oil ISUZU TF SERIES 2004 Workshop Manual
[x] Cancel search | Manufacturer: ISUZU, Model Year: 2004, Model line: TF SERIES, Model: ISUZU TF SERIES 2004Pages: 4264, PDF Size: 72.63 MB
Page 2339 of 4264
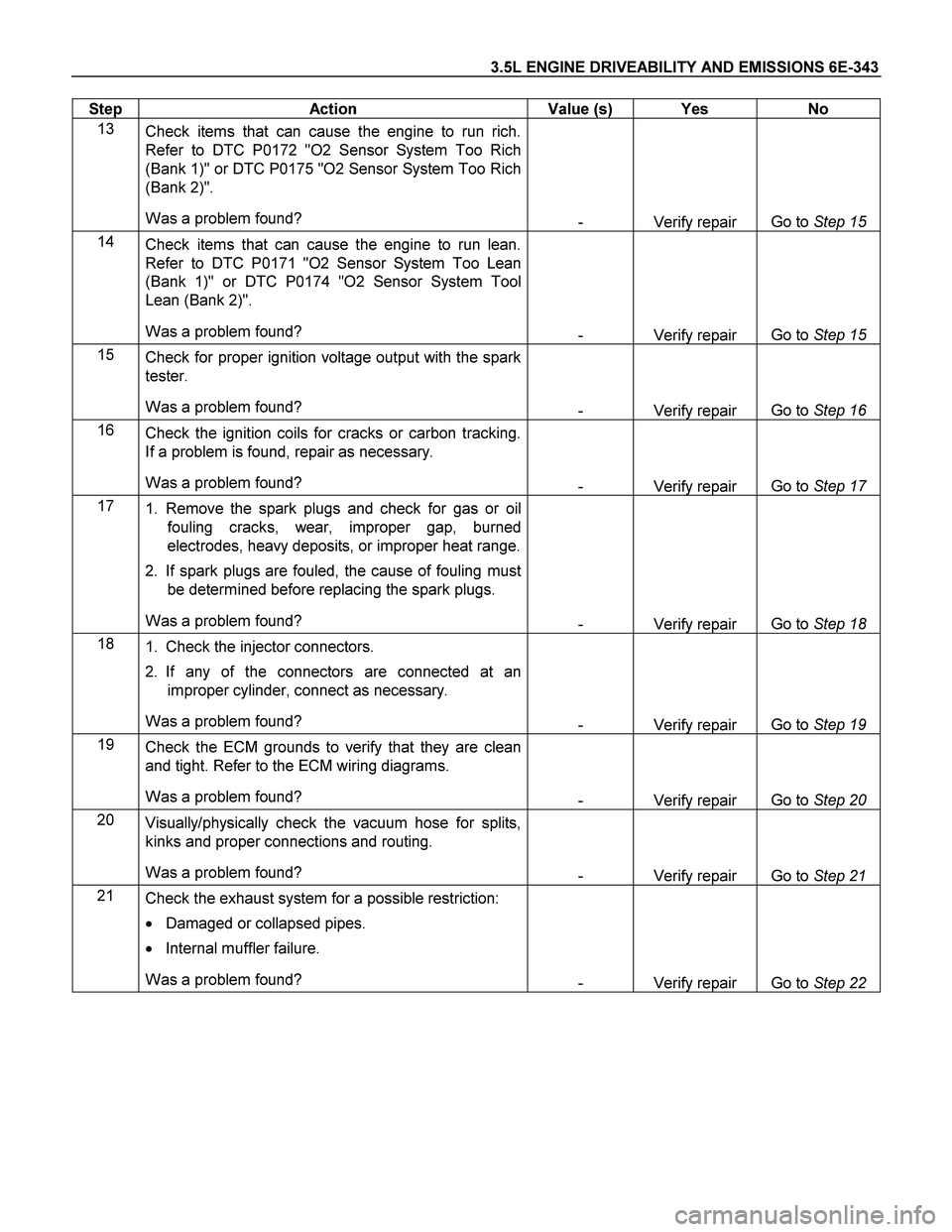
3.5L ENGINE DRIVEABILITY AND EMISSIONS 6E-343
Step Action Value (s) Yes No
13
Check items that can cause the engine to run rich.
Refer to DTC P0172 "O2 Sensor System Too Rich
(Bank 1)" or DTC P0175 "O2 Sensor System Too Rich
(Bank 2)".
Was a problem found?
- Verify repair Go to Step 15
14
Check items that can cause the engine to run lean.
Refer to DTC P0171 "O2 Sensor System Too Lean
(Bank 1)" or DTC P0174 "O2 Sensor System Tool
Lean (Bank 2)".
Was a problem found?
- Verify repair Go to Step 15
15
Check for proper ignition voltage output with the spark
tester.
Was a problem found?
- Verify repair Go to Step 16
16
Check the ignition coils for cracks or carbon tracking.
If a problem is found, repair as necessary.
Was a problem found?
- Verify repair Go to Step 17
17
1. Remove the spark plugs and check for gas or oil
fouling cracks, wear, improper gap, burned
electrodes, heavy deposits, or improper heat range.
2. If spark plugs are fouled, the cause of fouling must
be determined before replacing the spark plugs.
Was a problem found?
- Verify repair Go to Step 18
18
1. Check the injector connectors.
2. If any of the connectors are connected at an
improper cylinder, connect as necessary.
Was a problem found?
- Verify repair Go to Step 19
19
Check the ECM grounds to verify that they are clean
and tight. Refer to the ECM wiring diagrams.
Was a problem found?
- Verify repair Go to Step 20
20
Visually/physically check the vacuum hose for splits,
kinks and proper connections and routing.
Was a problem found?
- Verify repair Go to Step 21
21
Check the exhaust system for a possible restriction:
Damaged or collapsed pipes.
Internal muffler failure.
Was a problem found?
- Verify repair Go to Step 22
Page 2343 of 4264
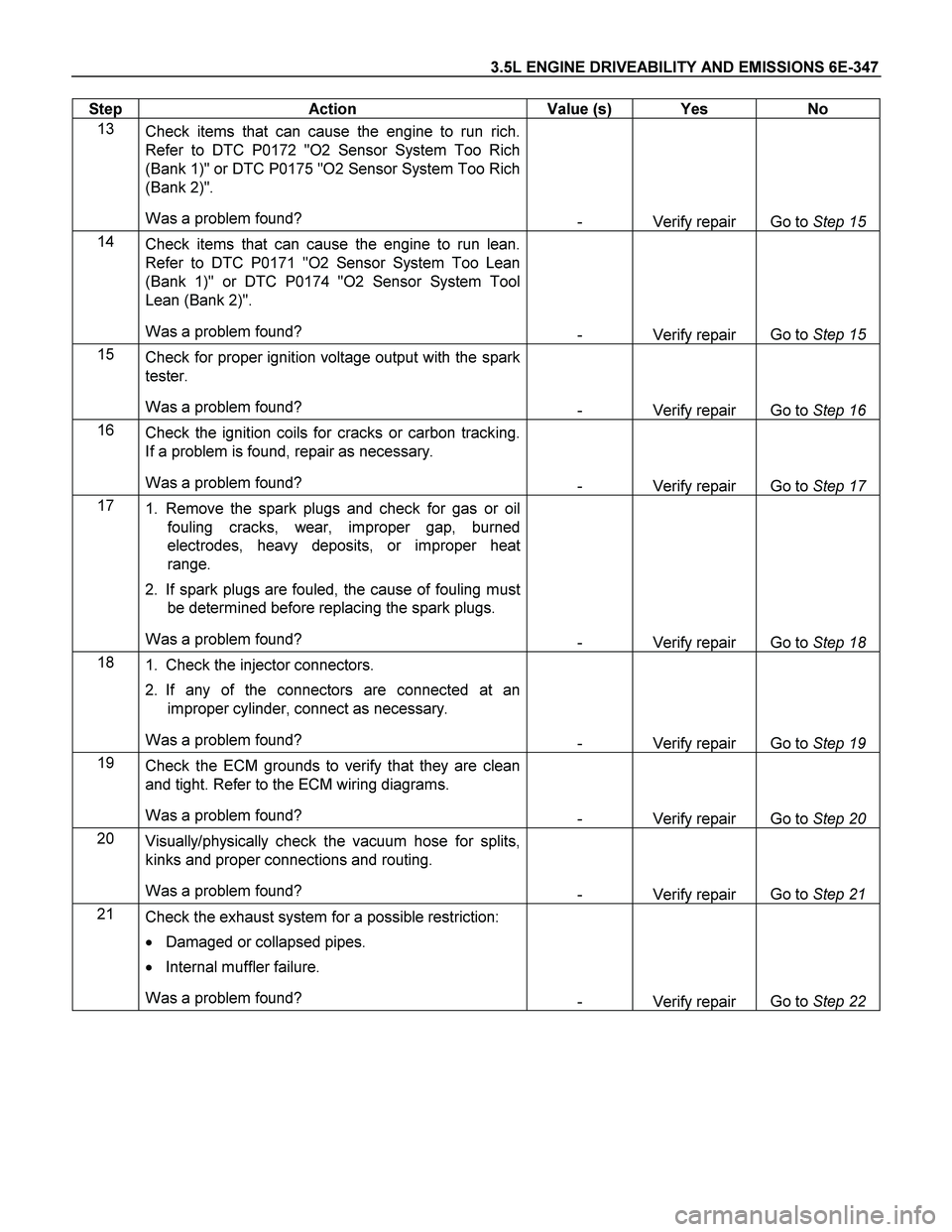
3.5L ENGINE DRIVEABILITY AND EMISSIONS 6E-347
Step Action Value (s) Yes No
13
Check items that can cause the engine to run rich.
Refer to DTC P0172 "O2 Sensor System Too Rich
(Bank 1)" or DTC P0175 "O2 Sensor System Too Rich
(Bank 2)".
Was a problem found?
- Verify repair Go to Step 15
14
Check items that can cause the engine to run lean.
Refer to DTC P0171 "O2 Sensor System Too Lean
(Bank 1)" or DTC P0174 "O2 Sensor System Tool
Lean (Bank 2)".
Was a problem found?
- Verify repair Go to Step 15
15
Check for proper ignition voltage output with the spark
tester.
Was a problem found?
- Verify repair Go to Step 16
16
Check the ignition coils for cracks or carbon tracking.
If a problem is found, repair as necessary.
Was a problem found?
- Verify repair Go to Step 17
17
1. Remove the spark plugs and check for gas or oil
fouling cracks, wear, improper gap, burned
electrodes, heavy deposits, or improper heat
range.
2. If spark plugs are fouled, the cause of fouling must
be determined before replacing the spark plugs.
Was a problem found?
- Verify repair Go to Step 18
18
1. Check the injector connectors.
2. If any of the connectors are connected at an
improper cylinder, connect as necessary.
Was a problem found?
- Verify repair Go to Step 19
19
Check the ECM grounds to verify that they are clean
and tight. Refer to the ECM wiring diagrams.
Was a problem found?
- Verify repair Go to Step 20
20
Visually/physically check the vacuum hose for splits,
kinks and proper connections and routing.
Was a problem found?
- Verify repair Go to Step 21
21
Check the exhaust system for a possible restriction:
Damaged or collapsed pipes.
Internal muffler failure.
Was a problem found?
- Verify repair Go to Step 22
Page 2346 of 4264
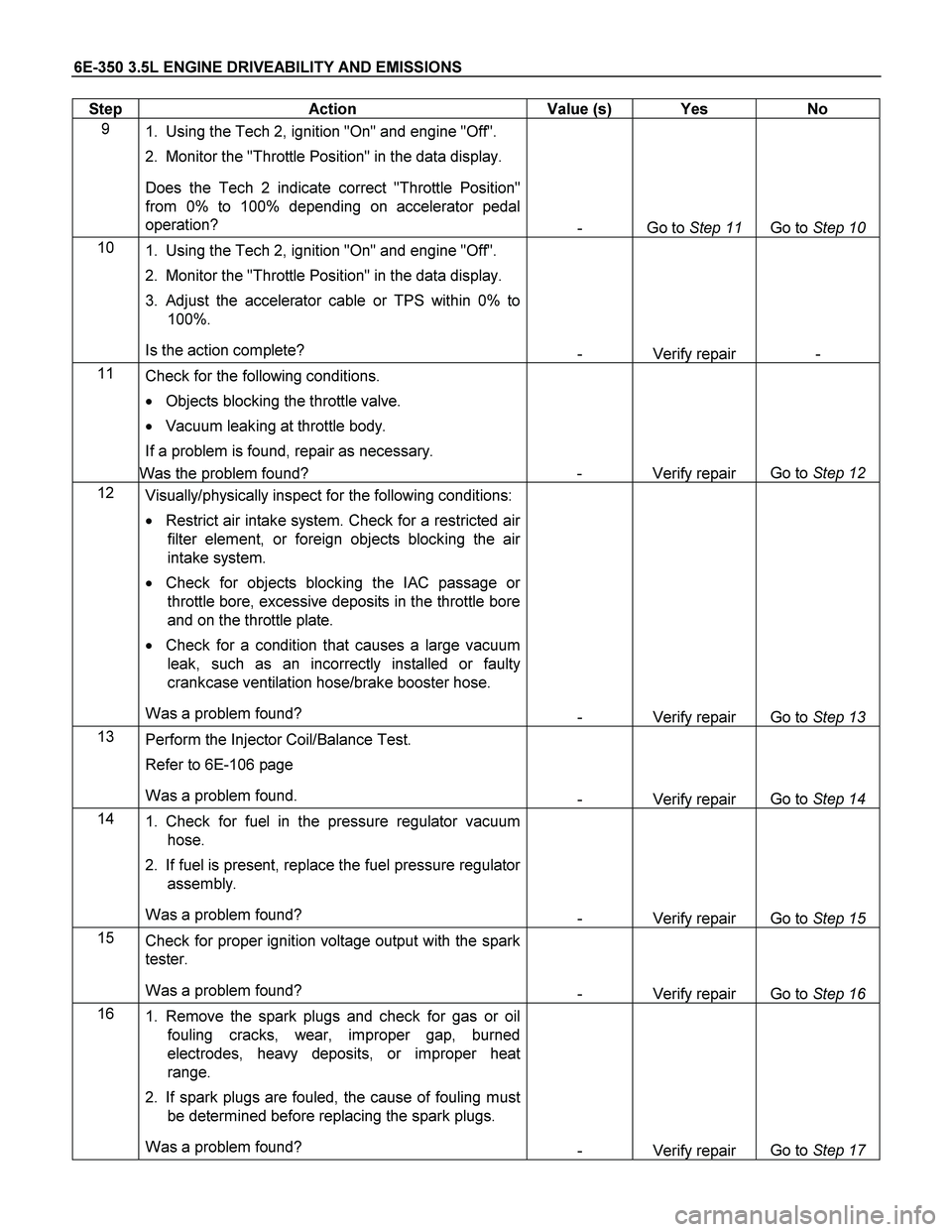
6E-350 3.5L ENGINE DRIVEABILITY AND EMISSIONS
Step Action Value (s) Yes No
9
1. Using the Tech 2, ignition "On" and engine "Off".
2. Monitor the "Throttle Position" in the data display.
Does the Tech 2 indicate correct "Throttle Position"
from 0% to 100% depending on accelerator pedal
operation?
- Go to Step 11 Go to Step 10
10
1. Using the Tech 2, ignition "On" and engine "Off".
2. Monitor the "Throttle Position" in the data display.
3. Adjust the accelerator cable or TPS within 0% to
100%.
Is the action complete?
- Verify repair -
11
Check for the following conditions.
Objects blocking the throttle valve.
Vacuum leaking at throttle body.
If a problem is found, repair as necessary.
Was the problem found? - Verify repair Go to Step 12
12
Visually/physically inspect for the following conditions:
Restrict air intake system. Check for a restricted air
filter element, or foreign objects blocking the air
intake system.
Check for objects blocking the IAC passage or
throttle bore, excessive deposits in the throttle bore
and on the throttle plate.
Check for a condition that causes a large vacuum
leak, such as an incorrectly installed or faulty
crankcase ventilation hose/brake booster hose.
Was a problem found?
- Verify repair Go to Step 13
13
Perform the Injector Coil/Balance Test.
Refer to 6E-106 page
Was a problem found.
- Verify repair Go to Step 14
14
1. Check for fuel in the pressure regulator vacuum
hose.
2. If fuel is present, replace the fuel pressure regulator
assembly.
Was a problem found?
- Verify repair Go to Step 15
15
Check for proper ignition voltage output with the spark
tester.
Was a problem found?
- Verify repair Go to Step 16
16
1. Remove the spark plugs and check for gas or oil
fouling cracks, wear, improper gap, burned
electrodes, heavy deposits, or improper heat
range.
2. If spark plugs are fouled, the cause of fouling must
be determined before replacing the spark plugs.
Was a problem found?
- Verify repair Go to Step 17
Page 2350 of 4264
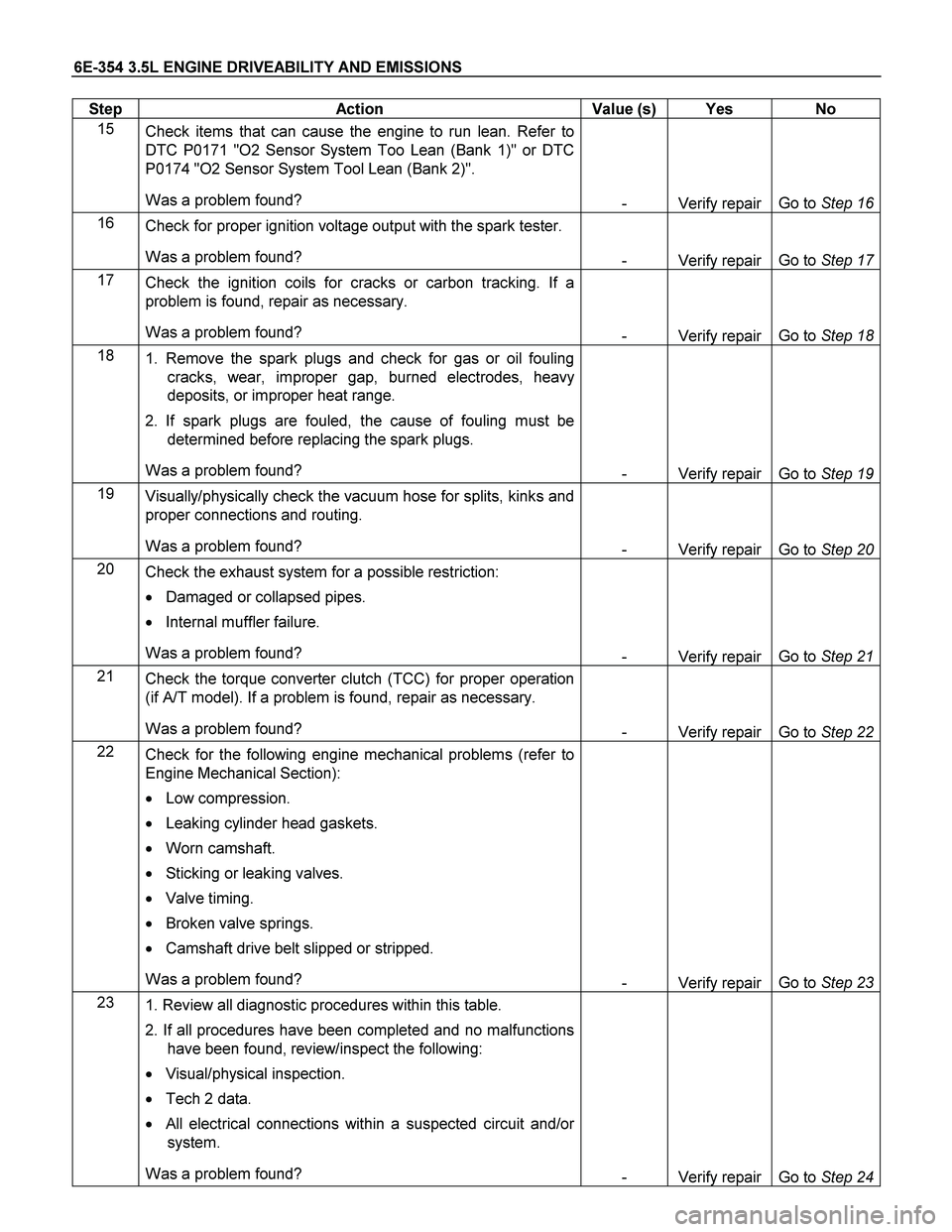
6E-354 3.5L ENGINE DRIVEABILITY AND EMISSIONS
Step Action Value (s) Yes No
15
Check items that can cause the engine to run lean. Refer to
DTC P0171 "O2 Sensor System Too Lean (Bank 1)" or DTC
P0174 "O2 Sensor System Tool Lean (Bank 2)".
Was a problem found?
- Verify repair Go to Step 16
16
Check for proper ignition voltage output with the spark tester.
Was a problem found?
- Verify repair Go to Step 17
17
Check the ignition coils for cracks or carbon tracking. If a
problem is found, repair as necessary.
Was a problem found?
- Verify repair Go to Step 18
18
1. Remove the spark plugs and check for gas or oil fouling
cracks, wear, improper gap, burned electrodes, heavy
deposits, or improper heat range.
2. If spark plugs are fouled, the cause of fouling must be
determined before replacing the spark plugs.
Was a problem found?
- Verify repair Go to Step 19
19
Visually/physically check the vacuum hose for splits, kinks and
proper connections and routing.
Was a problem found?
- Verify repair Go to Step 20
20
Check the exhaust system for a possible restriction:
Damaged or collapsed pipes.
Internal muffler failure.
Was a problem found?
- Verify repair Go to Step 21
21
Check the torque converter clutch (TCC) for proper operation
(if A/T model). If a problem is found, repair as necessary.
Was a problem found?
- Verify repair Go to Step 22
22
Check for the following engine mechanical problems (refer to
Engine Mechanical Section):
Low compression.
Leaking cylinder head gaskets.
Worn camshaft.
Sticking or leaking valves.
Valve timing.
Broken valve springs.
Camshaft drive belt slipped or stripped.
Was a problem found?
- Verify repair Go to Step 23
23
1. Review all diagnostic procedures within this table.
2. If all procedures have been completed and no malfunctions
have been found, review/inspect the following:
Visual/physical inspection.
Tech 2 data.
All electrical connections within a suspected circuit and/or
system.
Was a problem found?
- Verify repair Go to Step 24
Page 2356 of 4264
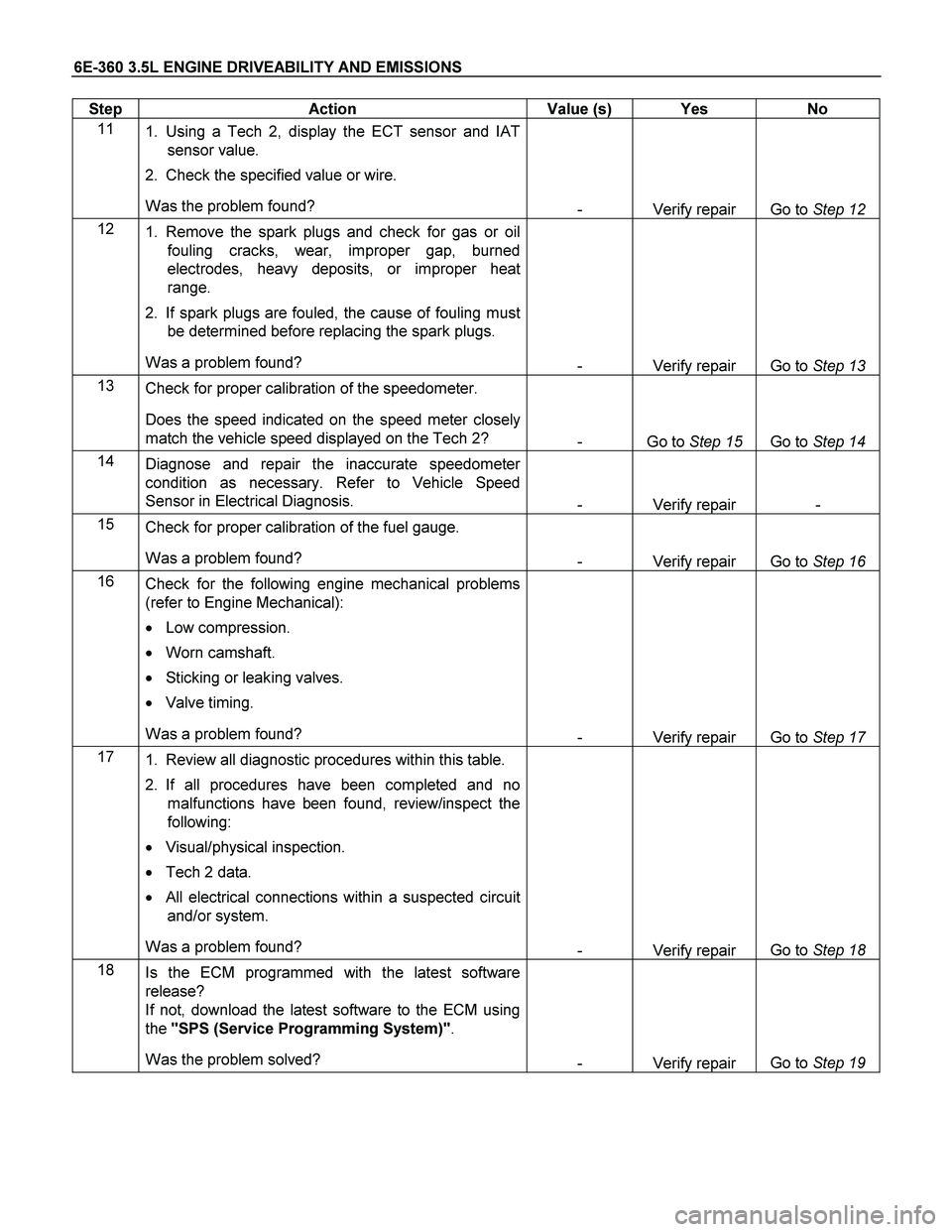
6E-360 3.5L ENGINE DRIVEABILITY AND EMISSIONS
Step Action Value (s) Yes No
11
1. Using a Tech 2, display the ECT sensor and IAT
sensor value.
2. Check the specified value or wire.
Was the problem found?
- Verify repair Go to Step 12
12
1. Remove the spark plugs and check for gas or oil
fouling cracks, wear, improper gap, burned
electrodes, heavy deposits, or improper heat
range.
2. If spark plugs are fouled, the cause of fouling must
be determined before replacing the spark plugs.
Was a problem found?
- Verify repair Go to Step 13
13
Check for proper calibration of the speedometer.
Does the speed indicated on the speed meter closely
match the vehicle speed displayed on the Tech 2?
- Go to Step 15 Go to Step 14
14
Diagnose and repair the inaccurate speedometer
condition as necessary. Refer to Vehicle Speed
Sensor in Electrical Diagnosis.
- Verify repair -
15
Check for proper calibration of the fuel gauge.
Was a problem found?
- Verify repair Go to Step 16
16
Check for the following engine mechanical problems
(refer to Engine Mechanical):
Low compression.
Worn camshaft.
Sticking or leaking valves.
Valve timing.
Was a problem found?
- Verify repair Go to Step 17
17
1. Review all diagnostic procedures within this table.
2. If all procedures have been completed and no
malfunctions have been found, review/inspect the
following:
Visual/physical inspection.
Tech 2 data.
All electrical connections within a suspected circuit
and/or system.
Was a problem found?
- Verify repair Go to Step 18
18
Is the ECM programmed with the latest software
release?
If not, download the latest software to the ECM using
the "SPS (Service Programming System)".
Was the problem solved?
- Verify repair Go to Step 19
Page 2358 of 4264
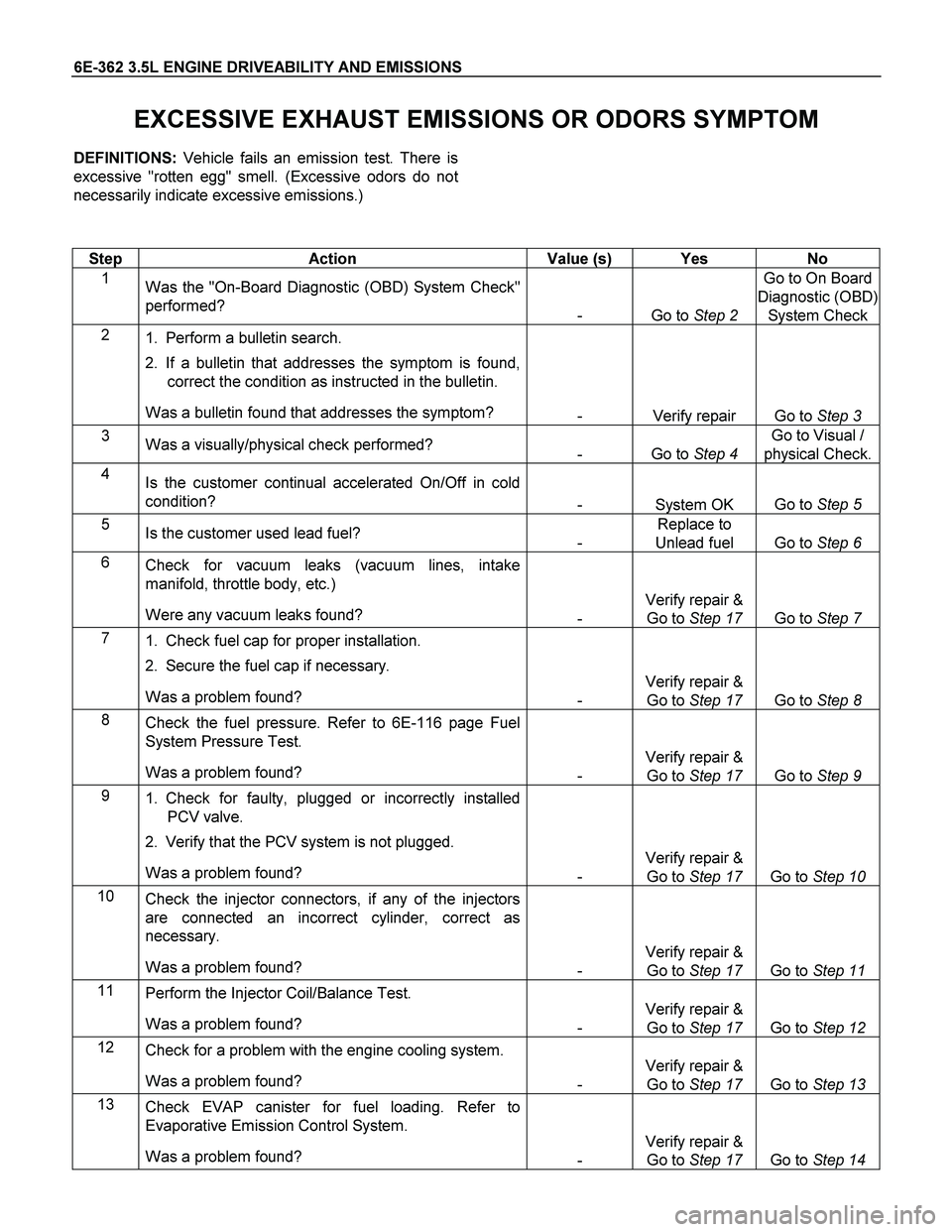
6E-362 3.5L ENGINE DRIVEABILITY AND EMISSIONS
EXCESSIVE EXHAUST EMISSIONS OR ODORS SYMPTOM
DEFINITIONS: Vehicle fails an emission test. There is
excessive "rotten egg" smell. (Excessive odors do no
t
necessarily indicate excessive emissions.)
Step Action Value (s) Yes No
1
Was the "On-Board Diagnostic (OBD) System Check"
performed?
- Go to Step 2 Go to On Board
Diagnostic (OBD)
System Check
2
1. Perform a bulletin search.
2. If a bulletin that addresses the symptom is found,
correct the condition as instructed in the bulletin.
Was a bulletin found that addresses the symptom?
- Verify repair Go to Step 3
3
Was a visually/physical check performed?
- Go to Step 4 Go to Visual /
physical Check.
4
Is the customer continual accelerated On/Off in cold
condition?
- System OK Go to Step 5
5
Is the customer used lead fuel?
- Replace to
Unlead fuel Go to Step 6
6
Check for vacuum leaks (vacuum lines, intake
manifold, throttle body, etc.)
Were any vacuum leaks found?
- Verify repair &
Go to Step 17 Go to Step 7
7
1. Check fuel cap for proper installation.
2. Secure the fuel cap if necessary.
Was a problem found?
- Verify repair &
Go to Step 17 Go to Step 8
8
Check the fuel pressure. Refer to 6E-116 page Fuel
System Pressure Test.
Was a problem found?
- Verify repair &
Go to Step 17 Go to Step 9
9
1. Check for faulty, plugged or incorrectly installed
PCV valve.
2. Verify that the PCV system is not plugged.
Was a problem found?
- Verify repair &
Go to Step 17 Go to Step 10
10
Check the injector connectors, if any of the injectors
are connected an incorrect cylinder, correct as
necessary.
Was a problem found?
- Verify repair &
Go to Step 17 Go to Step 11
11
Perform the Injector Coil/Balance Test.
Was a problem found?
- Verify repair &
Go to Step 17 Go to Step 12
12
Check for a problem with the engine cooling system.
Was a problem found?
- Verify repair &
Go to Step 17 Go to Step 13
13
Check EVAP canister for fuel loading. Refer to
Evaporative Emission Control System.
Was a problem found?
- Verify repair &
Go to Step 17 Go to Step 14
Page 2361 of 4264
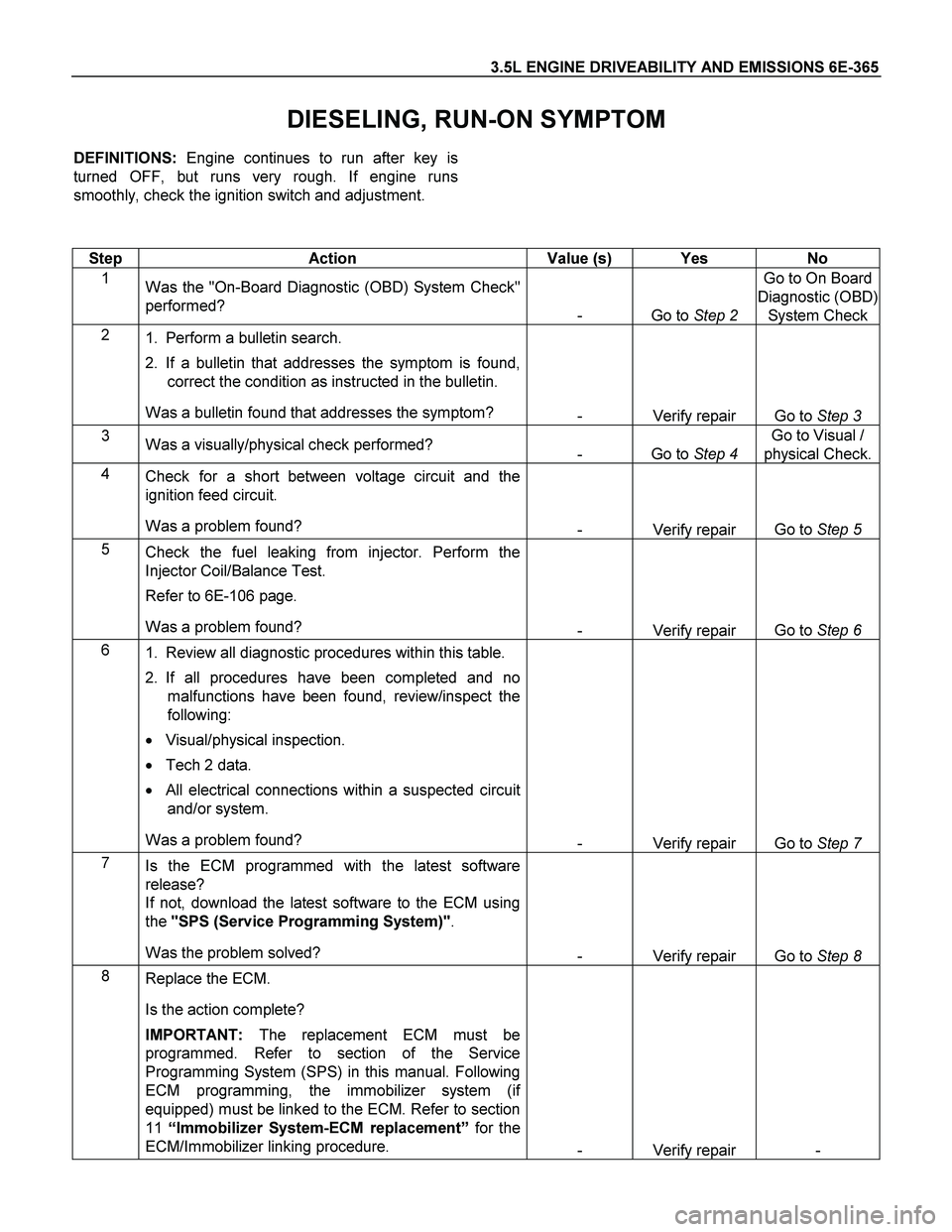
3.5L ENGINE DRIVEABILITY AND EMISSIONS 6E-365
DIESELING, RUN-ON SYMPTOM
DEFINITIONS: Engine continues to run after key is
turned OFF, but runs very rough. If engine runs
smoothly, check the ignition switch and adjustment.
Step Action Value (s) Yes No
1
Was the "On-Board Diagnostic (OBD) System Check"
performed?
- Go to Step 2 Go to On Board
Diagnostic (OBD)
System Check
2
1. Perform a bulletin search.
2. If a bulletin that addresses the symptom is found,
correct the condition as instructed in the bulletin.
Was a bulletin found that addresses the symptom?
- Verify repair Go to Step 3
3
Was a visually/physical check performed?
- Go to Step 4 Go to Visual /
physical Check.
4
Check for a short between voltage circuit and the
ignition feed circuit.
Was a problem found?
- Verify repair Go to Step 5
5
Check the fuel leaking from injector. Perform the
Injector Coil/Balance Test.
Refer to 6E-106 page.
Was a problem found?
- Verify repair Go to Step 6
6
1. Review all diagnostic procedures within this table.
2. If all procedures have been completed and no
malfunctions have been found, review/inspect the
following:
Visual/physical inspection.
Tech 2 data.
All electrical connections within a suspected circuit
and/or system.
Was a problem found?
- Verify repair Go to Step 7
7
Is the ECM programmed with the latest software
release?
If not, download the latest software to the ECM using
the "SPS (Service Programming System)".
Was the problem solved?
- Verify repair Go to Step 8
8
Replace the ECM.
Is the action complete?
IMPORTANT: The replacement ECM must be
programmed. Refer to section of the Service
Programming System (SPS) in this manual. Following
ECM programming, the immobilizer system (if
equipped) must be linked to the ECM. Refer to section
11 “Immobilizer System-ECM replacement” for the
ECM/Immobilizer linking procedure.
- Verify repair -
Page 2362 of 4264
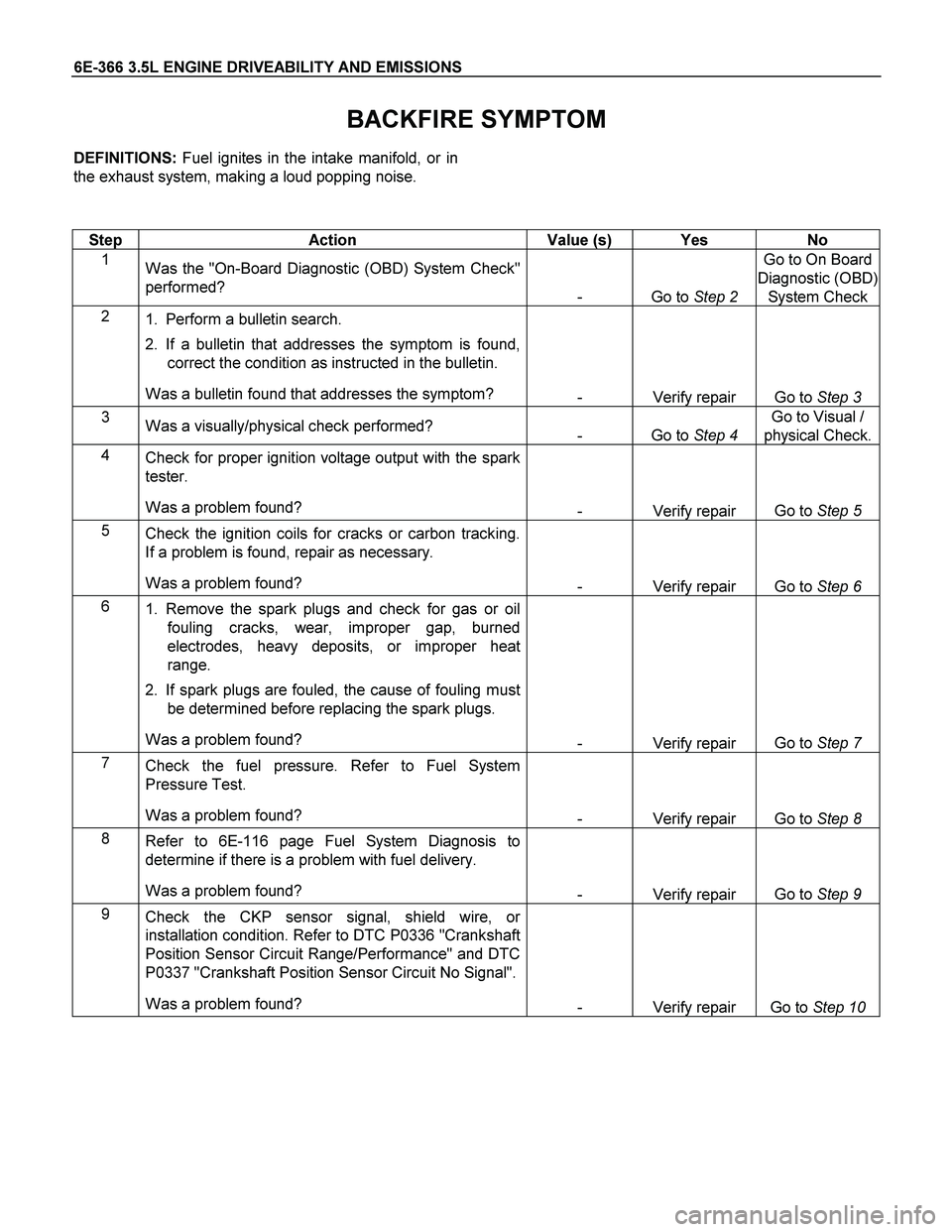
6E-366 3.5L ENGINE DRIVEABILITY AND EMISSIONS
BACKFIRE SYMPTOM
DEFINITIONS: Fuel ignites in the intake manifold, or in
the exhaust system, making a loud popping noise.
Step Action Value (s) Yes No
1
Was the "On-Board Diagnostic (OBD) System Check"
performed?
- Go to Step 2 Go to On Board
Diagnostic (OBD)
System Check
2
1. Perform a bulletin search.
2. If a bulletin that addresses the symptom is found,
correct the condition as instructed in the bulletin.
Was a bulletin found that addresses the symptom?
- Verify repair Go to Step 3
3
Was a visually/physical check performed?
- Go to Step 4 Go to Visual /
physical Check.
4
Check for proper ignition voltage output with the spark
tester.
Was a problem found?
- Verify repair Go to Step 5
5
Check the ignition coils for cracks or carbon tracking.
If a problem is found, repair as necessary.
Was a problem found?
- Verify repair Go to Step 6
6
1. Remove the spark plugs and check for gas or oil
fouling cracks, wear, improper gap, burned
electrodes, heavy deposits, or improper heat
range.
2. If spark plugs are fouled, the cause of fouling must
be determined before replacing the spark plugs.
Was a problem found?
- Verify repair Go to Step 7
7
Check the fuel pressure. Refer to Fuel System
Pressure Test.
Was a problem found?
- Verify repair Go to Step 8
8
Refer to 6E-116 page Fuel System Diagnosis to
determine if there is a problem with fuel delivery.
Was a problem found?
- Verify repair Go to Step 9
9
Check the CKP sensor signal, shield wire, or
installation condition. Refer to DTC P0336 "Crankshaft
Position Sensor Circuit Range/Performance" and DTC
P0337 "Crankshaft Position Sensor Circuit No Signal".
Was a problem found?
- Verify repair Go to Step 10
Page 2365 of 4264
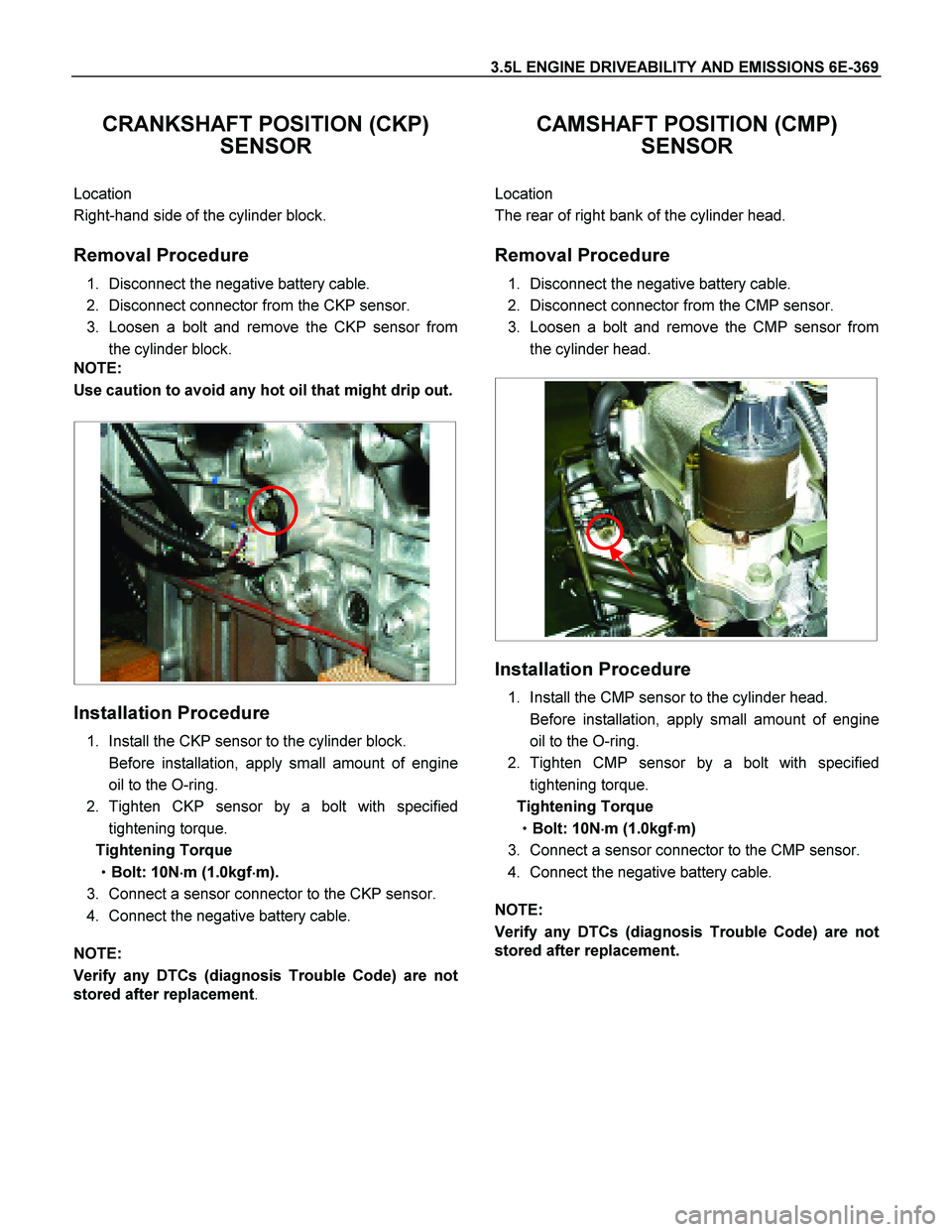
3.5L ENGINE DRIVEABILITY AND EMISSIONS 6E-369
CRANKSHAFT POSITION (CKP)
SENSOR
Location
Right-hand side of the cylinder block.
Removal Procedure
1. Disconnect the negative battery cable.
2. Disconnect connector from the CKP sensor.
3. Loosen a bolt and remove the CKP sensor from
the cylinder block.
NOTE:
Use caution to avoid any hot oil that might drip out.
Installation Procedure
1. Install the CKP sensor to the cylinder block.
Before installation, apply small amount of engine
oil to the O-ring.
2. Tighten CKP sensor by a bolt with specified
tightening torque.
Tightening Torque
Bolt: 10N
m (1.0kgf
m).
3. Connect a sensor connector to the CKP sensor.
4. Connect the negative battery cable.
NOTE:
Verify any DTCs (diagnosis Trouble Code) are not
stored after replacement.
CAMSHAFT POSITION (CMP)
SENSOR
Location
The rear of right bank of the cylinder head.
Removal Procedure
1. Disconnect the negative battery cable.
2. Disconnect connector from the CMP sensor.
3. Loosen a bolt and remove the CMP sensor from
the cylinder head.
Installation Procedure
1. Install the CMP sensor to the cylinder head.
Before installation, apply small amount of engine
oil to the O-ring.
2. Tighten CMP sensor by a bolt with specified
tightening torque.
Tightening Torque
Bolt: 10N
m (1.0kgf
m)
3. Connect a sensor connector to the CMP sensor.
4. Connect the negative battery cable.
NOTE:
Verify any DTCs (diagnosis Trouble Code) are not
stored after replacement.
Page 2371 of 4264
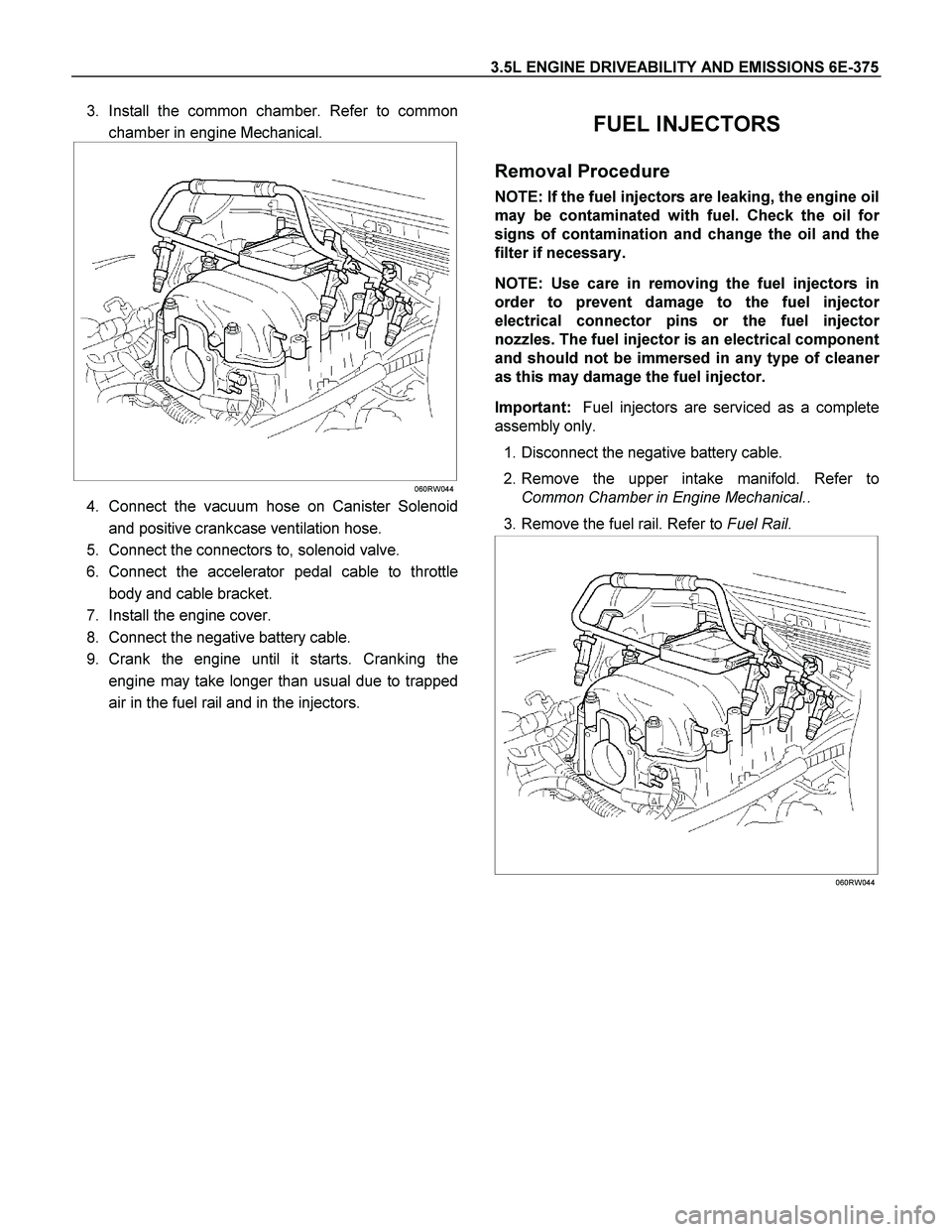
3.5L ENGINE DRIVEABILITY AND EMISSIONS 6E-375
3. Install the common chamber. Refer to common
chamber in engine Mechanical.
060RW044
4. Connect the vacuum hose on Canister Solenoid
and positive crankcase ventilation hose.
5. Connect the connectors to, solenoid valve.
6. Connect the accelerator pedal cable to throttle
body and cable bracket.
7. Install the engine cover.
8. Connect the negative battery cable.
9. Crank the engine until it starts. Cranking the
engine may take longer than usual due to trapped
air in the fuel rail and in the injectors.
FUEL INJECTORS
Removal Procedure
NOTE: If the fuel injectors are leaking, the engine oil
may be contaminated with fuel. Check the oil fo
r
signs of contamination and change the oil and the
filter if necessary.
NOTE: Use care in removing the fuel injectors in
order to prevent damage to the fuel injecto
r
electrical connector pins or the fuel injector
nozzles. The fuel injector is an electrical component
and should not be immersed in any type of cleane
r
as this may damage the fuel injector.
Important: Fuel injectors are serviced as a complete
assembly only.
1. Disconnect the negative battery cable.
2. Remove the upper intake manifold. Refer to
Common Chamber in Engine Mechanical..
3. Remove the fuel rail. Refer to Fuel Rail.
060RW044