service ISUZU TF SERIES 2004 Repair Manual
[x] Cancel search | Manufacturer: ISUZU, Model Year: 2004, Model line: TF SERIES, Model: ISUZU TF SERIES 2004Pages: 4264, PDF Size: 72.63 MB
Page 1176 of 4264
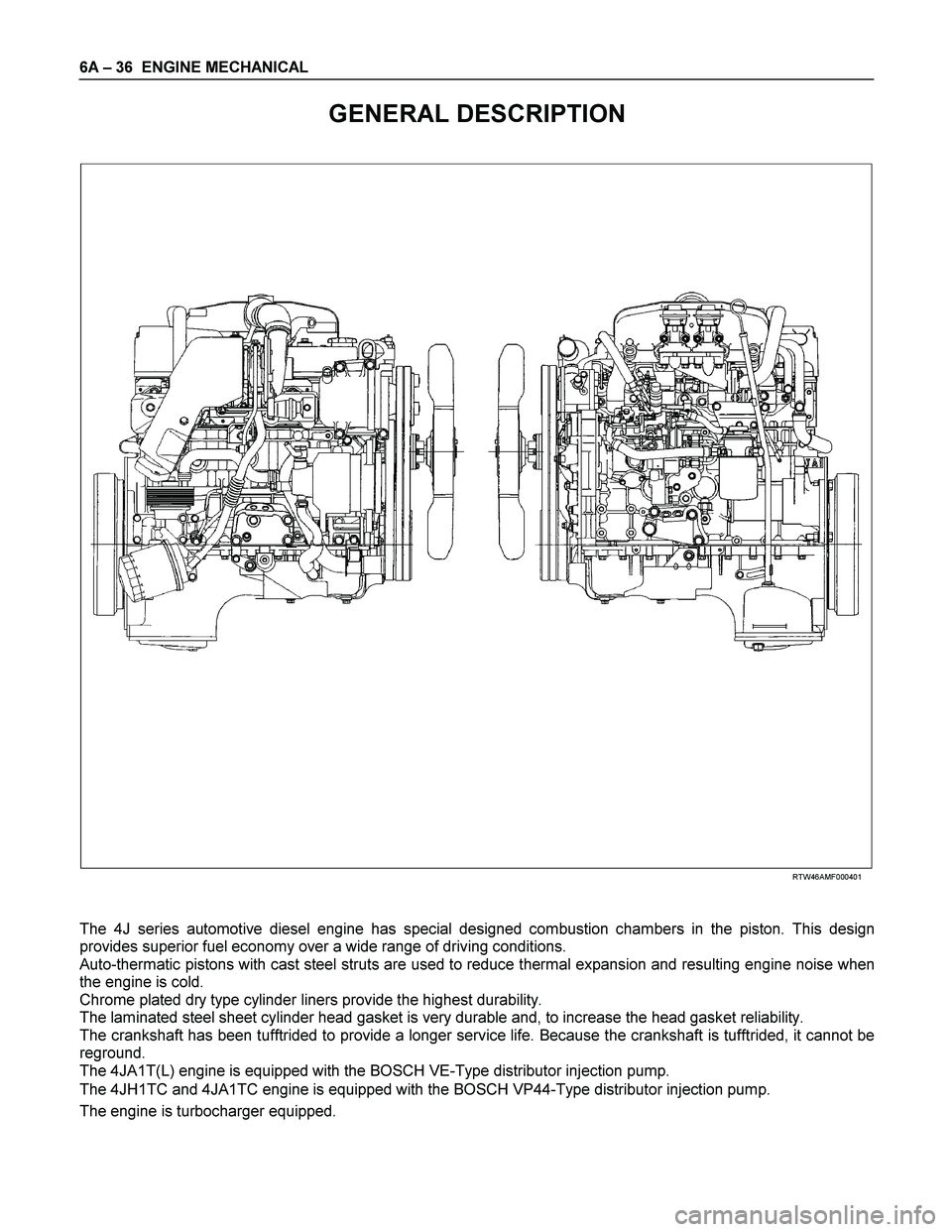
6A – 36 ENGINE MECHANICAL
GENERAL DESCRIPTION
RTW46AMF000401
The 4J series automotive diesel engine has special designed combustion chambers in the piston. This design
provides superior fuel economy over a wide range of driving conditions.
Auto-thermatic pistons with cast steel struts are used to reduce thermal expansion and resulting engine noise when
the engine is cold.
Chrome plated dry type cylinder liners provide the highest durability.
The laminated steel sheet cylinder head gasket is very durable and, to increase the head gasket reliability.
The crankshaft has been tufftrided to provide a longer service life. Because the crankshaft is tufftrided, it cannot be
reground.
The 4JA1T(L) engine is equipped with the BOSCH VE-Type distributor injection pump.
The 4JH1TC and 4JA1TC engine is equipped with the BOSCH VP44-Type distributor injection pump.
The engine is turbocharger equipped.
Page 1212 of 4264
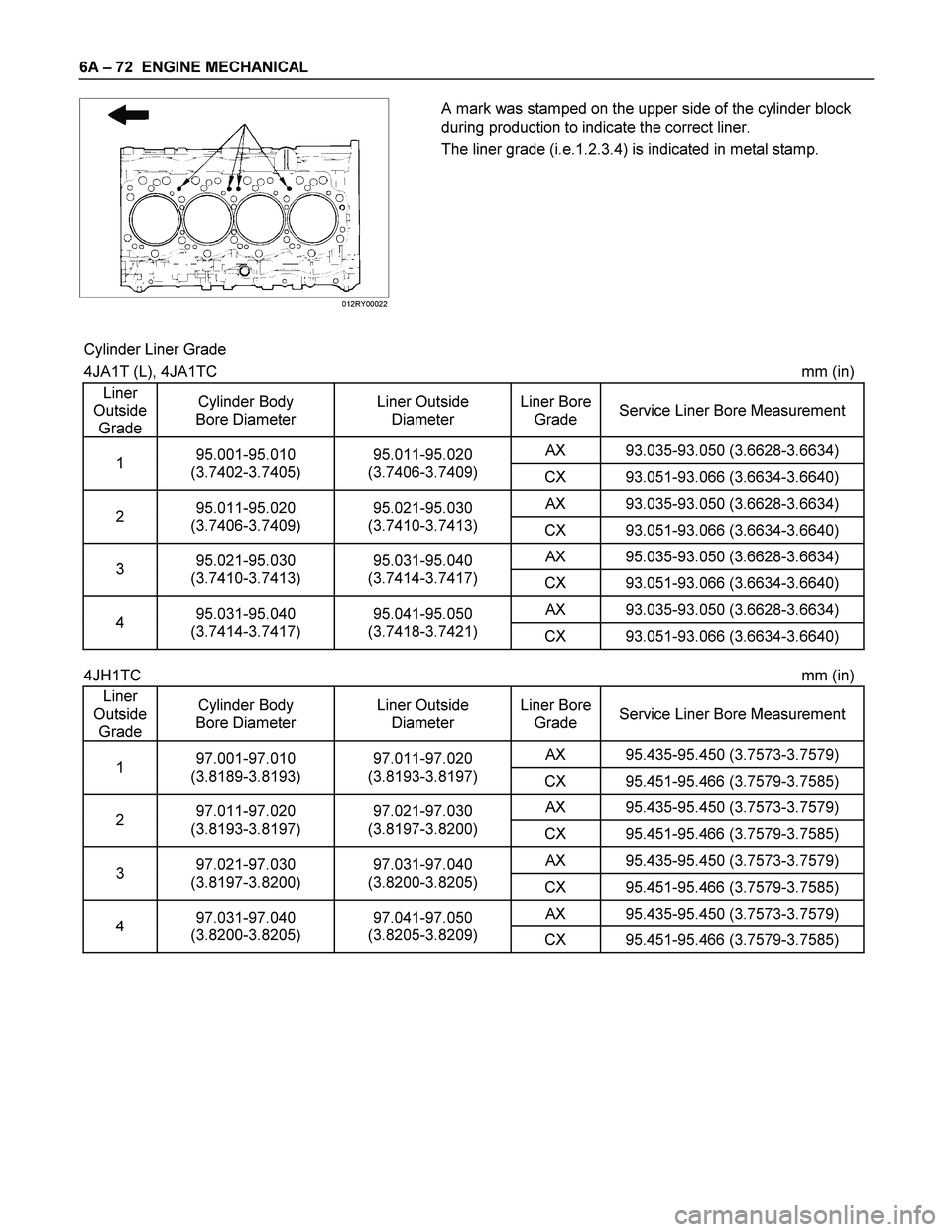
6A – 72 ENGINE MECHANICAL
012RY00022
A mark was stamped on the upper side of the cylinder block
during production to indicate the correct liner.
The liner grade (i.e.1.2.3.4) is indicated in metal stamp.
Cylinder Liner Grade
4JA1T (L), 4JA1TC mm (in)
Liner
Outside
Grade Cylinder Body
Bore Diameter Liner Outside
Diameter Liner Bore
Grade Service Liner Bore Measurement
AX 93.035-93.050 (3.6628-3.6634) 1 95.001-95.010
(3.7402-3.7405) 95.011-95.020
(3.7406-3.7409)
CX 93.051-93.066 (3.6634-3.6640)
AX 93.035-93.050 (3.6628-3.6634) 2 95.011-95.020
(3.7406-3.7409) 95.021-95.030
(3.7410-3.7413)
CX 93.051-93.066 (3.6634-3.6640)
AX 95.035-93.050 (3.6628-3.6634) 3 95.021-95.030
(3.7410-3.7413) 95.031-95.040
(3.7414-3.7417)
CX 93.051-93.066 (3.6634-3.6640)
AX 93.035-93.050 (3.6628-3.6634) 4 95.031-95.040
(3.7414-3.7417) 95.041-95.050
(3.7418-3.7421)
CX 93.051-93.066 (3.6634-3.6640)
4JH1TC mm (in)
Liner
Outside
Grade Cylinder Body
Bore Diameter Liner Outside
Diameter Liner Bore
Grade Service Liner Bore Measurement
AX 95.435-95.450 (3.7573-3.7579) 1 97.001-97.010
(3.8189-3.8193) 97.011-97.020
(3.8193-3.8197)
CX 95.451-95.466 (3.7579-3.7585)
AX 95.435-95.450 (3.7573-3.7579) 2 97.011-97.020
(3.8193-3.8197) 97.021-97.030
(3.8197-3.8200)
CX 95.451-95.466 (3.7579-3.7585)
AX 95.435-95.450 (3.7573-3.7579) 3 97.021-97.030
(3.8197-3.8200) 97.031-97.040
(3.8200-3.8205)
CX 95.451-95.466 (3.7579-3.7585)
AX 95.435-95.450 (3.7573-3.7579) 4 97.031-97.040
(3.8200-3.8205) 97.041-97.050
(3.8205-3.8209)
CX 95.451-95.466 (3.7579-3.7585)
Page 1214 of 4264
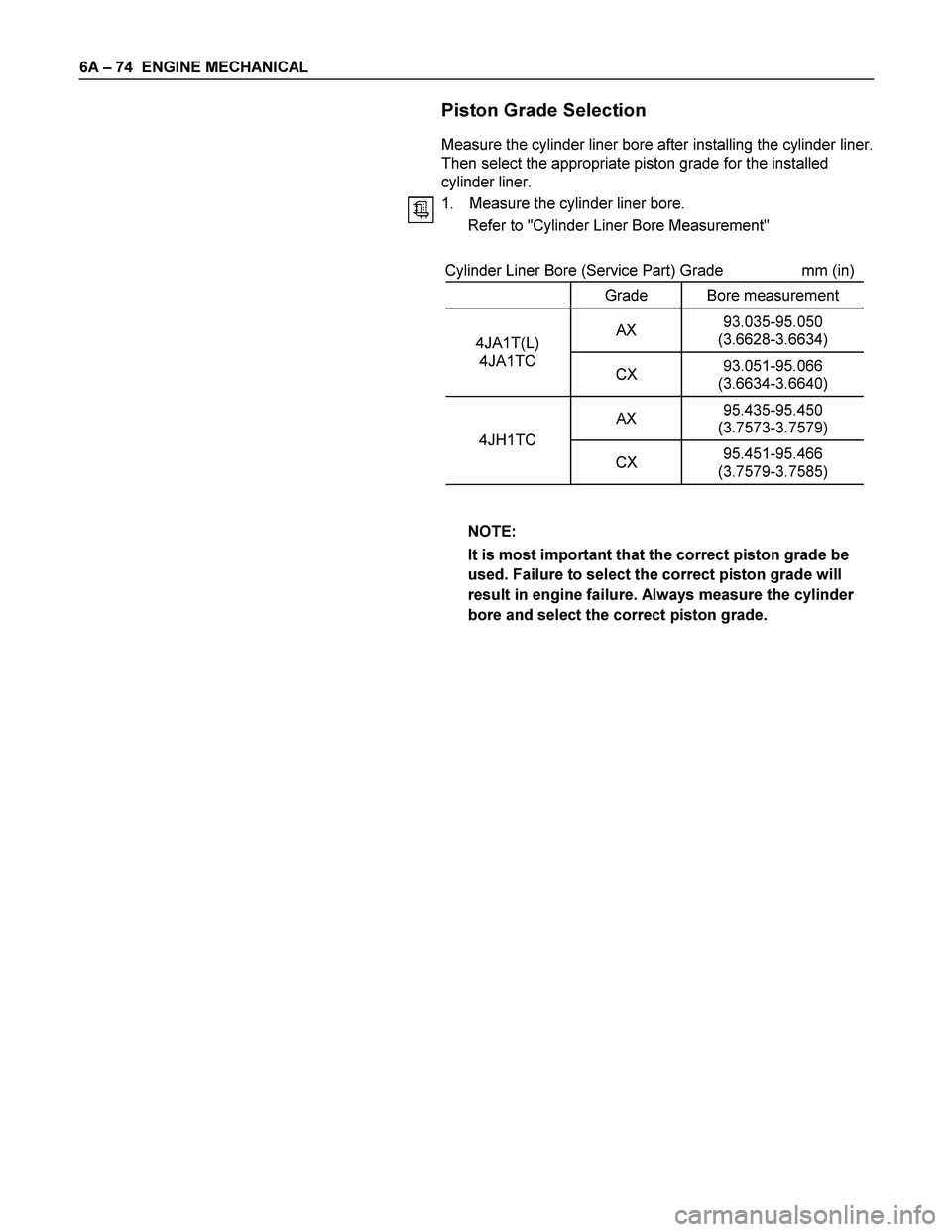
6A – 74 ENGINE MECHANICAL
Piston Grade Selection
Measure the cylinder liner bore after installing the cylinder liner.
Then select the appropriate piston grade for the installed
cylinder liner.
1. Measure the cylinder liner bore.
Refer to "Cylinder Liner Bore Measurement"
Cylinder Liner Bore (Service Part) Grade mm (in)
Grade Bore measurement
AX 93.035-95.050
(3.6628-3.6634) 4JA1T(L)
4JA1TC
CX 93.051-95.066
(3.6634-3.6640)
AX 95.435-95.450
(3.7573-3.7579)
4JH1TC
CX 95.451-95.466
(3.7579-3.7585)
NOTE:
It is most important that the correct piston grade be
used. Failure to select the correct piston grade will
result in engine failure. Always measure the cylinder
bore and select the correct piston grade.
Page 1215 of 4264
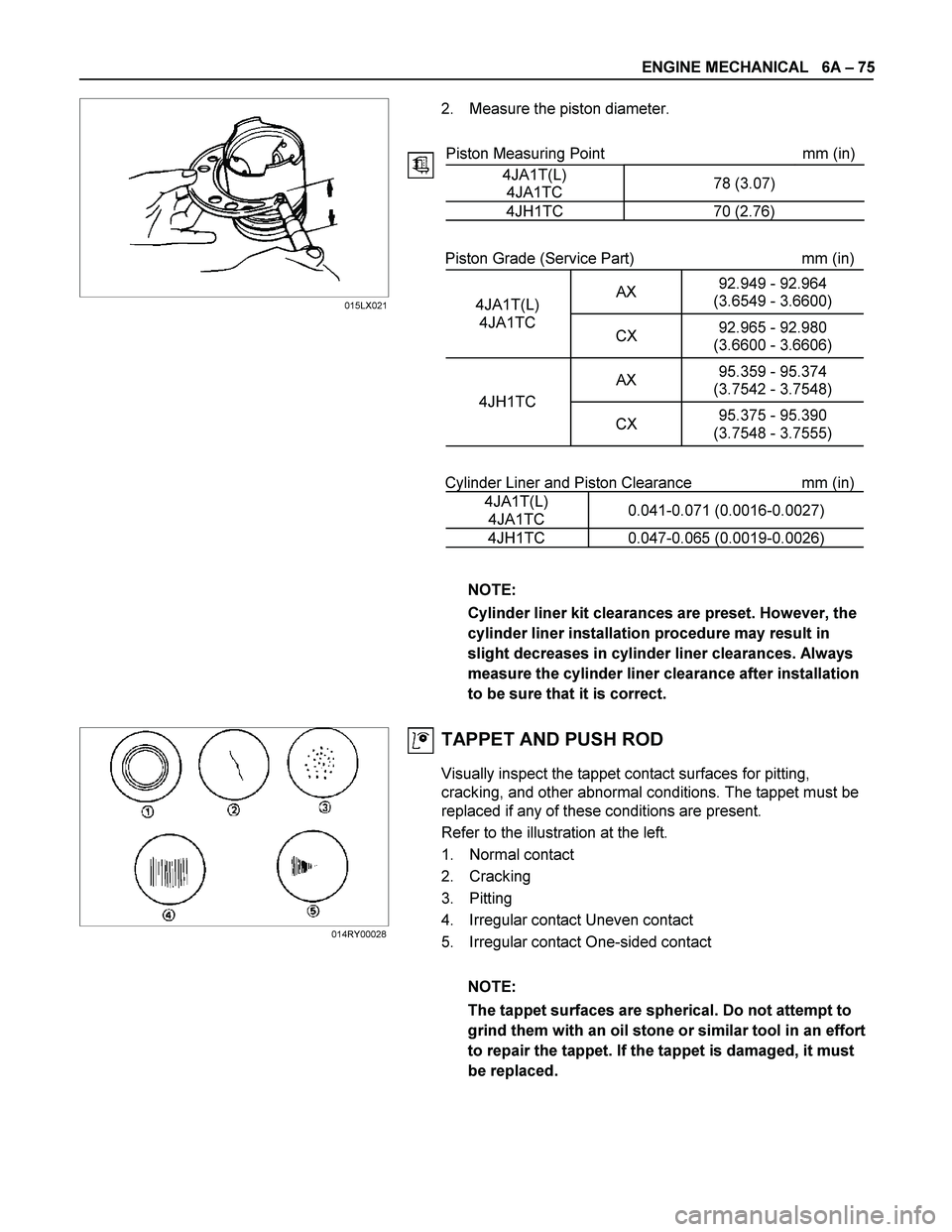
ENGINE MECHANICAL 6A – 75
2. Measure the piston diameter.
Piston Measuring Point mm (in)
4JA1T(L)
4JA1TC 78 (3.07)
4JH1TC 70 (2.76)
Piston Grade (Service Part) mm (in)
AX 92.949 - 92.964
(3.6549 - 3.6600)
4JA1T(L)
4JA1TC
CX 92.965 - 92.980
(3.6600 - 3.6606)
AX 95.359 - 95.374
(3.7542 - 3.7548)
4JH1TC
CX 95.375 - 95.390
(3.7548 - 3.7555)
Cylinder Liner and Piston Clearance mm (in)
4JA1T(L)
4JA1TC 0.041-0.071 (0.0016-0.0027)
4JH1TC 0.047-0.065 (0.0019-0.0026)
NOTE:
Cylinder liner kit clearances are preset. However, the
cylinder liner installation procedure may result in
slight decreases in cylinder liner clearances. Always
measure the cylinder liner clearance after installation
to be sure that it is correct.
TAPPET AND PUSH ROD
Visually inspect the tappet contact surfaces for pitting,
cracking, and other abnormal conditions. The tappet must be
replaced if any of these conditions are present.
Refer to the illustration at the left.
1. Normal contact
2. Cracking
3. Pitting
4. Irregular contact Uneven contact
5. Irregular contact One-sided contact
NOTE:
The tappet surfaces are spherical. Do not attempt to
grind them with an oil stone or similar tool in an effort
to repair the tappet. If the tappet is damaged, it must
be replaced.
015LX021
014RY00028
Page 1225 of 4264
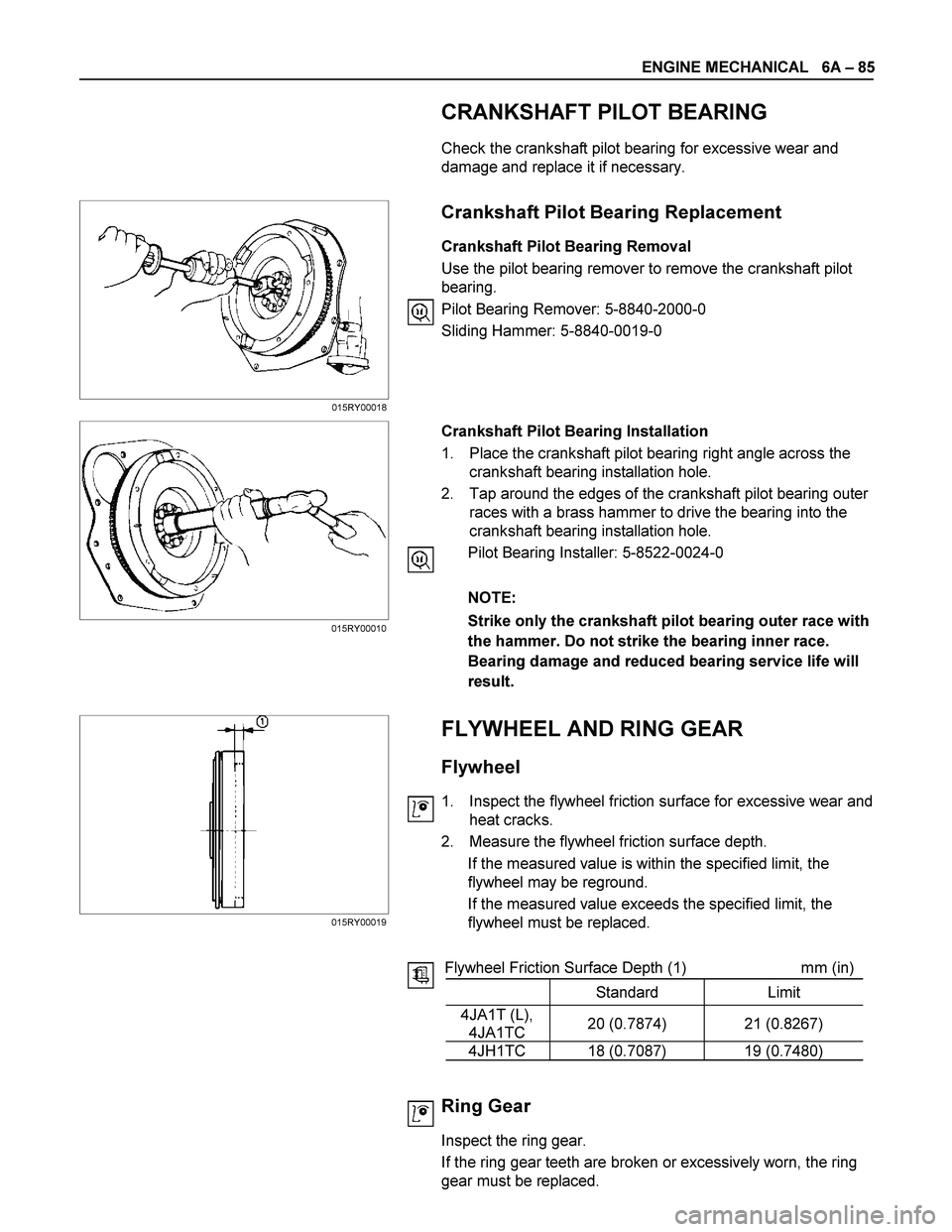
ENGINE MECHANICAL 6A – 85
CRANKSHAFT PILOT BEARING
Check the crankshaft pilot bearing for excessive wear and
damage and replace it if necessary.
Crankshaft Pilot Bearing Replacement
Crankshaft Pilot Bearing Removal
Use the pilot bearing remover to remove the crankshaft pilot
bearing.
Pilot Bearing Remover: 5-8840-2000-0
Sliding Hammer: 5-8840-0019-0
Crankshaft Pilot Bearing Installation
1. Place the crankshaft pilot bearing right angle across the
crankshaft bearing installation hole.
2. Tap around the edges of the crankshaft pilot bearing outer
races with a brass hammer to drive the bearing into the
crankshaft bearing installation hole.
Pilot Bearing Installer: 5-8522-0024-0
NOTE:
Strike only the crankshaft pilot bearing outer race with
the hammer. Do not strike the bearing inner race.
Bearing damage and reduced bearing service life will
result.
FLYWHEEL AND RING GEAR
Flywheel
1. Inspect the flywheel friction surface for excessive wear and
heat cracks.
2. Measure the flywheel friction surface depth.
If the measured value is within the specified limit, the
flywheel may be reground.
If the measured value exceeds the specified limit, the
flywheel must be replaced.
Flywheel Friction Surface Depth (1) mm (in)
Standard Limit
4JA1T (L),
4JA1TC 20 (0.7874) 21 (0.8267)
4JH1TC 18 (0.7087) 19 (0.7480)
Ring Gear
Inspect the ring gear.
If the ring gear teeth are broken or excessively worn, the ring
gear must be replaced.
015RY00010
015RY00019015RY00018
Page 1288 of 4264
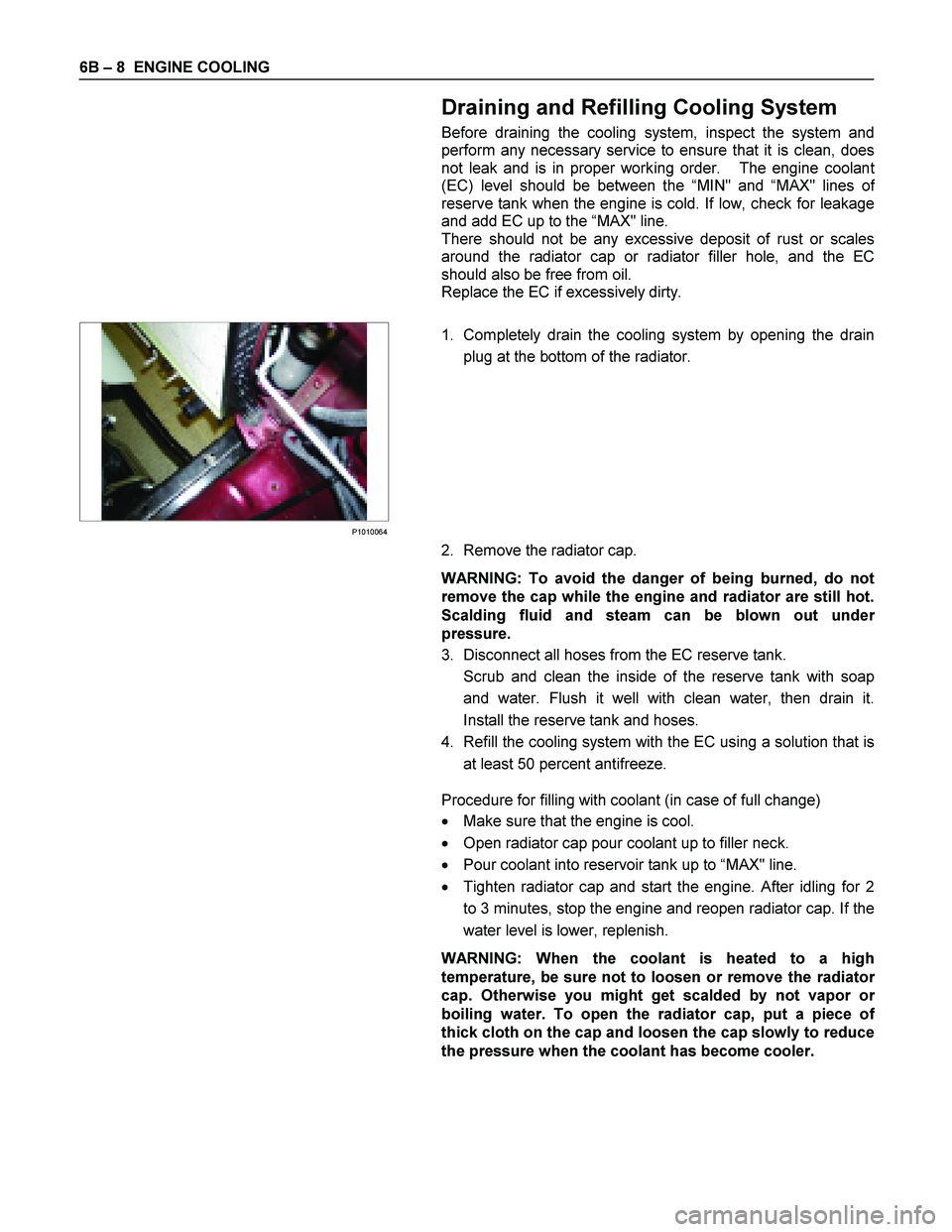
6B – 8 ENGINE COOLING
Draining and Refilling Cooling System
Before draining the cooling system, inspect the system and
perform any necessary service to ensure that it is clean, does
not leak and is in proper working order. The engine coolan
t
(EC) level should be between the “MIN" and “MAX" lines o
f
reserve tank when the engine is cold. If low, check for leakage
and add EC up to the “MAX" line.
There should not be any excessive deposit of rust or scales
around the radiator cap or radiator filler hole, and the EC
should also be free from oil.
Replace the EC if excessively dirty.
P1010064
1. Completely drain the cooling system by opening the drain
plug at the bottom of the radiator.
2. Remove the radiator cap.
WARNING: To avoid the danger of being burned, do not
remove the cap while the engine and radiator are still hot.
Scalding fluid and steam can be blown out unde
r
pressure.
3. Disconnect all hoses from the EC reserve tank.
Scrub and clean the inside of the reserve tank with soap and water. Flush it well with clean water, then drain it.
Install the reserve tank and hoses.
4. Refill the cooling system with the EC using a solution that is at least 50 percent antifreeze.
Procedure for filling with coolant (in case of full change)
Make sure that the engine is cool.
Open radiator cap pour coolant up to filler neck.
Pour coolant into reservoir tank up to “MAX" line.
Tighten radiator cap and start the engine. After idling for 2
to 3 minutes, stop the engine and reopen radiator cap. If the
water level is lower, replenish.
WARNING: When the coolant is heated to a high
temperature, be sure not to loosen or remove the radiato
r
cap. Otherwise you might get scalded by not vapor or
boiling water. To open the radiator cap, put a piece of
thick cloth on the cap and loosen the cap slowly to reduce
the pressure when the coolant has become cooler.
Page 1328 of 4264
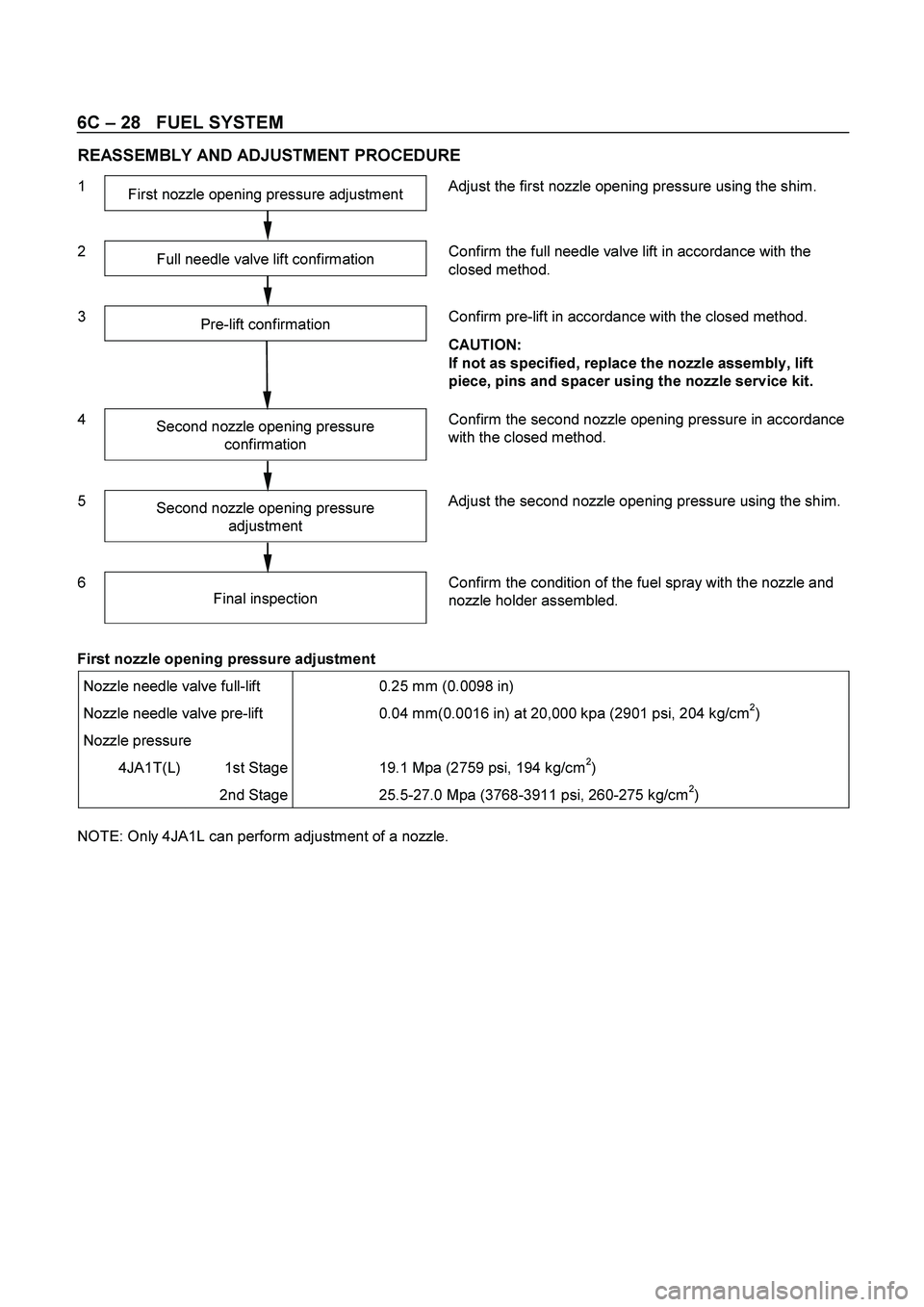
6C – 28 FUEL SYSTEM
REASSEMBLY AND ADJUSTMENT PROCEDURE
1
First nozzle opening pressure adjustment Adjust the first nozzle opening pressure using the shim.
2
Full needle valve lift confirmation Confirm the full needle valve lift in accordance with the
closed method.
3
Pre-lift confirmation
Confirm pre-lift in accordance with the closed method.
CAUTION:
If not as specified, replace the nozzle assembly, lift
piece, pins and spacer using the nozzle service kit.
4
Second nozzle opening pressure
confirmation Confirm the second nozzle opening pressure in accordance
with the closed method.
5
Second nozzle opening pressure
adjustment Adjust the second nozzle opening pressure using the shim.
6
Final inspection Confirm the condition of the fuel spray with the nozzle and
nozzle holder assembled.
First nozzle opening pressure adjustment
Nozzle needle valve full-lift 0.25 mm (0.0098 in)
Nozzle needle valve pre-lift 0.04 mm(0.0016 in) at 20,000 kpa (2901 psi, 204 kg/cm2)
Nozzle pressure
4JA1T(L) 1st Stage 19.1 Mpa (2759 psi, 194 kg/cm2)
2nd Stage 25.5-27.0 Mpa (3768-3911 psi, 260-275 kg/cm2)
NOTE: Only 4JA1L can perform adjustment of a nozzle.
Page 1334 of 4264
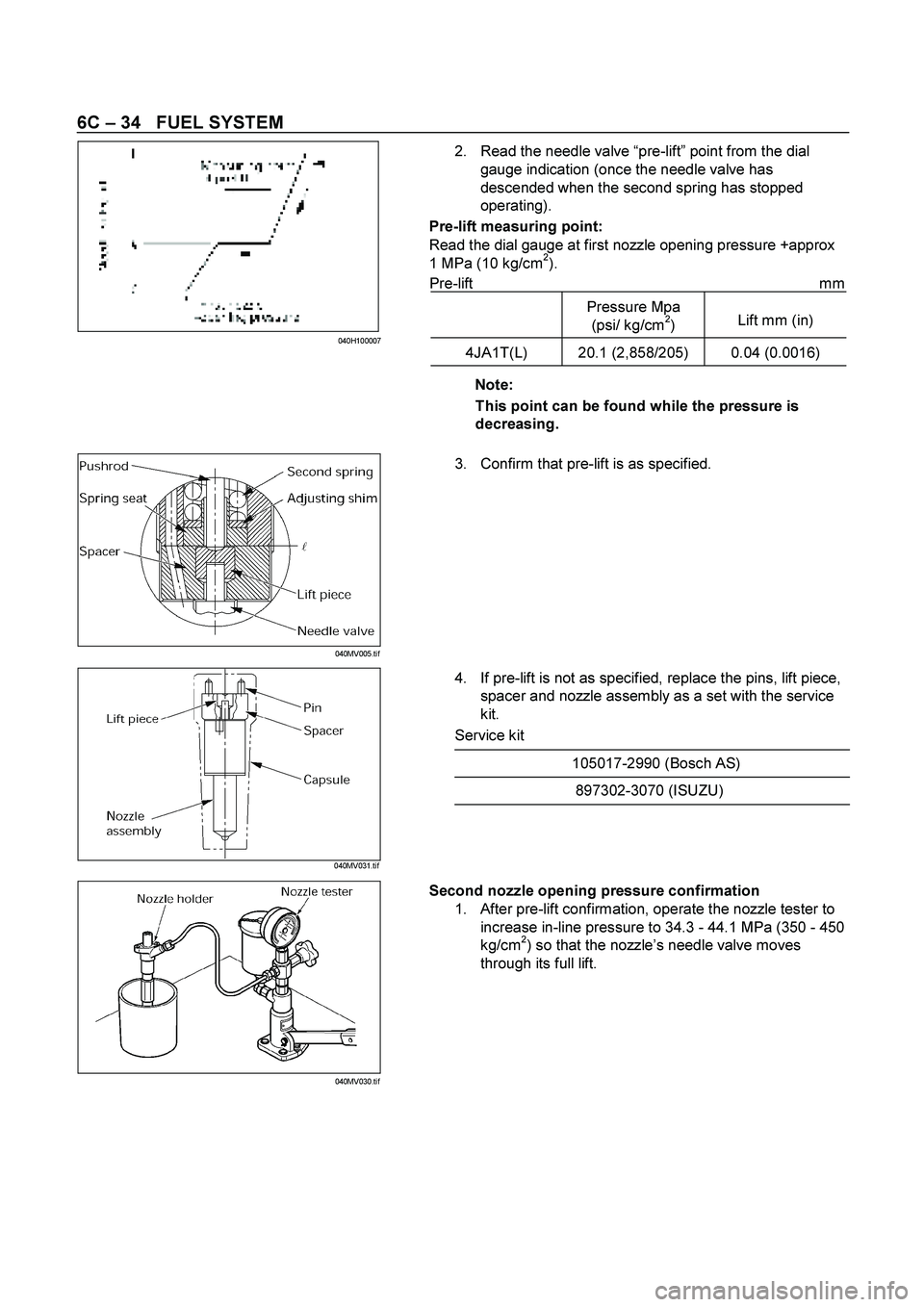
6C – 34 FUEL SYSTEM
2. Read the needle valve “pre-lift” point from the dial
gauge indication (once the needle valve has
descended when the second spring has stopped
operating).
Pre-lift measuring point:
Read the dial gauge at first nozzle opening pressure +approx
1 MPa (10 kg/cm
2).
Pre-lift mm
Pressure Mpa
(psi/ kg/cm
2) Lift mm (in)
4JA1T(L) 20.1 (2,858/205) 0.04 (0.0016)
Note:
This point can be found while the pressure is
decreasing.
3. Confirm that pre-lift is as specified.
4. If pre-lift is not as specified, replace the pins, lift piece,
spacer and nozzle assembly as a set with the service
kit.
Service kit
105017-2990 (Bosch AS)
897302-3070 (ISUZU)
Second nozzle opening pressure confirmation
1. After pre-lift confirmation, operate the nozzle tester to
increase in-line pressure to 34.3 - 44.1 MPa (350 - 450
kg/cm
2) so that the nozzle’s needle valve moves
through its full lift.
040MV005.tif
040MV031.ti f
040MV030.ti
f 040H100007
Page 1337 of 4264
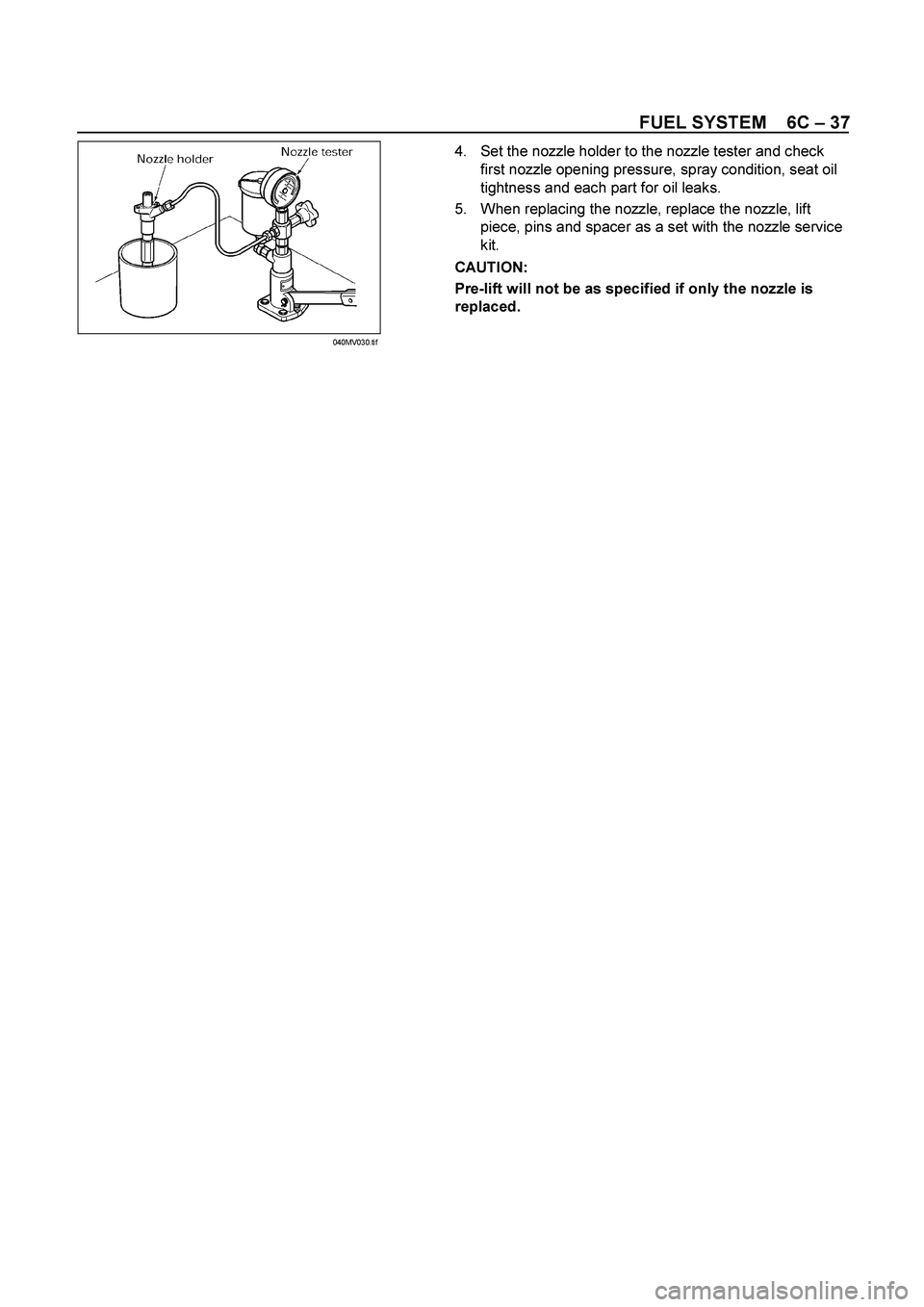
FUEL SYSTEM 6C – 37
4. Set the nozzle holder to the nozzle tester and check
first nozzle opening pressure, spray condition, seat oil
tightness and each part for oil leaks.
5. When replacing the nozzle, replace the nozzle, lift
piece, pins and spacer as a set with the nozzle service
kit.
CAUTION:
Pre-lift will not be as specified if only the nozzle is
replaced.
040MV030.tif
Page 1373 of 4264
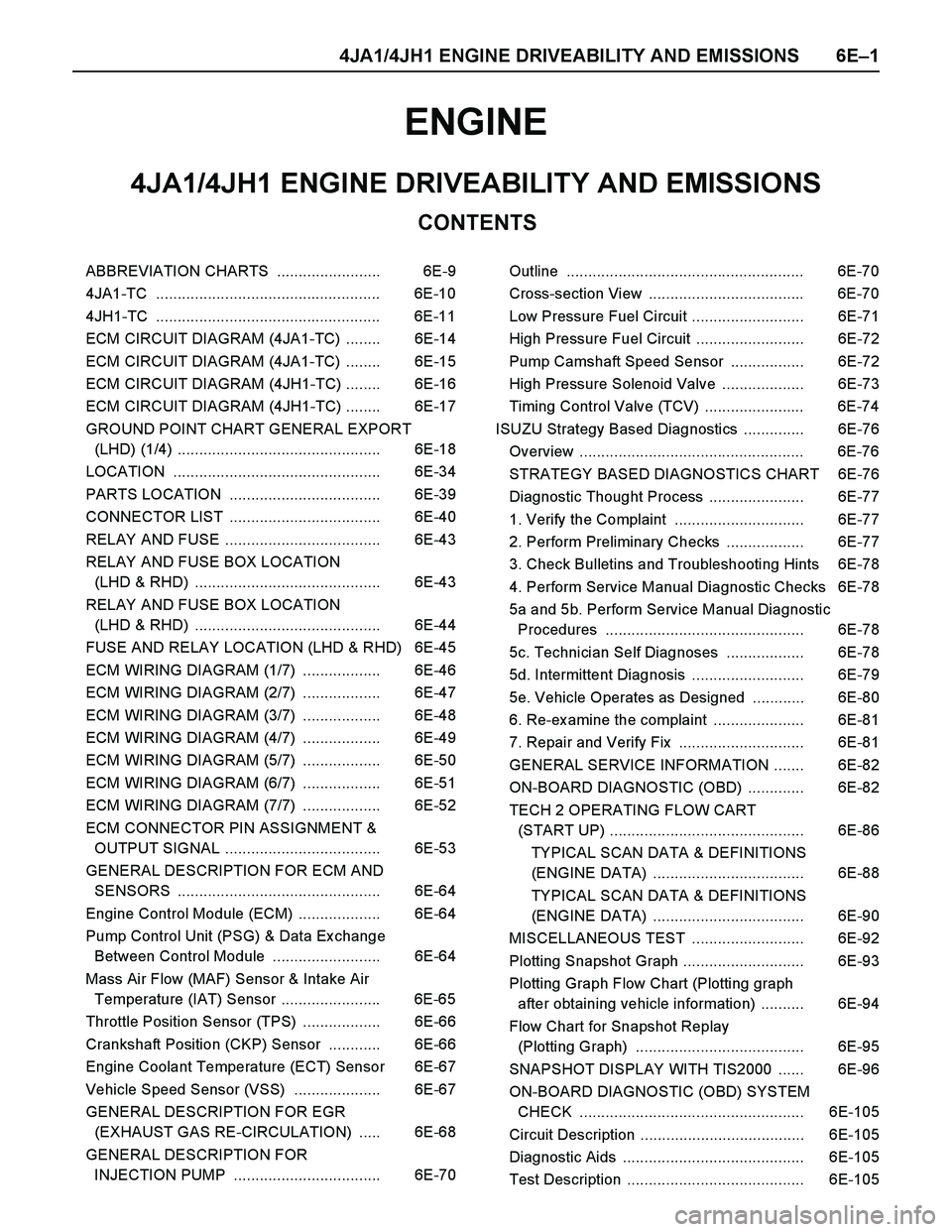
4JA1/4JH1 ENGINE DRIVEABILITY AND EMISSIONS 6E–1
ENGINE
CONTENTS
4JA1/4JH1 ENGINE DRIVEABILITY AND EMISSIONS
ABBREVIATION CHARTS ........................ 6E-9
4JA1-TC .................................................... 6E-10
4JH1-TC .................................................... 6E-11
ECM CIRCUIT DIAGRAM (4JA1-TC) ........ 6E-14
ECM CIRCUIT DIAGRAM (4JA1-TC) ........ 6E-15
ECM CIRCUIT DIAGRAM (4JH1-TC) ........ 6E-16
ECM CIRCUIT DIAGRAM (4JH1-TC) ........ 6E-17
GROUND POINT CHART GENERAL EXPORT
(LHD) (1/4) ............................................... 6E-18
LOCATION ................................................ 6E-34
PARTS LOCATION ................................... 6E-39
CONNECTOR LIST ................................... 6E-40
RELAY AND FUSE .................................... 6E-43
RELAY AND FUSE BOX LOCATION
(LHD & RHD) ........................................... 6E-43
RELAY AND FUSE BOX LOCATION
(LHD & RHD) ........................................... 6E-44
FUSE AND RELAY LOCATION (LHD & RHD) 6E-45
ECM WIRING DIAGRAM (1/7) .................. 6E-46
ECM WIRING DIAGRAM (2/7) .................. 6E-47
ECM WIRING DIAGRAM (3/7) .................. 6E-48
ECM WIRING DIAGRAM (4/7) .................. 6E-49
ECM WIRING DIAGRAM (5/7) .................. 6E-50
ECM WIRING DIAGRAM (6/7) .................. 6E-51
ECM WIRING DIAGRAM (7/7) .................. 6E-52
ECM CONNECTOR PIN ASSIGNMENT &
OUTPUT SIGNAL .................................... 6E-53
GENERAL DESCRIPTION FOR ECM AND
SENSORS ............................................... 6E-64
Engine Control Module (ECM) ................... 6E-64
Pump Control Unit (PSG) & Data Ex change
Between Control Module ......................... 6E-64
Mass Air Flow (MAF) Sensor & Intake Air
Temperature (IAT) Sensor ....................... 6E-65
Throttle Position Sensor (TPS) .................. 6E-66
Crankshaft Position (CKP) Sensor ............ 6E-66
Engine Coolant Temperature (ECT) Sensor 6E-67
Vehicle Speed Sensor (VSS) .................... 6E-67
GENERAL DESCRIPTION FOR EGR
(EXHAUST GAS RE-CIRCULATION) ..... 6E-68
GENERAL DESCRIPTION FOR
INJECTION PUMP .................................. 6E-70Outline ....................................................... 6E-70
Cross-section View .................................... 6E-70
Low Pressure Fuel Circuit .......................... 6E-71
High Pressure Fuel Circuit ......................... 6E-72
Pump Camshaft Speed Sensor ................. 6E-72
High Pressure Solenoid Valve ................... 6E-73
Timing Control Valve (TCV) ....................... 6E-74
ISUZU Strategy Based Diagnostics .............. 6E-76
Overview .................................................... 6E-76
STRATEGY BASED DIAGNOSTICS CHART 6E-76
Diagnostic Thought Process ...................... 6E-77
1. Verify the Complaint .............................. 6E-77
2. Perform Preliminary Checks .................. 6E-77
3. Check Bulletins and Troubleshooting Hints 6E-78
4. Perform Service Manual Diagnostic Checks 6E-78
5a and 5b. Perform Service Manual Diagnostic
Procedures .............................................. 6E-78
5c. Technician Self Diagnoses .................. 6E-78
5d. Intermittent Diagnosis .......................... 6E-79
5e. Vehicle Operates as Designed ............ 6E-80
6. Re-examine the complaint ..................... 6E-81
7. Repair and Verify Fix ............................. 6E-81
GENERAL SERVICE INFORMATION ....... 6E-82
ON-BOARD DIAGNOSTIC (OBD) ............. 6E-82
TECH 2 OPERATING FLOW CART
(START UP) ............................................. 6E-86
TYPICAL SCAN DATA & DEFINITIONS
(ENGINE DATA) ................................... 6E-88
TYPICAL SCAN DATA & DEFINITIONS
(ENGINE DATA) ................................... 6E-90
MISCELLANEOUS TEST .......................... 6E-92
Plotting Snapshot Graph ............................ 6E-93
Plotting Graph Flow Chart (Plotting graph
after obtaining vehicle information) .......... 6E-94
Flow Chart for Snapshot Replay
(Plotting Graph) ....................................... 6E-95
SNAPSHOT DISPLAY WITH TIS2000 ...... 6E-96
ON-BOARD DIAGNOSTIC (OBD) SYSTEM
CHECK .................................................... 6E-105
Circuit Description ...................................... 6E-105
Diagnostic Aids .......................................... 6E-105
Test Description ......................................... 6E-105