Module JAGUAR XFR 2010 1.G Workshop Manual
[x] Cancel search | Manufacturer: JAGUAR, Model Year: 2010, Model line: XFR, Model: JAGUAR XFR 2010 1.GPages: 3039, PDF Size: 58.49 MB
Page 1590 of 3039
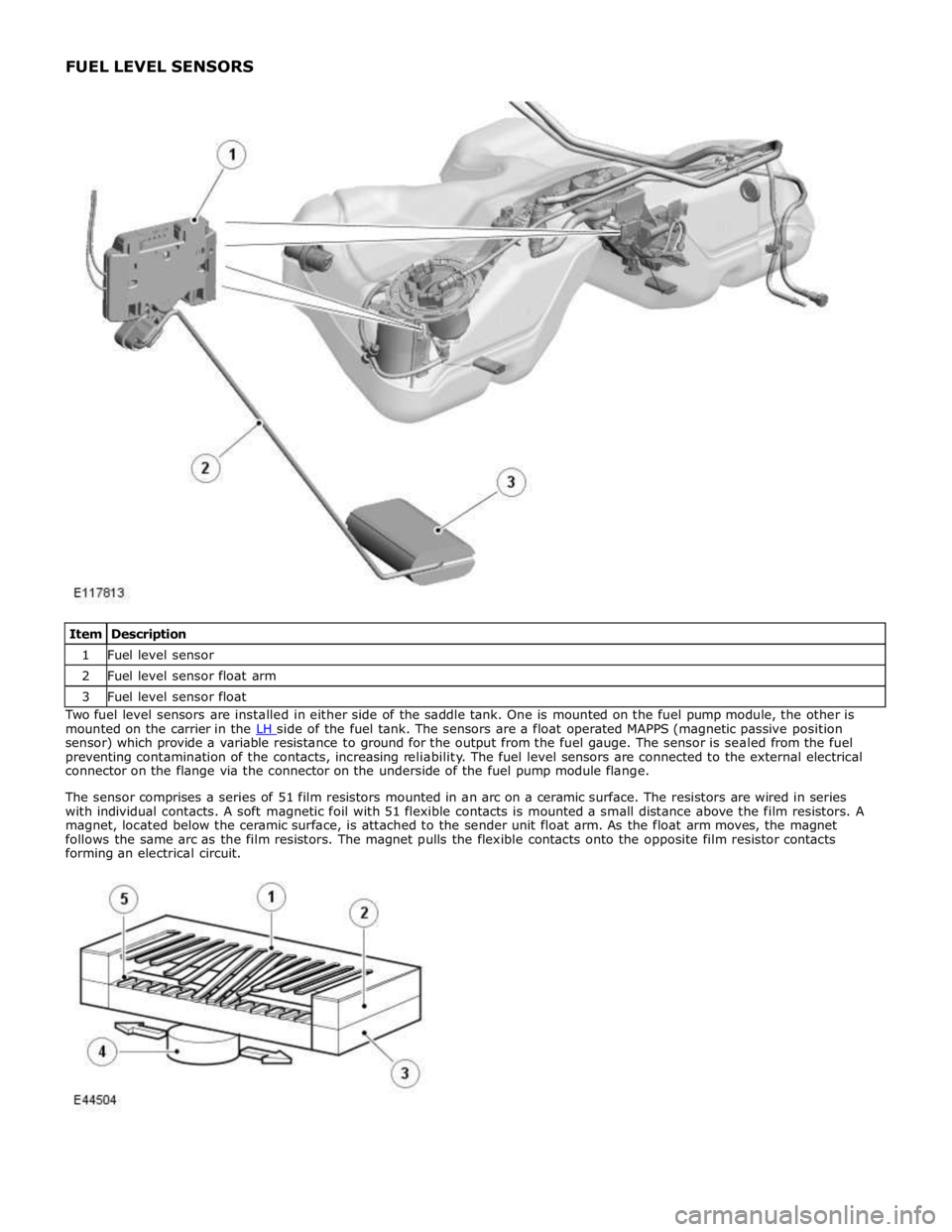
1 Fuel level sensor 2 Fuel level sensor float arm 3 Fuel level sensor float Two fuel level sensors are installed in either side of the saddle tank. One is mounted on the fuel pump module, the other is
mounted on the carrier in the LH side of the fuel tank. The sensors are a float operated MAPPS (magnetic passive position sensor) which provide a variable resistance to ground for the output from the fuel gauge. The sensor is sealed from the fuel
preventing contamination of the contacts, increasing reliability. The fuel level sensors are connected to the external electrical
connector on the flange via the connector on the underside of the fuel pump module flange.
The sensor comprises a series of 51 film resistors mounted in an arc on a ceramic surface. The resistors are wired in series
with individual contacts. A soft magnetic foil with 51 flexible contacts is mounted a small distance above the film resistors. A
magnet, located below the ceramic surface, is attached to the sender unit float arm. As the float arm moves, the magnet
follows the same arc as the film resistors. The magnet pulls the flexible contacts onto the opposite film resistor contacts
forming an electrical circuit.
Page 1591 of 3039
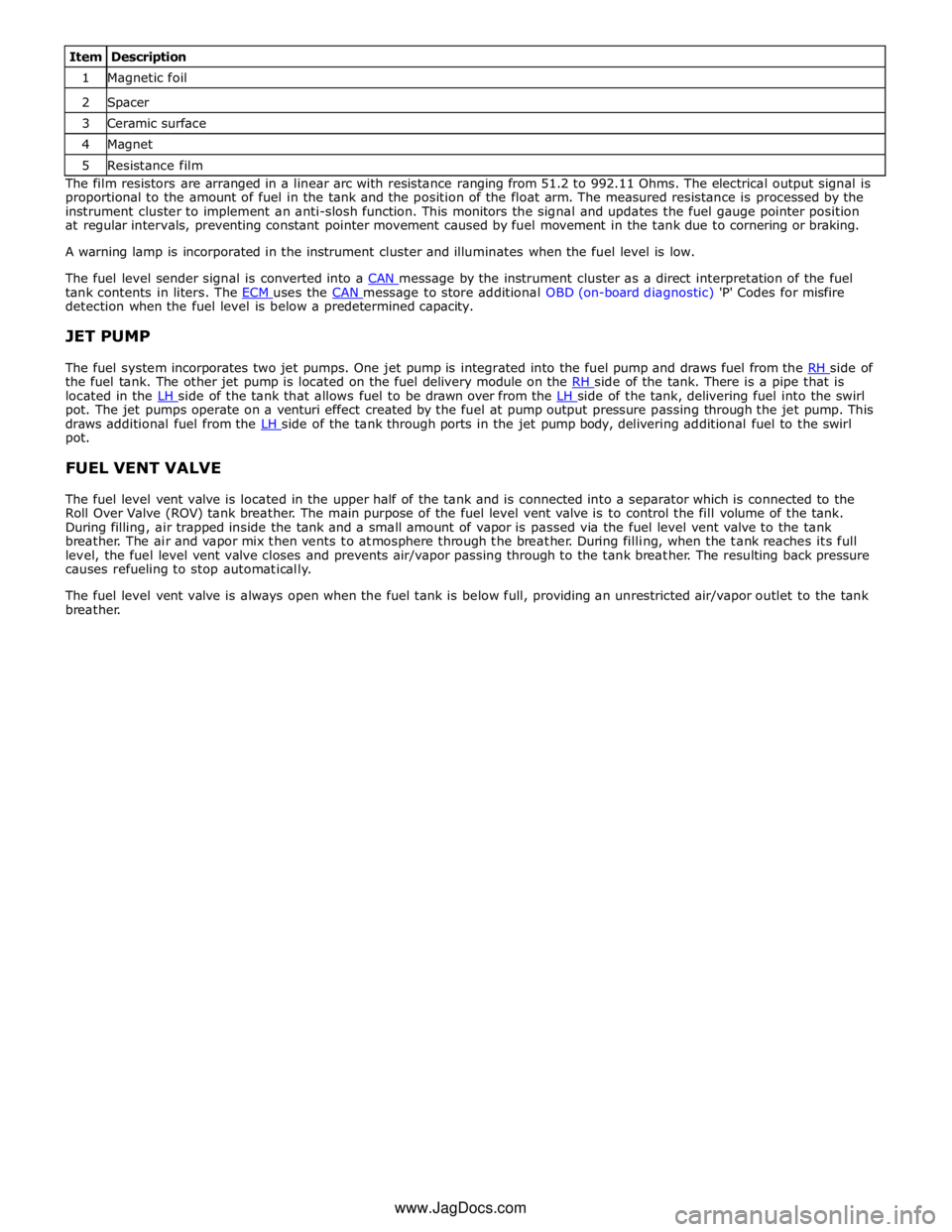
1 Magnetic foil 2 Spacer 3 Ceramic surface 4 Magnet 5 Resistance film The film resistors are arranged in a linear arc with resistance ranging from 51.2 to 992.11 Ohms. The electrical output signal is
proportional to the amount of fuel in the tank and the position of the float arm. The measured resistance is processed by the
instrument cluster to implement an anti-slosh function. This monitors the signal and updates the fuel gauge pointer position
at regular intervals, preventing constant pointer movement caused by fuel movement in the tank due to cornering or braking.
A warning lamp is incorporated in the instrument cluster and illuminates when the fuel level is low.
The fuel level sender signal is converted into a CAN message by the instrument cluster as a direct interpretation of the fuel tank contents in liters. The ECM uses the CAN message to store additional OBD (on-board diagnostic) 'P' Codes for misfire detection when the fuel level is below a predetermined capacity.
JET PUMP
The fuel system incorporates two jet pumps. One jet pump is integrated into the fuel pump and draws fuel from the RH side of the fuel tank. The other jet pump is located on the fuel delivery module on the RH side of the tank. There is a pipe that is located in the LH side of the tank that allows fuel to be drawn over from the LH side of the tank, delivering fuel into the swirl pot. The jet pumps operate on a venturi effect created by the fuel at pump output pressure passing through the jet pump. This
draws additional fuel from the LH side of the tank through ports in the jet pump body, delivering additional fuel to the swirl pot.
FUEL VENT VALVE
The fuel level vent valve is located in the upper half of the tank and is connected into a separator which is connected to the
Roll Over Valve (ROV) tank breather. The main purpose of the fuel level vent valve is to control the fill volume of the tank.
During filling, air trapped inside the tank and a small amount of vapor is passed via the fuel level vent valve to the tank
breather. The air and vapor mix then vents to atmosphere through the breather. During filling, when the tank reaches its full
level, the fuel level vent valve closes and prevents air/vapor passing through to the tank breather. The resulting back pressure
causes refueling to stop automatically.
The fuel level vent valve is always open when the fuel tank is below full, providing an unrestricted air/vapor outlet to the tank
breather.
www.JagDocs.com
Page 1595 of 3039
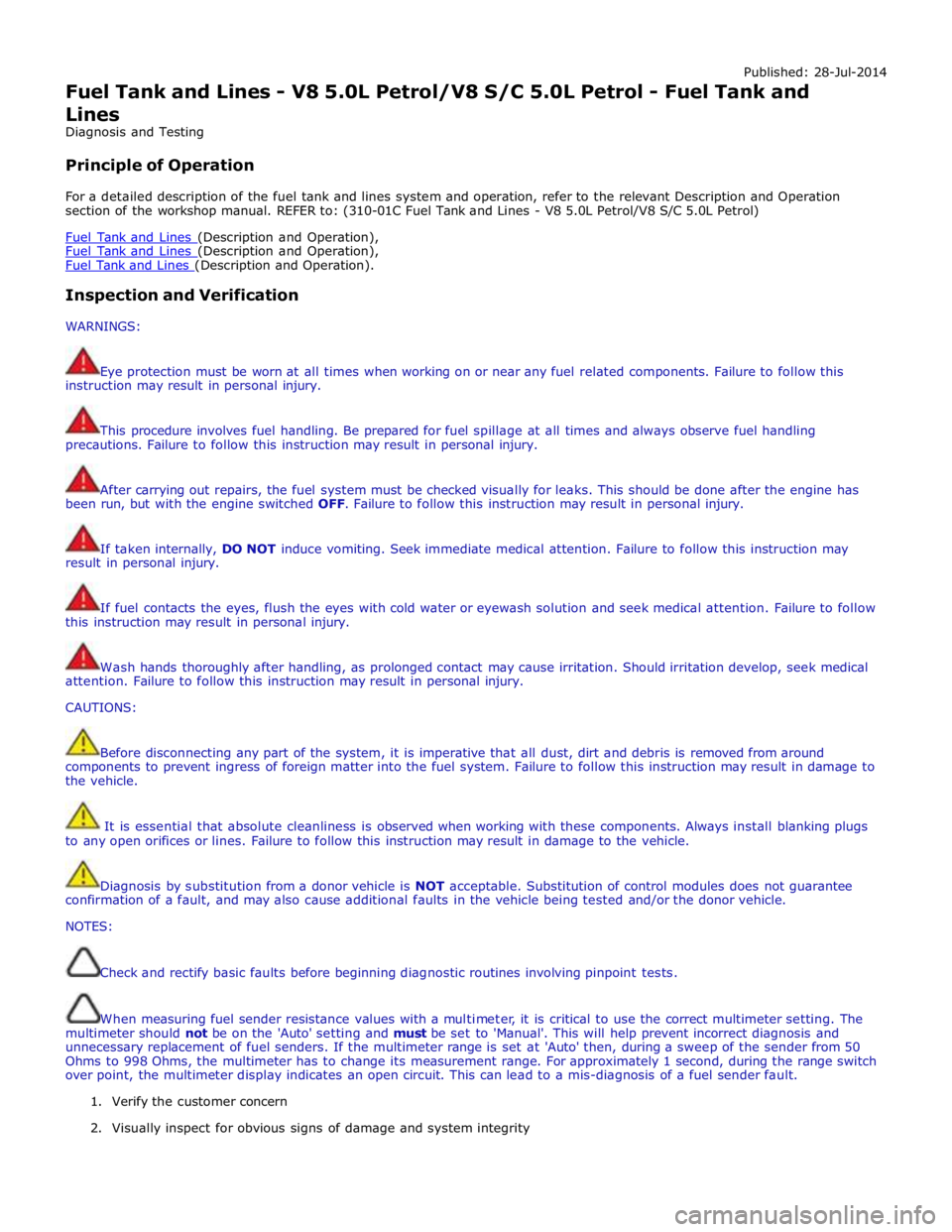
Published: 28-Jul-2014
Fuel Tank and Lines - V8 5.0L Petrol/V8 S/C 5.0L Petrol - Fuel Tank and
Lines
Diagnosis and Testing
Principle of Operation
For a detailed description of the fuel tank and lines system and operation, refer to the relevant Description and Operation
section of the workshop manual. REFER to: (310-01C Fuel Tank and Lines - V8 5.0L Petrol/V8 S/C 5.0L Petrol)
Fuel Tank and Lines (Description and Operation), Fuel Tank and Lines (Description and Operation), Fuel Tank and Lines (Description and Operation).
Inspection and Verification
WARNINGS:
Eye protection must be worn at all times when working on or near any fuel related components. Failure to follow this
instruction may result in personal injury.
This procedure involves fuel handling. Be prepared for fuel spillage at all times and always observe fuel handling
precautions. Failure to follow this instruction may result in personal injury.
After carrying out repairs, the fuel system must be checked visually for leaks. This should be done after the engine has
been run, but with the engine switched OFF. Failure to follow this instruction may result in personal injury.
If taken internally, DO NOT induce vomiting. Seek immediate medical attention. Failure to follow this instruction may
result in personal injury.
If fuel contacts the eyes, flush the eyes with cold water or eyewash solution and seek medical attention. Failure to follow
this instruction may result in personal injury.
Wash hands thoroughly after handling, as prolonged contact may cause irritation. Should irritation develop, seek medical
attention. Failure to follow this instruction may result in personal injury.
CAUTIONS:
Before disconnecting any part of the system, it is imperative that all dust, dirt and debris is removed from around
components to prevent ingress of foreign matter into the fuel system. Failure to follow this instruction may result in damage to
the vehicle.
It is essential that absolute cleanliness is observed when working with these components. Always install blanking plugs
to any open orifices or lines. Failure to follow this instruction may result in damage to the vehicle.
Diagnosis by substitution from a donor vehicle is NOT acceptable. Substitution of control modules does not guarantee
confirmation of a fault, and may also cause additional faults in the vehicle being tested and/or the donor vehicle.
NOTES:
Check and rectify basic faults before beginning diagnostic routines involving pinpoint tests.
When measuring fuel sender resistance values with a multimeter, it is critical to use the correct multimeter setting. The
multimeter should not be on the 'Auto' setting and must be set to 'Manual'. This will help prevent incorrect diagnosis and
unnecessary replacement of fuel senders. If the multimeter range is set at 'Auto' then, during a sweep of the sender from 50
Ohms to 998 Ohms, the multimeter has to change its measurement range. For approximately 1 second, during the range switch
over point, the multimeter display indicates an open circuit. This can lead to a mis-diagnosis of a fuel sender fault.
1. Verify the customer concern
2. Visually inspect for obvious signs of damage and system integrity
Page 1596 of 3039
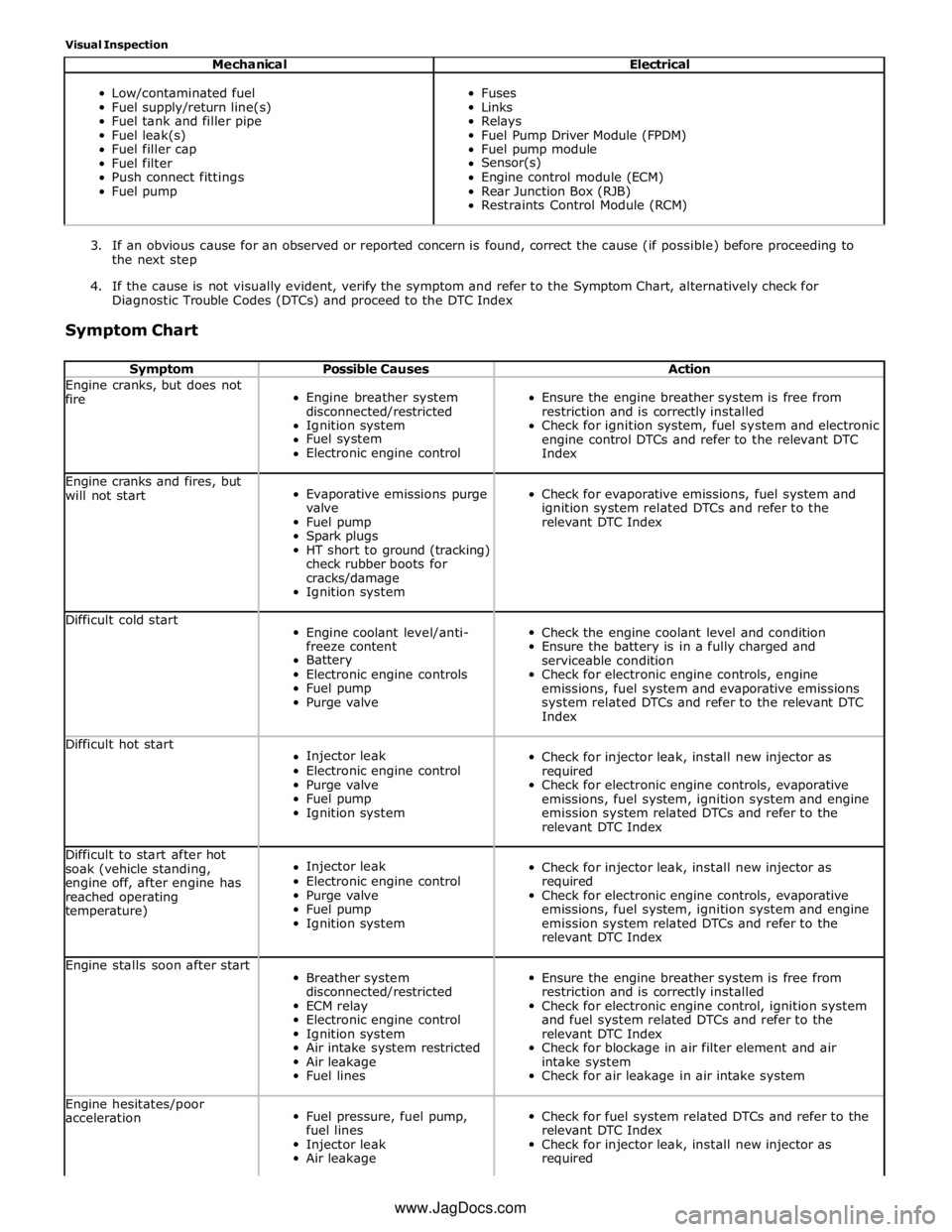
Visual Inspection
Mechanical Electrical
Low/contaminated fuel
Fuel supply/return line(s)
Fuel tank and filler pipe
Fuel leak(s)
Fuel filler cap
Fuel filter
Push connect fittings
Fuel pump
Fuses
Links
Relays
Fuel Pump Driver Module (FPDM)
Fuel pump module
Sensor(s)
Engine control module (ECM)
Rear Junction Box (RJB)
Restraints Control Module (RCM)
3. If an obvious cause for an observed or reported concern is found, correct the cause (if possible) before proceeding to
the next step
4. If the cause is not visually evident, verify the symptom and refer to the Symptom Chart, alternatively check for
Diagnostic Trouble Codes (DTCs) and proceed to the DTC Index
Symptom Chart
Symptom Possible Causes Action Engine cranks, but does not
fire
Engine breather system
disconnected/restricted
Ignition system
Fuel system
Electronic engine control
Ensure the engine breather system is free from
restriction and is correctly installed
Check for ignition system, fuel system and electronic
engine control DTCs and refer to the relevant DTC
Index Engine cranks and fires, but
will not start
Evaporative emissions purge
valve
Fuel pump
Spark plugs
HT short to ground (tracking)
check rubber boots for
cracks/damage
Ignition system
Check for evaporative emissions, fuel system and
ignition system related DTCs and refer to the
relevant DTC Index Difficult cold start
Engine coolant level/anti-
freeze content
Battery
Electronic engine controls
Fuel pump
Purge valve
Check the engine coolant level and condition
Ensure the battery is in a fully charged and
serviceable condition
Check for electronic engine controls, engine
emissions, fuel system and evaporative emissions
system related DTCs and refer to the relevant DTC
Index Difficult hot start
Injector leak
Electronic engine control
Purge valve
Fuel pump
Ignition system
Check for injector leak, install new injector as
required
Check for electronic engine controls, evaporative
emissions, fuel system, ignition system and engine
emission system related DTCs and refer to the
relevant DTC Index Difficult to start after hot
soak (vehicle standing,
engine off, after engine has
reached operating
temperature)
Injector leak
Electronic engine control
Purge valve
Fuel pump
Ignition system
Check for injector leak, install new injector as
required
Check for electronic engine controls, evaporative
emissions, fuel system, ignition system and engine
emission system related DTCs and refer to the
relevant DTC Index Engine stalls soon after start
Breather system
disconnected/restricted
ECM relay
Electronic engine control
Ignition system
Air intake system restricted
Air leakage
Fuel lines
Ensure the engine breather system is free from
restriction and is correctly installed
Check for electronic engine control, ignition system
and fuel system related DTCs and refer to the
relevant DTC Index
Check for blockage in air filter element and air
intake system
Check for air leakage in air intake system Engine hesitates/poor
acceleration
Fuel pressure, fuel pump,
fuel lines
Injector leak
Air leakage
Check for fuel system related DTCs and refer to the
relevant DTC Index
Check for injector leak, install new injector as
required www.JagDocs.com
Page 1598 of 3039
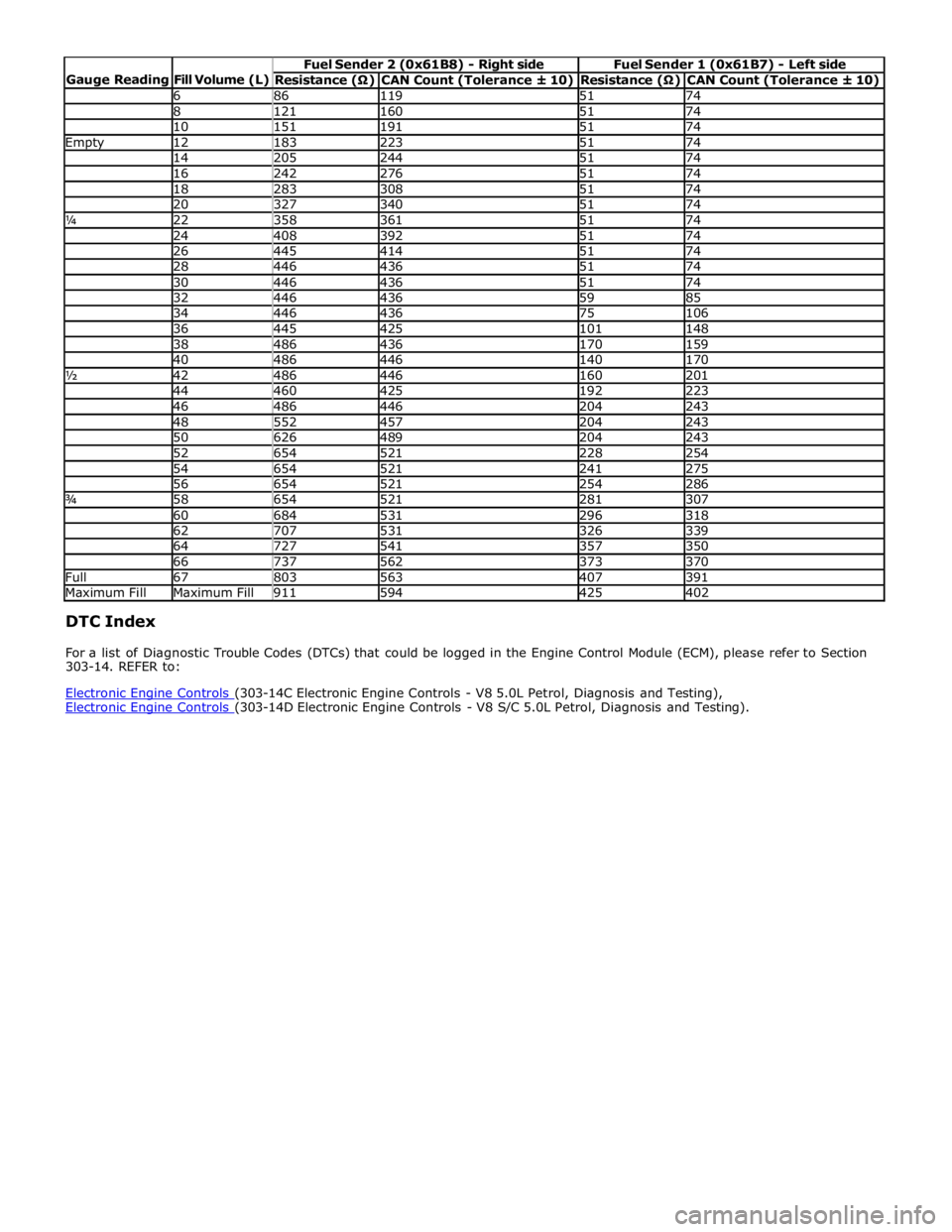
Resistance (Ω) CAN Count (Tolerance ± 10) Resistance (Ω) CAN Count (Tolerance ± 10) 6 86 119 51 74 8 121 160 51 74 10 151 191 51 74 Empty 12 183 223 51 74 14 205 244 51 74 16 242 276 51 74 18 283 308 51 74 20 327 340 51 74 ¼ 22 358 361 51 74 24 408 392 51 74 26 445 414 51 74 28 446 436 51 74 30 446 436 51 74 32 446 436 59 85 34 446 436 75 106 36 445 425 101 148 38 486 436 170 159 40 486 446 140 170 ½ 42 486 446 160 201 44 460 425 192 223 46 486 446 204 243 48 552 457 204 243 50 626 489 204 243 52 654 521 228 254 54 654 521 241 275 56 654 521 254 286 ¾ 58 654 521 281 307 60 684 531 296 318 62 707 531 326 339 64 727 541 357 350 66 737 562 373 370 Full 67 803 563 407 391 Maximum Fill Maximum Fill 911 594 425 402 DTC Index
For a list of Diagnostic Trouble Codes (DTCs) that could be logged in the Engine Control Module (ECM), please refer to Section
303-14. REFER to:
Electronic Engine Controls (303-14C Electronic Engine Controls - V8 5.0L Petrol, Diagnosis and Testing), Electronic Engine Controls (303-14D Electronic Engine Controls - V8 S/C 5.0L Petrol, Diagnosis and Testing).
Page 1631 of 3039
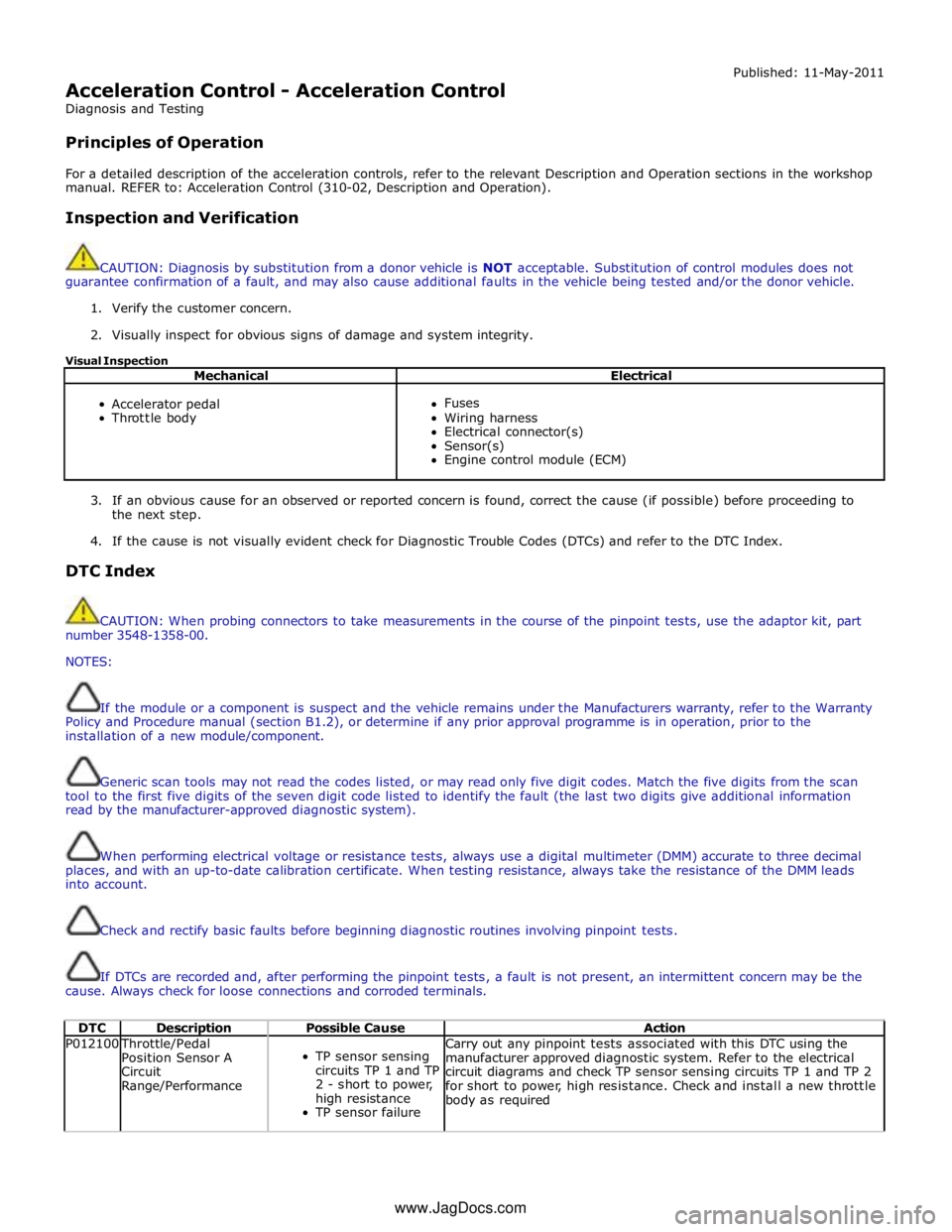
Acceleration Control - Acceleration Control
Diagnosis and Testing
Principles of Operation Published: 11-May-2011
For a detailed description of the acceleration controls, refer to the relevant Description and Operation sections in the workshop
manual. REFER to: Acceleration Control (310-02, Description and Operation).
Inspection and Verification
CAUTION: Diagnosis by substitution from a donor vehicle is NOT acceptable. Substitution of control modules does not
guarantee confirmation of a fault, and may also cause additional faults in the vehicle being tested and/or the donor vehicle.
1. Verify the customer concern.
2. Visually inspect for obvious signs of damage and system integrity.
Visual Inspection
Mechanical Electrical
Accelerator pedal
Throttle body
Fuses
Wiring harness
Electrical connector(s)
Sensor(s)
Engine control module (ECM)
3. If an obvious cause for an observed or reported concern is found, correct the cause (if possible) before proceeding to
the next step.
4. If the cause is not visually evident check for Diagnostic Trouble Codes (DTCs) and refer to the DTC Index.
DTC Index
CAUTION: When probing connectors to take measurements in the course of the pinpoint tests, use the adaptor kit, part
number 3548-1358-00.
NOTES:
If the module or a component is suspect and the vehicle remains under the Manufacturers warranty, refer to the Warranty
Policy and Procedure manual (section B1.2), or determine if any prior approval programme is in operation, prior to the
installation of a new module/component.
Generic scan tools may not read the codes listed, or may read only five digit codes. Match the five digits from the scan
tool to the first five digits of the seven digit code listed to identify the fault (the last two digits give additional information
read by the manufacturer-approved diagnostic system).
When performing electrical voltage or resistance tests, always use a digital multimeter (DMM) accurate to three decimal
places, and with an up-to-date calibration certificate. When testing resistance, always take the resistance of the DMM leads
into account.
Check and rectify basic faults before beginning diagnostic routines involving pinpoint tests.
If DTCs are recorded and, after performing the pinpoint tests, a fault is not present, an intermittent concern may be the
cause. Always check for loose connections and corroded terminals.
DTC Description Possible Cause Action P012100 Throttle/Pedal
Position Sensor A
Circuit
Range/Performance
TP sensor sensing
circuits TP 1 and TP
2 - short to power,
high resistance
TP sensor failure Carry out any pinpoint tests associated with this DTC using the
manufacturer approved diagnostic system. Refer to the electrical
circuit diagrams and check TP sensor sensing circuits TP 1 and TP 2
for short to power, high resistance. Check and install a new throttle
body as required www.JagDocs.com
Page 1632 of 3039
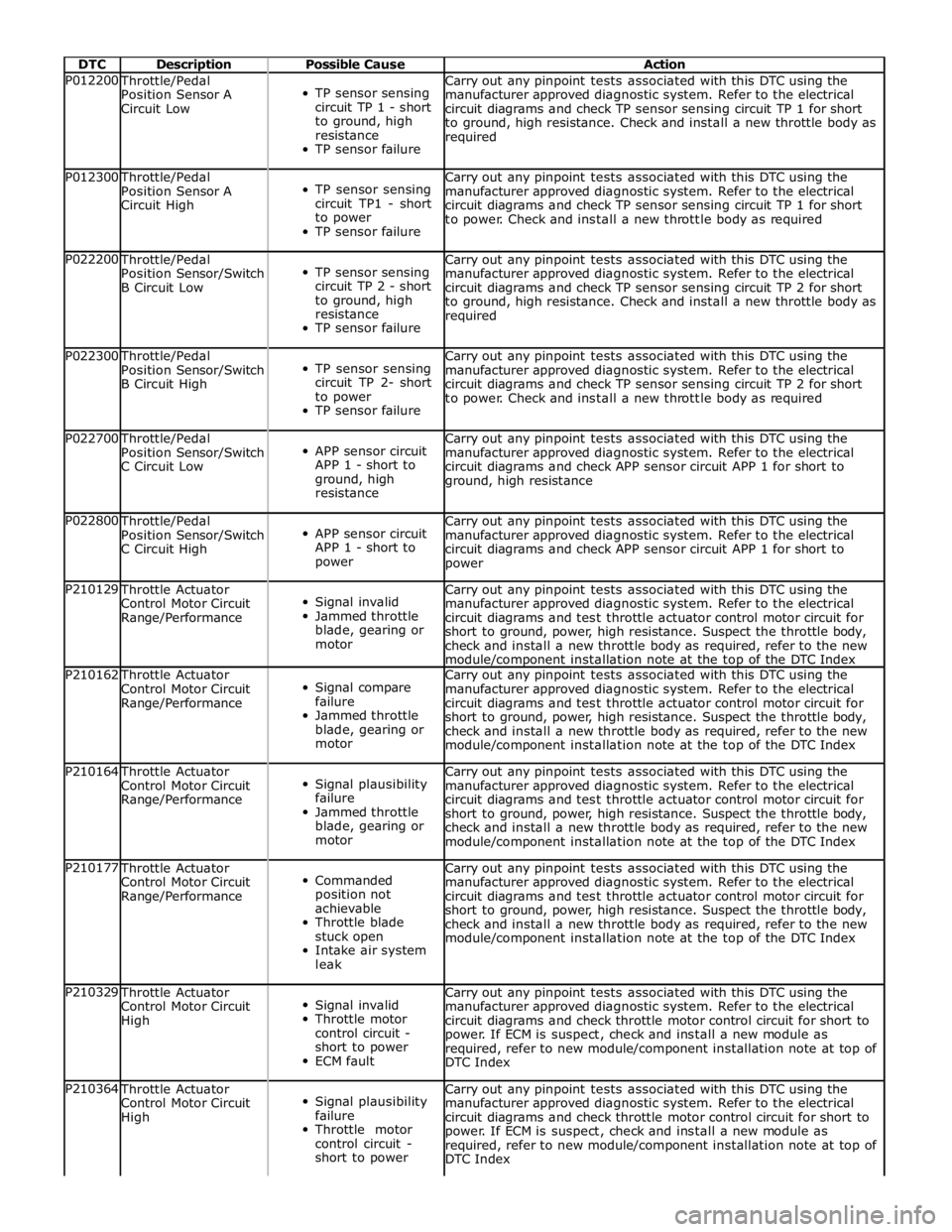
DTC Description Possible Cause Action P012200 Throttle/Pedal
Position Sensor A
Circuit Low
TP sensor sensing
circuit TP 1 - short
to ground, high
resistance
TP sensor failure Carry out any pinpoint tests associated with this DTC using the
manufacturer approved diagnostic system. Refer to the electrical
circuit diagrams and check TP sensor sensing circuit TP 1 for short
to ground, high resistance. Check and install a new throttle body as
required P012300 Throttle/Pedal
Position Sensor A
Circuit High
TP sensor sensing
circuit TP1 - short
to power
TP sensor failure Carry out any pinpoint tests associated with this DTC using the
manufacturer approved diagnostic system. Refer to the electrical
circuit diagrams and check TP sensor sensing circuit TP 1 for short
to power. Check and install a new throttle body as required P022200 Throttle/Pedal
Position Sensor/Switch
B Circuit Low
TP sensor sensing
circuit TP 2 - short
to ground, high
resistance
TP sensor failure Carry out any pinpoint tests associated with this DTC using the
manufacturer approved diagnostic system. Refer to the electrical
circuit diagrams and check TP sensor sensing circuit TP 2 for short
to ground, high resistance. Check and install a new throttle body as
required P022300 Throttle/Pedal
Position Sensor/Switch
B Circuit High
TP sensor sensing
circuit TP 2- short
to power
TP sensor failure Carry out any pinpoint tests associated with this DTC using the
manufacturer approved diagnostic system. Refer to the electrical
circuit diagrams and check TP sensor sensing circuit TP 2 for short
to power. Check and install a new throttle body as required P022700 Throttle/Pedal
Position Sensor/Switch
C Circuit Low
APP sensor circuit
APP 1 - short to
ground, high
resistance Carry out any pinpoint tests associated with this DTC using the
manufacturer approved diagnostic system. Refer to the electrical
circuit diagrams and check APP sensor circuit APP 1 for short to
ground, high resistance P022800 Throttle/Pedal
Position Sensor/Switch
C Circuit High
APP sensor circuit
APP 1 - short to
power Carry out any pinpoint tests associated with this DTC using the
manufacturer approved diagnostic system. Refer to the electrical
circuit diagrams and check APP sensor circuit APP 1 for short to
power P210129 Throttle Actuator
Control Motor Circuit
Range/Performance
Signal invalid
Jammed throttle
blade, gearing or
motor Carry out any pinpoint tests associated with this DTC using the
manufacturer approved diagnostic system. Refer to the electrical
circuit diagrams and test throttle actuator control motor circuit for
short to ground, power, high resistance. Suspect the throttle body,
check and install a new throttle body as required, refer to the new module/component installation note at the top of the DTC Index P210162 Throttle Actuator
Control Motor Circuit
Range/Performance
Signal compare
failure
Jammed throttle
blade, gearing or
motor Carry out any pinpoint tests associated with this DTC using the
manufacturer approved diagnostic system. Refer to the electrical
circuit diagrams and test throttle actuator control motor circuit for
short to ground, power, high resistance. Suspect the throttle body,
check and install a new throttle body as required, refer to the new
module/component installation note at the top of the DTC Index P210164 Throttle Actuator
Control Motor Circuit
Range/Performance
Signal plausibility
failure
Jammed throttle
blade, gearing or
motor Carry out any pinpoint tests associated with this DTC using the
manufacturer approved diagnostic system. Refer to the electrical
circuit diagrams and test throttle actuator control motor circuit for
short to ground, power, high resistance. Suspect the throttle body,
check and install a new throttle body as required, refer to the new
module/component installation note at the top of the DTC Index P210177 Throttle Actuator
Control Motor Circuit
Range/Performance
Commanded
position not
achievable
Throttle blade
stuck open
Intake air system
leak Carry out any pinpoint tests associated with this DTC using the
manufacturer approved diagnostic system. Refer to the electrical
circuit diagrams and test throttle actuator control motor circuit for
short to ground, power, high resistance. Suspect the throttle body,
check and install a new throttle body as required, refer to the new
module/component installation note at the top of the DTC Index P210329 Throttle Actuator
Control Motor Circuit
High
Signal invalid
Throttle motor
control circuit -
short to power
ECM fault Carry out any pinpoint tests associated with this DTC using the
manufacturer approved diagnostic system. Refer to the electrical
circuit diagrams and check throttle motor control circuit for short to
power. If ECM is suspect, check and install a new module as
required, refer to new module/component installation note at top of
DTC Index P210364 Throttle Actuator
Control Motor Circuit
High
Signal plausibility
failure
Throttle motor
control circuit -
short to power Carry out any pinpoint tests associated with this DTC using the
manufacturer approved diagnostic system. Refer to the electrical
circuit diagrams and check throttle motor control circuit for short to
power. If ECM is suspect, check and install a new module as
required, refer to new module/component installation note at top of
DTC Index
Page 1633 of 3039
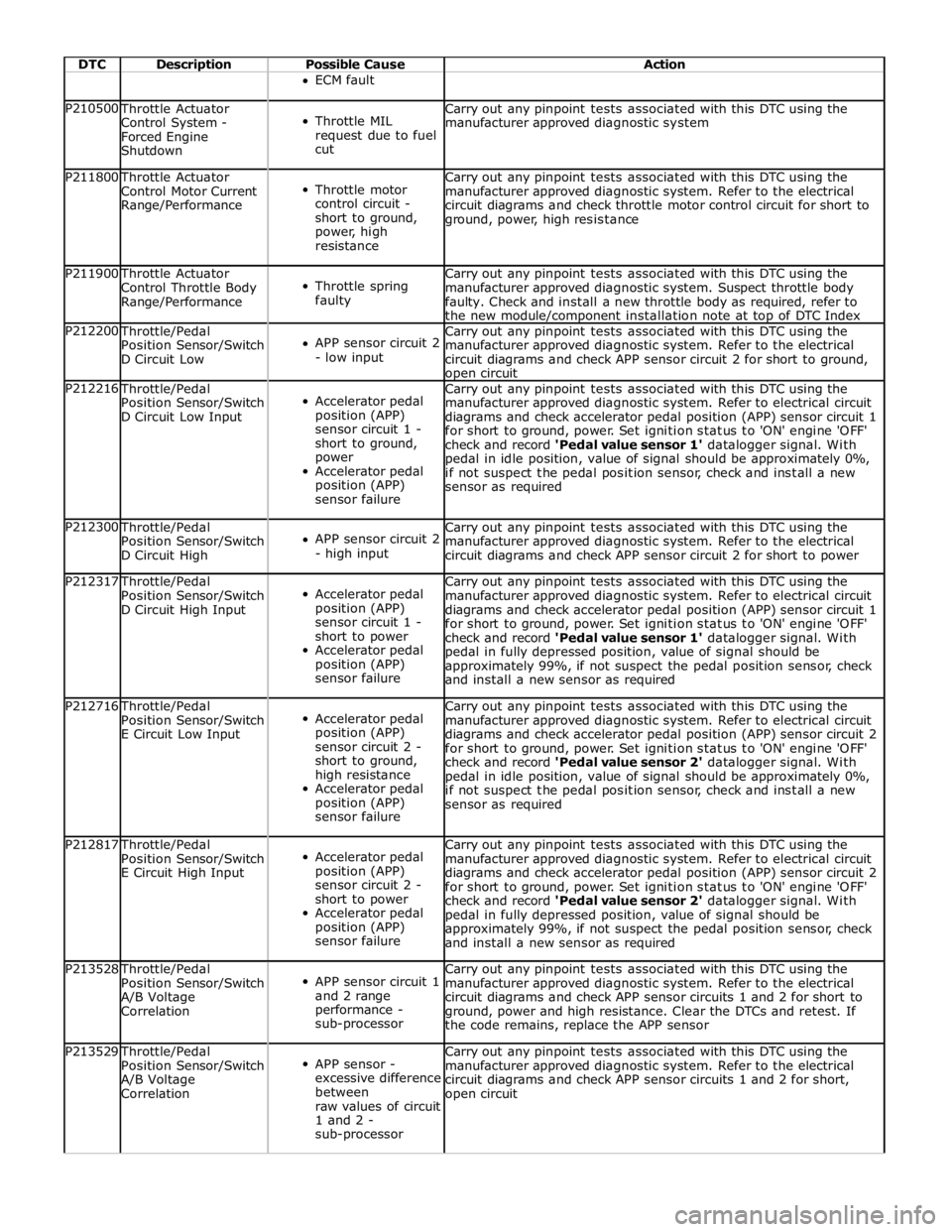
DTC Description Possible Cause Action ECM fault
P210500 Throttle Actuator
Control System -
Forced Engine
Shutdown
Throttle MIL
request due to fuel
cut Carry out any pinpoint tests associated with this DTC using the
manufacturer approved diagnostic system P211800 Throttle Actuator
Control Motor Current
Range/Performance
Throttle motor
control circuit -
short to ground,
power, high
resistance Carry out any pinpoint tests associated with this DTC using the
manufacturer approved diagnostic system. Refer to the electrical
circuit diagrams and check throttle motor control circuit for short to
ground, power, high resistance P211900 Throttle Actuator
Control Throttle Body
Range/Performance
Throttle spring
faulty Carry out any pinpoint tests associated with this DTC using the
manufacturer approved diagnostic system. Suspect throttle body
faulty. Check and install a new throttle body as required, refer to
the new module/component installation note at top of DTC Index P212200 Throttle/Pedal
Position Sensor/Switch
D Circuit Low
APP sensor circuit 2
- low input Carry out any pinpoint tests associated with this DTC using the
manufacturer approved diagnostic system. Refer to the electrical
circuit diagrams and check APP sensor circuit 2 for short to ground, open circuit P212216 Throttle/Pedal
Position Sensor/Switch
D Circuit Low Input
Accelerator pedal
position (APP)
sensor circuit 1 -
short to ground,
power
Accelerator pedal
position (APP)
sensor failure Carry out any pinpoint tests associated with this DTC using the
manufacturer approved diagnostic system. Refer to electrical circuit
diagrams and check accelerator pedal position (APP) sensor circuit 1
for short to ground, power. Set ignition status to 'ON' engine 'OFF'
check and record 'Pedal value sensor 1' datalogger signal. With
pedal in idle position, value of signal should be approximately 0%,
if not suspect the pedal position sensor, check and install a new
sensor as required P212300 Throttle/Pedal
Position Sensor/Switch
D Circuit High
APP sensor circuit 2
- high input Carry out any pinpoint tests associated with this DTC using the
manufacturer approved diagnostic system. Refer to the electrical
circuit diagrams and check APP sensor circuit 2 for short to power P212317 Throttle/Pedal
Position Sensor/Switch
D Circuit High Input
Accelerator pedal
position (APP)
sensor circuit 1 -
short to power
Accelerator pedal
position (APP)
sensor failure Carry out any pinpoint tests associated with this DTC using the
manufacturer approved diagnostic system. Refer to electrical circuit
diagrams and check accelerator pedal position (APP) sensor circuit 1
for short to ground, power. Set ignition status to 'ON' engine 'OFF'
check and record 'Pedal value sensor 1' datalogger signal. With
pedal in fully depressed position, value of signal should be
approximately 99%, if not suspect the pedal position sensor, check
and install a new sensor as required P212716 Throttle/Pedal
Position Sensor/Switch
E Circuit Low Input
Accelerator pedal
position (APP)
sensor circuit 2 -
short to ground,
high resistance
Accelerator pedal
position (APP)
sensor failure Carry out any pinpoint tests associated with this DTC using the
manufacturer approved diagnostic system. Refer to electrical circuit
diagrams and check accelerator pedal position (APP) sensor circuit 2
for short to ground, power. Set ignition status to 'ON' engine 'OFF'
check and record 'Pedal value sensor 2' datalogger signal. With
pedal in idle position, value of signal should be approximately 0%,
if not suspect the pedal position sensor, check and install a new
sensor as required P212817 Throttle/Pedal
Position Sensor/Switch
E Circuit High Input
Accelerator pedal
position (APP)
sensor circuit 2 -
short to power
Accelerator pedal
position (APP)
sensor failure Carry out any pinpoint tests associated with this DTC using the
manufacturer approved diagnostic system. Refer to electrical circuit
diagrams and check accelerator pedal position (APP) sensor circuit 2
for short to ground, power. Set ignition status to 'ON' engine 'OFF'
check and record 'Pedal value sensor 2' datalogger signal. With
pedal in fully depressed position, value of signal should be
approximately 99%, if not suspect the pedal position sensor, check
and install a new sensor as required P213528 Throttle/Pedal
Position Sensor/Switch
A/B Voltage
Correlation
APP sensor circuit 1
and 2 range
performance -
sub-processor Carry out any pinpoint tests associated with this DTC using the
manufacturer approved diagnostic system. Refer to the electrical
circuit diagrams and check APP sensor circuits 1 and 2 for short to
ground, power and high resistance. Clear the DTCs and retest. If
the code remains, replace the APP sensor P213529 Throttle/Pedal
Position Sensor/Switch
A/B Voltage
Correlation
APP sensor -
excessive difference
between
raw values of circuit
1 and 2 -
sub-processor Carry out any pinpoint tests associated with this DTC using the
manufacturer approved diagnostic system. Refer to the electrical
circuit diagrams and check APP sensor circuits 1 and 2 for short,
open circuit
Page 1636 of 3039
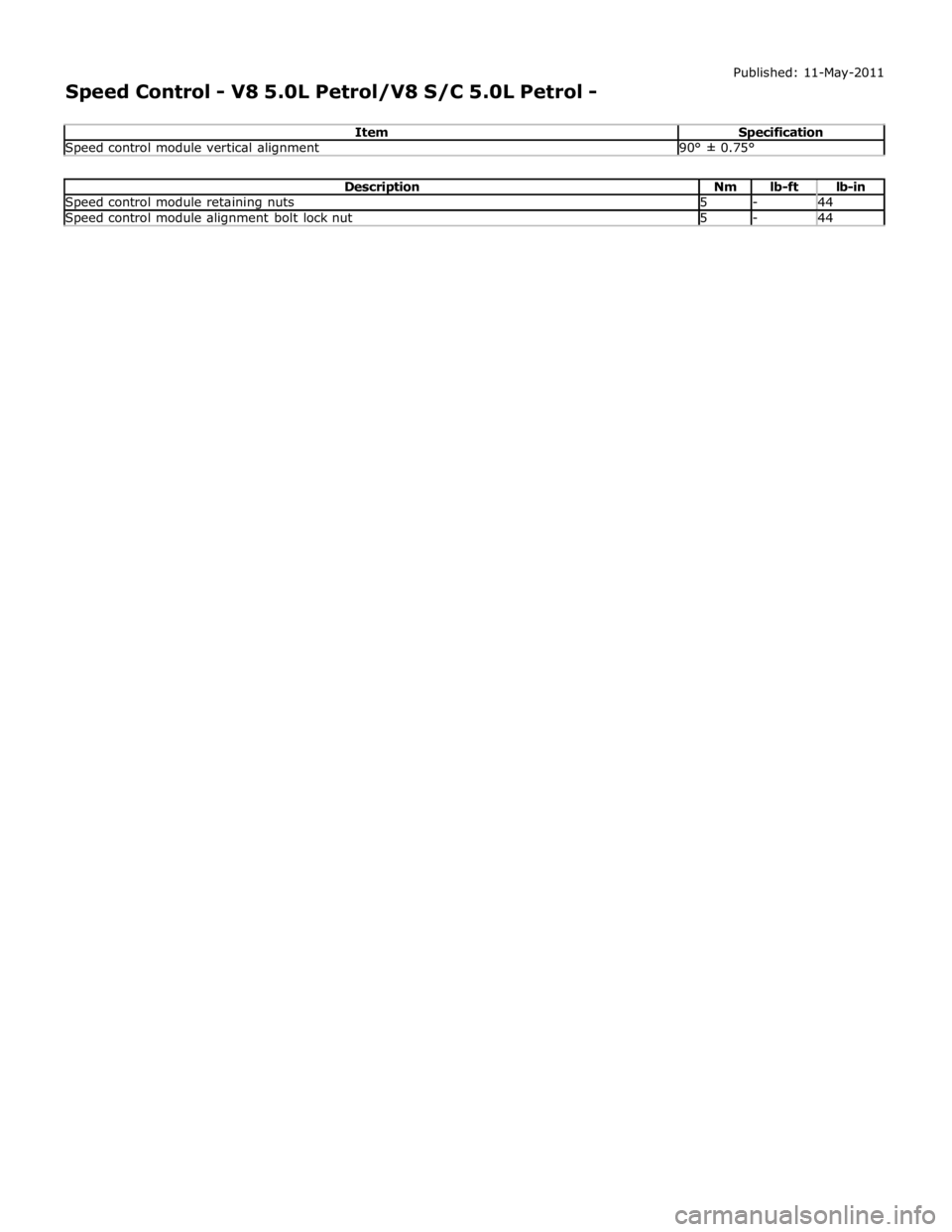
Speed control module vertical alignment 90° ± 0.75°
Description Nm lb-ft lb-in Speed control module retaining nuts 5 - 44 Speed control module alignment bolt lock nut 5 - 44
Page 1637 of 3039
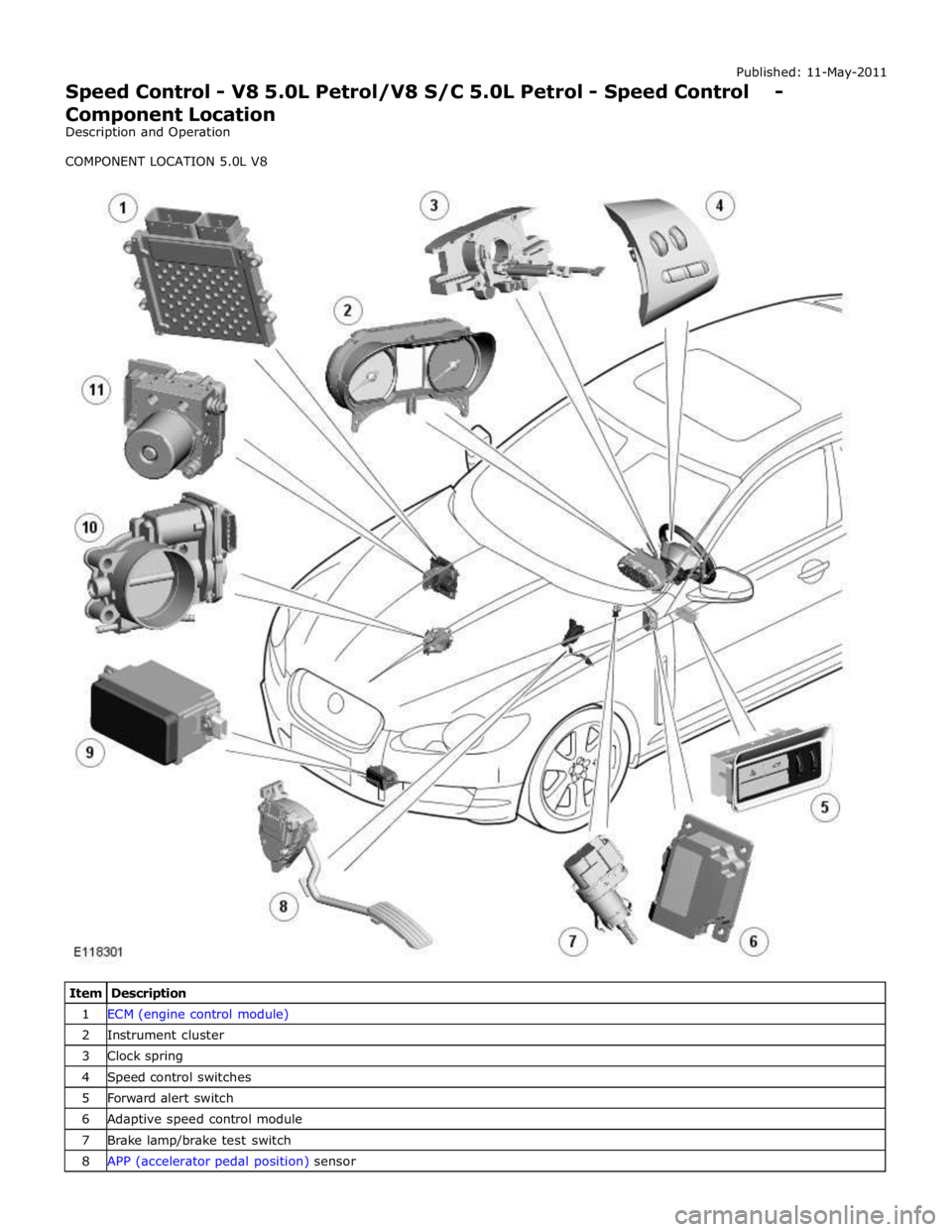
1 ECM (engine control module) 2 Instrument cluster 3 Clock spring 4 Speed control switches 5 Forward alert switch 6 Adaptive speed control module 7 Brake lamp/brake test switch 8 APP (accelerator pedal position) sensor