Heating & JEEP GRAND CHEROKEE 2002 WJ / 2.G Owner's Manual
[x] Cancel search | Manufacturer: JEEP, Model Year: 2002, Model line: GRAND CHEROKEE, Model: JEEP GRAND CHEROKEE 2002 WJ / 2.GPages: 2199, PDF Size: 76.01 MB
Page 268 of 2199
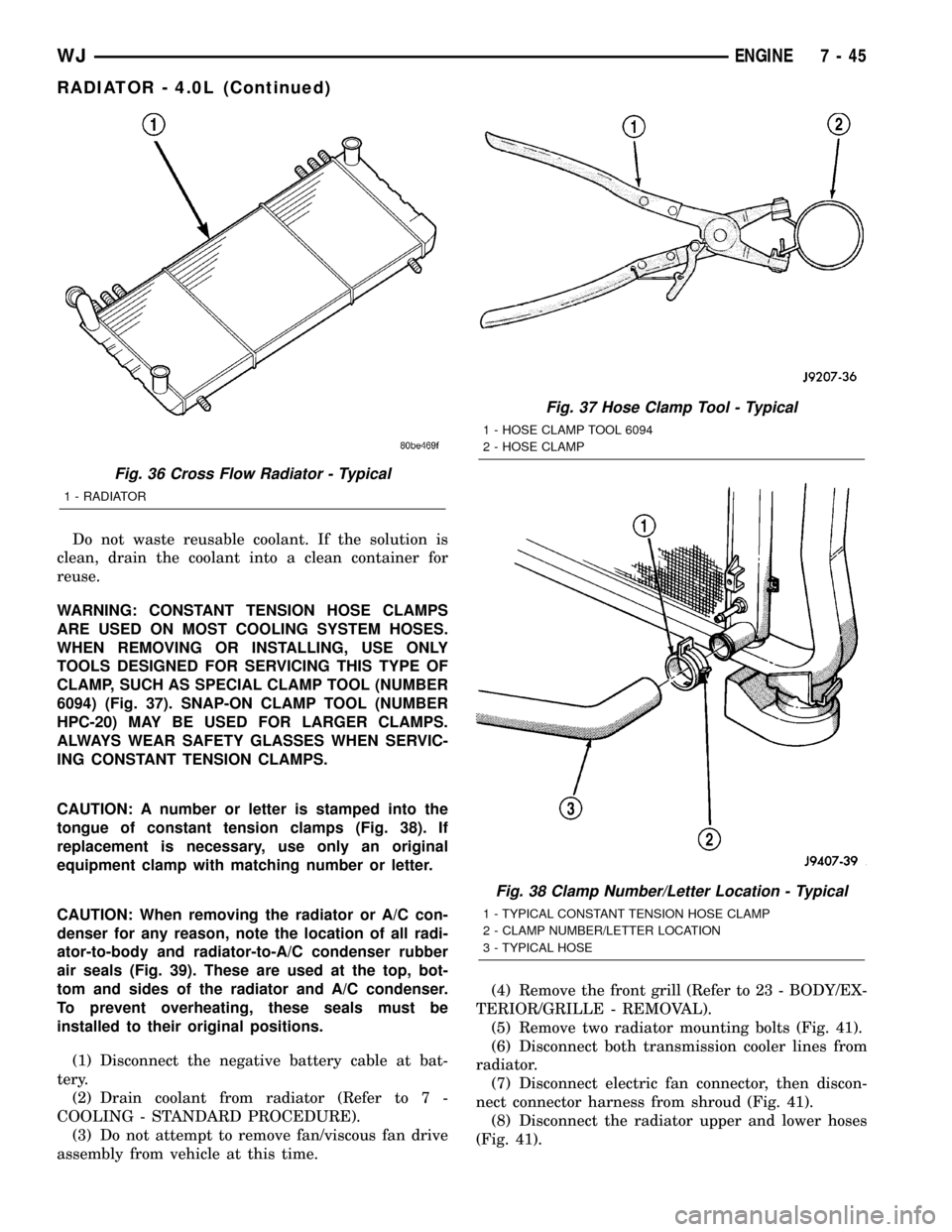
Do not waste reusable coolant. If the solution is
clean, drain the coolant into a clean container for
reuse.
WARNING: CONSTANT TENSION HOSE CLAMPS
ARE USED ON MOST COOLING SYSTEM HOSES.
WHEN REMOVING OR INSTALLING, USE ONLY
TOOLS DESIGNED FOR SERVICING THIS TYPE OF
CLAMP, SUCH AS SPECIAL CLAMP TOOL (NUMBER
6094) (Fig. 37). SNAP-ON CLAMP TOOL (NUMBER
HPC-20) MAY BE USED FOR LARGER CLAMPS.
ALWAYS WEAR SAFETY GLASSES WHEN SERVIC-
ING CONSTANT TENSION CLAMPS.
CAUTION: A number or letter is stamped into the
tongue of constant tension clamps (Fig. 38). If
replacement is necessary, use only an original
equipment clamp with matching number or letter.
CAUTION: When removing the radiator or A/C con-
denser for any reason, note the location of all radi-
ator-to-body and radiator-to-A/C condenser rubber
air seals (Fig. 39). These are used at the top, bot-
tom and sides of the radiator and A/C condenser.
To prevent overheating, these seals must be
installed to their original positions.
(1) Disconnect the negative battery cable at bat-
tery.
(2) Drain coolant from radiator (Refer to 7 -
COOLING - STANDARD PROCEDURE).
(3) Do not attempt to remove fan/viscous fan drive
assembly from vehicle at this time.(4) Remove the front grill (Refer to 23 - BODY/EX-
TERIOR/GRILLE - REMOVAL).
(5) Remove two radiator mounting bolts (Fig. 41).
(6) Disconnect both transmission cooler lines from
radiator.
(7) Disconnect electric fan connector, then discon-
nect connector harness from shroud (Fig. 41).
(8) Disconnect the radiator upper and lower hoses
(Fig. 41).
Fig. 36 Cross Flow Radiator - Typical
1 - RADIATOR
Fig. 37 Hose Clamp Tool - Typical
1 - HOSE CLAMP TOOL 6094
2 - HOSE CLAMP
Fig. 38 Clamp Number/Letter Location - Typical
1 - TYPICAL CONSTANT TENSION HOSE CLAMP
2 - CLAMP NUMBER/LETTER LOCATION
3 - TYPICAL HOSE
WJENGINE 7 - 45
RADIATOR - 4.0L (Continued)
Page 269 of 2199
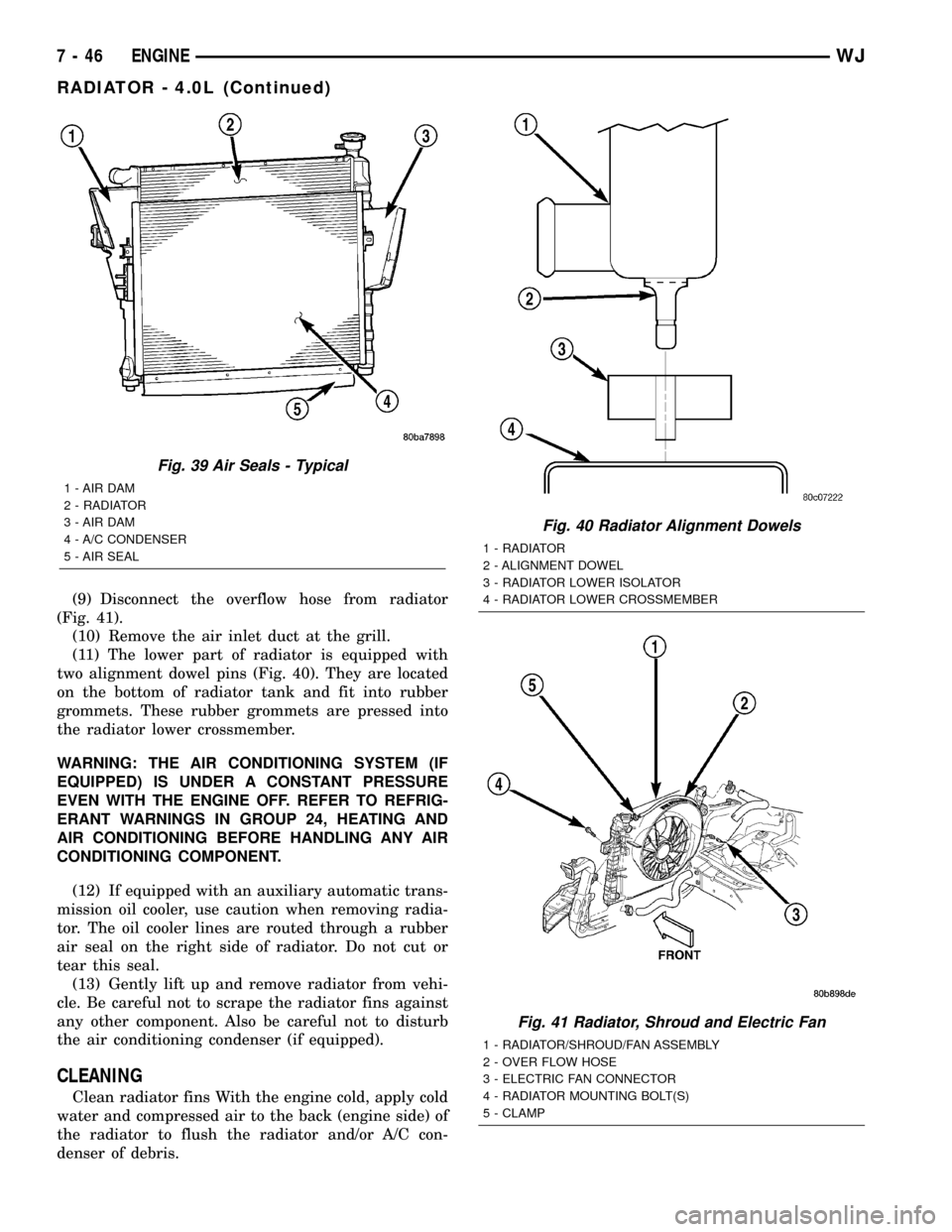
(9) Disconnect the overflow hose from radiator
(Fig. 41).
(10) Remove the air inlet duct at the grill.
(11) The lower part of radiator is equipped with
two alignment dowel pins (Fig. 40). They are located
on the bottom of radiator tank and fit into rubber
grommets. These rubber grommets are pressed into
the radiator lower crossmember.
WARNING: THE AIR CONDITIONING SYSTEM (IF
EQUIPPED) IS UNDER A CONSTANT PRESSURE
EVEN WITH THE ENGINE OFF. REFER TO REFRIG-
ERANT WARNINGS IN GROUP 24, HEATING AND
AIR CONDITIONING BEFORE HANDLING ANY AIR
CONDITIONING COMPONENT.
(12) If equipped with an auxiliary automatic trans-
mission oil cooler, use caution when removing radia-
tor. The oil cooler lines are routed through a rubber
air seal on the right side of radiator. Do not cut or
tear this seal.
(13) Gently lift up and remove radiator from vehi-
cle. Be careful not to scrape the radiator fins against
any other component. Also be careful not to disturb
the air conditioning condenser (if equipped).
CLEANING
Clean radiator fins With the engine cold, apply cold
water and compressed air to the back (engine side) of
the radiator to flush the radiator and/or A/C con-
denser of debris.
Fig. 39 Air Seals - Typical
1 - AIR DAM
2 - RADIATOR
3 - AIR DAM
4 - A/C CONDENSER
5 - AIR SEAL
Fig. 40 Radiator Alignment Dowels
1 - RADIATOR
2 - ALIGNMENT DOWEL
3 - RADIATOR LOWER ISOLATOR
4 - RADIATOR LOWER CROSSMEMBER
Fig. 41 Radiator, Shroud and Electric Fan
1 - RADIATOR/SHROUD/FAN ASSEMBLY
2 - OVER FLOW HOSE
3 - ELECTRIC FAN CONNECTOR
4 - RADIATOR MOUNTING BOLT(S)
5 - CLAMP
7 - 46 ENGINEWJ
RADIATOR - 4.0L (Continued)
Page 270 of 2199
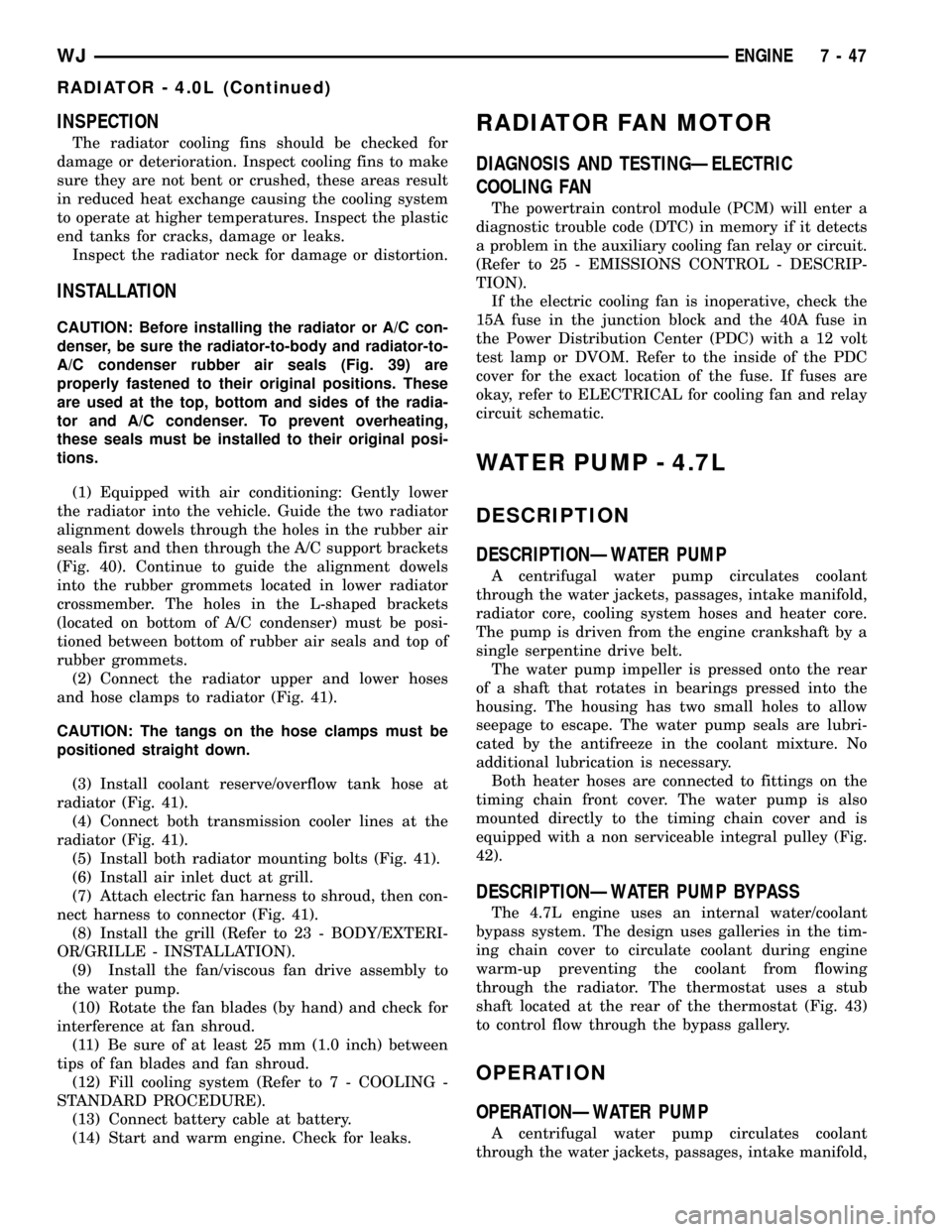
INSPECTION
The radiator cooling fins should be checked for
damage or deterioration. Inspect cooling fins to make
sure they are not bent or crushed, these areas result
in reduced heat exchange causing the cooling system
to operate at higher temperatures. Inspect the plastic
end tanks for cracks, damage or leaks.
Inspect the radiator neck for damage or distortion.
INSTALLATION
CAUTION: Before installing the radiator or A/C con-
denser, be sure the radiator-to-body and radiator-to-
A/C condenser rubber air seals (Fig. 39) are
properly fastened to their original positions. These
are used at the top, bottom and sides of the radia-
tor and A/C condenser. To prevent overheating,
these seals must be installed to their original posi-
tions.
(1) Equipped with air conditioning: Gently lower
the radiator into the vehicle. Guide the two radiator
alignment dowels through the holes in the rubber air
seals first and then through the A/C support brackets
(Fig. 40). Continue to guide the alignment dowels
into the rubber grommets located in lower radiator
crossmember. The holes in the L-shaped brackets
(located on bottom of A/C condenser) must be posi-
tioned between bottom of rubber air seals and top of
rubber grommets.
(2) Connect the radiator upper and lower hoses
and hose clamps to radiator (Fig. 41).
CAUTION: The tangs on the hose clamps must be
positioned straight down.
(3) Install coolant reserve/overflow tank hose at
radiator (Fig. 41).
(4) Connect both transmission cooler lines at the
radiator (Fig. 41).
(5) Install both radiator mounting bolts (Fig. 41).
(6) Install air inlet duct at grill.
(7) Attach electric fan harness to shroud, then con-
nect harness to connector (Fig. 41).
(8) Install the grill (Refer to 23 - BODY/EXTERI-
OR/GRILLE - INSTALLATION).
(9) Install the fan/viscous fan drive assembly to
the water pump.
(10) Rotate the fan blades (by hand) and check for
interference at fan shroud.
(11) Be sure of at least 25 mm (1.0 inch) between
tips of fan blades and fan shroud.
(12) Fill cooling system (Refer to 7 - COOLING -
STANDARD PROCEDURE).
(13) Connect battery cable at battery.
(14) Start and warm engine. Check for leaks.
RADIATOR FAN MOTOR
DIAGNOSIS AND TESTINGÐELECTRIC
COOLING FAN
The powertrain control module (PCM) will enter a
diagnostic trouble code (DTC) in memory if it detects
a problem in the auxiliary cooling fan relay or circuit.
(Refer to 25 - EMISSIONS CONTROL - DESCRIP-
TION).
If the electric cooling fan is inoperative, check the
15A fuse in the junction block and the 40A fuse in
the Power Distribution Center (PDC) with a 12 volt
test lamp or DVOM. Refer to the inside of the PDC
cover for the exact location of the fuse. If fuses are
okay, refer to ELECTRICAL for cooling fan and relay
circuit schematic.
WATER PUMP - 4.7L
DESCRIPTION
DESCRIPTIONÐWATER PUMP
A centrifugal water pump circulates coolant
through the water jackets, passages, intake manifold,
radiator core, cooling system hoses and heater core.
The pump is driven from the engine crankshaft by a
single serpentine drive belt.
The water pump impeller is pressed onto the rear
of a shaft that rotates in bearings pressed into the
housing. The housing has two small holes to allow
seepage to escape. The water pump seals are lubri-
cated by the antifreeze in the coolant mixture. No
additional lubrication is necessary.
Both heater hoses are connected to fittings on the
timing chain front cover. The water pump is also
mounted directly to the timing chain cover and is
equipped with a non serviceable integral pulley (Fig.
42).
DESCRIPTIONÐWATER PUMP BYPASS
The 4.7L engine uses an internal water/coolant
bypass system. The design uses galleries in the tim-
ing chain cover to circulate coolant during engine
warm-up preventing the coolant from flowing
through the radiator. The thermostat uses a stub
shaft located at the rear of the thermostat (Fig. 43)
to control flow through the bypass gallery.
OPERATION
OPERATIONÐWATER PUMP
A centrifugal water pump circulates coolant
through the water jackets, passages, intake manifold,
WJENGINE 7 - 47
RADIATOR - 4.0L (Continued)
Page 273 of 2199
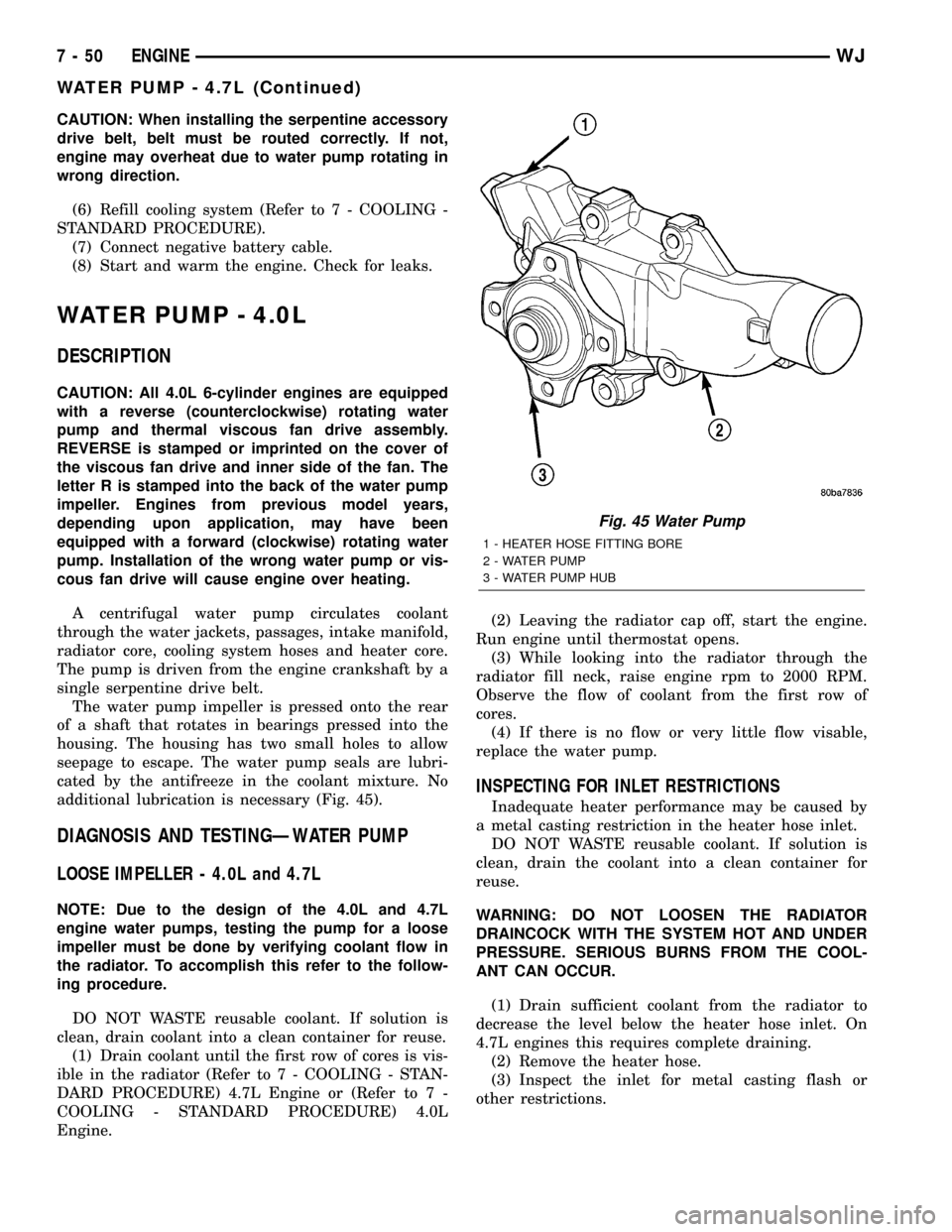
CAUTION: When installing the serpentine accessory
drive belt, belt must be routed correctly. If not,
engine may overheat due to water pump rotating in
wrong direction.
(6) Refill cooling system (Refer to 7 - COOLING -
STANDARD PROCEDURE).
(7) Connect negative battery cable.
(8) Start and warm the engine. Check for leaks.
WATER PUMP - 4.0L
DESCRIPTION
CAUTION: All 4.0L 6-cylinder engines are equipped
with a reverse (counterclockwise) rotating water
pump and thermal viscous fan drive assembly.
REVERSE is stamped or imprinted on the cover of
the viscous fan drive and inner side of the fan. The
letter R is stamped into the back of the water pump
impeller. Engines from previous model years,
depending upon application, may have been
equipped with a forward (clockwise) rotating water
pump. Installation of the wrong water pump or vis-
cous fan drive will cause engine over heating.
A centrifugal water pump circulates coolant
through the water jackets, passages, intake manifold,
radiator core, cooling system hoses and heater core.
The pump is driven from the engine crankshaft by a
single serpentine drive belt.
The water pump impeller is pressed onto the rear
of a shaft that rotates in bearings pressed into the
housing. The housing has two small holes to allow
seepage to escape. The water pump seals are lubri-
cated by the antifreeze in the coolant mixture. No
additional lubrication is necessary (Fig. 45).
DIAGNOSIS AND TESTINGÐWATER PUMP
LOOSE IMPELLER - 4.0L and 4.7L
NOTE: Due to the design of the 4.0L and 4.7L
engine water pumps, testing the pump for a loose
impeller must be done by verifying coolant flow in
the radiator. To accomplish this refer to the follow-
ing procedure.
DO NOT WASTE reusable coolant. If solution is
clean, drain coolant into a clean container for reuse.
(1) Drain coolant until the first row of cores is vis-
ible in the radiator (Refer to 7 - COOLING - STAN-
DARD PROCEDURE) 4.7L Engine or (Refer to 7 -
COOLING - STANDARD PROCEDURE) 4.0L
Engine.(2) Leaving the radiator cap off, start the engine.
Run engine until thermostat opens.
(3) While looking into the radiator through the
radiator fill neck, raise engine rpm to 2000 RPM.
Observe the flow of coolant from the first row of
cores.
(4) If there is no flow or very little flow visable,
replace the water pump.
INSPECTING FOR INLET RESTRICTIONS
Inadequate heater performance may be caused by
a metal casting restriction in the heater hose inlet.
DO NOT WASTE reusable coolant. If solution is
clean, drain the coolant into a clean container for
reuse.
WARNING: DO NOT LOOSEN THE RADIATOR
DRAINCOCK WITH THE SYSTEM HOT AND UNDER
PRESSURE. SERIOUS BURNS FROM THE COOL-
ANT CAN OCCUR.
(1) Drain sufficient coolant from the radiator to
decrease the level below the heater hose inlet. On
4.7L engines this requires complete draining.
(2) Remove the heater hose.
(3) Inspect the inlet for metal casting flash or
other restrictions.
Fig. 45 Water Pump
1 - HEATER HOSE FITTING BORE
2 - WATER PUMP
3 - WATER PUMP HUB
7 - 50 ENGINEWJ
WATER PUMP - 4.7L (Continued)
Page 372 of 2199
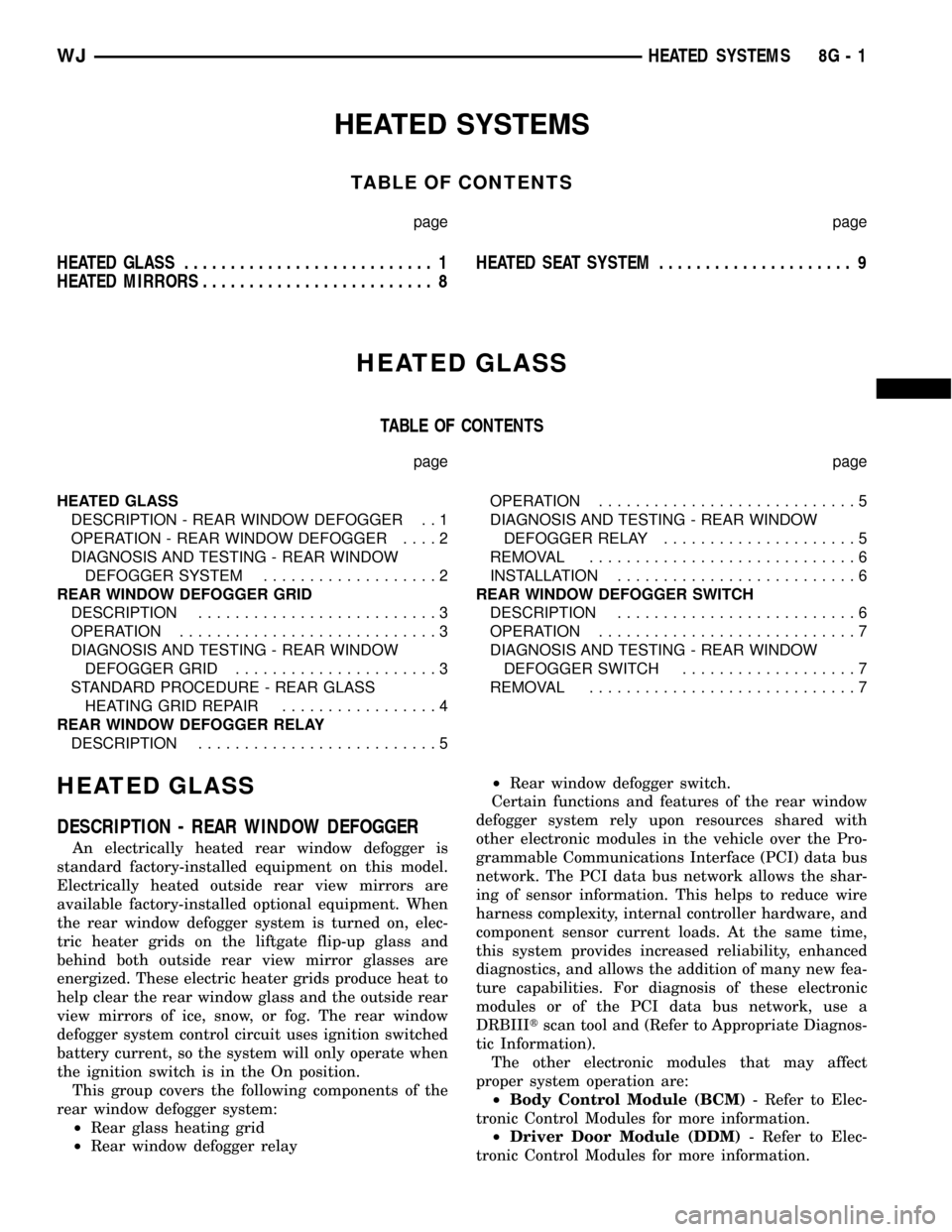
HEATED SYSTEMS
TABLE OF CONTENTS
page page
HEATED GLASS........................... 1
HEATED MIRRORS......................... 8HEATED SEAT SYSTEM..................... 9
HEATED GLASS
TABLE OF CONTENTS
page page
HEATED GLASS
DESCRIPTION - REAR WINDOW DEFOGGER . . 1
OPERATION - REAR WINDOW DEFOGGER....2
DIAGNOSIS AND TESTING - REAR WINDOW
DEFOGGER SYSTEM...................2
REAR WINDOW DEFOGGER GRID
DESCRIPTION..........................3
OPERATION............................3
DIAGNOSIS AND TESTING - REAR WINDOW
DEFOGGER GRID......................3
STANDARD PROCEDURE - REAR GLASS
HEATING GRID REPAIR.................4
REAR WINDOW DEFOGGER RELAY
DESCRIPTION..........................5OPERATION............................5
DIAGNOSIS AND TESTING - REAR WINDOW
DEFOGGER RELAY.....................5
REMOVAL.............................6
INSTALLATION..........................6
REAR WINDOW DEFOGGER SWITCH
DESCRIPTION..........................6
OPERATION............................7
DIAGNOSIS AND TESTING - REAR WINDOW
DEFOGGER SWITCH...................7
REMOVAL.............................7
HEATED GLASS
DESCRIPTION - REAR WINDOW DEFOGGER
An electrically heated rear window defogger is
standard factory-installed equipment on this model.
Electrically heated outside rear view mirrors are
available factory-installed optional equipment. When
the rear window defogger system is turned on, elec-
tric heater grids on the liftgate flip-up glass and
behind both outside rear view mirror glasses are
energized. These electric heater grids produce heat to
help clear the rear window glass and the outside rear
view mirrors of ice, snow, or fog. The rear window
defogger system control circuit uses ignition switched
battery current, so the system will only operate when
the ignition switch is in the On position.
This group covers the following components of the
rear window defogger system:
²Rear glass heating grid
²Rear window defogger relay²Rear window defogger switch.
Certain functions and features of the rear window
defogger system rely upon resources shared with
other electronic modules in the vehicle over the Pro-
grammable Communications Interface (PCI) data bus
network. The PCI data bus network allows the shar-
ing of sensor information. This helps to reduce wire
harness complexity, internal controller hardware, and
component sensor current loads. At the same time,
this system provides increased reliability, enhanced
diagnostics, and allows the addition of many new fea-
ture capabilities. For diagnosis of these electronic
modules or of the PCI data bus network, use a
DRBIIItscan tool and (Refer to Appropriate Diagnos-
tic Information).
The other electronic modules that may affect
proper system operation are:
²Body Control Module (BCM)- Refer to Elec-
tronic Control Modules for more information.
²Driver Door Module (DDM)- Refer to Elec-
tronic Control Modules for more information.
WJHEATED SYSTEMS 8G - 1
Page 373 of 2199
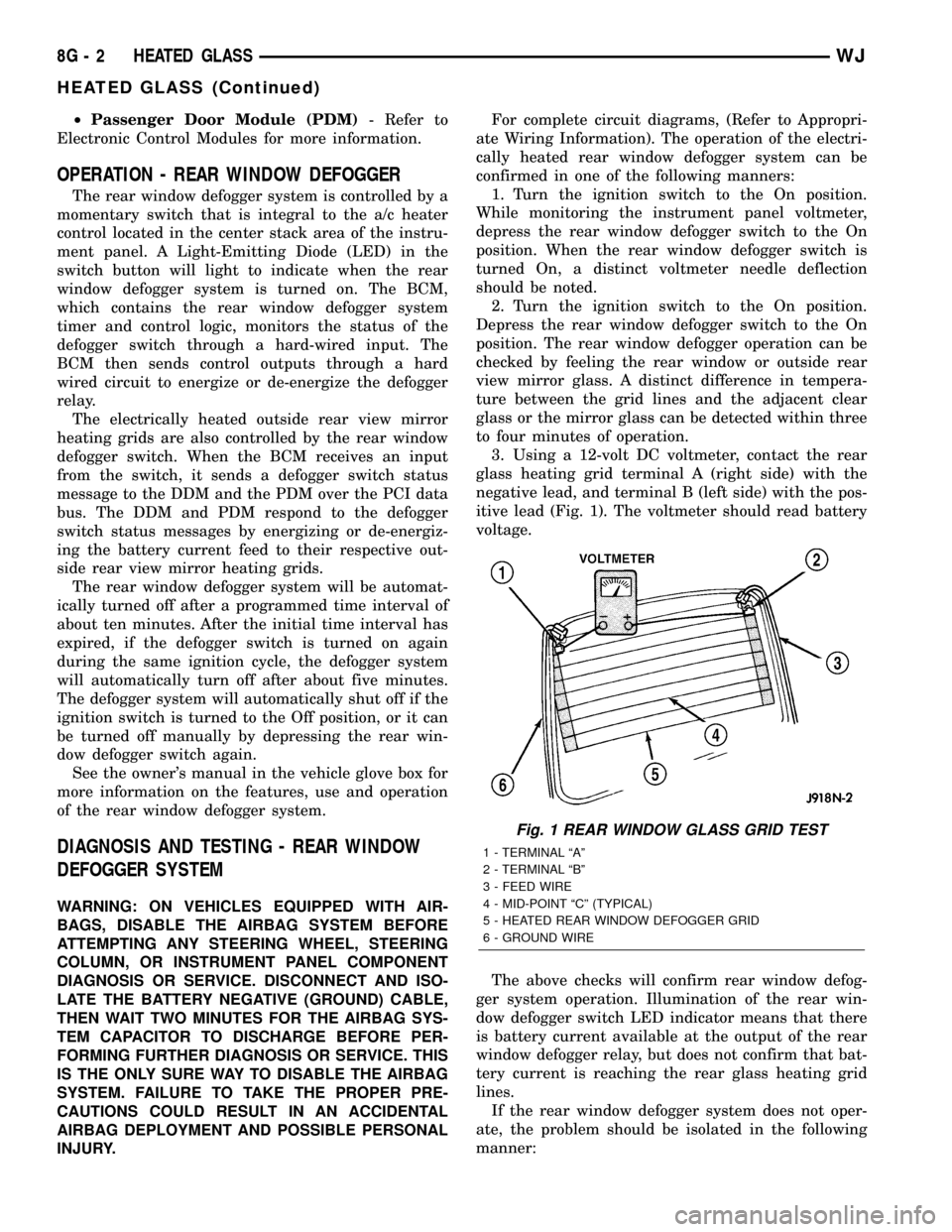
²Passenger Door Module (PDM)- Refer to
Electronic Control Modules for more information.
OPERATION - REAR WINDOW DEFOGGER
The rear window defogger system is controlled by a
momentary switch that is integral to the a/c heater
control located in the center stack area of the instru-
ment panel. A Light-Emitting Diode (LED) in the
switch button will light to indicate when the rear
window defogger system is turned on. The BCM,
which contains the rear window defogger system
timer and control logic, monitors the status of the
defogger switch through a hard-wired input. The
BCM then sends control outputs through a hard
wired circuit to energize or de-energize the defogger
relay.
The electrically heated outside rear view mirror
heating grids are also controlled by the rear window
defogger switch. When the BCM receives an input
from the switch, it sends a defogger switch status
message to the DDM and the PDM over the PCI data
bus. The DDM and PDM respond to the defogger
switch status messages by energizing or de-energiz-
ing the battery current feed to their respective out-
side rear view mirror heating grids.
The rear window defogger system will be automat-
ically turned off after a programmed time interval of
about ten minutes. After the initial time interval has
expired, if the defogger switch is turned on again
during the same ignition cycle, the defogger system
will automatically turn off after about five minutes.
The defogger system will automatically shut off if the
ignition switch is turned to the Off position, or it can
be turned off manually by depressing the rear win-
dow defogger switch again.
See the owner's manual in the vehicle glove box for
more information on the features, use and operation
of the rear window defogger system.
DIAGNOSIS AND TESTING - REAR WINDOW
DEFOGGER SYSTEM
WARNING: ON VEHICLES EQUIPPED WITH AIR-
BAGS, DISABLE THE AIRBAG SYSTEM BEFORE
ATTEMPTING ANY STEERING WHEEL, STEERING
COLUMN, OR INSTRUMENT PANEL COMPONENT
DIAGNOSIS OR SERVICE. DISCONNECT AND ISO-
LATE THE BATTERY NEGATIVE (GROUND) CABLE,
THEN WAIT TWO MINUTES FOR THE AIRBAG SYS-
TEM CAPACITOR TO DISCHARGE BEFORE PER-
FORMING FURTHER DIAGNOSIS OR SERVICE. THIS
IS THE ONLY SURE WAY TO DISABLE THE AIRBAG
SYSTEM. FAILURE TO TAKE THE PROPER PRE-
CAUTIONS COULD RESULT IN AN ACCIDENTAL
AIRBAG DEPLOYMENT AND POSSIBLE PERSONAL
INJURY.For complete circuit diagrams, (Refer to Appropri-
ate Wiring Information). The operation of the electri-
cally heated rear window defogger system can be
confirmed in one of the following manners:
1. Turn the ignition switch to the On position.
While monitoring the instrument panel voltmeter,
depress the rear window defogger switch to the On
position. When the rear window defogger switch is
turned On, a distinct voltmeter needle deflection
should be noted.
2. Turn the ignition switch to the On position.
Depress the rear window defogger switch to the On
position. The rear window defogger operation can be
checked by feeling the rear window or outside rear
view mirror glass. A distinct difference in tempera-
ture between the grid lines and the adjacent clear
glass or the mirror glass can be detected within three
to four minutes of operation.
3. Using a 12-volt DC voltmeter, contact the rear
glass heating grid terminal A (right side) with the
negative lead, and terminal B (left side) with the pos-
itive lead (Fig. 1). The voltmeter should read battery
voltage.
The above checks will confirm rear window defog-
ger system operation. Illumination of the rear win-
dow defogger switch LED indicator means that there
is battery current available at the output of the rear
window defogger relay, but does not confirm that bat-
tery current is reaching the rear glass heating grid
lines.
If the rear window defogger system does not oper-
ate, the problem should be isolated in the following
manner:
Fig. 1 REAR WINDOW GLASS GRID TEST
1 - TERMINAL ªAº
2 - TERMINAL ªBº
3 - FEED WIRE
4 - MID-POINT ªCº (TYPICAL)
5 - HEATED REAR WINDOW DEFOGGER GRID
6 - GROUND WIRE
8G - 2 HEATED GLASSWJ
HEATED GLASS (Continued)
Page 374 of 2199
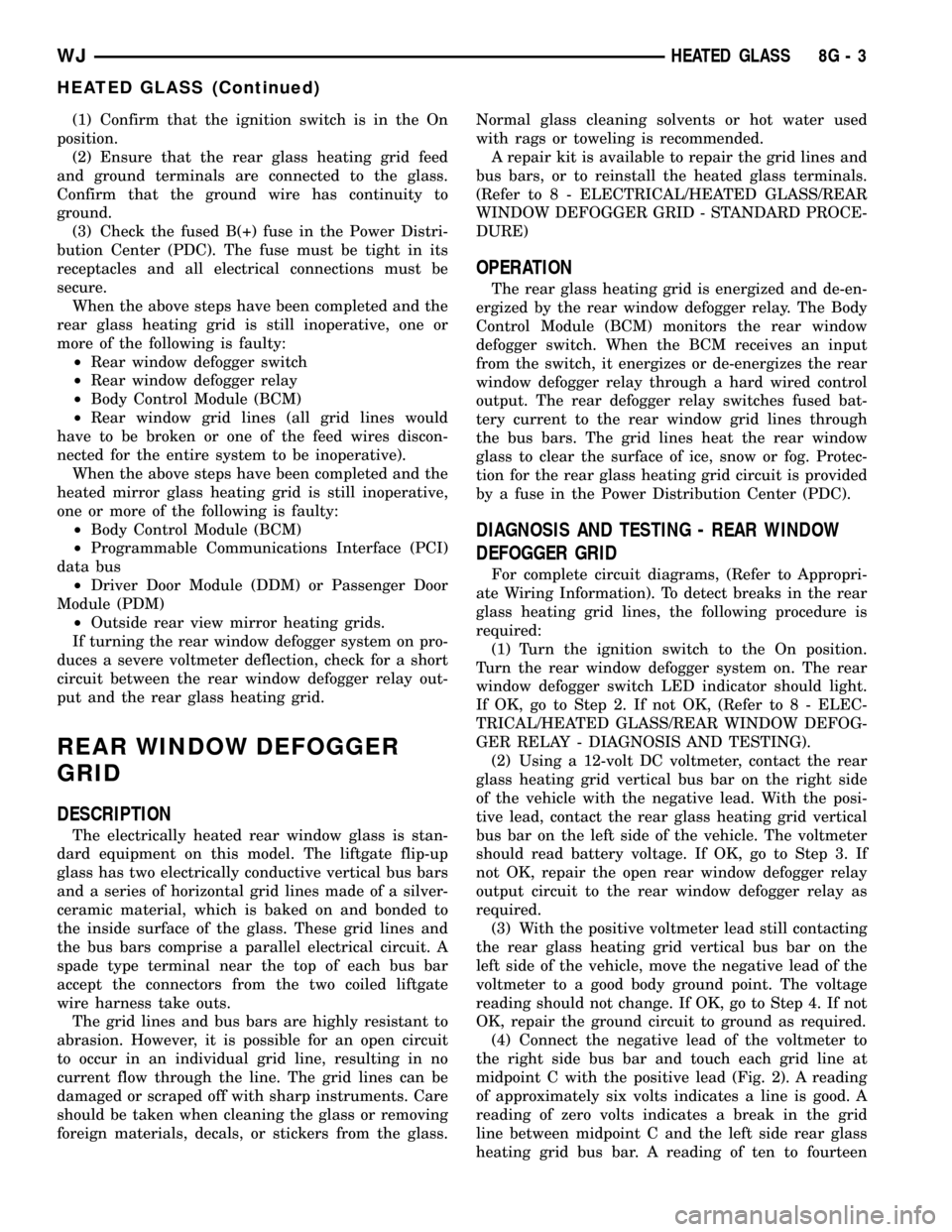
(1) Confirm that the ignition switch is in the On
position.
(2) Ensure that the rear glass heating grid feed
and ground terminals are connected to the glass.
Confirm that the ground wire has continuity to
ground.
(3) Check the fused B(+) fuse in the Power Distri-
bution Center (PDC). The fuse must be tight in its
receptacles and all electrical connections must be
secure.
When the above steps have been completed and the
rear glass heating grid is still inoperative, one or
more of the following is faulty:
²Rear window defogger switch
²Rear window defogger relay
²Body Control Module (BCM)
²Rear window grid lines (all grid lines would
have to be broken or one of the feed wires discon-
nected for the entire system to be inoperative).
When the above steps have been completed and the
heated mirror glass heating grid is still inoperative,
one or more of the following is faulty:
²Body Control Module (BCM)
²Programmable Communications Interface (PCI)
data bus
²Driver Door Module (DDM) or Passenger Door
Module (PDM)
²Outside rear view mirror heating grids.
If turning the rear window defogger system on pro-
duces a severe voltmeter deflection, check for a short
circuit between the rear window defogger relay out-
put and the rear glass heating grid.
REAR WINDOW DEFOGGER
GRID
DESCRIPTION
The electrically heated rear window glass is stan-
dard equipment on this model. The liftgate flip-up
glass has two electrically conductive vertical bus bars
and a series of horizontal grid lines made of a silver-
ceramic material, which is baked on and bonded to
the inside surface of the glass. These grid lines and
the bus bars comprise a parallel electrical circuit. A
spade type terminal near the top of each bus bar
accept the connectors from the two coiled liftgate
wire harness take outs.
The grid lines and bus bars are highly resistant to
abrasion. However, it is possible for an open circuit
to occur in an individual grid line, resulting in no
current flow through the line. The grid lines can be
damaged or scraped off with sharp instruments. Care
should be taken when cleaning the glass or removing
foreign materials, decals, or stickers from the glass.Normal glass cleaning solvents or hot water used
with rags or toweling is recommended.
A repair kit is available to repair the grid lines and
bus bars, or to reinstall the heated glass terminals.
(Refer to 8 - ELECTRICAL/HEATED GLASS/REAR
WINDOW DEFOGGER GRID - STANDARD PROCE-
DURE)
OPERATION
The rear glass heating grid is energized and de-en-
ergized by the rear window defogger relay. The Body
Control Module (BCM) monitors the rear window
defogger switch. When the BCM receives an input
from the switch, it energizes or de-energizes the rear
window defogger relay through a hard wired control
output. The rear defogger relay switches fused bat-
tery current to the rear window grid lines through
the bus bars. The grid lines heat the rear window
glass to clear the surface of ice, snow or fog. Protec-
tion for the rear glass heating grid circuit is provided
by a fuse in the Power Distribution Center (PDC).
DIAGNOSIS AND TESTING - REAR WINDOW
DEFOGGER GRID
For complete circuit diagrams, (Refer to Appropri-
ate Wiring Information). To detect breaks in the rear
glass heating grid lines, the following procedure is
required:
(1) Turn the ignition switch to the On position.
Turn the rear window defogger system on. The rear
window defogger switch LED indicator should light.
If OK, go to Step 2. If not OK, (Refer to 8 - ELEC-
TRICAL/HEATED GLASS/REAR WINDOW DEFOG-
GER RELAY - DIAGNOSIS AND TESTING).
(2) Using a 12-volt DC voltmeter, contact the rear
glass heating grid vertical bus bar on the right side
of the vehicle with the negative lead. With the posi-
tive lead, contact the rear glass heating grid vertical
bus bar on the left side of the vehicle. The voltmeter
should read battery voltage. If OK, go to Step 3. If
not OK, repair the open rear window defogger relay
output circuit to the rear window defogger relay as
required.
(3) With the positive voltmeter lead still contacting
the rear glass heating grid vertical bus bar on the
left side of the vehicle, move the negative lead of the
voltmeter to a good body ground point. The voltage
reading should not change. If OK, go to Step 4. If not
OK, repair the ground circuit to ground as required.
(4) Connect the negative lead of the voltmeter to
the right side bus bar and touch each grid line at
midpoint C with the positive lead (Fig. 2). A reading
of approximately six volts indicates a line is good. A
reading of zero volts indicates a break in the grid
line between midpoint C and the left side rear glass
heating grid bus bar. A reading of ten to fourteen
WJHEATED GLASS 8G - 3
HEATED GLASS (Continued)
Page 375 of 2199
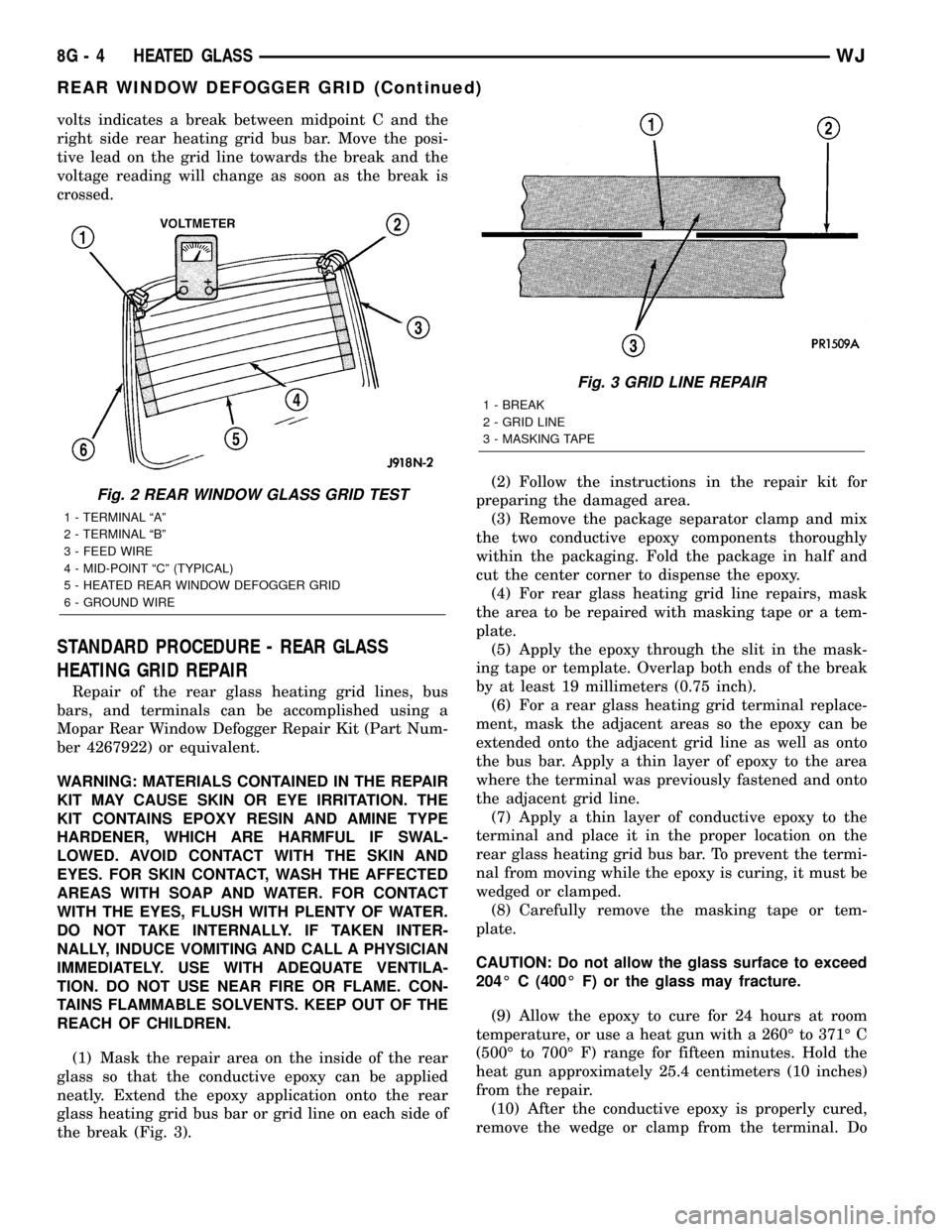
volts indicates a break between midpoint C and the
right side rear heating grid bus bar. Move the posi-
tive lead on the grid line towards the break and the
voltage reading will change as soon as the break is
crossed.
STANDARD PROCEDURE - REAR GLASS
HEATING GRID REPAIR
Repair of the rear glass heating grid lines, bus
bars, and terminals can be accomplished using a
Mopar Rear Window Defogger Repair Kit (Part Num-
ber 4267922) or equivalent.
WARNING: MATERIALS CONTAINED IN THE REPAIR
KIT MAY CAUSE SKIN OR EYE IRRITATION. THE
KIT CONTAINS EPOXY RESIN AND AMINE TYPE
HARDENER, WHICH ARE HARMFUL IF SWAL-
LOWED. AVOID CONTACT WITH THE SKIN AND
EYES. FOR SKIN CONTACT, WASH THE AFFECTED
AREAS WITH SOAP AND WATER. FOR CONTACT
WITH THE EYES, FLUSH WITH PLENTY OF WATER.
DO NOT TAKE INTERNALLY. IF TAKEN INTER-
NALLY, INDUCE VOMITING AND CALL A PHYSICIAN
IMMEDIATELY. USE WITH ADEQUATE VENTILA-
TION. DO NOT USE NEAR FIRE OR FLAME. CON-
TAINS FLAMMABLE SOLVENTS. KEEP OUT OF THE
REACH OF CHILDREN.
(1) Mask the repair area on the inside of the rear
glass so that the conductive epoxy can be applied
neatly. Extend the epoxy application onto the rear
glass heating grid bus bar or grid line on each side of
the break (Fig. 3).(2) Follow the instructions in the repair kit for
preparing the damaged area.
(3) Remove the package separator clamp and mix
the two conductive epoxy components thoroughly
within the packaging. Fold the package in half and
cut the center corner to dispense the epoxy.
(4) For rear glass heating grid line repairs, mask
the area to be repaired with masking tape or a tem-
plate.
(5) Apply the epoxy through the slit in the mask-
ing tape or template. Overlap both ends of the break
by at least 19 millimeters (0.75 inch).
(6) For a rear glass heating grid terminal replace-
ment, mask the adjacent areas so the epoxy can be
extended onto the adjacent grid line as well as onto
the bus bar. Apply a thin layer of epoxy to the area
where the terminal was previously fastened and onto
the adjacent grid line.
(7) Apply a thin layer of conductive epoxy to the
terminal and place it in the proper location on the
rear glass heating grid bus bar. To prevent the termi-
nal from moving while the epoxy is curing, it must be
wedged or clamped.
(8) Carefully remove the masking tape or tem-
plate.
CAUTION: Do not allow the glass surface to exceed
204É C (400É F) or the glass may fracture.
(9) Allow the epoxy to cure for 24 hours at room
temperature, or use a heat gun with a 260É to 371É C
(500É to 700É F) range for fifteen minutes. Hold the
heat gun approximately 25.4 centimeters (10 inches)
from the repair.
(10) After the conductive epoxy is properly cured,
remove the wedge or clamp from the terminal. Do
Fig. 2 REAR WINDOW GLASS GRID TEST
1 - TERMINAL ªAº
2 - TERMINAL ªBº
3 - FEED WIRE
4 - MID-POINT ªCº (TYPICAL)
5 - HEATED REAR WINDOW DEFOGGER GRID
6 - GROUND WIRE
Fig. 3 GRID LINE REPAIR
1 - BREAK
2 - GRID LINE
3 - MASKING TAPE
8G - 4 HEATED GLASSWJ
REAR WINDOW DEFOGGER GRID (Continued)
Page 376 of 2199
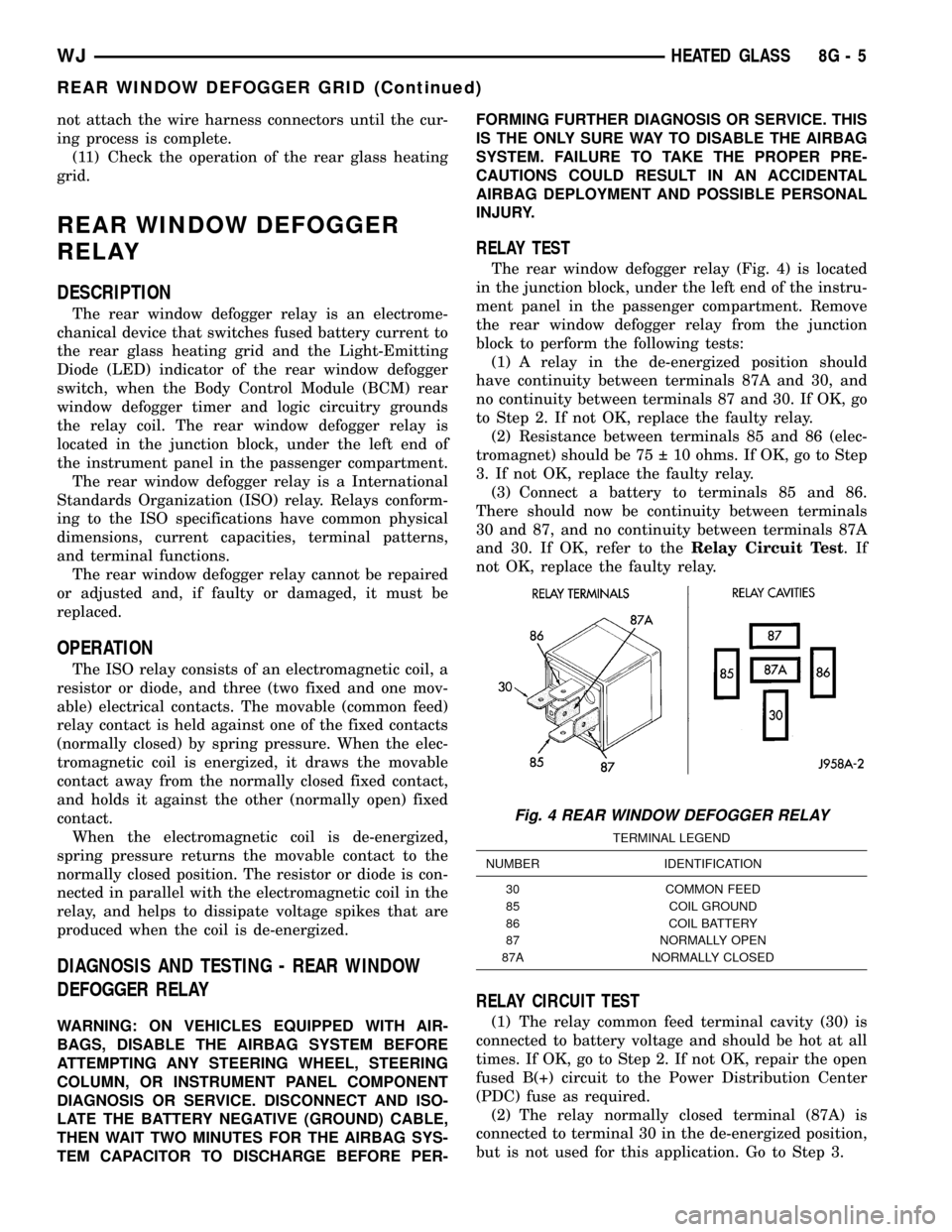
not attach the wire harness connectors until the cur-
ing process is complete.
(11) Check the operation of the rear glass heating
grid.
REAR WINDOW DEFOGGER
RELAY
DESCRIPTION
The rear window defogger relay is an electrome-
chanical device that switches fused battery current to
the rear glass heating grid and the Light-Emitting
Diode (LED) indicator of the rear window defogger
switch, when the Body Control Module (BCM) rear
window defogger timer and logic circuitry grounds
the relay coil. The rear window defogger relay is
located in the junction block, under the left end of
the instrument panel in the passenger compartment.
The rear window defogger relay is a International
Standards Organization (ISO) relay. Relays conform-
ing to the ISO specifications have common physical
dimensions, current capacities, terminal patterns,
and terminal functions.
The rear window defogger relay cannot be repaired
or adjusted and, if faulty or damaged, it must be
replaced.
OPERATION
The ISO relay consists of an electromagnetic coil, a
resistor or diode, and three (two fixed and one mov-
able) electrical contacts. The movable (common feed)
relay contact is held against one of the fixed contacts
(normally closed) by spring pressure. When the elec-
tromagnetic coil is energized, it draws the movable
contact away from the normally closed fixed contact,
and holds it against the other (normally open) fixed
contact.
When the electromagnetic coil is de-energized,
spring pressure returns the movable contact to the
normally closed position. The resistor or diode is con-
nected in parallel with the electromagnetic coil in the
relay, and helps to dissipate voltage spikes that are
produced when the coil is de-energized.
DIAGNOSIS AND TESTING - REAR WINDOW
DEFOGGER RELAY
WARNING: ON VEHICLES EQUIPPED WITH AIR-
BAGS, DISABLE THE AIRBAG SYSTEM BEFORE
ATTEMPTING ANY STEERING WHEEL, STEERING
COLUMN, OR INSTRUMENT PANEL COMPONENT
DIAGNOSIS OR SERVICE. DISCONNECT AND ISO-
LATE THE BATTERY NEGATIVE (GROUND) CABLE,
THEN WAIT TWO MINUTES FOR THE AIRBAG SYS-
TEM CAPACITOR TO DISCHARGE BEFORE PER-FORMING FURTHER DIAGNOSIS OR SERVICE. THIS
IS THE ONLY SURE WAY TO DISABLE THE AIRBAG
SYSTEM. FAILURE TO TAKE THE PROPER PRE-
CAUTIONS COULD RESULT IN AN ACCIDENTAL
AIRBAG DEPLOYMENT AND POSSIBLE PERSONAL
INJURY.
RELAY TEST
The rear window defogger relay (Fig. 4) is located
in the junction block, under the left end of the instru-
ment panel in the passenger compartment. Remove
the rear window defogger relay from the junction
block to perform the following tests:
(1) A relay in the de-energized position should
have continuity between terminals 87A and 30, and
no continuity between terminals 87 and 30. If OK, go
to Step 2. If not OK, replace the faulty relay.
(2) Resistance between terminals 85 and 86 (elec-
tromagnet) should be 75 10 ohms. If OK, go to Step
3. If not OK, replace the faulty relay.
(3) Connect a battery to terminals 85 and 86.
There should now be continuity between terminals
30 and 87, and no continuity between terminals 87A
and 30. If OK, refer to theRelay Circuit Test.If
not OK, replace the faulty relay.
RELAY CIRCUIT TEST
(1) The relay common feed terminal cavity (30) is
connected to battery voltage and should be hot at all
times. If OK, go to Step 2. If not OK, repair the open
fused B(+) circuit to the Power Distribution Center
(PDC) fuse as required.
(2) The relay normally closed terminal (87A) is
connected to terminal 30 in the de-energized position,
but is not used for this application. Go to Step 3.
Fig. 4 REAR WINDOW DEFOGGER RELAY
TERMINAL LEGEND
NUMBER IDENTIFICATION
30 COMMON FEED
85 COIL GROUND
86 COIL BATTERY
87 NORMALLY OPEN
87A NORMALLY CLOSED
WJHEATED GLASS 8G - 5
REAR WINDOW DEFOGGER GRID (Continued)
Page 377 of 2199
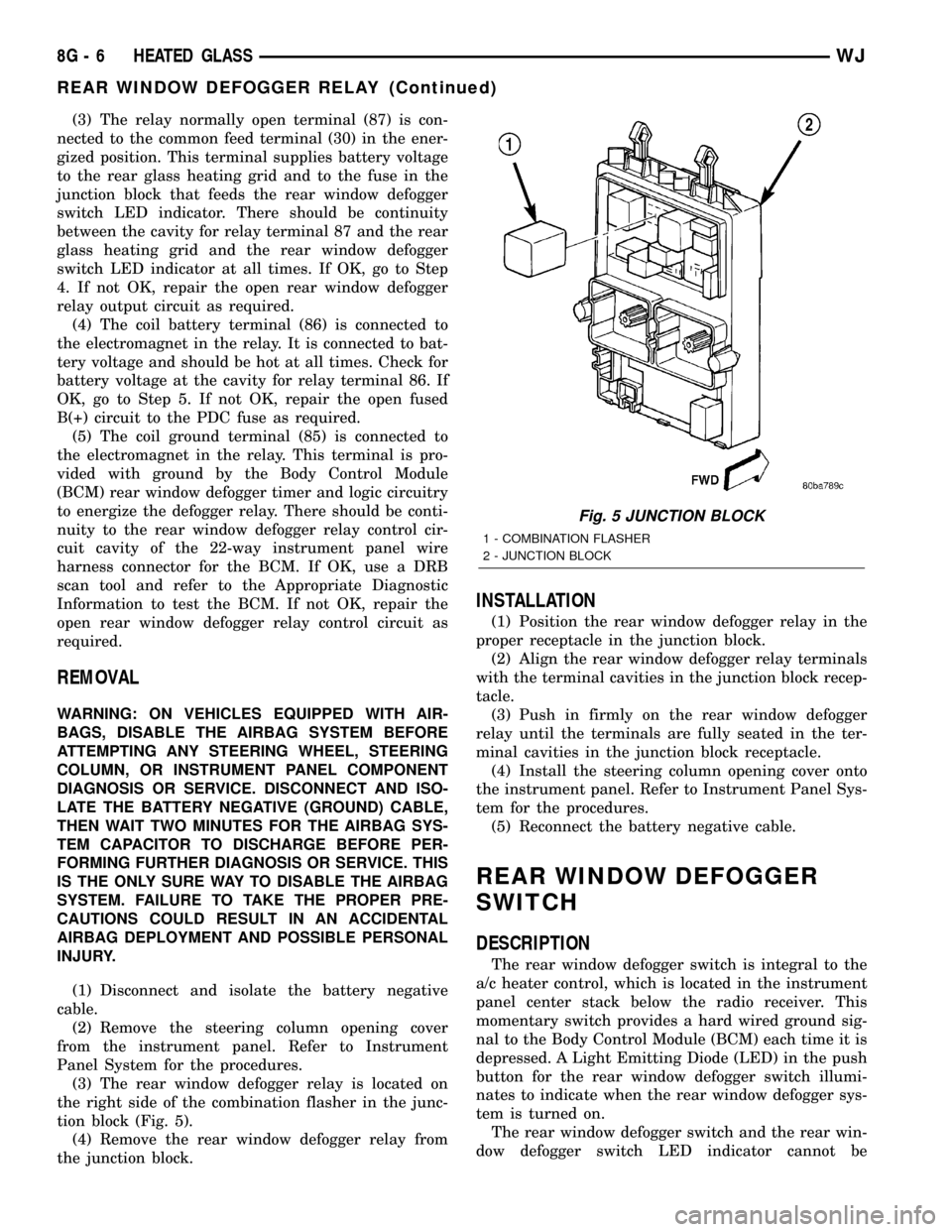
(3) The relay normally open terminal (87) is con-
nected to the common feed terminal (30) in the ener-
gized position. This terminal supplies battery voltage
to the rear glass heating grid and to the fuse in the
junction block that feeds the rear window defogger
switch LED indicator. There should be continuity
between the cavity for relay terminal 87 and the rear
glass heating grid and the rear window defogger
switch LED indicator at all times. If OK, go to Step
4. If not OK, repair the open rear window defogger
relay output circuit as required.
(4) The coil battery terminal (86) is connected to
the electromagnet in the relay. It is connected to bat-
tery voltage and should be hot at all times. Check for
battery voltage at the cavity for relay terminal 86. If
OK, go to Step 5. If not OK, repair the open fused
B(+) circuit to the PDC fuse as required.
(5) The coil ground terminal (85) is connected to
the electromagnet in the relay. This terminal is pro-
vided with ground by the Body Control Module
(BCM) rear window defogger timer and logic circuitry
to energize the defogger relay. There should be conti-
nuity to the rear window defogger relay control cir-
cuit cavity of the 22-way instrument panel wire
harness connector for the BCM. If OK, use a DRB
scan tool and refer to the Appropriate Diagnostic
Information to test the BCM. If not OK, repair the
open rear window defogger relay control circuit as
required.
REMOVAL
WARNING: ON VEHICLES EQUIPPED WITH AIR-
BAGS, DISABLE THE AIRBAG SYSTEM BEFORE
ATTEMPTING ANY STEERING WHEEL, STEERING
COLUMN, OR INSTRUMENT PANEL COMPONENT
DIAGNOSIS OR SERVICE. DISCONNECT AND ISO-
LATE THE BATTERY NEGATIVE (GROUND) CABLE,
THEN WAIT TWO MINUTES FOR THE AIRBAG SYS-
TEM CAPACITOR TO DISCHARGE BEFORE PER-
FORMING FURTHER DIAGNOSIS OR SERVICE. THIS
IS THE ONLY SURE WAY TO DISABLE THE AIRBAG
SYSTEM. FAILURE TO TAKE THE PROPER PRE-
CAUTIONS COULD RESULT IN AN ACCIDENTAL
AIRBAG DEPLOYMENT AND POSSIBLE PERSONAL
INJURY.
(1) Disconnect and isolate the battery negative
cable.
(2) Remove the steering column opening cover
from the instrument panel. Refer to Instrument
Panel System for the procedures.
(3) The rear window defogger relay is located on
the right side of the combination flasher in the junc-
tion block (Fig. 5).
(4) Remove the rear window defogger relay from
the junction block.
INSTALLATION
(1) Position the rear window defogger relay in the
proper receptacle in the junction block.
(2) Align the rear window defogger relay terminals
with the terminal cavities in the junction block recep-
tacle.
(3) Push in firmly on the rear window defogger
relay until the terminals are fully seated in the ter-
minal cavities in the junction block receptacle.
(4) Install the steering column opening cover onto
the instrument panel. Refer to Instrument Panel Sys-
tem for the procedures.
(5) Reconnect the battery negative cable.
REAR WINDOW DEFOGGER
SWITCH
DESCRIPTION
The rear window defogger switch is integral to the
a/c heater control, which is located in the instrument
panel center stack below the radio receiver. This
momentary switch provides a hard wired ground sig-
nal to the Body Control Module (BCM) each time it is
depressed. A Light Emitting Diode (LED) in the push
button for the rear window defogger switch illumi-
nates to indicate when the rear window defogger sys-
tem is turned on.
The rear window defogger switch and the rear win-
dow defogger switch LED indicator cannot be
Fig. 5 JUNCTION BLOCK
1 - COMBINATION FLASHER
2 - JUNCTION BLOCK
8G - 6 HEATED GLASSWJ
REAR WINDOW DEFOGGER RELAY (Continued)