Panel JEEP GRAND CHEROKEE 2003 WJ / 2.G Workshop Manual
[x] Cancel search | Manufacturer: JEEP, Model Year: 2003, Model line: GRAND CHEROKEE, Model: JEEP GRAND CHEROKEE 2003 WJ / 2.GPages: 2199, PDF Size: 76.01 MB
Page 2119 of 2199
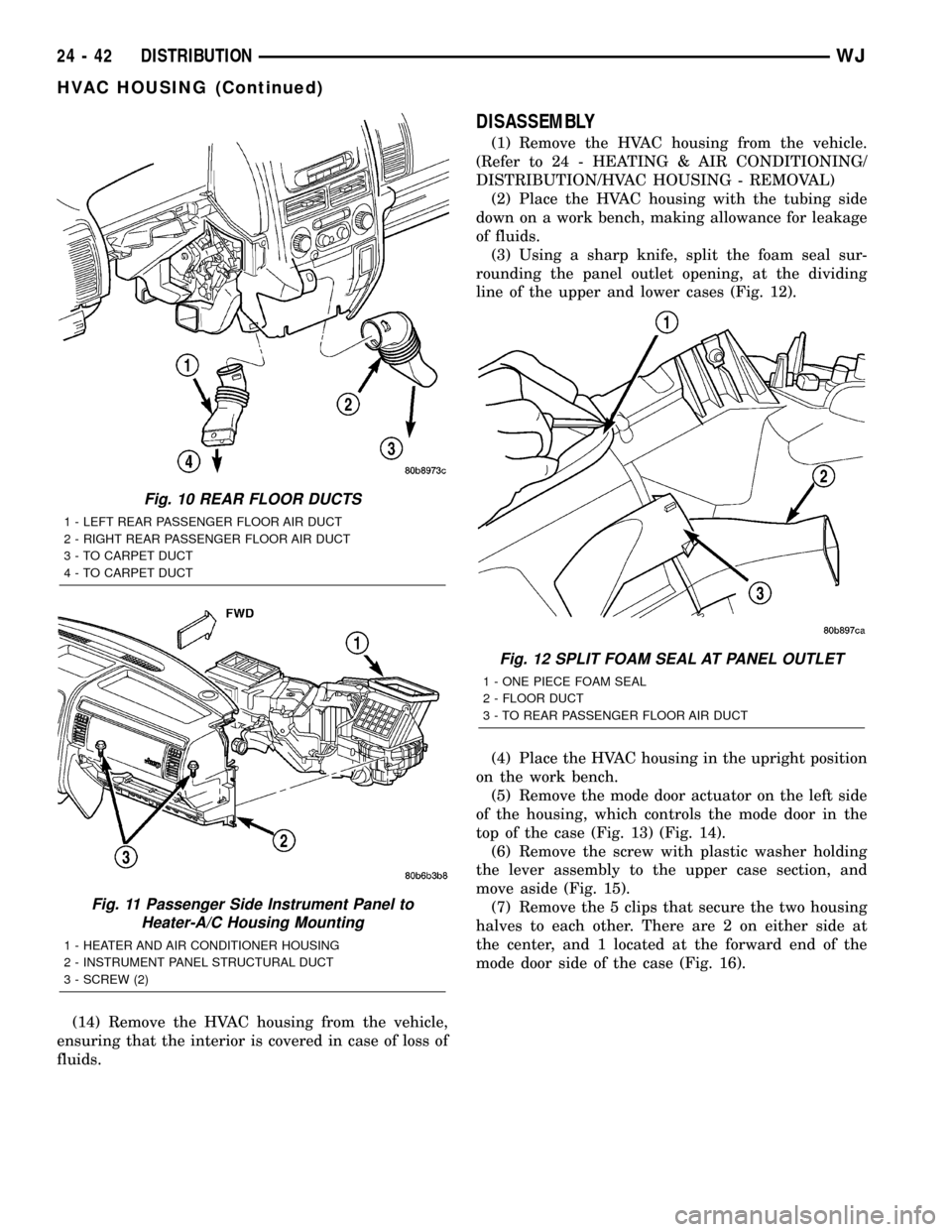
(14) Remove the HVAC housing from the vehicle,
ensuring that the interior is covered in case of loss of
fluids.
DISASSEMBLY
(1) Remove the HVAC housing from the vehicle.
(Refer to 24 - HEATING & AIR CONDITIONING/
DISTRIBUTION/HVAC HOUSING - REMOVAL)
(2) Place the HVAC housing with the tubing side
down on a work bench, making allowance for leakage
of fluids.
(3) Using a sharp knife, split the foam seal sur-
rounding the panel outlet opening, at the dividing
line of the upper and lower cases (Fig. 12).
(4) Place the HVAC housing in the upright position
on the work bench.
(5) Remove the mode door actuator on the left side
of the housing, which controls the mode door in the
top of the case (Fig. 13) (Fig. 14).
(6) Remove the screw with plastic washer holding
the lever assembly to the upper case section, and
move aside (Fig. 15).
(7) Remove the 5 clips that secure the two housing
halves to each other. There are 2 on either side at
the center, and 1 located at the forward end of the
mode door side of the case (Fig. 16).
Fig. 10 REAR FLOOR DUCTS
1 - LEFT REAR PASSENGER FLOOR AIR DUCT
2 - RIGHT REAR PASSENGER FLOOR AIR DUCT
3 - TO CARPET DUCT
4 - TO CARPET DUCT
Fig. 11 Passenger Side Instrument Panel to
Heater-A/C Housing Mounting
1 - HEATER AND AIR CONDITIONER HOUSING
2 - INSTRUMENT PANEL STRUCTURAL DUCT
3 - SCREW (2)
Fig. 12 SPLIT FOAM SEAL AT PANEL OUTLET
1 - ONE PIECE FOAM SEAL
2 - FLOOR DUCT
3 - TO REAR PASSENGER FLOOR AIR DUCT
24 - 42 DISTRIBUTIONWJ
HVAC HOUSING (Continued)
Page 2121 of 2199
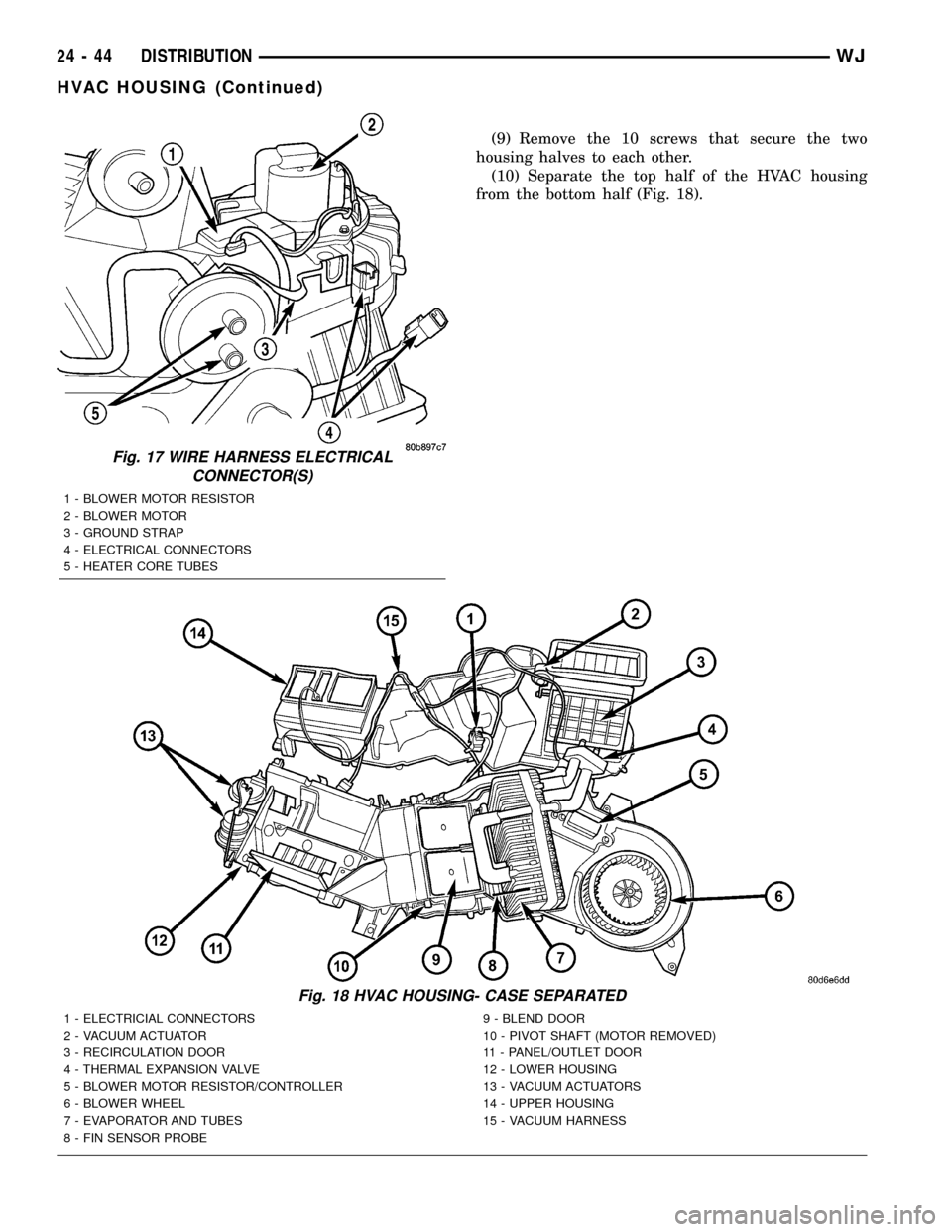
(9) Remove the 10 screws that secure the two
housing halves to each other.
(10) Separate the top half of the HVAC housing
from the bottom half (Fig. 18).
Fig. 17 WIRE HARNESS ELECTRICAL
CONNECTOR(S)
1 - BLOWER MOTOR RESISTOR
2 - BLOWER MOTOR
3 - GROUND STRAP
4 - ELECTRICAL CONNECTORS
5 - HEATER CORE TUBES
Fig. 18 HVAC HOUSING- CASE SEPARATED
1 - ELECTRICIAL CONNECTORS
2 - VACUUM ACTUATOR
3 - RECIRCULATION DOOR
4 - THERMAL EXPANSION VALVE
5 - BLOWER MOTOR RESISTOR/CONTROLLER
6 - BLOWER WHEEL
7 - EVAPORATOR AND TUBES
8 - FIN SENSOR PROBE9 - BLEND DOOR
10 - PIVOT SHAFT (MOTOR REMOVED)
11 - PANEL/OUTLET DOOR
12 - LOWER HOUSING
13 - VACUUM ACTUATORS
14 - UPPER HOUSING
15 - VACUUM HARNESS
24 - 44 DISTRIBUTIONWJ
HVAC HOUSING (Continued)
Page 2122 of 2199
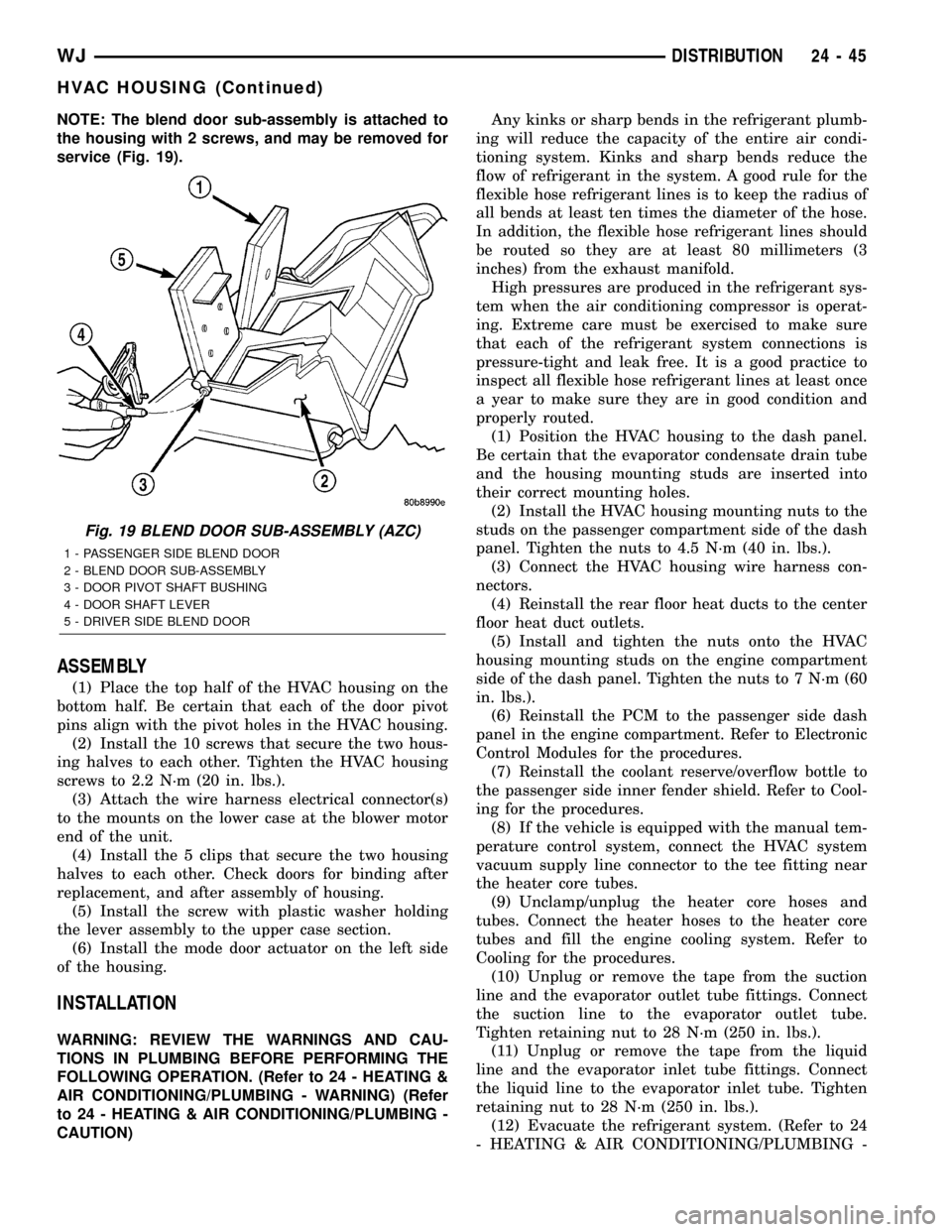
NOTE: The blend door sub-assembly is attached to
the housing with 2 screws, and may be removed for
service (Fig. 19).
ASSEMBLY
(1) Place the top half of the HVAC housing on the
bottom half. Be certain that each of the door pivot
pins align with the pivot holes in the HVAC housing.
(2) Install the 10 screws that secure the two hous-
ing halves to each other. Tighten the HVAC housing
screws to 2.2 N´m (20 in. lbs.).
(3) Attach the wire harness electrical connector(s)
to the mounts on the lower case at the blower motor
end of the unit.
(4) Install the 5 clips that secure the two housing
halves to each other. Check doors for binding after
replacement, and after assembly of housing.
(5) Install the screw with plastic washer holding
the lever assembly to the upper case section.
(6) Install the mode door actuator on the left side
of the housing.
INSTALLATION
WARNING: REVIEW THE WARNINGS AND CAU-
TIONS IN PLUMBING BEFORE PERFORMING THE
FOLLOWING OPERATION. (Refer to 24 - HEATING &
AIR CONDITIONING/PLUMBING - WARNING) (Refer
to 24 - HEATING & AIR CONDITIONING/PLUMBING -
CAUTION)Any kinks or sharp bends in the refrigerant plumb-
ing will reduce the capacity of the entire air condi-
tioning system. Kinks and sharp bends reduce the
flow of refrigerant in the system. A good rule for the
flexible hose refrigerant lines is to keep the radius of
all bends at least ten times the diameter of the hose.
In addition, the flexible hose refrigerant lines should
be routed so they are at least 80 millimeters (3
inches) from the exhaust manifold.
High pressures are produced in the refrigerant sys-
tem when the air conditioning compressor is operat-
ing. Extreme care must be exercised to make sure
that each of the refrigerant system connections is
pressure-tight and leak free. It is a good practice to
inspect all flexible hose refrigerant lines at least once
a year to make sure they are in good condition and
properly routed.
(1) Position the HVAC housing to the dash panel.
Be certain that the evaporator condensate drain tube
and the housing mounting studs are inserted into
their correct mounting holes.
(2) Install the HVAC housing mounting nuts to the
studs on the passenger compartment side of the dash
panel. Tighten the nuts to 4.5 N´m (40 in. lbs.).
(3) Connect the HVAC housing wire harness con-
nectors.
(4) Reinstall the rear floor heat ducts to the center
floor heat duct outlets.
(5) Install and tighten the nuts onto the HVAC
housing mounting studs on the engine compartment
side of the dash panel. Tighten the nuts to 7 N´m (60
in. lbs.).
(6) Reinstall the PCM to the passenger side dash
panel in the engine compartment. Refer to Electronic
Control Modules for the procedures.
(7) Reinstall the coolant reserve/overflow bottle to
the passenger side inner fender shield. Refer to Cool-
ing for the procedures.
(8) If the vehicle is equipped with the manual tem-
perature control system, connect the HVAC system
vacuum supply line connector to the tee fitting near
the heater core tubes.
(9) Unclamp/unplug the heater core hoses and
tubes. Connect the heater hoses to the heater core
tubes and fill the engine cooling system. Refer to
Cooling for the procedures.
(10) Unplug or remove the tape from the suction
line and the evaporator outlet tube fittings. Connect
the suction line to the evaporator outlet tube.
Tighten retaining nut to 28 N´m (250 in. lbs.).
(11) Unplug or remove the tape from the liquid
line and the evaporator inlet tube fittings. Connect
the liquid line to the evaporator inlet tube. Tighten
retaining nut to 28 N´m (250 in. lbs.).
(12) Evacuate the refrigerant system. (Refer to 24
- HEATING & AIR CONDITIONING/PLUMBING -
Fig. 19 BLEND DOOR SUB-ASSEMBLY (AZC)
1 - PASSENGER SIDE BLEND DOOR
2 - BLEND DOOR SUB-ASSEMBLY
3 - DOOR PIVOT SHAFT BUSHING
4 - DOOR SHAFT LEVER
5 - DRIVER SIDE BLEND DOOR
WJDISTRIBUTION 24 - 45
HVAC HOUSING (Continued)
Page 2123 of 2199
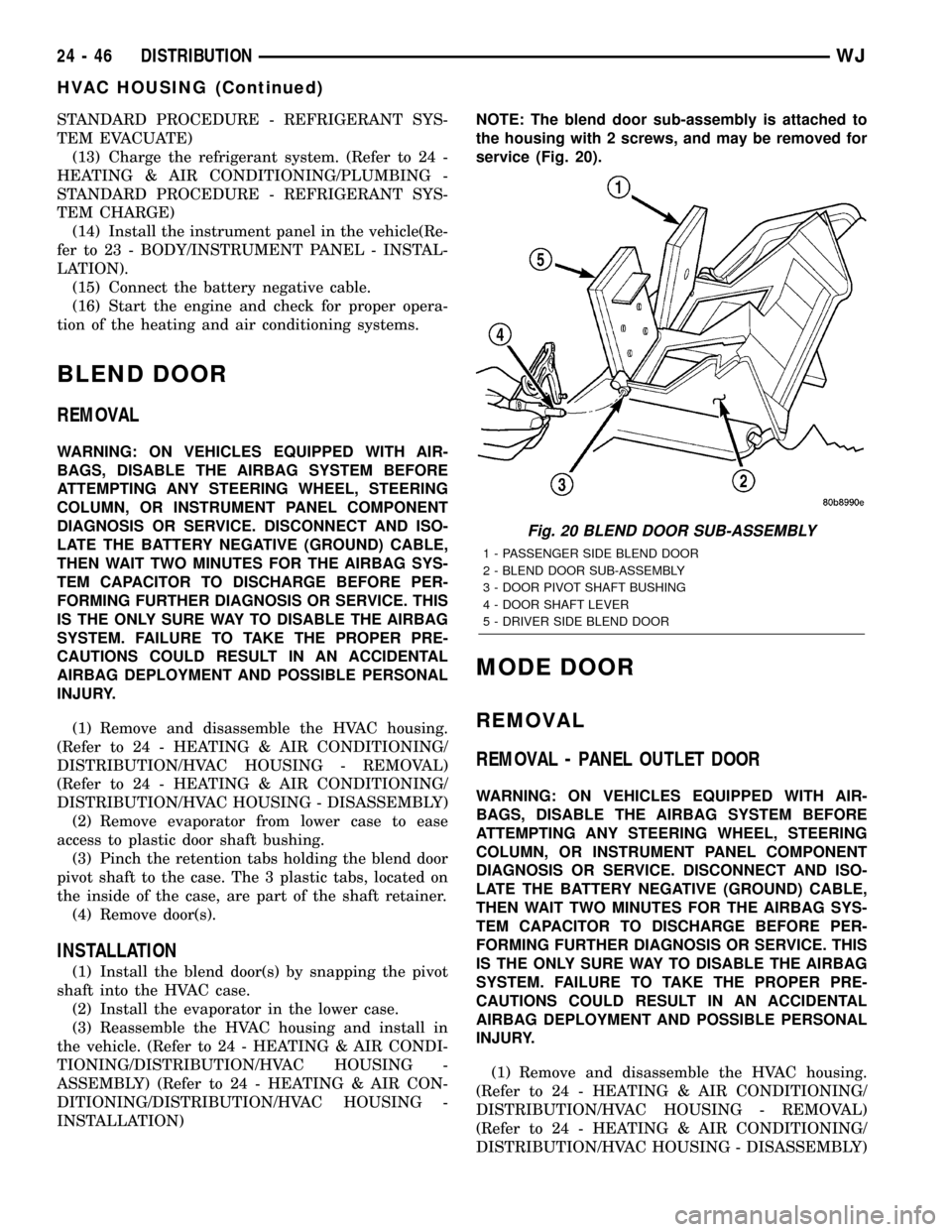
STANDARD PROCEDURE - REFRIGERANT SYS-
TEM EVACUATE)
(13) Charge the refrigerant system. (Refer to 24 -
HEATING & AIR CONDITIONING/PLUMBING -
STANDARD PROCEDURE - REFRIGERANT SYS-
TEM CHARGE)
(14) Install the instrument panel in the vehicle(Re-
fer to 23 - BODY/INSTRUMENT PANEL - INSTAL-
LATION).
(15) Connect the battery negative cable.
(16) Start the engine and check for proper opera-
tion of the heating and air conditioning systems.
BLEND DOOR
REMOVAL
WARNING: ON VEHICLES EQUIPPED WITH AIR-
BAGS, DISABLE THE AIRBAG SYSTEM BEFORE
ATTEMPTING ANY STEERING WHEEL, STEERING
COLUMN, OR INSTRUMENT PANEL COMPONENT
DIAGNOSIS OR SERVICE. DISCONNECT AND ISO-
LATE THE BATTERY NEGATIVE (GROUND) CABLE,
THEN WAIT TWO MINUTES FOR THE AIRBAG SYS-
TEM CAPACITOR TO DISCHARGE BEFORE PER-
FORMING FURTHER DIAGNOSIS OR SERVICE. THIS
IS THE ONLY SURE WAY TO DISABLE THE AIRBAG
SYSTEM. FAILURE TO TAKE THE PROPER PRE-
CAUTIONS COULD RESULT IN AN ACCIDENTAL
AIRBAG DEPLOYMENT AND POSSIBLE PERSONAL
INJURY.
(1) Remove and disassemble the HVAC housing.
(Refer to 24 - HEATING & AIR CONDITIONING/
DISTRIBUTION/HVAC HOUSING - REMOVAL)
(Refer to 24 - HEATING & AIR CONDITIONING/
DISTRIBUTION/HVAC HOUSING - DISASSEMBLY)
(2) Remove evaporator from lower case to ease
access to plastic door shaft bushing.
(3) Pinch the retention tabs holding the blend door
pivot shaft to the case. The 3 plastic tabs, located on
the inside of the case, are part of the shaft retainer.
(4) Remove door(s).
INSTALLATION
(1) Install the blend door(s) by snapping the pivot
shaft into the HVAC case.
(2) Install the evaporator in the lower case.
(3) Reassemble the HVAC housing and install in
the vehicle. (Refer to 24 - HEATING & AIR CONDI-
TIONING/DISTRIBUTION/HVAC HOUSING -
ASSEMBLY) (Refer to 24 - HEATING & AIR CON-
DITIONING/DISTRIBUTION/HVAC HOUSING -
INSTALLATION)NOTE: The blend door sub-assembly is attached to
the housing with 2 screws, and may be removed for
service (Fig. 20).
MODE DOOR
REMOVAL
REMOVAL - PANEL OUTLET DOOR
WARNING: ON VEHICLES EQUIPPED WITH AIR-
BAGS, DISABLE THE AIRBAG SYSTEM BEFORE
ATTEMPTING ANY STEERING WHEEL, STEERING
COLUMN, OR INSTRUMENT PANEL COMPONENT
DIAGNOSIS OR SERVICE. DISCONNECT AND ISO-
LATE THE BATTERY NEGATIVE (GROUND) CABLE,
THEN WAIT TWO MINUTES FOR THE AIRBAG SYS-
TEM CAPACITOR TO DISCHARGE BEFORE PER-
FORMING FURTHER DIAGNOSIS OR SERVICE. THIS
IS THE ONLY SURE WAY TO DISABLE THE AIRBAG
SYSTEM. FAILURE TO TAKE THE PROPER PRE-
CAUTIONS COULD RESULT IN AN ACCIDENTAL
AIRBAG DEPLOYMENT AND POSSIBLE PERSONAL
INJURY.
(1) Remove and disassemble the HVAC housing.
(Refer to 24 - HEATING & AIR CONDITIONING/
DISTRIBUTION/HVAC HOUSING - REMOVAL)
(Refer to 24 - HEATING & AIR CONDITIONING/
DISTRIBUTION/HVAC HOUSING - DISASSEMBLY)
Fig. 20 BLEND DOOR SUB-ASSEMBLY
1 - PASSENGER SIDE BLEND DOOR
2 - BLEND DOOR SUB-ASSEMBLY
3 - DOOR PIVOT SHAFT BUSHING
4 - DOOR SHAFT LEVER
5 - DRIVER SIDE BLEND DOOR
24 - 46 DISTRIBUTIONWJ
HVAC HOUSING (Continued)
Page 2124 of 2199
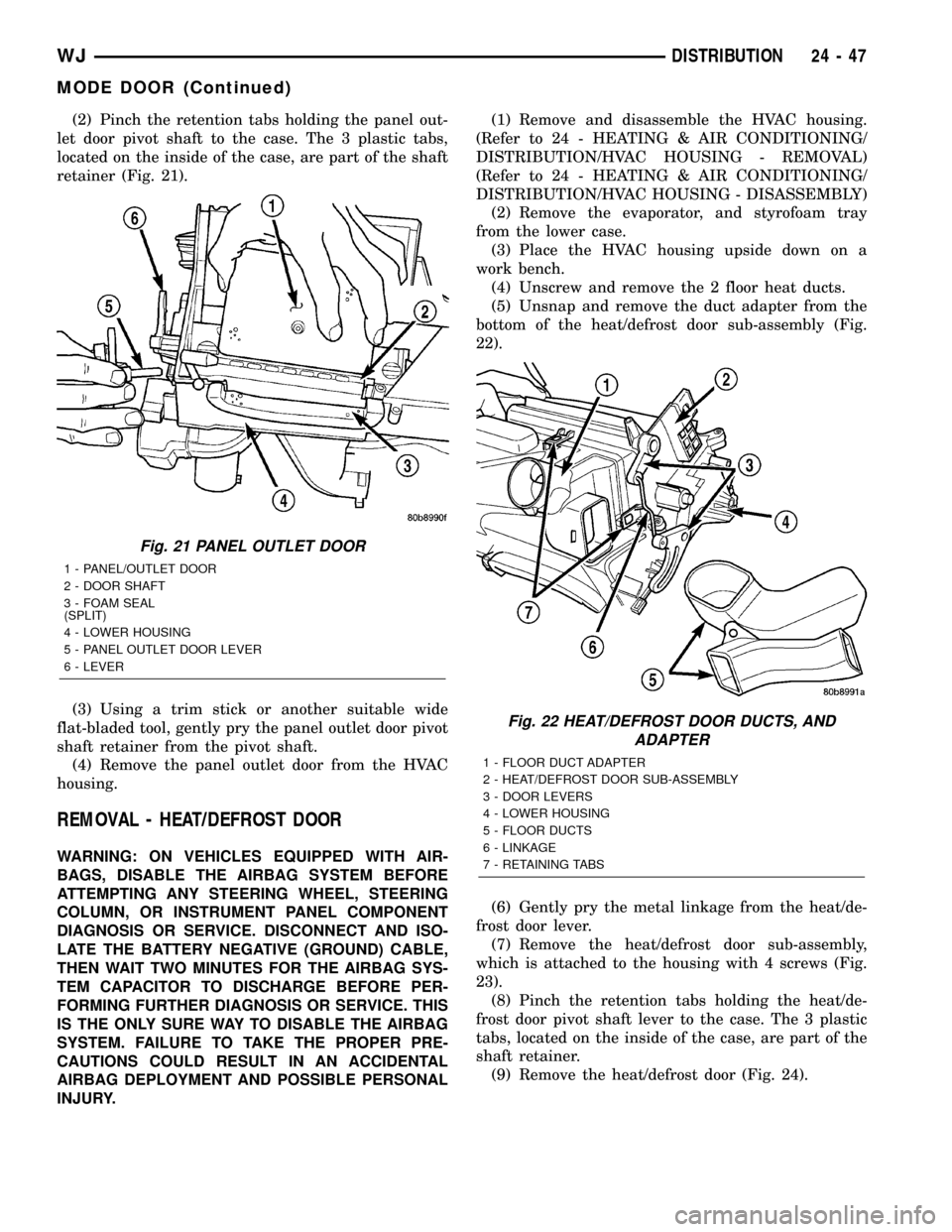
(2) Pinch the retention tabs holding the panel out-
let door pivot shaft to the case. The 3 plastic tabs,
located on the inside of the case, are part of the shaft
retainer (Fig. 21).
(3) Using a trim stick or another suitable wide
flat-bladed tool, gently pry the panel outlet door pivot
shaft retainer from the pivot shaft.
(4) Remove the panel outlet door from the HVAC
housing.
REMOVAL - HEAT/DEFROST DOOR
WARNING: ON VEHICLES EQUIPPED WITH AIR-
BAGS, DISABLE THE AIRBAG SYSTEM BEFORE
ATTEMPTING ANY STEERING WHEEL, STEERING
COLUMN, OR INSTRUMENT PANEL COMPONENT
DIAGNOSIS OR SERVICE. DISCONNECT AND ISO-
LATE THE BATTERY NEGATIVE (GROUND) CABLE,
THEN WAIT TWO MINUTES FOR THE AIRBAG SYS-
TEM CAPACITOR TO DISCHARGE BEFORE PER-
FORMING FURTHER DIAGNOSIS OR SERVICE. THIS
IS THE ONLY SURE WAY TO DISABLE THE AIRBAG
SYSTEM. FAILURE TO TAKE THE PROPER PRE-
CAUTIONS COULD RESULT IN AN ACCIDENTAL
AIRBAG DEPLOYMENT AND POSSIBLE PERSONAL
INJURY.(1) Remove and disassemble the HVAC housing.
(Refer to 24 - HEATING & AIR CONDITIONING/
DISTRIBUTION/HVAC HOUSING - REMOVAL)
(Refer to 24 - HEATING & AIR CONDITIONING/
DISTRIBUTION/HVAC HOUSING - DISASSEMBLY)
(2) Remove the evaporator, and styrofoam tray
from the lower case.
(3) Place the HVAC housing upside down on a
work bench.
(4) Unscrew and remove the 2 floor heat ducts.
(5) Unsnap and remove the duct adapter from the
bottom of the heat/defrost door sub-assembly (Fig.
22).
(6) Gently pry the metal linkage from the heat/de-
frost door lever.
(7) Remove the heat/defrost door sub-assembly,
which is attached to the housing with 4 screws (Fig.
23).
(8) Pinch the retention tabs holding the heat/de-
frost door pivot shaft lever to the case. The 3 plastic
tabs, located on the inside of the case, are part of the
shaft retainer.
(9) Remove the heat/defrost door (Fig. 24).
Fig. 21 PANEL OUTLET DOOR
1 - PANEL/OUTLET DOOR
2 - DOOR SHAFT
3 - FOAM SEAL
(SPLIT)
4 - LOWER HOUSING
5 - PANEL OUTLET DOOR LEVER
6 - LEVER
Fig. 22 HEAT/DEFROST DOOR DUCTS, AND
ADAPTER
1 - FLOOR DUCT ADAPTER
2 - HEAT/DEFROST DOOR SUB-ASSEMBLY
3 - DOOR LEVERS
4 - LOWER HOUSING
5 - FLOOR DUCTS
6 - LINKAGE
7 - RETAINING TABS
WJDISTRIBUTION 24 - 47
MODE DOOR (Continued)
Page 2125 of 2199
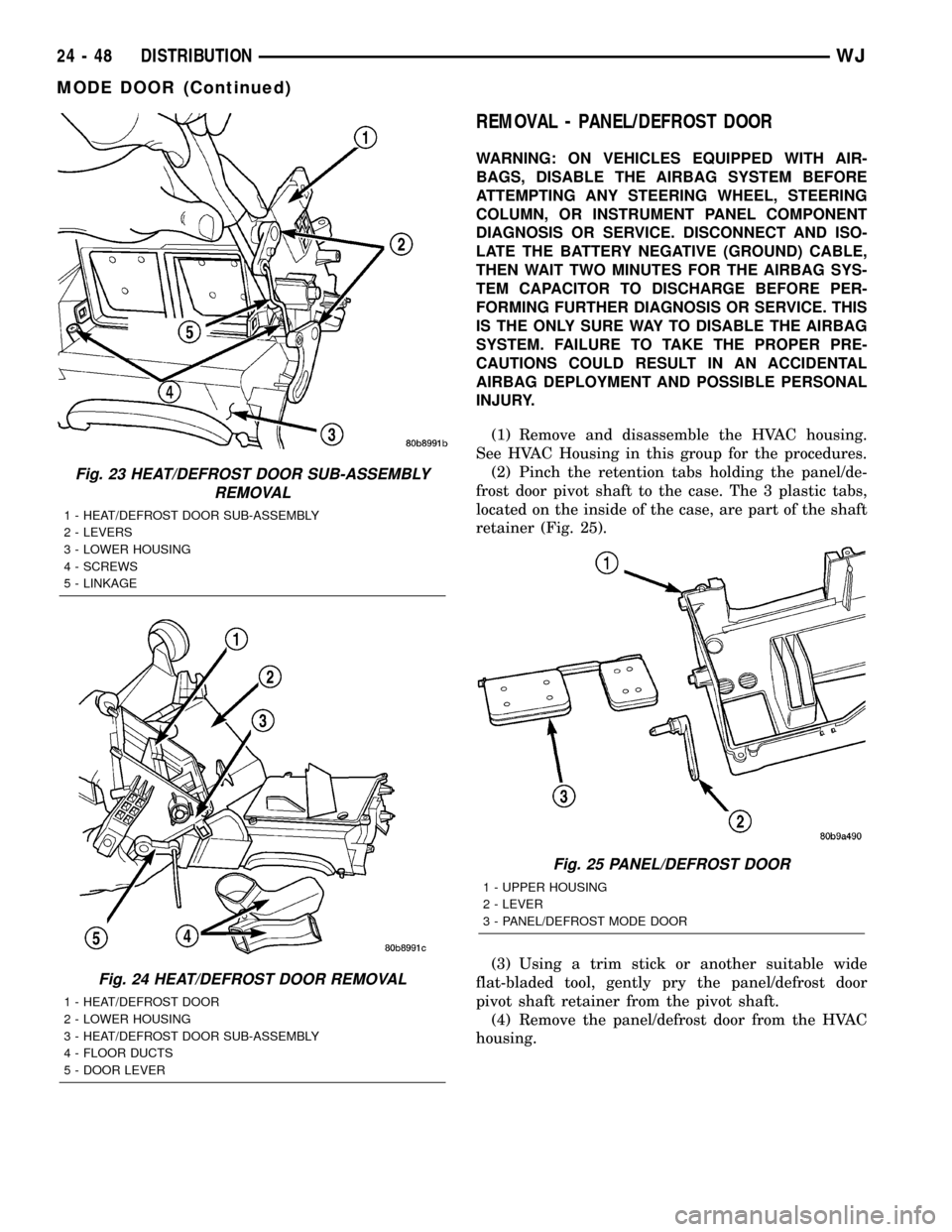
REMOVAL - PANEL/DEFROST DOOR
WARNING: ON VEHICLES EQUIPPED WITH AIR-
BAGS, DISABLE THE AIRBAG SYSTEM BEFORE
ATTEMPTING ANY STEERING WHEEL, STEERING
COLUMN, OR INSTRUMENT PANEL COMPONENT
DIAGNOSIS OR SERVICE. DISCONNECT AND ISO-
LATE THE BATTERY NEGATIVE (GROUND) CABLE,
THEN WAIT TWO MINUTES FOR THE AIRBAG SYS-
TEM CAPACITOR TO DISCHARGE BEFORE PER-
FORMING FURTHER DIAGNOSIS OR SERVICE. THIS
IS THE ONLY SURE WAY TO DISABLE THE AIRBAG
SYSTEM. FAILURE TO TAKE THE PROPER PRE-
CAUTIONS COULD RESULT IN AN ACCIDENTAL
AIRBAG DEPLOYMENT AND POSSIBLE PERSONAL
INJURY.
(1) Remove and disassemble the HVAC housing.
See HVAC Housing in this group for the procedures.
(2) Pinch the retention tabs holding the panel/de-
frost door pivot shaft to the case. The 3 plastic tabs,
located on the inside of the case, are part of the shaft
retainer (Fig. 25).
(3) Using a trim stick or another suitable wide
flat-bladed tool, gently pry the panel/defrost door
pivot shaft retainer from the pivot shaft.
(4) Remove the panel/defrost door from the HVAC
housing.
Fig. 23 HEAT/DEFROST DOOR SUB-ASSEMBLY
REMOVAL
1 - HEAT/DEFROST DOOR SUB-ASSEMBLY
2 - LEVERS
3 - LOWER HOUSING
4 - SCREWS
5 - LINKAGE
Fig. 24 HEAT/DEFROST DOOR REMOVAL
1 - HEAT/DEFROST DOOR
2 - LOWER HOUSING
3 - HEAT/DEFROST DOOR SUB-ASSEMBLY
4 - FLOOR DUCTS
5 - DOOR LEVER
Fig. 25 PANEL/DEFROST DOOR
1 - UPPER HOUSING
2 - LEVER
3 - PANEL/DEFROST MODE DOOR
24 - 48 DISTRIBUTIONWJ
MODE DOOR (Continued)
Page 2126 of 2199
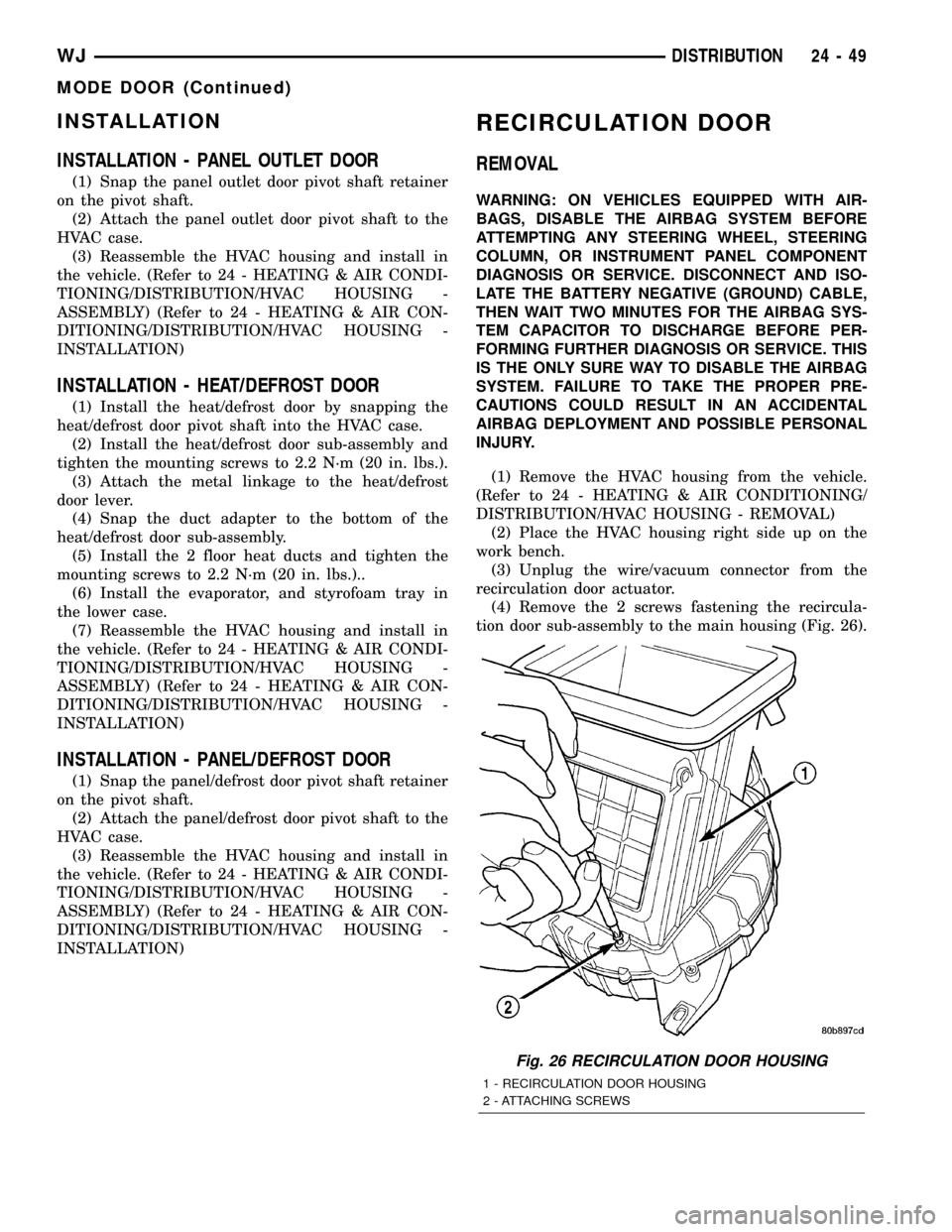
INSTALLATION
INSTALLATION - PANEL OUTLET DOOR
(1) Snap the panel outlet door pivot shaft retainer
on the pivot shaft.
(2) Attach the panel outlet door pivot shaft to the
HVAC case.
(3) Reassemble the HVAC housing and install in
the vehicle. (Refer to 24 - HEATING & AIR CONDI-
TIONING/DISTRIBUTION/HVAC HOUSING -
ASSEMBLY) (Refer to 24 - HEATING & AIR CON-
DITIONING/DISTRIBUTION/HVAC HOUSING -
INSTALLATION)
INSTALLATION - HEAT/DEFROST DOOR
(1) Install the heat/defrost door by snapping the
heat/defrost door pivot shaft into the HVAC case.
(2) Install the heat/defrost door sub-assembly and
tighten the mounting screws to 2.2 N´m (20 in. lbs.).
(3) Attach the metal linkage to the heat/defrost
door lever.
(4) Snap the duct adapter to the bottom of the
heat/defrost door sub-assembly.
(5) Install the 2 floor heat ducts and tighten the
mounting screws to 2.2 N´m (20 in. lbs.)..
(6) Install the evaporator, and styrofoam tray in
the lower case.
(7) Reassemble the HVAC housing and install in
the vehicle. (Refer to 24 - HEATING & AIR CONDI-
TIONING/DISTRIBUTION/HVAC HOUSING -
ASSEMBLY) (Refer to 24 - HEATING & AIR CON-
DITIONING/DISTRIBUTION/HVAC HOUSING -
INSTALLATION)
INSTALLATION - PANEL/DEFROST DOOR
(1) Snap the panel/defrost door pivot shaft retainer
on the pivot shaft.
(2) Attach the panel/defrost door pivot shaft to the
HVAC case.
(3) Reassemble the HVAC housing and install in
the vehicle. (Refer to 24 - HEATING & AIR CONDI-
TIONING/DISTRIBUTION/HVAC HOUSING -
ASSEMBLY) (Refer to 24 - HEATING & AIR CON-
DITIONING/DISTRIBUTION/HVAC HOUSING -
INSTALLATION)
RECIRCULATION DOOR
REMOVAL
WARNING: ON VEHICLES EQUIPPED WITH AIR-
BAGS, DISABLE THE AIRBAG SYSTEM BEFORE
ATTEMPTING ANY STEERING WHEEL, STEERING
COLUMN, OR INSTRUMENT PANEL COMPONENT
DIAGNOSIS OR SERVICE. DISCONNECT AND ISO-
LATE THE BATTERY NEGATIVE (GROUND) CABLE,
THEN WAIT TWO MINUTES FOR THE AIRBAG SYS-
TEM CAPACITOR TO DISCHARGE BEFORE PER-
FORMING FURTHER DIAGNOSIS OR SERVICE. THIS
IS THE ONLY SURE WAY TO DISABLE THE AIRBAG
SYSTEM. FAILURE TO TAKE THE PROPER PRE-
CAUTIONS COULD RESULT IN AN ACCIDENTAL
AIRBAG DEPLOYMENT AND POSSIBLE PERSONAL
INJURY.
(1) Remove the HVAC housing from the vehicle.
(Refer to 24 - HEATING & AIR CONDITIONING/
DISTRIBUTION/HVAC HOUSING - REMOVAL)
(2) Place the HVAC housing right side up on the
work bench.
(3) Unplug the wire/vacuum connector from the
recirculation door actuator.
(4) Remove the 2 screws fastening the recircula-
tion door sub-assembly to the main housing (Fig. 26).
Fig. 26 RECIRCULATION DOOR HOUSING
1 - RECIRCULATION DOOR HOUSING
2 - ATTACHING SCREWS
WJDISTRIBUTION 24 - 49
MODE DOOR (Continued)
Page 2131 of 2199
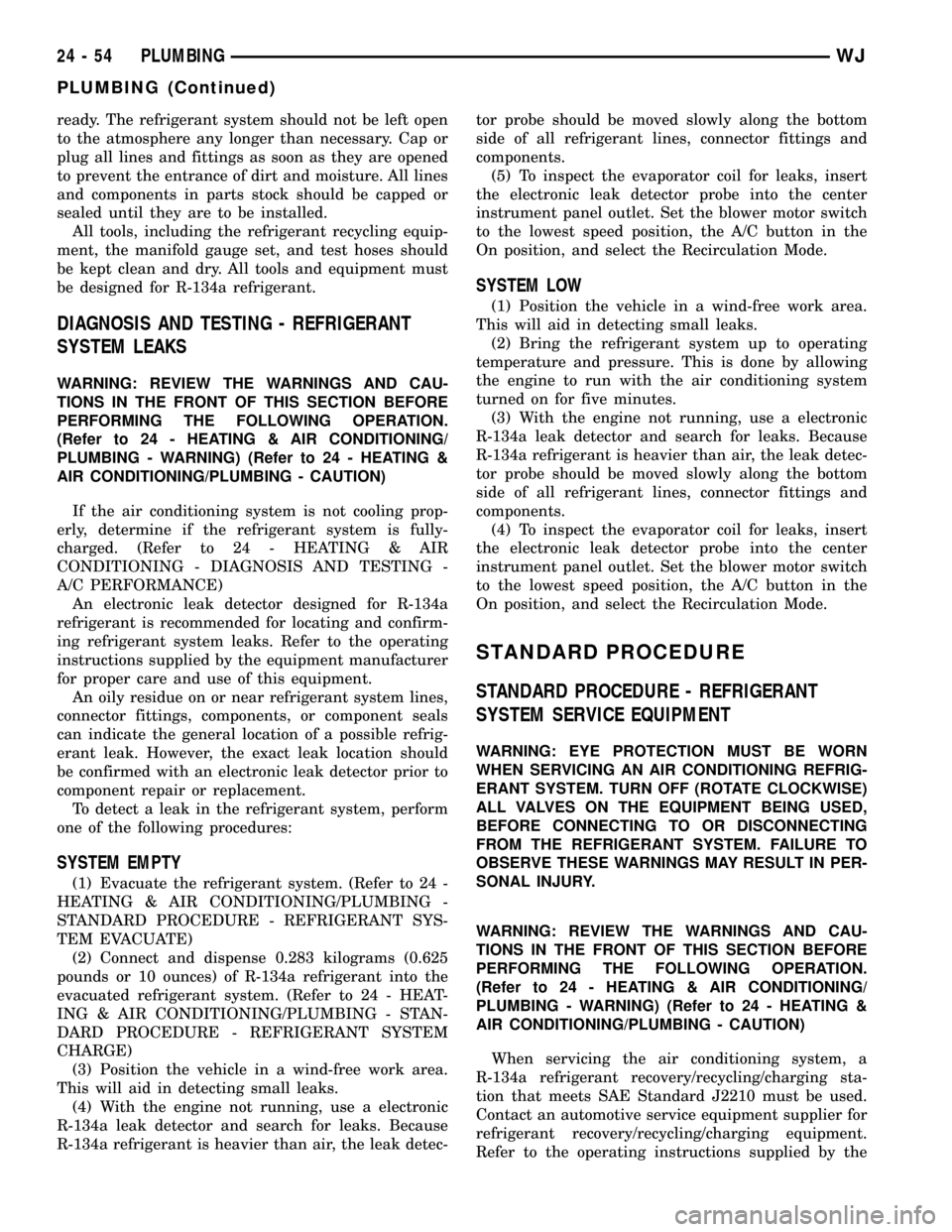
ready. The refrigerant system should not be left open
to the atmosphere any longer than necessary. Cap or
plug all lines and fittings as soon as they are opened
to prevent the entrance of dirt and moisture. All lines
and components in parts stock should be capped or
sealed until they are to be installed.
All tools, including the refrigerant recycling equip-
ment, the manifold gauge set, and test hoses should
be kept clean and dry. All tools and equipment must
be designed for R-134a refrigerant.
DIAGNOSIS AND TESTING - REFRIGERANT
SYSTEM LEAKS
WARNING: REVIEW THE WARNINGS AND CAU-
TIONS IN THE FRONT OF THIS SECTION BEFORE
PERFORMING THE FOLLOWING OPERATION.
(Refer to 24 - HEATING & AIR CONDITIONING/
PLUMBING - WARNING) (Refer to 24 - HEATING &
AIR CONDITIONING/PLUMBING - CAUTION)
If the air conditioning system is not cooling prop-
erly, determine if the refrigerant system is fully-
charged. (Refer to 24 - HEATING & AIR
CONDITIONING - DIAGNOSIS AND TESTING -
A/C PERFORMANCE)
An electronic leak detector designed for R-134a
refrigerant is recommended for locating and confirm-
ing refrigerant system leaks. Refer to the operating
instructions supplied by the equipment manufacturer
for proper care and use of this equipment.
An oily residue on or near refrigerant system lines,
connector fittings, components, or component seals
can indicate the general location of a possible refrig-
erant leak. However, the exact leak location should
be confirmed with an electronic leak detector prior to
component repair or replacement.
To detect a leak in the refrigerant system, perform
one of the following procedures:
SYSTEM EMPTY
(1) Evacuate the refrigerant system. (Refer to 24 -
HEATING & AIR CONDITIONING/PLUMBING -
STANDARD PROCEDURE - REFRIGERANT SYS-
TEM EVACUATE)
(2) Connect and dispense 0.283 kilograms (0.625
pounds or 10 ounces) of R-134a refrigerant into the
evacuated refrigerant system. (Refer to 24 - HEAT-
ING & AIR CONDITIONING/PLUMBING - STAN-
DARD PROCEDURE - REFRIGERANT SYSTEM
CHARGE)
(3) Position the vehicle in a wind-free work area.
This will aid in detecting small leaks.
(4) With the engine not running, use a electronic
R-134a leak detector and search for leaks. Because
R-134a refrigerant is heavier than air, the leak detec-tor probe should be moved slowly along the bottom
side of all refrigerant lines, connector fittings and
components.
(5) To inspect the evaporator coil for leaks, insert
the electronic leak detector probe into the center
instrument panel outlet. Set the blower motor switch
to the lowest speed position, the A/C button in the
On position, and select the Recirculation Mode.
SYSTEM LOW
(1) Position the vehicle in a wind-free work area.
This will aid in detecting small leaks.
(2) Bring the refrigerant system up to operating
temperature and pressure. This is done by allowing
the engine to run with the air conditioning system
turned on for five minutes.
(3) With the engine not running, use a electronic
R-134a leak detector and search for leaks. Because
R-134a refrigerant is heavier than air, the leak detec-
tor probe should be moved slowly along the bottom
side of all refrigerant lines, connector fittings and
components.
(4) To inspect the evaporator coil for leaks, insert
the electronic leak detector probe into the center
instrument panel outlet. Set the blower motor switch
to the lowest speed position, the A/C button in the
On position, and select the Recirculation Mode.
STANDARD PROCEDURE
STANDARD PROCEDURE - REFRIGERANT
SYSTEM SERVICE EQUIPMENT
WARNING: EYE PROTECTION MUST BE WORN
WHEN SERVICING AN AIR CONDITIONING REFRIG-
ERANT SYSTEM. TURN OFF (ROTATE CLOCKWISE)
ALL VALVES ON THE EQUIPMENT BEING USED,
BEFORE CONNECTING TO OR DISCONNECTING
FROM THE REFRIGERANT SYSTEM. FAILURE TO
OBSERVE THESE WARNINGS MAY RESULT IN PER-
SONAL INJURY.
WARNING: REVIEW THE WARNINGS AND CAU-
TIONS IN THE FRONT OF THIS SECTION BEFORE
PERFORMING THE FOLLOWING OPERATION.
(Refer to 24 - HEATING & AIR CONDITIONING/
PLUMBING - WARNING) (Refer to 24 - HEATING &
AIR CONDITIONING/PLUMBING - CAUTION)
When servicing the air conditioning system, a
R-134a refrigerant recovery/recycling/charging sta-
tion that meets SAE Standard J2210 must be used.
Contact an automotive service equipment supplier for
refrigerant recovery/recycling/charging equipment.
Refer to the operating instructions supplied by the
24 - 54 PLUMBINGWJ
PLUMBING (Continued)
Page 2132 of 2199
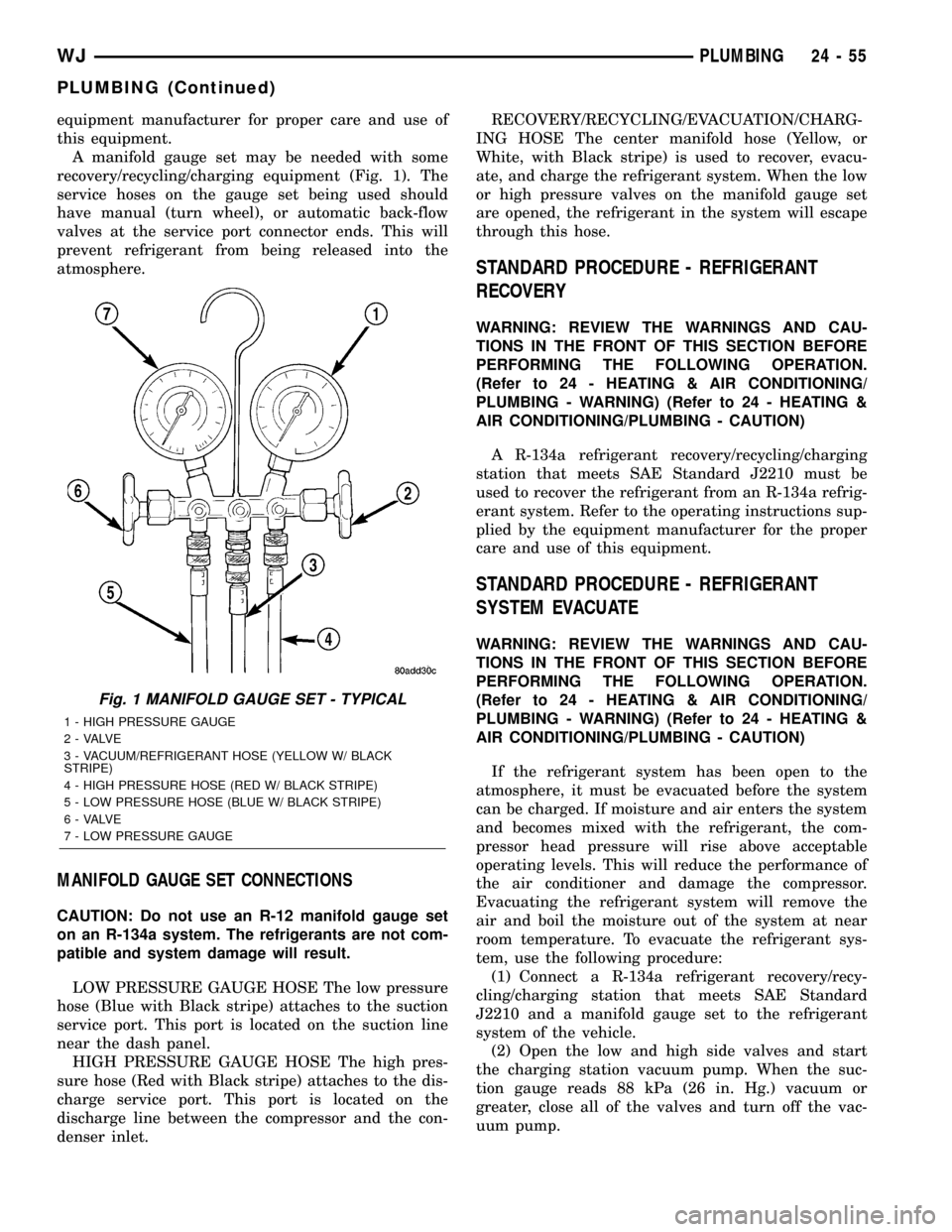
equipment manufacturer for proper care and use of
this equipment.
A manifold gauge set may be needed with some
recovery/recycling/charging equipment (Fig. 1). The
service hoses on the gauge set being used should
have manual (turn wheel), or automatic back-flow
valves at the service port connector ends. This will
prevent refrigerant from being released into the
atmosphere.
MANIFOLD GAUGE SET CONNECTIONS
CAUTION: Do not use an R-12 manifold gauge set
on an R-134a system. The refrigerants are not com-
patible and system damage will result.
LOW PRESSURE GAUGE HOSE The low pressure
hose (Blue with Black stripe) attaches to the suction
service port. This port is located on the suction line
near the dash panel.
HIGH PRESSURE GAUGE HOSE The high pres-
sure hose (Red with Black stripe) attaches to the dis-
charge service port. This port is located on the
discharge line between the compressor and the con-
denser inlet.RECOVERY/RECYCLING/EVACUATION/CHARG-
ING HOSE The center manifold hose (Yellow, or
White, with Black stripe) is used to recover, evacu-
ate, and charge the refrigerant system. When the low
or high pressure valves on the manifold gauge set
are opened, the refrigerant in the system will escape
through this hose.
STANDARD PROCEDURE - REFRIGERANT
RECOVERY
WARNING: REVIEW THE WARNINGS AND CAU-
TIONS IN THE FRONT OF THIS SECTION BEFORE
PERFORMING THE FOLLOWING OPERATION.
(Refer to 24 - HEATING & AIR CONDITIONING/
PLUMBING - WARNING) (Refer to 24 - HEATING &
AIR CONDITIONING/PLUMBING - CAUTION)
A R-134a refrigerant recovery/recycling/charging
station that meets SAE Standard J2210 must be
used to recover the refrigerant from an R-134a refrig-
erant system. Refer to the operating instructions sup-
plied by the equipment manufacturer for the proper
care and use of this equipment.
STANDARD PROCEDURE - REFRIGERANT
SYSTEM EVACUATE
WARNING: REVIEW THE WARNINGS AND CAU-
TIONS IN THE FRONT OF THIS SECTION BEFORE
PERFORMING THE FOLLOWING OPERATION.
(Refer to 24 - HEATING & AIR CONDITIONING/
PLUMBING - WARNING) (Refer to 24 - HEATING &
AIR CONDITIONING/PLUMBING - CAUTION)
If the refrigerant system has been open to the
atmosphere, it must be evacuated before the system
can be charged. If moisture and air enters the system
and becomes mixed with the refrigerant, the com-
pressor head pressure will rise above acceptable
operating levels. This will reduce the performance of
the air conditioner and damage the compressor.
Evacuating the refrigerant system will remove the
air and boil the moisture out of the system at near
room temperature. To evacuate the refrigerant sys-
tem, use the following procedure:
(1) Connect a R-134a refrigerant recovery/recy-
cling/charging station that meets SAE Standard
J2210 and a manifold gauge set to the refrigerant
system of the vehicle.
(2) Open the low and high side valves and start
the charging station vacuum pump. When the suc-
tion gauge reads 88 kPa (26 in. Hg.) vacuum or
greater, close all of the valves and turn off the vac-
uum pump.
Fig. 1 MANIFOLD GAUGE SET - TYPICAL
1 - HIGH PRESSURE GAUGE
2 - VALVE
3 - VACUUM/REFRIGERANT HOSE (YELLOW W/ BLACK
STRIPE)
4 - HIGH PRESSURE HOSE (RED W/ BLACK STRIPE)
5 - LOW PRESSURE HOSE (BLUE W/ BLACK STRIPE)
6 - VALVE
7 - LOW PRESSURE GAUGE
WJPLUMBING 24 - 55
PLUMBING (Continued)
Page 2142 of 2199
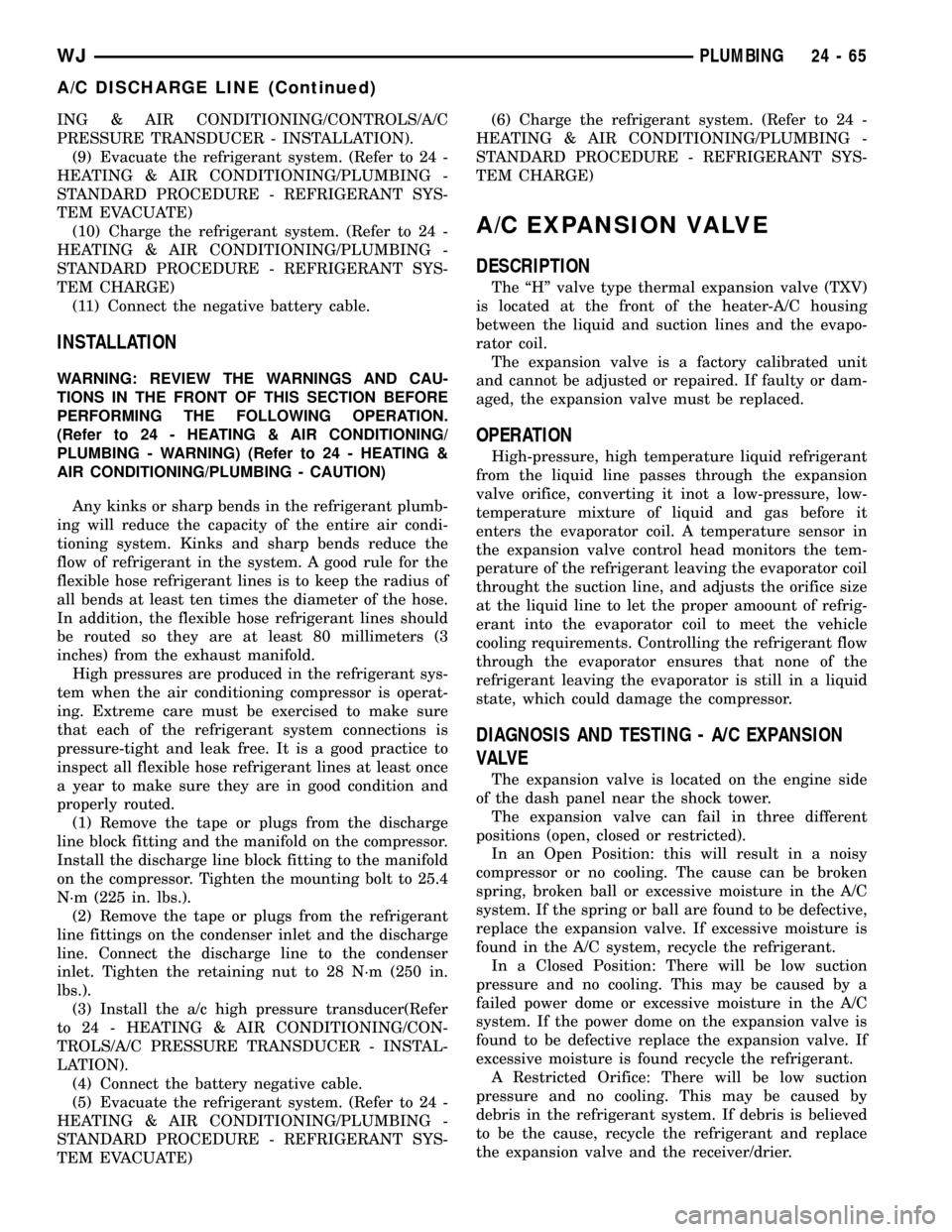
ING & AIR CONDITIONING/CONTROLS/A/C
PRESSURE TRANSDUCER - INSTALLATION).
(9) Evacuate the refrigerant system. (Refer to 24 -
HEATING & AIR CONDITIONING/PLUMBING -
STANDARD PROCEDURE - REFRIGERANT SYS-
TEM EVACUATE)
(10) Charge the refrigerant system. (Refer to 24 -
HEATING & AIR CONDITIONING/PLUMBING -
STANDARD PROCEDURE - REFRIGERANT SYS-
TEM CHARGE)
(11) Connect the negative battery cable.
INSTALLATION
WARNING: REVIEW THE WARNINGS AND CAU-
TIONS IN THE FRONT OF THIS SECTION BEFORE
PERFORMING THE FOLLOWING OPERATION.
(Refer to 24 - HEATING & AIR CONDITIONING/
PLUMBING - WARNING) (Refer to 24 - HEATING &
AIR CONDITIONING/PLUMBING - CAUTION)
Any kinks or sharp bends in the refrigerant plumb-
ing will reduce the capacity of the entire air condi-
tioning system. Kinks and sharp bends reduce the
flow of refrigerant in the system. A good rule for the
flexible hose refrigerant lines is to keep the radius of
all bends at least ten times the diameter of the hose.
In addition, the flexible hose refrigerant lines should
be routed so they are at least 80 millimeters (3
inches) from the exhaust manifold.
High pressures are produced in the refrigerant sys-
tem when the air conditioning compressor is operat-
ing. Extreme care must be exercised to make sure
that each of the refrigerant system connections is
pressure-tight and leak free. It is a good practice to
inspect all flexible hose refrigerant lines at least once
a year to make sure they are in good condition and
properly routed.
(1) Remove the tape or plugs from the discharge
line block fitting and the manifold on the compressor.
Install the discharge line block fitting to the manifold
on the compressor. Tighten the mounting bolt to 25.4
N´m (225 in. lbs.).
(2) Remove the tape or plugs from the refrigerant
line fittings on the condenser inlet and the discharge
line. Connect the discharge line to the condenser
inlet. Tighten the retaining nut to 28 N´m (250 in.
lbs.).
(3) Install the a/c high pressure transducer(Refer
to 24 - HEATING & AIR CONDITIONING/CON-
TROLS/A/C PRESSURE TRANSDUCER - INSTAL-
LATION).
(4) Connect the battery negative cable.
(5) Evacuate the refrigerant system. (Refer to 24 -
HEATING & AIR CONDITIONING/PLUMBING -
STANDARD PROCEDURE - REFRIGERANT SYS-
TEM EVACUATE)(6) Charge the refrigerant system. (Refer to 24 -
HEATING & AIR CONDITIONING/PLUMBING -
STANDARD PROCEDURE - REFRIGERANT SYS-
TEM CHARGE)
A/C EXPANSION VALVE
DESCRIPTION
The ªHº valve type thermal expansion valve (TXV)
is located at the front of the heater-A/C housing
between the liquid and suction lines and the evapo-
rator coil.
The expansion valve is a factory calibrated unit
and cannot be adjusted or repaired. If faulty or dam-
aged, the expansion valve must be replaced.
OPERATION
High-pressure, high temperature liquid refrigerant
from the liquid line passes through the expansion
valve orifice, converting it inot a low-pressure, low-
temperature mixture of liquid and gas before it
enters the evaporator coil. A temperature sensor in
the expansion valve control head monitors the tem-
perature of the refrigerant leaving the evaporator coil
throught the suction line, and adjusts the orifice size
at the liquid line to let the proper amoount of refrig-
erant into the evaporator coil to meet the vehicle
cooling requirements. Controlling the refrigerant flow
through the evaporator ensures that none of the
refrigerant leaving the evaporator is still in a liquid
state, which could damage the compressor.
DIAGNOSIS AND TESTING - A/C EXPANSION
VALVE
The expansion valve is located on the engine side
of the dash panel near the shock tower.
The expansion valve can fail in three different
positions (open, closed or restricted).
In an Open Position: this will result in a noisy
compressor or no cooling. The cause can be broken
spring, broken ball or excessive moisture in the A/C
system. If the spring or ball are found to be defective,
replace the expansion valve. If excessive moisture is
found in the A/C system, recycle the refrigerant.
In a Closed Position: There will be low suction
pressure and no cooling. This may be caused by a
failed power dome or excessive moisture in the A/C
system. If the power dome on the expansion valve is
found to be defective replace the expansion valve. If
excessive moisture is found recycle the refrigerant.
A Restricted Orifice: There will be low suction
pressure and no cooling. This may be caused by
debris in the refrigerant system. If debris is believed
to be the cause, recycle the refrigerant and replace
the expansion valve and the receiver/drier.
WJPLUMBING 24 - 65
A/C DISCHARGE LINE (Continued)