driver seat JEEP GRAND CHEROKEE 2002 WJ / 2.G Workshop Manual
[x] Cancel search | Manufacturer: JEEP, Model Year: 2002, Model line: GRAND CHEROKEE, Model: JEEP GRAND CHEROKEE 2002 WJ / 2.GPages: 2199, PDF Size: 76.01 MB
Page 1613 of 2199
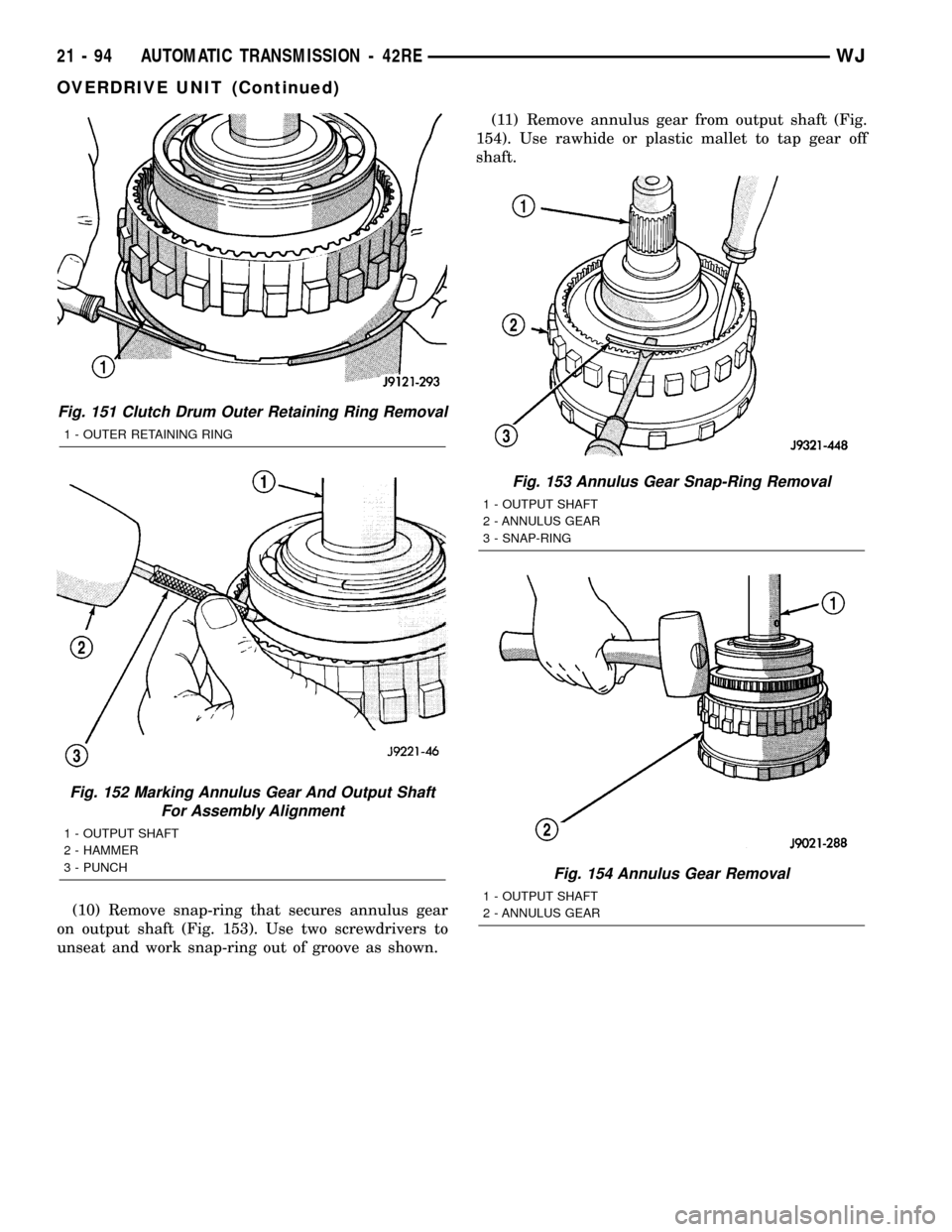
(10) Remove snap-ring that secures annulus gear
on output shaft (Fig. 153). Use two screwdrivers to
unseat and work snap-ring out of groove as shown.(11) Remove annulus gear from output shaft (Fig.
154). Use rawhide or plastic mallet to tap gear off
shaft.
Fig. 151 Clutch Drum Outer Retaining Ring Removal
1 - OUTER RETAINING RING
Fig. 152 Marking Annulus Gear And Output Shaft
For Assembly Alignment
1 - OUTPUT SHAFT
2 - HAMMER
3 - PUNCH
Fig. 153 Annulus Gear Snap-Ring Removal
1 - OUTPUT SHAFT
2 - ANNULUS GEAR
3 - SNAP-RING
Fig. 154 Annulus Gear Removal
1 - OUTPUT SHAFT
2 - ANNULUS GEAR
21 - 94 AUTOMATIC TRANSMISSION - 42REWJ
OVERDRIVE UNIT (Continued)
Page 1620 of 2199
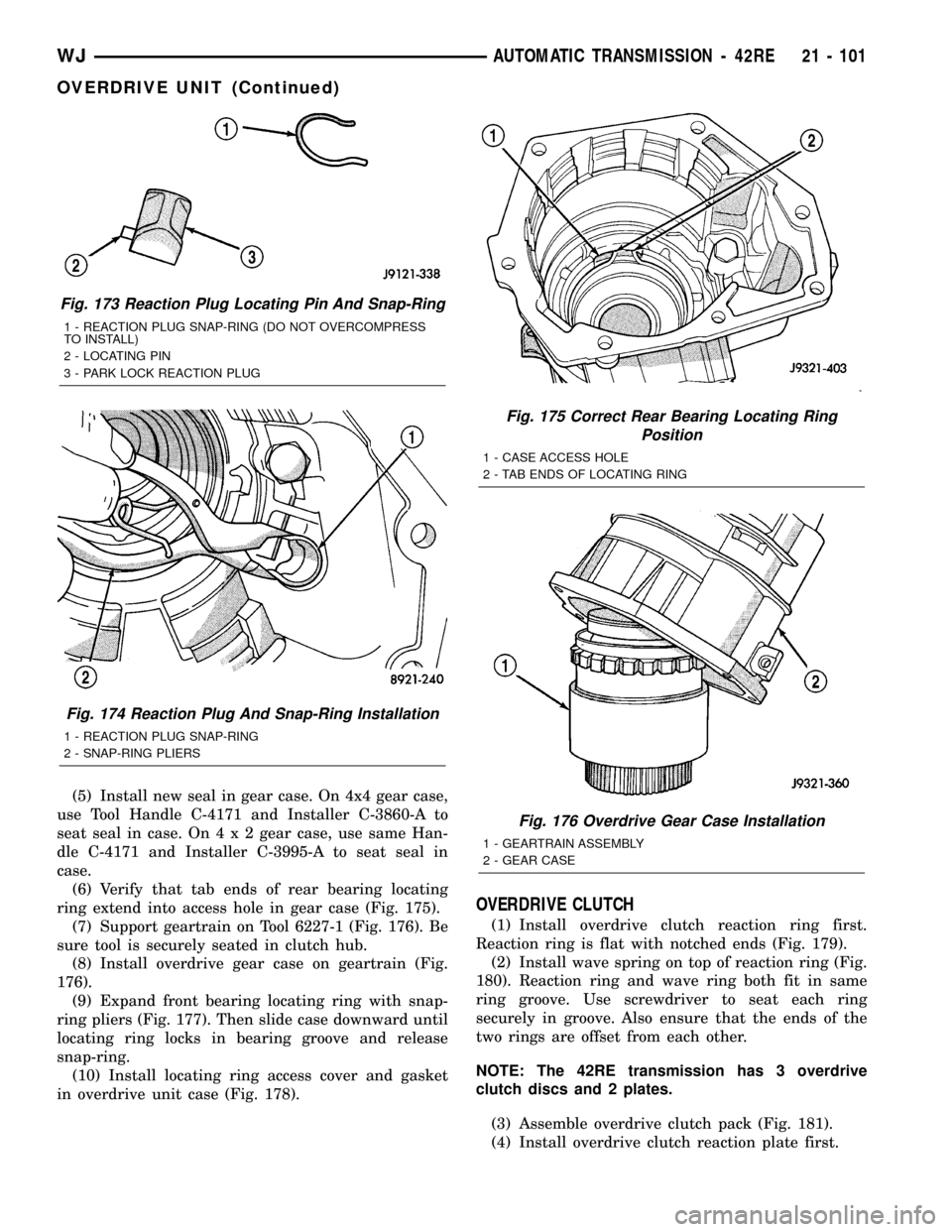
(5) Install new seal in gear case. On 4x4 gear case,
use Tool Handle C-4171 and Installer C-3860-A to
seat seal in case. On4x2gear case, use same Han-
dle C-4171 and Installer C-3995-A to seat seal in
case.
(6) Verify that tab ends of rear bearing locating
ring extend into access hole in gear case (Fig. 175).
(7) Support geartrain on Tool 6227-1 (Fig. 176). Be
sure tool is securely seated in clutch hub.
(8) Install overdrive gear case on geartrain (Fig.
176).
(9) Expand front bearing locating ring with snap-
ring pliers (Fig. 177). Then slide case downward until
locating ring locks in bearing groove and release
snap-ring.
(10) Install locating ring access cover and gasket
in overdrive unit case (Fig. 178).
OVERDRIVE CLUTCH
(1) Install overdrive clutch reaction ring first.
Reaction ring is flat with notched ends (Fig. 179).
(2) Install wave spring on top of reaction ring (Fig.
180). Reaction ring and wave ring both fit in same
ring groove. Use screwdriver to seat each ring
securely in groove. Also ensure that the ends of the
two rings are offset from each other.
NOTE: The 42RE transmission has 3 overdrive
clutch discs and 2 plates.
(3) Assemble overdrive clutch pack (Fig. 181).
(4) Install overdrive clutch reaction plate first.
Fig. 173 Reaction Plug Locating Pin And Snap-Ring
1 - REACTION PLUG SNAP-RING (DO NOT OVERCOMPRESS
TO INSTALL)
2 - LOCATING PIN
3 - PARK LOCK REACTION PLUG
Fig. 174 Reaction Plug And Snap-Ring Installation
1 - REACTION PLUG SNAP-RING
2 - SNAP-RING PLIERS
Fig. 175 Correct Rear Bearing Locating Ring
Position
1 - CASE ACCESS HOLE
2 - TAB ENDS OF LOCATING RING
Fig. 176 Overdrive Gear Case Installation
1 - GEARTRAIN ASSEMBLY
2 - GEAR CASE
WJAUTOMATIC TRANSMISSION - 42RE 21 - 101
OVERDRIVE UNIT (Continued)
Page 1621 of 2199
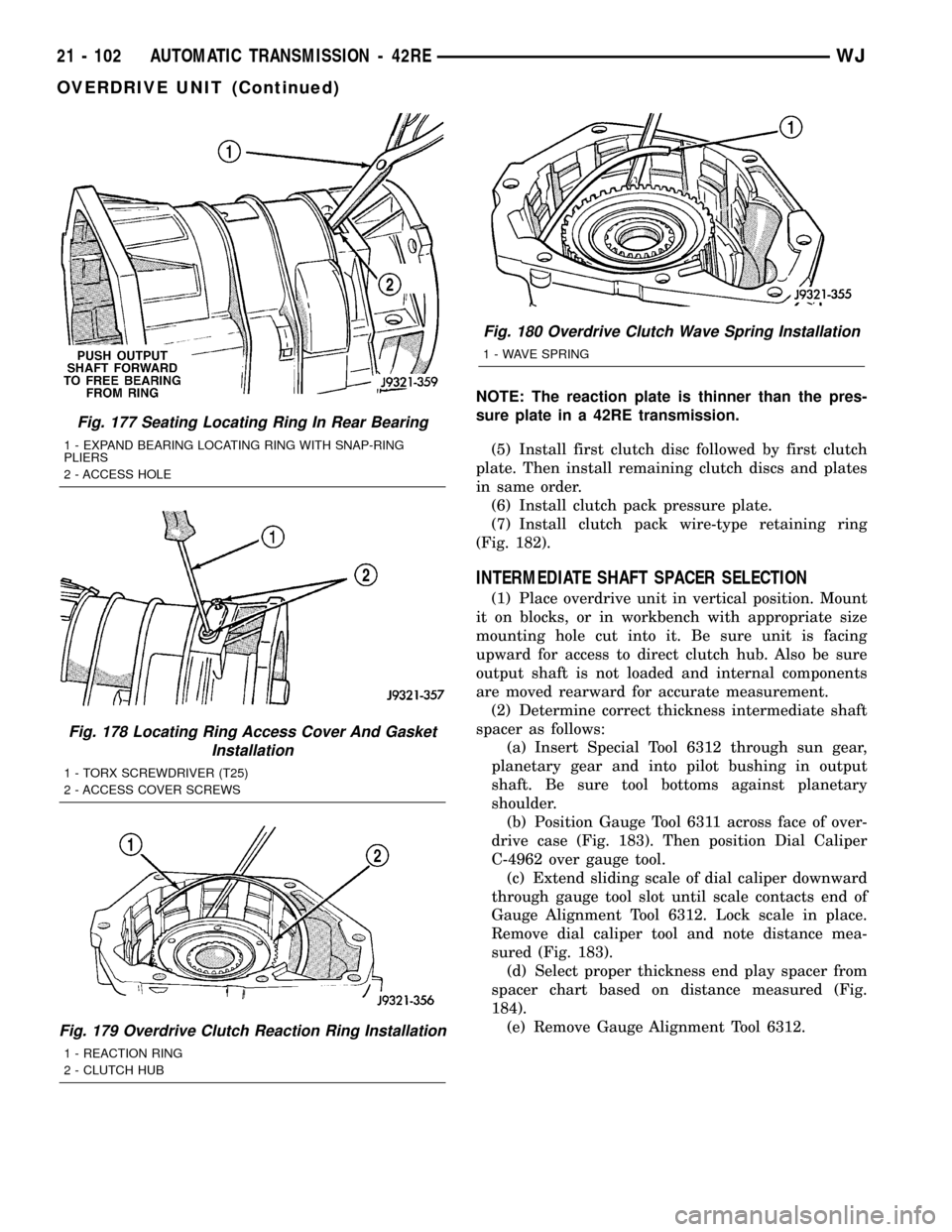
NOTE: The reaction plate is thinner than the pres-
sure plate in a 42RE transmission.
(5) Install first clutch disc followed by first clutch
plate. Then install remaining clutch discs and plates
in same order.
(6) Install clutch pack pressure plate.
(7) Install clutch pack wire-type retaining ring
(Fig. 182).
INTERMEDIATE SHAFT SPACER SELECTION
(1) Place overdrive unit in vertical position. Mount
it on blocks, or in workbench with appropriate size
mounting hole cut into it. Be sure unit is facing
upward for access to direct clutch hub. Also be sure
output shaft is not loaded and internal components
are moved rearward for accurate measurement.
(2) Determine correct thickness intermediate shaft
spacer as follows:
(a) Insert Special Tool 6312 through sun gear,
planetary gear and into pilot bushing in output
shaft. Be sure tool bottoms against planetary
shoulder.
(b) Position Gauge Tool 6311 across face of over-
drive case (Fig. 183). Then position Dial Caliper
C-4962 over gauge tool.
(c) Extend sliding scale of dial caliper downward
through gauge tool slot until scale contacts end of
Gauge Alignment Tool 6312. Lock scale in place.
Remove dial caliper tool and note distance mea-
sured (Fig. 183).
(d) Select proper thickness end play spacer from
spacer chart based on distance measured (Fig.
184).
(e) Remove Gauge Alignment Tool 6312.
Fig. 177 Seating Locating Ring In Rear Bearing
1 - EXPAND BEARING LOCATING RING WITH SNAP-RING
PLIERS
2 - ACCESS HOLE
Fig. 178 Locating Ring Access Cover And Gasket
Installation
1 - TORX SCREWDRIVER (T25)
2 - ACCESS COVER SCREWS
Fig. 179 Overdrive Clutch Reaction Ring Installation
1 - REACTION RING
2 - CLUTCH HUB
Fig. 180 Overdrive Clutch Wave Spring Installation
1 - WAVE SPRING
21 - 102 AUTOMATIC TRANSMISSION - 42REWJ
OVERDRIVE UNIT (Continued)
Page 1639 of 2199
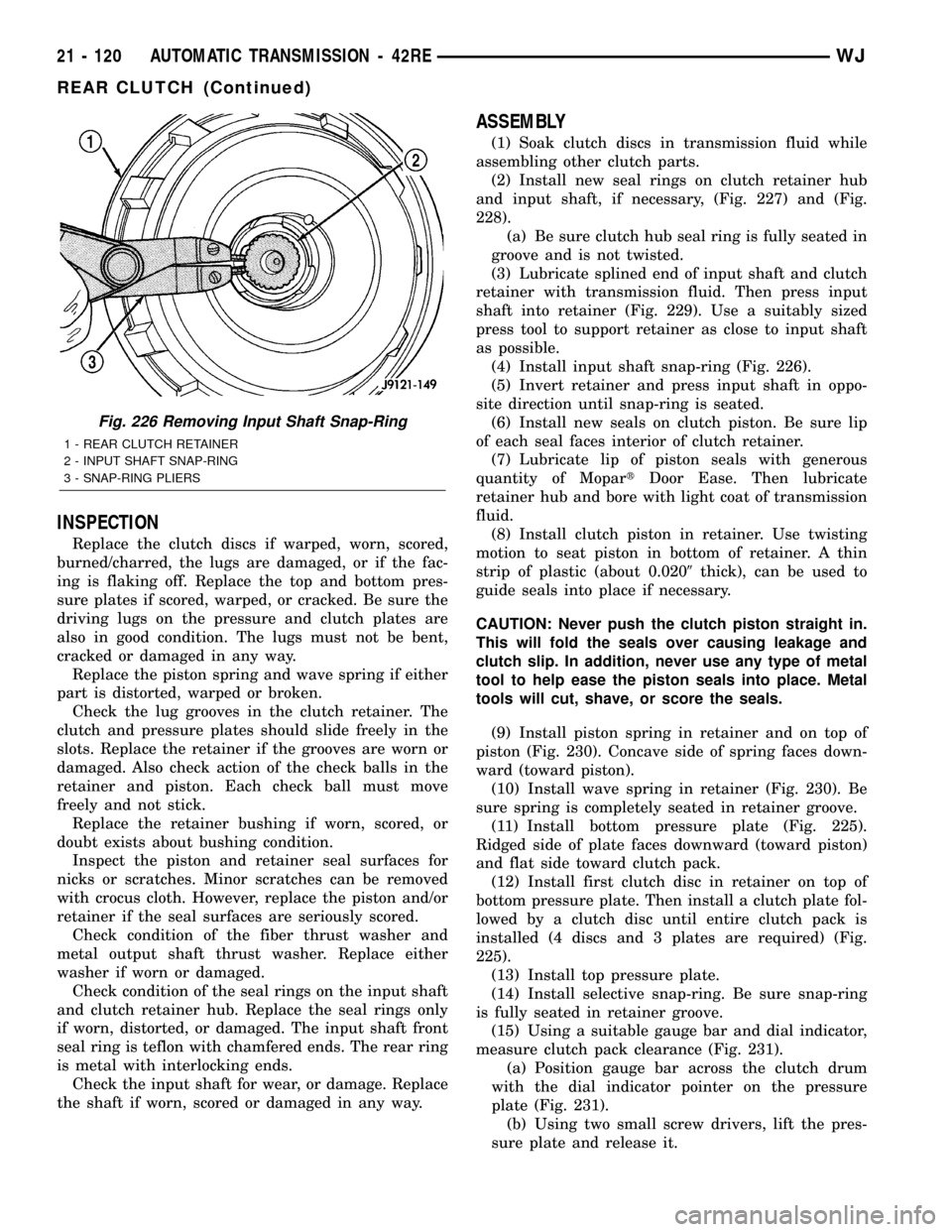
INSPECTION
Replace the clutch discs if warped, worn, scored,
burned/charred, the lugs are damaged, or if the fac-
ing is flaking off. Replace the top and bottom pres-
sure plates if scored, warped, or cracked. Be sure the
driving lugs on the pressure and clutch plates are
also in good condition. The lugs must not be bent,
cracked or damaged in any way.
Replace the piston spring and wave spring if either
part is distorted, warped or broken.
Check the lug grooves in the clutch retainer. The
clutch and pressure plates should slide freely in the
slots. Replace the retainer if the grooves are worn or
damaged. Also check action of the check balls in the
retainer and piston. Each check ball must move
freely and not stick.
Replace the retainer bushing if worn, scored, or
doubt exists about bushing condition.
Inspect the piston and retainer seal surfaces for
nicks or scratches. Minor scratches can be removed
with crocus cloth. However, replace the piston and/or
retainer if the seal surfaces are seriously scored.
Check condition of the fiber thrust washer and
metal output shaft thrust washer. Replace either
washer if worn or damaged.
Check condition of the seal rings on the input shaft
and clutch retainer hub. Replace the seal rings only
if worn, distorted, or damaged. The input shaft front
seal ring is teflon with chamfered ends. The rear ring
is metal with interlocking ends.
Check the input shaft for wear, or damage. Replace
the shaft if worn, scored or damaged in any way.
ASSEMBLY
(1) Soak clutch discs in transmission fluid while
assembling other clutch parts.
(2) Install new seal rings on clutch retainer hub
and input shaft, if necessary, (Fig. 227) and (Fig.
228).
(a) Be sure clutch hub seal ring is fully seated in
groove and is not twisted.
(3) Lubricate splined end of input shaft and clutch
retainer with transmission fluid. Then press input
shaft into retainer (Fig. 229). Use a suitably sized
press tool to support retainer as close to input shaft
as possible.
(4) Install input shaft snap-ring (Fig. 226).
(5) Invert retainer and press input shaft in oppo-
site direction until snap-ring is seated.
(6) Install new seals on clutch piston. Be sure lip
of each seal faces interior of clutch retainer.
(7) Lubricate lip of piston seals with generous
quantity of MopartDoor Ease. Then lubricate
retainer hub and bore with light coat of transmission
fluid.
(8) Install clutch piston in retainer. Use twisting
motion to seat piston in bottom of retainer. A thin
strip of plastic (about 0.0209thick), can be used to
guide seals into place if necessary.
CAUTION: Never push the clutch piston straight in.
This will fold the seals over causing leakage and
clutch slip. In addition, never use any type of metal
tool to help ease the piston seals into place. Metal
tools will cut, shave, or score the seals.
(9) Install piston spring in retainer and on top of
piston (Fig. 230). Concave side of spring faces down-
ward (toward piston).
(10) Install wave spring in retainer (Fig. 230). Be
sure spring is completely seated in retainer groove.
(11) Install bottom pressure plate (Fig. 225).
Ridged side of plate faces downward (toward piston)
and flat side toward clutch pack.
(12) Install first clutch disc in retainer on top of
bottom pressure plate. Then install a clutch plate fol-
lowed by a clutch disc until entire clutch pack is
installed (4 discs and 3 plates are required) (Fig.
225).
(13) Install top pressure plate.
(14) Install selective snap-ring. Be sure snap-ring
is fully seated in retainer groove.
(15) Using a suitable gauge bar and dial indicator,
measure clutch pack clearance (Fig. 231).
(a) Position gauge bar across the clutch drum
with the dial indicator pointer on the pressure
plate (Fig. 231).
(b) Using two small screw drivers, lift the pres-
sure plate and release it.
Fig. 226 Removing Input Shaft Snap-Ring
1 - REAR CLUTCH RETAINER
2 - INPUT SHAFT SNAP-RING
3 - SNAP-RING PLIERS
21 - 120 AUTOMATIC TRANSMISSION - 42REWJ
REAR CLUTCH (Continued)
Page 1844 of 2199
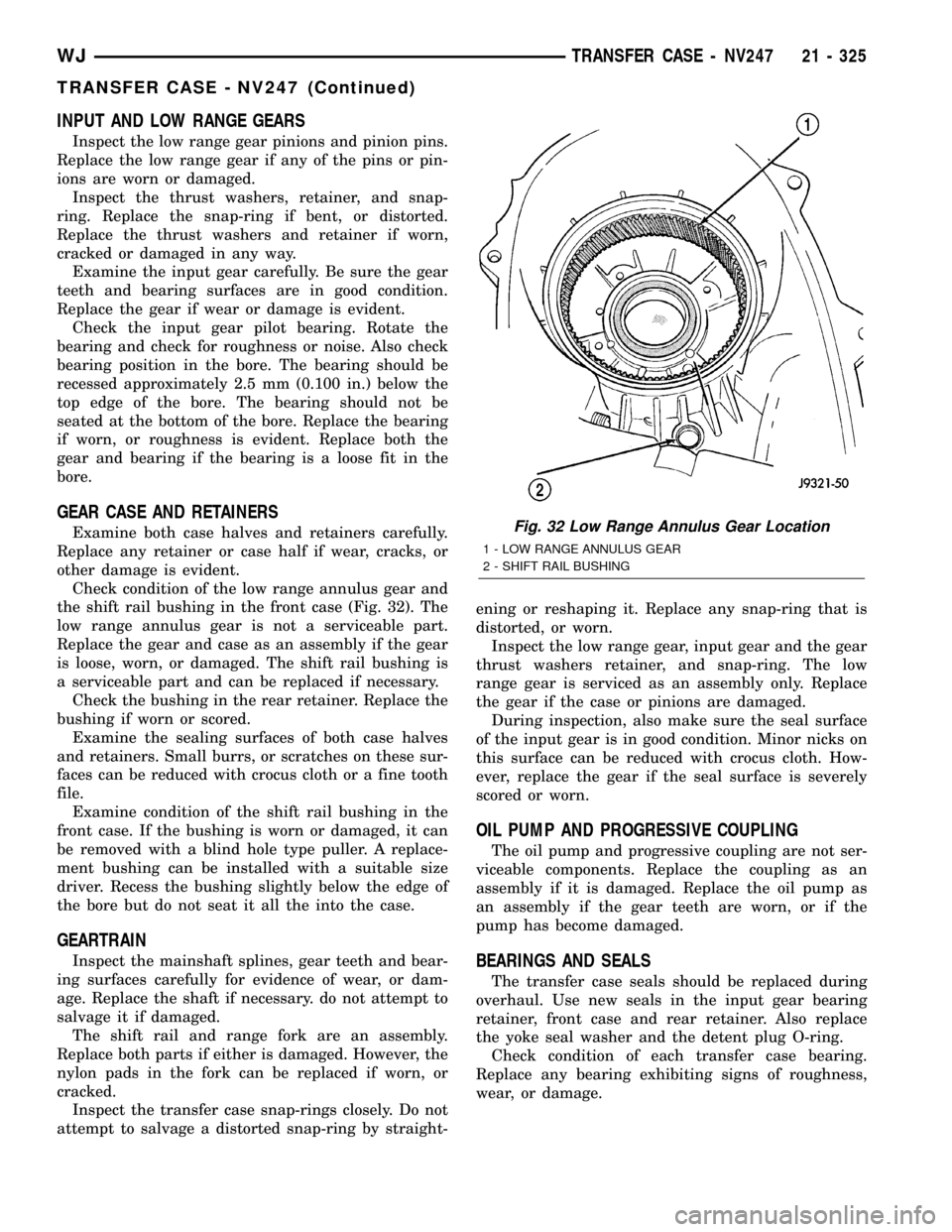
INPUT AND LOW RANGE GEARS
Inspect the low range gear pinions and pinion pins.
Replace the low range gear if any of the pins or pin-
ions are worn or damaged.
Inspect the thrust washers, retainer, and snap-
ring. Replace the snap-ring if bent, or distorted.
Replace the thrust washers and retainer if worn,
cracked or damaged in any way.
Examine the input gear carefully. Be sure the gear
teeth and bearing surfaces are in good condition.
Replace the gear if wear or damage is evident.
Check the input gear pilot bearing. Rotate the
bearing and check for roughness or noise. Also check
bearing position in the bore. The bearing should be
recessed approximately 2.5 mm (0.100 in.) below the
top edge of the bore. The bearing should not be
seated at the bottom of the bore. Replace the bearing
if worn, or roughness is evident. Replace both the
gear and bearing if the bearing is a loose fit in the
bore.
GEAR CASE AND RETAINERS
Examine both case halves and retainers carefully.
Replace any retainer or case half if wear, cracks, or
other damage is evident.
Check condition of the low range annulus gear and
the shift rail bushing in the front case (Fig. 32). The
low range annulus gear is not a serviceable part.
Replace the gear and case as an assembly if the gear
is loose, worn, or damaged. The shift rail bushing is
a serviceable part and can be replaced if necessary.
Check the bushing in the rear retainer. Replace the
bushing if worn or scored.
Examine the sealing surfaces of both case halves
and retainers. Small burrs, or scratches on these sur-
faces can be reduced with crocus cloth or a fine tooth
file.
Examine condition of the shift rail bushing in the
front case. If the bushing is worn or damaged, it can
be removed with a blind hole type puller. A replace-
ment bushing can be installed with a suitable size
driver. Recess the bushing slightly below the edge of
the bore but do not seat it all the into the case.
GEARTRAIN
Inspect the mainshaft splines, gear teeth and bear-
ing surfaces carefully for evidence of wear, or dam-
age. Replace the shaft if necessary. do not attempt to
salvage it if damaged.
The shift rail and range fork are an assembly.
Replace both parts if either is damaged. However, the
nylon pads in the fork can be replaced if worn, or
cracked.
Inspect the transfer case snap-rings closely. Do not
attempt to salvage a distorted snap-ring by straight-ening or reshaping it. Replace any snap-ring that is
distorted, or worn.
Inspect the low range gear, input gear and the gear
thrust washers retainer, and snap-ring. The low
range gear is serviced as an assembly only. Replace
the gear if the case or pinions are damaged.
During inspection, also make sure the seal surface
of the input gear is in good condition. Minor nicks on
this surface can be reduced with crocus cloth. How-
ever, replace the gear if the seal surface is severely
scored or worn.
OIL PUMP AND PROGRESSIVE COUPLING
The oil pump and progressive coupling are not ser-
viceable components. Replace the coupling as an
assembly if it is damaged. Replace the oil pump as
an assembly if the gear teeth are worn, or if the
pump has become damaged.
BEARINGS AND SEALS
The transfer case seals should be replaced during
overhaul. Use new seals in the input gear bearing
retainer, front case and rear retainer. Also replace
the yoke seal washer and the detent plug O-ring.
Check condition of each transfer case bearing.
Replace any bearing exhibiting signs of roughness,
wear, or damage.
Fig. 32 Low Range Annulus Gear Location
1 - LOW RANGE ANNULUS GEAR
2 - SHIFT RAIL BUSHING
WJTRANSFER CASE - NV247 21 - 325
TRANSFER CASE - NV247 (Continued)
Page 1916 of 2199
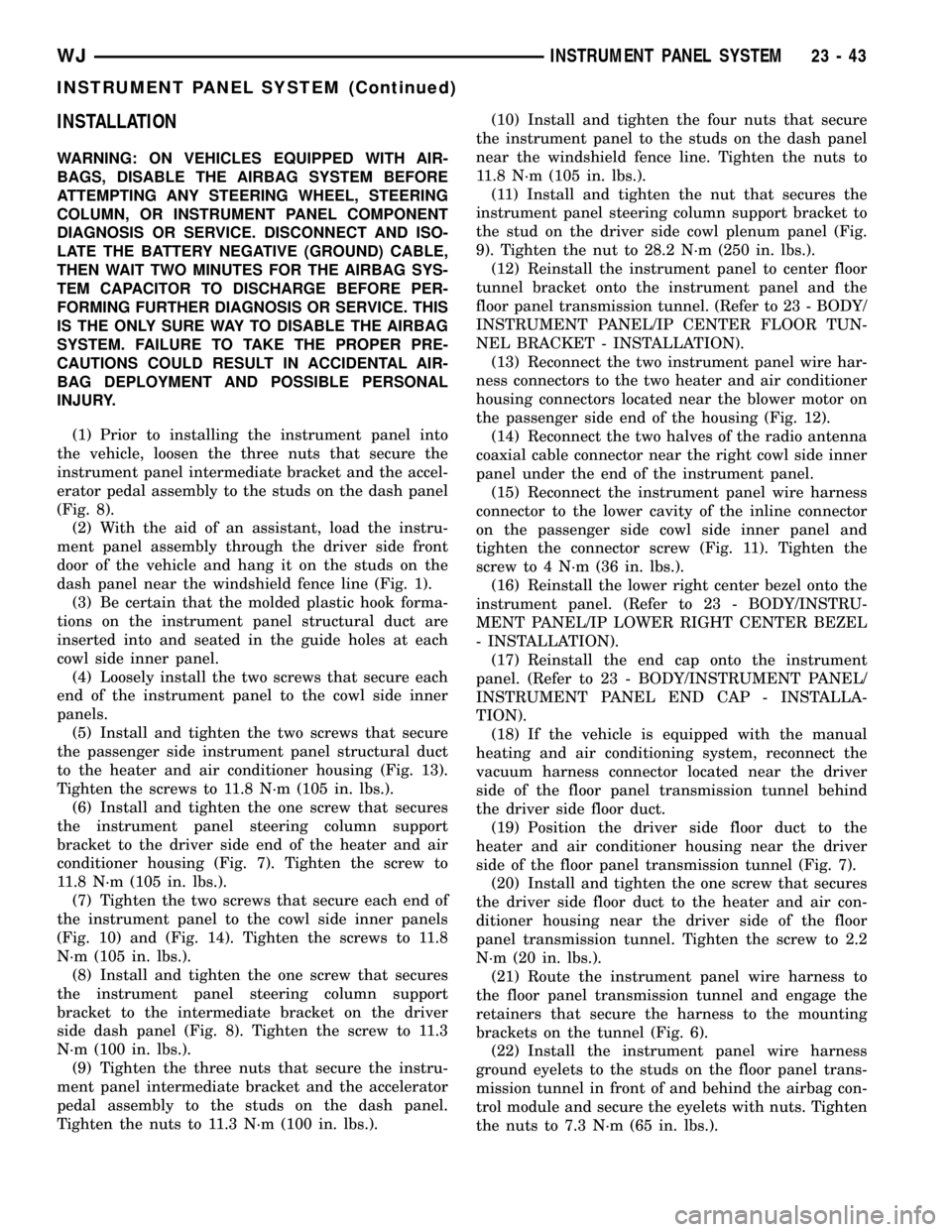
INSTALLATION
WARNING: ON VEHICLES EQUIPPED WITH AIR-
BAGS, DISABLE THE AIRBAG SYSTEM BEFORE
ATTEMPTING ANY STEERING WHEEL, STEERING
COLUMN, OR INSTRUMENT PANEL COMPONENT
DIAGNOSIS OR SERVICE. DISCONNECT AND ISO-
LATE THE BATTERY NEGATIVE (GROUND) CABLE,
THEN WAIT TWO MINUTES FOR THE AIRBAG SYS-
TEM CAPACITOR TO DISCHARGE BEFORE PER-
FORMING FURTHER DIAGNOSIS OR SERVICE. THIS
IS THE ONLY SURE WAY TO DISABLE THE AIRBAG
SYSTEM. FAILURE TO TAKE THE PROPER PRE-
CAUTIONS COULD RESULT IN ACCIDENTAL AIR-
BAG DEPLOYMENT AND POSSIBLE PERSONAL
INJURY.
(1) Prior to installing the instrument panel into
the vehicle, loosen the three nuts that secure the
instrument panel intermediate bracket and the accel-
erator pedal assembly to the studs on the dash panel
(Fig. 8).
(2) With the aid of an assistant, load the instru-
ment panel assembly through the driver side front
door of the vehicle and hang it on the studs on the
dash panel near the windshield fence line (Fig. 1).
(3) Be certain that the molded plastic hook forma-
tions on the instrument panel structural duct are
inserted into and seated in the guide holes at each
cowl side inner panel.
(4) Loosely install the two screws that secure each
end of the instrument panel to the cowl side inner
panels.
(5) Install and tighten the two screws that secure
the passenger side instrument panel structural duct
to the heater and air conditioner housing (Fig. 13).
Tighten the screws to 11.8 N´m (105 in. lbs.).
(6) Install and tighten the one screw that secures
the instrument panel steering column support
bracket to the driver side end of the heater and air
conditioner housing (Fig. 7). Tighten the screw to
11.8 N´m (105 in. lbs.).
(7) Tighten the two screws that secure each end of
the instrument panel to the cowl side inner panels
(Fig. 10) and (Fig. 14). Tighten the screws to 11.8
N´m (105 in. lbs.).
(8) Install and tighten the one screw that secures
the instrument panel steering column support
bracket to the intermediate bracket on the driver
side dash panel (Fig. 8). Tighten the screw to 11.3
N´m (100 in. lbs.).
(9) Tighten the three nuts that secure the instru-
ment panel intermediate bracket and the accelerator
pedal assembly to the studs on the dash panel.
Tighten the nuts to 11.3 N´m (100 in. lbs.).(10) Install and tighten the four nuts that secure
the instrument panel to the studs on the dash panel
near the windshield fence line. Tighten the nuts to
11.8 N´m (105 in. lbs.).
(11) Install and tighten the nut that secures the
instrument panel steering column support bracket to
the stud on the driver side cowl plenum panel (Fig.
9). Tighten the nut to 28.2 N´m (250 in. lbs.).
(12) Reinstall the instrument panel to center floor
tunnel bracket onto the instrument panel and the
floor panel transmission tunnel. (Refer to 23 - BODY/
INSTRUMENT PANEL/IP CENTER FLOOR TUN-
NEL BRACKET - INSTALLATION).
(13) Reconnect the two instrument panel wire har-
ness connectors to the two heater and air conditioner
housing connectors located near the blower motor on
the passenger side end of the housing (Fig. 12).
(14) Reconnect the two halves of the radio antenna
coaxial cable connector near the right cowl side inner
panel under the end of the instrument panel.
(15) Reconnect the instrument panel wire harness
connector to the lower cavity of the inline connector
on the passenger side cowl side inner panel and
tighten the connector screw (Fig. 11). Tighten the
screw to 4 N´m (36 in. lbs.).
(16) Reinstall the lower right center bezel onto the
instrument panel. (Refer to 23 - BODY/INSTRU-
MENT PANEL/IP LOWER RIGHT CENTER BEZEL
- INSTALLATION).
(17) Reinstall the end cap onto the instrument
panel. (Refer to 23 - BODY/INSTRUMENT PANEL/
INSTRUMENT PANEL END CAP - INSTALLA-
TION).
(18) If the vehicle is equipped with the manual
heating and air conditioning system, reconnect the
vacuum harness connector located near the driver
side of the floor panel transmission tunnel behind
the driver side floor duct.
(19) Position the driver side floor duct to the
heater and air conditioner housing near the driver
side of the floor panel transmission tunnel (Fig. 7).
(20) Install and tighten the one screw that secures
the driver side floor duct to the heater and air con-
ditioner housing near the driver side of the floor
panel transmission tunnel. Tighten the screw to 2.2
N´m (20 in. lbs.).
(21) Route the instrument panel wire harness to
the floor panel transmission tunnel and engage the
retainers that secure the harness to the mounting
brackets on the tunnel (Fig. 6).
(22) Install the instrument panel wire harness
ground eyelets to the studs on the floor panel trans-
mission tunnel in front of and behind the airbag con-
trol module and secure the eyelets with nuts. Tighten
the nuts to 7.3 N´m (65 in. lbs.).
WJINSTRUMENT PANEL SYSTEM 23 - 43
INSTRUMENT PANEL SYSTEM (Continued)
Page 1925 of 2199
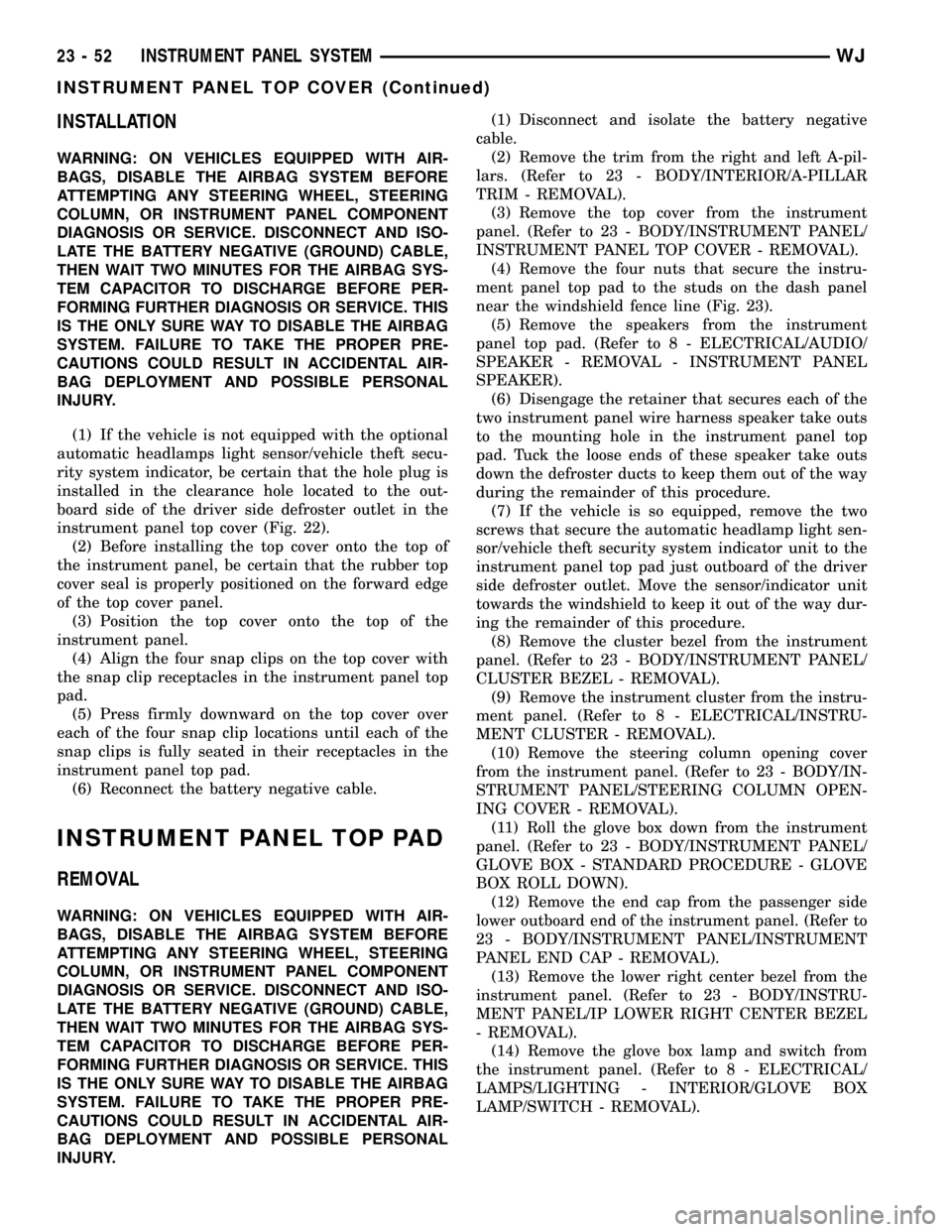
INSTALLATION
WARNING: ON VEHICLES EQUIPPED WITH AIR-
BAGS, DISABLE THE AIRBAG SYSTEM BEFORE
ATTEMPTING ANY STEERING WHEEL, STEERING
COLUMN, OR INSTRUMENT PANEL COMPONENT
DIAGNOSIS OR SERVICE. DISCONNECT AND ISO-
LATE THE BATTERY NEGATIVE (GROUND) CABLE,
THEN WAIT TWO MINUTES FOR THE AIRBAG SYS-
TEM CAPACITOR TO DISCHARGE BEFORE PER-
FORMING FURTHER DIAGNOSIS OR SERVICE. THIS
IS THE ONLY SURE WAY TO DISABLE THE AIRBAG
SYSTEM. FAILURE TO TAKE THE PROPER PRE-
CAUTIONS COULD RESULT IN ACCIDENTAL AIR-
BAG DEPLOYMENT AND POSSIBLE PERSONAL
INJURY.
(1) If the vehicle is not equipped with the optional
automatic headlamps light sensor/vehicle theft secu-
rity system indicator, be certain that the hole plug is
installed in the clearance hole located to the out-
board side of the driver side defroster outlet in the
instrument panel top cover (Fig. 22).
(2) Before installing the top cover onto the top of
the instrument panel, be certain that the rubber top
cover seal is properly positioned on the forward edge
of the top cover panel.
(3) Position the top cover onto the top of the
instrument panel.
(4) Align the four snap clips on the top cover with
the snap clip receptacles in the instrument panel top
pad.
(5) Press firmly downward on the top cover over
each of the four snap clip locations until each of the
snap clips is fully seated in their receptacles in the
instrument panel top pad.
(6) Reconnect the battery negative cable.
INSTRUMENT PANEL TOP PAD
REMOVAL
WARNING: ON VEHICLES EQUIPPED WITH AIR-
BAGS, DISABLE THE AIRBAG SYSTEM BEFORE
ATTEMPTING ANY STEERING WHEEL, STEERING
COLUMN, OR INSTRUMENT PANEL COMPONENT
DIAGNOSIS OR SERVICE. DISCONNECT AND ISO-
LATE THE BATTERY NEGATIVE (GROUND) CABLE,
THEN WAIT TWO MINUTES FOR THE AIRBAG SYS-
TEM CAPACITOR TO DISCHARGE BEFORE PER-
FORMING FURTHER DIAGNOSIS OR SERVICE. THIS
IS THE ONLY SURE WAY TO DISABLE THE AIRBAG
SYSTEM. FAILURE TO TAKE THE PROPER PRE-
CAUTIONS COULD RESULT IN ACCIDENTAL AIR-
BAG DEPLOYMENT AND POSSIBLE PERSONAL
INJURY.(1) Disconnect and isolate the battery negative
cable.
(2) Remove the trim from the right and left A-pil-
lars. (Refer to 23 - BODY/INTERIOR/A-PILLAR
TRIM - REMOVAL).
(3) Remove the top cover from the instrument
panel. (Refer to 23 - BODY/INSTRUMENT PANEL/
INSTRUMENT PANEL TOP COVER - REMOVAL).
(4) Remove the four nuts that secure the instru-
ment panel top pad to the studs on the dash panel
near the windshield fence line (Fig. 23).
(5) Remove the speakers from the instrument
panel top pad. (Refer to 8 - ELECTRICAL/AUDIO/
SPEAKER - REMOVAL - INSTRUMENT PANEL
SPEAKER).
(6) Disengage the retainer that secures each of the
two instrument panel wire harness speaker take outs
to the mounting hole in the instrument panel top
pad. Tuck the loose ends of these speaker take outs
down the defroster ducts to keep them out of the way
during the remainder of this procedure.
(7) If the vehicle is so equipped, remove the two
screws that secure the automatic headlamp light sen-
sor/vehicle theft security system indicator unit to the
instrument panel top pad just outboard of the driver
side defroster outlet. Move the sensor/indicator unit
towards the windshield to keep it out of the way dur-
ing the remainder of this procedure.
(8) Remove the cluster bezel from the instrument
panel. (Refer to 23 - BODY/INSTRUMENT PANEL/
CLUSTER BEZEL - REMOVAL).
(9) Remove the instrument cluster from the instru-
ment panel. (Refer to 8 - ELECTRICAL/INSTRU-
MENT CLUSTER - REMOVAL).
(10) Remove the steering column opening cover
from the instrument panel. (Refer to 23 - BODY/IN-
STRUMENT PANEL/STEERING COLUMN OPEN-
ING COVER - REMOVAL).
(11) Roll the glove box down from the instrument
panel. (Refer to 23 - BODY/INSTRUMENT PANEL/
GLOVE BOX - STANDARD PROCEDURE - GLOVE
BOX ROLL DOWN).
(12) Remove the end cap from the passenger side
lower outboard end of the instrument panel. (Refer to
23 - BODY/INSTRUMENT PANEL/INSTRUMENT
PANEL END CAP - REMOVAL).
(13) Remove the lower right center bezel from the
instrument panel. (Refer to 23 - BODY/INSTRU-
MENT PANEL/IP LOWER RIGHT CENTER BEZEL
- REMOVAL).
(14) Remove the glove box lamp and switch from
the instrument panel. (Refer to 8 - ELECTRICAL/
LAMPS/LIGHTING - INTERIOR/GLOVE BOX
LAMP/SWITCH - REMOVAL).
23 - 52 INSTRUMENT PANEL SYSTEMWJ
INSTRUMENT PANEL TOP COVER (Continued)
Page 2080 of 2199
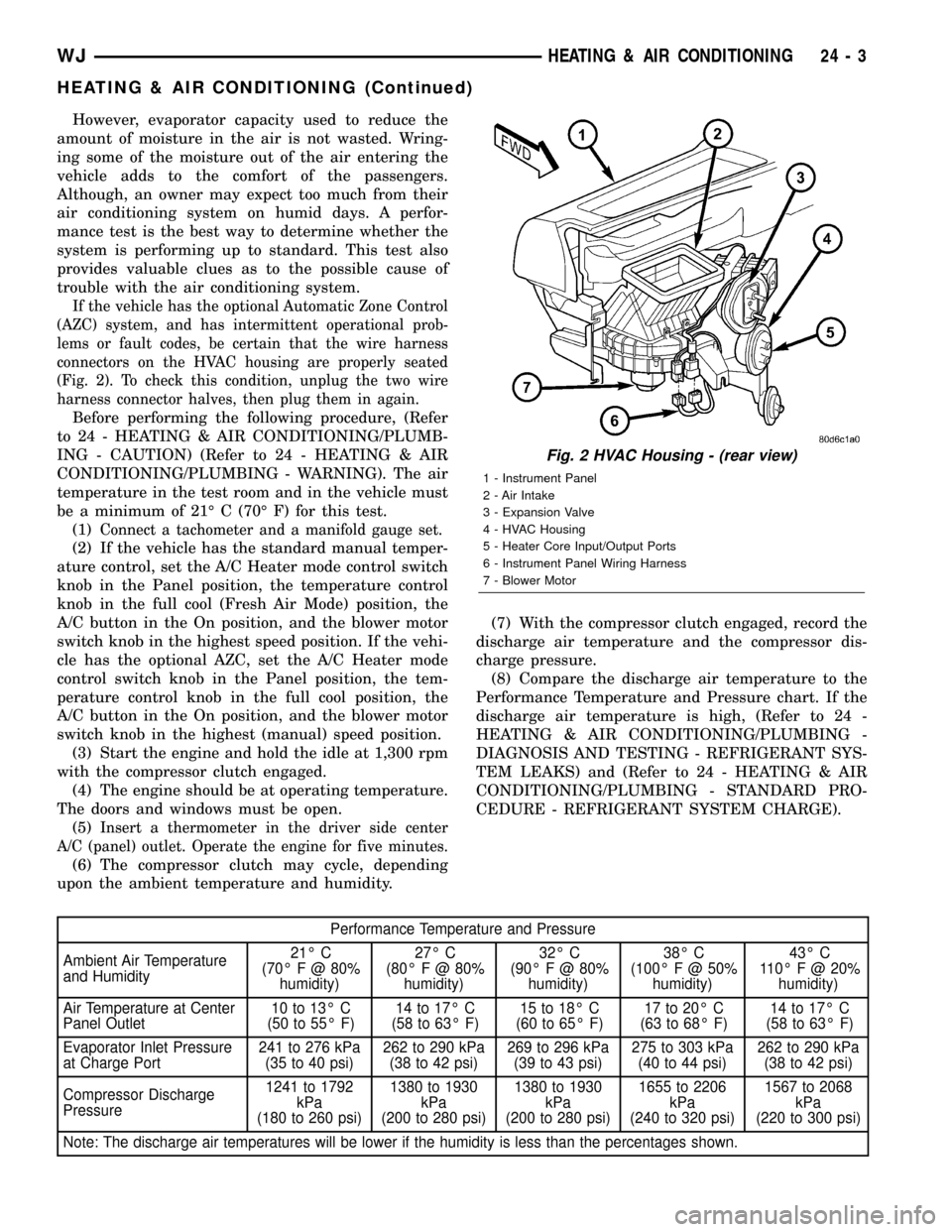
However, evaporator capacity used to reduce the
amount of moisture in the air is not wasted. Wring-
ing some of the moisture out of the air entering the
vehicle adds to the comfort of the passengers.
Although, an owner may expect too much from their
air conditioning system on humid days. A perfor-
mance test is the best way to determine whether the
system is performing up to standard. This test also
provides valuable clues as to the possible cause of
trouble with the air conditioning system.
If the vehicle has the optional Automatic Zone Control
(AZC) system, and has intermittent operational prob-
lems or fault codes, be certain that the wire harness
connectors on the HVAC housing are properly seated
(Fig. 2). To check this condition, unplug the two wire
harness connector halves, then plug them in again.
Before performing the following procedure, (Refer
to 24 - HEATING & AIR CONDITIONING/PLUMB-
ING - CAUTION) (Refer to 24 - HEATING & AIR
CONDITIONING/PLUMBING - WARNING). The air
temperature in the test room and in the vehicle must
be a minimum of 21É C (70É F) for this test.
(1)
Connect a tachometer and a manifold gauge set.
(2) If the vehicle has the standard manual temper-
ature control, set the A/C Heater mode control switch
knob in the Panel position, the temperature control
knob in the full cool (Fresh Air Mode) position, the
A/C button in the On position, and the blower motor
switch knob in the highest speed position. If the vehi-
cle has the optional AZC, set the A/C Heater mode
control switch knob in the Panel position, the tem-
perature control knob in the full cool position, the
A/C button in the On position, and the blower motor
switch knob in the highest (manual) speed position.
(3) Start the engine and hold the idle at 1,300 rpm
with the compressor clutch engaged.
(4) The engine should be at operating temperature.
The doors and windows must be open.
(5)
Insert a thermometer in the driver side center
A/C (panel) outlet. Operate the engine for five minutes.
(6) The compressor clutch may cycle, depending
upon the ambient temperature and humidity.(7) With the compressor clutch engaged, record the
discharge air temperature and the compressor dis-
charge pressure.
(8) Compare the discharge air temperature to the
Performance Temperature and Pressure chart. If the
discharge air temperature is high, (Refer to 24 -
HEATING & AIR CONDITIONING/PLUMBING -
DIAGNOSIS AND TESTING - REFRIGERANT SYS-
TEM LEAKS) and (Refer to 24 - HEATING & AIR
CONDITIONING/PLUMBING - STANDARD PRO-
CEDURE - REFRIGERANT SYSTEM CHARGE).
Performance Temperature and Pressure
Ambient Air Temperature
and Humidity21É C
(70É F @ 80%
humidity)27É C
(80É F @ 80%
humidity)32É C
(90É F @ 80%
humidity)38É C
(100ÉF@50%
humidity)43É C
110É F @ 20%
humidity)
Air Temperature at Center
Panel Outlet10 to 13É C
(50 to 55É F)14 to 17É C
(58 to 63É F)15 to 18É C
(60 to 65É F)17 to 20É C
(63 to 68É F)14 to 17É C
(58 to 63É F)
Evaporator Inlet Pressure
at Charge Port241 to 276 kPa
(35 to 40 psi)262 to 290 kPa
(38 to 42 psi)269 to 296 kPa
(39 to 43 psi)275 to 303 kPa
(40 to 44 psi)262 to 290 kPa
(38 to 42 psi)
Compressor Discharge
Pressure1241 to 1792
kPa
(180 to 260 psi)1380 to 1930
kPa
(200 to 280 psi)1380 to 1930
kPa
(200 to 280 psi)1655 to 2206
kPa
(240 to 320 psi)1567 to 2068
kPa
(220 to 300 psi)
Note: The discharge air temperatures will be lower if the humidity is less than the percentages shown.
Fig. 2 HVAC Housing - (rear view)
1 - Instrument Panel
2 - Air Intake
3 - Expansion Valve
4 - HVAC Housing
5 - Heater Core Input/Output Ports
6 - Instrument Panel Wiring Harness
7 - Blower Motor
WJHEATING & AIR CONDITIONING 24 - 3
HEATING & AIR CONDITIONING (Continued)
Page 2106 of 2199
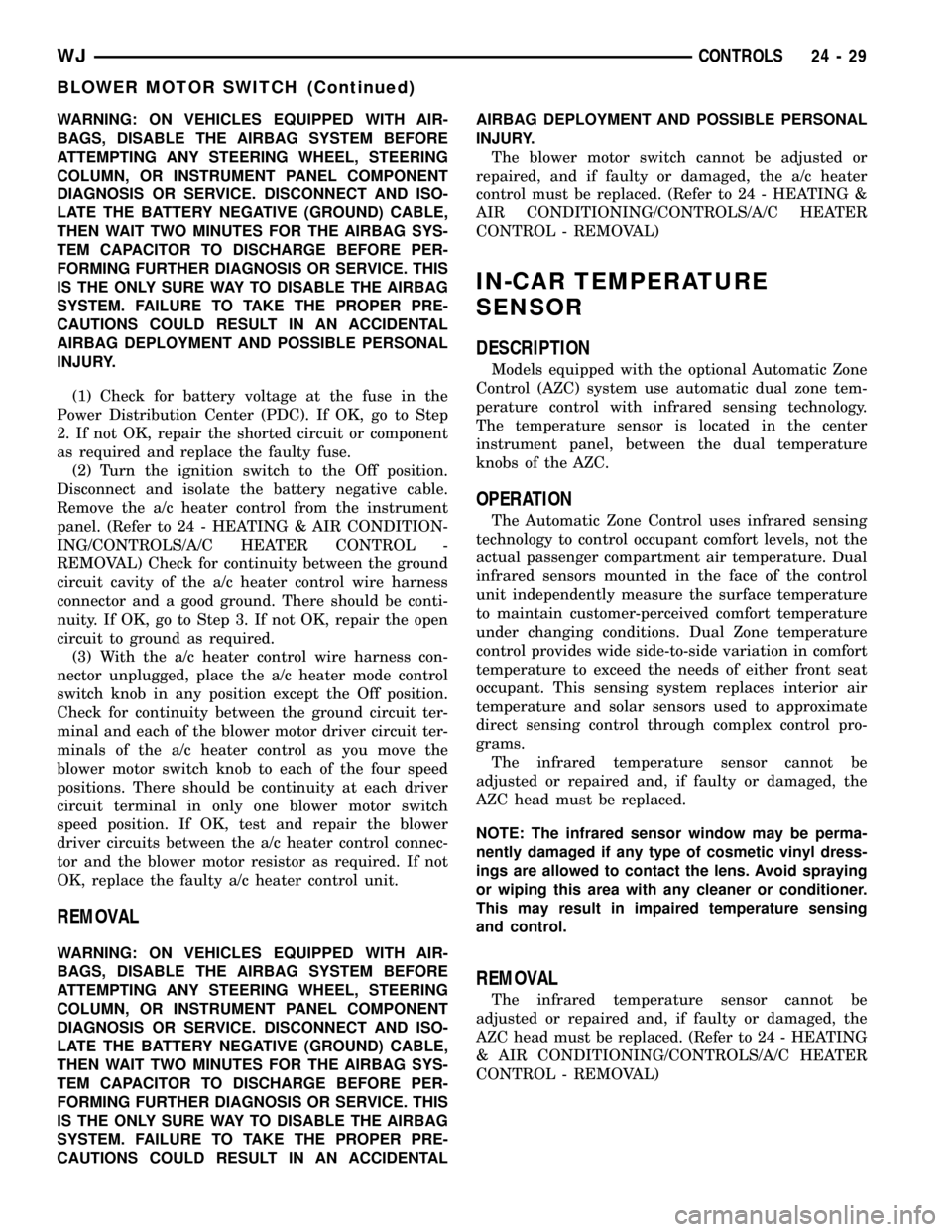
WARNING: ON VEHICLES EQUIPPED WITH AIR-
BAGS, DISABLE THE AIRBAG SYSTEM BEFORE
ATTEMPTING ANY STEERING WHEEL, STEERING
COLUMN, OR INSTRUMENT PANEL COMPONENT
DIAGNOSIS OR SERVICE. DISCONNECT AND ISO-
LATE THE BATTERY NEGATIVE (GROUND) CABLE,
THEN WAIT TWO MINUTES FOR THE AIRBAG SYS-
TEM CAPACITOR TO DISCHARGE BEFORE PER-
FORMING FURTHER DIAGNOSIS OR SERVICE. THIS
IS THE ONLY SURE WAY TO DISABLE THE AIRBAG
SYSTEM. FAILURE TO TAKE THE PROPER PRE-
CAUTIONS COULD RESULT IN AN ACCIDENTAL
AIRBAG DEPLOYMENT AND POSSIBLE PERSONAL
INJURY.
(1) Check for battery voltage at the fuse in the
Power Distribution Center (PDC). If OK, go to Step
2. If not OK, repair the shorted circuit or component
as required and replace the faulty fuse.
(2) Turn the ignition switch to the Off position.
Disconnect and isolate the battery negative cable.
Remove the a/c heater control from the instrument
panel. (Refer to 24 - HEATING & AIR CONDITION-
ING/CONTROLS/A/C HEATER CONTROL -
REMOVAL) Check for continuity between the ground
circuit cavity of the a/c heater control wire harness
connector and a good ground. There should be conti-
nuity. If OK, go to Step 3. If not OK, repair the open
circuit to ground as required.
(3) With the a/c heater control wire harness con-
nector unplugged, place the a/c heater mode control
switch knob in any position except the Off position.
Check for continuity between the ground circuit ter-
minal and each of the blower motor driver circuit ter-
minals of the a/c heater control as you move the
blower motor switch knob to each of the four speed
positions. There should be continuity at each driver
circuit terminal in only one blower motor switch
speed position. If OK, test and repair the blower
driver circuits between the a/c heater control connec-
tor and the blower motor resistor as required. If not
OK, replace the faulty a/c heater control unit.
REMOVAL
WARNING: ON VEHICLES EQUIPPED WITH AIR-
BAGS, DISABLE THE AIRBAG SYSTEM BEFORE
ATTEMPTING ANY STEERING WHEEL, STEERING
COLUMN, OR INSTRUMENT PANEL COMPONENT
DIAGNOSIS OR SERVICE. DISCONNECT AND ISO-
LATE THE BATTERY NEGATIVE (GROUND) CABLE,
THEN WAIT TWO MINUTES FOR THE AIRBAG SYS-
TEM CAPACITOR TO DISCHARGE BEFORE PER-
FORMING FURTHER DIAGNOSIS OR SERVICE. THIS
IS THE ONLY SURE WAY TO DISABLE THE AIRBAG
SYSTEM. FAILURE TO TAKE THE PROPER PRE-
CAUTIONS COULD RESULT IN AN ACCIDENTALAIRBAG DEPLOYMENT AND POSSIBLE PERSONAL
INJURY.
The blower motor switch cannot be adjusted or
repaired, and if faulty or damaged, the a/c heater
control must be replaced. (Refer to 24 - HEATING &
AIR CONDITIONING/CONTROLS/A/C HEATER
CONTROL - REMOVAL)
IN-CAR TEMPERATURE
SENSOR
DESCRIPTION
Models equipped with the optional Automatic Zone
Control (AZC) system use automatic dual zone tem-
perature control with infrared sensing technology.
The temperature sensor is located in the center
instrument panel, between the dual temperature
knobs of the AZC.
OPERATION
The Automatic Zone Control uses infrared sensing
technology to control occupant comfort levels, not the
actual passenger compartment air temperature. Dual
infrared sensors mounted in the face of the control
unit independently measure the surface temperature
to maintain customer-perceived comfort temperature
under changing conditions. Dual Zone temperature
control provides wide side-to-side variation in comfort
temperature to exceed the needs of either front seat
occupant. This sensing system replaces interior air
temperature and solar sensors used to approximate
direct sensing control through complex control pro-
grams.
The infrared temperature sensor cannot be
adjusted or repaired and, if faulty or damaged, the
AZC head must be replaced.
NOTE: The infrared sensor window may be perma-
nently damaged if any type of cosmetic vinyl dress-
ings are allowed to contact the lens. Avoid spraying
or wiping this area with any cleaner or conditioner.
This may result in impaired temperature sensing
and control.
REMOVAL
The infrared temperature sensor cannot be
adjusted or repaired and, if faulty or damaged, the
AZC head must be replaced. (Refer to 24 - HEATING
& AIR CONDITIONING/CONTROLS/A/C HEATER
CONTROL - REMOVAL)
WJCONTROLS 24 - 29
BLOWER MOTOR SWITCH (Continued)
Page 2135 of 2199
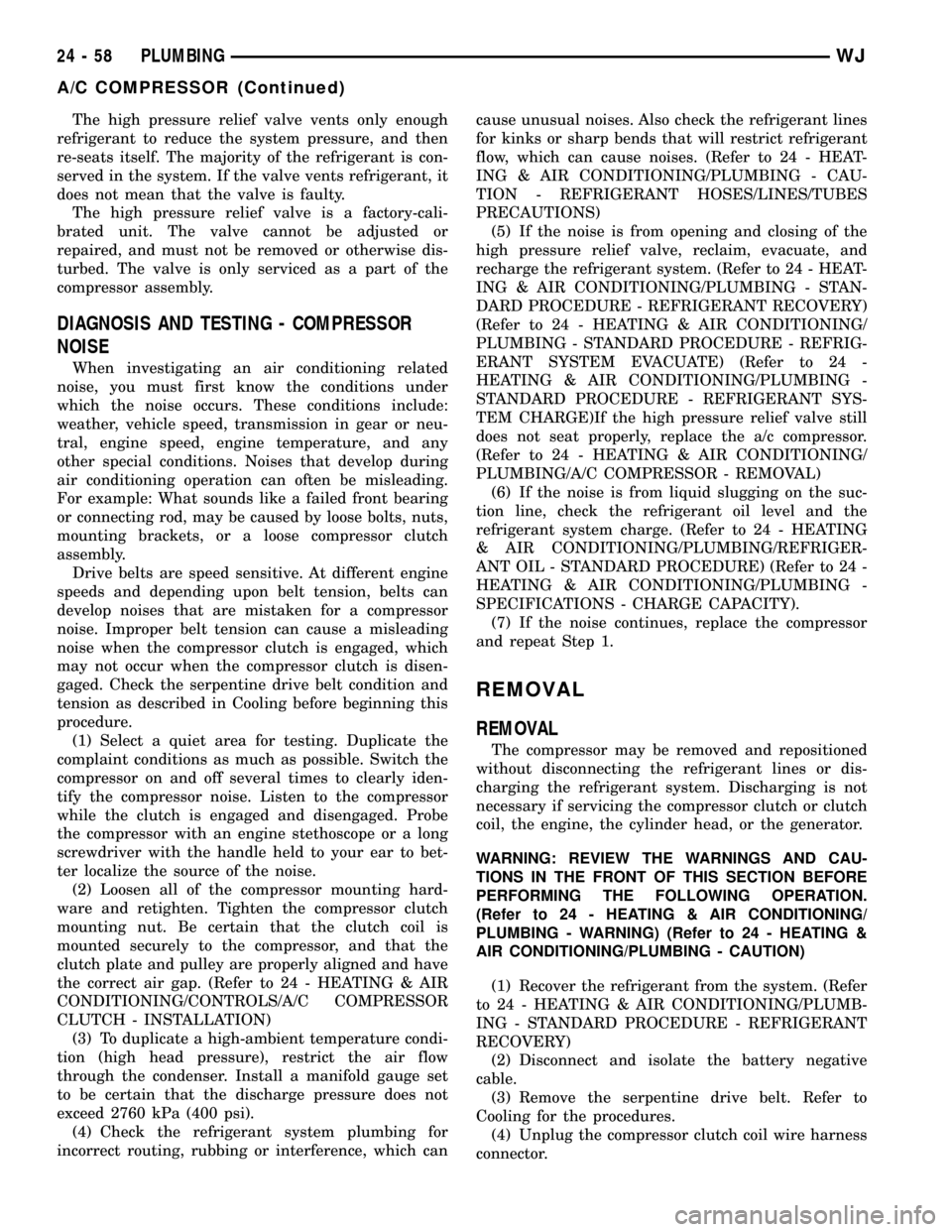
The high pressure relief valve vents only enough
refrigerant to reduce the system pressure, and then
re-seats itself. The majority of the refrigerant is con-
served in the system. If the valve vents refrigerant, it
does not mean that the valve is faulty.
The high pressure relief valve is a factory-cali-
brated unit. The valve cannot be adjusted or
repaired, and must not be removed or otherwise dis-
turbed. The valve is only serviced as a part of the
compressor assembly.
DIAGNOSIS AND TESTING - COMPRESSOR
NOISE
When investigating an air conditioning related
noise, you must first know the conditions under
which the noise occurs. These conditions include:
weather, vehicle speed, transmission in gear or neu-
tral, engine speed, engine temperature, and any
other special conditions. Noises that develop during
air conditioning operation can often be misleading.
For example: What sounds like a failed front bearing
or connecting rod, may be caused by loose bolts, nuts,
mounting brackets, or a loose compressor clutch
assembly.
Drive belts are speed sensitive. At different engine
speeds and depending upon belt tension, belts can
develop noises that are mistaken for a compressor
noise. Improper belt tension can cause a misleading
noise when the compressor clutch is engaged, which
may not occur when the compressor clutch is disen-
gaged. Check the serpentine drive belt condition and
tension as described in Cooling before beginning this
procedure.
(1) Select a quiet area for testing. Duplicate the
complaint conditions as much as possible. Switch the
compressor on and off several times to clearly iden-
tify the compressor noise. Listen to the compressor
while the clutch is engaged and disengaged. Probe
the compressor with an engine stethoscope or a long
screwdriver with the handle held to your ear to bet-
ter localize the source of the noise.
(2) Loosen all of the compressor mounting hard-
ware and retighten. Tighten the compressor clutch
mounting nut. Be certain that the clutch coil is
mounted securely to the compressor, and that the
clutch plate and pulley are properly aligned and have
the correct air gap. (Refer to 24 - HEATING & AIR
CONDITIONING/CONTROLS/A/C COMPRESSOR
CLUTCH - INSTALLATION)
(3) To duplicate a high-ambient temperature condi-
tion (high head pressure), restrict the air flow
through the condenser. Install a manifold gauge set
to be certain that the discharge pressure does not
exceed 2760 kPa (400 psi).
(4) Check the refrigerant system plumbing for
incorrect routing, rubbing or interference, which cancause unusual noises. Also check the refrigerant lines
for kinks or sharp bends that will restrict refrigerant
flow, which can cause noises. (Refer to 24 - HEAT-
ING & AIR CONDITIONING/PLUMBING - CAU-
TION - REFRIGERANT HOSES/LINES/TUBES
PRECAUTIONS)
(5) If the noise is from opening and closing of the
high pressure relief valve, reclaim, evacuate, and
recharge the refrigerant system. (Refer to 24 - HEAT-
ING & AIR CONDITIONING/PLUMBING - STAN-
DARD PROCEDURE - REFRIGERANT RECOVERY)
(Refer to 24 - HEATING & AIR CONDITIONING/
PLUMBING - STANDARD PROCEDURE - REFRIG-
ERANT SYSTEM EVACUATE) (Refer to 24 -
HEATING & AIR CONDITIONING/PLUMBING -
STANDARD PROCEDURE - REFRIGERANT SYS-
TEM CHARGE)If the high pressure relief valve still
does not seat properly, replace the a/c compressor.
(Refer to 24 - HEATING & AIR CONDITIONING/
PLUMBING/A/C COMPRESSOR - REMOVAL)
(6) If the noise is from liquid slugging on the suc-
tion line, check the refrigerant oil level and the
refrigerant system charge. (Refer to 24 - HEATING
& AIR CONDITIONING/PLUMBING/REFRIGER-
ANT OIL - STANDARD PROCEDURE) (Refer to 24 -
HEATING & AIR CONDITIONING/PLUMBING -
SPECIFICATIONS - CHARGE CAPACITY).
(7) If the noise continues, replace the compressor
and repeat Step 1.
REMOVAL
REMOVAL
The compressor may be removed and repositioned
without disconnecting the refrigerant lines or dis-
charging the refrigerant system. Discharging is not
necessary if servicing the compressor clutch or clutch
coil, the engine, the cylinder head, or the generator.
WARNING: REVIEW THE WARNINGS AND CAU-
TIONS IN THE FRONT OF THIS SECTION BEFORE
PERFORMING THE FOLLOWING OPERATION.
(Refer to 24 - HEATING & AIR CONDITIONING/
PLUMBING - WARNING) (Refer to 24 - HEATING &
AIR CONDITIONING/PLUMBING - CAUTION)
(1) Recover the refrigerant from the system. (Refer
to 24 - HEATING & AIR CONDITIONING/PLUMB-
ING - STANDARD PROCEDURE - REFRIGERANT
RECOVERY)
(2) Disconnect and isolate the battery negative
cable.
(3) Remove the serpentine drive belt. Refer to
Cooling for the procedures.
(4) Unplug the compressor clutch coil wire harness
connector.
24 - 58 PLUMBINGWJ
A/C COMPRESSOR (Continued)