O2 Sensors JEEP GRAND CHEROKEE 2002 WJ / 2.G User Guide
[x] Cancel search | Manufacturer: JEEP, Model Year: 2002, Model line: GRAND CHEROKEE, Model: JEEP GRAND CHEROKEE 2002 WJ / 2.GPages: 2199, PDF Size: 76.01 MB
Page 324 of 2199
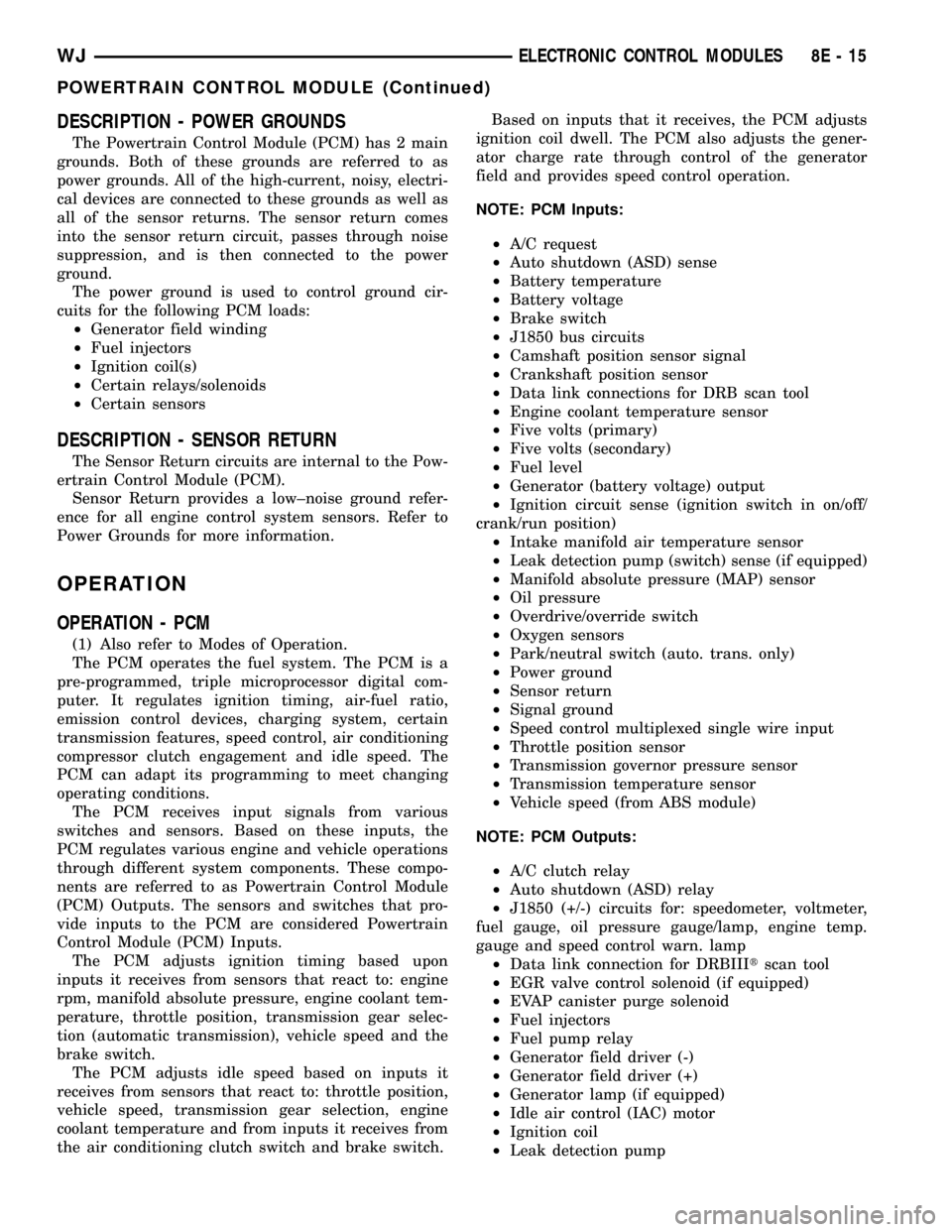
DESCRIPTION - POWER GROUNDS
The Powertrain Control Module (PCM) has 2 main
grounds. Both of these grounds are referred to as
power grounds. All of the high-current, noisy, electri-
cal devices are connected to these grounds as well as
all of the sensor returns. The sensor return comes
into the sensor return circuit, passes through noise
suppression, and is then connected to the power
ground.
The power ground is used to control ground cir-
cuits for the following PCM loads:
²Generator field winding
²Fuel injectors
²Ignition coil(s)
²Certain relays/solenoids
²Certain sensors
DESCRIPTION - SENSOR RETURN
The Sensor Return circuits are internal to the Pow-
ertrain Control Module (PCM).
Sensor Return provides a low±noise ground refer-
ence for all engine control system sensors. Refer to
Power Grounds for more information.
OPERATION
OPERATION - PCM
(1) Also refer to Modes of Operation.
The PCM operates the fuel system. The PCM is a
pre-programmed, triple microprocessor digital com-
puter. It regulates ignition timing, air-fuel ratio,
emission control devices, charging system, certain
transmission features, speed control, air conditioning
compressor clutch engagement and idle speed. The
PCM can adapt its programming to meet changing
operating conditions.
The PCM receives input signals from various
switches and sensors. Based on these inputs, the
PCM regulates various engine and vehicle operations
through different system components. These compo-
nents are referred to as Powertrain Control Module
(PCM) Outputs. The sensors and switches that pro-
vide inputs to the PCM are considered Powertrain
Control Module (PCM) Inputs.
The PCM adjusts ignition timing based upon
inputs it receives from sensors that react to: engine
rpm, manifold absolute pressure, engine coolant tem-
perature, throttle position, transmission gear selec-
tion (automatic transmission), vehicle speed and the
brake switch.
The PCM adjusts idle speed based on inputs it
receives from sensors that react to: throttle position,
vehicle speed, transmission gear selection, engine
coolant temperature and from inputs it receives from
the air conditioning clutch switch and brake switch.Based on inputs that it receives, the PCM adjusts
ignition coil dwell. The PCM also adjusts the gener-
ator charge rate through control of the generator
field and provides speed control operation.
NOTE: PCM Inputs:
²A/C request
²Auto shutdown (ASD) sense
²Battery temperature
²Battery voltage
²Brake switch
²J1850 bus circuits
²Camshaft position sensor signal
²Crankshaft position sensor
²Data link connections for DRB scan tool
²Engine coolant temperature sensor
²Five volts (primary)
²Five volts (secondary)
²Fuel level
²Generator (battery voltage) output
²Ignition circuit sense (ignition switch in on/off/
crank/run position)
²Intake manifold air temperature sensor
²Leak detection pump (switch) sense (if equipped)
²Manifold absolute pressure (MAP) sensor
²Oil pressure
²Overdrive/override switch
²Oxygen sensors
²Park/neutral switch (auto. trans. only)
²Power ground
²Sensor return
²Signal ground
²Speed control multiplexed single wire input
²Throttle position sensor
²Transmission governor pressure sensor
²Transmission temperature sensor
²Vehicle speed (from ABS module)
NOTE: PCM Outputs:
²A/C clutch relay
²Auto shutdown (ASD) relay
²J1850 (+/-) circuits for: speedometer, voltmeter,
fuel gauge, oil pressure gauge/lamp, engine temp.
gauge and speed control warn. lamp
²Data link connection for DRBIIItscan tool
²EGR valve control solenoid (if equipped)
²EVAP canister purge solenoid
²Fuel injectors
²Fuel pump relay
²Generator field driver (-)
²Generator field driver (+)
²Generator lamp (if equipped)
²Idle air control (IAC) motor
²Ignition coil
²Leak detection pump
WJELECTRONIC CONTROL MODULES 8E - 15
POWERTRAIN CONTROL MODULE (Continued)
Page 329 of 2199
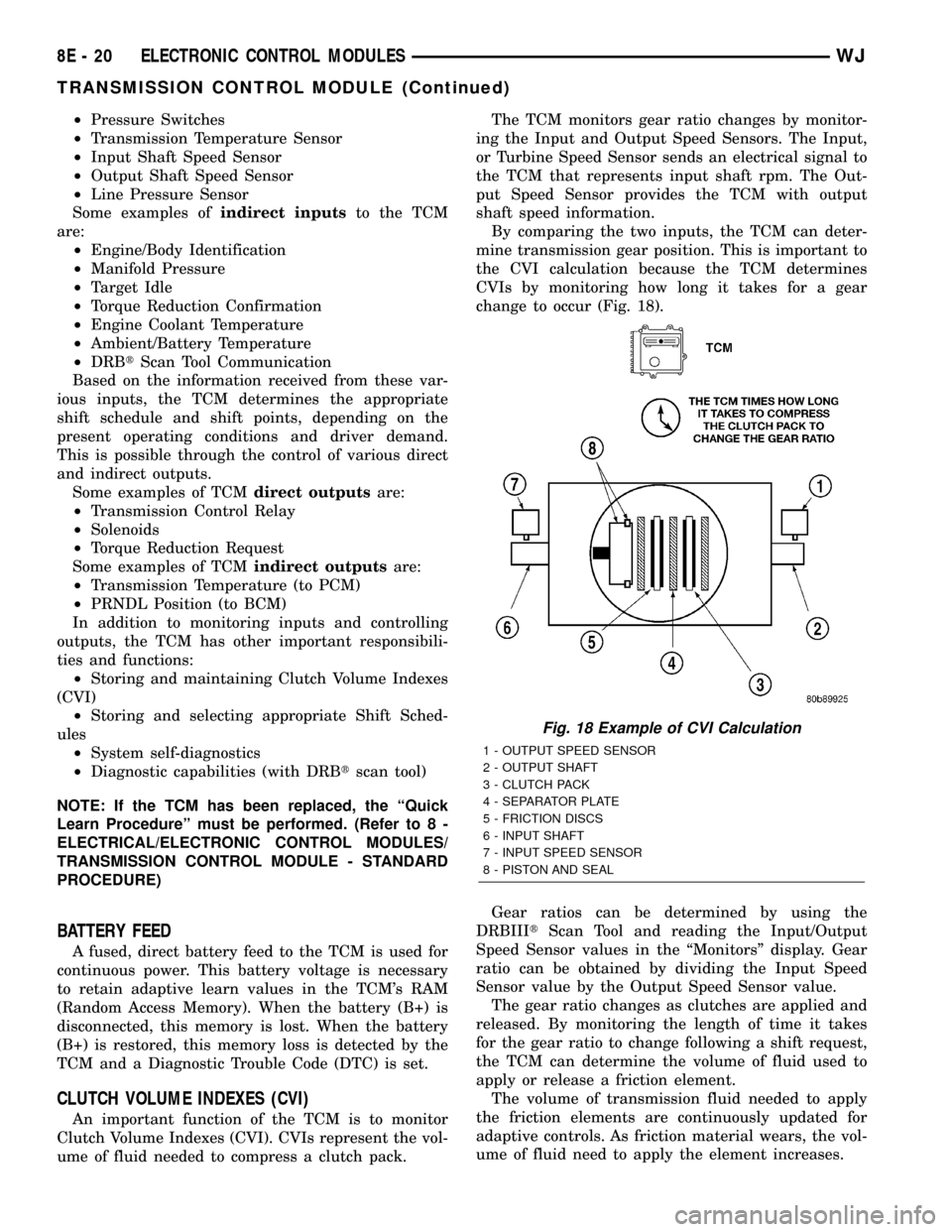
²Pressure Switches
²Transmission Temperature Sensor
²Input Shaft Speed Sensor
²Output Shaft Speed Sensor
²Line Pressure Sensor
Some examples ofindirect inputsto the TCM
are:
²Engine/Body Identification
²Manifold Pressure
²Target Idle
²Torque Reduction Confirmation
²Engine Coolant Temperature
²Ambient/Battery Temperature
²DRBtScan Tool Communication
Based on the information received from these var-
ious inputs, the TCM determines the appropriate
shift schedule and shift points, depending on the
present operating conditions and driver demand.
This is possible through the control of various direct
and indirect outputs.
Some examples of TCMdirect outputsare:
²Transmission Control Relay
²Solenoids
²Torque Reduction Request
Some examples of TCMindirect outputsare:
²Transmission Temperature (to PCM)
²PRNDL Position (to BCM)
In addition to monitoring inputs and controlling
outputs, the TCM has other important responsibili-
ties and functions:
²Storing and maintaining Clutch Volume Indexes
(CVI)
²Storing and selecting appropriate Shift Sched-
ules
²System self-diagnostics
²Diagnostic capabilities (with DRBtscan tool)
NOTE: If the TCM has been replaced, the ªQuick
Learn Procedureº must be performed. (Refer to 8 -
ELECTRICAL/ELECTRONIC CONTROL MODULES/
TRANSMISSION CONTROL MODULE - STANDARD
PROCEDURE)
BATTERY FEED
A fused, direct battery feed to the TCM is used for
continuous power. This battery voltage is necessary
to retain adaptive learn values in the TCM's RAM
(Random Access Memory). When the battery (B+) is
disconnected, this memory is lost. When the battery
(B+) is restored, this memory loss is detected by the
TCM and a Diagnostic Trouble Code (DTC) is set.
CLUTCH VOLUME INDEXES (CVI)
An important function of the TCM is to monitor
Clutch Volume Indexes (CVI). CVIs represent the vol-
ume of fluid needed to compress a clutch pack.The TCM monitors gear ratio changes by monitor-
ing the Input and Output Speed Sensors. The Input,
or Turbine Speed Sensor sends an electrical signal to
the TCM that represents input shaft rpm. The Out-
put Speed Sensor provides the TCM with output
shaft speed information.
By comparing the two inputs, the TCM can deter-
mine transmission gear position. This is important to
the CVI calculation because the TCM determines
CVIs by monitoring how long it takes for a gear
change to occur (Fig. 18).
Gear ratios can be determined by using the
DRBIIItScan Tool and reading the Input/Output
Speed Sensor values in the ªMonitorsº display. Gear
ratio can be obtained by dividing the Input Speed
Sensor value by the Output Speed Sensor value.
The gear ratio changes as clutches are applied and
released. By monitoring the length of time it takes
for the gear ratio to change following a shift request,
the TCM can determine the volume of fluid used to
apply or release a friction element.
The volume of transmission fluid needed to apply
the friction elements are continuously updated for
adaptive controls. As friction material wears, the vol-
ume of fluid need to apply the element increases.
Fig. 18 Example of CVI Calculation
1 - OUTPUT SPEED SENSOR
2 - OUTPUT SHAFT
3 - CLUTCH PACK
4 - SEPARATOR PLATE
5 - FRICTION DISCS
6 - INPUT SHAFT
7 - INPUT SPEED SENSOR
8 - PISTON AND SEAL
8E - 20 ELECTRONIC CONTROL MODULESWJ
TRANSMISSION CONTROL MODULE (Continued)
Page 330 of 2199
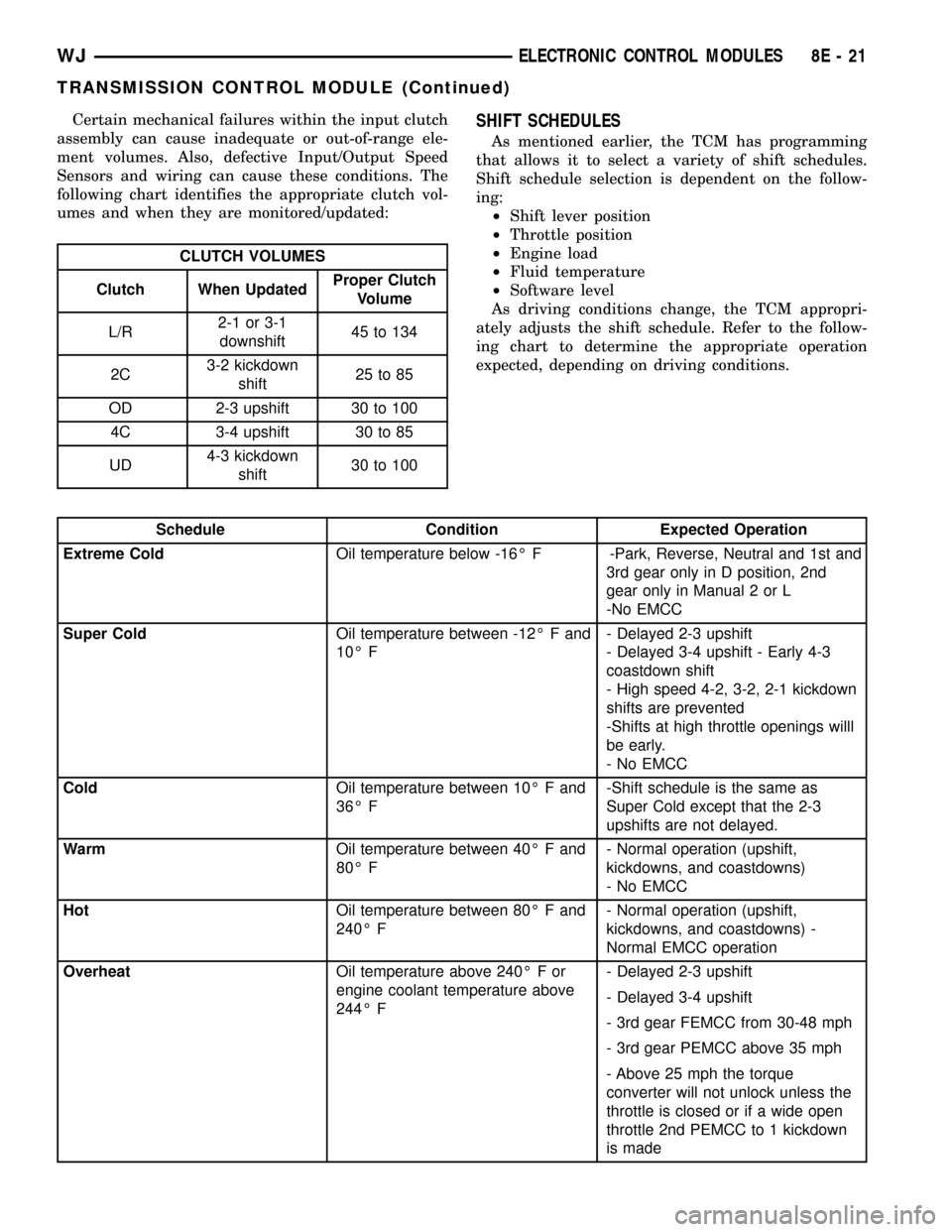
Certain mechanical failures within the input clutch
assembly can cause inadequate or out-of-range ele-
ment volumes. Also, defective Input/Output Speed
Sensors and wiring can cause these conditions. The
following chart identifies the appropriate clutch vol-
umes and when they are monitored/updated:
CLUTCH VOLUMES
Clutch When UpdatedProper Clutch
Volume
L/R2-1 or 3-1
downshift45 to 134
2C3-2 kickdown
shift25 to 85
OD 2-3 upshift 30 to 100
4C 3-4 upshift 30 to 85
UD4-3 kickdown
shift30 to 100
SHIFT SCHEDULES
As mentioned earlier, the TCM has programming
that allows it to select a variety of shift schedules.
Shift schedule selection is dependent on the follow-
ing:
²Shift lever position
²Throttle position
²Engine load
²Fluid temperature
²Software level
As driving conditions change, the TCM appropri-
ately adjusts the shift schedule. Refer to the follow-
ing chart to determine the appropriate operation
expected, depending on driving conditions.
Schedule Condition Expected Operation
Extreme ColdOil temperature below -16É F -Park, Reverse, Neutral and 1st and
3rd gear only in D position, 2nd
gear only in Manual 2 or L
-No EMCC
Super ColdOil temperature between -12É F and
10É F- Delayed 2-3 upshift
- Delayed 3-4 upshift - Early 4-3
coastdown shift
- High speed 4-2, 3-2, 2-1 kickdown
shifts are prevented
-Shifts at high throttle openings willl
be early.
- No EMCC
ColdOil temperature between 10É F and
36É F-Shift schedule is the same as
Super Cold except that the 2-3
upshifts are not delayed.
WarmOil temperature between 40É F and
80É F- Normal operation (upshift,
kickdowns, and coastdowns)
- No EMCC
HotOil temperature between 80É F and
240É F- Normal operation (upshift,
kickdowns, and coastdowns) -
Normal EMCC operation
OverheatOil temperature above 240É F or
engine coolant temperature above
244É F- Delayed 2-3 upshift
- Delayed 3-4 upshift
- 3rd gear FEMCC from 30-48 mph
- 3rd gear PEMCC above 35 mph
- Above 25 mph the torque
converter will not unlock unless the
throttle is closed or if a wide open
throttle 2nd PEMCC to 1 kickdown
is made
WJELECTRONIC CONTROL MODULES 8E - 21
TRANSMISSION CONTROL MODULE (Continued)
Page 380 of 2199
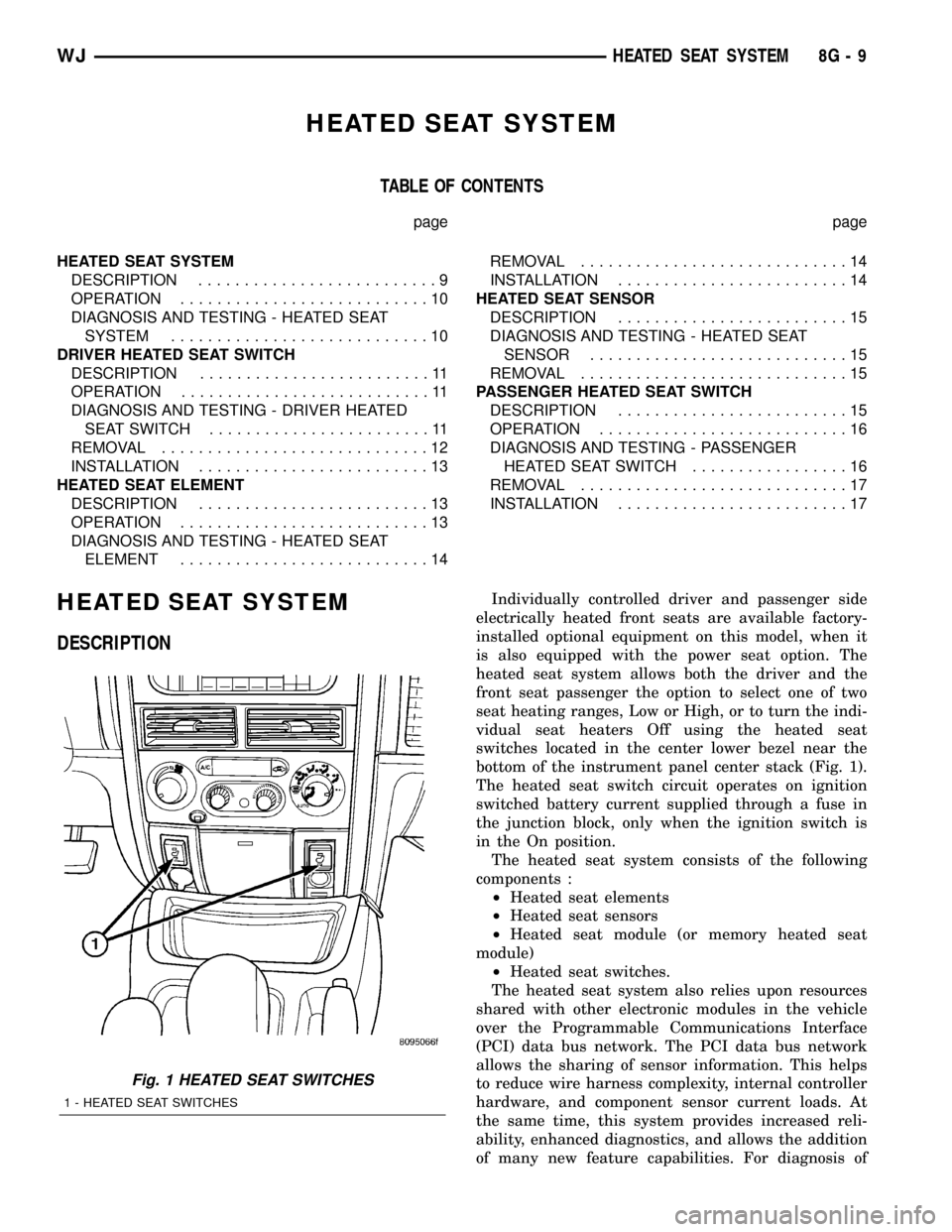
HEATED SEAT SYSTEM
TABLE OF CONTENTS
page page
HEATED SEAT SYSTEM
DESCRIPTION..........................9
OPERATION...........................10
DIAGNOSIS AND TESTING - HEATED SEAT
SYSTEM............................10
DRIVER HEATED SEAT SWITCH
DESCRIPTION.........................11
OPERATION...........................11
DIAGNOSIS AND TESTING - DRIVER HEATED
SEAT SWITCH........................11
REMOVAL.............................12
INSTALLATION.........................13
HEATED SEAT ELEMENT
DESCRIPTION.........................13
OPERATION...........................13
DIAGNOSIS AND TESTING - HEATED SEAT
ELEMENT...........................14REMOVAL.............................14
INSTALLATION.........................14
HEATED SEAT SENSOR
DESCRIPTION.........................15
DIAGNOSIS AND TESTING - HEATED SEAT
SENSOR............................15
REMOVAL.............................15
PASSENGER HEATED SEAT SWITCH
DESCRIPTION.........................15
OPERATION...........................16
DIAGNOSIS AND TESTING - PASSENGER
HEATED SEAT SWITCH.................16
REMOVAL.............................17
INSTALLATION.........................17
HEATED SEAT SYSTEM
DESCRIPTION
Individually controlled driver and passenger side
electrically heated front seats are available factory-
installed optional equipment on this model, when it
is also equipped with the power seat option. The
heated seat system allows both the driver and the
front seat passenger the option to select one of two
seat heating ranges, Low or High, or to turn the indi-
vidual seat heaters Off using the heated seat
switches located in the center lower bezel near the
bottom of the instrument panel center stack (Fig. 1).
The heated seat switch circuit operates on ignition
switched battery current supplied through a fuse in
the junction block, only when the ignition switch is
in the On position.
The heated seat system consists of the following
components :
²Heated seat elements
²Heated seat sensors
²Heated seat module (or memory heated seat
module)
²Heated seat switches.
The heated seat system also relies upon resources
shared with other electronic modules in the vehicle
over the Programmable Communications Interface
(PCI) data bus network. The PCI data bus network
allows the sharing of sensor information. This helps
to reduce wire harness complexity, internal controller
hardware, and component sensor current loads. At
the same time, this system provides increased reli-
ability, enhanced diagnostics, and allows the addition
of many new feature capabilities. For diagnosis of
Fig. 1 HEATED SEAT SWITCHES
1 - HEATED SEAT SWITCHES
WJHEATED SEAT SYSTEM 8G - 9
Page 381 of 2199
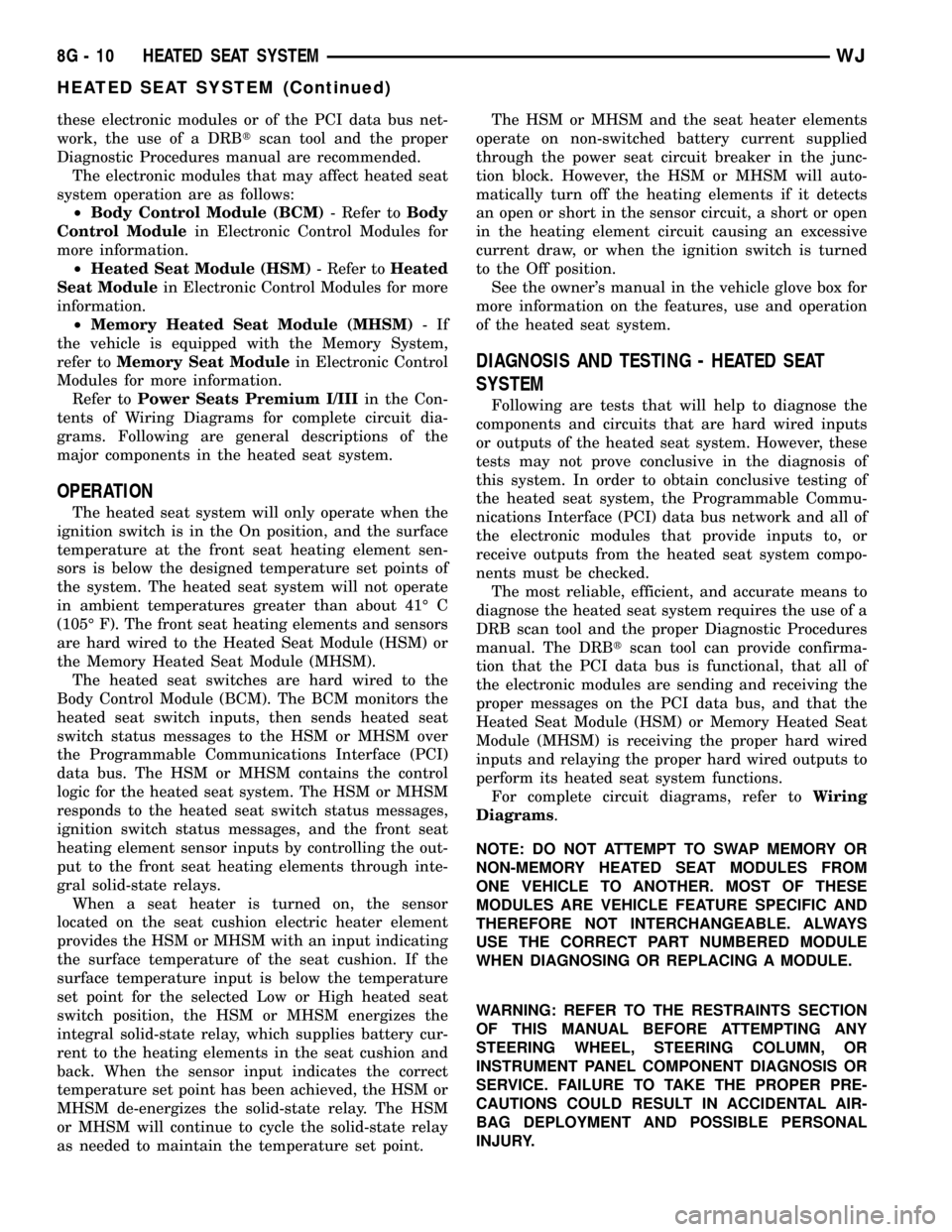
these electronic modules or of the PCI data bus net-
work, the use of a DRBtscan tool and the proper
Diagnostic Procedures manual are recommended.
The electronic modules that may affect heated seat
system operation are as follows:
²Body Control Module (BCM)- Refer toBody
Control Modulein Electronic Control Modules for
more information.
²Heated Seat Module (HSM)- Refer toHeated
Seat Modulein Electronic Control Modules for more
information.
²Memory Heated Seat Module (MHSM)-If
the vehicle is equipped with the Memory System,
refer toMemory Seat Modulein Electronic Control
Modules for more information.
Refer toPower Seats Premium I/IIIin the Con-
tents of Wiring Diagrams for complete circuit dia-
grams. Following are general descriptions of the
major components in the heated seat system.
OPERATION
The heated seat system will only operate when the
ignition switch is in the On position, and the surface
temperature at the front seat heating element sen-
sors is below the designed temperature set points of
the system. The heated seat system will not operate
in ambient temperatures greater than about 41É C
(105É F). The front seat heating elements and sensors
are hard wired to the Heated Seat Module (HSM) or
the Memory Heated Seat Module (MHSM).
The heated seat switches are hard wired to the
Body Control Module (BCM). The BCM monitors the
heated seat switch inputs, then sends heated seat
switch status messages to the HSM or MHSM over
the Programmable Communications Interface (PCI)
data bus. The HSM or MHSM contains the control
logic for the heated seat system. The HSM or MHSM
responds to the heated seat switch status messages,
ignition switch status messages, and the front seat
heating element sensor inputs by controlling the out-
put to the front seat heating elements through inte-
gral solid-state relays.
When a seat heater is turned on, the sensor
located on the seat cushion electric heater element
provides the HSM or MHSM with an input indicating
the surface temperature of the seat cushion. If the
surface temperature input is below the temperature
set point for the selected Low or High heated seat
switch position, the HSM or MHSM energizes the
integral solid-state relay, which supplies battery cur-
rent to the heating elements in the seat cushion and
back. When the sensor input indicates the correct
temperature set point has been achieved, the HSM or
MHSM de-energizes the solid-state relay. The HSM
or MHSM will continue to cycle the solid-state relay
as needed to maintain the temperature set point.The HSM or MHSM and the seat heater elements
operate on non-switched battery current supplied
through the power seat circuit breaker in the junc-
tion block. However, the HSM or MHSM will auto-
matically turn off the heating elements if it detects
an open or short in the sensor circuit, a short or open
in the heating element circuit causing an excessive
current draw, or when the ignition switch is turned
to the Off position.
See the owner's manual in the vehicle glove box for
more information on the features, use and operation
of the heated seat system.
DIAGNOSIS AND TESTING - HEATED SEAT
SYSTEM
Following are tests that will help to diagnose the
components and circuits that are hard wired inputs
or outputs of the heated seat system. However, these
tests may not prove conclusive in the diagnosis of
this system. In order to obtain conclusive testing of
the heated seat system, the Programmable Commu-
nications Interface (PCI) data bus network and all of
the electronic modules that provide inputs to, or
receive outputs from the heated seat system compo-
nents must be checked.
The most reliable, efficient, and accurate means to
diagnose the heated seat system requires the use of a
DRB scan tool and the proper Diagnostic Procedures
manual. The DRBtscan tool can provide confirma-
tion that the PCI data bus is functional, that all of
the electronic modules are sending and receiving the
proper messages on the PCI data bus, and that the
Heated Seat Module (HSM) or Memory Heated Seat
Module (MHSM) is receiving the proper hard wired
inputs and relaying the proper hard wired outputs to
perform its heated seat system functions.
For complete circuit diagrams, refer toWiring
Diagrams.
NOTE: DO NOT ATTEMPT TO SWAP MEMORY OR
NON-MEMORY HEATED SEAT MODULES FROM
ONE VEHICLE TO ANOTHER. MOST OF THESE
MODULES ARE VEHICLE FEATURE SPECIFIC AND
THEREFORE NOT INTERCHANGEABLE. ALWAYS
USE THE CORRECT PART NUMBERED MODULE
WHEN DIAGNOSING OR REPLACING A MODULE.
WARNING: REFER TO THE RESTRAINTS SECTION
OF THIS MANUAL BEFORE ATTEMPTING ANY
STEERING WHEEL, STEERING COLUMN, OR
INSTRUMENT PANEL COMPONENT DIAGNOSIS OR
SERVICE. FAILURE TO TAKE THE PROPER PRE-
CAUTIONS COULD RESULT IN ACCIDENTAL AIR-
BAG DEPLOYMENT AND POSSIBLE PERSONAL
INJURY.
8G - 10 HEATED SEAT SYSTEMWJ
HEATED SEAT SYSTEM (Continued)
Page 410 of 2199
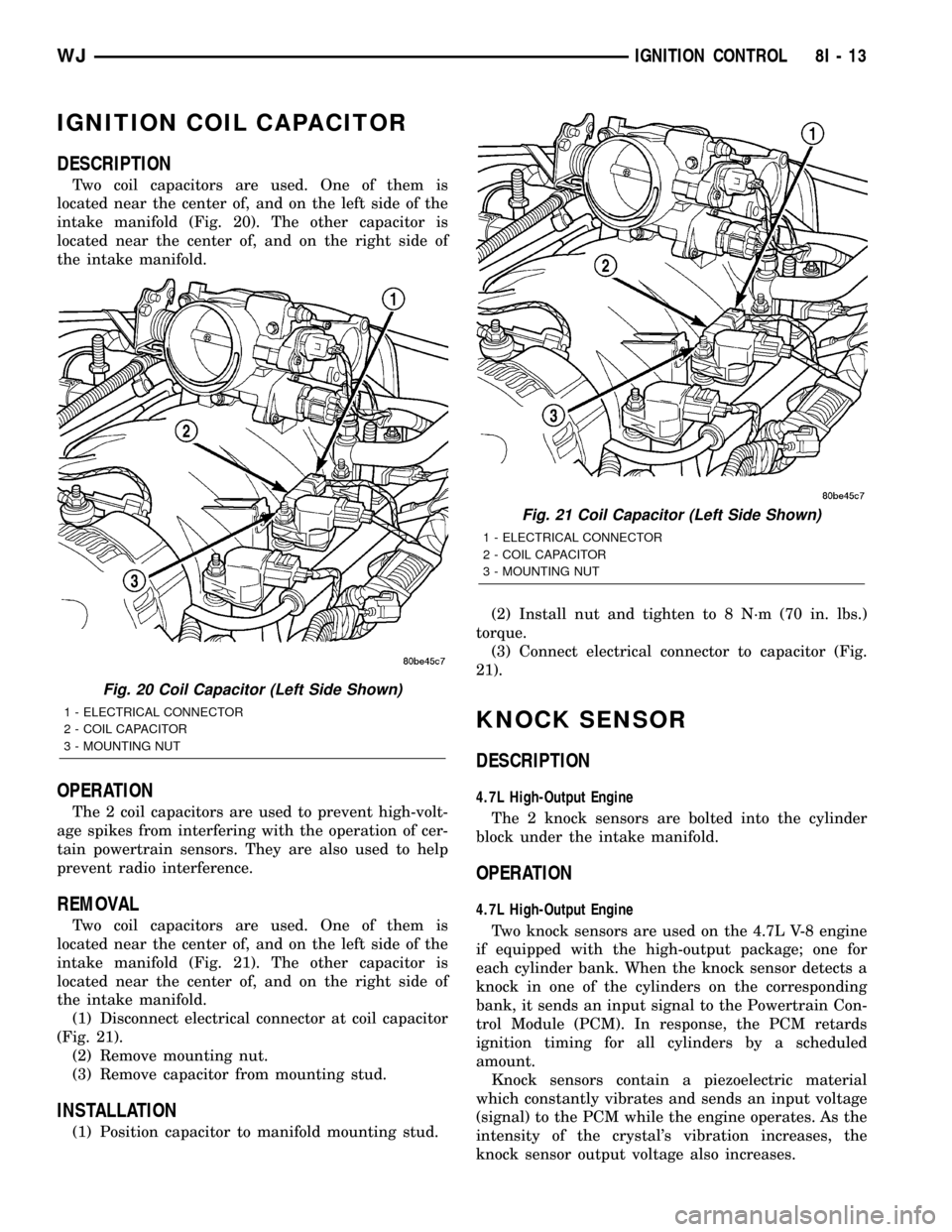
IGNITION COIL CAPACITOR
DESCRIPTION
Two coil capacitors are used. One of them is
located near the center of, and on the left side of the
intake manifold (Fig. 20). The other capacitor is
located near the center of, and on the right side of
the intake manifold.
OPERATION
The 2 coil capacitors are used to prevent high-volt-
age spikes from interfering with the operation of cer-
tain powertrain sensors. They are also used to help
prevent radio interference.
REMOVAL
Two coil capacitors are used. One of them is
located near the center of, and on the left side of the
intake manifold (Fig. 21). The other capacitor is
located near the center of, and on the right side of
the intake manifold.
(1) Disconnect electrical connector at coil capacitor
(Fig. 21).
(2) Remove mounting nut.
(3) Remove capacitor from mounting stud.
INSTALLATION
(1) Position capacitor to manifold mounting stud.(2) Install nut and tighten to 8 N´m (70 in. lbs.)
torque.
(3) Connect electrical connector to capacitor (Fig.
21).
KNOCK SENSOR
DESCRIPTION
4.7L High-Output Engine
The 2 knock sensors are bolted into the cylinder
block under the intake manifold.
OPERATION
4.7L High-Output Engine
Two knock sensors are used on the 4.7L V-8 engine
if equipped with the high-output package; one for
each cylinder bank. When the knock sensor detects a
knock in one of the cylinders on the corresponding
bank, it sends an input signal to the Powertrain Con-
trol Module (PCM). In response, the PCM retards
ignition timing for all cylinders by a scheduled
amount.
Knock sensors contain a piezoelectric material
which constantly vibrates and sends an input voltage
(signal) to the PCM while the engine operates. As the
intensity of the crystal's vibration increases, the
knock sensor output voltage also increases.
Fig. 20 Coil Capacitor (Left Side Shown)
1 - ELECTRICAL CONNECTOR
2 - COIL CAPACITOR
3 - MOUNTING NUT
Fig. 21 Coil Capacitor (Left Side Shown)
1 - ELECTRICAL CONNECTOR
2 - COIL CAPACITOR
3 - MOUNTING NUT
WJIGNITION CONTROL 8I - 13
Page 411 of 2199
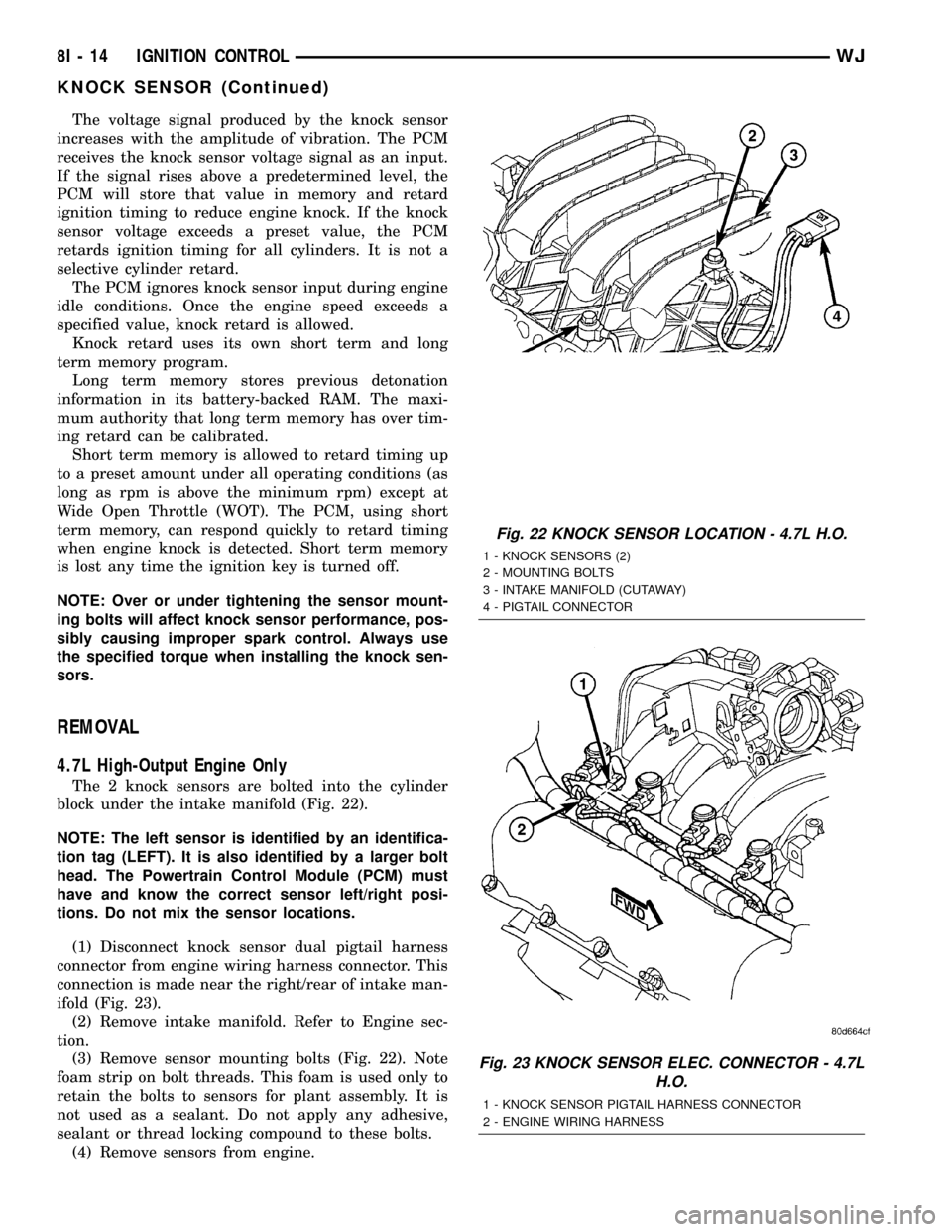
The voltage signal produced by the knock sensor
increases with the amplitude of vibration. The PCM
receives the knock sensor voltage signal as an input.
If the signal rises above a predetermined level, the
PCM will store that value in memory and retard
ignition timing to reduce engine knock. If the knock
sensor voltage exceeds a preset value, the PCM
retards ignition timing for all cylinders. It is not a
selective cylinder retard.
The PCM ignores knock sensor input during engine
idle conditions. Once the engine speed exceeds a
specified value, knock retard is allowed.
Knock retard uses its own short term and long
term memory program.
Long term memory stores previous detonation
information in its battery-backed RAM. The maxi-
mum authority that long term memory has over tim-
ing retard can be calibrated.
Short term memory is allowed to retard timing up
to a preset amount under all operating conditions (as
long as rpm is above the minimum rpm) except at
Wide Open Throttle (WOT). The PCM, using short
term memory, can respond quickly to retard timing
when engine knock is detected. Short term memory
is lost any time the ignition key is turned off.
NOTE: Over or under tightening the sensor mount-
ing bolts will affect knock sensor performance, pos-
sibly causing improper spark control. Always use
the specified torque when installing the knock sen-
sors.
REMOVAL
4.7L High-Output Engine Only
The 2 knock sensors are bolted into the cylinder
block under the intake manifold (Fig. 22).
NOTE: The left sensor is identified by an identifica-
tion tag (LEFT). It is also identified by a larger bolt
head. The Powertrain Control Module (PCM) must
have and know the correct sensor left/right posi-
tions. Do not mix the sensor locations.
(1) Disconnect knock sensor dual pigtail harness
connector from engine wiring harness connector. This
connection is made near the right/rear of intake man-
ifold (Fig. 23).
(2) Remove intake manifold. Refer to Engine sec-
tion.
(3) Remove sensor mounting bolts (Fig. 22). Note
foam strip on bolt threads. This foam is used only to
retain the bolts to sensors for plant assembly. It is
not used as a sealant. Do not apply any adhesive,
sealant or thread locking compound to these bolts.
(4) Remove sensors from engine.
Fig. 22 KNOCK SENSOR LOCATION - 4.7L H.O.
1 - KNOCK SENSORS (2)
2 - MOUNTING BOLTS
3 - INTAKE MANIFOLD (CUTAWAY)
4 - PIGTAIL CONNECTOR
Fig. 23 KNOCK SENSOR ELEC. CONNECTOR - 4.7L
H.O.
1 - KNOCK SENSOR PIGTAIL HARNESS CONNECTOR
2 - ENGINE WIRING HARNESS
8I - 14 IGNITION CONTROLWJ
KNOCK SENSOR (Continued)
Page 412 of 2199
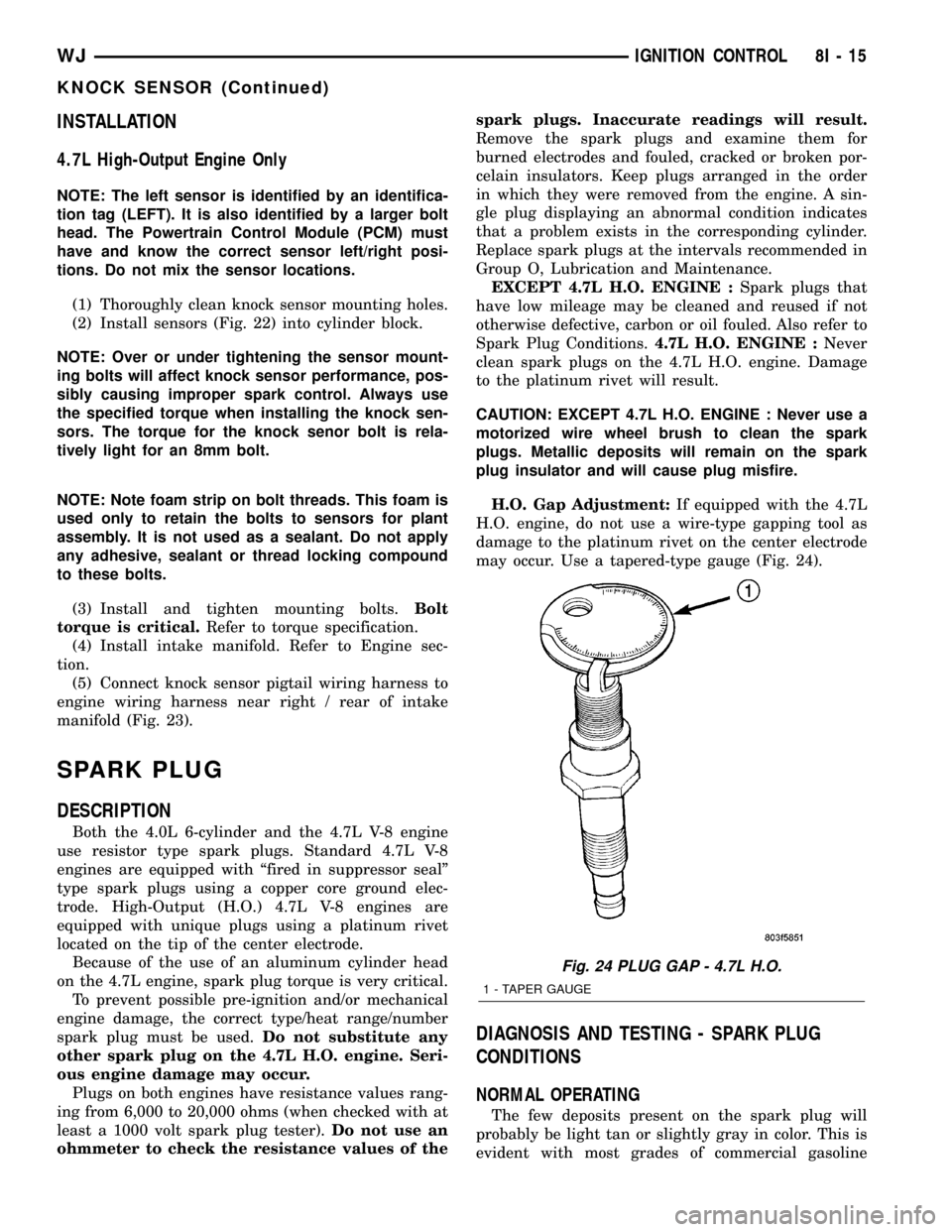
INSTALLATION
4.7L High-Output Engine Only
NOTE: The left sensor is identified by an identifica-
tion tag (LEFT). It is also identified by a larger bolt
head. The Powertrain Control Module (PCM) must
have and know the correct sensor left/right posi-
tions. Do not mix the sensor locations.
(1) Thoroughly clean knock sensor mounting holes.
(2) Install sensors (Fig. 22) into cylinder block.
NOTE: Over or under tightening the sensor mount-
ing bolts will affect knock sensor performance, pos-
sibly causing improper spark control. Always use
the specified torque when installing the knock sen-
sors. The torque for the knock senor bolt is rela-
tively light for an 8mm bolt.
NOTE: Note foam strip on bolt threads. This foam is
used only to retain the bolts to sensors for plant
assembly. It is not used as a sealant. Do not apply
any adhesive, sealant or thread locking compound
to these bolts.
(3) Install and tighten mounting bolts.Bolt
torque is critical.Refer to torque specification.
(4) Install intake manifold. Refer to Engine sec-
tion.
(5) Connect knock sensor pigtail wiring harness to
engine wiring harness near right / rear of intake
manifold (Fig. 23).
SPARK PLUG
DESCRIPTION
Both the 4.0L 6-cylinder and the 4.7L V-8 engine
use resistor type spark plugs. Standard 4.7L V-8
engines are equipped with ªfired in suppressor sealº
type spark plugs using a copper core ground elec-
trode. High-Output (H.O.) 4.7L V-8 engines are
equipped with unique plugs using a platinum rivet
located on the tip of the center electrode.
Because of the use of an aluminum cylinder head
on the 4.7L engine, spark plug torque is very critical.
To prevent possible pre-ignition and/or mechanical
engine damage, the correct type/heat range/number
spark plug must be used.Do not substitute any
other spark plug on the 4.7L H.O. engine. Seri-
ous engine damage may occur.
Plugs on both engines have resistance values rang-
ing from 6,000 to 20,000 ohms (when checked with at
least a 1000 volt spark plug tester).Do not use an
ohmmeter to check the resistance values of thespark plugs. Inaccurate readings will result.
Remove the spark plugs and examine them for
burned electrodes and fouled, cracked or broken por-
celain insulators. Keep plugs arranged in the order
in which they were removed from the engine. A sin-
gle plug displaying an abnormal condition indicates
that a problem exists in the corresponding cylinder.
Replace spark plugs at the intervals recommended in
Group O, Lubrication and Maintenance.
EXCEPT 4.7L H.O. ENGINE :Spark plugs that
have low mileage may be cleaned and reused if not
otherwise defective, carbon or oil fouled. Also refer to
Spark Plug Conditions.4.7L H.O. ENGINE :Never
clean spark plugs on the 4.7L H.O. engine. Damage
to the platinum rivet will result.
CAUTION: EXCEPT 4.7L H.O. ENGINE : Never use a
motorized wire wheel brush to clean the spark
plugs. Metallic deposits will remain on the spark
plug insulator and will cause plug misfire.
H.O. Gap Adjustment:If equipped with the 4.7L
H.O. engine, do not use a wire-type gapping tool as
damage to the platinum rivet on the center electrode
may occur. Use a tapered-type gauge (Fig. 24).
DIAGNOSIS AND TESTING - SPARK PLUG
CONDITIONS
NORMAL OPERATING
The few deposits present on the spark plug will
probably be light tan or slightly gray in color. This is
evident with most grades of commercial gasoline
Fig. 24 PLUG GAP - 4.7L H.O.
1 - TAPER GAUGE
WJIGNITION CONTROL 8I - 15
KNOCK SENSOR (Continued)
Page 429 of 2199
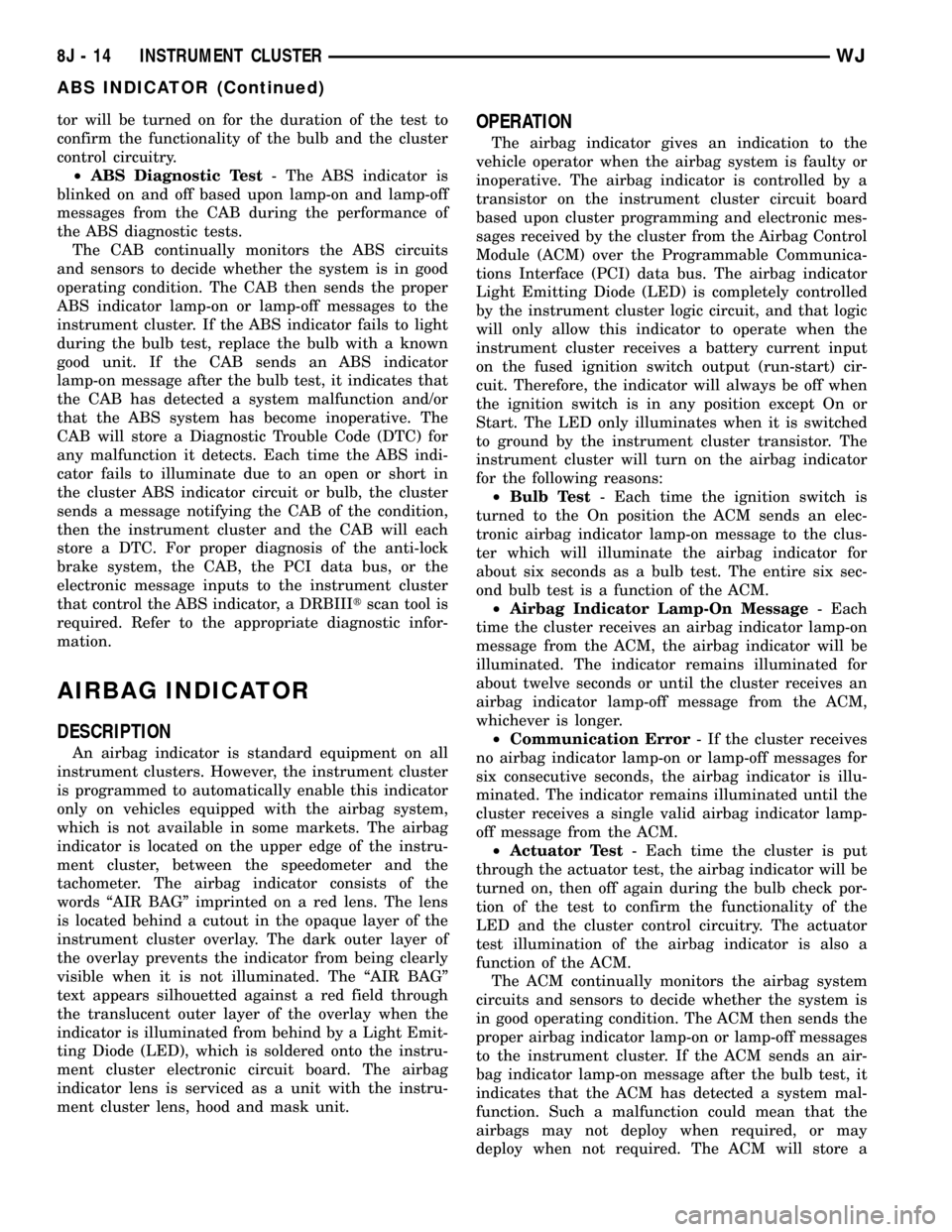
tor will be turned on for the duration of the test to
confirm the functionality of the bulb and the cluster
control circuitry.
²ABS Diagnostic Test- The ABS indicator is
blinked on and off based upon lamp-on and lamp-off
messages from the CAB during the performance of
the ABS diagnostic tests.
The CAB continually monitors the ABS circuits
and sensors to decide whether the system is in good
operating condition. The CAB then sends the proper
ABS indicator lamp-on or lamp-off messages to the
instrument cluster. If the ABS indicator fails to light
during the bulb test, replace the bulb with a known
good unit. If the CAB sends an ABS indicator
lamp-on message after the bulb test, it indicates that
the CAB has detected a system malfunction and/or
that the ABS system has become inoperative. The
CAB will store a Diagnostic Trouble Code (DTC) for
any malfunction it detects. Each time the ABS indi-
cator fails to illuminate due to an open or short in
the cluster ABS indicator circuit or bulb, the cluster
sends a message notifying the CAB of the condition,
then the instrument cluster and the CAB will each
store a DTC. For proper diagnosis of the anti-lock
brake system, the CAB, the PCI data bus, or the
electronic message inputs to the instrument cluster
that control the ABS indicator, a DRBIIItscan tool is
required. Refer to the appropriate diagnostic infor-
mation.
AIRBAG INDICATOR
DESCRIPTION
An airbag indicator is standard equipment on all
instrument clusters. However, the instrument cluster
is programmed to automatically enable this indicator
only on vehicles equipped with the airbag system,
which is not available in some markets. The airbag
indicator is located on the upper edge of the instru-
ment cluster, between the speedometer and the
tachometer. The airbag indicator consists of the
words ªAIR BAGº imprinted on a red lens. The lens
is located behind a cutout in the opaque layer of the
instrument cluster overlay. The dark outer layer of
the overlay prevents the indicator from being clearly
visible when it is not illuminated. The ªAIR BAGº
text appears silhouetted against a red field through
the translucent outer layer of the overlay when the
indicator is illuminated from behind by a Light Emit-
ting Diode (LED), which is soldered onto the instru-
ment cluster electronic circuit board. The airbag
indicator lens is serviced as a unit with the instru-
ment cluster lens, hood and mask unit.
OPERATION
The airbag indicator gives an indication to the
vehicle operator when the airbag system is faulty or
inoperative. The airbag indicator is controlled by a
transistor on the instrument cluster circuit board
based upon cluster programming and electronic mes-
sages received by the cluster from the Airbag Control
Module (ACM) over the Programmable Communica-
tions Interface (PCI) data bus. The airbag indicator
Light Emitting Diode (LED) is completely controlled
by the instrument cluster logic circuit, and that logic
will only allow this indicator to operate when the
instrument cluster receives a battery current input
on the fused ignition switch output (run-start) cir-
cuit. Therefore, the indicator will always be off when
the ignition switch is in any position except On or
Start. The LED only illuminates when it is switched
to ground by the instrument cluster transistor. The
instrument cluster will turn on the airbag indicator
for the following reasons:
²Bulb Test- Each time the ignition switch is
turned to the On position the ACM sends an elec-
tronic airbag indicator lamp-on message to the clus-
ter which will illuminate the airbag indicator for
about six seconds as a bulb test. The entire six sec-
ond bulb test is a function of the ACM.
²Airbag Indicator Lamp-On Message- Each
time the cluster receives an airbag indicator lamp-on
message from the ACM, the airbag indicator will be
illuminated. The indicator remains illuminated for
about twelve seconds or until the cluster receives an
airbag indicator lamp-off message from the ACM,
whichever is longer.
²Communication Error- If the cluster receives
no airbag indicator lamp-on or lamp-off messages for
six consecutive seconds, the airbag indicator is illu-
minated. The indicator remains illuminated until the
cluster receives a single valid airbag indicator lamp-
off message from the ACM.
²Actuator Test- Each time the cluster is put
through the actuator test, the airbag indicator will be
turned on, then off again during the bulb check por-
tion of the test to confirm the functionality of the
LED and the cluster control circuitry. The actuator
test illumination of the airbag indicator is also a
function of the ACM.
The ACM continually monitors the airbag system
circuits and sensors to decide whether the system is
in good operating condition. The ACM then sends the
proper airbag indicator lamp-on or lamp-off messages
to the instrument cluster. If the ACM sends an air-
bag indicator lamp-on message after the bulb test, it
indicates that the ACM has detected a system mal-
function. Such a malfunction could mean that the
airbags may not deploy when required, or may
deploy when not required. The ACM will store a
8J - 14 INSTRUMENT CLUSTERWJ
ABS INDICATOR (Continued)
Page 439 of 2199
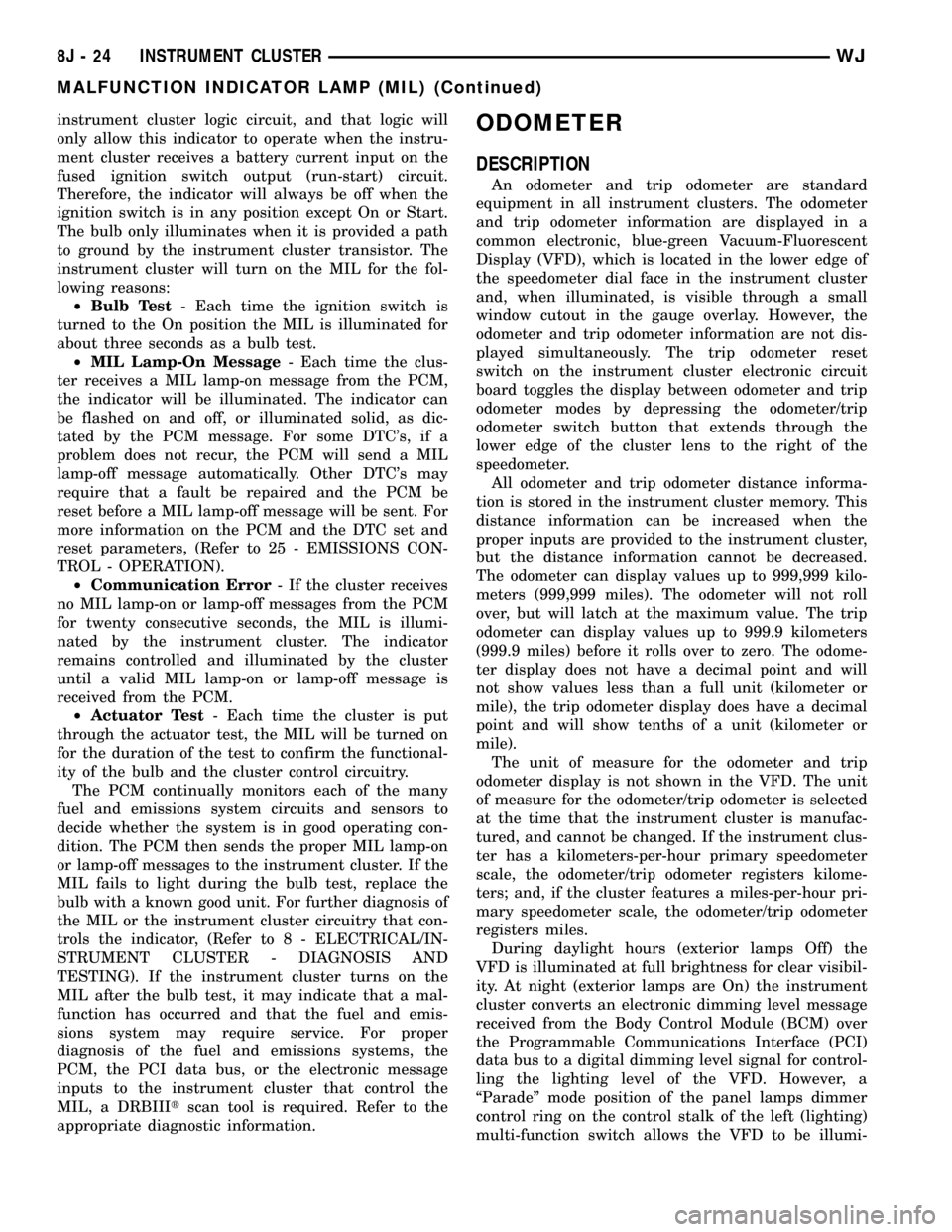
instrument cluster logic circuit, and that logic will
only allow this indicator to operate when the instru-
ment cluster receives a battery current input on the
fused ignition switch output (run-start) circuit.
Therefore, the indicator will always be off when the
ignition switch is in any position except On or Start.
The bulb only illuminates when it is provided a path
to ground by the instrument cluster transistor. The
instrument cluster will turn on the MIL for the fol-
lowing reasons:
²Bulb Test- Each time the ignition switch is
turned to the On position the MIL is illuminated for
about three seconds as a bulb test.
²MIL Lamp-On Message- Each time the clus-
ter receives a MIL lamp-on message from the PCM,
the indicator will be illuminated. The indicator can
be flashed on and off, or illuminated solid, as dic-
tated by the PCM message. For some DTC's, if a
problem does not recur, the PCM will send a MIL
lamp-off message automatically. Other DTC's may
require that a fault be repaired and the PCM be
reset before a MIL lamp-off message will be sent. For
more information on the PCM and the DTC set and
reset parameters, (Refer to 25 - EMISSIONS CON-
TROL - OPERATION).
²Communication Error- If the cluster receives
no MIL lamp-on or lamp-off messages from the PCM
for twenty consecutive seconds, the MIL is illumi-
nated by the instrument cluster. The indicator
remains controlled and illuminated by the cluster
until a valid MIL lamp-on or lamp-off message is
received from the PCM.
²Actuator Test- Each time the cluster is put
through the actuator test, the MIL will be turned on
for the duration of the test to confirm the functional-
ity of the bulb and the cluster control circuitry.
The PCM continually monitors each of the many
fuel and emissions system circuits and sensors to
decide whether the system is in good operating con-
dition. The PCM then sends the proper MIL lamp-on
or lamp-off messages to the instrument cluster. If the
MIL fails to light during the bulb test, replace the
bulb with a known good unit. For further diagnosis of
the MIL or the instrument cluster circuitry that con-
trols the indicator, (Refer to 8 - ELECTRICAL/IN-
STRUMENT CLUSTER - DIAGNOSIS AND
TESTING). If the instrument cluster turns on the
MIL after the bulb test, it may indicate that a mal-
function has occurred and that the fuel and emis-
sions system may require service. For proper
diagnosis of the fuel and emissions systems, the
PCM, the PCI data bus, or the electronic message
inputs to the instrument cluster that control the
MIL, a DRBIIItscan tool is required. Refer to the
appropriate diagnostic information.ODOMETER
DESCRIPTION
An odometer and trip odometer are standard
equipment in all instrument clusters. The odometer
and trip odometer information are displayed in a
common electronic, blue-green Vacuum-Fluorescent
Display (VFD), which is located in the lower edge of
the speedometer dial face in the instrument cluster
and, when illuminated, is visible through a small
window cutout in the gauge overlay. However, the
odometer and trip odometer information are not dis-
played simultaneously. The trip odometer reset
switch on the instrument cluster electronic circuit
board toggles the display between odometer and trip
odometer modes by depressing the odometer/trip
odometer switch button that extends through the
lower edge of the cluster lens to the right of the
speedometer.
All odometer and trip odometer distance informa-
tion is stored in the instrument cluster memory. This
distance information can be increased when the
proper inputs are provided to the instrument cluster,
but the distance information cannot be decreased.
The odometer can display values up to 999,999 kilo-
meters (999,999 miles). The odometer will not roll
over, but will latch at the maximum value. The trip
odometer can display values up to 999.9 kilometers
(999.9 miles) before it rolls over to zero. The odome-
ter display does not have a decimal point and will
not show values less than a full unit (kilometer or
mile), the trip odometer display does have a decimal
point and will show tenths of a unit (kilometer or
mile).
The unit of measure for the odometer and trip
odometer display is not shown in the VFD. The unit
of measure for the odometer/trip odometer is selected
at the time that the instrument cluster is manufac-
tured, and cannot be changed. If the instrument clus-
ter has a kilometers-per-hour primary speedometer
scale, the odometer/trip odometer registers kilome-
ters; and, if the cluster features a miles-per-hour pri-
mary speedometer scale, the odometer/trip odometer
registers miles.
During daylight hours (exterior lamps Off) the
VFD is illuminated at full brightness for clear visibil-
ity. At night (exterior lamps are On) the instrument
cluster converts an electronic dimming level message
received from the Body Control Module (BCM) over
the Programmable Communications Interface (PCI)
data bus to a digital dimming level signal for control-
ling the lighting level of the VFD. However, a
ªParadeº mode position of the panel lamps dimmer
control ring on the control stalk of the left (lighting)
multi-function switch allows the VFD to be illumi-
8J - 24 INSTRUMENT CLUSTERWJ
MALFUNCTION INDICATOR LAMP (MIL) (Continued)