Ignition switch JEEP GRAND CHEROKEE 2002 WJ / 2.G User Guide
[x] Cancel search | Manufacturer: JEEP, Model Year: 2002, Model line: GRAND CHEROKEE, Model: JEEP GRAND CHEROKEE 2002 WJ / 2.GPages: 2199, PDF Size: 76.01 MB
Page 300 of 2199
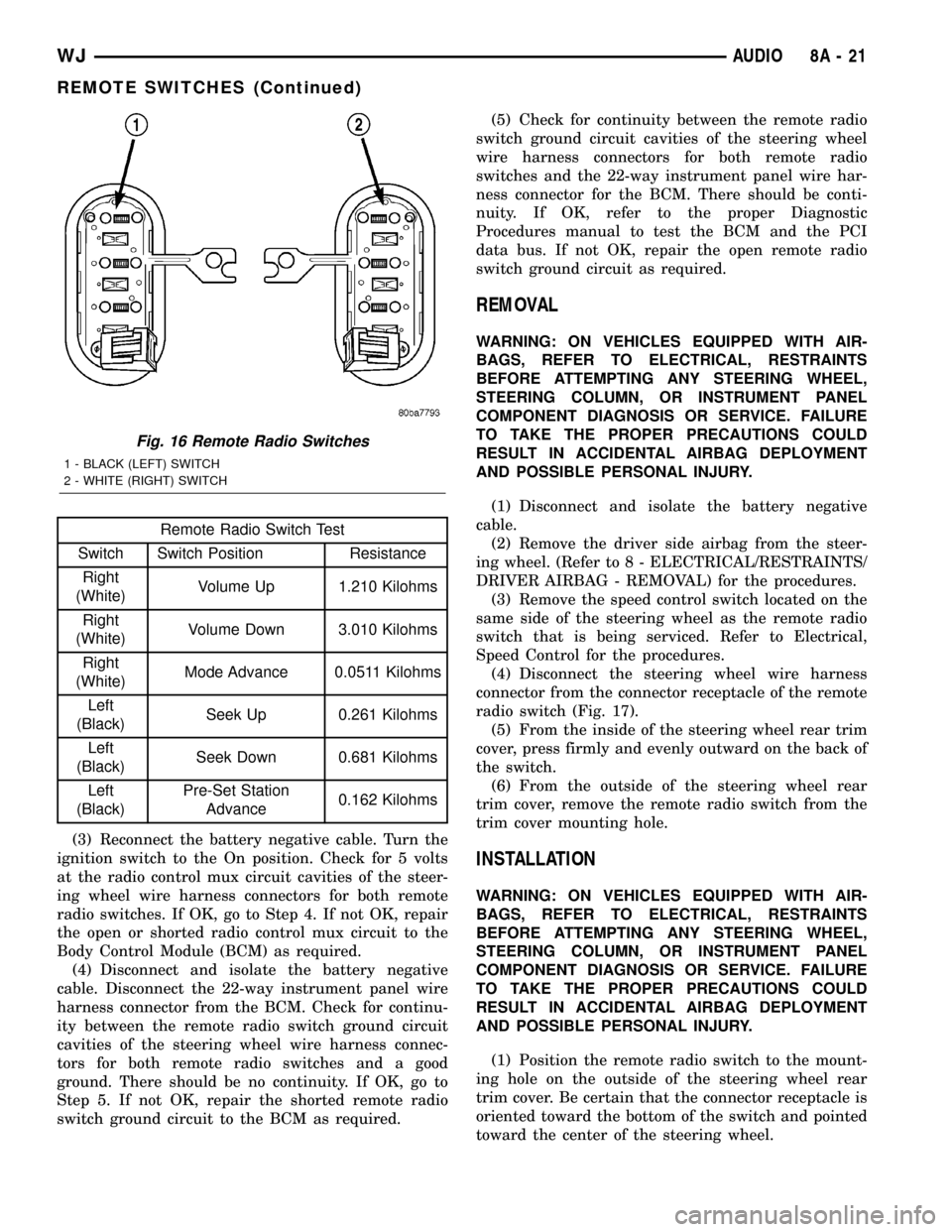
Remote Radio Switch Test
Switch Switch Position Resistance
Right
(White)Volume Up 1.210 Kilohms
Right
(White)Volume Down 3.010 Kilohms
Right
(White)Mode Advance 0.0511 Kilohms
Left
(Black)Seek Up 0.261 Kilohms
Left
(Black)Seek Down 0.681 Kilohms
Left
(Black)Pre-Set Station
Advance0.162 Kilohms
(3) Reconnect the battery negative cable. Turn the
ignition switch to the On position. Check for 5 volts
at the radio control mux circuit cavities of the steer-
ing wheel wire harness connectors for both remote
radio switches. If OK, go to Step 4. If not OK, repair
the open or shorted radio control mux circuit to the
Body Control Module (BCM) as required.
(4) Disconnect and isolate the battery negative
cable. Disconnect the 22-way instrument panel wire
harness connector from the BCM. Check for continu-
ity between the remote radio switch ground circuit
cavities of the steering wheel wire harness connec-
tors for both remote radio switches and a good
ground. There should be no continuity. If OK, go to
Step 5. If not OK, repair the shorted remote radio
switch ground circuit to the BCM as required.(5) Check for continuity between the remote radio
switch ground circuit cavities of the steering wheel
wire harness connectors for both remote radio
switches and the 22-way instrument panel wire har-
ness connector for the BCM. There should be conti-
nuity. If OK, refer to the proper Diagnostic
Procedures manual to test the BCM and the PCI
data bus. If not OK, repair the open remote radio
switch ground circuit as required.
REMOVAL
WARNING: ON VEHICLES EQUIPPED WITH AIR-
BAGS, REFER TO ELECTRICAL, RESTRAINTS
BEFORE ATTEMPTING ANY STEERING WHEEL,
STEERING COLUMN, OR INSTRUMENT PANEL
COMPONENT DIAGNOSIS OR SERVICE. FAILURE
TO TAKE THE PROPER PRECAUTIONS COULD
RESULT IN ACCIDENTAL AIRBAG DEPLOYMENT
AND POSSIBLE PERSONAL INJURY.
(1) Disconnect and isolate the battery negative
cable.
(2) Remove the driver side airbag from the steer-
ing wheel. (Refer to 8 - ELECTRICAL/RESTRAINTS/
DRIVER AIRBAG - REMOVAL) for the procedures.
(3) Remove the speed control switch located on the
same side of the steering wheel as the remote radio
switch that is being serviced. Refer to Electrical,
Speed Control for the procedures.
(4) Disconnect the steering wheel wire harness
connector from the connector receptacle of the remote
radio switch (Fig. 17).
(5) From the inside of the steering wheel rear trim
cover, press firmly and evenly outward on the back of
the switch.
(6) From the outside of the steering wheel rear
trim cover, remove the remote radio switch from the
trim cover mounting hole.
INSTALLATION
WARNING: ON VEHICLES EQUIPPED WITH AIR-
BAGS, REFER TO ELECTRICAL, RESTRAINTS
BEFORE ATTEMPTING ANY STEERING WHEEL,
STEERING COLUMN, OR INSTRUMENT PANEL
COMPONENT DIAGNOSIS OR SERVICE. FAILURE
TO TAKE THE PROPER PRECAUTIONS COULD
RESULT IN ACCIDENTAL AIRBAG DEPLOYMENT
AND POSSIBLE PERSONAL INJURY.
(1) Position the remote radio switch to the mount-
ing hole on the outside of the steering wheel rear
trim cover. Be certain that the connector receptacle is
oriented toward the bottom of the switch and pointed
toward the center of the steering wheel.
Fig. 16 Remote Radio Switches
1 - BLACK (LEFT) SWITCH
2 - WHITE (RIGHT) SWITCH
WJAUDIO 8A - 21
REMOTE SWITCHES (Continued)
Page 302 of 2199
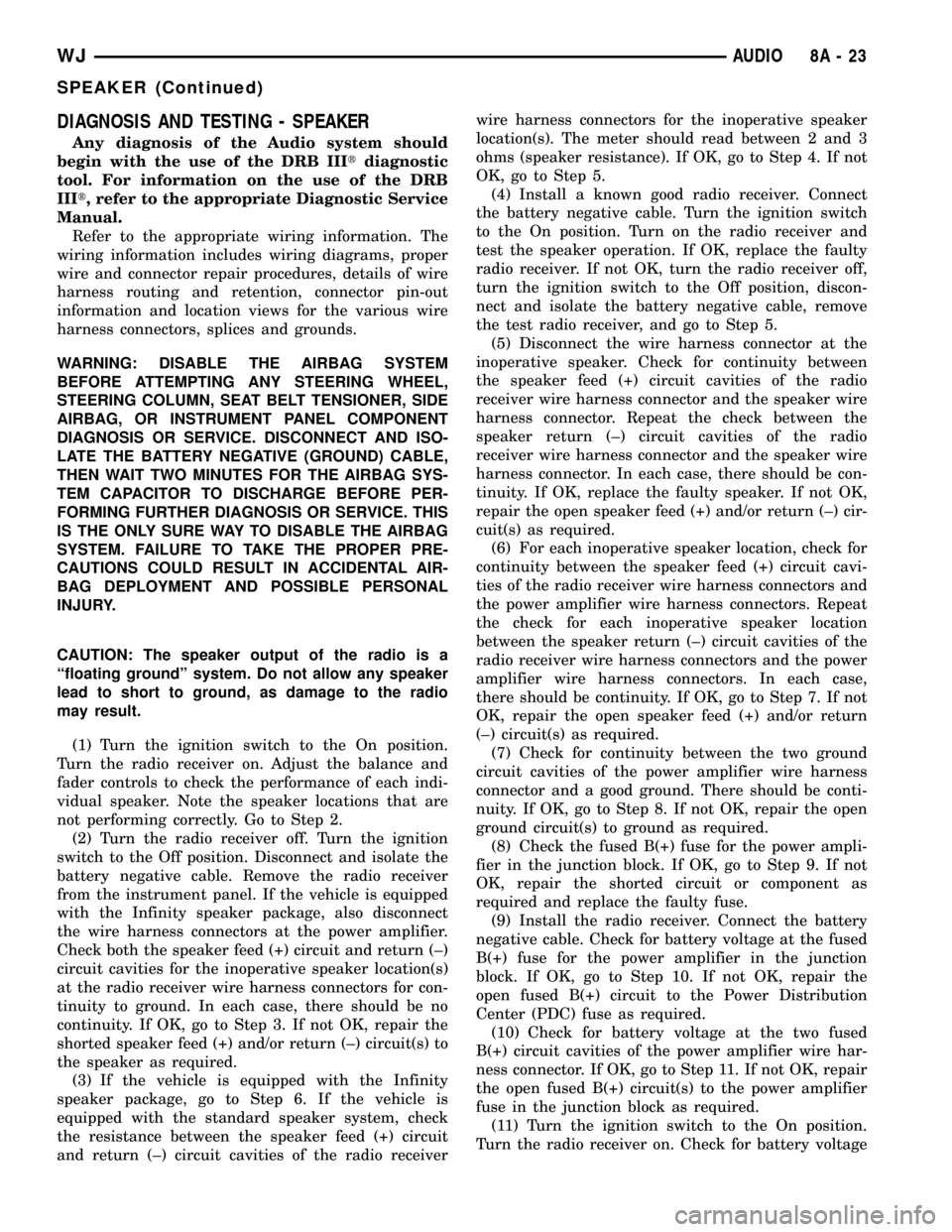
DIAGNOSIS AND TESTING - SPEAKER
Any diagnosis of the Audio system should
begin with the use of the DRB IIItdiagnostic
tool. For information on the use of the DRB
IIIt, refer to the appropriate Diagnostic Service
Manual.
Refer to the appropriate wiring information. The
wiring information includes wiring diagrams, proper
wire and connector repair procedures, details of wire
harness routing and retention, connector pin-out
information and location views for the various wire
harness connectors, splices and grounds.
WARNING: DISABLE THE AIRBAG SYSTEM
BEFORE ATTEMPTING ANY STEERING WHEEL,
STEERING COLUMN, SEAT BELT TENSIONER, SIDE
AIRBAG, OR INSTRUMENT PANEL COMPONENT
DIAGNOSIS OR SERVICE. DISCONNECT AND ISO-
LATE THE BATTERY NEGATIVE (GROUND) CABLE,
THEN WAIT TWO MINUTES FOR THE AIRBAG SYS-
TEM CAPACITOR TO DISCHARGE BEFORE PER-
FORMING FURTHER DIAGNOSIS OR SERVICE. THIS
IS THE ONLY SURE WAY TO DISABLE THE AIRBAG
SYSTEM. FAILURE TO TAKE THE PROPER PRE-
CAUTIONS COULD RESULT IN ACCIDENTAL AIR-
BAG DEPLOYMENT AND POSSIBLE PERSONAL
INJURY.
CAUTION: The speaker output of the radio is a
ªfloating groundº system. Do not allow any speaker
lead to short to ground, as damage to the radio
may result.
(1) Turn the ignition switch to the On position.
Turn the radio receiver on. Adjust the balance and
fader controls to check the performance of each indi-
vidual speaker. Note the speaker locations that are
not performing correctly. Go to Step 2.
(2) Turn the radio receiver off. Turn the ignition
switch to the Off position. Disconnect and isolate the
battery negative cable. Remove the radio receiver
from the instrument panel. If the vehicle is equipped
with the Infinity speaker package, also disconnect
the wire harness connectors at the power amplifier.
Check both the speaker feed (+) circuit and return (±)
circuit cavities for the inoperative speaker location(s)
at the radio receiver wire harness connectors for con-
tinuity to ground. In each case, there should be no
continuity. If OK, go to Step 3. If not OK, repair the
shorted speaker feed (+) and/or return (±) circuit(s) to
the speaker as required.
(3) If the vehicle is equipped with the Infinity
speaker package, go to Step 6. If the vehicle is
equipped with the standard speaker system, check
the resistance between the speaker feed (+) circuit
and return (±) circuit cavities of the radio receiverwire harness connectors for the inoperative speaker
location(s). The meter should read between 2 and 3
ohms (speaker resistance). If OK, go to Step 4. If not
OK, go to Step 5.
(4) Install a known good radio receiver. Connect
the battery negative cable. Turn the ignition switch
to the On position. Turn on the radio receiver and
test the speaker operation. If OK, replace the faulty
radio receiver. If not OK, turn the radio receiver off,
turn the ignition switch to the Off position, discon-
nect and isolate the battery negative cable, remove
the test radio receiver, and go to Step 5.
(5) Disconnect the wire harness connector at the
inoperative speaker. Check for continuity between
the speaker feed (+) circuit cavities of the radio
receiver wire harness connector and the speaker wire
harness connector. Repeat the check between the
speaker return (±) circuit cavities of the radio
receiver wire harness connector and the speaker wire
harness connector. In each case, there should be con-
tinuity. If OK, replace the faulty speaker. If not OK,
repair the open speaker feed (+) and/or return (±) cir-
cuit(s) as required.
(6) For each inoperative speaker location, check for
continuity between the speaker feed (+) circuit cavi-
ties of the radio receiver wire harness connectors and
the power amplifier wire harness connectors. Repeat
the check for each inoperative speaker location
between the speaker return (±) circuit cavities of the
radio receiver wire harness connectors and the power
amplifier wire harness connectors. In each case,
there should be continuity. If OK, go to Step 7. If not
OK, repair the open speaker feed (+) and/or return
(±) circuit(s) as required.
(7) Check for continuity between the two ground
circuit cavities of the power amplifier wire harness
connector and a good ground. There should be conti-
nuity. If OK, go to Step 8. If not OK, repair the open
ground circuit(s) to ground as required.
(8) Check the fused B(+) fuse for the power ampli-
fier in the junction block. If OK, go to Step 9. If not
OK, repair the shorted circuit or component as
required and replace the faulty fuse.
(9) Install the radio receiver. Connect the battery
negative cable. Check for battery voltage at the fused
B(+) fuse for the power amplifier in the junction
block. If OK, go to Step 10. If not OK, repair the
open fused B(+) circuit to the Power Distribution
Center (PDC) fuse as required.
(10) Check for battery voltage at the two fused
B(+) circuit cavities of the power amplifier wire har-
ness connector. If OK, go to Step 11. If not OK, repair
the open fused B(+) circuit(s) to the power amplifier
fuse in the junction block as required.
(11) Turn the ignition switch to the On position.
Turn the radio receiver on. Check for battery voltage
WJAUDIO 8A - 23
SPEAKER (Continued)
Page 303 of 2199
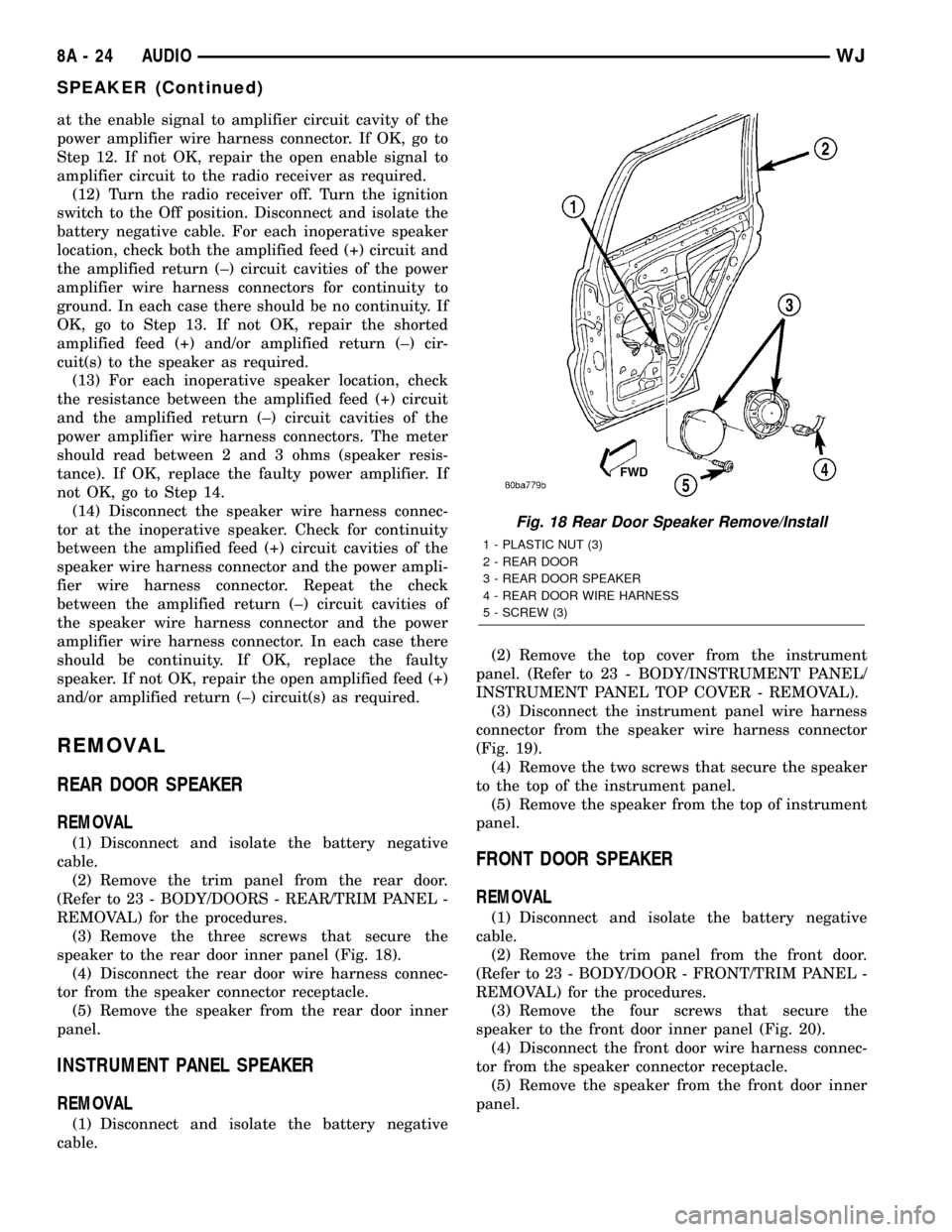
at the enable signal to amplifier circuit cavity of the
power amplifier wire harness connector. If OK, go to
Step 12. If not OK, repair the open enable signal to
amplifier circuit to the radio receiver as required.
(12) Turn the radio receiver off. Turn the ignition
switch to the Off position. Disconnect and isolate the
battery negative cable. For each inoperative speaker
location, check both the amplified feed (+) circuit and
the amplified return (±) circuit cavities of the power
amplifier wire harness connectors for continuity to
ground. In each case there should be no continuity. If
OK, go to Step 13. If not OK, repair the shorted
amplified feed (+) and/or amplified return (±) cir-
cuit(s) to the speaker as required.
(13) For each inoperative speaker location, check
the resistance between the amplified feed (+) circuit
and the amplified return (±) circuit cavities of the
power amplifier wire harness connectors. The meter
should read between 2 and 3 ohms (speaker resis-
tance). If OK, replace the faulty power amplifier. If
not OK, go to Step 14.
(14) Disconnect the speaker wire harness connec-
tor at the inoperative speaker. Check for continuity
between the amplified feed (+) circuit cavities of the
speaker wire harness connector and the power ampli-
fier wire harness connector. Repeat the check
between the amplified return (±) circuit cavities of
the speaker wire harness connector and the power
amplifier wire harness connector. In each case there
should be continuity. If OK, replace the faulty
speaker. If not OK, repair the open amplified feed (+)
and/or amplified return (±) circuit(s) as required.
REMOVAL
REAR DOOR SPEAKER
REMOVAL
(1) Disconnect and isolate the battery negative
cable.
(2) Remove the trim panel from the rear door.
(Refer to 23 - BODY/DOORS - REAR/TRIM PANEL -
REMOVAL) for the procedures.
(3) Remove the three screws that secure the
speaker to the rear door inner panel (Fig. 18).
(4) Disconnect the rear door wire harness connec-
tor from the speaker connector receptacle.
(5) Remove the speaker from the rear door inner
panel.
INSTRUMENT PANEL SPEAKER
REMOVAL
(1) Disconnect and isolate the battery negative
cable.(2) Remove the top cover from the instrument
panel. (Refer to 23 - BODY/INSTRUMENT PANEL/
INSTRUMENT PANEL TOP COVER - REMOVAL).
(3) Disconnect the instrument panel wire harness
connector from the speaker wire harness connector
(Fig. 19).
(4) Remove the two screws that secure the speaker
to the top of the instrument panel.
(5) Remove the speaker from the top of instrument
panel.
FRONT DOOR SPEAKER
REMOVAL
(1) Disconnect and isolate the battery negative
cable.
(2) Remove the trim panel from the front door.
(Refer to 23 - BODY/DOOR - FRONT/TRIM PANEL -
REMOVAL) for the procedures.
(3) Remove the four screws that secure the
speaker to the front door inner panel (Fig. 20).
(4) Disconnect the front door wire harness connec-
tor from the speaker connector receptacle.
(5) Remove the speaker from the front door inner
panel.
Fig. 18 Rear Door Speaker Remove/Install
1 - PLASTIC NUT (3)
2 - REAR DOOR
3 - REAR DOOR SPEAKER
4 - REAR DOOR WIRE HARNESS
5 - SCREW (3)
8A - 24 AUDIOWJ
SPEAKER (Continued)
Page 306 of 2199
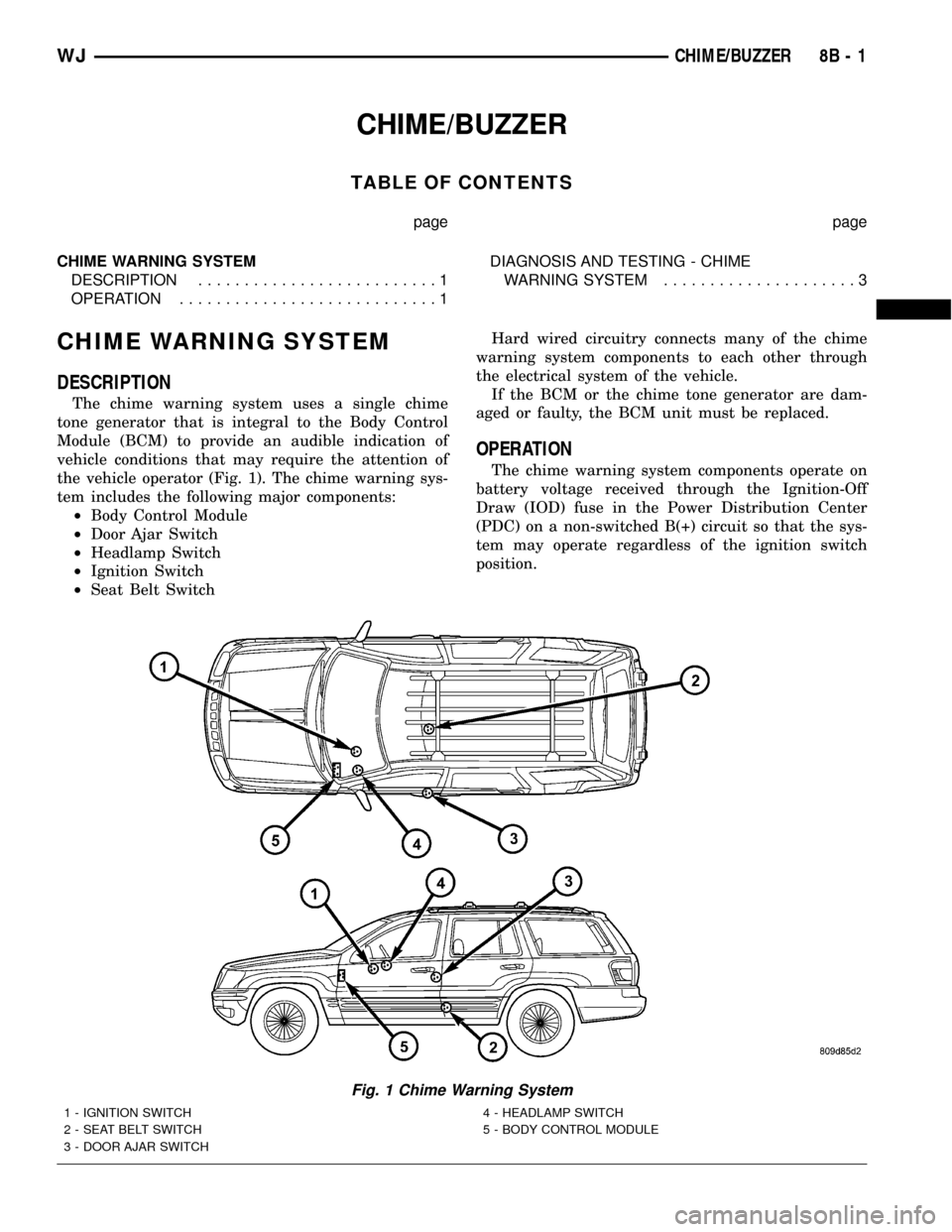
CHIME/BUZZER
TABLE OF CONTENTS
page page
CHIME WARNING SYSTEM
DESCRIPTION..........................1
OPERATION............................1DIAGNOSIS AND TESTING - CHIME
WARNING SYSTEM.....................3
CHIME WARNING SYSTEM
DESCRIPTION
The chime warning system uses a single chime
tone generator that is integral to the Body Control
Module (BCM) to provide an audible indication of
vehicle conditions that may require the attention of
the vehicle operator (Fig. 1). The chime warning sys-
tem includes the following major components:
²Body Control Module
²Door Ajar Switch
²Headlamp Switch
²Ignition Switch
²Seat Belt SwitchHard wired circuitry connects many of the chime
warning system components to each other through
the electrical system of the vehicle.
If the BCM or the chime tone generator are dam-
aged or faulty, the BCM unit must be replaced.
OPERATION
The chime warning system components operate on
battery voltage received through the Ignition-Off
Draw (IOD) fuse in the Power Distribution Center
(PDC) on a non-switched B(+) circuit so that the sys-
tem may operate regardless of the ignition switch
position.
Fig. 1 Chime Warning System
1 - IGNITION SWITCH
2 - SEAT BELT SWITCH
3 - DOOR AJAR SWITCH4 - HEADLAMP SWITCH
5 - BODY CONTROL MODULE
WJCHIME/BUZZER 8B - 1
Page 307 of 2199
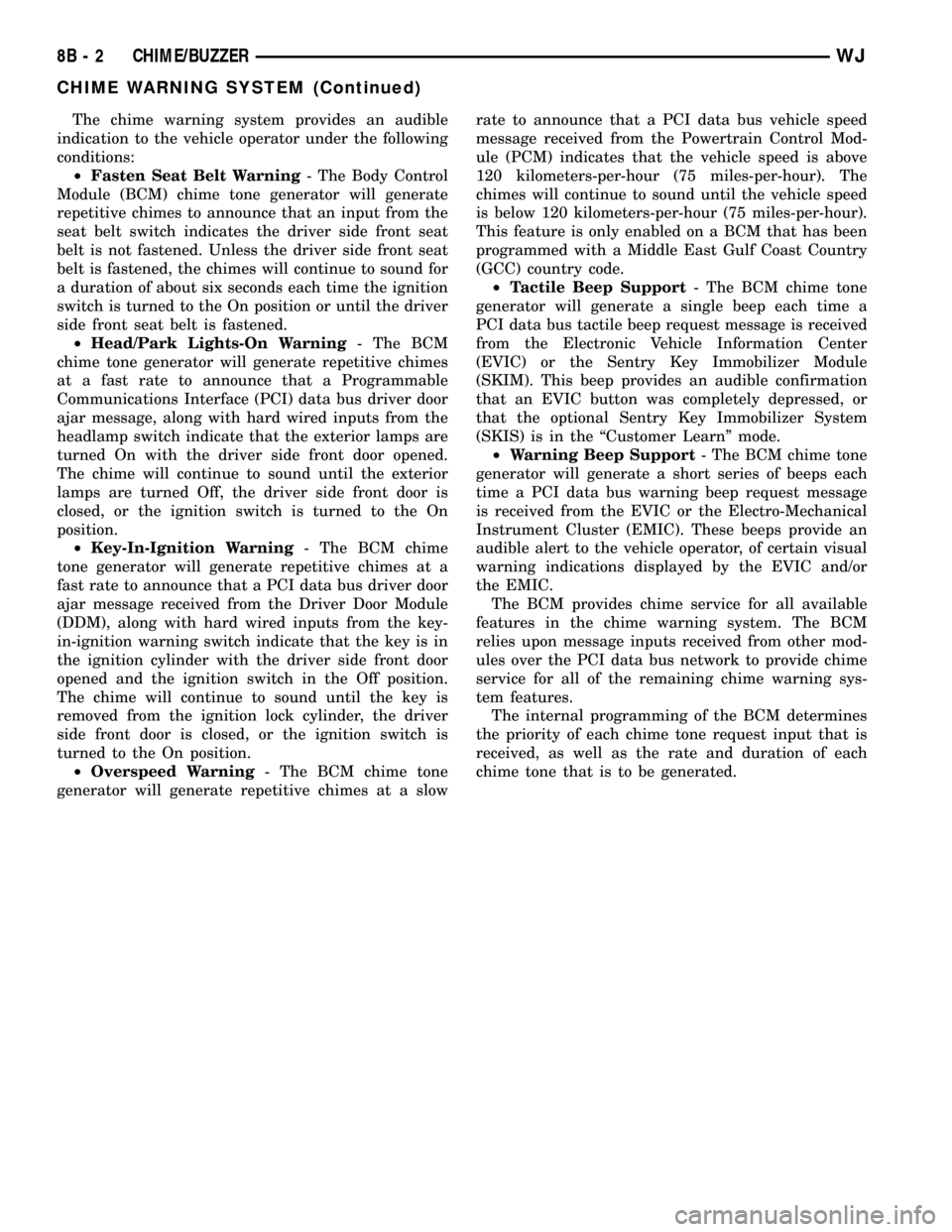
The chime warning system provides an audible
indication to the vehicle operator under the following
conditions:
²Fasten Seat Belt Warning- The Body Control
Module (BCM) chime tone generator will generate
repetitive chimes to announce that an input from the
seat belt switch indicates the driver side front seat
belt is not fastened. Unless the driver side front seat
belt is fastened, the chimes will continue to sound for
a duration of about six seconds each time the ignition
switch is turned to the On position or until the driver
side front seat belt is fastened.
²Head/Park Lights-On Warning- The BCM
chime tone generator will generate repetitive chimes
at a fast rate to announce that a Programmable
Communications Interface (PCI) data bus driver door
ajar message, along with hard wired inputs from the
headlamp switch indicate that the exterior lamps are
turned On with the driver side front door opened.
The chime will continue to sound until the exterior
lamps are turned Off, the driver side front door is
closed, or the ignition switch is turned to the On
position.
²Key-In-Ignition Warning- The BCM chime
tone generator will generate repetitive chimes at a
fast rate to announce that a PCI data bus driver door
ajar message received from the Driver Door Module
(DDM), along with hard wired inputs from the key-
in-ignition warning switch indicate that the key is in
the ignition cylinder with the driver side front door
opened and the ignition switch in the Off position.
The chime will continue to sound until the key is
removed from the ignition lock cylinder, the driver
side front door is closed, or the ignition switch is
turned to the On position.
²Overspeed Warning- The BCM chime tone
generator will generate repetitive chimes at a slowrate to announce that a PCI data bus vehicle speed
message received from the Powertrain Control Mod-
ule (PCM) indicates that the vehicle speed is above
120 kilometers-per-hour (75 miles-per-hour). The
chimes will continue to sound until the vehicle speed
is below 120 kilometers-per-hour (75 miles-per-hour).
This feature is only enabled on a BCM that has been
programmed with a Middle East Gulf Coast Country
(GCC) country code.
²Tactile Beep Support- The BCM chime tone
generator will generate a single beep each time a
PCI data bus tactile beep request message is received
from the Electronic Vehicle Information Center
(EVIC) or the Sentry Key Immobilizer Module
(SKIM). This beep provides an audible confirmation
that an EVIC button was completely depressed, or
that the optional Sentry Key Immobilizer System
(SKIS) is in the ªCustomer Learnº mode.
²Warning Beep Support- The BCM chime tone
generator will generate a short series of beeps each
time a PCI data bus warning beep request message
is received from the EVIC or the Electro-Mechanical
Instrument Cluster (EMIC). These beeps provide an
audible alert to the vehicle operator, of certain visual
warning indications displayed by the EVIC and/or
the EMIC.
The BCM provides chime service for all available
features in the chime warning system. The BCM
relies upon message inputs received from other mod-
ules over the PCI data bus network to provide chime
service for all of the remaining chime warning sys-
tem features.
The internal programming of the BCM determines
the priority of each chime tone request input that is
received, as well as the rate and duration of each
chime tone that is to be generated.
8B - 2 CHIME/BUZZERWJ
CHIME WARNING SYSTEM (Continued)
Page 309 of 2199
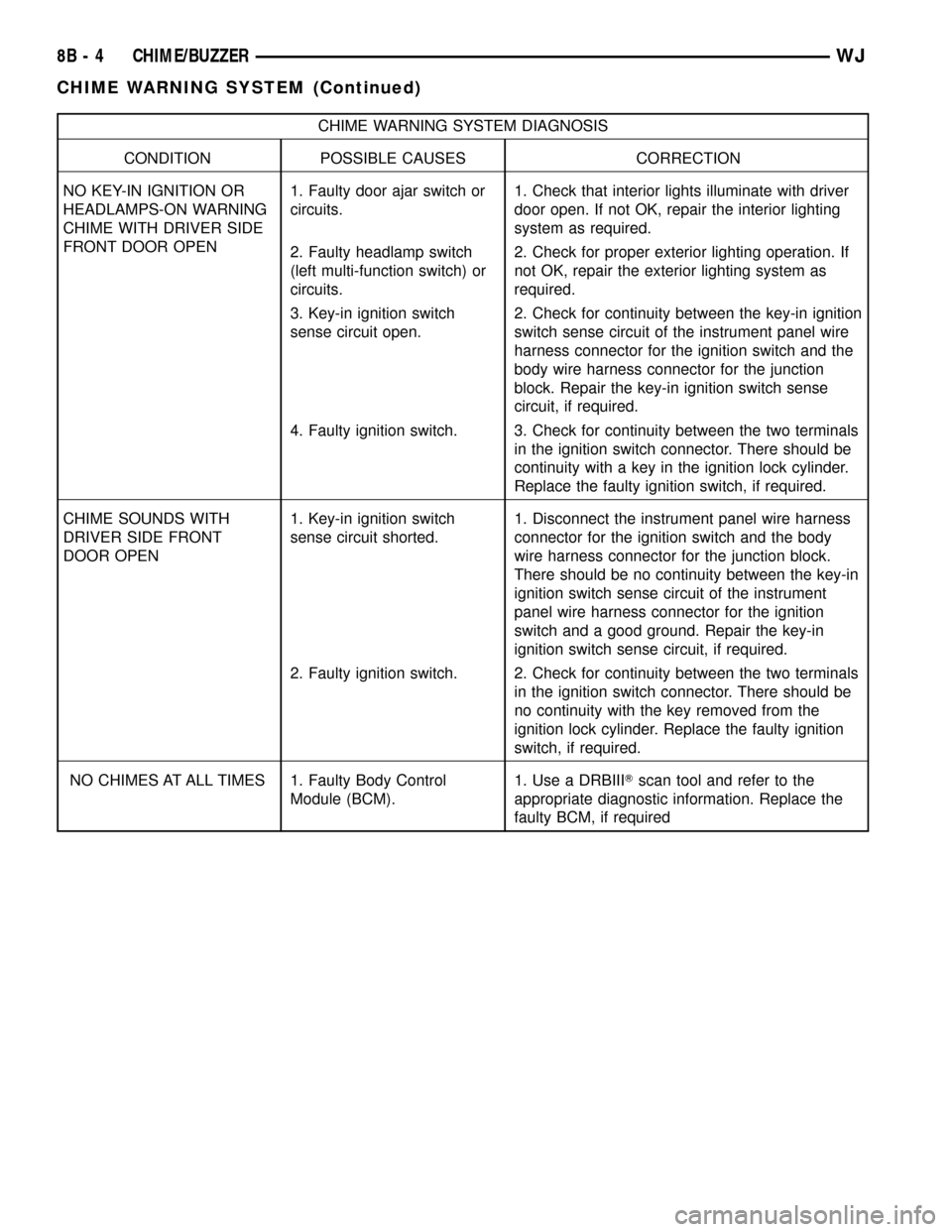
CHIME WARNING SYSTEM DIAGNOSIS
CONDITION POSSIBLE CAUSES CORRECTION
NO KEY-IN IGNITION OR
HEADLAMPS-ON WARNING
CHIME WITH DRIVER SIDE
FRONT DOOR OPEN1. Faulty door ajar switch or
circuits.1. Check that interior lights illuminate with driver
door open. If not OK, repair the interior lighting
system as required.
2. Faulty headlamp switch
(left multi-function switch) or
circuits.2. Check for proper exterior lighting operation. If
not OK, repair the exterior lighting system as
required.
3. Key-in ignition switch
sense circuit open.2. Check for continuity between the key-in ignition
switch sense circuit of the instrument panel wire
harness connector for the ignition switch and the
body wire harness connector for the junction
block. Repair the key-in ignition switch sense
circuit, if required.
4. Faulty ignition switch. 3. Check for continuity between the two terminals
in the ignition switch connector. There should be
continuity with a key in the ignition lock cylinder.
Replace the faulty ignition switch, if required.
CHIME SOUNDS WITH
DRIVER SIDE FRONT
DOOR OPEN1. Key-in ignition switch
sense circuit shorted.1. Disconnect the instrument panel wire harness
connector for the ignition switch and the body
wire harness connector for the junction block.
There should be no continuity between the key-in
ignition switch sense circuit of the instrument
panel wire harness connector for the ignition
switch and a good ground. Repair the key-in
ignition switch sense circuit, if required.
2. Faulty ignition switch. 2. Check for continuity between the two terminals
in the ignition switch connector. There should be
no continuity with the key removed from the
ignition lock cylinder. Replace the faulty ignition
switch, if required.
NO CHIMES AT ALL TIMES 1. Faulty Body Control
Module (BCM).1. Use a DRBIIITscan tool and refer to the
appropriate diagnostic information. Replace the
faulty BCM, if required
8B - 4 CHIME/BUZZERWJ
CHIME WARNING SYSTEM (Continued)
Page 310 of 2199
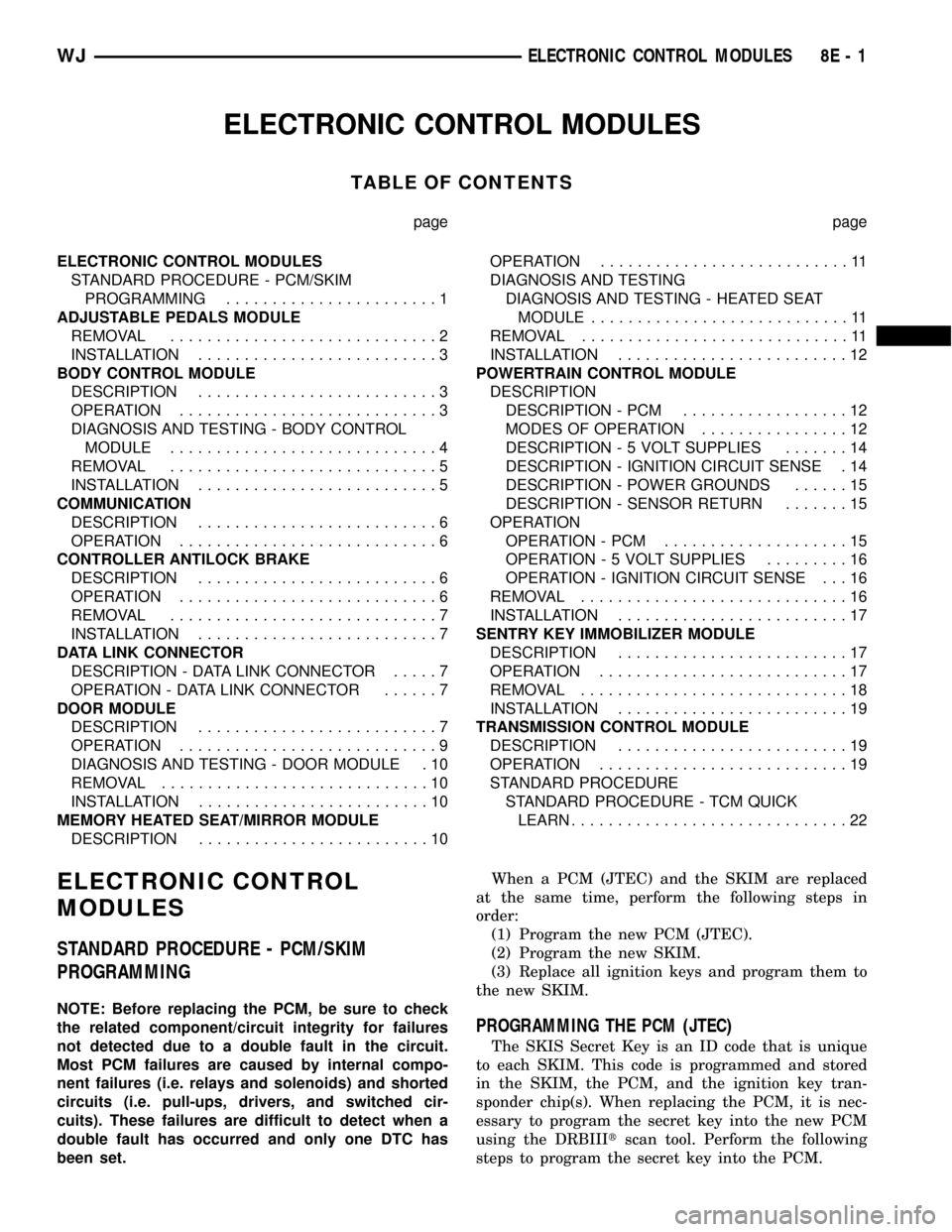
ELECTRONIC CONTROL MODULES
TABLE OF CONTENTS
page page
ELECTRONIC CONTROL MODULES
STANDARD PROCEDURE - PCM/SKIM
PROGRAMMING.......................1
ADJUSTABLE PEDALS MODULE
REMOVAL.............................2
INSTALLATION..........................3
BODY CONTROL MODULE
DESCRIPTION..........................3
OPERATION............................3
DIAGNOSIS AND TESTING - BODY CONTROL
MODULE.............................4
REMOVAL.............................5
INSTALLATION..........................5
COMMUNICATION
DESCRIPTION..........................6
OPERATION............................6
CONTROLLER ANTILOCK BRAKE
DESCRIPTION..........................6
OPERATION............................6
REMOVAL.............................7
INSTALLATION..........................7
DATA LINK CONNECTOR
DESCRIPTION - DATA LINK CONNECTOR.....7
OPERATION - DATA LINK CONNECTOR......7
DOOR MODULE
DESCRIPTION..........................7
OPERATION............................9
DIAGNOSIS AND TESTING - DOOR MODULE . 10
REMOVAL.............................10
INSTALLATION.........................10
MEMORY HEATED SEAT/MIRROR MODULE
DESCRIPTION.........................10OPERATION...........................11
DIAGNOSIS AND TESTING
DIAGNOSIS AND TESTING - HEATED SEAT
MODULE............................11
REMOVAL.............................11
INSTALLATION.........................12
POWERTRAIN CONTROL MODULE
DESCRIPTION
DESCRIPTION - PCM..................12
MODES OF OPERATION................12
DESCRIPTION - 5 VOLT SUPPLIES.......14
DESCRIPTION - IGNITION CIRCUIT SENSE . 14
DESCRIPTION - POWER GROUNDS......15
DESCRIPTION - SENSOR RETURN.......15
OPERATION
OPERATION - PCM....................15
OPERATION - 5 VOLT SUPPLIES.........16
OPERATION - IGNITION CIRCUIT SENSE . . . 16
REMOVAL.............................16
INSTALLATION.........................17
SENTRY KEY IMMOBILIZER MODULE
DESCRIPTION.........................17
OPERATION...........................17
REMOVAL.............................18
INSTALLATION.........................19
TRANSMISSION CONTROL MODULE
DESCRIPTION.........................19
OPERATION...........................19
STANDARD PROCEDURE
STANDARD PROCEDURE - TCM QUICK
LEARN..............................22
ELECTRONIC CONTROL
MODULES
STANDARD PROCEDURE - PCM/SKIM
PROGRAMMING
NOTE: Before replacing the PCM, be sure to check
the related component/circuit integrity for failures
not detected due to a double fault in the circuit.
Most PCM failures are caused by internal compo-
nent failures (i.e. relays and solenoids) and shorted
circuits (i.e. pull-ups, drivers, and switched cir-
cuits). These failures are difficult to detect when a
double fault has occurred and only one DTC has
been set.When a PCM (JTEC) and the SKIM are replaced
at the same time, perform the following steps in
order:
(1) Program the new PCM (JTEC).
(2) Program the new SKIM.
(3) Replace all ignition keys and program them to
the new SKIM.
PROGRAMMING THE PCM (JTEC)
The SKIS Secret Key is an ID code that is unique
to each SKIM. This code is programmed and stored
in the SKIM, the PCM, and the ignition key tran-
sponder chip(s). When replacing the PCM, it is nec-
essary to program the secret key into the new PCM
using the DRBIIItscan tool. Perform the following
steps to program the secret key into the PCM.
WJELECTRONIC CONTROL MODULES 8E - 1
Page 311 of 2199
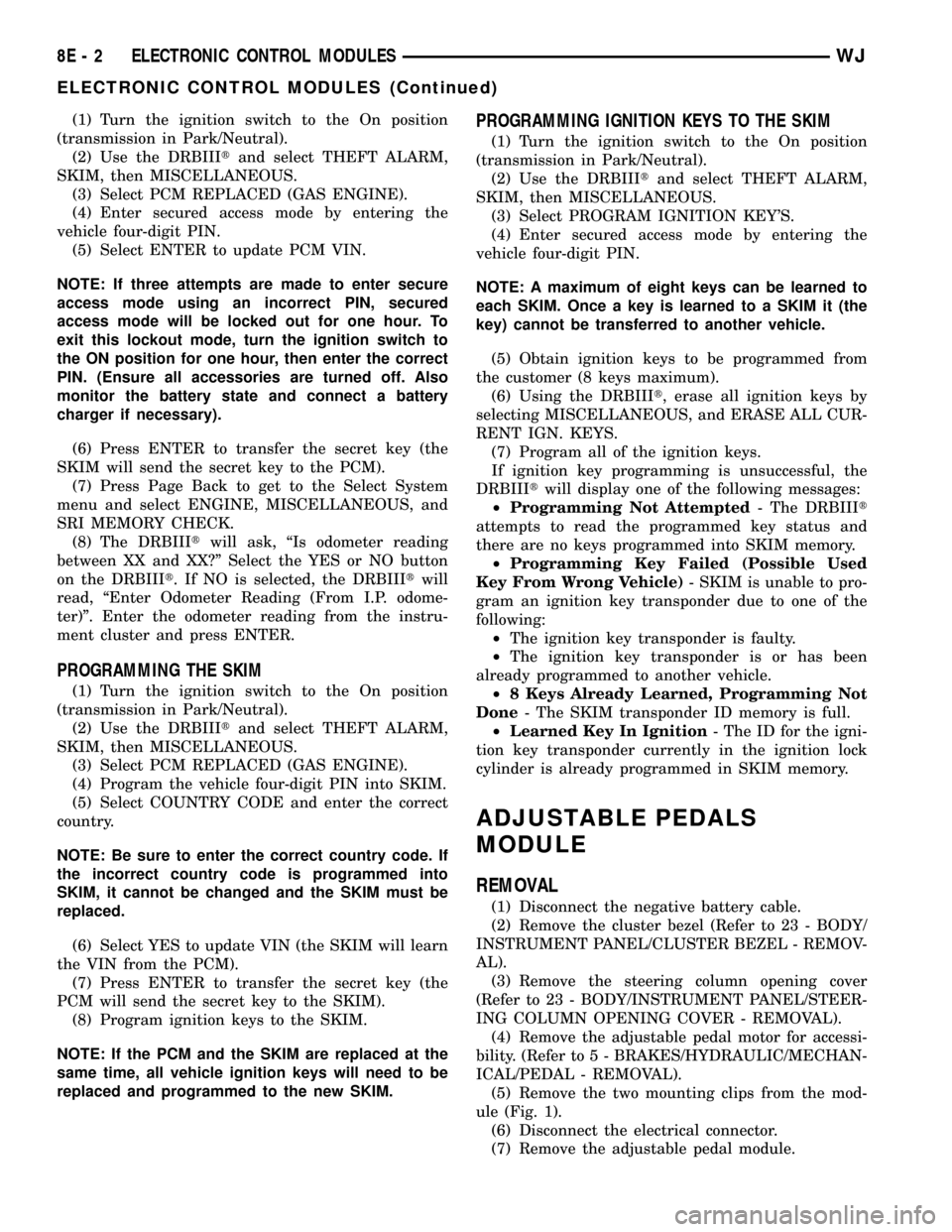
(1) Turn the ignition switch to the On position
(transmission in Park/Neutral).
(2) Use the DRBIIItand select THEFT ALARM,
SKIM, then MISCELLANEOUS.
(3) Select PCM REPLACED (GAS ENGINE).
(4) Enter secured access mode by entering the
vehicle four-digit PIN.
(5) Select ENTER to update PCM VIN.
NOTE: If three attempts are made to enter secure
access mode using an incorrect PIN, secured
access mode will be locked out for one hour. To
exit this lockout mode, turn the ignition switch to
the ON position for one hour, then enter the correct
PIN. (Ensure all accessories are turned off. Also
monitor the battery state and connect a battery
charger if necessary).
(6) Press ENTER to transfer the secret key (the
SKIM will send the secret key to the PCM).
(7) Press Page Back to get to the Select System
menu and select ENGINE, MISCELLANEOUS, and
SRI MEMORY CHECK.
(8) The DRBIIItwill ask, ªIs odometer reading
between XX and XX?º Select the YES or NO button
on the DRBIIIt. If NO is selected, the DRBIIItwill
read, ªEnter Odometer Reading (From I.P. odome-
ter)º. Enter the odometer reading from the instru-
ment cluster and press ENTER.
PROGRAMMING THE SKIM
(1) Turn the ignition switch to the On position
(transmission in Park/Neutral).
(2) Use the DRBIIItand select THEFT ALARM,
SKIM, then MISCELLANEOUS.
(3) Select PCM REPLACED (GAS ENGINE).
(4) Program the vehicle four-digit PIN into SKIM.
(5) Select COUNTRY CODE and enter the correct
country.
NOTE: Be sure to enter the correct country code. If
the incorrect country code is programmed into
SKIM, it cannot be changed and the SKIM must be
replaced.
(6) Select YES to update VIN (the SKIM will learn
the VIN from the PCM).
(7) Press ENTER to transfer the secret key (the
PCM will send the secret key to the SKIM).
(8) Program ignition keys to the SKIM.
NOTE: If the PCM and the SKIM are replaced at the
same time, all vehicle ignition keys will need to be
replaced and programmed to the new SKIM.
PROGRAMMING IGNITION KEYS TO THE SKIM
(1) Turn the ignition switch to the On position
(transmission in Park/Neutral).
(2) Use the DRBIIItand select THEFT ALARM,
SKIM, then MISCELLANEOUS.
(3) Select PROGRAM IGNITION KEY'S.
(4) Enter secured access mode by entering the
vehicle four-digit PIN.
NOTE: A maximum of eight keys can be learned to
each SKIM. Once a key is learned to a SKIM it (the
key) cannot be transferred to another vehicle.
(5) Obtain ignition keys to be programmed from
the customer (8 keys maximum).
(6) Using the DRBIIIt, erase all ignition keys by
selecting MISCELLANEOUS, and ERASE ALL CUR-
RENT IGN. KEYS.
(7) Program all of the ignition keys.
If ignition key programming is unsuccessful, the
DRBIIItwill display one of the following messages:
²Programming Not Attempted- The DRBIIIt
attempts to read the programmed key status and
there are no keys programmed into SKIM memory.
²Programming Key Failed (Possible Used
Key From Wrong Vehicle)- SKIM is unable to pro-
gram an ignition key transponder due to one of the
following:
²The ignition key transponder is faulty.
²The ignition key transponder is or has been
already programmed to another vehicle.
²8 Keys Already Learned, Programming Not
Done- The SKIM transponder ID memory is full.
²Learned Key In Ignition- The ID for the igni-
tion key transponder currently in the ignition lock
cylinder is already programmed in SKIM memory.
ADJUSTABLE PEDALS
MODULE
REMOVAL
(1) Disconnect the negative battery cable.
(2) Remove the cluster bezel (Refer to 23 - BODY/
INSTRUMENT PANEL/CLUSTER BEZEL - REMOV-
AL).
(3) Remove the steering column opening cover
(Refer to 23 - BODY/INSTRUMENT PANEL/STEER-
ING COLUMN OPENING COVER - REMOVAL).
(4) Remove the adjustable pedal motor for accessi-
bility. (Refer to 5 - BRAKES/HYDRAULIC/MECHAN-
ICAL/PEDAL - REMOVAL).
(5) Remove the two mounting clips from the mod-
ule (Fig. 1).
(6) Disconnect the electrical connector.
(7) Remove the adjustable pedal module.
8E - 2 ELECTRONIC CONTROL MODULESWJ
ELECTRONIC CONTROL MODULES (Continued)
Page 313 of 2199
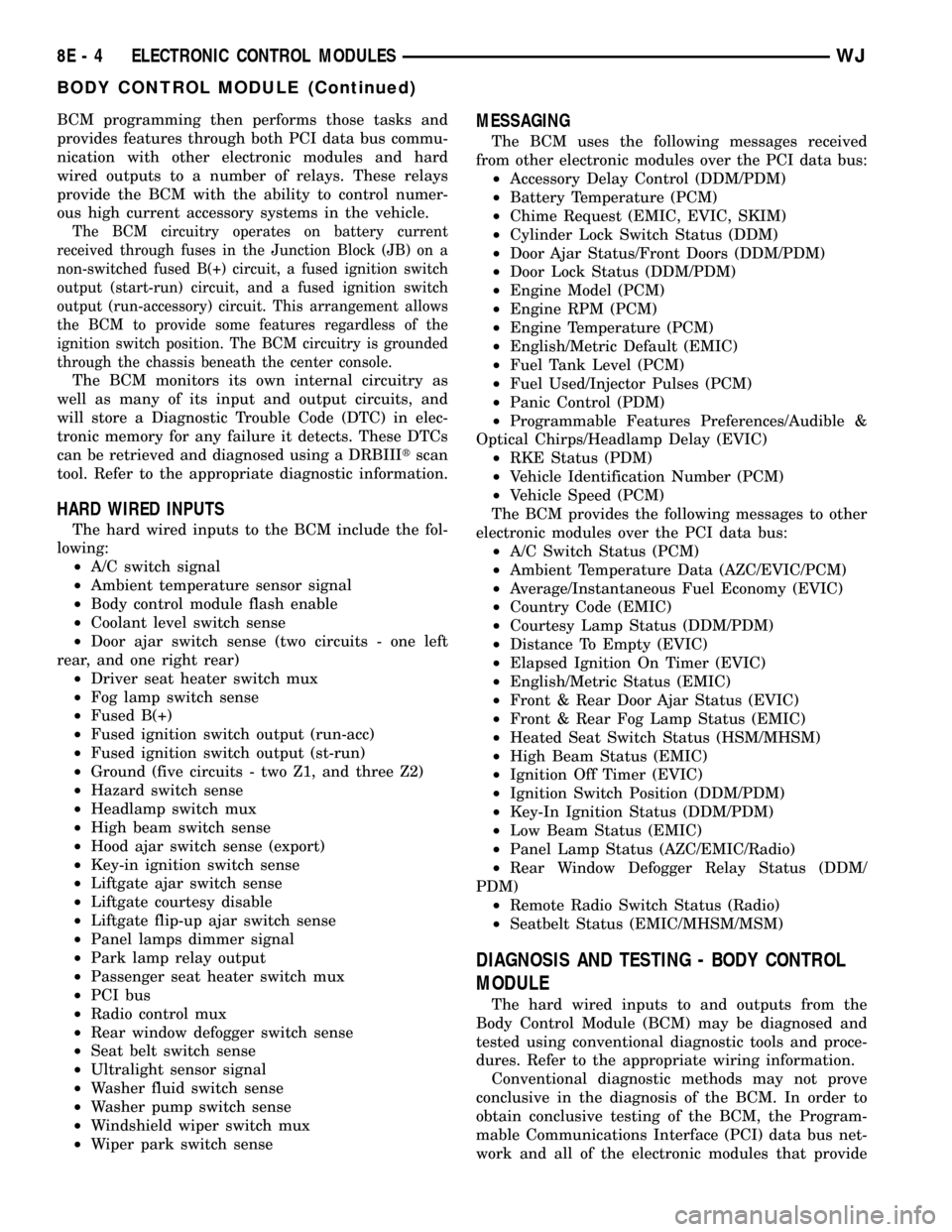
BCM programming then performs those tasks and
provides features through both PCI data bus commu-
nication with other electronic modules and hard
wired outputs to a number of relays. These relays
provide the BCM with the ability to control numer-
ous high current accessory systems in the vehicle.
The BCM circuitry operates on battery current
received through fuses in the Junction Block (JB) on a
non-switched fused B(+) circuit, a fused ignition switch
output (start-run) circuit, and a fused ignition switch
output (run-accessory) circuit. This arrangement allows
the BCM to provide some features regardless of the
ignition switch position. The BCM circuitry is grounded
through the chassis beneath the center console.
The BCM monitors its own internal circuitry as
well as many of its input and output circuits, and
will store a Diagnostic Trouble Code (DTC) in elec-
tronic memory for any failure it detects. These DTCs
can be retrieved and diagnosed using a DRBIIItscan
tool. Refer to the appropriate diagnostic information.
HARD WIRED INPUTS
The hard wired inputs to the BCM include the fol-
lowing:
²A/C switch signal
²Ambient temperature sensor signal
²Body control module flash enable
²Coolant level switch sense
²Door ajar switch sense (two circuits - one left
rear, and one right rear)
²Driver seat heater switch mux
²Fog lamp switch sense
²Fused B(+)
²Fused ignition switch output (run-acc)
²Fused ignition switch output (st-run)
²Ground (five circuits - two Z1, and three Z2)
²Hazard switch sense
²Headlamp switch mux
²High beam switch sense
²Hood ajar switch sense (export)
²Key-in ignition switch sense
²Liftgate ajar switch sense
²Liftgate courtesy disable
²Liftgate flip-up ajar switch sense
²Panel lamps dimmer signal
²Park lamp relay output
²Passenger seat heater switch mux
²PCI bus
²Radio control mux
²Rear window defogger switch sense
²Seat belt switch sense
²Ultralight sensor signal
²Washer fluid switch sense
²Washer pump switch sense
²Windshield wiper switch mux
²Wiper park switch sense
MESSAGING
The BCM uses the following messages received
from other electronic modules over the PCI data bus:
²Accessory Delay Control (DDM/PDM)
²Battery Temperature (PCM)
²Chime Request (EMIC, EVIC, SKIM)
²Cylinder Lock Switch Status (DDM)
²Door Ajar Status/Front Doors (DDM/PDM)
²Door Lock Status (DDM/PDM)
²Engine Model (PCM)
²Engine RPM (PCM)
²Engine Temperature (PCM)
²English/Metric Default (EMIC)
²Fuel Tank Level (PCM)
²Fuel Used/Injector Pulses (PCM)
²Panic Control (PDM)
²Programmable Features Preferences/Audible &
Optical Chirps/Headlamp Delay (EVIC)
²RKE Status (PDM)
²Vehicle Identification Number (PCM)
²Vehicle Speed (PCM)
The BCM provides the following messages to other
electronic modules over the PCI data bus:
²A/C Switch Status (PCM)
²Ambient Temperature Data (AZC/EVIC/PCM)
²Average/Instantaneous Fuel Economy (EVIC)
²Country Code (EMIC)
²Courtesy Lamp Status (DDM/PDM)
²Distance To Empty (EVIC)
²Elapsed Ignition On Timer (EVIC)
²English/Metric Status (EMIC)
²Front & Rear Door Ajar Status (EVIC)
²Front & Rear Fog Lamp Status (EMIC)
²Heated Seat Switch Status (HSM/MHSM)
²High Beam Status (EMIC)
²Ignition Off Timer (EVIC)
²Ignition Switch Position (DDM/PDM)
²Key-In Ignition Status (DDM/PDM)
²Low Beam Status (EMIC)
²Panel Lamp Status (AZC/EMIC/Radio)
²Rear Window Defogger Relay Status (DDM/
PDM)
²Remote Radio Switch Status (Radio)
²Seatbelt Status (EMIC/MHSM/MSM)
DIAGNOSIS AND TESTING - BODY CONTROL
MODULE
The hard wired inputs to and outputs from the
Body Control Module (BCM) may be diagnosed and
tested using conventional diagnostic tools and proce-
dures. Refer to the appropriate wiring information.
Conventional diagnostic methods may not prove
conclusive in the diagnosis of the BCM. In order to
obtain conclusive testing of the BCM, the Program-
mable Communications Interface (PCI) data bus net-
work and all of the electronic modules that provide
8E - 4 ELECTRONIC CONTROL MODULESWJ
BODY CONTROL MODULE (Continued)
Page 315 of 2199
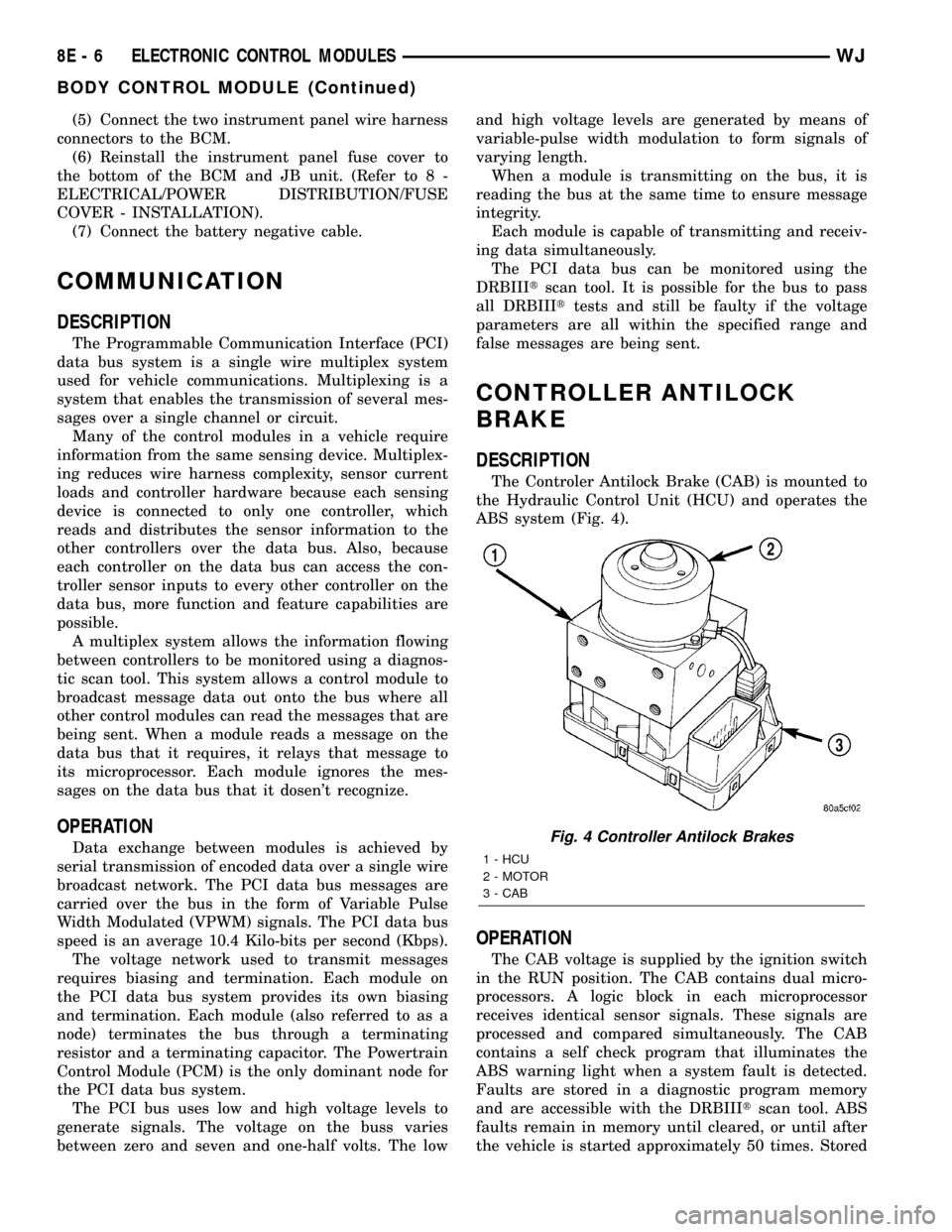
(5) Connect the two instrument panel wire harness
connectors to the BCM.
(6) Reinstall the instrument panel fuse cover to
the bottom of the BCM and JB unit. (Refer to 8 -
ELECTRICAL/POWER DISTRIBUTION/FUSE
COVER - INSTALLATION).
(7) Connect the battery negative cable.
COMMUNICATION
DESCRIPTION
The Programmable Communication Interface (PCI)
data bus system is a single wire multiplex system
used for vehicle communications. Multiplexing is a
system that enables the transmission of several mes-
sages over a single channel or circuit.
Many of the control modules in a vehicle require
information from the same sensing device. Multiplex-
ing reduces wire harness complexity, sensor current
loads and controller hardware because each sensing
device is connected to only one controller, which
reads and distributes the sensor information to the
other controllers over the data bus. Also, because
each controller on the data bus can access the con-
troller sensor inputs to every other controller on the
data bus, more function and feature capabilities are
possible.
A multiplex system allows the information flowing
between controllers to be monitored using a diagnos-
tic scan tool. This system allows a control module to
broadcast message data out onto the bus where all
other control modules can read the messages that are
being sent. When a module reads a message on the
data bus that it requires, it relays that message to
its microprocessor. Each module ignores the mes-
sages on the data bus that it dosen't recognize.
OPERATION
Data exchange between modules is achieved by
serial transmission of encoded data over a single wire
broadcast network. The PCI data bus messages are
carried over the bus in the form of Variable Pulse
Width Modulated (VPWM) signals. The PCI data bus
speed is an average 10.4 Kilo-bits per second (Kbps).
The voltage network used to transmit messages
requires biasing and termination. Each module on
the PCI data bus system provides its own biasing
and termination. Each module (also referred to as a
node) terminates the bus through a terminating
resistor and a terminating capacitor. The Powertrain
Control Module (PCM) is the only dominant node for
the PCI data bus system.
The PCI bus uses low and high voltage levels to
generate signals. The voltage on the buss varies
between zero and seven and one-half volts. The lowand high voltage levels are generated by means of
variable-pulse width modulation to form signals of
varying length.
When a module is transmitting on the bus, it is
reading the bus at the same time to ensure message
integrity.
Each module is capable of transmitting and receiv-
ing data simultaneously.
The PCI data bus can be monitored using the
DRBIIItscan tool. It is possible for the bus to pass
all DRBIIIttests and still be faulty if the voltage
parameters are all within the specified range and
false messages are being sent.
CONTROLLER ANTILOCK
BRAKE
DESCRIPTION
The Controler Antilock Brake (CAB) is mounted to
the Hydraulic Control Unit (HCU) and operates the
ABS system (Fig. 4).
OPERATION
The CAB voltage is supplied by the ignition switch
in the RUN position. The CAB contains dual micro-
processors. A logic block in each microprocessor
receives identical sensor signals. These signals are
processed and compared simultaneously. The CAB
contains a self check program that illuminates the
ABS warning light when a system fault is detected.
Faults are stored in a diagnostic program memory
and are accessible with the DRBIIItscan tool. ABS
faults remain in memory until cleared, or until after
the vehicle is started approximately 50 times. Stored
Fig. 4 Controller Antilock Brakes
1 - HCU
2 - MOTOR
3 - CAB
8E - 6 ELECTRONIC CONTROL MODULESWJ
BODY CONTROL MODULE (Continued)