4.7 v8 engine JEEP GRAND CHEROKEE 2003 WJ / 2.G Service Manual
[x] Cancel search | Manufacturer: JEEP, Model Year: 2003, Model line: GRAND CHEROKEE, Model: JEEP GRAND CHEROKEE 2003 WJ / 2.GPages: 2199, PDF Size: 76.01 MB
Page 351 of 2199
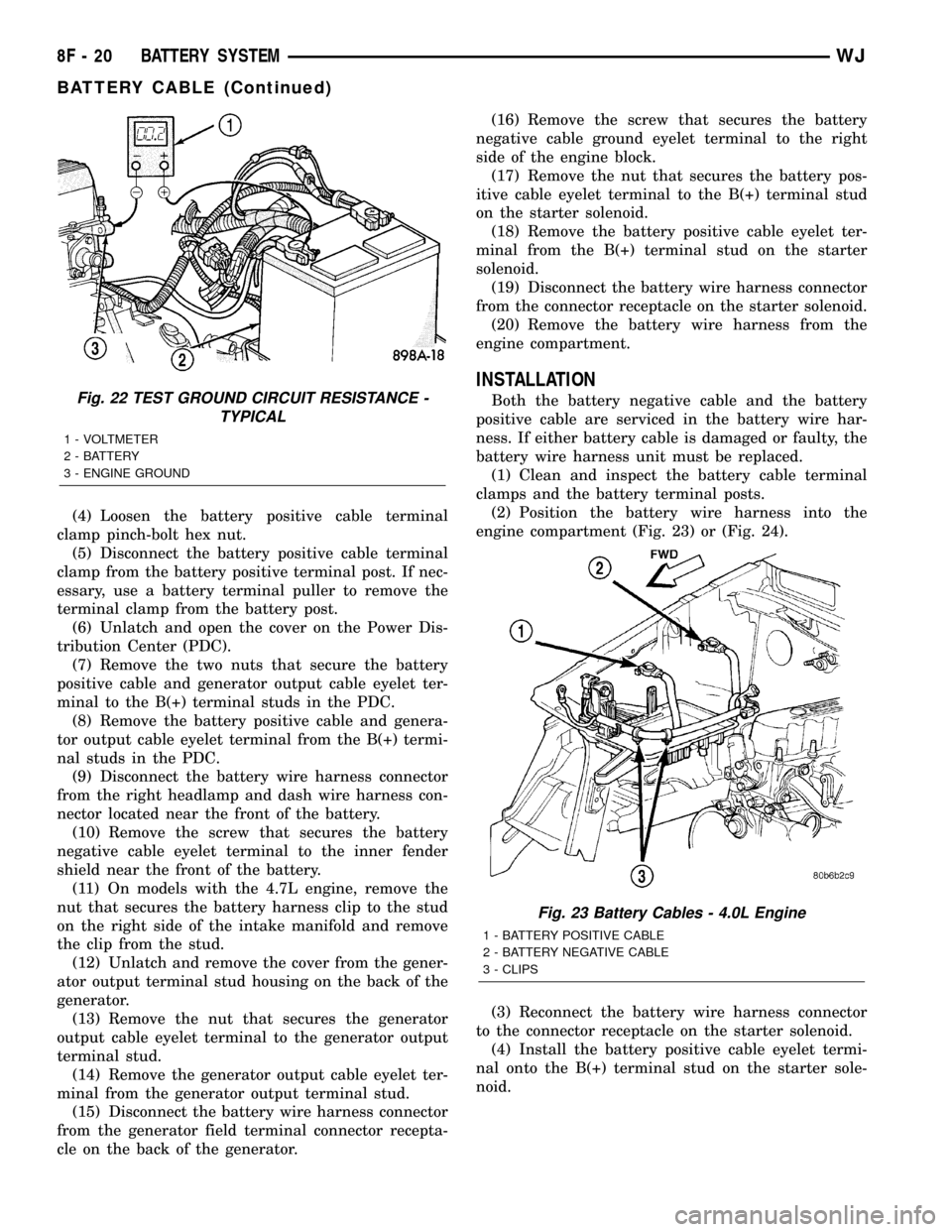
(4) Loosen the battery positive cable terminal
clamp pinch-bolt hex nut.
(5) Disconnect the battery positive cable terminal
clamp from the battery positive terminal post. If nec-
essary, use a battery terminal puller to remove the
terminal clamp from the battery post.
(6) Unlatch and open the cover on the Power Dis-
tribution Center (PDC).
(7) Remove the two nuts that secure the battery
positive cable and generator output cable eyelet ter-
minal to the B(+) terminal studs in the PDC.
(8) Remove the battery positive cable and genera-
tor output cable eyelet terminal from the B(+) termi-
nal studs in the PDC.
(9) Disconnect the battery wire harness connector
from the right headlamp and dash wire harness con-
nector located near the front of the battery.
(10) Remove the screw that secures the battery
negative cable eyelet terminal to the inner fender
shield near the front of the battery.
(11) On models with the 4.7L engine, remove the
nut that secures the battery harness clip to the stud
on the right side of the intake manifold and remove
the clip from the stud.
(12) Unlatch and remove the cover from the gener-
ator output terminal stud housing on the back of the
generator.
(13) Remove the nut that secures the generator
output cable eyelet terminal to the generator output
terminal stud.
(14) Remove the generator output cable eyelet ter-
minal from the generator output terminal stud.
(15) Disconnect the battery wire harness connector
from the generator field terminal connector recepta-
cle on the back of the generator.(16) Remove the screw that secures the battery
negative cable ground eyelet terminal to the right
side of the engine block.
(17) Remove the nut that secures the battery pos-
itive cable eyelet terminal to the B(+) terminal stud
on the starter solenoid.
(18) Remove the battery positive cable eyelet ter-
minal from the B(+) terminal stud on the starter
solenoid.
(19) Disconnect the battery wire harness connector
from the connector receptacle on the starter solenoid.
(20) Remove the battery wire harness from the
engine compartment.
INSTALLATION
Both the battery negative cable and the battery
positive cable are serviced in the battery wire har-
ness. If either battery cable is damaged or faulty, the
battery wire harness unit must be replaced.
(1) Clean and inspect the battery cable terminal
clamps and the battery terminal posts.
(2) Position the battery wire harness into the
engine compartment (Fig. 23) or (Fig. 24).
(3) Reconnect the battery wire harness connector
to the connector receptacle on the starter solenoid.
(4) Install the battery positive cable eyelet termi-
nal onto the B(+) terminal stud on the starter sole-
noid.Fig. 22 TEST GROUND CIRCUIT RESISTANCE -
TYPICAL
1 - VOLTMETER
2 - BATTERY
3 - ENGINE GROUND
Fig. 23 Battery Cables - 4.0L Engine
1 - BATTERY POSITIVE CABLE
2 - BATTERY NEGATIVE CABLE
3 - CLIPS
8F - 20 BATTERY SYSTEMWJ
BATTERY CABLE (Continued)
Page 352 of 2199
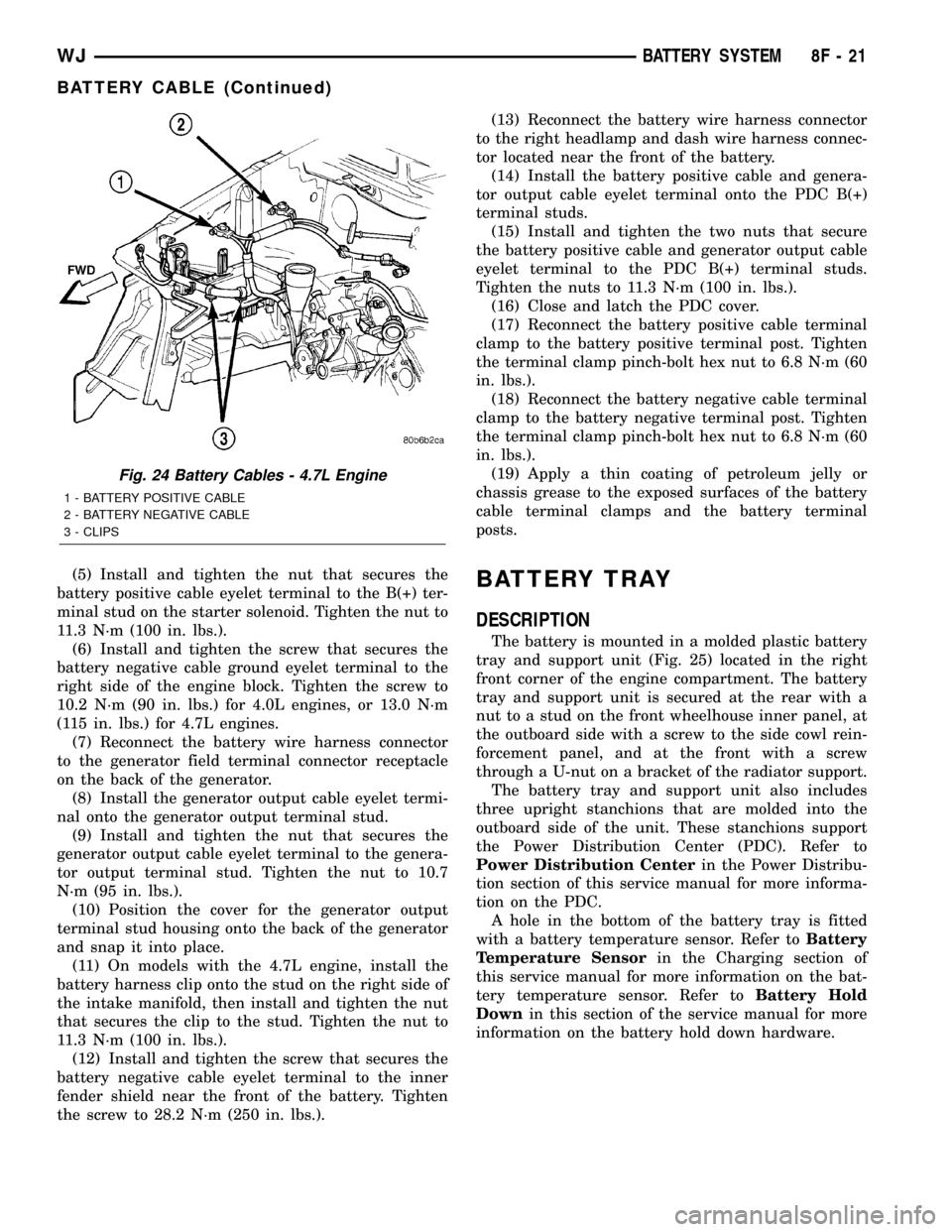
(5) Install and tighten the nut that secures the
battery positive cable eyelet terminal to the B(+) ter-
minal stud on the starter solenoid. Tighten the nut to
11.3 N´m (100 in. lbs.).
(6) Install and tighten the screw that secures the
battery negative cable ground eyelet terminal to the
right side of the engine block. Tighten the screw to
10.2 N´m (90 in. lbs.) for 4.0L engines, or 13.0 N´m
(115 in. lbs.) for 4.7L engines.
(7) Reconnect the battery wire harness connector
to the generator field terminal connector receptacle
on the back of the generator.
(8) Install the generator output cable eyelet termi-
nal onto the generator output terminal stud.
(9) Install and tighten the nut that secures the
generator output cable eyelet terminal to the genera-
tor output terminal stud. Tighten the nut to 10.7
N´m (95 in. lbs.).
(10) Position the cover for the generator output
terminal stud housing onto the back of the generator
and snap it into place.
(11) On models with the 4.7L engine, install the
battery harness clip onto the stud on the right side of
the intake manifold, then install and tighten the nut
that secures the clip to the stud. Tighten the nut to
11.3 N´m (100 in. lbs.).
(12) Install and tighten the screw that secures the
battery negative cable eyelet terminal to the inner
fender shield near the front of the battery. Tighten
the screw to 28.2 N´m (250 in. lbs.).(13) Reconnect the battery wire harness connector
to the right headlamp and dash wire harness connec-
tor located near the front of the battery.
(14) Install the battery positive cable and genera-
tor output cable eyelet terminal onto the PDC B(+)
terminal studs.
(15) Install and tighten the two nuts that secure
the battery positive cable and generator output cable
eyelet terminal to the PDC B(+) terminal studs.
Tighten the nuts to 11.3 N´m (100 in. lbs.).
(16) Close and latch the PDC cover.
(17) Reconnect the battery positive cable terminal
clamp to the battery positive terminal post. Tighten
the terminal clamp pinch-bolt hex nut to 6.8 N´m (60
in. lbs.).
(18) Reconnect the battery negative cable terminal
clamp to the battery negative terminal post. Tighten
the terminal clamp pinch-bolt hex nut to 6.8 N´m (60
in. lbs.).
(19) Apply a thin coating of petroleum jelly or
chassis grease to the exposed surfaces of the battery
cable terminal clamps and the battery terminal
posts.BATTERY TRAY
DESCRIPTION
The battery is mounted in a molded plastic battery
tray and support unit (Fig. 25) located in the right
front corner of the engine compartment. The battery
tray and support unit is secured at the rear with a
nut to a stud on the front wheelhouse inner panel, at
the outboard side with a screw to the side cowl rein-
forcement panel, and at the front with a screw
through a U-nut on a bracket of the radiator support.
The battery tray and support unit also includes
three upright stanchions that are molded into the
outboard side of the unit. These stanchions support
the Power Distribution Center (PDC). Refer to
Power Distribution Centerin the Power Distribu-
tion section of this service manual for more informa-
tion on the PDC.
A hole in the bottom of the battery tray is fitted
with a battery temperature sensor. Refer toBattery
Temperature Sensorin the Charging section of
this service manual for more information on the bat-
tery temperature sensor. Refer toBattery Hold
Downin this section of the service manual for more
information on the battery hold down hardware.
Fig. 24 Battery Cables - 4.7L Engine
1 - BATTERY POSITIVE CABLE
2 - BATTERY NEGATIVE CABLE
3 - CLIPS
WJBATTERY SYSTEM 8F - 21
BATTERY CABLE (Continued)
Page 356 of 2199
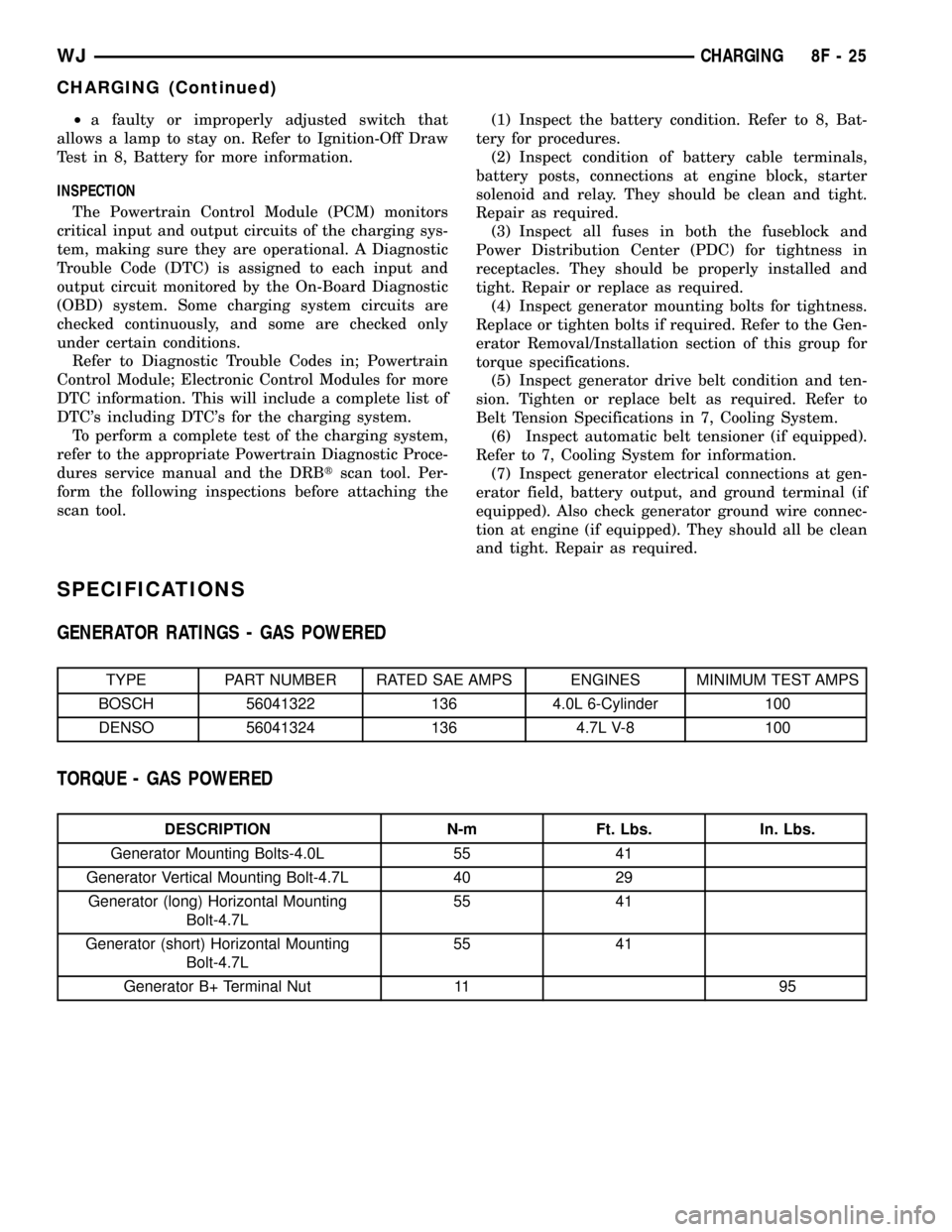
²a faulty or improperly adjusted switch that
allows a lamp to stay on. Refer to Ignition-Off Draw
Test in 8, Battery for more information.
INSPECTION
The Powertrain Control Module (PCM) monitors
critical input and output circuits of the charging sys-
tem, making sure they are operational. A Diagnostic
Trouble Code (DTC) is assigned to each input and
output circuit monitored by the On-Board Diagnostic
(OBD) system. Some charging system circuits are
checked continuously, and some are checked only
under certain conditions.
Refer to Diagnostic Trouble Codes in; Powertrain
Control Module; Electronic Control Modules for more
DTC information. This will include a complete list of
DTC's including DTC's for the charging system.
To perform a complete test of the charging system,
refer to the appropriate Powertrain Diagnostic Proce-
dures service manual and the DRBtscan tool. Per-
form the following inspections before attaching the
scan tool.(1) Inspect the battery condition. Refer to 8, Bat-
tery for procedures.
(2) Inspect condition of battery cable terminals,
battery posts, connections at engine block, starter
solenoid and relay. They should be clean and tight.
Repair as required.
(3) Inspect all fuses in both the fuseblock and
Power Distribution Center (PDC) for tightness in
receptacles. They should be properly installed and
tight. Repair or replace as required.
(4) Inspect generator mounting bolts for tightness.
Replace or tighten bolts if required. Refer to the Gen-
erator Removal/Installation section of this group for
torque specifications.
(5) Inspect generator drive belt condition and ten-
sion. Tighten or replace belt as required. Refer to
Belt Tension Specifications in 7, Cooling System.
(6) Inspect automatic belt tensioner (if equipped).
Refer to 7, Cooling System for information.
(7) Inspect generator electrical connections at gen-
erator field, battery output, and ground terminal (if
equipped). Also check generator ground wire connec-
tion at engine (if equipped). They should all be clean
and tight. Repair as required.
SPECIFICATIONS
GENERATOR RATINGS - GAS POWERED
TYPE PART NUMBER RATED SAE AMPS ENGINES MINIMUM TEST AMPS
BOSCH 56041322 136 4.0L 6-Cylinder 100
DENSO 56041324 136 4.7L V-8 100
TORQUE - GAS POWERED
DESCRIPTION N-m Ft. Lbs. In. Lbs.
Generator Mounting Bolts-4.0L 55 41
Generator Vertical Mounting Bolt-4.7L 40 29
Generator (long) Horizontal Mounting
Bolt-4.7L55 41
Generator (short) Horizontal Mounting
Bolt-4.7L55 41
Generator B+ Terminal Nut 11 95
WJCHARGING 8F - 25
CHARGING (Continued)
Page 358 of 2199
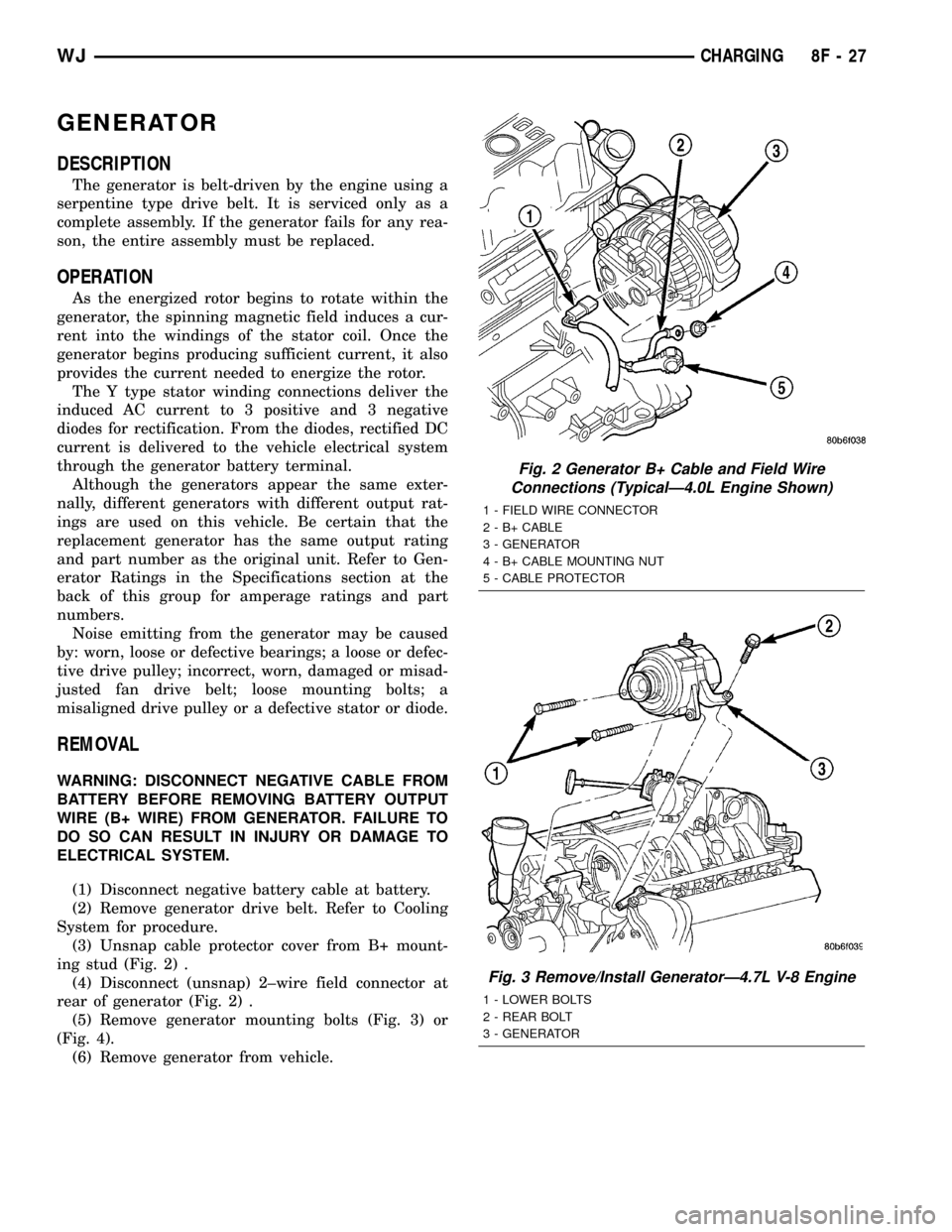
GENERATOR
DESCRIPTION
The generator is belt-driven by the engine using a
serpentine type drive belt. It is serviced only as a
complete assembly. If the generator fails for any rea-
son, the entire assembly must be replaced.
OPERATION
As the energized rotor begins to rotate within the
generator, the spinning magnetic field induces a cur-
rent into the windings of the stator coil. Once the
generator begins producing sufficient current, it also
provides the current needed to energize the rotor.
The Y type stator winding connections deliver the
induced AC current to 3 positive and 3 negative
diodes for rectification. From the diodes, rectified DC
current is delivered to the vehicle electrical system
through the generator battery terminal.
Although the generators appear the same exter-
nally, different generators with different output rat-
ings are used on this vehicle. Be certain that the
replacement generator has the same output rating
and part number as the original unit. Refer to Gen-
erator Ratings in the Specifications section at the
back of this group for amperage ratings and part
numbers.
Noise emitting from the generator may be caused
by: worn, loose or defective bearings; a loose or defec-
tive drive pulley; incorrect, worn, damaged or misad-
justed fan drive belt; loose mounting bolts; a
misaligned drive pulley or a defective stator or diode.
REMOVAL
WARNING: DISCONNECT NEGATIVE CABLE FROM
BATTERY BEFORE REMOVING BATTERY OUTPUT
WIRE (B+ WIRE) FROM GENERATOR. FAILURE TO
DO SO CAN RESULT IN INJURY OR DAMAGE TO
ELECTRICAL SYSTEM.
(1) Disconnect negative battery cable at battery.
(2) Remove generator drive belt. Refer to Cooling
System for procedure.
(3) Unsnap cable protector cover from B+ mount-
ing stud (Fig. 2) .
(4) Disconnect (unsnap) 2±wire field connector at
rear of generator (Fig. 2) .
(5) Remove generator mounting bolts (Fig. 3) or
(Fig. 4).
(6) Remove generator from vehicle.
Fig. 2 Generator B+ Cable and Field Wire
Connections (TypicalÐ4.0L Engine Shown)
1 - FIELD WIRE CONNECTOR
2 - B+ CABLE
3 - GENERATOR
4 - B+ CABLE MOUNTING NUT
5 - CABLE PROTECTOR
Fig. 3 Remove/Install GeneratorÐ4.7L V-8 Engine
1 - LOWER BOLTS
2 - REAR BOLT
3 - GENERATOR
WJCHARGING 8F - 27
Page 359 of 2199
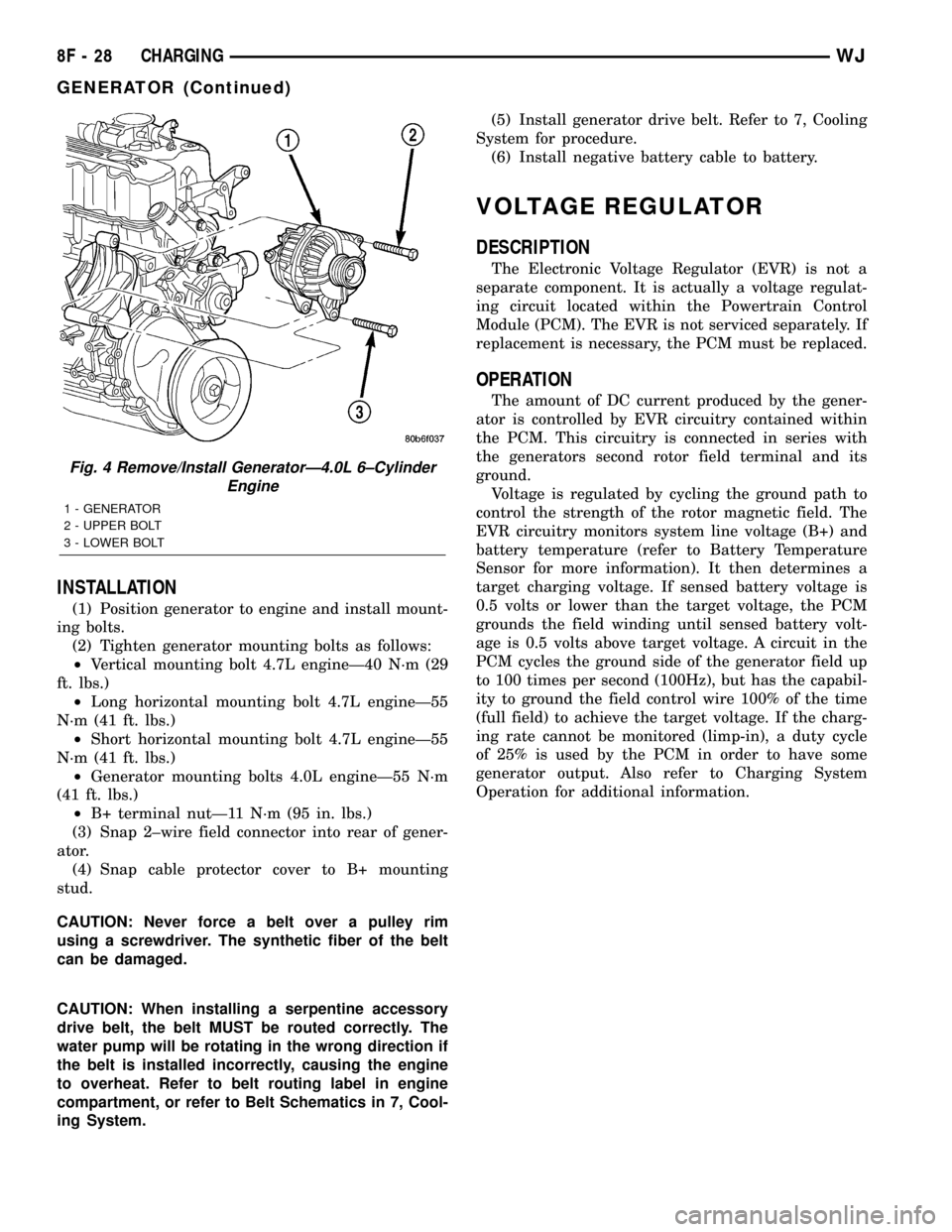
INSTALLATION
(1) Position generator to engine and install mount-
ing bolts.
(2) Tighten generator mounting bolts as follows:
²Vertical mounting bolt 4.7L engineÐ40 N´m (29
ft. lbs.)
²Long horizontal mounting bolt 4.7L engineÐ55
N´m (41 ft. lbs.)
²Short horizontal mounting bolt 4.7L engineÐ55
N´m (41 ft. lbs.)
²Generator mounting bolts 4.0L engineÐ55 N´m
(41 ft. lbs.)
²B+ terminal nutÐ11 N´m (95 in. lbs.)
(3) Snap 2±wire field connector into rear of gener-
ator.
(4) Snap cable protector cover to B+ mounting
stud.
CAUTION: Never force a belt over a pulley rim
using a screwdriver. The synthetic fiber of the belt
can be damaged.
CAUTION: When installing a serpentine accessory
drive belt, the belt MUST be routed correctly. The
water pump will be rotating in the wrong direction if
the belt is installed incorrectly, causing the engine
to overheat. Refer to belt routing label in engine
compartment, or refer to Belt Schematics in 7, Cool-
ing System.(5) Install generator drive belt. Refer to 7, Cooling
System for procedure.
(6) Install negative battery cable to battery.
VOLTAGE REGULATOR
DESCRIPTION
The Electronic Voltage Regulator (EVR) is not a
separate component. It is actually a voltage regulat-
ing circuit located within the Powertrain Control
Module (PCM). The EVR is not serviced separately. If
replacement is necessary, the PCM must be replaced.
OPERATION
The amount of DC current produced by the gener-
ator is controlled by EVR circuitry contained within
the PCM. This circuitry is connected in series with
the generators second rotor field terminal and its
ground.
Voltage is regulated by cycling the ground path to
control the strength of the rotor magnetic field. The
EVR circuitry monitors system line voltage (B+) and
battery temperature (refer to Battery Temperature
Sensor for more information). It then determines a
target charging voltage. If sensed battery voltage is
0.5 volts or lower than the target voltage, the PCM
grounds the field winding until sensed battery volt-
age is 0.5 volts above target voltage. A circuit in the
PCM cycles the ground side of the generator field up
to 100 times per second (100Hz), but has the capabil-
ity to ground the field control wire 100% of the time
(full field) to achieve the target voltage. If the charg-
ing rate cannot be monitored (limp-in), a duty cycle
of 25% is used by the PCM in order to have some
generator output. Also refer to Charging System
Operation for additional information.
Fig. 4 Remove/Install GeneratorÐ4.0L 6±Cylinder
Engine
1 - GENERATOR
2 - UPPER BOLT
3 - LOWER BOLT
8F - 28 CHARGINGWJ
GENERATOR (Continued)
Page 366 of 2199
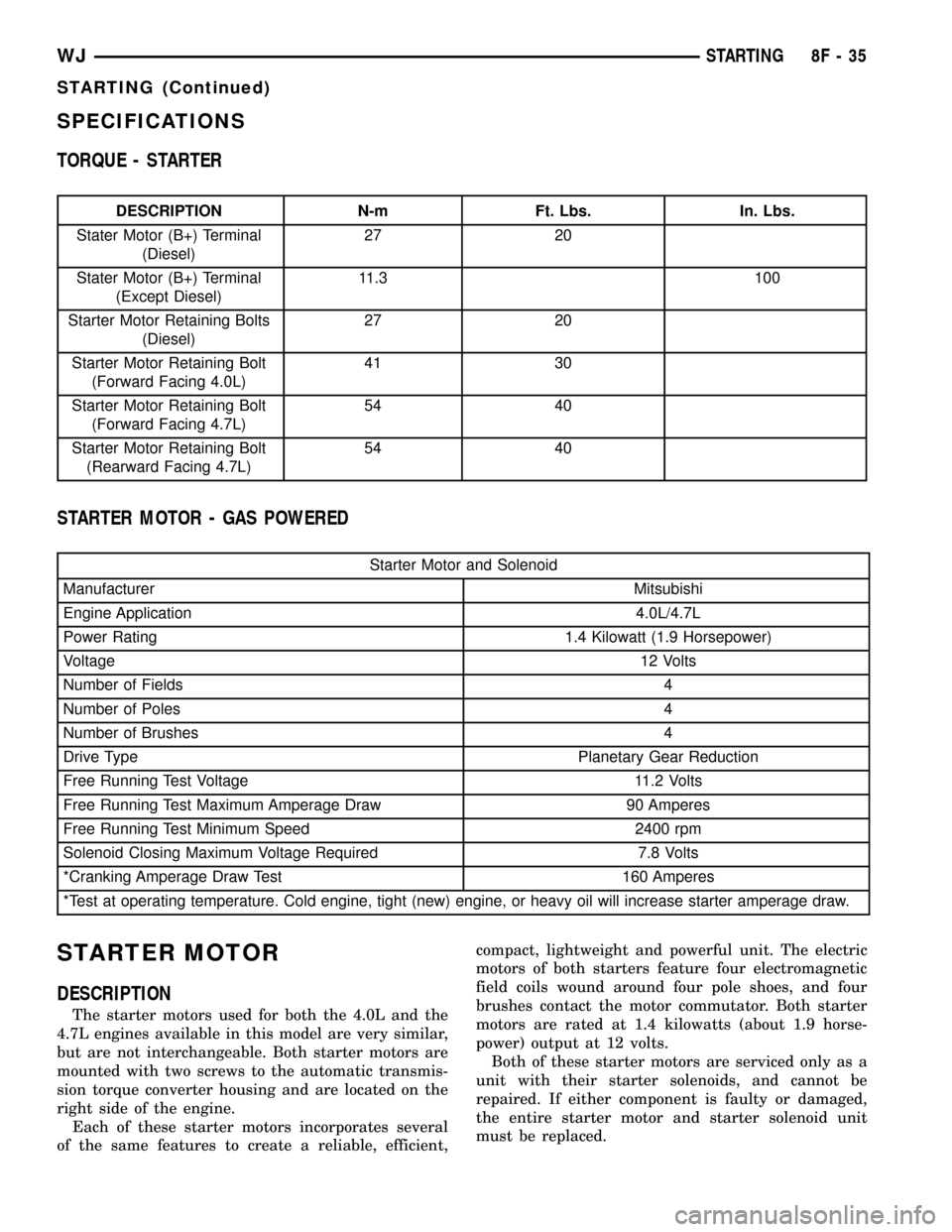
SPECIFICATIONS
TORQUE - STARTER
DESCRIPTION N-m Ft. Lbs. In. Lbs.
Stater Motor (B+) Terminal
(Diesel)27 20
Stater Motor (B+) Terminal
(Except Diesel)11.3 100
Starter Motor Retaining Bolts
(Diesel)27 20
Starter Motor Retaining Bolt
(Forward Facing 4.0L)41 30
Starter Motor Retaining Bolt
(Forward Facing 4.7L)54 40
Starter Motor Retaining Bolt
(Rearward Facing 4.7L)54 40
STARTER MOTOR - GAS POWERED
Starter Motor and Solenoid
Manufacturer Mitsubishi
Engine Application 4.0L/4.7L
Power Rating 1.4 Kilowatt (1.9 Horsepower)
Voltage12 Volts
Number of Fields 4
Number of Poles 4
Number of Brushes 4
Drive Type Planetary Gear Reduction
Free Running Test Voltage 11.2 Volts
Free Running Test Maximum Amperage Draw 90 Amperes
Free Running Test Minimum Speed 2400 rpm
Solenoid Closing Maximum Voltage Required 7.8 Volts
*Cranking Amperage Draw Test 160 Amperes
*Test at operating temperature. Cold engine, tight (new) engine, or heavy oil will increase starter amperage draw.
STARTER MOTOR
DESCRIPTION
The starter motors used for both the 4.0L and the
4.7L engines available in this model are very similar,
but are not interchangeable. Both starter motors are
mounted with two screws to the automatic transmis-
sion torque converter housing and are located on the
right side of the engine.
Each of these starter motors incorporates several
of the same features to create a reliable, efficient,compact, lightweight and powerful unit. The electric
motors of both starters feature four electromagnetic
field coils wound around four pole shoes, and four
brushes contact the motor commutator. Both starter
motors are rated at 1.4 kilowatts (about 1.9 horse-
power) output at 12 volts.
Both of these starter motors are serviced only as a
unit with their starter solenoids, and cannot be
repaired. If either component is faulty or damaged,
the entire starter motor and starter solenoid unit
must be replaced.
WJSTARTING 8F - 35
STARTING (Continued)
Page 368 of 2199
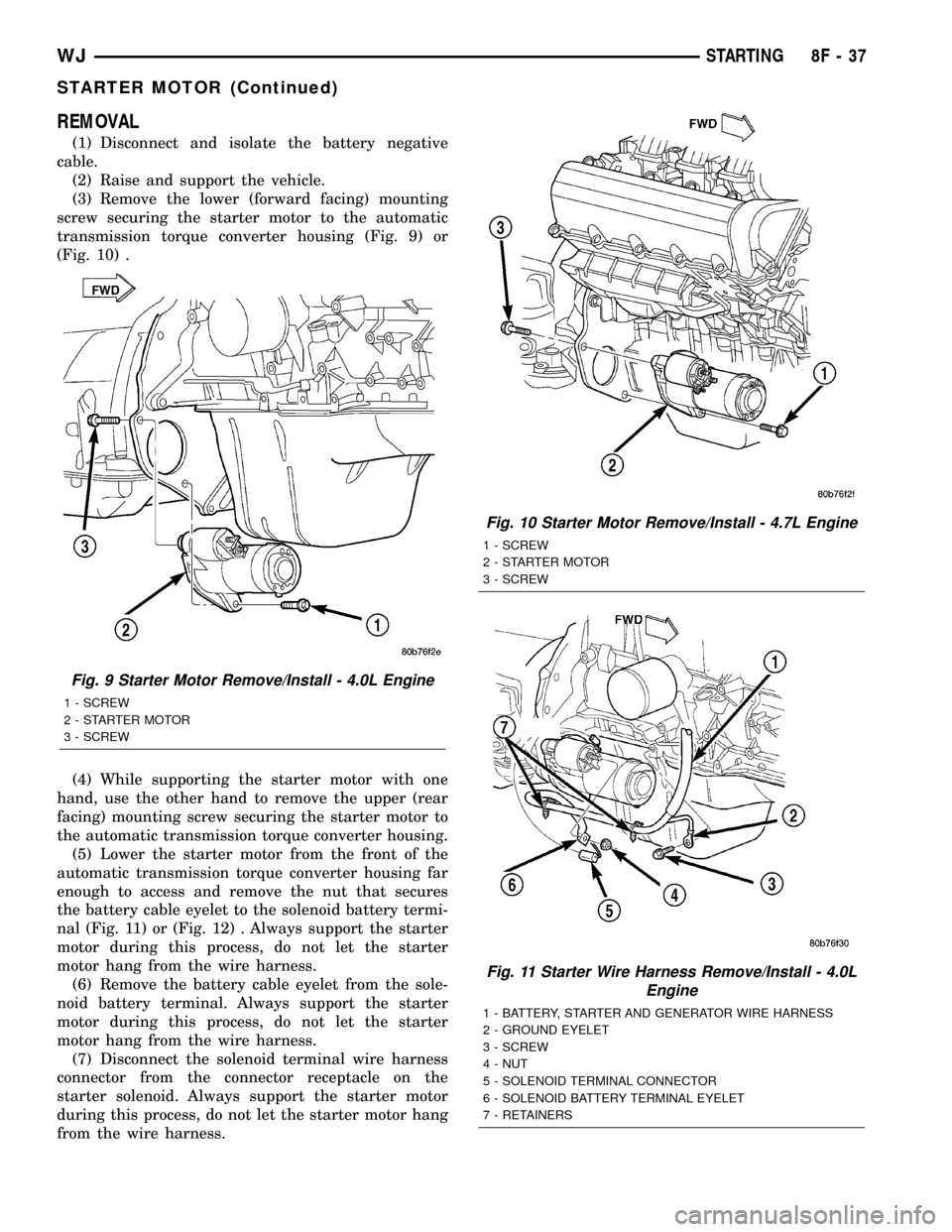
REMOVAL
(1) Disconnect and isolate the battery negative
cable.
(2) Raise and support the vehicle.
(3) Remove the lower (forward facing) mounting
screw securing the starter motor to the automatic
transmission torque converter housing (Fig. 9) or
(Fig. 10) .
(4) While supporting the starter motor with one
hand, use the other hand to remove the upper (rear
facing) mounting screw securing the starter motor to
the automatic transmission torque converter housing.
(5) Lower the starter motor from the front of the
automatic transmission torque converter housing far
enough to access and remove the nut that secures
the battery cable eyelet to the solenoid battery termi-
nal (Fig. 11) or (Fig. 12) . Always support the starter
motor during this process, do not let the starter
motor hang from the wire harness.
(6) Remove the battery cable eyelet from the sole-
noid battery terminal. Always support the starter
motor during this process, do not let the starter
motor hang from the wire harness.
(7) Disconnect the solenoid terminal wire harness
connector from the connector receptacle on the
starter solenoid. Always support the starter motor
during this process, do not let the starter motor hang
from the wire harness.
Fig. 9 Starter Motor Remove/Install - 4.0L Engine
1 - SCREW
2 - STARTER MOTOR
3 - SCREW
Fig. 10 Starter Motor Remove/Install - 4.7L Engine
1 - SCREW
2 - STARTER MOTOR
3 - SCREW
Fig. 11 Starter Wire Harness Remove/Install - 4.0L
Engine
1 - BATTERY, STARTER AND GENERATOR WIRE HARNESS
2 - GROUND EYELET
3 - SCREW
4 - NUT
5 - SOLENOID TERMINAL CONNECTOR
6 - SOLENOID BATTERY TERMINAL EYELET
7 - RETAINERS
WJSTARTING 8F - 37
STARTER MOTOR (Continued)
Page 369 of 2199
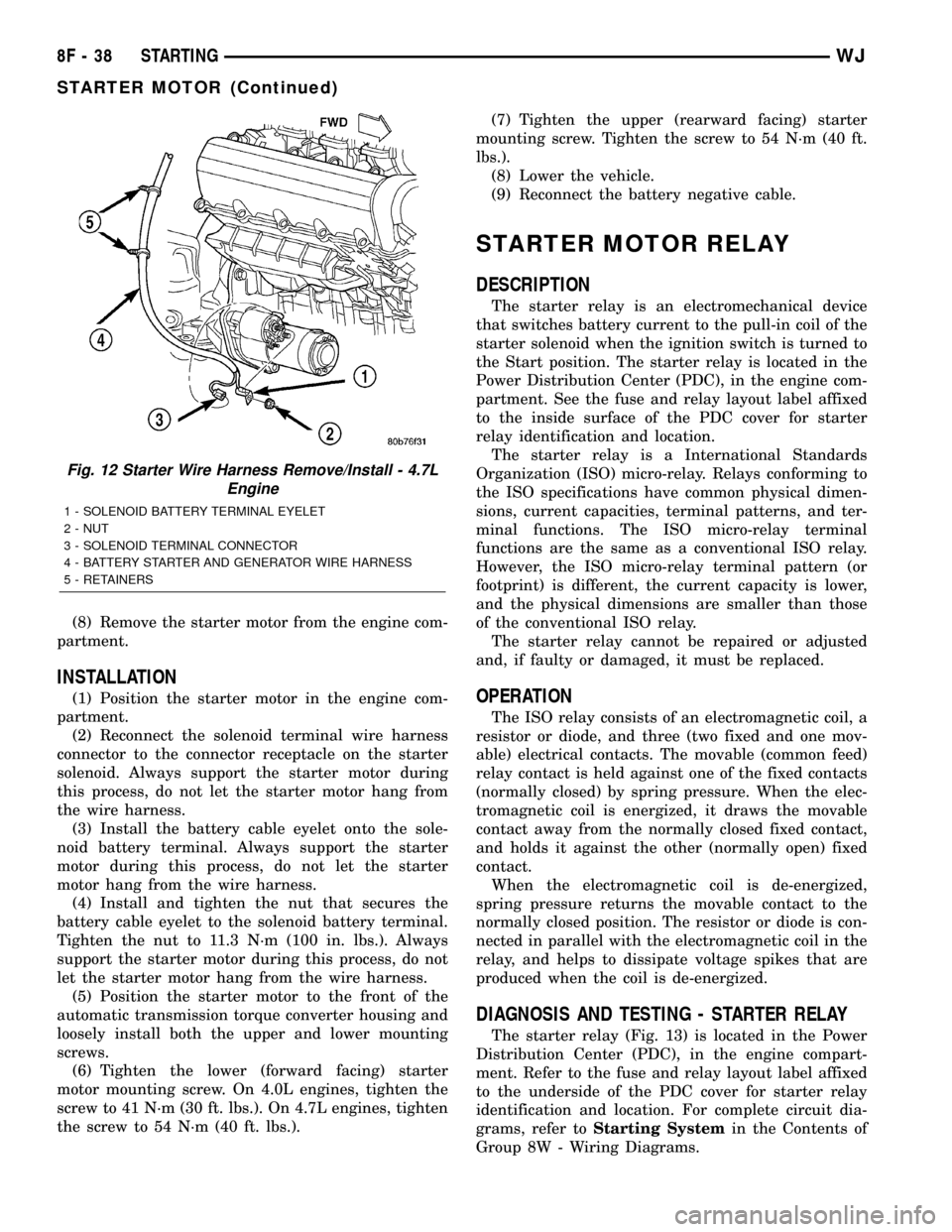
(8) Remove the starter motor from the engine com-
partment.
INSTALLATION
(1) Position the starter motor in the engine com-
partment.
(2) Reconnect the solenoid terminal wire harness
connector to the connector receptacle on the starter
solenoid. Always support the starter motor during
this process, do not let the starter motor hang from
the wire harness.
(3) Install the battery cable eyelet onto the sole-
noid battery terminal. Always support the starter
motor during this process, do not let the starter
motor hang from the wire harness.
(4) Install and tighten the nut that secures the
battery cable eyelet to the solenoid battery terminal.
Tighten the nut to 11.3 N´m (100 in. lbs.). Always
support the starter motor during this process, do not
let the starter motor hang from the wire harness.
(5) Position the starter motor to the front of the
automatic transmission torque converter housing and
loosely install both the upper and lower mounting
screws.
(6) Tighten the lower (forward facing) starter
motor mounting screw. On 4.0L engines, tighten the
screw to 41 N´m (30 ft. lbs.). On 4.7L engines, tighten
the screw to 54 N´m (40 ft. lbs.).(7) Tighten the upper (rearward facing) starter
mounting screw. Tighten the screw to 54 N´m (40 ft.
lbs.).
(8) Lower the vehicle.
(9) Reconnect the battery negative cable.
STARTER MOTOR RELAY
DESCRIPTION
The starter relay is an electromechanical device
that switches battery current to the pull-in coil of the
starter solenoid when the ignition switch is turned to
the Start position. The starter relay is located in the
Power Distribution Center (PDC), in the engine com-
partment. See the fuse and relay layout label affixed
to the inside surface of the PDC cover for starter
relay identification and location.
The starter relay is a International Standards
Organization (ISO) micro-relay. Relays conforming to
the ISO specifications have common physical dimen-
sions, current capacities, terminal patterns, and ter-
minal functions. The ISO micro-relay terminal
functions are the same as a conventional ISO relay.
However, the ISO micro-relay terminal pattern (or
footprint) is different, the current capacity is lower,
and the physical dimensions are smaller than those
of the conventional ISO relay.
The starter relay cannot be repaired or adjusted
and, if faulty or damaged, it must be replaced.
OPERATION
The ISO relay consists of an electromagnetic coil, a
resistor or diode, and three (two fixed and one mov-
able) electrical contacts. The movable (common feed)
relay contact is held against one of the fixed contacts
(normally closed) by spring pressure. When the elec-
tromagnetic coil is energized, it draws the movable
contact away from the normally closed fixed contact,
and holds it against the other (normally open) fixed
contact.
When the electromagnetic coil is de-energized,
spring pressure returns the movable contact to the
normally closed position. The resistor or diode is con-
nected in parallel with the electromagnetic coil in the
relay, and helps to dissipate voltage spikes that are
produced when the coil is de-energized.
DIAGNOSIS AND TESTING - STARTER RELAY
The starter relay (Fig. 13) is located in the Power
Distribution Center (PDC), in the engine compart-
ment. Refer to the fuse and relay layout label affixed
to the underside of the PDC cover for starter relay
identification and location. For complete circuit dia-
grams, refer toStarting Systemin the Contents of
Group 8W - Wiring Diagrams.
Fig. 12 Starter Wire Harness Remove/Install - 4.7L
Engine
1 - SOLENOID BATTERY TERMINAL EYELET
2 - NUT
3 - SOLENOID TERMINAL CONNECTOR
4 - BATTERY STARTER AND GENERATOR WIRE HARNESS
5 - RETAINERS
8F - 38 STARTINGWJ
STARTER MOTOR (Continued)
Page 398 of 2199
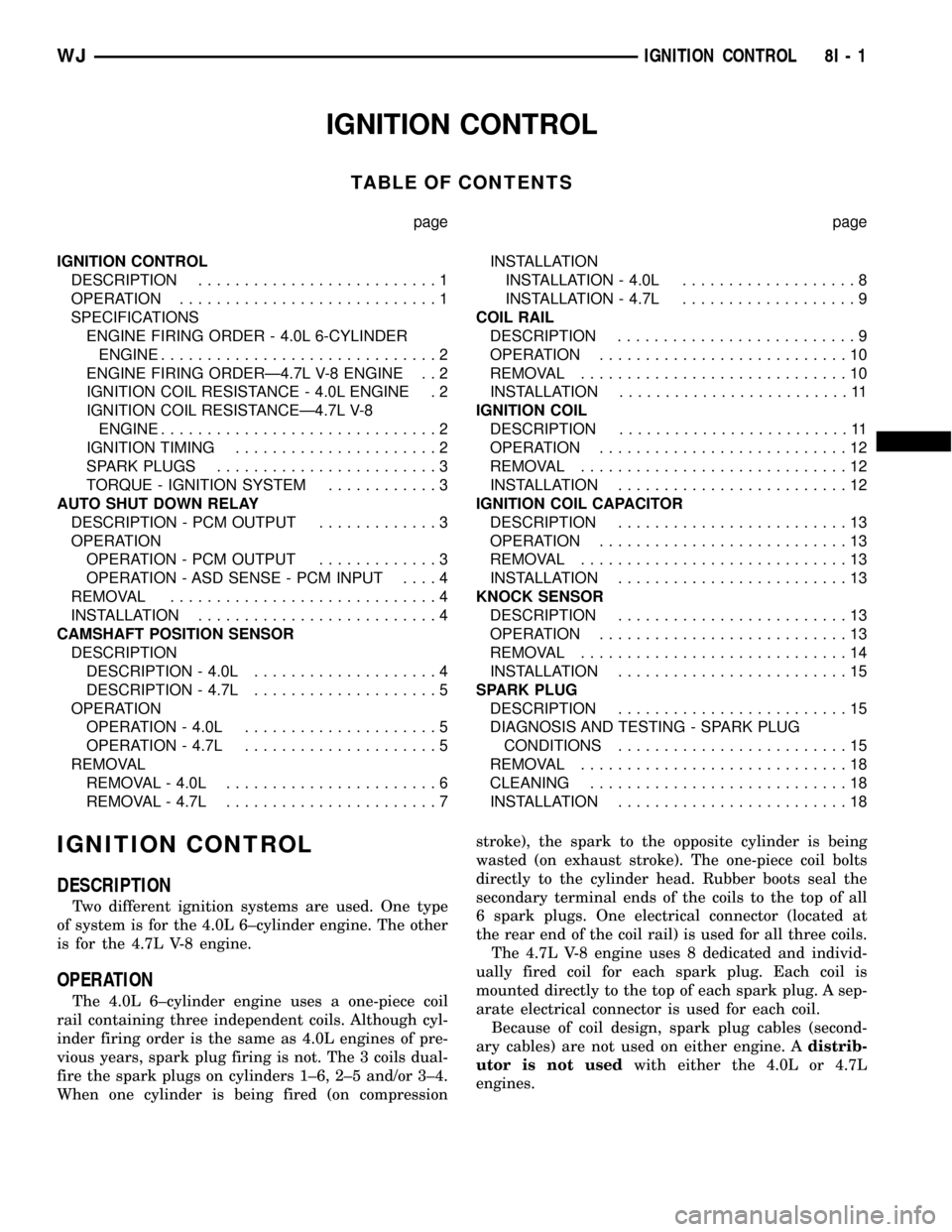
IGNITION CONTROL
TABLE OF CONTENTS
page page
IGNITION CONTROL
DESCRIPTION..........................1
OPERATION............................1
SPECIFICATIONS
ENGINE FIRING ORDER - 4.0L 6-CYLINDER
ENGINE..............................2
ENGINE FIRING ORDERÐ4.7L V-8 ENGINE . . 2
IGNITION COIL RESISTANCE - 4.0L ENGINE . 2
IGNITION COIL RESISTANCEÐ4.7L V-8
ENGINE..............................2
IGNITION TIMING......................2
SPARK PLUGS........................3
TORQUE - IGNITION SYSTEM............3
AUTO SHUT DOWN RELAY
DESCRIPTION - PCM OUTPUT.............3
OPERATION
OPERATION - PCM OUTPUT.............3
OPERATION - ASD SENSE - PCM INPUT....4
REMOVAL.............................4
INSTALLATION..........................4
CAMSHAFT POSITION SENSOR
DESCRIPTION
DESCRIPTION - 4.0L....................4
DESCRIPTION - 4.7L....................5
OPERATION
OPERATION - 4.0L.....................5
OPERATION - 4.7L.....................5
REMOVAL
REMOVAL - 4.0L.......................6
REMOVAL - 4.7L.......................7INSTALLATION
INSTALLATION - 4.0L...................8
INSTALLATION - 4.7L...................9
COIL RAIL
DESCRIPTION..........................9
OPERATION...........................10
REMOVAL.............................10
INSTALLATION.........................11
IGNITION COIL
DESCRIPTION.........................11
OPERATION...........................12
REMOVAL.............................12
INSTALLATION.........................12
IGNITION COIL CAPACITOR
DESCRIPTION.........................13
OPERATION...........................13
REMOVAL.............................13
INSTALLATION.........................13
KNOCK SENSOR
DESCRIPTION.........................13
OPERATION...........................13
REMOVAL.............................14
INSTALLATION.........................15
SPARK PLUG
DESCRIPTION.........................15
DIAGNOSIS AND TESTING - SPARK PLUG
CONDITIONS.........................15
REMOVAL.............................18
CLEANING............................18
INSTALLATION.........................18
IGNITION CONTROL
DESCRIPTION
Two different ignition systems are used. One type
of system is for the 4.0L 6±cylinder engine. The other
is for the 4.7L V-8 engine.
OPERATION
The 4.0L 6±cylinder engine uses a one-piece coil
rail containing three independent coils. Although cyl-
inder firing order is the same as 4.0L engines of pre-
vious years, spark plug firing is not. The 3 coils dual-
fire the spark plugs on cylinders 1±6, 2±5 and/or 3±4.
When one cylinder is being fired (on compressionstroke), the spark to the opposite cylinder is being
wasted (on exhaust stroke). The one-piece coil bolts
directly to the cylinder head. Rubber boots seal the
secondary terminal ends of the coils to the top of all
6 spark plugs. One electrical connector (located at
the rear end of the coil rail) is used for all three coils.
The 4.7L V-8 engine uses 8 dedicated and individ-
ually fired coil for each spark plug. Each coil is
mounted directly to the top of each spark plug. A sep-
arate electrical connector is used for each coil.
Because of coil design, spark plug cables (second-
ary cables) are not used on either engine. Adistrib-
utor is not usedwith either the 4.0L or 4.7L
engines.
WJIGNITION CONTROL 8I - 1
Page 399 of 2199
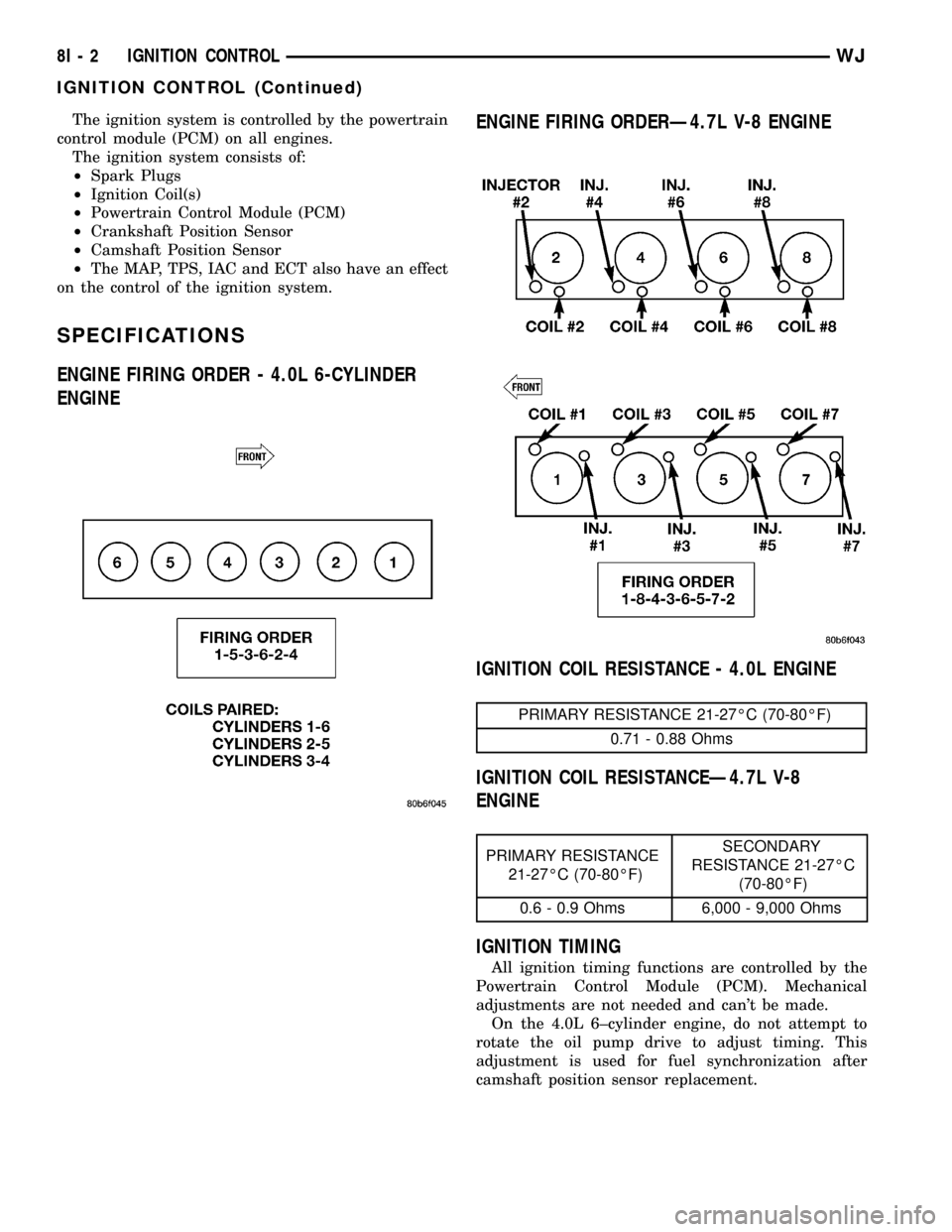
The ignition system is controlled by the powertrain
control module (PCM) on all engines.
The ignition system consists of:
²Spark Plugs
²Ignition Coil(s)
²Powertrain Control Module (PCM)
²Crankshaft Position Sensor
²Camshaft Position Sensor
²The MAP, TPS, IAC and ECT also have an effect
on the control of the ignition system.
SPECIFICATIONS
ENGINE FIRING ORDER - 4.0L 6-CYLINDER
ENGINEENGINE FIRING ORDERÐ4.7L V-8 ENGINE
IGNITION COIL RESISTANCE - 4.0L ENGINE
PRIMARY RESISTANCE 21-27ÉC (70-80ÉF)
0.71 - 0.88 Ohms
IGNITION COIL RESISTANCEÐ4.7L V-8
ENGINE
PRIMARY RESISTANCE
21-27ÉC (70-80ÉF)SECONDARY
RESISTANCE 21-27ÉC
(70-80ÉF)
0.6 - 0.9 Ohms 6,000 - 9,000 Ohms
IGNITION TIMING
All ignition timing functions are controlled by the
Powertrain Control Module (PCM). Mechanical
adjustments are not needed and can't be made.
On the 4.0L 6±cylinder engine, do not attempt to
rotate the oil pump drive to adjust timing. This
adjustment is used for fuel synchronization after
camshaft position sensor replacement.
8I - 2 IGNITION CONTROLWJ
IGNITION CONTROL (Continued)