run flat JAGUAR XJ6 1994 2.G Workshop Manual
[x] Cancel search | Manufacturer: JAGUAR, Model Year: 1994, Model line: XJ6, Model: JAGUAR XJ6 1994 2.GPages: 521, PDF Size: 17.35 MB
Page 35 of 521
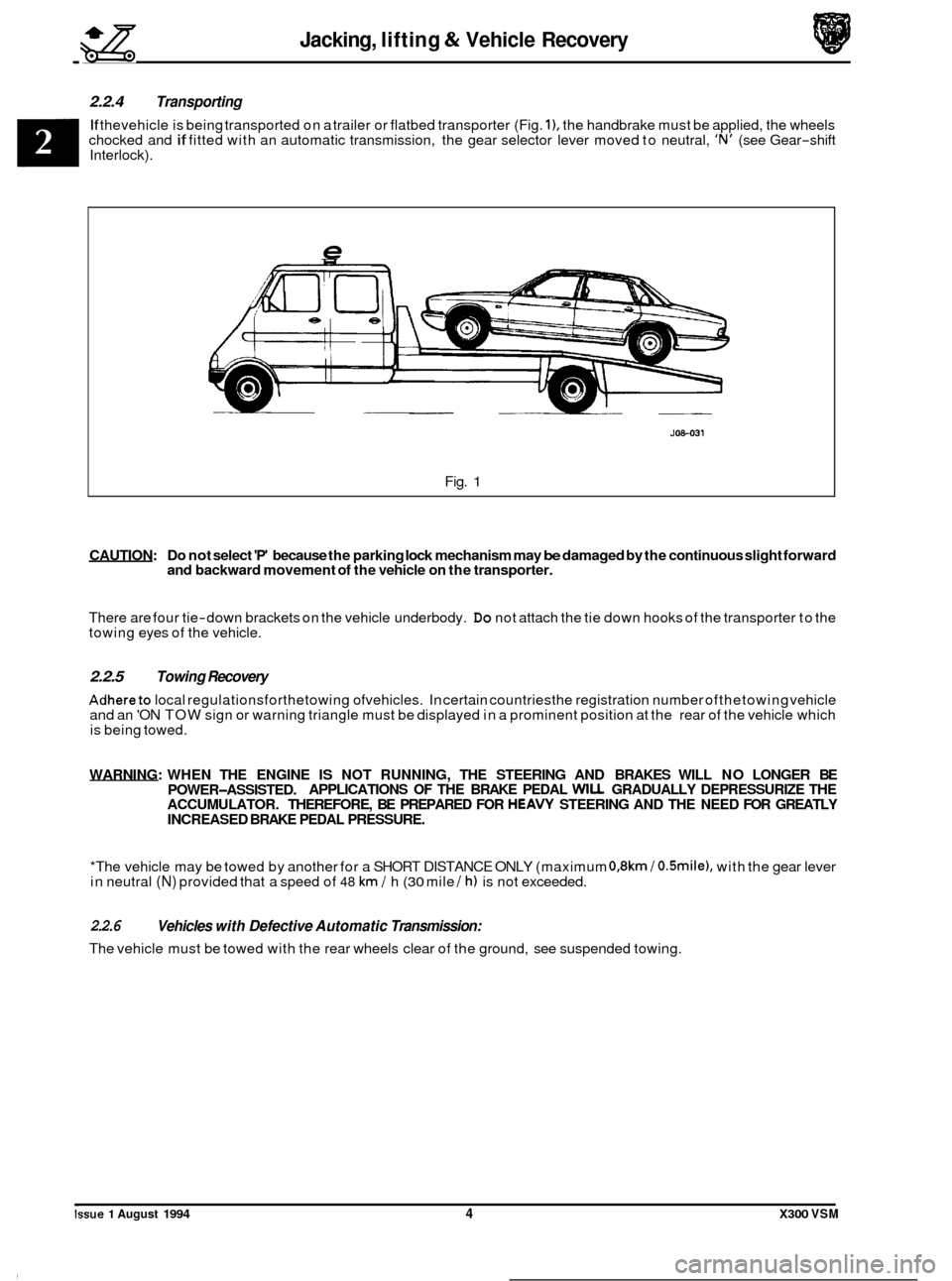
gg Jacking, lifting & Vehicle Recovery
2.2.4 Transporting
If thevehicle is being transported on a trailer or flatbed transporter (Fig. I), the handbrake must be applied, the wheels
chocked and if fitted with an automatic transmission, the gear selector lever moved to neutral, 'N' (see Gear-shift
Interlock).
e
JOS-031
Fig. 1
CAUTION: Do not select 'P' because the parking lock mechanism may be damaged by the continuous slight forward
and backward movement of the vehicle on the transporter.
There are four tie-down brackets on the vehicle underbody. Do not attach the tie down hooks of the transporter to the
towing eyes of the vehicle.
2.2.5 Towing Recovery
Adhereto local regulationsforthetowing ofvehicles. In certain countriesthe registration number ofthetowing vehicle
and an 'ON TOW sign or warning triangle must be displayed in a prominent position at the rear of the vehicle which
is being towed.
WARNING: WHEN THE ENGINE
IS NOT RUNNING, THE STEERING AND BRAKES WILL NO LONGER BE
ACCUMULATOR. THEREFORE, BE PREPARED FOR
HEAVY STEERING AND THE NEED FOR GREATLY
INCREASED BRAKE PEDAL PRESSURE.
POWER-ASSISTED.
APPLICATIONS
OF THE BRAKE PEDAL WILL GRADUALLY DEPRESSURIZE THE
*The vehicle may be towed by another for a SHORT DISTANCE ONLY (maximum
0,8km / O.Smile), with the gear lever
in neutral (N) provided that a speed of 48 km / h (30 mile / h) is not exceeded.
2.2.6
The vehicle must be towed with the rear wheels clear of the ground, see suspended towing.
Vehicles with Defective Automatic Transmission:
Issue 1 August 1994 4 X300 VSM
Page 187 of 521
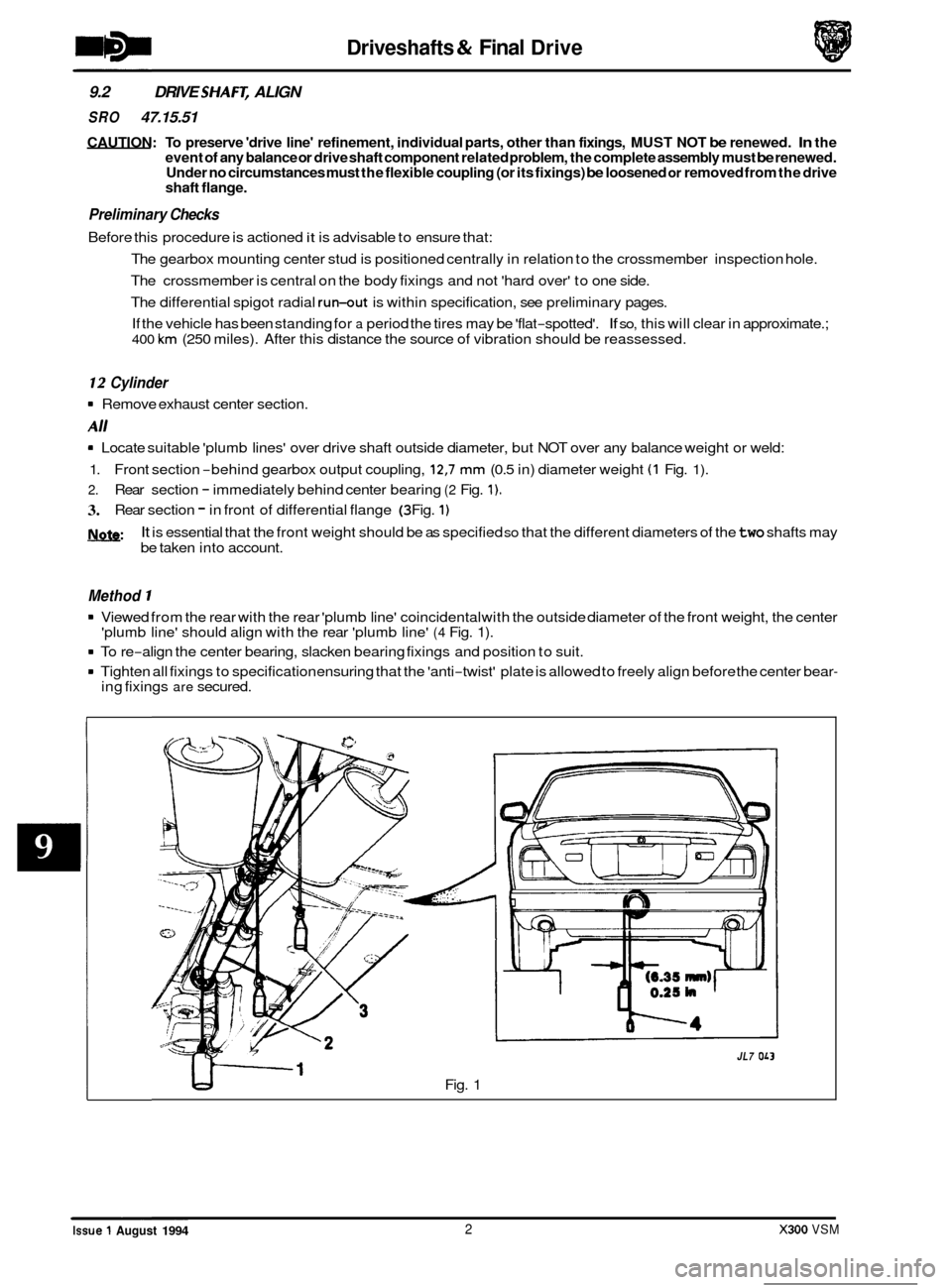
Driveshafts & Final Drive
9.2 DRIVE SHAm, ALIGN
SRO 47.15.51
CAUTION: To preserve 'drive line' refinement, individual parts, other than fixings, MUST NOT be renewed. In the
event of any balance or drive shaft component related problem, the complete assembly must be renewed.
Under no circumstances must the flexible coupling (or its fixings) be loosened or removed from the drive
shaft flange.
Preliminary Checks
Before this procedure is actioned it is advisable to ensure that:
The gearbox mounting center stud is positioned centrally in relation to the crossmember inspection hole.
The crossmember is central on the body fixings and not 'hard over' to one side.
The differential spigot radial
run-out is within specification, see preliminary pages.
If the vehicle has been standing for
a period the tires may be 'flat-spotted'. If so, this will clear in approximate.;
400 km (250 miles). After this distance the source of vibration should be reassessed.
12 Cylinder
8 Remove exhaust center section.
All
8 Locate suitable 'plumb lines' over drive shaft outside diameter, but NOT over any balance weight or weld:
1.
2.
3.
l\lnfe:
Front section -behind gearbox output coupling, 12,7 mm (0.5 in) diameter weight (1 Fig. 1).
Rear section - immediately behind center bearing (2 Fig. 1).
Rear section - in front of differential flange (3 Fig. 1)
It is essential that the front weight should be as specified so that the different diameters of the two shafts may
be taken into account.
Method 1
8 Viewed from the rear with the rear 'plumb line' coincidental with the outside diameter of the front weight, the center
8 To re-align the center bearing, slacken bearing fixings and position to suit.
8 Tighten all fixings to specification ensuring that the 'anti-twist' plate is allowed to freely align before the center bear-
'plumb line' should align with the rear 'plumb line' (4 Fig. 1).
ing fixings are secured.
Fig. 1
1
JL7 OL3
0
0
0
0 ~~~~
Issue 1 August 1994 2 X300 VSM
Page 219 of 521
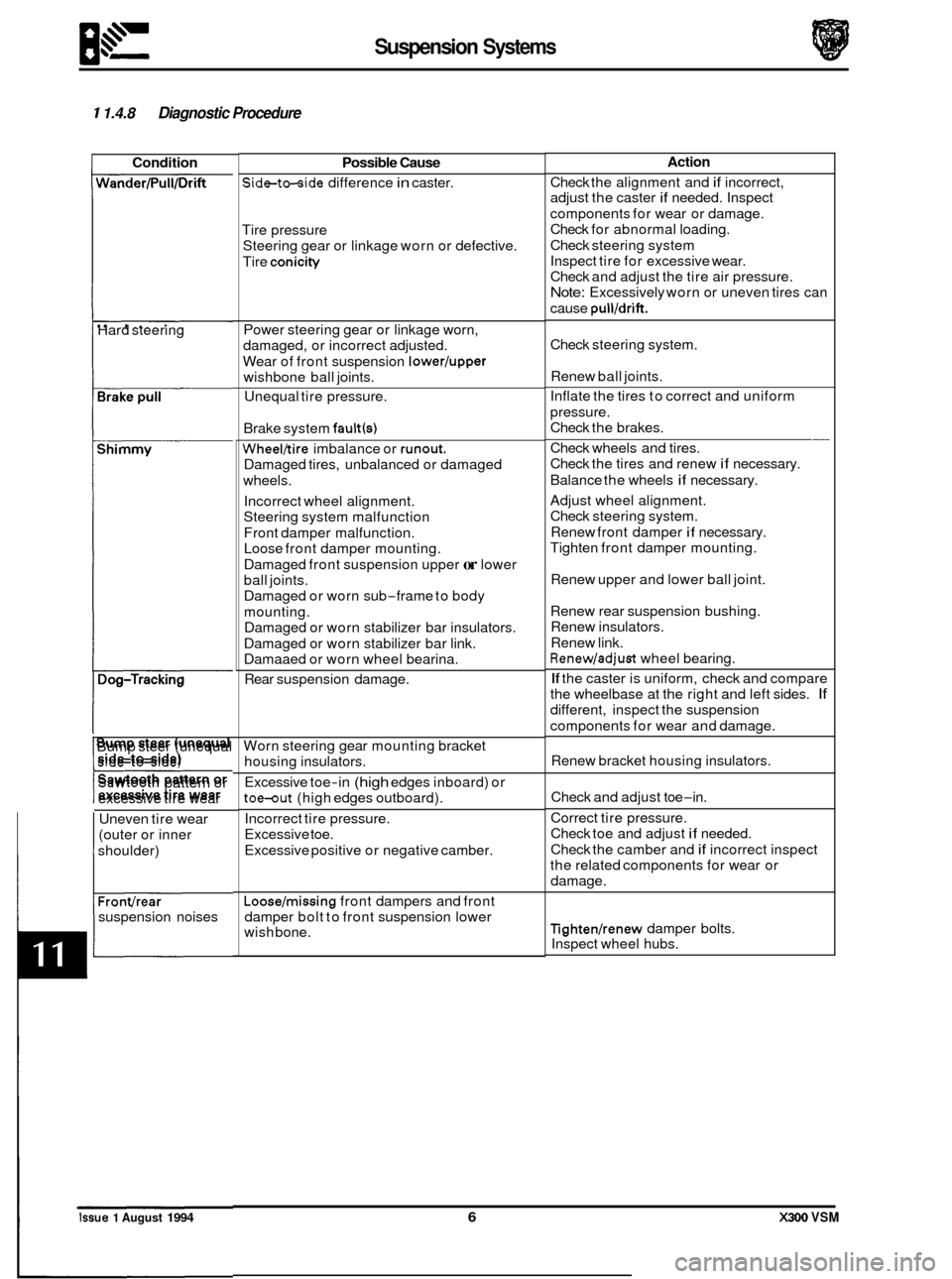
Suspension Systems
1 1.4.8 Diagnostic Procedure
Condition
Hard steering
Shimmy
I----
Bump steer (unequal
side-to-side)
Sawtooth pattern or
t excessive tire wear
Uneven tire wear
(outer or inner
shoulder)
Fronvrear
suspension noises
Possible Cause
Side-to-side difference in caster.
Tire pressure Steering gear or linkage worn or defective.
Tire
conicity
Power steering gear or linkage worn,
damaged, or incorrect adjusted.
Wear of front suspension
lower/upper
wishbone ball joints.
Unequal tire pressure.
Brake system
fault(s)
Wheel/tire imbalance or runout.
Damaged tires, unbalanced or damaged
wheels.
Incorrect wheel alignment.
Steering system malfunction
Front damper malfunction.
Loose front damper mounting.
Damaged front suspension upper
or lower
ball joints.
Damaged or worn sub
-frame to body
mounting. Damaged or worn stabilizer bar insulators.
Damaged or worn stabilizer bar link.
Damaaed or worn wheel bearina.
Rear suspension damage.
Worn steering gear mounting bracket
housing insulators.
Excessive toe
-in (high edges inboard) or
toe-out (high edges outboard).
Incorrect tire pressure.
Excessive toe.
Excessive positive or negative camber.
Loose/missing front dampers and front
damper bolt to front suspension lower
wish bone.
Action
Check the alignment and if incorrect,
adjust the caster
if needed. Inspect
components for wear or damage.
Check for abnormal loading.
Check steering system
Inspect tire for excessive wear.
Check and adjust the tire air pressure.
Note: Excessively worn or uneven tires can
cause
pull/drift.
Check steering system.
Renew ball joints.
Inflate the tires to correct and uniform
pressure.
Check the brakes.
Check wheels and tires.
Check the tires and renew
if necessary.
Balance the wheels
if necessary.
Adjust wheel alignment.
Check steering system.
Renew front damper
if necessary.
Tighten front damper mounting.
-
Renew upper and lower ball joint.
Renew rear suspension bushing.
Renew insulators.
Renew link.
Renew/adjust wheel bearing.
If the caster is uniform, check and compare
the wheelbase at the right and left sides.
If
different, inspect the suspension
components for wear and damage.
Renew bracket housing insulators.
Check and adjust toe
-in.
Correct tire pressure.
Check toe and adjust
if needed.
Check the camber and
if incorrect inspect
the related components for wear or
damage.
Tighten/renew damper bolts.
Inspect wheel hubs.
0
0
0
lssue 1 August 1994 6 X300 VSM
Page 415 of 521
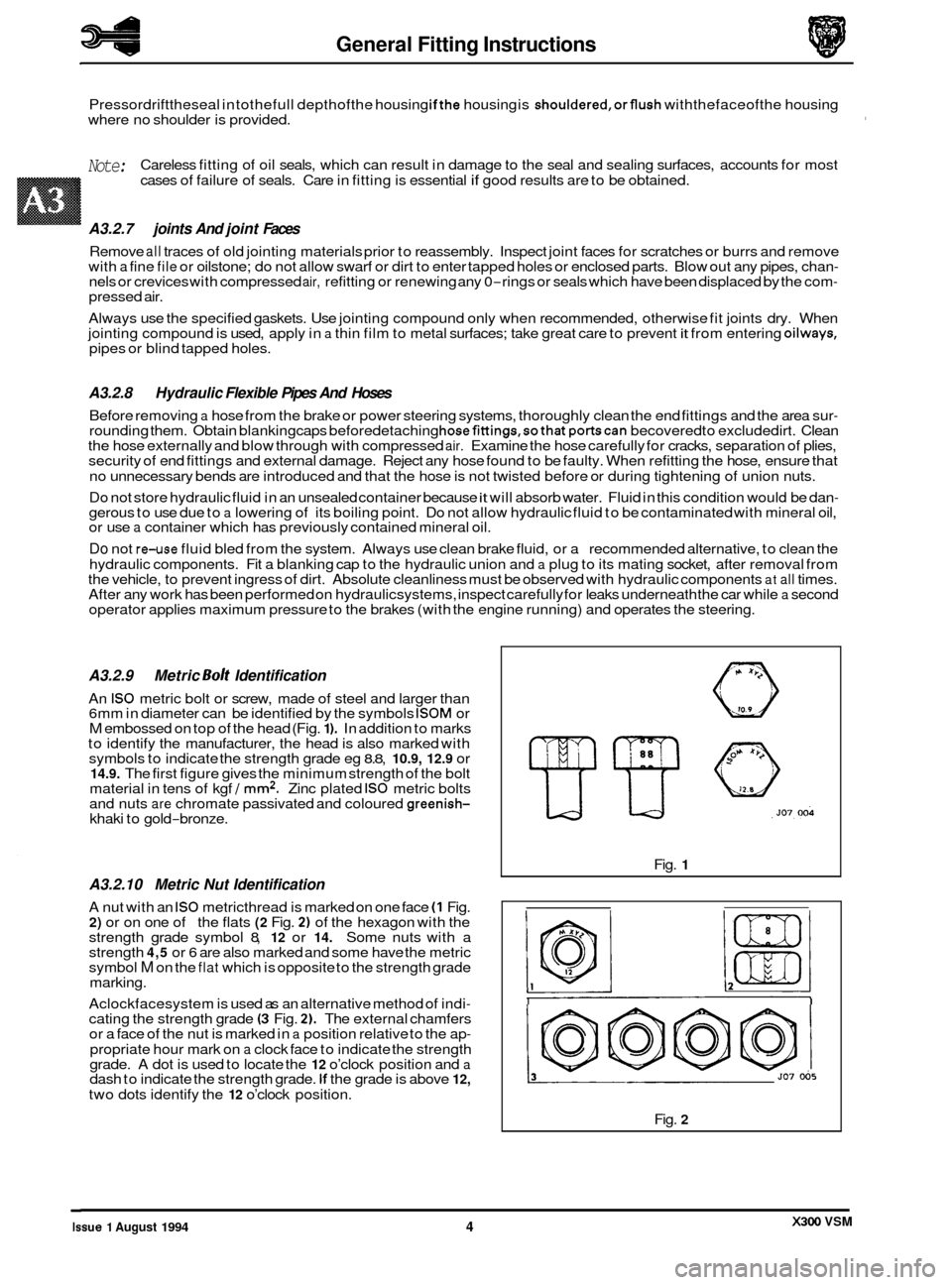
General Fitting Instructions
Pressordrifttheseal in tothefull depthofthe housing ifthe housing is shouldered,orflush withthefaceofthe housing
where no shoulder is provided.
Note: Careless fitting of oil seals, which can result in damage to the seal and sealing surfaces, accounts for most
cases of failure of seals. Care in fitting is essential
if good results are to be obtained.
A3.2.7 joints And joint Faces
Remove all traces of old jointing materials prior to reassembly. Inspect joint faces for scratches or burrs and remove
with a fine file or oilstone; do not allow swarf or dirt to enter tapped holes or enclosed parts. Blow out any pipes, chan- nels or crevices with compressed air, refitting or renewing any 0-rings or seals which have been displaced by the com- pressed air.
Always use the specified gaskets. Use jointing compound only when recommended, otherwise fit joints dry. When
jointing compound is used, apply in
a thin film to metal surfaces; take great care to prevent it from entering oilways, pipes or blind tapped holes.
A3.2.8
Before removing a hose from the brake or power steering systems, thoroughly clean the end fittings and the area sur- rounding them. Obtain blanking caps beforedetaching hosefittings,sothat portscan becovered to excludedirt. Clean
the hose externally and blow through with compressed air. Examine the hose carefully for cracks, separation of plies,
security of end fittings and external damage. Reject any hose found to be faulty. When refitting the hose, ensure that
no unnecessary bends are introduced and that the hose is not twisted before or during tightening of union nuts.
Do not store hydraulic fluid in an unsealed container because it will absorb water. Fluid in this condition would be dan- gerous to use due to a lowering of its boiling point. Do not allow hydraulic fluid to be contaminated with mineral oil,
or use a container which has previously contained mineral oil.
Do not re-use fluid bled from the system. Always use clean brake fluid, or a recommended alternative, to clean the
hydraulic components. Fit a blanking cap to the hydraulic union and
a plug to its mating socket, after removal from
the vehicle, to prevent ingress of dirt. Absolute cleanliness must be observed with hydraulic components at all times.
After any work has been performed on hydraulicsystems, inspect carefully for leaks underneath the car while a second
operator applies maximum pressure to the brakes (with the engine running) and operates the steering.
Hydraulic Flexible Pipes And Hoses
A3.2.9 Metric
Bolt Identification
An IS0 metric bolt or screw, made of steel and larger than
6mm in diameter can be identified by the symbols ISOM or M embossed on top of the head (Fig. 1 ). In addition to marks
to identify the manufacturer, the head is also marked with
symbols to indicate the strength grade eg
8.8, 10.9, 12.9 or 14.9. The first figure gives the minimum strength of the bolt
material in tens of kgf / mm2. Zinc plated IS0 metric bolts
and nuts are chromate passivated and coloured greenish- khaki to gold-bronze.
A3.2.10 Metric Nut Identification
A nut with an IS0 metricthread is marked on one face (1 Fig. 2) or on one of the flats (2 Fig. 2) of the hexagon with the
strength grade symbol 8, 12 or 14. Some nuts with a
strength 4,5 or 6 are also marked and some have the metric
symbol M on the flat which is opposite to the strength grade
marking.
Aclockfacesystem is used as an alternative method of indi
- cating the strength grade (3 Fig. 2). The external chamfers
or a face of the nut is marked in a position relative to the ap-
propriate hour mark on a clock face to indicate the strength
grade. A dot is used to locate the 12 o’clock position and a dash to indicate the strength grade. If the grade is above 12,
two dots identify the 12 o’clock position. Fig.
1
I I
Fig. 2
X300 VSM Issue 1 August 1994 4
Page 418 of 521

- A3.2.19 Unified Thread Identification - Bolts
A circular recess is stamped in the upper surface of the bolt
head (1 Fig. 1).
A3.2.20 Unified Thread Identification - Nuts
A continuous line of circles is stamped on one of the flats of
the hexagon, parallel to the axis of the nut (2 Fig. 1).
A3.2.2 1 Unified Thread Identification - Studs, Brake
Rods, etc.
The component is reduced to the core diameter for a short
length at its extremity (3 Fig. 1).
A3.2.16 Nuts
When tightening a slotted or castellated nut, never slacken it in order to insert the split pin or locking wire, but tighten
it to align the next slot. The exception is in those recommended cases where slackening the nut forms part of an adjust- ment e.g. bearing endfloat or preload adjustment. If difficulty is experienced, alternative washers or nuts should be
selected, or a washer of a different thickness used. Where self-locking nuts have been removed, replace them with
new ones.
A3.2.17 Locking Wire
Fit new locking wire of the correct type to the assemblies incorporating it. Arrange the wire so that its tension tends
to tighten the bolt heads, or nuts, to which it is fitted.
A3.2.18 Screw Threads
Metricthreads to IS0 standards and UNF threads are used. See below forthread identification. Fixings with damaged
threads must always be discarded. Cleaning the threads with a die or tap impairs the strength and closeness of fit and
is not recommended. Always ensure that replacement bolts are of equal strength to those removed. Do not allow oil,
grease or jointing compound to enter blind threaded holes because the hydraulic action which would be generated
when screwing in the bolt or stud could split the housing. Oil the thread lightly before tightening to ensure
a free run- ning thread, except in the case of self locking nuts. Always tighten a nut or bolt to the recommended torque figure.
Damaged or corroded threads will affect the torque reading. To check or retighten a bolt or screw to a specified torque
figure, first slacken by a quarter of a turn, then retighten to the correct figure.
I
7
-3
‘2 507 011
Fig. 1
X300 VSM 7 Issue 1 August 1994