Electric Parking Brake JAGUAR XFR 2010 1.G Workshop Manual
[x] Cancel search | Manufacturer: JAGUAR, Model Year: 2010, Model line: XFR, Model: JAGUAR XFR 2010 1.GPages: 3039, PDF Size: 58.49 MB
Page 2 of 3039
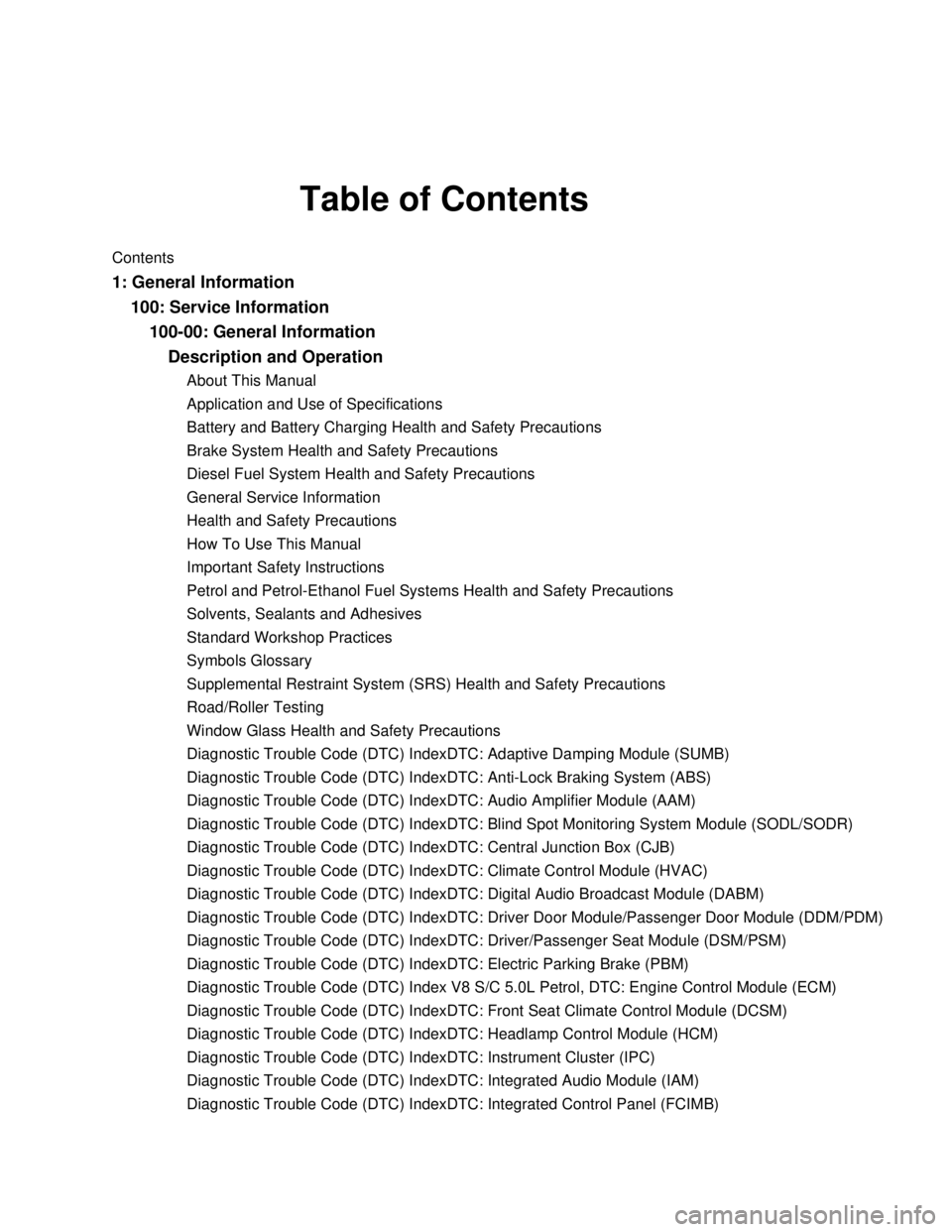
Table of ContentsContents1: General Information
100: Service Information
100-00: General Information
Description and OperationAbout This Manual
Application and Use of Specifications
Battery and Battery Charging Health and Safety Precautions
Brake System Health and Safety Precautions
Diesel Fuel System Health and Safety Precautions
General Service Information
Health and Safety Precautions
How To Use This Manual
Important Safety Instructions
Petrol and Petrol-Ethanol Fuel Systems Health and Safety Precautions
Solvents, Sealants and Adhesives
Standard Workshop Practices
Symbols Glossary
Supplemental Restraint System (SRS) Health and Safety Precautions
Road/Roller Testing
Window Glass Health and Safety Precautions
Diagnostic Trouble Code (DTC) IndexDTC: Adaptive Damping Module (SUMB)
Diagnostic Trouble Code (DTC) IndexDTC: Anti-Lock Braking System (ABS)
Diagnostic Trouble Code (DTC) IndexDTC: Audio Amplifier Module (AAM)
Diagnostic Trouble Code (DTC) IndexDTC: Blind Spot Monitoring System Module (SODL/SODR)
Diagnostic Trouble Code (DTC) IndexDTC: Central Junction Box (CJB)
Diagnostic Trouble Code (DTC) IndexDTC: Climate Control Module (HVAC)
Diagnostic Trouble Code (DTC) IndexDTC: Digital Audio Broadcast Module (DABM)
Diagnostic Trouble Code (DTC) IndexDTC: Driver Door Module/Passenger Door Module (DDM/PDM)
Diagnostic Trouble Code (DTC) IndexDTC: Driver/Passenger Seat Module (DSM/PSM)
Diagnostic Trouble Code (DTC) IndexDTC: Electric Parking Brake (PBM)
Diagnostic Trouble Code (DTC) Index V8 S/C 5.0L Petrol, DTC: Engine Control Module (ECM)
Diagnostic Trouble Code (DTC) IndexDTC: Front Seat Climate Control Module (DCSM)
Diagnostic Trouble Code (DTC) IndexDTC: Headlamp Control Module (HCM)
Diagnostic Trouble Code (DTC) IndexDTC: Instrument Cluster (IPC)
Diagnostic Trouble Code (DTC) IndexDTC: Integrated Audio Module (IAM)
Diagnostic Trouble Code (DTC) IndexDTC: Integrated Control Panel (FCIMB)
Page 67 of 3039
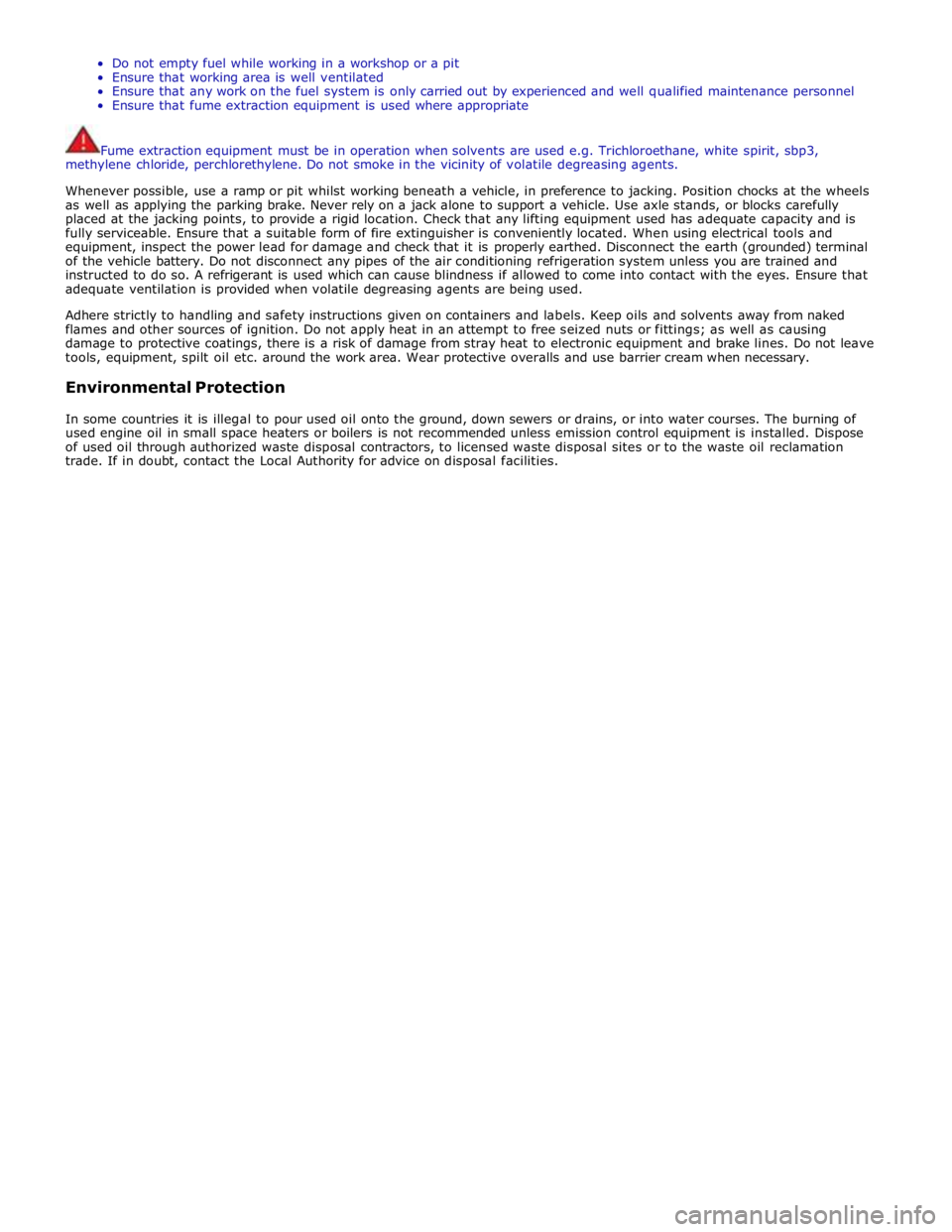
Do not empty fuel while working in a workshop or a pit
Ensure that working area is well ventilated
Ensure that any work on the fuel system is only carried out by experienced and well qualified maintenance personnel
Ensure that fume extraction equipment is used where appropriate
Fume extraction equipment must be in operation when solvents are used e.g. Trichloroethane, white spirit, sbp3,
methylene chloride, perchlorethylene. Do not smoke in the vicinity of volatile degreasing agents.
Whenever possible, use a ramp or pit whilst working beneath a vehicle, in preference to jacking. Position chocks at the wheels
as well as applying the parking brake. Never rely on a jack alone to support a vehicle. Use axle stands, or blocks carefully
placed at the jacking points, to provide a rigid location. Check that any lifting equipment used has adequate capacity and is
fully serviceable. Ensure that a suitable form of fire extinguisher is conveniently located. When using electrical tools and
equipment, inspect the power lead for damage and check that it is properly earthed. Disconnect the earth (grounded) terminal
of the vehicle battery. Do not disconnect any pipes of the air conditioning refrigeration system unless you are trained and
instructed to do so. A refrigerant is used which can cause blindness if allowed to come into contact with the eyes. Ensure that
adequate ventilation is provided when volatile degreasing agents are being used.
Adhere strictly to handling and safety instructions given on containers and labels. Keep oils and solvents away from naked
flames and other sources of ignition. Do not apply heat in an attempt to free seized nuts or fittings; as well as causing
damage to protective coatings, there is a risk of damage from stray heat to electronic equipment and brake lines. Do not leave
tools, equipment, spilt oil etc. around the work area. Wear protective overalls and use barrier cream when necessary.
Environmental Protection
In some countries it is illegal to pour used oil onto the ground, down sewers or drains, or into water courses. The burning of
used engine oil in small space heaters or boilers is not recommended unless emission control equipment is installed. Dispose
of used oil through authorized waste disposal contractors, to licensed waste disposal sites or to the waste oil reclamation
trade. If in doubt, contact the Local Authority for advice on disposal facilities.
Page 72 of 3039
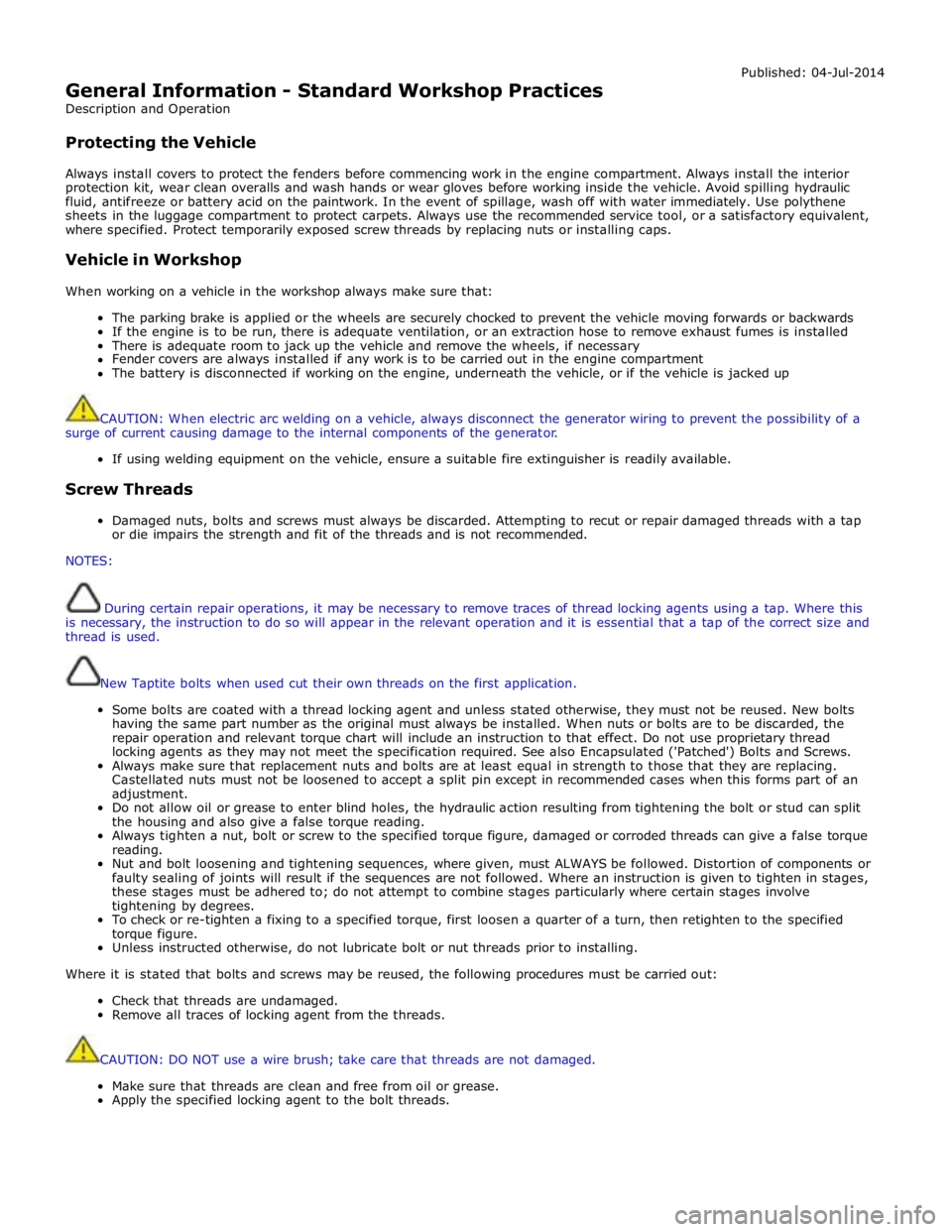
General Information - Standard Workshop Practices
Description and Operation
Protecting the Vehicle Published: 04-Jul-2014
Always install covers to protect the fenders before commencing work in the engine compartment. Always install the interior
protection kit, wear clean overalls and wash hands or wear gloves before working inside the vehicle. Avoid spilling hydraulic
fluid, antifreeze or battery acid on the paintwork. In the event of spillage, wash off with water immediately. Use polythene
sheets in the luggage compartment to protect carpets. Always use the recommended service tool, or a satisfactory equivalent,
where specified. Protect temporarily exposed screw threads by replacing nuts or installing caps.
Vehicle in Workshop
When working on a vehicle in the workshop always make sure that:
The parking brake is applied or the wheels are securely chocked to prevent the vehicle moving forwards or backwards
If the engine is to be run, there is adequate ventilation, or an extraction hose to remove exhaust fumes is installed
There is adequate room to jack up the vehicle and remove the wheels, if necessary
Fender covers are always installed if any work is to be carried out in the engine compartment
The battery is disconnected if working on the engine, underneath the vehicle, or if the vehicle is jacked up
CAUTION: When electric arc welding on a vehicle, always disconnect the generator wiring to prevent the possibility of a
surge of current causing damage to the internal components of the generator.
If using welding equipment on the vehicle, ensure a suitable fire extinguisher is readily available.
Screw Threads
Damaged nuts, bolts and screws must always be discarded. Attempting to recut or repair damaged threads with a tap
or die impairs the strength and fit of the threads and is not recommended.
NOTES:
During certain repair operations, it may be necessary to remove traces of thread locking agents using a tap. Where this
is necessary, the instruction to do so will appear in the relevant operation and it is essential that a tap of the correct size and
thread is used.
New Taptite bolts when used cut their own threads on the first application.
Some bolts are coated with a thread locking agent and unless stated otherwise, they must not be reused. New bolts
having the same part number as the original must always be installed. When nuts or bolts are to be discarded, the
repair operation and relevant torque chart will include an instruction to that effect. Do not use proprietary thread
locking agents as they may not meet the specification required. See also Encapsulated ('Patched') Bolts and Screws.
Always make sure that replacement nuts and bolts are at least equal in strength to those that they are replacing.
Castellated nuts must not be loosened to accept a split pin except in recommended cases when this forms part of an
adjustment.
Do not allow oil or grease to enter blind holes, the hydraulic action resulting from tightening the bolt or stud can split
the housing and also give a false torque reading.
Always tighten a nut, bolt or screw to the specified torque figure, damaged or corroded threads can give a false torque
reading.
Nut and bolt loosening and tightening sequences, where given, must ALWAYS be followed. Distortion of components or
faulty sealing of joints will result if the sequences are not followed. Where an instruction is given to tighten in stages,
these stages must be adhered to; do not attempt to combine stages particularly where certain stages involve
tightening by degrees.
To check or re-tighten a fixing to a specified torque, first loosen a quarter of a turn, then retighten to the specified
torque figure.
Unless instructed otherwise, do not lubricate bolt or nut threads prior to installing.
Where it is stated that bolts and screws may be reused, the following procedures must be carried out:
Check that threads are undamaged.
Remove all traces of locking agent from the threads.
CAUTION: DO NOT use a wire brush; take care that threads are not damaged.
Make sure that threads are clean and free from oil or grease.
Apply the specified locking agent to the bolt threads.
Page 158 of 3039
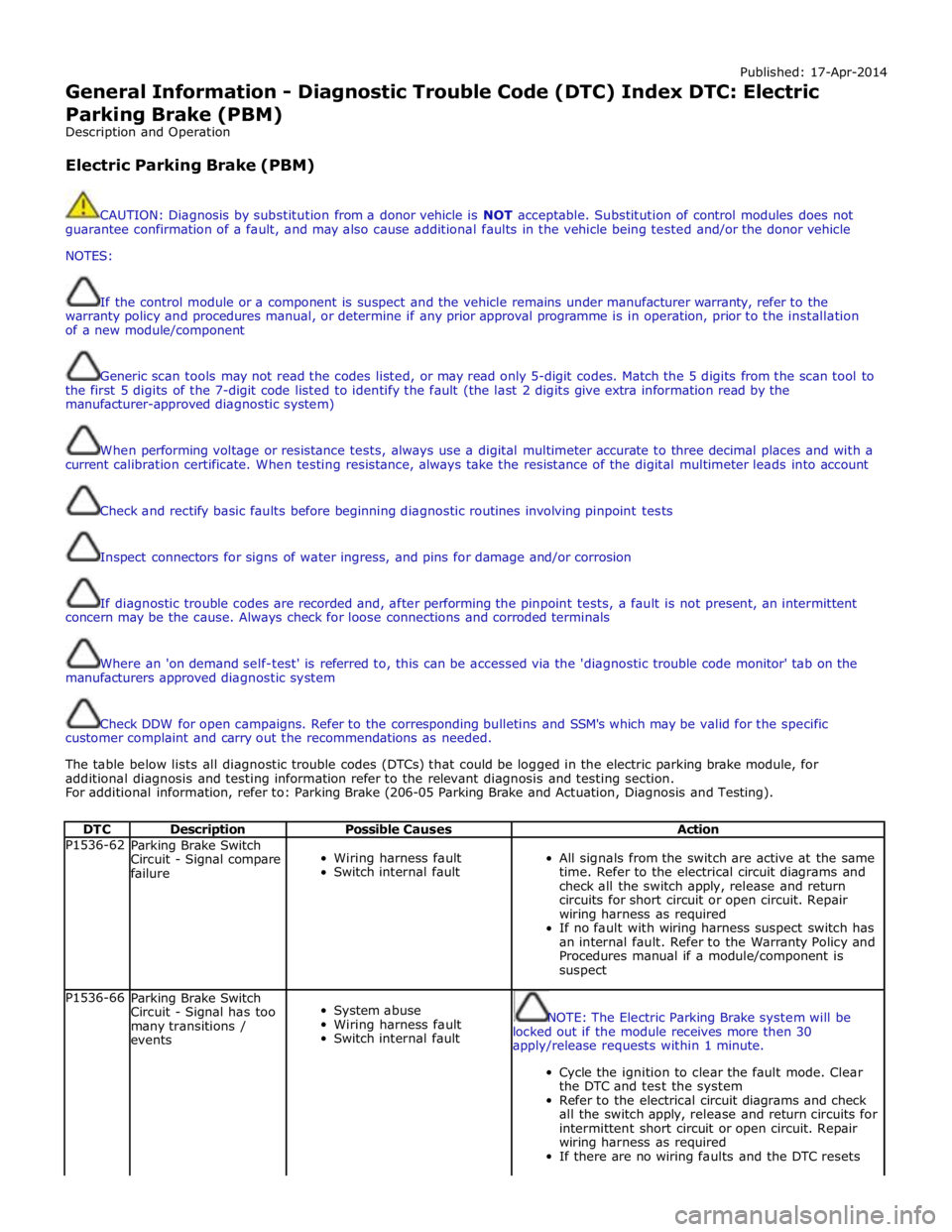
Published: 17-Apr-2014
General Information - Diagnostic Trouble Code (DTC) Index DTC: Electric
Parking Brake (PBM)
Description and Operation
Electric Parking Brake (PBM)
CAUTION: Diagnosis by substitution from a donor vehicle is NOT acceptable. Substitution of control modules does not
guarantee confirmation of a fault, and may also cause additional faults in the vehicle being tested and/or the donor vehicle
NOTES:
If the control module or a component is suspect and the vehicle remains under manufacturer warranty, refer to the
warranty policy and procedures manual, or determine if any prior approval programme is in operation, prior to the installation
of a new module/component
Generic scan tools may not read the codes listed, or may read only 5-digit codes. Match the 5 digits from the scan tool to
the first 5 digits of the 7-digit code listed to identify the fault (the last 2 digits give extra information read by the
manufacturer-approved diagnostic system)
When performing voltage or resistance tests, always use a digital multimeter accurate to three decimal places and with a
current calibration certificate. When testing resistance, always take the resistance of the digital multimeter leads into account
Check and rectify basic faults before beginning diagnostic routines involving pinpoint tests
Inspect connectors for signs of water ingress, and pins for damage and/or corrosion
If diagnostic trouble codes are recorded and, after performing the pinpoint tests, a fault is not present, an intermittent
concern may be the cause. Always check for loose connections and corroded terminals
Where an 'on demand self-test' is referred to, this can be accessed via the 'diagnostic trouble code monitor' tab on the
manufacturers approved diagnostic system
Check DDW for open campaigns. Refer to the corresponding bulletins and SSM's which may be valid for the specific
customer complaint and carry out the recommendations as needed.
The table below lists all diagnostic trouble codes (DTCs) that could be logged in the electric parking brake module, for
additional diagnosis and testing information refer to the relevant diagnosis and testing section.
For additional information, refer to: Parking Brake (206-05 Parking Brake and Actuation, Diagnosis and Testing).
DTC Description Possible Causes Action P1536-62
Parking Brake Switch
Circuit - Signal compare
failure
Wiring harness fault
Switch internal fault
All signals from the switch are active at the same
time. Refer to the electrical circuit diagrams and
check all the switch apply, release and return
circuits for short circuit or open circuit. Repair
wiring harness as required
If no fault with wiring harness suspect switch has
an internal fault. Refer to the Warranty Policy and
Procedures manual if a module/component is
suspect P1536-66
Parking Brake Switch
Circuit - Signal has too
many transitions /
events
System abuse
Wiring harness fault
Switch internal fault
NOTE: The Electric Parking Brake system will be
locked out if the module receives more then 30
apply/release requests within 1 minute.
Cycle the ignition to clear the fault mode. Clear
the DTC and test the system
Refer to the electrical circuit diagrams and check
all the switch apply, release and return circuits for
intermittent short circuit or open circuit. Repair
wiring harness as required
If there are no wiring faults and the DTC resets
Page 159 of 3039
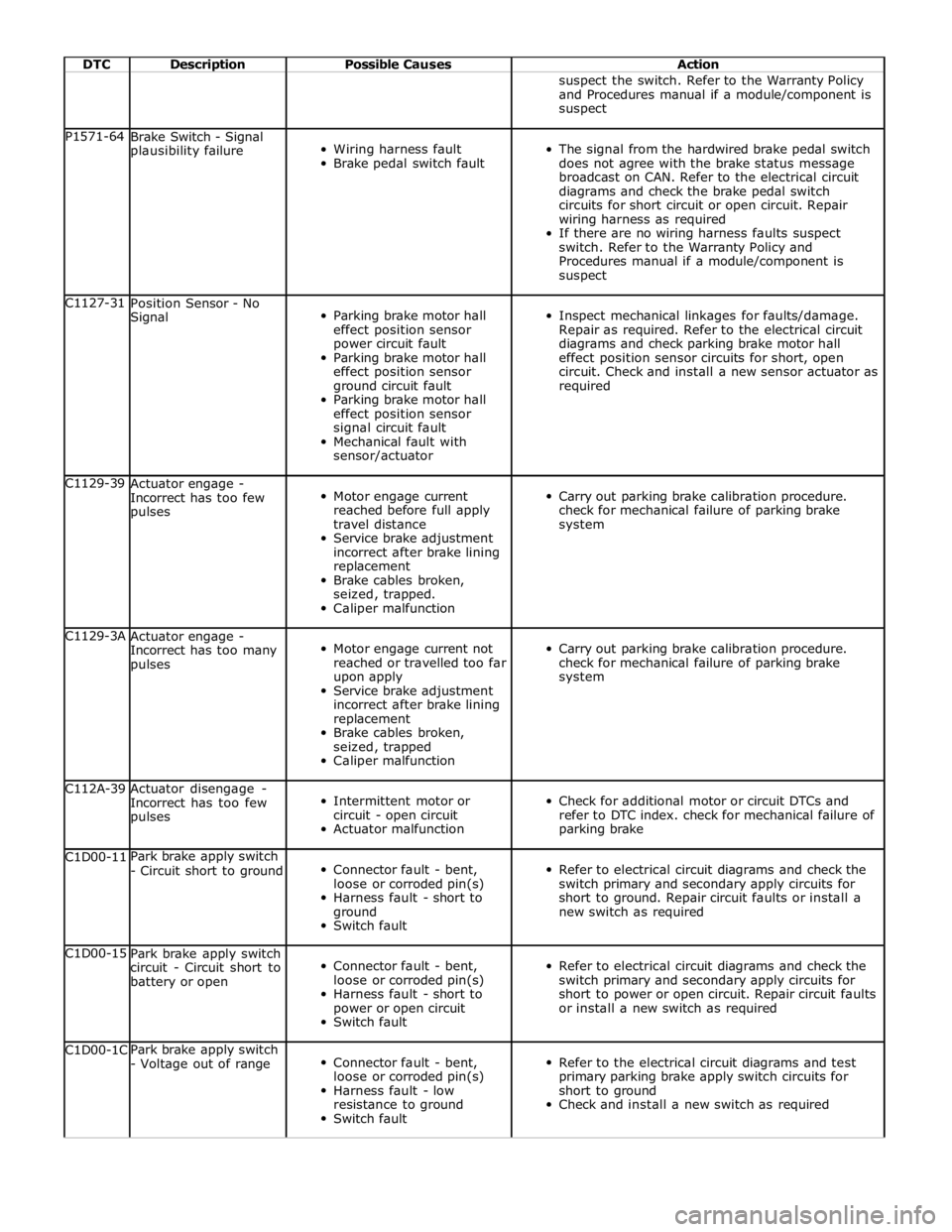
DTC Description Possible Causes Action suspect the switch. Refer to the Warranty Policy
and Procedures manual if a module/component is
suspect P1571-64
Brake Switch - Signal
plausibility failure
Wiring harness fault
Brake pedal switch fault
The signal from the hardwired brake pedal switch
does not agree with the brake status message
broadcast on CAN. Refer to the electrical circuit
diagrams and check the brake pedal switch
circuits for short circuit or open circuit. Repair
wiring harness as required
If there are no wiring harness faults suspect
switch. Refer to the Warranty Policy and
Procedures manual if a module/component is
suspect C1127-31
Position Sensor - No
Signal
Parking brake motor hall
effect position sensor
power circuit fault
Parking brake motor hall
effect position sensor
ground circuit fault
Parking brake motor hall
effect position sensor
signal circuit fault
Mechanical fault with
sensor/actuator
Inspect mechanical linkages for faults/damage.
Repair as required. Refer to the electrical circuit
diagrams and check parking brake motor hall
effect position sensor circuits for short, open
circuit. Check and install a new sensor actuator as
required C1129-39
Actuator engage -
Incorrect has too few
pulses
Motor engage current
reached before full apply
travel distance
Service brake adjustment
incorrect after brake lining
replacement
Brake cables broken,
seized, trapped.
Caliper malfunction
Carry out parking brake calibration procedure.
check for mechanical failure of parking brake
system C1129-3A
Actuator engage -
Incorrect has too many
pulses
Motor engage current not
reached or travelled too far
upon apply
Service brake adjustment
incorrect after brake lining
replacement
Brake cables broken,
seized, trapped
Caliper malfunction
Carry out parking brake calibration procedure.
check for mechanical failure of parking brake
system C112A-39
Actuator disengage -
Incorrect has too few
pulses
Intermittent motor or
circuit - open circuit
Actuator malfunction
Check for additional motor or circuit DTCs and
refer to DTC index. check for mechanical failure of
parking brake C1D00-11 Park brake apply switch
- Circuit short to ground
Connector fault - bent,
loose or corroded pin(s)
Harness fault - short to
ground
Switch fault
Refer to electrical circuit diagrams and check the
switch primary and secondary apply circuits for
short to ground. Repair circuit faults or install a
new switch as required C1D00-15
Park brake apply switch
circuit - Circuit short to
battery or open
Connector fault - bent,
loose or corroded pin(s)
Harness fault - short to
power or open circuit
Switch fault
Refer to electrical circuit diagrams and check the
switch primary and secondary apply circuits for
short to power or open circuit. Repair circuit faults
or install a new switch as required C1D00-1C Park brake apply switch
- Voltage out of range
Connector fault - bent,
loose or corroded pin(s)
Harness fault - low
resistance to ground
Switch fault
Refer to the electrical circuit diagrams and test
primary parking brake apply switch circuits for
short to ground
Check and install a new switch as required
Page 160 of 3039
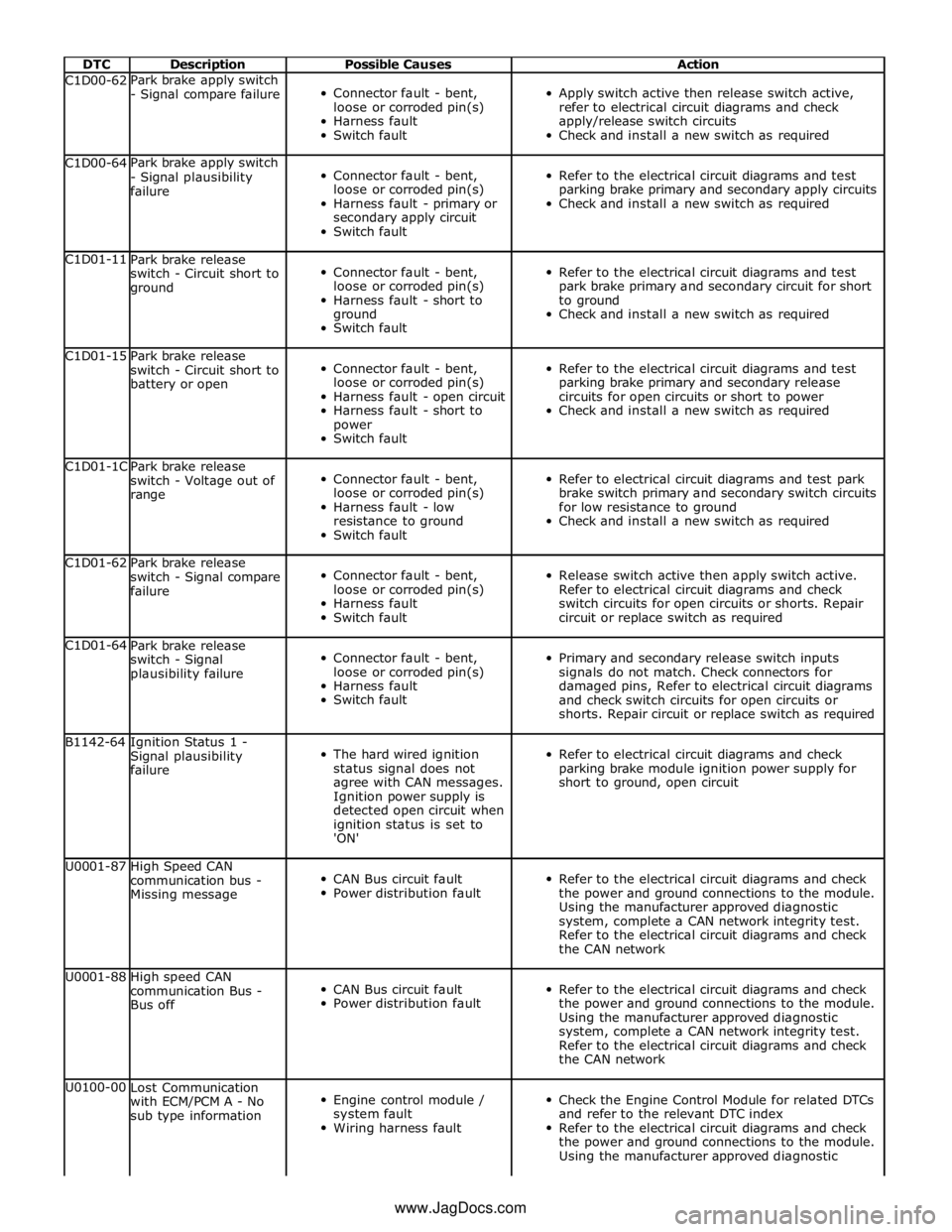
DTC Description Possible Causes Action C1D00-62 Park brake apply switch
- Signal compare failure
Connector fault - bent,
loose or corroded pin(s)
Harness fault
Switch fault
Apply switch active then release switch active,
refer to electrical circuit diagrams and check
apply/release switch circuits
Check and install a new switch as required C1D00-64 Park brake apply switch
- Signal plausibility
failure
Connector fault - bent,
loose or corroded pin(s)
Harness fault - primary or
secondary apply circuit
Switch fault
Refer to the electrical circuit diagrams and test
parking brake primary and secondary apply circuits
Check and install a new switch as required C1D01-11
Park brake release
switch - Circuit short to
ground
Connector fault - bent,
loose or corroded pin(s)
Harness fault - short to
ground
Switch fault
Refer to the electrical circuit diagrams and test
park brake primary and secondary circuit for short
to ground
Check and install a new switch as required C1D01-15
Park brake release
switch - Circuit short to
battery or open
Connector fault - bent,
loose or corroded pin(s)
Harness fault - open circuit
Harness fault - short to
power
Switch fault
Refer to the electrical circuit diagrams and test
parking brake primary and secondary release
circuits for open circuits or short to power
Check and install a new switch as required C1D01-1C
Park brake release
switch - Voltage out of
range
Connector fault - bent,
loose or corroded pin(s)
Harness fault - low
resistance to ground
Switch fault
Refer to electrical circuit diagrams and test park
brake switch primary and secondary switch circuits
for low resistance to ground
Check and install a new switch as required C1D01-62
Park brake release
switch - Signal compare
failure
Connector fault - bent,
loose or corroded pin(s)
Harness fault
Switch fault
Release switch active then apply switch active.
Refer to electrical circuit diagrams and check
switch circuits for open circuits or shorts. Repair
circuit or replace switch as required C1D01-64
Park brake release
switch - Signal
plausibility failure
Connector fault - bent,
loose or corroded pin(s)
Harness fault
Switch fault
Primary and secondary release switch inputs
signals do not match. Check connectors for
damaged pins, Refer to electrical circuit diagrams
and check switch circuits for open circuits or
shorts. Repair circuit or replace switch as required B1142-64
Ignition Status 1 -
Signal plausibility
failure
The hard wired ignition
status signal does not
agree with CAN messages.
Ignition power supply is
detected open circuit when
ignition status is set to
'ON'
Refer to electrical circuit diagrams and check
parking brake module ignition power supply for
short to ground, open circuit U0001-87
High Speed CAN
communication bus -
Missing message
CAN Bus circuit fault
Power distribution fault
Refer to the electrical circuit diagrams and check
the power and ground connections to the module.
Using the manufacturer approved diagnostic
system, complete a CAN network integrity test.
Refer to the electrical circuit diagrams and check
the CAN network U0001-88
High speed CAN
communication Bus -
Bus off
CAN Bus circuit fault
Power distribution fault
Refer to the electrical circuit diagrams and check
the power and ground connections to the module.
Using the manufacturer approved diagnostic
system, complete a CAN network integrity test.
Refer to the electrical circuit diagrams and check
the CAN network U0100-00
Lost Communication
with ECM/PCM A - No
sub type information
Engine control module /
system fault
Wiring harness fault
Check the Engine Control Module for related DTCs
and refer to the relevant DTC index
Refer to the electrical circuit diagrams and check
the power and ground connections to the module.
Using the manufacturer approved diagnostic www.JagDocs.com
Page 162 of 3039
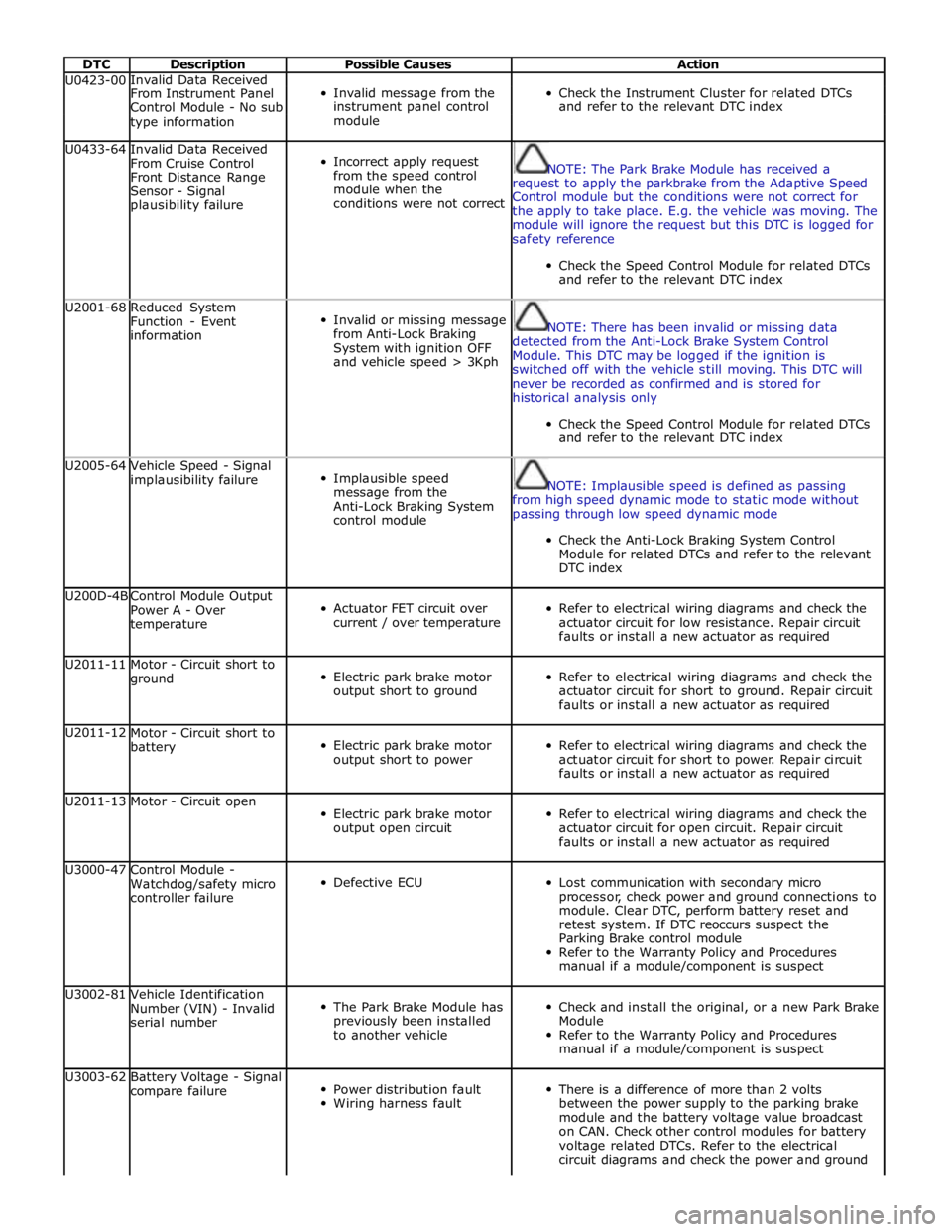
DTC Description Possible Causes Action U0423-00 Invalid Data Received
Invalid message from the
Check the Instrument Cluster for related DTCs From Instrument Panel Control Module - No sub instrument panel control and refer to the relevant DTC index type information module U0433-64
Invalid Data Received
From Cruise Control
Front Distance Range
Sensor - Signal
plausibility failure
Incorrect apply request
from the speed control
module when the
conditions were not correct
NOTE: The Park Brake Module has received a
request to apply the parkbrake from the Adaptive Speed
Control module but the conditions were not correct for
the apply to take place. E.g. the vehicle was moving. The
module will ignore the request but this DTC is logged for
safety reference
Check the Speed Control Module for related DTCs
and refer to the relevant DTC index U2001-68
Reduced System
Function - Event
information
Invalid or missing message
from Anti-Lock Braking
System with ignition OFF
and vehicle speed > 3Kph
NOTE: There has been invalid or missing data
detected from the Anti-Lock Brake System Control
Module. This DTC may be logged if the ignition is
switched off with the vehicle still moving. This DTC will
never be recorded as confirmed and is stored for
historical analysis only
Check the Speed Control Module for related DTCs
and refer to the relevant DTC index U2005-64
Vehicle Speed - Signal
implausibility failure
Implausible speed
message from the
Anti-Lock Braking System
control module
NOTE: Implausible speed is defined as passing
from high speed dynamic mode to static mode without
passing through low speed dynamic mode
Check the Anti-Lock Braking System Control
Module for related DTCs and refer to the relevant
DTC index U200D-4B
Control Module Output
Power A - Over
temperature
Actuator FET circuit over
current / over temperature
Refer to electrical wiring diagrams and check the
actuator circuit for low resistance. Repair circuit
faults or install a new actuator as required U2011-11
Motor - Circuit short to
ground
Electric park brake motor
output short to ground
Refer to electrical wiring diagrams and check the
actuator circuit for short to ground. Repair circuit
faults or install a new actuator as required U2011-12
Motor - Circuit short to
battery
Electric park brake motor
output short to power
Refer to electrical wiring diagrams and check the
actuator circuit for short to power. Repair circuit
faults or install a new actuator as required U2011-13 Motor - Circuit open
Electric park brake motor
output open circuit
Refer to electrical wiring diagrams and check the
actuator circuit for open circuit. Repair circuit
faults or install a new actuator as required U3000-47
Control Module -
Watchdog/safety micro
controller failure
Defective ECU
Lost communication with secondary micro
processor, check power and ground connections to
module. Clear DTC, perform battery reset and
retest system. If DTC reoccurs suspect the
Parking Brake control module
Refer to the Warranty Policy and Procedures
manual if a module/component is suspect U3002-81
Vehicle Identification
Number (VIN) - Invalid
serial number
The Park Brake Module has
previously been installed
to another vehicle
Check and install the original, or a new Park Brake
Module
Refer to the Warranty Policy and Procedures
manual if a module/component is suspect U3003-62
Battery Voltage - Signal
compare failure
Power distribution fault
Wiring harness fault
There is a difference of more than 2 volts
between the power supply to the parking brake
module and the battery voltage value broadcast
on CAN. Check other control modules for battery
voltage related DTCs. Refer to the electrical
circuit diagrams and check the power and ground
Page 239 of 3039
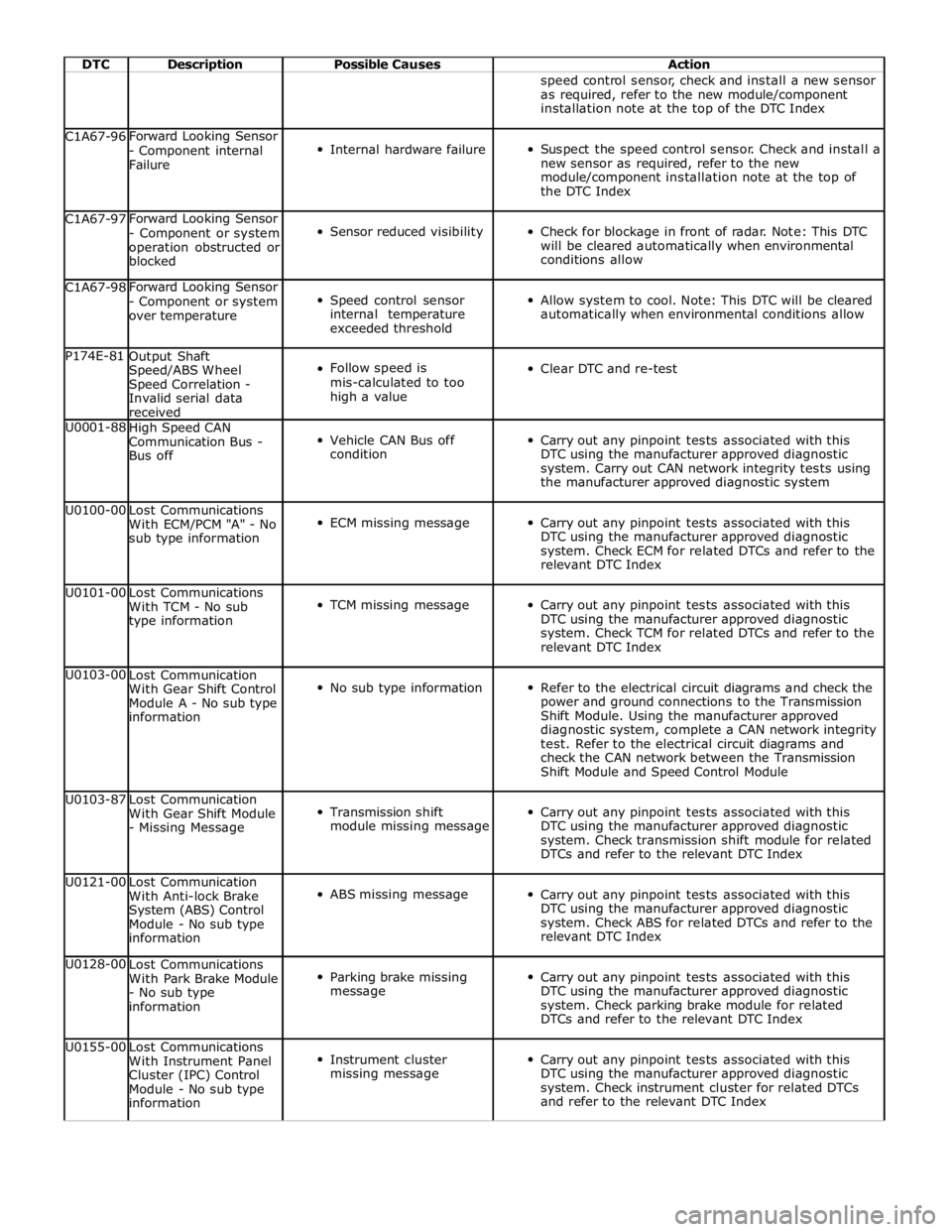
DTC Description Possible Causes Action speed control sensor, check and install a new sensor
as required, refer to the new module/component
installation note at the top of the DTC Index C1A67-96 Forward Looking Sensor
- Component internal
Failure
Internal hardware failure
Suspect the speed control sensor. Check and install a
new sensor as required, refer to the new
module/component installation note at the top of
the DTC Index C1A67-97 Forward Looking Sensor
- Component or system
operation obstructed or
blocked
Sensor reduced visibility
Check for blockage in front of radar. Note: This DTC
will be cleared automatically when environmental
conditions allow C1A67-98 Forward Looking Sensor
- Component or system
over temperature
Speed control sensor
internal temperature
exceeded threshold
Allow system to cool. Note: This DTC will be cleared
automatically when environmental conditions allow P174E-81
Output Shaft
Speed/ABS Wheel
Speed Correlation -
Invalid serial data
received
Follow speed is
mis-calculated to too
high a value
Clear DTC and re-test U0001-88
High Speed CAN
Communication Bus -
Bus off
Vehicle CAN Bus off
condition
Carry out any pinpoint tests associated with this
DTC using the manufacturer approved diagnostic
system. Carry out CAN network integrity tests using
the manufacturer approved diagnostic system U0100-00
Lost Communications
With ECM/PCM "A" - No
sub type information
ECM missing message
Carry out any pinpoint tests associated with this
DTC using the manufacturer approved diagnostic
system. Check ECM for related DTCs and refer to the
relevant DTC Index U0101-00
Lost Communications
With TCM - No sub
type information
TCM missing message
Carry out any pinpoint tests associated with this
DTC using the manufacturer approved diagnostic
system. Check TCM for related DTCs and refer to the
relevant DTC Index U0103-00
Lost Communication
With Gear Shift Control
Module A - No sub type
information
No sub type information
Refer to the electrical circuit diagrams and check the
power and ground connections to the Transmission
Shift Module. Using the manufacturer approved
diagnostic system, complete a CAN network integrity
test. Refer to the electrical circuit diagrams and
check the CAN network between the Transmission
Shift Module and Speed Control Module U0103-87
Lost Communication
With Gear Shift Module
- Missing Message
Transmission shift
module missing message
Carry out any pinpoint tests associated with this
DTC using the manufacturer approved diagnostic
system. Check transmission shift module for related
DTCs and refer to the relevant DTC Index U0121-00
Lost Communication
With Anti-lock Brake
System (ABS) Control
Module - No sub type
information
ABS missing message
Carry out any pinpoint tests associated with this
DTC using the manufacturer approved diagnostic
system. Check ABS for related DTCs and refer to the
relevant DTC Index U0128-00
Lost Communications
With Park Brake Module
- No sub type
information
Parking brake missing
message
Carry out any pinpoint tests associated with this
DTC using the manufacturer approved diagnostic
system. Check parking brake module for related
DTCs and refer to the relevant DTC Index U0155-00
Lost Communications
With Instrument Panel
Cluster (IPC) Control
Module - No sub type
information
Instrument cluster
missing message
Carry out any pinpoint tests associated with this
DTC using the manufacturer approved diagnostic
system. Check instrument cluster for related DTCs
and refer to the relevant DTC Index
Page 240 of 3039
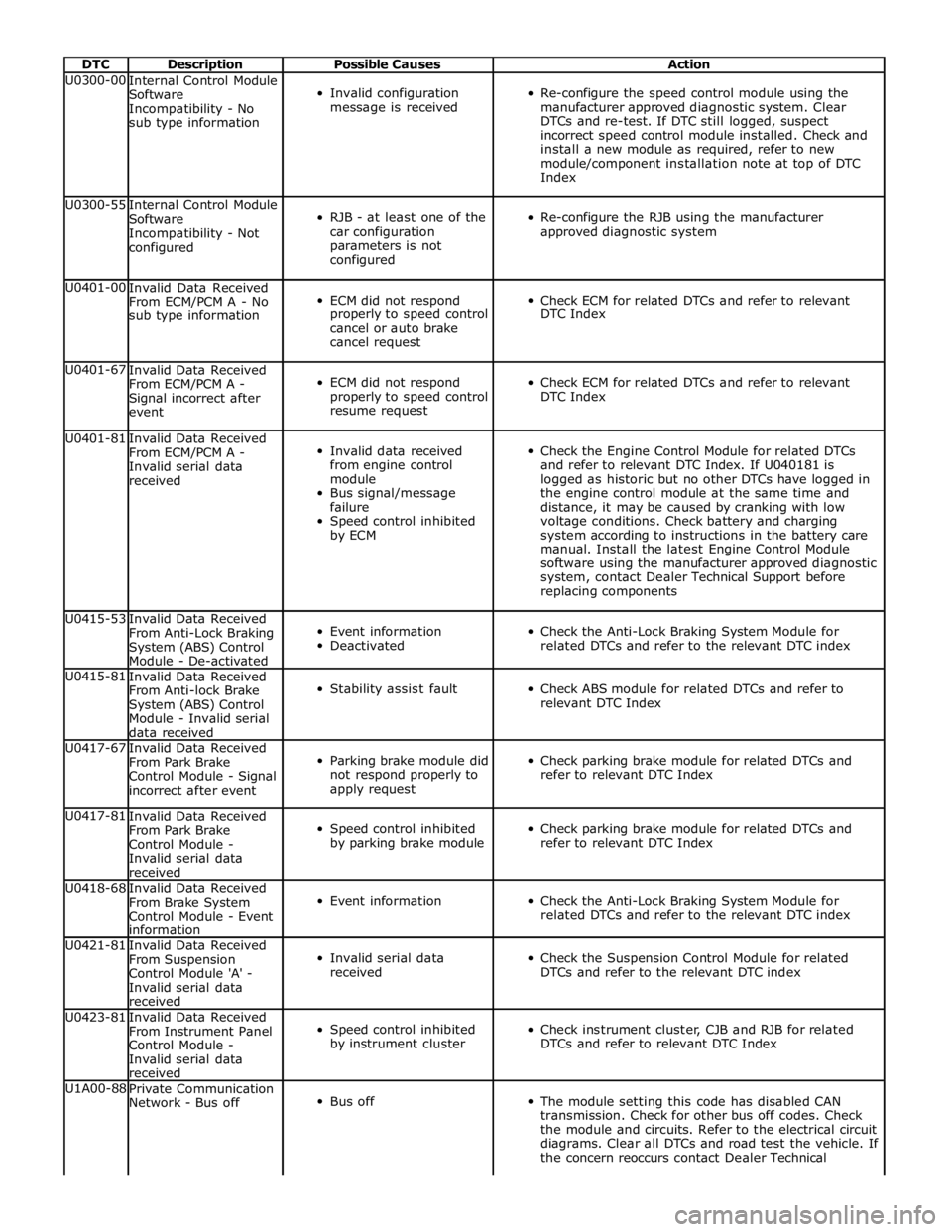
DTC Description Possible Causes Action U0300-00
Internal Control Module
Software
Incompatibility - No
sub type information
Invalid configuration
message is received
Re-configure the speed control module using the
manufacturer approved diagnostic system. Clear
DTCs and re-test. If DTC still logged, suspect
incorrect speed control module installed. Check and
install a new module as required, refer to new
module/component installation note at top of DTC
Index U0300-55
Internal Control Module
Software
Incompatibility - Not
configured
RJB - at least one of the
car configuration
parameters is not
configured
Re-configure the RJB using the manufacturer
approved diagnostic system U0401-00
Invalid Data Received
From ECM/PCM A - No
sub type information
ECM did not respond
properly to speed control
cancel or auto brake
cancel request
Check ECM for related DTCs and refer to relevant
DTC Index U0401-67
Invalid Data Received
From ECM/PCM A -
Signal incorrect after
event
ECM did not respond
properly to speed control
resume request
Check ECM for related DTCs and refer to relevant
DTC Index U0401-81
Invalid Data Received
From ECM/PCM A -
Invalid serial data
received
Invalid data received
from engine control
module
Bus signal/message
failure
Speed control inhibited
by ECM
Check the Engine Control Module for related DTCs
and refer to relevant DTC Index. If U040181 is
logged as historic but no other DTCs have logged in
the engine control module at the same time and
distance, it may be caused by cranking with low
voltage conditions. Check battery and charging
system according to instructions in the battery care
manual. Install the latest Engine Control Module
software using the manufacturer approved diagnostic
system, contact Dealer Technical Support before
replacing components U0415-53
Invalid Data Received
From Anti-Lock Braking
System (ABS) Control
Module - De-activated
Event information
Deactivated
Check the Anti-Lock Braking System Module for
related DTCs and refer to the relevant DTC index U0415-81
Invalid Data Received
From Anti-lock Brake
System (ABS) Control
Module - Invalid serial
data received
Stability assist fault
Check ABS module for related DTCs and refer to
relevant DTC Index U0417-67
Invalid Data Received
From Park Brake
Control Module - Signal
incorrect after event
Parking brake module did
not respond properly to
apply request
Check parking brake module for related DTCs and
refer to relevant DTC Index U0417-81
Invalid Data Received
From Park Brake
Control Module -
Invalid serial data
received
Speed control inhibited
by parking brake module
Check parking brake module for related DTCs and
refer to relevant DTC Index U0418-68
Invalid Data Received
From Brake System
Control Module - Event
information
Event information
Check the Anti-Lock Braking System Module for
related DTCs and refer to the relevant DTC index U0421-81
Invalid Data Received
From Suspension
Control Module 'A' -
Invalid serial data
received
Invalid serial data
received
Check the Suspension Control Module for related
DTCs and refer to the relevant DTC index U0423-81
Invalid Data Received
From Instrument Panel
Control Module -
Invalid serial data
received
Speed control inhibited
by instrument cluster
Check instrument cluster, CJB and RJB for related
DTCs and refer to relevant DTC Index U1A00-88
Private Communication
Network - Bus off
Bus off
The module setting this code has disabled CAN
transmission. Check for other bus off codes. Check
the module and circuits. Refer to the electrical circuit
diagrams. Clear all DTCs and road test the vehicle. If
the concern reoccurs contact Dealer Technical
Page 413 of 3039
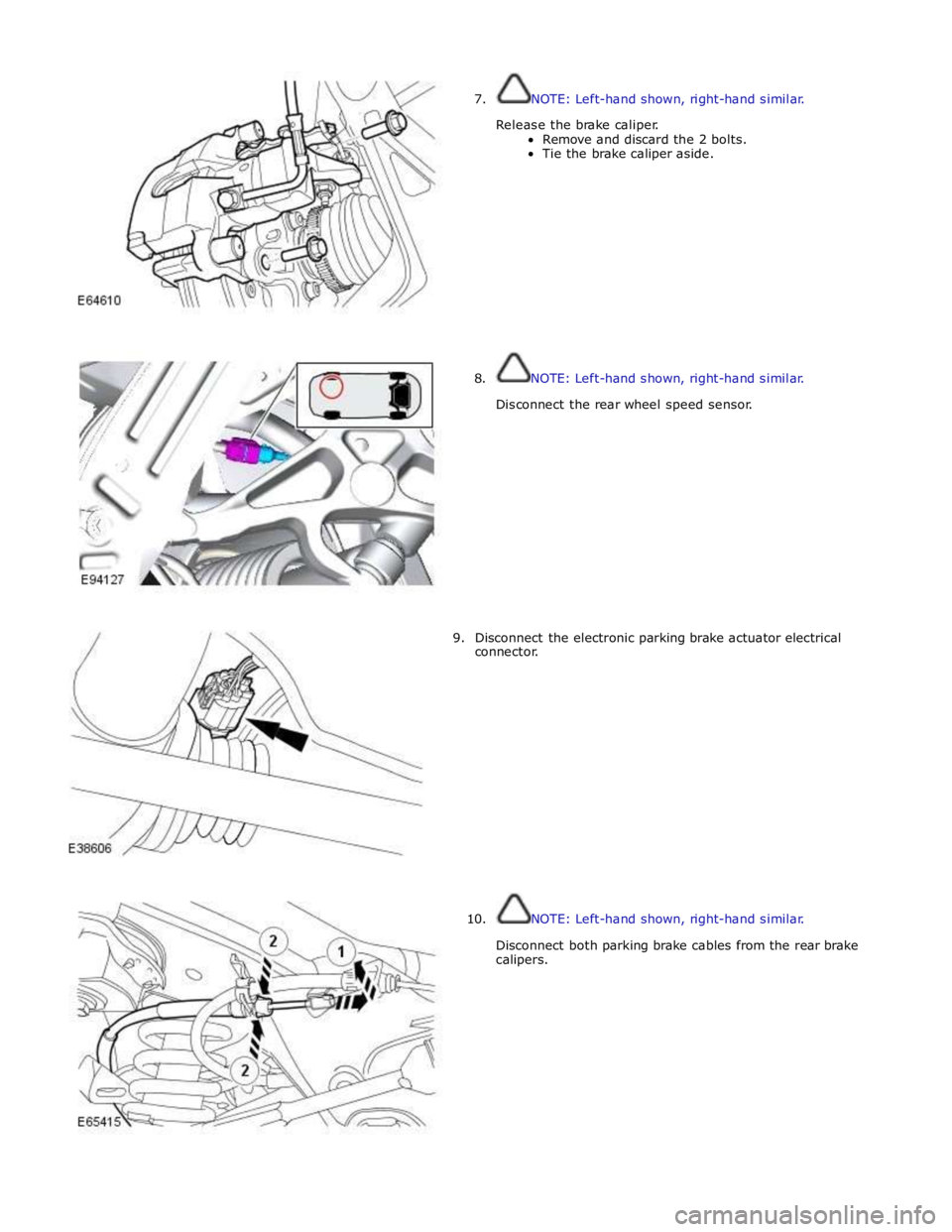
7. NOTE: Left-hand shown, right-hand similar.
Release the brake caliper.
Remove and discard the 2 bolts.
Tie the brake caliper aside.
8. NOTE: Left-hand shown, right-hand similar.
Disconnect the rear wheel speed sensor.
9. Disconnect the electronic parking brake actuator electrical
connector.
10. NOTE: Left-hand shown, right-hand similar.
Disconnect both parking brake cables from the rear brake
calipers.