transfer case JEEP GRAND CHEROKEE 2002 WJ / 2.G Owner's Manual
[x] Cancel search | Manufacturer: JEEP, Model Year: 2002, Model line: GRAND CHEROKEE, Model: JEEP GRAND CHEROKEE 2002 WJ / 2.GPages: 2199, PDF Size: 76.01 MB
Page 136 of 2199
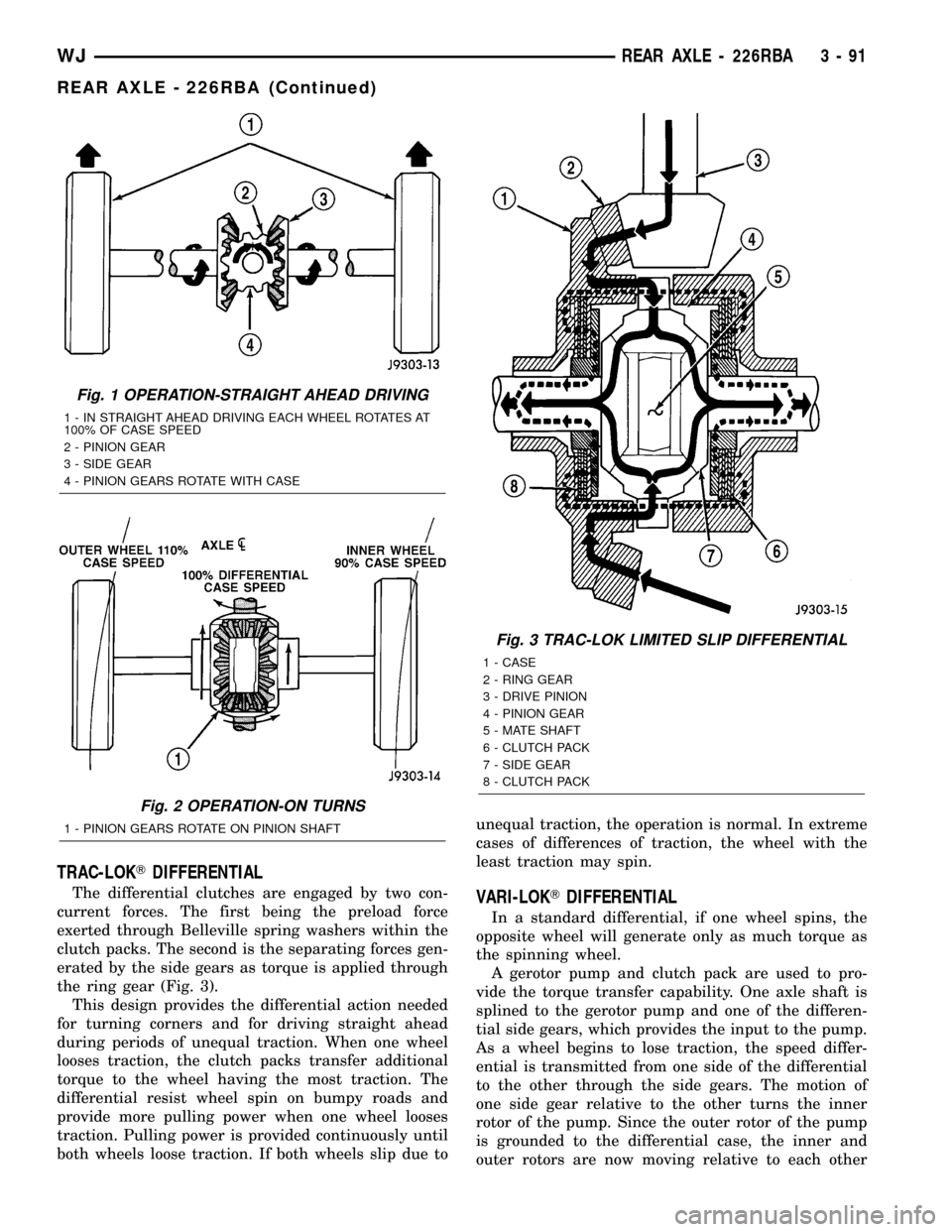
TRAC-LOKTDIFFERENTIAL
The differential clutches are engaged by two con-
current forces. The first being the preload force
exerted through Belleville spring washers within the
clutch packs. The second is the separating forces gen-
erated by the side gears as torque is applied through
the ring gear (Fig. 3).
This design provides the differential action needed
for turning corners and for driving straight ahead
during periods of unequal traction. When one wheel
looses traction, the clutch packs transfer additional
torque to the wheel having the most traction. The
differential resist wheel spin on bumpy roads and
provide more pulling power when one wheel looses
traction. Pulling power is provided continuously until
both wheels loose traction. If both wheels slip due tounequal traction, the operation is normal. In extreme
cases of differences of traction, the wheel with the
least traction may spin.VARI-LOKTDIFFERENTIAL
In a standard differential, if one wheel spins, the
opposite wheel will generate only as much torque as
the spinning wheel.
A gerotor pump and clutch pack are used to pro-
vide the torque transfer capability. One axle shaft is
splined to the gerotor pump and one of the differen-
tial side gears, which provides the input to the pump.
As a wheel begins to lose traction, the speed differ-
ential is transmitted from one side of the differential
to the other through the side gears. The motion of
one side gear relative to the other turns the inner
rotor of the pump. Since the outer rotor of the pump
is grounded to the differential case, the inner and
outer rotors are now moving relative to each other
Fig. 1 OPERATION-STRAIGHT AHEAD DRIVING
1 - IN STRAIGHT AHEAD DRIVING EACH WHEEL ROTATES AT
100% OF CASE SPEED
2 - PINION GEAR
3 - SIDE GEAR
4 - PINION GEARS ROTATE WITH CASE
Fig. 2 OPERATION-ON TURNS
1 - PINION GEARS ROTATE ON PINION SHAFT
Fig. 3 TRAC-LOK LIMITED SLIP DIFFERENTIAL
1 - CASE
2 - RING GEAR
3 - DRIVE PINION
4 - PINION GEAR
5 - MATE SHAFT
6 - CLUTCH PACK
7 - SIDE GEAR
8 - CLUTCH PACK
WJREAR AXLE - 226RBA 3 - 91
REAR AXLE - 226RBA (Continued)
Page 138 of 2199
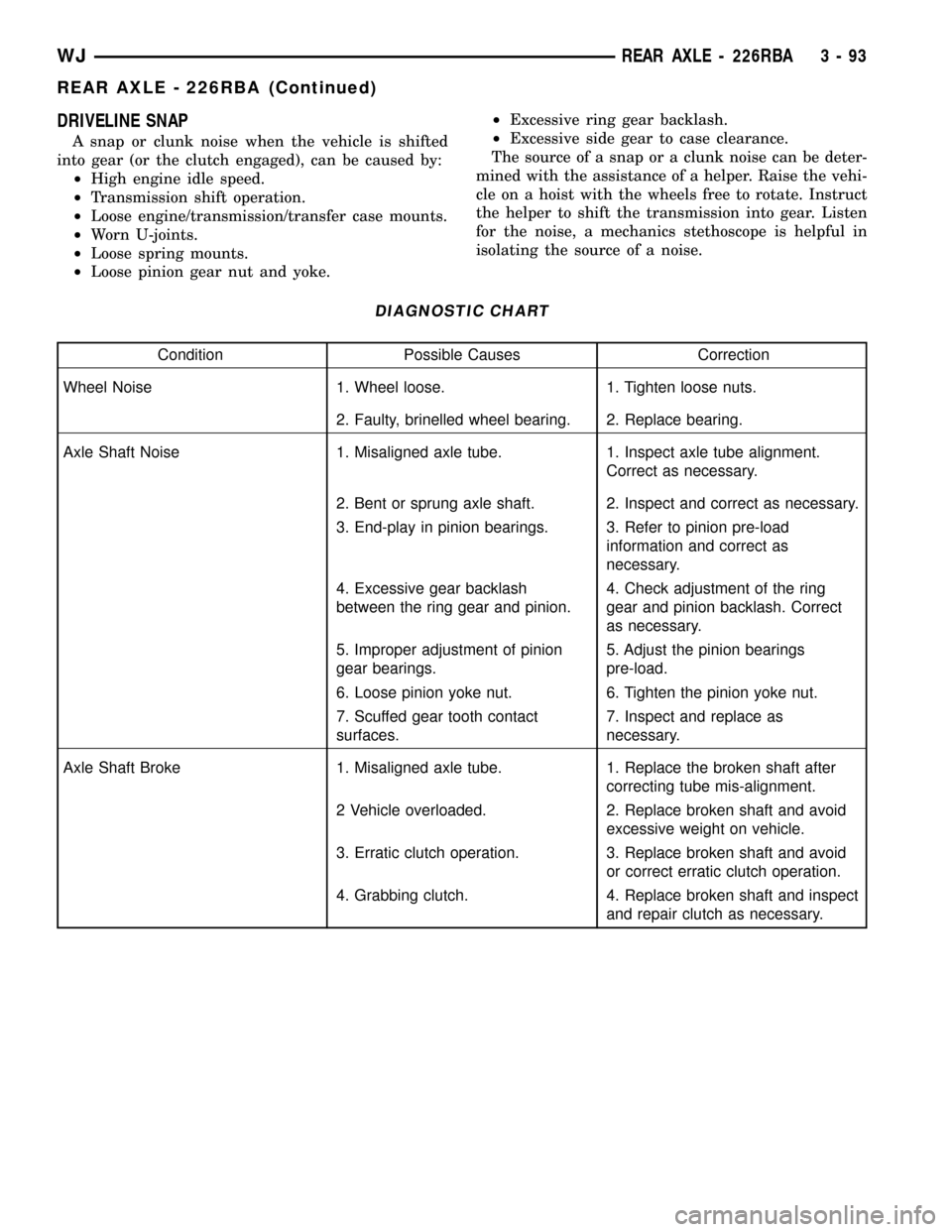
DRIVELINE SNAP
A snap or clunk noise when the vehicle is shifted
into gear (or the clutch engaged), can be caused by:
²High engine idle speed.
²Transmission shift operation.
²Loose engine/transmission/transfer case mounts.
²Worn U-joints.
²Loose spring mounts.
²Loose pinion gear nut and yoke.²Excessive ring gear backlash.
²Excessive side gear to case clearance.
The source of a snap or a clunk noise can be deter-
mined with the assistance of a helper. Raise the vehi-
cle on a hoist with the wheels free to rotate. Instruct
the helper to shift the transmission into gear. Listen
for the noise, a mechanics stethoscope is helpful in
isolating the source of a noise.
DIAGNOSTIC CHART
Condition Possible Causes Correction
Wheel Noise 1. Wheel loose. 1. Tighten loose nuts.
2. Faulty, brinelled wheel bearing. 2. Replace bearing.
Axle Shaft Noise 1. Misaligned axle tube. 1. Inspect axle tube alignment.
Correct as necessary.
2. Bent or sprung axle shaft. 2. Inspect and correct as necessary.
3. End-play in pinion bearings. 3. Refer to pinion pre-load
information and correct as
necessary.
4. Excessive gear backlash
between the ring gear and pinion.4. Check adjustment of the ring
gear and pinion backlash. Correct
as necessary.
5. Improper adjustment of pinion
gear bearings.5. Adjust the pinion bearings
pre-load.
6. Loose pinion yoke nut. 6. Tighten the pinion yoke nut.
7. Scuffed gear tooth contact
surfaces.7. Inspect and replace as
necessary.
Axle Shaft Broke 1. Misaligned axle tube. 1. Replace the broken shaft after
correcting tube mis-alignment.
2 Vehicle overloaded. 2. Replace broken shaft and avoid
excessive weight on vehicle.
3. Erratic clutch operation. 3. Replace broken shaft and avoid
or correct erratic clutch operation.
4. Grabbing clutch. 4. Replace broken shaft and inspect
and repair clutch as necessary.
WJREAR AXLE - 226RBA 3 - 93
REAR AXLE - 226RBA (Continued)
Page 140 of 2199
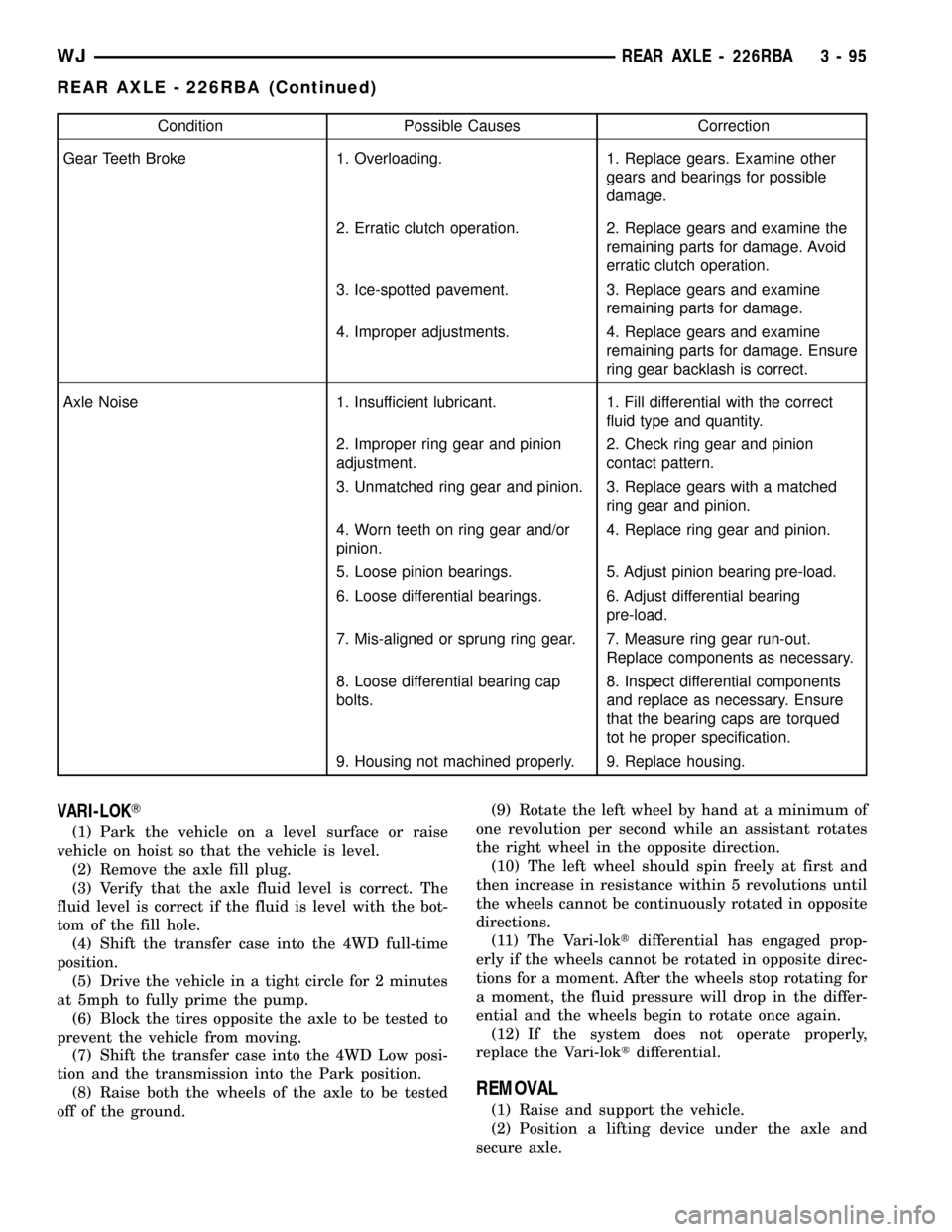
Condition Possible Causes Correction
Gear Teeth Broke 1. Overloading. 1. Replace gears. Examine other
gears and bearings for possible
damage.
2. Erratic clutch operation. 2. Replace gears and examine the
remaining parts for damage. Avoid
erratic clutch operation.
3. Ice-spotted pavement. 3. Replace gears and examine
remaining parts for damage.
4. Improper adjustments. 4. Replace gears and examine
remaining parts for damage. Ensure
ring gear backlash is correct.
Axle Noise 1. Insufficient lubricant. 1. Fill differential with the correct
fluid type and quantity.
2. Improper ring gear and pinion
adjustment.2. Check ring gear and pinion
contact pattern.
3. Unmatched ring gear and pinion. 3. Replace gears with a matched
ring gear and pinion.
4. Worn teeth on ring gear and/or
pinion.4. Replace ring gear and pinion.
5. Loose pinion bearings. 5. Adjust pinion bearing pre-load.
6. Loose differential bearings. 6. Adjust differential bearing
pre-load.
7. Mis-aligned or sprung ring gear. 7. Measure ring gear run-out.
Replace components as necessary.
8. Loose differential bearing cap
bolts.8. Inspect differential components
and replace as necessary. Ensure
that the bearing caps are torqued
tot he proper specification.
9. Housing not machined properly. 9. Replace housing.
VARI-LOKT
(1) Park the vehicle on a level surface or raise
vehicle on hoist so that the vehicle is level.
(2) Remove the axle fill plug.
(3) Verify that the axle fluid level is correct. The
fluid level is correct if the fluid is level with the bot-
tom of the fill hole.
(4) Shift the transfer case into the 4WD full-time
position.
(5) Drive the vehicle in a tight circle for 2 minutes
at 5mph to fully prime the pump.
(6) Block the tires opposite the axle to be tested to
prevent the vehicle from moving.
(7) Shift the transfer case into the 4WD Low posi-
tion and the transmission into the Park position.
(8) Raise both the wheels of the axle to be tested
off of the ground.(9) Rotate the left wheel by hand at a minimum of
one revolution per second while an assistant rotates
the right wheel in the opposite direction.
(10) The left wheel should spin freely at first and
then increase in resistance within 5 revolutions until
the wheels cannot be continuously rotated in opposite
directions.
(11) The Vari-loktdifferential has engaged prop-
erly if the wheels cannot be rotated in opposite direc-
tions for a moment. After the wheels stop rotating for
a moment, the fluid pressure will drop in the differ-
ential and the wheels begin to rotate once again.
(12) If the system does not operate properly,
replace the Vari-loktdifferential.
REMOVAL
(1) Raise and support the vehicle.
(2) Position a lifting device under the axle and
secure axle.
WJREAR AXLE - 226RBA 3 - 95
REAR AXLE - 226RBA (Continued)
Page 148 of 2199
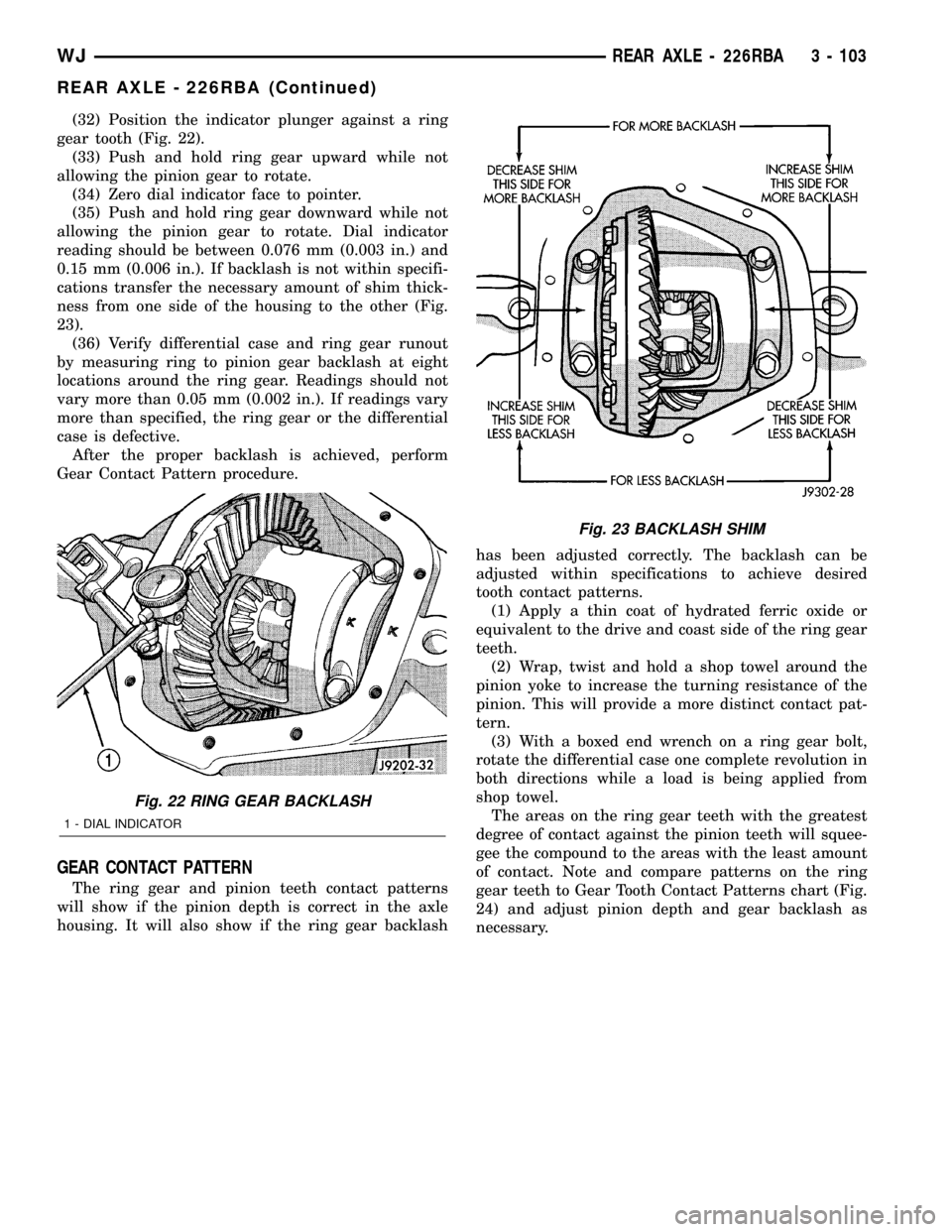
(32) Position the indicator plunger against a ring
gear tooth (Fig. 22).
(33) Push and hold ring gear upward while not
allowing the pinion gear to rotate.
(34) Zero dial indicator face to pointer.
(35) Push and hold ring gear downward while not
allowing the pinion gear to rotate. Dial indicator
reading should be between 0.076 mm (0.003 in.) and
0.15 mm (0.006 in.). If backlash is not within specifi-
cations transfer the necessary amount of shim thick-
ness from one side of the housing to the other (Fig.
23).
(36) Verify differential case and ring gear runout
by measuring ring to pinion gear backlash at eight
locations around the ring gear. Readings should not
vary more than 0.05 mm (0.002 in.). If readings vary
more than specified, the ring gear or the differential
case is defective.
After the proper backlash is achieved, perform
Gear Contact Pattern procedure.
GEAR CONTACT PATTERN
The ring gear and pinion teeth contact patterns
will show if the pinion depth is correct in the axle
housing. It will also show if the ring gear backlashhas been adjusted correctly. The backlash can be
adjusted within specifications to achieve desired
tooth contact patterns.
(1) Apply a thin coat of hydrated ferric oxide or
equivalent to the drive and coast side of the ring gear
teeth.
(2) Wrap, twist and hold a shop towel around the
pinion yoke to increase the turning resistance of the
pinion. This will provide a more distinct contact pat-
tern.
(3) With a boxed end wrench on a ring gear bolt,
rotate the differential case one complete revolution in
both directions while a load is being applied from
shop towel.
The areas on the ring gear teeth with the greatest
degree of contact against the pinion teeth will squee-
gee the compound to the areas with the least amount
of contact. Note and compare patterns on the ring
gear teeth to Gear Tooth Contact Patterns chart (Fig.
24) and adjust pinion depth and gear backlash as
necessary.
Fig. 22 RING GEAR BACKLASH
1 - DIAL INDICATOR
Fig. 23 BACKLASH SHIM
WJREAR AXLE - 226RBA 3 - 103
REAR AXLE - 226RBA (Continued)
Page 207 of 2199
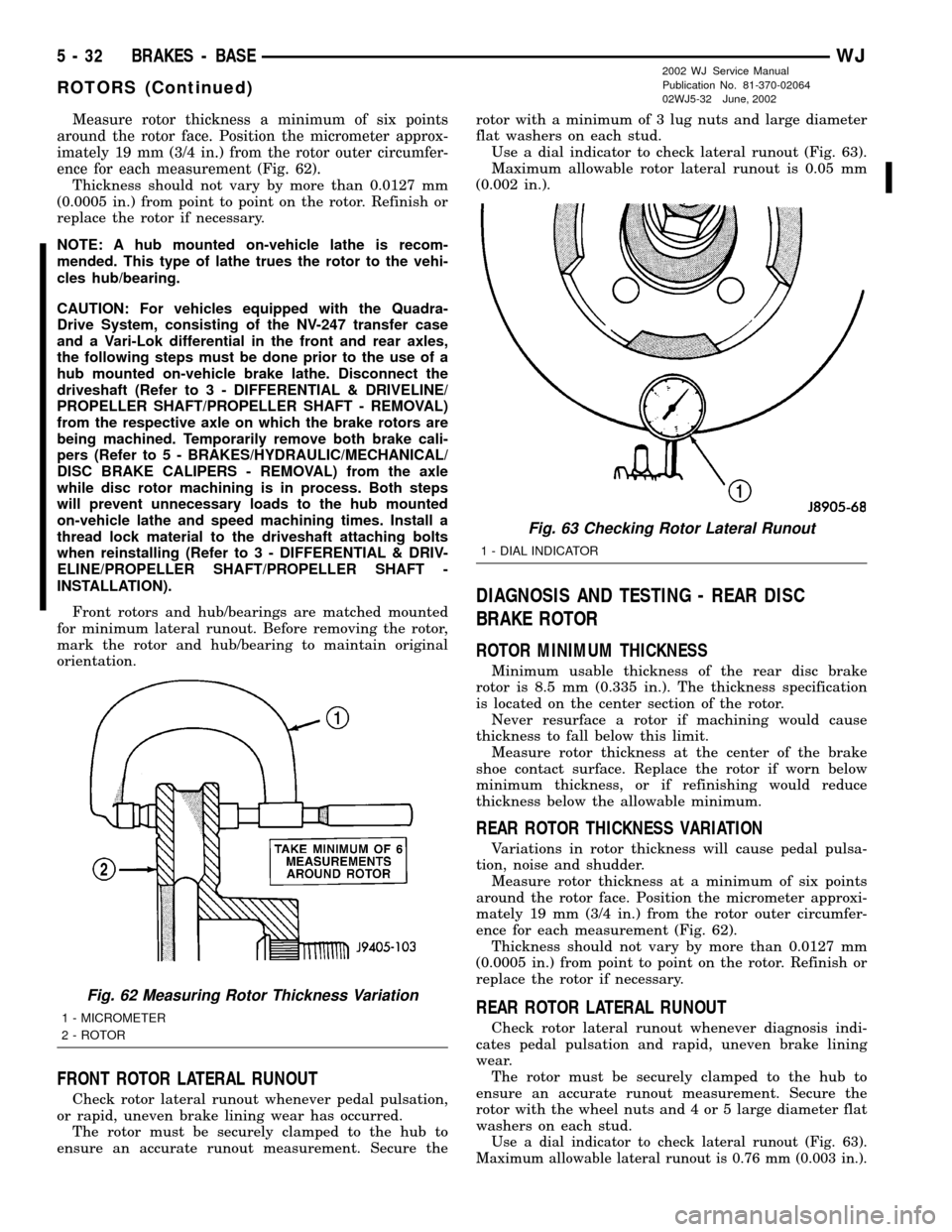
Measure rotor thickness a minimum of six points
around the rotor face. Position the micrometer approx-
imately 19 mm (3/4 in.) from the rotor outer circumfer-
ence for each measurement (Fig. 62).
Thickness should not vary by more than 0.0127 mm
(0.0005 in.) from point to point on the rotor. Refinish or
replace the rotor if necessary.
NOTE: A hub mounted on-vehicle lathe is recom-
mended. This type of lathe trues the rotor to the vehi-
cles hub/bearing.
CAUTION: For vehicles equipped with the Quadra-
Drive System, consisting of the NV-247 transfer case
and a Vari-Lok differential in the front and rear axles,
the following steps must be done prior to the use of a
hub mounted on-vehicle brake lathe. Disconnect the
driveshaft (Refer to 3 - DIFFERENTIAL & DRIVELINE/
PROPELLER SHAFT/PROPELLER SHAFT - REMOVAL)
from the respective axle on which the brake rotors are
being machined. Temporarily remove both brake cali-
pers (Refer to 5 - BRAKES/HYDRAULIC/MECHANICAL/
DISC BRAKE CALIPERS - REMOVAL) from the axle
while disc rotor machining is in process. Both steps
will prevent unnecessary loads to the hub mounted
on-vehicle lathe and speed machining times. Install a
thread lock material to the driveshaft attaching bolts
when reinstalling (Refer to 3 - DIFFERENTIAL & DRIV-
ELINE/PROPELLER SHAFT/PROPELLER SHAFT -
INSTALLATION).
Front rotors and hub/bearings are matched mounted
for minimum lateral runout. Before removing the rotor,
mark the rotor and hub/bearing to maintain original
orientation.
FRONT ROTOR LATERAL RUNOUT
Check rotor lateral runout whenever pedal pulsation,
or rapid, uneven brake lining wear has occurred.
The rotor must be securely clamped to the hub to
ensure an accurate runout measurement. Secure therotor with a minimum of 3 lug nuts and large diameter
flat washers on each stud.
Use a dial indicator to check lateral runout (Fig. 63).
Maximum allowable rotor lateral runout is 0.05 mm
(0.002 in.).
DIAGNOSIS AND TESTING - REAR DISC
BRAKE ROTOR
ROTOR MINIMUM THICKNESS
Minimum usable thickness of the rear disc brake
rotor is 8.5 mm (0.335 in.). The thickness specification
is located on the center section of the rotor.
Never resurface a rotor if machining would cause
thickness to fall below this limit.
Measure rotor thickness at the center of the brake
shoe contact surface. Replace the rotor if worn below
minimum thickness, or if refinishing would reduce
thickness below the allowable minimum.
REAR ROTOR THICKNESS VARIATION
Variations in rotor thickness will cause pedal pulsa-
tion, noise and shudder.
Measure rotor thickness at a minimum of six points
around the rotor face. Position the micrometer approxi-
mately 19 mm (3/4 in.) from the rotor outer circumfer-
ence for each measurement (Fig. 62).
Thickness should not vary by more than 0.0127 mm
(0.0005 in.) from point to point on the rotor. Refinish or
replace the rotor if necessary.
REAR ROTOR LATERAL RUNOUT
Check rotor lateral runout whenever diagnosis indi-
cates pedal pulsation and rapid, uneven brake lining
wear.
The rotor must be securely clamped to the hub to
ensure an accurate runout measurement. Secure the
rotor with the wheel nuts and 4 or 5 large diameter flat
washers on each stud.
Use a dial indicator to check lateral runout (Fig. 63).
Maximum allowable lateral runout is 0.76 mm (0.003 in.).
Fig. 62 Measuring Rotor Thickness Variation
1 - MICROMETER
2 - ROTOR
Fig. 63 Checking Rotor Lateral Runout
1 - DIAL INDICATOR
5 - 32 BRAKES - BASEWJ
ROTORS (Continued)
2002 WJ Service Manual
Publication No. 81-370-02064
02WJ5-32 June, 2002
Page 208 of 2199
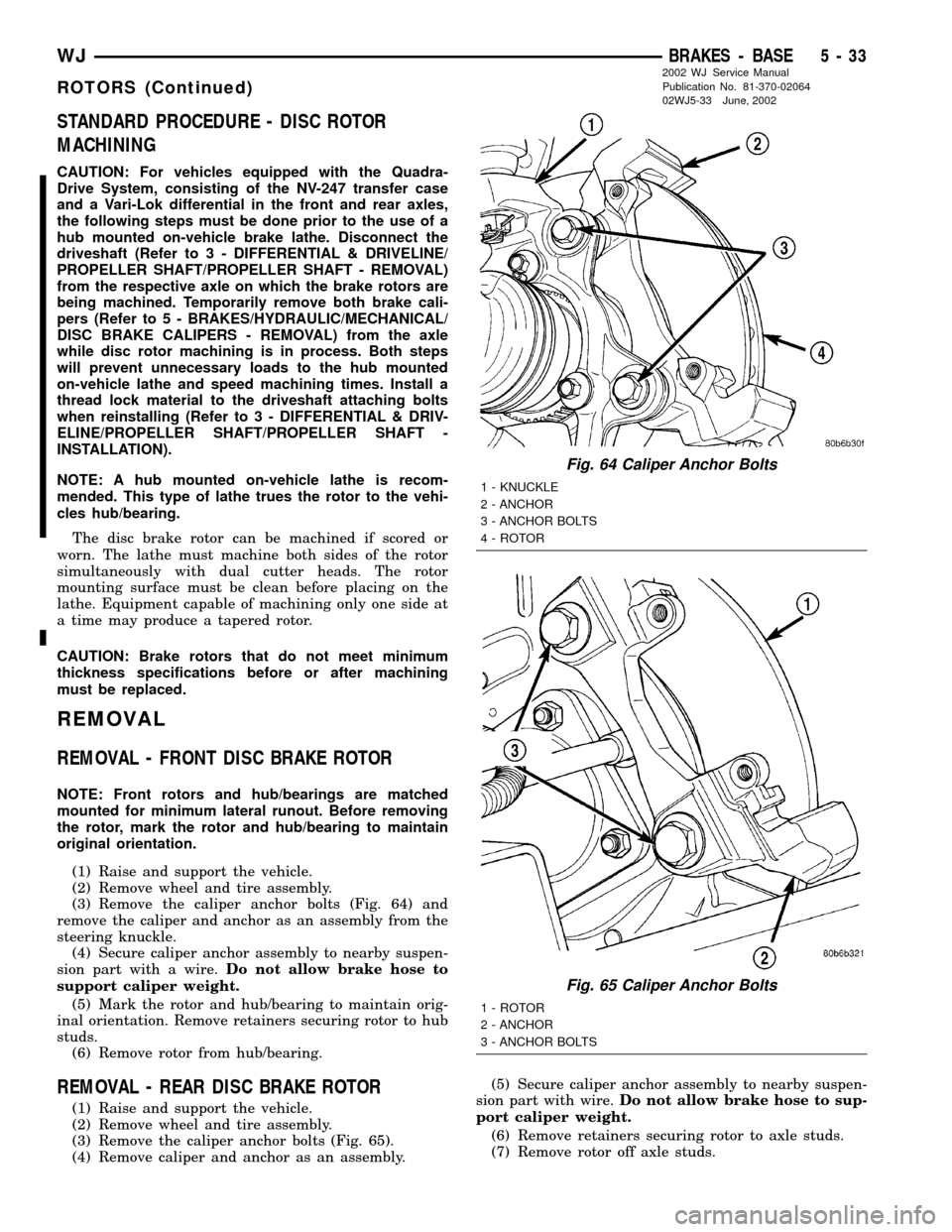
STANDARD PROCEDURE - DISC ROTOR
MACHINING
CAUTION: For vehicles equipped with the Quadra-
Drive System, consisting of the NV-247 transfer case
and a Vari-Lok differential in the front and rear axles,
the following steps must be done prior to the use of a
hub mounted on-vehicle brake lathe. Disconnect the
driveshaft (Refer to 3 - DIFFERENTIAL & DRIVELINE/
PROPELLER SHAFT/PROPELLER SHAFT - REMOVAL)
from the respective axle on which the brake rotors are
being machined. Temporarily remove both brake cali-
pers (Refer to 5 - BRAKES/HYDRAULIC/MECHANICAL/
DISC BRAKE CALIPERS - REMOVAL) from the axle
while disc rotor machining is in process. Both steps
will prevent unnecessary loads to the hub mounted
on-vehicle lathe and speed machining times. Install a
thread lock material to the driveshaft attaching bolts
when reinstalling (Refer to 3 - DIFFERENTIAL & DRIV-
ELINE/PROPELLER SHAFT/PROPELLER SHAFT -
INSTALLATION).
NOTE: A hub mounted on-vehicle lathe is recom-
mended. This type of lathe trues the rotor to the vehi-
cles hub/bearing.
The disc brake rotor can be machined if scored or
worn. The lathe must machine both sides of the rotor
simultaneously with dual cutter heads. The rotor
mounting surface must be clean before placing on the
lathe. Equipment capable of machining only one side at
a time may produce a tapered rotor.
CAUTION: Brake rotors that do not meet minimum
thickness specifications before or after machining
must be replaced.
REMOVAL
REMOVAL - FRONT DISC BRAKE ROTOR
NOTE: Front rotors and hub/bearings are matched
mounted for minimum lateral runout. Before removing
the rotor, mark the rotor and hub/bearing to maintain
original orientation.
(1) Raise and support the vehicle.
(2) Remove wheel and tire assembly.
(3) Remove the caliper anchor bolts (Fig. 64) and
remove the caliper and anchor as an assembly from the
steering knuckle.
(4) Secure caliper anchor assembly to nearby suspen-
sion part with a wire.Do not allow brake hose to
support caliper weight.
(5) Mark the rotor and hub/bearing to maintain orig-
inal orientation. Remove retainers securing rotor to hub
studs.
(6) Remove rotor from hub/bearing.
REMOVAL - REAR DISC BRAKE ROTOR
(1) Raise and support the vehicle.
(2) Remove wheel and tire assembly.
(3) Remove the caliper anchor bolts (Fig. 65).
(4) Remove caliper and anchor as an assembly.(5) Secure caliper anchor assembly to nearby suspen-
sion part with wire.Do not allow brake hose to sup-
port caliper weight.
(6) Remove retainers securing rotor to axle studs.
(7) Remove rotor off axle studs.
Fig. 64 Caliper Anchor Bolts
1 - KNUCKLE
2 - ANCHOR
3 - ANCHOR BOLTS
4 - ROTOR
Fig. 65 Caliper Anchor Bolts
1 - ROTOR
2 - ANCHOR
3 - ANCHOR BOLTS
WJBRAKES - BASE 5 - 33
ROTORS (Continued)
2002 WJ Service Manual
Publication No. 81-370-02064
02WJ5-33 June, 2002
Page 298 of 2199
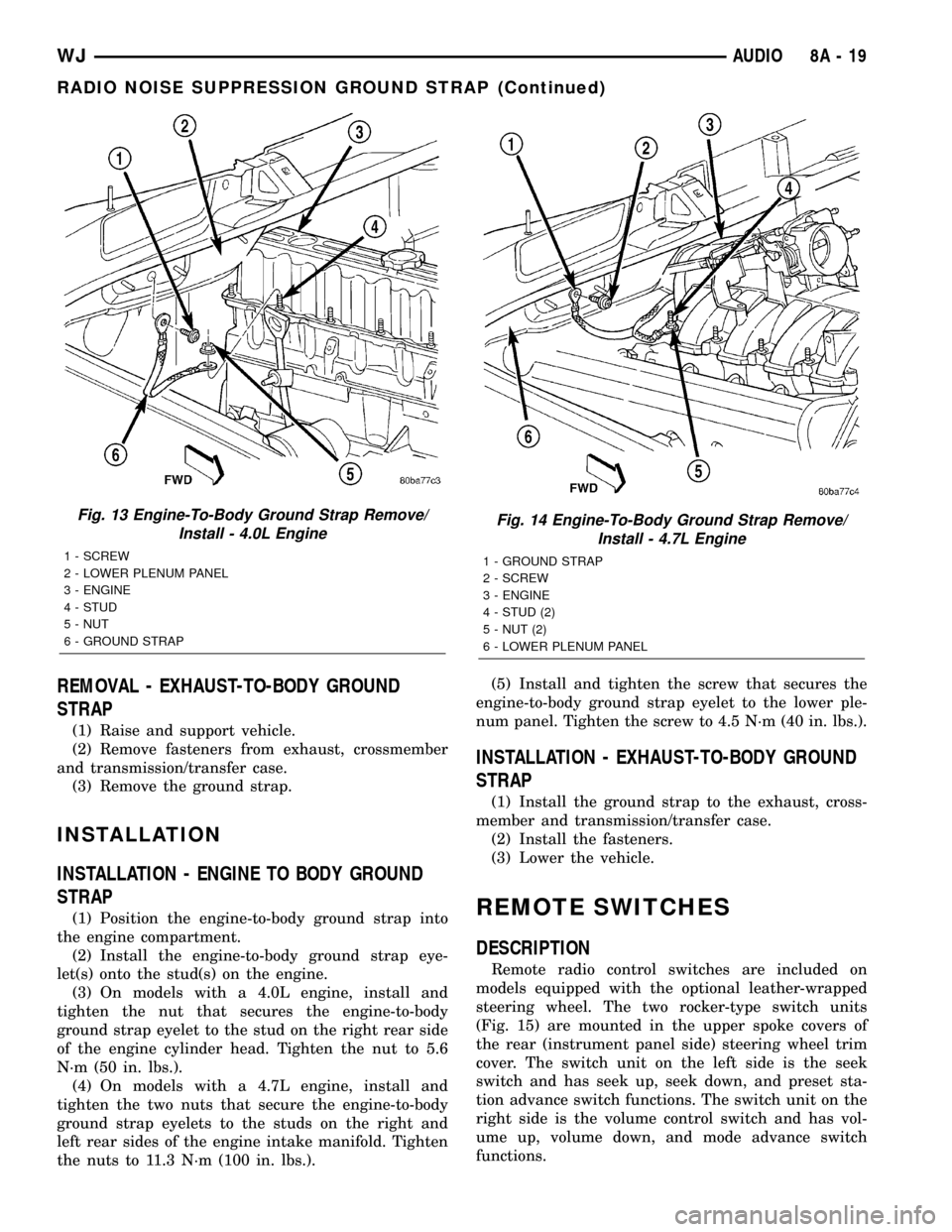
REMOVAL - EXHAUST-TO-BODY GROUND
STRAP
(1) Raise and support vehicle.
(2) Remove fasteners from exhaust, crossmember
and transmission/transfer case.
(3) Remove the ground strap.
INSTALLATION
INSTALLATION - ENGINE TO BODY GROUND
STRAP
(1) Position the engine-to-body ground strap into
the engine compartment.
(2) Install the engine-to-body ground strap eye-
let(s) onto the stud(s) on the engine.
(3) On models with a 4.0L engine, install and
tighten the nut that secures the engine-to-body
ground strap eyelet to the stud on the right rear side
of the engine cylinder head. Tighten the nut to 5.6
N´m (50 in. lbs.).
(4) On models with a 4.7L engine, install and
tighten the two nuts that secure the engine-to-body
ground strap eyelets to the studs on the right and
left rear sides of the engine intake manifold. Tighten
the nuts to 11.3 N´m (100 in. lbs.).(5) Install and tighten the screw that secures the
engine-to-body ground strap eyelet to the lower ple-
num panel. Tighten the screw to 4.5 N´m (40 in. lbs.).
INSTALLATION - EXHAUST-TO-BODY GROUND
STRAP
(1) Install the ground strap to the exhaust, cross-
member and transmission/transfer case.
(2) Install the fasteners.
(3) Lower the vehicle.
REMOTE SWITCHES
DESCRIPTION
Remote radio control switches are included on
models equipped with the optional leather-wrapped
steering wheel. The two rocker-type switch units
(Fig. 15) are mounted in the upper spoke covers of
the rear (instrument panel side) steering wheel trim
cover. The switch unit on the left side is the seek
switch and has seek up, seek down, and preset sta-
tion advance switch functions. The switch unit on the
right side is the volume control switch and has vol-
ume up, volume down, and mode advance switch
functions.
Fig. 13 Engine-To-Body Ground Strap Remove/
Install - 4.0L Engine
1 - SCREW
2 - LOWER PLENUM PANEL
3 - ENGINE
4 - STUD
5 - NUT
6 - GROUND STRAP
Fig. 14 Engine-To-Body Ground Strap Remove/
Install - 4.7L Engine
1 - GROUND STRAP
2 - SCREW
3 - ENGINE
4 - STUD (2)
5 - NUT (2)
6 - LOWER PLENUM PANEL
WJAUDIO 8A - 19
RADIO NOISE SUPPRESSION GROUND STRAP (Continued)
Page 416 of 2199
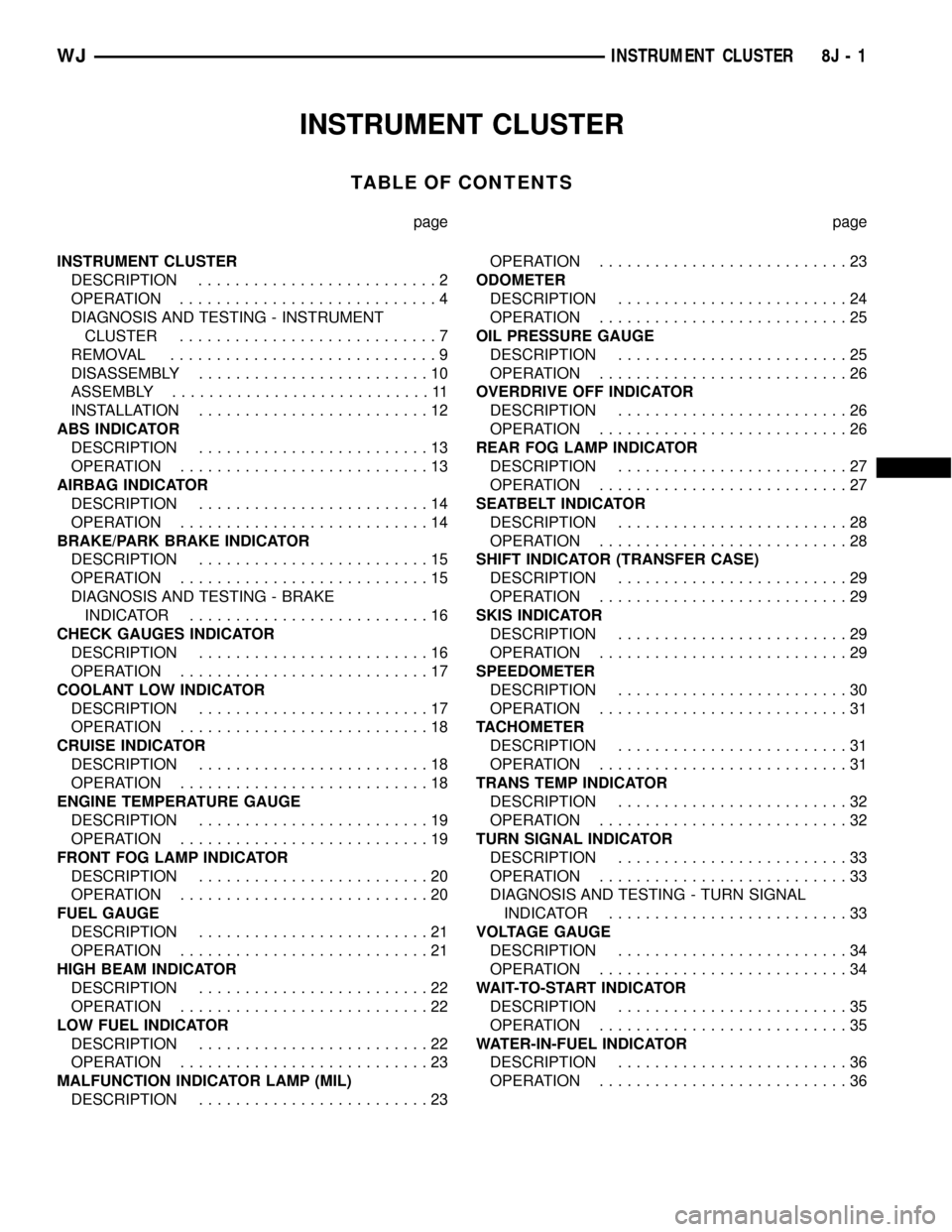
INSTRUMENT CLUSTER
TABLE OF CONTENTS
page page
INSTRUMENT CLUSTER
DESCRIPTION..........................2
OPERATION............................4
DIAGNOSIS AND TESTING - INSTRUMENT
CLUSTER............................7
REMOVAL.............................9
DISASSEMBLY.........................10
ASSEMBLY............................11
INSTALLATION.........................12
ABS INDICATOR
DESCRIPTION.........................13
OPERATION...........................13
AIRBAG INDICATOR
DESCRIPTION.........................14
OPERATION...........................14
BRAKE/PARK BRAKE INDICATOR
DESCRIPTION.........................15
OPERATION...........................15
DIAGNOSIS AND TESTING - BRAKE
INDICATOR..........................16
CHECK GAUGES INDICATOR
DESCRIPTION.........................16
OPERATION...........................17
COOLANT LOW INDICATOR
DESCRIPTION.........................17
OPERATION...........................18
CRUISE INDICATOR
DESCRIPTION.........................18
OPERATION...........................18
ENGINE TEMPERATURE GAUGE
DESCRIPTION.........................19
OPERATION...........................19
FRONT FOG LAMP INDICATOR
DESCRIPTION.........................20
OPERATION...........................20
FUEL GAUGE
DESCRIPTION.........................21
OPERATION...........................21
HIGH BEAM INDICATOR
DESCRIPTION.........................22
OPERATION...........................22
LOW FUEL INDICATOR
DESCRIPTION.........................22
OPERATION...........................23
MALFUNCTION INDICATOR LAMP (MIL)
DESCRIPTION.........................23OPERATION...........................23
ODOMETER
DESCRIPTION.........................24
OPERATION...........................25
OIL PRESSURE GAUGE
DESCRIPTION.........................25
OPERATION...........................26
OVERDRIVE OFF INDICATOR
DESCRIPTION.........................26
OPERATION...........................26
REAR FOG LAMP INDICATOR
DESCRIPTION.........................27
OPERATION...........................27
SEATBELT INDICATOR
DESCRIPTION.........................28
OPERATION...........................28
SHIFT INDICATOR (TRANSFER CASE)
DESCRIPTION.........................29
OPERATION...........................29
SKIS INDICATOR
DESCRIPTION.........................29
OPERATION...........................29
SPEEDOMETER
DESCRIPTION.........................30
OPERATION...........................31
TACHOMETER
DESCRIPTION.........................31
OPERATION...........................31
TRANS TEMP INDICATOR
DESCRIPTION.........................32
OPERATION...........................32
TURN SIGNAL INDICATOR
DESCRIPTION.........................33
OPERATION...........................33
DIAGNOSIS AND TESTING - TURN SIGNAL
INDICATOR..........................33
VOLTAGE GAUGE
DESCRIPTION.........................34
OPERATION...........................34
WAIT-TO-START INDICATOR
DESCRIPTION.........................35
OPERATION...........................35
WATER-IN-FUEL INDICATOR
DESCRIPTION.........................36
OPERATION...........................36
WJINSTRUMENT CLUSTER 8J - 1
Page 418 of 2199
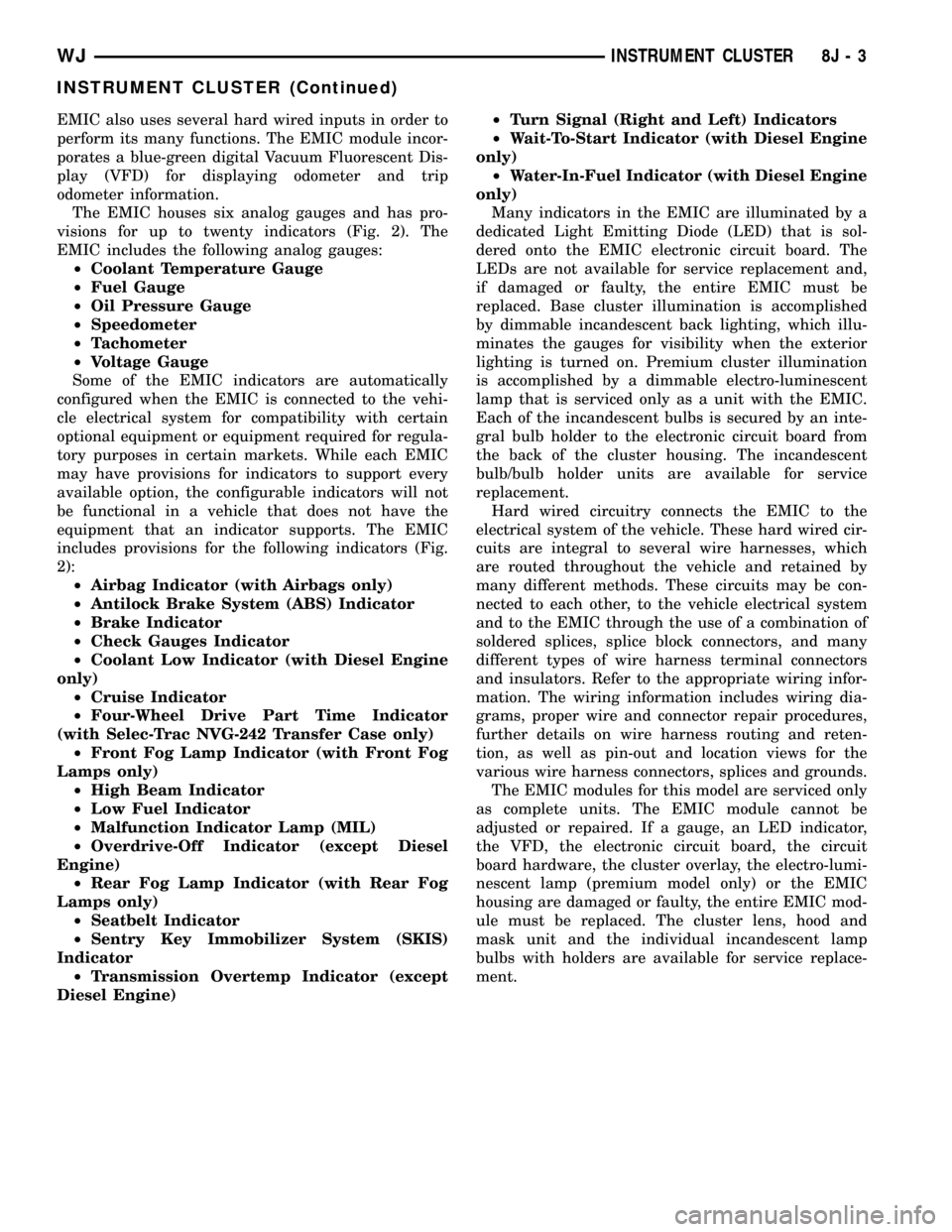
EMIC also uses several hard wired inputs in order to
perform its many functions. The EMIC module incor-
porates a blue-green digital Vacuum Fluorescent Dis-
play (VFD) for displaying odometer and trip
odometer information.
The EMIC houses six analog gauges and has pro-
visions for up to twenty indicators (Fig. 2). The
EMIC includes the following analog gauges:
²Coolant Temperature Gauge
²Fuel Gauge
²Oil Pressure Gauge
²Speedometer
²Tachometer
²Voltage Gauge
Some of the EMIC indicators are automatically
configured when the EMIC is connected to the vehi-
cle electrical system for compatibility with certain
optional equipment or equipment required for regula-
tory purposes in certain markets. While each EMIC
may have provisions for indicators to support every
available option, the configurable indicators will not
be functional in a vehicle that does not have the
equipment that an indicator supports. The EMIC
includes provisions for the following indicators (Fig.
2):
²Airbag Indicator (with Airbags only)
²Antilock Brake System (ABS) Indicator
²Brake Indicator
²Check Gauges Indicator
²Coolant Low Indicator (with Diesel Engine
only)
²Cruise Indicator
²Four-Wheel Drive Part Time Indicator
(with Selec-Trac NVG-242 Transfer Case only)
²Front Fog Lamp Indicator (with Front Fog
Lamps only)
²High Beam Indicator
²Low Fuel Indicator
²Malfunction Indicator Lamp (MIL)
²Overdrive-Off Indicator (except Diesel
Engine)
²Rear Fog Lamp Indicator (with Rear Fog
Lamps only)
²Seatbelt Indicator
²Sentry Key Immobilizer System (SKIS)
Indicator
²Transmission Overtemp Indicator (except
Diesel Engine)²Turn Signal (Right and Left) Indicators
²Wait-To-Start Indicator (with Diesel Engine
only)
²Water-In-Fuel Indicator (with Diesel Engine
only)
Many indicators in the EMIC are illuminated by a
dedicated Light Emitting Diode (LED) that is sol-
dered onto the EMIC electronic circuit board. The
LEDs are not available for service replacement and,
if damaged or faulty, the entire EMIC must be
replaced. Base cluster illumination is accomplished
by dimmable incandescent back lighting, which illu-
minates the gauges for visibility when the exterior
lighting is turned on. Premium cluster illumination
is accomplished by a dimmable electro-luminescent
lamp that is serviced only as a unit with the EMIC.
Each of the incandescent bulbs is secured by an inte-
gral bulb holder to the electronic circuit board from
the back of the cluster housing. The incandescent
bulb/bulb holder units are available for service
replacement.
Hard wired circuitry connects the EMIC to the
electrical system of the vehicle. These hard wired cir-
cuits are integral to several wire harnesses, which
are routed throughout the vehicle and retained by
many different methods. These circuits may be con-
nected to each other, to the vehicle electrical system
and to the EMIC through the use of a combination of
soldered splices, splice block connectors, and many
different types of wire harness terminal connectors
and insulators. Refer to the appropriate wiring infor-
mation. The wiring information includes wiring dia-
grams, proper wire and connector repair procedures,
further details on wire harness routing and reten-
tion, as well as pin-out and location views for the
various wire harness connectors, splices and grounds.
The EMIC modules for this model are serviced only
as complete units. The EMIC module cannot be
adjusted or repaired. If a gauge, an LED indicator,
the VFD, the electronic circuit board, the circuit
board hardware, the cluster overlay, the electro-lumi-
nescent lamp (premium model only) or the EMIC
housing are damaged or faulty, the entire EMIC mod-
ule must be replaced. The cluster lens, hood and
mask unit and the individual incandescent lamp
bulbs with holders are available for service replace-
ment.
WJINSTRUMENT CLUSTER 8J - 3
INSTRUMENT CLUSTER (Continued)
Page 444 of 2199
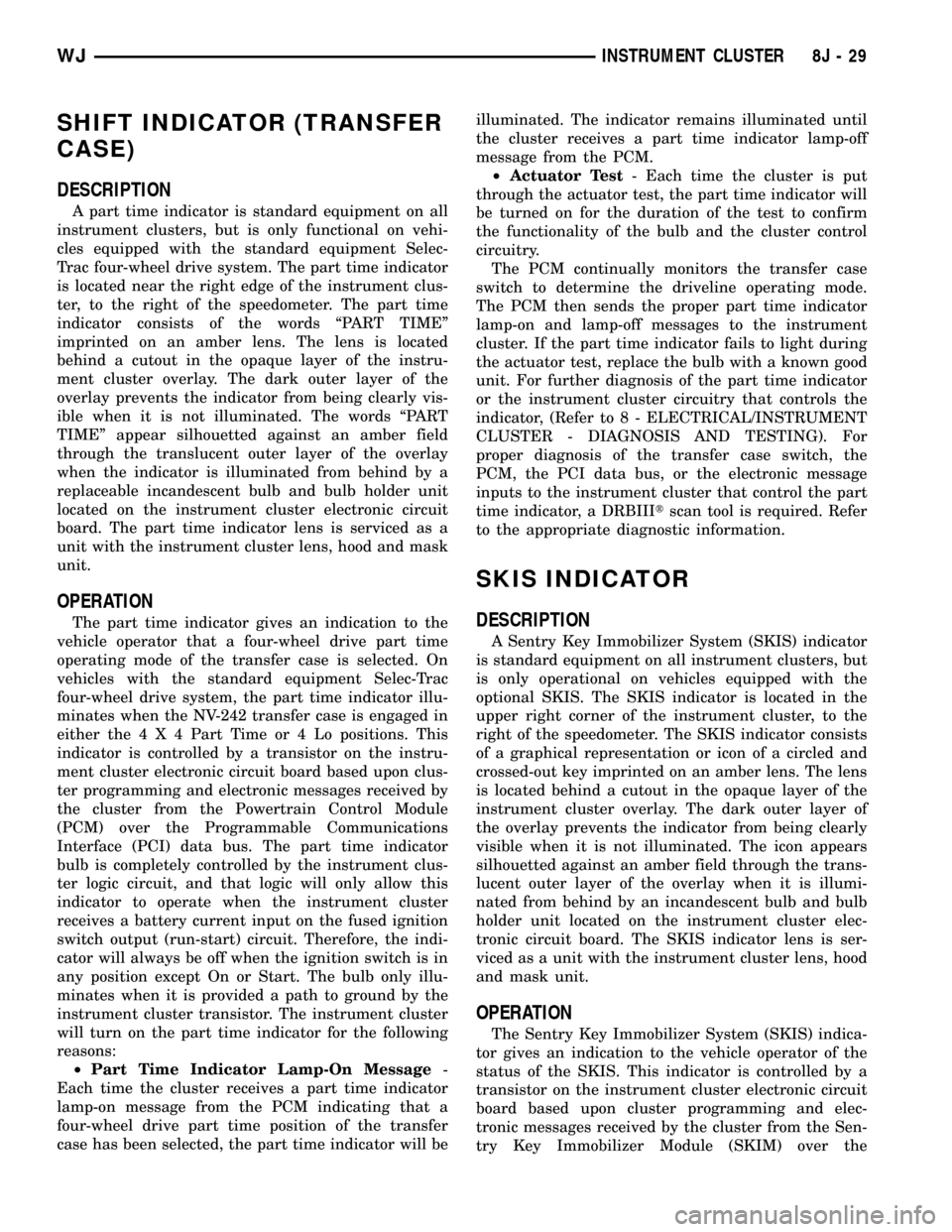
SHIFT INDICATOR (TRANSFER
CASE)
DESCRIPTION
A part time indicator is standard equipment on all
instrument clusters, but is only functional on vehi-
cles equipped with the standard equipment Selec-
Trac four-wheel drive system. The part time indicator
is located near the right edge of the instrument clus-
ter, to the right of the speedometer. The part time
indicator consists of the words ªPART TIMEº
imprinted on an amber lens. The lens is located
behind a cutout in the opaque layer of the instru-
ment cluster overlay. The dark outer layer of the
overlay prevents the indicator from being clearly vis-
ible when it is not illuminated. The words ªPART
TIMEº appear silhouetted against an amber field
through the translucent outer layer of the overlay
when the indicator is illuminated from behind by a
replaceable incandescent bulb and bulb holder unit
located on the instrument cluster electronic circuit
board. The part time indicator lens is serviced as a
unit with the instrument cluster lens, hood and mask
unit.
OPERATION
The part time indicator gives an indication to the
vehicle operator that a four-wheel drive part time
operating mode of the transfer case is selected. On
vehicles with the standard equipment Selec-Trac
four-wheel drive system, the part time indicator illu-
minates when the NV-242 transfer case is engaged in
either the4X4Part Time or 4 Lo positions. This
indicator is controlled by a transistor on the instru-
ment cluster electronic circuit board based upon clus-
ter programming and electronic messages received by
the cluster from the Powertrain Control Module
(PCM) over the Programmable Communications
Interface (PCI) data bus. The part time indicator
bulb is completely controlled by the instrument clus-
ter logic circuit, and that logic will only allow this
indicator to operate when the instrument cluster
receives a battery current input on the fused ignition
switch output (run-start) circuit. Therefore, the indi-
cator will always be off when the ignition switch is in
any position except On or Start. The bulb only illu-
minates when it is provided a path to ground by the
instrument cluster transistor. The instrument cluster
will turn on the part time indicator for the following
reasons:
²Part Time Indicator Lamp-On Message-
Each time the cluster receives a part time indicator
lamp-on message from the PCM indicating that a
four-wheel drive part time position of the transfer
case has been selected, the part time indicator will beilluminated. The indicator remains illuminated until
the cluster receives a part time indicator lamp-off
message from the PCM.
²Actuator Test- Each time the cluster is put
through the actuator test, the part time indicator will
be turned on for the duration of the test to confirm
the functionality of the bulb and the cluster control
circuitry.
The PCM continually monitors the transfer case
switch to determine the driveline operating mode.
The PCM then sends the proper part time indicator
lamp-on and lamp-off messages to the instrument
cluster. If the part time indicator fails to light during
the actuator test, replace the bulb with a known good
unit. For further diagnosis of the part time indicator
or the instrument cluster circuitry that controls the
indicator, (Refer to 8 - ELECTRICAL/INSTRUMENT
CLUSTER - DIAGNOSIS AND TESTING). For
proper diagnosis of the transfer case switch, the
PCM, the PCI data bus, or the electronic message
inputs to the instrument cluster that control the part
time indicator, a DRBIIItscan tool is required. Refer
to the appropriate diagnostic information.
SKIS INDICATOR
DESCRIPTION
A Sentry Key Immobilizer System (SKIS) indicator
is standard equipment on all instrument clusters, but
is only operational on vehicles equipped with the
optional SKIS. The SKIS indicator is located in the
upper right corner of the instrument cluster, to the
right of the speedometer. The SKIS indicator consists
of a graphical representation or icon of a circled and
crossed-out key imprinted on an amber lens. The lens
is located behind a cutout in the opaque layer of the
instrument cluster overlay. The dark outer layer of
the overlay prevents the indicator from being clearly
visible when it is not illuminated. The icon appears
silhouetted against an amber field through the trans-
lucent outer layer of the overlay when it is illumi-
nated from behind by an incandescent bulb and bulb
holder unit located on the instrument cluster elec-
tronic circuit board. The SKIS indicator lens is ser-
viced as a unit with the instrument cluster lens, hood
and mask unit.
OPERATION
The Sentry Key Immobilizer System (SKIS) indica-
tor gives an indication to the vehicle operator of the
status of the SKIS. This indicator is controlled by a
transistor on the instrument cluster electronic circuit
board based upon cluster programming and elec-
tronic messages received by the cluster from the Sen-
try Key Immobilizer Module (SKIM) over the
WJINSTRUMENT CLUSTER 8J - 29