gas type JAGUAR XJ6 1994 2.G Workshop Manual
[x] Cancel search | Manufacturer: JAGUAR, Model Year: 1994, Model line: XJ6, Model: JAGUAR XJ6 1994 2.GPages: 521, PDF Size: 17.35 MB
Page 10 of 521
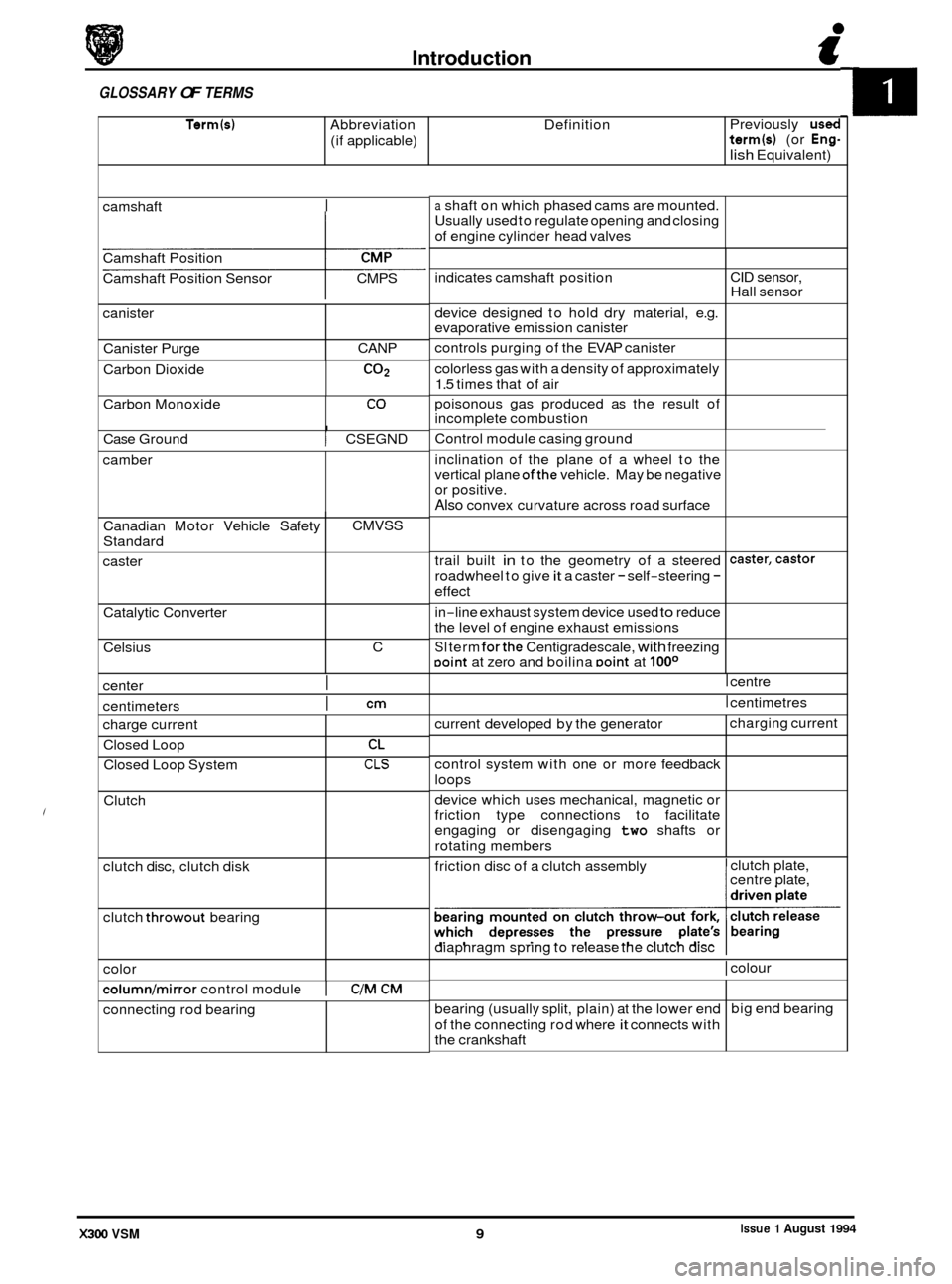
Introduction i
Term(s) Abbreviation Definition
(if applicable)
GLOSSARY OF TERMS
Previously used term(s) (or Eng-
lish Equivalent)
indicates camshaft position
device designed to hold dry material, e.g.
evaporative emission canister
controls purging of the EVAP canister
colorless gas with a density of approximately
1.5 times that of air
poisonous gas produced as the result of
incomplete combustion
camshaft
I
CID
sensor,
Hall sensor
Camshaft
Position
Camshaft Position Sensor CMPS
canister
Canister Purge CANP
Carbon Dioxide
CO2
I Case Ground I CSEGND
Carbon
Monoxide
camber
CO
Canadian Motor Vehicle Safety
Standard
caster
Catalytic Converter
Celsius
center
I
CMVSS
C
centimeters
I cm
trail built in to the geometry of a steered
roadwheel to give
it a caster - self-steering -
effect
caster,castor
color
columnlmirror control module I C/M CM
charge current
Closed Loop
Closed Loop System
Clutch
clutch disc, clutch disk
clutch
throwout bearing
connecting rod bearing
CL
CLS
a shaft on which phased cams are mounted.
Usually used to regulate opening and closing
of engine cylinder head valves
current developed by the generator
control system with one or more feedback
loops
device which uses mechanical, magnetic or
friction type connections to facilitate
engaging or disengaging
two shafts or
rotating members charging
current
Control
module casing ground
inclination of the plane of a wheel to the
vertical plane
ofthe vehicle. May be negative
or positive.
Also convex curvature across road surface
bearing (usually split, plain) at the lower end
of the connecting rod where
it connects with
the crankshaft big
end bearing
in
-line exhaust
system device used to reduce
the level of engine exhaust emissions
SI term forthe Centigradescale, with freezing Doint at zero and boilina Doint at looo
I centre
I centimetres
friction disc of a clutch assembly clutch
plate,
centre plate,
diaphragm spring to release the clutch disc
I colour
Issue 1 August 1994 X300 VSM 9
Page 43 of 521
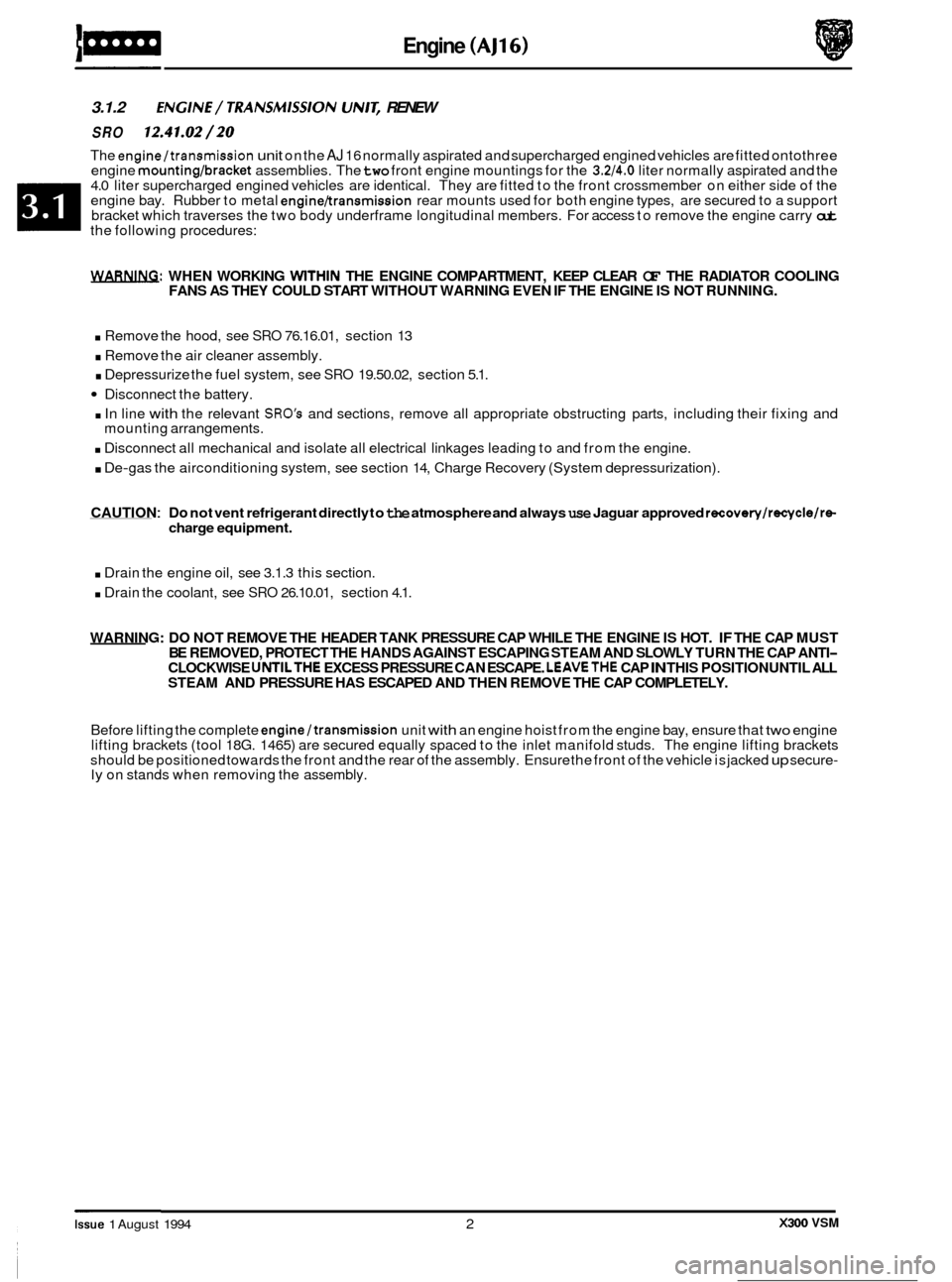
Engine (AJ16)
3.1.2 ENGlNE/ TRANSMlSSlON UN/& RENEW
SRO 12.41.02/20
The engine/transmission unit on the AJ 16 normally aspirated and supercharged engined vehicles are fitted ontothree
engine mounting/bracket assemblies. The two front engine mountings for the 3.2/4.0 liter normally aspirated and the
4.0 liter supercharged engined vehicles are identical. They are fitted to the front crossmember on either side of the
engine bay. Rubber to metal
engine/transmission rear mounts used for both engine types, are secured to a support
bracket which traverses the two body underframe longitudinal members. For access to remove the engine carry out the following procedures:
WARNING: WHEN WORKING WlTHlN THE ENGINE COMPARTMENT, KEEP CLEAR OF THE RADIATOR COOLING
FANS AS THEY COULD START WITHOUT WARNING EVEN IF THE ENGINE IS NOT RUNNING.
. Remove the hood, see SRO 76.16.01, section 13
. Remove the air cleaner assembly.
. Depressurize the fuel system, see SRO 19.50.02, section 5.1.
Disconnect the battery.
. In line with the relevant SRO's and sections, remove all appropriate obstructing parts, including their fixing and
. Disconnect all mechanical and isolate all electrical linkages leading to and from the engine.
. De-gas the airconditioning system, see section 14, Charge Recovery (System depressurization).
mounting
arrangements.
CAUTION : Do not vent refrigerant directly to the atmosphere and always use Jaguar approved recovery/recycle/re- charge equipment.
. Drain the engine oil, see 3.1.3 this section.
. Drain the coolant, see SRO 26.10.01, section 4.1.
WARNING: DO NOT REMOVE THE HEADER TANK PRESSURE CAP WHILE THE ENGINE IS HOT. IF THE CAP MUST
BE REMOVED, PROTECT THE HANDS AGAINST ESCAPING STEAM AND SLOWLY TURN THE CAP ANTI- CLOCKWISE UNTILTHE EXCESS PRESSURE CAN ESCAPE. LEAVETHE CAP IN THIS POSITION UNTIL ALL
STEAM AND PRESSURE HAS ESCAPED AND THEN REMOVE THE CAP COMPLETELY.
Before lifting the complete engine/transmission unit with an engine hoist from the engine bay, ensure that two engine
lifting brackets (tool 18G. 1465) are secured equally spaced to the inlet manifold studs. The engine lifting brackets
should be positioned towards the front and the rear of the assembly. Ensure the front of the vehicle is jacked
up secure- ly on stands when removing the assembly.
e
0
0
X300 VSM Issue 1 August 1994 2
Page 312 of 521

Climate Control Systems
Description U-
HFC 134A - ICI Klea or
equivalent
Polyalkyleneglycol (PAG) Compressor lubricant
Refrigerant
111.
Notes
Recyclable. NOT
compatible
with CFC 12
Absorbs water readily. NOT
compatible with mineral based
oils
SERVICE MATERIALS
Standard for Recovery I Recycle 1 Recharge Equipment.
Recovery rate
Cleaning capability
Oil separator
.Moisture indicator
Vacuum pump
Filter Replaceable with moisture indicator
Charge Hoses
Feature Requirement
0,014 - 0,062 m3 / min. (1,36 kg in 20 minutes)
15 parts per million (ppm) moisture; 4000 ppm oil; 330 ppm non condensable gases
in air
With hermetic compressor and automatic oil return
Sight glass type, sensitive to 15 ppm minimum
2 stage 0,07 - 0,127 m3 I min.
Selectable charge weight and automatic delivery
Dedicated HFC 134A port connections.
Iv. SERVICE DATA
Application
Charae weight
Lubricant capacity
Compressor pressure relief valve
Drive belt 12 cylinder
Drive belt tension
All figures apply to a cold belt
Special note
Drive belt tension measuring point
Drive belt 6 cyclinder
Drive belt tension
All figures apply to a cold belt
Drive belt tension measuring point
Specification
160 - 200 ml
Opening point 34 Bar. Closing point 27,6 Bar.
Maximum leakage rate of 113 liters 1 minute @ 41 Bar
7 rib Poly
-vee; 1450 mm long
Burroughs method
- New belt 790 N; If tension falls
below 270 N reset at 630 N
Clavis method
- New belt 114 to 120 Hz; If tension falls
below 70 Hz reset at 87 to 93 Hz
For new belt; rotate engine 3 revolutions minimum and
retension
Mid-way between crankshaft and compressor pulley ~
4
rib Poly-vee X 1010 mm long
Burroughs method
- New belt 556 to 578 N; If tension
falls below 245 N reset at 378 to 400
N
Clavis method - New belt 167 to 173 Hz; If tension falls
below 85 Hz reset at 127 to 133 Hz
Mid
-way between crankshaft and compressor pulley on
the upper run
1 Charge pressure I Heating element to increase pressure
Issue 1 August 1994 X300 VSM iii
Page 387 of 521
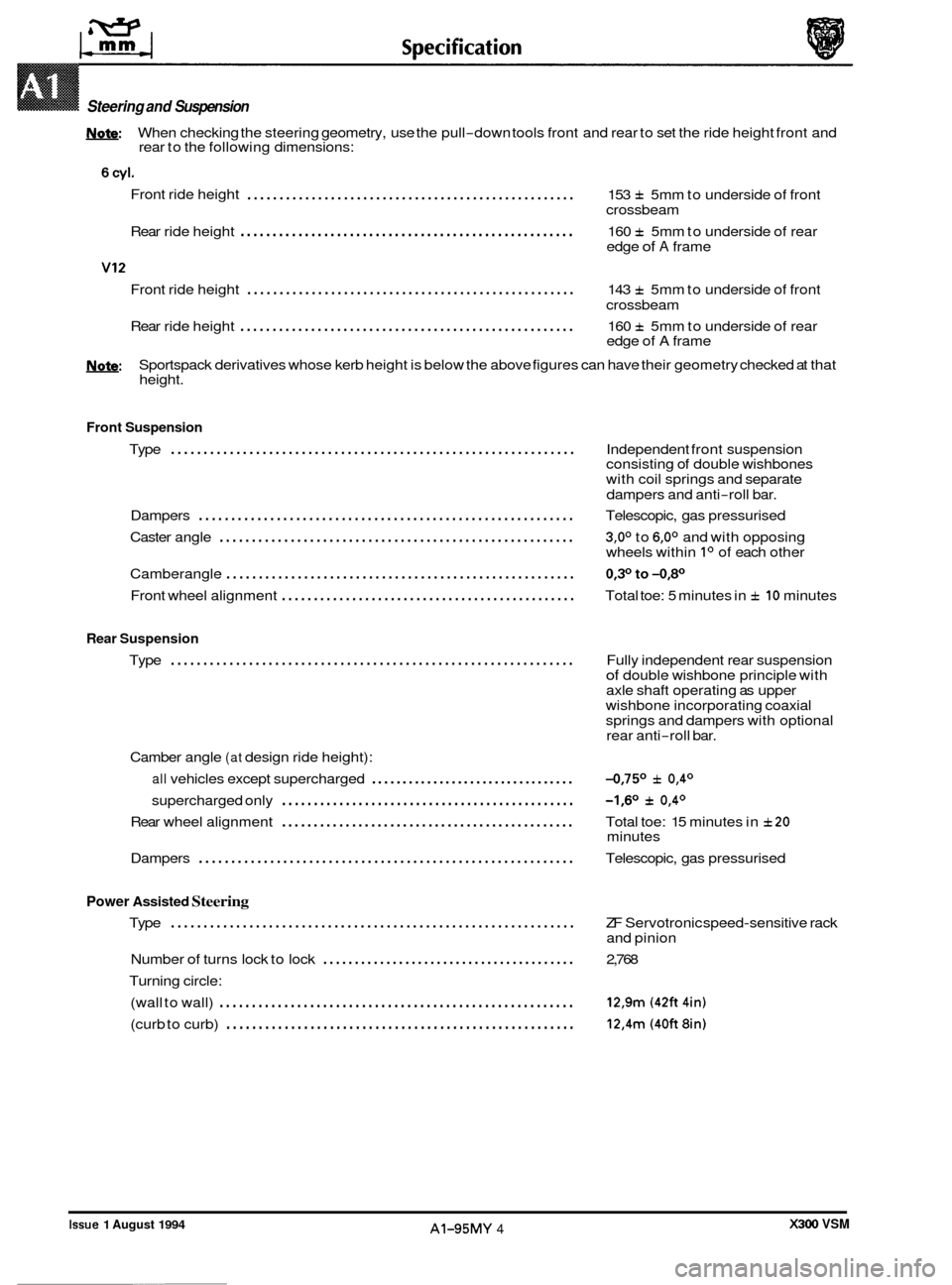
Steering and Suspension
W: When checking the steering geometry, use the pull-down tools front and rear to set the ride height front and
rear to the following dimensions:
Front ride height
................................................... 153 f 5mm to underside of front
crossbeam
Rear ride height
.................................................... 160 f 5mm to underside of rear
edge of A frame
Front ride height
................................................... 143 f 5mm to underside of front
crossbeam
Rear ride height
.................................................... 160 f 5mm to underside of rear
edge of A frame
U: Sportspack derivatives whose kerb height is below the above figures can have their geometry checked at that
height.
Front Suspension
..............................................................
0
Type Independent front suspension
consisting of double wishbones
with coil springs and separate
dampers and anti
-roll bar.
Dampers
.......................................................... Telescopic, gas pressurised
Caster angle
....................................................... 3,0° to 6,0° and with opposing
wheels within Io of each other
Camberangle
...................................................... 0,3°to-0,80
Front wheel alignment .............................................. Total toe: 5 minutes in f 10 minutes
Rear Suspension
Type .............................................................. Fully independent rear suspension of double wishbone principle with
axle shaft operating as upper
wishbone incorporating coaxial
springs and dampers with optional
rear anti
-roll bar.
Camber angle
(at design ride height):
all vehicles except supercharged ................................. -0,75O f 0,4O
supercharged only -1,6O f 0,4O ..............................................
0 Rear wheel alignment .............................................. Total toe: 15 minutes in f20
Dampers .......................................................... Telescopic, gas pressurised
minutes
Power Assisted Steering
Type .............................................................. ZF
Servotronic speed-sensitive rack
and pinion
Number
of turns lock to lock ........................................ 2,768
Turning circle: (wall to wall)
....................................................... 12,9m (42ft 4in)
(curb to curb) ...................................................... 12,4m (40ft 8in)
0
X300 VSM Issue 1 August 1994 AI-95MY 4 ~~~~
Page 417 of 521
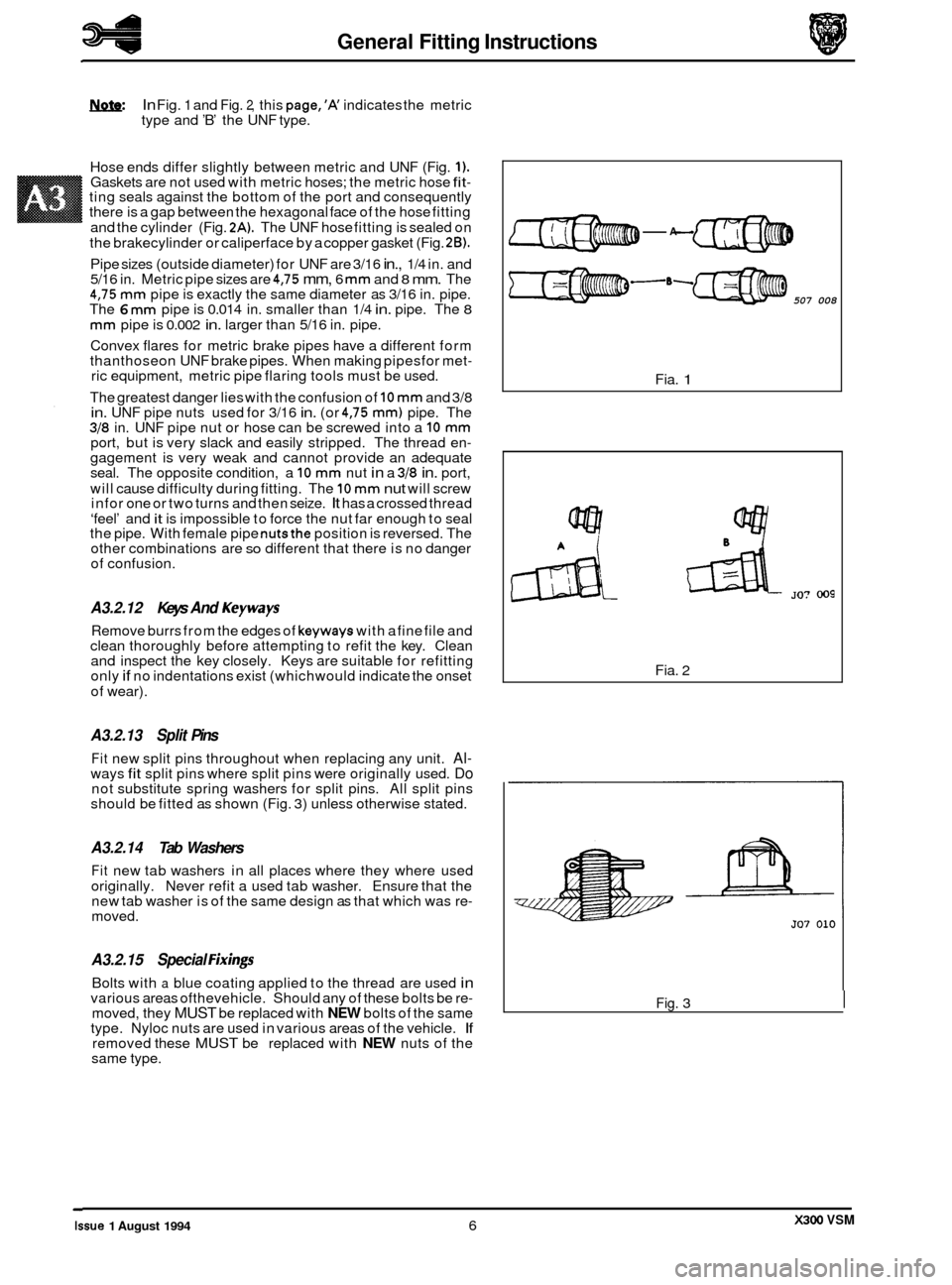
General Fitting Instructions
In Fig. 1 and Fig. 2, this page,’K indicates the metric
type and ’B’ the UNF type.
Hose ends differ slightly between metric and UNF (Fig.
1). Gaskets are not used with metric hoses; the metric hose fit- ting seals against the bottom of the port and consequently
there is a gap between the hexagonal face of the hose fitting
and the cylinder (Fig.
2A). The UNF hose fitting is sealed on
the brakecylinder or caliperface by a copper gasket (Fig.
2B).
Pipe sizes (outside diameter) for UNF are 3/16 in., 1/4 in. and
5/16 in. Metric pipe sizes are 4,75 mm, 6 mm and 8 mm. The 4,75 mm pipe is exactly the same diameter as 3/16 in. pipe.
The 6 mm pipe is 0.014 in. smaller than 1/4 in. pipe. The 8
mm pipe is 0.002 in. larger than 5/16 in. pipe.
Convex flares for metric brake pipes have a different form
thanthoseon UNF brake pipes. When making pipesfor met
- ric equipment, metric pipe flaring tools must be used.
The greatest danger lies with the confusion of
10 mm and 3/8 in. UNF pipe nuts used for 3/16 in. (or 4,75 mm) pipe. The 318 in. UNF pipe nut or hose can be screwed into a 10 mm port, but is very slack and easily stripped. The thread en- gagement is very weak and cannot provide an adequate
seal. The opposite condition, a 10 mm nut in a 318 in. port,
will cause difficulty during fitting. The
10 mm nut will screw
in for one or two turns and then seize. It has a crossed thread
‘feel’ and
it is impossible to force the nut far enough to seal
the pipe. With female pipe nutsthe position is reversed. The
other combinations are so different that there is no danger
of confusion.
A3.2.12 Keys And Keyways
Remove burrs from the edges of keyways with a fine file and
clean thoroughly before attempting to refit the key. Clean
and inspect the key closely. Keys are suitable for refitting
only
if no indentations exist (which would indicate the onset
of wear).
A3.2.13 Split Pins
Fit new split pins throughout when replacing any unit. Al- ways fit split pins where split pins were originally used. Do not substitute spring washers for split pins. All split pins
should be fitted as shown (Fig. 3) unless otherwise stated.
A3.2.14 Tab Washers
Fit new tab washers in all places where they where used
originally. Never refit a used tab washer. Ensure that the
new tab washer is of the same design as that which was re
- moved.
A3.2.15 Special Fixing
Bolts with a blue coating applied to the thread are used in various areas ofthevehicle. Should any of these bolts be re- moved, they MUST be replaced with NEW bolts of the same
type. Nyloc nuts are used in various areas of the vehicle. If removed these MUST be replaced with NEW nuts of the
same type.
-A
507 008
Fia. 1
Fia. 2
Fig. 3 I
X300 VSM Issue 1 August 1994 6
Page 424 of 521
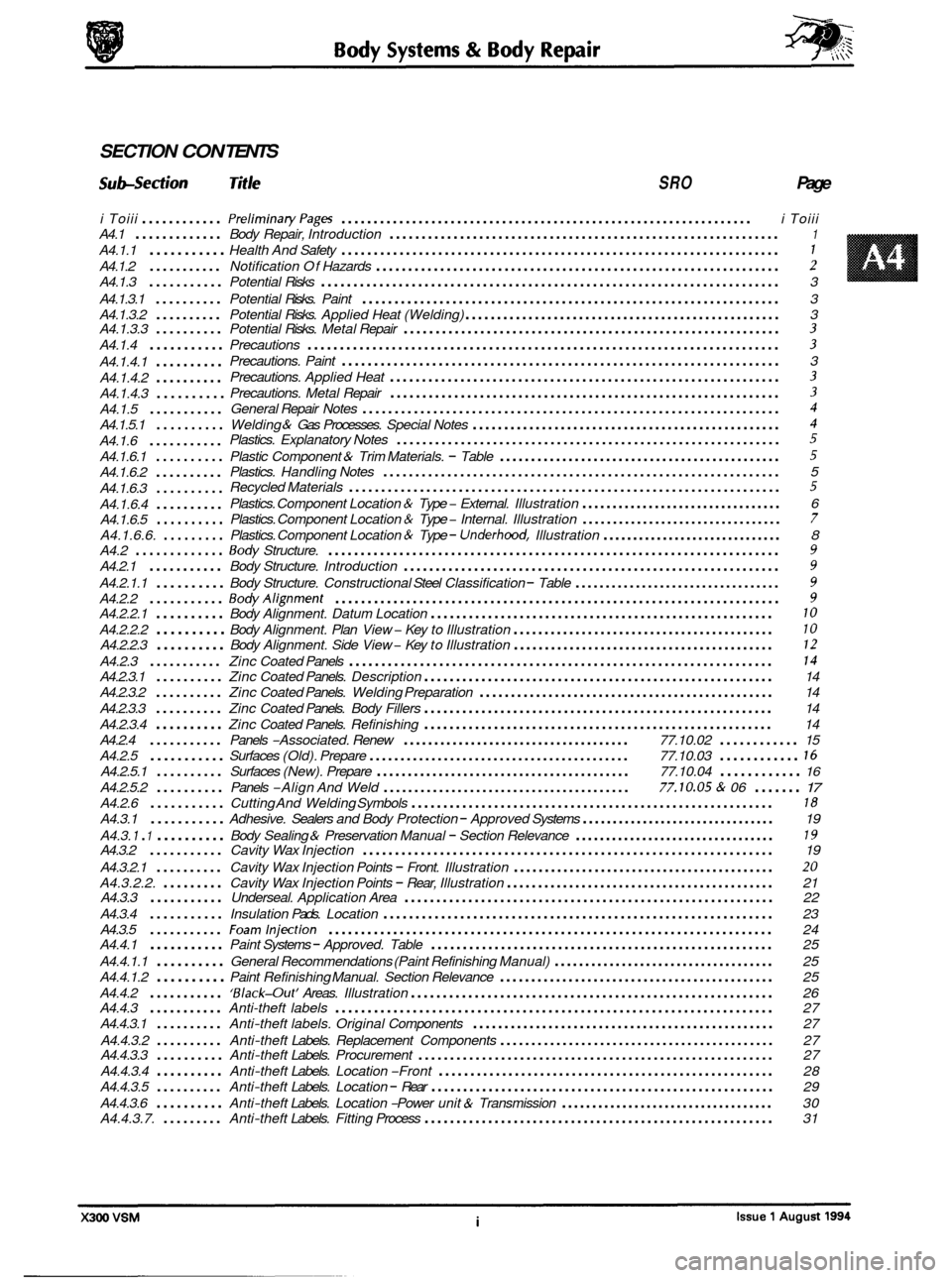
SECTION CON TENTS
Suh-Section Title SRO Page
i Toiii ............ PreliminaryPages ................................................................ i Toiii
A4.1
............. Body Repair, Introduction ............................................................. 1
A4.1.1 ........... Health And Safety .................................................................... 1
A4.1.2 ........... Notification Of Hazards ............................................................... 2
A4.1.3 ........... Potential Risks ....................................................................... \
3
A4.1.3.1
.......... Potential Risks. Paint ................................................................. 3
A4.1.3.2
.......... Potential Risks. Applied Heat (Welding) .................................................. 3
A4.1.3.3 .......... Potential Risks. Metal Repair ........................................................... 3
A4.1.4 ........... Precautions ........................................................................\
. 3
A4.1.4.1 ..........
A4.1.4.2 ..........
A4.1.4.3 ..........
A4.1.5 ...........
A4.1.5.1 ..........
A4.1.6 ...........
A4.1.6.1 ..........
A4.1.6.2 ..........
A4.1.6.3 ..........
A4.1.6.4 ..........
A4.1.6.5 ..........
A4.1.6.6. .........
Precautions. Paint .................................................................... 3
Precautions. Applied Heat
............................................................. 3
Precautions. Metal Repair ............................................................. 3
General Repair Notes ................................................................. 4
Welding & Gas Processes. Special Notes ................................................. 4
Plastic Component & Trim Materials. - Table ............................................. 5
Plastics. Explanatory Notes ............................................................ 5
Plastics. Handling Notes .............................................................. 5
Recycled Materials
................................................................... 5
Plastics. Component Location & Type - External. Illustration ................................. 6
Plastics. Component Location
& Type - Internal. Illustration ................................. 7
Plastics. Component Location & Type - Underhood. Illustration .............................. 8
A4.2 ............. Body Structure. ...................................................................... 9
A4.2.1 ........... Body Structure. Introduction ........................................................... 9
A4.2.2.1 .......... Body Alignment. Datum Location ...................................................... 10
A4.2.2.2 .......... Body Alignment. Plan View - Key to Illustration .......................................... 10
A4.2.2.3 .......... Body Alignment. Side View - Key to Illustration .......................................... 12
A4.2.3 ........... Zinc Coated Panels .................................................................. 14
A4.2.3.1 .......... Zinc Coated Panels. Description ....................................................... 14
A4.2.3.2
.......... Zinc Coated Panels. Welding Preparation ............................................... 14
A4.2.3.3
.......... Zinc Coated Panels. Body Fillers ....................................................... 14
A4.2.3.4
.......... Zinc Coated Panels. Refinishing ....................................................... 14
A4.2.4
........... Panels -Associated. Renew ..................................... 77.10.02 ............ 15
A4.2.5
........... Surfaces (Old). Prepare .......................................... 77.10.03 ............ 16
A4.2.5.1 .......... Surfaces (New). Prepare ......................................... 77.10.04 ............ 16
A4.2.5.2 .......... Panels -Align And Weld ........................................ 77.10.05 & 06 ....... 17
A4.2.6 ........... Cutting And Welding Symbols ......................................................... 18
A4.3.1 ........... Adhesive. Sealers and Body Protection - Approved Systems ................................ 19
A4.3.
1 . 1 .......... Body Sealing & Preservation Manual - Section Relevance ................................. 19 A4.3.2 ........... Cavity Wax Injection ................................................................ 19
A4.3.2.1
.......... Cavity Wax Injection Points - Front. Illustration .......................................... 20
A4.3.2.2. ......... Cavity Wax Injection Points - Rear, Illustration ........................................... 21
A4.3.3 ........... Underseal. Application Area .......................................................... 22
A4.3.4
........... Insulation Pads. Location ............................................................. 23
A4.3.5
........... Foamlnjection ..................................................................... 24
A4.4.1 ........... Paint Systems - Approved. Table ...................................................... 25
A4.4.1.1
.......... General Recommendations (Paint Refinishing Manual) .................................... 25
A4.4.1.2
.......... Paint Refinishing Manual. Section Relevance ............................................ 25
A4.4.2
........... ‘Black-Out’ Areas. Illustration ......................................................... 26
A4.4.3 ........... Anti-theft labels .................................................................... 27
A4.4.3.1
.......... Anti-theft labels. Original Components ................................................ 27
A4.4.3.2
.......... Anti-theft Labels. Replacement Components ............................................ 27
A4.4.3.3 .......... Anti-theft Labels. Procurement ........................................................ 27
A4.4.3.4
.......... Anti-theft Labels. Location -Front ..................................................... 28
A4.4.3.5
.......... Anti-theft Labels. Location - Rear ...................................................... 29
A4.4.3.7.
......... Anti-theft Labels. Fitting Process ....................................................... 31
A4.2.1.1
.......... Body Structure.
Constructional Steel Classification - Table .................................. 9
A4.2.2 ........... BodyAlignment ..................................................................... 9
A4.4.3.6 .......... Anti-theft Labels. Location -Power unit & Transmission ................................... 30
Page 430 of 521
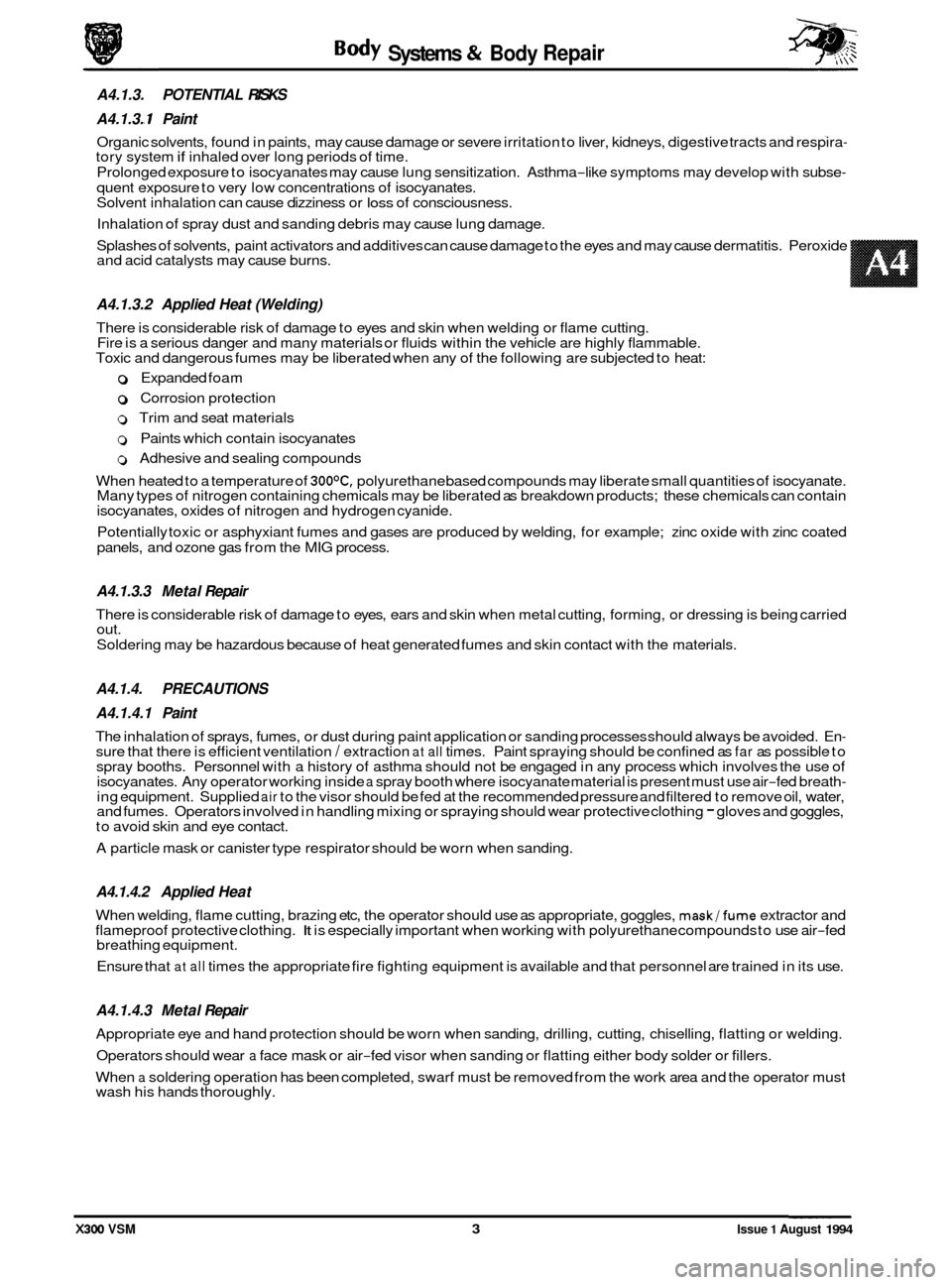
Systems Repair Body & Body -
A4.1.3. POTENTIAL RISKS I
A4.1.3. Paint
Organic solvents, found in paints, may cause damage or severe irritation to liver, kidneys, digestive tracts and respira- tory system if inhaled over long periods of time.
Prolonged exposure to isocyanates may cause lung sensitization. Asthma
-like symptoms may develop with subse-
quent exposure to very low concentrations of isocyanates.
Solvent inhalation can cause dizziness or loss of consciousness.
Splashes of solvents, paint activators and additives can cause damage to the eyes and may cause dermatitis. Peroxide
and acid catalysts may cause burns.
Inhalation of
spray dust and sanding debris may cause lung damage.
I
A4.1.3.2 Applied Heat (Welding)
There is considerable risk of damage to eyes and skin when welding or flame cutting.
Fire is a serious danger and many materials or fluids within the vehicle are highly flammable.
Toxic and dangerous fumes may be liberated when any of the following are subjected to heat:
0 Expanded foam
0 Corrosion protection
0 Trim and seat materials
0 Paints which contain isocyanates
0 Adhesive and sealing compounds
When heated to a temperature of 3OO0C, polyurethane based compounds may liberate small quantities of isocyanate.
Many types of nitrogen containing chemicals may be liberated as breakdown products; these chemicals can contain
isocyanates, oxides of nitrogen and hydrogen cyanide.
Potentially toxic or asphyxiant fumes and gases are produced by welding, for example; zinc oxide with zinc coated
panels, and ozone gas from the MIG process.
A4.1.3.3 Metal Repair
There is considerable risk of damage to eyes, ears and skin when metal cutting, forming, or dressing is being carried
out.
Soldering may be hazardous because of heat generated fumes and skin contact with the materials.
A4.1.4. PRECAUTIONS
A4.1.4.1 Paint
The inhalation of sprays, fumes, or dust during paint application or sanding processes should always be avoided. En- sure that there is efficient ventilation / extraction at all times. Paint spraying should be confined as far as possible to
spray booths. Personnel with a history of asthma should not be engaged in any process which involves the use of
isocyanates. Any operator working inside
a spray booth where isocyanate material is present must use air-fed breath- ing equipment. Supplied air to the visor should be fed at the recommended pressure and filtered to remove oil, water,
and fumes. Operators involved in handling mixing or spraying should wear protective clothing - gloves and goggles,
to avoid skin and eye contact.
A particle mask or canister type respirator should be worn when sanding.
A4.1.4.2 Applied Heat
When welding, flame cutting, brazing etc, the operator should use as appropriate, goggles, mask/fume extractor and
flameproof protective clothing. It is especially important when working with polyurethane compounds to use air-fed
breathing equipment.
Ensure that
at all times the appropriate fire fighting equipment is available and that personnel are trained in its use.
A4.1.4.3 Metal Repair
Appropriate eye and hand protection should be worn when sanding, drilling, cutting, chiselling, flatting or welding.
Operators should wear
a face mask or air-fed visor when sanding or flatting either body solder or fillers.
When
a soldering operation has been completed, swarf must be removed from the work area and the operator must
wash his hands thoroughly.
X300 VSM 3 Issue 1 August 1994