o2 location JEEP GRAND CHEROKEE 2002 WJ / 2.G Workshop Manual
[x] Cancel search | Manufacturer: JEEP, Model Year: 2002, Model line: GRAND CHEROKEE, Model: JEEP GRAND CHEROKEE 2002 WJ / 2.GPages: 2199, PDF Size: 76.01 MB
Page 1792 of 2199
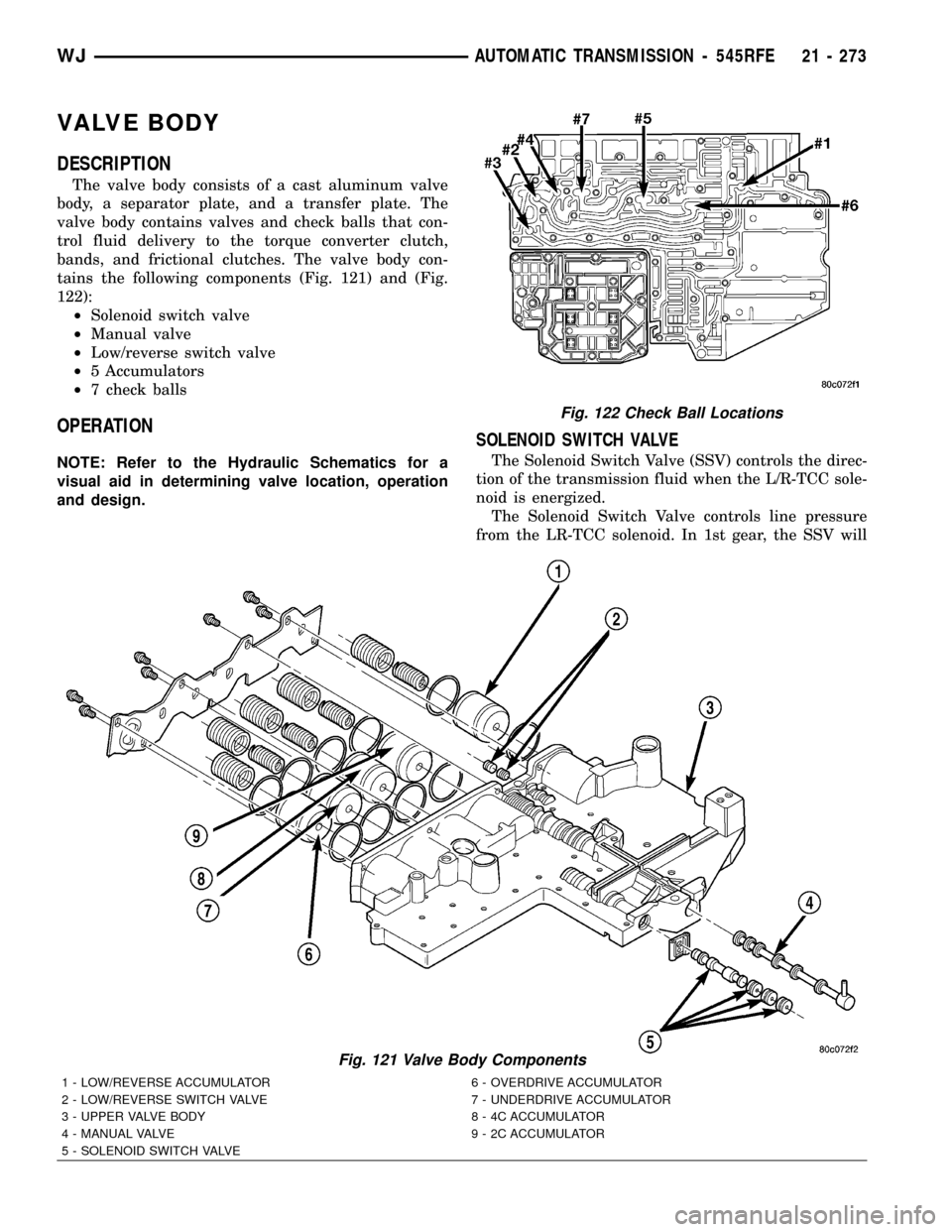
VALVE BODY
DESCRIPTION
The valve body consists of a cast aluminum valve
body, a separator plate, and a transfer plate. The
valve body contains valves and check balls that con-
trol fluid delivery to the torque converter clutch,
bands, and frictional clutches. The valve body con-
tains the following components (Fig. 121) and (Fig.
122):
²Solenoid switch valve
²Manual valve
²Low/reverse switch valve
²5 Accumulators
²7 check balls
OPERATION
NOTE: Refer to the Hydraulic Schematics for a
visual aid in determining valve location, operation
and design.
SOLENOID SWITCH VALVE
The Solenoid Switch Valve (SSV) controls the direc-
tion of the transmission fluid when the L/R-TCC sole-
noid is energized.
The Solenoid Switch Valve controls line pressure
from the LR-TCC solenoid. In 1st gear, the SSV will
Fig. 121 Valve Body Components
1 - LOW/REVERSE ACCUMULATOR 6 - OVERDRIVE ACCUMULATOR
2 - LOW/REVERSE SWITCH VALVE 7 - UNDERDRIVE ACCUMULATOR
3 - UPPER VALVE BODY 8 - 4C ACCUMULATOR
4 - MANUAL VALVE 9 - 2C ACCUMULATOR
5 - SOLENOID SWITCH VALVE
Fig. 122 Check Ball Locations
WJAUTOMATIC TRANSMISSION - 545RFE 21 - 273
Page 1795 of 2199
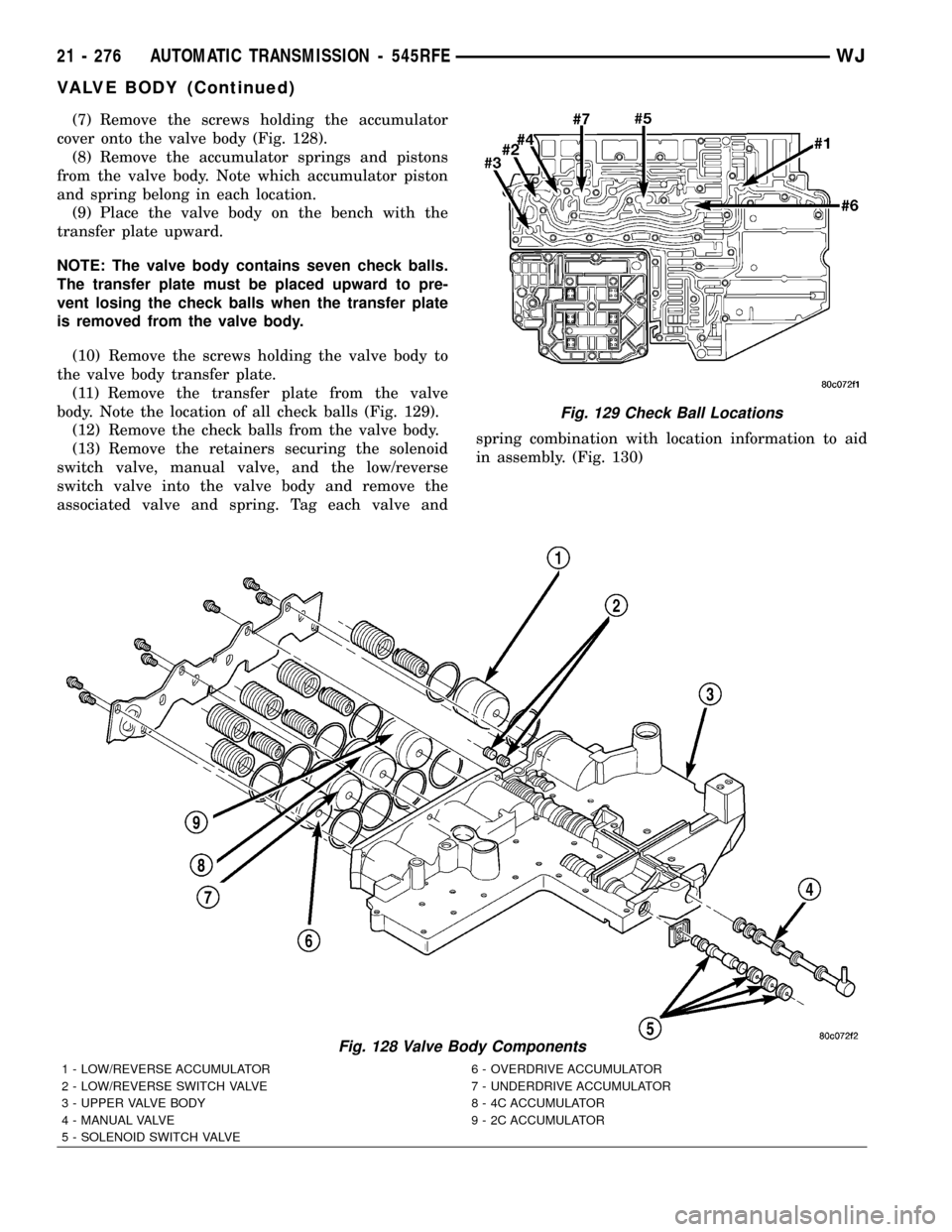
(7) Remove the screws holding the accumulator
cover onto the valve body (Fig. 128).
(8) Remove the accumulator springs and pistons
from the valve body. Note which accumulator piston
and spring belong in each location.
(9) Place the valve body on the bench with the
transfer plate upward.
NOTE: The valve body contains seven check balls.
The transfer plate must be placed upward to pre-
vent losing the check balls when the transfer plate
is removed from the valve body.
(10) Remove the screws holding the valve body to
the valve body transfer plate.
(11) Remove the transfer plate from the valve
body. Note the location of all check balls (Fig. 129).
(12) Remove the check balls from the valve body.
(13) Remove the retainers securing the solenoid
switch valve, manual valve, and the low/reverse
switch valve into the valve body and remove the
associated valve and spring. Tag each valve andspring combination with location information to aid
in assembly. (Fig. 130)
Fig. 128 Valve Body Components
1 - LOW/REVERSE ACCUMULATOR 6 - OVERDRIVE ACCUMULATOR
2 - LOW/REVERSE SWITCH VALVE 7 - UNDERDRIVE ACCUMULATOR
3 - UPPER VALVE BODY 8 - 4C ACCUMULATOR
4 - MANUAL VALVE 9 - 2C ACCUMULATOR
5 - SOLENOID SWITCH VALVE
Fig. 129 Check Ball Locations
21 - 276 AUTOMATIC TRANSMISSION - 545RFEWJ
VALVE BODY (Continued)
Page 1797 of 2199
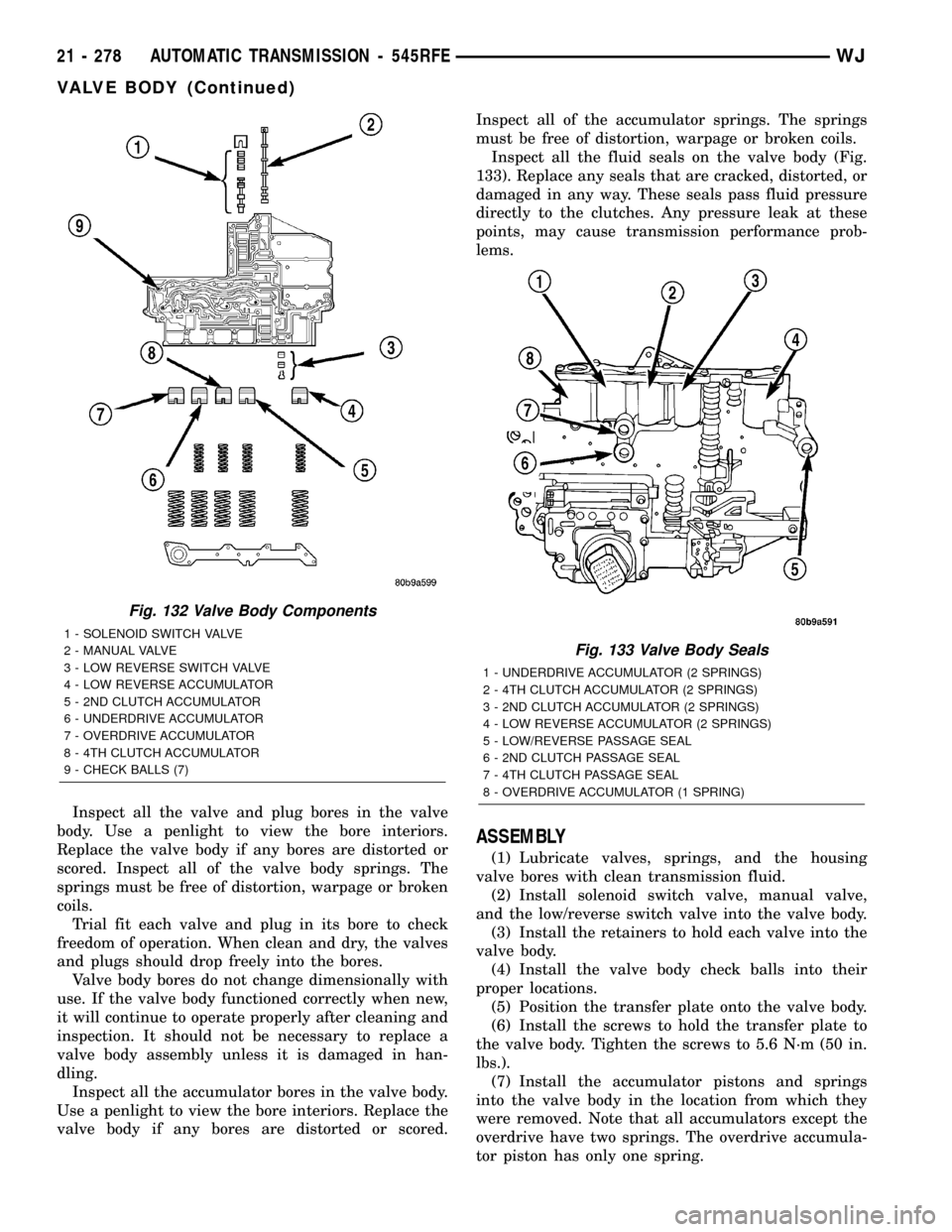
Inspect all the valve and plug bores in the valve
body. Use a penlight to view the bore interiors.
Replace the valve body if any bores are distorted or
scored. Inspect all of the valve body springs. The
springs must be free of distortion, warpage or broken
coils.
Trial fit each valve and plug in its bore to check
freedom of operation. When clean and dry, the valves
and plugs should drop freely into the bores.
Valve body bores do not change dimensionally with
use. If the valve body functioned correctly when new,
it will continue to operate properly after cleaning and
inspection. It should not be necessary to replace a
valve body assembly unless it is damaged in han-
dling.
Inspect all the accumulator bores in the valve body.
Use a penlight to view the bore interiors. Replace the
valve body if any bores are distorted or scored.Inspect all of the accumulator springs. The springs
must be free of distortion, warpage or broken coils.
Inspect all the fluid seals on the valve body (Fig.
133). Replace any seals that are cracked, distorted, or
damaged in any way. These seals pass fluid pressure
directly to the clutches. Any pressure leak at these
points, may cause transmission performance prob-
lems.
ASSEMBLY
(1) Lubricate valves, springs, and the housing
valve bores with clean transmission fluid.
(2) Install solenoid switch valve, manual valve,
and the low/reverse switch valve into the valve body.
(3) Install the retainers to hold each valve into the
valve body.
(4) Install the valve body check balls into their
proper locations.
(5) Position the transfer plate onto the valve body.
(6) Install the screws to hold the transfer plate to
the valve body. Tighten the screws to 5.6 N´m (50 in.
lbs.).
(7) Install the accumulator pistons and springs
into the valve body in the location from which they
were removed. Note that all accumulators except the
overdrive have two springs. The overdrive accumula-
tor piston has only one spring.
Fig. 132 Valve Body Components
1 - SOLENOID SWITCH VALVE
2 - MANUAL VALVE
3 - LOW REVERSE SWITCH VALVE
4 - LOW REVERSE ACCUMULATOR
5 - 2ND CLUTCH ACCUMULATOR
6 - UNDERDRIVE ACCUMULATOR
7 - OVERDRIVE ACCUMULATOR
8 - 4TH CLUTCH ACCUMULATOR
9 - CHECK BALLS (7)
Fig. 133 Valve Body Seals
1 - UNDERDRIVE ACCUMULATOR (2 SPRINGS)
2 - 4TH CLUTCH ACCUMULATOR (2 SPRINGS)
3 - 2ND CLUTCH ACCUMULATOR (2 SPRINGS)
4 - LOW REVERSE ACCUMULATOR (2 SPRINGS)
5 - LOW/REVERSE PASSAGE SEAL
6 - 2ND CLUTCH PASSAGE SEAL
7 - 4TH CLUTCH PASSAGE SEAL
8 - OVERDRIVE ACCUMULATOR (1 SPRING)
21 - 278 AUTOMATIC TRANSMISSION - 545RFEWJ
VALVE BODY (Continued)
Page 1800 of 2199
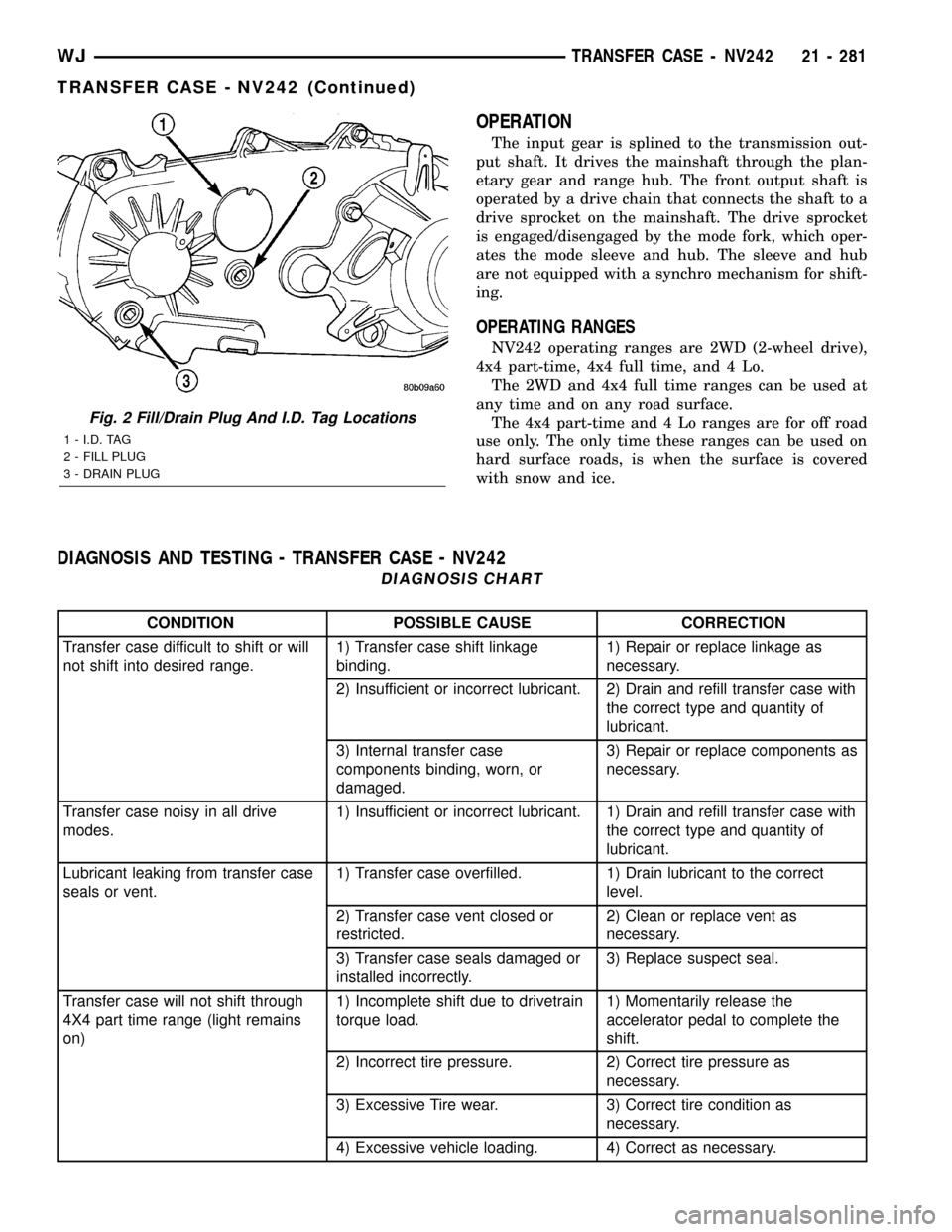
OPERATION
The input gear is splined to the transmission out-
put shaft. It drives the mainshaft through the plan-
etary gear and range hub. The front output shaft is
operated by a drive chain that connects the shaft to a
drive sprocket on the mainshaft. The drive sprocket
is engaged/disengaged by the mode fork, which oper-
ates the mode sleeve and hub. The sleeve and hub
are not equipped with a synchro mechanism for shift-
ing.
OPERATING RANGES
NV242 operating ranges are 2WD (2-wheel drive),
4x4 part-time, 4x4 full time, and 4 Lo.
The 2WD and 4x4 full time ranges can be used at
any time and on any road surface.
The 4x4 part-time and 4 Lo ranges are for off road
use only. The only time these ranges can be used on
hard surface roads, is when the surface is covered
with snow and ice.
DIAGNOSIS AND TESTING - TRANSFER CASE - NV242
DIAGNOSIS CHART
CONDITION POSSIBLE CAUSE CORRECTION
Transfer case difficult to shift or will
not shift into desired range.1) Transfer case shift linkage
binding.1) Repair or replace linkage as
necessary.
2) Insufficient or incorrect lubricant. 2) Drain and refill transfer case with
the correct type and quantity of
lubricant.
3) Internal transfer case
components binding, worn, or
damaged.3) Repair or replace components as
necessary.
Transfer case noisy in all drive
modes.1) Insufficient or incorrect lubricant. 1) Drain and refill transfer case with
the correct type and quantity of
lubricant.
Lubricant leaking from transfer case
seals or vent.1) Transfer case overfilled. 1) Drain lubricant to the correct
level.
2) Transfer case vent closed or
restricted.2) Clean or replace vent as
necessary.
3) Transfer case seals damaged or
installed incorrectly.3) Replace suspect seal.
Transfer case will not shift through
4X4 part time range (light remains
on)1) Incomplete shift due to drivetrain
torque load.1) Momentarily release the
accelerator pedal to complete the
shift.
2) Incorrect tire pressure. 2) Correct tire pressure as
necessary.
3) Excessive Tire wear. 3) Correct tire condition as
necessary.
4) Excessive vehicle loading. 4) Correct as necessary.
Fig. 2 Fill/Drain Plug And I.D. Tag Locations
1 - I.D. TAG
2 - FILL PLUG
3 - DRAIN PLUG
WJTRANSFER CASE - NV242 21 - 281
TRANSFER CASE - NV242 (Continued)
Page 1804 of 2199
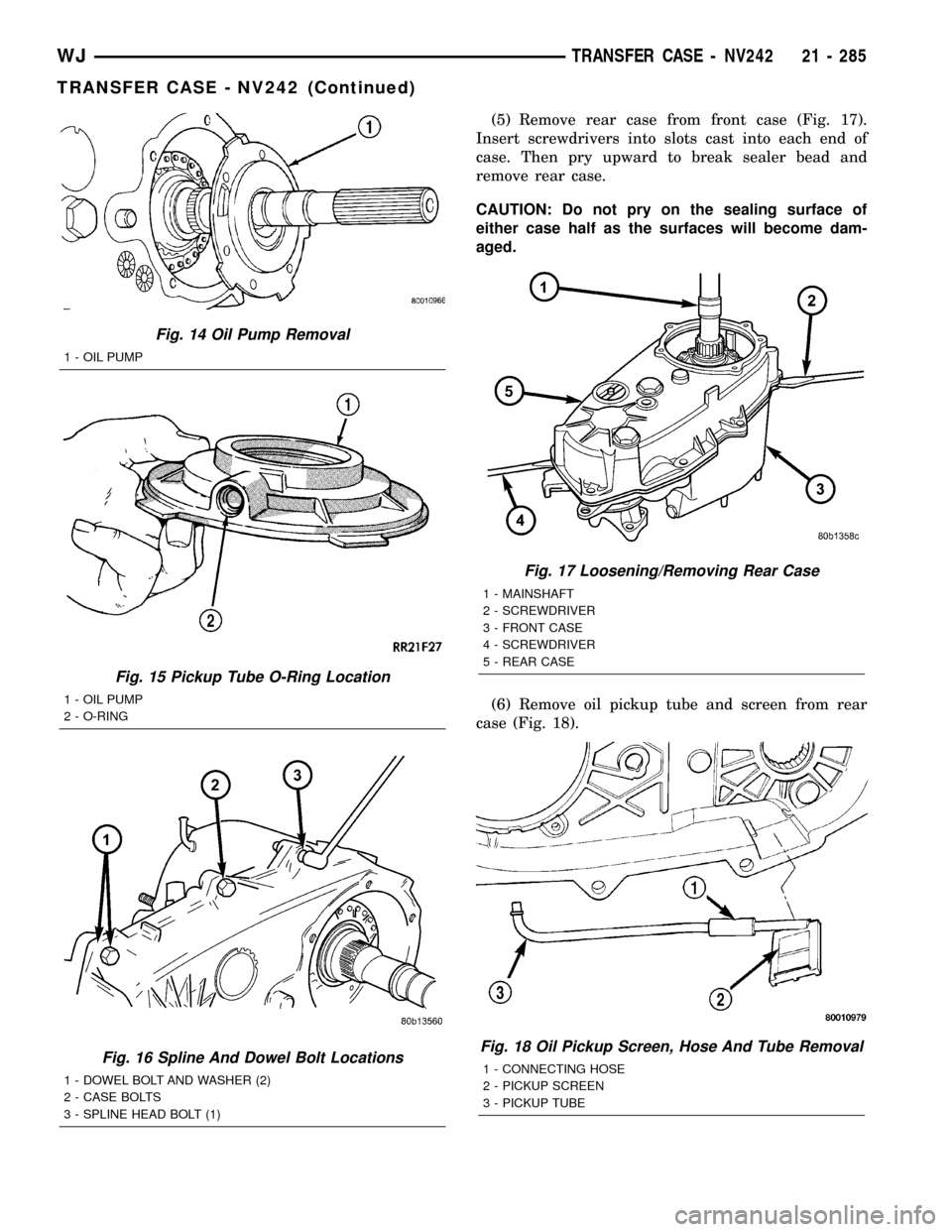
(5) Remove rear case from front case (Fig. 17).
Insert screwdrivers into slots cast into each end of
case. Then pry upward to break sealer bead and
remove rear case.
CAUTION: Do not pry on the sealing surface of
either case half as the surfaces will become dam-
aged.
(6) Remove oil pickup tube and screen from rear
case (Fig. 18).
Fig. 14 Oil Pump Removal
1 - OIL PUMP
Fig. 15 Pickup Tube O-Ring Location
1 - OIL PUMP
2 - O-RING
Fig. 16 Spline And Dowel Bolt Locations
1 - DOWEL BOLT AND WASHER (2)
2 - CASE BOLTS
3 - SPLINE HEAD BOLT (1)
Fig. 17 Loosening/Removing Rear Case
1 - MAINSHAFT
2 - SCREWDRIVER
3 - FRONT CASE
4 - SCREWDRIVER
5 - REAR CASE
Fig. 18 Oil Pickup Screen, Hose And Tube Removal
1 - CONNECTING HOSE
2 - PICKUP SCREEN
3 - PICKUP TUBE
WJTRANSFER CASE - NV242 21 - 285
TRANSFER CASE - NV242 (Continued)
Page 1813 of 2199
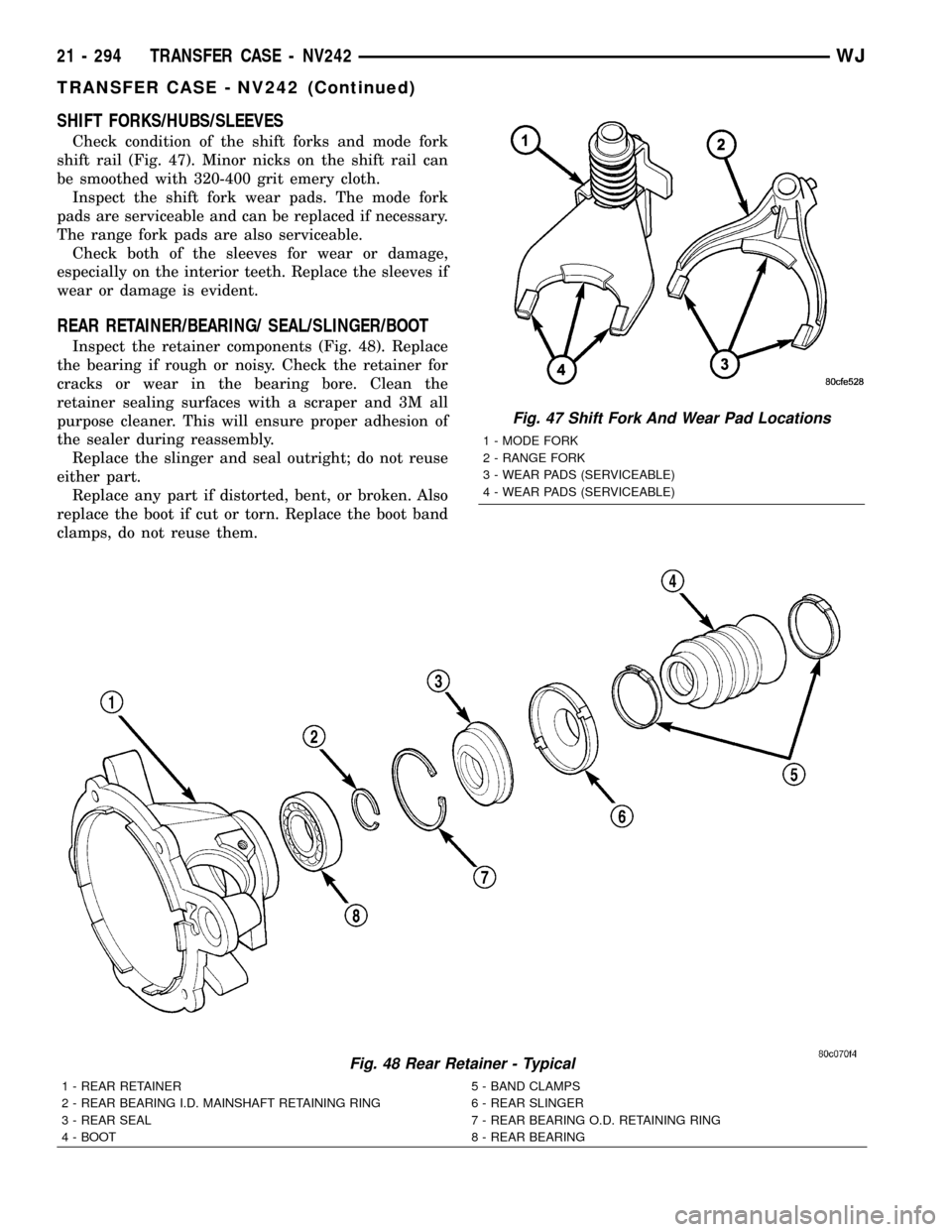
SHIFT FORKS/HUBS/SLEEVES
Check condition of the shift forks and mode fork
shift rail (Fig. 47). Minor nicks on the shift rail can
be smoothed with 320-400 grit emery cloth.
Inspect the shift fork wear pads. The mode fork
pads are serviceable and can be replaced if necessary.
The range fork pads are also serviceable.
Check both of the sleeves for wear or damage,
especially on the interior teeth. Replace the sleeves if
wear or damage is evident.
REAR RETAINER/BEARING/ SEAL/SLINGER/BOOT
Inspect the retainer components (Fig. 48). Replace
the bearing if rough or noisy. Check the retainer for
cracks or wear in the bearing bore. Clean the
retainer sealing surfaces with a scraper and 3M all
purpose cleaner. This will ensure proper adhesion of
the sealer during reassembly.
Replace the slinger and seal outright; do not reuse
either part.
Replace any part if distorted, bent, or broken. Also
replace the boot if cut or torn. Replace the boot band
clamps, do not reuse them.
Fig. 48 Rear Retainer - Typical
1 - REAR RETAINER 5 - BAND CLAMPS
2 - REAR BEARING I.D. MAINSHAFT RETAINING RING 6 - REAR SLINGER
3 - REAR SEAL 7 - REAR BEARING O.D. RETAINING RING
4 - BOOT 8 - REAR BEARING
Fig. 47 Shift Fork And Wear Pad Locations
1 - MODE FORK
2 - RANGE FORK
3 - WEAR PADS (SERVICEABLE)
4 - WEAR PADS (SERVICEABLE)
21 - 294 TRANSFER CASE - NV242WJ
TRANSFER CASE - NV242 (Continued)
Page 1824 of 2199
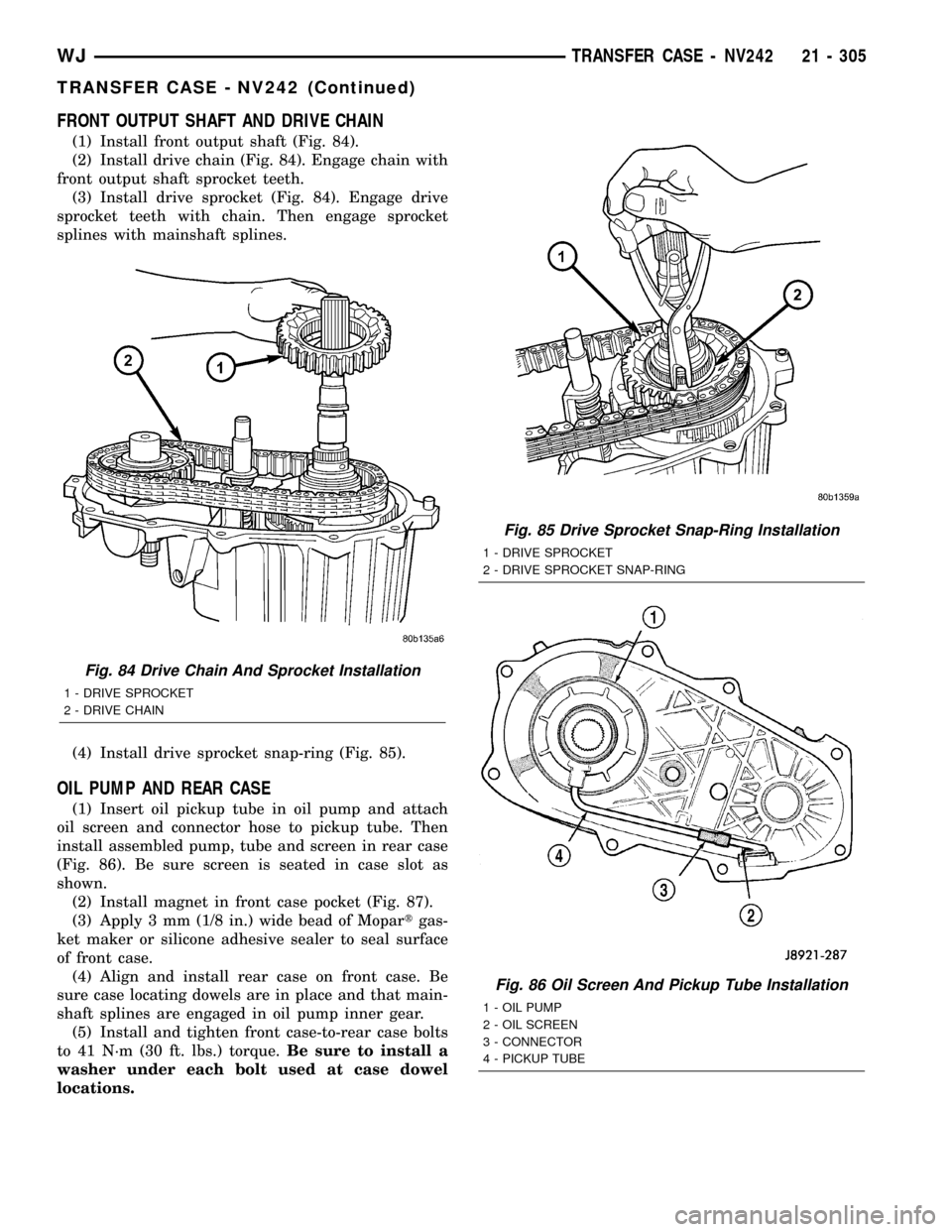
FRONT OUTPUT SHAFT AND DRIVE CHAIN
(1) Install front output shaft (Fig. 84).
(2) Install drive chain (Fig. 84). Engage chain with
front output shaft sprocket teeth.
(3) Install drive sprocket (Fig. 84). Engage drive
sprocket teeth with chain. Then engage sprocket
splines with mainshaft splines.
(4) Install drive sprocket snap-ring (Fig. 85).
OIL PUMP AND REAR CASE
(1) Insert oil pickup tube in oil pump and attach
oil screen and connector hose to pickup tube. Then
install assembled pump, tube and screen in rear case
(Fig. 86). Be sure screen is seated in case slot as
shown.
(2) Install magnet in front case pocket (Fig. 87).
(3) Apply 3 mm (1/8 in.) wide bead of Mopartgas-
ket maker or silicone adhesive sealer to seal surface
of front case.
(4) Align and install rear case on front case. Be
sure case locating dowels are in place and that main-
shaft splines are engaged in oil pump inner gear.
(5) Install and tighten front case-to-rear case bolts
to 41 N´m (30 ft. lbs.) torque.Be sure to install a
washer under each bolt used at case dowel
locations.
Fig. 84 Drive Chain And Sprocket Installation
1 - DRIVE SPROCKET
2 - DRIVE CHAIN
Fig. 85 Drive Sprocket Snap-Ring Installation
1 - DRIVE SPROCKET
2 - DRIVE SPROCKET SNAP-RING
Fig. 86 Oil Screen And Pickup Tube Installation
1 - OIL PUMP
2 - OIL SCREEN
3 - CONNECTOR
4 - PICKUP TUBE
WJTRANSFER CASE - NV242 21 - 305
TRANSFER CASE - NV242 (Continued)
Page 1829 of 2199
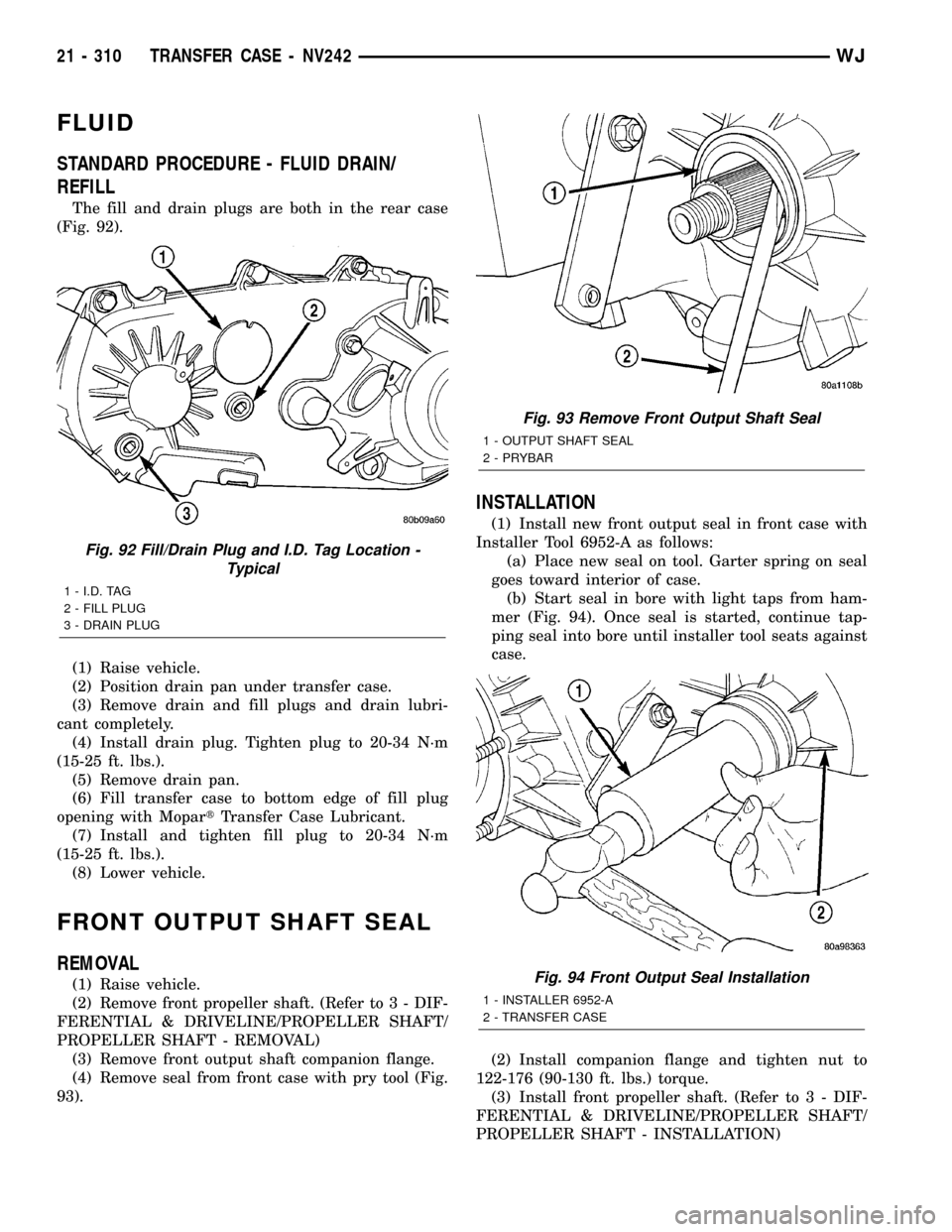
FLUID
STANDARD PROCEDURE - FLUID DRAIN/
REFILL
The fill and drain plugs are both in the rear case
(Fig. 92).
(1) Raise vehicle.
(2) Position drain pan under transfer case.
(3) Remove drain and fill plugs and drain lubri-
cant completely.
(4) Install drain plug. Tighten plug to 20-34 N´m
(15-25 ft. lbs.).
(5) Remove drain pan.
(6) Fill transfer case to bottom edge of fill plug
opening with MopartTransfer Case Lubricant.
(7) Install and tighten fill plug to 20-34 N´m
(15-25 ft. lbs.).
(8) Lower vehicle.
FRONT OUTPUT SHAFT SEAL
REMOVAL
(1) Raise vehicle.
(2) Remove front propeller shaft. (Refer to 3 - DIF-
FERENTIAL & DRIVELINE/PROPELLER SHAFT/
PROPELLER SHAFT - REMOVAL)
(3) Remove front output shaft companion flange.
(4) Remove seal from front case with pry tool (Fig.
93).
INSTALLATION
(1) Install new front output seal in front case with
Installer Tool 6952-A as follows:
(a) Place new seal on tool. Garter spring on seal
goes toward interior of case.
(b) Start seal in bore with light taps from ham-
mer (Fig. 94). Once seal is started, continue tap-
ping seal into bore until installer tool seats against
case.
(2) Install companion flange and tighten nut to
122-176 (90-130 ft. lbs.) torque.
(3) Install front propeller shaft. (Refer to 3 - DIF-
FERENTIAL & DRIVELINE/PROPELLER SHAFT/
PROPELLER SHAFT - INSTALLATION)
Fig. 92 Fill/Drain Plug and I.D. Tag Location -
Typical
1 - I.D. TAG
2 - FILL PLUG
3 - DRAIN PLUG
Fig. 93 Remove Front Output Shaft Seal
1 - OUTPUT SHAFT SEAL
2 - PRYBAR
Fig. 94 Front Output Seal Installation
1 - INSTALLER 6952-A
2 - TRANSFER CASE
21 - 310 TRANSFER CASE - NV242WJ
Page 1834 of 2199
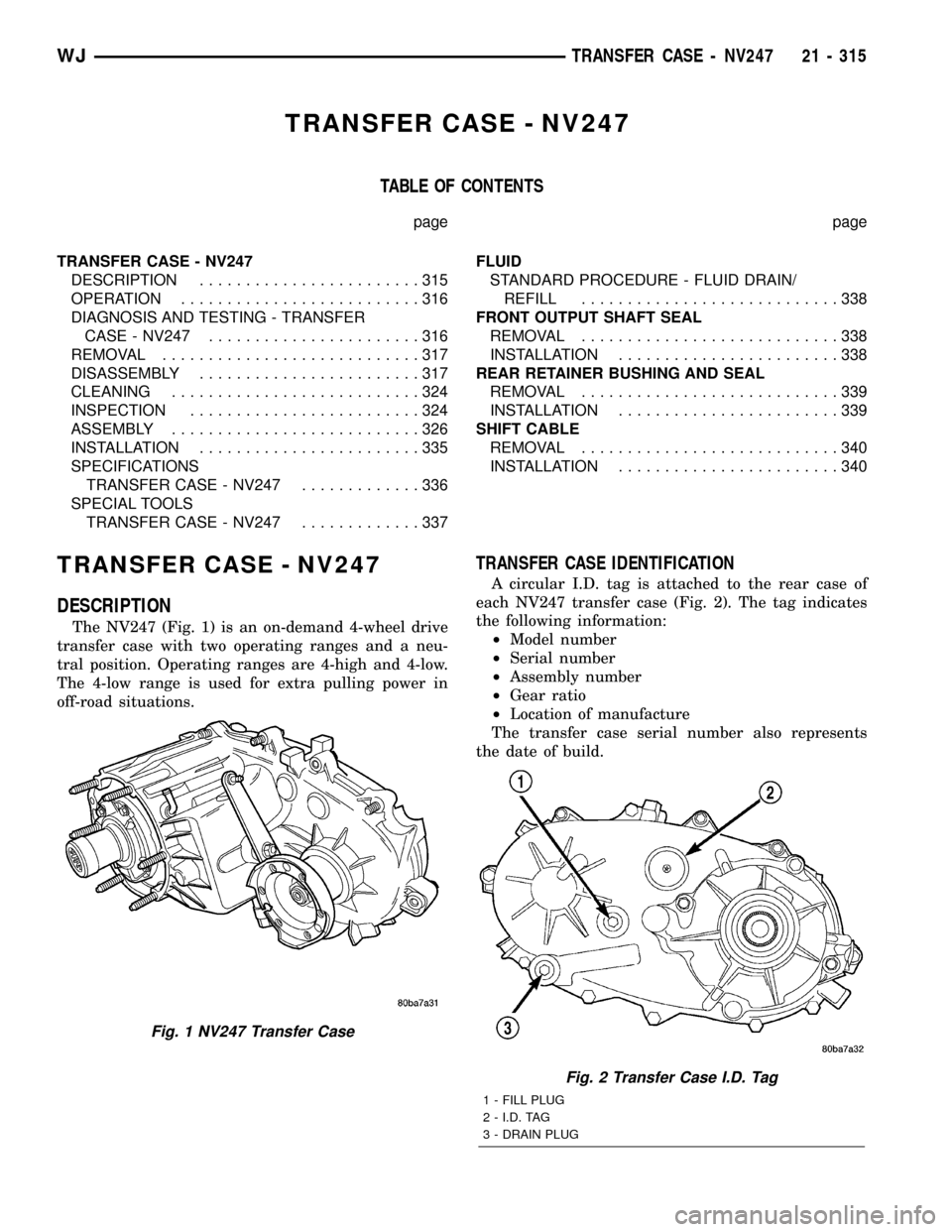
TRANSFER CASE - NV247
TABLE OF CONTENTS
page page
TRANSFER CASE - NV247
DESCRIPTION........................315
OPERATION..........................316
DIAGNOSIS AND TESTING - TRANSFER
CASE - NV247.......................316
REMOVAL............................317
DISASSEMBLY........................317
CLEANING...........................324
INSPECTION.........................324
ASSEMBLY...........................326
INSTALLATION........................335
SPECIFICATIONS
TRANSFER CASE - NV247.............336
SPECIAL TOOLS
TRANSFER CASE - NV247.............337FLUID
STANDARD PROCEDURE - FLUID DRAIN/
REFILL............................338
FRONT OUTPUT SHAFT SEAL
REMOVAL............................338
INSTALLATION........................338
REAR RETAINER BUSHING AND SEAL
REMOVAL............................339
INSTALLATION........................339
SHIFT CABLE
REMOVAL............................340
INSTALLATION........................340
TRANSFER CASE - NV247
DESCRIPTION
The NV247 (Fig. 1) is an on-demand 4-wheel drive
transfer case with two operating ranges and a neu-
tral position. Operating ranges are 4-high and 4-low.
The 4-low range is used for extra pulling power in
off-road situations.
TRANSFER CASE IDENTIFICATION
A circular I.D. tag is attached to the rear case of
each NV247 transfer case (Fig. 2). The tag indicates
the following information:
²Model number
²Serial number
²Assembly number
²Gear ratio
²Location of manufacture
The transfer case serial number also represents
the date of build.
Fig. 1 NV247 Transfer Case
Fig. 2 Transfer Case I.D. Tag
1 - FILL PLUG
2 - I.D. TAG
3 - DRAIN PLUG
WJTRANSFER CASE - NV247 21 - 315
Page 1838 of 2199
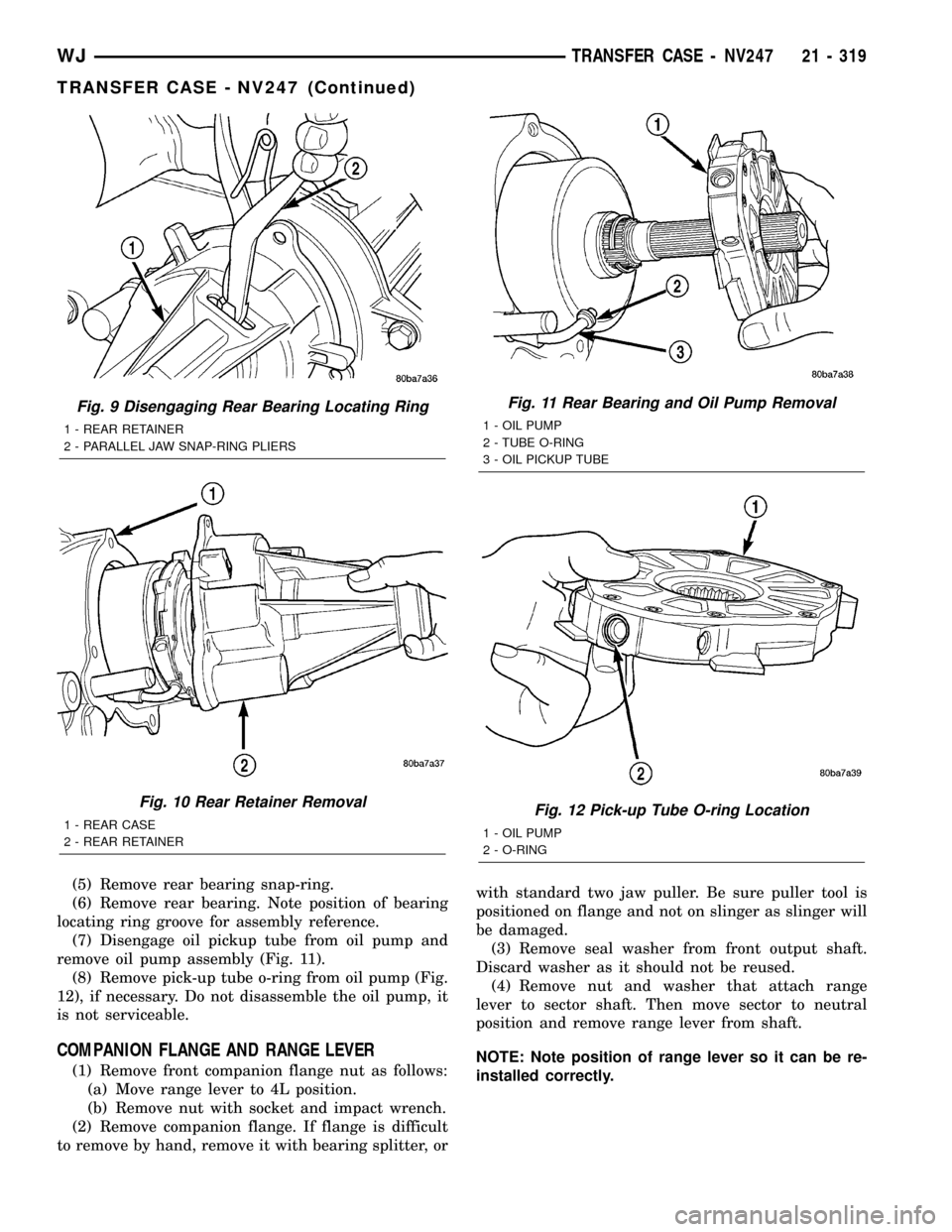
(5) Remove rear bearing snap-ring.
(6) Remove rear bearing. Note position of bearing
locating ring groove for assembly reference.
(7) Disengage oil pickup tube from oil pump and
remove oil pump assembly (Fig. 11).
(8) Remove pick-up tube o-ring from oil pump (Fig.
12), if necessary. Do not disassemble the oil pump, it
is not serviceable.
COMPANION FLANGE AND RANGE LEVER
(1) Remove front companion flange nut as follows:
(a) Move range lever to 4L position.
(b) Remove nut with socket and impact wrench.
(2) Remove companion flange. If flange is difficult
to remove by hand, remove it with bearing splitter, orwith standard two jaw puller. Be sure puller tool is
positioned on flange and not on slinger as slinger will
be damaged.
(3) Remove seal washer from front output shaft.
Discard washer as it should not be reused.
(4) Remove nut and washer that attach range
lever to sector shaft. Then move sector to neutral
position and remove range lever from shaft.
NOTE: Note position of range lever so it can be re-
installed correctly.
Fig. 9 Disengaging Rear Bearing Locating Ring
1 - REAR RETAINER
2 - PARALLEL JAW SNAP-RING PLIERS
Fig. 10 Rear Retainer Removal
1 - REAR CASE
2 - REAR RETAINER
Fig. 11 Rear Bearing and Oil Pump Removal
1 - OIL PUMP
2 - TUBE O-RING
3 - OIL PICKUP TUBE
Fig. 12 Pick-up Tube O-ring Location
1 - OIL PUMP
2 - O-RING
WJTRANSFER CASE - NV247 21 - 319
TRANSFER CASE - NV247 (Continued)