dimensions JAGUAR XJ6 1997 2.G Workshop Manual
[x] Cancel search | Manufacturer: JAGUAR, Model Year: 1997, Model line: XJ6, Model: JAGUAR XJ6 1997 2.GPages: 227, PDF Size: 7.2 MB
Page 3 of 227
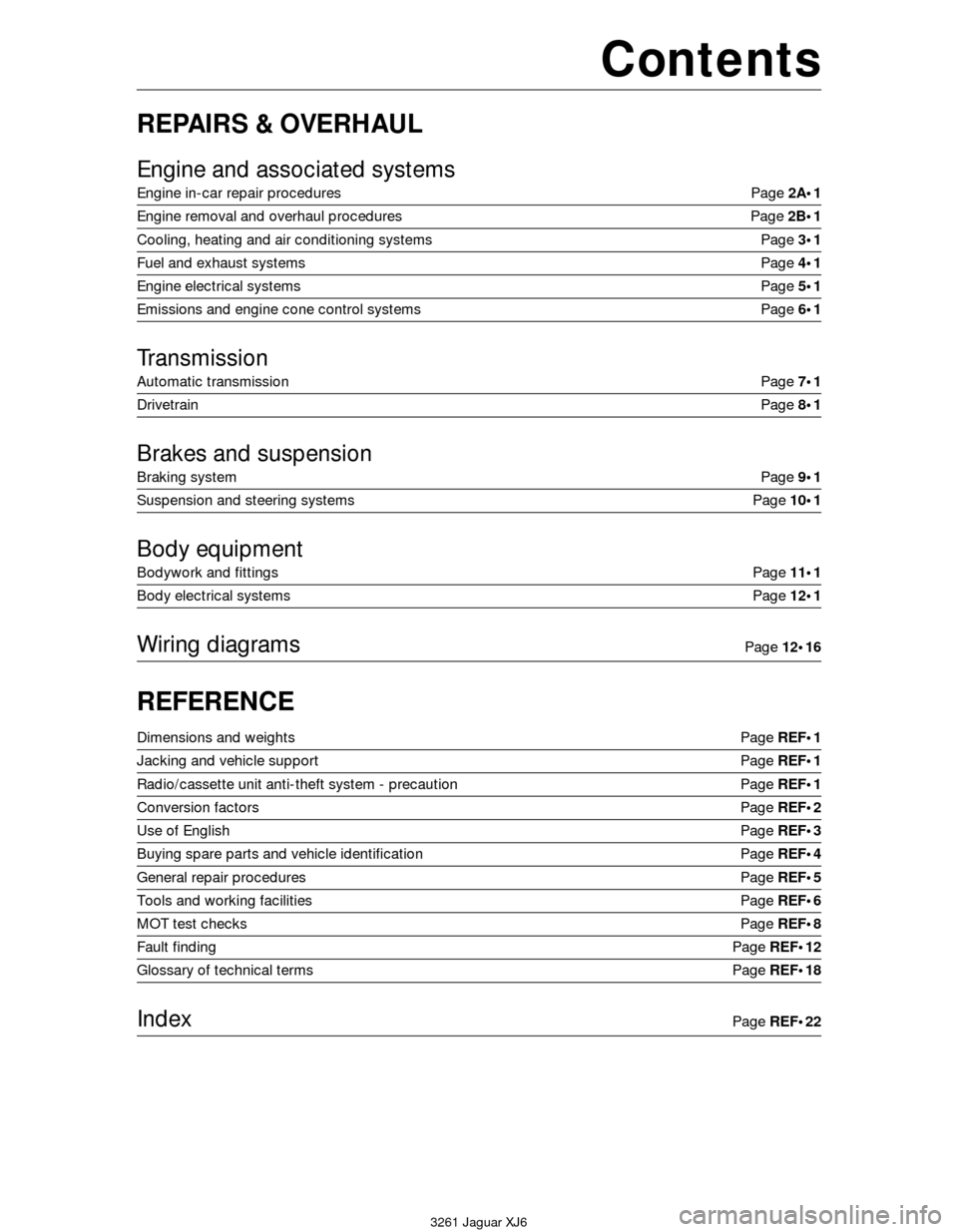
3261 Jaguar XJ6
REPAIRS & OVERHAUL
Engine and associated systems
Engine in-car repair procedures Page 2A•1
Engine removal and overhaul procedures Page 2B•1
Cooling, heating and air conditioning systems Page 3•1
Fuel and exhaust systems Page 4•1
Engine electrical systems Page 5•1
Emissions and engine cone control systems Page 6•1
Transmission
Automatic transmissionPage 7•1
DrivetrainPage 8•1
Brakes and suspension
Braking systemPage 9•1
Suspension and steering systems Page 10•1
Body equipment
Bodywork and fittingsPage 11•1
Body electrical systems Page 12•1
Wiring diagramsPage 12•16
REFERENCE
Dimensions and weights Page REF•1
Jacking and vehicle support Page REF•1
Radio/cassette unit anti-theft system - precaution Page REF•1
Conversion factorsPage REF•2
Use of EnglishPage REF•3
Buying spare parts and vehicle identification Page REF•4
General repair procedures Page REF•5
Tools and working facilities Page REF•6
MOT test checksPage REF•8
Fault findingPage REF•12
Glossary of technical terms Page REF•18
IndexPage REF•22
Contents
Page 104 of 227
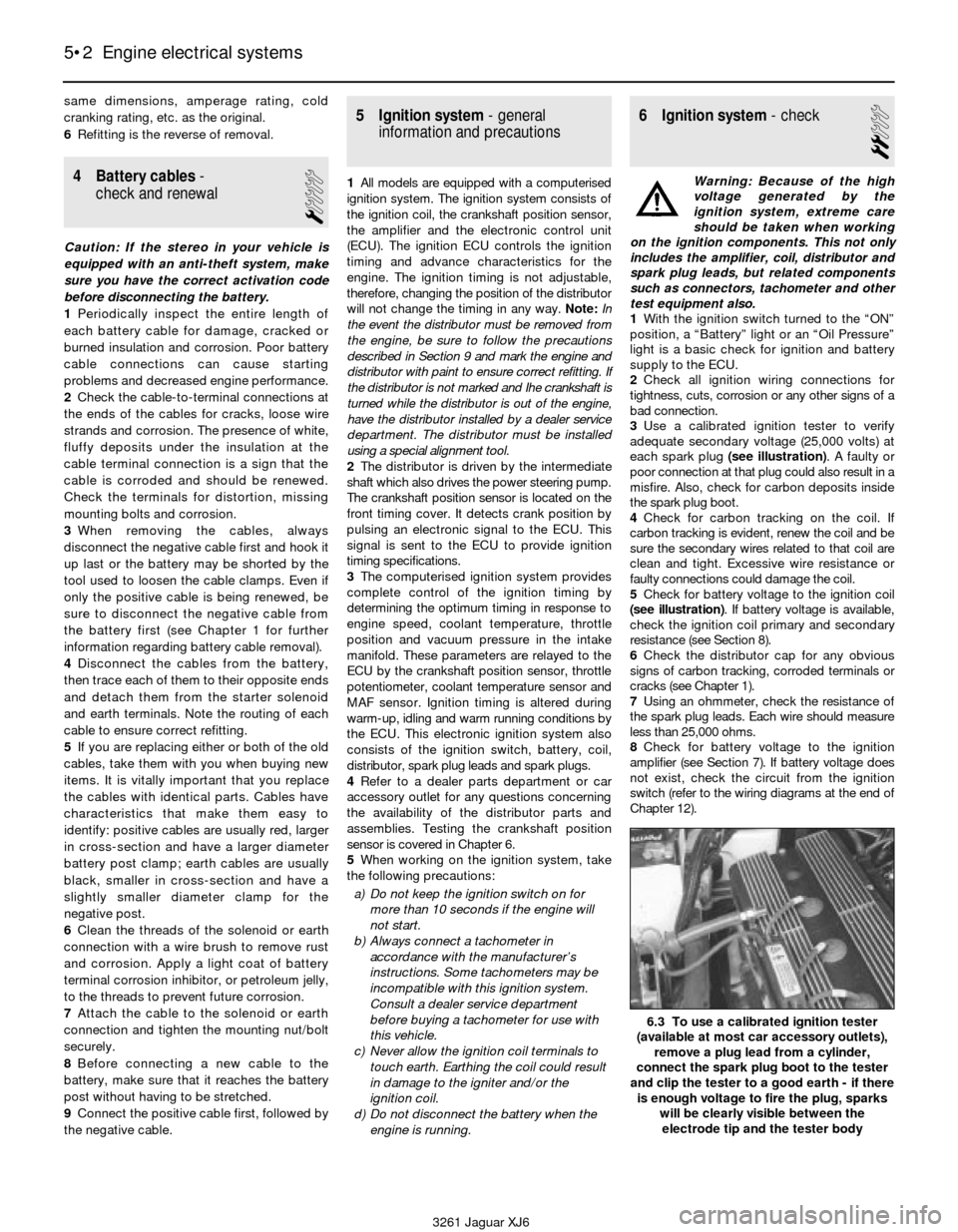
same dimensions, amperage rating, cold
cranking rating, etc. as the original.
6Refitting is the reverse of removal.
4 Battery cables-
check and renewal
1
Caution: If the stereo in your vehicle is
equipped with an anti-theft system, make
sure you have the correct activation code
before disconnecting the battery.
1Periodically inspect the entire length of
each battery cable for damage, cracked or
burned insulation and corrosion. Poor battery
cable connections can cause starting
problems and decreased engine performance.
2Check the cable-to-terminal connections at
the ends of the cables for cracks, loose wire
strands and corrosion. The presence of white,
fluffy deposits under the insulation at the
cable terminal connection is a sign that the
cable is corroded and should be renewed.
Check the terminals for distortion, missing
mounting bolts and corrosion.
3When removing the cables, always
disconnect the negative cable first and hook it
up last or the battery may be shorted by the
tool used to loosen the cable clamps. Even if
only the positive cable is being renewed, be
sure to disconnect the negative cable from
the battery first (see Chapter 1 for further
information regarding battery cable removal).
4Disconnect the cables from the battery,
then trace each of them to their opposite ends
and detach them from the starter solenoid
and earth terminals. Note the routing of each
cable to ensure correct refitting.
5If you are replacing either or both of the old
cables, take them with you when buying new
items. It is vitally important that you replace
the cables with identical parts. Cables have
characteristics that make them easy to
identify: positive cables are usually red, larger
in cross-section and have a larger diameter
battery post clamp; earth cables are usually
black, smaller in cross-section and have a
slightly smaller diameter clamp for the
negative post.
6Clean the threads of the solenoid or earth
connection with a wire brush to remove rust
and corrosion. Apply a light coat of battery
terminal corrosion inhibitor, or petroleum jelly,
to the threads to prevent future corrosion.
7Attach the cable to the solenoid or earth
connection and tighten the mounting nut/bolt
securely.
8Before connecting a new cable to the
battery, make sure that it reaches the battery
post without having to be stretched.
9Connect the positive cable first, followed by
the negative cable.
5 Ignition system- general
information and precautions
1All models are equipped with a computerised
ignition system. The ignition system consists of
the ignition coil, the crankshaft position sensor,
the amplifier and the electronic control unit
(ECU). The ignition ECU controls the ignition
timing and advance characteristics for the
engine. The ignition timing is not adjustable,
therefore, changing the position of the distributor
will not change the timing in any way. Note:In
the event the distributor must be removed from
the engine, be sure to follow the precautions
described in Section 9 and mark the engine and
distributor with paint to ensure correct refitting. If
the distributor is not marked and Ihe crankshaft is
turned while the distributor is out of the engine,
have the distributor installed by a dealer service
department. The distributor must be installed
using a special alignment tool.
2The distributor is driven by the intermediate
shaft which also drives the power steering pump.
The crankshaft position sensor is located on the
front timing cover. It detects crank position by
pulsing an electronic signal to the ECU. This
signal is sent to the ECU to provide ignition
timing specifications.
3The computerised ignition system provides
complete control of the ignition timing by
determining the optimum timing in response to
engine speed, coolant temperature, throttle
position and vacuum pressure in the intake
manifold. These parameters are relayed to the
ECU by the crankshaft position sensor, throttle
potentiometer, coolant temperature sensor and
MAF sensor. Ignition timing is altered during
warm-up, idling and warm running conditions by
the ECU. This electronic ignition system also
consists of the ignition switch, battery, coil,
distributor, spark plug leads and spark plugs.
4Refer to a dealer parts department or car
accessory outlet for any questions concerning
the availability of the distributor parts and
assemblies. Testing the crankshaft position
sensor is covered in Chapter 6.
5When working on the ignition system, take
the following precautions:
a) Do not keep the ignition switch on for
more than 10 seconds if the engine will
not start.
b) Always connect a tachometer in
accordance with the manufacturer’s
instructions. Some tachometers may be
incompatible with this ignition system.
Consult a dealer service department
before buying a tachometer for use with
this vehicle.
c) Never allow the ignition coil terminals to
touch earth. Earthing the coil could result
in damage to the igniter and/or the
ignition coil.
d) Do not disconnect the battery when the
engine is running.
6 Ignition system- check
2
Warning: Because of the high
voltage generated by the
ignition system, extreme care
should be taken when working
on the ignition components. This not only
includes the amplifier, coil, distributor and
spark plug leads, but related components
such as connectors, tachometer and other
test equipment also.
1With the ignition switch turned to the “ON”
position, a “Battery” light or an “Oil Pressure”
light is a basic check for ignition and battery
supply to the ECU.
2Check all ignition wiring connections for
tightness, cuts, corrosion or any other signs of a
bad connection.
3Use a calibrated ignition tester to verify
adequate secondary voltage (25,000 volts) at
each spark plug (see illustration). A faulty or
poor connection at that plug could also result in a
misfire. Also, check for carbon deposits inside
the spark plug boot.
4Check for carbon tracking on the coil. If
carbon tracking is evident, renew the coil and be
sure the secondary wires related to that coil are
clean and tight. Excessive wire resistance or
faulty connections could damage the coil.
5Check for battery voltage to the ignition coil
(see illustration). If battery voltage is available,
check the ignition coil primary and secondary
resistance (see Section 8).
6Check the distributor cap for any obvious
signs of carbon tracking, corroded terminals or
cracks (see Chapter 1).
7Using an ohmmeter, check the resistance of
the spark plug leads. Each wire should measure
less than 25,000 ohms.
8Check for battery voltage to the ignition
amplifier (see Section 7). If battery voltage does
not exist, check the circuit from the ignition
switch (refer to the wiring diagrams at the end of
Chapter 12).
5•2 Engine electrical systems
6.3 To use a calibrated ignition tester
(available at most car accessory outlets),
remove a plug lead from a cylinder,
connect the spark plug boot to the tester
and clip the tester to a good earth - if there
is enough voltage to fire the plug, sparks
will be clearly visible between the
electrode tip and the tester body
3261 Jaguar XJ6
Page 202 of 227
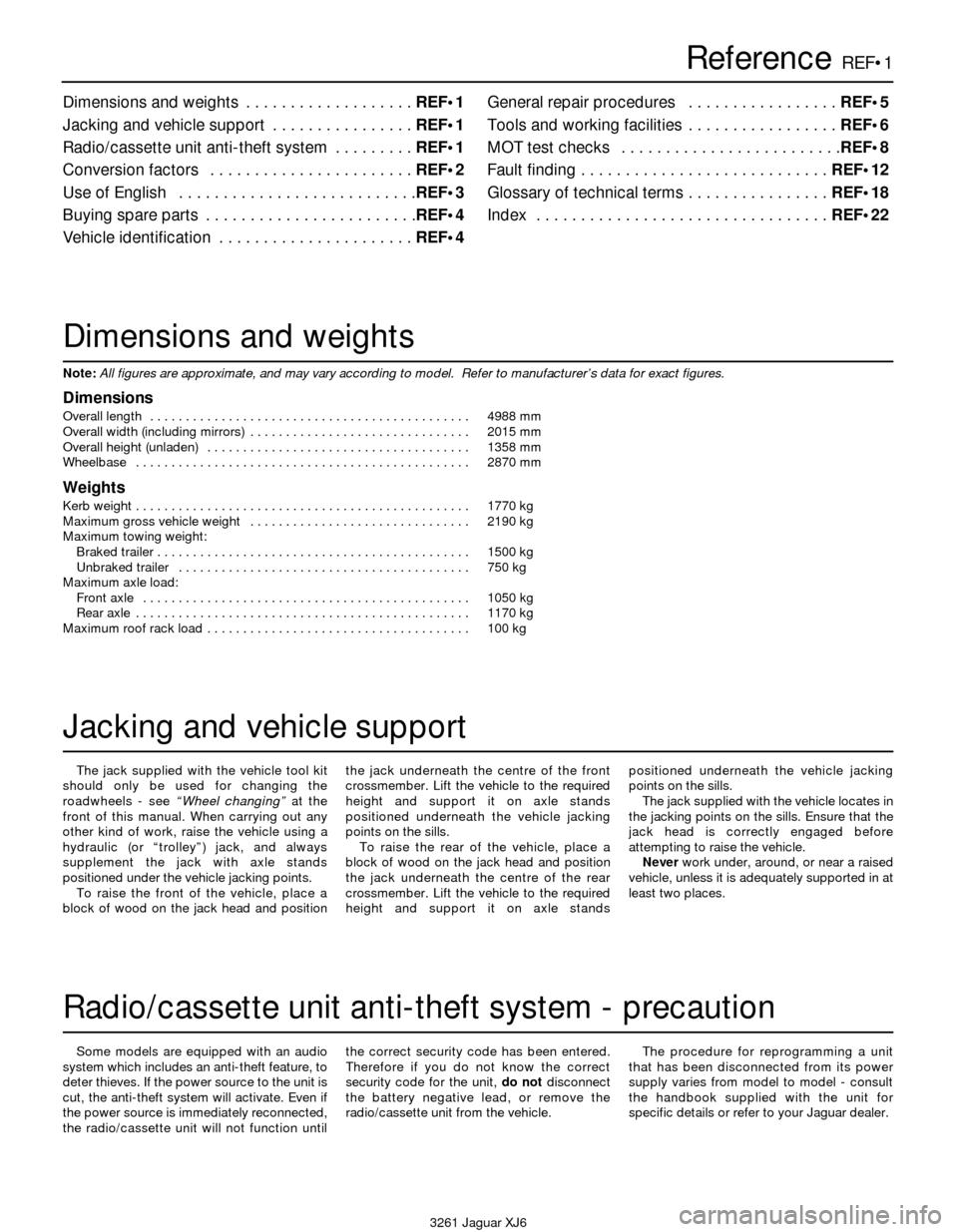
3261 Jaguar XJ6
Dimensions and weights . . . . . . . . . . . . . . . . . . .REF•1
Jacking and vehicle support . . . . . . . . . . . . . . . .REF•1
Radio/cassette unit anti-theft system . . . . . . . . .REF•1
Conversion factors . . . . . . . . . . . . . . . . . . . . . . .REF•2
Use of English . . . . . . . . . . . . . . . . . . . . . . . . . . .REF•3
Buying spare parts . . . . . . . . . . . . . . . . . . . . . . . .REF•4
Vehicle identification . . . . . . . . . . . . . . . . . . . . . .REF•4General repair procedures . . . . . . . . . . . . . . . . .REF•5
Tools and working facilities . . . . . . . . . . . . . . . . .REF•6
MOT test checks . . . . . . . . . . . . . . . . . . . . . . . . .REF•8
Fault finding . . . . . . . . . . . . . . . . . . . . . . . . . . . .REF•12
Glossary of technical terms . . . . . . . . . . . . . . . .REF•18
Index . . . . . . . . . . . . . . . . . . . . . . . . . . . . . . . . .REF•22
Dimensions and weights
Note:All figures are approximate, and may vary according to model. Refer to manufacturer’s data for exact figures.
Dimensions
Overall length . . . . . . . . . . . . . . . . . . . . . . . . . . . . . . . . . . . . . . . . . . . . . 4988 mm
Overall width (including mirrors) . . . . . . . . . . . . . . . . . . . . . . . . . . . . . . . 2015 mm
Overall height (unladen) . . . . . . . . . . . . . . . . . . . . . . . . . . . . . . . . . . . . . 1358 mm
Wheelbase . . . . . . . . . . . . . . . . . . . . . . . . . . . . . . . . . . . . . . . . . . . . . . . 2870 mm
Weights
Kerb weight . . . . . . . . . . . . . . . . . . . . . . . . . . . . . . . . . . . . . . . . . . . . . . . 1770 kg
Maximum gross vehicle weight . . . . . . . . . . . . . . . . . . . . . . . . . . . . . . . 2190 kg
Maximum towing weight:
Braked trailer . . . . . . . . . . . . . . . . . . . . . . . . . . . . . . . . . . . . . . . . . . . . 1500 kg
Unbraked trailer . . . . . . . . . . . . . . . . . . . . . . . . . . . . . . . . . . . . . . . . . 750 kg
Maximum axle load:
Front axle . . . . . . . . . . . . . . . . . . . . . . . . . . . . . . . . . . . . . . . . . . . . . . 1050 kg
Rear axle . . . . . . . . . . . . . . . . . . . . . . . . . . . . . . . . . . . . . . . . . . . . . . . 1170 kg
Maximum roof rack load . . . . . . . . . . . . . . . . . . . . . . . . . . . . . . . . . . . . . 100 kg
ReferenceREF•1
Radio/cassette unit anti-theft system - precaution
Some models are equipped with an audio
system which includes an anti-theft feature, to
deter thieves. If the power source to the unit is
cut, the anti-theft system will activate. Even if
the power source is immediately reconnected,
the radio/cassette unit will not function untilthe correct security code has been entered.
Therefore if you do not know the correct
security code for the unit, do notdisconnect
the battery negative lead, or remove the
radio/cassette unit from the vehicle.The procedure for reprogramming a unit
that has been disconnected from its power
supply varies from model to model - consult
the handbook supplied with the unit for
specific details or refer to your Jaguar dealer. The jack supplied with the vehicle tool kit
should only be used for changing the
roadwheels - see “Wheel changing”at the
front of this manual. When carrying out any
other kind of work, raise the vehicle using a
hydraulic (or “trolley”) jack, and always
supplement the jack with axle stands
positioned under the vehicle jacking points.
To raise the front of the vehicle, place a
block of wood on the jack head and positionthe jack underneath the centre of the front
crossmember. Lift the vehicle to the required
height and support it on axle stands
positioned underneath the vehicle jacking
points on the sills.
To raise the rear of the vehicle, place a
block of wood on the jack head and position
the jack underneath the centre of the rear
crossmember. Lift the vehicle to the required
height and support it on axle standspositioned underneath the vehicle jacking
points on the sills.
The jack supplied with the vehicle locates in
the jacking points on the sills. Ensure that the
jack head is correctly engaged before
attempting to raise the vehicle.
Neverwork under, around, or near a raised
vehicle, unless it is adequately supported in at
least two places.
Jacking and vehicle support
Page 219 of 227
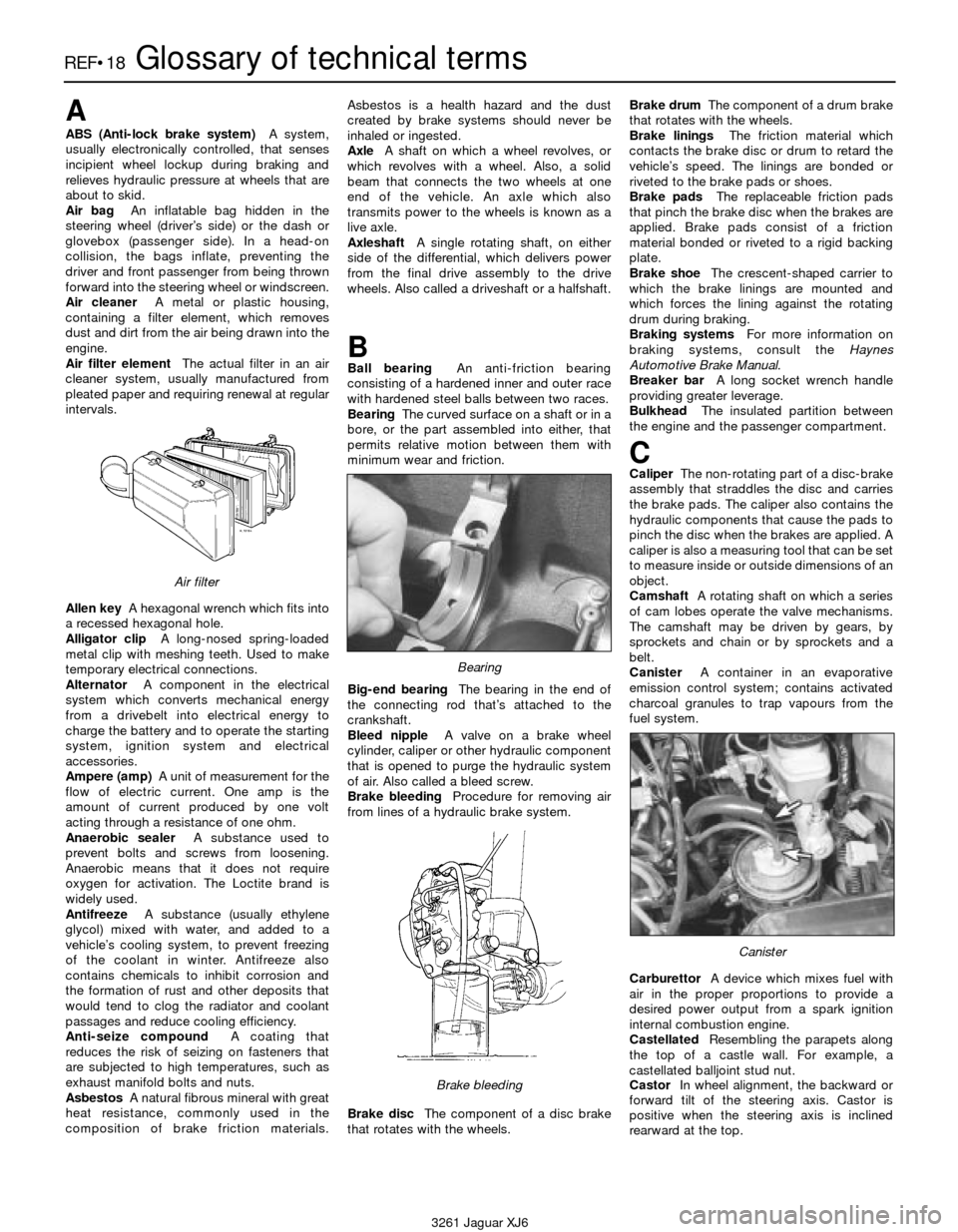
3261 Jaguar XJ6
REF•18Glossary of technical terms
A
ABS (Anti-lock brake system)A system,
usually electronically controlled, that senses
incipient wheel lockup during braking and
relieves hydraulic pressure at wheels that are
about to skid.
Air bag An inflatable bag hidden in the
steering wheel (driver’s side) or the dash or
glovebox (passenger side). In a head-on
collision, the bags inflate, preventing the
driver and front passenger from being thrown
forward into the steering wheel or windscreen.
Air cleanerA metal or plastic housing,
containing a filter element, which removes
dust and dirt from the air being drawn into the
engine.
Air filter elementThe actual filter in an air
cleaner system, usually manufactured from
pleated paper and requiring renewal at regular
intervals.
Allen keyA hexagonal wrench which fits into
a recessed hexagonal hole.
Alligator clipA long-nosed spring-loaded
metal clip with meshing teeth. Used to make
temporary electrical connections.
AlternatorA component in the electrical
system which converts mechanical energy
from a drivebelt into electrical energy to
charge the battery and to operate the starting
system, ignition system and electrical
accessories.
Ampere (amp)A unit of measurement for the
flow of electric current. One amp is the
amount of current produced by one volt
acting through a resistance of one ohm.
Anaerobic sealerA substance used to
prevent bolts and screws from loosening.
Anaerobic means that it does not require
oxygen for activation. The Loctite brand is
widely used.
AntifreezeA substance (usually ethylene
glycol) mixed with water, and added to a
vehicle’s cooling system, to prevent freezing
of the coolant in winter. Antifreeze also
contains chemicals to inhibit corrosion and
the formation of rust and other deposits that
would tend to clog the radiator and coolant
passages and reduce cooling efficiency.
Anti-seize compoundA coating that
reduces the risk of seizing on fasteners that
are subjected to high temperatures, such as
exhaust manifold bolts and nuts.
AsbestosA natural fibrous mineral with great
heat resistance, commonly used in the
composition of brake friction materials.Asbestos is a health hazard and the dust
created by brake systems should never be
inhaled or ingested.
AxleA shaft on which a wheel revolves, or
which revolves with a wheel. Also, a solid
beam that connects the two wheels at one
end of the vehicle. An axle which also
transmits power to the wheels is known as a
live axle.
AxleshaftA single rotating shaft, on either
side of the differential, which delivers power
from the final drive assembly to the drive
wheels. Also called a driveshaft or a halfshaft.
BBall bearingAn anti-friction bearing
consisting of a hardened inner and outer race
with hardened steel balls between two races.
BearingThe curved surface on a shaft or in a
bore, or the part assembled into either, that
permits relative motion between them with
minimum wear and friction.
Big-end bearingThe bearing in the end of
the connecting rod that’s attached to the
crankshaft.
Bleed nippleA valve on a brake wheel
cylinder, caliper or other hydraulic component
that is opened to purge the hydraulic system
of air. Also called a bleed screw.
Brake bleedingProcedure for removing air
from lines of a hydraulic brake system.
Brake discThe component of a disc brake
that rotates with the wheels.Brake drumThe component of a drum brake
that rotates with the wheels.
Brake liningsThe friction material which
contacts the brake disc or drum to retard the
vehicle’s speed. The linings are bonded or
riveted to the brake pads or shoes.
Brake padsThe replaceable friction pads
that pinch the brake disc when the brakes are
applied. Brake pads consist of a friction
material bonded or riveted to a rigid backing
plate.
Brake shoeThe crescent-shaped carrier to
which the brake linings are mounted and
which forces the lining against the rotating
drum during braking.
Braking systemsFor more information on
braking systems, consult the Haynes
Automotive Brake Manual.
Breaker barA long socket wrench handle
providing greater leverage.
BulkheadThe insulated partition between
the engine and the passenger compartment.
CCaliperThe non-rotating part of a disc-brake
assembly that straddles the disc and carries
the brake pads. The caliper also contains the
hydraulic components that cause the pads to
pinch the disc when the brakes are applied. A
caliper is also a measuring tool that can be set
to measure inside or outside dimensions of an
object.
CamshaftA rotating shaft on which a series
of cam lobes operate the valve mechanisms.
The camshaft may be driven by gears, by
sprockets and chain or by sprockets and a
belt.
CanisterA container in an evaporative
emission control system; contains activated
charcoal granules to trap vapours from the
fuel system.
CarburettorA device which mixes fuel with
air in the proper proportions to provide a
desired power output from a spark ignition
internal combustion engine.
CastellatedResembling the parapets along
the top of a castle wall. For example, a
castellated balljoint stud nut.
CastorIn wheel alignment, the backward or
forward tilt of the steering axis. Castor is
positive when the steering axis is inclined
rearward at the top.
Canister
Brake bleeding
Bearing
Air filter
Page 222 of 227
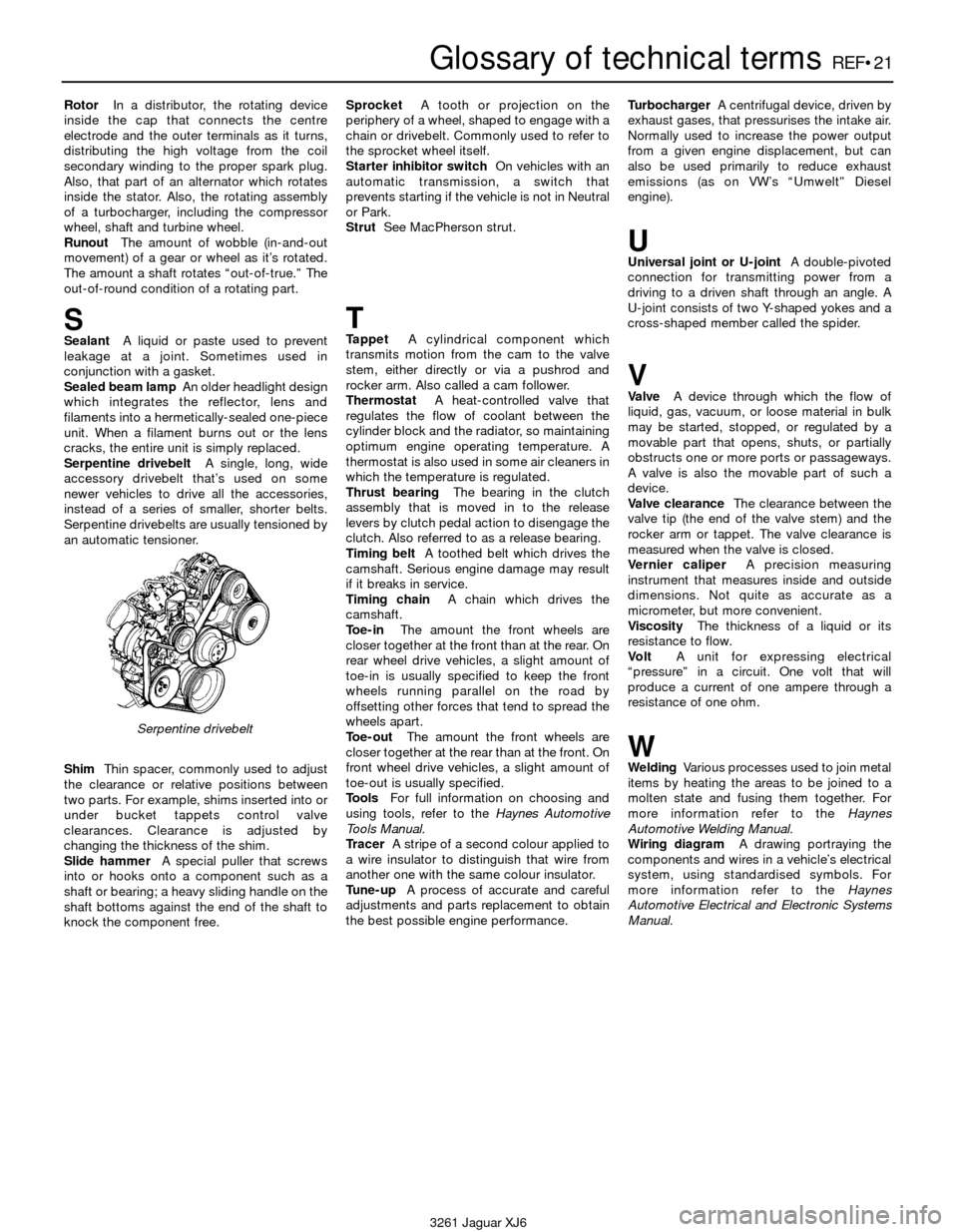
3261 Jaguar XJ6
Glossary of technical termsREF•21
RotorIn a distributor, the rotating device
inside the cap that connects the centre
electrode and the outer terminals as it turns,
distributing the high voltage from the coil
secondary winding to the proper spark plug.
Also, that part of an alternator which rotates
inside the stator. Also, the rotating assembly
of a turbocharger, including the compressor
wheel, shaft and turbine wheel.
RunoutThe amount of wobble (in-and-out
movement) of a gear or wheel as it’s rotated.
The amount a shaft rotates “out-of-true.” The
out-of-round condition of a rotating part.
SSealantA liquid or paste used to prevent
leakage at a joint. Sometimes used in
conjunction with a gasket.
Sealed beam lampAn older headlight design
which integrates the reflector, lens and
filaments into a hermetically-sealed one-piece
unit. When a filament burns out or the lens
cracks, the entire unit is simply replaced.
Serpentine drivebeltA single, long, wide
accessory drivebelt that’s used on some
newer vehicles to drive all the accessories,
instead of a series of smaller, shorter belts.
Serpentine drivebelts are usually tensioned by
an automatic tensioner.
ShimThin spacer, commonly used to adjust
the clearance or relative positions between
two parts. For example, shims inserted into or
under bucket tappets control valve
clearances. Clearance is adjusted by
changing the thickness of the shim.
Slide hammerA special puller that screws
into or hooks onto a component such as a
shaft or bearing; a heavy sliding handle on the
shaft bottoms against the end of the shaft to
knock the component free.SprocketA tooth or projection on the
periphery of a wheel, shaped to engage with a
chain or drivebelt. Commonly used to refer to
the sprocket wheel itself.
Starter inhibitor switchOn vehicles with an
automatic transmission, a switch that
prevents starting if the vehicle is not in Neutral
or Park.
StrutSee MacPherson strut.
TTappetA cylindrical component which
transmits motion from the cam to the valve
stem, either directly or via a pushrod and
rocker arm. Also called a cam follower.
ThermostatA heat-controlled valve that
regulates the flow of coolant between the
cylinder block and the radiator, so maintaining
optimum engine operating temperature. A
thermostat is also used in some air cleaners in
which the temperature is regulated.
Thrust bearingThe bearing in the clutch
assembly that is moved in to the release
levers by clutch pedal action to disengage the
clutch. Also referred to as a release bearing.
Timing beltA toothed belt which drives the
camshaft. Serious engine damage may result
if it breaks in service.
Timing chainA chain which drives the
camshaft.
Toe-inThe amount the front wheels are
closer together at the front than at the rear. On
rear wheel drive vehicles, a slight amount of
toe-in is usually specified to keep the front
wheels running parallel on the road by
offsetting other forces that tend to spread the
wheels apart.
Toe-outThe amount the front wheels are
closer together at the rear than at the front. On
front wheel drive vehicles, a slight amount of
toe-out is usually specified.
ToolsFor full information on choosing and
using tools, refer to the Haynes Automotive
Tools Manual.
TracerA stripe of a second colour applied to
a wire insulator to distinguish that wire from
another one with the same colour insulator.
Tune-upA process of accurate and careful
adjustments and parts replacement to obtain
the best possible engine performance.TurbochargerA centrifugal device, driven by
exhaust gases, that pressurises the intake air.
Normally used to increase the power output
from a given engine displacement, but can
also be used primarily to reduce exhaust
emissions (as on VW’s “Umwelt” Diesel
engine).
UUniversal joint or U-jointA double-pivoted
connection for transmitting power from a
driving to a driven shaft through an angle. A
U-joint consists of two Y-shaped yokes and a
cross-shaped member called the spider.
VValveA device through which the flow of
liquid, gas, vacuum, or loose material in bulk
may be started, stopped, or regulated by a
movable part that opens, shuts, or partially
obstructs one or more ports or passageways.
A valve is also the movable part of such a
device.
Valve clearanceThe clearance between the
valve tip (the end of the valve stem) and the
rocker arm or tappet. The valve clearance is
measured when the valve is closed.
Vernier caliperA precision measuring
instrument that measures inside and outside
dimensions. Not quite as accurate as a
micrometer, but more convenient.
ViscosityThe thickness of a liquid or its
resistance to flow.
VoltA unit for expressing electrical
“pressure” in a circuit. One volt that will
produce a current of one ampere through a
resistance of one ohm.
WWeldingVarious processes used to join metal
items by heating the areas to be joined to a
molten state and fusing them together. For
more information refer to the Haynes
Automotive Welding Manual.
Wiring diagramA drawing portraying the
components and wires in a vehicle’s electrical
system, using standardised symbols. For
more information refer to the Haynes
Automotive Electrical and Electronic Systems
Manual.
Serpentine drivebelt
Page 223 of 227
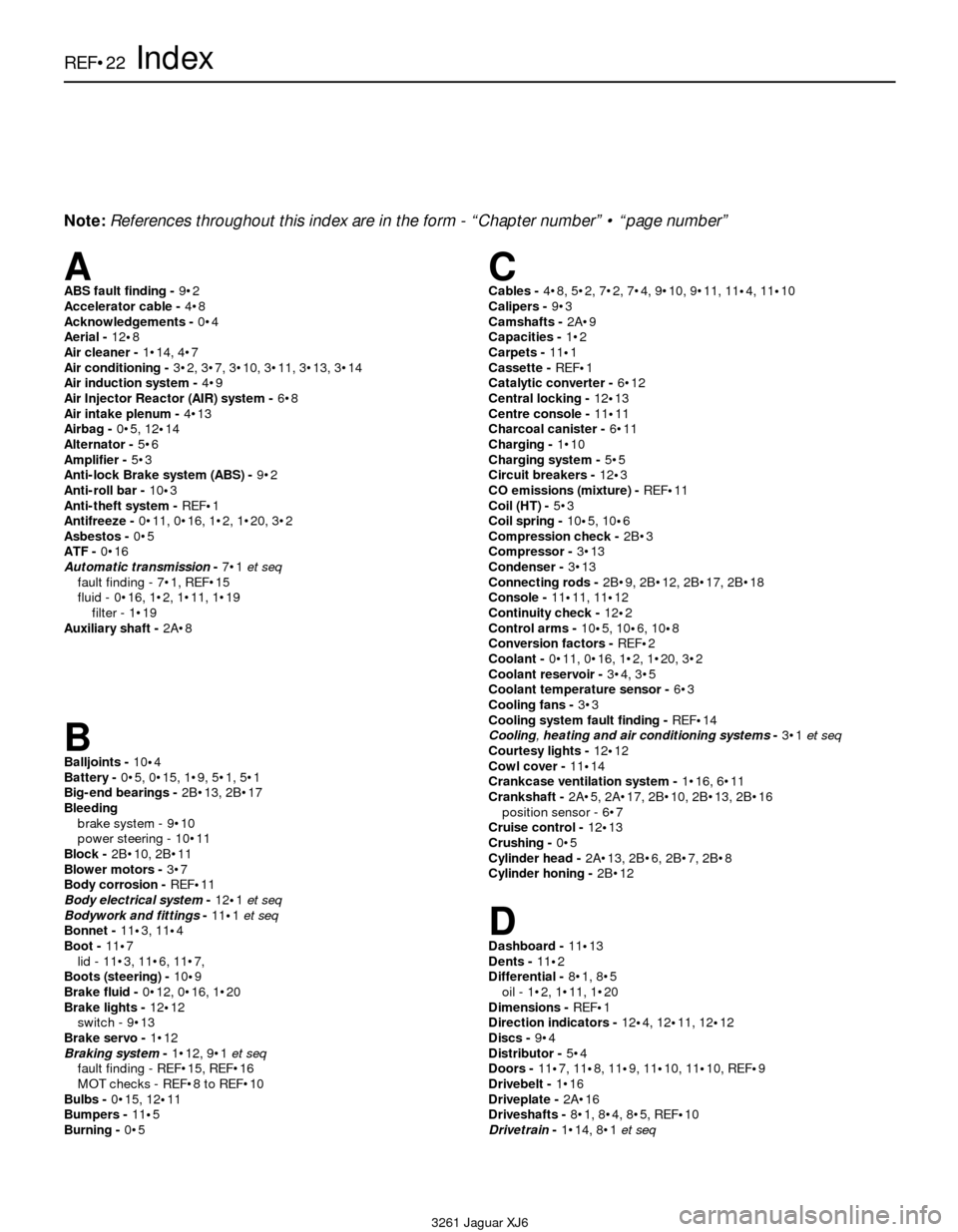
3261 Jaguar XJ6
REF•22Index
AABS fault finding -9•2
Accelerator cable -4•8
Acknowledgements -0•4
Aerial - 12•8
Air cleaner -1•14, 4•7
Air conditioning -3•2, 3•7, 3•10, 3•11, 3•13, 3•14
Air induction system -4•9
Air Injector Reactor (AIR) system -6•8
Air intake plenum -4•13
Airbag - 0•5, 12•14
Alternator -5•6
Amplifier -5•3
Anti-lock Brake system (ABS) -9•2
Anti-roll bar - 10•3
Anti-theft system - REF•1
Antifreeze -0•11, 0•16, 1•2, 1•20, 3•2
Asbestos -0•5
ATF -0•16
Automatic transmission-7•1et seq
fault finding - 7•1, REF•15
fluid - 0•16, 1•2, 1•11, 1•19
filter - 1•19
Auxiliary shaft -2A•8
BBalljoints - 10•4
Battery -0•5, 0•15, 1•9, 5•1, 5•1
Big-end bearings -2B•13, 2B•17
Bleeding
brake system - 9•10
power steering - 10•11
Block -2B•10, 2B•11
Blower motors -3•7
Body corrosion - REF•11
Body electrical system- 12•1et seq
Bodywork and fittings- 11•1et seq
Bonnet - 11•3, 11•4
Boot - 11•7
lid - 11•3, 11•6, 11•7,
Boots (steering) - 10•9
Brake fluid -0•12, 0•16, 1•20
Brake lights - 12•12
switch - 9•13
Brake servo -1•12
Braking system-1•12, 9•1et seq
fault finding - REF•15, REF•16
MOT checks - REF•8 to REF•10
Bulbs -0•15, 12•11
Bumpers - 11•5
Burning -0•5
CCables -4•8, 5•2, 7•2, 7•4, 9•10, 9•11, 11•4, 11•10
Calipers -9•3
Camshafts -2A•9
Capacities -1•2
Carpets - 11•1
Cassette - REF•1
Catalytic converter -6•12
Central locking - 12•13
Centre console - 11•11
Charcoal canister -6•11
Charging -1•10
Charging system -5•5
Circuit breakers - 12•3
CO emissions (mixture) - REF•11
Coil (HT) -5•3
Coil spring - 10•5, 10•6
Compression check -2B•3
Compressor -3•13
Condenser -3•13
Connecting rods -2B•9, 2B•12, 2B•17, 2B•18
Console - 11•11, 11•12
Continuity check - 12•2
Control arms - 10•5, 10•6, 10•8
Conversion factors - REF•2
Coolant -0•11, 0•16, 1•2, 1•20, 3•2
Coolant reservoir -3•4, 3•5
Coolant temperature sensor -6•3
Cooling fans -3•3
Cooling system fault finding - REF•14
Cooling,heating and air conditioning systems-3•1et seq
Courtesy lights - 12•12
Cowl cover - 11•14
Crankcase ventilation system -1•16, 6•11
Crankshaft -2A•5, 2A•17, 2B•10, 2B•13, 2B•16
position sensor - 6•7
Cruise control - 12•13
Crushing -0•5
Cylinder head -2A•13, 2B•6, 2B•7, 2B•8
Cylinder honing -2B•12
DDashboard - 11•13
Dents - 11•2
Differential -8•1, 8•5
oil - 1•2, 1•11, 1•20
Dimensions - REF•1
Direction indicators - 12•4, 12•11, 12•12
Discs -9•4
Distributor -5•4
Doors - 11•7, 11•8, 11•9, 11•10, 11•10, REF•9
Drivebelt -1•16
Driveplate -2A•16
Driveshafts -8•1, 8•4, 8•5, REF•10
Drivetrain-1•14, 8•1et seq
Note:References throughout this index are in the form - “Chapter number” • “page number”