Control arm JEEP GRAND CHEROKEE 2002 WJ / 2.G Repair Manual
[x] Cancel search | Manufacturer: JEEP, Model Year: 2002, Model line: GRAND CHEROKEE, Model: JEEP GRAND CHEROKEE 2002 WJ / 2.GPages: 2199, PDF Size: 76.01 MB
Page 621 of 2199
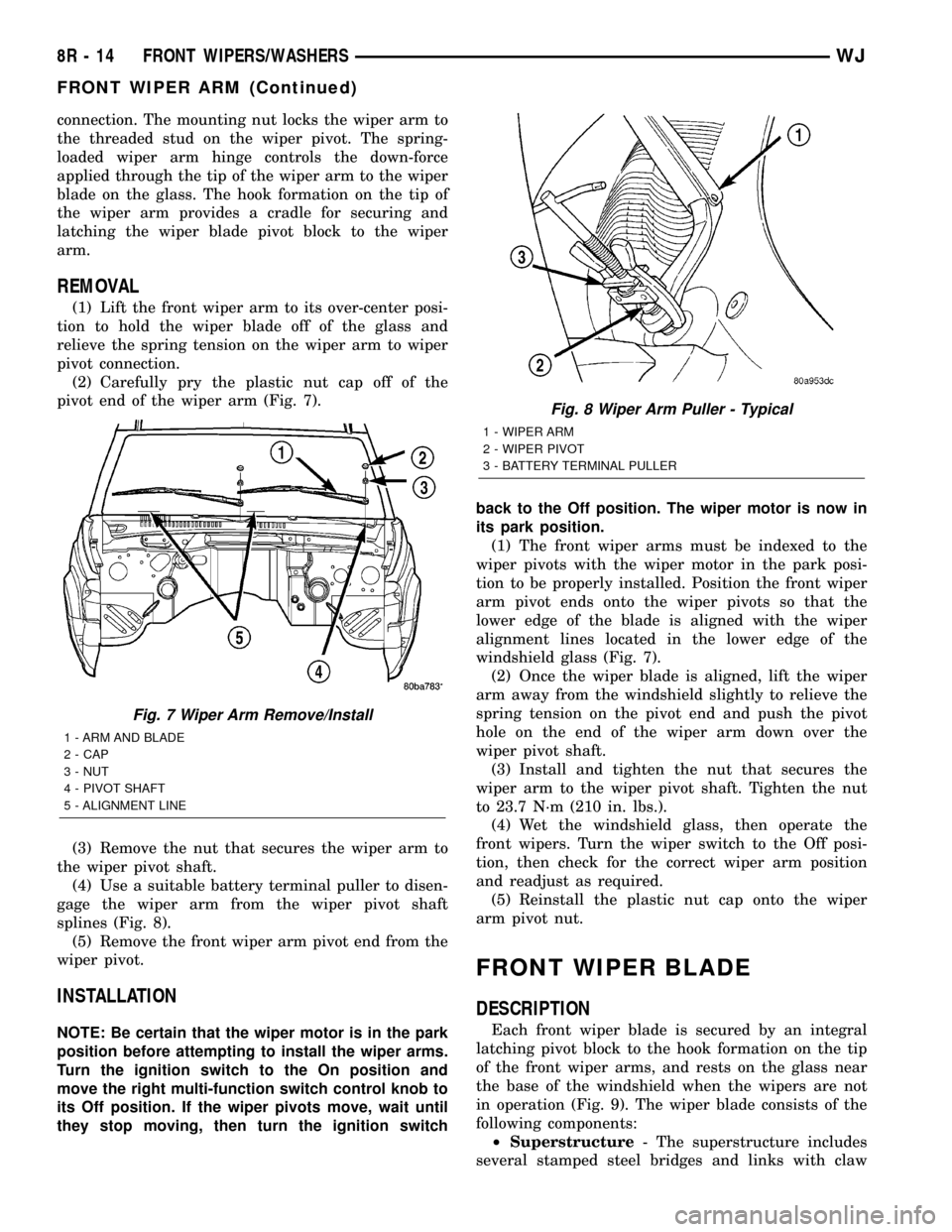
connection. The mounting nut locks the wiper arm to
the threaded stud on the wiper pivot. The spring-
loaded wiper arm hinge controls the down-force
applied through the tip of the wiper arm to the wiper
blade on the glass. The hook formation on the tip of
the wiper arm provides a cradle for securing and
latching the wiper blade pivot block to the wiper
arm.
REMOVAL
(1) Lift the front wiper arm to its over-center posi-
tion to hold the wiper blade off of the glass and
relieve the spring tension on the wiper arm to wiper
pivot connection.
(2) Carefully pry the plastic nut cap off of the
pivot end of the wiper arm (Fig. 7).
(3) Remove the nut that secures the wiper arm to
the wiper pivot shaft.
(4) Use a suitable battery terminal puller to disen-
gage the wiper arm from the wiper pivot shaft
splines (Fig. 8).
(5) Remove the front wiper arm pivot end from the
wiper pivot.
INSTALLATION
NOTE: Be certain that the wiper motor is in the park
position before attempting to install the wiper arms.
Turn the ignition switch to the On position and
move the right multi-function switch control knob to
its Off position. If the wiper pivots move, wait until
they stop moving, then turn the ignition switchback to the Off position. The wiper motor is now in
its park position.
(1) The front wiper arms must be indexed to the
wiper pivots with the wiper motor in the park posi-
tion to be properly installed. Position the front wiper
arm pivot ends onto the wiper pivots so that the
lower edge of the blade is aligned with the wiper
alignment lines located in the lower edge of the
windshield glass (Fig. 7).
(2) Once the wiper blade is aligned, lift the wiper
arm away from the windshield slightly to relieve the
spring tension on the pivot end and push the pivot
hole on the end of the wiper arm down over the
wiper pivot shaft.
(3) Install and tighten the nut that secures the
wiper arm to the wiper pivot shaft. Tighten the nut
to 23.7 N´m (210 in. lbs.).
(4) Wet the windshield glass, then operate the
front wipers. Turn the wiper switch to the Off posi-
tion, then check for the correct wiper arm position
and readjust as required.
(5) Reinstall the plastic nut cap onto the wiper
arm pivot nut.
FRONT WIPER BLADE
DESCRIPTION
Each front wiper blade is secured by an integral
latching pivot block to the hook formation on the tip
of the front wiper arms, and rests on the glass near
the base of the windshield when the wipers are not
in operation (Fig. 9). The wiper blade consists of the
following components:
²Superstructure- The superstructure includes
several stamped steel bridges and links with claw
Fig. 7 Wiper Arm Remove/Install
1 - ARM AND BLADE
2 - CAP
3 - NUT
4 - PIVOT SHAFT
5 - ALIGNMENT LINE
Fig. 8 Wiper Arm Puller - Typical
1 - WIPER ARM
2 - WIPER PIVOT
3 - BATTERY TERMINAL PULLER
8R - 14 FRONT WIPERS/WASHERSWJ
FRONT WIPER ARM (Continued)
Page 623 of 2199
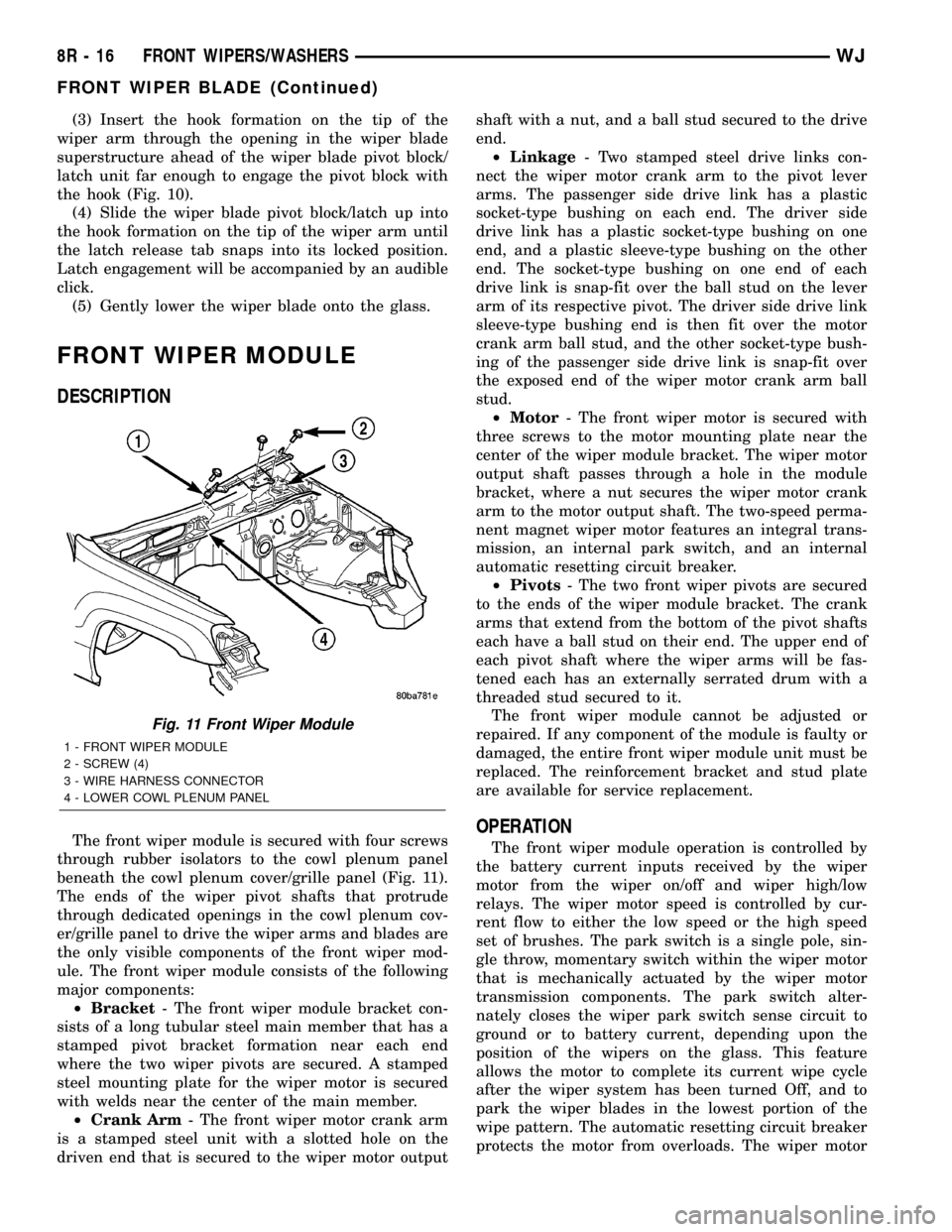
(3) Insert the hook formation on the tip of the
wiper arm through the opening in the wiper blade
superstructure ahead of the wiper blade pivot block/
latch unit far enough to engage the pivot block with
the hook (Fig. 10).
(4) Slide the wiper blade pivot block/latch up into
the hook formation on the tip of the wiper arm until
the latch release tab snaps into its locked position.
Latch engagement will be accompanied by an audible
click.
(5) Gently lower the wiper blade onto the glass.
FRONT WIPER MODULE
DESCRIPTION
The front wiper module is secured with four screws
through rubber isolators to the cowl plenum panel
beneath the cowl plenum cover/grille panel (Fig. 11).
The ends of the wiper pivot shafts that protrude
through dedicated openings in the cowl plenum cov-
er/grille panel to drive the wiper arms and blades are
the only visible components of the front wiper mod-
ule. The front wiper module consists of the following
major components:
²Bracket- The front wiper module bracket con-
sists of a long tubular steel main member that has a
stamped pivot bracket formation near each end
where the two wiper pivots are secured. A stamped
steel mounting plate for the wiper motor is secured
with welds near the center of the main member.
²Crank Arm- The front wiper motor crank arm
is a stamped steel unit with a slotted hole on the
driven end that is secured to the wiper motor outputshaft with a nut, and a ball stud secured to the drive
end.
²Linkage- Two stamped steel drive links con-
nect the wiper motor crank arm to the pivot lever
arms. The passenger side drive link has a plastic
socket-type bushing on each end. The driver side
drive link has a plastic socket-type bushing on one
end, and a plastic sleeve-type bushing on the other
end. The socket-type bushing on one end of each
drive link is snap-fit over the ball stud on the lever
arm of its respective pivot. The driver side drive link
sleeve-type bushing end is then fit over the motor
crank arm ball stud, and the other socket-type bush-
ing of the passenger side drive link is snap-fit over
the exposed end of the wiper motor crank arm ball
stud.
²Motor- The front wiper motor is secured with
three screws to the motor mounting plate near the
center of the wiper module bracket. The wiper motor
output shaft passes through a hole in the module
bracket, where a nut secures the wiper motor crank
arm to the motor output shaft. The two-speed perma-
nent magnet wiper motor features an integral trans-
mission, an internal park switch, and an internal
automatic resetting circuit breaker.
²Pivots- The two front wiper pivots are secured
to the ends of the wiper module bracket. The crank
arms that extend from the bottom of the pivot shafts
each have a ball stud on their end. The upper end of
each pivot shaft where the wiper arms will be fas-
tened each has an externally serrated drum with a
threaded stud secured to it.
The front wiper module cannot be adjusted or
repaired. If any component of the module is faulty or
damaged, the entire front wiper module unit must be
replaced. The reinforcement bracket and stud plate
are available for service replacement.OPERATION
The front wiper module operation is controlled by
the battery current inputs received by the wiper
motor from the wiper on/off and wiper high/low
relays. The wiper motor speed is controlled by cur-
rent flow to either the low speed or the high speed
set of brushes. The park switch is a single pole, sin-
gle throw, momentary switch within the wiper motor
that is mechanically actuated by the wiper motor
transmission components. The park switch alter-
nately closes the wiper park switch sense circuit to
ground or to battery current, depending upon the
position of the wipers on the glass. This feature
allows the motor to complete its current wipe cycle
after the wiper system has been turned Off, and to
park the wiper blades in the lowest portion of the
wipe pattern. The automatic resetting circuit breaker
protects the motor from overloads. The wiper motor
Fig. 11 Front Wiper Module
1 - FRONT WIPER MODULE
2 - SCREW (4)
3 - WIRE HARNESS CONNECTOR
4 - LOWER COWL PLENUM PANEL
8R - 16 FRONT WIPERS/WASHERSWJ
FRONT WIPER BLADE (Continued)
Page 625 of 2199
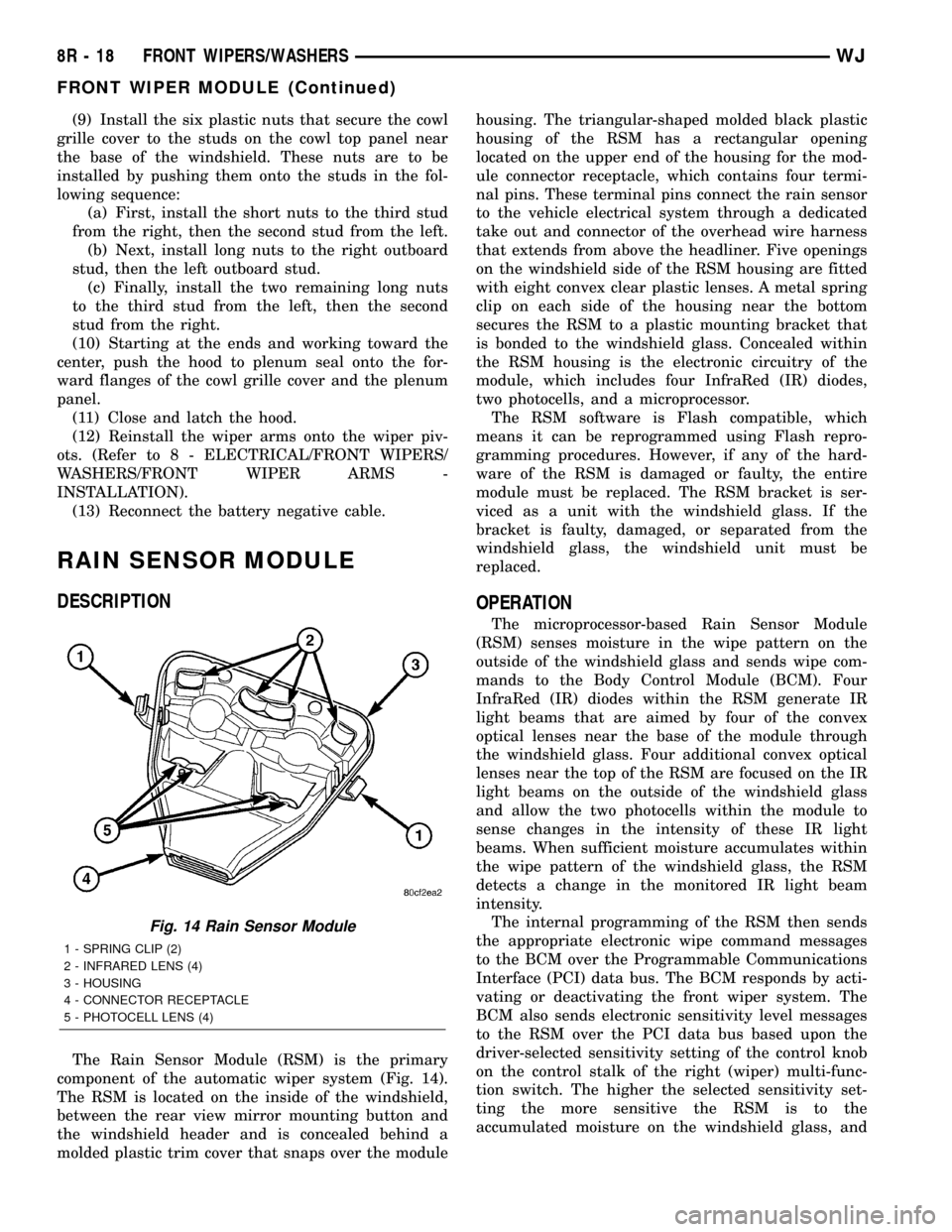
(9) Install the six plastic nuts that secure the cowl
grille cover to the studs on the cowl top panel near
the base of the windshield. These nuts are to be
installed by pushing them onto the studs in the fol-
lowing sequence:
(a) First, install the short nuts to the third stud
from the right, then the second stud from the left.
(b) Next, install long nuts to the right outboard
stud, then the left outboard stud.
(c) Finally, install the two remaining long nuts
to the third stud from the left, then the second
stud from the right.
(10) Starting at the ends and working toward the
center, push the hood to plenum seal onto the for-
ward flanges of the cowl grille cover and the plenum
panel.
(11) Close and latch the hood.
(12) Reinstall the wiper arms onto the wiper piv-
ots. (Refer to 8 - ELECTRICAL/FRONT WIPERS/
WASHERS/FRONT WIPER ARMS -
INSTALLATION).
(13) Reconnect the battery negative cable.
RAIN SENSOR MODULE
DESCRIPTION
The Rain Sensor Module (RSM) is the primary
component of the automatic wiper system (Fig. 14).
The RSM is located on the inside of the windshield,
between the rear view mirror mounting button and
the windshield header and is concealed behind a
molded plastic trim cover that snaps over the modulehousing. The triangular-shaped molded black plastic
housing of the RSM has a rectangular opening
located on the upper end of the housing for the mod-
ule connector receptacle, which contains four termi-
nal pins. These terminal pins connect the rain sensor
to the vehicle electrical system through a dedicated
take out and connector of the overhead wire harness
that extends from above the headliner. Five openings
on the windshield side of the RSM housing are fitted
with eight convex clear plastic lenses. A metal spring
clip on each side of the housing near the bottom
secures the RSM to a plastic mounting bracket that
is bonded to the windshield glass. Concealed within
the RSM housing is the electronic circuitry of the
module, which includes four InfraRed (IR) diodes,
two photocells, and a microprocessor.
The RSM software is Flash compatible, which
means it can be reprogrammed using Flash repro-
gramming procedures. However, if any of the hard-
ware of the RSM is damaged or faulty, the entire
module must be replaced. The RSM bracket is ser-
viced as a unit with the windshield glass. If the
bracket is faulty, damaged, or separated from the
windshield glass, the windshield unit must be
replaced.
OPERATION
The microprocessor-based Rain Sensor Module
(RSM) senses moisture in the wipe pattern on the
outside of the windshield glass and sends wipe com-
mands to the Body Control Module (BCM). Four
InfraRed (IR) diodes within the RSM generate IR
light beams that are aimed by four of the convex
optical lenses near the base of the module through
the windshield glass. Four additional convex optical
lenses near the top of the RSM are focused on the IR
light beams on the outside of the windshield glass
and allow the two photocells within the module to
sense changes in the intensity of these IR light
beams. When sufficient moisture accumulates within
the wipe pattern of the windshield glass, the RSM
detects a change in the monitored IR light beam
intensity.
The internal programming of the RSM then sends
the appropriate electronic wipe command messages
to the BCM over the Programmable Communications
Interface (PCI) data bus. The BCM responds by acti-
vating or deactivating the front wiper system. The
BCM also sends electronic sensitivity level messages
to the RSM over the PCI data bus based upon the
driver-selected sensitivity setting of the control knob
on the control stalk of the right (wiper) multi-func-
tion switch. The higher the selected sensitivity set-
ting the more sensitive the RSM is to the
accumulated moisture on the windshield glass, and
Fig. 14 Rain Sensor Module
1 - SPRING CLIP (2)
2 - INFRARED LENS (4)
3 - HOUSING
4 - CONNECTOR RECEPTACLE
5 - PHOTOCELL LENS (4)
8R - 18 FRONT WIPERS/WASHERSWJ
FRONT WIPER MODULE (Continued)
Page 640 of 2199
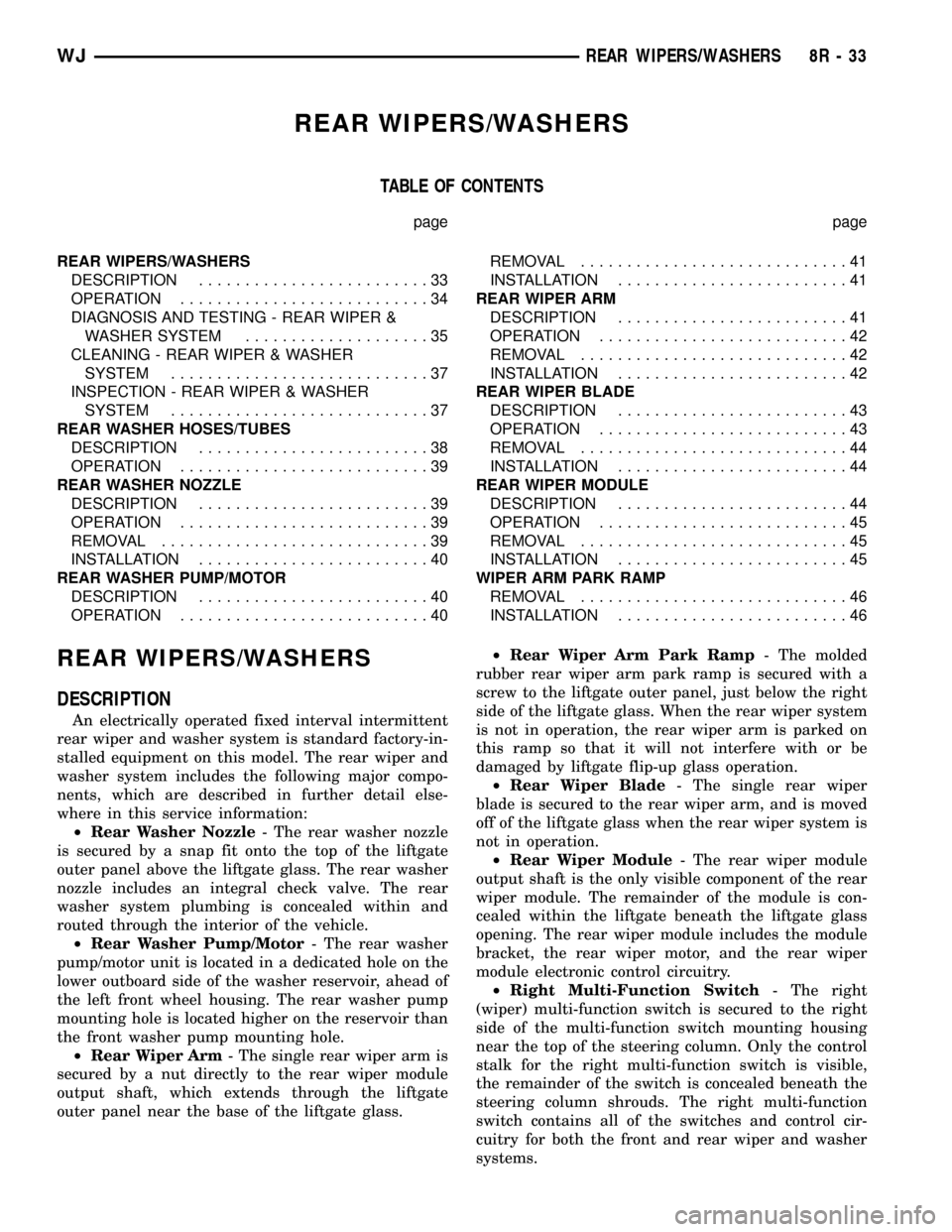
REAR WIPERS/WASHERS
TABLE OF CONTENTS
page page
REAR WIPERS/WASHERS
DESCRIPTION.........................33
OPERATION...........................34
DIAGNOSIS AND TESTING - REAR WIPER &
WASHER SYSTEM....................35
CLEANING - REAR WIPER & WASHER
SYSTEM............................37
INSPECTION - REAR WIPER & WASHER
SYSTEM............................37
REAR WASHER HOSES/TUBES
DESCRIPTION.........................38
OPERATION...........................39
REAR WASHER NOZZLE
DESCRIPTION.........................39
OPERATION...........................39
REMOVAL.............................39
INSTALLATION.........................40
REAR WASHER PUMP/MOTOR
DESCRIPTION.........................40
OPERATION...........................40REMOVAL.............................41
INSTALLATION.........................41
REAR WIPER ARM
DESCRIPTION.........................41
OPERATION...........................42
REMOVAL.............................42
INSTALLATION.........................42
REAR WIPER BLADE
DESCRIPTION.........................43
OPERATION...........................43
REMOVAL.............................44
INSTALLATION.........................44
REAR WIPER MODULE
DESCRIPTION.........................44
OPERATION...........................45
REMOVAL.............................45
INSTALLATION.........................45
WIPER ARM PARK RAMP
REMOVAL.............................46
INSTALLATION.........................46
REAR WIPERS/WASHERS
DESCRIPTION
An electrically operated fixed interval intermittent
rear wiper and washer system is standard factory-in-
stalled equipment on this model. The rear wiper and
washer system includes the following major compo-
nents, which are described in further detail else-
where in this service information:
²Rear Washer Nozzle- The rear washer nozzle
is secured by a snap fit onto the top of the liftgate
outer panel above the liftgate glass. The rear washer
nozzle includes an integral check valve. The rear
washer system plumbing is concealed within and
routed through the interior of the vehicle.
²Rear Washer Pump/Motor- The rear washer
pump/motor unit is located in a dedicated hole on the
lower outboard side of the washer reservoir, ahead of
the left front wheel housing. The rear washer pump
mounting hole is located higher on the reservoir than
the front washer pump mounting hole.
²Rear Wiper Arm- The single rear wiper arm is
secured by a nut directly to the rear wiper module
output shaft, which extends through the liftgate
outer panel near the base of the liftgate glass.²Rear Wiper Arm Park Ramp- The molded
rubber rear wiper arm park ramp is secured with a
screw to the liftgate outer panel, just below the right
side of the liftgate glass. When the rear wiper system
is not in operation, the rear wiper arm is parked on
this ramp so that it will not interfere with or be
damaged by liftgate flip-up glass operation.
²Rear Wiper Blade- The single rear wiper
blade is secured to the rear wiper arm, and is moved
off of the liftgate glass when the rear wiper system is
not in operation.
²Rear Wiper Module- The rear wiper module
output shaft is the only visible component of the rear
wiper module. The remainder of the module is con-
cealed within the liftgate beneath the liftgate glass
opening. The rear wiper module includes the module
bracket, the rear wiper motor, and the rear wiper
module electronic control circuitry.
²Right Multi-Function Switch- The right
(wiper) multi-function switch is secured to the right
side of the multi-function switch mounting housing
near the top of the steering column. Only the control
stalk for the right multi-function switch is visible,
the remainder of the switch is concealed beneath the
steering column shrouds. The right multi-function
switch contains all of the switches and control cir-
cuitry for both the front and rear wiper and washer
systems.
WJREAR WIPERS/WASHERS 8R - 33
Page 644 of 2199
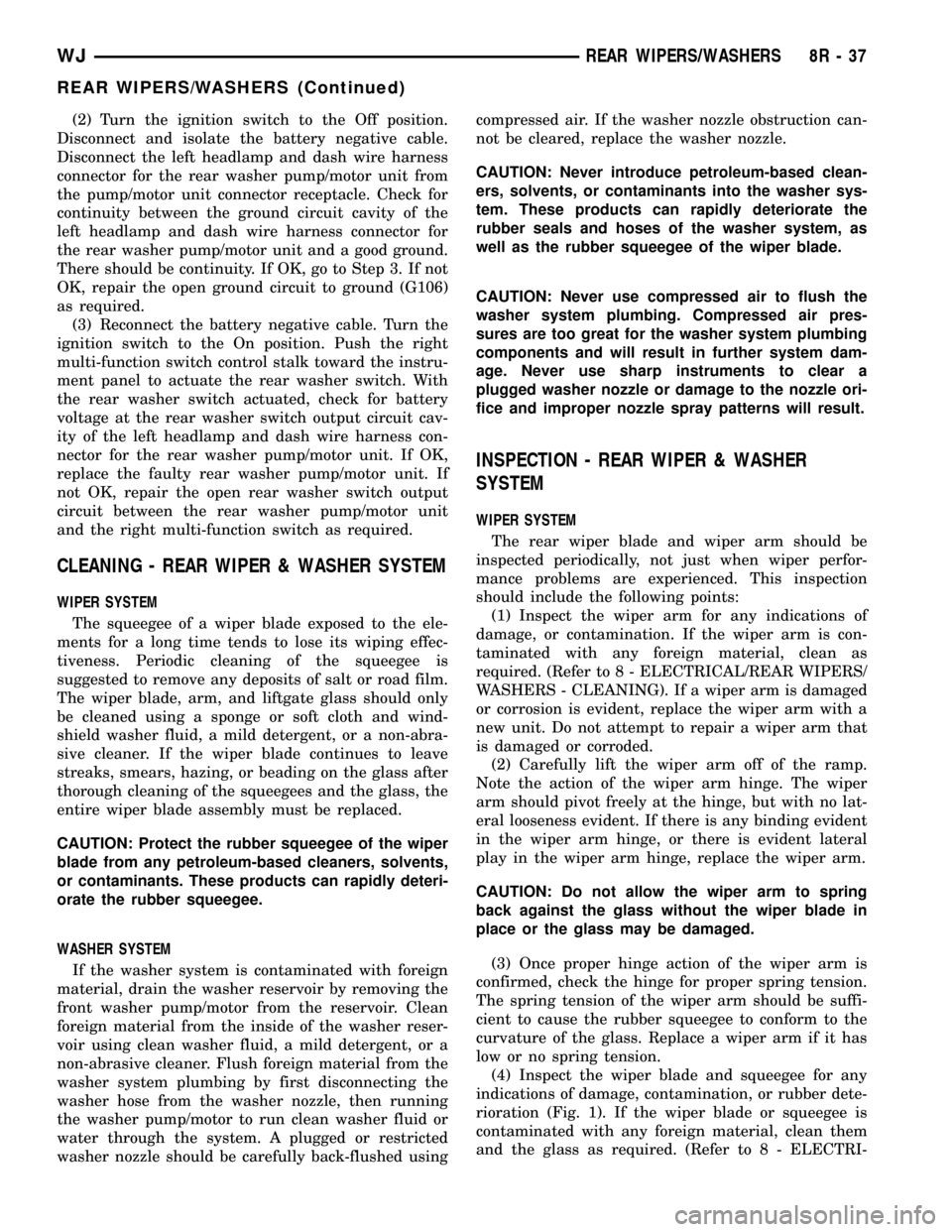
(2) Turn the ignition switch to the Off position.
Disconnect and isolate the battery negative cable.
Disconnect the left headlamp and dash wire harness
connector for the rear washer pump/motor unit from
the pump/motor unit connector receptacle. Check for
continuity between the ground circuit cavity of the
left headlamp and dash wire harness connector for
the rear washer pump/motor unit and a good ground.
There should be continuity. If OK, go to Step 3. If not
OK, repair the open ground circuit to ground (G106)
as required.
(3) Reconnect the battery negative cable. Turn the
ignition switch to the On position. Push the right
multi-function switch control stalk toward the instru-
ment panel to actuate the rear washer switch. With
the rear washer switch actuated, check for battery
voltage at the rear washer switch output circuit cav-
ity of the left headlamp and dash wire harness con-
nector for the rear washer pump/motor unit. If OK,
replace the faulty rear washer pump/motor unit. If
not OK, repair the open rear washer switch output
circuit between the rear washer pump/motor unit
and the right multi-function switch as required.
CLEANING - REAR WIPER & WASHER SYSTEM
WIPER SYSTEM
The squeegee of a wiper blade exposed to the ele-
ments for a long time tends to lose its wiping effec-
tiveness. Periodic cleaning of the squeegee is
suggested to remove any deposits of salt or road film.
The wiper blade, arm, and liftgate glass should only
be cleaned using a sponge or soft cloth and wind-
shield washer fluid, a mild detergent, or a non-abra-
sive cleaner. If the wiper blade continues to leave
streaks, smears, hazing, or beading on the glass after
thorough cleaning of the squeegees and the glass, the
entire wiper blade assembly must be replaced.
CAUTION: Protect the rubber squeegee of the wiper
blade from any petroleum-based cleaners, solvents,
or contaminants. These products can rapidly deteri-
orate the rubber squeegee.
WASHER SYSTEM
If the washer system is contaminated with foreign
material, drain the washer reservoir by removing the
front washer pump/motor from the reservoir. Clean
foreign material from the inside of the washer reser-
voir using clean washer fluid, a mild detergent, or a
non-abrasive cleaner. Flush foreign material from the
washer system plumbing by first disconnecting the
washer hose from the washer nozzle, then running
the washer pump/motor to run clean washer fluid or
water through the system. A plugged or restricted
washer nozzle should be carefully back-flushed usingcompressed air. If the washer nozzle obstruction can-
not be cleared, replace the washer nozzle.
CAUTION: Never introduce petroleum-based clean-
ers, solvents, or contaminants into the washer sys-
tem. These products can rapidly deteriorate the
rubber seals and hoses of the washer system, as
well as the rubber squeegee of the wiper blade.
CAUTION: Never use compressed air to flush the
washer system plumbing. Compressed air pres-
sures are too great for the washer system plumbing
components and will result in further system dam-
age. Never use sharp instruments to clear a
plugged washer nozzle or damage to the nozzle ori-
fice and improper nozzle spray patterns will result.
INSPECTION - REAR WIPER & WASHER
SYSTEM
WIPER SYSTEM
The rear wiper blade and wiper arm should be
inspected periodically, not just when wiper perfor-
mance problems are experienced. This inspection
should include the following points:
(1) Inspect the wiper arm for any indications of
damage, or contamination. If the wiper arm is con-
taminated with any foreign material, clean as
required. (Refer to 8 - ELECTRICAL/REAR WIPERS/
WASHERS - CLEANING). If a wiper arm is damaged
or corrosion is evident, replace the wiper arm with a
new unit. Do not attempt to repair a wiper arm that
is damaged or corroded.
(2) Carefully lift the wiper arm off of the ramp.
Note the action of the wiper arm hinge. The wiper
arm should pivot freely at the hinge, but with no lat-
eral looseness evident. If there is any binding evident
in the wiper arm hinge, or there is evident lateral
play in the wiper arm hinge, replace the wiper arm.
CAUTION: Do not allow the wiper arm to spring
back against the glass without the wiper blade in
place or the glass may be damaged.
(3) Once proper hinge action of the wiper arm is
confirmed, check the hinge for proper spring tension.
The spring tension of the wiper arm should be suffi-
cient to cause the rubber squeegee to conform to the
curvature of the glass. Replace a wiper arm if it has
low or no spring tension.
(4) Inspect the wiper blade and squeegee for any
indications of damage, contamination, or rubber dete-
rioration (Fig. 1). If the wiper blade or squeegee is
contaminated with any foreign material, clean them
and the glass as required. (Refer to 8 - ELECTRI-
WJREAR WIPERS/WASHERS 8R - 37
REAR WIPERS/WASHERS (Continued)
Page 649 of 2199
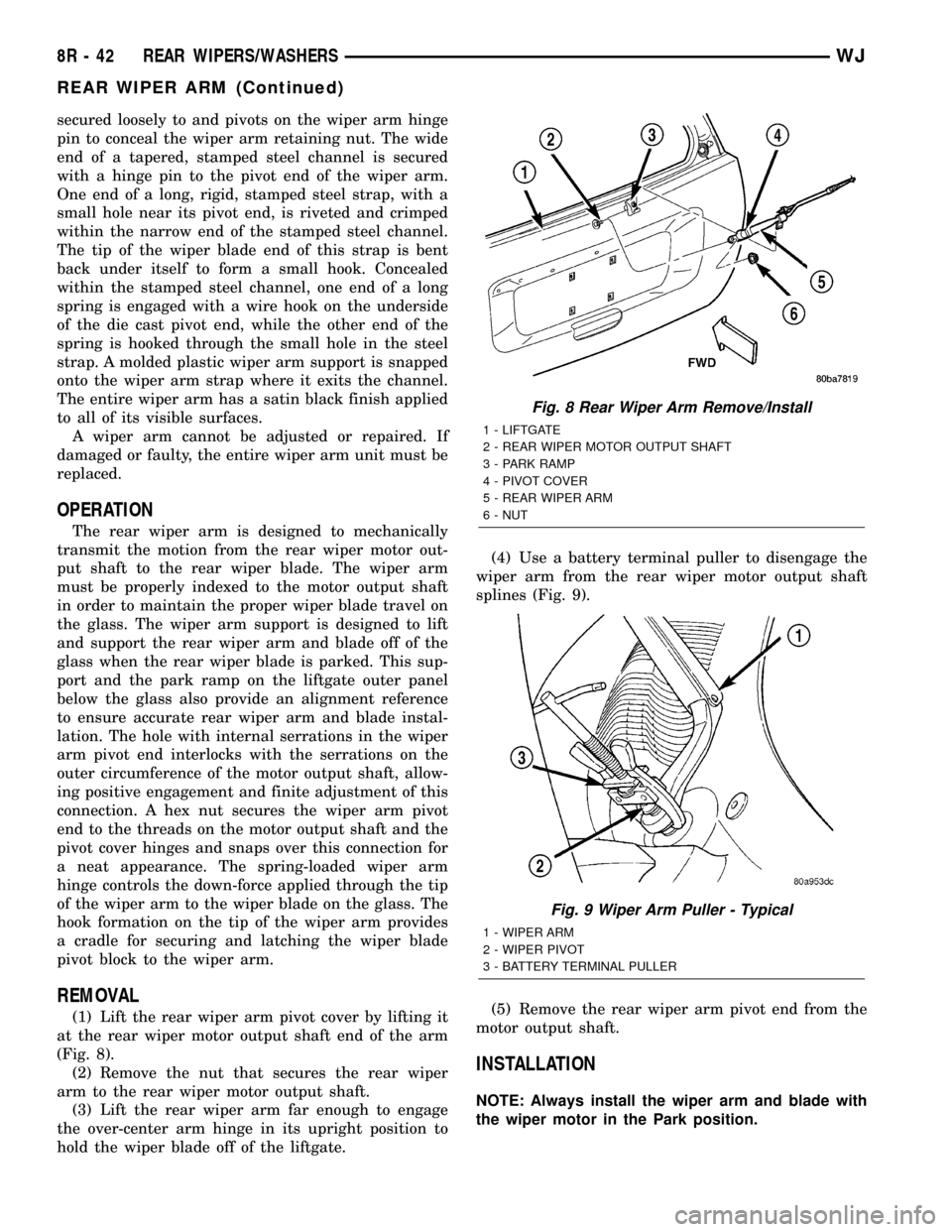
secured loosely to and pivots on the wiper arm hinge
pin to conceal the wiper arm retaining nut. The wide
end of a tapered, stamped steel channel is secured
with a hinge pin to the pivot end of the wiper arm.
One end of a long, rigid, stamped steel strap, with a
small hole near its pivot end, is riveted and crimped
within the narrow end of the stamped steel channel.
The tip of the wiper blade end of this strap is bent
back under itself to form a small hook. Concealed
within the stamped steel channel, one end of a long
spring is engaged with a wire hook on the underside
of the die cast pivot end, while the other end of the
spring is hooked through the small hole in the steel
strap. A molded plastic wiper arm support is snapped
onto the wiper arm strap where it exits the channel.
The entire wiper arm has a satin black finish applied
to all of its visible surfaces.
A wiper arm cannot be adjusted or repaired. If
damaged or faulty, the entire wiper arm unit must be
replaced.
OPERATION
The rear wiper arm is designed to mechanically
transmit the motion from the rear wiper motor out-
put shaft to the rear wiper blade. The wiper arm
must be properly indexed to the motor output shaft
in order to maintain the proper wiper blade travel on
the glass. The wiper arm support is designed to lift
and support the rear wiper arm and blade off of the
glass when the rear wiper blade is parked. This sup-
port and the park ramp on the liftgate outer panel
below the glass also provide an alignment reference
to ensure accurate rear wiper arm and blade instal-
lation. The hole with internal serrations in the wiper
arm pivot end interlocks with the serrations on the
outer circumference of the motor output shaft, allow-
ing positive engagement and finite adjustment of this
connection. A hex nut secures the wiper arm pivot
end to the threads on the motor output shaft and the
pivot cover hinges and snaps over this connection for
a neat appearance. The spring-loaded wiper arm
hinge controls the down-force applied through the tip
of the wiper arm to the wiper blade on the glass. The
hook formation on the tip of the wiper arm provides
a cradle for securing and latching the wiper blade
pivot block to the wiper arm.
REMOVAL
(1) Lift the rear wiper arm pivot cover by lifting it
at the rear wiper motor output shaft end of the arm
(Fig. 8).
(2) Remove the nut that secures the rear wiper
arm to the rear wiper motor output shaft.
(3) Lift the rear wiper arm far enough to engage
the over-center arm hinge in its upright position to
hold the wiper blade off of the liftgate.(4) Use a battery terminal puller to disengage the
wiper arm from the rear wiper motor output shaft
splines (Fig. 9).
(5) Remove the rear wiper arm pivot end from the
motor output shaft.
INSTALLATION
NOTE: Always install the wiper arm and blade with
the wiper motor in the Park position.
Fig. 8 Rear Wiper Arm Remove/Install
1 - LIFTGATE
2 - REAR WIPER MOTOR OUTPUT SHAFT
3 - PARK RAMP
4 - PIVOT COVER
5 - REAR WIPER ARM
6 - NUT
Fig. 9 Wiper Arm Puller - Typical
1 - WIPER ARM
2 - WIPER PIVOT
3 - BATTERY TERMINAL PULLER
8R - 42 REAR WIPERS/WASHERSWJ
REAR WIPER ARM (Continued)
Page 652 of 2199
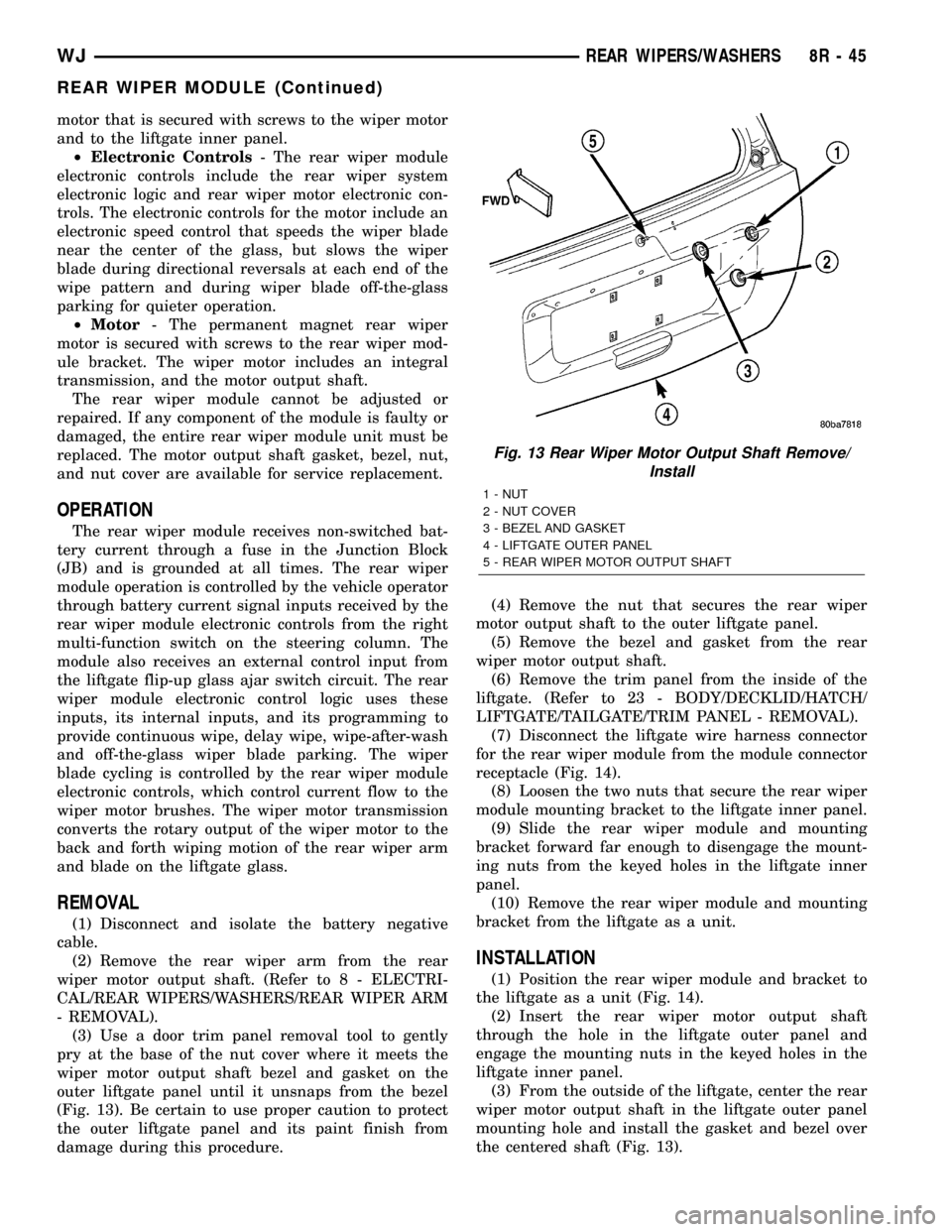
motor that is secured with screws to the wiper motor
and to the liftgate inner panel.
²Electronic Controls- The rear wiper module
electronic controls include the rear wiper system
electronic logic and rear wiper motor electronic con-
trols. The electronic controls for the motor include an
electronic speed control that speeds the wiper blade
near the center of the glass, but slows the wiper
blade during directional reversals at each end of the
wipe pattern and during wiper blade off-the-glass
parking for quieter operation.
²Motor- The permanent magnet rear wiper
motor is secured with screws to the rear wiper mod-
ule bracket. The wiper motor includes an integral
transmission, and the motor output shaft.
The rear wiper module cannot be adjusted or
repaired. If any component of the module is faulty or
damaged, the entire rear wiper module unit must be
replaced. The motor output shaft gasket, bezel, nut,
and nut cover are available for service replacement.
OPERATION
The rear wiper module receives non-switched bat-
tery current through a fuse in the Junction Block
(JB) and is grounded at all times. The rear wiper
module operation is controlled by the vehicle operator
through battery current signal inputs received by the
rear wiper module electronic controls from the right
multi-function switch on the steering column. The
module also receives an external control input from
the liftgate flip-up glass ajar switch circuit. The rear
wiper module electronic control logic uses these
inputs, its internal inputs, and its programming to
provide continuous wipe, delay wipe, wipe-after-wash
and off-the-glass wiper blade parking. The wiper
blade cycling is controlled by the rear wiper module
electronic controls, which control current flow to the
wiper motor brushes. The wiper motor transmission
converts the rotary output of the wiper motor to the
back and forth wiping motion of the rear wiper arm
and blade on the liftgate glass.
REMOVAL
(1) Disconnect and isolate the battery negative
cable.
(2) Remove the rear wiper arm from the rear
wiper motor output shaft. (Refer to 8 - ELECTRI-
CAL/REAR WIPERS/WASHERS/REAR WIPER ARM
- REMOVAL).
(3) Use a door trim panel removal tool to gently
pry at the base of the nut cover where it meets the
wiper motor output shaft bezel and gasket on the
outer liftgate panel until it unsnaps from the bezel
(Fig. 13). Be certain to use proper caution to protect
the outer liftgate panel and its paint finish from
damage during this procedure.(4) Remove the nut that secures the rear wiper
motor output shaft to the outer liftgate panel.
(5) Remove the bezel and gasket from the rear
wiper motor output shaft.
(6) Remove the trim panel from the inside of the
liftgate. (Refer to 23 - BODY/DECKLID/HATCH/
LIFTGATE/TAILGATE/TRIM PANEL - REMOVAL).
(7) Disconnect the liftgate wire harness connector
for the rear wiper module from the module connector
receptacle (Fig. 14).
(8) Loosen the two nuts that secure the rear wiper
module mounting bracket to the liftgate inner panel.
(9) Slide the rear wiper module and mounting
bracket forward far enough to disengage the mount-
ing nuts from the keyed holes in the liftgate inner
panel.
(10) Remove the rear wiper module and mounting
bracket from the liftgate as a unit.
INSTALLATION
(1) Position the rear wiper module and bracket to
the liftgate as a unit (Fig. 14).
(2) Insert the rear wiper motor output shaft
through the hole in the liftgate outer panel and
engage the mounting nuts in the keyed holes in the
liftgate inner panel.
(3) From the outside of the liftgate, center the rear
wiper motor output shaft in the liftgate outer panel
mounting hole and install the gasket and bezel over
the centered shaft (Fig. 13).
Fig. 13 Rear Wiper Motor Output Shaft Remove/
Install
1 - NUT
2 - NUT COVER
3 - BEZEL AND GASKET
4 - LIFTGATE OUTER PANEL
5 - REAR WIPER MOTOR OUTPUT SHAFT
WJREAR WIPERS/WASHERS 8R - 45
REAR WIPER MODULE (Continued)
Page 1177 of 2199
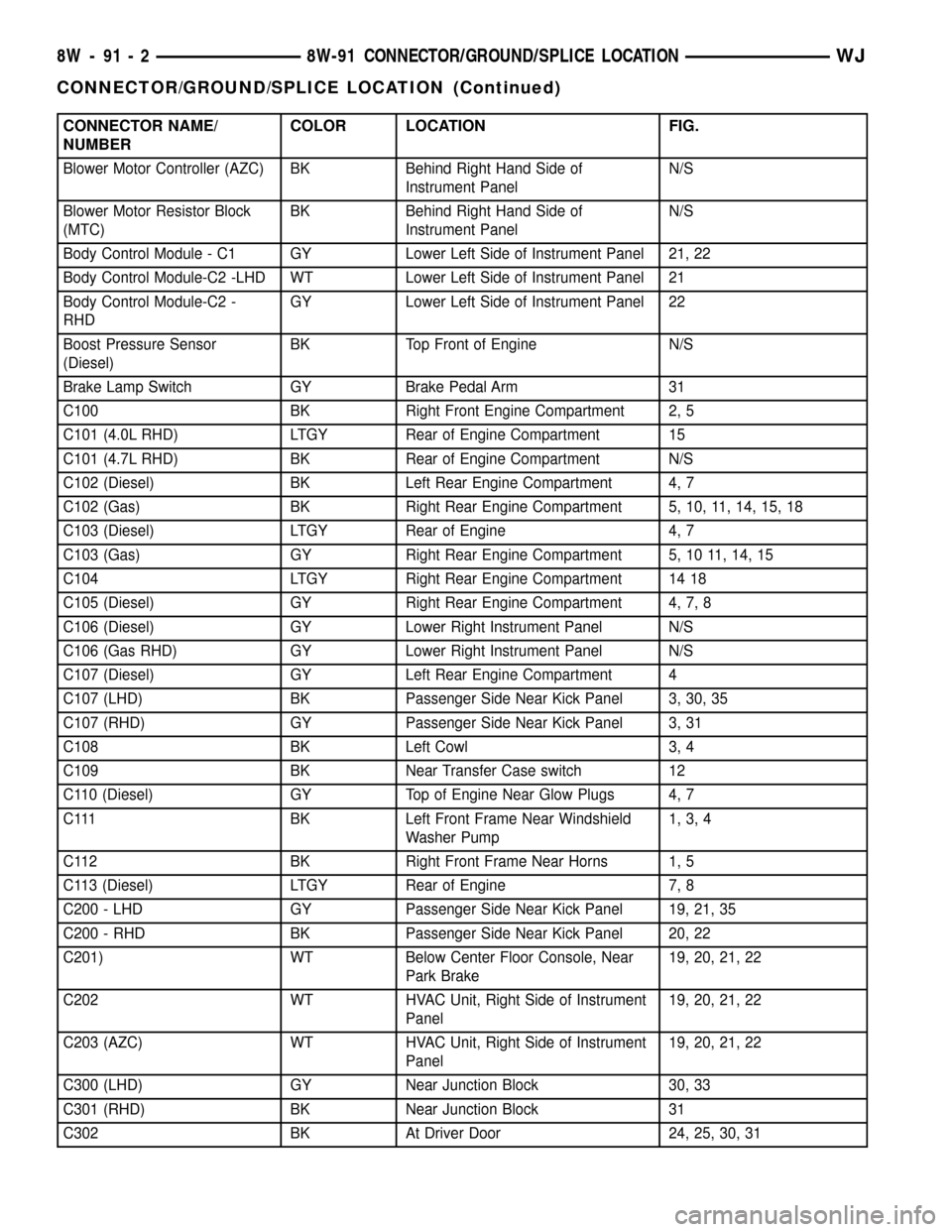
CONNECTOR NAME/
NUMBERCOLOR LOCATION FIG.
Blower Motor Controller (AZC) BK Behind Right Hand Side of
Instrument PanelN/S
Blower Motor Resistor Block
(MTC)BK Behind Right Hand Side of
Instrument PanelN/S
Body Control Module - C1 GY Lower Left Side of Instrument Panel 21, 22
Body Control Module-C2 -LHD WT Lower Left Side of Instrument Panel 21
Body Control Module-C2 -
RHDGY Lower Left Side of Instrument Panel 22
Boost Pressure Sensor
(Diesel)BK Top Front of Engine N/S
Brake Lamp Switch GY Brake Pedal Arm 31
C100 BK Right Front Engine Compartment 2, 5
C101 (4.0L RHD) LTGY Rear of Engine Compartment 15
C101 (4.7L RHD) BK Rear of Engine Compartment N/S
C102 (Diesel) BK Left Rear Engine Compartment 4, 7
C102 (Gas) BK Right Rear Engine Compartment 5, 10, 11, 14, 15, 18
C103 (Diesel) LTGY Rear of Engine 4, 7
C103 (Gas) GY Right Rear Engine Compartment 5, 10 11, 14, 15
C104 LTGY Right Rear Engine Compartment 14 18
C105 (Diesel) GY Right Rear Engine Compartment 4, 7, 8
C106 (Diesel) GY Lower Right Instrument Panel N/S
C106 (Gas RHD) GY Lower Right Instrument Panel N/S
C107 (Diesel) GY Left Rear Engine Compartment 4
C107 (LHD) BK Passenger Side Near Kick Panel 3, 30, 35
C107 (RHD) GY Passenger Side Near Kick Panel 3, 31
C108 BK Left Cowl 3, 4
C109 BK Near Transfer Case switch 12
C110 (Diesel) GY Top of Engine Near Glow Plugs 4, 7
C111 BK Left Front Frame Near Windshield
Washer Pump1, 3, 4
C112 BK Right Front Frame Near Horns 1, 5
C113 (Diesel) LTGY Rear of Engine 7, 8
C200 - LHD GY Passenger Side Near Kick Panel 19, 21, 35
C200 - RHD BK Passenger Side Near Kick Panel 20, 22
C201) WT Below Center Floor Console, Near
Park Brake19, 20, 21, 22
C202 WT HVAC Unit, Right Side of Instrument
Panel19, 20, 21, 22
C203 (AZC) WT HVAC Unit, Right Side of Instrument
Panel19, 20, 21, 22
C300 (LHD) GY Near Junction Block 30, 33
C301 (RHD) BK Near Junction Block 31
C302 BK At Driver Door 24, 25, 30, 31
8W - 91 - 2 8W-91 CONNECTOR/GROUND/SPLICE LOCATIONWJ
CONNECTOR/GROUND/SPLICE LOCATION (Continued)
Page 1259 of 2199
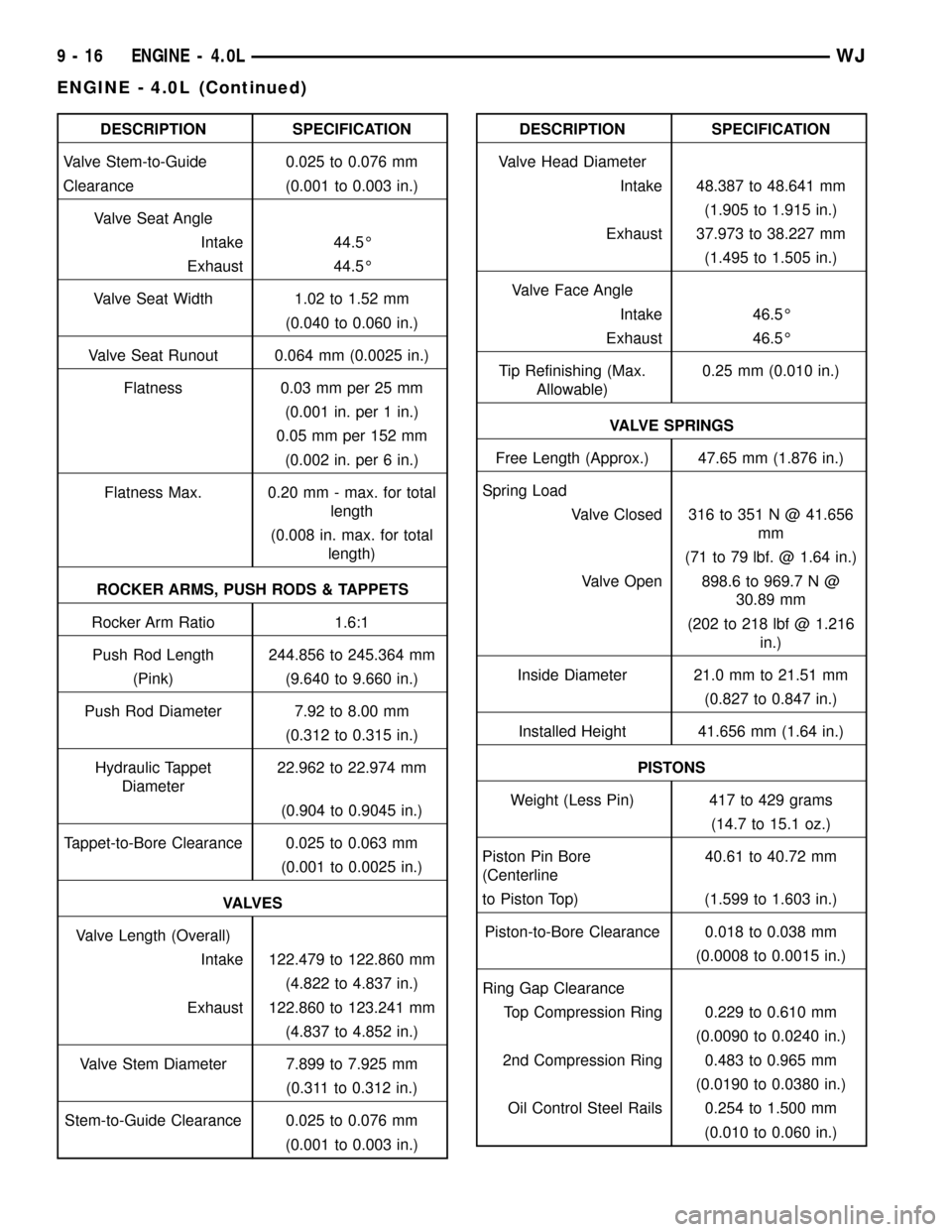
DESCRIPTION SPECIFICATION
Valve Stem-to-Guide 0.025 to 0.076 mm
Clearance (0.001 to 0.003 in.)
Valve Seat Angle
Intake 44.5É
Exhaust 44.5É
Valve Seat Width 1.02 to 1.52 mm
(0.040 to 0.060 in.)
Valve Seat Runout 0.064 mm (0.0025 in.)
Flatness 0.03 mm per 25 mm
(0.001 in. per 1 in.)
0.05 mm per 152 mm
(0.002 in. per 6 in.)
Flatness Max. 0.20 mm - max. for total
length
(0.008 in. max. for total
length)
ROCKER ARMS, PUSH RODS & TAPPETS
Rocker Arm Ratio 1.6:1
Push Rod Length 244.856 to 245.364 mm
(Pink) (9.640 to 9.660 in.)
Push Rod Diameter 7.92 to 8.00 mm
(0.312 to 0.315 in.)
Hydraulic Tappet
Diameter22.962 to 22.974 mm
(0.904 to 0.9045 in.)
Tappet-to-Bore Clearance 0.025 to 0.063 mm
(0.001 to 0.0025 in.)
VA LV E S
Valve Length (Overall)
Intake 122.479 to 122.860 mm
(4.822 to 4.837 in.)
Exhaust 122.860 to 123.241 mm
(4.837 to 4.852 in.)
Valve Stem Diameter 7.899 to 7.925 mm
(0.311 to 0.312 in.)
Stem-to-Guide Clearance 0.025 to 0.076 mm
(0.001 to 0.003 in.)DESCRIPTION SPECIFICATION
Valve Head Diameter
Intake 48.387 to 48.641 mm
(1.905 to 1.915 in.)
Exhaust 37.973 to 38.227 mm
(1.495 to 1.505 in.)
Valve Face Angle
Intake 46.5É
Exhaust 46.5É
Tip Refinishing (Max.
Allowable)0.25 mm (0.010 in.)
VALVE SPRINGS
Free Length (Approx.) 47.65 mm (1.876 in.)
Spring Load
Valve Closed 316 to 351 N @ 41.656
mm
(71 to 79 lbf. @ 1.64 in.)
Valve Open 898.6 to 969.7 N @
30.89 mm
(202 to 218 lbf @ 1.216
in.)
Inside Diameter 21.0 mm to 21.51 mm
(0.827 to 0.847 in.)
Installed Height 41.656 mm (1.64 in.)
PISTONS
Weight (Less Pin) 417 to 429 grams
(14.7 to 15.1 oz.)
Piston Pin Bore
(Centerline40.61 to 40.72 mm
to Piston Top) (1.599 to 1.603 in.)
Piston-to-Bore Clearance 0.018 to 0.038 mm
(0.0008 to 0.0015 in.)
Ring Gap Clearance
Top Compression Ring 0.229 to 0.610 mm
(0.0090 to 0.0240 in.)
2nd Compression Ring 0.483 to 0.965 mm
(0.0190 to 0.0380 in.)
Oil Control Steel Rails 0.254 to 1.500 mm
(0.010 to 0.060 in.)
9 - 16 ENGINE - 4.0LWJ
ENGINE - 4.0L (Continued)
Page 1263 of 2199
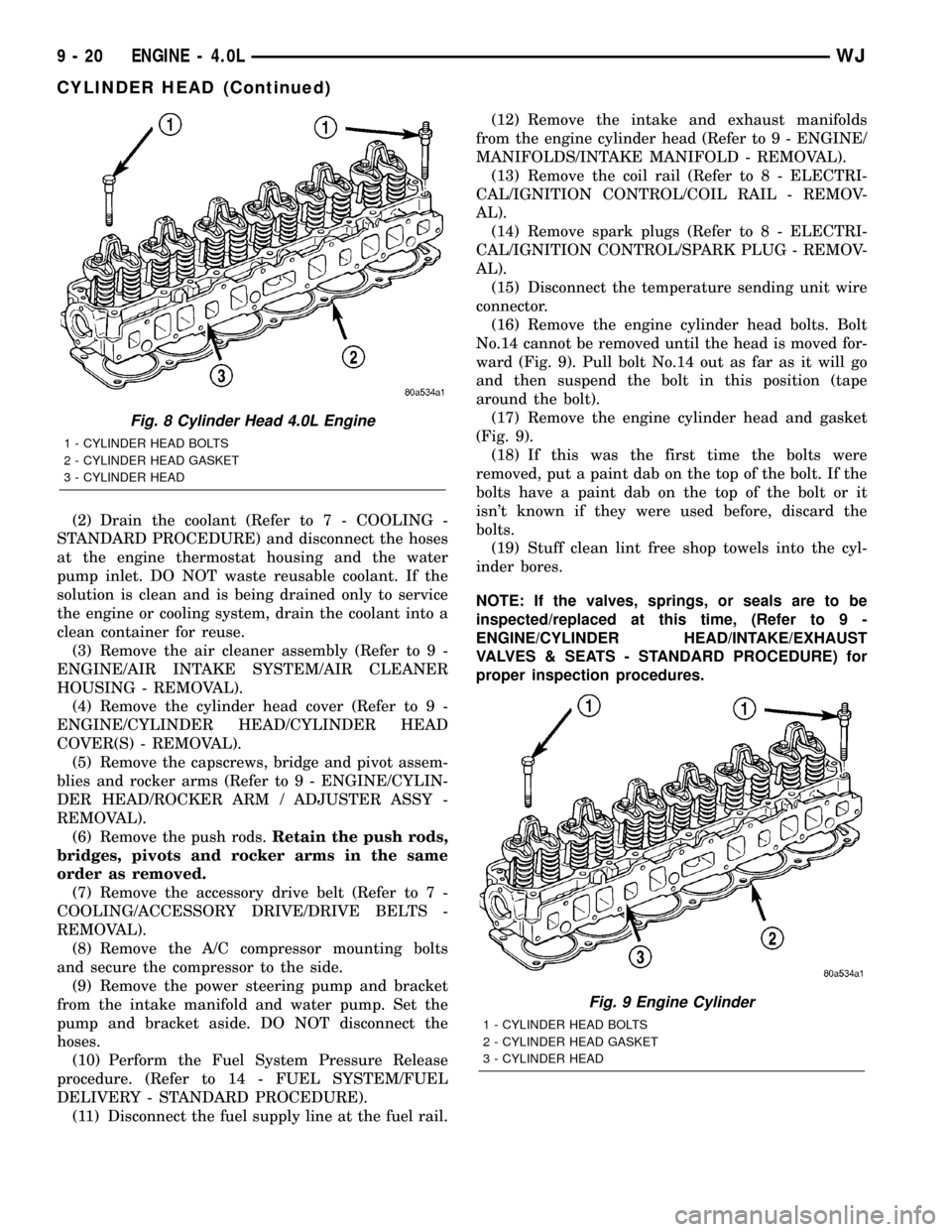
(2) Drain the coolant (Refer to 7 - COOLING -
STANDARD PROCEDURE) and disconnect the hoses
at the engine thermostat housing and the water
pump inlet. DO NOT waste reusable coolant. If the
solution is clean and is being drained only to service
the engine or cooling system, drain the coolant into a
clean container for reuse.
(3) Remove the air cleaner assembly (Refer to 9 -
ENGINE/AIR INTAKE SYSTEM/AIR CLEANER
HOUSING - REMOVAL).
(4) Remove the cylinder head cover (Refer to 9 -
ENGINE/CYLINDER HEAD/CYLINDER HEAD
COVER(S) - REMOVAL).
(5) Remove the capscrews, bridge and pivot assem-
blies and rocker arms (Refer to 9 - ENGINE/CYLIN-
DER HEAD/ROCKER ARM / ADJUSTER ASSY -
REMOVAL).
(6) Remove the push rods.Retain the push rods,
bridges, pivots and rocker arms in the same
order as removed.
(7) Remove the accessory drive belt (Refer to 7 -
COOLING/ACCESSORY DRIVE/DRIVE BELTS -
REMOVAL).
(8) Remove the A/C compressor mounting bolts
and secure the compressor to the side.
(9) Remove the power steering pump and bracket
from the intake manifold and water pump. Set the
pump and bracket aside. DO NOT disconnect the
hoses.
(10) Perform the Fuel System Pressure Release
procedure. (Refer to 14 - FUEL SYSTEM/FUEL
DELIVERY - STANDARD PROCEDURE).
(11) Disconnect the fuel supply line at the fuel rail.(12) Remove the intake and exhaust manifolds
from the engine cylinder head (Refer to 9 - ENGINE/
MANIFOLDS/INTAKE MANIFOLD - REMOVAL).
(13) Remove the coil rail (Refer to 8 - ELECTRI-
CAL/IGNITION CONTROL/COIL RAIL - REMOV-
AL).
(14) Remove spark plugs (Refer to 8 - ELECTRI-
CAL/IGNITION CONTROL/SPARK PLUG - REMOV-
AL).
(15) Disconnect the temperature sending unit wire
connector.
(16) Remove the engine cylinder head bolts. Bolt
No.14 cannot be removed until the head is moved for-
ward (Fig. 9). Pull bolt No.14 out as far as it will go
and then suspend the bolt in this position (tape
around the bolt).
(17) Remove the engine cylinder head and gasket
(Fig. 9).
(18) If this was the first time the bolts were
removed, put a paint dab on the top of the bolt. If the
bolts have a paint dab on the top of the bolt or it
isn't known if they were used before, discard the
bolts.
(19) Stuff clean lint free shop towels into the cyl-
inder bores.
NOTE: If the valves, springs, or seals are to be
inspected/replaced at this time, (Refer to 9 -
ENGINE/CYLINDER HEAD/INTAKE/EXHAUST
VALVES & SEATS - STANDARD PROCEDURE) for
proper inspection procedures.
Fig. 8 Cylinder Head 4.0L Engine
1 - CYLINDER HEAD BOLTS
2 - CYLINDER HEAD GASKET
3 - CYLINDER HEAD
Fig. 9 Engine Cylinder
1 - CYLINDER HEAD BOLTS
2 - CYLINDER HEAD GASKET
3 - CYLINDER HEAD
9 - 20 ENGINE - 4.0LWJ
CYLINDER HEAD (Continued)