Code JEEP GRAND CHEROKEE 2003 WJ / 2.G Service Manual
[x] Cancel search | Manufacturer: JEEP, Model Year: 2003, Model line: GRAND CHEROKEE, Model: JEEP GRAND CHEROKEE 2003 WJ / 2.GPages: 2199, PDF Size: 76.01 MB
Page 542 of 2199
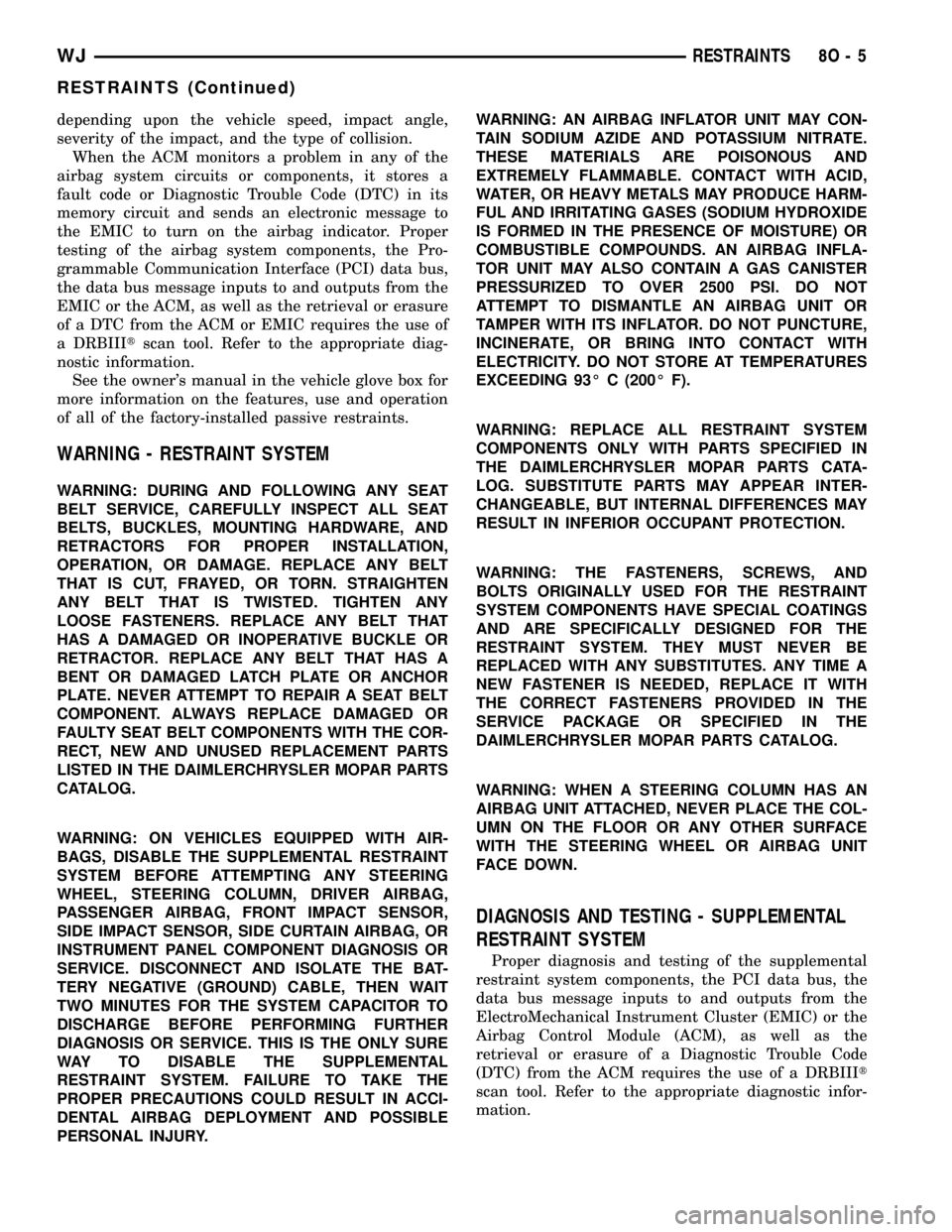
depending upon the vehicle speed, impact angle,
severity of the impact, and the type of collision.
When the ACM monitors a problem in any of the
airbag system circuits or components, it stores a
fault code or Diagnostic Trouble Code (DTC) in its
memory circuit and sends an electronic message to
the EMIC to turn on the airbag indicator. Proper
testing of the airbag system components, the Pro-
grammable Communication Interface (PCI) data bus,
the data bus message inputs to and outputs from the
EMIC or the ACM, as well as the retrieval or erasure
of a DTC from the ACM or EMIC requires the use of
a DRBIIItscan tool. Refer to the appropriate diag-
nostic information.
See the owner's manual in the vehicle glove box for
more information on the features, use and operation
of all of the factory-installed passive restraints.
WARNING - RESTRAINT SYSTEM
WARNING: DURING AND FOLLOWING ANY SEAT
BELT SERVICE, CAREFULLY INSPECT ALL SEAT
BELTS, BUCKLES, MOUNTING HARDWARE, AND
RETRACTORS FOR PROPER INSTALLATION,
OPERATION, OR DAMAGE. REPLACE ANY BELT
THAT IS CUT, FRAYED, OR TORN. STRAIGHTEN
ANY BELT THAT IS TWISTED. TIGHTEN ANY
LOOSE FASTENERS. REPLACE ANY BELT THAT
HAS A DAMAGED OR INOPERATIVE BUCKLE OR
RETRACTOR. REPLACE ANY BELT THAT HAS A
BENT OR DAMAGED LATCH PLATE OR ANCHOR
PLATE. NEVER ATTEMPT TO REPAIR A SEAT BELT
COMPONENT. ALWAYS REPLACE DAMAGED OR
FAULTY SEAT BELT COMPONENTS WITH THE COR-
RECT, NEW AND UNUSED REPLACEMENT PARTS
LISTED IN THE DAIMLERCHRYSLER MOPAR PARTS
CATALOG.
WARNING: ON VEHICLES EQUIPPED WITH AIR-
BAGS, DISABLE THE SUPPLEMENTAL RESTRAINT
SYSTEM BEFORE ATTEMPTING ANY STEERING
WHEEL, STEERING COLUMN, DRIVER AIRBAG,
PASSENGER AIRBAG, FRONT IMPACT SENSOR,
SIDE IMPACT SENSOR, SIDE CURTAIN AIRBAG, OR
INSTRUMENT PANEL COMPONENT DIAGNOSIS OR
SERVICE. DISCONNECT AND ISOLATE THE BAT-
TERY NEGATIVE (GROUND) CABLE, THEN WAIT
TWO MINUTES FOR THE SYSTEM CAPACITOR TO
DISCHARGE BEFORE PERFORMING FURTHER
DIAGNOSIS OR SERVICE. THIS IS THE ONLY SURE
WAY TO DISABLE THE SUPPLEMENTAL
RESTRAINT SYSTEM. FAILURE TO TAKE THE
PROPER PRECAUTIONS COULD RESULT IN ACCI-
DENTAL AIRBAG DEPLOYMENT AND POSSIBLE
PERSONAL INJURY.WARNING: AN AIRBAG INFLATOR UNIT MAY CON-
TAIN SODIUM AZIDE AND POTASSIUM NITRATE.
THESE MATERIALS ARE POISONOUS AND
EXTREMELY FLAMMABLE. CONTACT WITH ACID,
WATER, OR HEAVY METALS MAY PRODUCE HARM-
FUL AND IRRITATING GASES (SODIUM HYDROXIDE
IS FORMED IN THE PRESENCE OF MOISTURE) OR
COMBUSTIBLE COMPOUNDS. AN AIRBAG INFLA-
TOR UNIT MAY ALSO CONTAIN A GAS CANISTER
PRESSURIZED TO OVER 2500 PSI. DO NOT
ATTEMPT TO DISMANTLE AN AIRBAG UNIT OR
TAMPER WITH ITS INFLATOR. DO NOT PUNCTURE,
INCINERATE, OR BRING INTO CONTACT WITH
ELECTRICITY. DO NOT STORE AT TEMPERATURES
EXCEEDING 93É C (200É F).
WARNING: REPLACE ALL RESTRAINT SYSTEM
COMPONENTS ONLY WITH PARTS SPECIFIED IN
THE DAIMLERCHRYSLER MOPAR PARTS CATA-
LOG. SUBSTITUTE PARTS MAY APPEAR INTER-
CHANGEABLE, BUT INTERNAL DIFFERENCES MAY
RESULT IN INFERIOR OCCUPANT PROTECTION.
WARNING: THE FASTENERS, SCREWS, AND
BOLTS ORIGINALLY USED FOR THE RESTRAINT
SYSTEM COMPONENTS HAVE SPECIAL COATINGS
AND ARE SPECIFICALLY DESIGNED FOR THE
RESTRAINT SYSTEM. THEY MUST NEVER BE
REPLACED WITH ANY SUBSTITUTES. ANY TIME A
NEW FASTENER IS NEEDED, REPLACE IT WITH
THE CORRECT FASTENERS PROVIDED IN THE
SERVICE PACKAGE OR SPECIFIED IN THE
DAIMLERCHRYSLER MOPAR PARTS CATALOG.
WARNING: WHEN A STEERING COLUMN HAS AN
AIRBAG UNIT ATTACHED, NEVER PLACE THE COL-
UMN ON THE FLOOR OR ANY OTHER SURFACE
WITH THE STEERING WHEEL OR AIRBAG UNIT
FACE DOWN.
DIAGNOSIS AND TESTING - SUPPLEMENTAL
RESTRAINT SYSTEM
Proper diagnosis and testing of the supplemental
restraint system components, the PCI data bus, the
data bus message inputs to and outputs from the
ElectroMechanical Instrument Cluster (EMIC) or the
Airbag Control Module (ACM), as well as the
retrieval or erasure of a Diagnostic Trouble Code
(DTC) from the ACM requires the use of a DRBIIIt
scan tool. Refer to the appropriate diagnostic infor-
mation.
WJRESTRAINTS 8O - 5
RESTRAINTS (Continued)
Page 544 of 2199
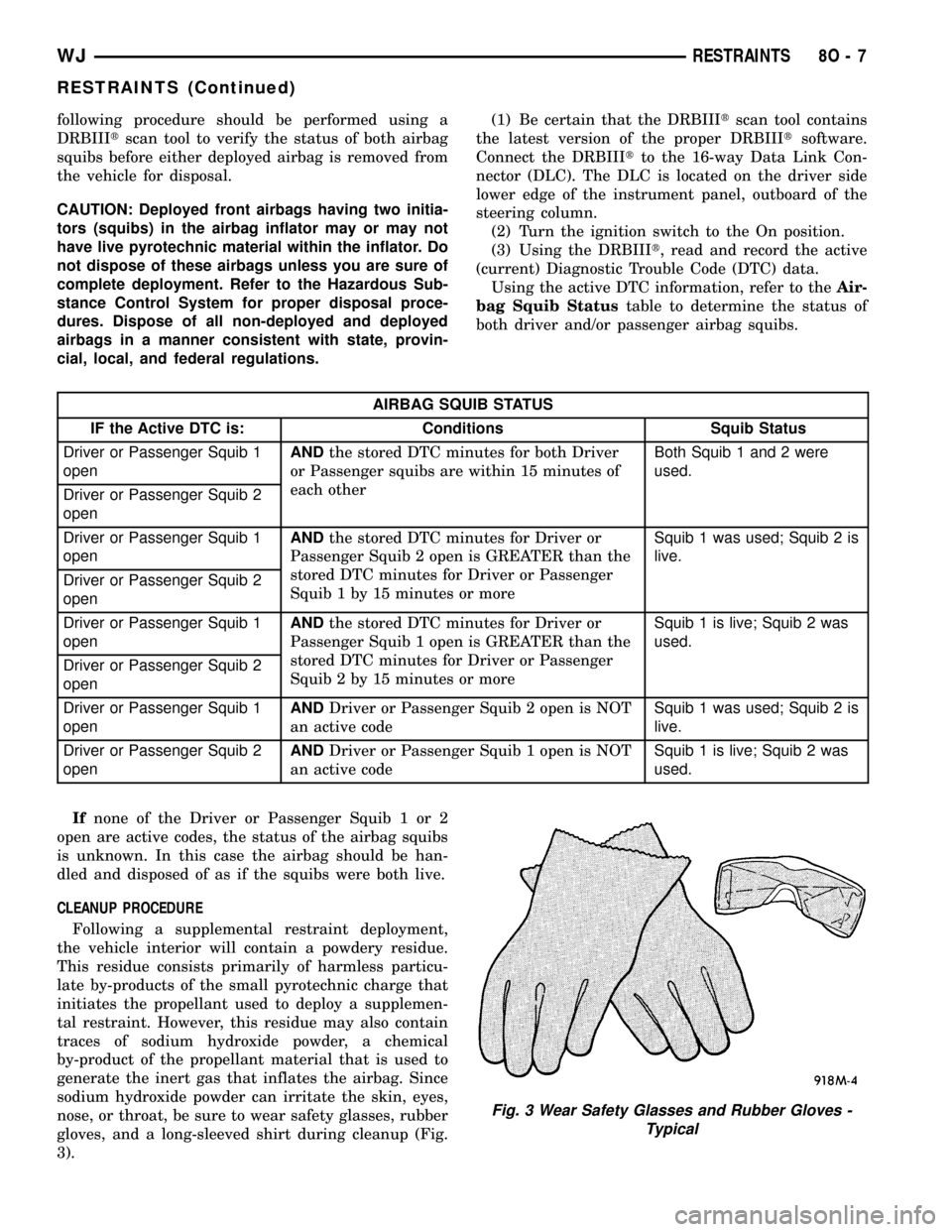
following procedure should be performed using a
DRBIIItscan tool to verify the status of both airbag
squibs before either deployed airbag is removed from
the vehicle for disposal.
CAUTION: Deployed front airbags having two initia-
tors (squibs) in the airbag inflator may or may not
have live pyrotechnic material within the inflator. Do
not dispose of these airbags unless you are sure of
complete deployment. Refer to the Hazardous Sub-
stance Control System for proper disposal proce-
dures. Dispose of all non-deployed and deployed
airbags in a manner consistent with state, provin-
cial, local, and federal regulations.(1) Be certain that the DRBIIItscan tool contains
the latest version of the proper DRBIIItsoftware.
Connect the DRBIIItto the 16-way Data Link Con-
nector (DLC). The DLC is located on the driver side
lower edge of the instrument panel, outboard of the
steering column.
(2) Turn the ignition switch to the On position.
(3) Using the DRBIIIt, read and record the active
(current) Diagnostic Trouble Code (DTC) data.
Using the active DTC information, refer to theAir-
bag Squib Statustable to determine the status of
both driver and/or passenger airbag squibs.
AIRBAG SQUIB STATUS
IF the Active DTC is: Conditions Squib Status
Driver or Passenger Squib 1
openANDthe stored DTC minutes for both Driver
or Passenger squibs are within 15 minutes of
each otherBoth Squib 1 and 2 were
used.
Driver or Passenger Squib 2
open
Driver or Passenger Squib 1
openANDthe stored DTC minutes for Driver or
Passenger Squib 2 open is GREATER than the
stored DTC minutes for Driver or Passenger
Squib 1 by 15 minutes or moreSquib 1 was used; Squib 2 is
live.
Driver or Passenger Squib 2
open
Driver or Passenger Squib 1
openANDthe stored DTC minutes for Driver or
Passenger Squib 1 open is GREATER than the
stored DTC minutes for Driver or Passenger
Squib 2 by 15 minutes or moreSquib 1 is live; Squib 2 was
used.
Driver or Passenger Squib 2
open
Driver or Passenger Squib 1
openANDDriver or Passenger Squib 2 open is NOT
an active codeSquib 1 was used; Squib 2 is
live.
Driver or Passenger Squib 2
openANDDriver or Passenger Squib 1 open is NOT
an active codeSquib 1 is live; Squib 2 was
used.
Ifnone of the Driver or Passenger Squib 1 or 2
open are active codes, the status of the airbag squibs
is unknown. In this case the airbag should be han-
dled and disposed of as if the squibs were both live.
CLEANUP PROCEDURE
Following a supplemental restraint deployment,
the vehicle interior will contain a powdery residue.
This residue consists primarily of harmless particu-
late by-products of the small pyrotechnic charge that
initiates the propellant used to deploy a supplemen-
tal restraint. However, this residue may also contain
traces of sodium hydroxide powder, a chemical
by-product of the propellant material that is used to
generate the inert gas that inflates the airbag. Since
sodium hydroxide powder can irritate the skin, eyes,
nose, or throat, be sure to wear safety glasses, rubber
gloves, and a long-sleeved shirt during cleanup (Fig.
3).
Fig. 3 Wear Safety Glasses and Rubber Gloves -
Typical
WJRESTRAINTS 8O - 7
RESTRAINTS (Continued)
Page 546 of 2199
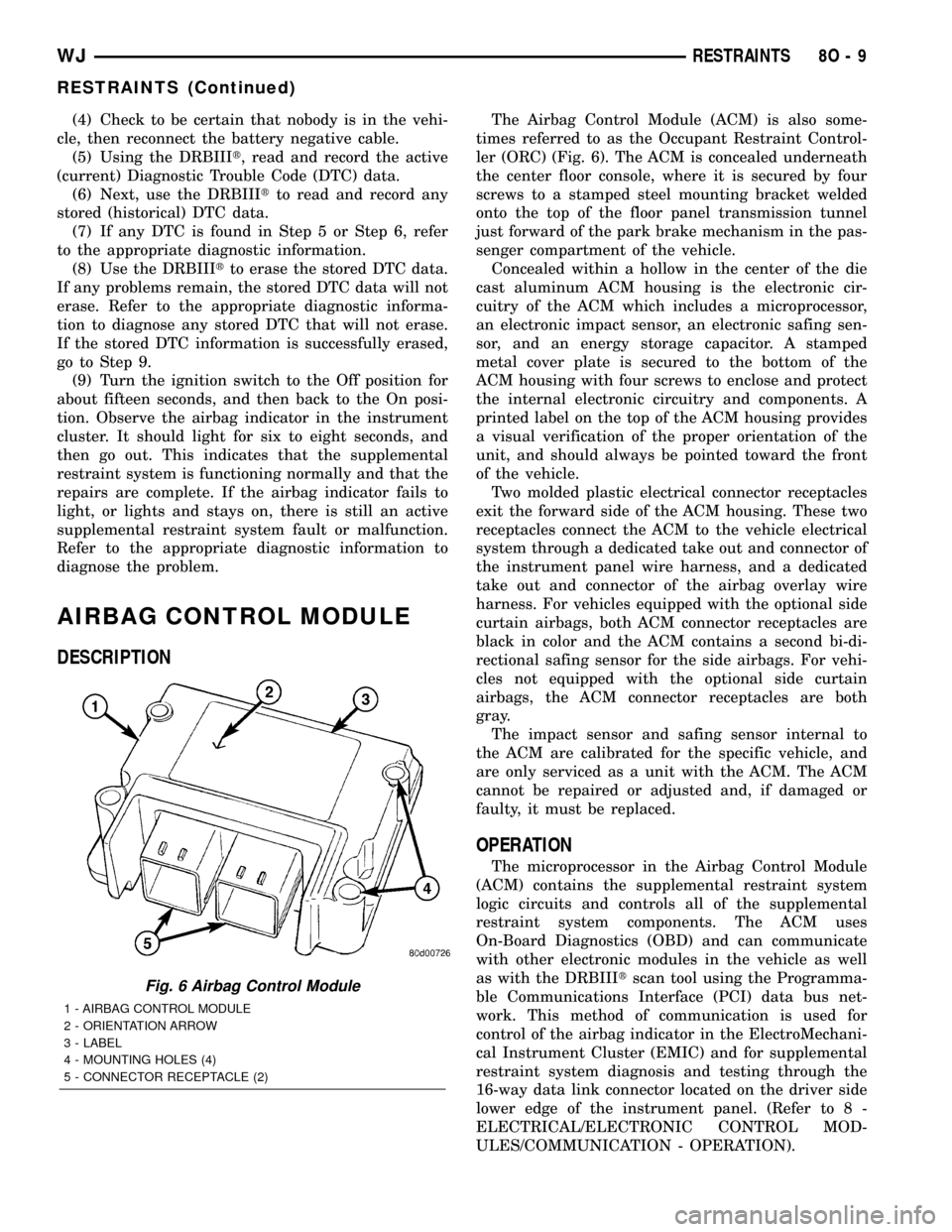
(4) Check to be certain that nobody is in the vehi-
cle, then reconnect the battery negative cable.
(5) Using the DRBIIIt, read and record the active
(current) Diagnostic Trouble Code (DTC) data.
(6) Next, use the DRBIIItto read and record any
stored (historical) DTC data.
(7) If any DTC is found in Step 5 or Step 6, refer
to the appropriate diagnostic information.
(8) Use the DRBIIItto erase the stored DTC data.
If any problems remain, the stored DTC data will not
erase. Refer to the appropriate diagnostic informa-
tion to diagnose any stored DTC that will not erase.
If the stored DTC information is successfully erased,
go to Step 9.
(9) Turn the ignition switch to the Off position for
about fifteen seconds, and then back to the On posi-
tion. Observe the airbag indicator in the instrument
cluster. It should light for six to eight seconds, and
then go out. This indicates that the supplemental
restraint system is functioning normally and that the
repairs are complete. If the airbag indicator fails to
light, or lights and stays on, there is still an active
supplemental restraint system fault or malfunction.
Refer to the appropriate diagnostic information to
diagnose the problem.
AIRBAG CONTROL MODULE
DESCRIPTION
The Airbag Control Module (ACM) is also some-
times referred to as the Occupant Restraint Control-
ler (ORC) (Fig. 6). The ACM is concealed underneath
the center floor console, where it is secured by four
screws to a stamped steel mounting bracket welded
onto the top of the floor panel transmission tunnel
just forward of the park brake mechanism in the pas-
senger compartment of the vehicle.
Concealed within a hollow in the center of the die
cast aluminum ACM housing is the electronic cir-
cuitry of the ACM which includes a microprocessor,
an electronic impact sensor, an electronic safing sen-
sor, and an energy storage capacitor. A stamped
metal cover plate is secured to the bottom of the
ACM housing with four screws to enclose and protect
the internal electronic circuitry and components. A
printed label on the top of the ACM housing provides
a visual verification of the proper orientation of the
unit, and should always be pointed toward the front
of the vehicle.
Two molded plastic electrical connector receptacles
exit the forward side of the ACM housing. These two
receptacles connect the ACM to the vehicle electrical
system through a dedicated take out and connector of
the instrument panel wire harness, and a dedicated
take out and connector of the airbag overlay wire
harness. For vehicles equipped with the optional side
curtain airbags, both ACM connector receptacles are
black in color and the ACM contains a second bi-di-
rectional safing sensor for the side airbags. For vehi-
cles not equipped with the optional side curtain
airbags, the ACM connector receptacles are both
gray.
The impact sensor and safing sensor internal to
the ACM are calibrated for the specific vehicle, and
are only serviced as a unit with the ACM. The ACM
cannot be repaired or adjusted and, if damaged or
faulty, it must be replaced.
OPERATION
The microprocessor in the Airbag Control Module
(ACM) contains the supplemental restraint system
logic circuits and controls all of the supplemental
restraint system components. The ACM uses
On-Board Diagnostics (OBD) and can communicate
with other electronic modules in the vehicle as well
as with the DRBIIItscan tool using the Programma-
ble Communications Interface (PCI) data bus net-
work. This method of communication is used for
control of the airbag indicator in the ElectroMechani-
cal Instrument Cluster (EMIC) and for supplemental
restraint system diagnosis and testing through the
16-way data link connector located on the driver side
lower edge of the instrument panel. (Refer to 8 -
ELECTRICAL/ELECTRONIC CONTROL MOD-
ULES/COMMUNICATION - OPERATION).
Fig. 6 Airbag Control Module
1 - AIRBAG CONTROL MODULE
2 - ORIENTATION ARROW
3 - LABEL
4 - MOUNTING HOLES (4)
5 - CONNECTOR RECEPTACLE (2)
WJRESTRAINTS 8O - 9
RESTRAINTS (Continued)
Page 547 of 2199
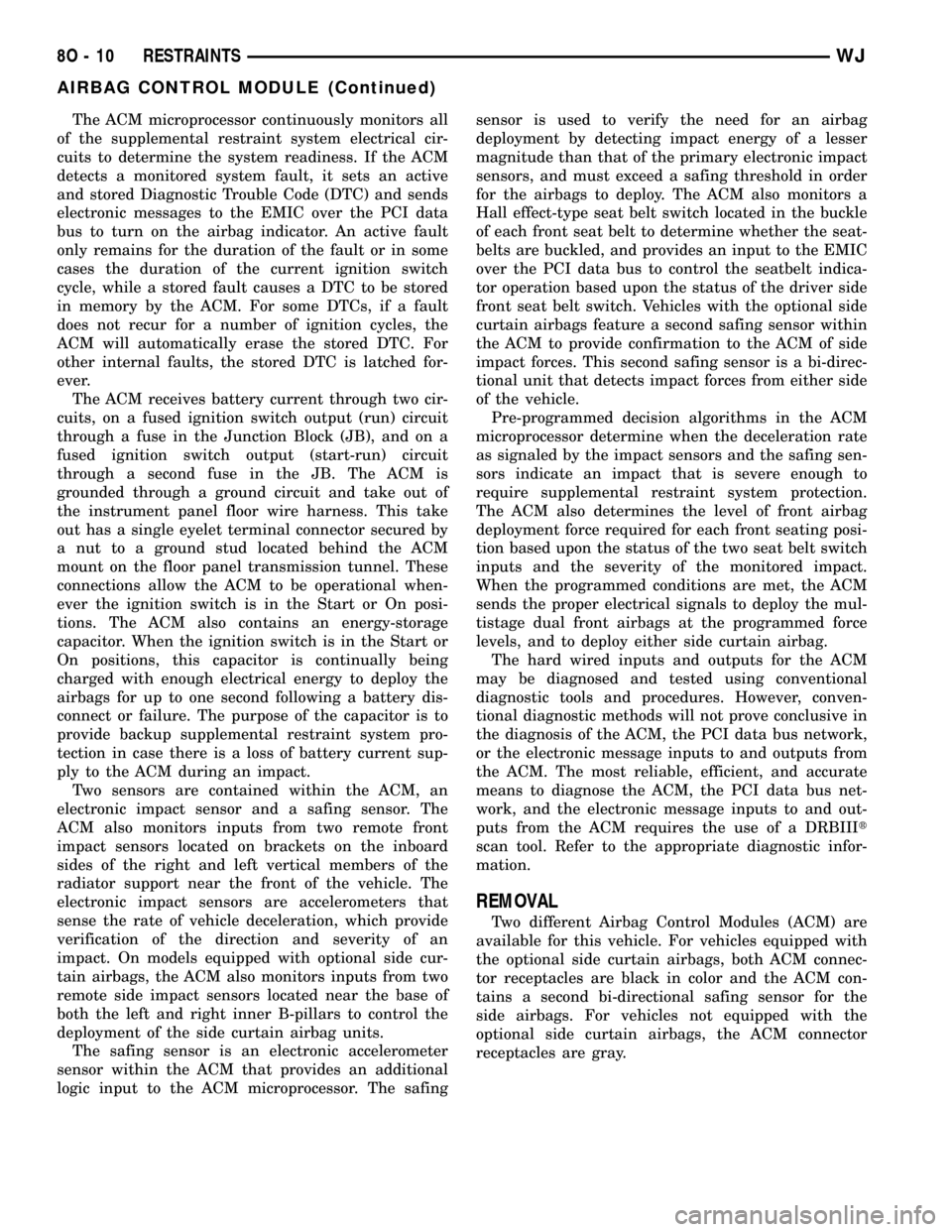
The ACM microprocessor continuously monitors all
of the supplemental restraint system electrical cir-
cuits to determine the system readiness. If the ACM
detects a monitored system fault, it sets an active
and stored Diagnostic Trouble Code (DTC) and sends
electronic messages to the EMIC over the PCI data
bus to turn on the airbag indicator. An active fault
only remains for the duration of the fault or in some
cases the duration of the current ignition switch
cycle, while a stored fault causes a DTC to be stored
in memory by the ACM. For some DTCs, if a fault
does not recur for a number of ignition cycles, the
ACM will automatically erase the stored DTC. For
other internal faults, the stored DTC is latched for-
ever.
The ACM receives battery current through two cir-
cuits, on a fused ignition switch output (run) circuit
through a fuse in the Junction Block (JB), and on a
fused ignition switch output (start-run) circuit
through a second fuse in the JB. The ACM is
grounded through a ground circuit and take out of
the instrument panel floor wire harness. This take
out has a single eyelet terminal connector secured by
a nut to a ground stud located behind the ACM
mount on the floor panel transmission tunnel. These
connections allow the ACM to be operational when-
ever the ignition switch is in the Start or On posi-
tions. The ACM also contains an energy-storage
capacitor. When the ignition switch is in the Start or
On positions, this capacitor is continually being
charged with enough electrical energy to deploy the
airbags for up to one second following a battery dis-
connect or failure. The purpose of the capacitor is to
provide backup supplemental restraint system pro-
tection in case there is a loss of battery current sup-
ply to the ACM during an impact.
Two sensors are contained within the ACM, an
electronic impact sensor and a safing sensor. The
ACM also monitors inputs from two remote front
impact sensors located on brackets on the inboard
sides of the right and left vertical members of the
radiator support near the front of the vehicle. The
electronic impact sensors are accelerometers that
sense the rate of vehicle deceleration, which provide
verification of the direction and severity of an
impact. On models equipped with optional side cur-
tain airbags, the ACM also monitors inputs from two
remote side impact sensors located near the base of
both the left and right inner B-pillars to control the
deployment of the side curtain airbag units.
The safing sensor is an electronic accelerometer
sensor within the ACM that provides an additional
logic input to the ACM microprocessor. The safingsensor is used to verify the need for an airbag
deployment by detecting impact energy of a lesser
magnitude than that of the primary electronic impact
sensors, and must exceed a safing threshold in order
for the airbags to deploy. The ACM also monitors a
Hall effect-type seat belt switch located in the buckle
of each front seat belt to determine whether the seat-
belts are buckled, and provides an input to the EMIC
over the PCI data bus to control the seatbelt indica-
tor operation based upon the status of the driver side
front seat belt switch. Vehicles with the optional side
curtain airbags feature a second safing sensor within
the ACM to provide confirmation to the ACM of side
impact forces. This second safing sensor is a bi-direc-
tional unit that detects impact forces from either side
of the vehicle.
Pre-programmed decision algorithms in the ACM
microprocessor determine when the deceleration rate
as signaled by the impact sensors and the safing sen-
sors indicate an impact that is severe enough to
require supplemental restraint system protection.
The ACM also determines the level of front airbag
deployment force required for each front seating posi-
tion based upon the status of the two seat belt switch
inputs and the severity of the monitored impact.
When the programmed conditions are met, the ACM
sends the proper electrical signals to deploy the mul-
tistage dual front airbags at the programmed force
levels, and to deploy either side curtain airbag.
The hard wired inputs and outputs for the ACM
may be diagnosed and tested using conventional
diagnostic tools and procedures. However, conven-
tional diagnostic methods will not prove conclusive in
the diagnosis of the ACM, the PCI data bus network,
or the electronic message inputs to and outputs from
the ACM. The most reliable, efficient, and accurate
means to diagnose the ACM, the PCI data bus net-
work, and the electronic message inputs to and out-
puts from the ACM requires the use of a DRBIIIt
scan tool. Refer to the appropriate diagnostic infor-
mation.
REMOVAL
Two different Airbag Control Modules (ACM) are
available for this vehicle. For vehicles equipped with
the optional side curtain airbags, both ACM connec-
tor receptacles are black in color and the ACM con-
tains a second bi-directional safing sensor for the
side airbags. For vehicles not equipped with the
optional side curtain airbags, the ACM connector
receptacles are gray.
8O - 10 RESTRAINTSWJ
AIRBAG CONTROL MODULE (Continued)
Page 555 of 2199
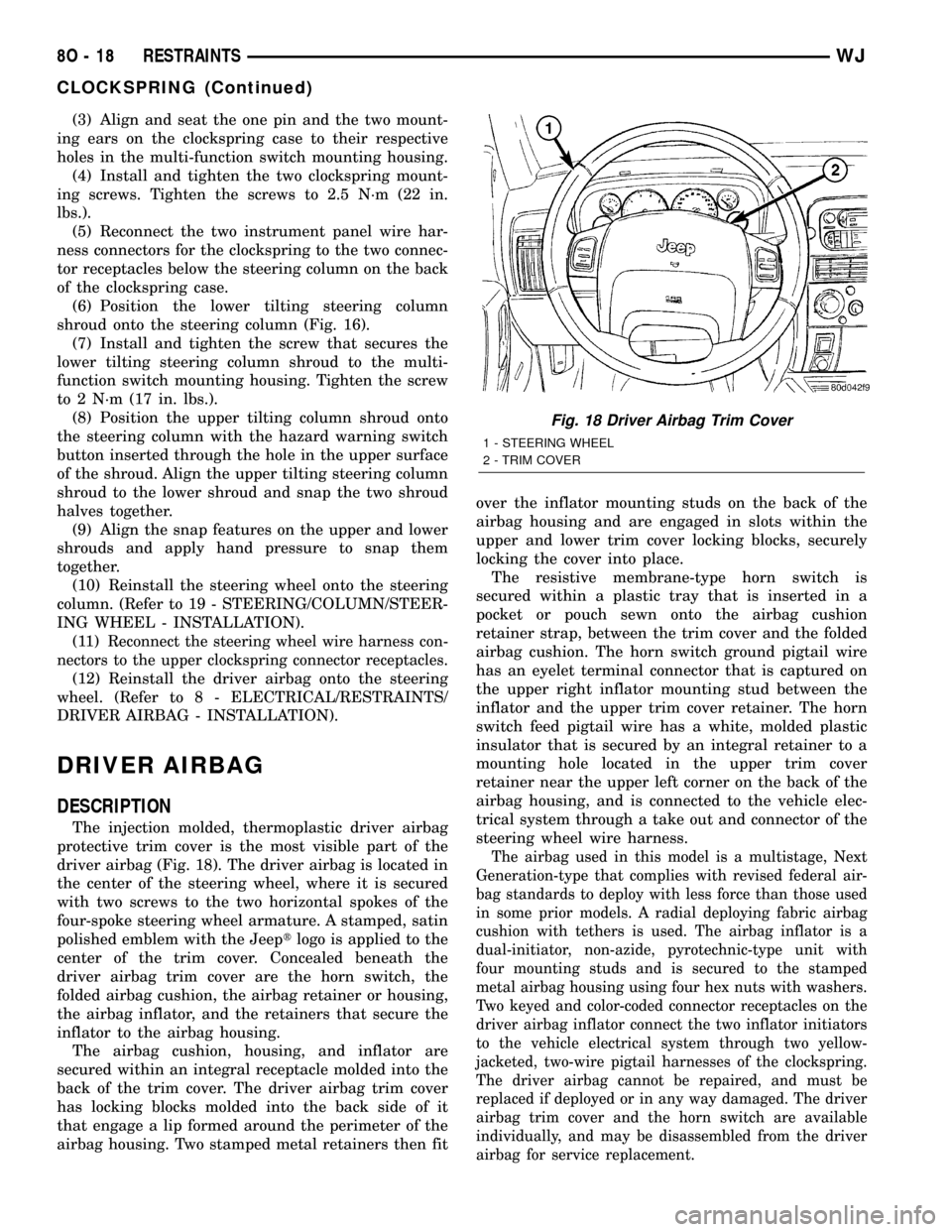
(3) Align and seat the one pin and the two mount-
ing ears on the clockspring case to their respective
holes in the multi-function switch mounting housing.
(4) Install and tighten the two clockspring mount-
ing screws. Tighten the screws to 2.5 N´m (22 in.
lbs.).
(5) Reconnect the two instrument panel wire har-
ness connectors for the clockspring to the two connec-
tor receptacles below the steering column on the back
of the clockspring case.
(6) Position the lower tilting steering column
shroud onto the steering column (Fig. 16).
(7) Install and tighten the screw that secures the
lower tilting steering column shroud to the multi-
function switch mounting housing. Tighten the screw
to 2 N´m (17 in. lbs.).
(8) Position the upper tilting column shroud onto
the steering column with the hazard warning switch
button inserted through the hole in the upper surface
of the shroud. Align the upper tilting steering column
shroud to the lower shroud and snap the two shroud
halves together.
(9) Align the snap features on the upper and lower
shrouds and apply hand pressure to snap them
together.
(10) Reinstall the steering wheel onto the steering
column. (Refer to 19 - STEERING/COLUMN/STEER-
ING WHEEL - INSTALLATION).
(11)
Reconnect the steering wheel wire harness con-
nectors to the upper clockspring connector receptacles.
(12) Reinstall the driver airbag onto the steering
wheel. (Refer to 8 - ELECTRICAL/RESTRAINTS/
DRIVER AIRBAG - INSTALLATION).
DRIVER AIRBAG
DESCRIPTION
The injection molded, thermoplastic driver airbag
protective trim cover is the most visible part of the
driver airbag (Fig. 18). The driver airbag is located in
the center of the steering wheel, where it is secured
with two screws to the two horizontal spokes of the
four-spoke steering wheel armature. A stamped, satin
polished emblem with the Jeeptlogo is applied to the
center of the trim cover. Concealed beneath the
driver airbag trim cover are the horn switch, the
folded airbag cushion, the airbag retainer or housing,
the airbag inflator, and the retainers that secure the
inflator to the airbag housing.
The airbag cushion, housing, and inflator are
secured within an integral receptacle molded into the
back of the trim cover. The driver airbag trim cover
has locking blocks molded into the back side of it
that engage a lip formed around the perimeter of the
airbag housing. Two stamped metal retainers then fitover the inflator mounting studs on the back of the
airbag housing and are engaged in slots within the
upper and lower trim cover locking blocks, securely
locking the cover into place.
The resistive membrane-type horn switch is
secured within a plastic tray that is inserted in a
pocket or pouch sewn onto the airbag cushion
retainer strap, between the trim cover and the folded
airbag cushion. The horn switch ground pigtail wire
has an eyelet terminal connector that is captured on
the upper right inflator mounting stud between the
inflator and the upper trim cover retainer. The horn
switch feed pigtail wire has a white, molded plastic
insulator that is secured by an integral retainer to a
mounting hole located in the upper trim cover
retainer near the upper left corner on the back of the
airbag housing, and is connected to the vehicle elec-
trical system through a take out and connector of the
steering wheel wire harness.
The airbag used in this model is a multistage, Next
Generation-type that complies with revised federal air-
bag standards to deploy with less force than those used
in some prior models. A radial deploying fabric airbag
cushion with tethers is used. The airbag inflator is a
dual-initiator, non-azide, pyrotechnic-type unit with
four mounting studs and is secured to the stamped
metal airbag housing using four hex nuts with washers.
Two keyed and color-coded connector receptacles on the
driver airbag inflator connect the two inflator initiators
to the vehicle electrical system through two yellow-
jacketed, two-wire pigtail harnesses of the clockspring.
The driver airbag cannot be repaired, and must be
replaced if deployed or in any way damaged. The driver
airbag trim cover and the horn switch are available
individually, and may be disassembled from the driver
airbag for service replacement.
Fig. 18 Driver Airbag Trim Cover
1 - STEERING WHEEL
2 - TRIM COVER
8O - 18 RESTRAINTSWJ
CLOCKSPRING (Continued)
Page 561 of 2199
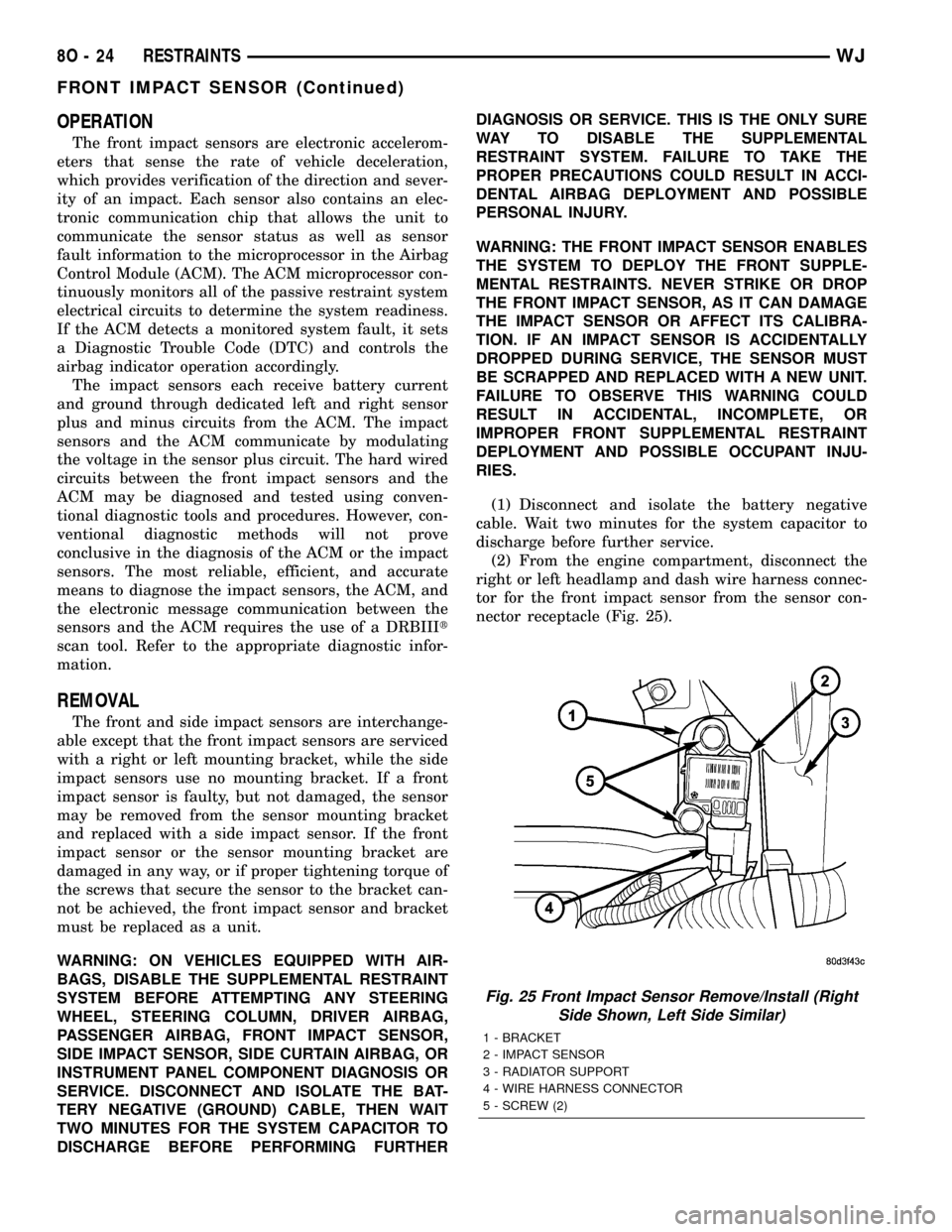
OPERATION
The front impact sensors are electronic accelerom-
eters that sense the rate of vehicle deceleration,
which provides verification of the direction and sever-
ity of an impact. Each sensor also contains an elec-
tronic communication chip that allows the unit to
communicate the sensor status as well as sensor
fault information to the microprocessor in the Airbag
Control Module (ACM). The ACM microprocessor con-
tinuously monitors all of the passive restraint system
electrical circuits to determine the system readiness.
If the ACM detects a monitored system fault, it sets
a Diagnostic Trouble Code (DTC) and controls the
airbag indicator operation accordingly.
The impact sensors each receive battery current
and ground through dedicated left and right sensor
plus and minus circuits from the ACM. The impact
sensors and the ACM communicate by modulating
the voltage in the sensor plus circuit. The hard wired
circuits between the front impact sensors and the
ACM may be diagnosed and tested using conven-
tional diagnostic tools and procedures. However, con-
ventional diagnostic methods will not prove
conclusive in the diagnosis of the ACM or the impact
sensors. The most reliable, efficient, and accurate
means to diagnose the impact sensors, the ACM, and
the electronic message communication between the
sensors and the ACM requires the use of a DRBIIIt
scan tool. Refer to the appropriate diagnostic infor-
mation.
REMOVAL
The front and side impact sensors are interchange-
able except that the front impact sensors are serviced
with a right or left mounting bracket, while the side
impact sensors use no mounting bracket. If a front
impact sensor is faulty, but not damaged, the sensor
may be removed from the sensor mounting bracket
and replaced with a side impact sensor. If the front
impact sensor or the sensor mounting bracket are
damaged in any way, or if proper tightening torque of
the screws that secure the sensor to the bracket can-
not be achieved, the front impact sensor and bracket
must be replaced as a unit.
WARNING: ON VEHICLES EQUIPPED WITH AIR-
BAGS, DISABLE THE SUPPLEMENTAL RESTRAINT
SYSTEM BEFORE ATTEMPTING ANY STEERING
WHEEL, STEERING COLUMN, DRIVER AIRBAG,
PASSENGER AIRBAG, FRONT IMPACT SENSOR,
SIDE IMPACT SENSOR, SIDE CURTAIN AIRBAG, OR
INSTRUMENT PANEL COMPONENT DIAGNOSIS OR
SERVICE. DISCONNECT AND ISOLATE THE BAT-
TERY NEGATIVE (GROUND) CABLE, THEN WAIT
TWO MINUTES FOR THE SYSTEM CAPACITOR TO
DISCHARGE BEFORE PERFORMING FURTHERDIAGNOSIS OR SERVICE. THIS IS THE ONLY SURE
WAY TO DISABLE THE SUPPLEMENTAL
RESTRAINT SYSTEM. FAILURE TO TAKE THE
PROPER PRECAUTIONS COULD RESULT IN ACCI-
DENTAL AIRBAG DEPLOYMENT AND POSSIBLE
PERSONAL INJURY.
WARNING: THE FRONT IMPACT SENSOR ENABLES
THE SYSTEM TO DEPLOY THE FRONT SUPPLE-
MENTAL RESTRAINTS. NEVER STRIKE OR DROP
THE FRONT IMPACT SENSOR, AS IT CAN DAMAGE
THE IMPACT SENSOR OR AFFECT ITS CALIBRA-
TION. IF AN IMPACT SENSOR IS ACCIDENTALLY
DROPPED DURING SERVICE, THE SENSOR MUST
BE SCRAPPED AND REPLACED WITH A NEW UNIT.
FAILURE TO OBSERVE THIS WARNING COULD
RESULT IN ACCIDENTAL, INCOMPLETE, OR
IMPROPER FRONT SUPPLEMENTAL RESTRAINT
DEPLOYMENT AND POSSIBLE OCCUPANT INJU-
RIES.
(1) Disconnect and isolate the battery negative
cable. Wait two minutes for the system capacitor to
discharge before further service.
(2) From the engine compartment, disconnect the
right or left headlamp and dash wire harness connec-
tor for the front impact sensor from the sensor con-
nector receptacle (Fig. 25).
Fig. 25 Front Impact Sensor Remove/Install (Right
Side Shown, Left Side Similar)
1 - BRACKET
2 - IMPACT SENSOR
3 - RADIATOR SUPPORT
4 - WIRE HARNESS CONNECTOR
5 - SCREW (2)
8O - 24 RESTRAINTSWJ
FRONT IMPACT SENSOR (Continued)
Page 574 of 2199
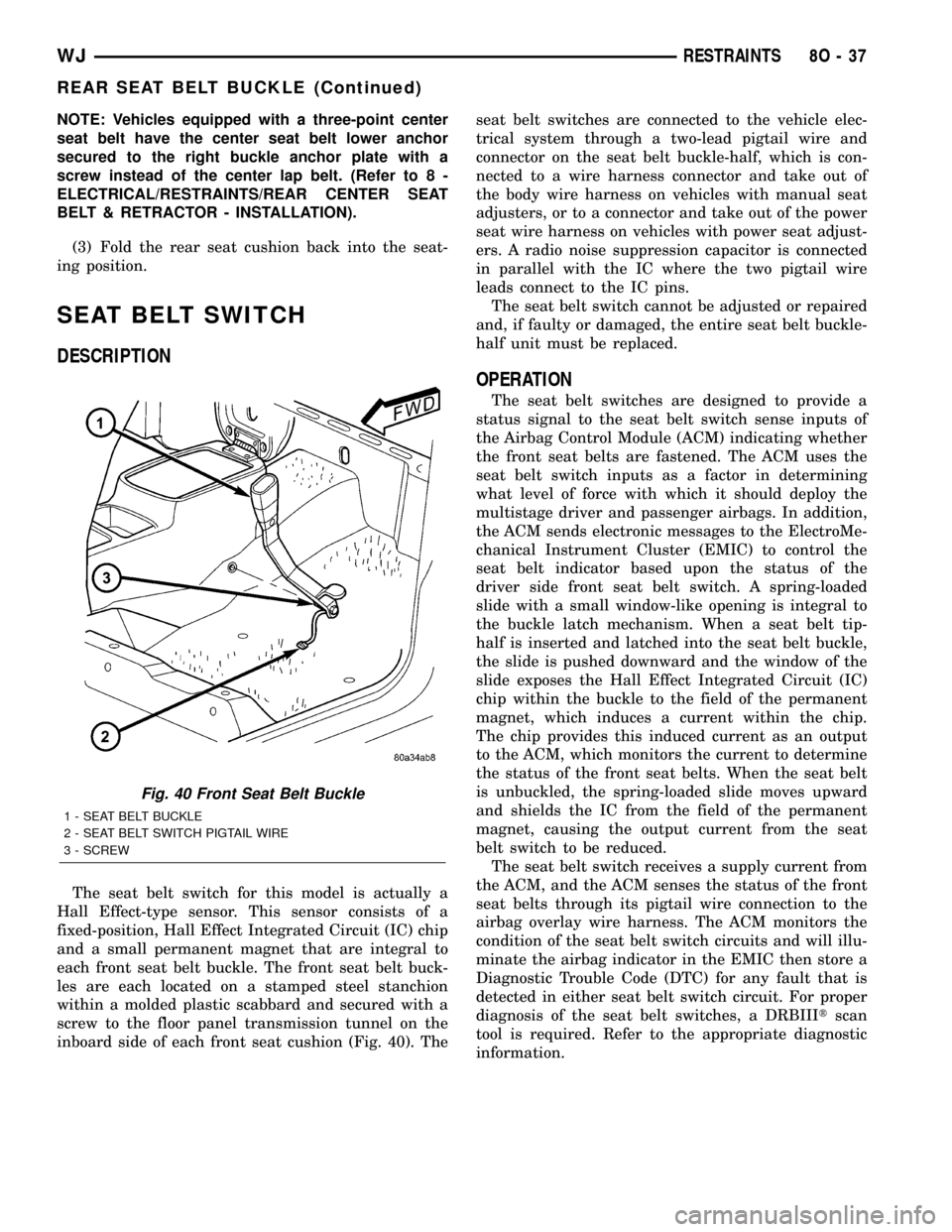
NOTE: Vehicles equipped with a three-point center
seat belt have the center seat belt lower anchor
secured to the right buckle anchor plate with a
screw instead of the center lap belt. (Refer to 8 -
ELECTRICAL/RESTRAINTS/REAR CENTER SEAT
BELT & RETRACTOR - INSTALLATION).
(3) Fold the rear seat cushion back into the seat-
ing position.
SEAT BELT SWITCH
DESCRIPTION
The seat belt switch for this model is actually a
Hall Effect-type sensor. This sensor consists of a
fixed-position, Hall Effect Integrated Circuit (IC) chip
and a small permanent magnet that are integral to
each front seat belt buckle. The front seat belt buck-
les are each located on a stamped steel stanchion
within a molded plastic scabbard and secured with a
screw to the floor panel transmission tunnel on the
inboard side of each front seat cushion (Fig. 40). Theseat belt switches are connected to the vehicle elec-
trical system through a two-lead pigtail wire and
connector on the seat belt buckle-half, which is con-
nected to a wire harness connector and take out of
the body wire harness on vehicles with manual seat
adjusters, or to a connector and take out of the power
seat wire harness on vehicles with power seat adjust-
ers. A radio noise suppression capacitor is connected
in parallel with the IC where the two pigtail wire
leads connect to the IC pins.
The seat belt switch cannot be adjusted or repaired
and, if faulty or damaged, the entire seat belt buckle-
half unit must be replaced.
OPERATION
The seat belt switches are designed to provide a
status signal to the seat belt switch sense inputs of
the Airbag Control Module (ACM) indicating whether
the front seat belts are fastened. The ACM uses the
seat belt switch inputs as a factor in determining
what level of force with which it should deploy the
multistage driver and passenger airbags. In addition,
the ACM sends electronic messages to the ElectroMe-
chanical Instrument Cluster (EMIC) to control the
seat belt indicator based upon the status of the
driver side front seat belt switch. A spring-loaded
slide with a small window-like opening is integral to
the buckle latch mechanism. When a seat belt tip-
half is inserted and latched into the seat belt buckle,
the slide is pushed downward and the window of the
slide exposes the Hall Effect Integrated Circuit (IC)
chip within the buckle to the field of the permanent
magnet, which induces a current within the chip.
The chip provides this induced current as an output
to the ACM, which monitors the current to determine
the status of the front seat belts. When the seat belt
is unbuckled, the spring-loaded slide moves upward
and shields the IC from the field of the permanent
magnet, causing the output current from the seat
belt switch to be reduced.
The seat belt switch receives a supply current from
the ACM, and the ACM senses the status of the front
seat belts through its pigtail wire connection to the
airbag overlay wire harness. The ACM monitors the
condition of the seat belt switch circuits and will illu-
minate the airbag indicator in the EMIC then store a
Diagnostic Trouble Code (DTC) for any fault that is
detected in either seat belt switch circuit. For proper
diagnosis of the seat belt switches, a DRBIIItscan
tool is required. Refer to the appropriate diagnostic
information.
Fig. 40 Front Seat Belt Buckle
1 - SEAT BELT BUCKLE
2 - SEAT BELT SWITCH PIGTAIL WIRE
3 - SCREW
WJRESTRAINTS 8O - 37
REAR SEAT BELT BUCKLE (Continued)
Page 580 of 2199
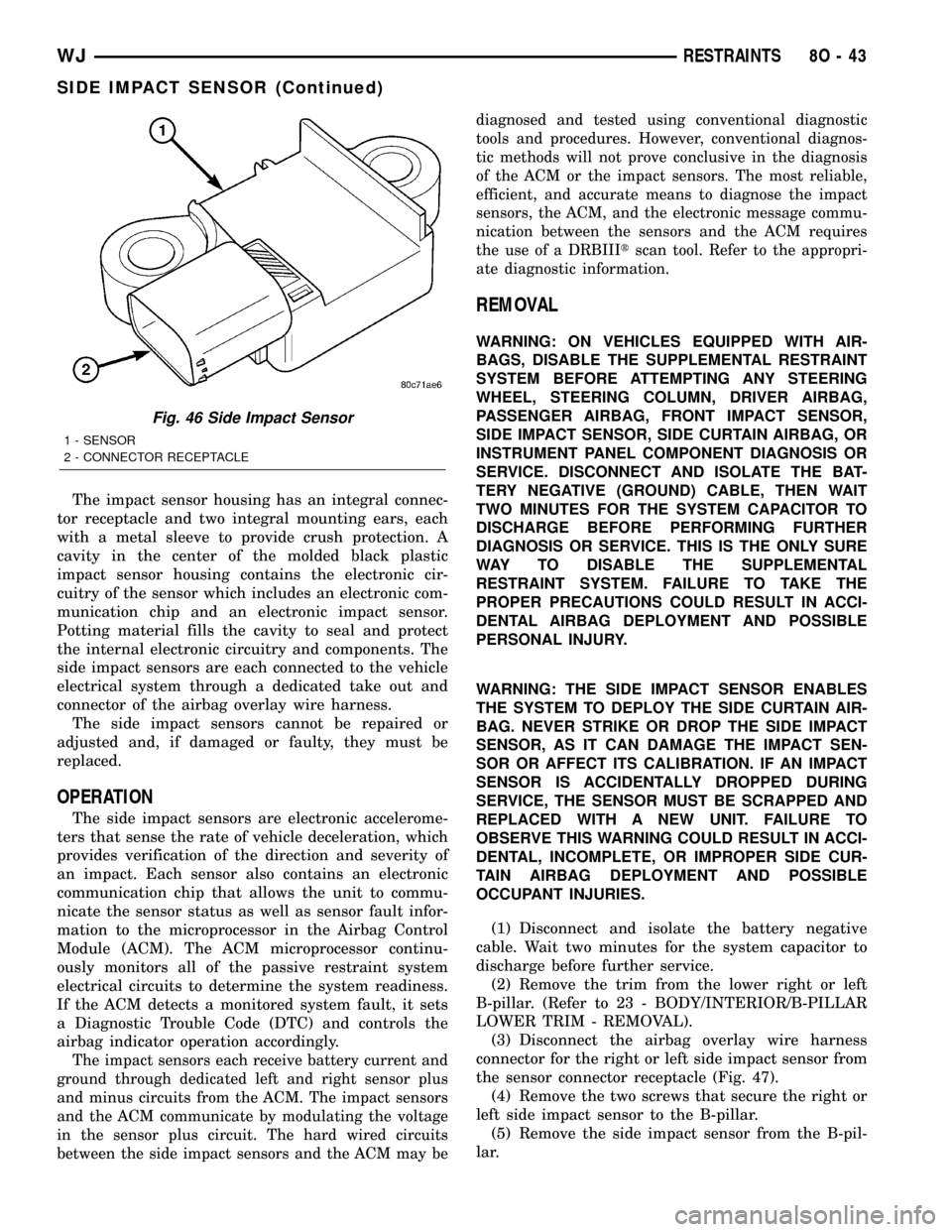
The impact sensor housing has an integral connec-
tor receptacle and two integral mounting ears, each
with a metal sleeve to provide crush protection. A
cavity in the center of the molded black plastic
impact sensor housing contains the electronic cir-
cuitry of the sensor which includes an electronic com-
munication chip and an electronic impact sensor.
Potting material fills the cavity to seal and protect
the internal electronic circuitry and components. The
side impact sensors are each connected to the vehicle
electrical system through a dedicated take out and
connector of the airbag overlay wire harness.
The side impact sensors cannot be repaired or
adjusted and, if damaged or faulty, they must be
replaced.
OPERATION
The side impact sensors are electronic accelerome-
ters that sense the rate of vehicle deceleration, which
provides verification of the direction and severity of
an impact. Each sensor also contains an electronic
communication chip that allows the unit to commu-
nicate the sensor status as well as sensor fault infor-
mation to the microprocessor in the Airbag Control
Module (ACM). The ACM microprocessor continu-
ously monitors all of the passive restraint system
electrical circuits to determine the system readiness.
If the ACM detects a monitored system fault, it sets
a Diagnostic Trouble Code (DTC) and controls the
airbag indicator operation accordingly.
The impact sensors each receive battery current and
ground through dedicated left and right sensor plus
and minus circuits from the ACM. The impact sensors
and the ACM communicate by modulating the voltage
in the sensor plus circuit. The hard wired circuits
between the side impact sensors and the ACM may bediagnosed and tested using conventional diagnostic
tools and procedures. However, conventional diagnos-
tic methods will not prove conclusive in the diagnosis
of the ACM or the impact sensors. The most reliable,
efficient, and accurate means to diagnose the impact
sensors, the ACM, and the electronic message commu-
nication between the sensors and the ACM requires
the use of a DRBIIItscan tool. Refer to the appropri-
ate diagnostic information.
REMOVAL
WARNING: ON VEHICLES EQUIPPED WITH AIR-
BAGS, DISABLE THE SUPPLEMENTAL RESTRAINT
SYSTEM BEFORE ATTEMPTING ANY STEERING
WHEEL, STEERING COLUMN, DRIVER AIRBAG,
PASSENGER AIRBAG, FRONT IMPACT SENSOR,
SIDE IMPACT SENSOR, SIDE CURTAIN AIRBAG, OR
INSTRUMENT PANEL COMPONENT DIAGNOSIS OR
SERVICE. DISCONNECT AND ISOLATE THE BAT-
TERY NEGATIVE (GROUND) CABLE, THEN WAIT
TWO MINUTES FOR THE SYSTEM CAPACITOR TO
DISCHARGE BEFORE PERFORMING FURTHER
DIAGNOSIS OR SERVICE. THIS IS THE ONLY SURE
WAY TO DISABLE THE SUPPLEMENTAL
RESTRAINT SYSTEM. FAILURE TO TAKE THE
PROPER PRECAUTIONS COULD RESULT IN ACCI-
DENTAL AIRBAG DEPLOYMENT AND POSSIBLE
PERSONAL INJURY.
WARNING: THE SIDE IMPACT SENSOR ENABLES
THE SYSTEM TO DEPLOY THE SIDE CURTAIN AIR-
BAG. NEVER STRIKE OR DROP THE SIDE IMPACT
SENSOR, AS IT CAN DAMAGE THE IMPACT SEN-
SOR OR AFFECT ITS CALIBRATION. IF AN IMPACT
SENSOR IS ACCIDENTALLY DROPPED DURING
SERVICE, THE SENSOR MUST BE SCRAPPED AND
REPLACED WITH A NEW UNIT. FAILURE TO
OBSERVE THIS WARNING COULD RESULT IN ACCI-
DENTAL, INCOMPLETE, OR IMPROPER SIDE CUR-
TAIN AIRBAG DEPLOYMENT AND POSSIBLE
OCCUPANT INJURIES.
(1) Disconnect and isolate the battery negative
cable. Wait two minutes for the system capacitor to
discharge before further service.
(2) Remove the trim from the lower right or left
B-pillar. (Refer to 23 - BODY/INTERIOR/B-PILLAR
LOWER TRIM - REMOVAL).
(3) Disconnect the airbag overlay wire harness
connector for the right or left side impact sensor from
the sensor connector receptacle (Fig. 47).
(4) Remove the two screws that secure the right or
left side impact sensor to the B-pillar.
(5) Remove the side impact sensor from the B-pil-
lar.
Fig. 46 Side Impact Sensor
1 - SENSOR
2 - CONNECTOR RECEPTACLE
WJRESTRAINTS 8O - 43
SIDE IMPACT SENSOR (Continued)
Page 583 of 2199
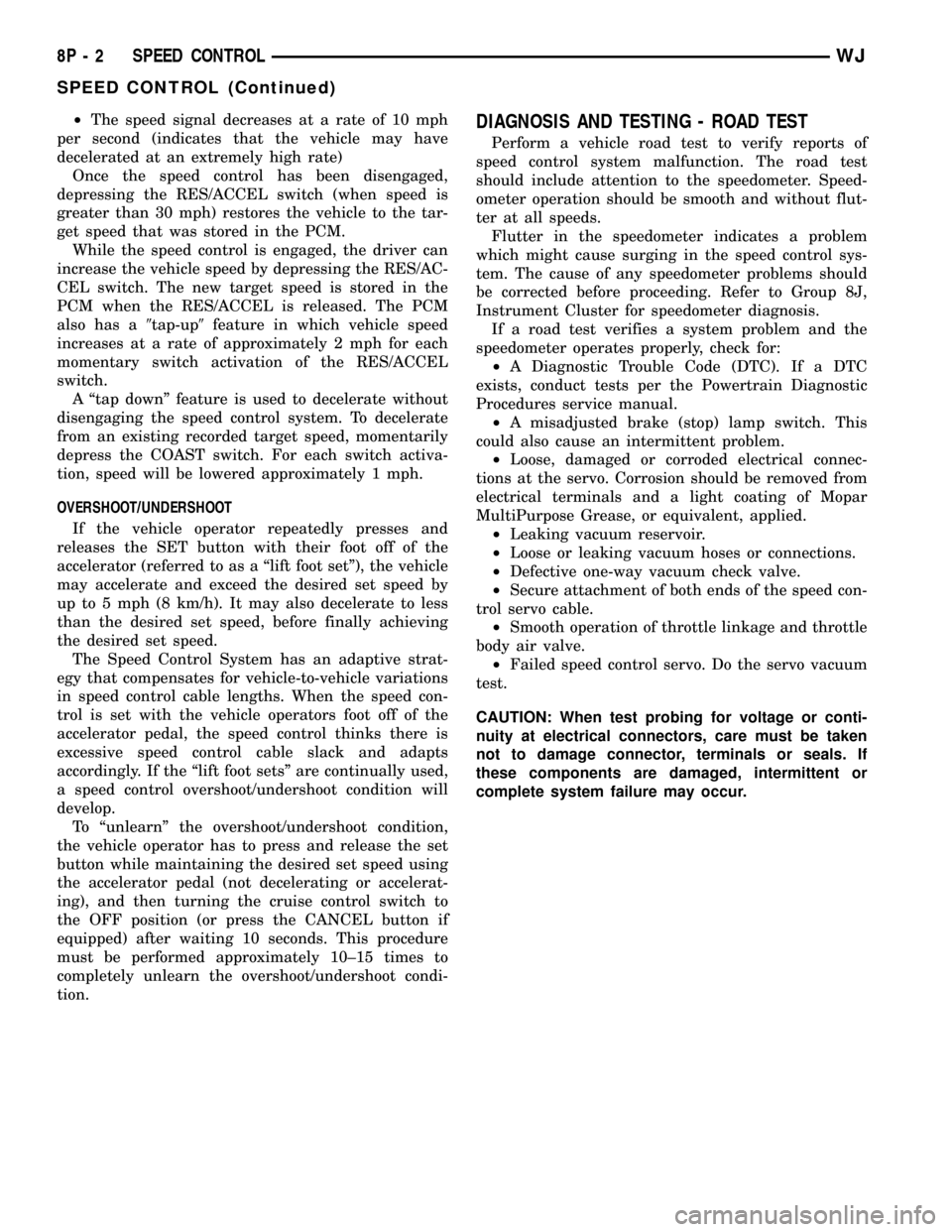
²The speed signal decreases at a rate of 10 mph
per second (indicates that the vehicle may have
decelerated at an extremely high rate)
Once the speed control has been disengaged,
depressing the RES/ACCEL switch (when speed is
greater than 30 mph) restores the vehicle to the tar-
get speed that was stored in the PCM.
While the speed control is engaged, the driver can
increase the vehicle speed by depressing the RES/AC-
CEL switch. The new target speed is stored in the
PCM when the RES/ACCEL is released. The PCM
also has a9tap-up9feature in which vehicle speed
increases at a rate of approximately 2 mph for each
momentary switch activation of the RES/ACCEL
switch.
A ªtap downº feature is used to decelerate without
disengaging the speed control system. To decelerate
from an existing recorded target speed, momentarily
depress the COAST switch. For each switch activa-
tion, speed will be lowered approximately 1 mph.
OVERSHOOT/UNDERSHOOT
If the vehicle operator repeatedly presses and
releases the SET button with their foot off of the
accelerator (referred to as a ªlift foot setº), the vehicle
may accelerate and exceed the desired set speed by
up to 5 mph (8 km/h). It may also decelerate to less
than the desired set speed, before finally achieving
the desired set speed.
The Speed Control System has an adaptive strat-
egy that compensates for vehicle-to-vehicle variations
in speed control cable lengths. When the speed con-
trol is set with the vehicle operators foot off of the
accelerator pedal, the speed control thinks there is
excessive speed control cable slack and adapts
accordingly. If the ªlift foot setsº are continually used,
a speed control overshoot/undershoot condition will
develop.
To ªunlearnº the overshoot/undershoot condition,
the vehicle operator has to press and release the set
button while maintaining the desired set speed using
the accelerator pedal (not decelerating or accelerat-
ing), and then turning the cruise control switch to
the OFF position (or press the CANCEL button if
equipped) after waiting 10 seconds. This procedure
must be performed approximately 10±15 times to
completely unlearn the overshoot/undershoot condi-
tion.DIAGNOSIS AND TESTING - ROAD TEST
Perform a vehicle road test to verify reports of
speed control system malfunction. The road test
should include attention to the speedometer. Speed-
ometer operation should be smooth and without flut-
ter at all speeds.
Flutter in the speedometer indicates a problem
which might cause surging in the speed control sys-
tem. The cause of any speedometer problems should
be corrected before proceeding. Refer to Group 8J,
Instrument Cluster for speedometer diagnosis.
If a road test verifies a system problem and the
speedometer operates properly, check for:
²A Diagnostic Trouble Code (DTC). If a DTC
exists, conduct tests per the Powertrain Diagnostic
Procedures service manual.
²A misadjusted brake (stop) lamp switch. This
could also cause an intermittent problem.
²Loose, damaged or corroded electrical connec-
tions at the servo. Corrosion should be removed from
electrical terminals and a light coating of Mopar
MultiPurpose Grease, or equivalent, applied.
²Leaking vacuum reservoir.
²Loose or leaking vacuum hoses or connections.
²Defective one-way vacuum check valve.
²Secure attachment of both ends of the speed con-
trol servo cable.
²Smooth operation of throttle linkage and throttle
body air valve.
²Failed speed control servo. Do the servo vacuum
test.
CAUTION: When test probing for voltage or conti-
nuity at electrical connectors, care must be taken
not to damage connector, terminals or seals. If
these components are damaged, intermittent or
complete system failure may occur.
8P - 2 SPEED CONTROLWJ
SPEED CONTROL (Continued)
Page 592 of 2199
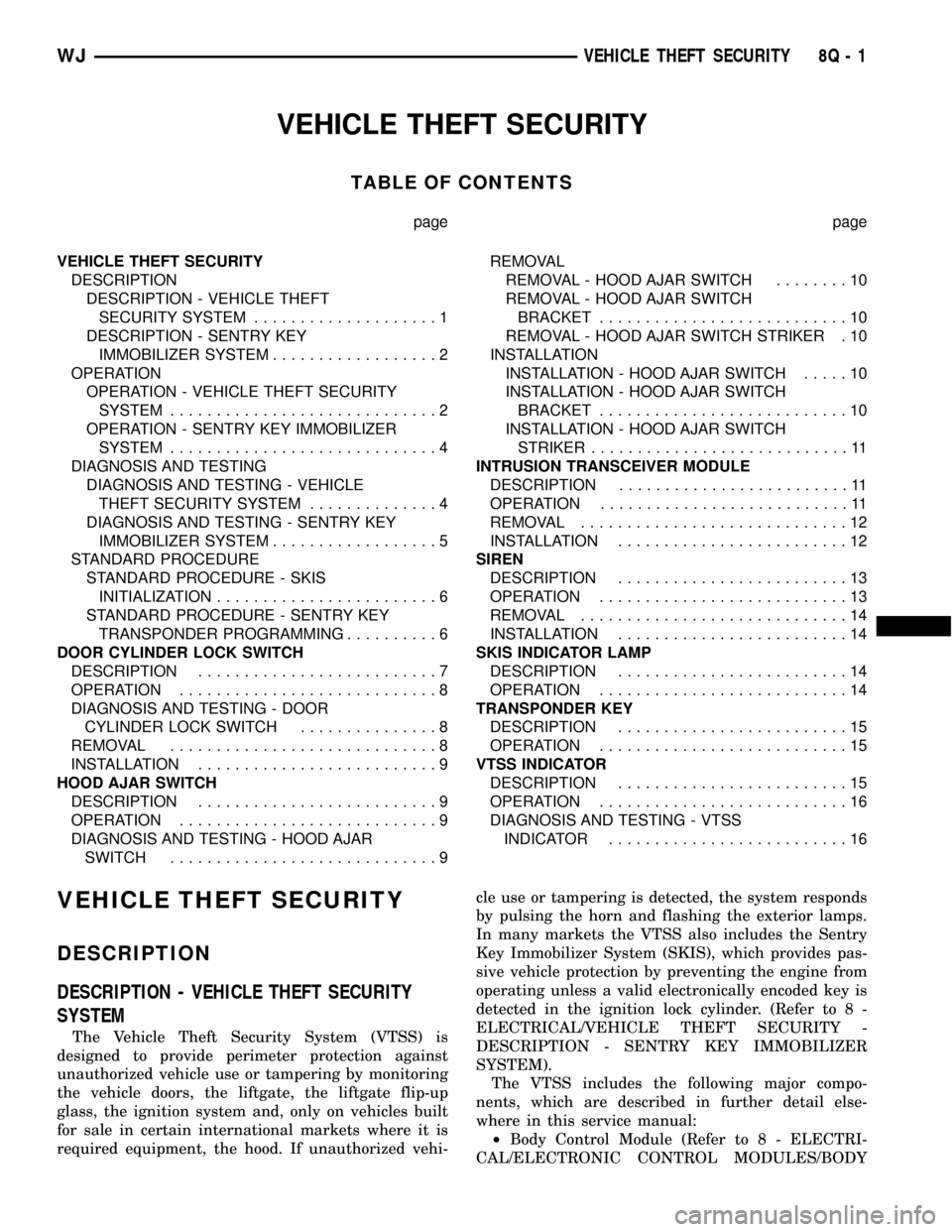
VEHICLE THEFT SECURITY
TABLE OF CONTENTS
page page
VEHICLE THEFT SECURITY
DESCRIPTION
DESCRIPTION - VEHICLE THEFT
SECURITY SYSTEM....................1
DESCRIPTION - SENTRY KEY
IMMOBILIZER SYSTEM..................2
OPERATION
OPERATION - VEHICLE THEFT SECURITY
SYSTEM.............................2
OPERATION - SENTRY KEY IMMOBILIZER
SYSTEM.............................4
DIAGNOSIS AND TESTING
DIAGNOSIS AND TESTING - VEHICLE
THEFT SECURITY SYSTEM..............4
DIAGNOSIS AND TESTING - SENTRY KEY
IMMOBILIZER SYSTEM..................5
STANDARD PROCEDURE
STANDARD PROCEDURE - SKIS
INITIALIZATION........................6
STANDARD PROCEDURE - SENTRY KEY
TRANSPONDER PROGRAMMING..........6
DOOR CYLINDER LOCK SWITCH
DESCRIPTION..........................7
OPERATION............................8
DIAGNOSIS AND TESTING - DOOR
CYLINDER LOCK SWITCH...............8
REMOVAL.............................8
INSTALLATION..........................9
HOOD AJAR SWITCH
DESCRIPTION..........................9
OPERATION............................9
DIAGNOSIS AND TESTING - HOOD AJAR
SWITCH.............................9REMOVAL
REMOVAL - HOOD AJAR SWITCH........10
REMOVAL - HOOD AJAR SWITCH
BRACKET...........................10
REMOVAL - HOOD AJAR SWITCH STRIKER . 10
INSTALLATION
INSTALLATION - HOOD AJAR SWITCH.....10
INSTALLATION - HOOD AJAR SWITCH
BRACKET...........................10
INSTALLATION - HOOD AJAR SWITCH
STRIKER............................11
INTRUSION TRANSCEIVER MODULE
DESCRIPTION.........................11
OPERATION...........................11
REMOVAL.............................12
INSTALLATION.........................12
SIREN
DESCRIPTION.........................13
OPERATION...........................13
REMOVAL.............................14
INSTALLATION.........................14
SKIS INDICATOR LAMP
DESCRIPTION.........................14
OPERATION...........................14
TRANSPONDER KEY
DESCRIPTION.........................15
OPERATION...........................15
VTSS INDICATOR
DESCRIPTION.........................15
OPERATION...........................16
DIAGNOSIS AND TESTING - VTSS
INDICATOR..........................16
VEHICLE THEFT SECURITY
DESCRIPTION
DESCRIPTION - VEHICLE THEFT SECURITY
SYSTEM
The Vehicle Theft Security System (VTSS) is
designed to provide perimeter protection against
unauthorized vehicle use or tampering by monitoring
the vehicle doors, the liftgate, the liftgate flip-up
glass, the ignition system and, only on vehicles built
for sale in certain international markets where it is
required equipment, the hood. If unauthorized vehi-cle use or tampering is detected, the system responds
by pulsing the horn and flashing the exterior lamps.
In many markets the VTSS also includes the Sentry
Key Immobilizer System (SKIS), which provides pas-
sive vehicle protection by preventing the engine from
operating unless a valid electronically encoded key is
detected in the ignition lock cylinder. (Refer to 8 -
ELECTRICAL/VEHICLE THEFT SECURITY -
DESCRIPTION - SENTRY KEY IMMOBILIZER
SYSTEM).
The VTSS includes the following major compo-
nents, which are described in further detail else-
where in this service manual:
²Body Control Module (Refer to 8 - ELECTRI-
CAL/ELECTRONIC CONTROL MODULES/BODY
WJVEHICLE THEFT SECURITY 8Q - 1