driver seat JEEP GRAND CHEROKEE 2002 WJ / 2.G Workshop Manual
[x] Cancel search | Manufacturer: JEEP, Model Year: 2002, Model line: GRAND CHEROKEE, Model: JEEP GRAND CHEROKEE 2002 WJ / 2.GPages: 2199, PDF Size: 76.01 MB
Page 47 of 2199
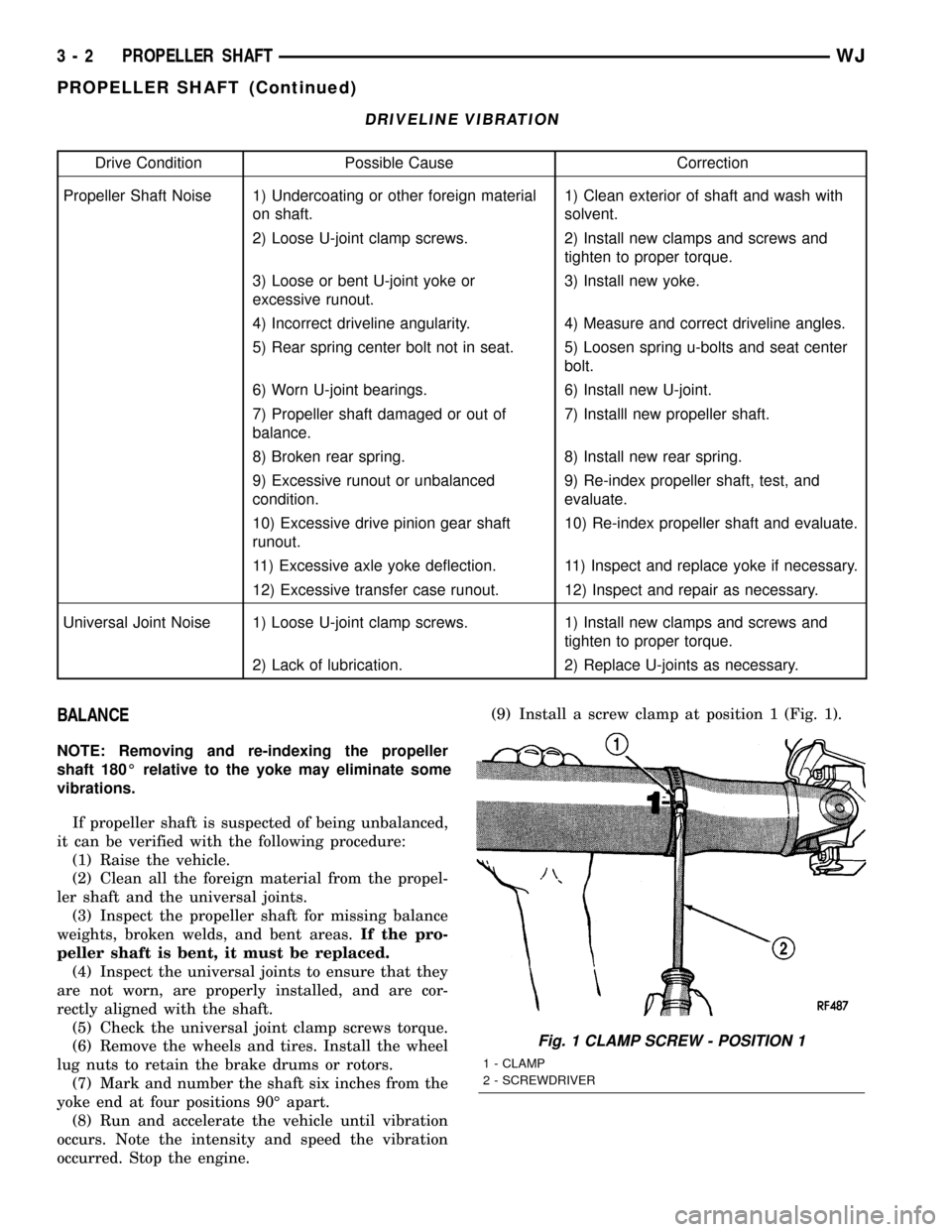
DRIVELINE VIBRATION
Drive Condition Possible Cause Correction
Propeller Shaft Noise 1) Undercoating or other foreign material
on shaft.1) Clean exterior of shaft and wash with
solvent.
2) Loose U-joint clamp screws. 2) Install new clamps and screws and
tighten to proper torque.
3) Loose or bent U-joint yoke or
excessive runout.3) Install new yoke.
4) Incorrect driveline angularity. 4) Measure and correct driveline angles.
5) Rear spring center bolt not in seat. 5) Loosen spring u-bolts and seat center
bolt.
6) Worn U-joint bearings. 6) Install new U-joint.
7) Propeller shaft damaged or out of
balance.7) Installl new propeller shaft.
8) Broken rear spring. 8) Install new rear spring.
9) Excessive runout or unbalanced
condition.9) Re-index propeller shaft, test, and
evaluate.
10) Excessive drive pinion gear shaft
runout.10) Re-index propeller shaft and evaluate.
11) Excessive axle yoke deflection. 11) Inspect and replace yoke if necessary.
12) Excessive transfer case runout. 12) Inspect and repair as necessary.
Universal Joint Noise 1) Loose U-joint clamp screws. 1) Install new clamps and screws and
tighten to proper torque.
2) Lack of lubrication. 2) Replace U-joints as necessary.
BALANCE
NOTE: Removing and re-indexing the propeller
shaft 180É relative to the yoke may eliminate some
vibrations.
If propeller shaft is suspected of being unbalanced,
it can be verified with the following procedure:
(1) Raise the vehicle.
(2) Clean all the foreign material from the propel-
ler shaft and the universal joints.
(3) Inspect the propeller shaft for missing balance
weights, broken welds, and bent areas.If the pro-
peller shaft is bent, it must be replaced.
(4) Inspect the universal joints to ensure that they
are not worn, are properly installed, and are cor-
rectly aligned with the shaft.
(5) Check the universal joint clamp screws torque.
(6) Remove the wheels and tires. Install the wheel
lug nuts to retain the brake drums or rotors.
(7) Mark and number the shaft six inches from the
yoke end at four positions 90É apart.
(8) Run and accelerate the vehicle until vibration
occurs. Note the intensity and speed the vibration
occurred. Stop the engine.(9) Install a screw clamp at position 1 (Fig. 1).
Fig. 1 CLAMP SCREW - POSITION 1
1 - CLAMP
2 - SCREWDRIVER
3 - 2 PROPELLER SHAFTWJ
PROPELLER SHAFT (Continued)
Page 132 of 2199
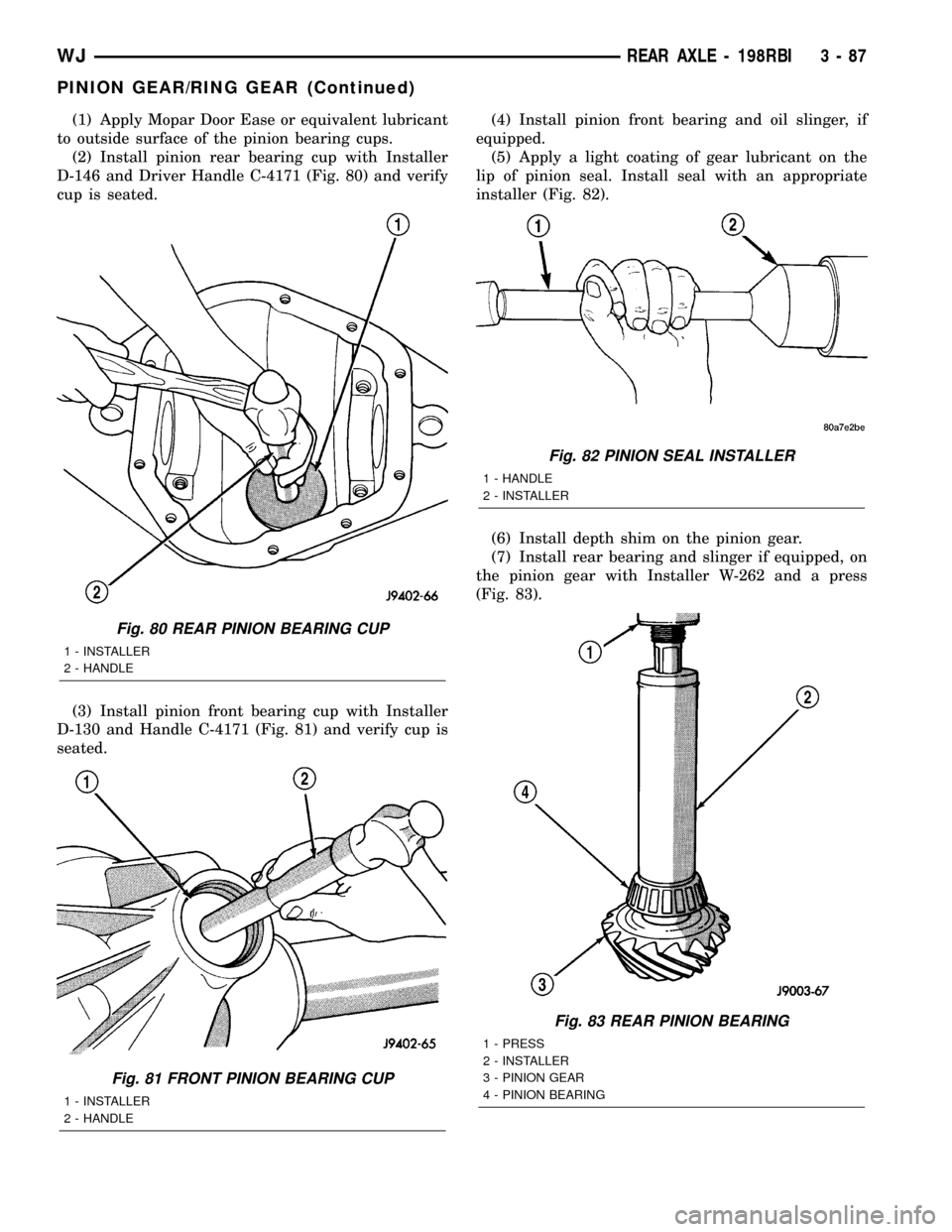
(1) Apply Mopar Door Ease or equivalent lubricant
to outside surface of the pinion bearing cups.
(2) Install pinion rear bearing cup with Installer
D-146 and Driver Handle C-4171 (Fig. 80) and verify
cup is seated.
(3) Install pinion front bearing cup with Installer
D-130 and Handle C-4171 (Fig. 81) and verify cup is
seated.(4) Install pinion front bearing and oil slinger, if
equipped.
(5) Apply a light coating of gear lubricant on the
lip of pinion seal. Install seal with an appropriate
installer (Fig. 82).
(6) Install depth shim on the pinion gear.
(7) Install rear bearing and slinger if equipped, on
the pinion gear with Installer W-262 and a press
(Fig. 83).
Fig. 80 REAR PINION BEARING CUP
1 - INSTALLER
2 - HANDLE
Fig. 81 FRONT PINION BEARING CUP
1 - INSTALLER
2 - HANDLE
Fig. 82 PINION SEAL INSTALLER
1 - HANDLE
2 - INSTALLER
Fig. 83 REAR PINION BEARING
1 - PRESS
2 - INSTALLER
3 - PINION GEAR
4 - PINION BEARING
WJREAR AXLE - 198RBI 3 - 87
PINION GEAR/RING GEAR (Continued)
Page 172 of 2199
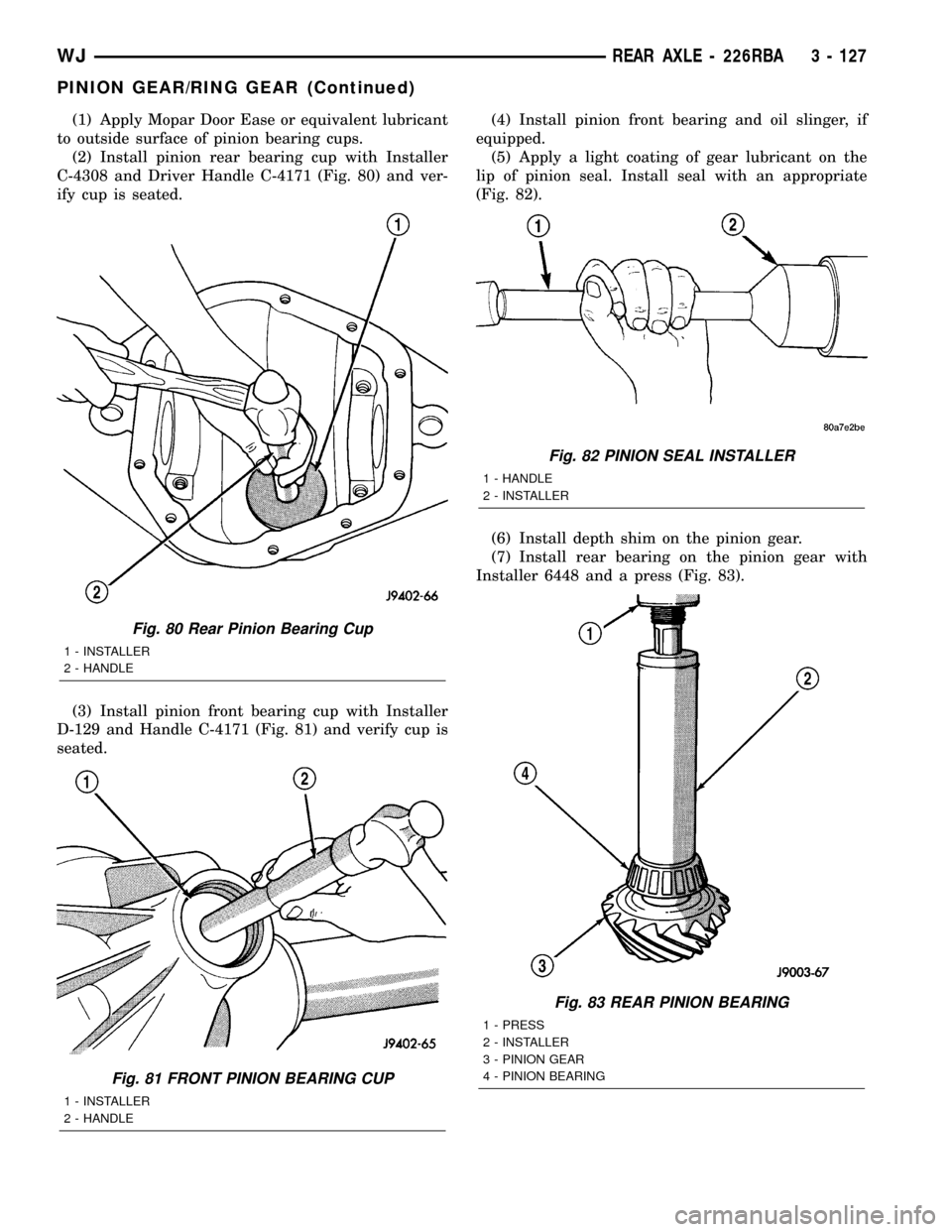
(1) Apply Mopar Door Ease or equivalent lubricant
to outside surface of pinion bearing cups.
(2) Install pinion rear bearing cup with Installer
C-4308 and Driver Handle C-4171 (Fig. 80) and ver-
ify cup is seated.
(3) Install pinion front bearing cup with Installer
D-129 and Handle C-4171 (Fig. 81) and verify cup is
seated.(4) Install pinion front bearing and oil slinger, if
equipped.
(5) Apply a light coating of gear lubricant on the
lip of pinion seal. Install seal with an appropriate
(Fig. 82).
(6) Install depth shim on the pinion gear.
(7) Install rear bearing on the pinion gear with
Installer 6448 and a press (Fig. 83).
Fig. 80 Rear Pinion Bearing Cup
1 - INSTALLER
2 - HANDLE
Fig. 81 FRONT PINION BEARING CUP
1 - INSTALLER
2 - HANDLE
Fig. 82 PINION SEAL INSTALLER
1 - HANDLE
2 - INSTALLER
Fig. 83 REAR PINION BEARING
1 - PRESS
2 - INSTALLER
3 - PINION GEAR
4 - PINION BEARING
WJREAR AXLE - 226RBA 3 - 127
PINION GEAR/RING GEAR (Continued)
Page 201 of 2199
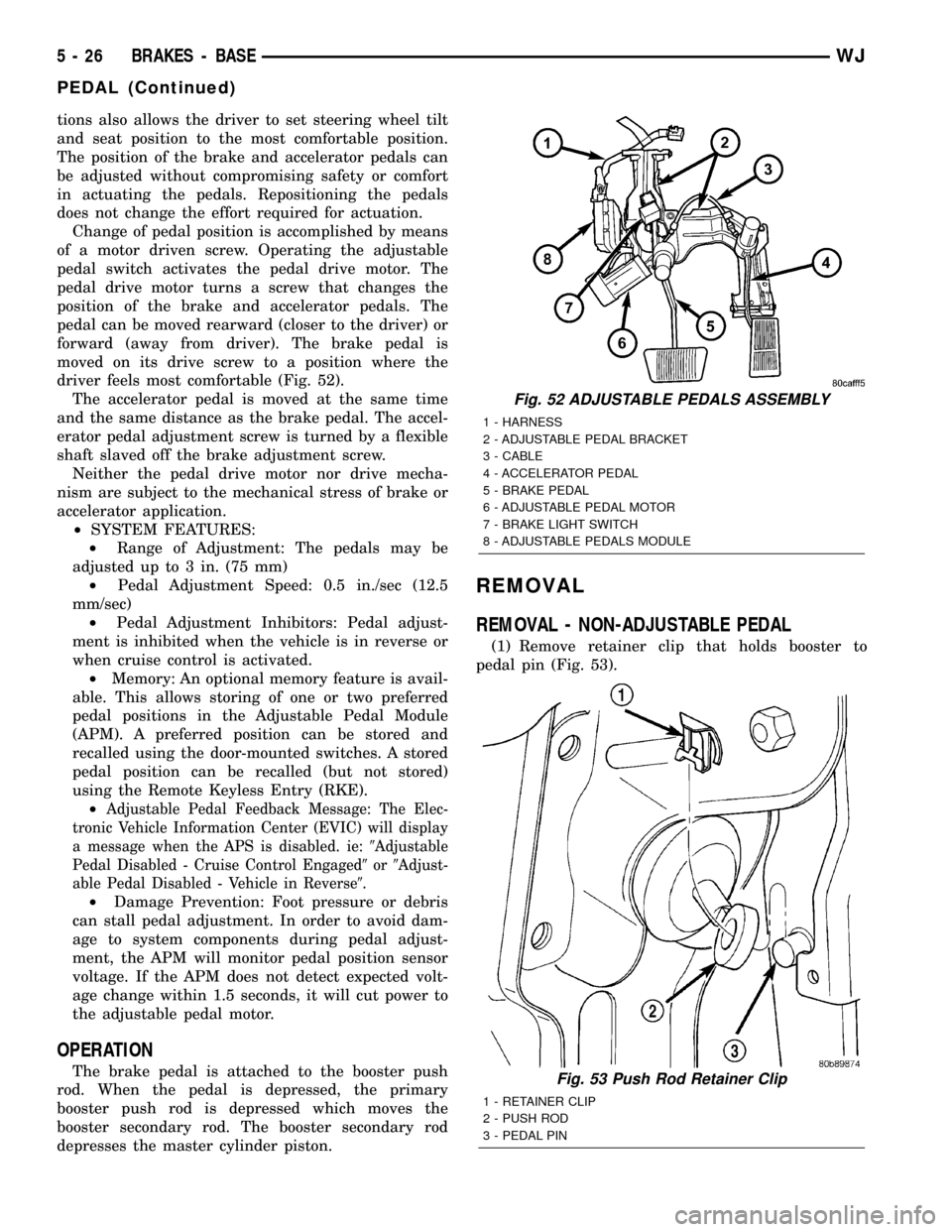
tions also allows the driver to set steering wheel tilt
and seat position to the most comfortable position.
The position of the brake and accelerator pedals can
be adjusted without compromising safety or comfort
in actuating the pedals. Repositioning the pedals
does not change the effort required for actuation.
Change of pedal position is accomplished by means
of a motor driven screw. Operating the adjustable
pedal switch activates the pedal drive motor. The
pedal drive motor turns a screw that changes the
position of the brake and accelerator pedals. The
pedal can be moved rearward (closer to the driver) or
forward (away from driver). The brake pedal is
moved on its drive screw to a position where the
driver feels most comfortable (Fig. 52).
The accelerator pedal is moved at the same time
and the same distance as the brake pedal. The accel-
erator pedal adjustment screw is turned by a flexible
shaft slaved off the brake adjustment screw.
Neither the pedal drive motor nor drive mecha-
nism are subject to the mechanical stress of brake or
accelerator application.
²SYSTEM FEATURES:
²Range of Adjustment: The pedals may be
adjusted up to 3 in. (75 mm)
²Pedal Adjustment Speed: 0.5 in./sec (12.5
mm/sec)
²Pedal Adjustment Inhibitors: Pedal adjust-
ment is inhibited when the vehicle is in reverse or
when cruise control is activated.
²Memory: An optional memory feature is avail-
able. This allows storing of one or two preferred
pedal positions in the Adjustable Pedal Module
(APM). A preferred position can be stored and
recalled using the door-mounted switches. A stored
pedal position can be recalled (but not stored)
using the Remote Keyless Entry (RKE).
²
Adjustable Pedal Feedback Message: The Elec-
tronic Vehicle Information Center (EVIC) will display
a message when the APS is disabled. ie:9Adjustable
Pedal Disabled - Cruise Control Engaged9or9Adjust-
able Pedal Disabled - Vehicle in Reverse9.
²Damage Prevention: Foot pressure or debris
can stall pedal adjustment. In order to avoid dam-
age to system components during pedal adjust-
ment, the APM will monitor pedal position sensor
voltage. If the APM does not detect expected volt-
age change within 1.5 seconds, it will cut power to
the adjustable pedal motor.
OPERATION
The brake pedal is attached to the booster push
rod. When the pedal is depressed, the primary
booster push rod is depressed which moves the
booster secondary rod. The booster secondary rod
depresses the master cylinder piston.
REMOVAL
REMOVAL - NON-ADJUSTABLE PEDAL
(1) Remove retainer clip that holds booster to
pedal pin (Fig. 53).
Fig. 52 ADJUSTABLE PEDALS ASSEMBLY
1 - HARNESS
2 - ADJUSTABLE PEDAL BRACKET
3 - CABLE
4 - ACCELERATOR PEDAL
5 - BRAKE PEDAL
6 - ADJUSTABLE PEDAL MOTOR
7 - BRAKE LIGHT SWITCH
8 - ADJUSTABLE PEDALS MODULE
Fig. 53 Push Rod Retainer Clip
1 - RETAINER CLIP
2 - PUSH ROD
3 - PEDAL PIN
5 - 26 BRAKES - BASEWJ
PEDAL (Continued)
Page 210 of 2199
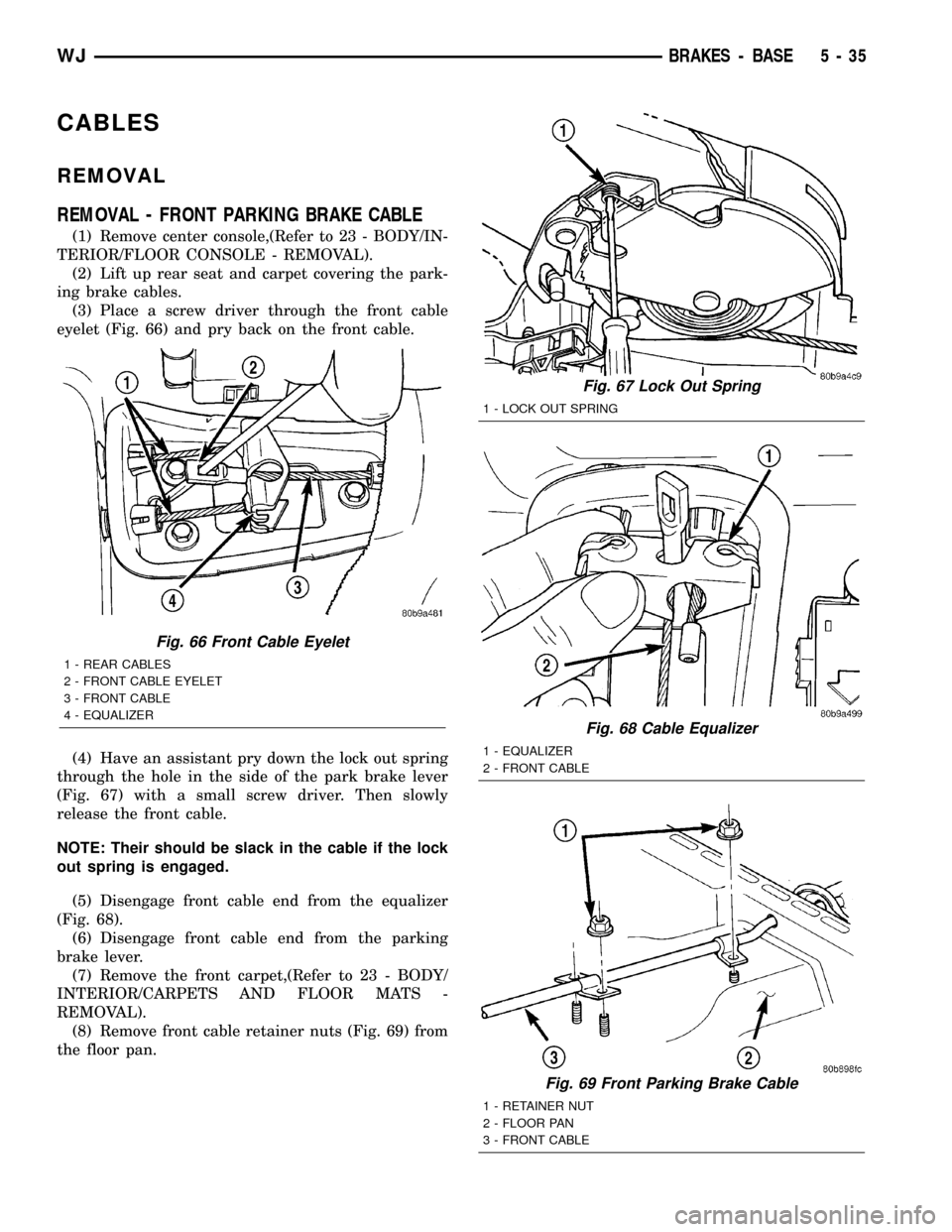
CABLES
REMOVAL
REMOVAL - FRONT PARKING BRAKE CABLE
(1) Remove center console,(Refer to 23 - BODY/IN-
TERIOR/FLOOR CONSOLE - REMOVAL).
(2) Lift up rear seat and carpet covering the park-
ing brake cables.
(3) Place a screw driver through the front cable
eyelet (Fig. 66) and pry back on the front cable.
(4) Have an assistant pry down the lock out spring
through the hole in the side of the park brake lever
(Fig. 67) with a small screw driver. Then slowly
release the front cable.
NOTE: Their should be slack in the cable if the lock
out spring is engaged.
(5) Disengage front cable end from the equalizer
(Fig. 68).
(6) Disengage front cable end from the parking
brake lever.
(7) Remove the front carpet,(Refer to 23 - BODY/
INTERIOR/CARPETS AND FLOOR MATS -
REMOVAL).
(8) Remove front cable retainer nuts (Fig. 69) from
the floor pan.
Fig. 66 Front Cable Eyelet
1 - REAR CABLES
2 - FRONT CABLE EYELET
3 - FRONT CABLE
4 - EQUALIZER
Fig. 67 Lock Out Spring
1 - LOCK OUT SPRING
Fig. 68 Cable Equalizer
1 - EQUALIZER
2 - FRONT CABLE
Fig. 69 Front Parking Brake Cable
1 - RETAINER NUT
2 - FLOOR PAN
3 - FRONT CABLE
WJBRAKES - BASE 5 - 35
Page 211 of 2199
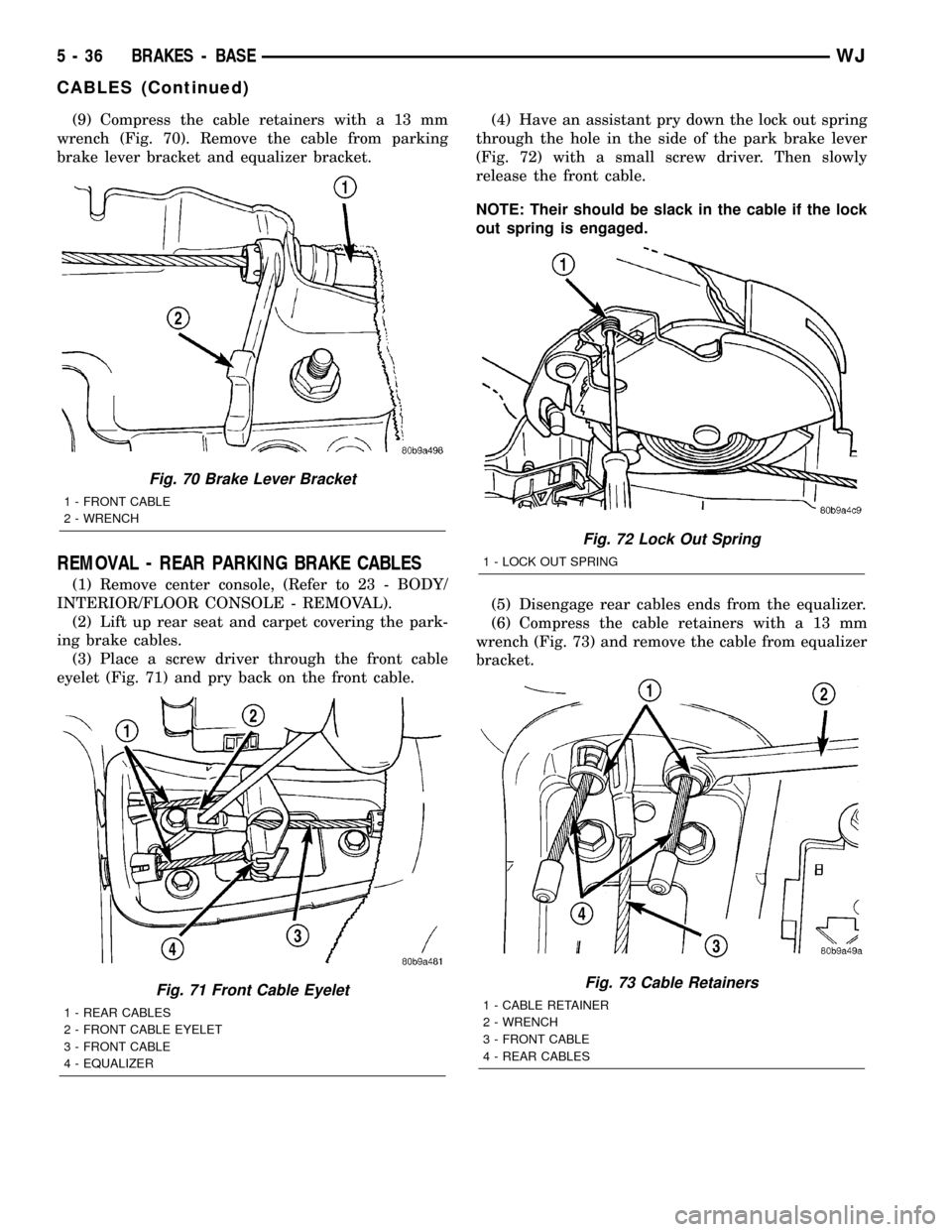
(9) Compress the cable retainers with a 13 mm
wrench (Fig. 70). Remove the cable from parking
brake lever bracket and equalizer bracket.
REMOVAL - REAR PARKING BRAKE CABLES
(1) Remove center console, (Refer to 23 - BODY/
INTERIOR/FLOOR CONSOLE - REMOVAL).
(2) Lift up rear seat and carpet covering the park-
ing brake cables.
(3) Place a screw driver through the front cable
eyelet (Fig. 71) and pry back on the front cable.(4) Have an assistant pry down the lock out spring
through the hole in the side of the park brake lever
(Fig. 72) with a small screw driver. Then slowly
release the front cable.
NOTE: Their should be slack in the cable if the lock
out spring is engaged.
(5) Disengage rear cables ends from the equalizer.
(6) Compress the cable retainers with a 13 mm
wrench (Fig. 73) and remove the cable from equalizer
bracket.
Fig. 70 Brake Lever Bracket
1 - FRONT CABLE
2 - WRENCH
Fig. 71 Front Cable Eyelet
1 - REAR CABLES
2 - FRONT CABLE EYELET
3 - FRONT CABLE
4 - EQUALIZER
Fig. 72 Lock Out Spring
1 - LOCK OUT SPRING
Fig. 73 Cable Retainers
1 - CABLE RETAINER
2 - WRENCH
3 - FRONT CABLE
4 - REAR CABLES
5 - 36 BRAKES - BASEWJ
CABLES (Continued)
Page 212 of 2199
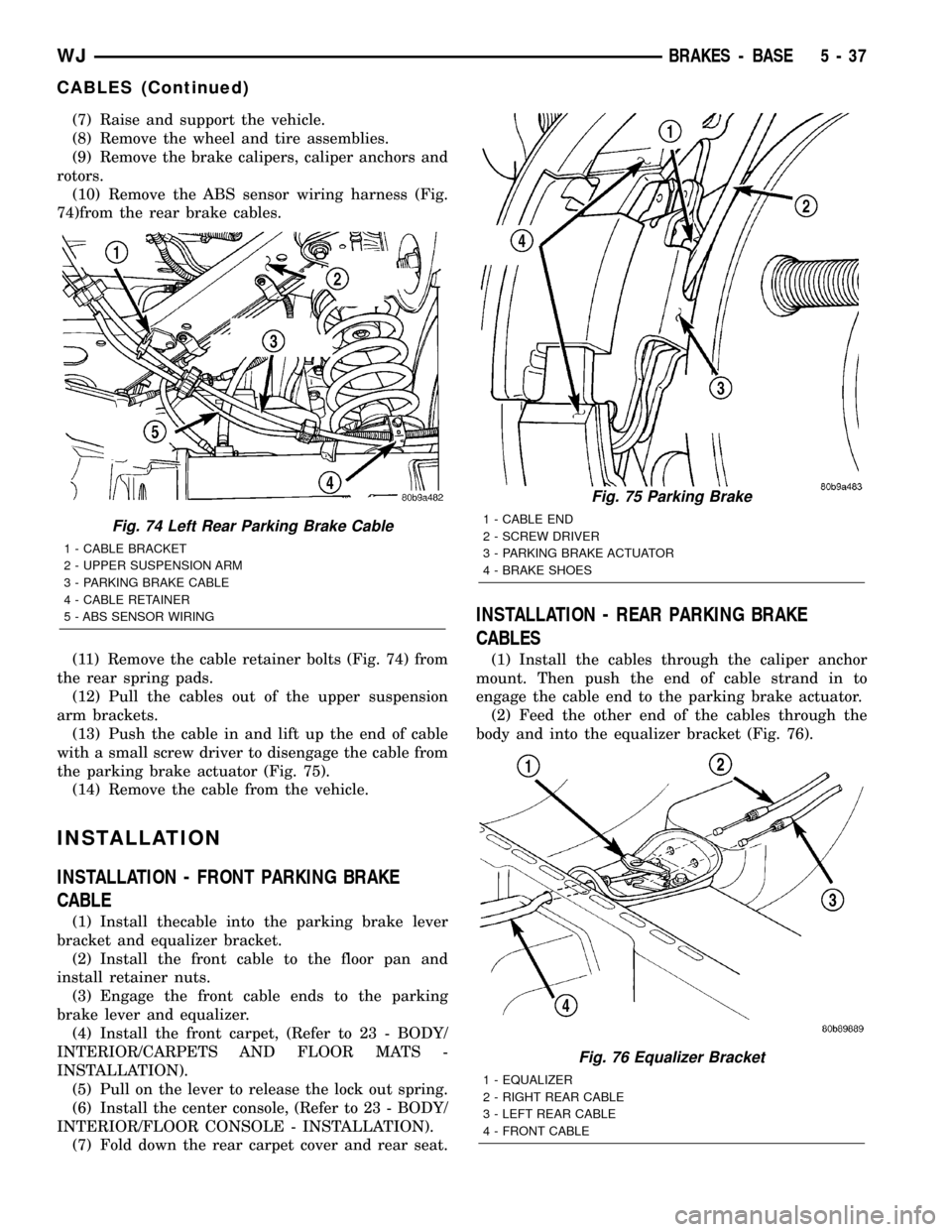
(7) Raise and support the vehicle.
(8) Remove the wheel and tire assemblies.
(9) Remove the brake calipers, caliper anchors and
rotors.
(10) Remove the ABS sensor wiring harness (Fig.
74)from the rear brake cables.
(11) Remove the cable retainer bolts (Fig. 74) from
the rear spring pads.
(12) Pull the cables out of the upper suspension
arm brackets.
(13) Push the cable in and lift up the end of cable
with a small screw driver to disengage the cable from
the parking brake actuator (Fig. 75).
(14) Remove the cable from the vehicle.
INSTALLATION
INSTALLATION - FRONT PARKING BRAKE
CABLE
(1) Install thecable into the parking brake lever
bracket and equalizer bracket.
(2) Install the front cable to the floor pan and
install retainer nuts.
(3) Engage the front cable ends to the parking
brake lever and equalizer.
(4) Install the front carpet, (Refer to 23 - BODY/
INTERIOR/CARPETS AND FLOOR MATS -
INSTALLATION).
(5) Pull on the lever to release the lock out spring.
(6) Install the center console, (Refer to 23 - BODY/
INTERIOR/FLOOR CONSOLE - INSTALLATION).
(7) Fold down the rear carpet cover and rear seat.
INSTALLATION - REAR PARKING BRAKE
CABLES
(1) Install the cables through the caliper anchor
mount. Then push the end of cable strand in to
engage the cable end to the parking brake actuator.
(2) Feed the other end of the cables through the
body and into the equalizer bracket (Fig. 76).
Fig. 74 Left Rear Parking Brake Cable
1 - CABLE BRACKET
2 - UPPER SUSPENSION ARM
3 - PARKING BRAKE CABLE
4 - CABLE RETAINER
5 - ABS SENSOR WIRING
Fig. 75 Parking Brake
1 - CABLE END
2 - SCREW DRIVER
3 - PARKING BRAKE ACTUATOR
4 - BRAKE SHOES
Fig. 76 Equalizer Bracket
1 - EQUALIZER
2 - RIGHT REAR CABLE
3 - LEFT REAR CABLE
4 - FRONT CABLE
WJBRAKES - BASE 5 - 37
CABLES (Continued)
Page 213 of 2199
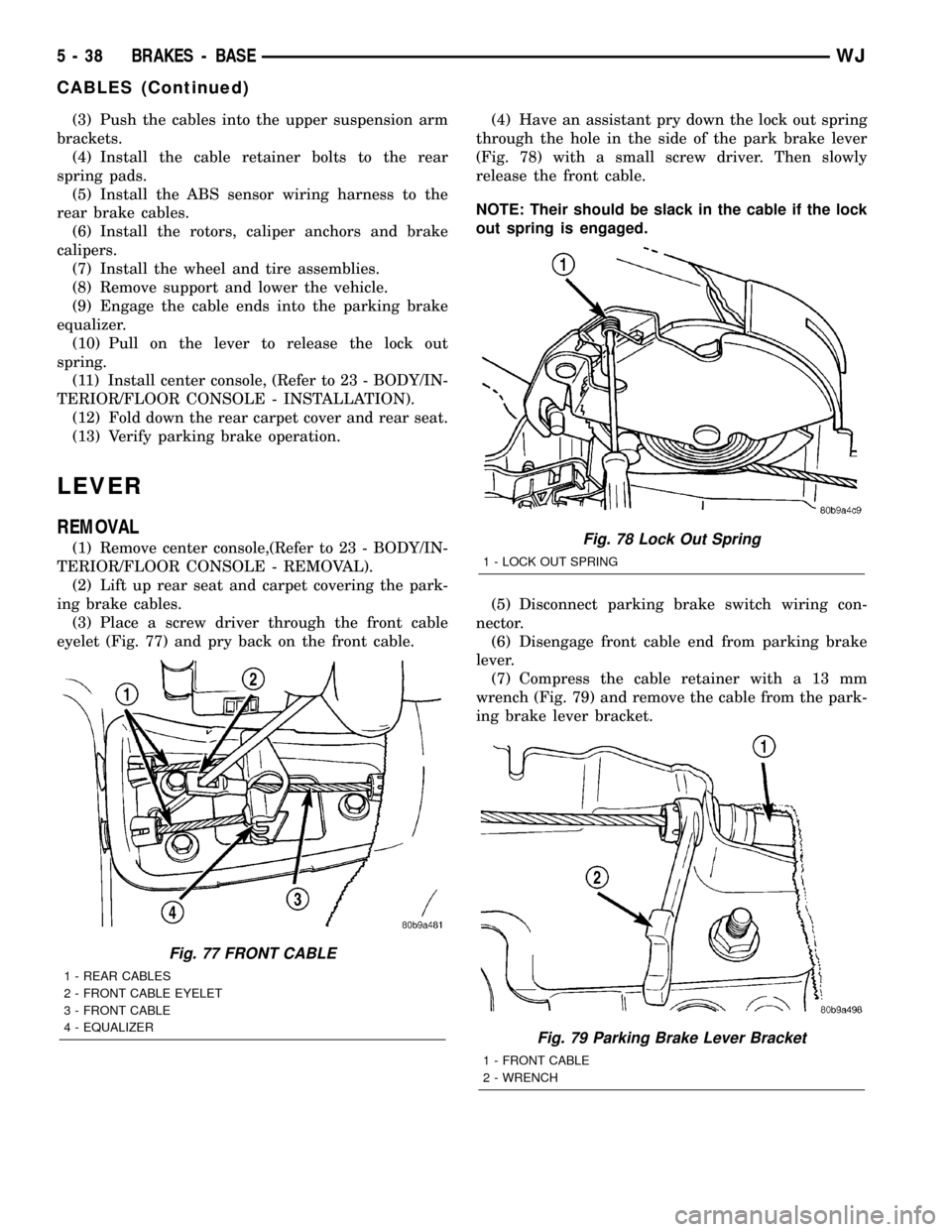
(3) Push the cables into the upper suspension arm
brackets.
(4) Install the cable retainer bolts to the rear
spring pads.
(5) Install the ABS sensor wiring harness to the
rear brake cables.
(6) Install the rotors, caliper anchors and brake
calipers.
(7) Install the wheel and tire assemblies.
(8) Remove support and lower the vehicle.
(9) Engage the cable ends into the parking brake
equalizer.
(10) Pull on the lever to release the lock out
spring.
(11) Install center console, (Refer to 23 - BODY/IN-
TERIOR/FLOOR CONSOLE - INSTALLATION).
(12) Fold down the rear carpet cover and rear seat.
(13) Verify parking brake operation.
LEVER
REMOVAL
(1) Remove center console,(Refer to 23 - BODY/IN-
TERIOR/FLOOR CONSOLE - REMOVAL).
(2) Lift up rear seat and carpet covering the park-
ing brake cables.
(3) Place a screw driver through the front cable
eyelet (Fig. 77) and pry back on the front cable.(4) Have an assistant pry down the lock out spring
through the hole in the side of the park brake lever
(Fig. 78) with a small screw driver. Then slowly
release the front cable.
NOTE: Their should be slack in the cable if the lock
out spring is engaged.
(5) Disconnect parking brake switch wiring con-
nector.
(6) Disengage front cable end from parking brake
lever.
(7) Compress the cable retainer with a 13 mm
wrench (Fig. 79) and remove the cable from the park-
ing brake lever bracket.
Fig. 77 FRONT CABLE
1 - REAR CABLES
2 - FRONT CABLE EYELET
3 - FRONT CABLE
4 - EQUALIZER
Fig. 78 Lock Out Spring
1 - LOCK OUT SPRING
Fig. 79 Parking Brake Lever Bracket
1 - FRONT CABLE
2 - WRENCH
5 - 38 BRAKES - BASEWJ
CABLES (Continued)
Page 281 of 2199
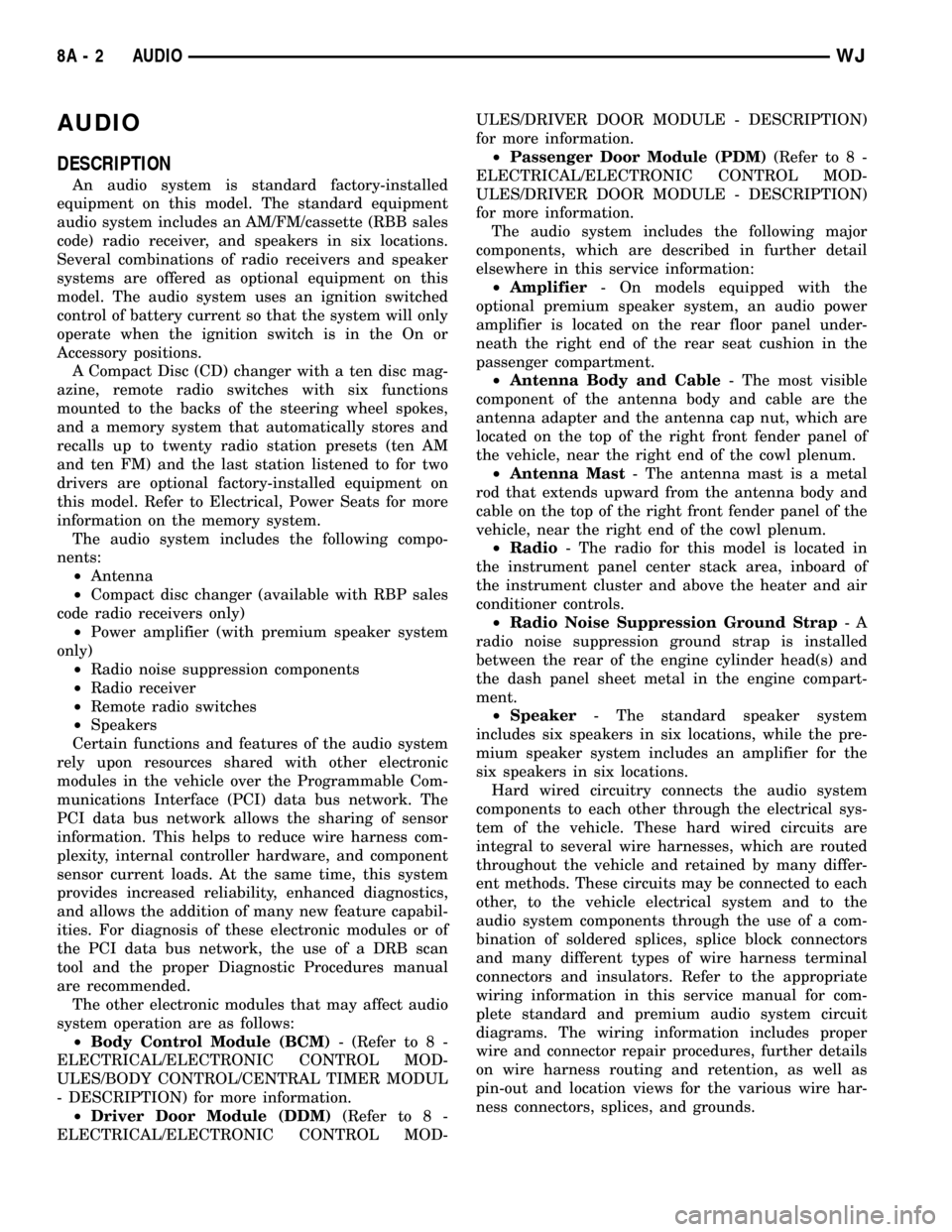
AUDIO
DESCRIPTION
An audio system is standard factory-installed
equipment on this model. The standard equipment
audio system includes an AM/FM/cassette (RBB sales
code) radio receiver, and speakers in six locations.
Several combinations of radio receivers and speaker
systems are offered as optional equipment on this
model. The audio system uses an ignition switched
control of battery current so that the system will only
operate when the ignition switch is in the On or
Accessory positions.
A Compact Disc (CD) changer with a ten disc mag-
azine, remote radio switches with six functions
mounted to the backs of the steering wheel spokes,
and a memory system that automatically stores and
recalls up to twenty radio station presets (ten AM
and ten FM) and the last station listened to for two
drivers are optional factory-installed equipment on
this model. Refer to Electrical, Power Seats for more
information on the memory system.
The audio system includes the following compo-
nents:
²Antenna
²Compact disc changer (available with RBP sales
code radio receivers only)
²Power amplifier (with premium speaker system
only)
²Radio noise suppression components
²Radio receiver
²Remote radio switches
²Speakers
Certain functions and features of the audio system
rely upon resources shared with other electronic
modules in the vehicle over the Programmable Com-
munications Interface (PCI) data bus network. The
PCI data bus network allows the sharing of sensor
information. This helps to reduce wire harness com-
plexity, internal controller hardware, and component
sensor current loads. At the same time, this system
provides increased reliability, enhanced diagnostics,
and allows the addition of many new feature capabil-
ities. For diagnosis of these electronic modules or of
the PCI data bus network, the use of a DRB scan
tool and the proper Diagnostic Procedures manual
are recommended.
The other electronic modules that may affect audio
system operation are as follows:
²Body Control Module (BCM)- (Refer to 8 -
ELECTRICAL/ELECTRONIC CONTROL MOD-
ULES/BODY CONTROL/CENTRAL TIMER MODUL
- DESCRIPTION) for more information.
²Driver Door Module (DDM)(Refer to 8 -
ELECTRICAL/ELECTRONIC CONTROL MOD-ULES/DRIVER DOOR MODULE - DESCRIPTION)
for more information.
²Passenger Door Module (PDM)(Refer to 8 -
ELECTRICAL/ELECTRONIC CONTROL MOD-
ULES/DRIVER DOOR MODULE - DESCRIPTION)
for more information.
The audio system includes the following major
components, which are described in further detail
elsewhere in this service information:
²Amplifier- On models equipped with the
optional premium speaker system, an audio power
amplifier is located on the rear floor panel under-
neath the right end of the rear seat cushion in the
passenger compartment.
²Antenna Body and Cable- The most visible
component of the antenna body and cable are the
antenna adapter and the antenna cap nut, which are
located on the top of the right front fender panel of
the vehicle, near the right end of the cowl plenum.
²Antenna Mast- The antenna mast is a metal
rod that extends upward from the antenna body and
cable on the top of the right front fender panel of the
vehicle, near the right end of the cowl plenum.
²Radio- The radio for this model is located in
the instrument panel center stack area, inboard of
the instrument cluster and above the heater and air
conditioner controls.
²Radio Noise Suppression Ground Strap-A
radio noise suppression ground strap is installed
between the rear of the engine cylinder head(s) and
the dash panel sheet metal in the engine compart-
ment.
²Speaker- The standard speaker system
includes six speakers in six locations, while the pre-
mium speaker system includes an amplifier for the
six speakers in six locations.
Hard wired circuitry connects the audio system
components to each other through the electrical sys-
tem of the vehicle. These hard wired circuits are
integral to several wire harnesses, which are routed
throughout the vehicle and retained by many differ-
ent methods. These circuits may be connected to each
other, to the vehicle electrical system and to the
audio system components through the use of a com-
bination of soldered splices, splice block connectors
and many different types of wire harness terminal
connectors and insulators. Refer to the appropriate
wiring information in this service manual for com-
plete standard and premium audio system circuit
diagrams. The wiring information includes proper
wire and connector repair procedures, further details
on wire harness routing and retention, as well as
pin-out and location views for the various wire har-
ness connectors, splices, and grounds.
8A - 2 AUDIOWJ
Page 282 of 2199
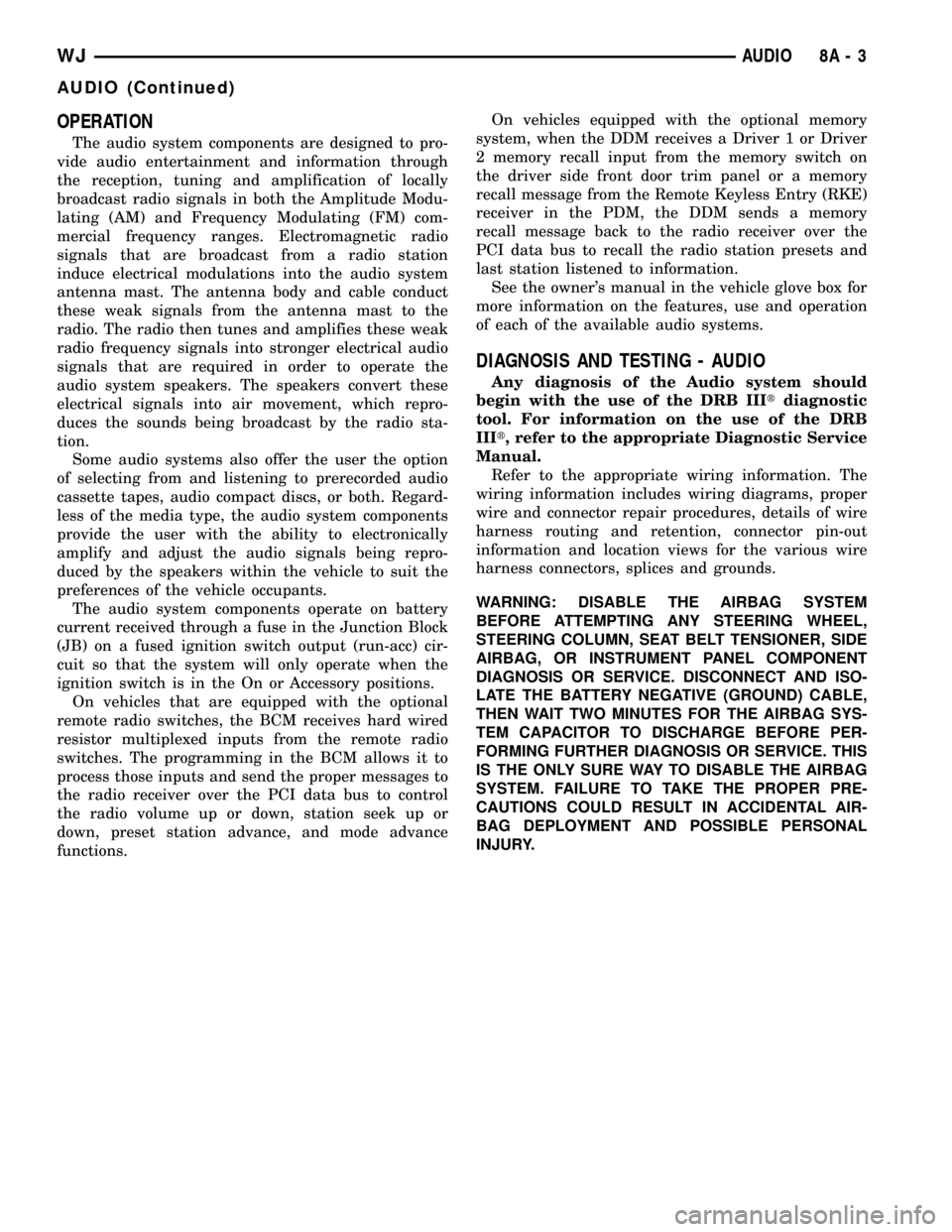
OPERATION
The audio system components are designed to pro-
vide audio entertainment and information through
the reception, tuning and amplification of locally
broadcast radio signals in both the Amplitude Modu-
lating (AM) and Frequency Modulating (FM) com-
mercial frequency ranges. Electromagnetic radio
signals that are broadcast from a radio station
induce electrical modulations into the audio system
antenna mast. The antenna body and cable conduct
these weak signals from the antenna mast to the
radio. The radio then tunes and amplifies these weak
radio frequency signals into stronger electrical audio
signals that are required in order to operate the
audio system speakers. The speakers convert these
electrical signals into air movement, which repro-
duces the sounds being broadcast by the radio sta-
tion.
Some audio systems also offer the user the option
of selecting from and listening to prerecorded audio
cassette tapes, audio compact discs, or both. Regard-
less of the media type, the audio system components
provide the user with the ability to electronically
amplify and adjust the audio signals being repro-
duced by the speakers within the vehicle to suit the
preferences of the vehicle occupants.
The audio system components operate on battery
current received through a fuse in the Junction Block
(JB) on a fused ignition switch output (run-acc) cir-
cuit so that the system will only operate when the
ignition switch is in the On or Accessory positions.
On vehicles that are equipped with the optional
remote radio switches, the BCM receives hard wired
resistor multiplexed inputs from the remote radio
switches. The programming in the BCM allows it to
process those inputs and send the proper messages to
the radio receiver over the PCI data bus to control
the radio volume up or down, station seek up or
down, preset station advance, and mode advance
functions.On vehicles equipped with the optional memory
system, when the DDM receives a Driver 1 or Driver
2 memory recall input from the memory switch on
the driver side front door trim panel or a memory
recall message from the Remote Keyless Entry (RKE)
receiver in the PDM, the DDM sends a memory
recall message back to the radio receiver over the
PCI data bus to recall the radio station presets and
last station listened to information.
See the owner's manual in the vehicle glove box for
more information on the features, use and operation
of each of the available audio systems.
DIAGNOSIS AND TESTING - AUDIO
Any diagnosis of the Audio system should
begin with the use of the DRB IIItdiagnostic
tool. For information on the use of the DRB
IIIt, refer to the appropriate Diagnostic Service
Manual.
Refer to the appropriate wiring information. The
wiring information includes wiring diagrams, proper
wire and connector repair procedures, details of wire
harness routing and retention, connector pin-out
information and location views for the various wire
harness connectors, splices and grounds.
WARNING: DISABLE THE AIRBAG SYSTEM
BEFORE ATTEMPTING ANY STEERING WHEEL,
STEERING COLUMN, SEAT BELT TENSIONER, SIDE
AIRBAG, OR INSTRUMENT PANEL COMPONENT
DIAGNOSIS OR SERVICE. DISCONNECT AND ISO-
LATE THE BATTERY NEGATIVE (GROUND) CABLE,
THEN WAIT TWO MINUTES FOR THE AIRBAG SYS-
TEM CAPACITOR TO DISCHARGE BEFORE PER-
FORMING FURTHER DIAGNOSIS OR SERVICE. THIS
IS THE ONLY SURE WAY TO DISABLE THE AIRBAG
SYSTEM. FAILURE TO TAKE THE PROPER PRE-
CAUTIONS COULD RESULT IN ACCIDENTAL AIR-
BAG DEPLOYMENT AND POSSIBLE PERSONAL
INJURY.
WJAUDIO 8A - 3
AUDIO (Continued)