ISUZU TFS SERIES 1997 Service Manual
TFS SERIES 1997
ISUZU
ISUZU
https://www.carmanualsonline.info/img/61/57182/w960_57182-0.png
ISUZU TFS SERIES 1997 Service Manual
Page 566 of 1600
7C-26 CLUTCH
Rivet Head Depression
Use a depth gauge or a straight edge with steel rule to
measure the rivet head depression
1 from the facing surface
2.
Be sure to measure the rivet head depression on both sides of
the driven plate.
If the measured value is less than the specified limit, the facing
must be replaced.
Rivet Head Depression mm(in)
Standard
Fly wheel side P/Plate side
HEC 1.652.25
(0.065-0.089)
4JA1 1.351.95
(0.053-0.077)1.652.25
(0.065-0.089)0.2
(0.008)
4JB1T, 4JG2T 1.31.9
(0.051-0.075)
6VD1 1.6 (0.063)
Limit
Page 567 of 1600
CLUTCH 7C-27
CLUTCH CONTROL
REMOVAL AND INSTALLATION
Except 6VD1 Engine
Removal Steps
1. Pin
2. Jaw joint pin
3. Pedal assembly
4. Oil line
5. Master cylinder assembly
6. Oil line
7. Slave cylinder assembly
8. Damper cylinder assembly
Installation Steps
To install, follow the removal steps in the
reverse order.
Page 568 of 1600
7C-28 CLUTCH
6VD1 RHD Model
Removal Steps
1. Pin and jaw joint pin
2. Pedal assembly and switch
3. Oil line pipe
4. Slave cylinder assembly and heat
protector
5. Master cylinder assembly
6. Damper cylinder assembly
Installation Steps
To install, follow the removal steps in the
reverse order.
Page 569 of 1600
CLUTCH 7C-29
6VD1 LHD Model
Removal Steps
1. Pin and jaw joint pin
2. Pedal assembly and switch
3. Oil line pipe4. Slave cylinder assembly
5. Master cylinder assmebly
6. Oil line hose
Installation Steps
To install, follow the removal steps in the
reverse order.
Page 570 of 1600
7C-30 CLUTCH
MASTER CYLINDER (Except 6VD1 Engine)
DISASSEMBLY
Repair Kit
Disassembly Steps
1. Oil tank band
2. Oil tank assembly
3. Joint
4. Lock nut
5. Dust cover6. Stopper ring
7. Stopper
8. Push rod
9. Piston assembly
10. Cylinder body
Important : Take care not to disassemble the push rod stopper for master cylinder which calk to the master cylinder
body due to the component parts do not disassemble.
Page 571 of 1600
CLUTCH 7C-31
INSPECTION AND REPAIR
Make the necessary adjustments, repairs, and part replacements if excessive wear or damage is discovered during
inspection.
Cylinder Body
1. Clean the cylinder body.
2. Check the fluid return port for restrictions and clean it if
necessary.
Cylinder Bore and piston Clearance
1. Clean the cylinder body and the piston.
2. Use an inside dial indicator to measure the cylinder bore.
3. Use a micrometer to measure the piston diameter.
4. Calculate the clearance between the cylinder bore and the
piston diameter.
If the clearance exceeds the limit, the entire slave cylinder
assembly must be replaced.
Cylinder Bore and Piston Clearance mm(in)
Standard Limit
0.07 (0.0028) 0.15 (0.006)
Inner Parts
Replace the inner parts with new parts shown in the illustration.
Page 572 of 1600
7C-32 CLUTCH
REASSEMBLY
* Apply grease
(COSMO rubber grease)
Repair Kit
Reassembly Steps
1. Cylinder body
2. Piston and assembly
3. Push rod
4. Stopper
5. Stopper ring6. Dust cover
7. Lock nut
8. Joint
9. Oil tank assembly
10. Oil tank band
Important Operations
1. Cylinder Body
Immerse the cylinder body in clean brake fluid.
Page 573 of 1600
CLUTCH 7C-33
Master Cylinder (6VD1 LHD Model)
DISASSEMBLY AND REASSEMBLY
Disassembly Steps
1. Reservoir cap
2. Base cap
3. Seal
4. Clip
5. Reservoir
6. Gasket
7. Yoke
8. Nut
9. Rod stopper10. Push rod
11. Piston assembly
12. Plate
13. O-ring
14. Damper ring
15. Diaphragm
16. Seal ring
17. Cylinder body
Reassembly Steps
To reassemble, follow disassembly
steps in the reverse order.
Disassembly
1. Disassemble reservoir cap 1., base cap 2., seal
3., clip 4., and reservoir 5..
2. Disassembly gasket 6., yoke 7., and nut 8..
3. Disassemble rod stopper 9., push rod 10., and
piston assembly 11..4. Disassemble plate 12., o-ring 13., damper ring
14., diaphragm 15., and seal ring 16. from
cylinder body 17..
Page 574 of 1600
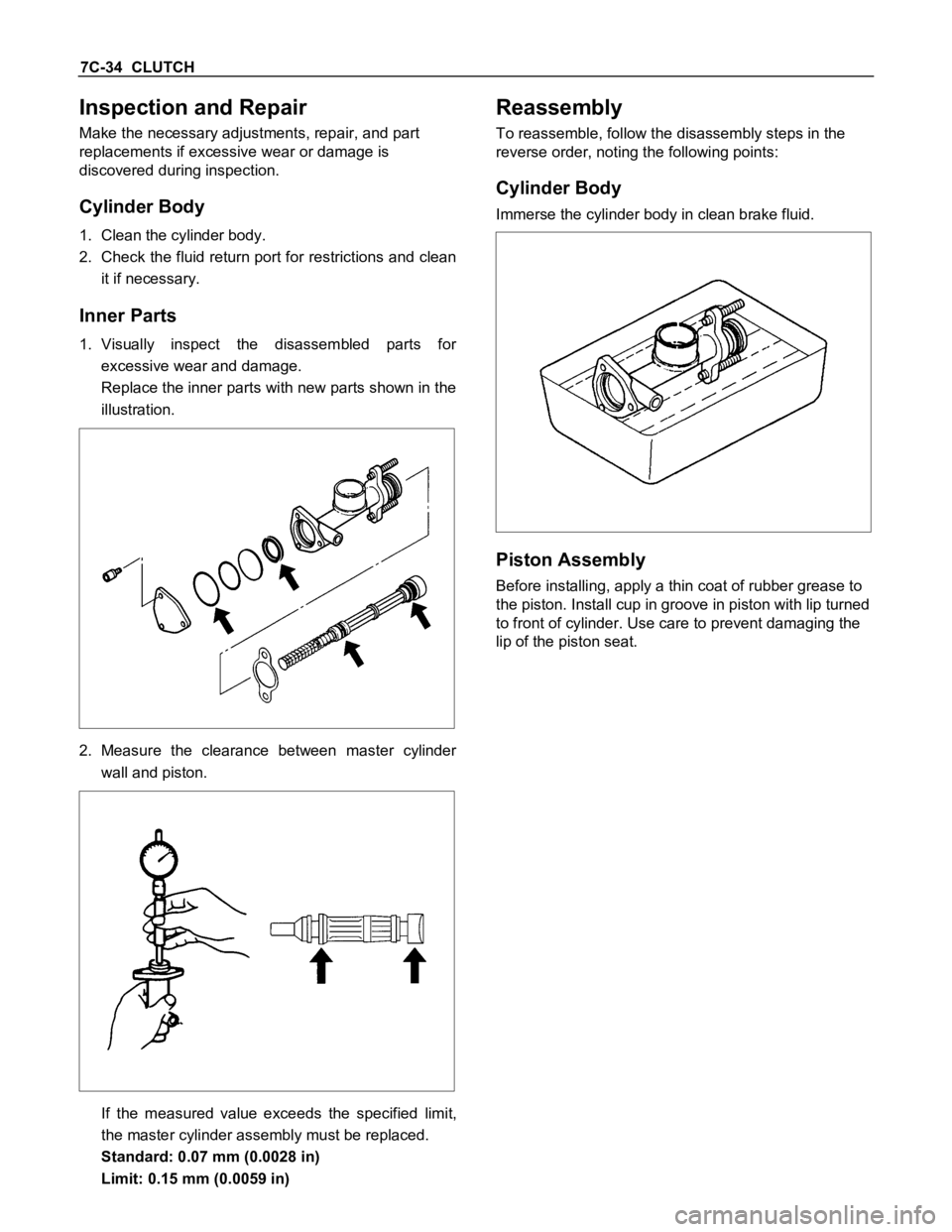
7C-34 CLUTCH
Inspection and Repair
Make the necessary adjustments, repair, and part
replacements if excessive wear or damage is
discovered during inspection.
Cylinder Body
1. Clean the cylinder body.
2. Check the fluid return port for restrictions and clean
it if necessary.
Inner Parts
1. Visually inspect the disassembled parts for
excessive wear and damage.
Replace the inner parts with new parts shown in the
illustration.
2. Measure the clearance between master cylinder
wall and piston.
If the measured value exceeds the specified limit,
the master cylinder assembly must be replaced.
Standard: 0.07 mm (0.0028 in)
Limit: 0.15 mm (0.0059 in)
Reassembly
To reassemble, follow the disassembly steps in the
reverse order, noting the following points:
Cylinder Body
Immerse the cylinder body in clean brake fluid.
Piston Assembly
Before installing, apply a thin coat of rubber grease to
the piston. Install cup in groove in piston with lip turned
to front of cylinder. Use care to prevent damaging the
lip of the piston seat.
Page 575 of 1600
CLUTCH 7C-35
SLAVE CYLINDER (Except 6VD1 Engine)
DISASSEMBLY
Disassembly Steps
1. Boot
2. Push rod
3. Piston and piston cup4. Spring
5. Cylinder body
6. Solenoid switch
Important Operations
1. Boot
Brake fluid spilled on painted or plastic surfaces will cause
serious damage.
Take care not to spill brake fluid.