Ref 1 JAGUAR XJ6 1997 2.G Workshop Manual
[x] Cancel search | Manufacturer: JAGUAR, Model Year: 1997, Model line: XJ6, Model: JAGUAR XJ6 1997 2.GPages: 227, PDF Size: 7.2 MB
Page 132 of 227
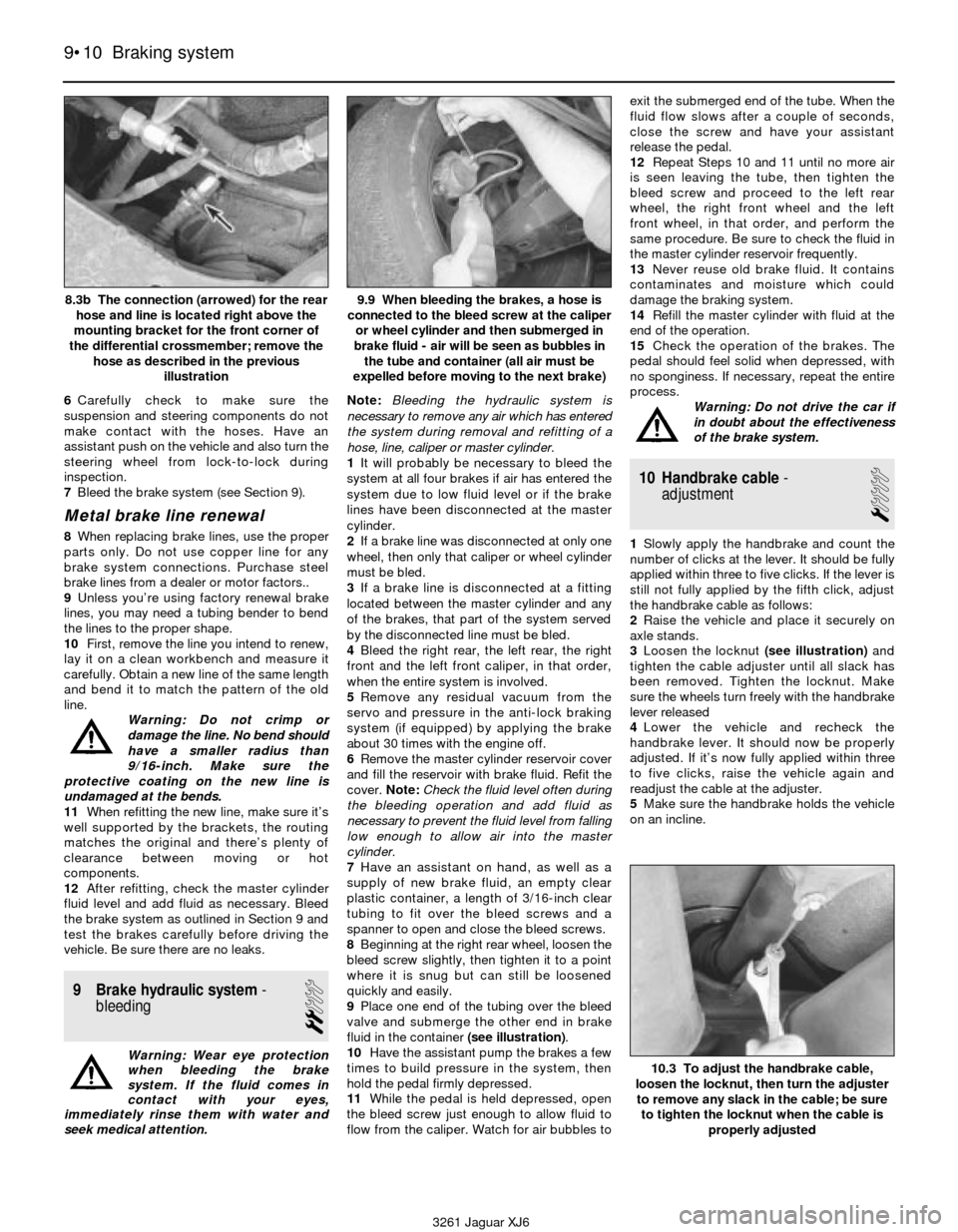
6Carefully check to make sure the
suspension and steering components do not
make contact with the hoses. Have an
assistant push on the vehicle and also turn the
steering wheel from lock-to-lock during
inspection.
7Bleed the brake system (see Section 9).
Metal brake line renewal
8When replacing brake lines, use the proper
parts only. Do not use copper line for any
brake system connections. Purchase steel
brake lines from a dealer or motor factors..
9Unless you’re using factory renewal brake
lines, you may need a tubing bender to bend
the lines to the proper shape.
10First, remove the line you intend to renew,
lay it on a clean workbench and measure it
carefully. Obtain a new line of the same length
and bend it to match the pattern of the old
line.
Warning: Do not crimp or
damage the line. No bend should
have a smaller radius than
9/16-inch. Make sure the
protective coating on the new line is
undamaged at the bends.
11When refitting the new line, make sure it’s
well supported by the brackets, the routing
matches the original and there’s plenty of
clearance between moving or hot
components.
12After refitting, check the master cylinder
fluid level and add fluid as necessary. Bleed
the brake system as outlined in Section 9 and
test the brakes carefully before driving the
vehicle. Be sure there are no leaks.
9 Brake hydraulic system-
bleeding
2
Warning: Wear eye protection
when bleeding the brake
system. If the fluid comes in
contact with your eyes,
immediately rinse them with water and
seek medical attention.Note:Bleeding the hydraulic system is
necessary to remove any air which has entered
the system during removal and refitting of a
hose, line, caliper or master cylinder.
1It will probably be necessary to bleed the
system at all four brakes if air has entered the
system due to low fluid level or if the brake
lines have been disconnected at the master
cylinder.
2If a brake line was disconnected at only one
wheel, then only that caliper or wheel cylinder
must be bled.
3If a brake line is disconnected at a fitting
located between the master cylinder and any
of the brakes, that part of the system served
by the disconnected line must be bled.
4Bleed the right rear, the left rear, the right
front and the left front caliper, in that order,
when the entire system is involved.
5Remove any residual vacuum from the
servo and pressure in the anti-lock braking
system (if equipped) by applying the brake
about 30 times with the engine off.
6Remove the master cylinder reservoir cover
and fill the reservoir with brake fluid. Refit the
cover. Note:Check the fluid level often during
the bleeding operation and add fluid as
necessary to prevent the fluid level from falling
low enough to allow air into the master
cylinder.
7Have an assistant on hand, as well as a
supply of new brake fluid, an empty clear
plastic container, a length of 3/16-inch clear
tubing to fit over the bleed screws and a
spanner to open and close the bleed screws.
8Beginning at the right rear wheel, loosen the
bleed screw slightly, then tighten it to a point
where it is snug but can still be loosened
quickly and easily.
9Place one end of the tubing over the bleed
valve and submerge the other end in brake
fluid in the container (see illustration).
10Have the assistant pump the brakes a few
times to build pressure in the system, then
hold the pedal firmly depressed.
11While the pedal is held depressed, open
the bleed screw just enough to allow fluid to
flow from the caliper. Watch for air bubbles toexit the submerged end of the tube. When the
fluid flow slows after a couple of seconds,
close the screw and have your assistant
release the pedal.
12Repeat Steps 10 and 11 until no more air
is seen leaving the tube, then tighten the
bleed screw and proceed to the left rear
wheel, the right front wheel and the left
front wheel, in that order, and perform the
same procedure. Be sure to check the fluid in
the master cylinder reservoir frequently.
13Never reuse old brake fluid. It contains
contaminates and moisture which could
damage the braking system.
14Refill the master cylinder with fluid at the
end of the operation.
15Check the operation of the brakes. The
pedal should feel solid when depressed, with
no sponginess. If necessary, repeat the entire
process.
Warning: Do not drive the car if
in doubt about the effectiveness
of the brake system.
10 Handbrake cable-
adjustment
1
1Slowly apply the handbrake and count the
number of clicks at the lever. It should be fully
applied within three to five clicks. If the lever is
still not fully applied by the fifth click, adjust
the handbrake cable as follows:
2Raise the vehicle and place it securely on
axle stands.
3Loosen the locknut (see illustration)and
tighten the cable adjuster until all slack has
been removed. Tighten the locknut. Make
sure the wheels turn freely with the handbrake
lever released
4Lower the vehicle and recheck the
handbrake lever. It should now be properly
adjusted. If it’s now fully applied within three
to five clicks, raise the vehicle again and
readjust the cable at the adjuster.
5Make sure the handbrake holds the vehicle
on an incline.
9•10 Braking system
8.3b The connection (arrowed) for the rear
hose and line is located right above the
mounting bracket for the front corner of
the differential crossmember; remove the
hose as described in the previous
illustration9.9 When bleeding the brakes, a hose is
connected to the bleed screw at the caliper
or wheel cylinder and then submerged in
brake fluid - air will be seen as bubbles in
the tube and container (all air must be
expelled before moving to the next brake)
10.3 To adjust the handbrake cable,
loosen the locknut, then turn the adjuster
to remove any slack in the cable; be sure
to tighten the locknut when the cable is
properly adjusted
3261 Jaguar XJ6
Page 133 of 227
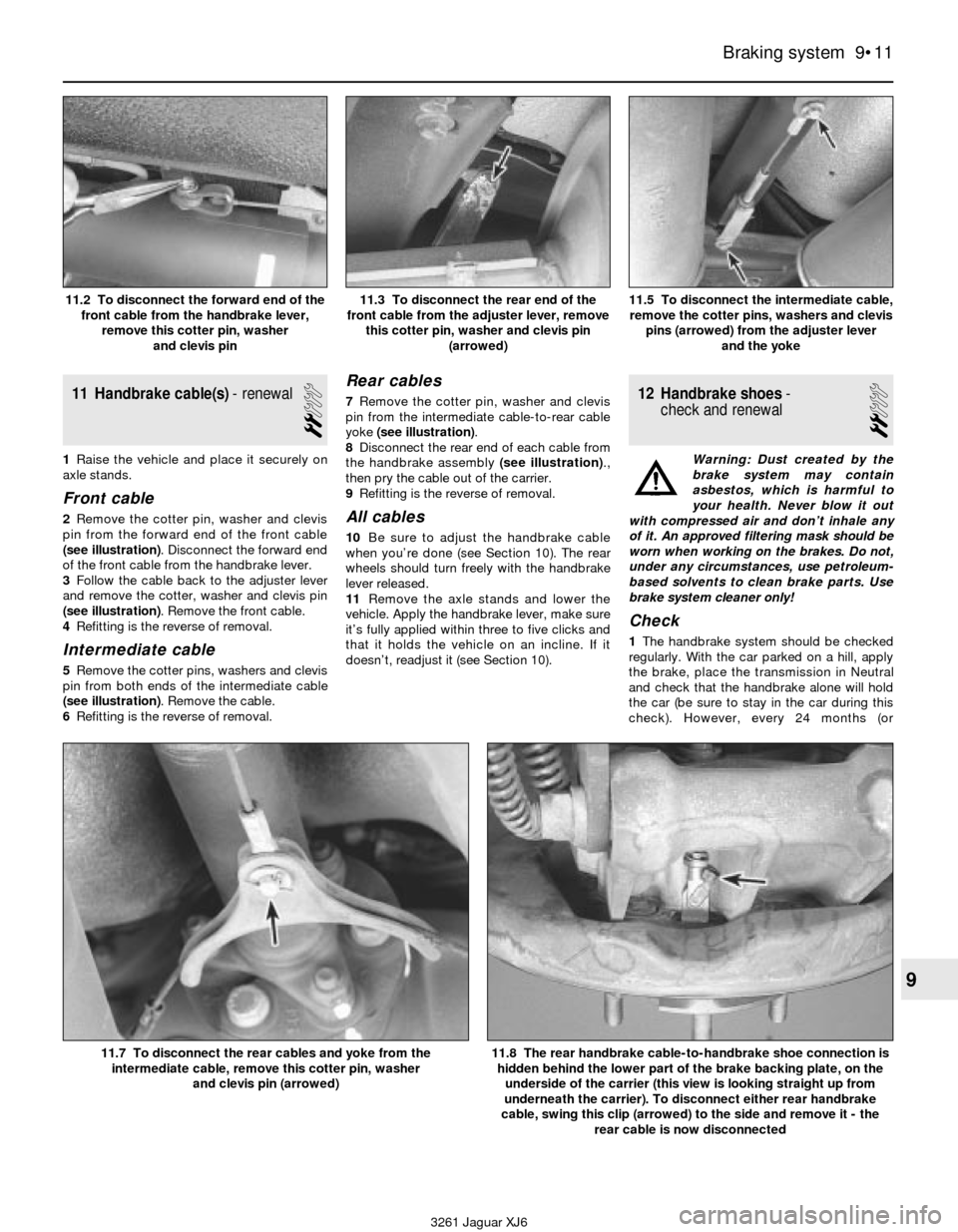
11 Handbrake cable(s)- renewal
2
1Raise the vehicle and place it securely on
axle stands.
Front cable
2Remove the cotter pin, washer and clevis
pin from the forward end of the front cable
(see illustration). Disconnect the forward end
of the front cable from the handbrake lever.
3Follow the cable back to the adjuster lever
and remove the cotter, washer and clevis pin
(see illustration). Remove the front cable.
4Refitting is the reverse of removal.
Intermediate cable
5Remove the cotter pins, washers and clevis
pin from both ends of the intermediate cable
(see illustration). Remove the cable.
6Refitting is the reverse of removal.
Rear cables
7Remove the cotter pin, washer and clevis
pin from the intermediate cable-to-rear cable
yoke (see illustration).
8Disconnect the rear end of each cable from
the handbrake assembly (see illustration).,
then pry the cable out of the carrier.
9Refitting is the reverse of removal.
All cables
10Be sure to adjust the handbrake cable
when you’re done (see Section 10). The rear
wheels should turn freely with the handbrake
lever released.
11Remove the axle stands and lower the
vehicle. Apply the handbrake lever, make sure
it’s fully applied within three to five clicks and
that it holds the vehicle on an incline. If it
doesn’t, readjust it (see Section 10).
12 Handbrake shoes-
check and renewal
2
Warning: Dust created by the
brake system may contain
asbestos, which is harmful to
your health. Never blow it out
with compressed air and don’t inhale any
of it. An approved filtering mask should be
worn when working on the brakes. Do not,
under any circumstances, use petroleum-
based solvents to clean brake parts. Use
brake system cleaner only!
Check
1The handbrake system should be checked
regularly. With the car parked on a hill, apply
the brake, place the transmission in Neutral
and check that the handbrake alone will hold
the car (be sure to stay in the car during this
check). However, every 24 months (or
Braking system 9•11
9
3261 Jaguar XJ6 11.2 To disconnect the forward end of the
front cable from the handbrake lever,
remove this cotter pin, washer
and clevis pin
11.3 To disconnect the rear end of the
front cable from the adjuster lever, remove
this cotter pin, washer and clevis pin
(arrowed)11.5 To disconnect the intermediate cable,
remove the cotter pins, washers and clevis
pins (arrowed) from the adjuster lever
and the yoke
11.7 To disconnect the rear cables and yoke from the
intermediate cable, remove this cotter pin, washer
and clevis pin (arrowed)11.8 The rear handbrake cable-to-handbrake shoe connection is
hidden behind the lower part of the brake backing plate, on the
underside of the carrier (this view is looking straight up from
underneath the carrier). To disconnect either rear handbrake
cable, swing this clip (arrowed) to the side and remove it - the
rear cable is now disconnected
Page 135 of 227
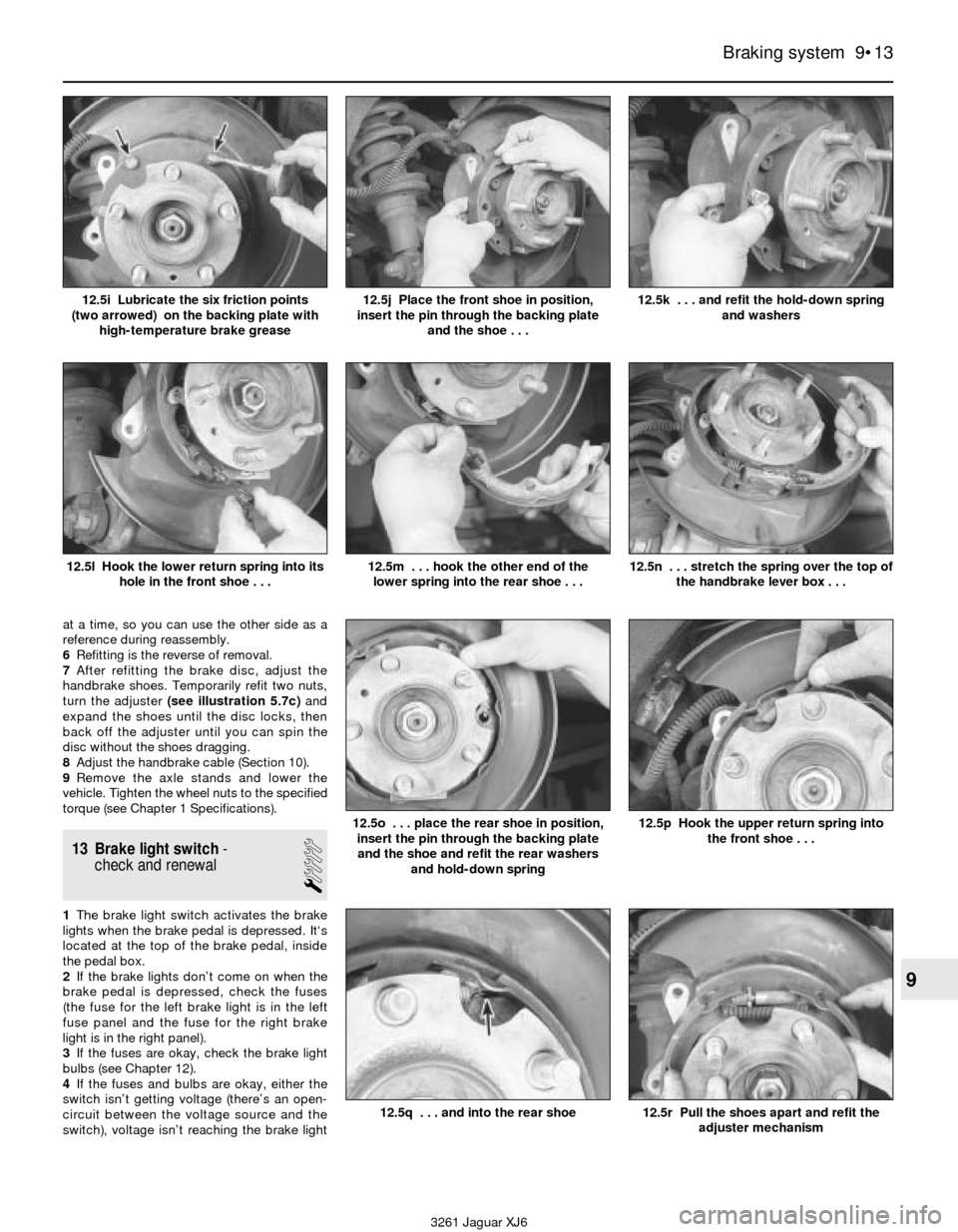
at a time, so you can use the other side as a
reference during reassembly.
6Refitting is the reverse of removal.
7After refitting the brake disc, adjust the
handbrake shoes. Temporarily refit two nuts,
turn the adjuster (see illustration 5.7c)and
expand the shoes until the disc locks, then
back off the adjuster until you can spin the
disc without the shoes dragging.
8Adjust the handbrake cable (Section 10).
9Remove the axle stands and lower the
vehicle. Tighten the wheel nuts to the specified
torque (see Chapter 1 Specifications).
13 Brake light switch-
check and renewal
1
1The brake light switch activates the brake
lights when the brake pedal is depressed. It‘s
located at the top of the brake pedal, inside
the pedal box.
2If the brake lights don’t come on when the
brake pedal is depressed, check the fuses
(the fuse for the left brake light is in the left
fuse panel and the fuse for the right brake
light is in the right panel).
3If the fuses are okay, check the brake light
bulbs (see Chapter 12).
4If the fuses and bulbs are okay, either the
switch isn’t getting voltage (there’s an open-
circuit between the voltage source and the
switch), voltage isn’t reaching the brake light
Braking system 9•13
9
12.5j Place the front shoe in position,
insert the pin through the backing plate
and the shoe . . .12.5k . . . and refit the hold-down spring
and washers12.5i Lubricate the six friction points
(two arrowed) on the backing plate with
high-temperature brake grease
3261 Jaguar XJ6 12.5l Hook the lower return spring into its
hole in the front shoe . . .
12.5m . . . hook the other end of the
lower spring into the rear shoe . . .12.5n . . . stretch the spring over the top of
the handbrake lever box . . .
12.5o . . . place the rear shoe in position,
insert the pin through the backing plate
and the shoe and refit the rear washers
and hold-down spring12.5p Hook the upper return spring into
the front shoe . . .
12.5q . . . and into the rear shoe12.5r Pull the shoes apart and refit the
adjuster mechanism
Page 136 of 227
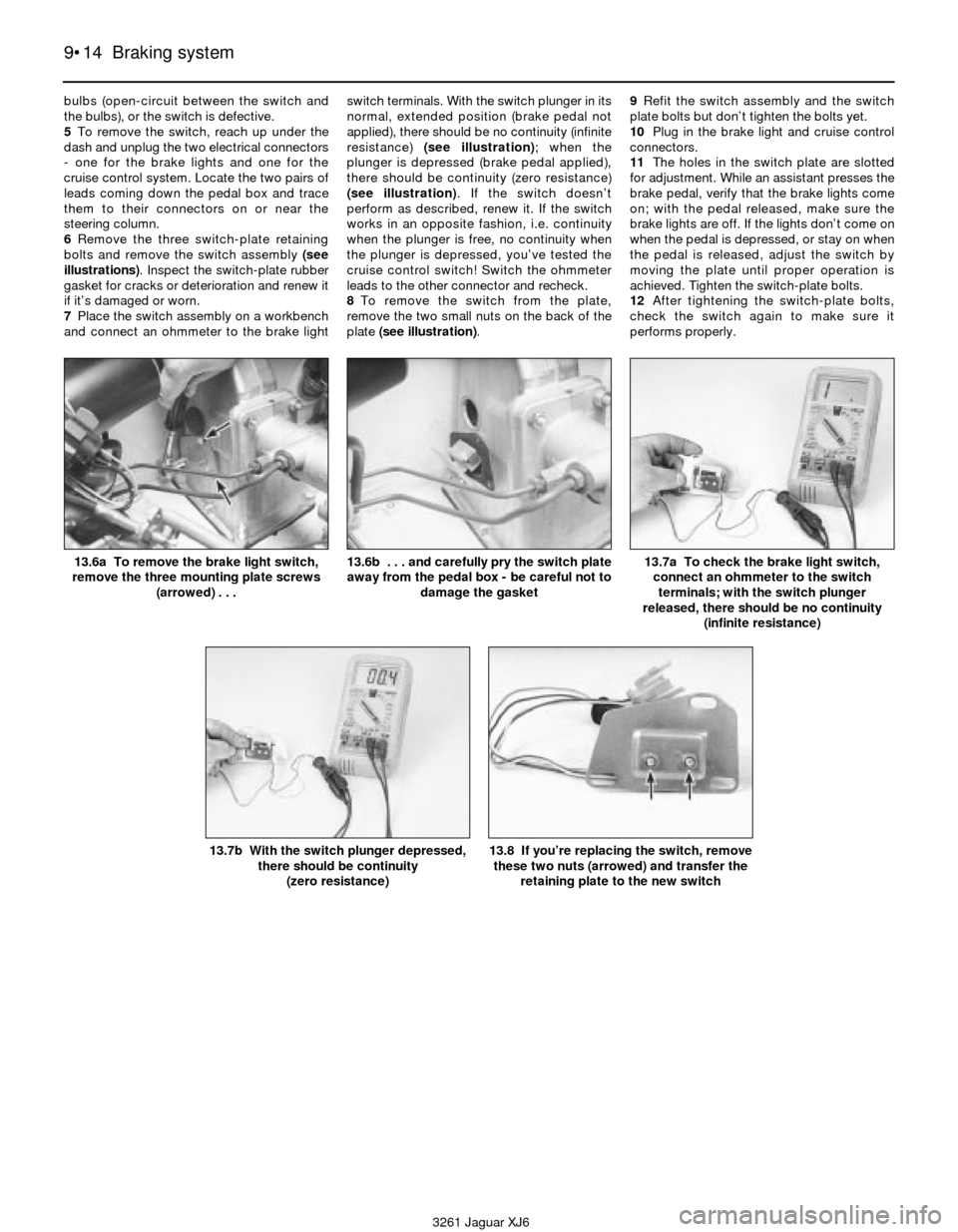
bulbs (open-circuit between the switch and
the bulbs), or the switch is defective.
5To remove the switch, reach up under the
dash and unplug the two electrical connectors
- one for the brake lights and one for the
cruise control system. Locate the two pairs of
leads coming down the pedal box and trace
them to their connectors on or near the
steering column.
6Remove the three switch-plate retaining
bolts and remove the switch assembly (see
illustrations). Inspect the switch-plate rubber
gasket for cracks or deterioration and renew it
if it’s damaged or worn.
7Place the switch assembly on a workbench
and connect an ohmmeter to the brake lightswitch terminals. With the switch plunger in its
normal, extended position (brake pedal not
applied), there should be no continuity (infinite
resistance) (see illustration); when the
plunger is depressed (brake pedal applied),
there should be continuity (zero resistance)
(see illustration). If the switch doesn’t
perform as described, renew it. If the switch
works in an opposite fashion, i.e. continuity
when the plunger is free, no continuity when
the plunger is depressed, you’ve tested the
cruise control switch! Switch the ohmmeter
leads to the other connector and recheck.
8To remove the switch from the plate,
remove the two small nuts on the back of the
plate (see illustration).9Refit the switch assembly and the switch
plate bolts but don’t tighten the bolts yet.
10Plug in the brake light and cruise control
connectors.
11The holes in the switch plate are slotted
for adjustment. While an assistant presses the
brake pedal, verify that the brake lights come
on; with the pedal released, make sure the
brake lights are off. If the lights don’t come on
when the pedal is depressed, or stay on when
the pedal is released, adjust the switch by
moving the plate until proper operation is
achieved. Tighten the switch-plate bolts.
12After tightening the switch-plate bolts,
check the switch again to make sure it
performs properly.
9•14 Braking system
13.6a To remove the brake light switch,
remove the three mounting plate screws
(arrowed) . . .13.6b . . . and carefully pry the switch plate
away from the pedal box - be careful not to
damage the gasket13.7a To check the brake light switch,
connect an ohmmeter to the switch
terminals; with the switch plunger
released, there should be no continuity
(infinite resistance)
13.7b With the switch plunger depressed,
there should be continuity
(zero resistance)13.8 If you’re replacing the switch, remove
these two nuts (arrowed) and transfer the
retaining plate to the new switch
3261 Jaguar XJ6
Page 137 of 227
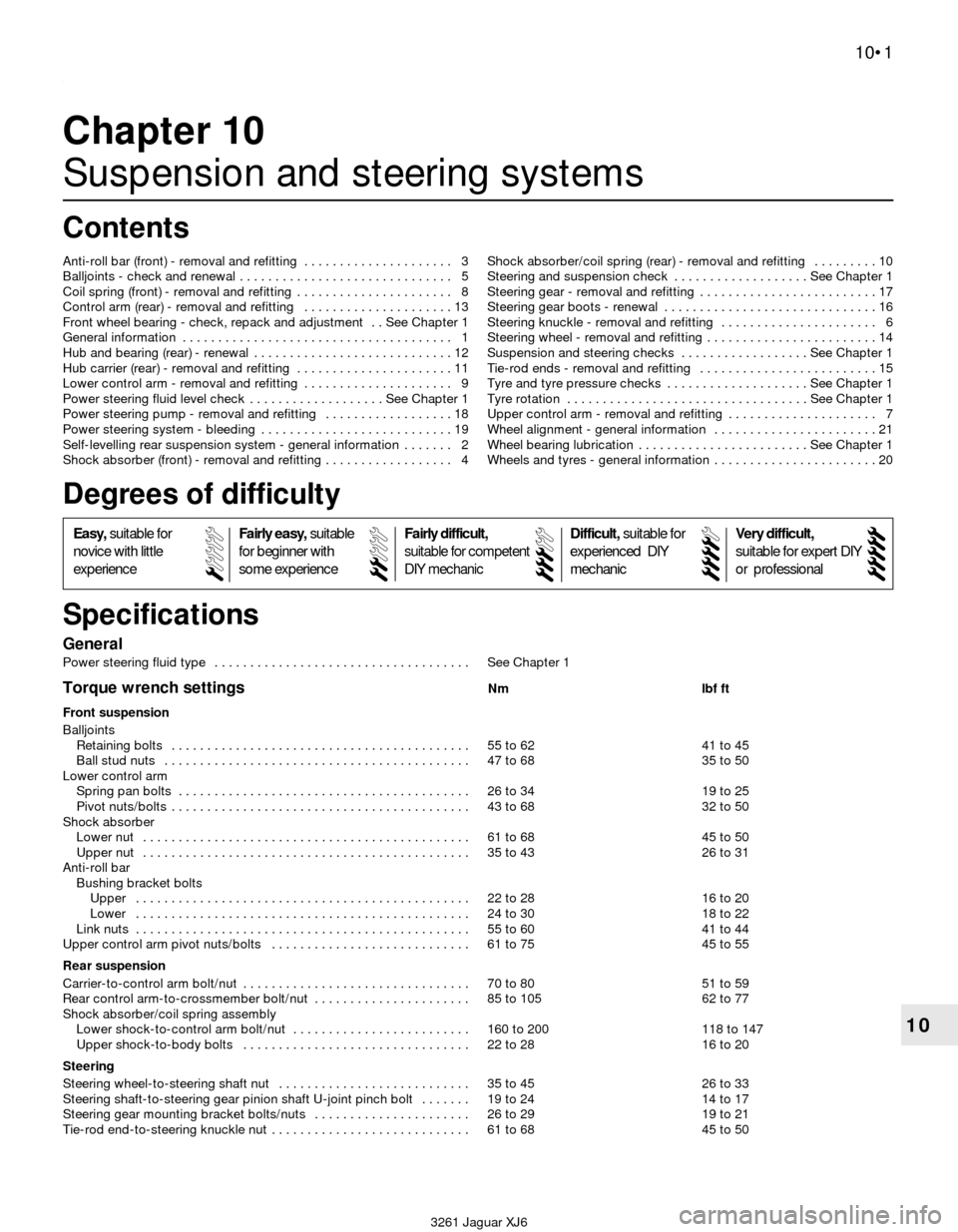
3261 Jaguar XJ6
10
Chapter 10
Suspension and steering systems
General
Power steering fluid type . . . . . . . . . . . . . . . . . . . . . . . . . . . . . . . . . . . . See Chapter 1
Torque wrench settingsNm lbf ft
Front suspension
Balljoints
Retaining bolts . . . . . . . . . . . . . . . . . . . . . . . . . . . . . . . . . . . . . . . . . . 55 to 62 41 to 45
Ball stud nuts . . . . . . . . . . . . . . . . . . . . . . . . . . . . . . . . . . . . . . . . . . . 47 to 68 35 to 50
Lower control arm
Spring pan bolts . . . . . . . . . . . . . . . . . . . . . . . . . . . . . . . . . . . . . . . . . 26 to 34 19 to 25
Pivot nuts/bolts . . . . . . . . . . . . . . . . . . . . . . . . . . . . . . . . . . . . . . . . . . 43 to 68 32 to 50
Shock absorber
Lower nut . . . . . . . . . . . . . . . . . . . . . . . . . . . . . . . . . . . . . . . . . . . . . . 61 to 68 45 to 50
Upper nut . . . . . . . . . . . . . . . . . . . . . . . . . . . . . . . . . . . . . . . . . . . . . . 35 to 43 26 to 31
Anti-roll bar
Bushing bracket bolts
Upper . . . . . . . . . . . . . . . . . . . . . . . . . . . . . . . . . . . . . . . . . . . . . . . 22 to 28 16 to 20
Lower . . . . . . . . . . . . . . . . . . . . . . . . . . . . . . . . . . . . . . . . . . . . . . . 24 to 30 18 to 22
Link nuts . . . . . . . . . . . . . . . . . . . . . . . . . . . . . . . . . . . . . . . . . . . . . . . 55 to 60 41 to 44
Upper control arm pivot nuts/bolts . . . . . . . . . . . . . . . . . . . . . . . . . . . . 61 to 75 45 to 55
Rear suspension
Carrier-to-control arm bolt/nut . . . . . . . . . . . . . . . . . . . . . . . . . . . . . . . . 70 to 80 51 to 59
Rear control arm-to-crossmember bolt/nut . . . . . . . . . . . . . . . . . . . . . . 85 to 105 62 to 77
Shock absorber/coil spring assembly
Lower shock-to-control arm bolt/nut . . . . . . . . . . . . . . . . . . . . . . . . . 160 to 200 118 to 147
Upper shock-to-body bolts . . . . . . . . . . . . . . . . . . . . . . . . . . . . . . . . 22 to 28 16 to 20
Steering
Steering wheel-to-steering shaft nut . . . . . . . . . . . . . . . . . . . . . . . . . . . 35 to 45 26 to 33
Steering shaft-to-steering gear pinion shaft U-joint pinch bolt . . . . . . . 19 to 24 14 to 17
Steering gear mounting bracket bolts/nuts . . . . . . . . . . . . . . . . . . . . . . 26 to 29 19 to 21
Tie-rod end-to-steering knuckle nut . . . . . . . . . . . . . . . . . . . . . . . . . . . . 61 to 68 45 to 50 Anti-roll bar (front) - removal and refitting . . . . . . . . . . . . . . . . . . . . . 3
Balljoints - check and renewal . . . . . . . . . . . . . . . . . . . . . . . . . . . . . . 5
Coil spring (front) - removal and refitting . . . . . . . . . . . . . . . . . . . . . . 8
Control arm (rear) - removal and refitting . . . . . . . . . . . . . . . . . . . . . 13
Front wheel bearing - check, repack and adjustment . . See Chapter 1
General information . . . . . . . . . . . . . . . . . . . . . . . . . . . . . . . . . . . . . . 1
Hub and bearing (rear) - renewal . . . . . . . . . . . . . . . . . . . . . . . . . . . . 12
Hub carrier (rear) - removal and refitting . . . . . . . . . . . . . . . . . . . . . . 11
Lower control arm - removal and refitting . . . . . . . . . . . . . . . . . . . . . 9
Power steering fluid level check . . . . . . . . . . . . . . . . . . . See Chapter 1
Power steering pump - removal and refitting . . . . . . . . . . . . . . . . . . 18
Power steering system - bleeding . . . . . . . . . . . . . . . . . . . . . . . . . . . 19
Self-levelling rear suspension system - general information . . . . . . . 2
Shock absorber (front) - removal and refitting . . . . . . . . . . . . . . . . . . 4Shock absorber/coil spring (rear) - removal and refitting . . . . . . . . . 10
Steering and suspension check . . . . . . . . . . . . . . . . . . . See Chapter 1
Steering gear - removal and refitting . . . . . . . . . . . . . . . . . . . . . . . . . 17
Steering gear boots - renewal . . . . . . . . . . . . . . . . . . . . . . . . . . . . . . 16
Steering knuckle - removal and refitting . . . . . . . . . . . . . . . . . . . . . . 6
Steering wheel - removal and refitting . . . . . . . . . . . . . . . . . . . . . . . . 14
Suspension and steering checks . . . . . . . . . . . . . . . . . . See Chapter 1
Tie-rod ends - removal and refitting . . . . . . . . . . . . . . . . . . . . . . . . . 15
Tyre and tyre pressure checks . . . . . . . . . . . . . . . . . . . . See Chapter 1
Tyre rotation . . . . . . . . . . . . . . . . . . . . . . . . . . . . . . . . . . See Chapter 1
Upper control arm - removal and refitting . . . . . . . . . . . . . . . . . . . . . 7
Wheel alignment - general information . . . . . . . . . . . . . . . . . . . . . . . 21
Wheel bearing lubrication . . . . . . . . . . . . . . . . . . . . . . . . See Chapter 1
Wheels and tyres - general information . . . . . . . . . . . . . . . . . . . . . . . 20
10•1
Specifications Contents
Easy,suitable for
novice with little
experienceFairly easy,suitable
for beginner with
some experienceFairly difficult,
suitable for competent
DIY mechanic
Difficult,suitable for
experienced DIY
mechanicVery difficult,
suitable for expert DIY
or professional
Degrees of difficulty
54321
Page 139 of 227
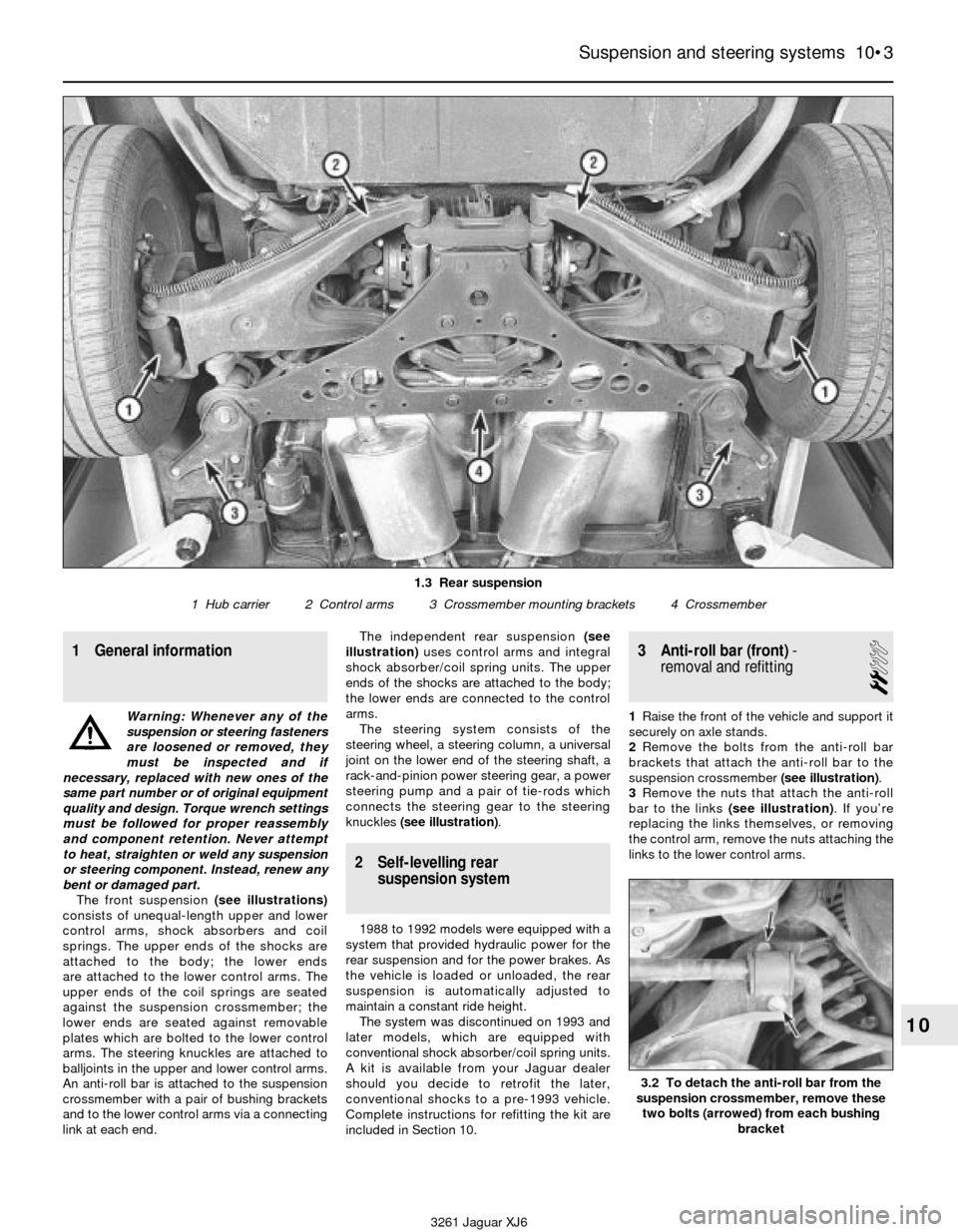
1 General information
Warning: Whenever any of the
suspension or steering fasteners
are loosened or removed, they
must be inspected and if
necessary, replaced with new ones of the
same part number or of original equipment
quality and design. Torque wrench settings
must be followed for proper reassembly
and component retention. Never attempt
to heat, straighten or weld any suspension
or steering component. Instead, renew any
bent or damaged part.
The front suspension (see illustrations)
consists of unequal-length upper and lower
control arms, shock absorbers and coil
springs. The upper ends of the shocks are
attached to the body; the lower ends
are attached to the lower control arms. The
upper ends of the coil springs are seated
against the suspension crossmember; the
lower ends are seated against removable
plates which are bolted to the lower control
arms. The steering knuckles are attached to
balljoints in the upper and lower control arms.
An anti-roll bar is attached to the suspension
crossmember with a pair of bushing brackets
and to the lower control arms via a connecting
link at each end.The independent rear suspension (see
illustration)uses control arms and integral
shock absorber/coil spring units. The upper
ends of the shocks are attached to the body;
the lower ends are connected to the control
arms.
The steering system consists of the
steering wheel, a steering column, a universal
joint on the lower end of the steering shaft, a
rack-and-pinion power steering gear, a power
steering pump and a pair of tie-rods which
connects the steering gear to the steering
knuckles (see illustration).
2 Self-levelling rear
suspension system
1988 to 1992 models were equipped with a
system that provided hydraulic power for the
rear suspension and for the power brakes. As
the vehicle is loaded or unloaded, the rear
suspension is automatically adjusted to
maintain a constant ride height.
The system was discontinued on 1993 and
later models, which are equipped with
conventional shock absorber/coil spring units.
A kit is available from your Jaguar dealer
should you decide to retrofit the later,
conventional shocks to a pre-1993 vehicle.
Complete instructions for refitting the kit are
included in Section 10.
3 Anti-roll bar (front)-
removal and refitting
2
1Raise the front of the vehicle and support it
securely on axle stands.
2Remove the bolts from the anti-roll bar
brackets that attach the anti-roll bar to the
suspension crossmember (see illustration).
3Remove the nuts that attach the anti-roll
bar to the links (see illustration). If you’re
replacing the links themselves, or removing
the control arm, remove the nuts attaching the
links to the lower control arms.
Suspension and steering systems 10•3
10
1.3 Rear suspension
1 Hub carrier 2 Control arms 3 Crossmember mounting brackets 4 Crossmember
3.2 To detach the anti-roll bar from the
suspension crossmember, remove these
two bolts (arrowed) from each bushing
bracket
3261 Jaguar XJ6
Page 140 of 227
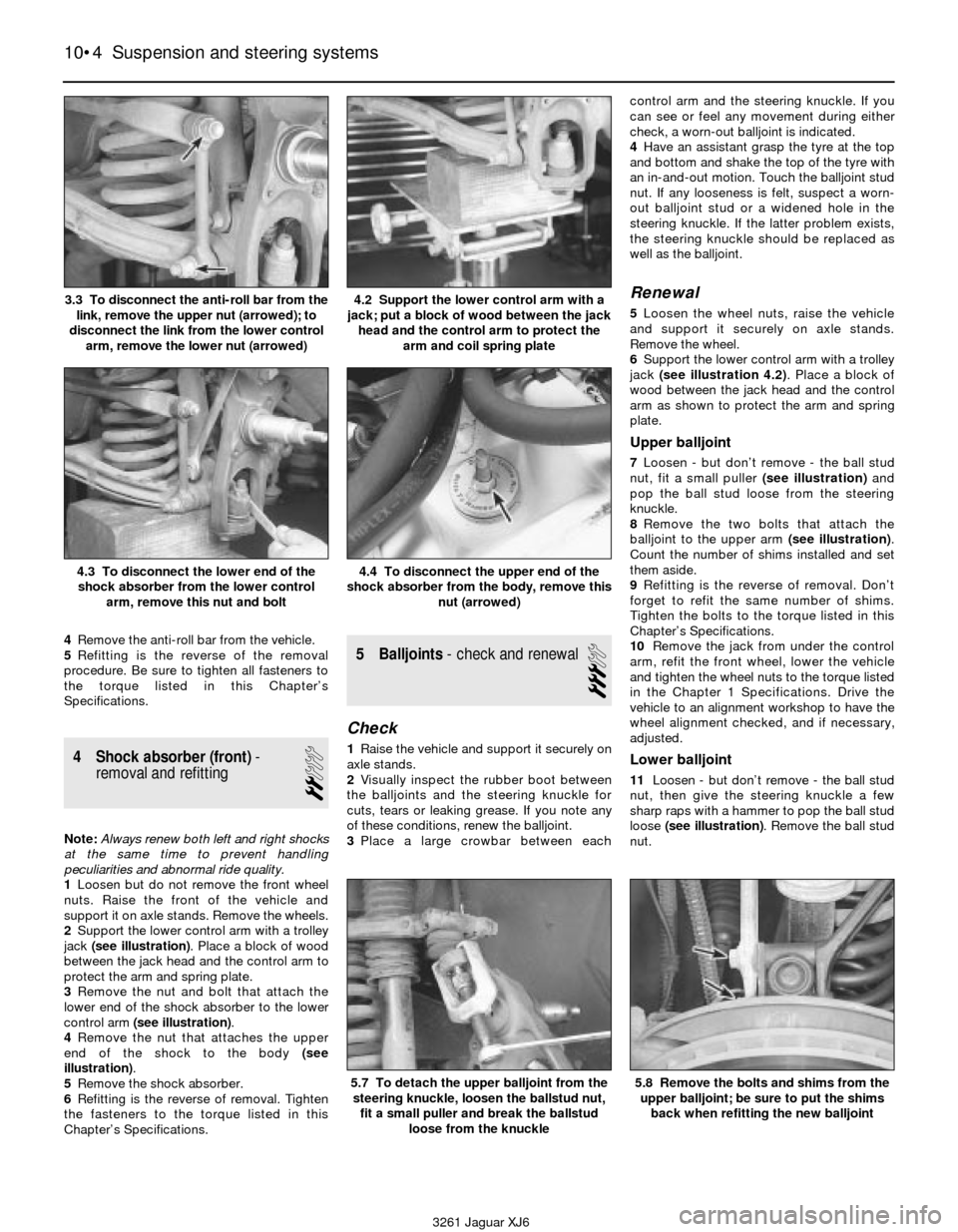
4Remove the anti-roll bar from the vehicle.
5Refitting is the reverse of the removal
procedure. Be sure to tighten all fasteners to
the torque listed in this Chapter’s
Specifications.
4 Shock absorber (front)-
removal and refitting
2
Note: Always renew both left and right shocks
at the same time to prevent handling
peculiarities and abnormal ride quality.
1Loosen but do not remove the front wheel
nuts. Raise the front of the vehicle and
support it on axle stands. Remove the wheels.
2Support the lower control arm with a trolley
jack (see illustration). Place a block of wood
between the jack head and the control arm to
protect the arm and spring plate.
3Remove the nut and bolt that attach the
lower end of the shock absorber to the lower
control arm (see illustration).
4Remove the nut that attaches the upper
end of the shock to the body (see
illustration).
5Remove the shock absorber.
6Refitting is the reverse of removal. Tighten
the fasteners to the torque listed in this
Chapter’s Specifications.
5 Balljoints- check and renewal
3
Check
1Raise the vehicle and support it securely on
axle stands.
2Visually inspect the rubber boot between
the balljoints and the steering knuckle for
cuts, tears or leaking grease. If you note any
of these conditions, renew the balljoint.
3Place a large crowbar between eachcontrol arm and the steering knuckle. If you
can see or feel any movement during either
check, a worn-out balljoint is indicated.
4Have an assistant grasp the tyre at the top
and bottom and shake the top of the tyre with
an in-and-out motion. Touch the balljoint stud
nut. If any looseness is felt, suspect a worn-
out balljoint stud or a widened hole in the
steering knuckle. If the latter problem exists,
the steering knuckle should be replaced as
well as the balljoint.
Renewal
5Loosen the wheel nuts, raise the vehicle
and support it securely on axle stands.
Remove the wheel.
6Support the lower control arm with a trolley
jack (see illustration 4.2). Place a block of
wood between the jack head and the control
arm as shown to protect the arm and spring
plate.
Upper balljoint
7Loosen - but don’t remove - the ball stud
nut, fit a small puller (see illustration)and
pop the ball stud loose from the steering
knuckle.
8Remove the two bolts that attach the
balljoint to the upper arm (see illustration).
Count the number of shims installed and set
them aside.
9Refitting is the reverse of removal. Don’t
forget to refit the same number of shims.
Tighten the bolts to the torque listed in this
Chapter’s Specifications.
10Remove the jack from under the control
arm, refit the front wheel, lower the vehicle
and tighten the wheel nuts to the torque listed
in the Chapter 1 Specifications. Drive the
vehicle to an alignment workshop to have the
wheel alignment checked, and if necessary,
adjusted.
Lower balljoint
11Loosen - but don’t remove - the ball stud
nut, then give the steering knuckle a few
sharp raps with a hammer to pop the ball stud
loose (see illustration). Remove the ball stud
nut.
10•4 Suspension and steering systems
3.3 To disconnect the anti-roll bar from the
link, remove the upper nut (arrowed); to
disconnect the link from the lower control
arm, remove the lower nut (arrowed)4.2 Support the lower control arm with a
jack; put a block of wood between the jack
head and the control arm to protect the
arm and coil spring plate
4.3 To disconnect the lower end of the
shock absorber from the lower control
arm, remove this nut and bolt4.4 To disconnect the upper end of the
shock absorber from the body, remove this
nut (arrowed)
5.7 To detach the upper balljoint from the
steering knuckle, loosen the ballstud nut,
fit a small puller and break the ballstud
loose from the knuckle5.8 Remove the bolts and shims from the
upper balljoint; be sure to put the shims
back when refitting the new balljoint
3261 Jaguar XJ6
Page 141 of 227
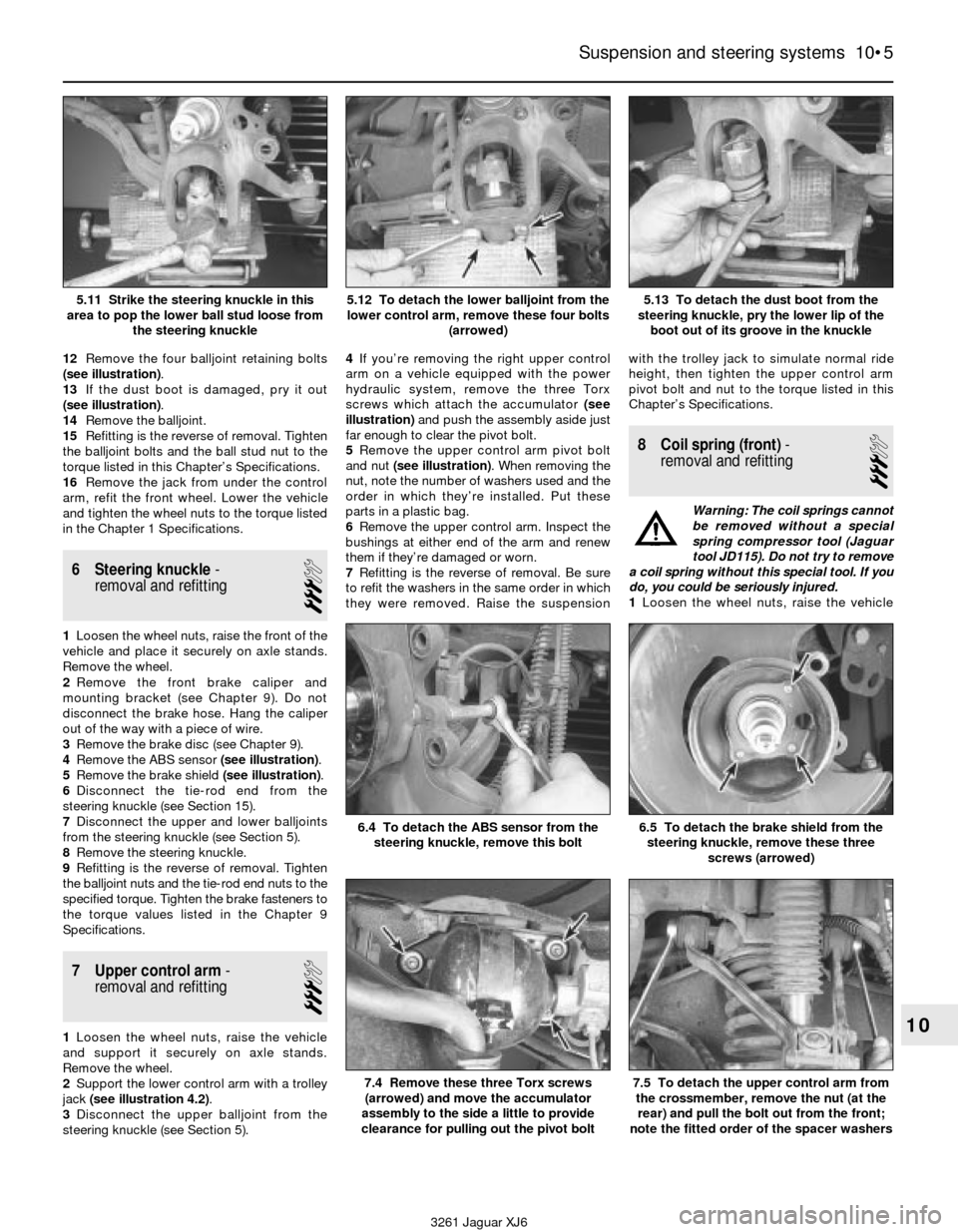
12Remove the four balljoint retaining bolts
(see illustration).
13If the dust boot is damaged, pry it out
(see illustration).
14Remove the balljoint.
15Refitting is the reverse of removal. Tighten
the balljoint bolts and the ball stud nut to the
torque listed in this Chapter’s Specifications.
16Remove the jack from under the control
arm, refit the front wheel. Lower the vehicle
and tighten the wheel nuts to the torque listed
in the Chapter 1 Specifications.
6 Steering knuckle-
removal and refitting
3
1Loosen the wheel nuts, raise the front of the
vehicle and place it securely on axle stands.
Remove the wheel.
2Remove the front brake caliper and
mounting bracket (see Chapter 9). Do not
disconnect the brake hose. Hang the caliper
out of the way with a piece of wire.
3Remove the brake disc (see Chapter 9).
4Remove the ABS sensor (see illustration).
5Remove the brake shield (see illustration).
6Disconnect the tie-rod end from the
steering knuckle (see Section 15).
7Disconnect the upper and lower balljoints
from the steering knuckle (see Section 5).
8Remove the steering knuckle.
9Refitting is the reverse of removal. Tighten
the balljoint nuts and the tie-rod end nuts to the
specified torque. Tighten the brake fasteners to
the torque values listed in the Chapter 9
Specifications.
7 Upper control arm-
removal and refitting
3
1Loosen the wheel nuts, raise the vehicle
and support it securely on axle stands.
Remove the wheel.
2Support the lower control arm with a trolley
jack (see illustration 4.2).
3Disconnect the upper balljoint from the
steering knuckle (see Section 5).4If you’re removing the right upper control
arm on a vehicle equipped with the power
hydraulic system, remove the three Torx
screws which attach the accumulator (see
illustration)and push the assembly aside just
far enough to clear the pivot bolt.
5Remove the upper control arm pivot bolt
and nut (see illustration). When removing the
nut, note the number of washers used and the
order in which they’re installed. Put these
parts in a plastic bag.
6Remove the upper control arm. Inspect the
bushings at either end of the arm and renew
them if they’re damaged or worn.
7Refitting is the reverse of removal. Be sure
to refit the washers in the same order in which
they were removed. Raise the suspensionwith the trolley jack to simulate normal ride
height, then tighten the upper control arm
pivot bolt and nut to the torque listed in this
Chapter’s Specifications.
8 Coil spring (front)-
removal and refitting
3
Warning: The coil springs cannot
be removed without a special
spring compressor tool (Jaguar
tool JD115). Do not try to remove
a coil spring without this special tool. If you
do, you could be seriously injured.
1Loosen the wheel nuts, raise the vehicle
Suspension and steering systems 10•5
10
5.11 Strike the steering knuckle in this
area to pop the lower ball stud loose from
the steering knuckle5.12 To detach the lower balljoint from the
lower control arm, remove these four bolts
(arrowed)5.13 To detach the dust boot from the
steering knuckle, pry the lower lip of the
boot out of its groove in the knuckle
6.5 To detach the brake shield from the
steering knuckle, remove these three
screws (arrowed)6.4 To detach the ABS sensor from the
steering knuckle, remove this bolt
7.4 Remove these three Torx screws
(arrowed) and move the accumulator
assembly to the side a little to provide
clearance for pulling out the pivot bolt7.5 To detach the upper control arm from
the crossmember, remove the nut (at the
rear) and pull the bolt out from the front;
note the fitted order of the spacer washers
3261 Jaguar XJ6
Page 142 of 227
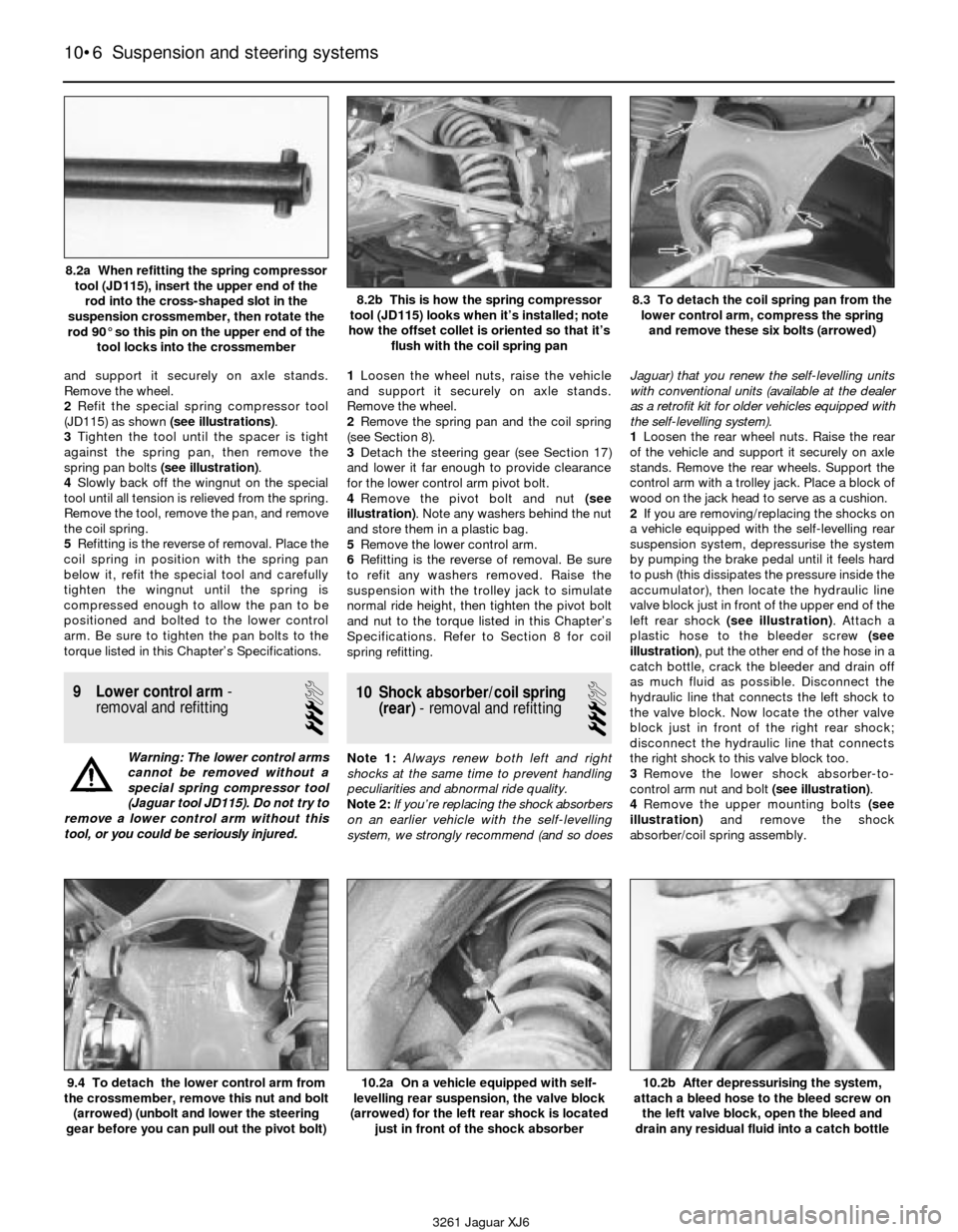
and support it securely on axle stands.
Remove the wheel.
2Refit the special spring compressor tool
(JD115) as shown (see illustrations).
3Tighten the tool until the spacer is tight
against the spring pan, then remove the
spring pan bolts (see illustration).
4Slowly back off the wingnut on the special
tool until all tension is relieved from the spring.
Remove the tool, remove the pan, and remove
the coil spring.
5Refitting is the reverse of removal. Place the
coil spring in position with the spring pan
below it, refit the special tool and carefully
tighten the wingnut until the spring is
compressed enough to allow the pan to be
positioned and bolted to the lower control
arm. Be sure to tighten the pan bolts to the
torque listed in this Chapter’s Specifications.
9 Lower control arm-
removal and refitting
3
Warning: The lower control arms
cannot be removed without a
special spring compressor tool
(Jaguar tool JD115). Do not try to
remove a lower control arm without this
tool, or you could be seriously injured.1Loosen the wheel nuts, raise the vehicle
and support it securely on axle stands.
Remove the wheel.
2Remove the spring pan and the coil spring
(see Section 8).
3Detach the steering gear (see Section 17)
and lower it far enough to provide clearance
for the lower control arm pivot bolt.
4Remove the pivot bolt and nut (see
illustration). Note any washers behind the nut
and store them in a plastic bag.
5Remove the lower control arm.
6Refitting is the reverse of removal. Be sure
to refit any washers removed. Raise the
suspension with the trolley jack to simulate
normal ride height, then tighten the pivot bolt
and nut to the torque listed in this Chapter’s
Specifications. Refer to Section 8 for coil
spring refitting.
10 Shock absorber/coil spring
(rear)- removal and refitting
3
Note 1: Always renew both left and right
shocks at the same time to prevent handling
peculiarities and abnormal ride quality.
Note 2:If you’re replacing the shock absorbers
on an earlier vehicle with the self-levelling
system, we strongly recommend (and so doesJaguar) that you renew the self-levelling units
with conventional units (available at the dealer
as a retrofit kit for older vehicles equipped with
the self-levelling system).
1Loosen the rear wheel nuts. Raise the rear
of the vehicle and support it securely on axle
stands. Remove the rear wheels. Support the
control arm with a trolley jack. Place a block of
wood on the jack head to serve as a cushion.
2If you are removing/replacing the shocks on
a vehicle equipped with the self-levelling rear
suspension system, depressurise the system
by pumping the brake pedal until it feels hard
to push (this dissipates the pressure inside the
accumulator), then locate the hydraulic line
valve block just in front of the upper end of the
left rear shock (see illustration). Attach a
plastic hose to the bleeder screw (see
illustration), put the other end of the hose in a
catch bottle, crack the bleeder and drain off
as much fluid as possible. Disconnect the
hydraulic line that connects the left shock to
the valve block. Now locate the other valve
block just in front of the right rear shock;
disconnect the hydraulic line that connects
the right shock to this valve block too.
3Remove the lower shock absorber-to-
control arm nut and bolt (see illustration).
4Remove the upper mounting bolts (see
illustration)and remove the shock
absorber/coil spring assembly.
10•6 Suspension and steering systems
9.4 To detach the lower control arm from
the crossmember, remove this nut and bolt
(arrowed) (unbolt and lower the steering
gear before you can pull out the pivot bolt)10.2a On a vehicle equipped with self-
levelling rear suspension, the valve block
(arrowed) for the left rear shock is located
just in front of the shock absorber10.2b After depressurising the system,
attach a bleed hose to the bleed screw on
the left valve block, open the bleed and
drain any residual fluid into a catch bottle
3261 Jaguar XJ6 8.2a When refitting the spring compressor
tool (JD115), insert the upper end of the
rod into the cross-shaped slot in the
suspension crossmember, then rotate the
rod 90° so this pin on the upper end of the
tool locks into the crossmember
8.2b This is how the spring compressor
tool (JD115) looks when it’s installed; note
how the offset collet is oriented so that it’s
flush with the coil spring pan8.3 To detach the coil spring pan from the
lower control arm, compress the spring
and remove these six bolts (arrowed)
Page 143 of 227
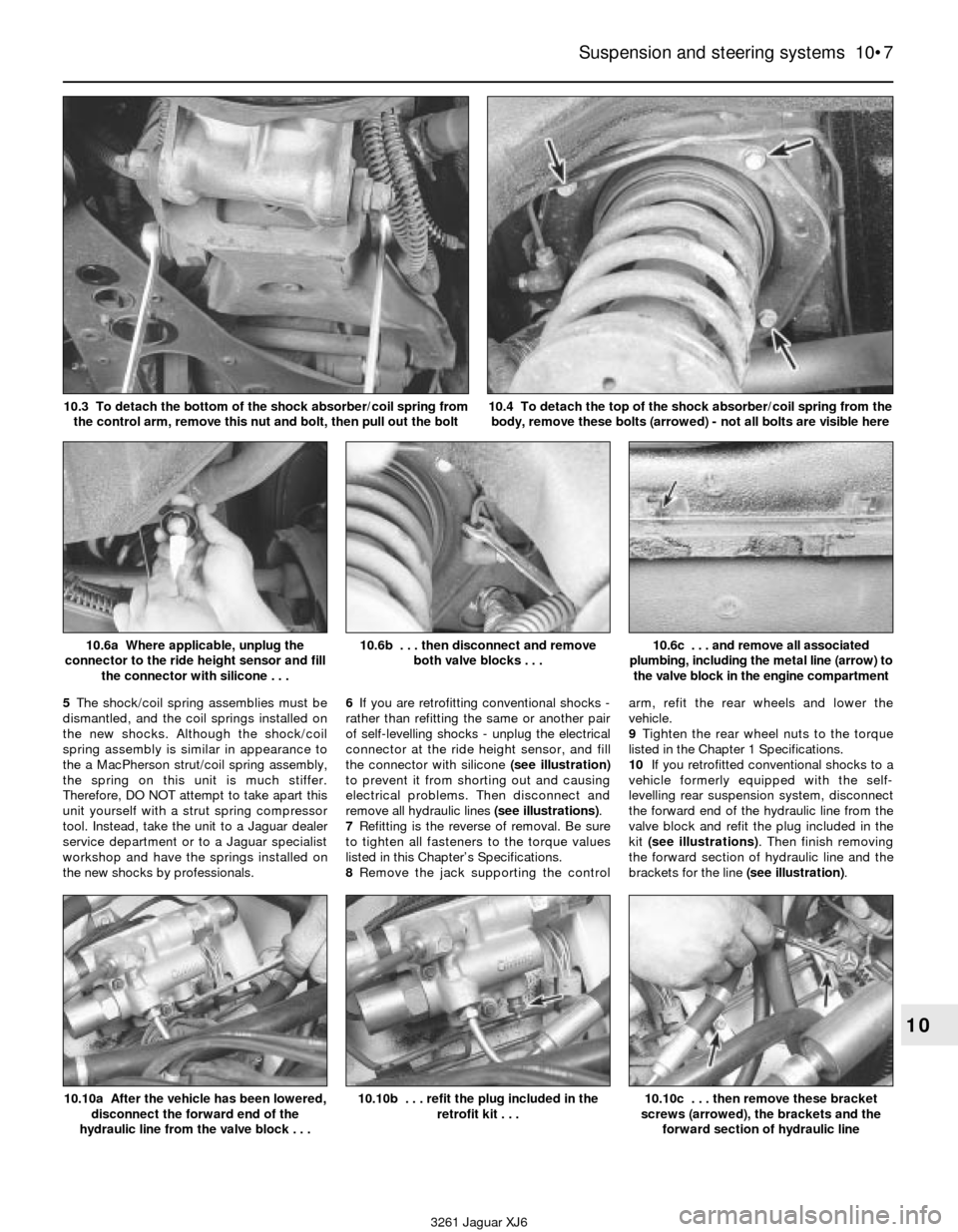
5The shock/coil spring assemblies must be
dismantled, and the coil springs installed on
the new shocks. Although the shock/coil
spring assembly is similar in appearance to
the a MacPherson strut/coil spring assembly,
the spring on this unit is much stiffer.
Therefore, DO NOT attempt to take apart this
unit yourself with a strut spring compressor
tool. Instead, take the unit to a Jaguar dealer
service department or to a Jaguar specialist
workshop and have the springs installed on
the new shocks by professionals.6If you are retrofitting conventional shocks -
rather than refitting the same or another pair
of self-levelling shocks - unplug the electrical
connector at the ride height sensor, and fill
the connector with silicone (see illustration)
to prevent it from shorting out and causing
electrical problems. Then disconnect and
remove all hydraulic lines (see illustrations).
7Refitting is the reverse of removal. Be sure
to tighten all fasteners to the torque values
listed in this Chapter’s Specifications.
8Remove the jack supporting the controlarm, refit the rear wheels and lower the
vehicle.
9Tighten the rear wheel nuts to the torque
listed in the Chapter 1 Specifications.
10If you retrofitted conventional shocks to a
vehicle formerly equipped with the self-
levelling rear suspension system, disconnect
the forward end of the hydraulic line from the
valve block and refit the plug included in the
kit (see illustrations). Then finish removing
the forward section of hydraulic line and the
brackets for the line (see illustration).
Suspension and steering systems 10•7
10
10.6a Where applicable, unplug the
connector to the ride height sensor and fill
the connector with silicone . . .10.6b . . . then disconnect and remove
both valve blocks . . .10.6c . . . and remove all associated
plumbing, including the metal line (arrow) to
the valve block in the engine compartment
3261 Jaguar XJ6 10.3 To detach the bottom of the shock absorber/coil spring from
the control arm, remove this nut and bolt, then pull out the bolt
10.4 To detach the top of the shock absorber/coil spring from the
body, remove these bolts (arrowed) - not all bolts are visible here
10.10a After the vehicle has been lowered,
disconnect the forward end of the
hydraulic line from the valve block . . .10.10b . . . refit the plug included in the
retrofit kit . . .10.10c . . . then remove these bracket
screws (arrowed), the brackets and the
forward section of hydraulic line