diagram JAGUAR XJ6 1997 2.G Workshop Manual
[x] Cancel search | Manufacturer: JAGUAR, Model Year: 1997, Model line: XJ6, Model: JAGUAR XJ6 1997 2.GPages: 227, PDF Size: 7.2 MB
Page 3 of 227
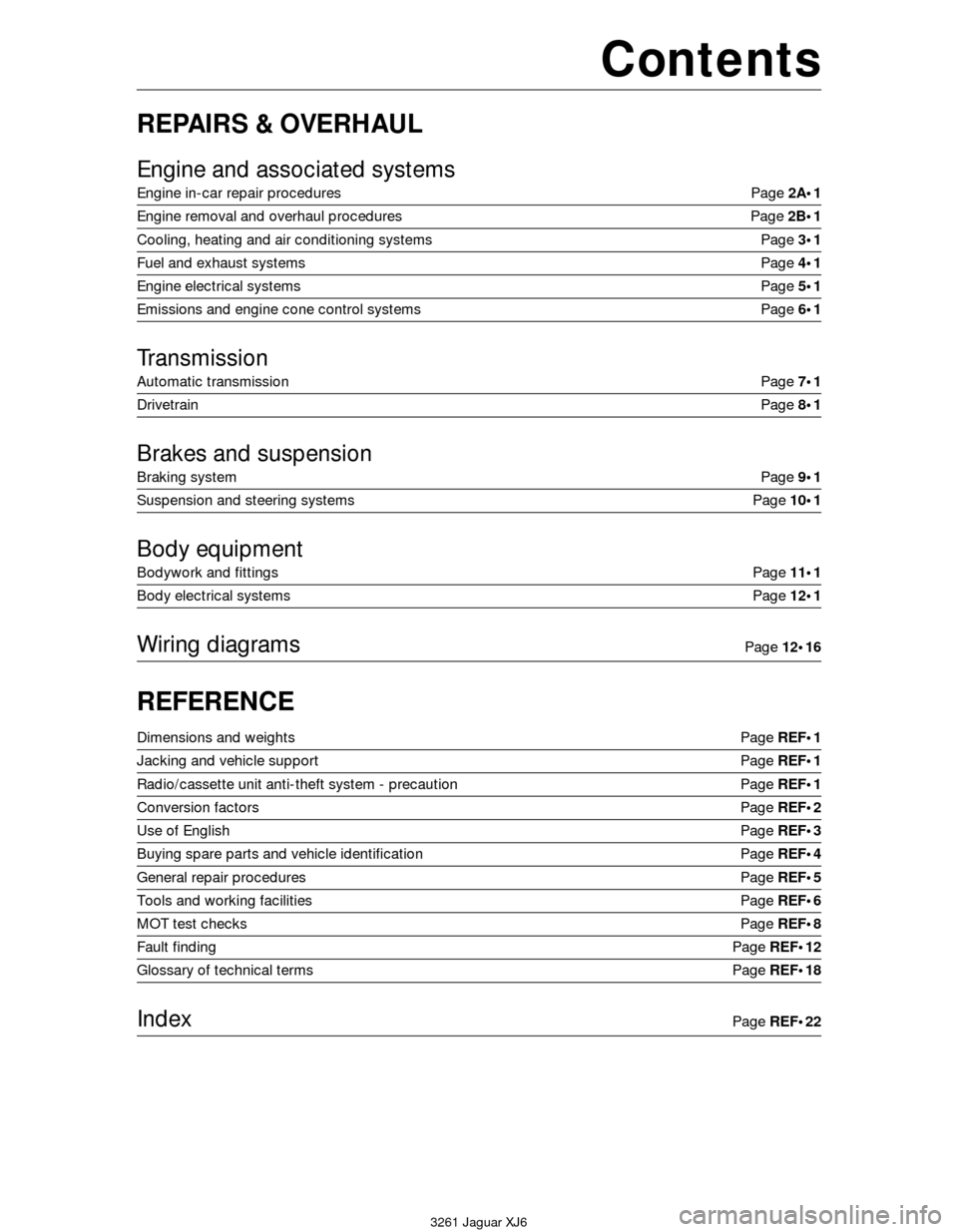
3261 Jaguar XJ6
REPAIRS & OVERHAUL
Engine and associated systems
Engine in-car repair procedures Page 2A•1
Engine removal and overhaul procedures Page 2B•1
Cooling, heating and air conditioning systems Page 3•1
Fuel and exhaust systems Page 4•1
Engine electrical systems Page 5•1
Emissions and engine cone control systems Page 6•1
Transmission
Automatic transmissionPage 7•1
DrivetrainPage 8•1
Brakes and suspension
Braking systemPage 9•1
Suspension and steering systems Page 10•1
Body equipment
Bodywork and fittingsPage 11•1
Body electrical systems Page 12•1
Wiring diagramsPage 12•16
REFERENCE
Dimensions and weights Page REF•1
Jacking and vehicle support Page REF•1
Radio/cassette unit anti-theft system - precaution Page REF•1
Conversion factorsPage REF•2
Use of EnglishPage REF•3
Buying spare parts and vehicle identification Page REF•4
General repair procedures Page REF•5
Tools and working facilities Page REF•6
MOT test checksPage REF•8
Fault findingPage REF•12
Glossary of technical terms Page REF•18
IndexPage REF•22
Contents
Page 89 of 227
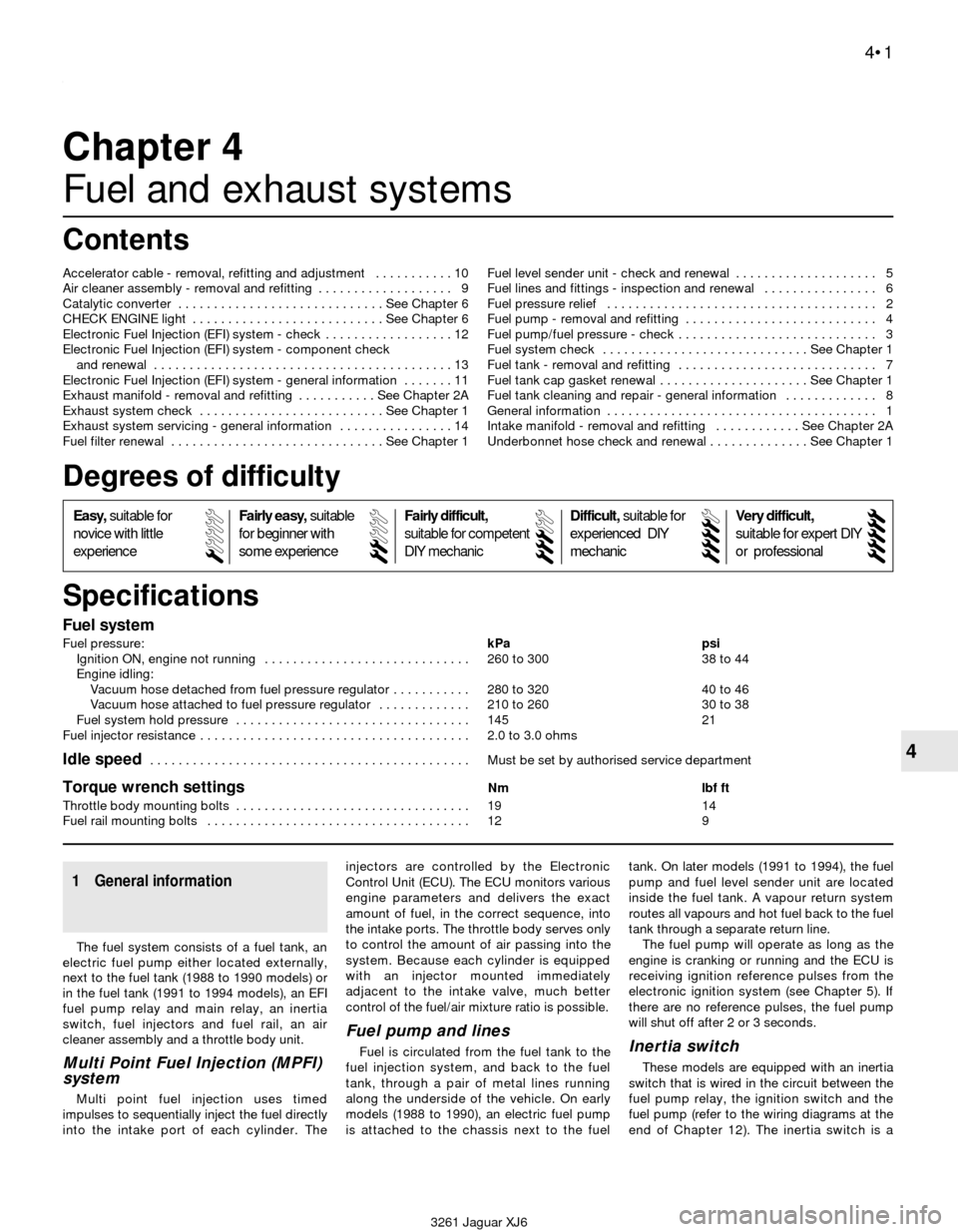
3261 Jaguar XJ6
4
Chapter 4
Fuel and exhaust systems
Fuel system
Fuel pressure:kPa psi
Ignition ON, engine not running . . . . . . . . . . . . . . . . . . . . . . . . . . . . . 260 to 300 38 to 44
Engine idling:
Vacuum hose detached from fuel pressure regulator . . . . . . . . . . . 280 to 320 40 to 46
Vacuum hose attached to fuel pressure regulator . . . . . . . . . . . . . 210 to 260 30 to 38
Fuel system hold pressure . . . . . . . . . . . . . . . . . . . . . . . . . . . . . . . . . 145 21
Fuel injector resistance . . . . . . . . . . . . . . . . . . . . . . . . . . . . . . . . . . . . . . 2.0 to 3.0 ohms
Idle speed . . . . . . . . . . . . . . . . . . . . . . . . . . . . . . . . . . . . . . . . . . . . . Must be set by authorised service department
Torque wrench settingsNm lbf ft
Throttle body mounting bolts . . . . . . . . . . . . . . . . . . . . . . . . . . . . . . . . . 19 14
Fuel rail mounting bolts . . . . . . . . . . . . . . . . . . . . . . . . . . . . . . . . . . . . . 12 9 Accelerator cable - removal, refitting and adjustment . . . . . . . . . . . 10
Air cleaner assembly - removal and refitting . . . . . . . . . . . . . . . . . . . 9
Catalytic converter . . . . . . . . . . . . . . . . . . . . . . . . . . . . . See Chapter 6
CHECK ENGINE light . . . . . . . . . . . . . . . . . . . . . . . . . . . See Chapter 6
Electronic Fuel Injection (EFI) system - check . . . . . . . . . . . . . . . . . . 12
Electronic Fuel Injection (EFI) system - component check
and renewal . . . . . . . . . . . . . . . . . . . . . . . . . . . . . . . . . . . . . . . . . . 13
Electronic Fuel Injection (EFI) system - general information . . . . . . . 11
Exhaust manifold - removal and refitting . . . . . . . . . . . See Chapter 2A
Exhaust system check . . . . . . . . . . . . . . . . . . . . . . . . . . See Chapter 1
Exhaust system servicing - general information . . . . . . . . . . . . . . . . 14
Fuel filter renewal . . . . . . . . . . . . . . . . . . . . . . . . . . . . . . See Chapter 1Fuel level sender unit - check and renewal . . . . . . . . . . . . . . . . . . . . 5
Fuel lines and fittings - inspection and renewal . . . . . . . . . . . . . . . . 6
Fuel pressure relief . . . . . . . . . . . . . . . . . . . . . . . . . . . . . . . . . . . . . . 2
Fuel pump - removal and refitting . . . . . . . . . . . . . . . . . . . . . . . . . . . 4
Fuel pump/fuel pressure - check . . . . . . . . . . . . . . . . . . . . . . . . . . . . 3
Fuel system check . . . . . . . . . . . . . . . . . . . . . . . . . . . . . See Chapter 1
Fuel tank - removal and refitting . . . . . . . . . . . . . . . . . . . . . . . . . . . . 7
Fuel tank cap gasket renewal . . . . . . . . . . . . . . . . . . . . . See Chapter 1
Fuel tank cleaning and repair - general information . . . . . . . . . . . . . 8
General information . . . . . . . . . . . . . . . . . . . . . . . . . . . . . . . . . . . . . . 1
Intake manifold - removal and refitting . . . . . . . . . . . . See Chapter 2A
Underbonnet hose check and renewal . . . . . . . . . . . . . . See Chapter 1
4•1
Specifications Contents
Easy,suitable for
novice with little
experienceFairly easy,suitable
for beginner with
some experienceFairly difficult,
suitable for competent
DIY mechanic
Difficult,suitable for
experienced DIY
mechanicVery difficult,
suitable for expert DIY
or professional
Degrees of difficulty
54321
1 General information
The fuel system consists of a fuel tank, an
electric fuel pump either located externally,
next to the fuel tank (1988 to 1990 models) or
in the fuel tank (1991 to 1994 models), an EFI
fuel pump relay and main relay, an inertia
switch, fuel injectors and fuel rail, an air
cleaner assembly and a throttle body unit.
Multi Point Fuel Injection (MPFI)
system
Multi point fuel injection uses timed
impulses to sequentially inject the fuel directly
into the intake port of each cylinder. Theinjectors are controlled by the Electronic
Control Unit (ECU). The ECU monitors various
engine parameters and delivers the exact
amount of fuel, in the correct sequence, into
the intake ports. The throttle body serves only
to control the amount of air passing into the
system. Because each cylinder is equipped
with an injector mounted immediately
adjacent to the intake valve, much better
control of the fuel/air mixture ratio is possible.
Fuel pump and lines
Fuel is circulated from the fuel tank to the
fuel injection system, and back to the fuel
tank, through a pair of metal lines running
along the underside of the vehicle. On early
models (1988 to 1990), an electric fuel pump
is attached to the chassis next to the fueltank. On later models (1991 to 1994), the fuel
pump and fuel level sender unit are located
inside the fuel tank. A vapour return system
routes all vapours and hot fuel back to the fuel
tank through a separate return line.
The fuel pump will operate as long as the
engine is cranking or running and the ECU is
receiving ignition reference pulses from the
electronic ignition system (see Chapter 5). If
there are no reference pulses, the fuel pump
will shut off after 2 or 3 seconds.Inertia switch
These models are equipped with an inertia
switch that is wired in the circuit between the
fuel pump relay, the ignition switch and the
fuel pump (refer to the wiring diagrams at the
end of Chapter 12). The inertia switch is a
Page 91 of 227
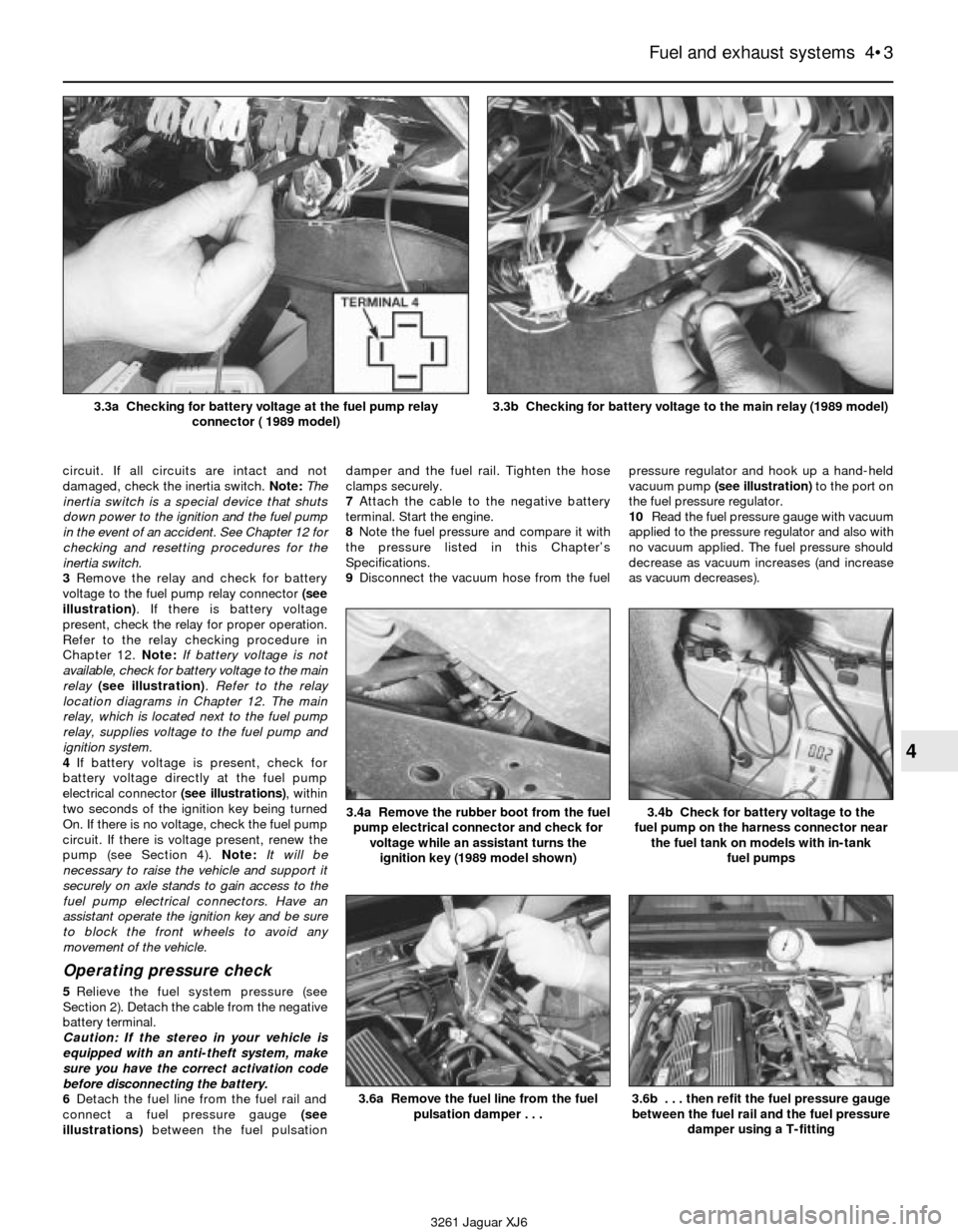
circuit. If all circuits are intact and not
damaged, check the inertia switch. Note: The
inertia switch is a special device that shuts
down power to the ignition and the fuel pump
in the event of an accident. See Chapter 12 for
checking and resetting procedures for the
inertia switch.
3Remove the relay and check for battery
voltage to the fuel pump relay connector (see
illustration). If there is battery voltage
present, check the relay for proper operation.
Refer to the relay checking procedure in
Chapter 12. Note:If battery voltage is not
available, check for battery voltage to the main
relay(see illustration). Refer to the relay
location diagrams in Chapter 12. The main
relay, which is located next to the fuel pump
relay, supplies voltage to the fuel pump and
ignition system.
4If battery voltage is present, check for
battery voltage directly at the fuel pump
electrical connector (see illustrations), within
two seconds of the ignition key being turned
On. If there is no voltage, check the fuel pump
circuit. If there is voltage present, renew the
pump (see Section 4). Note:It will be
necessary to raise the vehicle and support it
securely on axle stands to gain access to the
fuel pump electrical connectors. Have an
assistant operate the ignition key and be sure
to block the front wheels to avoid any
movement of the vehicle.
Operating pressure check
5Relieve the fuel system pressure (see
Section 2). Detach the cable from the negative
battery terminal.
Caution: If the stereo in your vehicle is
equipped with an anti-theft system, make
sure you have the correct activation code
before disconnecting the battery.
6Detach the fuel line from the fuel rail and
connect a fuel pressure gauge(see
illustrations)between the fuel pulsationdamper and the fuel rail. Tighten the hose
clamps securely.
7Attach the cable to the negative battery
terminal. Start the engine.
8Note the fuel pressure and compare it with
the pressure listed in this Chapter’s
Specifications.
9Disconnect the vacuum hose from the fuelpressure regulator and hook up a hand-held
vacuum pump (see illustration)to the port on
the fuel pressure regulator.
10Read the fuel pressure gauge with vacuum
applied to the pressure regulator and also with
no vacuum applied. The fuel pressure should
decrease as vacuum increases (and increase
as vacuum decreases).
Fuel and exhaust systems 4•3
4
3261 Jaguar XJ6 3.3a Checking for battery voltage at the fuel pump relay
connector ( 1989 model)
3.3b Checking for battery voltage to the main relay (1989 model)
3.6a Remove the fuel line from the fuel
pulsation damper . . .
3.4b Check for battery voltage to the
fuel pump on the harness connector near
the fuel tank on models with in-tank
fuel pumps3.4a Remove the rubber boot from the fuel
pump electrical connector and check for
voltage while an assistant turns the
ignition key (1989 model shown)
3.6b . . . then refit the fuel pressure gauge
between the fuel rail and the fuel pressure
damper using a T-fitting
Page 100 of 227
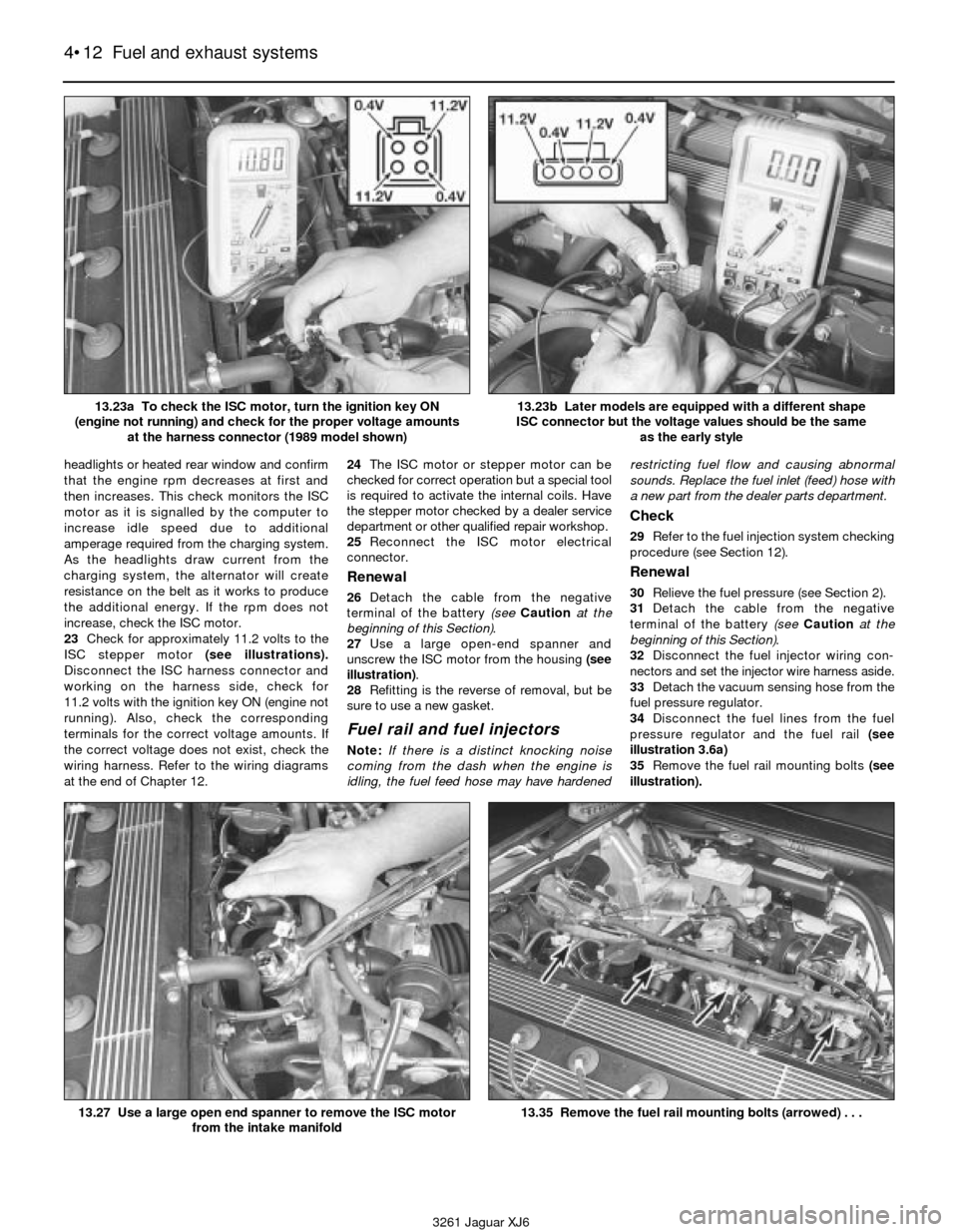
headlights or heated rear window and confirm
that the engine rpm decreases at first and
then increases. This check monitors the ISC
motor as it is signalled by the computer to
increase idle speed due to additional
amperage required from the charging system.
As the headlights draw current from the
charging system, the alternator will create
resistance on the belt as it works to produce
the additional energy. If the rpm does not
increase, check the ISC motor.
23Check for approximately 11.2 volts to the
ISC stepper motor (see illustrations).
Disconnect the ISC harness connector and
working on the harness side, check for
11.2 volts with the ignition key ON (engine not
running). Also, check the corresponding
terminals for the correct voltage amounts. If
the correct voltage does not exist, check the
wiring harness. Refer to the wiring diagrams
at the end of Chapter 12.24The ISC motor or stepper motor can be
checked for correct operation but a special tool
is required to activate the internal coils. Have
the stepper motor checked by a dealer service
department or other qualified repair workshop.
25Reconnect the ISC motor electrical
connector.
Renewal
26Detach the cable from the negative
terminal of the battery (see Cautionat the
beginning of this Section).
27Use a large open-end spanner and
unscrew the ISC motor from the housing (see
illustration).
28Refitting is the reverse of removal, but be
sure to use a new gasket.
Fuel rail and fuel injectors
Note:If there is a distinct knocking noise
coming from the dash when the engine is
idling, the fuel feed hose may have hardenedrestricting fuel flow and causing abnormal
sounds. Replace the fuel inlet (feed) hose with
a new part from the dealer parts department.
Check
29Refer to the fuel injection system checking
procedure (see Section 12).
Renewal
30Relieve the fuel pressure (see Section 2).
31Detach the cable from the negative
terminal of the battery (see Cautionat the
beginning of this Section).
32Disconnect the fuel injector wiring con-
nectors and set the injector wire harness aside.
33Detach the vacuum sensing hose from the
fuel pressure regulator.
34Disconnect the fuel lines from the fuel
pressure regulator and the fuel rail (see
illustration 3.6a)
35Remove the fuel rail mounting bolts (see
illustration).
4•12 Fuel and exhaust systems
3261 Jaguar XJ6 13.23a To check the ISC motor, turn the ignition key ON
(engine not running) and check for the proper voltage amounts
at the harness connector (1989 model shown)
13.23b Later models are equipped with a different shape
ISC connector but the voltage values should be the same
as the early style
13.27 Use a large open end spanner to remove the ISC motor
from the intake manifold13.35 Remove the fuel rail mounting bolts (arrowed) . . .
Page 104 of 227
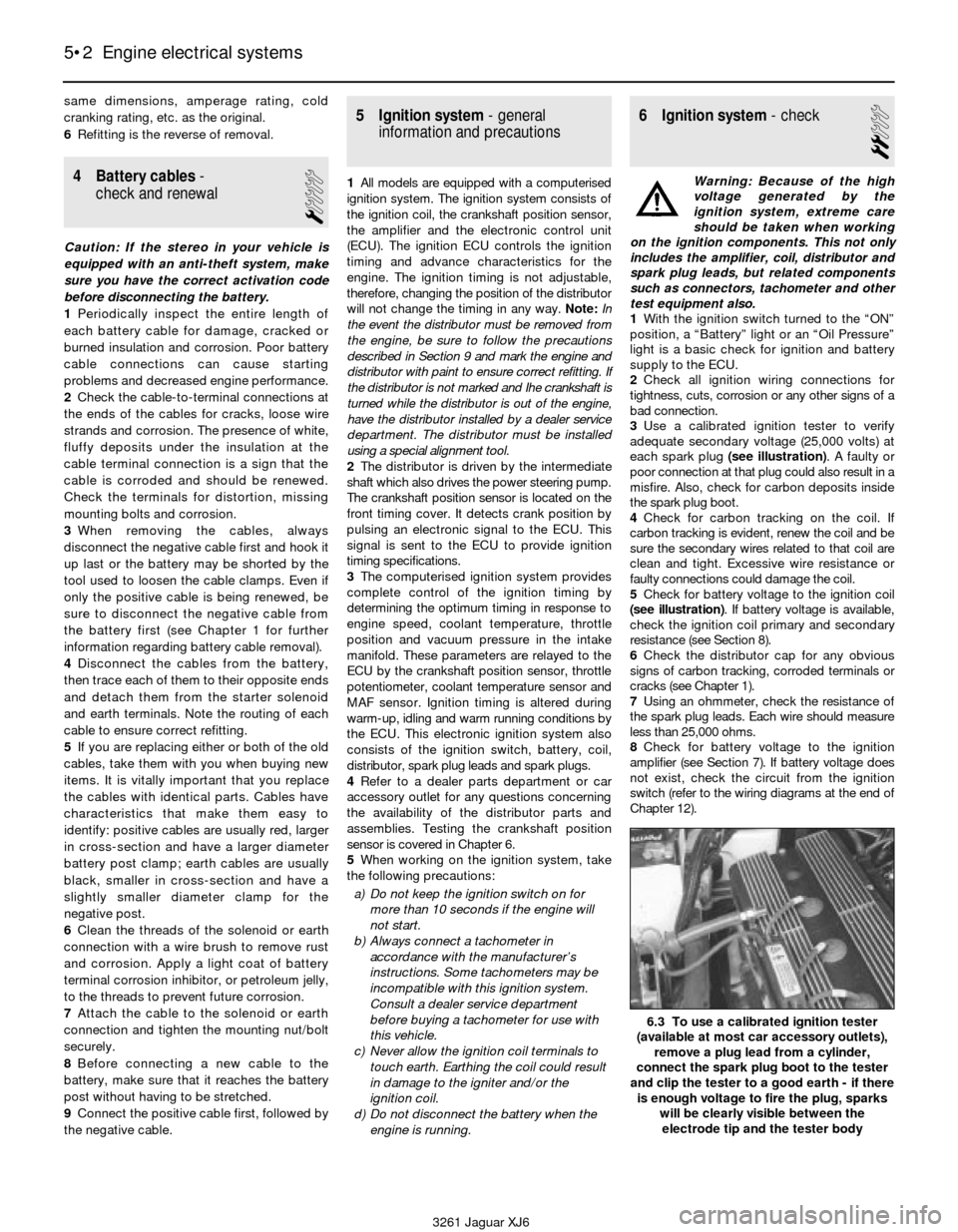
same dimensions, amperage rating, cold
cranking rating, etc. as the original.
6Refitting is the reverse of removal.
4 Battery cables-
check and renewal
1
Caution: If the stereo in your vehicle is
equipped with an anti-theft system, make
sure you have the correct activation code
before disconnecting the battery.
1Periodically inspect the entire length of
each battery cable for damage, cracked or
burned insulation and corrosion. Poor battery
cable connections can cause starting
problems and decreased engine performance.
2Check the cable-to-terminal connections at
the ends of the cables for cracks, loose wire
strands and corrosion. The presence of white,
fluffy deposits under the insulation at the
cable terminal connection is a sign that the
cable is corroded and should be renewed.
Check the terminals for distortion, missing
mounting bolts and corrosion.
3When removing the cables, always
disconnect the negative cable first and hook it
up last or the battery may be shorted by the
tool used to loosen the cable clamps. Even if
only the positive cable is being renewed, be
sure to disconnect the negative cable from
the battery first (see Chapter 1 for further
information regarding battery cable removal).
4Disconnect the cables from the battery,
then trace each of them to their opposite ends
and detach them from the starter solenoid
and earth terminals. Note the routing of each
cable to ensure correct refitting.
5If you are replacing either or both of the old
cables, take them with you when buying new
items. It is vitally important that you replace
the cables with identical parts. Cables have
characteristics that make them easy to
identify: positive cables are usually red, larger
in cross-section and have a larger diameter
battery post clamp; earth cables are usually
black, smaller in cross-section and have a
slightly smaller diameter clamp for the
negative post.
6Clean the threads of the solenoid or earth
connection with a wire brush to remove rust
and corrosion. Apply a light coat of battery
terminal corrosion inhibitor, or petroleum jelly,
to the threads to prevent future corrosion.
7Attach the cable to the solenoid or earth
connection and tighten the mounting nut/bolt
securely.
8Before connecting a new cable to the
battery, make sure that it reaches the battery
post without having to be stretched.
9Connect the positive cable first, followed by
the negative cable.
5 Ignition system- general
information and precautions
1All models are equipped with a computerised
ignition system. The ignition system consists of
the ignition coil, the crankshaft position sensor,
the amplifier and the electronic control unit
(ECU). The ignition ECU controls the ignition
timing and advance characteristics for the
engine. The ignition timing is not adjustable,
therefore, changing the position of the distributor
will not change the timing in any way. Note:In
the event the distributor must be removed from
the engine, be sure to follow the precautions
described in Section 9 and mark the engine and
distributor with paint to ensure correct refitting. If
the distributor is not marked and Ihe crankshaft is
turned while the distributor is out of the engine,
have the distributor installed by a dealer service
department. The distributor must be installed
using a special alignment tool.
2The distributor is driven by the intermediate
shaft which also drives the power steering pump.
The crankshaft position sensor is located on the
front timing cover. It detects crank position by
pulsing an electronic signal to the ECU. This
signal is sent to the ECU to provide ignition
timing specifications.
3The computerised ignition system provides
complete control of the ignition timing by
determining the optimum timing in response to
engine speed, coolant temperature, throttle
position and vacuum pressure in the intake
manifold. These parameters are relayed to the
ECU by the crankshaft position sensor, throttle
potentiometer, coolant temperature sensor and
MAF sensor. Ignition timing is altered during
warm-up, idling and warm running conditions by
the ECU. This electronic ignition system also
consists of the ignition switch, battery, coil,
distributor, spark plug leads and spark plugs.
4Refer to a dealer parts department or car
accessory outlet for any questions concerning
the availability of the distributor parts and
assemblies. Testing the crankshaft position
sensor is covered in Chapter 6.
5When working on the ignition system, take
the following precautions:
a) Do not keep the ignition switch on for
more than 10 seconds if the engine will
not start.
b) Always connect a tachometer in
accordance with the manufacturer’s
instructions. Some tachometers may be
incompatible with this ignition system.
Consult a dealer service department
before buying a tachometer for use with
this vehicle.
c) Never allow the ignition coil terminals to
touch earth. Earthing the coil could result
in damage to the igniter and/or the
ignition coil.
d) Do not disconnect the battery when the
engine is running.
6 Ignition system- check
2
Warning: Because of the high
voltage generated by the
ignition system, extreme care
should be taken when working
on the ignition components. This not only
includes the amplifier, coil, distributor and
spark plug leads, but related components
such as connectors, tachometer and other
test equipment also.
1With the ignition switch turned to the “ON”
position, a “Battery” light or an “Oil Pressure”
light is a basic check for ignition and battery
supply to the ECU.
2Check all ignition wiring connections for
tightness, cuts, corrosion or any other signs of a
bad connection.
3Use a calibrated ignition tester to verify
adequate secondary voltage (25,000 volts) at
each spark plug (see illustration). A faulty or
poor connection at that plug could also result in a
misfire. Also, check for carbon deposits inside
the spark plug boot.
4Check for carbon tracking on the coil. If
carbon tracking is evident, renew the coil and be
sure the secondary wires related to that coil are
clean and tight. Excessive wire resistance or
faulty connections could damage the coil.
5Check for battery voltage to the ignition coil
(see illustration). If battery voltage is available,
check the ignition coil primary and secondary
resistance (see Section 8).
6Check the distributor cap for any obvious
signs of carbon tracking, corroded terminals or
cracks (see Chapter 1).
7Using an ohmmeter, check the resistance of
the spark plug leads. Each wire should measure
less than 25,000 ohms.
8Check for battery voltage to the ignition
amplifier (see Section 7). If battery voltage does
not exist, check the circuit from the ignition
switch (refer to the wiring diagrams at the end of
Chapter 12).
5•2 Engine electrical systems
6.3 To use a calibrated ignition tester
(available at most car accessory outlets),
remove a plug lead from a cylinder,
connect the spark plug boot to the tester
and clip the tester to a good earth - if there
is enough voltage to fire the plug, sparks
will be clearly visible between the
electrode tip and the tester body
3261 Jaguar XJ6
Page 105 of 227
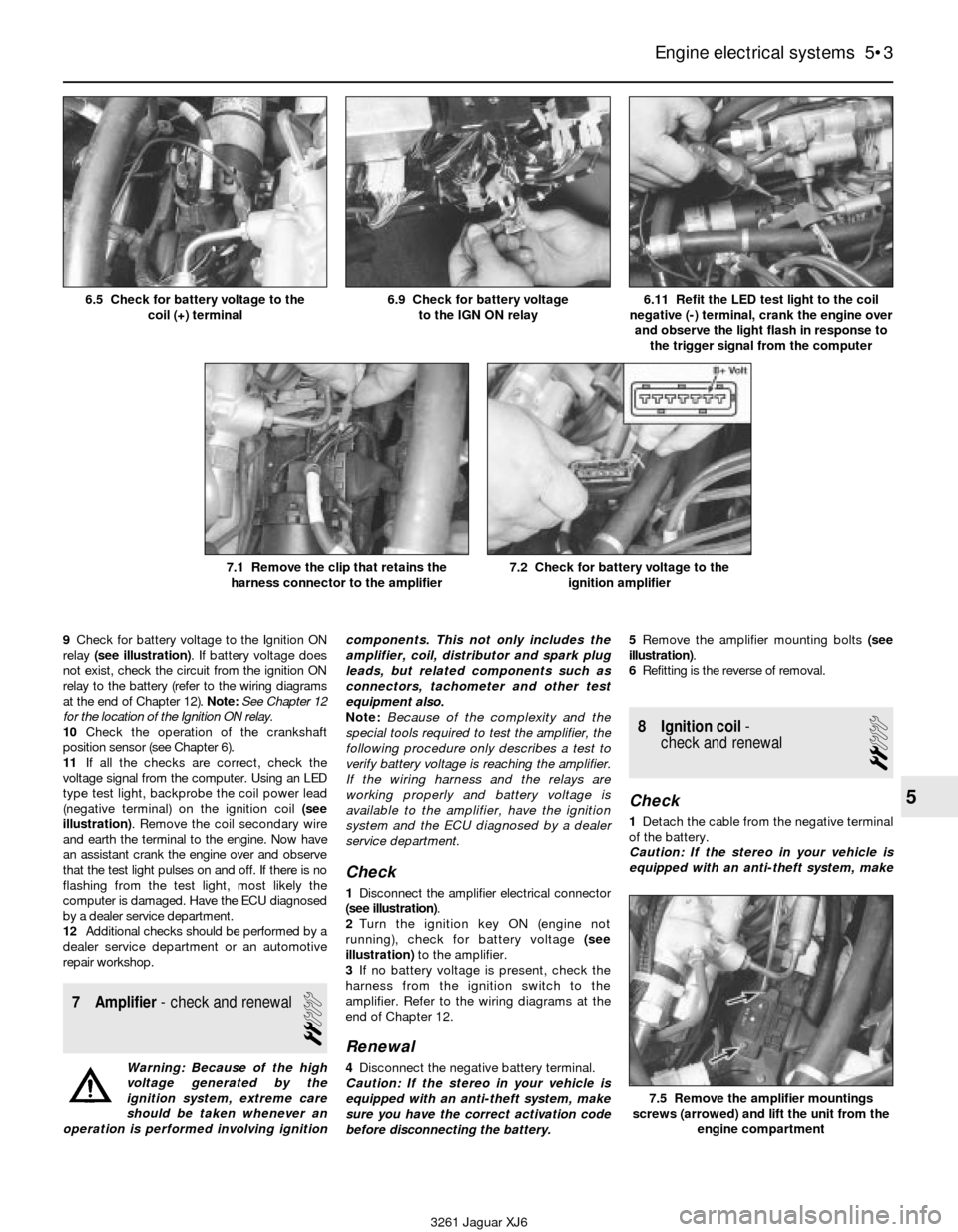
9Check for battery voltage to the Ignition ON
relay (see illustration). If battery voltage does
not exist, check the circuit from the ignition ON
relay to the battery (refer to the wiring diagrams
at the end of Chapter 12). Note:See Chapter 12
for the location of the Ignition ON relay.
10Check the operation of the crankshaft
position sensor (see Chapter 6).
11If all the checks are correct, check the
voltage signal from the computer. Using an LED
type test light, backprobe the coil power lead
(negative terminal) on the ignition coil (see
illustration). Remove the coil secondary wire
and earth the terminal to the engine. Now have
an assistant crank the engine over and observe
that the test light pulses on and off. If there is no
flashing from the test light, most likely the
computer is damaged. Have the ECU diagnosed
by a dealer service department.
12Additional checks should be performed by a
dealer service department or an automotive
repair workshop.
7 Amplifier- check and renewal
2
Warning: Because of the high
voltage generated by the
ignition system, extreme care
should be taken whenever an
operation is performed involving ignitioncomponents. This not only includes the
amplifier, coil, distributor and spark plug
leads, but related components such as
connectors, tachometer and other test
equipment also.
Note:Because of the complexity and the
special tools required to test the amplifier, the
following procedure only describes a test to
verify battery voltage is reaching the amplifier.
If the wiring harness and the relays are
working properly and battery voltage is
available to the amplifier, have the ignition
system and the ECU diagnosed by a dealer
service department.
Check
1Disconnect the amplifier electrical connector
(see illustration).
2Turn the ignition key ON (engine not
running), check for battery voltage (see
illustration) to the amplifier.
3If no battery voltage is present, check the
harness from the ignition switch to the
amplifier. Refer to the wiring diagrams at the
end of Chapter 12.
Renewal
4Disconnect the negative battery terminal.
Caution: If the stereo in your vehicle is
equipped with an anti-theft system, make
sure you have the correct activation code
before disconnecting the battery.5Remove the amplifier mounting bolts (see
illustration).
6Refitting is the reverse of removal.
8 Ignition coil-
check and renewal
2
Check
1Detach the cable from the negative terminal
of the battery.
Caution: If the stereo in your vehicle is
equipped with an anti-theft system, make
Engine electrical systems 5•3
5
6.5 Check for battery voltage to the
coil (+) terminal6.9 Check for battery voltage
to the IGN ON relay6.11 Refit the LED test light to the coil
negative (-) terminal, crank the engine over
and observe the light flash in response to
the trigger signal from the computer
7.1 Remove the clip that retains the
harness connector to the amplifier7.2 Check for battery voltage to the
ignition amplifier
7.5 Remove the amplifier mountings
screws (arrowed) and lift the unit from the
engine compartment
3261 Jaguar XJ6
Page 108 of 227
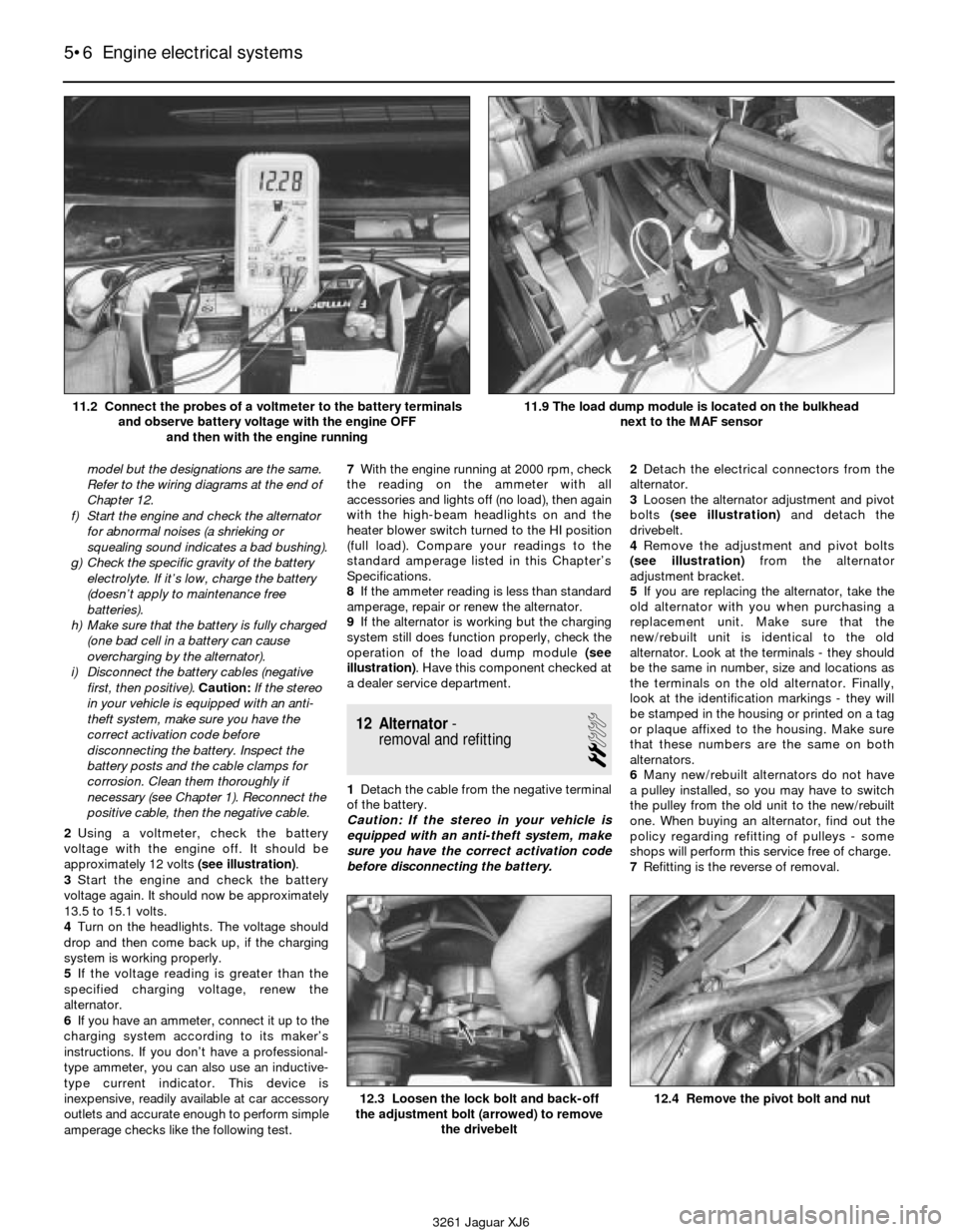
model but the designations are the same.
Refer to the wiring diagrams at the end of
Chapter 12.
f) Start the engine and check the alternator
for abnormal noises (a shrieking or
squealing sound indicates a bad bushing).
g) Check the specific gravity of the battery
electrolyte. If it’s low, charge the battery
(doesn’t apply to maintenance free
batteries).
h) Make sure that the battery is fully charged
(one bad cell in a battery can cause
overcharging by the alternator).
i) Disconnect the battery cables (negative
first, then positive). Caution:If the stereo
in your vehicle is equipped with an anti-
theft system, make sure you have the
correct activation code before
disconnecting the battery. Inspect the
battery posts and the cable clamps for
corrosion. Clean them thoroughly if
necessary (see Chapter 1). Reconnect the
positive cable, then the negative cable.
2Using a voltmeter, check the battery
voltage with the engine off. It should be
approximately 12 volts (see illustration).
3Start the engine and check the battery
voltage again. It should now be approximately
13.5 to 15.1 volts.
4Turn on the headlights. The voltage should
drop and then come back up, if the charging
system is working properly.
5If the voltage reading is greater than the
specified charging voltage, renew the
alternator.
6If you have an ammeter, connect it up to the
charging system according to its maker’s
instructions. If you don’t have a professional-
type ammeter, you can also use an inductive-
type current indicator. This device is
inexpensive, readily available at car accessory
outlets and accurate enough to perform simple
amperage checks like the following test.7With the engine running at 2000 rpm, check
the reading on the ammeter with all
accessories and lights off (no load), then again
with the high-beam headlights on and the
heater blower switch turned to the HI position
(full load). Compare your readings to the
standard amperage listed in this Chapter’s
Specifications.
8If the ammeter reading is less than standard
amperage, repair or renew the alternator.
9If the alternator is working but the charging
system still does function properly, check the
operation of the load dump module (see
illustration). Have this component checked at
a dealer service department.
12 Alternator-
removal and refitting
2
1Detach the cable from the negative terminal
of the battery.
Caution: If the stereo in your vehicle is
equipped with an anti-theft system, make
sure you have the correct activation code
before disconnecting the battery.2Detach the electrical connectors from the
alternator.
3Loosen the alternator adjustment and pivot
bolts (see illustration) and detach the
drivebelt.
4Remove the adjustment and pivot bolts
(see illustration)from the alternator
adjustment bracket.
5If you are replacing the alternator, take the
old alternator with you when purchasing a
replacement unit. Make sure that the
new/rebuilt unit is identical to the old
alternator. Look at the terminals - they should
be the same in number, size and locations as
the terminals on the old alternator. Finally,
look at the identification markings - they will
be stamped in the housing or printed on a tag
or plaque affixed to the housing. Make sure
that these numbers are the same on both
alternators.
6Many new/rebuilt alternators do not have
a pulley installed, so you may have to switch
the pulley from the old unit to the new/rebuilt
one. When buying an alternator, find out the
policy regarding refitting of pulleys - some
shops will perform this service free of charge.
7Refitting is the reverse of removal.
5•6 Engine electrical systems
12.3 Loosen the lock bolt and back-off
the adjustment bolt (arrowed) to remove
the drivebelt12.4 Remove the pivot bolt and nut
3261 Jaguar XJ6 11.2 Connect the probes of a voltmeter to the battery terminals
and observe battery voltage with the engine OFF
and then with the engine running
11.9 The load dump module is located on the bulkhead
next to the MAF sensor
Page 111 of 227
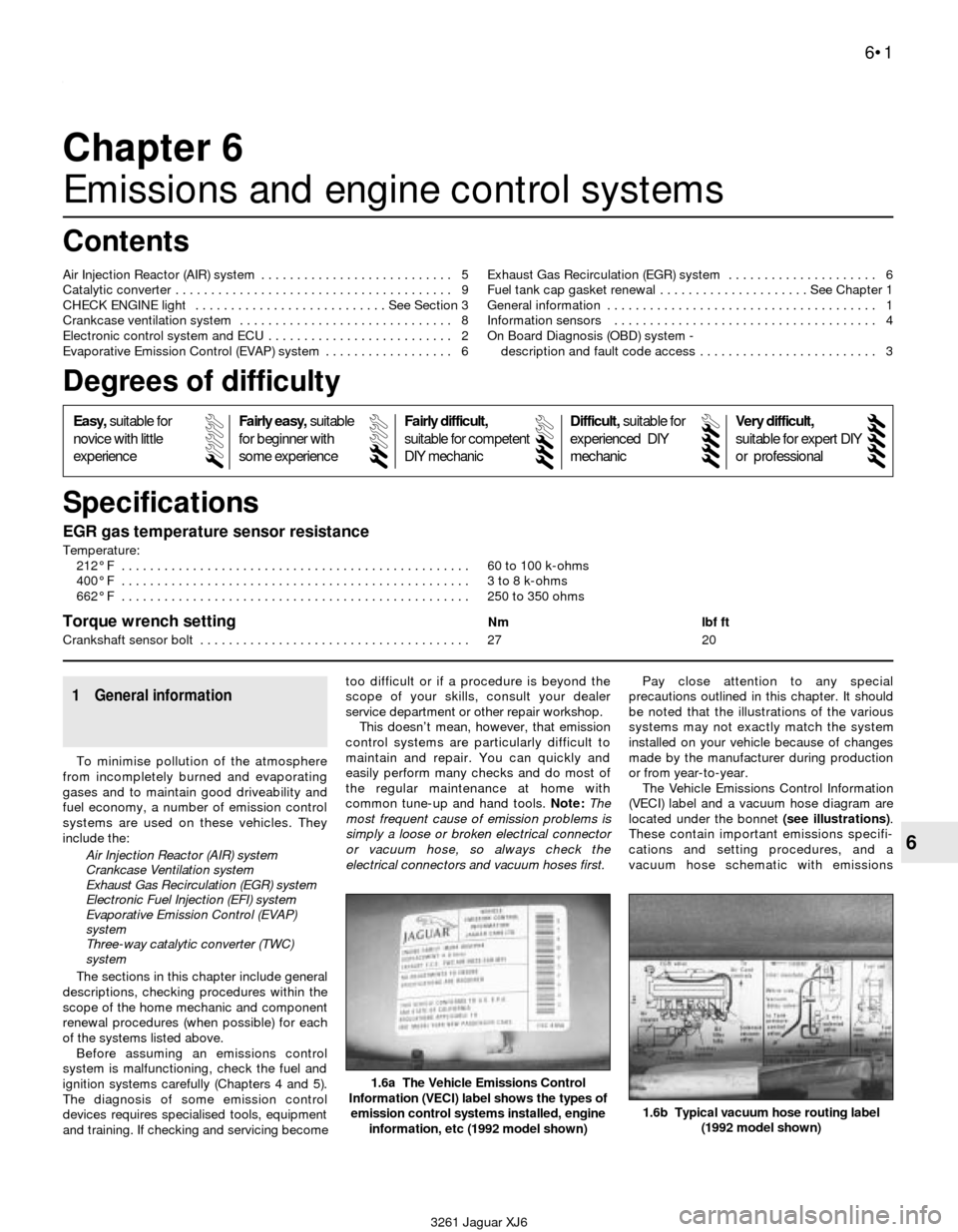
3261 Jaguar XJ6
6
Chapter 6
Emissions and engine control systems
EGR gas temperature sensor resistance
Temperature:
212° F . . . . . . . . . . . . . . . . . . . . . . . . . . . . . . . . . . . . . . . . . . . . . . . . . 60 to 100 k-ohms
400° F . . . . . . . . . . . . . . . . . . . . . . . . . . . . . . . . . . . . . . . . . . . . . . . . . 3 to 8 k-ohms
662° F . . . . . . . . . . . . . . . . . . . . . . . . . . . . . . . . . . . . . . . . . . . . . . . . . 250 to 350 ohms
Torque wrench settingNm lbf ft
Crankshaft sensor bolt . . . . . . . . . . . . . . . . . . . . . . . . . . . . . . . . . . . . . . 27 20 Air Injection Reactor (AIR) system . . . . . . . . . . . . . . . . . . . . . . . . . . . 5
Catalytic converter . . . . . . . . . . . . . . . . . . . . . . . . . . . . . . . . . . . . . . . 9
CHECK ENGINE light . . . . . . . . . . . . . . . . . . . . . . . . . . . See Section 3
Crankcase ventilation system . . . . . . . . . . . . . . . . . . . . . . . . . . . . . . 8
Electronic control system and ECU . . . . . . . . . . . . . . . . . . . . . . . . . . 2
Evaporative Emission Control (EVAP) system . . . . . . . . . . . . . . . . . . 6Exhaust Gas Recirculation (EGR) system . . . . . . . . . . . . . . . . . . . . . 6
Fuel tank cap gasket renewal . . . . . . . . . . . . . . . . . . . . . See Chapter 1
General information . . . . . . . . . . . . . . . . . . . . . . . . . . . . . . . . . . . . . . 1
Information sensors . . . . . . . . . . . . . . . . . . . . . . . . . . . . . . . . . . . . . 4
On Board Diagnosis (OBD) system -
description and fault code access . . . . . . . . . . . . . . . . . . . . . . . . . 3
6•1
Specifications Contents
Easy,suitable for
novice with little
experienceFairly easy,suitable
for beginner with
some experienceFairly difficult,
suitable for competent
DIY mechanic
Difficult,suitable for
experienced DIY
mechanicVery difficult,
suitable for expert DIY
or professional
Degrees of difficulty
54321
1 General information
To minimise pollution of the atmosphere
from incompletely burned and evaporating
gases and to maintain good driveability and
fuel economy, a number of emission control
systems are used on these vehicles. They
include the:
Air Injection Reactor (AIR) system
Crankcase Ventilation system
Exhaust Gas Recirculation (EGR) system
Electronic Fuel Injection (EFI) system
Evaporative Emission Control (EVAP)
system
Three-way catalytic converter (TWC)
system
The sections in this chapter include general
descriptions, checking procedures within the
scope of the home mechanic and component
renewal procedures (when possible) for each
of the systems listed above.
Before assuming an emissions control
system is malfunctioning, check the fuel and
ignition systems carefully (Chapters 4 and 5).
The diagnosis of some emission control
devices requires specialised tools, equipment
and training. If checking and servicing becometoo difficult or if a procedure is beyond the
scope of your skills, consult your dealer
service department or other repair workshop.
This doesn’t mean, however, that emission
control systems are particularly difficult to
maintain and repair. You can quickly and
easily perform many checks and do most of
the regular maintenance at home with
common tune-up and hand tools. Note:The
most frequent cause of emission problems is
simply a loose or broken electrical connector
or vacuum hose, so always check the
electrical connectors and vacuum hoses first.Pay close attention to any special
precautions outlined in this chapter. It should
be noted that the illustrations of the various
systems may not exactly match the system
installed on your vehicle because of changes
made by the manufacturer during production
or from year-to-year.
The Vehicle Emissions Control Information
(VECI) label and a vacuum hose diagram are
located under the bonnet (see illustrations).
These contain important emissions specifi-
cations and setting procedures, and a
vacuum hose schematic with emissions
1.6a The Vehicle Emissions Control
Information (VECI) label shows the types of
emission control systems installed, engine
information, etc (1992 model shown)
1.6b Typical vacuum hose routing label
(1992 model shown)
Page 115 of 227
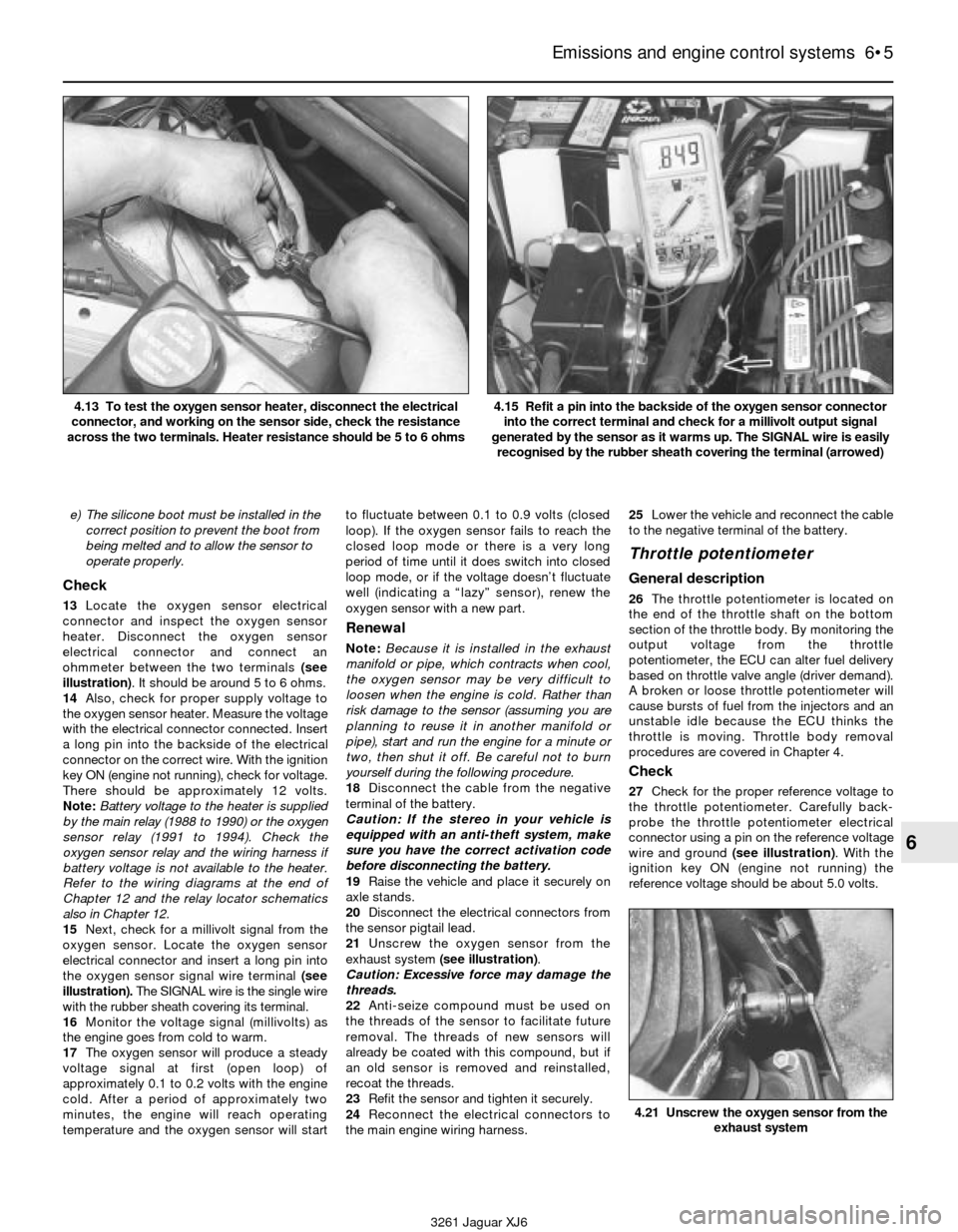
e) The silicone boot must be installed in the
correct position to prevent the boot from
being melted and to allow the sensor to
operate properly.
Check
13Locate the oxygen sensor electrical
connector and inspect the oxygen sensor
heater. Disconnect the oxygen sensor
electrical connector and connect an
ohmmeter between the two terminals (see
illustration). It should be around 5 to 6 ohms.
14Also, check for proper supply voltage to
the oxygen sensor heater. Measure the voltage
with the electrical connector connected. Insert
a long pin into the backside of the electrical
connector on the correct wire. With the ignition
key ON (engine not running), check for voltage.
There should be approximately 12 volts.
Note:Battery voltage to the heater is supplied
by the main relay (1988 to 1990) or the oxygen
sensor relay (1991 to 1994). Check the
oxygen sensor relay and the wiring harness if
battery voltage is not available to the heater.
Refer to the wiring diagrams at the end of
Chapter 12 and the relay locator schematics
also in Chapter 12.
15Next, check for a millivolt signal from the
oxygen sensor. Locate the oxygen sensor
electrical connector and insert a long pin into
the oxygen sensor signal wire terminal (see
illustration). The SIGNAL wire is the single wire
with the rubber sheath covering its terminal.
16Monitor the voltage signal (millivolts) as
the engine goes from cold to warm.
17The oxygen sensor will produce a steady
voltage signal at first (open loop) of
approximately 0.1 to 0.2 volts with the engine
cold. After a period of approximately two
minutes, the engine will reach operating
temperature and the oxygen sensor will startto fluctuate between 0.1 to 0.9 volts (closed
loop). If the oxygen sensor fails to reach the
closed loop mode or there is a very long
period of time until it does switch into closed
loop mode, or if the voltage doesn’t fluctuate
well (indicating a “lazy” sensor), renew the
oxygen sensor with a new part.
Renewal
Note:Because it is installed in the exhaust
manifold or pipe, which contracts when cool,
the oxygen sensor may be very difficult to
loosen when the engine is cold. Rather than
risk damage to the sensor (assuming you are
planning to reuse it in another manifold or
pipe), start and run the engine for a minute or
two, then shut it off. Be careful not to burn
yourself during the following procedure.
18Disconnect the cable from the negative
terminal of the battery.
Caution: If the stereo in your vehicle is
equipped with an anti-theft system, make
sure you have the correct activation code
before disconnecting the battery.
19Raise the vehicle and place it securely on
axle stands.
20Disconnect the electrical connectors from
the sensor pigtail lead.
21Unscrew the oxygen sensor from the
exhaust system (see illustration).
Caution: Excessive force may damage the
threads.
22Anti-seize compound must be used on
the threads of the sensor to facilitate future
removal. The threads of new sensors will
already be coated with this compound, but if
an old sensor is removed and reinstalled,
recoat the threads.
23Refit the sensor and tighten it securely.
24Reconnect the electrical connectors to
the main engine wiring harness.25Lower the vehicle and reconnect the cable
to the negative terminal of the battery.
Throttle potentiometer
General description
26The throttle potentiometer is located on
the end of the throttle shaft on the bottom
section of the throttle body. By monitoring the
output voltage from the throttle
potentiometer, the ECU can alter fuel delivery
based on throttle valve angle (driver demand).
A broken or loose throttle potentiometer will
cause bursts of fuel from the injectors and an
unstable idle because the ECU thinks the
throttle is moving. Throttle body removal
procedures are covered in Chapter 4.
Check
27Check for the proper reference voltage to
the throttle potentiometer. Carefully back-
probe the throttle potentiometer electrical
connector using a pin on the reference voltage
wire and ground (see illustration). With the
ignition key ON (engine not running) the
reference voltage should be about 5.0 volts.
Emissions and engine control systems 6•5
6
4.21 Unscrew the oxygen sensor from the
exhaust system
3261 Jaguar XJ6 4.13 To test the oxygen sensor heater, disconnect the electrical
connector, and working on the sensor side, check the resistance
across the two terminals. Heater resistance should be 5 to 6 ohms
4.15 Refit a pin into the backside of the oxygen sensor connector
into the correct terminal and check for a millivolt output signal
generated by the sensor as it warms up. The SIGNAL wire is easily
recognised by the rubber sheath covering the terminal (arrowed)
Page 120 of 227
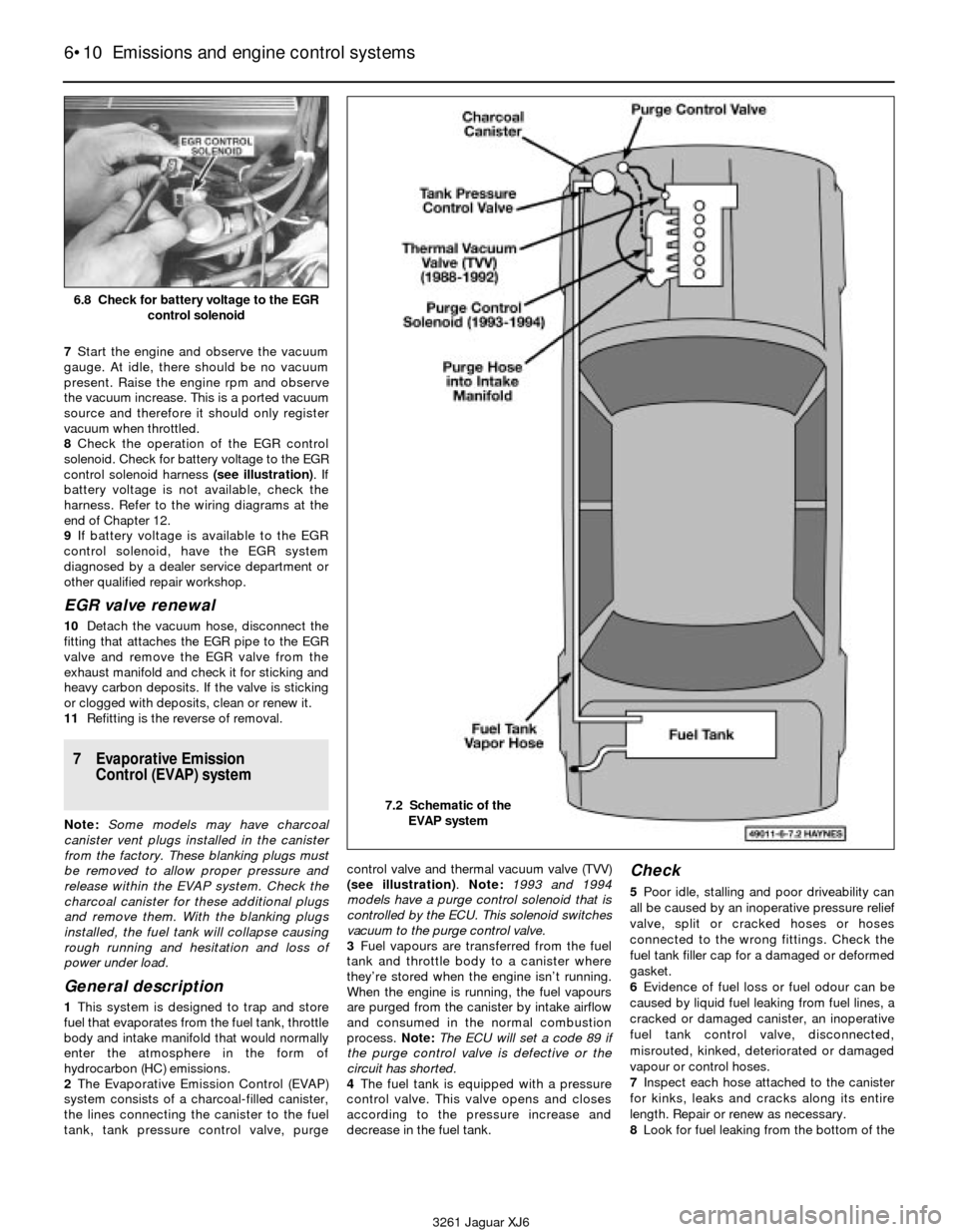
7Start the engine and observe the vacuum
gauge. At idle, there should be no vacuum
present. Raise the engine rpm and observe
the vacuum increase. This is a ported vacuum
source and therefore it should only register
vacuum when throttled.
8Check the operation of the EGR control
solenoid. Check for battery voltage to the EGR
control solenoid harness (see illustration). If
battery voltage is not available, check the
harness. Refer to the wiring diagrams at the
end of Chapter 12.
9If battery voltage is available to the EGR
control solenoid, have the EGR system
diagnosed by a dealer service department or
other qualified repair workshop.
EGR valve renewal
10Detach the vacuum hose, disconnect the
fitting that attaches the EGR pipe to the EGR
valve and remove the EGR valve from the
exhaust manifold and check it for sticking and
heavy carbon deposits. If the valve is sticking
or clogged with deposits, clean or renew it.
11Refitting is the reverse of removal.
7 Evaporative Emission
Control (EVAP) system
Note: Some models may have charcoal
canister vent plugs installed in the canister
from the factory. These blanking plugs must
be removed to allow proper pressure and
release within the EVAP system. Check the
charcoal canister for these additional plugs
and remove them. With the blanking plugs
installed, the fuel tank will collapse causing
rough running and hesitation and loss of
power under load.
General description
1This system is designed to trap and store
fuel that evaporates from the fuel tank, throttle
body and intake manifold that would normally
enter the atmosphere in the form of
hydrocarbon (HC) emissions.
2The Evaporative Emission Control (EVAP)
system consists of a charcoal-filled canister,
the lines connecting the canister to the fuel
tank, tank pressure control valve, purgecontrol valve and thermal vacuum valve (TVV)
(see illustration). Note: 1993 and 1994
models have a purge control solenoid that is
controlled by the ECU. This solenoid switches
vacuum to the purge control valve.
3Fuel vapours are transferred from the fuel
tank and throttle body to a canister where
they’re stored when the engine isn’t running.
When the engine is running, the fuel vapours
are purged from the canister by intake airflow
and consumed in the normal combustion
process.Note: The ECU will set a code 89 if
the purge control valve is defective or the
circuit has shorted.
4The fuel tank is equipped with a pressure
control valve. This valve opens and closes
according to the pressure increase and
decrease in the fuel tank.
Check
5Poor idle, stalling and poor driveability can
all be caused by an inoperative pressure relief
valve, split or cracked hoses or hoses
connected to the wrong fittings. Check the
fuel tank filler cap for a damaged or deformed
gasket.
6Evidence of fuel loss or fuel odour can be
caused by liquid fuel leaking from fuel lines, a
cracked or damaged canister, an inoperative
fuel tank control valve, disconnected,
misrouted, kinked, deteriorated or damaged
vapour or control hoses.
7Inspect each hose attached to the canister
for kinks, leaks and cracks along its entire
length. Repair or renew as necessary.
8Look for fuel leaking from the bottom of the
6•10 Emissions and engine control systems
6.8 Check for battery voltage to the EGR
control solenoid
3261 Jaguar XJ6
7.2 Schematic of the
EVAP system