sensor JEEP GRAND CHEROKEE 2003 WJ / 2.G Workshop Manual
[x] Cancel search | Manufacturer: JEEP, Model Year: 2003, Model line: GRAND CHEROKEE, Model: JEEP GRAND CHEROKEE 2003 WJ / 2.GPages: 2199, PDF Size: 76.01 MB
Page 1826 of 2199
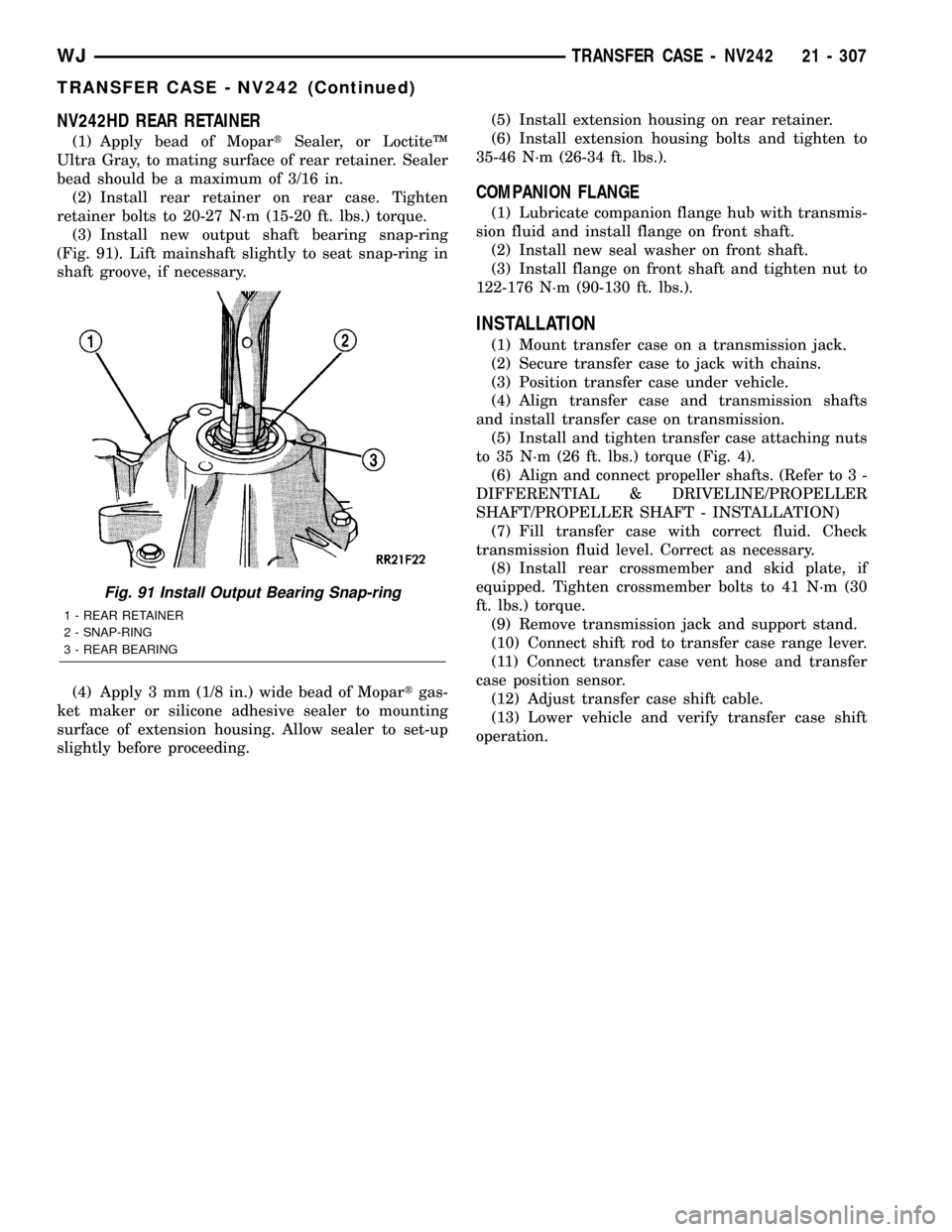
NV242HD REAR RETAINER
(1) Apply bead of MopartSealer, or LoctiteŸ
Ultra Gray, to mating surface of rear retainer. Sealer
bead should be a maximum of 3/16 in.
(2) Install rear retainer on rear case. Tighten
retainer bolts to 20-27 N´m (15-20 ft. lbs.) torque.
(3) Install new output shaft bearing snap-ring
(Fig. 91). Lift mainshaft slightly to seat snap-ring in
shaft groove, if necessary.
(4) Apply 3 mm (1/8 in.) wide bead of Mopartgas-
ket maker or silicone adhesive sealer to mounting
surface of extension housing. Allow sealer to set-up
slightly before proceeding.(5) Install extension housing on rear retainer.
(6) Install extension housing bolts and tighten to
35-46 N´m (26-34 ft. lbs.).
COMPANION FLANGE
(1) Lubricate companion flange hub with transmis-
sion fluid and install flange on front shaft.
(2) Install new seal washer on front shaft.
(3) Install flange on front shaft and tighten nut to
122-176 N´m (90-130 ft. lbs.).
INSTALLATION
(1) Mount transfer case on a transmission jack.
(2) Secure transfer case to jack with chains.
(3) Position transfer case under vehicle.
(4) Align transfer case and transmission shafts
and install transfer case on transmission.
(5) Install and tighten transfer case attaching nuts
to 35 N´m (26 ft. lbs.) torque (Fig. 4).
(6) Align and connect propeller shafts. (Refer to 3 -
DIFFERENTIAL & DRIVELINE/PROPELLER
SHAFT/PROPELLER SHAFT - INSTALLATION)
(7) Fill transfer case with correct fluid. Check
transmission fluid level. Correct as necessary.
(8) Install rear crossmember and skid plate, if
equipped. Tighten crossmember bolts to 41 N´m (30
ft. lbs.) torque.
(9) Remove transmission jack and support stand.
(10) Connect shift rod to transfer case range lever.
(11) Connect transfer case vent hose and transfer
case position sensor.
(12) Adjust transfer case shift cable.
(13) Lower vehicle and verify transfer case shift
operation.
Fig. 91 Install Output Bearing Snap-ring
1 - REAR RETAINER
2 - SNAP-RING
3 - REAR BEARING
WJTRANSFER CASE - NV242 21 - 307
TRANSFER CASE - NV242 (Continued)
Page 1830 of 2199
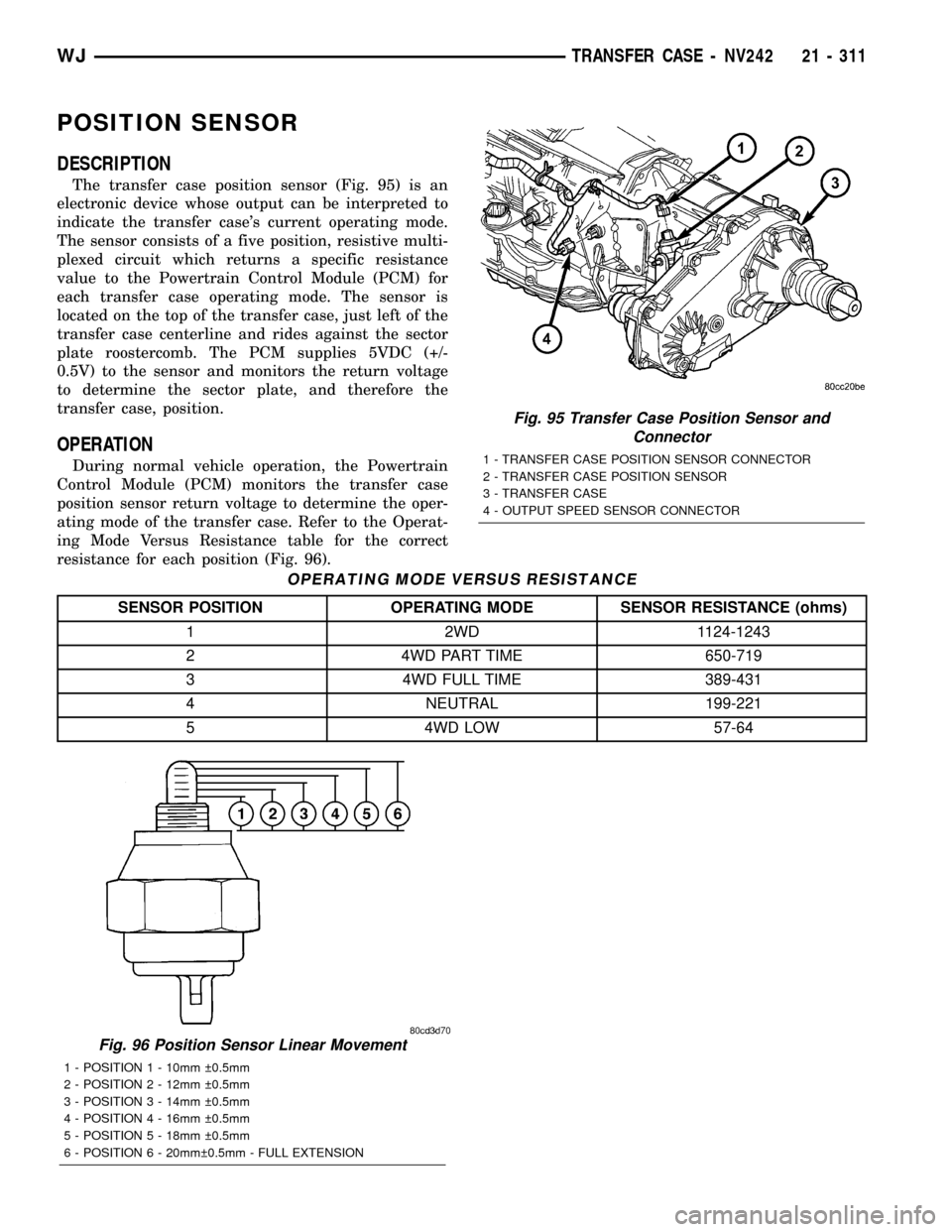
POSITION SENSOR
DESCRIPTION
The transfer case position sensor (Fig. 95) is an
electronic device whose output can be interpreted to
indicate the transfer case's current operating mode.
The sensor consists of a five position, resistive multi-
plexed circuit which returns a specific resistance
value to the Powertrain Control Module (PCM) for
each transfer case operating mode. The sensor is
located on the top of the transfer case, just left of the
transfer case centerline and rides against the sector
plate roostercomb. The PCM supplies 5VDC (+/-
0.5V) to the sensor and monitors the return voltage
to determine the sector plate, and therefore the
transfer case, position.
OPERATION
During normal vehicle operation, the Powertrain
Control Module (PCM) monitors the transfer case
position sensor return voltage to determine the oper-
ating mode of the transfer case. Refer to the Operat-
ing Mode Versus Resistance table for the correct
resistance for each position (Fig. 96).
OPERATING MODE VERSUS RESISTANCE
SENSOR POSITION OPERATING MODE SENSOR RESISTANCE (ohms)
1 2WD 1124-1243
2 4WD PART TIME 650-719
3 4WD FULL TIME 389-431
4 NEUTRAL 199-221
5 4WD LOW 57-64
Fig. 96 Position Sensor Linear Movement
1 - POSITION 1 - 10mm 0.5mm
2 - POSITION 2 - 12mm 0.5mm
3 - POSITION 3 - 14mm 0.5mm
4 - POSITION 4 - 16mm 0.5mm
5 - POSITION 5 - 18mm 0.5mm
6 - POSITION 6 - 20mm 0.5mm - FULL EXTENSION
Fig. 95 Transfer Case Position Sensor and
Connector
1 - TRANSFER CASE POSITION SENSOR CONNECTOR
2 - TRANSFER CASE POSITION SENSOR
3 - TRANSFER CASE
4 - OUTPUT SPEED SENSOR CONNECTOR
WJTRANSFER CASE - NV242 21 - 311
Page 1831 of 2199
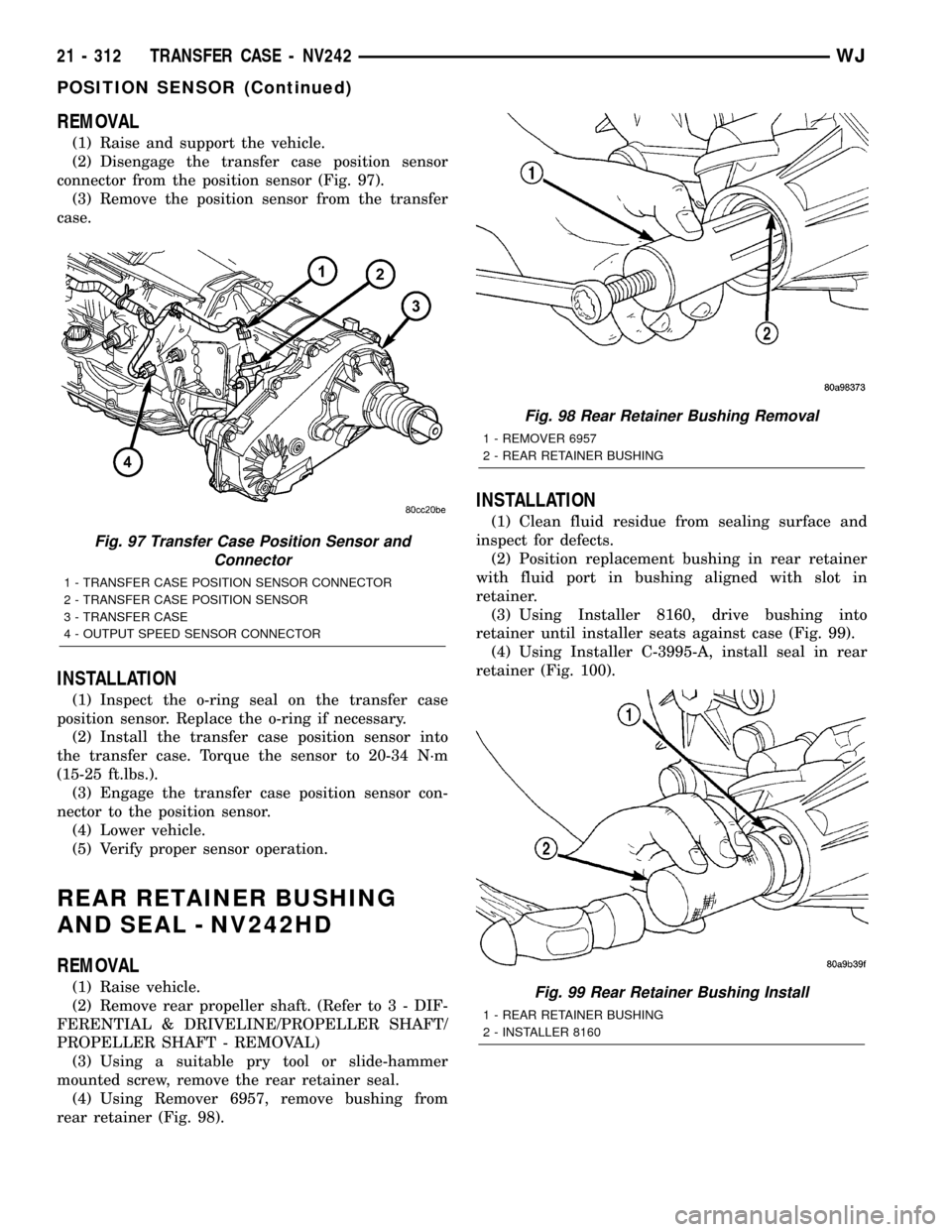
REMOVAL
(1) Raise and support the vehicle.
(2) Disengage the transfer case position sensor
connector from the position sensor (Fig. 97).
(3) Remove the position sensor from the transfer
case.
INSTALLATION
(1) Inspect the o-ring seal on the transfer case
position sensor. Replace the o-ring if necessary.
(2) Install the transfer case position sensor into
the transfer case. Torque the sensor to 20-34 N´m
(15-25 ft.lbs.).
(3) Engage the transfer case position sensor con-
nector to the position sensor.
(4) Lower vehicle.
(5) Verify proper sensor operation.
REAR RETAINER BUSHING
AND SEAL - NV242HD
REMOVAL
(1) Raise vehicle.
(2) Remove rear propeller shaft. (Refer to 3 - DIF-
FERENTIAL & DRIVELINE/PROPELLER SHAFT/
PROPELLER SHAFT - REMOVAL)
(3) Using a suitable pry tool or slide-hammer
mounted screw, remove the rear retainer seal.
(4) Using Remover 6957, remove bushing from
rear retainer (Fig. 98).
INSTALLATION
(1) Clean fluid residue from sealing surface and
inspect for defects.
(2) Position replacement bushing in rear retainer
with fluid port in bushing aligned with slot in
retainer.
(3) Using Installer 8160, drive bushing into
retainer until installer seats against case (Fig. 99).
(4) Using Installer C-3995-A, install seal in rear
retainer (Fig. 100).
Fig. 97 Transfer Case Position Sensor and
Connector
1 - TRANSFER CASE POSITION SENSOR CONNECTOR
2 - TRANSFER CASE POSITION SENSOR
3 - TRANSFER CASE
4 - OUTPUT SPEED SENSOR CONNECTOR
Fig. 98 Rear Retainer Bushing Removal
1 - REMOVER 6957
2 - REAR RETAINER BUSHING
Fig. 99 Rear Retainer Bushing Install
1 - REAR RETAINER BUSHING
2 - INSTALLER 8160
21 - 312 TRANSFER CASE - NV242WJ
POSITION SENSOR (Continued)
Page 1860 of 2199
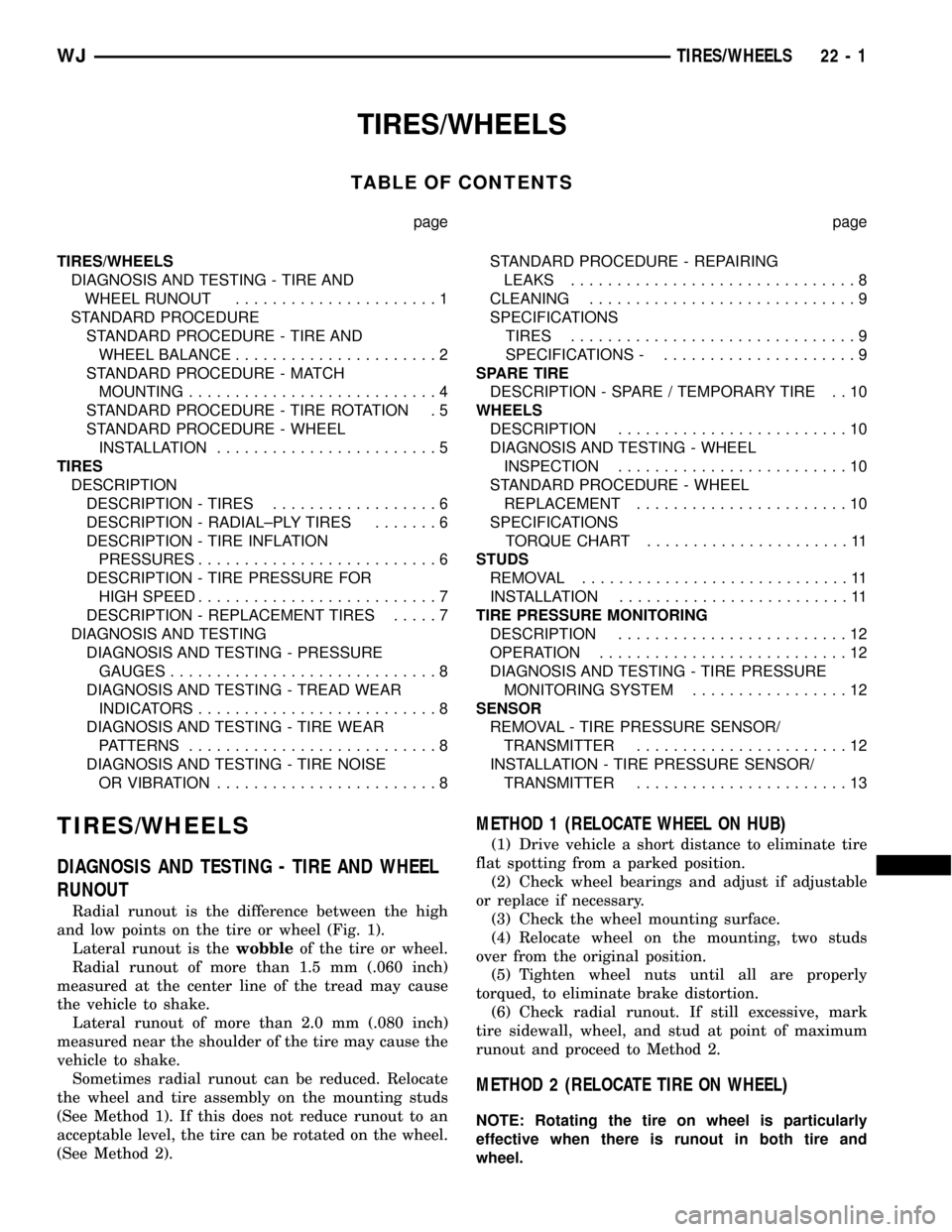
TIRES/WHEELS
TABLE OF CONTENTS
page page
TIRES/WHEELS
DIAGNOSIS AND TESTING - TIRE AND
WHEEL RUNOUT......................1
STANDARD PROCEDURE
STANDARD PROCEDURE - TIRE AND
WHEEL BALANCE......................2
STANDARD PROCEDURE - MATCH
MOUNTING...........................4
STANDARD PROCEDURE - TIRE ROTATION . 5
STANDARD PROCEDURE - WHEEL
INSTALLATION........................5
TIRES
DESCRIPTION
DESCRIPTION - TIRES..................6
DESCRIPTION - RADIAL±PLY TIRES.......6
DESCRIPTION - TIRE INFLATION
PRESSURES..........................6
DESCRIPTION - TIRE PRESSURE FOR
HIGH SPEED..........................7
DESCRIPTION - REPLACEMENT TIRES.....7
DIAGNOSIS AND TESTING
DIAGNOSIS AND TESTING - PRESSURE
GAUGES.............................8
DIAGNOSIS AND TESTING - TREAD WEAR
INDICATORS..........................8
DIAGNOSIS AND TESTING - TIRE WEAR
PATTERNS...........................8
DIAGNOSIS AND TESTING - TIRE NOISE
OR VIBRATION........................8STANDARD PROCEDURE - REPAIRING
LEAKS...............................8
CLEANING.............................9
SPECIFICATIONS
TIRES...............................9
SPECIFICATIONS -.....................9
SPARE TIRE
DESCRIPTION - SPARE / TEMPORARY TIRE . . 10
WHEELS
DESCRIPTION.........................10
DIAGNOSIS AND TESTING - WHEEL
INSPECTION.........................10
STANDARD PROCEDURE - WHEEL
REPLACEMENT.......................10
SPECIFICATIONS
TORQUE CHART......................11
STUDS
REMOVAL.............................11
INSTALLATION.........................11
TIRE PRESSURE MONITORING
DESCRIPTION.........................12
OPERATION...........................12
DIAGNOSIS AND TESTING - TIRE PRESSURE
MONITORING SYSTEM.................12
SENSOR
REMOVAL - TIRE PRESSURE SENSOR/
TRANSMITTER.......................12
INSTALLATION - TIRE PRESSURE SENSOR/
TRANSMITTER.......................13
TIRES/WHEELS
DIAGNOSIS AND TESTING - TIRE AND WHEEL
RUNOUT
Radial runout is the difference between the high
and low points on the tire or wheel (Fig. 1).
Lateral runout is thewobbleof the tire or wheel.
Radial runout of more than 1.5 mm (.060 inch)
measured at the center line of the tread may cause
the vehicle to shake.
Lateral runout of more than 2.0 mm (.080 inch)
measured near the shoulder of the tire may cause the
vehicle to shake.
Sometimes radial runout can be reduced. Relocate
the wheel and tire assembly on the mounting studs
(See Method 1). If this does not reduce runout to an
acceptable level, the tire can be rotated on the wheel.
(See Method 2).
METHOD 1 (RELOCATE WHEEL ON HUB)
(1) Drive vehicle a short distance to eliminate tire
flat spotting from a parked position.
(2) Check wheel bearings and adjust if adjustable
or replace if necessary.
(3) Check the wheel mounting surface.
(4) Relocate wheel on the mounting, two studs
over from the original position.
(5) Tighten wheel nuts until all are properly
torqued, to eliminate brake distortion.
(6) Check radial runout. If still excessive, mark
tire sidewall, wheel, and stud at point of maximum
runout and proceed to Method 2.
METHOD 2 (RELOCATE TIRE ON WHEEL)
NOTE: Rotating the tire on wheel is particularly
effective when there is runout in both tire and
wheel.
WJTIRES/WHEELS 22 - 1
Page 1871 of 2199
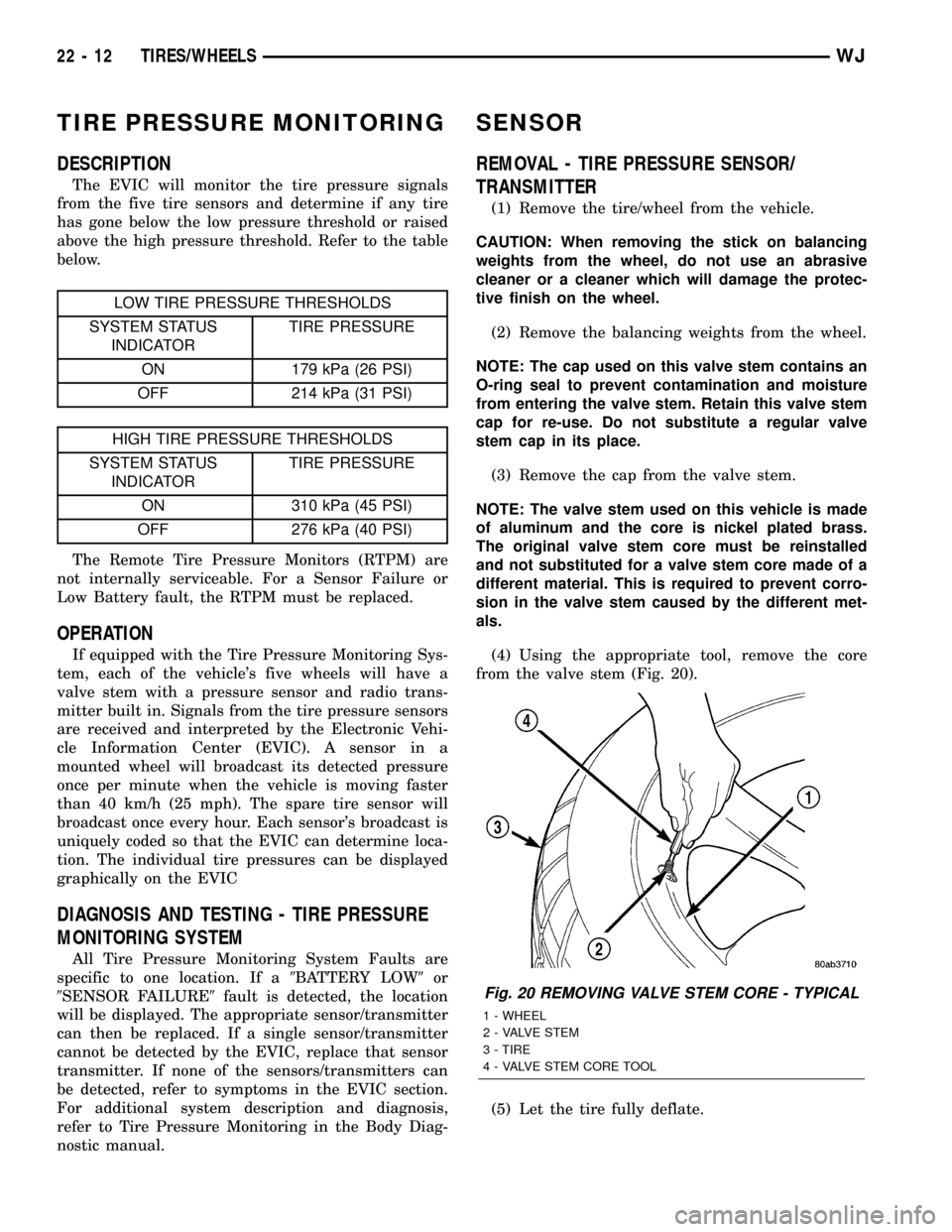
TIRE PRESSURE MONITORING
DESCRIPTION
The EVIC will monitor the tire pressure signals
from the five tire sensors and determine if any tire
has gone below the low pressure threshold or raised
above the high pressure threshold. Refer to the table
below.
LOW TIRE PRESSURE THRESHOLDS
SYSTEM STATUS
INDICATORTIRE PRESSURE
ON 179 kPa (26 PSI)
OFF 214 kPa (31 PSI)
HIGH TIRE PRESSURE THRESHOLDS
SYSTEM STATUS
INDICATORTIRE PRESSURE
ON 310 kPa (45 PSI)
OFF 276 kPa (40 PSI)
The Remote Tire Pressure Monitors (RTPM) are
not internally serviceable. For a Sensor Failure or
Low Battery fault, the RTPM must be replaced.
OPERATION
If equipped with the Tire Pressure Monitoring Sys-
tem, each of the vehicle's five wheels will have a
valve stem with a pressure sensor and radio trans-
mitter built in. Signals from the tire pressure sensors
are received and interpreted by the Electronic Vehi-
cle Information Center (EVIC). A sensor in a
mounted wheel will broadcast its detected pressure
once per minute when the vehicle is moving faster
than 40 km/h (25 mph). The spare tire sensor will
broadcast once every hour. Each sensor's broadcast is
uniquely coded so that the EVIC can determine loca-
tion. The individual tire pressures can be displayed
graphically on the EVIC
DIAGNOSIS AND TESTING - TIRE PRESSURE
MONITORING SYSTEM
All Tire Pressure Monitoring System Faults are
specific to one location. If a9BATTERY LOW9or
9SENSOR FAILURE9fault is detected, the location
will be displayed. The appropriate sensor/transmitter
can then be replaced. If a single sensor/transmitter
cannot be detected by the EVIC, replace that sensor
transmitter. If none of the sensors/transmitters can
be detected, refer to symptoms in the EVIC section.
For additional system description and diagnosis,
refer to Tire Pressure Monitoring in the Body Diag-
nostic manual.
SENSOR
REMOVAL - TIRE PRESSURE SENSOR/
TRANSMITTER
(1) Remove the tire/wheel from the vehicle.
CAUTION: When removing the stick on balancing
weights from the wheel, do not use an abrasive
cleaner or a cleaner which will damage the protec-
tive finish on the wheel.
(2) Remove the balancing weights from the wheel.
NOTE: The cap used on this valve stem contains an
O-ring seal to prevent contamination and moisture
from entering the valve stem. Retain this valve stem
cap for re-use. Do not substitute a regular valve
stem cap in its place.
(3) Remove the cap from the valve stem.
NOTE: The valve stem used on this vehicle is made
of aluminum and the core is nickel plated brass.
The original valve stem core must be reinstalled
and not substituted for a valve stem core made of a
different material. This is required to prevent corro-
sion in the valve stem caused by the different met-
als.
(4) Using the appropriate tool, remove the core
from the valve stem (Fig. 20).
(5) Let the tire fully deflate.
Fig. 20 REMOVING VALVE STEM CORE - TYPICAL
1 - WHEEL
2 - VALVE STEM
3 - TIRE
4 - VALVE STEM CORE TOOL
22 - 12 TIRES/WHEELSWJ
Page 1872 of 2199
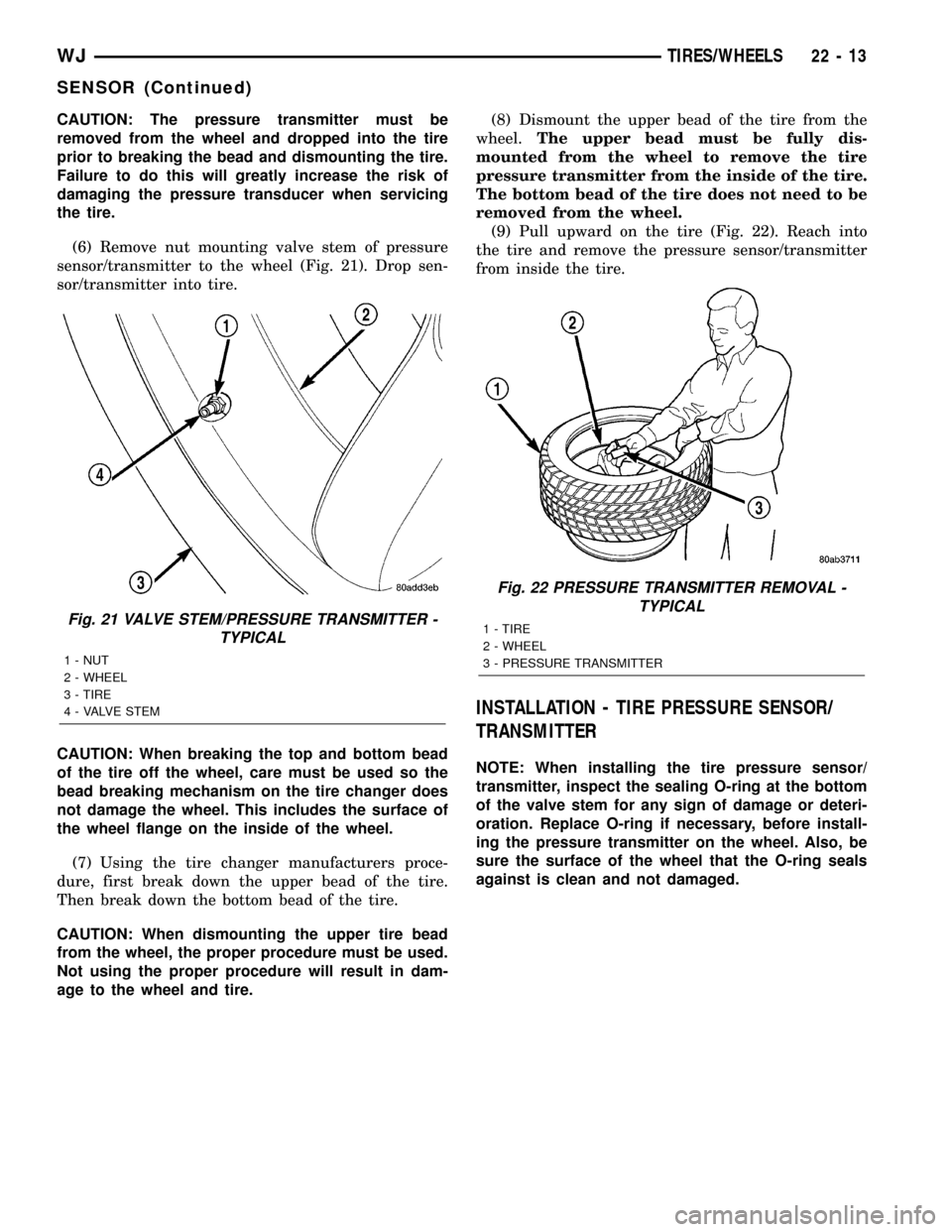
CAUTION: The pressure transmitter must be
removed from the wheel and dropped into the tire
prior to breaking the bead and dismounting the tire.
Failure to do this will greatly increase the risk of
damaging the pressure transducer when servicing
the tire.
(6) Remove nut mounting valve stem of pressure
sensor/transmitter to the wheel (Fig. 21). Drop sen-
sor/transmitter into tire.
CAUTION: When breaking the top and bottom bead
of the tire off the wheel, care must be used so the
bead breaking mechanism on the tire changer does
not damage the wheel. This includes the surface of
the wheel flange on the inside of the wheel.
(7) Using the tire changer manufacturers proce-
dure, first break down the upper bead of the tire.
Then break down the bottom bead of the tire.
CAUTION: When dismounting the upper tire bead
from the wheel, the proper procedure must be used.
Not using the proper procedure will result in dam-
age to the wheel and tire.(8) Dismount the upper bead of the tire from the
wheel.The upper bead must be fully dis-
mounted from the wheel to remove the tire
pressure transmitter from the inside of the tire.
The bottom bead of the tire does not need to be
removed from the wheel.
(9) Pull upward on the tire (Fig. 22). Reach into
the tire and remove the pressure sensor/transmitter
from inside the tire.
INSTALLATION - TIRE PRESSURE SENSOR/
TRANSMITTER
NOTE: When installing the tire pressure sensor/
transmitter, inspect the sealing O-ring at the bottom
of the valve stem for any sign of damage or deteri-
oration. Replace O-ring if necessary, before install-
ing the pressure transmitter on the wheel. Also, be
sure the surface of the wheel that the O-ring seals
against is clean and not damaged.
Fig. 21 VALVE STEM/PRESSURE TRANSMITTER -
TYPICAL
1 - NUT
2 - WHEEL
3 - TIRE
4 - VALVE STEM
Fig. 22 PRESSURE TRANSMITTER REMOVAL -
TYPICAL
1 - TIRE
2 - WHEEL
3 - PRESSURE TRANSMITTER
WJTIRES/WHEELS 22 - 13
SENSOR (Continued)
Page 1873 of 2199
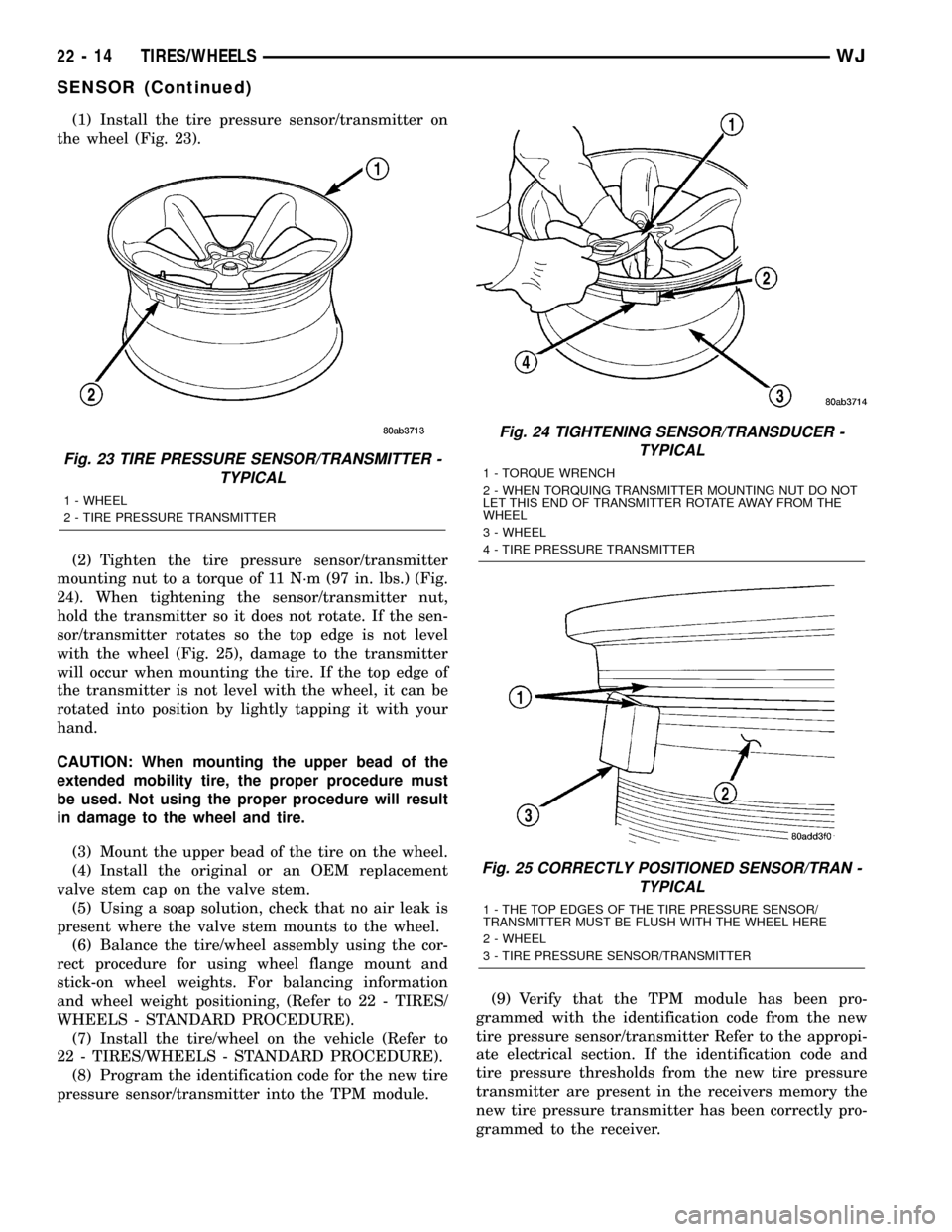
(1) Install the tire pressure sensor/transmitter on
the wheel (Fig. 23).
(2) Tighten the tire pressure sensor/transmitter
mounting nut to a torque of 11 N´m (97 in. lbs.) (Fig.
24). When tightening the sensor/transmitter nut,
hold the transmitter so it does not rotate. If the sen-
sor/transmitter rotates so the top edge is not level
with the wheel (Fig. 25), damage to the transmitter
will occur when mounting the tire. If the top edge of
the transmitter is not level with the wheel, it can be
rotated into position by lightly tapping it with your
hand.
CAUTION: When mounting the upper bead of the
extended mobility tire, the proper procedure must
be used. Not using the proper procedure will result
in damage to the wheel and tire.
(3) Mount the upper bead of the tire on the wheel.
(4) Install the original or an OEM replacement
valve stem cap on the valve stem.
(5) Using a soap solution, check that no air leak is
present where the valve stem mounts to the wheel.
(6) Balance the tire/wheel assembly using the cor-
rect procedure for using wheel flange mount and
stick-on wheel weights. For balancing information
and wheel weight positioning, (Refer to 22 - TIRES/
WHEELS - STANDARD PROCEDURE).
(7) Install the tire/wheel on the vehicle (Refer to
22 - TIRES/WHEELS - STANDARD PROCEDURE).
(8) Program the identification code for the new tire
pressure sensor/transmitter into the TPM module.(9) Verify that the TPM module has been pro-
grammed with the identification code from the new
tire pressure sensor/transmitter Refer to the appropi-
ate electrical section. If the identification code and
tire pressure thresholds from the new tire pressure
transmitter are present in the receivers memory the
new tire pressure transmitter has been correctly pro-
grammed to the receiver.
Fig. 23 TIRE PRESSURE SENSOR/TRANSMITTER -
TYPICAL
1 - WHEEL
2 - TIRE PRESSURE TRANSMITTER
Fig. 24 TIGHTENING SENSOR/TRANSDUCER -
TYPICAL
1 - TORQUE WRENCH
2 - WHEN TORQUING TRANSMITTER MOUNTING NUT DO NOT
LET THIS END OF TRANSMITTER ROTATE AWAY FROM THE
WHEEL
3 - WHEEL
4 - TIRE PRESSURE TRANSMITTER
Fig. 25 CORRECTLY POSITIONED SENSOR/TRAN -
TYPICAL
1 - THE TOP EDGES OF THE TIRE PRESSURE SENSOR/
TRANSMITTER MUST BE FLUSH WITH THE WHEEL HERE
2 - WHEEL
3 - TIRE PRESSURE SENSOR/TRANSMITTER
22 - 14 TIRES/WHEELSWJ
SENSOR (Continued)
Page 1924 of 2199
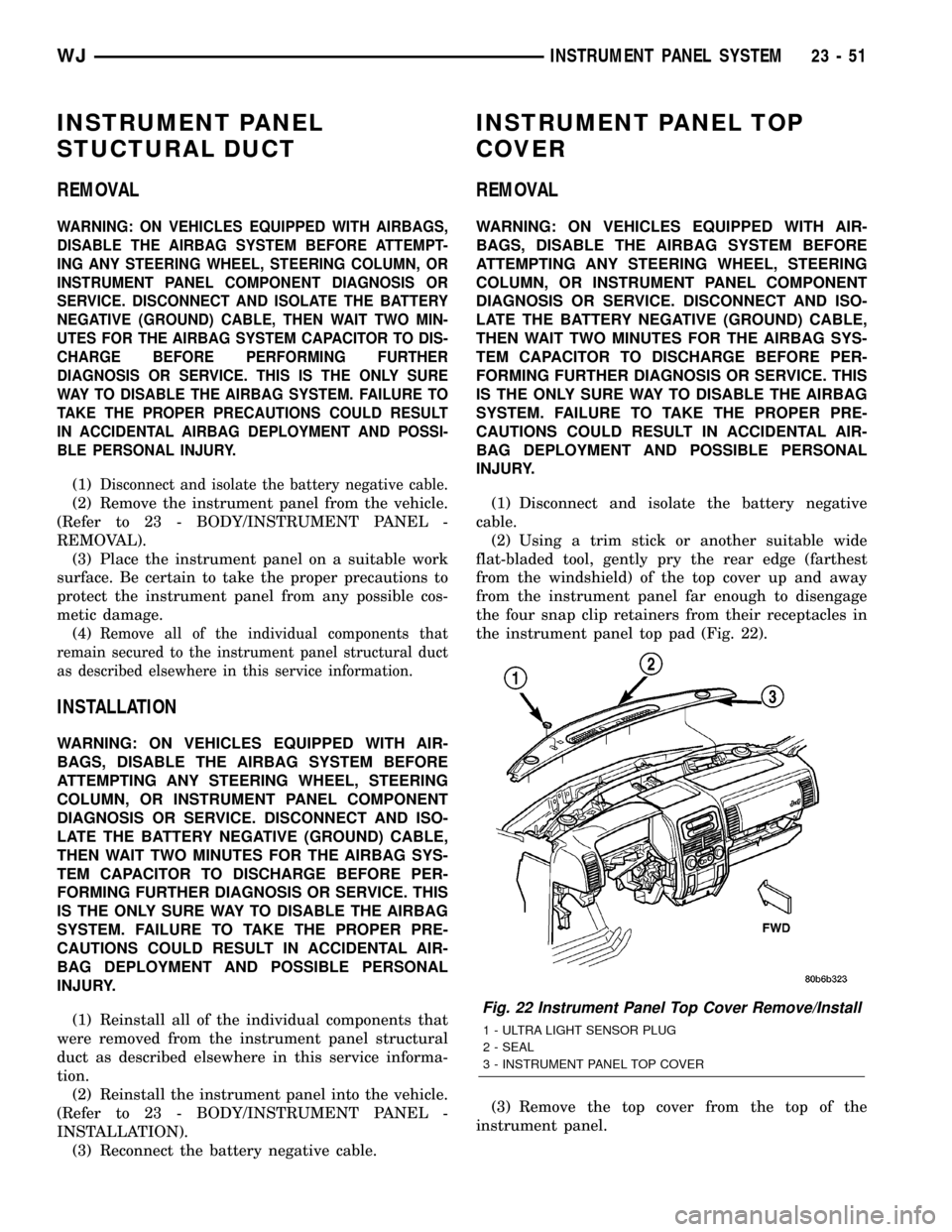
INSTRUMENT PANEL
STUCTURAL DUCT
REMOVAL
WARNING: ON VEHICLES EQUIPPED WITH AIRBAGS,
DISABLE THE AIRBAG SYSTEM BEFORE ATTEMPT-
ING ANY STEERING WHEEL, STEERING COLUMN, OR
INSTRUMENT PANEL COMPONENT DIAGNOSIS OR
SERVICE. DISCONNECT AND ISOLATE THE BATTERY
NEGATIVE (GROUND) CABLE, THEN WAIT TWO MIN-
UTES FOR THE AIRBAG SYSTEM CAPACITOR TO DIS-
CHARGE BEFORE PERFORMING FURTHER
DIAGNOSIS OR SERVICE. THIS IS THE ONLY SURE
WAY TO DISABLE THE AIRBAG SYSTEM. FAILURE TO
TAKE THE PROPER PRECAUTIONS COULD RESULT
IN ACCIDENTAL AIRBAG DEPLOYMENT AND POSSI-
BLE PERSONAL INJURY.
(1)Disconnect and isolate the battery negative cable.
(2) Remove the instrument panel from the vehicle.
(Refer to 23 - BODY/INSTRUMENT PANEL -
REMOVAL).
(3) Place the instrument panel on a suitable work
surface. Be certain to take the proper precautions to
protect the instrument panel from any possible cos-
metic damage.
(4)
Remove all of the individual components that
remain secured to the instrument panel structural duct
as described elsewhere in this service information.
INSTALLATION
WARNING: ON VEHICLES EQUIPPED WITH AIR-
BAGS, DISABLE THE AIRBAG SYSTEM BEFORE
ATTEMPTING ANY STEERING WHEEL, STEERING
COLUMN, OR INSTRUMENT PANEL COMPONENT
DIAGNOSIS OR SERVICE. DISCONNECT AND ISO-
LATE THE BATTERY NEGATIVE (GROUND) CABLE,
THEN WAIT TWO MINUTES FOR THE AIRBAG SYS-
TEM CAPACITOR TO DISCHARGE BEFORE PER-
FORMING FURTHER DIAGNOSIS OR SERVICE. THIS
IS THE ONLY SURE WAY TO DISABLE THE AIRBAG
SYSTEM. FAILURE TO TAKE THE PROPER PRE-
CAUTIONS COULD RESULT IN ACCIDENTAL AIR-
BAG DEPLOYMENT AND POSSIBLE PERSONAL
INJURY.
(1) Reinstall all of the individual components that
were removed from the instrument panel structural
duct as described elsewhere in this service informa-
tion.
(2) Reinstall the instrument panel into the vehicle.
(Refer to 23 - BODY/INSTRUMENT PANEL -
INSTALLATION).
(3) Reconnect the battery negative cable.
INSTRUMENT PANEL TOP
COVER
REMOVAL
WARNING: ON VEHICLES EQUIPPED WITH AIR-
BAGS, DISABLE THE AIRBAG SYSTEM BEFORE
ATTEMPTING ANY STEERING WHEEL, STEERING
COLUMN, OR INSTRUMENT PANEL COMPONENT
DIAGNOSIS OR SERVICE. DISCONNECT AND ISO-
LATE THE BATTERY NEGATIVE (GROUND) CABLE,
THEN WAIT TWO MINUTES FOR THE AIRBAG SYS-
TEM CAPACITOR TO DISCHARGE BEFORE PER-
FORMING FURTHER DIAGNOSIS OR SERVICE. THIS
IS THE ONLY SURE WAY TO DISABLE THE AIRBAG
SYSTEM. FAILURE TO TAKE THE PROPER PRE-
CAUTIONS COULD RESULT IN ACCIDENTAL AIR-
BAG DEPLOYMENT AND POSSIBLE PERSONAL
INJURY.
(1) Disconnect and isolate the battery negative
cable.
(2) Using a trim stick or another suitable wide
flat-bladed tool, gently pry the rear edge (farthest
from the windshield) of the top cover up and away
from the instrument panel far enough to disengage
the four snap clip retainers from their receptacles in
the instrument panel top pad (Fig. 22).
(3) Remove the top cover from the top of the
instrument panel.
Fig. 22 Instrument Panel Top Cover Remove/Install
1 - ULTRA LIGHT SENSOR PLUG
2 - SEAL
3 - INSTRUMENT PANEL TOP COVER
WJINSTRUMENT PANEL SYSTEM 23 - 51
Page 1925 of 2199
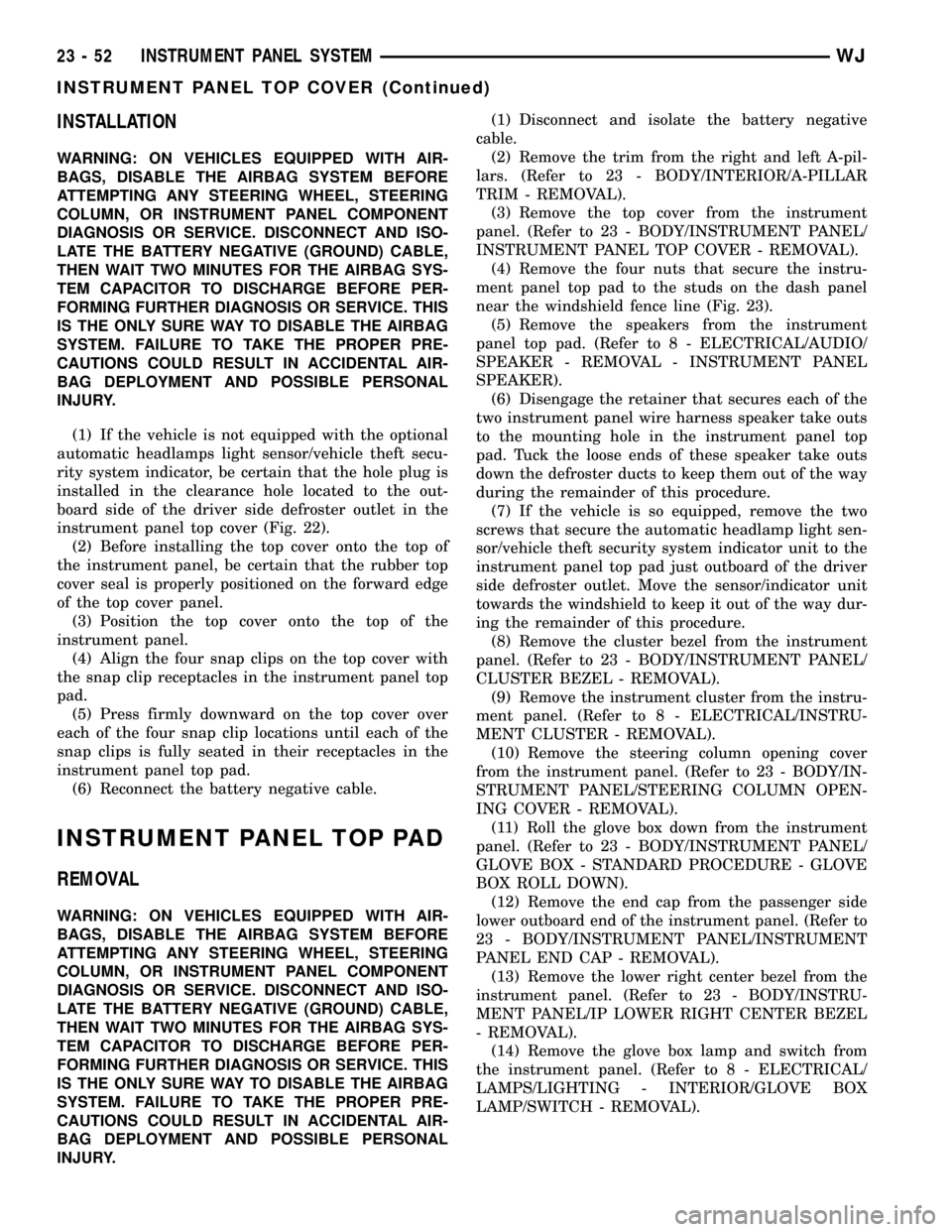
INSTALLATION
WARNING: ON VEHICLES EQUIPPED WITH AIR-
BAGS, DISABLE THE AIRBAG SYSTEM BEFORE
ATTEMPTING ANY STEERING WHEEL, STEERING
COLUMN, OR INSTRUMENT PANEL COMPONENT
DIAGNOSIS OR SERVICE. DISCONNECT AND ISO-
LATE THE BATTERY NEGATIVE (GROUND) CABLE,
THEN WAIT TWO MINUTES FOR THE AIRBAG SYS-
TEM CAPACITOR TO DISCHARGE BEFORE PER-
FORMING FURTHER DIAGNOSIS OR SERVICE. THIS
IS THE ONLY SURE WAY TO DISABLE THE AIRBAG
SYSTEM. FAILURE TO TAKE THE PROPER PRE-
CAUTIONS COULD RESULT IN ACCIDENTAL AIR-
BAG DEPLOYMENT AND POSSIBLE PERSONAL
INJURY.
(1) If the vehicle is not equipped with the optional
automatic headlamps light sensor/vehicle theft secu-
rity system indicator, be certain that the hole plug is
installed in the clearance hole located to the out-
board side of the driver side defroster outlet in the
instrument panel top cover (Fig. 22).
(2) Before installing the top cover onto the top of
the instrument panel, be certain that the rubber top
cover seal is properly positioned on the forward edge
of the top cover panel.
(3) Position the top cover onto the top of the
instrument panel.
(4) Align the four snap clips on the top cover with
the snap clip receptacles in the instrument panel top
pad.
(5) Press firmly downward on the top cover over
each of the four snap clip locations until each of the
snap clips is fully seated in their receptacles in the
instrument panel top pad.
(6) Reconnect the battery negative cable.
INSTRUMENT PANEL TOP PAD
REMOVAL
WARNING: ON VEHICLES EQUIPPED WITH AIR-
BAGS, DISABLE THE AIRBAG SYSTEM BEFORE
ATTEMPTING ANY STEERING WHEEL, STEERING
COLUMN, OR INSTRUMENT PANEL COMPONENT
DIAGNOSIS OR SERVICE. DISCONNECT AND ISO-
LATE THE BATTERY NEGATIVE (GROUND) CABLE,
THEN WAIT TWO MINUTES FOR THE AIRBAG SYS-
TEM CAPACITOR TO DISCHARGE BEFORE PER-
FORMING FURTHER DIAGNOSIS OR SERVICE. THIS
IS THE ONLY SURE WAY TO DISABLE THE AIRBAG
SYSTEM. FAILURE TO TAKE THE PROPER PRE-
CAUTIONS COULD RESULT IN ACCIDENTAL AIR-
BAG DEPLOYMENT AND POSSIBLE PERSONAL
INJURY.(1) Disconnect and isolate the battery negative
cable.
(2) Remove the trim from the right and left A-pil-
lars. (Refer to 23 - BODY/INTERIOR/A-PILLAR
TRIM - REMOVAL).
(3) Remove the top cover from the instrument
panel. (Refer to 23 - BODY/INSTRUMENT PANEL/
INSTRUMENT PANEL TOP COVER - REMOVAL).
(4) Remove the four nuts that secure the instru-
ment panel top pad to the studs on the dash panel
near the windshield fence line (Fig. 23).
(5) Remove the speakers from the instrument
panel top pad. (Refer to 8 - ELECTRICAL/AUDIO/
SPEAKER - REMOVAL - INSTRUMENT PANEL
SPEAKER).
(6) Disengage the retainer that secures each of the
two instrument panel wire harness speaker take outs
to the mounting hole in the instrument panel top
pad. Tuck the loose ends of these speaker take outs
down the defroster ducts to keep them out of the way
during the remainder of this procedure.
(7) If the vehicle is so equipped, remove the two
screws that secure the automatic headlamp light sen-
sor/vehicle theft security system indicator unit to the
instrument panel top pad just outboard of the driver
side defroster outlet. Move the sensor/indicator unit
towards the windshield to keep it out of the way dur-
ing the remainder of this procedure.
(8) Remove the cluster bezel from the instrument
panel. (Refer to 23 - BODY/INSTRUMENT PANEL/
CLUSTER BEZEL - REMOVAL).
(9) Remove the instrument cluster from the instru-
ment panel. (Refer to 8 - ELECTRICAL/INSTRU-
MENT CLUSTER - REMOVAL).
(10) Remove the steering column opening cover
from the instrument panel. (Refer to 23 - BODY/IN-
STRUMENT PANEL/STEERING COLUMN OPEN-
ING COVER - REMOVAL).
(11) Roll the glove box down from the instrument
panel. (Refer to 23 - BODY/INSTRUMENT PANEL/
GLOVE BOX - STANDARD PROCEDURE - GLOVE
BOX ROLL DOWN).
(12) Remove the end cap from the passenger side
lower outboard end of the instrument panel. (Refer to
23 - BODY/INSTRUMENT PANEL/INSTRUMENT
PANEL END CAP - REMOVAL).
(13) Remove the lower right center bezel from the
instrument panel. (Refer to 23 - BODY/INSTRU-
MENT PANEL/IP LOWER RIGHT CENTER BEZEL
- REMOVAL).
(14) Remove the glove box lamp and switch from
the instrument panel. (Refer to 8 - ELECTRICAL/
LAMPS/LIGHTING - INTERIOR/GLOVE BOX
LAMP/SWITCH - REMOVAL).
23 - 52 INSTRUMENT PANEL SYSTEMWJ
INSTRUMENT PANEL TOP COVER (Continued)
Page 1928 of 2199
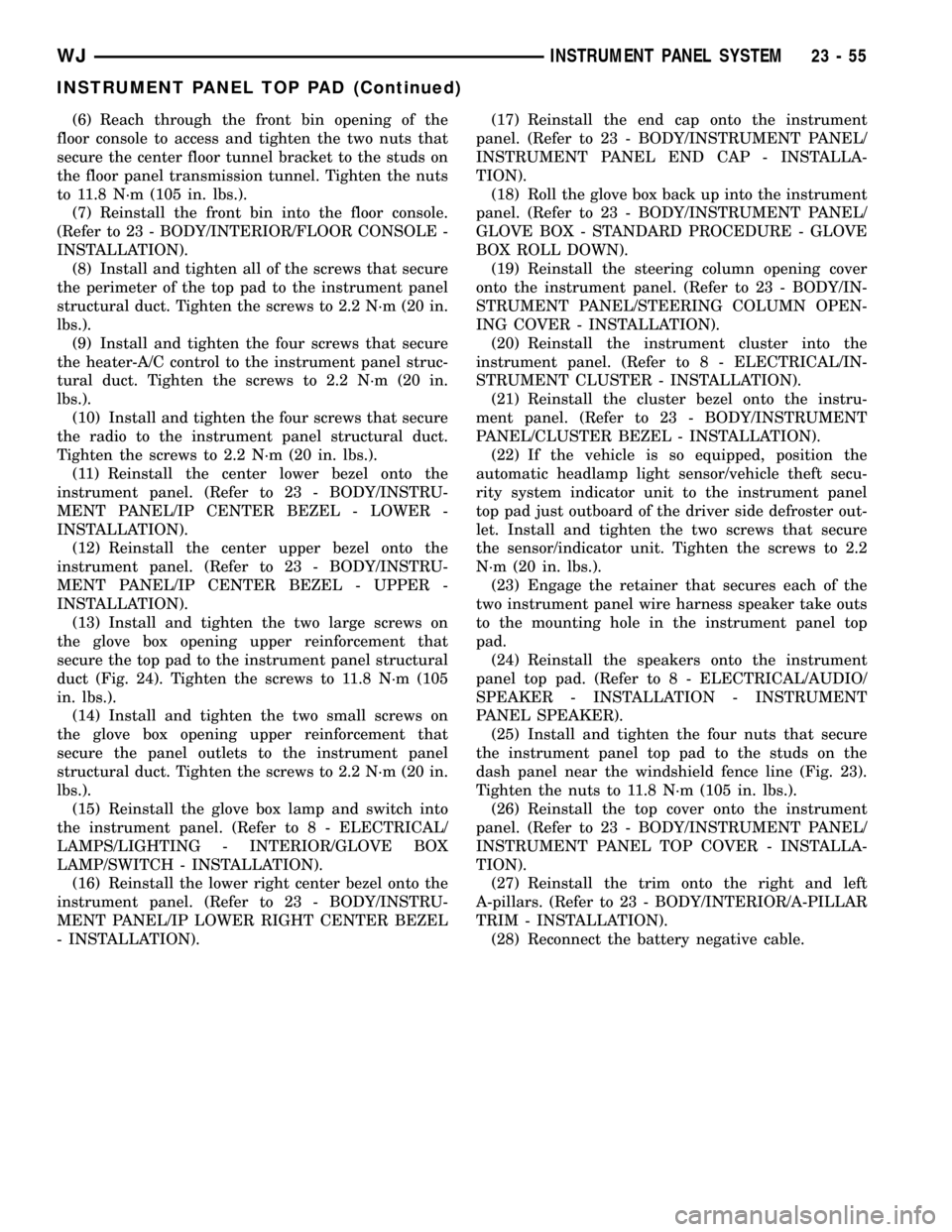
(6) Reach through the front bin opening of the
floor console to access and tighten the two nuts that
secure the center floor tunnel bracket to the studs on
the floor panel transmission tunnel. Tighten the nuts
to 11.8 N´m (105 in. lbs.).
(7) Reinstall the front bin into the floor console.
(Refer to 23 - BODY/INTERIOR/FLOOR CONSOLE -
INSTALLATION).
(8) Install and tighten all of the screws that secure
the perimeter of the top pad to the instrument panel
structural duct. Tighten the screws to 2.2 N´m (20 in.
lbs.).
(9) Install and tighten the four screws that secure
the heater-A/C control to the instrument panel struc-
tural duct. Tighten the screws to 2.2 N´m (20 in.
lbs.).
(10) Install and tighten the four screws that secure
the radio to the instrument panel structural duct.
Tighten the screws to 2.2 N´m (20 in. lbs.).
(11) Reinstall the center lower bezel onto the
instrument panel. (Refer to 23 - BODY/INSTRU-
MENT PANEL/IP CENTER BEZEL - LOWER -
INSTALLATION).
(12) Reinstall the center upper bezel onto the
instrument panel. (Refer to 23 - BODY/INSTRU-
MENT PANEL/IP CENTER BEZEL - UPPER -
INSTALLATION).
(13) Install and tighten the two large screws on
the glove box opening upper reinforcement that
secure the top pad to the instrument panel structural
duct (Fig. 24). Tighten the screws to 11.8 N´m (105
in. lbs.).
(14) Install and tighten the two small screws on
the glove box opening upper reinforcement that
secure the panel outlets to the instrument panel
structural duct. Tighten the screws to 2.2 N´m (20 in.
lbs.).
(15) Reinstall the glove box lamp and switch into
the instrument panel. (Refer to 8 - ELECTRICAL/
LAMPS/LIGHTING - INTERIOR/GLOVE BOX
LAMP/SWITCH - INSTALLATION).
(16) Reinstall the lower right center bezel onto the
instrument panel. (Refer to 23 - BODY/INSTRU-
MENT PANEL/IP LOWER RIGHT CENTER BEZEL
- INSTALLATION).(17) Reinstall the end cap onto the instrument
panel. (Refer to 23 - BODY/INSTRUMENT PANEL/
INSTRUMENT PANEL END CAP - INSTALLA-
TION).
(18) Roll the glove box back up into the instrument
panel. (Refer to 23 - BODY/INSTRUMENT PANEL/
GLOVE BOX - STANDARD PROCEDURE - GLOVE
BOX ROLL DOWN).
(19) Reinstall the steering column opening cover
onto the instrument panel. (Refer to 23 - BODY/IN-
STRUMENT PANEL/STEERING COLUMN OPEN-
ING COVER - INSTALLATION).
(20) Reinstall the instrument cluster into the
instrument panel. (Refer to 8 - ELECTRICAL/IN-
STRUMENT CLUSTER - INSTALLATION).
(21) Reinstall the cluster bezel onto the instru-
ment panel. (Refer to 23 - BODY/INSTRUMENT
PANEL/CLUSTER BEZEL - INSTALLATION).
(22) If the vehicle is so equipped, position the
automatic headlamp light sensor/vehicle theft secu-
rity system indicator unit to the instrument panel
top pad just outboard of the driver side defroster out-
let. Install and tighten the two screws that secure
the sensor/indicator unit. Tighten the screws to 2.2
N´m (20 in. lbs.).
(23) Engage the retainer that secures each of the
two instrument panel wire harness speaker take outs
to the mounting hole in the instrument panel top
pad.
(24) Reinstall the speakers onto the instrument
panel top pad. (Refer to 8 - ELECTRICAL/AUDIO/
SPEAKER - INSTALLATION - INSTRUMENT
PANEL SPEAKER).
(25) Install and tighten the four nuts that secure
the instrument panel top pad to the studs on the
dash panel near the windshield fence line (Fig. 23).
Tighten the nuts to 11.8 N´m (105 in. lbs.).
(26) Reinstall the top cover onto the instrument
panel. (Refer to 23 - BODY/INSTRUMENT PANEL/
INSTRUMENT PANEL TOP COVER - INSTALLA-
TION).
(27) Reinstall the trim onto the right and left
A-pillars. (Refer to 23 - BODY/INTERIOR/A-PILLAR
TRIM - INSTALLATION).
(28) Reconnect the battery negative cable.
WJINSTRUMENT PANEL SYSTEM 23 - 55
INSTRUMENT PANEL TOP PAD (Continued)