Speed control JEEP GRAND CHEROKEE 2002 WJ / 2.G Repair Manual
[x] Cancel search | Manufacturer: JEEP, Model Year: 2002, Model line: GRAND CHEROKEE, Model: JEEP GRAND CHEROKEE 2002 WJ / 2.GPages: 2199, PDF Size: 76.01 MB
Page 456 of 2199
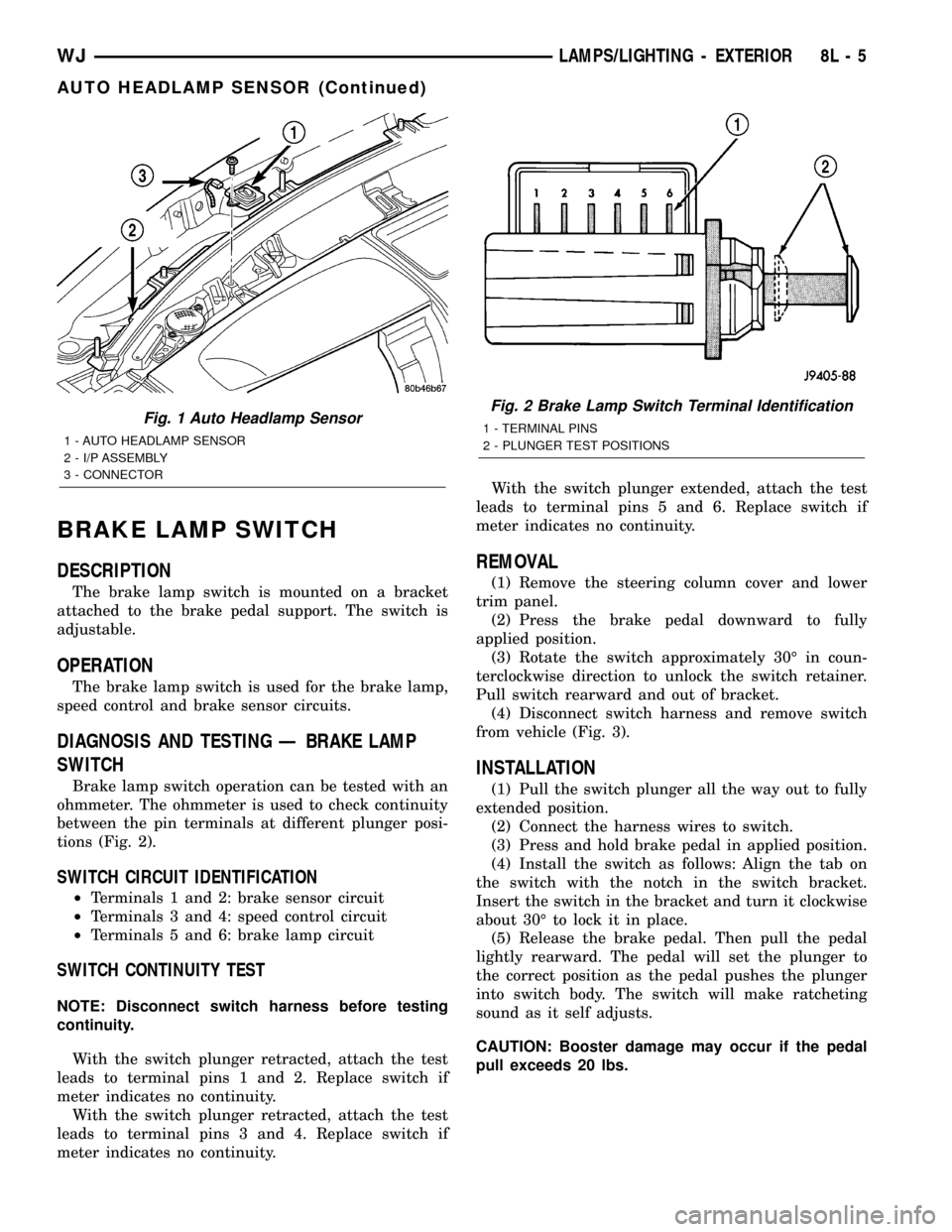
BRAKE LAMP SWITCH
DESCRIPTION
The brake lamp switch is mounted on a bracket
attached to the brake pedal support. The switch is
adjustable.
OPERATION
The brake lamp switch is used for the brake lamp,
speed control and brake sensor circuits.
DIAGNOSIS AND TESTING Ð BRAKE LAMP
SWITCH
Brake lamp switch operation can be tested with an
ohmmeter. The ohmmeter is used to check continuity
between the pin terminals at different plunger posi-
tions (Fig. 2).
SWITCH CIRCUIT IDENTIFICATION
²Terminals 1 and 2: brake sensor circuit
²Terminals 3 and 4: speed control circuit
²Terminals 5 and 6: brake lamp circuit
SWITCH CONTINUITY TEST
NOTE: Disconnect switch harness before testing
continuity.
With the switch plunger retracted, attach the test
leads to terminal pins 1 and 2. Replace switch if
meter indicates no continuity.
With the switch plunger retracted, attach the test
leads to terminal pins 3 and 4. Replace switch if
meter indicates no continuity.With the switch plunger extended, attach the test
leads to terminal pins 5 and 6. Replace switch if
meter indicates no continuity.
REMOVAL
(1) Remove the steering column cover and lower
trim panel.
(2) Press the brake pedal downward to fully
applied position.
(3) Rotate the switch approximately 30É in coun-
terclockwise direction to unlock the switch retainer.
Pull switch rearward and out of bracket.
(4) Disconnect switch harness and remove switch
from vehicle (Fig. 3).
INSTALLATION
(1) Pull the switch plunger all the way out to fully
extended position.
(2) Connect the harness wires to switch.
(3) Press and hold brake pedal in applied position.
(4) Install the switch as follows: Align the tab on
the switch with the notch in the switch bracket.
Insert the switch in the bracket and turn it clockwise
about 30É to lock it in place.
(5) Release the brake pedal. Then pull the pedal
lightly rearward. The pedal will set the plunger to
the correct position as the pedal pushes the plunger
into switch body. The switch will make ratcheting
sound as it self adjusts.
CAUTION: Booster damage may occur if the pedal
pull exceeds 20 lbs.
Fig. 1 Auto Headlamp Sensor
1 - AUTO HEADLAMP SENSOR
2 - I/P ASSEMBLY
3 - CONNECTOR
Fig. 2 Brake Lamp Switch Terminal Identification
1 - TERMINAL PINS
2 - PLUNGER TEST POSITIONS
WJLAMPS/LIGHTING - EXTERIOR 8L - 5
AUTO HEADLAMP SENSOR (Continued)
Page 491 of 2199
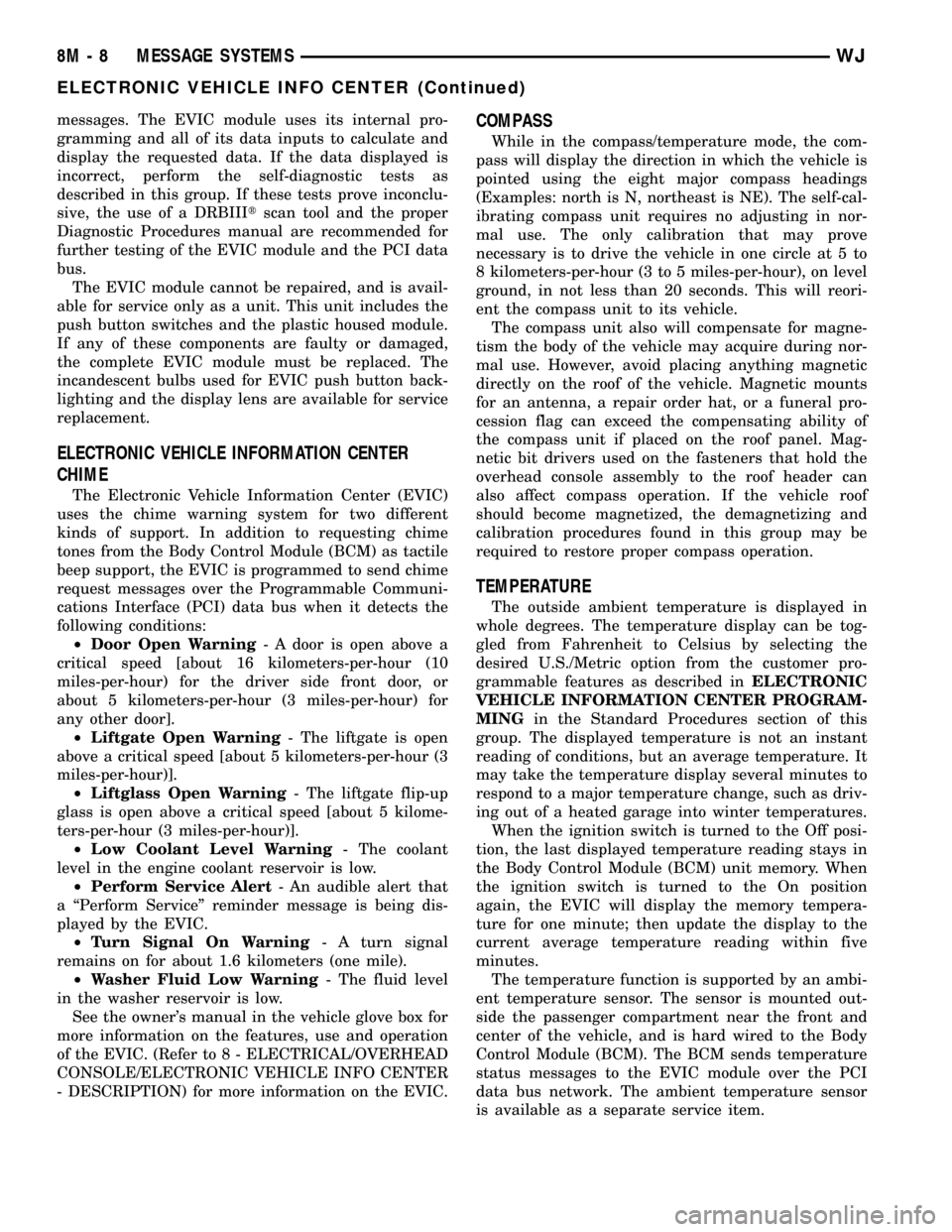
messages. The EVIC module uses its internal pro-
gramming and all of its data inputs to calculate and
display the requested data. If the data displayed is
incorrect, perform the self-diagnostic tests as
described in this group. If these tests prove inconclu-
sive, the use of a DRBIIItscan tool and the proper
Diagnostic Procedures manual are recommended for
further testing of the EVIC module and the PCI data
bus.
The EVIC module cannot be repaired, and is avail-
able for service only as a unit. This unit includes the
push button switches and the plastic housed module.
If any of these components are faulty or damaged,
the complete EVIC module must be replaced. The
incandescent bulbs used for EVIC push button back-
lighting and the display lens are available for service
replacement.
ELECTRONIC VEHICLE INFORMATION CENTER
CHIME
The Electronic Vehicle Information Center (EVIC)
uses the chime warning system for two different
kinds of support. In addition to requesting chime
tones from the Body Control Module (BCM) as tactile
beep support, the EVIC is programmed to send chime
request messages over the Programmable Communi-
cations Interface (PCI) data bus when it detects the
following conditions:
²Door Open Warning- A door is open above a
critical speed [about 16 kilometers-per-hour (10
miles-per-hour) for the driver side front door, or
about 5 kilometers-per-hour (3 miles-per-hour) for
any other door].
²Liftgate Open Warning- The liftgate is open
above a critical speed [about 5 kilometers-per-hour (3
miles-per-hour)].
²Liftglass Open Warning- The liftgate flip-up
glass is open above a critical speed [about 5 kilome-
ters-per-hour (3 miles-per-hour)].
²Low Coolant Level Warning- The coolant
level in the engine coolant reservoir is low.
²Perform Service Alert- An audible alert that
a ªPerform Serviceº reminder message is being dis-
played by the EVIC.
²Turn Signal On Warning- A turn signal
remains on for about 1.6 kilometers (one mile).
²Washer Fluid Low Warning- The fluid level
in the washer reservoir is low.
See the owner's manual in the vehicle glove box for
more information on the features, use and operation
of the EVIC. (Refer to 8 - ELECTRICAL/OVERHEAD
CONSOLE/ELECTRONIC VEHICLE INFO CENTER
- DESCRIPTION) for more information on the EVIC.
COMPASS
While in the compass/temperature mode, the com-
pass will display the direction in which the vehicle is
pointed using the eight major compass headings
(Examples: north is N, northeast is NE). The self-cal-
ibrating compass unit requires no adjusting in nor-
mal use. The only calibration that may prove
necessary is to drive the vehicle in one circle at 5 to
8 kilometers-per-hour (3 to 5 miles-per-hour), on level
ground, in not less than 20 seconds. This will reori-
ent the compass unit to its vehicle.
The compass unit also will compensate for magne-
tism the body of the vehicle may acquire during nor-
mal use. However, avoid placing anything magnetic
directly on the roof of the vehicle. Magnetic mounts
for an antenna, a repair order hat, or a funeral pro-
cession flag can exceed the compensating ability of
the compass unit if placed on the roof panel. Mag-
netic bit drivers used on the fasteners that hold the
overhead console assembly to the roof header can
also affect compass operation. If the vehicle roof
should become magnetized, the demagnetizing and
calibration procedures found in this group may be
required to restore proper compass operation.
TEMPERATURE
The outside ambient temperature is displayed in
whole degrees. The temperature display can be tog-
gled from Fahrenheit to Celsius by selecting the
desired U.S./Metric option from the customer pro-
grammable features as described inELECTRONIC
VEHICLE INFORMATION CENTER PROGRAM-
MINGin the Standard Procedures section of this
group. The displayed temperature is not an instant
reading of conditions, but an average temperature. It
may take the temperature display several minutes to
respond to a major temperature change, such as driv-
ing out of a heated garage into winter temperatures.
When the ignition switch is turned to the Off posi-
tion, the last displayed temperature reading stays in
the Body Control Module (BCM) unit memory. When
the ignition switch is turned to the On position
again, the EVIC will display the memory tempera-
ture for one minute; then update the display to the
current average temperature reading within five
minutes.
The temperature function is supported by an ambi-
ent temperature sensor. The sensor is mounted out-
side the passenger compartment near the front and
center of the vehicle, and is hard wired to the Body
Control Module (BCM). The BCM sends temperature
status messages to the EVIC module over the PCI
data bus network. The ambient temperature sensor
is available as a separate service item.
8M - 8 MESSAGE SYSTEMSWJ
ELECTRONIC VEHICLE INFO CENTER (Continued)
Page 499 of 2199
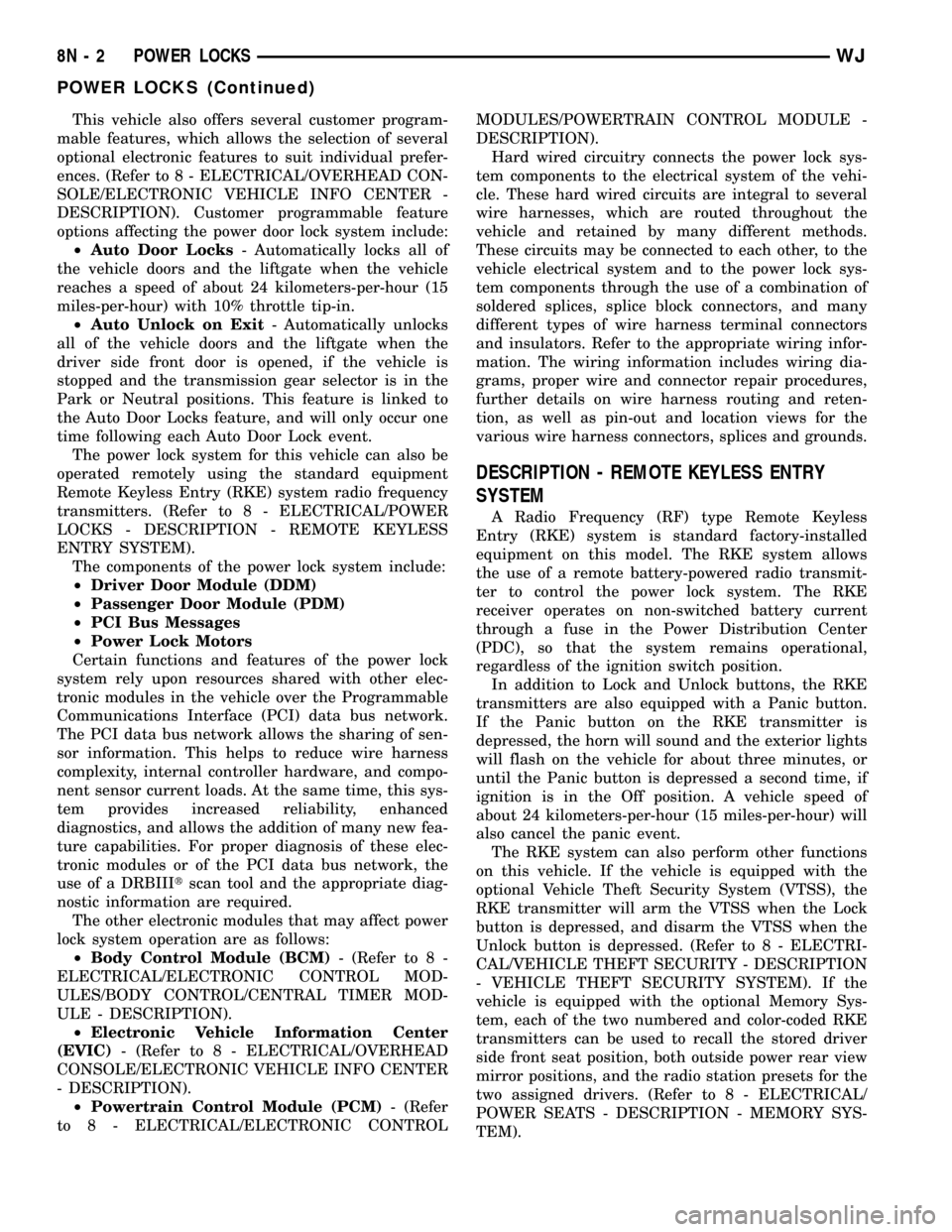
This vehicle also offers several customer program-
mable features, which allows the selection of several
optional electronic features to suit individual prefer-
ences. (Refer to 8 - ELECTRICAL/OVERHEAD CON-
SOLE/ELECTRONIC VEHICLE INFO CENTER -
DESCRIPTION). Customer programmable feature
options affecting the power door lock system include:
²Auto Door Locks- Automatically locks all of
the vehicle doors and the liftgate when the vehicle
reaches a speed of about 24 kilometers-per-hour (15
miles-per-hour) with 10% throttle tip-in.
²Auto Unlock on Exit- Automatically unlocks
all of the vehicle doors and the liftgate when the
driver side front door is opened, if the vehicle is
stopped and the transmission gear selector is in the
Park or Neutral positions. This feature is linked to
the Auto Door Locks feature, and will only occur one
time following each Auto Door Lock event.
The power lock system for this vehicle can also be
operated remotely using the standard equipment
Remote Keyless Entry (RKE) system radio frequency
transmitters. (Refer to 8 - ELECTRICAL/POWER
LOCKS - DESCRIPTION - REMOTE KEYLESS
ENTRY SYSTEM).
The components of the power lock system include:
²Driver Door Module (DDM)
²Passenger Door Module (PDM)
²PCI Bus Messages
²Power Lock Motors
Certain functions and features of the power lock
system rely upon resources shared with other elec-
tronic modules in the vehicle over the Programmable
Communications Interface (PCI) data bus network.
The PCI data bus network allows the sharing of sen-
sor information. This helps to reduce wire harness
complexity, internal controller hardware, and compo-
nent sensor current loads. At the same time, this sys-
tem provides increased reliability, enhanced
diagnostics, and allows the addition of many new fea-
ture capabilities. For proper diagnosis of these elec-
tronic modules or of the PCI data bus network, the
use of a DRBIIItscan tool and the appropriate diag-
nostic information are required.
The other electronic modules that may affect power
lock system operation are as follows:
²Body Control Module (BCM)- (Refer to 8 -
ELECTRICAL/ELECTRONIC CONTROL MOD-
ULES/BODY CONTROL/CENTRAL TIMER MOD-
ULE - DESCRIPTION).
²Electronic Vehicle Information Center
(EVIC)- (Refer to 8 - ELECTRICAL/OVERHEAD
CONSOLE/ELECTRONIC VEHICLE INFO CENTER
- DESCRIPTION).
²Powertrain Control Module (PCM)- (Refer
to 8 - ELECTRICAL/ELECTRONIC CONTROLMODULES/POWERTRAIN CONTROL MODULE -
DESCRIPTION).
Hard wired circuitry connects the power lock sys-
tem components to the electrical system of the vehi-
cle. These hard wired circuits are integral to several
wire harnesses, which are routed throughout the
vehicle and retained by many different methods.
These circuits may be connected to each other, to the
vehicle electrical system and to the power lock sys-
tem components through the use of a combination of
soldered splices, splice block connectors, and many
different types of wire harness terminal connectors
and insulators. Refer to the appropriate wiring infor-
mation. The wiring information includes wiring dia-
grams, proper wire and connector repair procedures,
further details on wire harness routing and reten-
tion, as well as pin-out and location views for the
various wire harness connectors, splices and grounds.
DESCRIPTION - REMOTE KEYLESS ENTRY
SYSTEM
A Radio Frequency (RF) type Remote Keyless
Entry (RKE) system is standard factory-installed
equipment on this model. The RKE system allows
the use of a remote battery-powered radio transmit-
ter to control the power lock system. The RKE
receiver operates on non-switched battery current
through a fuse in the Power Distribution Center
(PDC), so that the system remains operational,
regardless of the ignition switch position.
In addition to Lock and Unlock buttons, the RKE
transmitters are also equipped with a Panic button.
If the Panic button on the RKE transmitter is
depressed, the horn will sound and the exterior lights
will flash on the vehicle for about three minutes, or
until the Panic button is depressed a second time, if
ignition is in the Off position. A vehicle speed of
about 24 kilometers-per-hour (15 miles-per-hour) will
also cancel the panic event.
The RKE system can also perform other functions
on this vehicle. If the vehicle is equipped with the
optional Vehicle Theft Security System (VTSS), the
RKE transmitter will arm the VTSS when the Lock
button is depressed, and disarm the VTSS when the
Unlock button is depressed. (Refer to 8 - ELECTRI-
CAL/VEHICLE THEFT SECURITY - DESCRIPTION
- VEHICLE THEFT SECURITY SYSTEM). If the
vehicle is equipped with the optional Memory Sys-
tem, each of the two numbered and color-coded RKE
transmitters can be used to recall the stored driver
side front seat position, both outside power rear view
mirror positions, and the radio station presets for the
two assigned drivers. (Refer to 8 - ELECTRICAL/
POWER SEATS - DESCRIPTION - MEMORY SYS-
TEM).
8N - 2 POWER LOCKSWJ
POWER LOCKS (Continued)
Page 501 of 2199
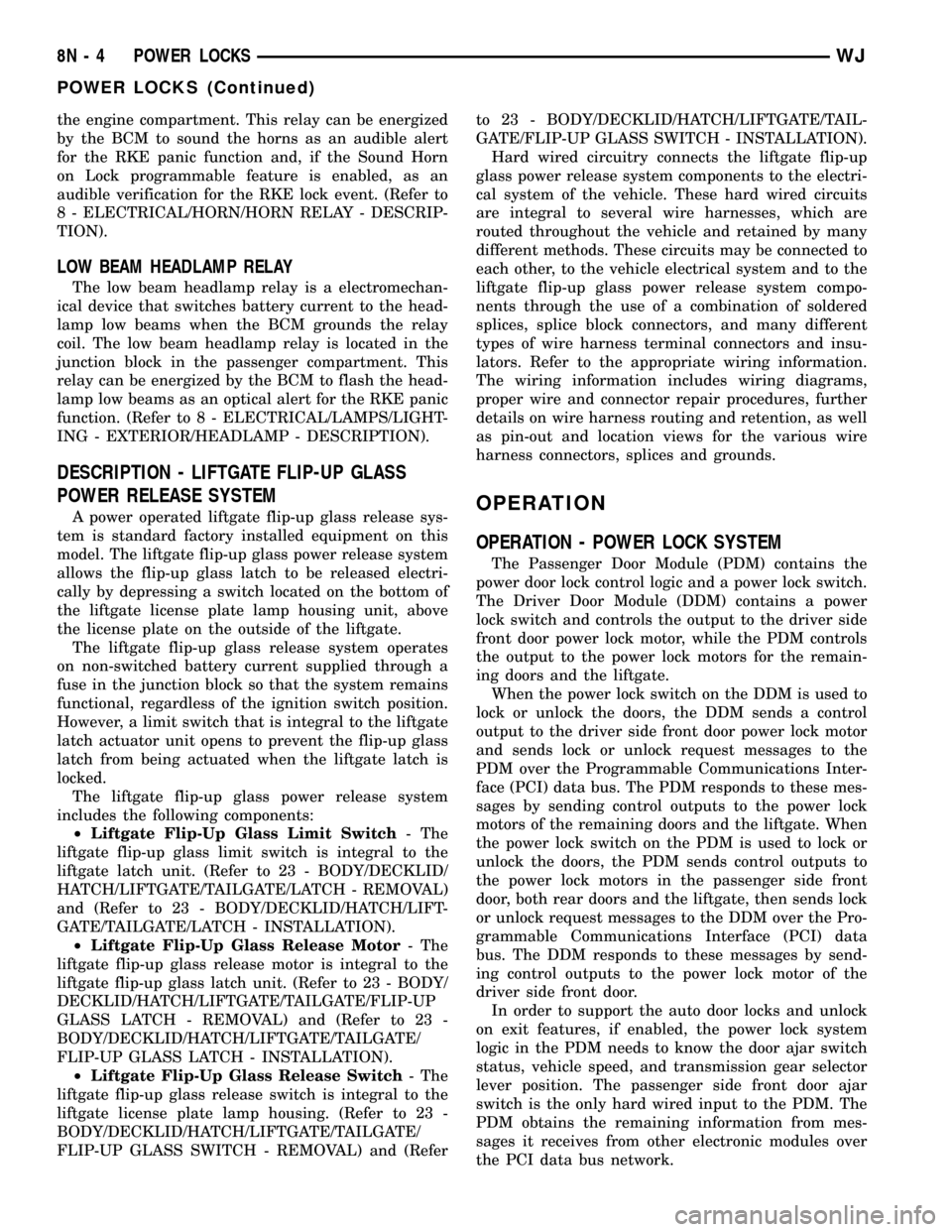
the engine compartment. This relay can be energized
by the BCM to sound the horns as an audible alert
for the RKE panic function and, if the Sound Horn
on Lock programmable feature is enabled, as an
audible verification for the RKE lock event. (Refer to
8 - ELECTRICAL/HORN/HORN RELAY - DESCRIP-
TION).
LOW BEAM HEADLAMP RELAY
The low beam headlamp relay is a electromechan-
ical device that switches battery current to the head-
lamp low beams when the BCM grounds the relay
coil. The low beam headlamp relay is located in the
junction block in the passenger compartment. This
relay can be energized by the BCM to flash the head-
lamp low beams as an optical alert for the RKE panic
function. (Refer to 8 - ELECTRICAL/LAMPS/LIGHT-
ING - EXTERIOR/HEADLAMP - DESCRIPTION).
DESCRIPTION - LIFTGATE FLIP-UP GLASS
POWER RELEASE SYSTEM
A power operated liftgate flip-up glass release sys-
tem is standard factory installed equipment on this
model. The liftgate flip-up glass power release system
allows the flip-up glass latch to be released electri-
cally by depressing a switch located on the bottom of
the liftgate license plate lamp housing unit, above
the license plate on the outside of the liftgate.
The liftgate flip-up glass release system operates
on non-switched battery current supplied through a
fuse in the junction block so that the system remains
functional, regardless of the ignition switch position.
However, a limit switch that is integral to the liftgate
latch actuator unit opens to prevent the flip-up glass
latch from being actuated when the liftgate latch is
locked.
The liftgate flip-up glass power release system
includes the following components:
²Liftgate Flip-Up Glass Limit Switch- The
liftgate flip-up glass limit switch is integral to the
liftgate latch unit. (Refer to 23 - BODY/DECKLID/
HATCH/LIFTGATE/TAILGATE/LATCH - REMOVAL)
and (Refer to 23 - BODY/DECKLID/HATCH/LIFT-
GATE/TAILGATE/LATCH - INSTALLATION).
²Liftgate Flip-Up Glass Release Motor- The
liftgate flip-up glass release motor is integral to the
liftgate flip-up glass latch unit. (Refer to 23 - BODY/
DECKLID/HATCH/LIFTGATE/TAILGATE/FLIP-UP
GLASS LATCH - REMOVAL) and (Refer to 23 -
BODY/DECKLID/HATCH/LIFTGATE/TAILGATE/
FLIP-UP GLASS LATCH - INSTALLATION).
²Liftgate Flip-Up Glass Release Switch- The
liftgate flip-up glass release switch is integral to the
liftgate license plate lamp housing. (Refer to 23 -
BODY/DECKLID/HATCH/LIFTGATE/TAILGATE/
FLIP-UP GLASS SWITCH - REMOVAL) and (Referto 23 - BODY/DECKLID/HATCH/LIFTGATE/TAIL-
GATE/FLIP-UP GLASS SWITCH - INSTALLATION).
Hard wired circuitry connects the liftgate flip-up
glass power release system components to the electri-
cal system of the vehicle. These hard wired circuits
are integral to several wire harnesses, which are
routed throughout the vehicle and retained by many
different methods. These circuits may be connected to
each other, to the vehicle electrical system and to the
liftgate flip-up glass power release system compo-
nents through the use of a combination of soldered
splices, splice block connectors, and many different
types of wire harness terminal connectors and insu-
lators. Refer to the appropriate wiring information.
The wiring information includes wiring diagrams,
proper wire and connector repair procedures, further
details on wire harness routing and retention, as well
as pin-out and location views for the various wire
harness connectors, splices and grounds.OPERATION
OPERATION - POWER LOCK SYSTEM
The Passenger Door Module (PDM) contains the
power door lock control logic and a power lock switch.
The Driver Door Module (DDM) contains a power
lock switch and controls the output to the driver side
front door power lock motor, while the PDM controls
the output to the power lock motors for the remain-
ing doors and the liftgate.
When the power lock switch on the DDM is used to
lock or unlock the doors, the DDM sends a control
output to the driver side front door power lock motor
and sends lock or unlock request messages to the
PDM over the Programmable Communications Inter-
face (PCI) data bus. The PDM responds to these mes-
sages by sending control outputs to the power lock
motors of the remaining doors and the liftgate. When
the power lock switch on the PDM is used to lock or
unlock the doors, the PDM sends control outputs to
the power lock motors in the passenger side front
door, both rear doors and the liftgate, then sends lock
or unlock request messages to the DDM over the Pro-
grammable Communications Interface (PCI) data
bus. The DDM responds to these messages by send-
ing control outputs to the power lock motor of the
driver side front door.
In order to support the auto door locks and unlock
on exit features, if enabled, the power lock system
logic in the PDM needs to know the door ajar switch
status, vehicle speed, and transmission gear selector
lever position. The passenger side front door ajar
switch is the only hard wired input to the PDM. The
PDM obtains the remaining information from mes-
sages it receives from other electronic modules over
the PCI data bus network.
8N - 4 POWER LOCKSWJ
POWER LOCKS (Continued)
Page 502 of 2199
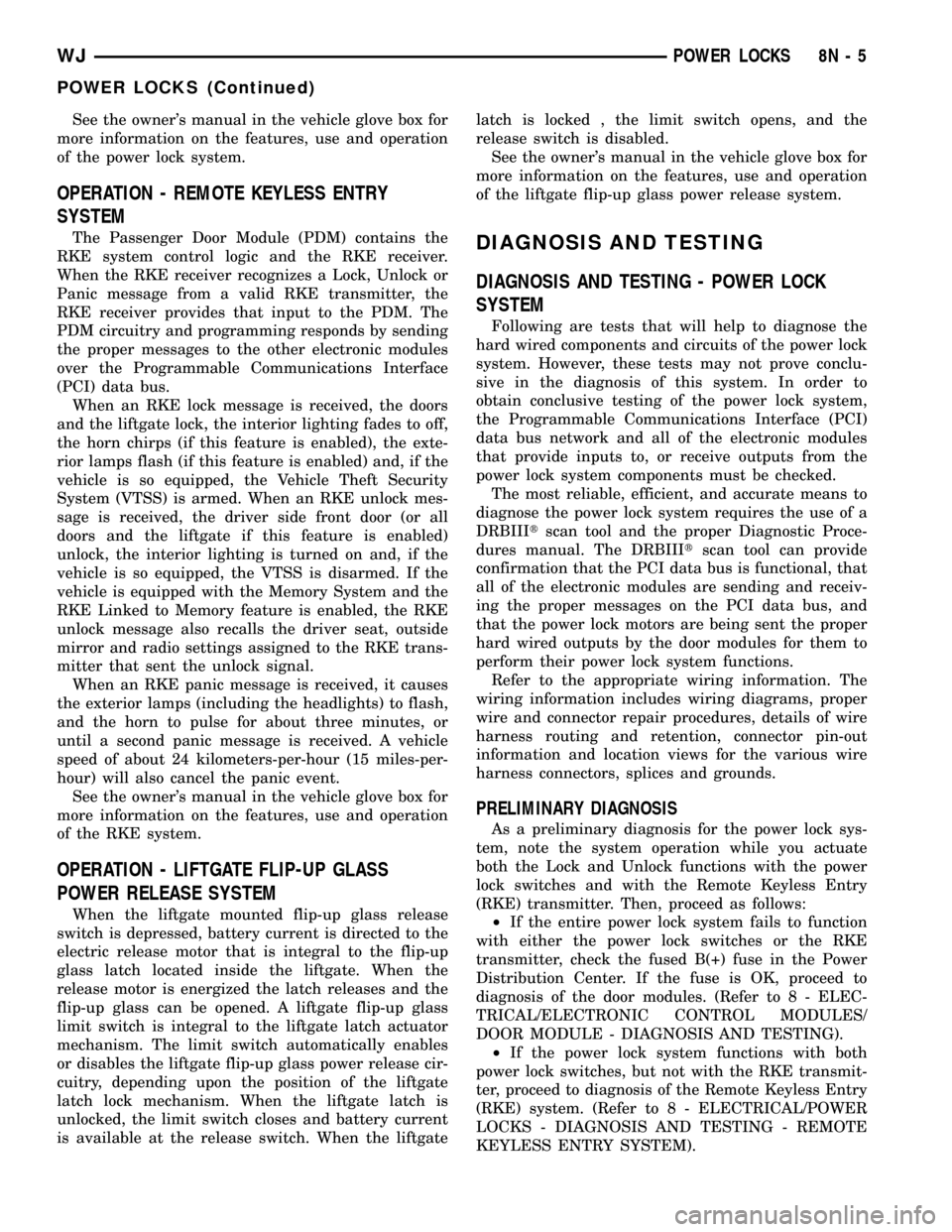
See the owner's manual in the vehicle glove box for
more information on the features, use and operation
of the power lock system.
OPERATION - REMOTE KEYLESS ENTRY
SYSTEM
The Passenger Door Module (PDM) contains the
RKE system control logic and the RKE receiver.
When the RKE receiver recognizes a Lock, Unlock or
Panic message from a valid RKE transmitter, the
RKE receiver provides that input to the PDM. The
PDM circuitry and programming responds by sending
the proper messages to the other electronic modules
over the Programmable Communications Interface
(PCI) data bus.
When an RKE lock message is received, the doors
and the liftgate lock, the interior lighting fades to off,
the horn chirps (if this feature is enabled), the exte-
rior lamps flash (if this feature is enabled) and, if the
vehicle is so equipped, the Vehicle Theft Security
System (VTSS) is armed. When an RKE unlock mes-
sage is received, the driver side front door (or all
doors and the liftgate if this feature is enabled)
unlock, the interior lighting is turned on and, if the
vehicle is so equipped, the VTSS is disarmed. If the
vehicle is equipped with the Memory System and the
RKE Linked to Memory feature is enabled, the RKE
unlock message also recalls the driver seat, outside
mirror and radio settings assigned to the RKE trans-
mitter that sent the unlock signal.
When an RKE panic message is received, it causes
the exterior lamps (including the headlights) to flash,
and the horn to pulse for about three minutes, or
until a second panic message is received. A vehicle
speed of about 24 kilometers-per-hour (15 miles-per-
hour) will also cancel the panic event.
See the owner's manual in the vehicle glove box for
more information on the features, use and operation
of the RKE system.
OPERATION - LIFTGATE FLIP-UP GLASS
POWER RELEASE SYSTEM
When the liftgate mounted flip-up glass release
switch is depressed, battery current is directed to the
electric release motor that is integral to the flip-up
glass latch located inside the liftgate. When the
release motor is energized the latch releases and the
flip-up glass can be opened. A liftgate flip-up glass
limit switch is integral to the liftgate latch actuator
mechanism. The limit switch automatically enables
or disables the liftgate flip-up glass power release cir-
cuitry, depending upon the position of the liftgate
latch lock mechanism. When the liftgate latch is
unlocked, the limit switch closes and battery current
is available at the release switch. When the liftgatelatch is locked , the limit switch opens, and the
release switch is disabled.
See the owner's manual in the vehicle glove box for
more information on the features, use and operation
of the liftgate flip-up glass power release system.
DIAGNOSIS AND TESTING
DIAGNOSIS AND TESTING - POWER LOCK
SYSTEM
Following are tests that will help to diagnose the
hard wired components and circuits of the power lock
system. However, these tests may not prove conclu-
sive in the diagnosis of this system. In order to
obtain conclusive testing of the power lock system,
the Programmable Communications Interface (PCI)
data bus network and all of the electronic modules
that provide inputs to, or receive outputs from the
power lock system components must be checked.
The most reliable, efficient, and accurate means to
diagnose the power lock system requires the use of a
DRBIIItscan tool and the proper Diagnostic Proce-
dures manual. The DRBIIItscan tool can provide
confirmation that the PCI data bus is functional, that
all of the electronic modules are sending and receiv-
ing the proper messages on the PCI data bus, and
that the power lock motors are being sent the proper
hard wired outputs by the door modules for them to
perform their power lock system functions.
Refer to the appropriate wiring information. The
wiring information includes wiring diagrams, proper
wire and connector repair procedures, details of wire
harness routing and retention, connector pin-out
information and location views for the various wire
harness connectors, splices and grounds.
PRELIMINARY DIAGNOSIS
As a preliminary diagnosis for the power lock sys-
tem, note the system operation while you actuate
both the Lock and Unlock functions with the power
lock switches and with the Remote Keyless Entry
(RKE) transmitter. Then, proceed as follows:
²If the entire power lock system fails to function
with either the power lock switches or the RKE
transmitter, check the fused B(+) fuse in the Power
Distribution Center. If the fuse is OK, proceed to
diagnosis of the door modules. (Refer to 8 - ELEC-
TRICAL/ELECTRONIC CONTROL MODULES/
DOOR MODULE - DIAGNOSIS AND TESTING).
²If the power lock system functions with both
power lock switches, but not with the RKE transmit-
ter, proceed to diagnosis of the Remote Keyless Entry
(RKE) system. (Refer to 8 - ELECTRICAL/POWER
LOCKS - DIAGNOSIS AND TESTING - REMOTE
KEYLESS ENTRY SYSTEM).
WJPOWER LOCKS 8N - 5
POWER LOCKS (Continued)
Page 541 of 2199
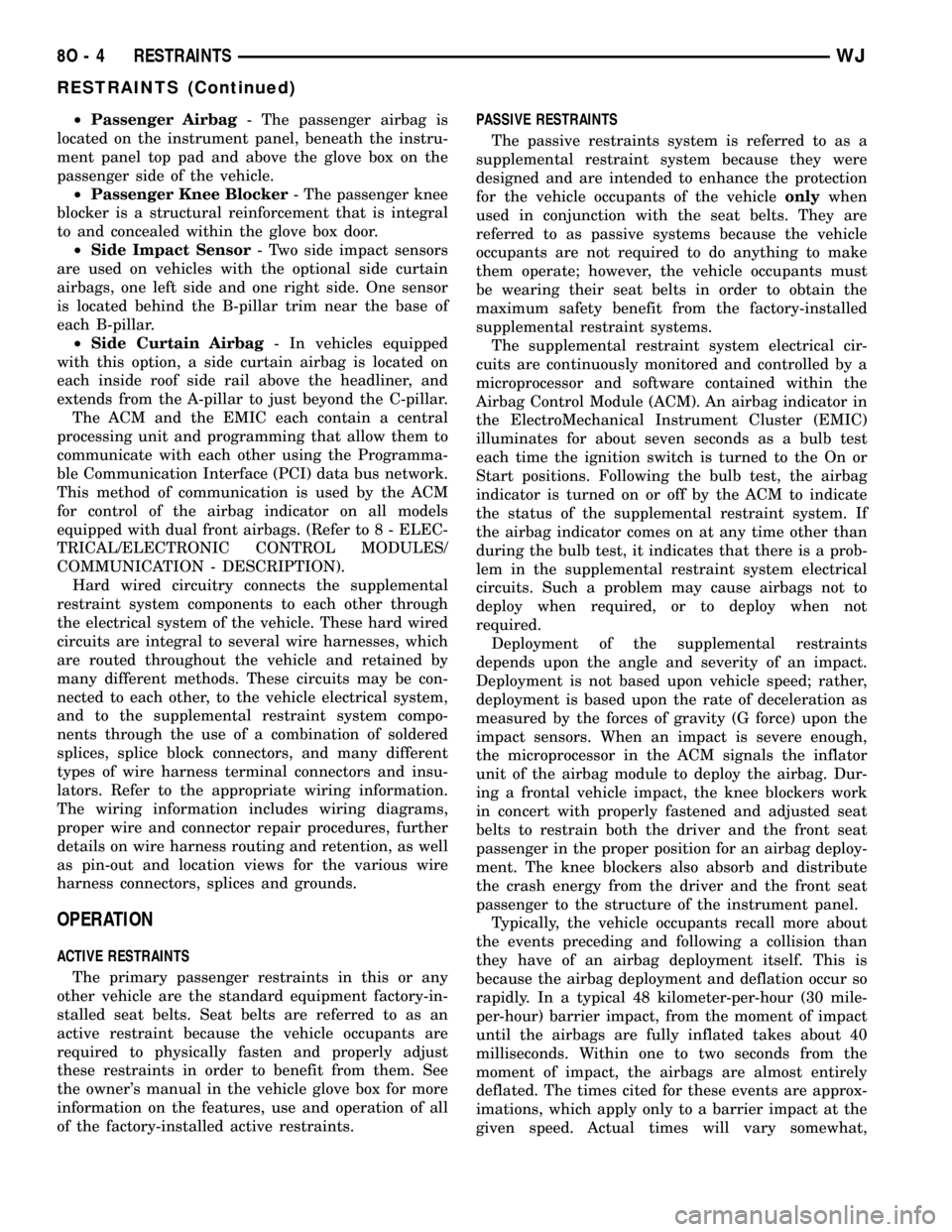
²Passenger Airbag- The passenger airbag is
located on the instrument panel, beneath the instru-
ment panel top pad and above the glove box on the
passenger side of the vehicle.
²Passenger Knee Blocker- The passenger knee
blocker is a structural reinforcement that is integral
to and concealed within the glove box door.
²Side Impact Sensor- Two side impact sensors
are used on vehicles with the optional side curtain
airbags, one left side and one right side. One sensor
is located behind the B-pillar trim near the base of
each B-pillar.
²Side Curtain Airbag- In vehicles equipped
with this option, a side curtain airbag is located on
each inside roof side rail above the headliner, and
extends from the A-pillar to just beyond the C-pillar.
The ACM and the EMIC each contain a central
processing unit and programming that allow them to
communicate with each other using the Programma-
ble Communication Interface (PCI) data bus network.
This method of communication is used by the ACM
for control of the airbag indicator on all models
equipped with dual front airbags. (Refer to 8 - ELEC-
TRICAL/ELECTRONIC CONTROL MODULES/
COMMUNICATION - DESCRIPTION).
Hard wired circuitry connects the supplemental
restraint system components to each other through
the electrical system of the vehicle. These hard wired
circuits are integral to several wire harnesses, which
are routed throughout the vehicle and retained by
many different methods. These circuits may be con-
nected to each other, to the vehicle electrical system,
and to the supplemental restraint system compo-
nents through the use of a combination of soldered
splices, splice block connectors, and many different
types of wire harness terminal connectors and insu-
lators. Refer to the appropriate wiring information.
The wiring information includes wiring diagrams,
proper wire and connector repair procedures, further
details on wire harness routing and retention, as well
as pin-out and location views for the various wire
harness connectors, splices and grounds.
OPERATION
ACTIVE RESTRAINTS
The primary passenger restraints in this or any
other vehicle are the standard equipment factory-in-
stalled seat belts. Seat belts are referred to as an
active restraint because the vehicle occupants are
required to physically fasten and properly adjust
these restraints in order to benefit from them. See
the owner's manual in the vehicle glove box for more
information on the features, use and operation of all
of the factory-installed active restraints.PASSIVE RESTRAINTS
The passive restraints system is referred to as a
supplemental restraint system because they were
designed and are intended to enhance the protection
for the vehicle occupants of the vehicleonlywhen
used in conjunction with the seat belts. They are
referred to as passive systems because the vehicle
occupants are not required to do anything to make
them operate; however, the vehicle occupants must
be wearing their seat belts in order to obtain the
maximum safety benefit from the factory-installed
supplemental restraint systems.
The supplemental restraint system electrical cir-
cuits are continuously monitored and controlled by a
microprocessor and software contained within the
Airbag Control Module (ACM). An airbag indicator in
the ElectroMechanical Instrument Cluster (EMIC)
illuminates for about seven seconds as a bulb test
each time the ignition switch is turned to the On or
Start positions. Following the bulb test, the airbag
indicator is turned on or off by the ACM to indicate
the status of the supplemental restraint system. If
the airbag indicator comes on at any time other than
during the bulb test, it indicates that there is a prob-
lem in the supplemental restraint system electrical
circuits. Such a problem may cause airbags not to
deploy when required, or to deploy when not
required.
Deployment of the supplemental restraints
depends upon the angle and severity of an impact.
Deployment is not based upon vehicle speed; rather,
deployment is based upon the rate of deceleration as
measured by the forces of gravity (G force) upon the
impact sensors. When an impact is severe enough,
the microprocessor in the ACM signals the inflator
unit of the airbag module to deploy the airbag. Dur-
ing a frontal vehicle impact, the knee blockers work
in concert with properly fastened and adjusted seat
belts to restrain both the driver and the front seat
passenger in the proper position for an airbag deploy-
ment. The knee blockers also absorb and distribute
the crash energy from the driver and the front seat
passenger to the structure of the instrument panel.
Typically, the vehicle occupants recall more about
the events preceding and following a collision than
they have of an airbag deployment itself. This is
because the airbag deployment and deflation occur so
rapidly. In a typical 48 kilometer-per-hour (30 mile-
per-hour) barrier impact, from the moment of impact
until the airbags are fully inflated takes about 40
milliseconds. Within one to two seconds from the
moment of impact, the airbags are almost entirely
deflated. The times cited for these events are approx-
imations, which apply only to a barrier impact at the
given speed. Actual times will vary somewhat,
8O - 4 RESTRAINTSWJ
RESTRAINTS (Continued)
Page 542 of 2199
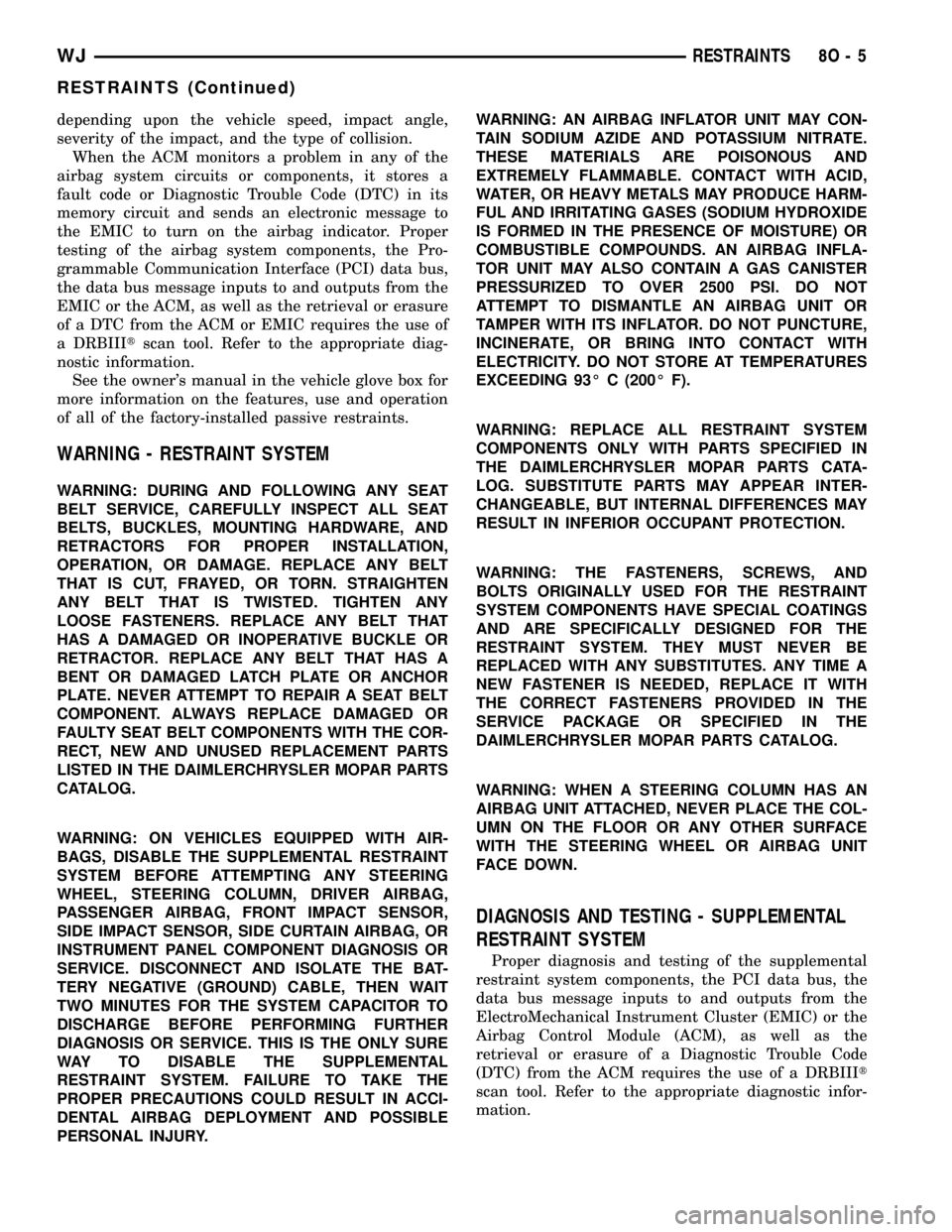
depending upon the vehicle speed, impact angle,
severity of the impact, and the type of collision.
When the ACM monitors a problem in any of the
airbag system circuits or components, it stores a
fault code or Diagnostic Trouble Code (DTC) in its
memory circuit and sends an electronic message to
the EMIC to turn on the airbag indicator. Proper
testing of the airbag system components, the Pro-
grammable Communication Interface (PCI) data bus,
the data bus message inputs to and outputs from the
EMIC or the ACM, as well as the retrieval or erasure
of a DTC from the ACM or EMIC requires the use of
a DRBIIItscan tool. Refer to the appropriate diag-
nostic information.
See the owner's manual in the vehicle glove box for
more information on the features, use and operation
of all of the factory-installed passive restraints.
WARNING - RESTRAINT SYSTEM
WARNING: DURING AND FOLLOWING ANY SEAT
BELT SERVICE, CAREFULLY INSPECT ALL SEAT
BELTS, BUCKLES, MOUNTING HARDWARE, AND
RETRACTORS FOR PROPER INSTALLATION,
OPERATION, OR DAMAGE. REPLACE ANY BELT
THAT IS CUT, FRAYED, OR TORN. STRAIGHTEN
ANY BELT THAT IS TWISTED. TIGHTEN ANY
LOOSE FASTENERS. REPLACE ANY BELT THAT
HAS A DAMAGED OR INOPERATIVE BUCKLE OR
RETRACTOR. REPLACE ANY BELT THAT HAS A
BENT OR DAMAGED LATCH PLATE OR ANCHOR
PLATE. NEVER ATTEMPT TO REPAIR A SEAT BELT
COMPONENT. ALWAYS REPLACE DAMAGED OR
FAULTY SEAT BELT COMPONENTS WITH THE COR-
RECT, NEW AND UNUSED REPLACEMENT PARTS
LISTED IN THE DAIMLERCHRYSLER MOPAR PARTS
CATALOG.
WARNING: ON VEHICLES EQUIPPED WITH AIR-
BAGS, DISABLE THE SUPPLEMENTAL RESTRAINT
SYSTEM BEFORE ATTEMPTING ANY STEERING
WHEEL, STEERING COLUMN, DRIVER AIRBAG,
PASSENGER AIRBAG, FRONT IMPACT SENSOR,
SIDE IMPACT SENSOR, SIDE CURTAIN AIRBAG, OR
INSTRUMENT PANEL COMPONENT DIAGNOSIS OR
SERVICE. DISCONNECT AND ISOLATE THE BAT-
TERY NEGATIVE (GROUND) CABLE, THEN WAIT
TWO MINUTES FOR THE SYSTEM CAPACITOR TO
DISCHARGE BEFORE PERFORMING FURTHER
DIAGNOSIS OR SERVICE. THIS IS THE ONLY SURE
WAY TO DISABLE THE SUPPLEMENTAL
RESTRAINT SYSTEM. FAILURE TO TAKE THE
PROPER PRECAUTIONS COULD RESULT IN ACCI-
DENTAL AIRBAG DEPLOYMENT AND POSSIBLE
PERSONAL INJURY.WARNING: AN AIRBAG INFLATOR UNIT MAY CON-
TAIN SODIUM AZIDE AND POTASSIUM NITRATE.
THESE MATERIALS ARE POISONOUS AND
EXTREMELY FLAMMABLE. CONTACT WITH ACID,
WATER, OR HEAVY METALS MAY PRODUCE HARM-
FUL AND IRRITATING GASES (SODIUM HYDROXIDE
IS FORMED IN THE PRESENCE OF MOISTURE) OR
COMBUSTIBLE COMPOUNDS. AN AIRBAG INFLA-
TOR UNIT MAY ALSO CONTAIN A GAS CANISTER
PRESSURIZED TO OVER 2500 PSI. DO NOT
ATTEMPT TO DISMANTLE AN AIRBAG UNIT OR
TAMPER WITH ITS INFLATOR. DO NOT PUNCTURE,
INCINERATE, OR BRING INTO CONTACT WITH
ELECTRICITY. DO NOT STORE AT TEMPERATURES
EXCEEDING 93É C (200É F).
WARNING: REPLACE ALL RESTRAINT SYSTEM
COMPONENTS ONLY WITH PARTS SPECIFIED IN
THE DAIMLERCHRYSLER MOPAR PARTS CATA-
LOG. SUBSTITUTE PARTS MAY APPEAR INTER-
CHANGEABLE, BUT INTERNAL DIFFERENCES MAY
RESULT IN INFERIOR OCCUPANT PROTECTION.
WARNING: THE FASTENERS, SCREWS, AND
BOLTS ORIGINALLY USED FOR THE RESTRAINT
SYSTEM COMPONENTS HAVE SPECIAL COATINGS
AND ARE SPECIFICALLY DESIGNED FOR THE
RESTRAINT SYSTEM. THEY MUST NEVER BE
REPLACED WITH ANY SUBSTITUTES. ANY TIME A
NEW FASTENER IS NEEDED, REPLACE IT WITH
THE CORRECT FASTENERS PROVIDED IN THE
SERVICE PACKAGE OR SPECIFIED IN THE
DAIMLERCHRYSLER MOPAR PARTS CATALOG.
WARNING: WHEN A STEERING COLUMN HAS AN
AIRBAG UNIT ATTACHED, NEVER PLACE THE COL-
UMN ON THE FLOOR OR ANY OTHER SURFACE
WITH THE STEERING WHEEL OR AIRBAG UNIT
FACE DOWN.
DIAGNOSIS AND TESTING - SUPPLEMENTAL
RESTRAINT SYSTEM
Proper diagnosis and testing of the supplemental
restraint system components, the PCI data bus, the
data bus message inputs to and outputs from the
ElectroMechanical Instrument Cluster (EMIC) or the
Airbag Control Module (ACM), as well as the
retrieval or erasure of a Diagnostic Trouble Code
(DTC) from the ACM requires the use of a DRBIIIt
scan tool. Refer to the appropriate diagnostic infor-
mation.
WJRESTRAINTS 8O - 5
RESTRAINTS (Continued)
Page 545 of 2199
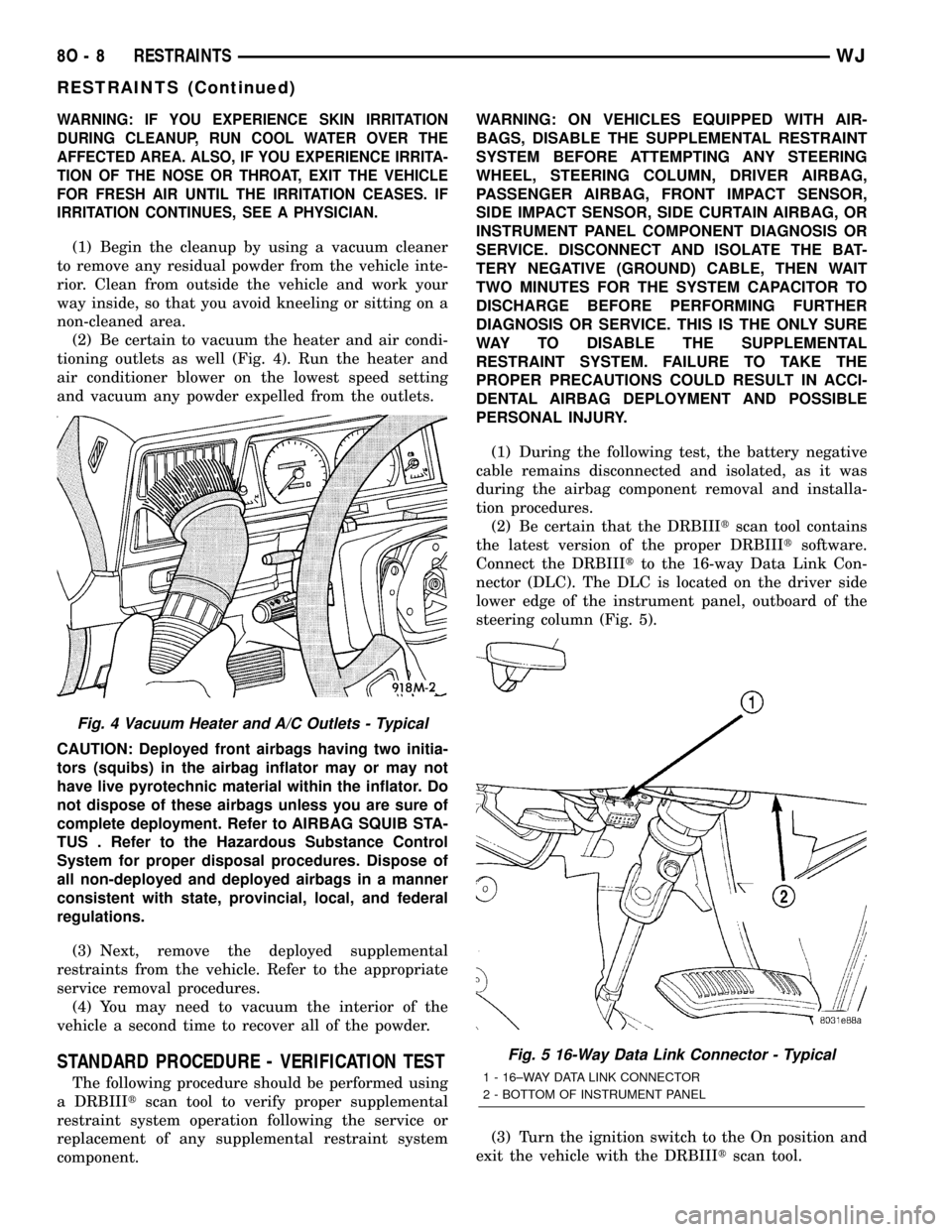
WARNING: IF YOU EXPERIENCE SKIN IRRITATION
DURING CLEANUP, RUN COOL WATER OVER THE
AFFECTED AREA. ALSO, IF YOU EXPERIENCE IRRITA-
TION OF THE NOSE OR THROAT, EXIT THE VEHICLE
FOR FRESH AIR UNTIL THE IRRITATION CEASES. IF
IRRITATION CONTINUES, SEE A PHYSICIAN.
(1) Begin the cleanup by using a vacuum cleaner
to remove any residual powder from the vehicle inte-
rior. Clean from outside the vehicle and work your
way inside, so that you avoid kneeling or sitting on a
non-cleaned area.
(2) Be certain to vacuum the heater and air condi-
tioning outlets as well (Fig. 4). Run the heater and
air conditioner blower on the lowest speed setting
and vacuum any powder expelled from the outlets.
CAUTION: Deployed front airbags having two initia-
tors (squibs) in the airbag inflator may or may not
have live pyrotechnic material within the inflator. Do
not dispose of these airbags unless you are sure of
complete deployment. Refer to AIRBAG SQUIB STA-
TUS . Refer to the Hazardous Substance Control
System for proper disposal procedures. Dispose of
all non-deployed and deployed airbags in a manner
consistent with state, provincial, local, and federal
regulations.
(3) Next, remove the deployed supplemental
restraints from the vehicle. Refer to the appropriate
service removal procedures.
(4) You may need to vacuum the interior of the
vehicle a second time to recover all of the powder.
STANDARD PROCEDURE - VERIFICATION TEST
The following procedure should be performed using
a DRBIIItscan tool to verify proper supplemental
restraint system operation following the service or
replacement of any supplemental restraint system
component.WARNING: ON VEHICLES EQUIPPED WITH AIR-
BAGS, DISABLE THE SUPPLEMENTAL RESTRAINT
SYSTEM BEFORE ATTEMPTING ANY STEERING
WHEEL, STEERING COLUMN, DRIVER AIRBAG,
PASSENGER AIRBAG, FRONT IMPACT SENSOR,
SIDE IMPACT SENSOR, SIDE CURTAIN AIRBAG, OR
INSTRUMENT PANEL COMPONENT DIAGNOSIS OR
SERVICE. DISCONNECT AND ISOLATE THE BAT-
TERY NEGATIVE (GROUND) CABLE, THEN WAIT
TWO MINUTES FOR THE SYSTEM CAPACITOR TO
DISCHARGE BEFORE PERFORMING FURTHER
DIAGNOSIS OR SERVICE. THIS IS THE ONLY SURE
WAY TO DISABLE THE SUPPLEMENTAL
RESTRAINT SYSTEM. FAILURE TO TAKE THE
PROPER PRECAUTIONS COULD RESULT IN ACCI-
DENTAL AIRBAG DEPLOYMENT AND POSSIBLE
PERSONAL INJURY.
(1) During the following test, the battery negative
cable remains disconnected and isolated, as it was
during the airbag component removal and installa-
tion procedures.
(2) Be certain that the DRBIIItscan tool contains
the latest version of the proper DRBIIItsoftware.
Connect the DRBIIItto the 16-way Data Link Con-
nector (DLC). The DLC is located on the driver side
lower edge of the instrument panel, outboard of the
steering column (Fig. 5).
(3) Turn the ignition switch to the On position and
exit the vehicle with the DRBIIItscan tool.
Fig. 4 Vacuum Heater and A/C Outlets - Typical
Fig. 5 16-Way Data Link Connector - Typical
1 - 16±WAY DATA LINK CONNECTOR
2 - BOTTOM OF INSTRUMENT PANEL
8O - 8 RESTRAINTSWJ
RESTRAINTS (Continued)
Page 552 of 2199
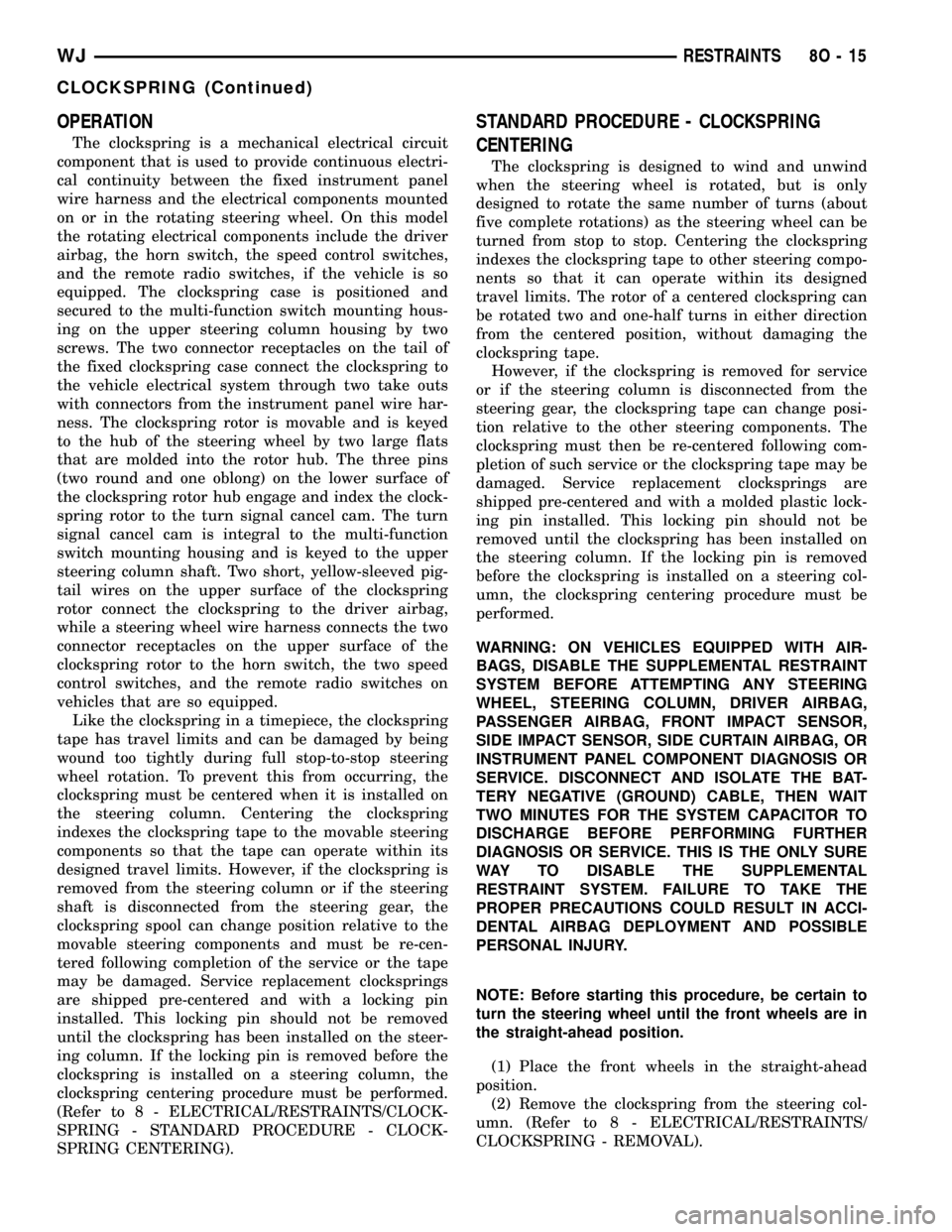
OPERATION
The clockspring is a mechanical electrical circuit
component that is used to provide continuous electri-
cal continuity between the fixed instrument panel
wire harness and the electrical components mounted
on or in the rotating steering wheel. On this model
the rotating electrical components include the driver
airbag, the horn switch, the speed control switches,
and the remote radio switches, if the vehicle is so
equipped. The clockspring case is positioned and
secured to the multi-function switch mounting hous-
ing on the upper steering column housing by two
screws. The two connector receptacles on the tail of
the fixed clockspring case connect the clockspring to
the vehicle electrical system through two take outs
with connectors from the instrument panel wire har-
ness. The clockspring rotor is movable and is keyed
to the hub of the steering wheel by two large flats
that are molded into the rotor hub. The three pins
(two round and one oblong) on the lower surface of
the clockspring rotor hub engage and index the clock-
spring rotor to the turn signal cancel cam. The turn
signal cancel cam is integral to the multi-function
switch mounting housing and is keyed to the upper
steering column shaft. Two short, yellow-sleeved pig-
tail wires on the upper surface of the clockspring
rotor connect the clockspring to the driver airbag,
while a steering wheel wire harness connects the two
connector receptacles on the upper surface of the
clockspring rotor to the horn switch, the two speed
control switches, and the remote radio switches on
vehicles that are so equipped.
Like the clockspring in a timepiece, the clockspring
tape has travel limits and can be damaged by being
wound too tightly during full stop-to-stop steering
wheel rotation. To prevent this from occurring, the
clockspring must be centered when it is installed on
the steering column. Centering the clockspring
indexes the clockspring tape to the movable steering
components so that the tape can operate within its
designed travel limits. However, if the clockspring is
removed from the steering column or if the steering
shaft is disconnected from the steering gear, the
clockspring spool can change position relative to the
movable steering components and must be re-cen-
tered following completion of the service or the tape
may be damaged. Service replacement clocksprings
are shipped pre-centered and with a locking pin
installed. This locking pin should not be removed
until the clockspring has been installed on the steer-
ing column. If the locking pin is removed before the
clockspring is installed on a steering column, the
clockspring centering procedure must be performed.
(Refer to 8 - ELECTRICAL/RESTRAINTS/CLOCK-
SPRING - STANDARD PROCEDURE - CLOCK-
SPRING CENTERING).
STANDARD PROCEDURE - CLOCKSPRING
CENTERING
The clockspring is designed to wind and unwind
when the steering wheel is rotated, but is only
designed to rotate the same number of turns (about
five complete rotations) as the steering wheel can be
turned from stop to stop. Centering the clockspring
indexes the clockspring tape to other steering compo-
nents so that it can operate within its designed
travel limits. The rotor of a centered clockspring can
be rotated two and one-half turns in either direction
from the centered position, without damaging the
clockspring tape.
However, if the clockspring is removed for service
or if the steering column is disconnected from the
steering gear, the clockspring tape can change posi-
tion relative to the other steering components. The
clockspring must then be re-centered following com-
pletion of such service or the clockspring tape may be
damaged. Service replacement clocksprings are
shipped pre-centered and with a molded plastic lock-
ing pin installed. This locking pin should not be
removed until the clockspring has been installed on
the steering column. If the locking pin is removed
before the clockspring is installed on a steering col-
umn, the clockspring centering procedure must be
performed.
WARNING: ON VEHICLES EQUIPPED WITH AIR-
BAGS, DISABLE THE SUPPLEMENTAL RESTRAINT
SYSTEM BEFORE ATTEMPTING ANY STEERING
WHEEL, STEERING COLUMN, DRIVER AIRBAG,
PASSENGER AIRBAG, FRONT IMPACT SENSOR,
SIDE IMPACT SENSOR, SIDE CURTAIN AIRBAG, OR
INSTRUMENT PANEL COMPONENT DIAGNOSIS OR
SERVICE. DISCONNECT AND ISOLATE THE BAT-
TERY NEGATIVE (GROUND) CABLE, THEN WAIT
TWO MINUTES FOR THE SYSTEM CAPACITOR TO
DISCHARGE BEFORE PERFORMING FURTHER
DIAGNOSIS OR SERVICE. THIS IS THE ONLY SURE
WAY TO DISABLE THE SUPPLEMENTAL
RESTRAINT SYSTEM. FAILURE TO TAKE THE
PROPER PRECAUTIONS COULD RESULT IN ACCI-
DENTAL AIRBAG DEPLOYMENT AND POSSIBLE
PERSONAL INJURY.
NOTE: Before starting this procedure, be certain to
turn the steering wheel until the front wheels are in
the straight-ahead position.
(1) Place the front wheels in the straight-ahead
position.
(2) Remove the clockspring from the steering col-
umn. (Refer to 8 - ELECTRICAL/RESTRAINTS/
CLOCKSPRING - REMOVAL).
WJRESTRAINTS 8O - 15
CLOCKSPRING (Continued)
Page 582 of 2199
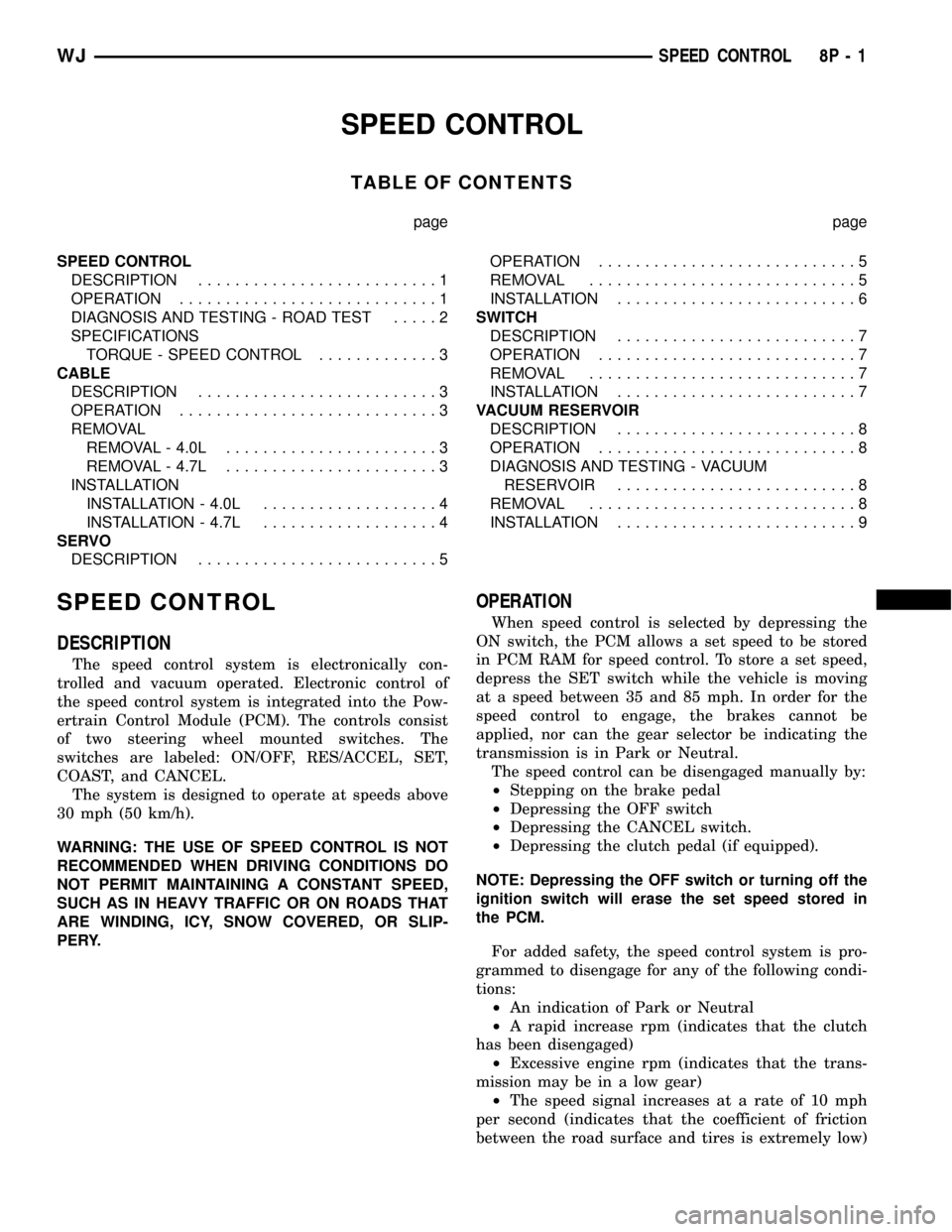
SPEED CONTROL
TABLE OF CONTENTS
page page
SPEED CONTROL
DESCRIPTION..........................1
OPERATION............................1
DIAGNOSIS AND TESTING - ROAD TEST.....2
SPECIFICATIONS
TORQUE - SPEED CONTROL.............3
CABLE
DESCRIPTION..........................3
OPERATION............................3
REMOVAL
REMOVAL - 4.0L.......................3
REMOVAL - 4.7L.......................3
INSTALLATION
INSTALLATION - 4.0L...................4
INSTALLATION - 4.7L...................4
SERVO
DESCRIPTION..........................5OPERATION............................5
REMOVAL.............................5
INSTALLATION..........................6
SWITCH
DESCRIPTION..........................7
OPERATION............................7
REMOVAL.............................7
INSTALLATION..........................7
VACUUM RESERVOIR
DESCRIPTION..........................8
OPERATION............................8
DIAGNOSIS AND TESTING - VACUUM
RESERVOIR..........................8
REMOVAL.............................8
INSTALLATION..........................9
SPEED CONTROL
DESCRIPTION
The speed control system is electronically con-
trolled and vacuum operated. Electronic control of
the speed control system is integrated into the Pow-
ertrain Control Module (PCM). The controls consist
of two steering wheel mounted switches. The
switches are labeled: ON/OFF, RES/ACCEL, SET,
COAST, and CANCEL.
The system is designed to operate at speeds above
30 mph (50 km/h).
WARNING: THE USE OF SPEED CONTROL IS NOT
RECOMMENDED WHEN DRIVING CONDITIONS DO
NOT PERMIT MAINTAINING A CONSTANT SPEED,
SUCH AS IN HEAVY TRAFFIC OR ON ROADS THAT
ARE WINDING, ICY, SNOW COVERED, OR SLIP-
PERY.
OPERATION
When speed control is selected by depressing the
ON switch, the PCM allows a set speed to be stored
in PCM RAM for speed control. To store a set speed,
depress the SET switch while the vehicle is moving
at a speed between 35 and 85 mph. In order for the
speed control to engage, the brakes cannot be
applied, nor can the gear selector be indicating the
transmission is in Park or Neutral.
The speed control can be disengaged manually by:
²Stepping on the brake pedal
²Depressing the OFF switch
²Depressing the CANCEL switch.
²Depressing the clutch pedal (if equipped).
NOTE: Depressing the OFF switch or turning off the
ignition switch will erase the set speed stored in
the PCM.
For added safety, the speed control system is pro-
grammed to disengage for any of the following condi-
tions:
²An indication of Park or Neutral
²A rapid increase rpm (indicates that the clutch
has been disengaged)
²Excessive engine rpm (indicates that the trans-
mission may be in a low gear)
²The speed signal increases at a rate of 10 mph
per second (indicates that the coefficient of friction
between the road surface and tires is extremely low)
WJSPEED CONTROL 8P - 1