JAGUAR S TYPE 1999 1.G Powertrain Manual
Manufacturer: JAGUAR, Model Year: 1999, Model line: S TYPE, Model: JAGUAR S TYPE 1999 1.GPages: 75, PDF Size: 3.4 MB
Page 31 of 75
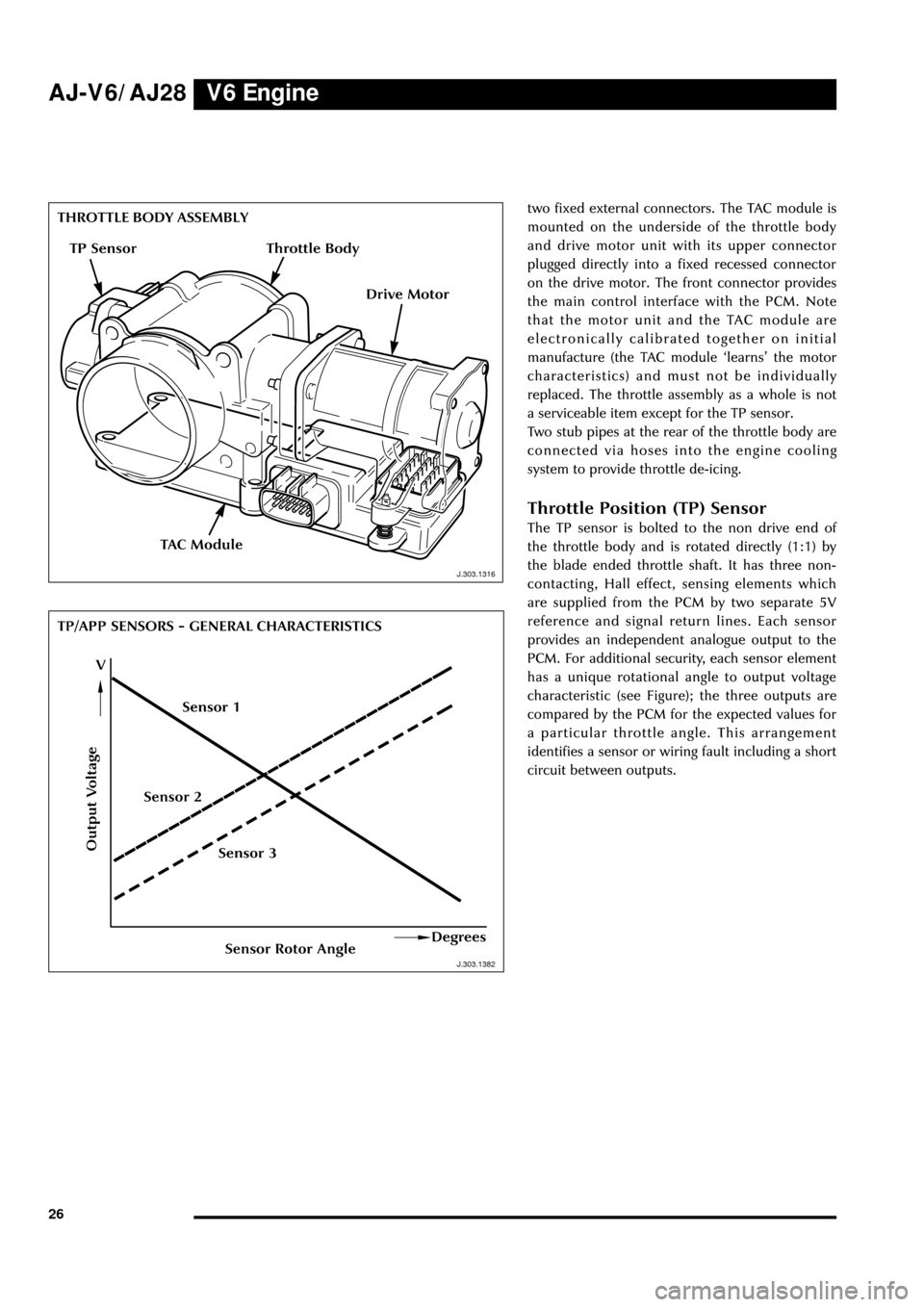
V6 Engine AJ-V6/AJ28
26
J.303.1316
J.303.1362
THROTTLE BODY ASSEMBLY
TP/APP SENSORS - GENERAL CHARACTERISTICStwo fixed external connectors. The TAC module is
mounted on the underside of the throttle body
and drive motor unit with its upper connector
plugged directly into a fixed recessed connector
on the drive motor. The front connector provides
the main control interface with the PCM. Note
that the motor unit and the TAC module are
electronically calibrated together on initial
manufacture (the TAC module ÔlearnsÕ the motor
characteristics) and must not be individually
replaced. The throttle assembly as a whole is not
a serviceable item except for the TP sensor.
Two stub pipes at the rear of the throttle body are
connected via hoses into the engine cooling
system to provide throttle de-icing.
Throttle Position (TP) Sensor
The TP sensor is bolted to the non drive end of
the throttle body and is rotated directly (1:1) by
the blade ended throttle shaft. It has three non-
contacting, Hall effect, sensing elements which
are supplied from the PCM by two separate 5V
reference and signal return lines. Each sensor
provides an independent analogue output to the
PCM. For additional security, each sensor element
has a unique rotational angle to output voltage
characteristic (see Figure); the three outputs are
compared by the PCM for the expected values for
a particular throttle angle. This arrangement
identifies a sensor or wiring fault including a short
circuit between outputs.
Output Voltage
Sensor Rotor AngleDegrees
V
TAC Module
J.303.1382 J.303.1316
TP Sensor
Drive Motor
Sensor 3 Sensor 2Sensor 1
Throttle Body
Page 32 of 75
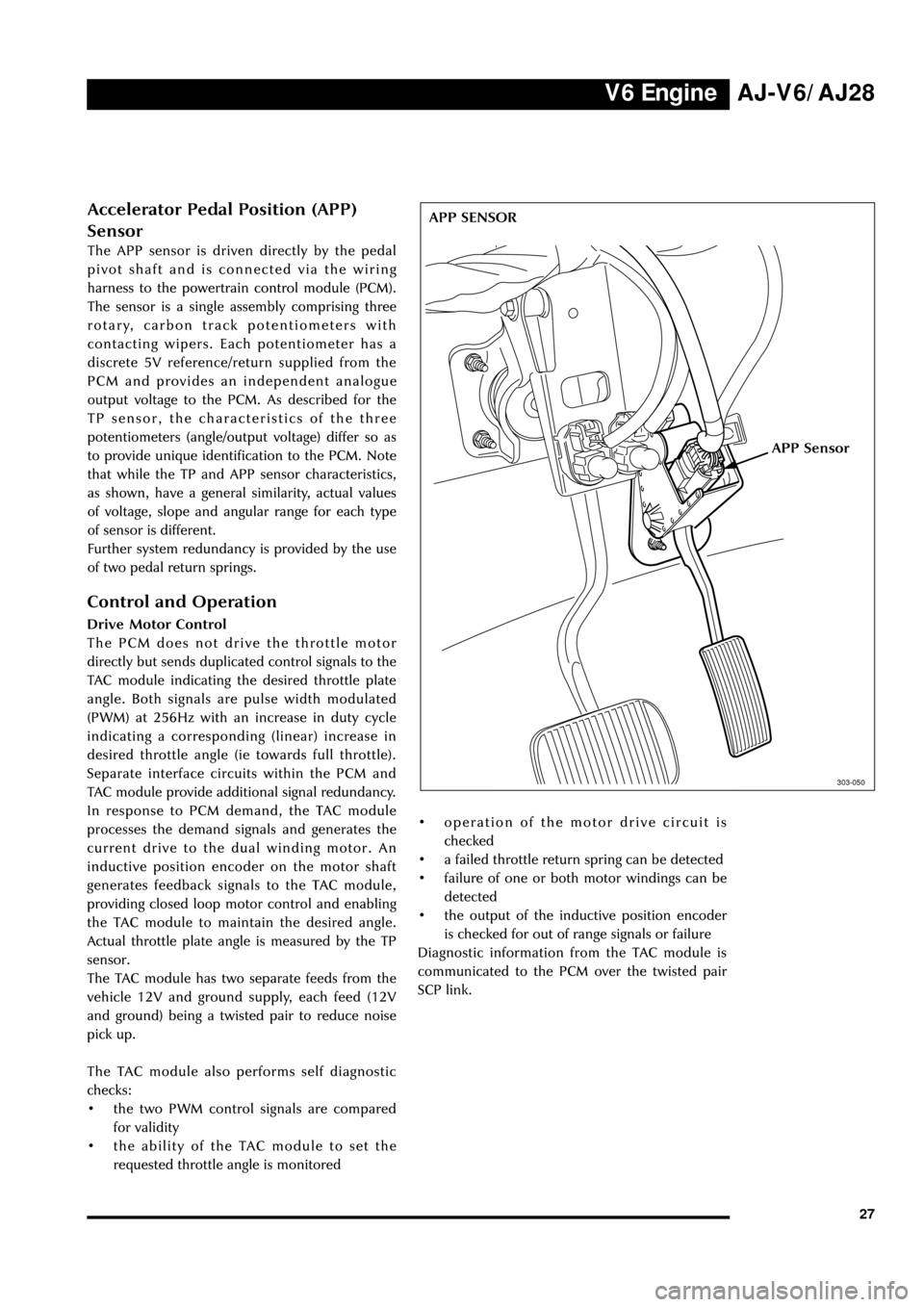
V6 EngineAJ-V6/AJ28
27
D.418.428
APP Sensor
303-050
APP SENSORAccelerator Pedal Position (APP)
Sensor
The APP sensor is driven directly by the pedal
pivot shaft and is connected via the wiring
harness to the powertrain control module (PCM).
The sensor is a single assembly comprising three
rotary, carbon track potentiometers with
contacting wipers. Each potentiometer has a
discrete 5V reference/return supplied from the
PCM and provides an independent analogue
output voltage to the PCM. As described for the
TP sensor, the characteristics of the three
potentiometers (angle/output voltage) differ so as
to provide unique identification to the PCM. Note
that while the TP and APP sensor characteristics,
as shown, have a general similarity, actual values
of voltage, slope and angular range for each type
of sensor is different.
Further system redundancy is provided by the use
of two pedal return springs.
Control and Operation
Drive Motor Control
The PCM does not drive the throttle motor
directly but sends duplicated control signals to the
TAC module indicating the desired throttle plate
angle. Both signals are pulse width modulated
(PWM) at 256Hz with an increase in duty cycle
indicating a corresponding (linear) increase in
desired throttle angle (ie towards full throttle).
Separate interface circuits within the PCM and
TAC module provide additional signal redundancy.
In response to PCM demand, the TAC module
processes the demand signals and generates the
current drive to the dual winding motor. An
inductive position encoder on the motor shaft
generates feedback signals to the TAC module,
providing closed loop motor control and enabling
the TAC module to maintain the desired angle.
Actual throttle plate angle is measured by the TP
sensor.
The TAC module has two separate feeds from the
vehicle 12V and ground supply, each feed (12V
and ground) being a twisted pair to reduce noise
pick up.
The TAC module also performs self diagnostic
checks:
¥ the two PWM control signals are compared
for validity
¥ the ability of the TAC module to set the
requested throttle angle is monitored¥ operation of the motor drive circuit is
checked
¥ a failed throttle return spring can be detected
¥ failure of one or both motor windings can be
detected
¥ the output of the inductive position encoder
is checked for out of range signals or failure
Diagnostic information from the TAC module is
communicated to the PCM over the twisted pair
SCP link.
Page 33 of 75
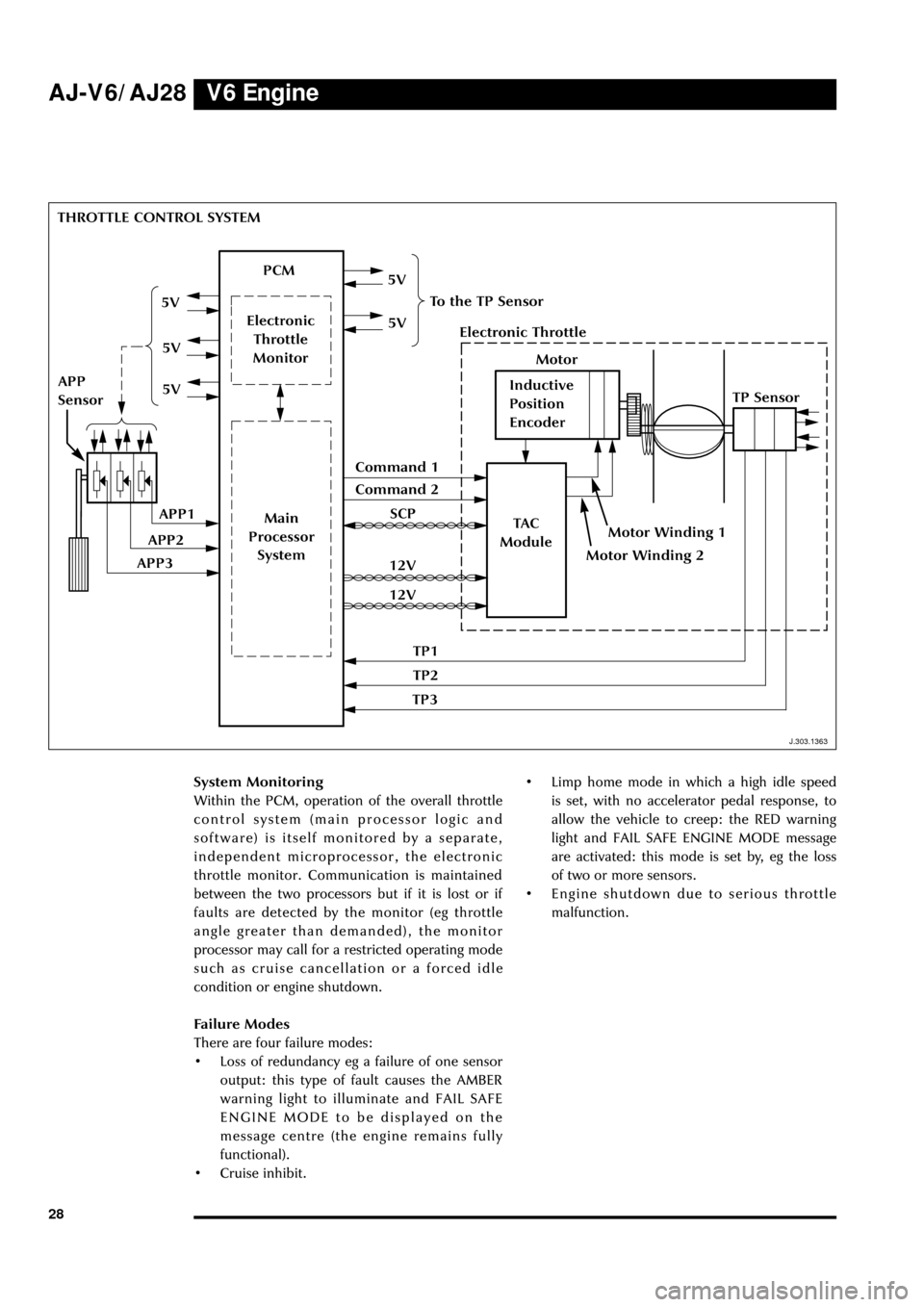
V6 Engine AJ-V6/AJ28
28¥ Limp home mode in which a high idle speed
is set, with no accelerator pedal response, to
allow the vehicle to creep: the RED warning
light and FAIL SAFE ENGINE MODE message
are activated: this mode is set by, eg the loss
of two or more sensors.
¥ Engine shutdown due to serious throttle
malfunction.
J.303.1363
THROTTLE CONTROL SYSTEM
System Monitoring
Within the PCM, operation of the overall throttle
control system (main processor logic and
software) is itself monitored by a separate,
independent microprocessor, the electronic
throttle monitor. Communication is maintained
between the two processors but if it is lost or if
faults are detected by the monitor (eg throttle
angle greater than demanded), the monitor
processor may call for a restricted operating mode
such as cruise cancellation or a forced idle
condition or engine shutdown.
Failure Modes
There are four failure modes:
¥ Loss of redundancy eg a failure of one sensor
output: this type of fault causes the AMBER
warning light to illuminate and FAIL SAFE
ENGINE MODE to be displayed on the
message centre (the engine remains fully
functional).
¥ Cruise inhibit.
J.303.1363
PCM
Electronic
Throttle
Monitor
Main
Processor
SystemTAC
Module
Motor
Electronic Throttle
TP Sensor
Command 1
Command 2
SCP
APP
Sensor
Motor Winding 1
Motor Winding 2
To the TP Sensor
APP1
APP2
APP3
5V
5V
5V
5V
5V
12V
12V
TP1
TP2
TP3
Inductive
Position
Encoder
Page 34 of 75
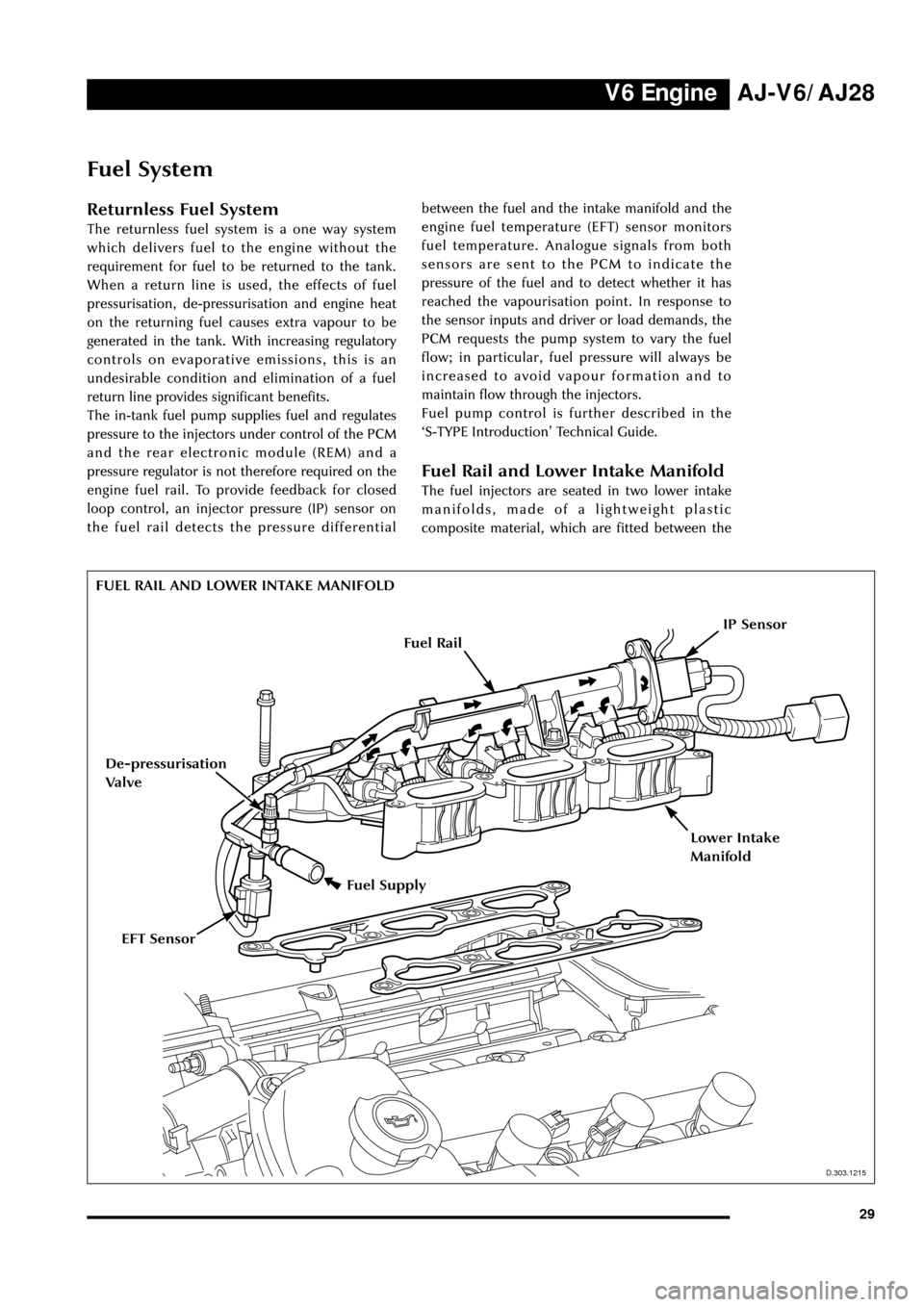
V6 EngineAJ-V6/AJ28
29
D.303.1215
FUEL RAIL AND LOWER INTAKE MANIFOLD
Fuel Supply
D.303.1215
EFT Sensor
De-pressurisation
Valve
IP Sensor
Fuel System
Returnless Fuel System
The returnless fuel system is a one way system
which delivers fuel to the engine without the
requirement for fuel to be returned to the tank.
When a return line is used, the effects of fuel
pressurisation, de-pressurisation and engine heat
on the returning fuel causes extra vapour to be
generated in the tank. With increasing regulatory
controls on evaporative emissions, this is an
undesirable condition and elimination of a fuel
return line provides significant benefits.
The in-tank fuel pump supplies fuel and regulates
pressure to the injectors under control of the PCM
and the rear electronic module (REM) and a
pressure regulator is not therefore required on the
engine fuel rail. To provide feedback for closed
loop control, an injector pressure (IP) sensor on
the fuel rail detects the pressure differentialbetween the fuel and the intake manifold and the
engine fuel temperature (EFT) sensor monitors
fuel temperature. Analogue signals from both
sensors are sent to the PCM to indicate the
pressure of the fuel and to detect whether it has
reached the vapourisation point. In response to
the sensor inputs and driver or load demands, the
PCM requests the pump system to vary the fuel
flow; in particular, fuel pressure will always be
increased to avoid vapour formation and to
maintain flow through the injectors.
Fuel pump control is further described in the
ÔS-TYPE IntroductionÕ Technical Guide.
Fuel Rail and Lower Intake Manifold
The fuel injectors are seated in two lower intake
manifolds, made of a lightweight plastic
composite material, which are fitted between the
Fuel Rail
Lower Intake
Manifold
Page 35 of 75
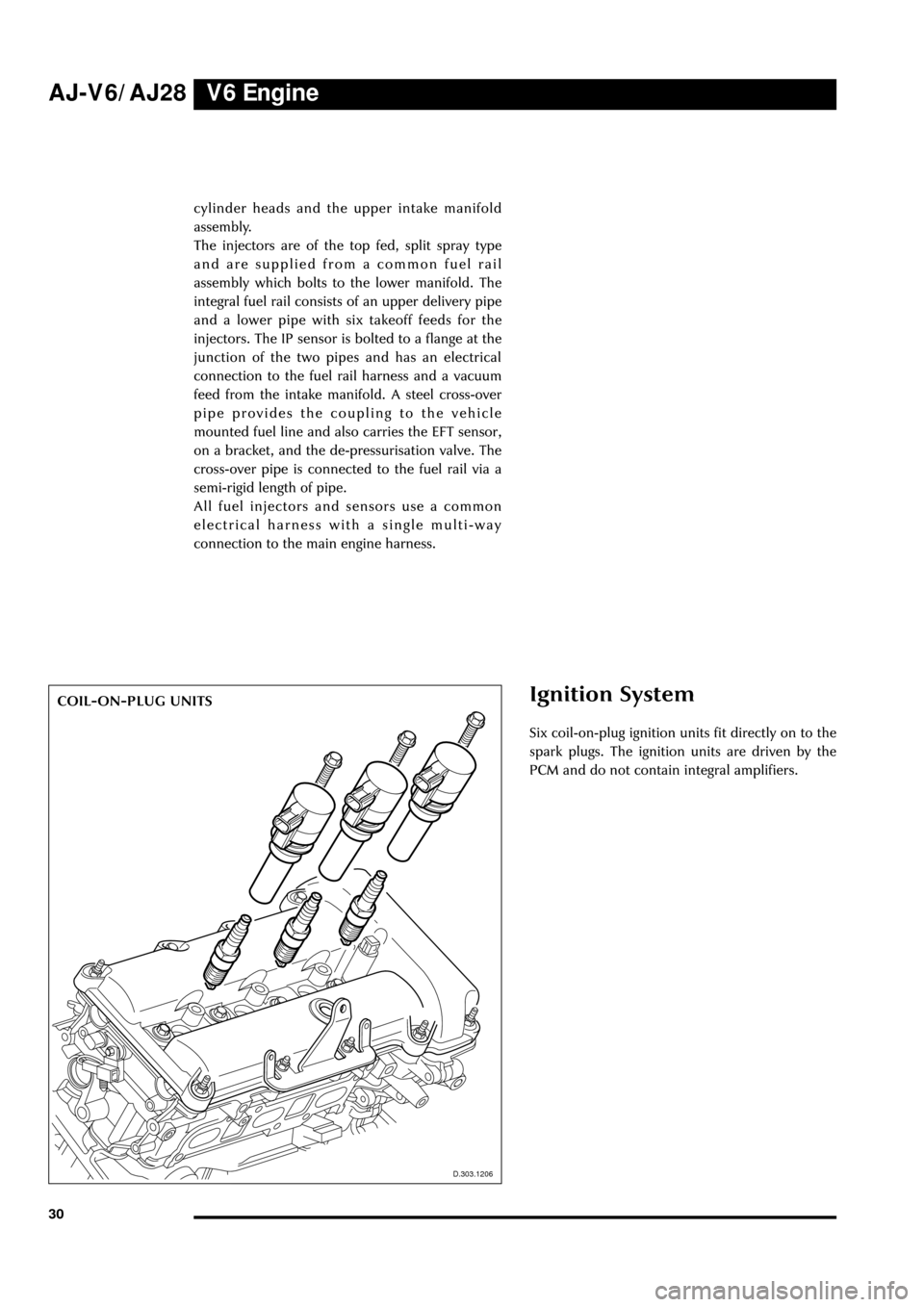
Ignition System
V6 Engine AJ-V6/AJ28
30cylinder heads and the upper intake manifold
assembly.
The injectors are of the top fed, split spray type
and are supplied from a common fuel rail
assembly which bolts to the lower manifold. The
integral fuel rail consists of an upper delivery pipe
and a lower pipe with six takeoff feeds for the
injectors. The IP sensor is bolted to a flange at the
junction of the two pipes and has an electrical
connection to the fuel rail harness and a vacuum
feed from the intake manifold. A steel cross-over
pipe provides the coupling to the vehicle
mounted fuel line and also carries the EFT sensor,
on a bracket, and the de-pressurisation valve. The
cross-over pipe is connected to the fuel rail via a
semi-rigid length of pipe.
All fuel injectors and sensors use a common
electrical harness with a single multi-way
connection to the main engine harness.
Six coil-on-plug ignition units fit directly on to the
spark plugs. The ignition units are driven by the
PCM and do not contain integral amplifiers.
D.303.1206D.303.1206
COIL-ON-PLUG UNITS
Page 36 of 75
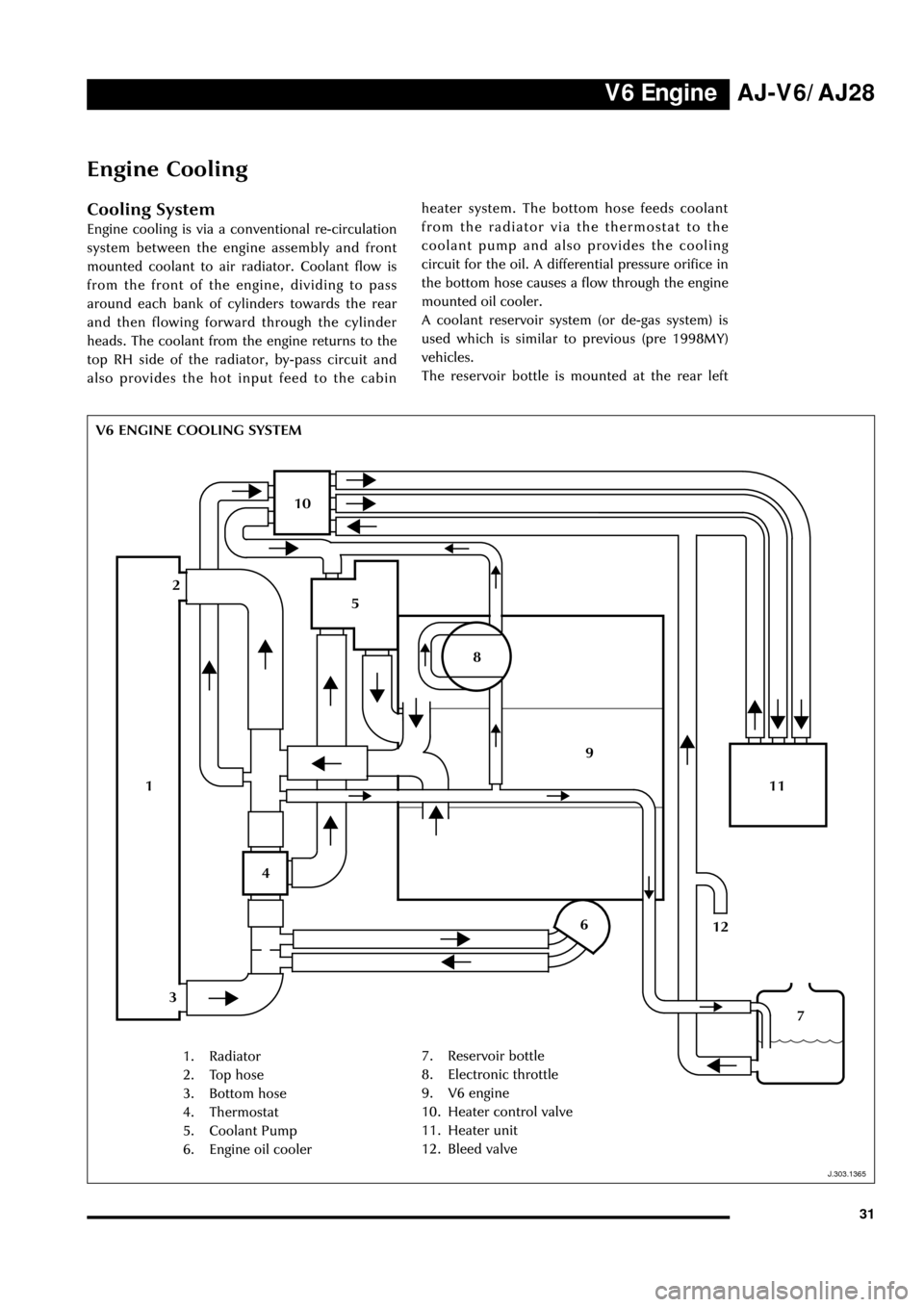
V6 EngineAJ-V6/AJ28
31
J.303.1365
Engine Cooling
Cooling System
Engine cooling is via a conventional re-circulation
system between the engine assembly and front
mounted coolant to air radiator. Coolant flow is
from the front of the engine, dividing to pass
around each bank of cylinders towards the rear
and then flowing forward through the cylinder
heads. The coolant from the engine returns to the
top RH side of the radiator, by-pass circuit and
also provides the hot input feed to the cabin
V6 ENGINE COOLING SYSTEMheater system. The bottom hose feeds coolant
from the radiator via the thermostat to the
coolant pump and also provides the cooling
circuit for the oil. A differential pressure orifice in
the bottom hose causes a flow through the engine
mounted oil cooler.
A coolant reservoir system (or de-gas system) is
used which is similar to previous (pre 1998MY)
vehicles.
The reservoir bottle is mounted at the rear left
1. Radiator
2. Top hose
3. Bottom hose
4. Thermostat
5. Coolant Pump
6. Engine oil cooler7. Reservoir bottle
8. Electronic throttle
9. V6 engine
10. Heater control valve
11. Heater unit
12. Bleed valve
1
10
5
11
9
4
6
2
3
8
12
7
J.303.1365
Page 37 of 75
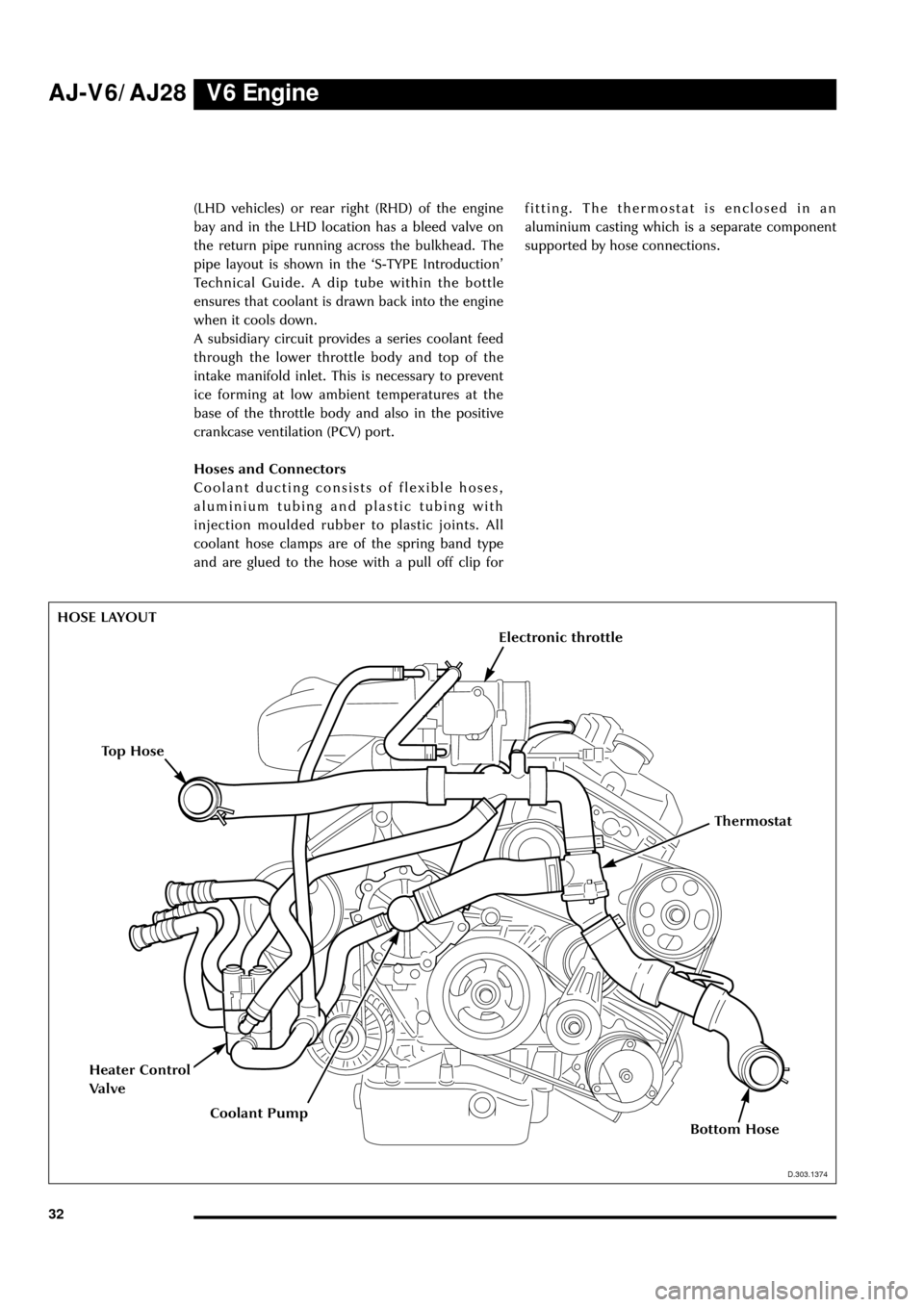
V6 Engine AJ-V6/AJ28
32(LHD vehicles) or rear right (RHD) of the engine
bay and in the LHD location has a bleed valve on
the return pipe running across the bulkhead. The
pipe layout is shown in the ÔS-TYPE IntroductionÕ
Technical Guide. A dip tube within the bottle
ensures that coolant is drawn back into the engine
when it cools down.
A subsidiary circuit provides a series coolant feed
through the lower throttle body and top of the
intake manifold inlet. This is necessary to prevent
ice forming at low ambient temperatures at the
base of the throttle body and also in the positive
crankcase ventilation (PCV) port.
Hoses and Connectors
Coolant ducting consists of flexible hoses,
aluminium tubing and plastic tubing with
injection moulded rubber to plastic joints. All
coolant hose clamps are of the spring band type
and are glued to the hose with a pull off clip for
D.303.1374
HOSE LAYOUT
Electronic throttle
D.303.1374
fitting. The thermostat is enclosed in an
aluminium casting which is a separate component
supported by hose connections.
Top Hose
Bottom Hose
Heater Control
Valve
Thermostat
Coolant Pump
Page 38 of 75
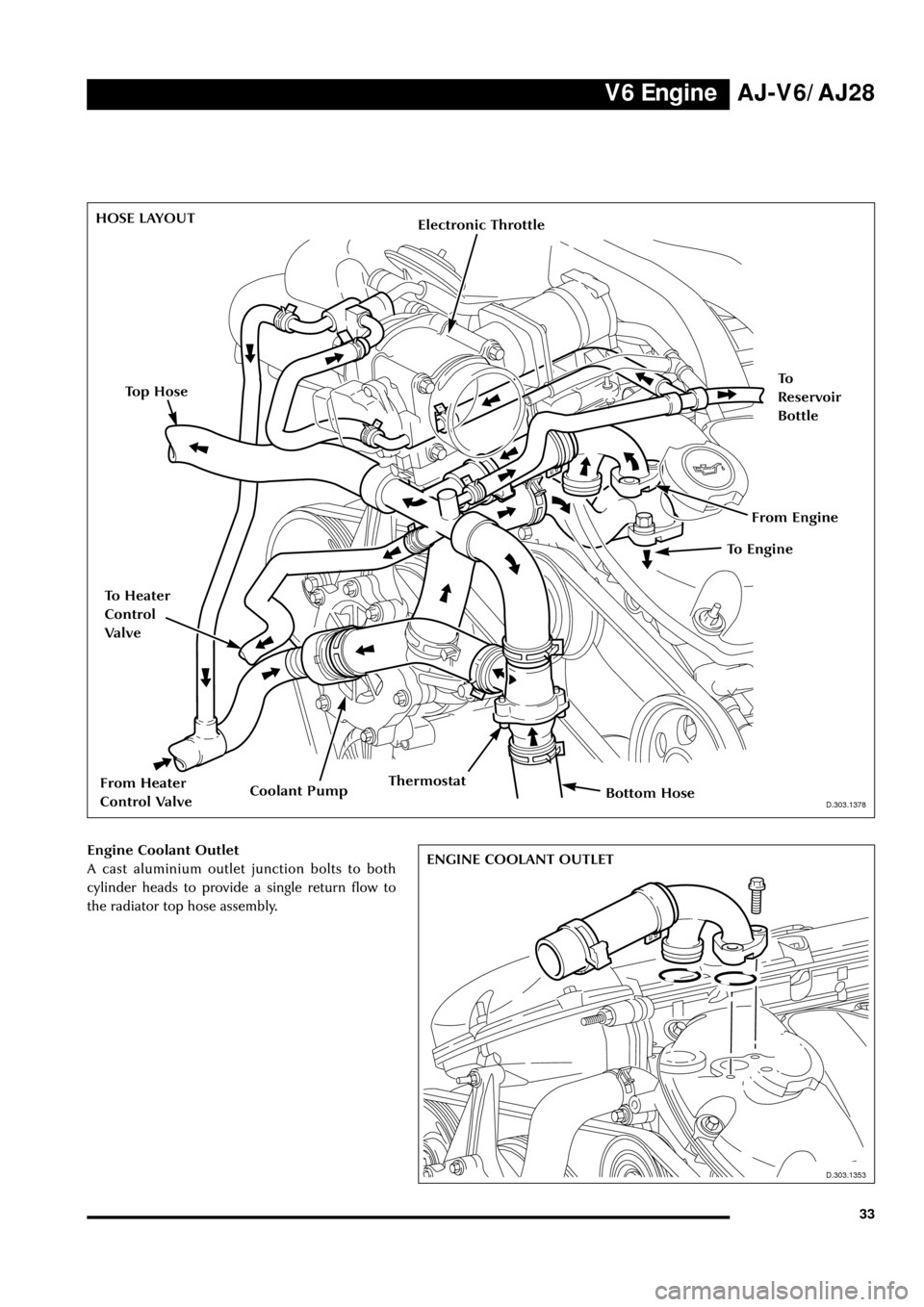
V6 EngineAJ-V6/AJ28
33
J.303.1378
HOSE LAYOUT
D.303.1378
Electronic Throttle
Top Hose
Bottom HoseFrom Heater
Control Valve
To
Reservoir
Bottle
Engine Coolant Outlet
A cast aluminium outlet junction bolts to both
cylinder heads to provide a single return flow to
the radiator top hose assembly.
D.303.1353
ENGINE COOLANT OUTLET
D.303.1353
To Engine
From Engine
To Heater
Control
Valve
ThermostatCoolant Pump
Page 39 of 75
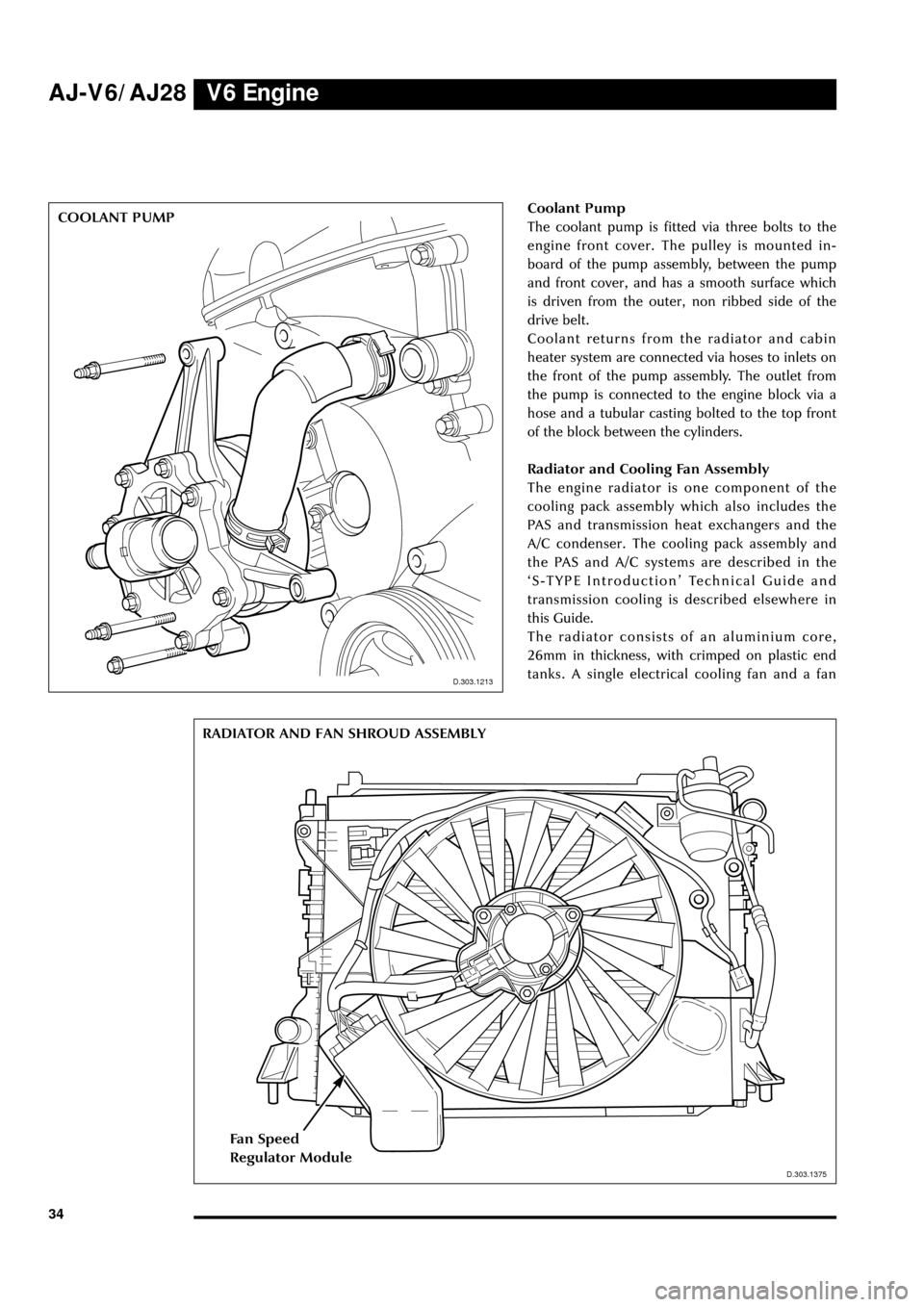
V6 Engine AJ-V6/AJ28
34Coolant Pump
The coolant pump is fitted via three bolts to the
engine front cover. The pulley is mounted in-
board of the pump assembly, between the pump
and front cover, and has a smooth surface which
is driven from the outer, non ribbed side of the
drive belt.
Coolant returns from the radiator and cabin
heater system are connected via hoses to inlets on
the front of the pump assembly. The outlet from
the pump is connected to the engine block via a
hose and a tubular casting bolted to the top front
of the block between the cylinders.
Radiator and Cooling Fan Assembly
The engine radiator is one component of the
cooling pack assembly which also includes the
PAS and transmission heat exchangers and the
A/C condenser. The cooling pack assembly and
the PAS and A/C systems are described in the
ÔS-TYPE IntroductionÕ Technical Guide and
transmission cooling is described elsewhere in
this Guide.
The radiator consists of an aluminium core,
26mm in thickness, with crimped on plastic end
tanks. A single electrical cooling fan and a fan
D.303.1213
COOLANT PUMP
D.303.1213
D.303.1375
RADIATOR AND FAN SHROUD ASSEMBLY
D.303.1375
Fan Speed
Regulator Module
Page 40 of 75
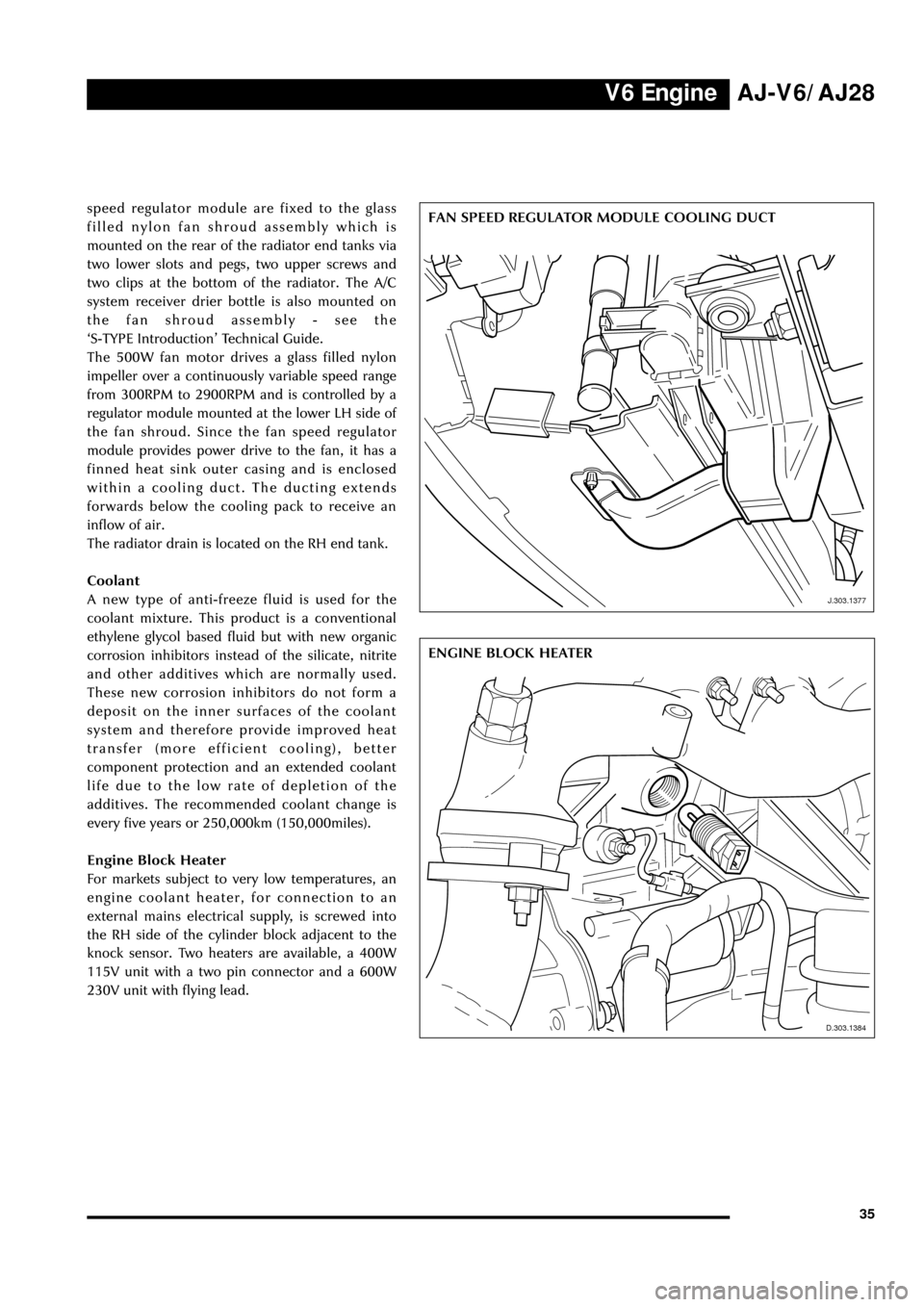
V6 EngineAJ-V6/AJ28
35
J.303.1384
ENGINE BLOCK HEATER
D.303.1384
J.303.1377
FAN SPEED REGULATOR MODULE COOLING DUCT speed regulator module are fixed to the glass
filled nylon fan shroud assembly which is
mounted on the rear of the radiator end tanks via
two lower slots and pegs, two upper screws and
two clips at the bottom of the radiator. The A/C
system receiver drier bottle is also mounted on
the fan shroud assembly - see the
ÔS-TYPE IntroductionÕ Technical Guide.
The 500W fan motor drives a glass filled nylon
impeller over a continuously variable speed range
from 300RPM to 2900RPM and is controlled by a
regulator module mounted at the lower LH side of
the fan shroud. Since the fan speed regulator
module provides power drive to the fan, it has a
finned heat sink outer casing and is enclosed
within a cooling duct. The ducting extends
forwards below the cooling pack to receive an
inflow of air.
The radiator drain is located on the RH end tank.
Coolant
A new type of anti-freeze fluid is used for the
coolant mixture. This product is a conventional
ethylene glycol based fluid but with new organic
corrosion inhibitors instead of the silicate, nitrite
and other additives which are normally used.
These new corrosion inhibitors do not form a
deposit on the inner surfaces of the coolant
system and therefore provide improved heat
transfer (more efficient cooling), better
component protection and an extended coolant
life due to the low rate of depletion of the
additives. The recommended coolant change is
every five years or 250,000km (150,000miles).
Engine Block Heater
For markets subject to very low temperatures, an
engine coolant heater, for connection to an
external mains electrical supply, is screwed into
the RH side of the cylinder block adjacent to the
knock sensor. Two heaters are available, a 400W
115V unit with a two pin connector and a 600W
230V unit with flying lead.
J.303.1377