4.7 v8 engine JEEP GRAND CHEROKEE 2003 WJ / 2.G Repair Manual
[x] Cancel search | Manufacturer: JEEP, Model Year: 2003, Model line: GRAND CHEROKEE, Model: JEEP GRAND CHEROKEE 2003 WJ / 2.GPages: 2199, PDF Size: 76.01 MB
Page 400 of 2199
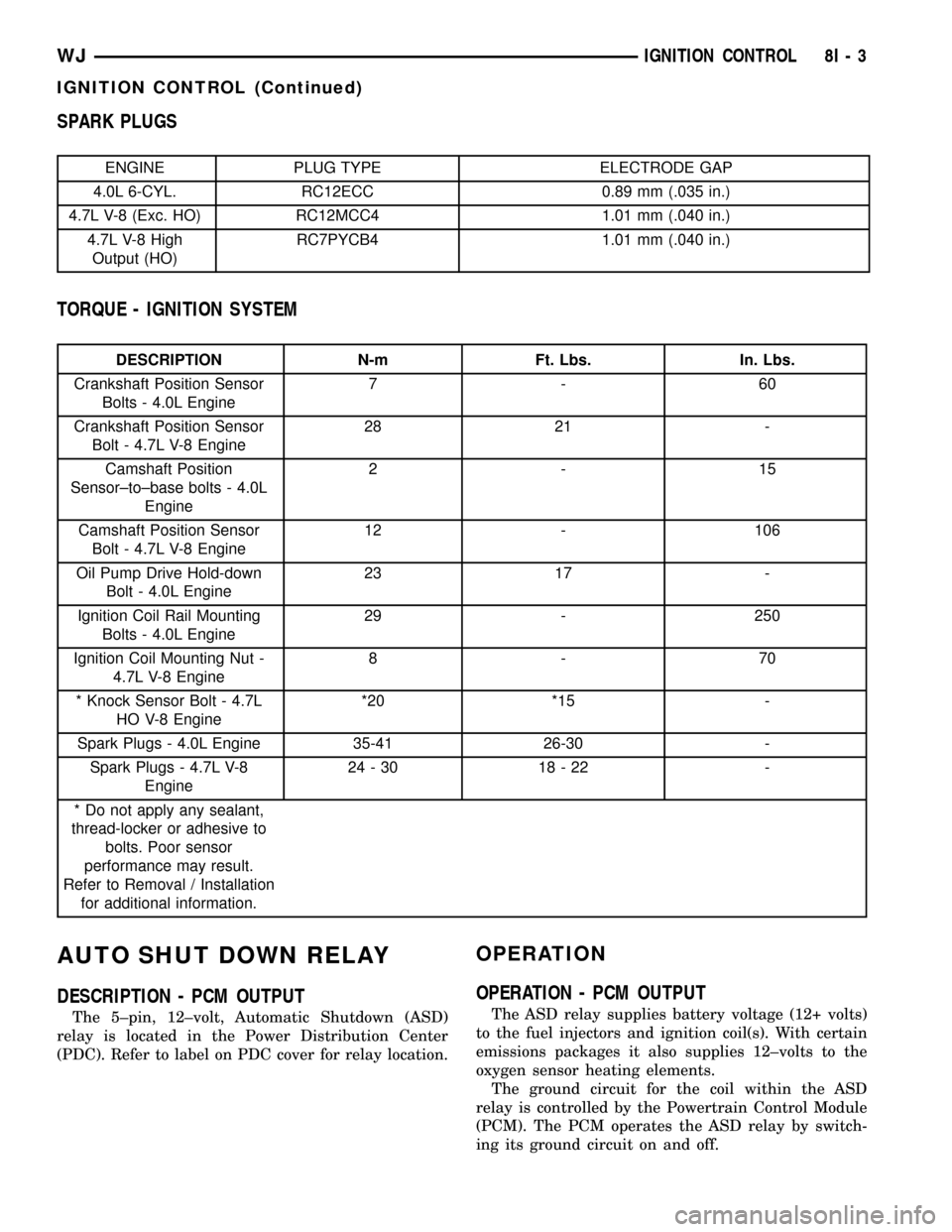
SPARK PLUGS
ENGINE PLUG TYPE ELECTRODE GAP
4.0L 6-CYL. RC12ECC 0.89 mm (.035 in.)
4.7L V-8 (Exc. HO) RC12MCC4 1.01 mm (.040 in.)
4.7L V-8 High
Output (HO)RC7PYCB4 1.01 mm (.040 in.)
TORQUE - IGNITION SYSTEM
DESCRIPTION N-m Ft. Lbs. In. Lbs.
Crankshaft Position Sensor
Bolts - 4.0L Engine7- 60
Crankshaft Position Sensor
Bolt - 4.7L V-8 Engine28 21 -
Camshaft Position
Sensor±to±base bolts - 4.0L
Engine2- 15
Camshaft Position Sensor
Bolt - 4.7L V-8 Engine12 - 106
Oil Pump Drive Hold-down
Bolt - 4.0L Engine23 17 -
Ignition Coil Rail Mounting
Bolts - 4.0L Engine29 - 250
Ignition Coil Mounting Nut -
4.7L V-8 Engine8- 70
* Knock Sensor Bolt - 4.7L
HO V-8 Engine*20 *15 -
Spark Plugs - 4.0L Engine 35-41 26-30 -
Spark Plugs - 4.7L V-8
Engine24-30 18-22 -
* Do not apply any sealant,
thread-locker or adhesive to
bolts. Poor sensor
performance may result.
Refer to Removal / Installation
for additional information.
AUTO SHUT DOWN RELAY
DESCRIPTION - PCM OUTPUT
The 5±pin, 12±volt, Automatic Shutdown (ASD)
relay is located in the Power Distribution Center
(PDC). Refer to label on PDC cover for relay location.
OPERATION
OPERATION - PCM OUTPUT
The ASD relay supplies battery voltage (12+ volts)
to the fuel injectors and ignition coil(s). With certain
emissions packages it also supplies 12±volts to the
oxygen sensor heating elements.
The ground circuit for the coil within the ASD
relay is controlled by the Powertrain Control Module
(PCM). The PCM operates the ASD relay by switch-
ing its ground circuit on and off.
WJIGNITION CONTROL 8I - 3
IGNITION CONTROL (Continued)
Page 402 of 2199
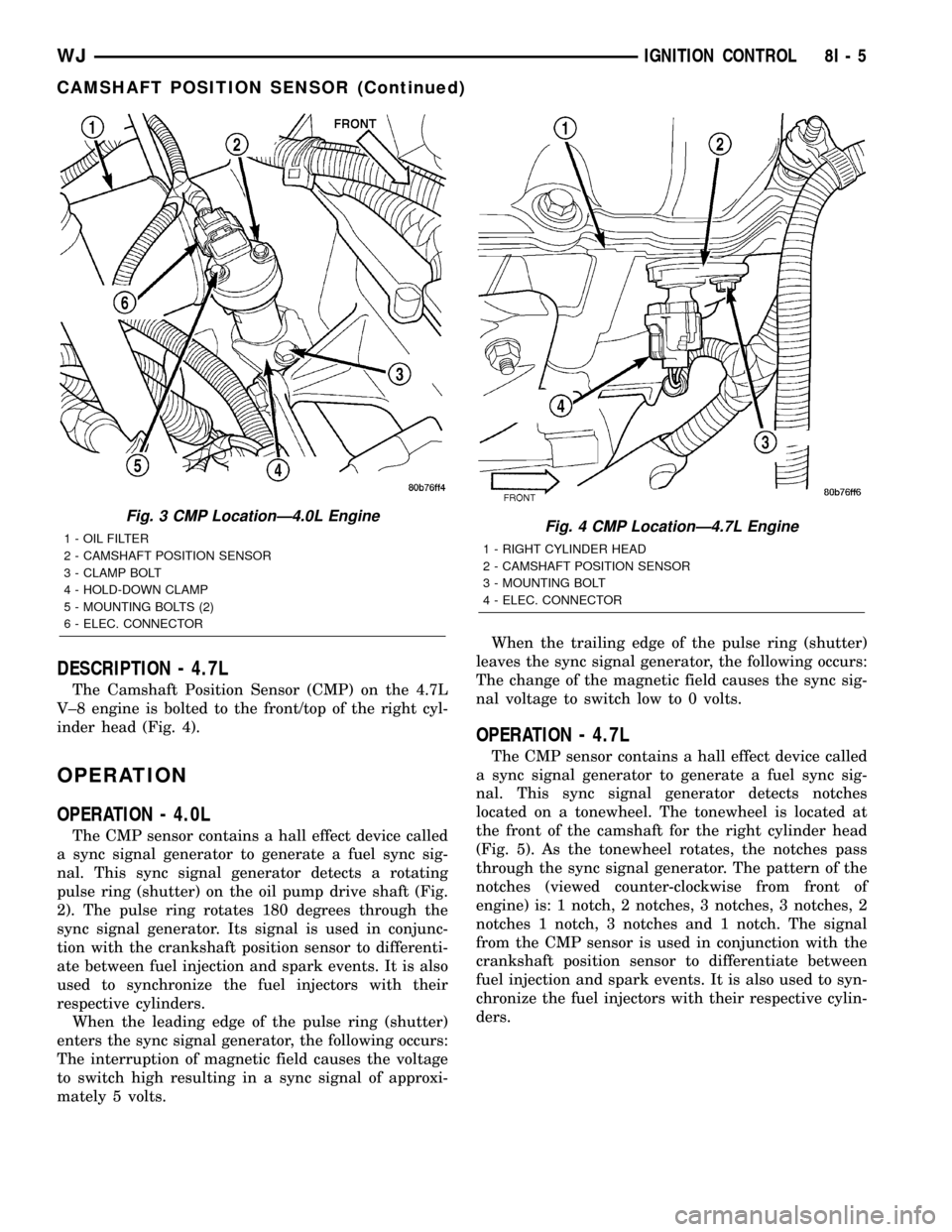
DESCRIPTION - 4.7L
The Camshaft Position Sensor (CMP) on the 4.7L
V±8 engine is bolted to the front/top of the right cyl-
inder head (Fig. 4).
OPERATION
OPERATION - 4.0L
The CMP sensor contains a hall effect device called
a sync signal generator to generate a fuel sync sig-
nal. This sync signal generator detects a rotating
pulse ring (shutter) on the oil pump drive shaft (Fig.
2). The pulse ring rotates 180 degrees through the
sync signal generator. Its signal is used in conjunc-
tion with the crankshaft position sensor to differenti-
ate between fuel injection and spark events. It is also
used to synchronize the fuel injectors with their
respective cylinders.
When the leading edge of the pulse ring (shutter)
enters the sync signal generator, the following occurs:
The interruption of magnetic field causes the voltage
to switch high resulting in a sync signal of approxi-
mately 5 volts.When the trailing edge of the pulse ring (shutter)
leaves the sync signal generator, the following occurs:
The change of the magnetic field causes the sync sig-
nal voltage to switch low to 0 volts.
OPERATION - 4.7L
The CMP sensor contains a hall effect device called
a sync signal generator to generate a fuel sync sig-
nal. This sync signal generator detects notches
located on a tonewheel. The tonewheel is located at
the front of the camshaft for the right cylinder head
(Fig. 5). As the tonewheel rotates, the notches pass
through the sync signal generator. The pattern of the
notches (viewed counter-clockwise from front of
engine) is: 1 notch, 2 notches, 3 notches, 3 notches, 2
notches 1 notch, 3 notches and 1 notch. The signal
from the CMP sensor is used in conjunction with the
crankshaft position sensor to differentiate between
fuel injection and spark events. It is also used to syn-
chronize the fuel injectors with their respective cylin-
ders.
Fig. 3 CMP LocationÐ4.0L Engine
1 - OIL FILTER
2 - CAMSHAFT POSITION SENSOR
3 - CLAMP BOLT
4 - HOLD-DOWN CLAMP
5 - MOUNTING BOLTS (2)
6 - ELEC. CONNECTORFig. 4 CMP LocationÐ4.7L Engine
1 - RIGHT CYLINDER HEAD
2 - CAMSHAFT POSITION SENSOR
3 - MOUNTING BOLT
4 - ELEC. CONNECTOR
WJIGNITION CONTROL 8I - 5
CAMSHAFT POSITION SENSOR (Continued)
Page 403 of 2199
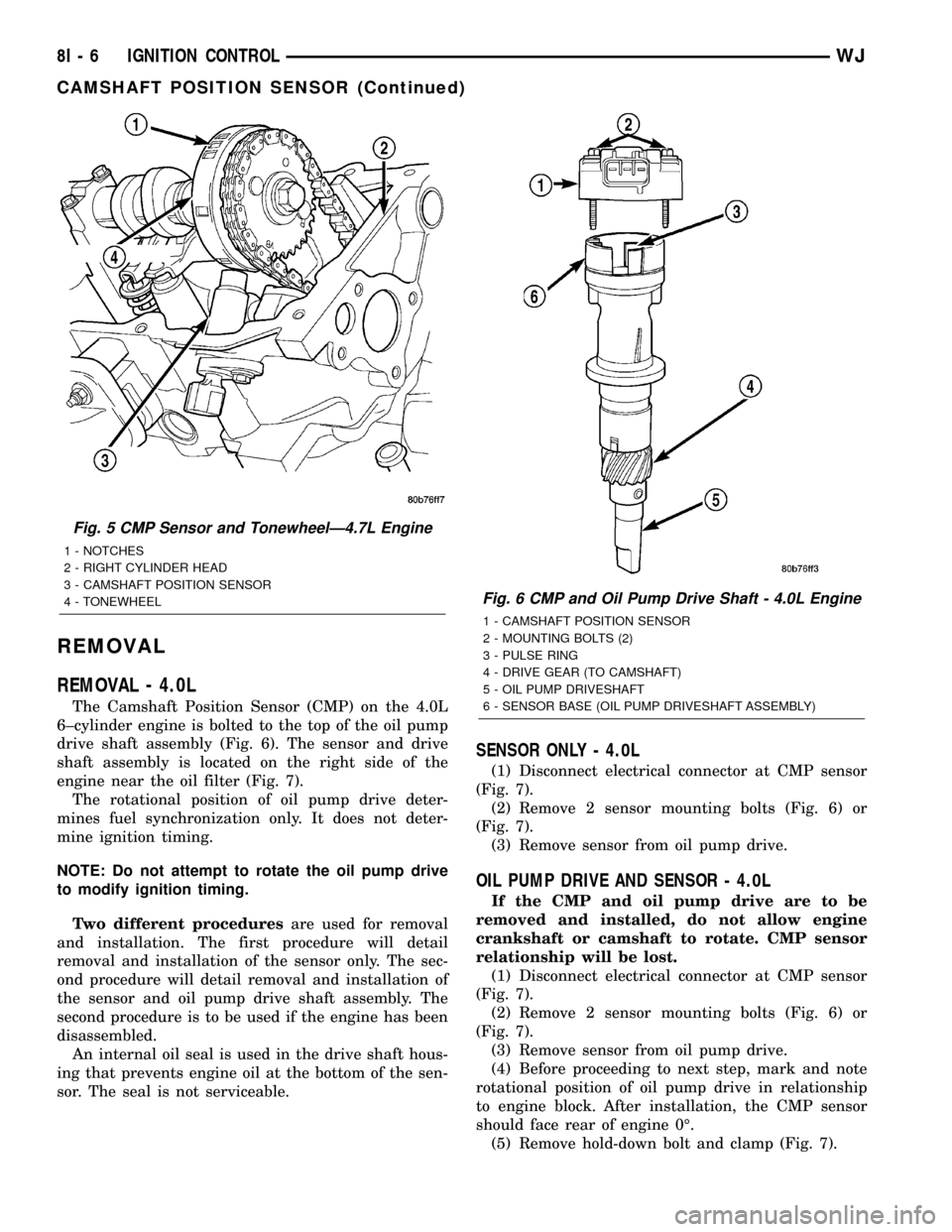
REMOVAL
REMOVAL - 4.0L
The Camshaft Position Sensor (CMP) on the 4.0L
6±cylinder engine is bolted to the top of the oil pump
drive shaft assembly (Fig. 6). The sensor and drive
shaft assembly is located on the right side of the
engine near the oil filter (Fig. 7).
The rotational position of oil pump drive deter-
mines fuel synchronization only. It does not deter-
mine ignition timing.
NOTE: Do not attempt to rotate the oil pump drive
to modify ignition timing.
Two different proceduresare used for removal
and installation. The first procedure will detail
removal and installation of the sensor only. The sec-
ond procedure will detail removal and installation of
the sensor and oil pump drive shaft assembly. The
second procedure is to be used if the engine has been
disassembled.
An internal oil seal is used in the drive shaft hous-
ing that prevents engine oil at the bottom of the sen-
sor. The seal is not serviceable.
SENSOR ONLY - 4.0L
(1) Disconnect electrical connector at CMP sensor
(Fig. 7).
(2) Remove 2 sensor mounting bolts (Fig. 6) or
(Fig. 7).
(3) Remove sensor from oil pump drive.
OIL PUMP DRIVE AND SENSOR - 4.0L
If the CMP and oil pump drive are to be
removed and installed, do not allow engine
crankshaft or camshaft to rotate. CMP sensor
relationship will be lost.
(1) Disconnect electrical connector at CMP sensor
(Fig. 7).
(2) Remove 2 sensor mounting bolts (Fig. 6) or
(Fig. 7).
(3) Remove sensor from oil pump drive.
(4) Before proceeding to next step, mark and note
rotational position of oil pump drive in relationship
to engine block. After installation, the CMP sensor
should face rear of engine 0É.
(5) Remove hold-down bolt and clamp (Fig. 7).
Fig. 5 CMP Sensor and TonewheelÐ4.7L Engine
1 - NOTCHES
2 - RIGHT CYLINDER HEAD
3 - CAMSHAFT POSITION SENSOR
4 - TONEWHEEL
Fig. 6 CMP and Oil Pump Drive Shaft - 4.0L Engine
1 - CAMSHAFT POSITION SENSOR
2 - MOUNTING BOLTS (2)
3 - PULSE RING
4 - DRIVE GEAR (TO CAMSHAFT)
5 - OIL PUMP DRIVESHAFT
6 - SENSOR BASE (OIL PUMP DRIVESHAFT ASSEMBLY)
8I - 6 IGNITION CONTROLWJ
CAMSHAFT POSITION SENSOR (Continued)
Page 404 of 2199
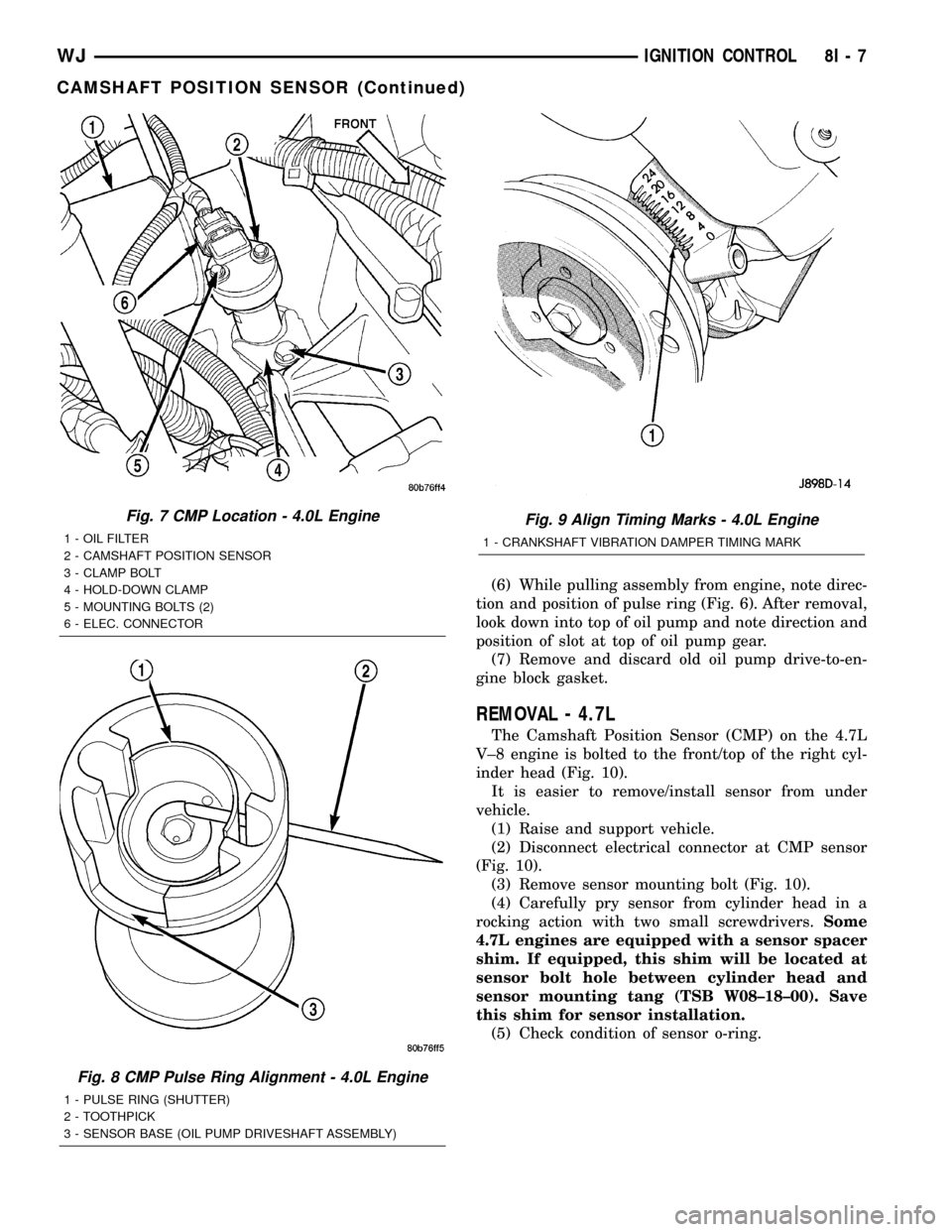
(6) While pulling assembly from engine, note direc-
tion and position of pulse ring (Fig. 6). After removal,
look down into top of oil pump and note direction and
position of slot at top of oil pump gear.
(7) Remove and discard old oil pump drive-to-en-
gine block gasket.
REMOVAL - 4.7L
The Camshaft Position Sensor (CMP) on the 4.7L
V±8 engine is bolted to the front/top of the right cyl-
inder head (Fig. 10).
It is easier to remove/install sensor from under
vehicle.
(1) Raise and support vehicle.
(2) Disconnect electrical connector at CMP sensor
(Fig. 10).
(3) Remove sensor mounting bolt (Fig. 10).
(4) Carefully pry sensor from cylinder head in a
rocking action with two small screwdrivers.Some
4.7L engines are equipped with a sensor spacer
shim. If equipped, this shim will be located at
sensor bolt hole between cylinder head and
sensor mounting tang (TSB W08±18±00). Save
this shim for sensor installation.
(5) Check condition of sensor o-ring.
Fig. 7 CMP Location - 4.0L Engine
1 - OIL FILTER
2 - CAMSHAFT POSITION SENSOR
3 - CLAMP BOLT
4 - HOLD-DOWN CLAMP
5 - MOUNTING BOLTS (2)
6 - ELEC. CONNECTOR
Fig. 8 CMP Pulse Ring Alignment - 4.0L Engine
1 - PULSE RING (SHUTTER)
2 - TOOTHPICK
3 - SENSOR BASE (OIL PUMP DRIVESHAFT ASSEMBLY)
Fig. 9 Align Timing Marks - 4.0L Engine
1 - CRANKSHAFT VIBRATION DAMPER TIMING MARK
WJIGNITION CONTROL 8I - 7
CAMSHAFT POSITION SENSOR (Continued)
Page 405 of 2199
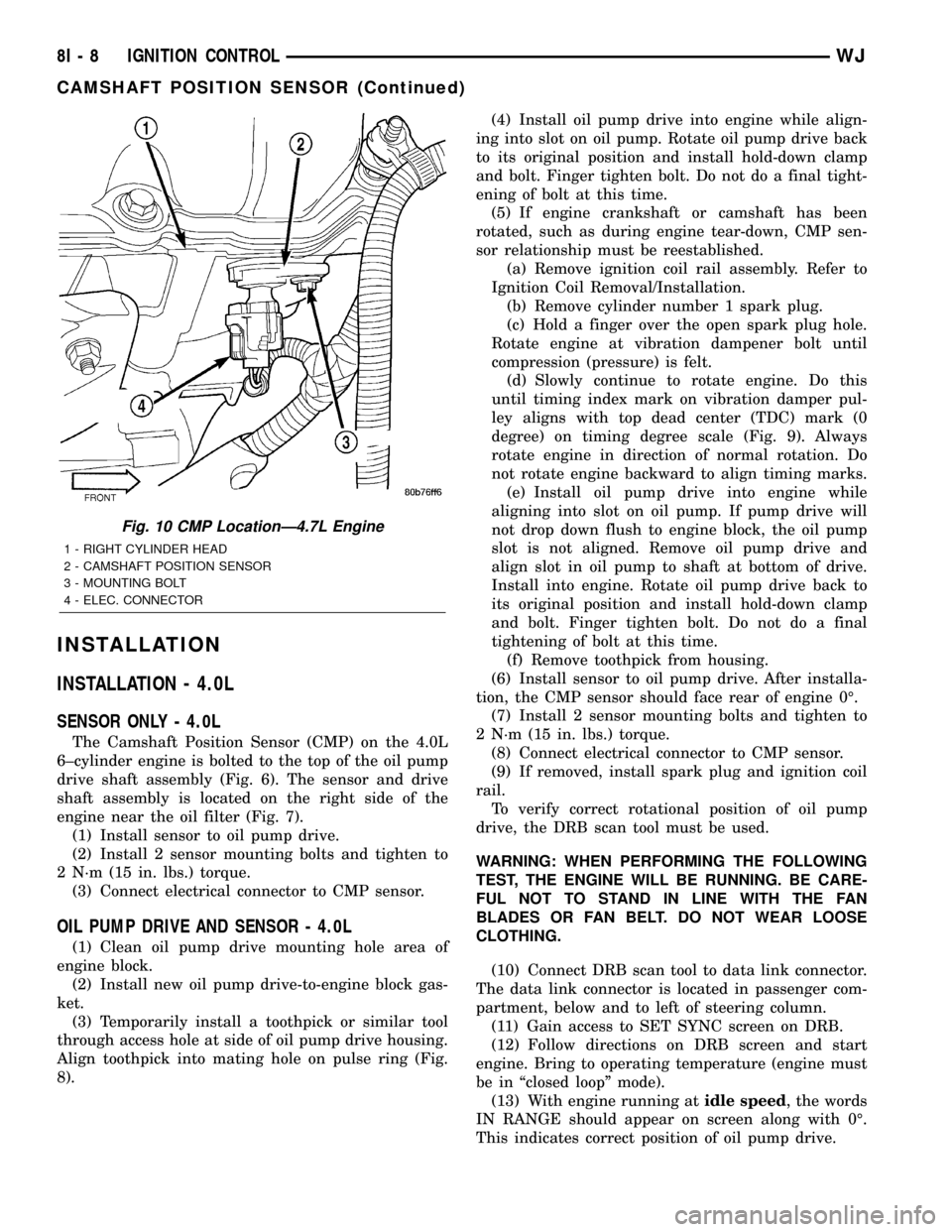
INSTALLATION
INSTALLATION - 4.0L
SENSOR ONLY - 4.0L
The Camshaft Position Sensor (CMP) on the 4.0L
6±cylinder engine is bolted to the top of the oil pump
drive shaft assembly (Fig. 6). The sensor and drive
shaft assembly is located on the right side of the
engine near the oil filter (Fig. 7).
(1) Install sensor to oil pump drive.
(2) Install 2 sensor mounting bolts and tighten to
2 N´m (15 in. lbs.) torque.
(3) Connect electrical connector to CMP sensor.
OIL PUMP DRIVE AND SENSOR - 4.0L
(1) Clean oil pump drive mounting hole area of
engine block.
(2) Install new oil pump drive-to-engine block gas-
ket.
(3) Temporarily install a toothpick or similar tool
through access hole at side of oil pump drive housing.
Align toothpick into mating hole on pulse ring (Fig.
8).(4) Install oil pump drive into engine while align-
ing into slot on oil pump. Rotate oil pump drive back
to its original position and install hold-down clamp
and bolt. Finger tighten bolt. Do not do a final tight-
ening of bolt at this time.
(5) If engine crankshaft or camshaft has been
rotated, such as during engine tear-down, CMP sen-
sor relationship must be reestablished.
(a) Remove ignition coil rail assembly. Refer to
Ignition Coil Removal/Installation.
(b) Remove cylinder number 1 spark plug.
(c) Hold a finger over the open spark plug hole.
Rotate engine at vibration dampener bolt until
compression (pressure) is felt.
(d) Slowly continue to rotate engine. Do this
until timing index mark on vibration damper pul-
ley aligns with top dead center (TDC) mark (0
degree) on timing degree scale (Fig. 9). Always
rotate engine in direction of normal rotation. Do
not rotate engine backward to align timing marks.
(e) Install oil pump drive into engine while
aligning into slot on oil pump. If pump drive will
not drop down flush to engine block, the oil pump
slot is not aligned. Remove oil pump drive and
align slot in oil pump to shaft at bottom of drive.
Install into engine. Rotate oil pump drive back to
its original position and install hold-down clamp
and bolt. Finger tighten bolt. Do not do a final
tightening of bolt at this time.
(f) Remove toothpick from housing.
(6) Install sensor to oil pump drive. After installa-
tion, the CMP sensor should face rear of engine 0É.
(7) Install 2 sensor mounting bolts and tighten to
2 N´m (15 in. lbs.) torque.
(8) Connect electrical connector to CMP sensor.
(9) If removed, install spark plug and ignition coil
rail.
To verify correct rotational position of oil pump
drive, the DRB scan tool must be used.
WARNING: WHEN PERFORMING THE FOLLOWING
TEST, THE ENGINE WILL BE RUNNING. BE CARE-
FUL NOT TO STAND IN LINE WITH THE FAN
BLADES OR FAN BELT. DO NOT WEAR LOOSE
CLOTHING.
(10) Connect DRB scan tool to data link connector.
The data link connector is located in passenger com-
partment, below and to left of steering column.
(11) Gain access to SET SYNC screen on DRB.
(12) Follow directions on DRB screen and start
engine. Bring to operating temperature (engine must
be in ªclosed loopº mode).
(13) With engine running atidle speed, the words
IN RANGE should appear on screen along with 0É.
This indicates correct position of oil pump drive.
Fig. 10 CMP LocationÐ4.7L Engine
1 - RIGHT CYLINDER HEAD
2 - CAMSHAFT POSITION SENSOR
3 - MOUNTING BOLT
4 - ELEC. CONNECTOR
8I - 8 IGNITION CONTROLWJ
CAMSHAFT POSITION SENSOR (Continued)
Page 406 of 2199
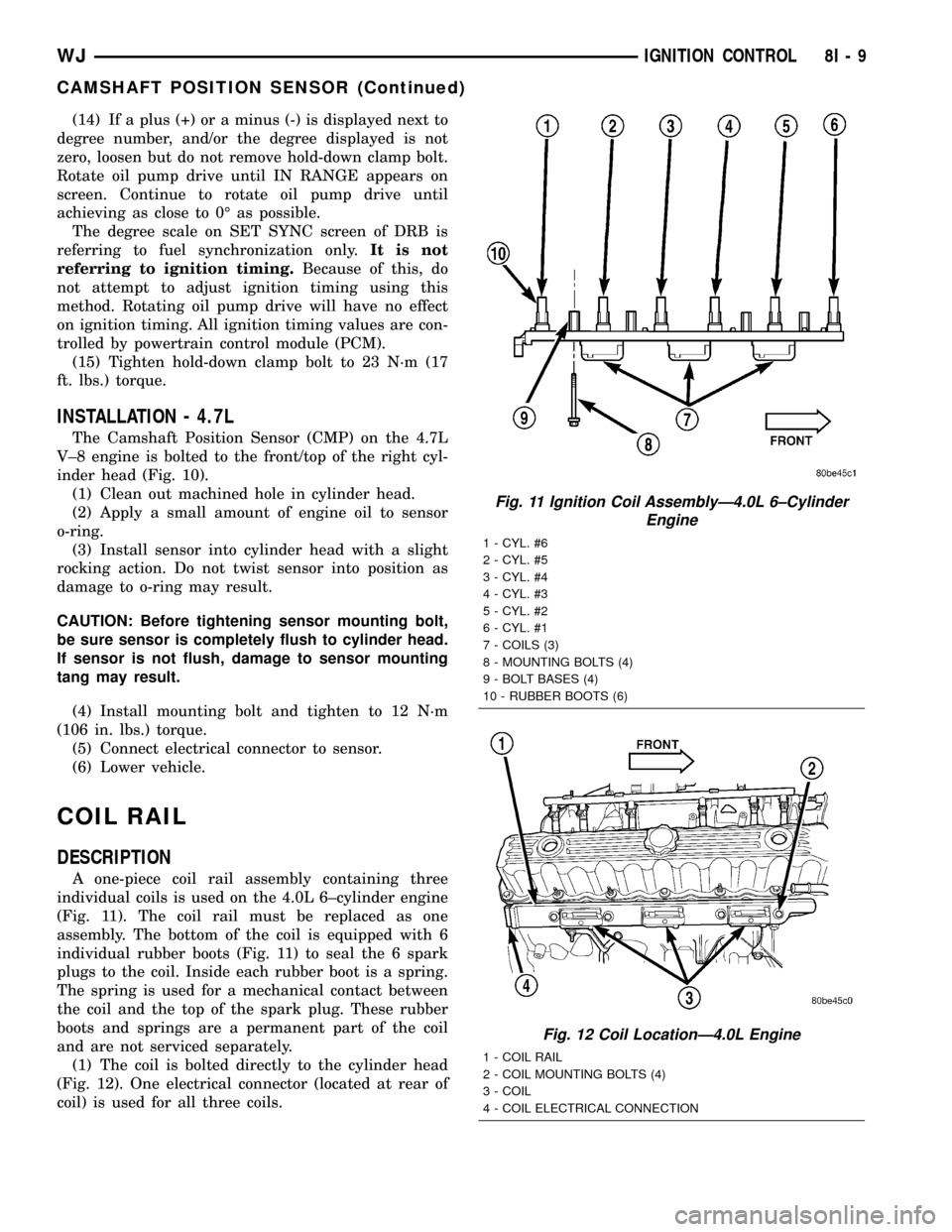
(14) If a plus (+) or a minus (-) is displayed next to
degree number, and/or the degree displayed is not
zero, loosen but do not remove hold-down clamp bolt.
Rotate oil pump drive until IN RANGE appears on
screen. Continue to rotate oil pump drive until
achieving as close to 0É as possible.
The degree scale on SET SYNC screen of DRB is
referring to fuel synchronization only.It is not
referring to ignition timing.Because of this, do
not attempt to adjust ignition timing using this
method. Rotating oil pump drive will have no effect
on ignition timing. All ignition timing values are con-
trolled by powertrain control module (PCM).
(15) Tighten hold-down clamp bolt to 23 N´m (17
ft. lbs.) torque.
INSTALLATION - 4.7L
The Camshaft Position Sensor (CMP) on the 4.7L
V±8 engine is bolted to the front/top of the right cyl-
inder head (Fig. 10).
(1) Clean out machined hole in cylinder head.
(2) Apply a small amount of engine oil to sensor
o-ring.
(3) Install sensor into cylinder head with a slight
rocking action. Do not twist sensor into position as
damage to o-ring may result.
CAUTION: Before tightening sensor mounting bolt,
be sure sensor is completely flush to cylinder head.
If sensor is not flush, damage to sensor mounting
tang may result.
(4) Install mounting bolt and tighten to 12 N´m
(106 in. lbs.) torque.
(5) Connect electrical connector to sensor.
(6) Lower vehicle.
COIL RAIL
DESCRIPTION
A one-piece coil rail assembly containing three
individual coils is used on the 4.0L 6±cylinder engine
(Fig. 11). The coil rail must be replaced as one
assembly. The bottom of the coil is equipped with 6
individual rubber boots (Fig. 11) to seal the 6 spark
plugs to the coil. Inside each rubber boot is a spring.
The spring is used for a mechanical contact between
the coil and the top of the spark plug. These rubber
boots and springs are a permanent part of the coil
and are not serviced separately.
(1) The coil is bolted directly to the cylinder head
(Fig. 12). One electrical connector (located at rear of
coil) is used for all three coils.
Fig. 11 Ignition Coil AssemblyÐ4.0L 6±Cylinder
Engine
1 - CYL. #6
2 - CYL. #5
3 - CYL. #4
4 - CYL. #3
5 - CYL. #2
6 - CYL. #1
7 - COILS (3)
8 - MOUNTING BOLTS (4)
9 - BOLT BASES (4)
10 - RUBBER BOOTS (6)
Fig. 12 Coil LocationÐ4.0L Engine
1 - COIL RAIL
2 - COIL MOUNTING BOLTS (4)
3 - COIL
4 - COIL ELECTRICAL CONNECTION
WJIGNITION CONTROL 8I - 9
CAMSHAFT POSITION SENSOR (Continued)
Page 408 of 2199
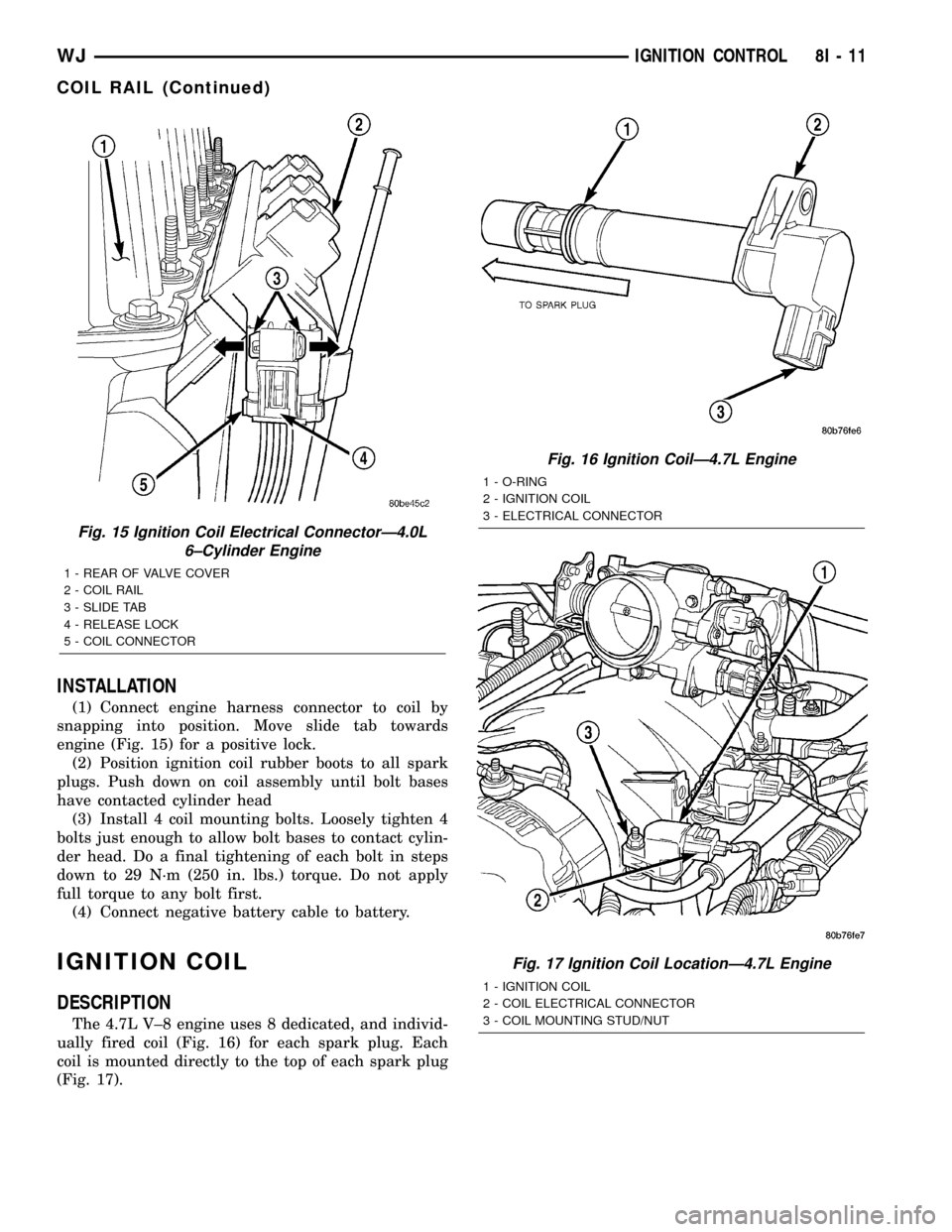
INSTALLATION
(1) Connect engine harness connector to coil by
snapping into position. Move slide tab towards
engine (Fig. 15) for a positive lock.
(2) Position ignition coil rubber boots to all spark
plugs. Push down on coil assembly until bolt bases
have contacted cylinder head
(3) Install 4 coil mounting bolts. Loosely tighten 4
bolts just enough to allow bolt bases to contact cylin-
der head. Do a final tightening of each bolt in steps
down to 29 N´m (250 in. lbs.) torque. Do not apply
full torque to any bolt first.
(4) Connect negative battery cable to battery.
IGNITION COIL
DESCRIPTION
The 4.7L V±8 engine uses 8 dedicated, and individ-
ually fired coil (Fig. 16) for each spark plug. Each
coil is mounted directly to the top of each spark plug
(Fig. 17).
Fig. 15 Ignition Coil Electrical ConnectorÐ4.0L
6±Cylinder Engine
1 - REAR OF VALVE COVER
2 - COIL RAIL
3 - SLIDE TAB
4 - RELEASE LOCK
5 - COIL CONNECTOR
Fig. 16 Ignition CoilÐ4.7L Engine
1 - O-RING
2 - IGNITION COIL
3 - ELECTRICAL CONNECTOR
Fig. 17 Ignition Coil LocationÐ4.7L Engine
1 - IGNITION COIL
2 - COIL ELECTRICAL CONNECTOR
3 - COIL MOUNTING STUD/NUT
WJIGNITION CONTROL 8I - 11
COIL RAIL (Continued)
Page 409 of 2199
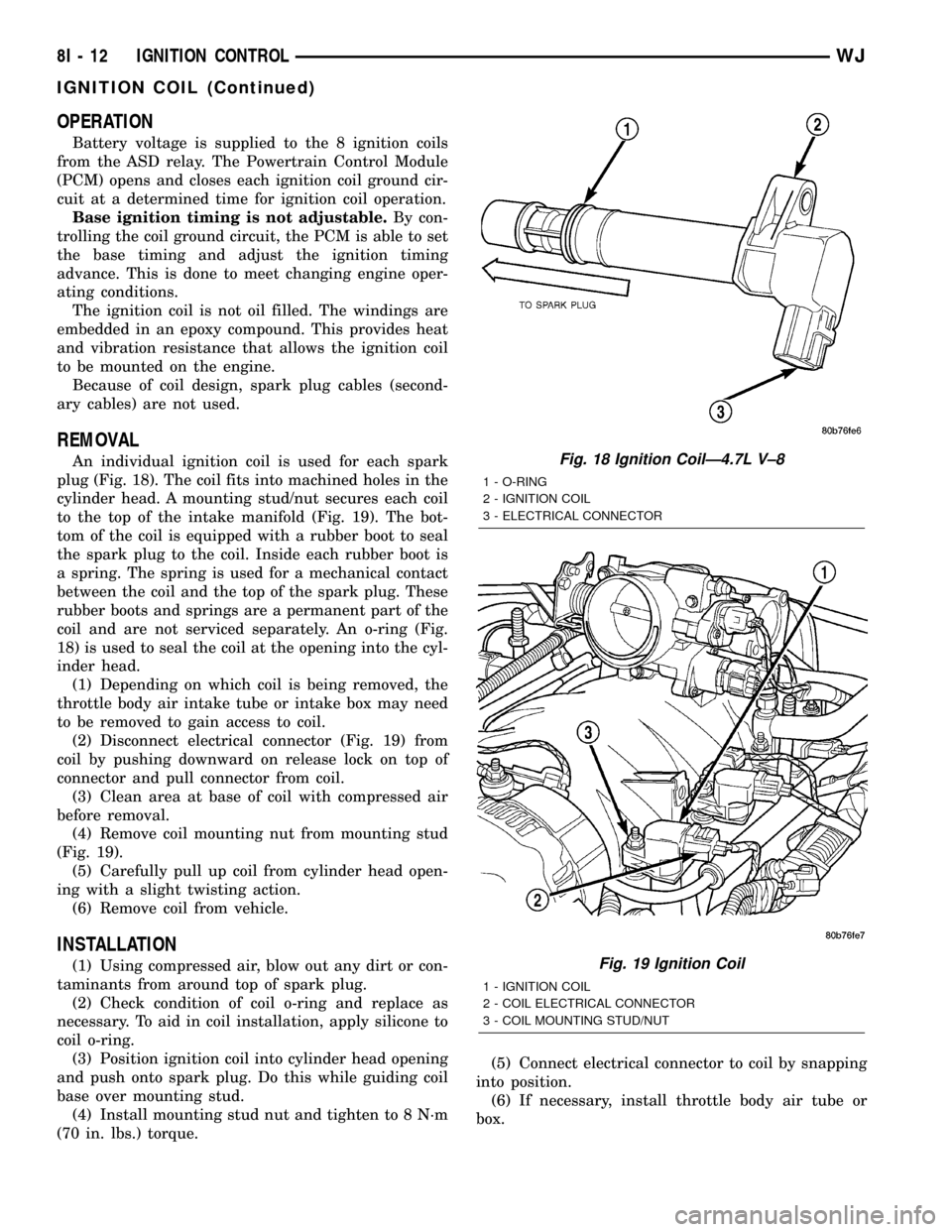
OPERATION
Battery voltage is supplied to the 8 ignition coils
from the ASD relay. The Powertrain Control Module
(PCM) opens and closes each ignition coil ground cir-
cuit at a determined time for ignition coil operation.
Base ignition timing is not adjustable.By con-
trolling the coil ground circuit, the PCM is able to set
the base timing and adjust the ignition timing
advance. This is done to meet changing engine oper-
ating conditions.
The ignition coil is not oil filled. The windings are
embedded in an epoxy compound. This provides heat
and vibration resistance that allows the ignition coil
to be mounted on the engine.
Because of coil design, spark plug cables (second-
ary cables) are not used.
REMOVAL
An individual ignition coil is used for each spark
plug (Fig. 18). The coil fits into machined holes in the
cylinder head. A mounting stud/nut secures each coil
to the top of the intake manifold (Fig. 19). The bot-
tom of the coil is equipped with a rubber boot to seal
the spark plug to the coil. Inside each rubber boot is
a spring. The spring is used for a mechanical contact
between the coil and the top of the spark plug. These
rubber boots and springs are a permanent part of the
coil and are not serviced separately. An o-ring (Fig.
18) is used to seal the coil at the opening into the cyl-
inder head.
(1) Depending on which coil is being removed, the
throttle body air intake tube or intake box may need
to be removed to gain access to coil.
(2) Disconnect electrical connector (Fig. 19) from
coil by pushing downward on release lock on top of
connector and pull connector from coil.
(3) Clean area at base of coil with compressed air
before removal.
(4) Remove coil mounting nut from mounting stud
(Fig. 19).
(5) Carefully pull up coil from cylinder head open-
ing with a slight twisting action.
(6) Remove coil from vehicle.
INSTALLATION
(1) Using compressed air, blow out any dirt or con-
taminants from around top of spark plug.
(2) Check condition of coil o-ring and replace as
necessary. To aid in coil installation, apply silicone to
coil o-ring.
(3) Position ignition coil into cylinder head opening
and push onto spark plug. Do this while guiding coil
base over mounting stud.
(4) Install mounting stud nut and tighten to 8 N´m
(70 in. lbs.) torque.(5) Connect electrical connector to coil by snapping
into position.
(6) If necessary, install throttle body air tube or
box.
Fig. 18 Ignition CoilÐ4.7L V±8
1 - O-RING
2 - IGNITION COIL
3 - ELECTRICAL CONNECTOR
Fig. 19 Ignition Coil
1 - IGNITION COIL
2 - COIL ELECTRICAL CONNECTOR
3 - COIL MOUNTING STUD/NUT
8I - 12 IGNITION CONTROLWJ
IGNITION COIL (Continued)
Page 410 of 2199
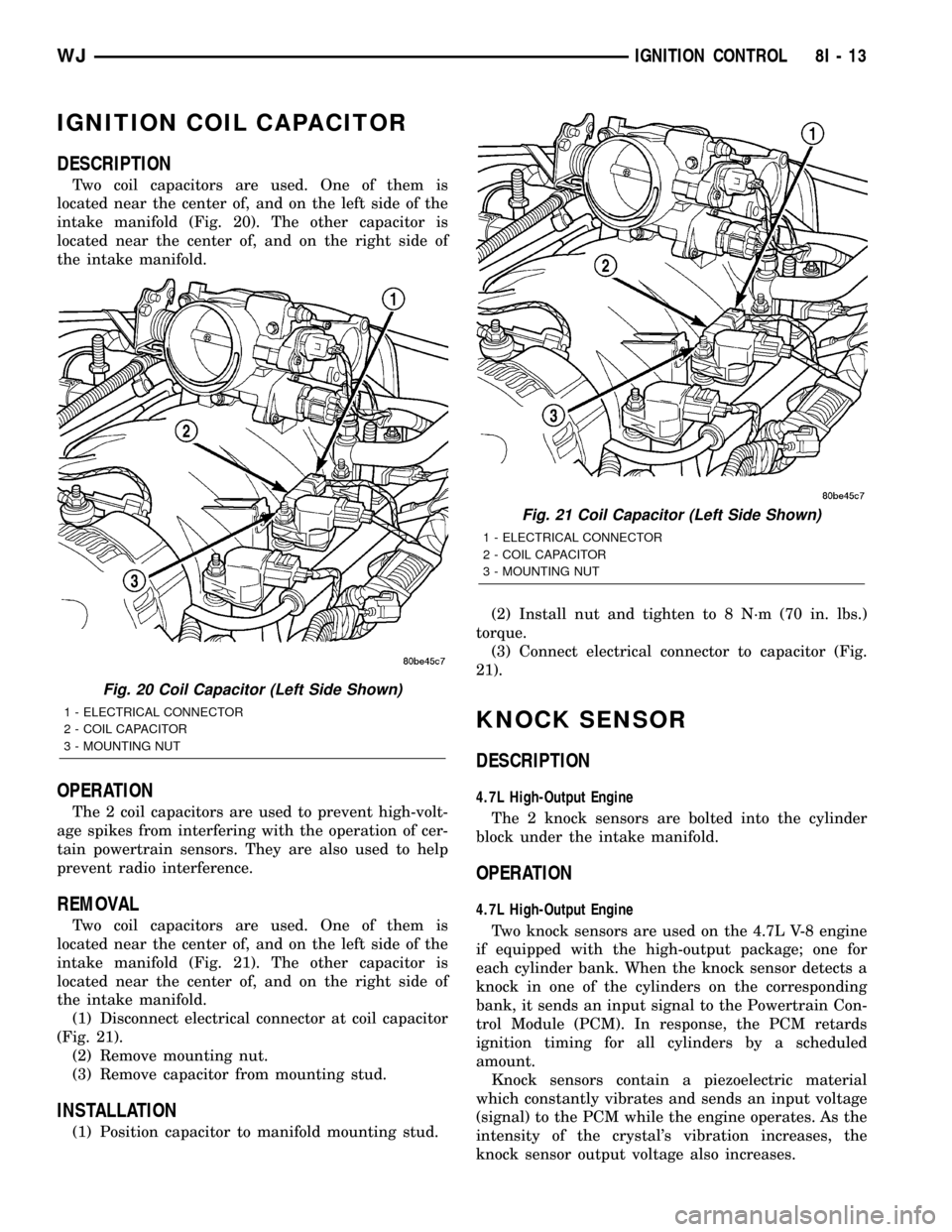
IGNITION COIL CAPACITOR
DESCRIPTION
Two coil capacitors are used. One of them is
located near the center of, and on the left side of the
intake manifold (Fig. 20). The other capacitor is
located near the center of, and on the right side of
the intake manifold.
OPERATION
The 2 coil capacitors are used to prevent high-volt-
age spikes from interfering with the operation of cer-
tain powertrain sensors. They are also used to help
prevent radio interference.
REMOVAL
Two coil capacitors are used. One of them is
located near the center of, and on the left side of the
intake manifold (Fig. 21). The other capacitor is
located near the center of, and on the right side of
the intake manifold.
(1) Disconnect electrical connector at coil capacitor
(Fig. 21).
(2) Remove mounting nut.
(3) Remove capacitor from mounting stud.
INSTALLATION
(1) Position capacitor to manifold mounting stud.(2) Install nut and tighten to 8 N´m (70 in. lbs.)
torque.
(3) Connect electrical connector to capacitor (Fig.
21).
KNOCK SENSOR
DESCRIPTION
4.7L High-Output Engine
The 2 knock sensors are bolted into the cylinder
block under the intake manifold.
OPERATION
4.7L High-Output Engine
Two knock sensors are used on the 4.7L V-8 engine
if equipped with the high-output package; one for
each cylinder bank. When the knock sensor detects a
knock in one of the cylinders on the corresponding
bank, it sends an input signal to the Powertrain Con-
trol Module (PCM). In response, the PCM retards
ignition timing for all cylinders by a scheduled
amount.
Knock sensors contain a piezoelectric material
which constantly vibrates and sends an input voltage
(signal) to the PCM while the engine operates. As the
intensity of the crystal's vibration increases, the
knock sensor output voltage also increases.
Fig. 20 Coil Capacitor (Left Side Shown)
1 - ELECTRICAL CONNECTOR
2 - COIL CAPACITOR
3 - MOUNTING NUT
Fig. 21 Coil Capacitor (Left Side Shown)
1 - ELECTRICAL CONNECTOR
2 - COIL CAPACITOR
3 - MOUNTING NUT
WJIGNITION CONTROL 8I - 13
Page 411 of 2199
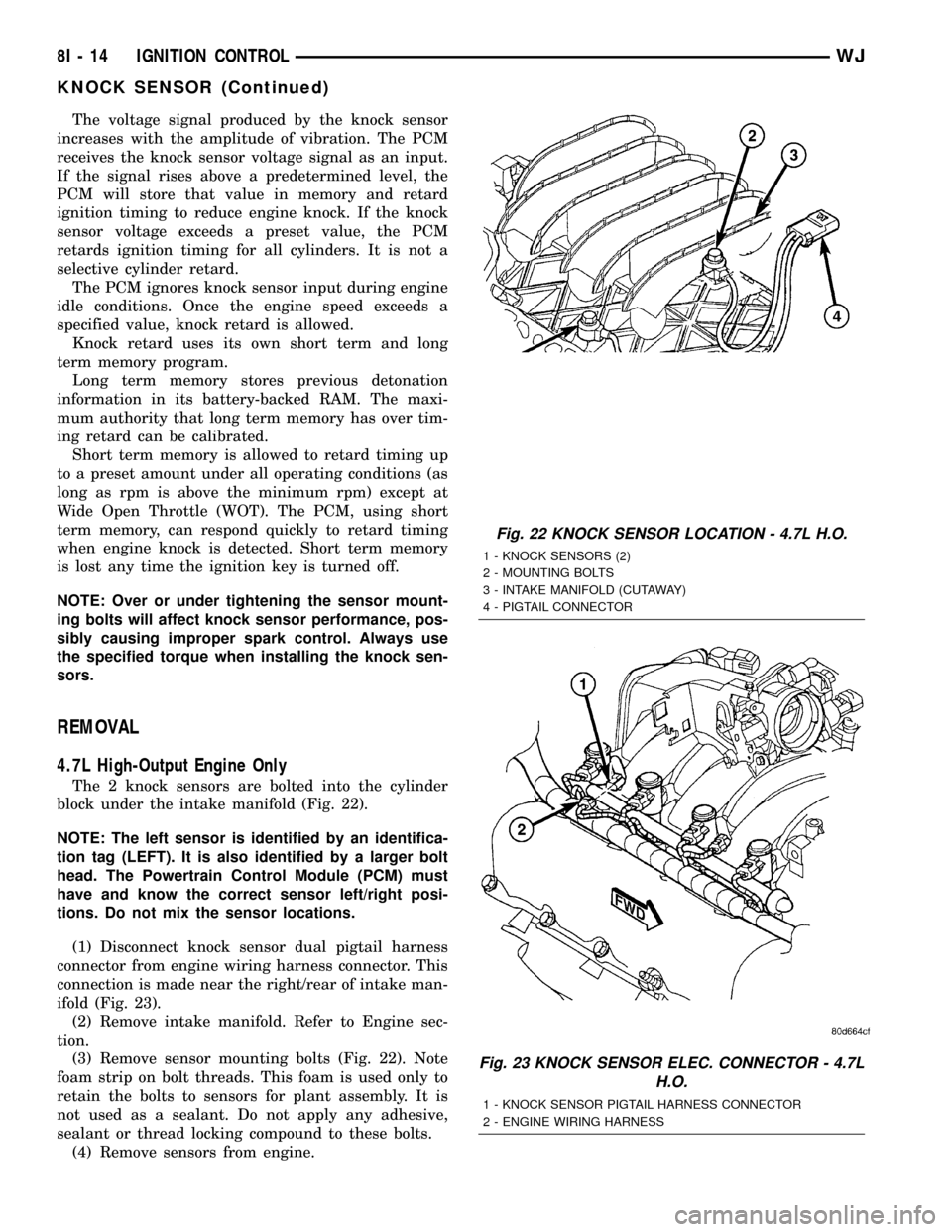
The voltage signal produced by the knock sensor
increases with the amplitude of vibration. The PCM
receives the knock sensor voltage signal as an input.
If the signal rises above a predetermined level, the
PCM will store that value in memory and retard
ignition timing to reduce engine knock. If the knock
sensor voltage exceeds a preset value, the PCM
retards ignition timing for all cylinders. It is not a
selective cylinder retard.
The PCM ignores knock sensor input during engine
idle conditions. Once the engine speed exceeds a
specified value, knock retard is allowed.
Knock retard uses its own short term and long
term memory program.
Long term memory stores previous detonation
information in its battery-backed RAM. The maxi-
mum authority that long term memory has over tim-
ing retard can be calibrated.
Short term memory is allowed to retard timing up
to a preset amount under all operating conditions (as
long as rpm is above the minimum rpm) except at
Wide Open Throttle (WOT). The PCM, using short
term memory, can respond quickly to retard timing
when engine knock is detected. Short term memory
is lost any time the ignition key is turned off.
NOTE: Over or under tightening the sensor mount-
ing bolts will affect knock sensor performance, pos-
sibly causing improper spark control. Always use
the specified torque when installing the knock sen-
sors.
REMOVAL
4.7L High-Output Engine Only
The 2 knock sensors are bolted into the cylinder
block under the intake manifold (Fig. 22).
NOTE: The left sensor is identified by an identifica-
tion tag (LEFT). It is also identified by a larger bolt
head. The Powertrain Control Module (PCM) must
have and know the correct sensor left/right posi-
tions. Do not mix the sensor locations.
(1) Disconnect knock sensor dual pigtail harness
connector from engine wiring harness connector. This
connection is made near the right/rear of intake man-
ifold (Fig. 23).
(2) Remove intake manifold. Refer to Engine sec-
tion.
(3) Remove sensor mounting bolts (Fig. 22). Note
foam strip on bolt threads. This foam is used only to
retain the bolts to sensors for plant assembly. It is
not used as a sealant. Do not apply any adhesive,
sealant or thread locking compound to these bolts.
(4) Remove sensors from engine.
Fig. 22 KNOCK SENSOR LOCATION - 4.7L H.O.
1 - KNOCK SENSORS (2)
2 - MOUNTING BOLTS
3 - INTAKE MANIFOLD (CUTAWAY)
4 - PIGTAIL CONNECTOR
Fig. 23 KNOCK SENSOR ELEC. CONNECTOR - 4.7L
H.O.
1 - KNOCK SENSOR PIGTAIL HARNESS CONNECTOR
2 - ENGINE WIRING HARNESS
8I - 14 IGNITION CONTROLWJ
KNOCK SENSOR (Continued)