oil ISUZU TF SERIES 2004 Workshop Manual
[x] Cancel search | Manufacturer: ISUZU, Model Year: 2004, Model line: TF SERIES, Model: ISUZU TF SERIES 2004Pages: 4264, PDF Size: 72.63 MB
Page 2295 of 4264
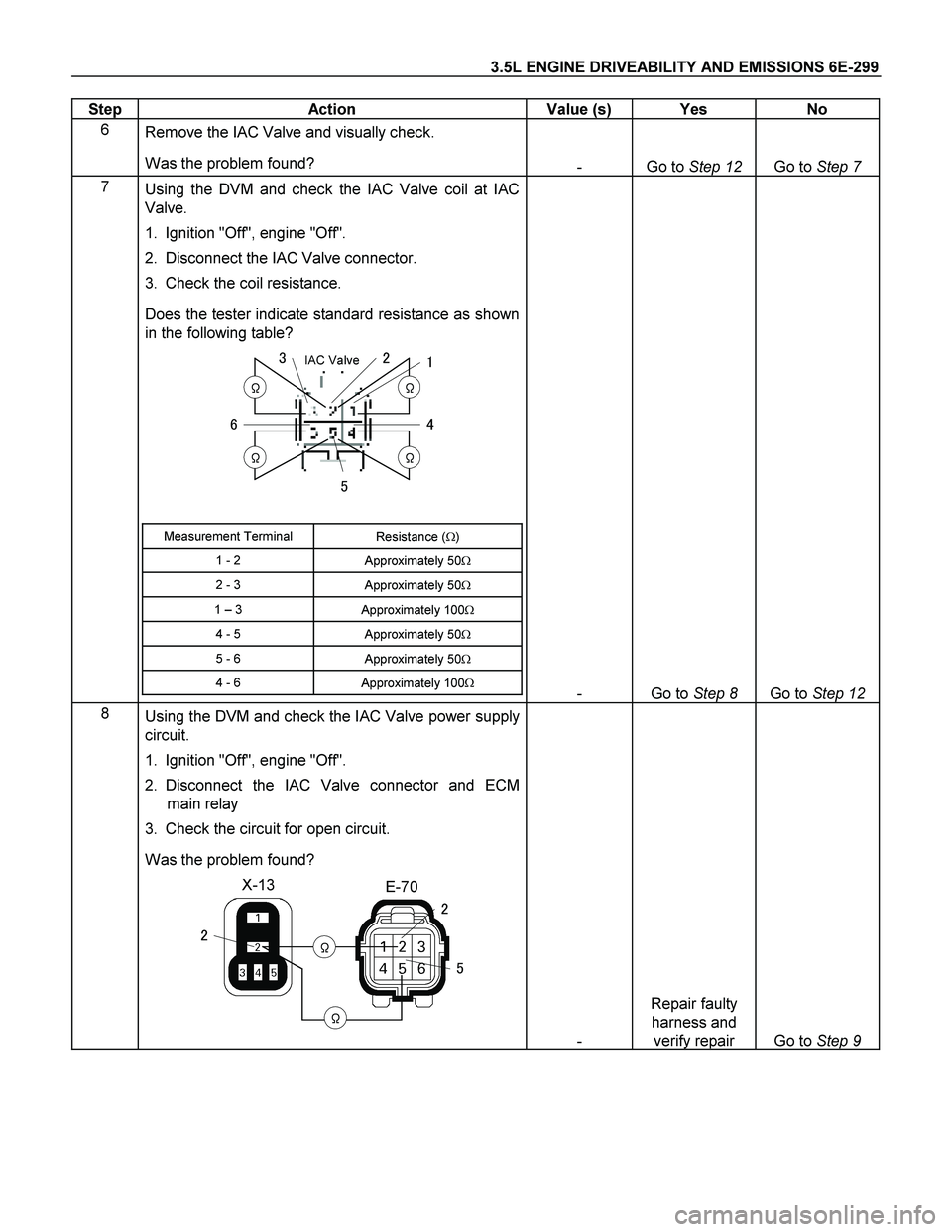
3.5L ENGINE DRIVEABILITY AND EMISSIONS 6E-299
Step Action Value (s) Yes No
6
Remove the IAC Valve and visually check.
Was the problem found?
- Go to Step 12 Go to Step 7
7
Using the DVM and check the IAC Valve coil at IAC
Valve.
1. Ignition "Off", engine "Off".
2. Disconnect the IAC Valve connector.
3. Check the coil resistance.
Does the tester indicate standard resistance as shown
in the following table?
IAC Valve
Measurement Terminal Resistance ()
1 - 2 Approximately 50
2 - 3 Approximately 50
1 – 3 Approximately 100
4 - 5 Approximately 50
5 - 6 Approximately 50
4 - 6 Approximately 100
-
Go to Step 8
Go to Step 12
8
Using the DVM and check the IAC Valve power supply
circuit.
1. Ignition "Off", engine "Off".
2. Disconnect the IAC Valve connector and ECM
main relay
3. Check the circuit for open circuit.
Was the problem found?
X-13E-70
-
Repair faulty
harness and
verify repair
Go to Step 9
Page 2296 of 4264
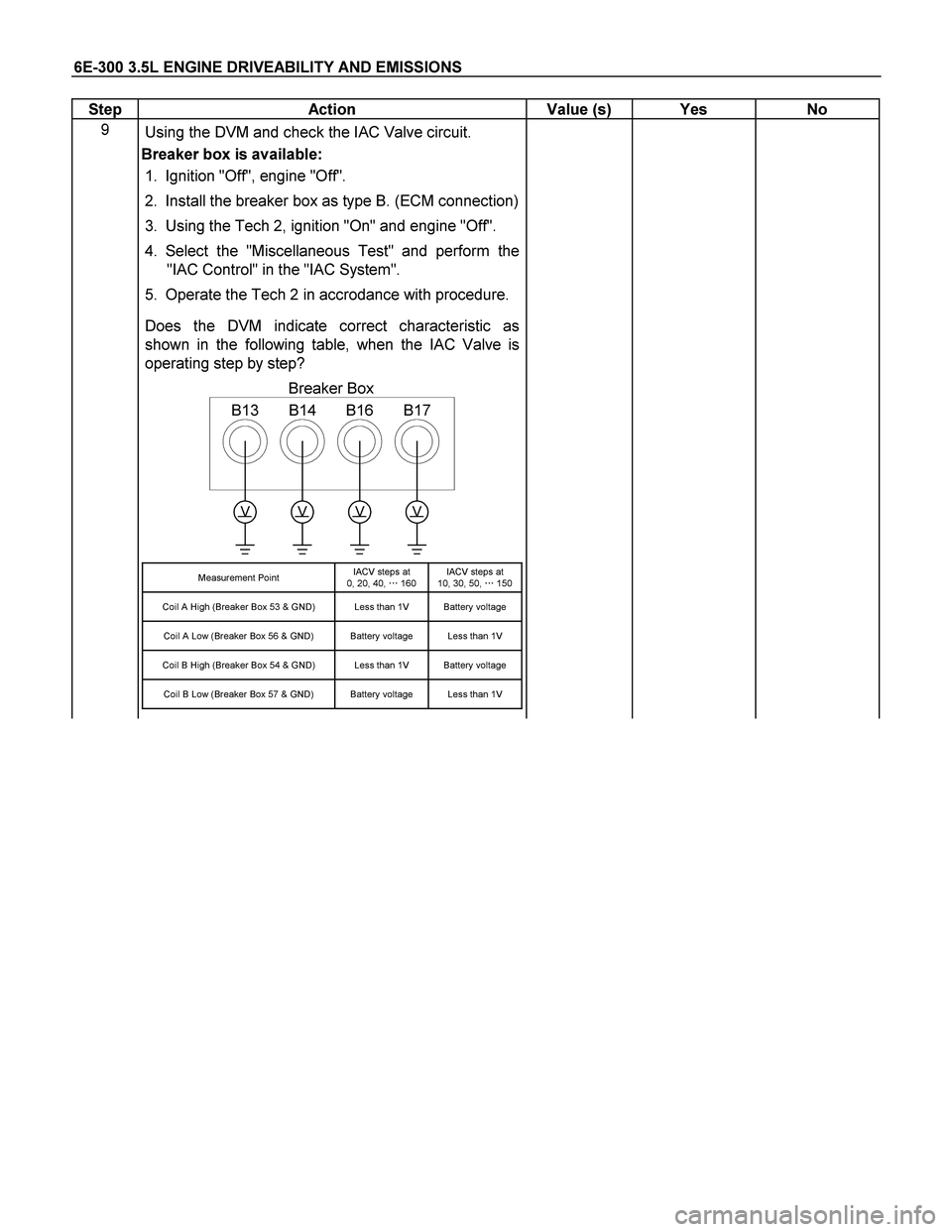
6E-300 3.5L ENGINE DRIVEABILITY AND EMISSIONS
Step Action Value (s) Yes No
9
Using the DVM and check the IAC Valve circuit.
Breaker box is available:
1. Ignition "Off", engine "Off".
2. Install the breaker box as type B. (ECM connection)
3. Using the Tech 2, ignition "On" and engine "Off".
4. Select the "Miscellaneous Test" and perform the
"IAC Control" in the "IAC System".
5. Operate the Tech 2 in accrodance with procedure.
Does the DVM indicate correct characteristic as
shown in the following table, when the IAC Valve is
operating step by step?
B13B14 Breaker BoxB17 B16
VVVV
Measurement Point IACV steps at 0, 20, 40, 160 IACV steps at 10, 30, 50, 150
Coil A High (Breaker Box 53 & GND) Less than 1V Battery voltage
Coil A Low (Breaker Box 56 & GND) Battery voltage Less than 1V
Coil B High (Breaker Box 54 & GND) Less than 1V Battery voltage
Coil B Low (Breaker Box 57 & GND) Battery voltage Less than 1V
Page 2297 of 4264
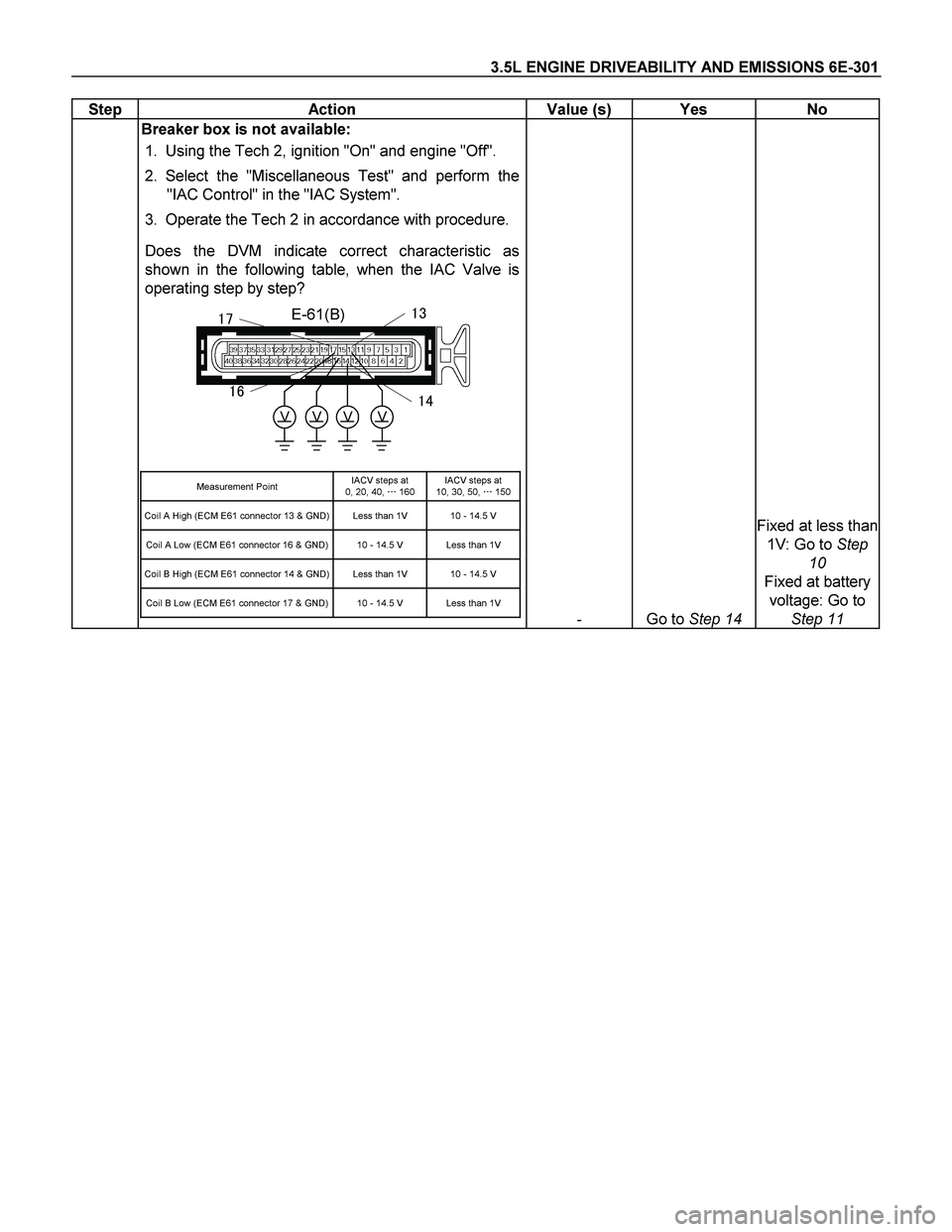
3.5L ENGINE DRIVEABILITY AND EMISSIONS 6E-301
Step Action Value (s) Yes No
Breaker box is not available:
1. Using the Tech 2, ignition "On" and engine "Off".
2. Select the "Miscellaneous Test" and perform the
"IAC Control" in the "IAC System".
3. Operate the Tech 2 in accordance with procedure.
Does the DVM indicate correct characteristic as
shown in the following table, when the IAC Valve is
operating step by step?
E-61(B)
VVVV
Measurement Point IACV steps at 0, 20, 40, 160 IACV steps at 10, 30, 50, 150
Coil A High (ECM E61 connector 13 & GND) Less than 1V 10 - 14.5 V
Coil A Low (ECM E61 connector 16 & GND) 10 - 14.5 V Less than 1V
Coil B High (ECM E61 connector 14 & GND) Less than 1V 10 - 14.5 V
Coil B Low (ECM E61 connector 17 & GND) 10 - 14.5 V Less than 1V
-
Go to Step 14 Fixed at less than
1V: Go to Step
10
Fixed at battery
voltage: Go to
Step 11
Page 2300 of 4264
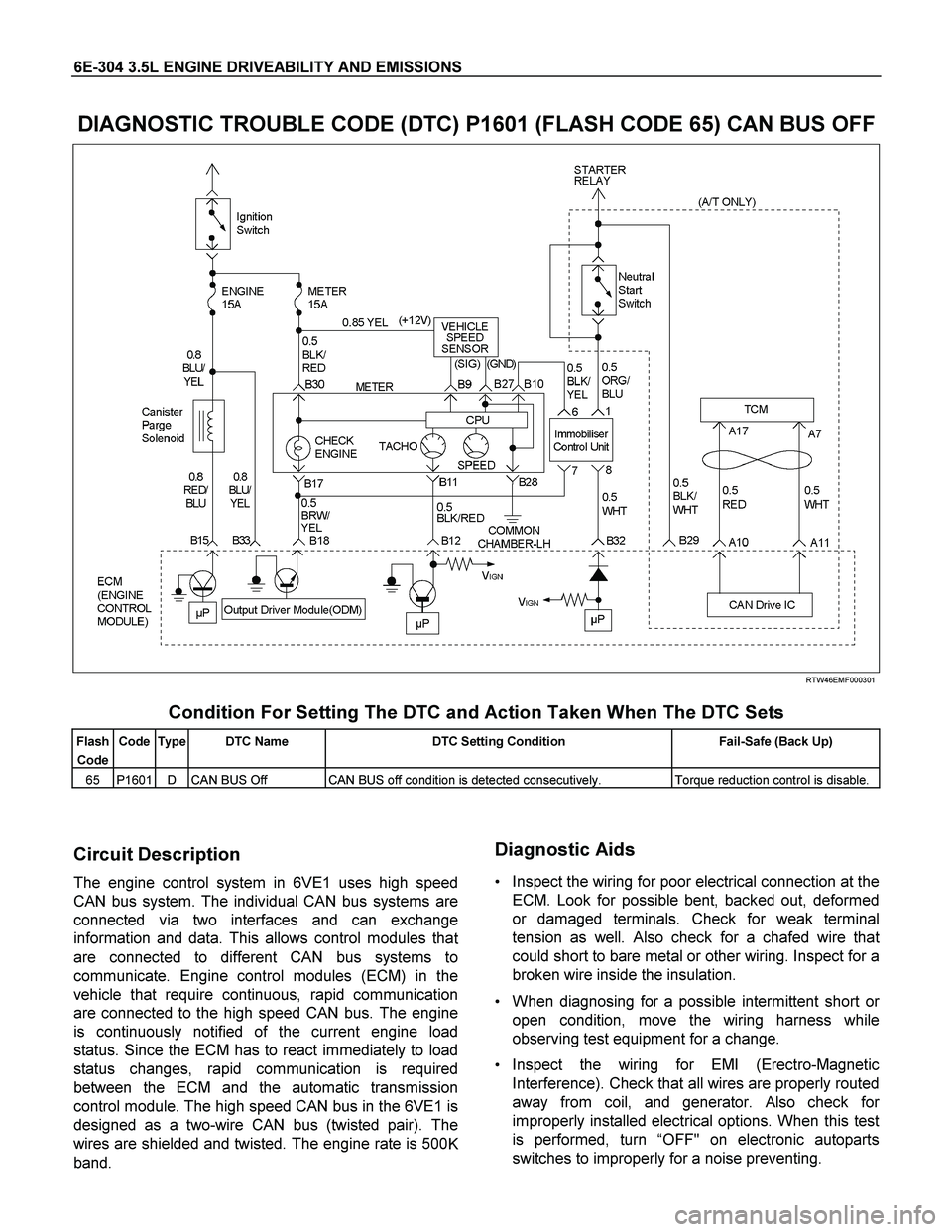
6E-304 3.5L ENGINE DRIVEABILITY AND EMISSIONS
DIAGNOSTIC TROUBLE CODE (DTC) P1601 (FLASH CODE 65) CAN BUS OFF
RTW46EMF000301
Condition For Setting The DTC and Action Taken When The DTC Sets
Flash
Code Code Type DTC Name DTC Setting Condition Fail-Safe (Back Up)
65 P1601 D CAN BUS Off CAN BUS off condition is detected consecutively. Torque reduction control is disable.
Circuit Description
The engine control system in 6VE1 uses high speed
CAN bus system. The individual CAN bus systems are
connected via two interfaces and can exchange
information and data. This allows control modules tha
t
are connected to different CAN bus systems to
communicate. Engine control modules (ECM) in the
vehicle that require continuous, rapid communication
are connected to the high speed CAN bus. The engine
is continuously notified of the current engine load
status. Since the ECM has to react immediately to load
status changes, rapid communication is required
between the ECM and the automatic transmission
control module. The high speed CAN bus in the 6VE1 is
designed as a two-wire CAN bus (twisted pair). The
wires are shielded and twisted. The engine rate is 500
K
band.
Diagnostic Aids
Inspect the wiring for poor electrical connection at the
ECM. Look for possible bent, backed out, deformed
or damaged terminals. Check for weak terminal
tension as well. Also check for a chafed wire tha
t
could short to bare metal or other wiring. Inspect for a
broken wire inside the insulation.
When diagnosing for a possible intermittent short o
r
open condition, move the wiring harness while
observing test equipment for a change.
Inspect the wiring for EMI (Erectro-Magnetic
Interference). Check that all wires are properly routed
away from coil, and generator. Also check fo
r
improperly installed electrical options. When this test
is performed, turn “OFF" on electronic autoparts
switches to improperly for a noise preventing.
Page 2306 of 4264
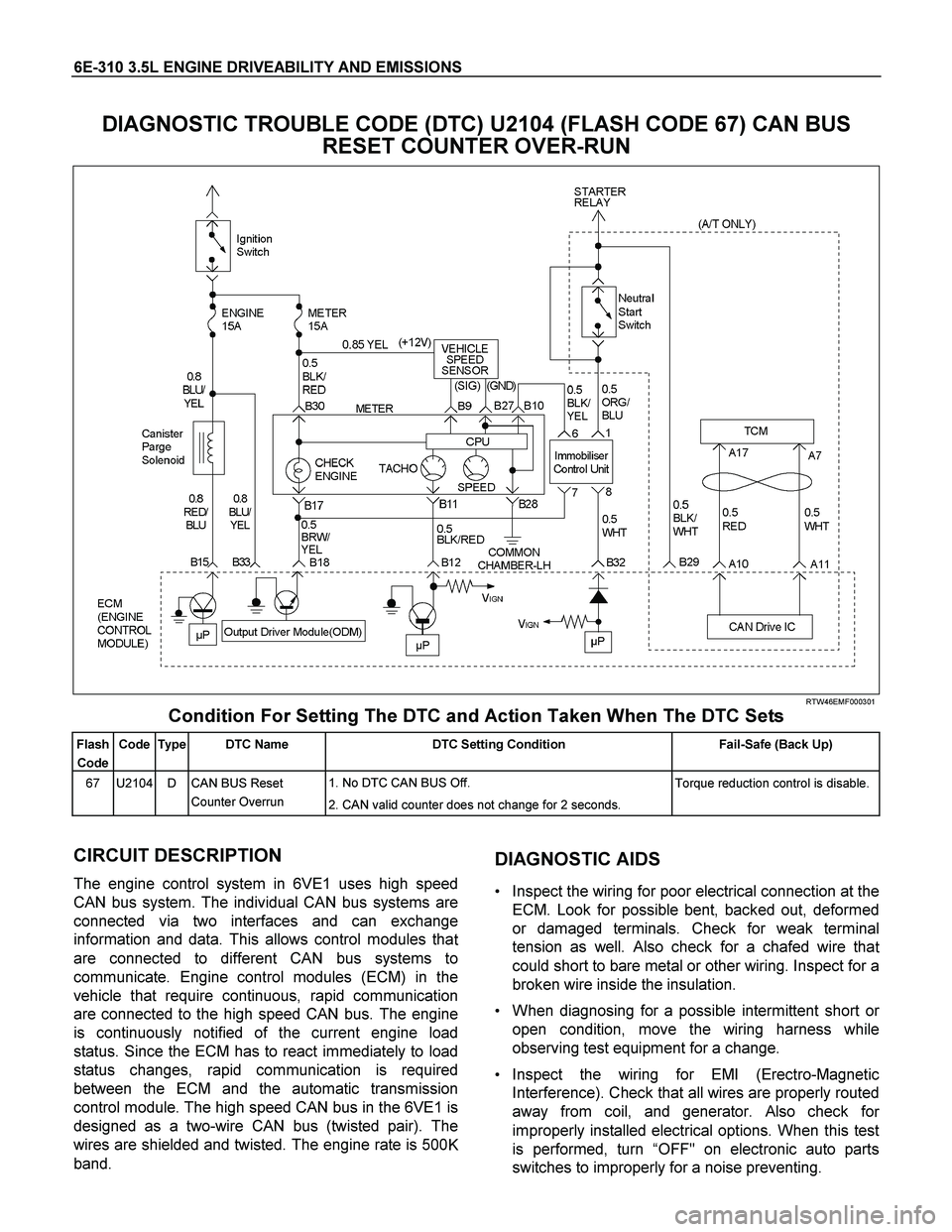
6E-310 3.5L ENGINE DRIVEABILITY AND EMISSIONS
DIAGNOSTIC TROUBLE CODE (DTC) U2104 (FLASH CODE 67) CAN BUS
RESET COUNTER OVER-RUN
RTW46EMF000301
Condition For Setting The DTC and Action Taken When The DTC Sets
Flash
Code Code Type DTC Name DTC Setting Condition Fail-Safe (Back Up)
67 U2104 D CAN BUS Reset
Counter Overrun 1. No DTC CAN BUS Off.
2. CAN valid counter does not change for 2 seconds. Torque reduction control is disable.
CIRCUIT DESCRIPTION
The engine control system in 6VE1 uses high speed
CAN bus system. The individual CAN bus systems are
connected via two interfaces and can exchange
information and data. This allows control modules tha
t
are connected to different CAN bus systems to
communicate. Engine control modules (ECM) in the
vehicle that require continuous, rapid communication
are connected to the high speed CAN bus. The engine
is continuously notified of the current engine load
status. Since the ECM has to react immediately to load
status changes, rapid communication is required
between the ECM and the automatic transmission
control module. The high speed CAN bus in the 6VE1 is
designed as a two-wire CAN bus (twisted pair). The
wires are shielded and twisted. The engine rate is 500
K
band.
DIAGNOSTIC AIDS
Inspect the wiring for poor electrical connection at the
ECM. Look for possible bent, backed out, deformed
or damaged terminals. Check for weak terminal
tension as well. Also check for a chafed wire tha
t
could short to bare metal or other wiring. Inspect for a
broken wire inside the insulation.
When diagnosing for a possible intermittent short o
r
open condition, move the wiring harness while
observing test equipment for a change.
Inspect the wiring for EMI (Erectro-Magnetic
Interference). Check that all wires are properly routed
away from coil, and generator. Also check fo
r
improperly installed electrical options. When this test
is performed, turn “OFF" on electronic auto parts
switches to improperly for a noise preventing.
Page 2325 of 4264
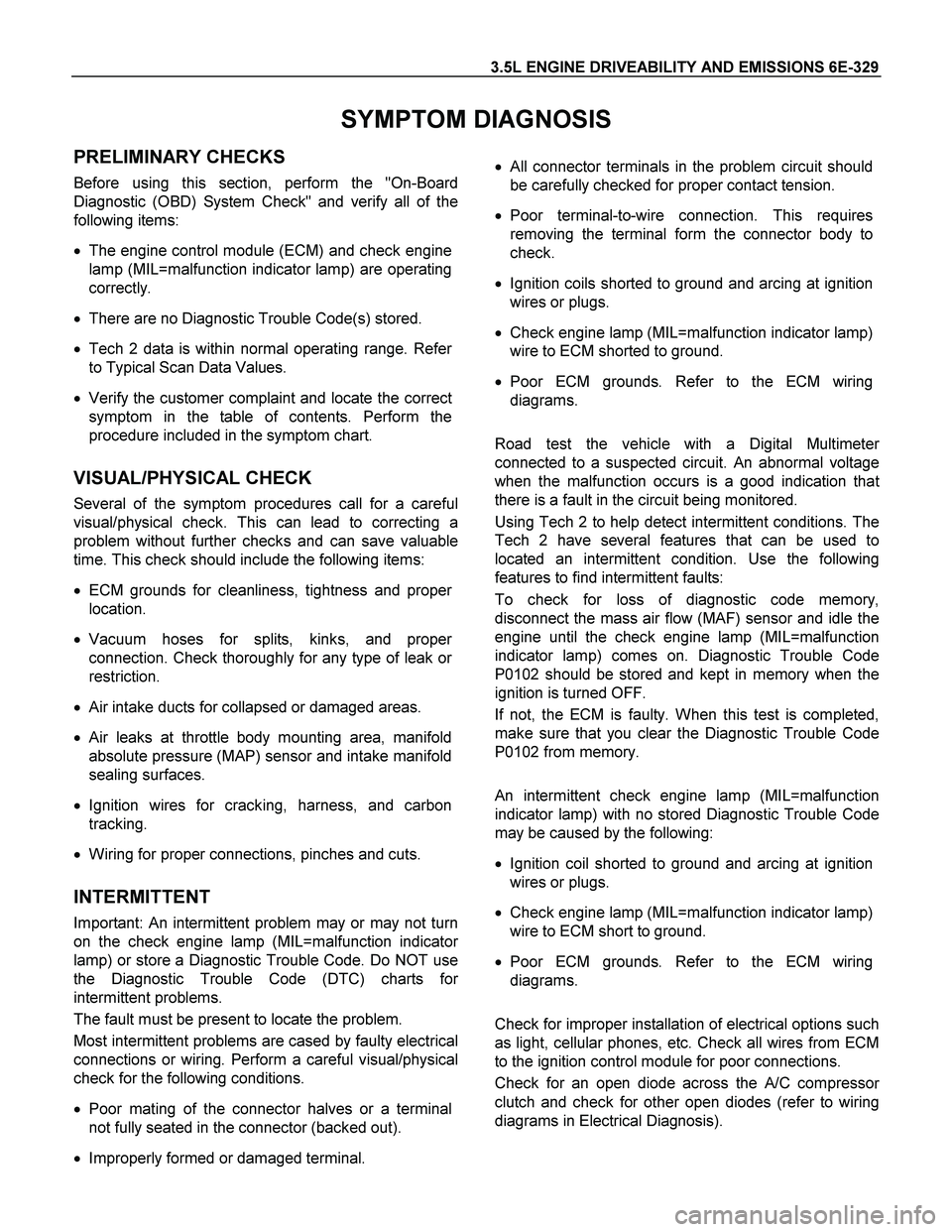
3.5L ENGINE DRIVEABILITY AND EMISSIONS 6E-329
SYMPTOM DIAGNOSIS
PRELIMINARY CHECKS
Before using this section, perform the "On-Board
Diagnostic (OBD) System Check" and verify all of the
following items:
The engine control module (ECM) and check engine
lamp (MIL=malfunction indicator lamp) are operating
correctly.
There are no Diagnostic Trouble Code(s) stored.
Tech 2 data is within normal operating range. Refer
to Typical Scan Data Values.
Verify the customer complaint and locate the correct
symptom in the table of contents. Perform the
procedure included in the symptom chart.
VISUAL/PHYSICAL CHECK
Several of the symptom procedures call for a careful
visual/physical check. This can lead to correcting a
problem without further checks and can save valuable
time. This check should include the following items:
ECM grounds for cleanliness, tightness and proper
location.
Vacuum hoses for splits, kinks, and proper
connection. Check thoroughly for any type of leak or
restriction.
Air intake ducts for collapsed or damaged areas.
Air leaks at throttle body mounting area, manifold
absolute pressure (MAP) sensor and intake manifold
sealing surfaces.
Ignition wires for cracking, harness, and carbon
tracking.
Wiring for proper connections, pinches and cuts.
INTERMITTENT
Important: An intermittent problem may or may not turn
on the check engine lamp (MIL=malfunction indicato
r
lamp) or store a Diagnostic Trouble Code. Do NOT use
the Diagnostic Trouble Code (DTC) charts fo
r
intermittent problems.
The fault must be present to locate the problem.
Most intermittent problems are cased by faulty electrical
connections or wiring. Perform a careful visual/physical
check for the following conditions.
Poor mating of the connector halves or a terminal
not fully seated in the connector (backed out).
Improperly formed or damaged terminal.
All connector terminals in the problem circuit should
be carefully checked for proper contact tension.
Poor terminal-to-wire connection. This requires
removing the terminal form the connector body to
check.
Ignition coils shorted to ground and arcing at ignition
wires or plugs.
Check engine lamp (MIL=malfunction indicator lamp)
wire to ECM shorted to ground.
Poor ECM grounds. Refer to the ECM wiring
diagrams.
Road test the vehicle with a Digital Multimete
r
connected to a suspected circuit. An abnormal voltage
when the malfunction occurs is a good indication tha
t
there is a fault in the circuit being monitored.
Using Tech 2 to help detect intermittent conditions. The
Tech 2 have several features that can be used to
located an intermittent condition. Use the following
features to find intermittent faults:
To check for loss of diagnostic code memory,
disconnect the mass air flow (MAF) sensor and idle the
engine until the check engine lamp (MIL=malfunction
indicator lamp) comes on. Diagnostic Trouble Code
P0102 should be stored and kept in memory when the
ignition is turned OFF.
If not, the ECM is faulty. When this test is completed,
make sure that you clear the Diagnostic Trouble Code
P0102 from memory.
An intermittent check engine lamp (MIL=malfunction
indicator lamp) with no stored Diagnostic Trouble Code
may be caused by the following:
Ignition coil shorted to ground and arcing at ignition
wires or plugs.
Check engine lamp (MIL=malfunction indicator lamp)
wire to ECM short to ground.
Poor ECM grounds. Refer to the ECM wiring
diagrams.
Check for improper installation of electrical options such
as light, cellular phones, etc. Check all wires from ECM
to the ignition control module for poor connections.
Check for an open diode across the A/C compresso
r
clutch and check for other open diodes (refer to wiring
diagrams in Electrical Diagnosis).
Page 2327 of 4264
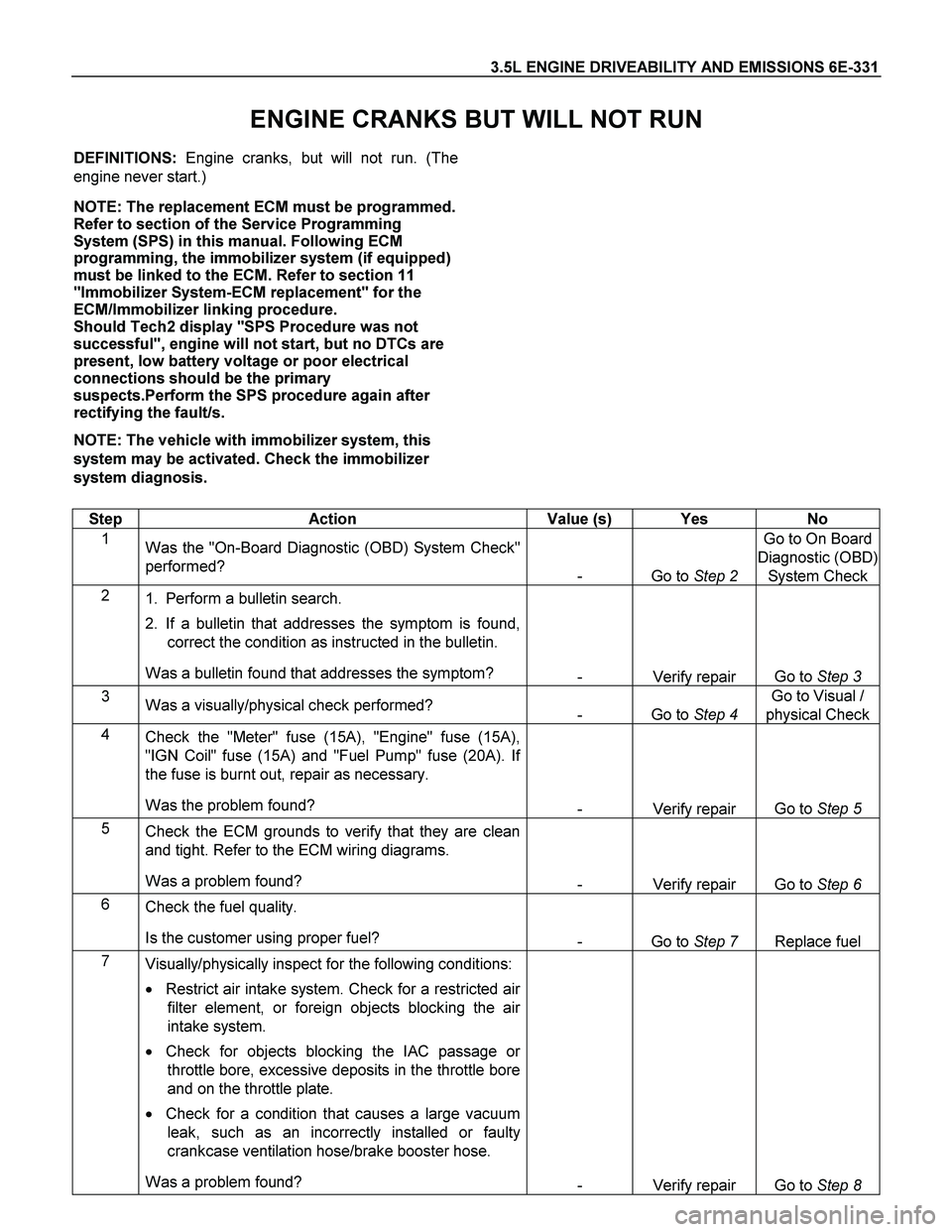
3.5L ENGINE DRIVEABILITY AND EMISSIONS 6E-331
ENGINE CRANKS BUT WILL NOT RUN
DEFINITIONS: Engine cranks, but will not run. (The
engine never start.)
NOTE: The replacement ECM must be programmed.
Refer to section of the Service Programming
System (SPS) in this manual. Following ECM
programming, the immobilizer system (if equipped)
must be linked to the ECM. Refer to section 11
"Immobilizer System-ECM replacement" for the
ECM/Immobilizer linking procedure.
Should Tech2 display "SPS Procedure was not
successful", engine will not start, but no DTCs are
present, low battery voltage or poor electrical
connections should be the primary
suspects.Perform the SPS procedure again after
rectifying the fault/s.
NOTE: The vehicle with immobilizer system, this
system may be activated. Check the immobilizer
system diagnosis.
Step Action Value (s) Yes No
1
Was the "On-Board Diagnostic (OBD) System Check"
performed?
- Go to Step 2 Go to On Board
Diagnostic (OBD)
System Check
2
1. Perform a bulletin search.
2. If a bulletin that addresses the symptom is found,
correct the condition as instructed in the bulletin.
Was a bulletin found that addresses the symptom?
- Verify repair Go to Step 3
3
Was a visually/physical check performed?
- Go to Step 4 Go to Visual /
physical Check
4
Check the "Meter" fuse (15A), "Engine" fuse (15A),
"IGN Coil" fuse (15A) and "Fuel Pump" fuse (20A). If
the fuse is burnt out, repair as necessary.
Was the problem found?
- Verify repair Go to Step 5
5
Check the ECM grounds to verify that they are clean
and tight. Refer to the ECM wiring diagrams.
Was a problem found?
- Verify repair Go to Step 6
6
Check the fuel quality.
Is the customer using proper fuel?
- Go to Step 7
Replace fuel
7
Visually/physically inspect for the following conditions:
Restrict air intake system. Check for a restricted air
filter element, or foreign objects blocking the air
intake system.
Check for objects blocking the IAC passage or
throttle bore, excessive deposits in the throttle bore
and on the throttle plate.
Check for a condition that causes a large vacuum
leak, such as an incorrectly installed or faulty
crankcase ventilation hose/brake booster hose.
Was a problem found?
- Verify repair Go to Step 8
Page 2328 of 4264
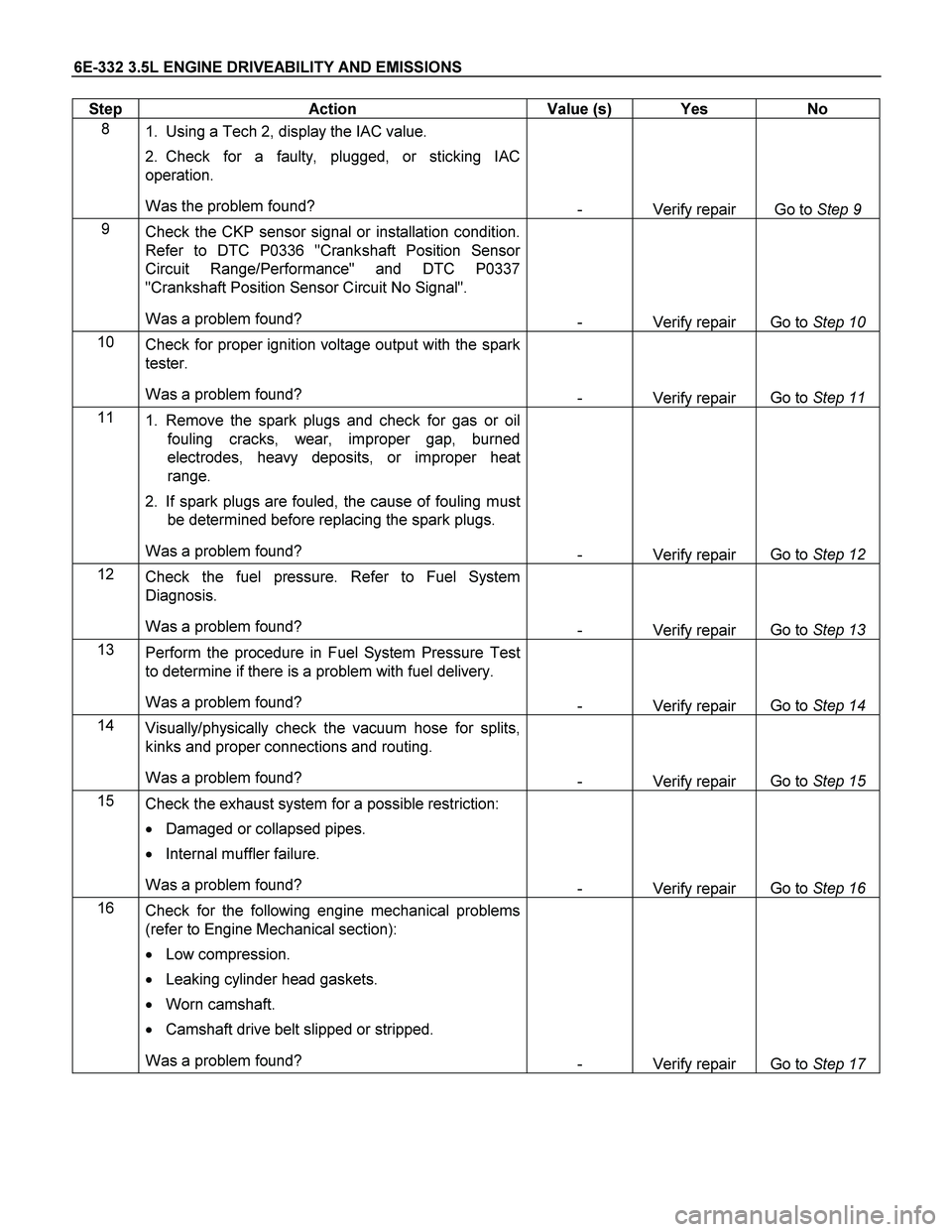
6E-332 3.5L ENGINE DRIVEABILITY AND EMISSIONS
Step Action Value (s) Yes No
8
1. Using a Tech 2, display the IAC value.
2. Check for a faulty, plugged, or sticking IAC
operation.
Was the problem found?
- Verify repair Go to Step 9
9
Check the CKP sensor signal or installation condition.
Refer to DTC P0336 "Crankshaft Position Sensor
Circuit Range/Performance" and DTC P0337
"Crankshaft Position Sensor Circuit No Signal".
Was a problem found?
- Verify repair Go to Step 10
10
Check for proper ignition voltage output with the spark
tester.
Was a problem found?
- Verify repair Go to Step 11
11
1. Remove the spark plugs and check for gas or oil
fouling cracks, wear, improper gap, burned
electrodes, heavy deposits, or improper heat
range.
2. If spark plugs are fouled, the cause of fouling must
be determined before replacing the spark plugs.
Was a problem found?
- Verify repair Go to Step 12
12
Check the fuel pressure. Refer to Fuel System
Diagnosis.
Was a problem found?
- Verify repair Go to Step 13
13
Perform the procedure in Fuel System Pressure Test
to determine if there is a problem with fuel delivery.
Was a problem found?
- Verify repair Go to Step 14
14
Visually/physically check the vacuum hose for splits,
kinks and proper connections and routing.
Was a problem found?
- Verify repair Go to Step 15
15
Check the exhaust system for a possible restriction:
Damaged or collapsed pipes.
Internal muffler failure.
Was a problem found?
- Verify repair Go to Step 16
16
Check for the following engine mechanical problems
(refer to Engine Mechanical section):
Low compression.
Leaking cylinder head gaskets.
Worn camshaft.
Camshaft drive belt slipped or stripped.
Was a problem found?
- Verify repair Go to Step 17
Page 2331 of 4264

3.5L ENGINE DRIVEABILITY AND EMISSIONS 6E-335
Step Action Value (s) Yes No
10
1. Remove the spark plugs and check for gas or oil
fouling cracks, wear, improper gap, burned
electrodes, heavy deposits, or improper heat
range.
2. If spark plugs are fouled, the cause of fouling must
be determined before replacing the spark plugs.
Was a problem found?
- Verify repair Go to Step 11
11
Check for water or alcohol contaminated fuel.
Was a problem found?
- Verify repair Go to Step 12
12
Perform the procedure in Fuel System Pressure Test
to determine if there is a problem with fuel delivery.
Refer to 6E-116 page.
Was a problem found?
- Verify repair Go to Step 13
13
1. Check the injector connectors.
2. If any of the connectors are connected at an
improper cylinder, connect as necessary.
Was a problem found?
- Verify repair Go to Step 14
14
Check for the following engine mechanical problems
(refer to Engine Mechanical section):
Low compression.
Leaking cylinder head gaskets.
Worn camshaft.
Camshaft drive belt slipped or stripped.
Was a problem found?
- Verify repair Go to Step 15
15
1. Review all diagnostic procedures within this table.
2. If all procedures have been completed and no
malfunctions have been found, review/inspect the
following:
Visual/physical inspection.
Tech 2 data.
All electrical connections within a suspected circuit
and/or system.
Was a problem found?
- Verify repair Go to Step 16
16
Is the ECM programmed with the latest software
release?
If not, download the latest software to the ECM using
the "SPS (Service Programming System)".
Was the problem solved?
- Verify repair Go to Step 17
Page 2335 of 4264
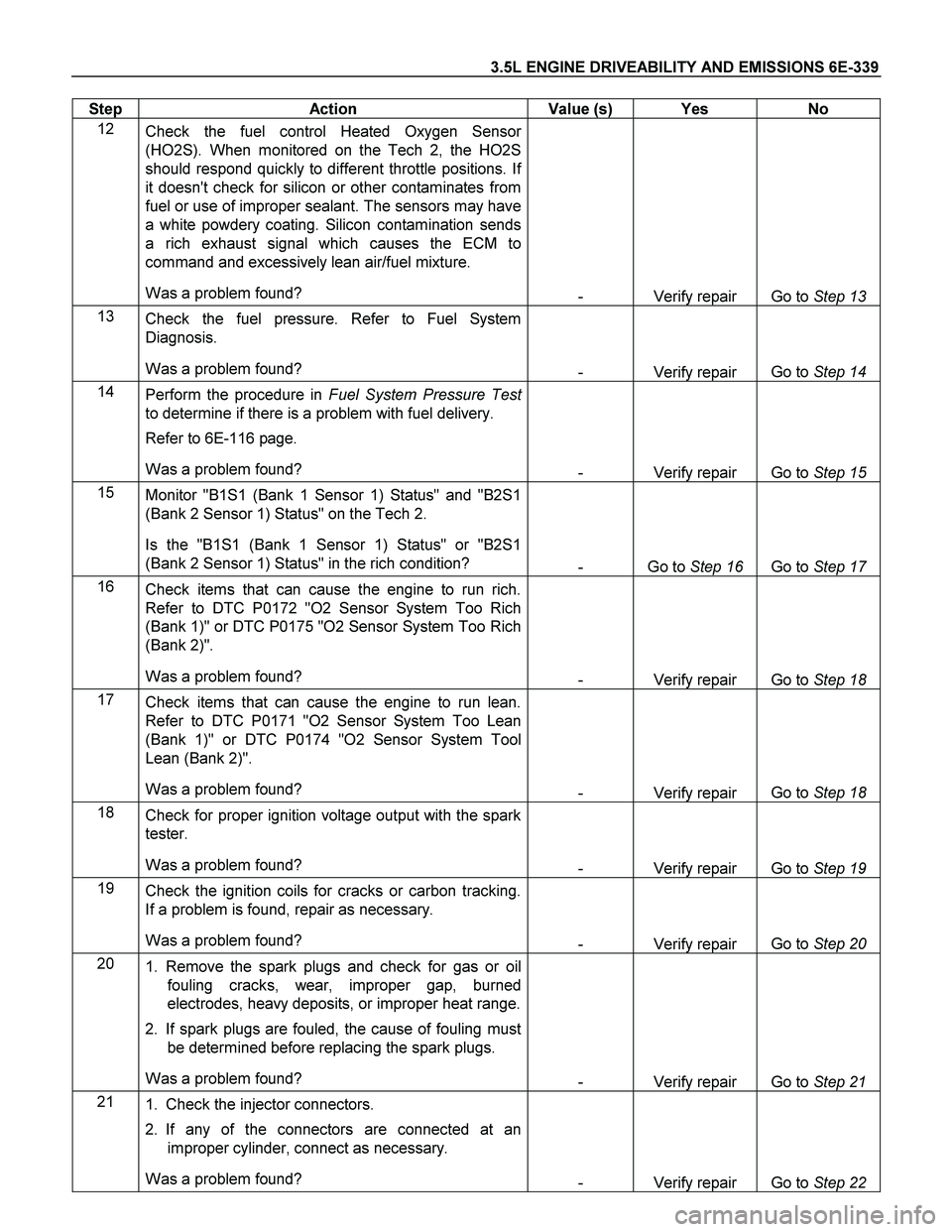
3.5L ENGINE DRIVEABILITY AND EMISSIONS 6E-339
Step Action Value (s) Yes No
12
Check the fuel control Heated Oxygen Sensor
(HO2S). When monitored on the Tech 2, the HO2S
should respond quickly to different throttle positions. If
it doesn't check for silicon or other contaminates from
fuel or use of improper sealant. The sensors may have
a white powdery coating. Silicon contamination sends
a rich exhaust signal which causes the ECM to
command and excessively lean air/fuel mixture.
Was a problem found?
- Verify repair Go to Step 13
13
Check the fuel pressure. Refer to Fuel System
Diagnosis.
Was a problem found?
- Verify repair Go to Step 14
14
Perform the procedure in Fuel System Pressure Test
to determine if there is a problem with fuel delivery.
Refer to 6E-116 page.
Was a problem found?
- Verify repair Go to Step 15
15
Monitor "B1S1 (Bank 1 Sensor 1) Status" and "B2S1
(Bank 2 Sensor 1) Status" on the Tech 2.
Is the "B1S1 (Bank 1 Sensor 1) Status" or "B2S1
(Bank 2 Sensor 1) Status" in the rich condition?
- Go to Step 16 Go to Step 17
16
Check items that can cause the engine to run rich.
Refer to DTC P0172 "O2 Sensor System Too Rich
(Bank 1)" or DTC P0175 "O2 Sensor System Too Rich
(Bank 2)".
Was a problem found?
- Verify repair Go to Step 18
17
Check items that can cause the engine to run lean.
Refer to DTC P0171 "O2 Sensor System Too Lean
(Bank 1)" or DTC P0174 "O2 Sensor System Tool
Lean (Bank 2)".
Was a problem found?
- Verify repair Go to Step 18
18
Check for proper ignition voltage output with the spark
tester.
Was a problem found?
- Verify repair Go to Step 19
19
Check the ignition coils for cracks or carbon tracking.
If a problem is found, repair as necessary.
Was a problem found?
- Verify repair Go to Step 20
20
1. Remove the spark plugs and check for gas or oil
fouling cracks, wear, improper gap, burned
electrodes, heavy deposits, or improper heat range.
2. If spark plugs are fouled, the cause of fouling must
be determined before replacing the spark plugs.
Was a problem found?
- Verify repair Go to Step 21
21
1. Check the injector connectors.
2. If any of the connectors are connected at an
improper cylinder, connect as necessary.
Was a problem found?
- Verify repair Go to Step 22