. Check the specified value or wire.
Was the problem found?—Verify repair Go to Step 12
12 Check the knock sensor wire, shield wire, or
installation condition.
Was a problem found?—Verify repair Go to Step 13
13 Check the fuel pressure. Refer to 6E-108 pageFuel
System Diagnosis.
Was a problem found?—Verify repair Go to Step 14
Page 2834 of 4264
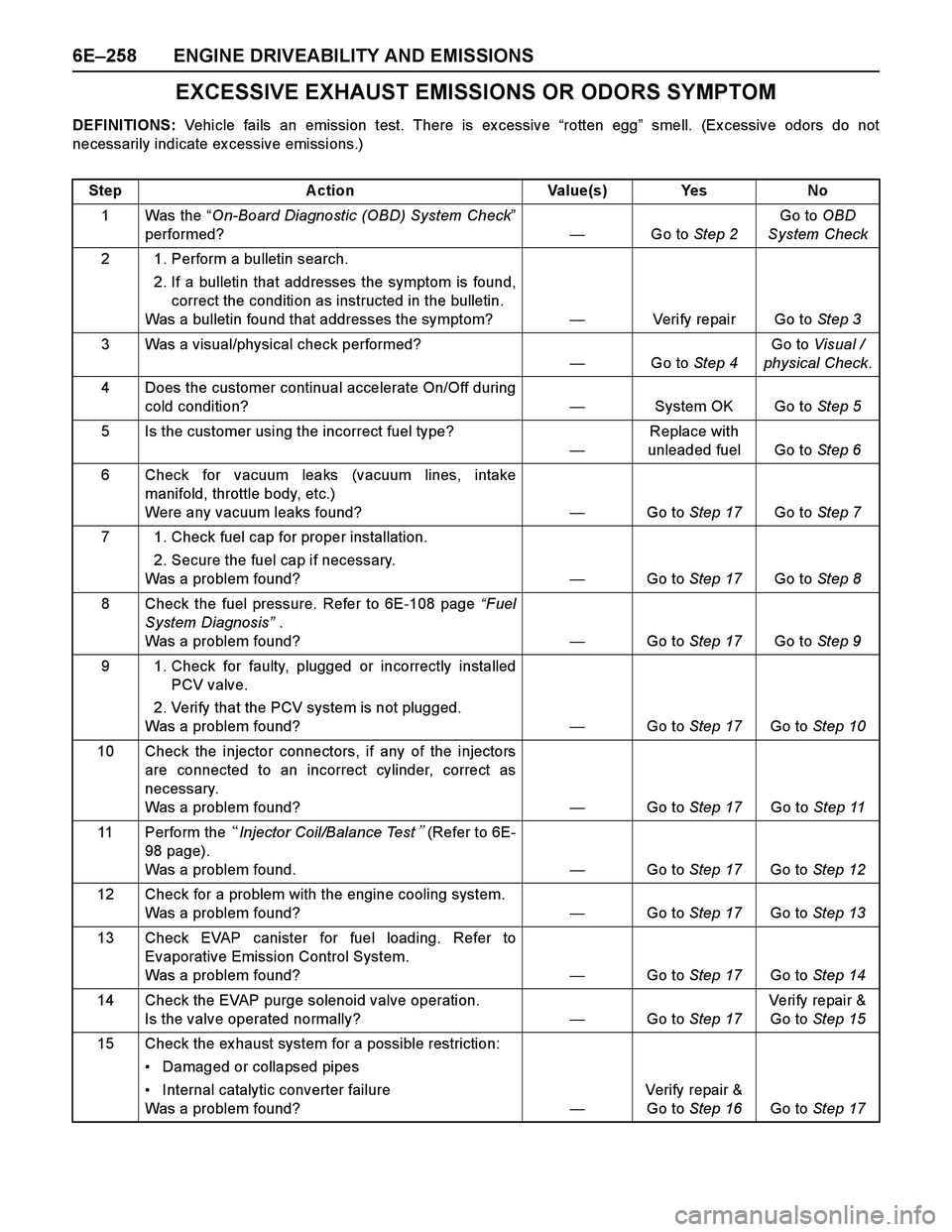
6E–258 ENGINE DRIVEABILITY AND EMISSIONS
EXCESSIVE EXHAUST EMISSIONS OR ODORS SYMPTOM
DEFINITIONS: Vehicle fails an emission test. There is ex cessive “rotten egg” smell. (Ex cessive odors do not
necessarily indicate ex cessive emissions.)
Step Action Value(s) Yes No
1Was the “On-Board Diagnostic (OBD) System Check”
performed?—Go to Step 2Go to OBD
System Check
2 1. Perform a bulletin search.
2. If a bulletin that addresses the symptom is found,
correct the condition as instructed in the bulletin.
Was a bulletin found that addresses the symptom?—Verify repair Go to Step 3
3 Was a visual/physical check performed?
—Go to Step 4Go to Visual /
physical Check.
4 Does the customer continual accelerate On/Off during
cold condition?—System OK Go to Step 5
5 Is the customer using the incorrect fuel type?
—Replace with
unleaded fuel Go to Step 6
6 Check for vacuum leaks (vacuum lines, intake
manifold, throttle body, etc.)
Were any vacuum leaks found?—Go to Step 17Go to Step 7
7 1. Check fuel cap for proper installation.
2. Secure the fuel cap if necessary.
Was a problem found?—Go to Step 17Go to Step 8
8 Check the fuel pressure. Refer to 6E-108 page “Fuel
System Diagnosis” .
Was a problem found?—Go to Step 17Go to Step 9
9 1. Check for faulty, plugged or incorrectly installed
PCV valve.
2. Verify that the PCV system is not plugged.
Was a problem found? —Go to Step 17Go to Step 10
10 Check the injector connectors, if any of the injectors
are connected to an incorrect cylinder, correct as
necessary.
Was a problem found?—Go to Step 17Go to Step 11
11 Perform the Injector Coil/Balance Test (Refer to 6E-
98 page).
Was a problem found.—Go to Step 17Go to Step 12
12 Check for a problem with the engine cooling system.
Was a problem found?—Go to Step 17Go to Step 13
13 Check EVAP canister for fuel loading. Refer to
Evaporative Emission Control System.
Was a problem found?—Go to Step 17Go to Step 14
14 Check the EVAP purge solenoid valve operation.
Is the valve operated normally?—Go to Step 17Veri fy repai r &
Go to Step 15
15 Check the ex haust system for a possible restriction:
Damaged or collapsed pipes
Internal catalytic converter failure
Was a problem found?—Verify repair &
Go to Step 16Go to Step 17
Page 2838 of 4264
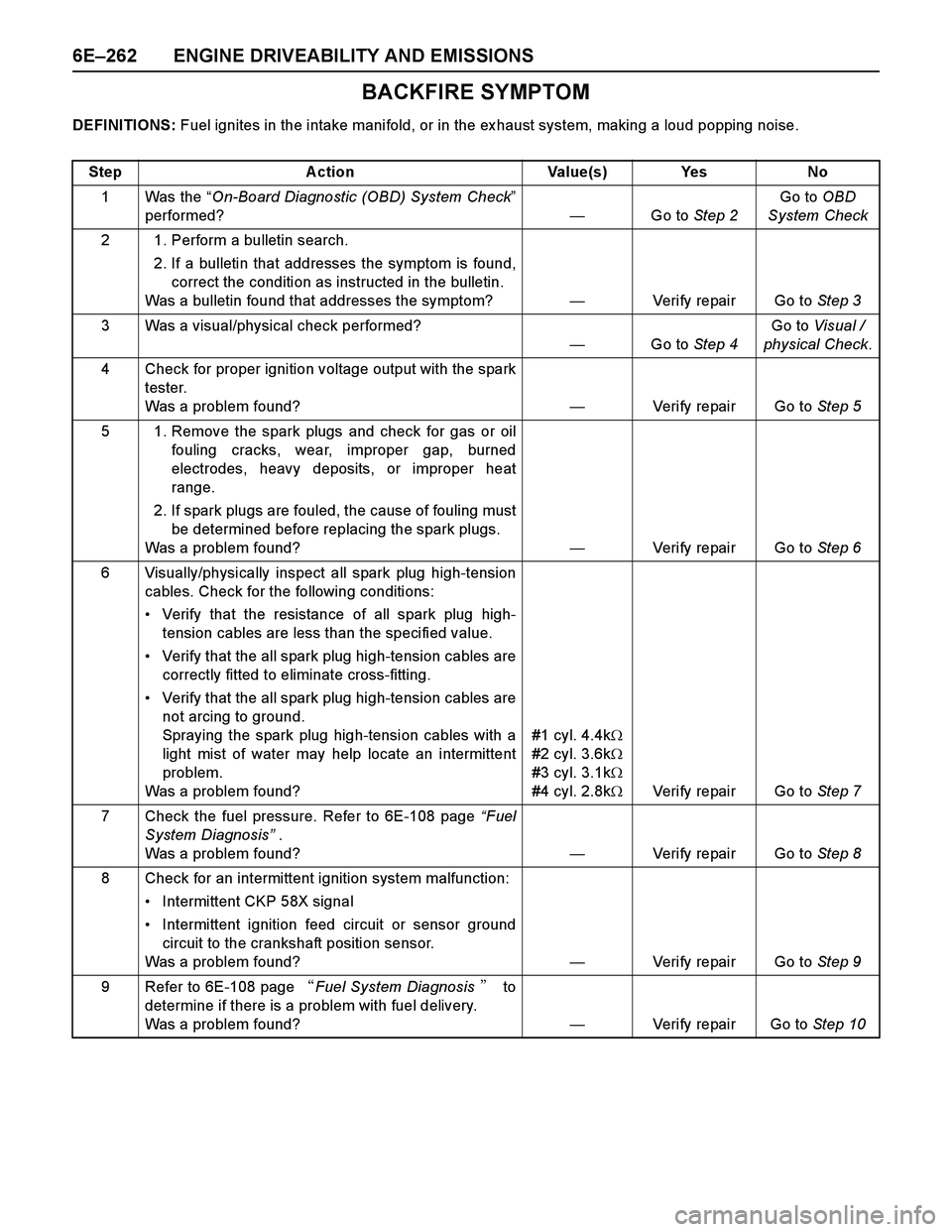
6E–262 ENGINE DRIVEABILITY AND EMISSIONS
BACKFIRE SYMPTOM
DEFINITIONS: Fuel ignites in the intake manifold, or in the ex haust system, making a loud popping noise.
Step Action Value(s) Yes No
1Was the “On-Board Diagnostic (OBD) System Check”
performed?—Go to Step 2Go to OBD
System Check
2 1. Perform a bulletin search.
2. If a bulletin that addresses the symptom is found,
correct the condition as instructed in the bulletin.
Was a bulletin found that addresses the symptom?—Verify repair Go to Step 3
3 Was a visual/physical check performed?
—Go to Step 4Go to Visual /
physical Check.
4 Check for proper ignition voltage output with the spark
tester.
Was a problem found?—Verify repair Go to Step 5
5 1. Remove the spark plugs and check for gas or oil
fouling cracks, wear, improper gap, burned
electrodes, heavy deposits, or improper heat
range.
2. If spark plugs are fouled, the cause of fouling must
be determined before replacing the spark plugs.
Was a problem found?—Verify repair Go to Step 6
6 Visually/physically inspect all spark plug high-tension
cables. Check for the following conditions:
Verify that the resistance of all spark plug high-
tension cables are less than the specified value.
Verify that the all spark plug high-tension cables are
correctly fitted to eliminate cross-fitting.
Verify that the all spark plug high-tension cables are
not arcing to ground.
Spraying the spark plug high-tension cables with a
light mist of water may help locate an intermittent
problem.
Was a problem found?#1 cyl. 4.4k
#2 cyl. 3.6k
#3 cyl. 3.1k
#4 cyl. 2.8kVerify repair Go to Step 7
7 Check the fuel pressure. Refer to 6E-108 page “Fuel
System Diagnosis” .
Was a problem found?—Verify repair Go to Step 8
8 Check for an intermittent ignition system malfunction:
Intermittent CKP 58X signal
Intermittent ignition feed circuit or sensor ground
circuit to the crankshaft position sensor.
Was a problem found?—Verify repair Go to Step 9
9 Refer to 6E-108 page Fuel System Diagnosis to
determine if there is a problem with fuel delivery.
Was a problem found?—Verify repair Go to Step 10
Page 2846 of 4264
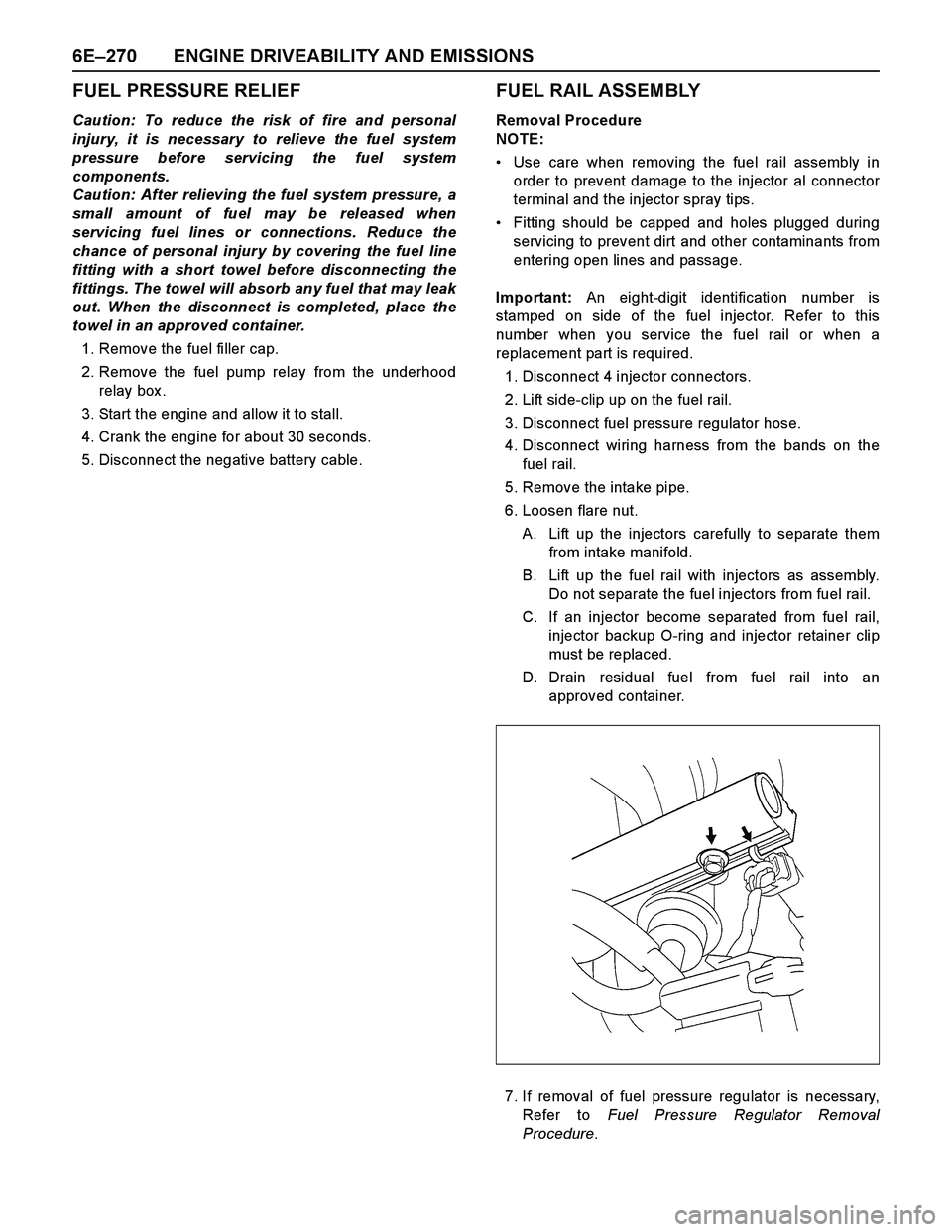
6E–270 ENGINE DRIVEABILITY AND EMISSIONS
FUEL PRESSURE RELIEF
Caution: To reduce the risk of fire and personal
injury, it is necessary to relieve the fuel system
pressure before servicing the fuel system
components.
Caution: After relieving the fuel system pressure, a
small amount of fuel may be released when
servicing fuel lines or connections. Reduce the
chance of personal injury by covering the fuel line
fitting with a short towel before disconnecting the
fittings. The towel will absorb any fuel that may leak
out. When the disconnect is completed, place the
towel in an approved container.
1. Remove the fuel filler cap.
2. Remove the fuel pump relay from the underhood
relay box .
3. Start the engine and allow it to stall.
4. Crank the engine for about 30 seconds.
5. Disconnect the negative battery cable.
FUEL RAIL ASSEMBLY
Removal Procedure
NOTE:
Use care when removing the fuel rail assembly in
order to prevent damage to the injector al connector
terminal and the injector spray tips.
Fitting should be capped and holes plugged during
servicing to prevent dirt and other contaminants from
entering open lines and passage.
Important: An eight-digit identification number is
stamped on side of the fuel injector. Refer to this
number when you service the fuel rail or when a
replacement part is required.
1. Disconnect 4 injector connectors.
2. Lift side-clip up on the fuel rail.
3. Disconnect fuel pressure regulator hose.
4. Disconnect wiring harness from the bands on the
fuel rail.
5. Remove the intake pipe.
6. Loosen flare nut.
A. Lift up the injectors carefully to separate them
from intake manifold.
B. Lift up the fuel rail with injectors as assembly.
Do not separate the fuel injectors from fuel rail.
C. If an injector become separated from fuel rail,
injector backup O-ring and injector retainer clip
must be replaced.
D. Drain residual fuel from fuel rail into an
approved container.
7. If removal of fuel pressure regulator is necessary,
Refer to Fuel Pressure Regulator Removal
Procedure.
Page 2847 of 4264
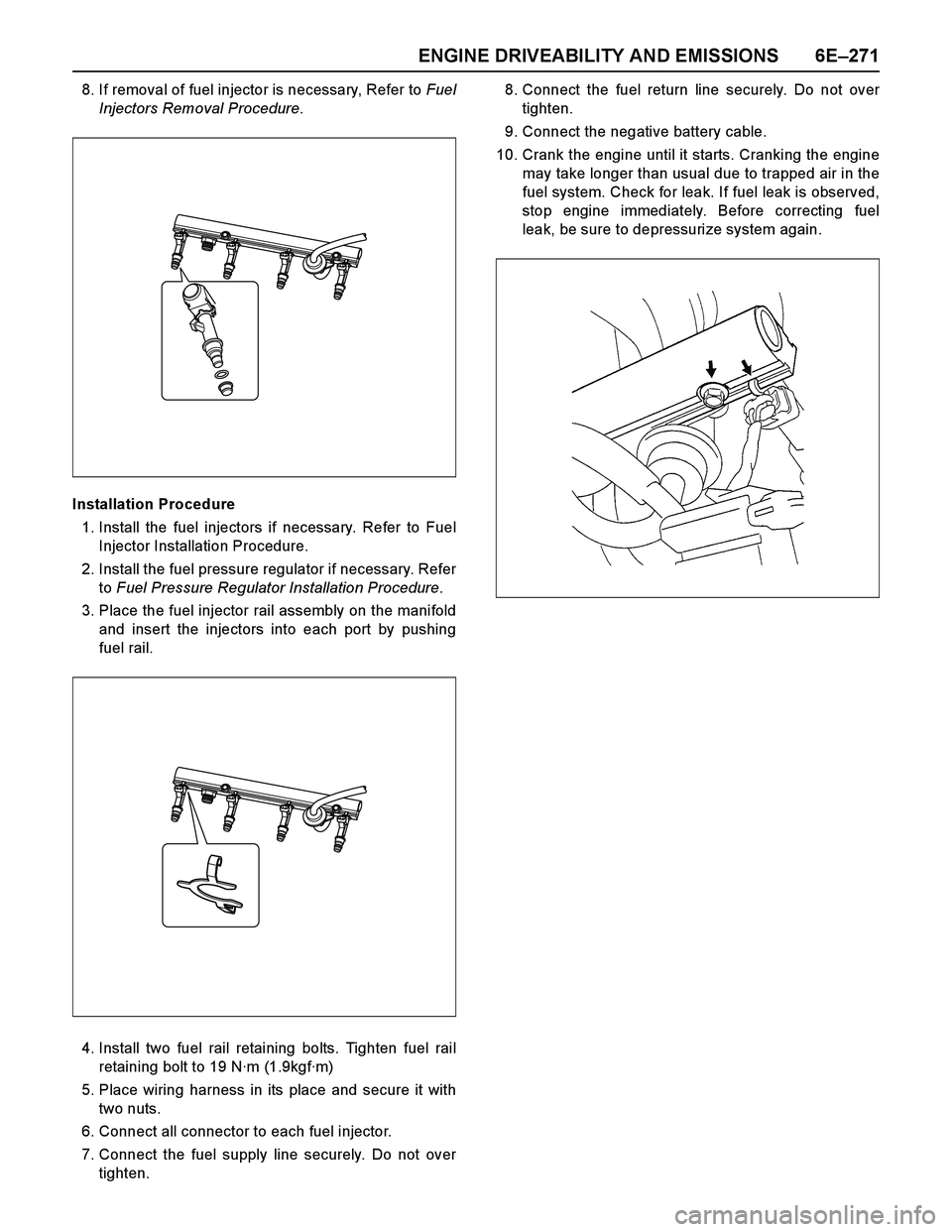
ENGINE DRIVEABILITY AND EMISSIONS 6E–271
8. If removal of fuel injector is necessary, Refer to Fuel
Injectors Removal Procedure.
Installation Procedure
1. Install the fuel injectors if necessary. Refer to Fuel
Injector Installation Procedure.
2. Install the fuel pressure regulator if necessary. Refer
to Fuel Pressure Regulator Installation Procedure.
3. Place the fuel injector rail assembly on the manifold
and insert the injectors into each port by pushing
fuel rail.
4. Install two fuel rail retaining bolts. Tighten fuel rail
retaining bolt to 19 N·m (1.9kgf·m)
5. Place wiring harness in its place and secure it with
two nuts.
6. Connect all connector to each fuel injector.
7. Connect the fuel supply line securely. Do not over
tighten.8. Connect the fuel return line securely. Do not over
tighten.
9. Connect the negative battery cable.
10. Crank the engine until it starts. Cranking the engine
may take longer than usual due to trapped air in the
fuel system. Check for leak. If fuel leak is observed,
stop engine immediately. Before correcting fuel
leak, be sure to depressurize system again.
Page 2849 of 4264
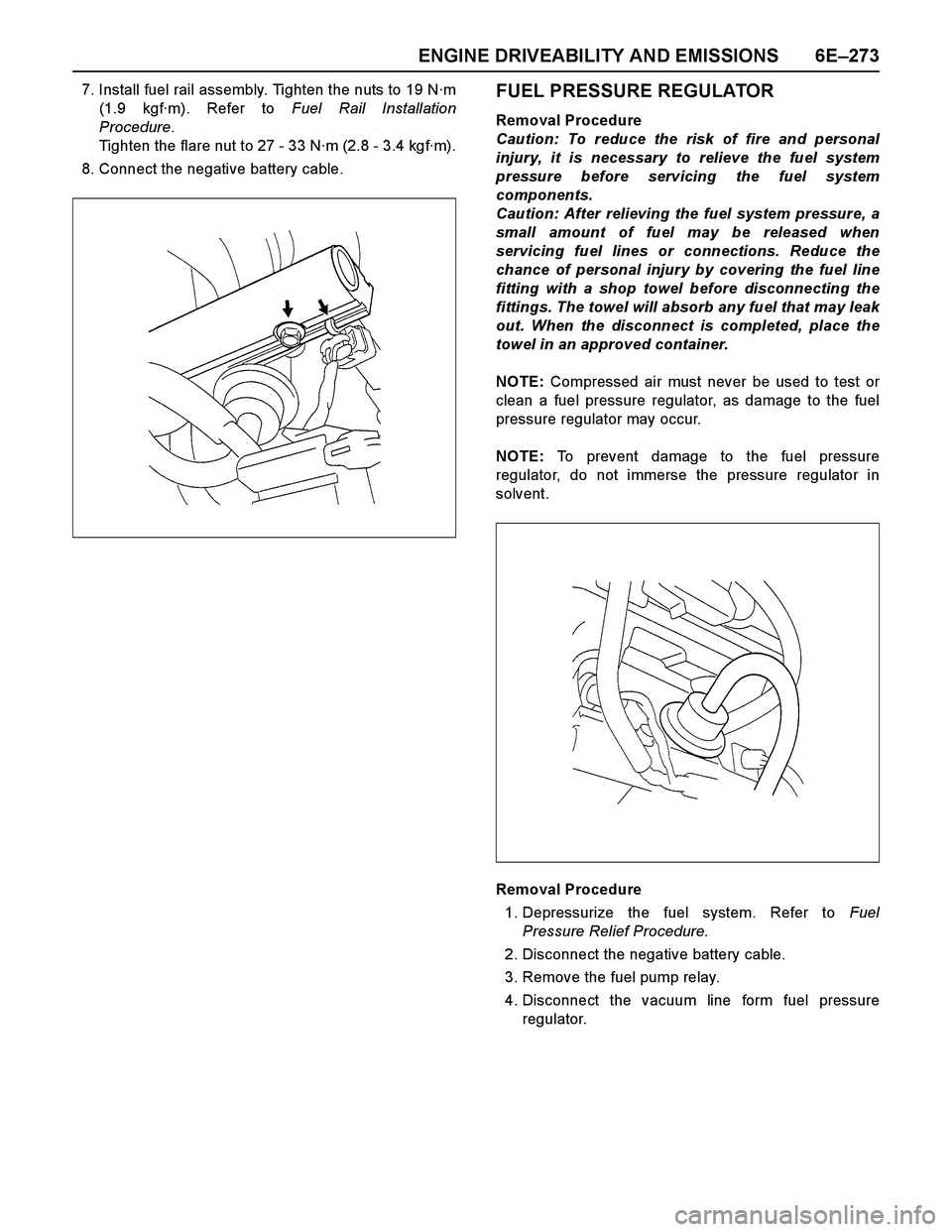
ENGINE DRIVEABILITY AND EMISSIONS 6E–273
7. Install fuel rail assembly. Tighten the nuts to 19 N·m
(1.9 kgf·m). Refer to Fuel Rail Installation
Procedure.
Tighten the flare nut to 27 - 33 N·m (2.8 - 3.4 kgf·m).
8. Connect the negative battery cable.FUEL PRESSURE REGULATOR
Removal Procedure
Caution: To reduce the risk of fire and personal
injury, it is necessary to relieve the fuel system
pressure before servicing the fuel system
components.
Caution: After relieving the fuel system pressure, a
small amount of fuel may be released when
servicing fuel lines or connections. Reduce the
chance of personal injury by covering the fuel line
fitting with a shop towel before disconnecting the
fittings. The towel will absorb any fuel that may leak
out. When the disconnect is completed, place the
towel in an approved container.
NOTE: Compressed air must never be used to test or
clean a fuel pressure regulator, as damage to the fuel
pressure regulator may occur.
NOTE: To prevent damage to the fuel pressure
regulator, do not immerse the pressure regulator in
solvent.
Removal Procedure
1. Depressurize the fuel system. Refer to Fuel
Pressure Relief Procedure.
2. Disconnect the negative battery cable.
3. Remove the fuel pump relay.
4. Disconnect the vacuum line form fuel pressure
regulator.
Page 2850 of 4264
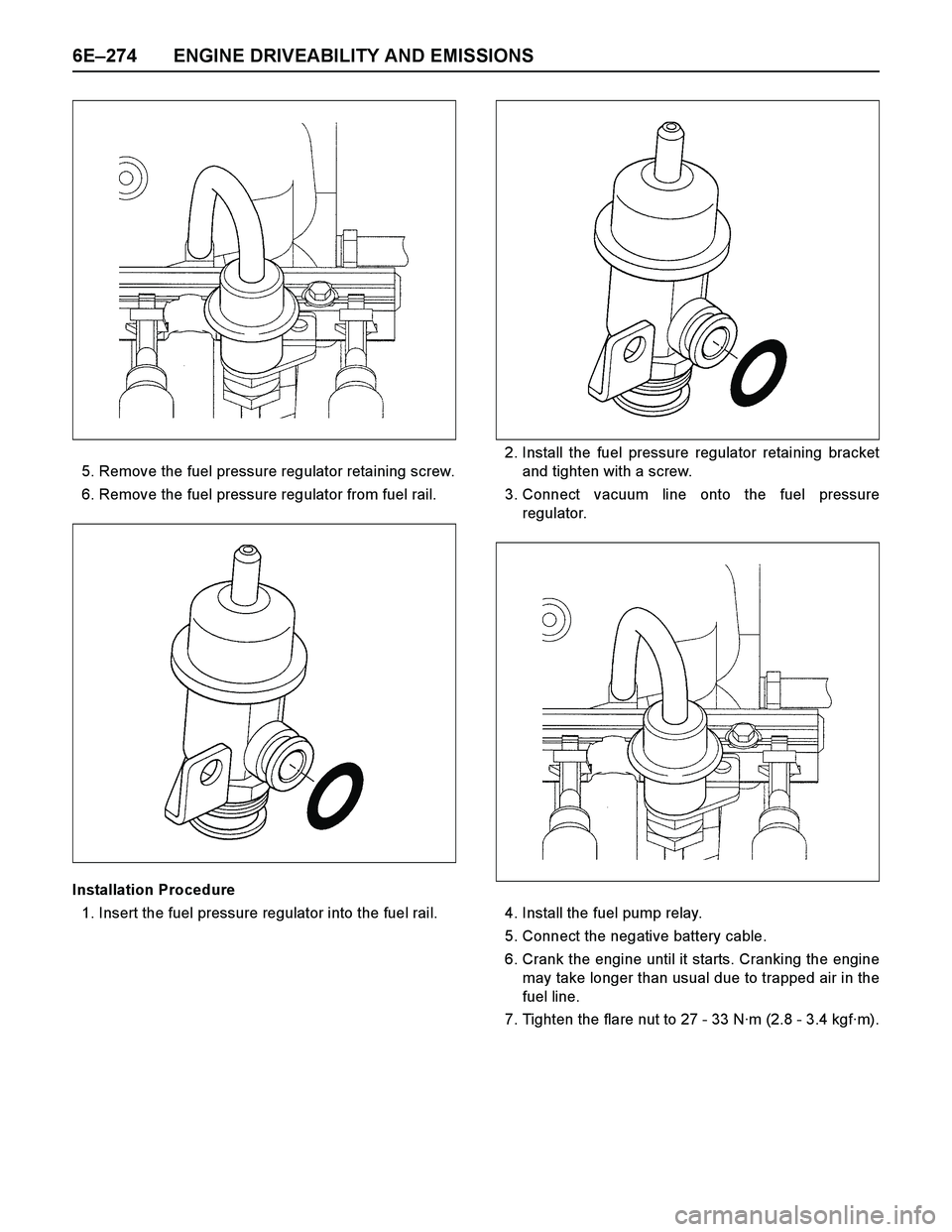
6E–274 ENGINE DRIVEABILITY AND EMISSIONS
5. Remove the fuel pressure regulator retaining screw.
6. Remove the fuel pressure regulator from fuel rail.
Installation Procedure
1. Insert the fuel pressure regulator into the fuel rail.2. Install the fuel pressure regulator retaining bracket
and tighten with a screw.
3. Connect vacuum line onto the fuel pressure
regulator.
4. Install the fuel pump relay.
5. Connect the negative battery cable.
6. Crank the engine until it starts. Cranking the engine
may take longer than usual due to trapped air in the
fuel line.
7. Tighten the flare nut to 27 - 33 N·m (2.8 - 3.4 kgf·m).
Page 3682 of 4264
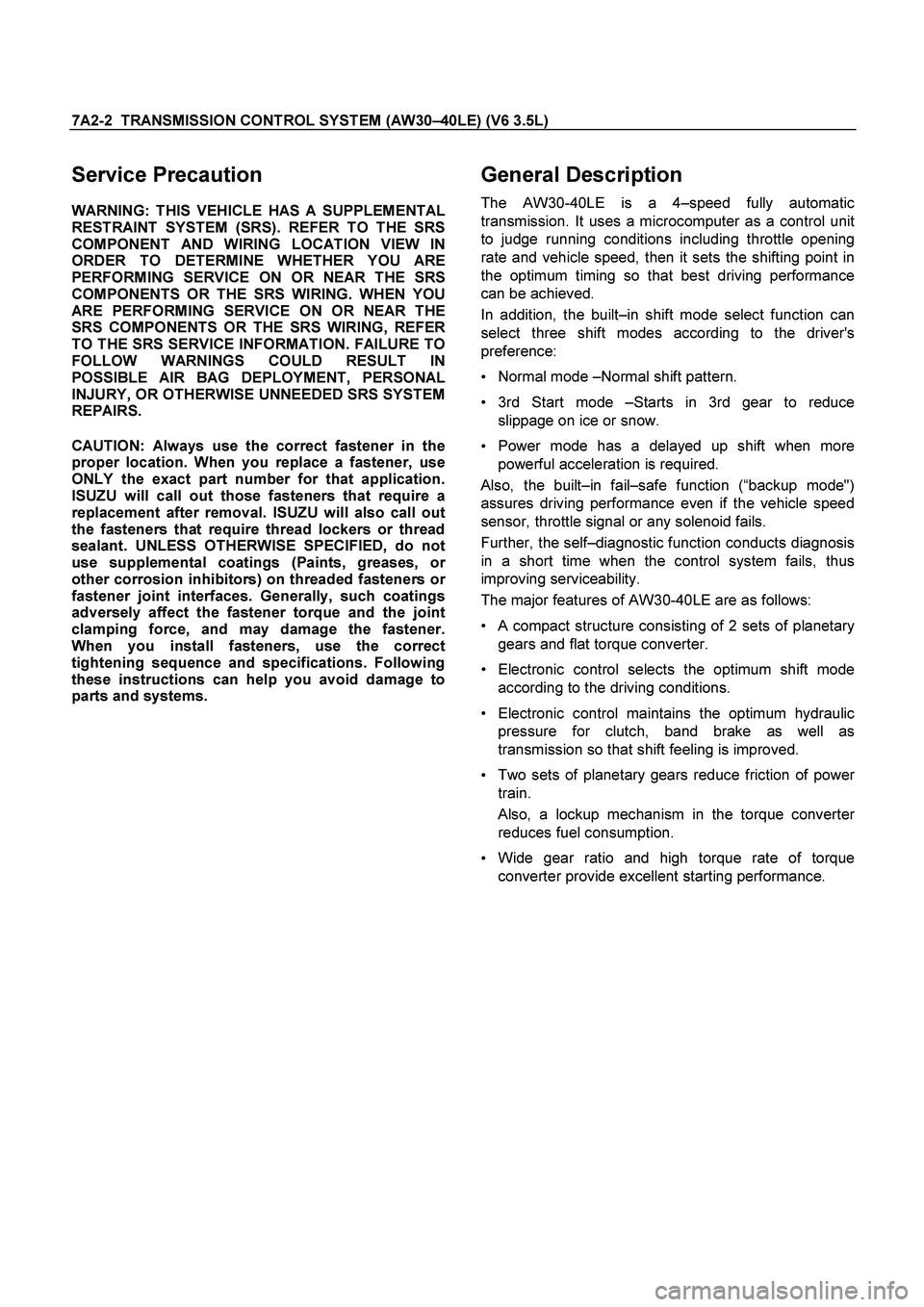
7A2-2 TRANSMISSION CONTROL SYSTEM (AW30 –40LE) (V6 3.5L)
Service Precaution
WARNING: THIS VEHICLE HAS A SUPPLEMENTAL
RESTRAINT SYSTEM (SRS). REFER TO THE SRS
COMPONENT AND WIRING LOCATION VIEW IN
ORDER TO DETERMINE WHETHER YOU ARE
PERFORMING SERVICE ON OR NEAR THE SRS
COMPONENTS OR THE SRS WIRING. WHEN YOU
ARE PERFORMING SERVICE ON OR NEAR THE
SRS COMPONENTS OR THE SRS WIRING, REFE
R
TO THE SRS SERVICE INFORMATION. FAILURE TO
FOLLOW WARNINGS COULD RESULT IN
POSSIBLE AIR BAG DEPLOYMENT, PERSONAL
INJURY, OR OTHERWISE UNNEEDED SRS SYSTEM
REPAIRS.
CAUTION: Always use the correct fastener in the
proper location. When you replace a fastener, use
ONLY the exact part number for that application.
ISUZU will call out those fasteners that require a
replacement after removal. ISUZU will also call out
the fasteners that require thread lockers or thread
sealant. UNLESS OTHERWISE SPECIFIED, do not
use supplemental coatings (Paints, greases, o
r
other corrosion inhibitors) on threaded fasteners or
fastener joint interfaces. Generally, such coatings
adversely affect the fastener torque and the joint
clamping force, and may damage the fastener.
When you install fasteners, use the correct
tightening sequence and specifications. Following
these instructions can help you avoid damage to
parts and systems.
General Description
The AW30-40LE is a 4–speed fully automatic
transmission. It uses a microcomputer as a control unit
to judge running conditions including throttle opening
rate and vehicle speed, then it sets the shifting point in
the optimum timing so that best driving performance
can be achieved.
In addition, the built–in shift mode select function can
select three shift modes according to the driver's
preference:
Normal mode –Normal shift pattern.
3rd Start mode –Starts in 3rd gear to reduce
slippage on ice or snow.
Power mode has a delayed up shift when more
powerful acceleration is required.
Also, the built–in fail–safe function (“backup mode")
assures driving performance even if the vehicle speed
sensor, throttle signal or any solenoid fails.
Further, the self–diagnostic function conducts diagnosis
in a short time when the control system fails, thus
improving serviceability.
The major features of AW30-40LE are as follows:
A compact structure consisting of 2 sets of planetary
gears and flat torque converter.
Electronic control selects the optimum shift mode according to the driving conditions.
Electronic control maintains the optimum hydraulic
pressure for clutch, band brake as well as
transmission so that shift feeling is improved.
Two sets of planetary gears reduce friction of powe
r
train.
Also, a lockup mechanism in the torque converter
reduces fuel consumption.
Wide gear ratio and high torque rate of torque
converter provide excellent starting performance.
Page 3997 of 4264
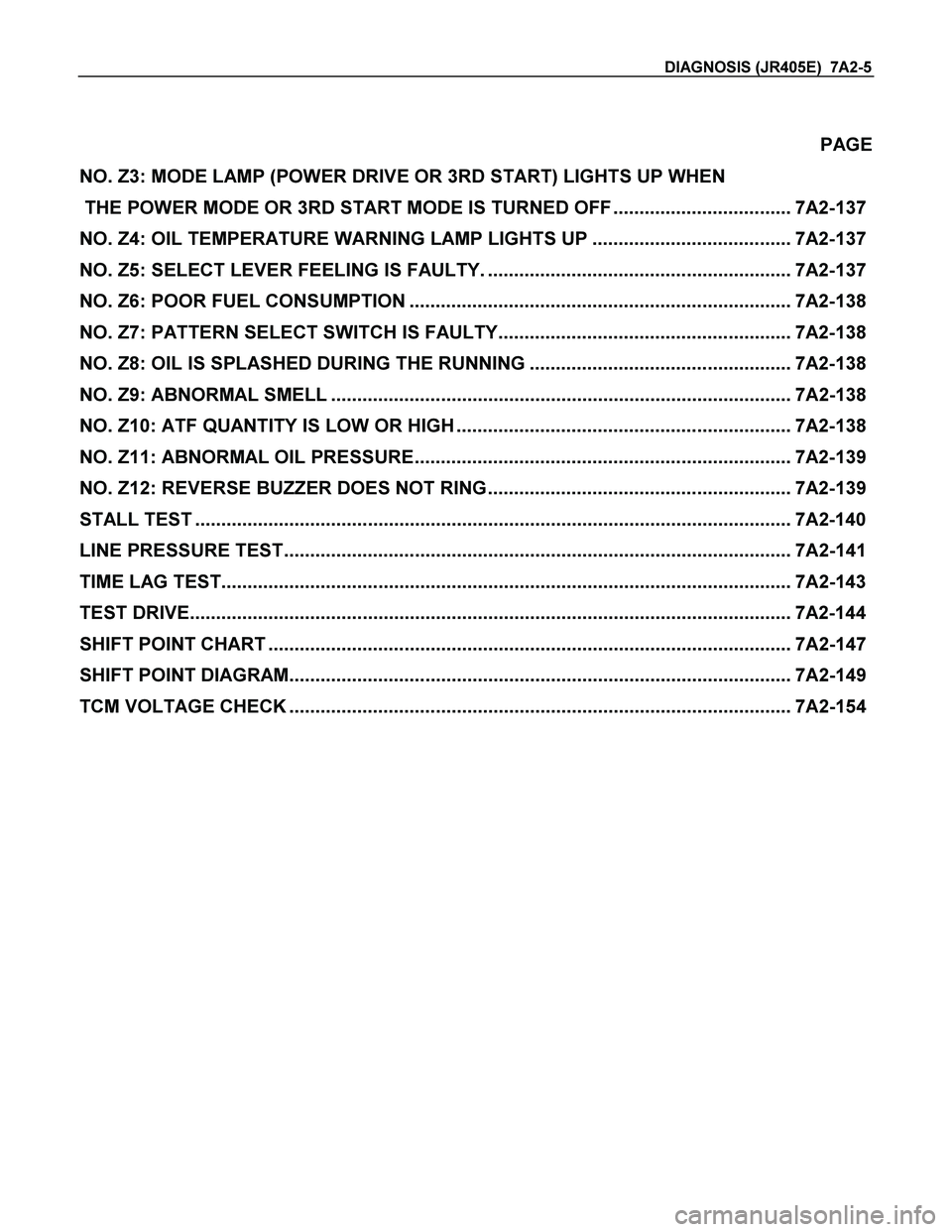
DIAGNOSIS (JR405E) 7A2-5
PAGE
NO. Z3: MODE LAMP (POWER DRIVE OR 3RD START) LIGHTS UP WHEN
THE POWER MODE OR 3RD START MODE IS TURNED OFF .................................. 7A2-137
NO. Z4: OIL TEMPERATURE WARNING LAMP LIGHTS UP ...................................... 7A2-137
NO. Z5: SELECT LEVER FEELING IS FAULTY. .......................................................... 7A2-137
NO. Z6: POOR FUEL CONSUMPTION ......................................................................... 7A2-138
NO. Z7: PATTERN SELECT SWITCH IS FAULTY........................................................ 7A2-138
NO. Z8: OIL IS SPLASHED DURING THE RUNNING .................................................. 7A2-138
NO. Z9: ABNORMAL SMELL ........................................................................................ 7A2-138
NO. Z10: ATF QUANTITY IS LOW OR HIGH ................................................................ 7A2-138
NO. Z11: ABNORMAL OIL PRESSURE........................................................................ 7A2-139
NO. Z12: REVERSE BUZZER DOES NOT RING .......................................................... 7A2-139
STALL TEST .................................................................................................................. 7A2-140
LINE PRESSURE TEST................................................................................................. 7A2-141
TIME LAG TEST............................................................................................................. 7A2-143
TEST DRIVE................................................................................................................... 7A2-144
SHIFT POINT CHART .................................................................................................... 7A2-147
SHIFT POINT DIAGRAM................................................................................................ 7A2-149
TCM VOLTAGE CHECK ................................................................................................ 7A2-154