service indicator JEEP GRAND CHEROKEE 2003 WJ / 2.G Repair Manual
[x] Cancel search | Manufacturer: JEEP, Model Year: 2003, Model line: GRAND CHEROKEE, Model: JEEP GRAND CHEROKEE 2003 WJ / 2.GPages: 2199, PDF Size: 76.01 MB
Page 453 of 2199
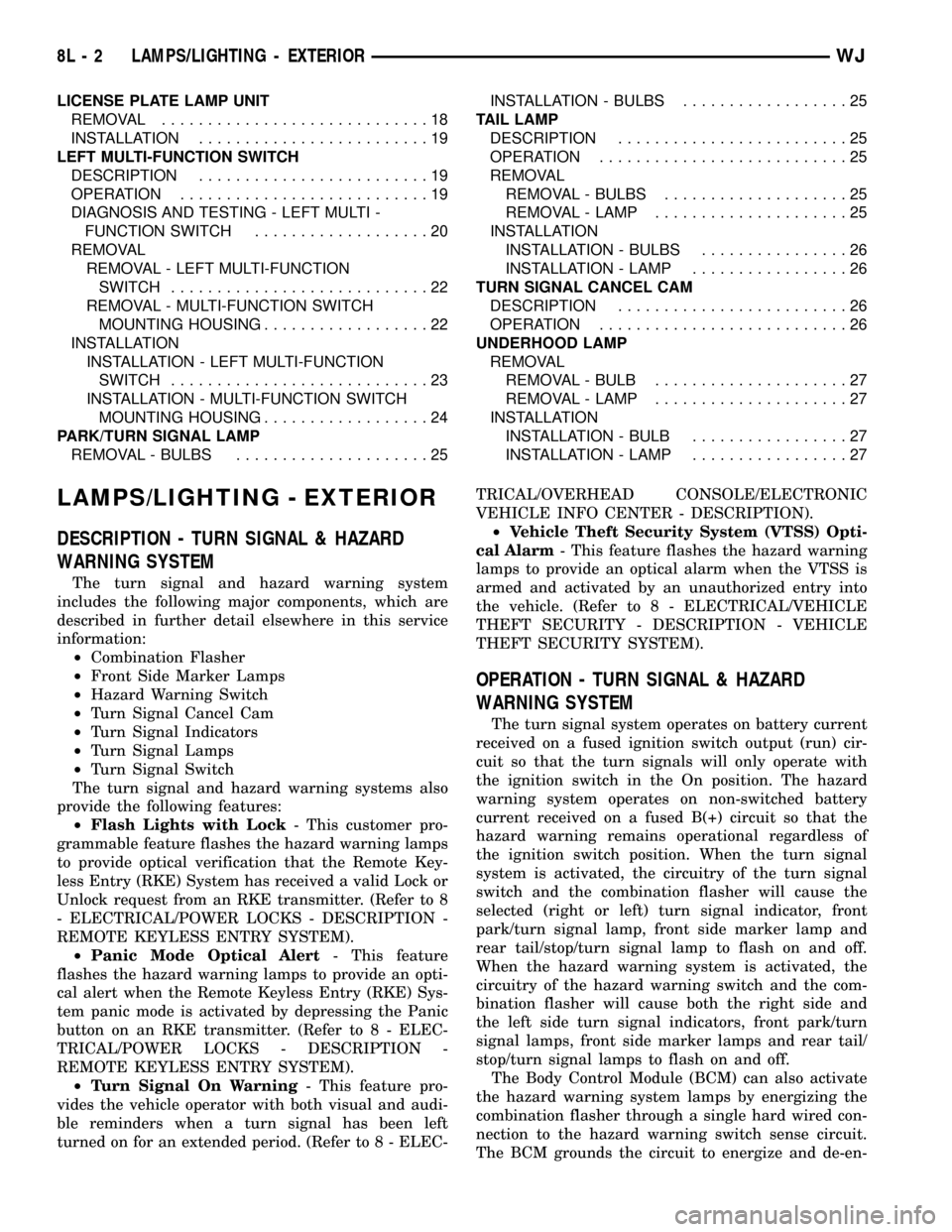
LICENSE PLATE LAMP UNIT
REMOVAL.............................18
INSTALLATION.........................19
LEFT MULTI-FUNCTION SWITCH
DESCRIPTION.........................19
OPERATION...........................19
DIAGNOSIS AND TESTING - LEFT MULTI -
FUNCTION SWITCH...................20
REMOVAL
REMOVAL - LEFT MULTI-FUNCTION
SWITCH............................22
REMOVAL - MULTI-FUNCTION SWITCH
MOUNTING HOUSING..................22
INSTALLATION
INSTALLATION - LEFT MULTI-FUNCTION
SWITCH............................23
INSTALLATION - MULTI-FUNCTION SWITCH
MOUNTING HOUSING..................24
PARK/TURN SIGNAL LAMP
REMOVAL - BULBS.....................25INSTALLATION - BULBS..................25
TAIL LAMP
DESCRIPTION.........................25
OPERATION...........................25
REMOVAL
REMOVAL - BULBS....................25
REMOVAL - LAMP.....................25
INSTALLATION
INSTALLATION - BULBS................26
INSTALLATION - LAMP.................26
TURN SIGNAL CANCEL CAM
DESCRIPTION.........................26
OPERATION...........................26
UNDERHOOD LAMP
REMOVAL
REMOVAL - BULB.....................27
REMOVAL - LAMP.....................27
INSTALLATION
INSTALLATION - BULB.................27
INSTALLATION - LAMP.................27
LAMPS/LIGHTING - EXTERIOR
DESCRIPTION - TURN SIGNAL & HAZARD
WARNING SYSTEM
The turn signal and hazard warning system
includes the following major components, which are
described in further detail elsewhere in this service
information:
²Combination Flasher
²Front Side Marker Lamps
²Hazard Warning Switch
²Turn Signal Cancel Cam
²Turn Signal Indicators
²Turn Signal Lamps
²Turn Signal Switch
The turn signal and hazard warning systems also
provide the following features:
²Flash Lights with Lock- This customer pro-
grammable feature flashes the hazard warning lamps
to provide optical verification that the Remote Key-
less Entry (RKE) System has received a valid Lock or
Unlock request from an RKE transmitter. (Refer to 8
- ELECTRICAL/POWER LOCKS - DESCRIPTION -
REMOTE KEYLESS ENTRY SYSTEM).
²Panic Mode Optical Alert- This feature
flashes the hazard warning lamps to provide an opti-
cal alert when the Remote Keyless Entry (RKE) Sys-
tem panic mode is activated by depressing the Panic
button on an RKE transmitter. (Refer to 8 - ELEC-
TRICAL/POWER LOCKS - DESCRIPTION -
REMOTE KEYLESS ENTRY SYSTEM).
²Turn Signal On Warning- This feature pro-
vides the vehicle operator with both visual and audi-
ble reminders when a turn signal has been left
turned on for an extended period. (Refer to 8 - ELEC-TRICAL/OVERHEAD CONSOLE/ELECTRONIC
VEHICLE INFO CENTER - DESCRIPTION).
²Vehicle Theft Security System (VTSS) Opti-
cal Alarm- This feature flashes the hazard warning
lamps to provide an optical alarm when the VTSS is
armed and activated by an unauthorized entry into
the vehicle. (Refer to 8 - ELECTRICAL/VEHICLE
THEFT SECURITY - DESCRIPTION - VEHICLE
THEFT SECURITY SYSTEM).
OPERATION - TURN SIGNAL & HAZARD
WARNING SYSTEM
The turn signal system operates on battery current
received on a fused ignition switch output (run) cir-
cuit so that the turn signals will only operate with
the ignition switch in the On position. The hazard
warning system operates on non-switched battery
current received on a fused B(+) circuit so that the
hazard warning remains operational regardless of
the ignition switch position. When the turn signal
system is activated, the circuitry of the turn signal
switch and the combination flasher will cause the
selected (right or left) turn signal indicator, front
park/turn signal lamp, front side marker lamp and
rear tail/stop/turn signal lamp to flash on and off.
When the hazard warning system is activated, the
circuitry of the hazard warning switch and the com-
bination flasher will cause both the right side and
the left side turn signal indicators, front park/turn
signal lamps, front side marker lamps and rear tail/
stop/turn signal lamps to flash on and off.
The Body Control Module (BCM) can also activate
the hazard warning system lamps by energizing the
combination flasher through a single hard wired con-
nection to the hazard warning switch sense circuit.
The BCM grounds the circuit to energize and de-en-
8L - 2 LAMPS/LIGHTING - EXTERIORWJ
Page 454 of 2199
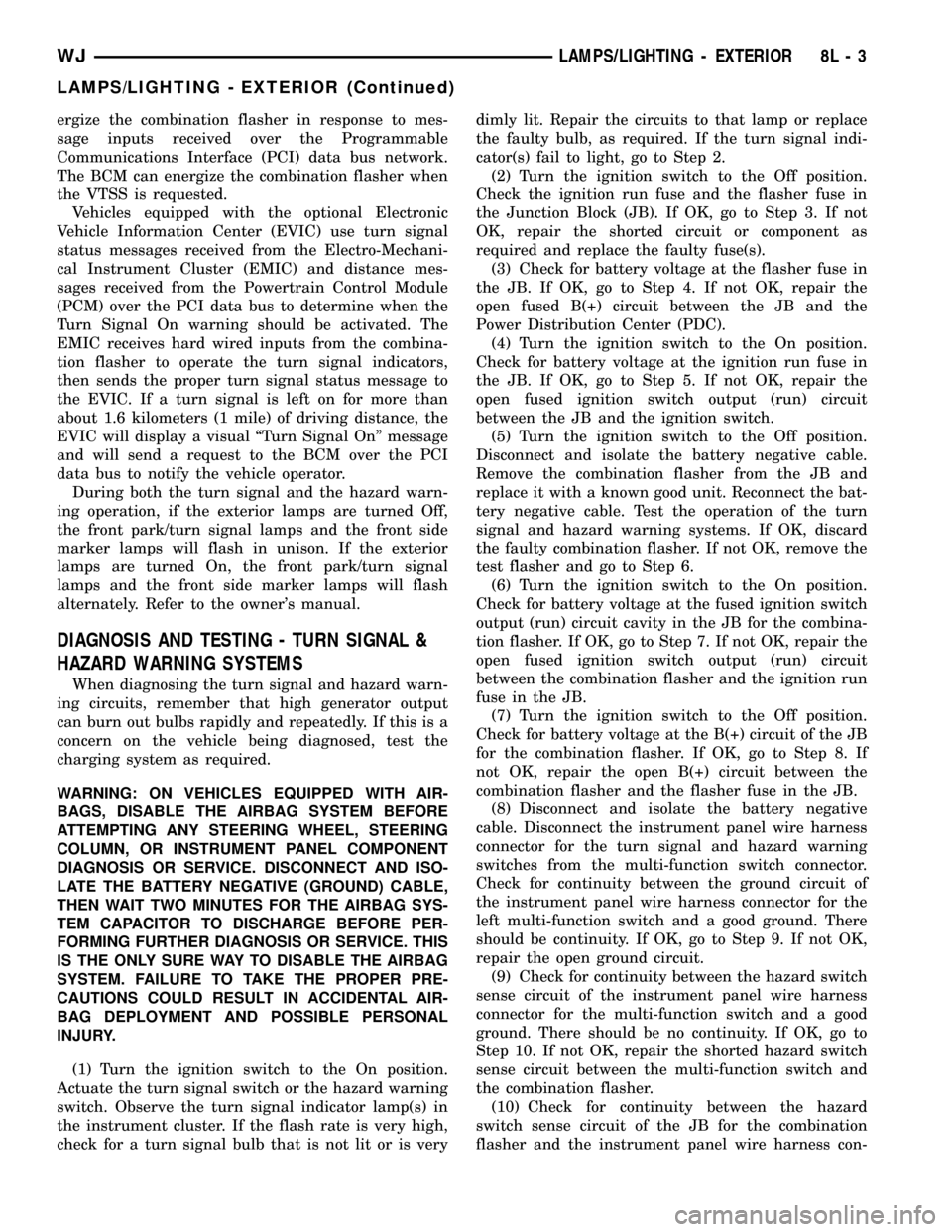
ergize the combination flasher in response to mes-
sage inputs received over the Programmable
Communications Interface (PCI) data bus network.
The BCM can energize the combination flasher when
the VTSS is requested.
Vehicles equipped with the optional Electronic
Vehicle Information Center (EVIC) use turn signal
status messages received from the Electro-Mechani-
cal Instrument Cluster (EMIC) and distance mes-
sages received from the Powertrain Control Module
(PCM) over the PCI data bus to determine when the
Turn Signal On warning should be activated. The
EMIC receives hard wired inputs from the combina-
tion flasher to operate the turn signal indicators,
then sends the proper turn signal status message to
the EVIC. If a turn signal is left on for more than
about 1.6 kilometers (1 mile) of driving distance, the
EVIC will display a visual ªTurn Signal Onº message
and will send a request to the BCM over the PCI
data bus to notify the vehicle operator.
During both the turn signal and the hazard warn-
ing operation, if the exterior lamps are turned Off,
the front park/turn signal lamps and the front side
marker lamps will flash in unison. If the exterior
lamps are turned On, the front park/turn signal
lamps and the front side marker lamps will flash
alternately. Refer to the owner's manual.
DIAGNOSIS AND TESTING - TURN SIGNAL &
HAZARD WARNING SYSTEMS
When diagnosing the turn signal and hazard warn-
ing circuits, remember that high generator output
can burn out bulbs rapidly and repeatedly. If this is a
concern on the vehicle being diagnosed, test the
charging system as required.
WARNING: ON VEHICLES EQUIPPED WITH AIR-
BAGS, DISABLE THE AIRBAG SYSTEM BEFORE
ATTEMPTING ANY STEERING WHEEL, STEERING
COLUMN, OR INSTRUMENT PANEL COMPONENT
DIAGNOSIS OR SERVICE. DISCONNECT AND ISO-
LATE THE BATTERY NEGATIVE (GROUND) CABLE,
THEN WAIT TWO MINUTES FOR THE AIRBAG SYS-
TEM CAPACITOR TO DISCHARGE BEFORE PER-
FORMING FURTHER DIAGNOSIS OR SERVICE. THIS
IS THE ONLY SURE WAY TO DISABLE THE AIRBAG
SYSTEM. FAILURE TO TAKE THE PROPER PRE-
CAUTIONS COULD RESULT IN ACCIDENTAL AIR-
BAG DEPLOYMENT AND POSSIBLE PERSONAL
INJURY.
(1) Turn the ignition switch to the On position.
Actuate the turn signal switch or the hazard warning
switch. Observe the turn signal indicator lamp(s) in
the instrument cluster. If the flash rate is very high,
check for a turn signal bulb that is not lit or is verydimly lit. Repair the circuits to that lamp or replace
the faulty bulb, as required. If the turn signal indi-
cator(s) fail to light, go to Step 2.
(2) Turn the ignition switch to the Off position.
Check the ignition run fuse and the flasher fuse in
the Junction Block (JB). If OK, go to Step 3. If not
OK, repair the shorted circuit or component as
required and replace the faulty fuse(s).
(3) Check for battery voltage at the flasher fuse in
the JB. If OK, go to Step 4. If not OK, repair the
open fused B(+) circuit between the JB and the
Power Distribution Center (PDC).
(4) Turn the ignition switch to the On position.
Check for battery voltage at the ignition run fuse in
the JB. If OK, go to Step 5. If not OK, repair the
open fused ignition switch output (run) circuit
between the JB and the ignition switch.
(5) Turn the ignition switch to the Off position.
Disconnect and isolate the battery negative cable.
Remove the combination flasher from the JB and
replace it with a known good unit. Reconnect the bat-
tery negative cable. Test the operation of the turn
signal and hazard warning systems. If OK, discard
the faulty combination flasher. If not OK, remove the
test flasher and go to Step 6.
(6) Turn the ignition switch to the On position.
Check for battery voltage at the fused ignition switch
output (run) circuit cavity in the JB for the combina-
tion flasher. If OK, go to Step 7. If not OK, repair the
open fused ignition switch output (run) circuit
between the combination flasher and the ignition run
fuse in the JB.
(7) Turn the ignition switch to the Off position.
Check for battery voltage at the B(+) circuit of the JB
for the combination flasher. If OK, go to Step 8. If
not OK, repair the open B(+) circuit between the
combination flasher and the flasher fuse in the JB.
(8) Disconnect and isolate the battery negative
cable. Disconnect the instrument panel wire harness
connector for the turn signal and hazard warning
switches from the multi-function switch connector.
Check for continuity between the ground circuit of
the instrument panel wire harness connector for the
left multi-function switch and a good ground. There
should be continuity. If OK, go to Step 9. If not OK,
repair the open ground circuit.
(9) Check for continuity between the hazard switch
sense circuit of the instrument panel wire harness
connector for the multi-function switch and a good
ground. There should be no continuity. If OK, go to
Step 10. If not OK, repair the shorted hazard switch
sense circuit between the multi-function switch and
the combination flasher.
(10) Check for continuity between the hazard
switch sense circuit of the JB for the combination
flasher and the instrument panel wire harness con-
WJLAMPS/LIGHTING - EXTERIOR 8L - 3
LAMPS/LIGHTING - EXTERIOR (Continued)
Page 479 of 2199
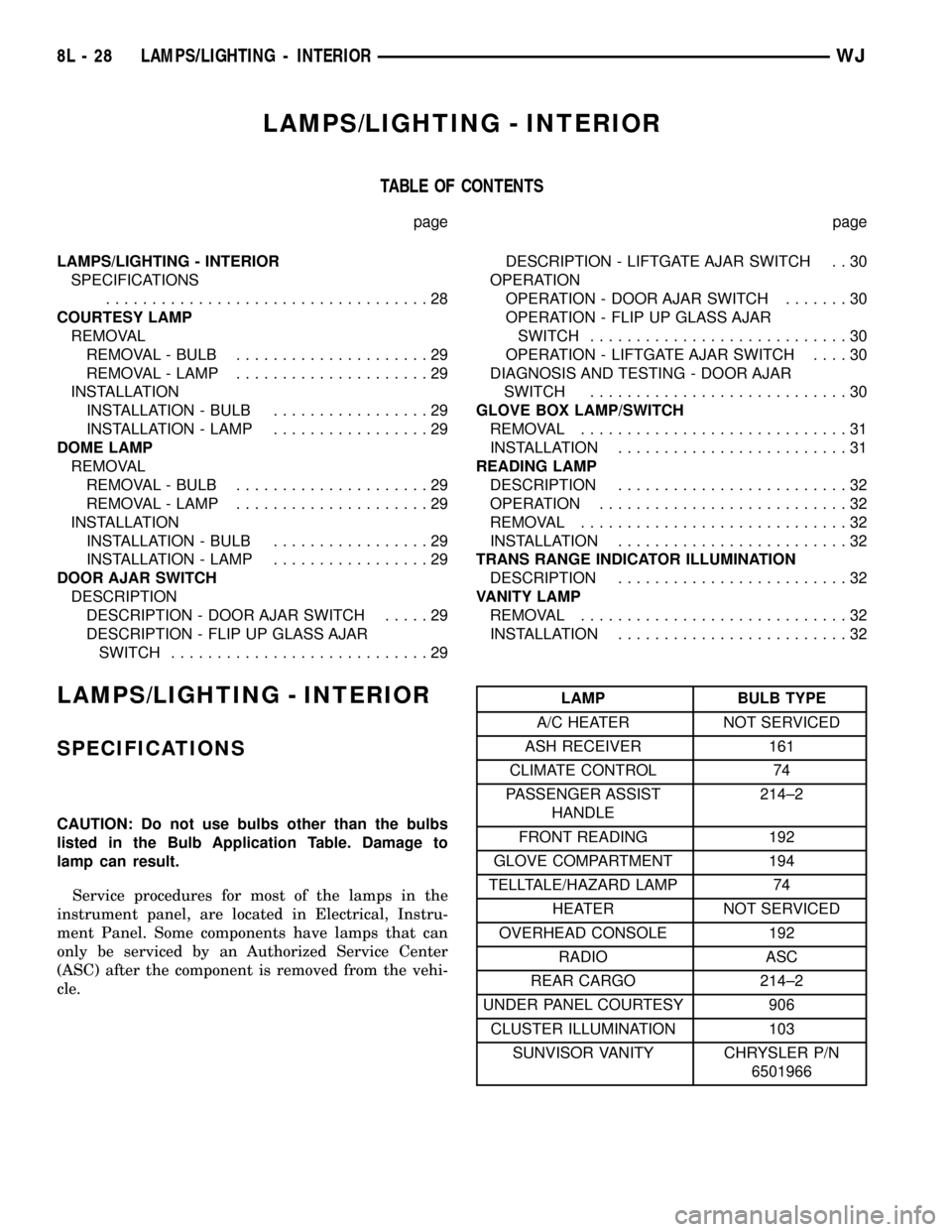
LAMPS/LIGHTING - INTERIOR
TABLE OF CONTENTS
page page
LAMPS/LIGHTING - INTERIOR
SPECIFICATIONS
...................................28
COURTESY LAMP
REMOVAL
REMOVAL - BULB.....................29
REMOVAL - LAMP.....................29
INSTALLATION
INSTALLATION - BULB.................29
INSTALLATION - LAMP.................29
DOME LAMP
REMOVAL
REMOVAL - BULB.....................29
REMOVAL - LAMP.....................29
INSTALLATION
INSTALLATION - BULB.................29
INSTALLATION - LAMP.................29
DOOR AJAR SWITCH
DESCRIPTION
DESCRIPTION - DOOR AJAR SWITCH.....29
DESCRIPTION - FLIP UP GLASS AJAR
SWITCH............................29DESCRIPTION - LIFTGATE AJAR SWITCH . . 30
OPERATION
OPERATION - DOOR AJAR SWITCH.......30
OPERATION - FLIP UP GLASS AJAR
SWITCH............................30
OPERATION - LIFTGATE AJAR SWITCH....30
DIAGNOSIS AND TESTING - DOOR AJAR
SWITCH............................30
GLOVE BOX LAMP/SWITCH
REMOVAL.............................31
INSTALLATION.........................31
READING LAMP
DESCRIPTION.........................32
OPERATION...........................32
REMOVAL.............................32
INSTALLATION.........................32
TRANS RANGE INDICATOR ILLUMINATION
DESCRIPTION.........................32
VANITY LAMP
REMOVAL.............................32
INSTALLATION.........................32
LAMPS/LIGHTING - INTERIOR
SPECIFICATIONS
CAUTION: Do not use bulbs other than the bulbs
listed in the Bulb Application Table. Damage to
lamp can result.
Service procedures for most of the lamps in the
instrument panel, are located in Electrical, Instru-
ment Panel. Some components have lamps that can
only be serviced by an Authorized Service Center
(ASC) after the component is removed from the vehi-
cle.
LAMP BULB TYPE
A/C HEATER NOT SERVICED
ASH RECEIVER 161
CLIMATE CONTROL 74
PASSENGER ASSIST
HANDLE214±2
FRONT READING 192
GLOVE COMPARTMENT 194
TELLTALE/HAZARD LAMP 74
HEATER NOT SERVICED
OVERHEAD CONSOLE 192
RADIO ASC
REAR CARGO 214±2
UNDER PANEL COURTESY 906
CLUSTER ILLUMINATION 103
SUNVISOR VANITY CHRYSLER P/N
6501966
8L - 28 LAMPS/LIGHTING - INTERIORWJ
Page 483 of 2199
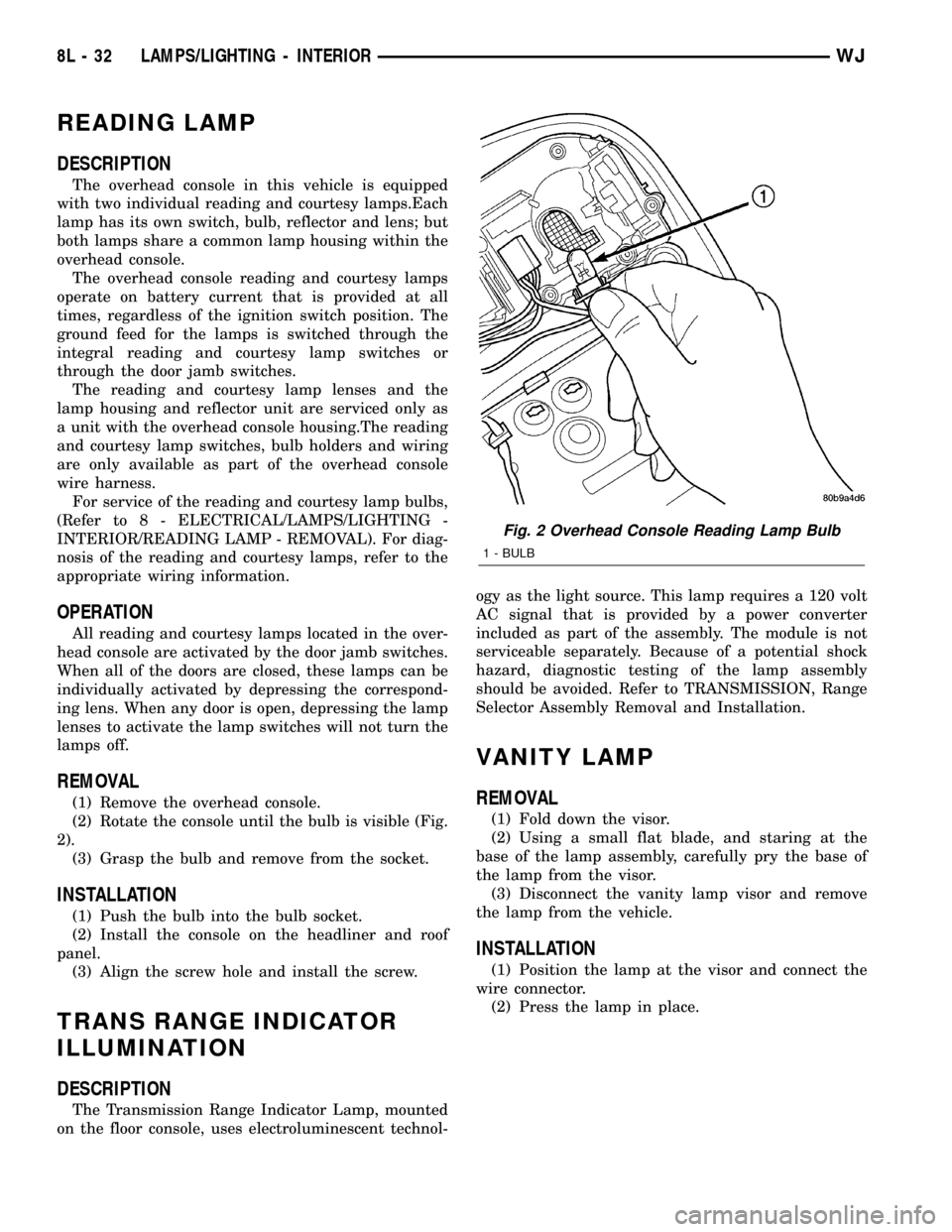
READING LAMP
DESCRIPTION
The overhead console in this vehicle is equipped
with two individual reading and courtesy lamps.Each
lamp has its own switch, bulb, reflector and lens; but
both lamps share a common lamp housing within the
overhead console.
The overhead console reading and courtesy lamps
operate on battery current that is provided at all
times, regardless of the ignition switch position. The
ground feed for the lamps is switched through the
integral reading and courtesy lamp switches or
through the door jamb switches.
The reading and courtesy lamp lenses and the
lamp housing and reflector unit are serviced only as
a unit with the overhead console housing.The reading
and courtesy lamp switches, bulb holders and wiring
are only available as part of the overhead console
wire harness.
For service of the reading and courtesy lamp bulbs,
(Refer to 8 - ELECTRICAL/LAMPS/LIGHTING -
INTERIOR/READING LAMP - REMOVAL). For diag-
nosis of the reading and courtesy lamps, refer to the
appropriate wiring information.
OPERATION
All reading and courtesy lamps located in the over-
head console are activated by the door jamb switches.
When all of the doors are closed, these lamps can be
individually activated by depressing the correspond-
ing lens. When any door is open, depressing the lamp
lenses to activate the lamp switches will not turn the
lamps off.
REMOVAL
(1) Remove the overhead console.
(2) Rotate the console until the bulb is visible (Fig.
2).
(3) Grasp the bulb and remove from the socket.
INSTALLATION
(1) Push the bulb into the bulb socket.
(2) Install the console on the headliner and roof
panel.
(3) Align the screw hole and install the screw.
TRANS RANGE INDICATOR
ILLUMINATION
DESCRIPTION
The Transmission Range Indicator Lamp, mounted
on the floor console, uses electroluminescent technol-ogy as the light source. This lamp requires a 120 volt
AC signal that is provided by a power converter
included as part of the assembly. The module is not
serviceable separately. Because of a potential shock
hazard, diagnostic testing of the lamp assembly
should be avoided. Refer to TRANSMISSION, Range
Selector Assembly Removal and Installation.
VANITY LAMP
REMOVAL
(1) Fold down the visor.
(2) Using a small flat blade, and staring at the
base of the lamp assembly, carefully pry the base of
the lamp from the visor.
(3) Disconnect the vanity lamp visor and remove
the lamp from the vehicle.
INSTALLATION
(1) Position the lamp at the visor and connect the
wire connector.
(2) Press the lamp in place.
Fig. 2 Overhead Console Reading Lamp Bulb
1 - BULB
8L - 32 LAMPS/LIGHTING - INTERIORWJ
Page 490 of 2199
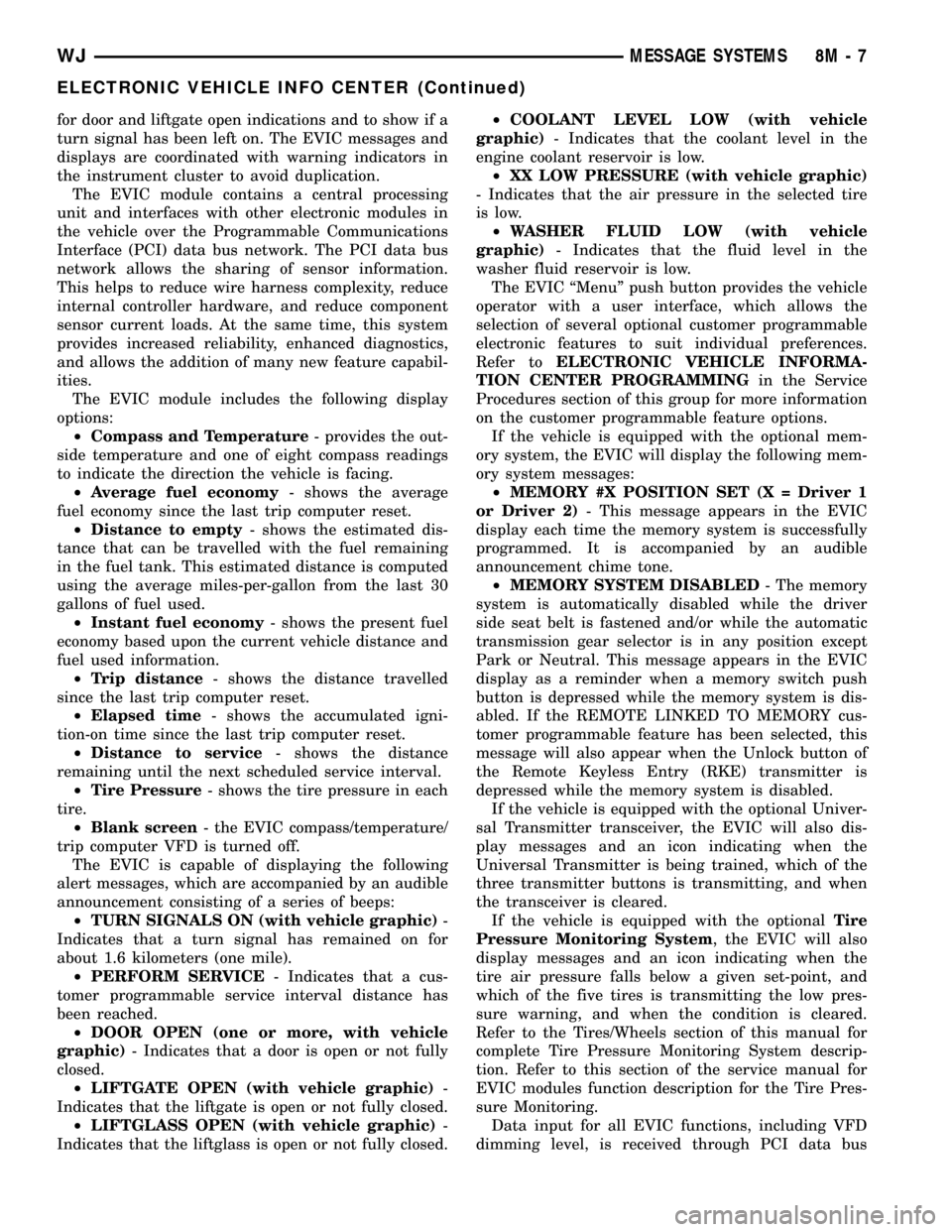
for door and liftgate open indications and to show if a
turn signal has been left on. The EVIC messages and
displays are coordinated with warning indicators in
the instrument cluster to avoid duplication.
The EVIC module contains a central processing
unit and interfaces with other electronic modules in
the vehicle over the Programmable Communications
Interface (PCI) data bus network. The PCI data bus
network allows the sharing of sensor information.
This helps to reduce wire harness complexity, reduce
internal controller hardware, and reduce component
sensor current loads. At the same time, this system
provides increased reliability, enhanced diagnostics,
and allows the addition of many new feature capabil-
ities.
The EVIC module includes the following display
options:
²Compass and Temperature- provides the out-
side temperature and one of eight compass readings
to indicate the direction the vehicle is facing.
²Average fuel economy- shows the average
fuel economy since the last trip computer reset.
²Distance to empty- shows the estimated dis-
tance that can be travelled with the fuel remaining
in the fuel tank. This estimated distance is computed
using the average miles-per-gallon from the last 30
gallons of fuel used.
²Instant fuel economy- shows the present fuel
economy based upon the current vehicle distance and
fuel used information.
²Trip distance- shows the distance travelled
since the last trip computer reset.
²Elapsed time- shows the accumulated igni-
tion-on time since the last trip computer reset.
²Distance to service- shows the distance
remaining until the next scheduled service interval.
²Tire Pressure- shows the tire pressure in each
tire.
²Blank screen- the EVIC compass/temperature/
trip computer VFD is turned off.
The EVIC is capable of displaying the following
alert messages, which are accompanied by an audible
announcement consisting of a series of beeps:
²TURN SIGNALS ON (with vehicle graphic)-
Indicates that a turn signal has remained on for
about 1.6 kilometers (one mile).
²PERFORM SERVICE- Indicates that a cus-
tomer programmable service interval distance has
been reached.
²DOOR OPEN (one or more, with vehicle
graphic)- Indicates that a door is open or not fully
closed.
²LIFTGATE OPEN (with vehicle graphic)-
Indicates that the liftgate is open or not fully closed.
²LIFTGLASS OPEN (with vehicle graphic)-
Indicates that the liftglass is open or not fully closed.²COOLANT LEVEL LOW (with vehicle
graphic)- Indicates that the coolant level in the
engine coolant reservoir is low.
²XX LOW PRESSURE (with vehicle graphic)
- Indicates that the air pressure in the selected tire
is low.
²WASHER FLUID LOW (with vehicle
graphic)- Indicates that the fluid level in the
washer fluid reservoir is low.
The EVIC ªMenuº push button provides the vehicle
operator with a user interface, which allows the
selection of several optional customer programmable
electronic features to suit individual preferences.
Refer toELECTRONIC VEHICLE INFORMA-
TION CENTER PROGRAMMINGin the Service
Procedures section of this group for more information
on the customer programmable feature options.
If the vehicle is equipped with the optional mem-
ory system, the EVIC will display the following mem-
ory system messages:
²MEMORY #X POSITION SET (X = Driver 1
or Driver 2)- This message appears in the EVIC
display each time the memory system is successfully
programmed. It is accompanied by an audible
announcement chime tone.
²MEMORY SYSTEM DISABLED- The memory
system is automatically disabled while the driver
side seat belt is fastened and/or while the automatic
transmission gear selector is in any position except
Park or Neutral. This message appears in the EVIC
display as a reminder when a memory switch push
button is depressed while the memory system is dis-
abled. If the REMOTE LINKED TO MEMORY cus-
tomer programmable feature has been selected, this
message will also appear when the Unlock button of
the Remote Keyless Entry (RKE) transmitter is
depressed while the memory system is disabled.
If the vehicle is equipped with the optional Univer-
sal Transmitter transceiver, the EVIC will also dis-
play messages and an icon indicating when the
Universal Transmitter is being trained, which of the
three transmitter buttons is transmitting, and when
the transceiver is cleared.
If the vehicle is equipped with the optionalTire
Pressure Monitoring System, the EVIC will also
display messages and an icon indicating when the
tire air pressure falls below a given set-point, and
which of the five tires is transmitting the low pres-
sure warning, and when the condition is cleared.
Refer to the Tires/Wheels section of this manual for
complete Tire Pressure Monitoring System descrip-
tion. Refer to this section of the service manual for
EVIC modules function description for the Tire Pres-
sure Monitoring.
Data input for all EVIC functions, including VFD
dimming level, is received through PCI data bus
WJMESSAGE SYSTEMS 8M - 7
ELECTRONIC VEHICLE INFO CENTER (Continued)
Page 511 of 2199
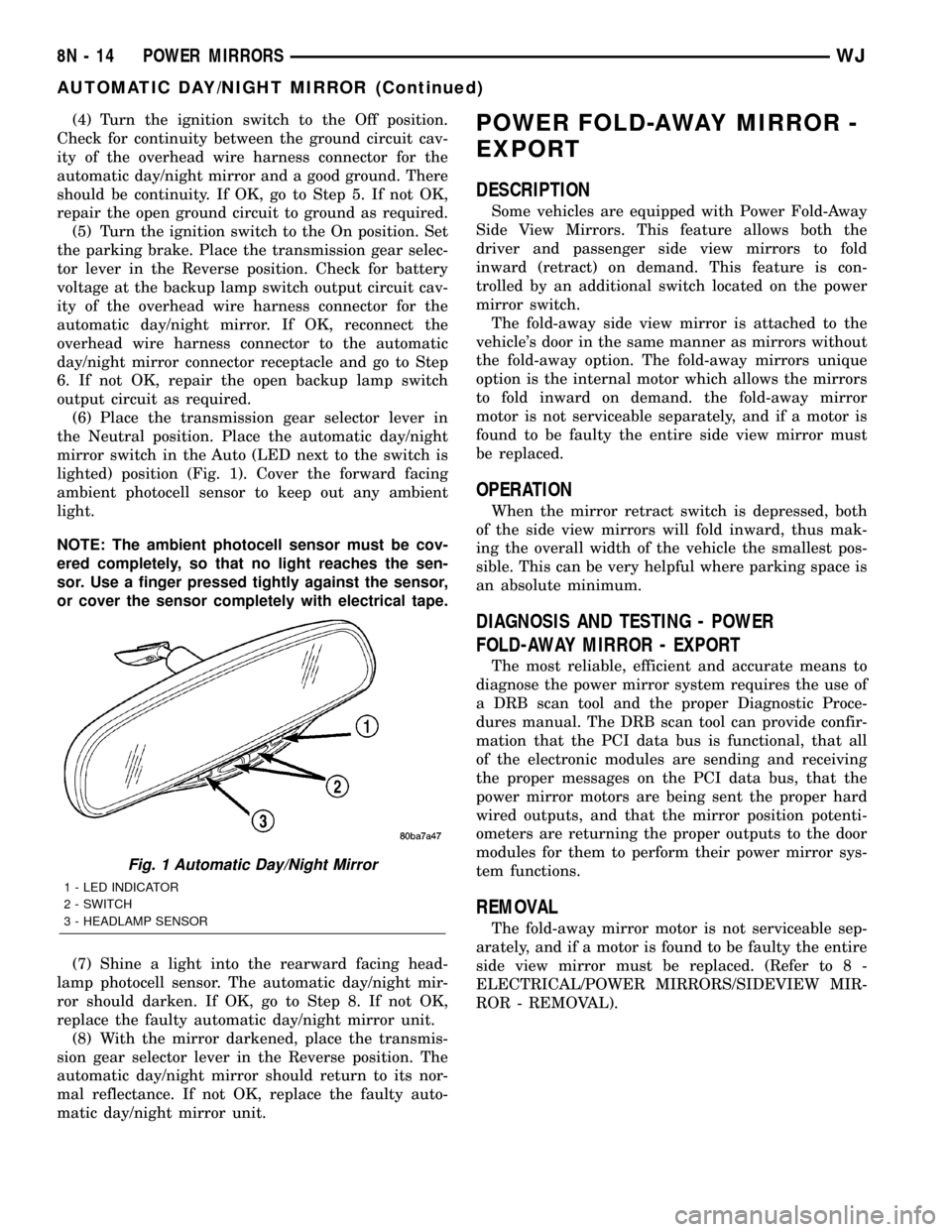
(4) Turn the ignition switch to the Off position.
Check for continuity between the ground circuit cav-
ity of the overhead wire harness connector for the
automatic day/night mirror and a good ground. There
should be continuity. If OK, go to Step 5. If not OK,
repair the open ground circuit to ground as required.
(5) Turn the ignition switch to the On position. Set
the parking brake. Place the transmission gear selec-
tor lever in the Reverse position. Check for battery
voltage at the backup lamp switch output circuit cav-
ity of the overhead wire harness connector for the
automatic day/night mirror. If OK, reconnect the
overhead wire harness connector to the automatic
day/night mirror connector receptacle and go to Step
6. If not OK, repair the open backup lamp switch
output circuit as required.
(6) Place the transmission gear selector lever in
the Neutral position. Place the automatic day/night
mirror switch in the Auto (LED next to the switch is
lighted) position (Fig. 1). Cover the forward facing
ambient photocell sensor to keep out any ambient
light.
NOTE: The ambient photocell sensor must be cov-
ered completely, so that no light reaches the sen-
sor. Use a finger pressed tightly against the sensor,
or cover the sensor completely with electrical tape.
(7) Shine a light into the rearward facing head-
lamp photocell sensor. The automatic day/night mir-
ror should darken. If OK, go to Step 8. If not OK,
replace the faulty automatic day/night mirror unit.
(8) With the mirror darkened, place the transmis-
sion gear selector lever in the Reverse position. The
automatic day/night mirror should return to its nor-
mal reflectance. If not OK, replace the faulty auto-
matic day/night mirror unit.POWER FOLD-AWAY MIRROR -
EXPORT
DESCRIPTION
Some vehicles are equipped with Power Fold-Away
Side View Mirrors. This feature allows both the
driver and passenger side view mirrors to fold
inward (retract) on demand. This feature is con-
trolled by an additional switch located on the power
mirror switch.
The fold-away side view mirror is attached to the
vehicle's door in the same manner as mirrors without
the fold-away option. The fold-away mirrors unique
option is the internal motor which allows the mirrors
to fold inward on demand. the fold-away mirror
motor is not serviceable separately, and if a motor is
found to be faulty the entire side view mirror must
be replaced.
OPERATION
When the mirror retract switch is depressed, both
of the side view mirrors will fold inward, thus mak-
ing the overall width of the vehicle the smallest pos-
sible. This can be very helpful where parking space is
an absolute minimum.
DIAGNOSIS AND TESTING - POWER
FOLD-AWAY MIRROR - EXPORT
The most reliable, efficient and accurate means to
diagnose the power mirror system requires the use of
a DRB scan tool and the proper Diagnostic Proce-
dures manual. The DRB scan tool can provide confir-
mation that the PCI data bus is functional, that all
of the electronic modules are sending and receiving
the proper messages on the PCI data bus, that the
power mirror motors are being sent the proper hard
wired outputs, and that the mirror position potenti-
ometers are returning the proper outputs to the door
modules for them to perform their power mirror sys-
tem functions.
REMOVAL
The fold-away mirror motor is not serviceable sep-
arately, and if a motor is found to be faulty the entire
side view mirror must be replaced. (Refer to 8 -
ELECTRICAL/POWER MIRRORS/SIDEVIEW MIR-
ROR - REMOVAL).
Fig. 1 Automatic Day/Night Mirror
1 - LED INDICATOR
2 - SWITCH
3 - HEADLAMP SENSOR
8N - 14 POWER MIRRORSWJ
AUTOMATIC DAY/NIGHT MIRROR (Continued)
Page 540 of 2199
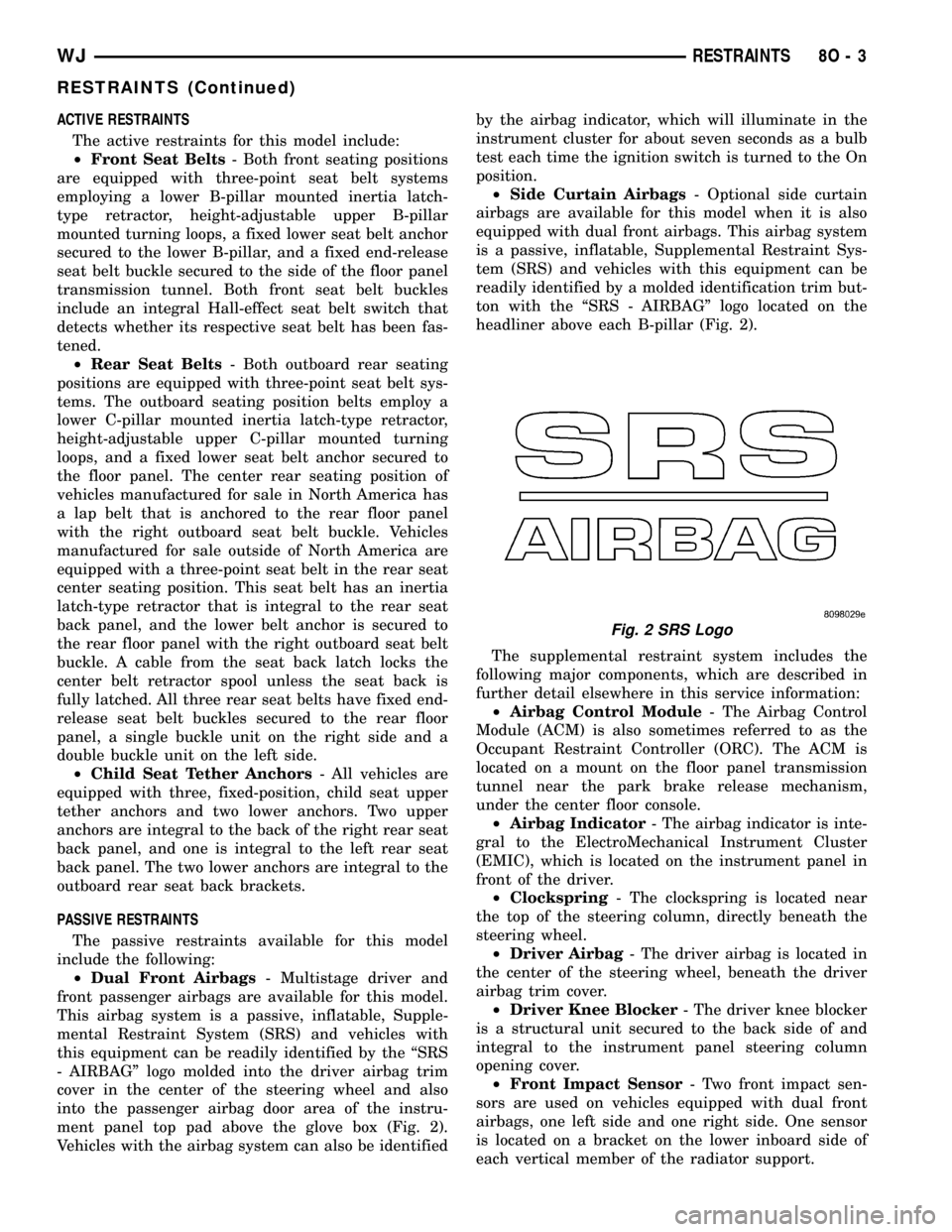
ACTIVE RESTRAINTS
The active restraints for this model include:
²Front Seat Belts- Both front seating positions
are equipped with three-point seat belt systems
employing a lower B-pillar mounted inertia latch-
type retractor, height-adjustable upper B-pillar
mounted turning loops, a fixed lower seat belt anchor
secured to the lower B-pillar, and a fixed end-release
seat belt buckle secured to the side of the floor panel
transmission tunnel. Both front seat belt buckles
include an integral Hall-effect seat belt switch that
detects whether its respective seat belt has been fas-
tened.
²Rear Seat Belts- Both outboard rear seating
positions are equipped with three-point seat belt sys-
tems. The outboard seating position belts employ a
lower C-pillar mounted inertia latch-type retractor,
height-adjustable upper C-pillar mounted turning
loops, and a fixed lower seat belt anchor secured to
the floor panel. The center rear seating position of
vehicles manufactured for sale in North America has
a lap belt that is anchored to the rear floor panel
with the right outboard seat belt buckle. Vehicles
manufactured for sale outside of North America are
equipped with a three-point seat belt in the rear seat
center seating position. This seat belt has an inertia
latch-type retractor that is integral to the rear seat
back panel, and the lower belt anchor is secured to
the rear floor panel with the right outboard seat belt
buckle. A cable from the seat back latch locks the
center belt retractor spool unless the seat back is
fully latched. All three rear seat belts have fixed end-
release seat belt buckles secured to the rear floor
panel, a single buckle unit on the right side and a
double buckle unit on the left side.
²Child Seat Tether Anchors- All vehicles are
equipped with three, fixed-position, child seat upper
tether anchors and two lower anchors. Two upper
anchors are integral to the back of the right rear seat
back panel, and one is integral to the left rear seat
back panel. The two lower anchors are integral to the
outboard rear seat back brackets.
PASSIVE RESTRAINTS
The passive restraints available for this model
include the following:
²Dual Front Airbags- Multistage driver and
front passenger airbags are available for this model.
This airbag system is a passive, inflatable, Supple-
mental Restraint System (SRS) and vehicles with
this equipment can be readily identified by the ªSRS
- AIRBAGº logo molded into the driver airbag trim
cover in the center of the steering wheel and also
into the passenger airbag door area of the instru-
ment panel top pad above the glove box (Fig. 2).
Vehicles with the airbag system can also be identifiedby the airbag indicator, which will illuminate in the
instrument cluster for about seven seconds as a bulb
test each time the ignition switch is turned to the On
position.
²Side Curtain Airbags- Optional side curtain
airbags are available for this model when it is also
equipped with dual front airbags. This airbag system
is a passive, inflatable, Supplemental Restraint Sys-
tem (SRS) and vehicles with this equipment can be
readily identified by a molded identification trim but-
ton with the ªSRS - AIRBAGº logo located on the
headliner above each B-pillar (Fig. 2).
The supplemental restraint system includes the
following major components, which are described in
further detail elsewhere in this service information:
²Airbag Control Module- The Airbag Control
Module (ACM) is also sometimes referred to as the
Occupant Restraint Controller (ORC). The ACM is
located on a mount on the floor panel transmission
tunnel near the park brake release mechanism,
under the center floor console.
²Airbag Indicator- The airbag indicator is inte-
gral to the ElectroMechanical Instrument Cluster
(EMIC), which is located on the instrument panel in
front of the driver.
²Clockspring- The clockspring is located near
the top of the steering column, directly beneath the
steering wheel.
²Driver Airbag- The driver airbag is located in
the center of the steering wheel, beneath the driver
airbag trim cover.
²Driver Knee Blocker- The driver knee blocker
is a structural unit secured to the back side of and
integral to the instrument panel steering column
opening cover.
²Front Impact Sensor- Two front impact sen-
sors are used on vehicles equipped with dual front
airbags, one left side and one right side. One sensor
is located on a bracket on the lower inboard side of
each vertical member of the radiator support.
Fig. 2 SRS Logo
WJRESTRAINTS 8O - 3
RESTRAINTS (Continued)
Page 542 of 2199
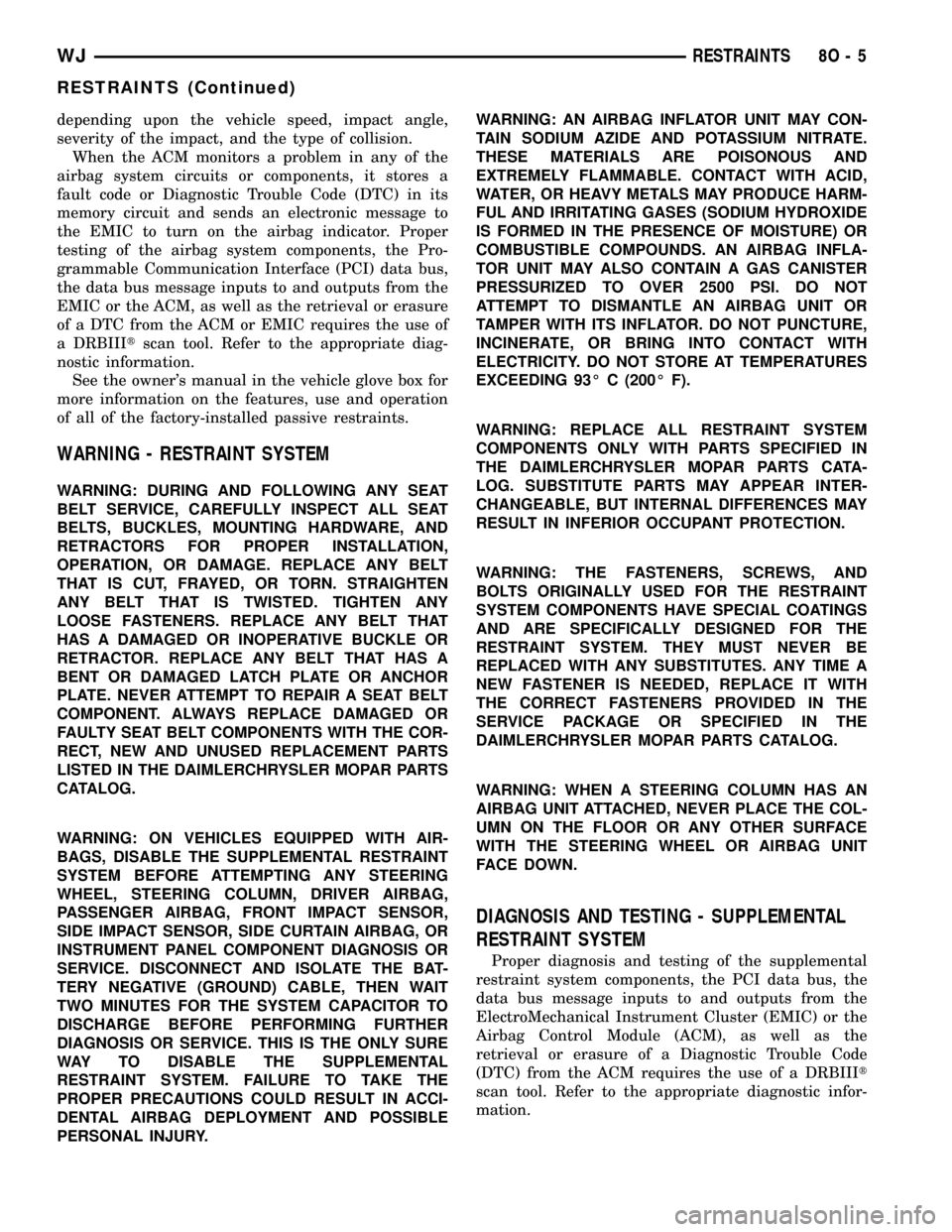
depending upon the vehicle speed, impact angle,
severity of the impact, and the type of collision.
When the ACM monitors a problem in any of the
airbag system circuits or components, it stores a
fault code or Diagnostic Trouble Code (DTC) in its
memory circuit and sends an electronic message to
the EMIC to turn on the airbag indicator. Proper
testing of the airbag system components, the Pro-
grammable Communication Interface (PCI) data bus,
the data bus message inputs to and outputs from the
EMIC or the ACM, as well as the retrieval or erasure
of a DTC from the ACM or EMIC requires the use of
a DRBIIItscan tool. Refer to the appropriate diag-
nostic information.
See the owner's manual in the vehicle glove box for
more information on the features, use and operation
of all of the factory-installed passive restraints.
WARNING - RESTRAINT SYSTEM
WARNING: DURING AND FOLLOWING ANY SEAT
BELT SERVICE, CAREFULLY INSPECT ALL SEAT
BELTS, BUCKLES, MOUNTING HARDWARE, AND
RETRACTORS FOR PROPER INSTALLATION,
OPERATION, OR DAMAGE. REPLACE ANY BELT
THAT IS CUT, FRAYED, OR TORN. STRAIGHTEN
ANY BELT THAT IS TWISTED. TIGHTEN ANY
LOOSE FASTENERS. REPLACE ANY BELT THAT
HAS A DAMAGED OR INOPERATIVE BUCKLE OR
RETRACTOR. REPLACE ANY BELT THAT HAS A
BENT OR DAMAGED LATCH PLATE OR ANCHOR
PLATE. NEVER ATTEMPT TO REPAIR A SEAT BELT
COMPONENT. ALWAYS REPLACE DAMAGED OR
FAULTY SEAT BELT COMPONENTS WITH THE COR-
RECT, NEW AND UNUSED REPLACEMENT PARTS
LISTED IN THE DAIMLERCHRYSLER MOPAR PARTS
CATALOG.
WARNING: ON VEHICLES EQUIPPED WITH AIR-
BAGS, DISABLE THE SUPPLEMENTAL RESTRAINT
SYSTEM BEFORE ATTEMPTING ANY STEERING
WHEEL, STEERING COLUMN, DRIVER AIRBAG,
PASSENGER AIRBAG, FRONT IMPACT SENSOR,
SIDE IMPACT SENSOR, SIDE CURTAIN AIRBAG, OR
INSTRUMENT PANEL COMPONENT DIAGNOSIS OR
SERVICE. DISCONNECT AND ISOLATE THE BAT-
TERY NEGATIVE (GROUND) CABLE, THEN WAIT
TWO MINUTES FOR THE SYSTEM CAPACITOR TO
DISCHARGE BEFORE PERFORMING FURTHER
DIAGNOSIS OR SERVICE. THIS IS THE ONLY SURE
WAY TO DISABLE THE SUPPLEMENTAL
RESTRAINT SYSTEM. FAILURE TO TAKE THE
PROPER PRECAUTIONS COULD RESULT IN ACCI-
DENTAL AIRBAG DEPLOYMENT AND POSSIBLE
PERSONAL INJURY.WARNING: AN AIRBAG INFLATOR UNIT MAY CON-
TAIN SODIUM AZIDE AND POTASSIUM NITRATE.
THESE MATERIALS ARE POISONOUS AND
EXTREMELY FLAMMABLE. CONTACT WITH ACID,
WATER, OR HEAVY METALS MAY PRODUCE HARM-
FUL AND IRRITATING GASES (SODIUM HYDROXIDE
IS FORMED IN THE PRESENCE OF MOISTURE) OR
COMBUSTIBLE COMPOUNDS. AN AIRBAG INFLA-
TOR UNIT MAY ALSO CONTAIN A GAS CANISTER
PRESSURIZED TO OVER 2500 PSI. DO NOT
ATTEMPT TO DISMANTLE AN AIRBAG UNIT OR
TAMPER WITH ITS INFLATOR. DO NOT PUNCTURE,
INCINERATE, OR BRING INTO CONTACT WITH
ELECTRICITY. DO NOT STORE AT TEMPERATURES
EXCEEDING 93É C (200É F).
WARNING: REPLACE ALL RESTRAINT SYSTEM
COMPONENTS ONLY WITH PARTS SPECIFIED IN
THE DAIMLERCHRYSLER MOPAR PARTS CATA-
LOG. SUBSTITUTE PARTS MAY APPEAR INTER-
CHANGEABLE, BUT INTERNAL DIFFERENCES MAY
RESULT IN INFERIOR OCCUPANT PROTECTION.
WARNING: THE FASTENERS, SCREWS, AND
BOLTS ORIGINALLY USED FOR THE RESTRAINT
SYSTEM COMPONENTS HAVE SPECIAL COATINGS
AND ARE SPECIFICALLY DESIGNED FOR THE
RESTRAINT SYSTEM. THEY MUST NEVER BE
REPLACED WITH ANY SUBSTITUTES. ANY TIME A
NEW FASTENER IS NEEDED, REPLACE IT WITH
THE CORRECT FASTENERS PROVIDED IN THE
SERVICE PACKAGE OR SPECIFIED IN THE
DAIMLERCHRYSLER MOPAR PARTS CATALOG.
WARNING: WHEN A STEERING COLUMN HAS AN
AIRBAG UNIT ATTACHED, NEVER PLACE THE COL-
UMN ON THE FLOOR OR ANY OTHER SURFACE
WITH THE STEERING WHEEL OR AIRBAG UNIT
FACE DOWN.
DIAGNOSIS AND TESTING - SUPPLEMENTAL
RESTRAINT SYSTEM
Proper diagnosis and testing of the supplemental
restraint system components, the PCI data bus, the
data bus message inputs to and outputs from the
ElectroMechanical Instrument Cluster (EMIC) or the
Airbag Control Module (ACM), as well as the
retrieval or erasure of a Diagnostic Trouble Code
(DTC) from the ACM requires the use of a DRBIIIt
scan tool. Refer to the appropriate diagnostic infor-
mation.
WJRESTRAINTS 8O - 5
RESTRAINTS (Continued)
Page 546 of 2199
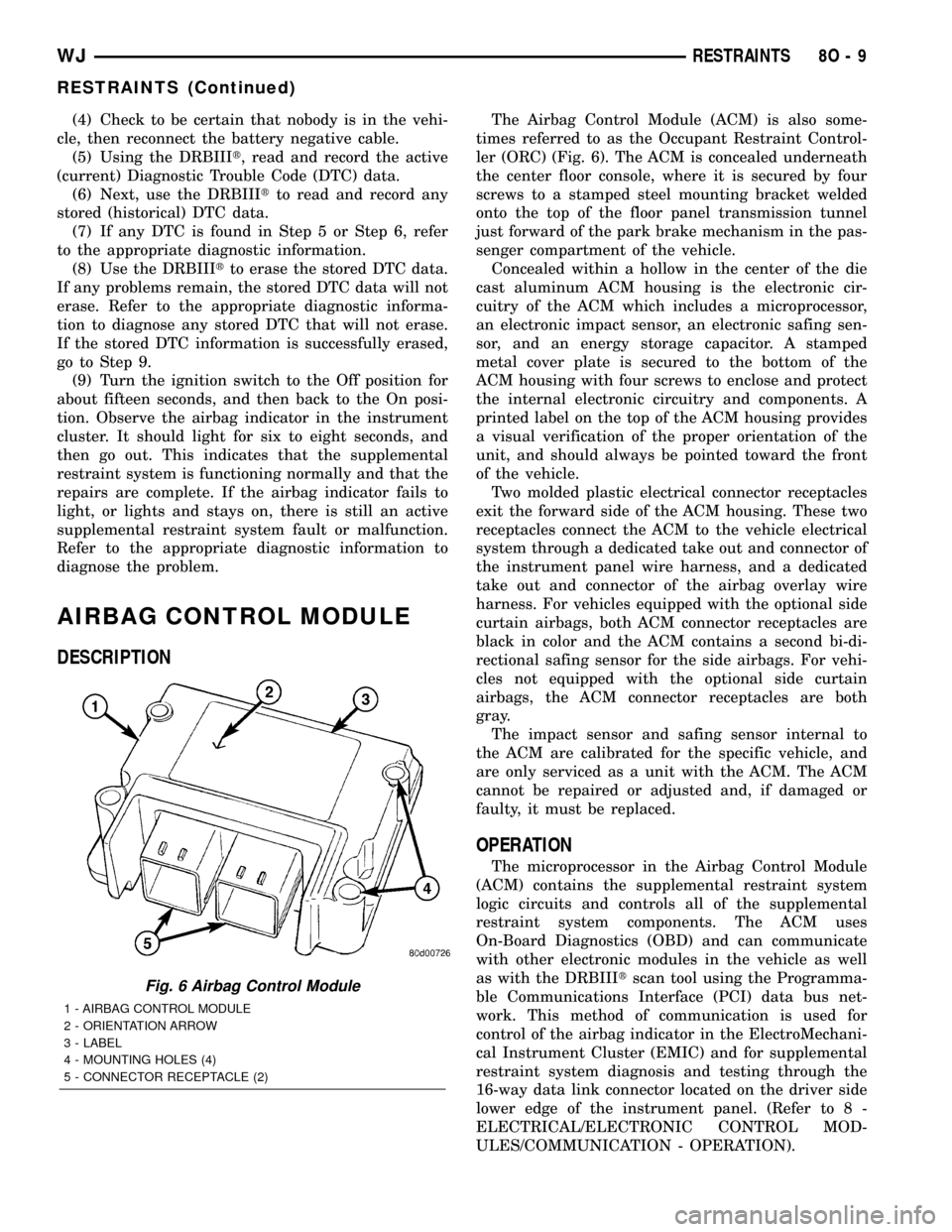
(4) Check to be certain that nobody is in the vehi-
cle, then reconnect the battery negative cable.
(5) Using the DRBIIIt, read and record the active
(current) Diagnostic Trouble Code (DTC) data.
(6) Next, use the DRBIIItto read and record any
stored (historical) DTC data.
(7) If any DTC is found in Step 5 or Step 6, refer
to the appropriate diagnostic information.
(8) Use the DRBIIItto erase the stored DTC data.
If any problems remain, the stored DTC data will not
erase. Refer to the appropriate diagnostic informa-
tion to diagnose any stored DTC that will not erase.
If the stored DTC information is successfully erased,
go to Step 9.
(9) Turn the ignition switch to the Off position for
about fifteen seconds, and then back to the On posi-
tion. Observe the airbag indicator in the instrument
cluster. It should light for six to eight seconds, and
then go out. This indicates that the supplemental
restraint system is functioning normally and that the
repairs are complete. If the airbag indicator fails to
light, or lights and stays on, there is still an active
supplemental restraint system fault or malfunction.
Refer to the appropriate diagnostic information to
diagnose the problem.
AIRBAG CONTROL MODULE
DESCRIPTION
The Airbag Control Module (ACM) is also some-
times referred to as the Occupant Restraint Control-
ler (ORC) (Fig. 6). The ACM is concealed underneath
the center floor console, where it is secured by four
screws to a stamped steel mounting bracket welded
onto the top of the floor panel transmission tunnel
just forward of the park brake mechanism in the pas-
senger compartment of the vehicle.
Concealed within a hollow in the center of the die
cast aluminum ACM housing is the electronic cir-
cuitry of the ACM which includes a microprocessor,
an electronic impact sensor, an electronic safing sen-
sor, and an energy storage capacitor. A stamped
metal cover plate is secured to the bottom of the
ACM housing with four screws to enclose and protect
the internal electronic circuitry and components. A
printed label on the top of the ACM housing provides
a visual verification of the proper orientation of the
unit, and should always be pointed toward the front
of the vehicle.
Two molded plastic electrical connector receptacles
exit the forward side of the ACM housing. These two
receptacles connect the ACM to the vehicle electrical
system through a dedicated take out and connector of
the instrument panel wire harness, and a dedicated
take out and connector of the airbag overlay wire
harness. For vehicles equipped with the optional side
curtain airbags, both ACM connector receptacles are
black in color and the ACM contains a second bi-di-
rectional safing sensor for the side airbags. For vehi-
cles not equipped with the optional side curtain
airbags, the ACM connector receptacles are both
gray.
The impact sensor and safing sensor internal to
the ACM are calibrated for the specific vehicle, and
are only serviced as a unit with the ACM. The ACM
cannot be repaired or adjusted and, if damaged or
faulty, it must be replaced.
OPERATION
The microprocessor in the Airbag Control Module
(ACM) contains the supplemental restraint system
logic circuits and controls all of the supplemental
restraint system components. The ACM uses
On-Board Diagnostics (OBD) and can communicate
with other electronic modules in the vehicle as well
as with the DRBIIItscan tool using the Programma-
ble Communications Interface (PCI) data bus net-
work. This method of communication is used for
control of the airbag indicator in the ElectroMechani-
cal Instrument Cluster (EMIC) and for supplemental
restraint system diagnosis and testing through the
16-way data link connector located on the driver side
lower edge of the instrument panel. (Refer to 8 -
ELECTRICAL/ELECTRONIC CONTROL MOD-
ULES/COMMUNICATION - OPERATION).
Fig. 6 Airbag Control Module
1 - AIRBAG CONTROL MODULE
2 - ORIENTATION ARROW
3 - LABEL
4 - MOUNTING HOLES (4)
5 - CONNECTOR RECEPTACLE (2)
WJRESTRAINTS 8O - 9
RESTRAINTS (Continued)
Page 561 of 2199
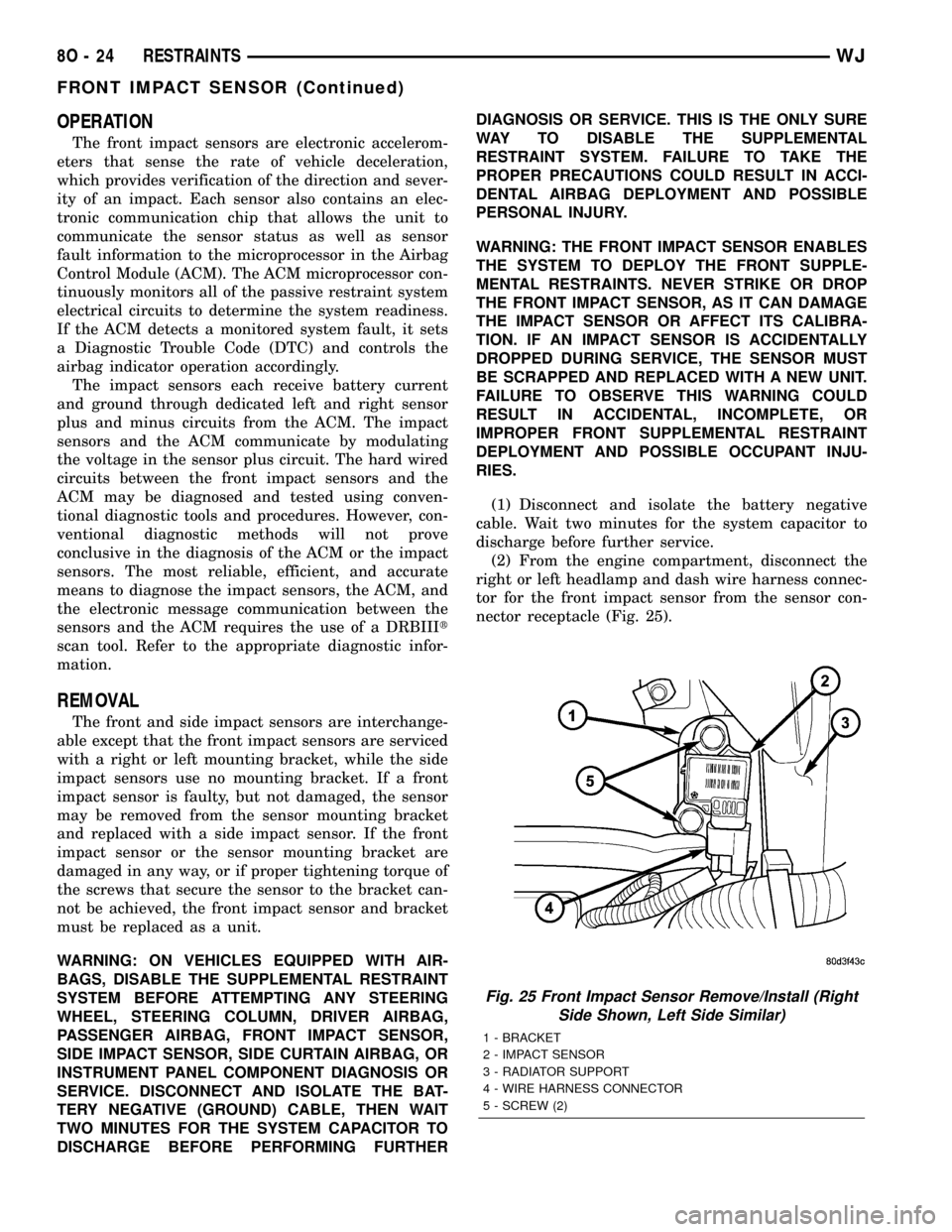
OPERATION
The front impact sensors are electronic accelerom-
eters that sense the rate of vehicle deceleration,
which provides verification of the direction and sever-
ity of an impact. Each sensor also contains an elec-
tronic communication chip that allows the unit to
communicate the sensor status as well as sensor
fault information to the microprocessor in the Airbag
Control Module (ACM). The ACM microprocessor con-
tinuously monitors all of the passive restraint system
electrical circuits to determine the system readiness.
If the ACM detects a monitored system fault, it sets
a Diagnostic Trouble Code (DTC) and controls the
airbag indicator operation accordingly.
The impact sensors each receive battery current
and ground through dedicated left and right sensor
plus and minus circuits from the ACM. The impact
sensors and the ACM communicate by modulating
the voltage in the sensor plus circuit. The hard wired
circuits between the front impact sensors and the
ACM may be diagnosed and tested using conven-
tional diagnostic tools and procedures. However, con-
ventional diagnostic methods will not prove
conclusive in the diagnosis of the ACM or the impact
sensors. The most reliable, efficient, and accurate
means to diagnose the impact sensors, the ACM, and
the electronic message communication between the
sensors and the ACM requires the use of a DRBIIIt
scan tool. Refer to the appropriate diagnostic infor-
mation.
REMOVAL
The front and side impact sensors are interchange-
able except that the front impact sensors are serviced
with a right or left mounting bracket, while the side
impact sensors use no mounting bracket. If a front
impact sensor is faulty, but not damaged, the sensor
may be removed from the sensor mounting bracket
and replaced with a side impact sensor. If the front
impact sensor or the sensor mounting bracket are
damaged in any way, or if proper tightening torque of
the screws that secure the sensor to the bracket can-
not be achieved, the front impact sensor and bracket
must be replaced as a unit.
WARNING: ON VEHICLES EQUIPPED WITH AIR-
BAGS, DISABLE THE SUPPLEMENTAL RESTRAINT
SYSTEM BEFORE ATTEMPTING ANY STEERING
WHEEL, STEERING COLUMN, DRIVER AIRBAG,
PASSENGER AIRBAG, FRONT IMPACT SENSOR,
SIDE IMPACT SENSOR, SIDE CURTAIN AIRBAG, OR
INSTRUMENT PANEL COMPONENT DIAGNOSIS OR
SERVICE. DISCONNECT AND ISOLATE THE BAT-
TERY NEGATIVE (GROUND) CABLE, THEN WAIT
TWO MINUTES FOR THE SYSTEM CAPACITOR TO
DISCHARGE BEFORE PERFORMING FURTHERDIAGNOSIS OR SERVICE. THIS IS THE ONLY SURE
WAY TO DISABLE THE SUPPLEMENTAL
RESTRAINT SYSTEM. FAILURE TO TAKE THE
PROPER PRECAUTIONS COULD RESULT IN ACCI-
DENTAL AIRBAG DEPLOYMENT AND POSSIBLE
PERSONAL INJURY.
WARNING: THE FRONT IMPACT SENSOR ENABLES
THE SYSTEM TO DEPLOY THE FRONT SUPPLE-
MENTAL RESTRAINTS. NEVER STRIKE OR DROP
THE FRONT IMPACT SENSOR, AS IT CAN DAMAGE
THE IMPACT SENSOR OR AFFECT ITS CALIBRA-
TION. IF AN IMPACT SENSOR IS ACCIDENTALLY
DROPPED DURING SERVICE, THE SENSOR MUST
BE SCRAPPED AND REPLACED WITH A NEW UNIT.
FAILURE TO OBSERVE THIS WARNING COULD
RESULT IN ACCIDENTAL, INCOMPLETE, OR
IMPROPER FRONT SUPPLEMENTAL RESTRAINT
DEPLOYMENT AND POSSIBLE OCCUPANT INJU-
RIES.
(1) Disconnect and isolate the battery negative
cable. Wait two minutes for the system capacitor to
discharge before further service.
(2) From the engine compartment, disconnect the
right or left headlamp and dash wire harness connec-
tor for the front impact sensor from the sensor con-
nector receptacle (Fig. 25).
Fig. 25 Front Impact Sensor Remove/Install (Right
Side Shown, Left Side Similar)
1 - BRACKET
2 - IMPACT SENSOR
3 - RADIATOR SUPPORT
4 - WIRE HARNESS CONNECTOR
5 - SCREW (2)
8O - 24 RESTRAINTSWJ
FRONT IMPACT SENSOR (Continued)